玉米脱粒机结构原理设计
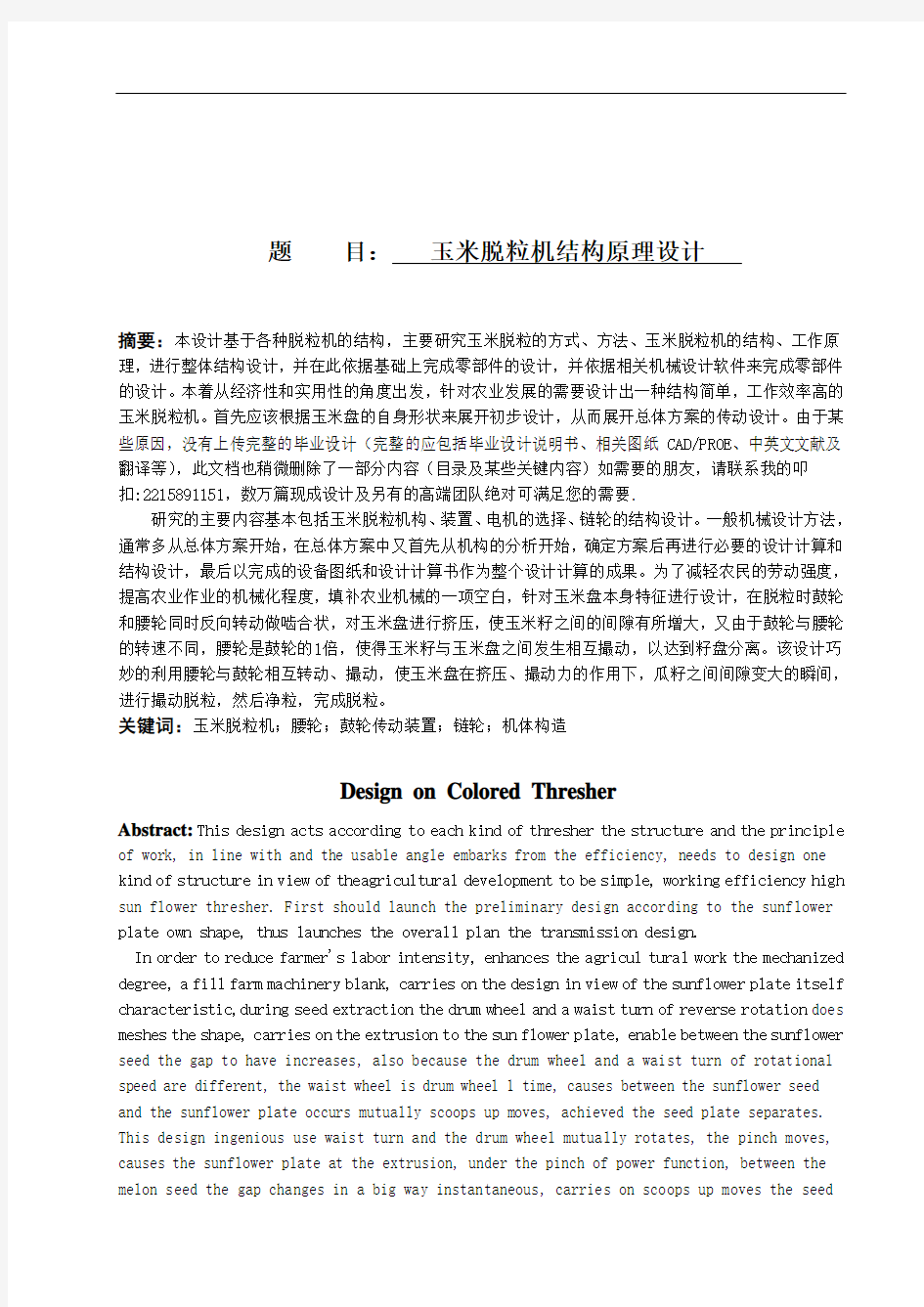

题目:玉米脱粒机结构原理设计
摘要:本设计基于各种脱粒机的结构,主要研究玉米脱粒的方式、方法、玉米脱粒机的结构、工作原理,进行整体结构设计,并在此依据基础上完成零部件的设计,并依据相关机械设计软件来完成零部件的设计。本着从经济性和实用性的角度出发,针对农业发展的需要设计出一种结构简单,工作效率高的玉米脱粒机。首先应该根据玉米盘的自身形状来展开初步设计,从而展开总体方案的传动设计。由于某些原因,没有上传完整的毕业设计(完整的应包括毕业设计说明书、相关图纸CAD/PROE、中英文文献及翻译等),此文档也稍微删除了一部分内容(目录及某些关键内容)如需要的朋友,请联系我的叩
扣:2215891151,数万篇现成设计及另有的高端团队绝对可满足您的需要.
研究的主要内容基本包括玉米脱粒机构、装置、电机的选择、链轮的结构设计。一般机械设计方法,通常多从总体方案开始,在总体方案中又首先从机构的分析开始,确定方案后再进行必要的设计计算和结构设计,最后以完成的设备图纸和设计计算书作为整个设计计算的成果。为了减轻农民的劳动强度,提高农业作业的机械化程度,填补农业机械的一项空白,针对玉米盘本身特征进行设计,在脱粒时鼓轮和腰轮同时反向转动做啮合状,对玉米盘进行挤压,使玉米籽之间的间隙有所增大,又由于鼓轮与腰轮的转速不同,腰轮是鼓轮的1倍,使得玉米籽与玉米盘之间发生相互撮动,以达到籽盘分离。该设计巧妙的利用腰轮与鼓轮相互转动、撮动,使玉米盘在挤压、撮动力的作用下,瓜籽之间间隙变大的瞬间,进行撮动脱粒,然后净粒,完成脱粒。
关键词:玉米脱粒机;腰轮;鼓轮传动装置;链轮;机体构造
Design on Colored Thresher
Abstract:This design acts according to each kind of thresher the structure and the principle of work, in line with and the usable angle embarks from the efficiency, needs to design one kind of structure in view of theagricultural development to be simple, working efficiency high sun flower thresher. First should launch the preliminary design according to the sunflower plate own shape, thus launches the overall plan the transmission design.
In order to reduce farmer's labor intensity, enhances the agricul tural work the mechanized degree, a fill farm machinery blank, carries on the design in view of the sunflower plate itself characteristic,during seed extraction the drum wheel and a waist turn of reverse rotation does meshes the shape, carries on the extrusion to the sun flower plate, enable between the sunflower seed the gap to have increases, also because the drum wheel and a waist turn of rotational speed are different, the waist wheel is drum wheel 1 time, causes between the sunflower seed and the sunflower plate occurs mutually scoops up moves, achieved the seed plate separates. This design ingenious use waist turn and the drum wheel mutually rotates, the pinch moves, causes the sunflower plate at the extrusion, under the pinch of power function, between the melon seed the gap changes in a big way instantaneous, carries on scoops up moves the seed
extraction, then only the grain, completes the entire design request task.The manufacture principle by the rack, the waist wheel, the drum wheel, the transmission device, the electrical machinery bearing and so on is composed. Turn and the drum wheel outline shape forces the sun flower plate using the waist to have the distortion along its own shape, between the melon seed the gap changes in a big way instantaneous, carries on scoops up moves the seed extraction, uses the ventilator only grain, this design structure reasonable, the usability is strong. Cost inexpensive, the market prospect is broad, does not lose is one kind of sunflower seed extraction best choice.
Key word:Sunflower threshers, waist wheel, drum wheel transmission device, chain wheel, organism structure;
引言
脱粒机是用于对小麦、水稻、玉米、高粱、大豆及其它杂粮等作物进行脱粒作业的重要收获机械,在我国广大农村使用十分广泛。脱粒机在我国生产使用已有数十年的历史,将玉米籽(谷物)从作物的穗头上分离下来所使用的机具,称为脱粒机具。质量合格的脱粒机,应该是坚固耐用的、故障少、使用保养方便、结构简单可靠。同时,还应满足以下的农业技术要求:玉米籽应当从玉米盘上脱下来,脱粒要干净。脱下的玉米籽不要破碎、情洁、不混其它玉米盘、杂物等脱粒时应尽量减少玉米盘的损坏,以保证玉米籽的完整。脱粒机在一定程度上应有一定的通用性,尽可能适用于托多种农作物,从而以提高机具的利用率。所设计的脱粒机应有较高的生产率,功率消耗少,即其造价低。脱粒系统是联合收割机的核心,它决定着其他各部分的工作性能。研究脱粒空间内谷物的运动规律是联合收割机脱粒机理研究的关键内容之一。
脱粒机生产在我国虽已有数十年历史,但不少企业仍延袭十几年以前的生产方式进行生产和管理,企业管理水平相对落后。全国200多家企业中,至今只有1家企业进行了质量保证体系认证就足以说明这一问题。此外,产品品种单一,产品更新换代适应不了市场的需求,一些产品多年存在的性能问题,如风扇型脱粒机存在的对作物干湿度适应性差的问题一直得不到解决,原因就是多数企业经济效益欠佳,拿不出更多的资金和技术力量用于科研和开发新产品;也有的是由于企业领导急功近利,对开发新产品的重要性认识不足。然而产品更新换代的越慢,越难占领市场,企业效益越差,从而使不少企业的生产陷入了恶性循坏。
目前脱粒机生产企业产量最大的为3万多台,最少的仅几十台,不少企业的生产未能形成适度的规模。这主要是因为脱粒机是季节性很强的产品,产品销售往往仅在1个月或者十几天的时间,资金周转时间长,不少企业明知进行技术改造形成适度规模生产能降低成本,提高经济效益,但苦于流动资金不足或贷款困难,无力进行适度规模生产,再加上近几年脱粒机行业活动和信息交流不畅,不能根据市场变化及时调整生产结构、产品品种及生产数量,从而导致经济效益不理想。
因此我们可以看出脱粒机目前仍有较大的存在空间,对脱粒机的改进设计,使其价格
低廉、工作可靠、性能优良、尽可能同时完成多项作业是时代的需要。
初步拟定设计过程
查阅相关资料进行调查研究、进行方案设计(是否合理)、进行整体结构相关零件的设计、进行并不断优化设计、试制完成设计内容。
1 设计方案
1.1 总体方案设计
包括传动装置的总体设计,传动件与支撑零件的设计计算。一般机械设计方法,通常多从总体方案开始,在总体方案中又首先从机构的分析开始,确定方案后再进行必要的设计计算和结构设计,最后以完成的设备图纸和设计计算书作为整个设计计算的成果。
1.2总体结构设计
确定传动方案,选择电动机,计算传动装置的运动和动力参数从而去确定总传动比和分配各级传动比,计算各轴功率、转速转矩。
图1 玉米脱粒机简图
2 玉米脱粒机的设计
2.1 选择电动机
2.1.1 确定电机转速脱粒机最大功率的确定根据公式:P=Tn/9550 (KW)可以算出轴的计算功率Pa。其中 T—为轴的工作转矩;n—为工作轴的转速。根据资料结合实际可以知道腰轮和鼓轮的搓动力的大小F≧500N,大概估计 F=600N,可以确定工作轴的计算转矩Ta 。根据资料估计腰轮的转速为700 r/min 根据公式 Ta=FD 其中D 为切削力作用点到轴的距离,Dmax=0.125m。故可以得到最大转矩Tmax=F Dmax=600×0.125=75(Nm)。最大计算功率根据公式:Pamax=Tn/9550=(75×700)/9550=5.4973822≈5.5 (KW)。根据工作负载的大小和性质、速度以及工作环境来选择电动机的类型、结构型式、功率转速,确定电动机的型号。根据玉米脱粒机结构特点,传动装置的体积、重量小;所以速度不要太高。因此确定电动机转速时要综合考虑,分析电动机及传动装置的性能,尺寸、重量和价格因素。通常选用同步电动机。
2.1.2 确定电机工作效率电机所需功率按式:Pd = Pw/ηa (KW)、 Pw = FV/1000 (KW)所以 Pd= FV/1000ηa (KW)由电动机至链轮的传动总效率为:按设计要求可以知道从电动机到工作轴的传动总效率ηa=η1·η2·η3 其中η1—为带的传动效率、η2—为轴承的传动效率、η3—为链的传动效率。根据机械设计手册查出η1=0.96,η2=0.98,η3=0.98。所以可知ηa=η1·η24·η32=0.96×0.984×0.982= 0.85。通常情况下链传动的链速V≦12-15m/s 符合链传动的实际工作要求。根据资料选择链轮的转速为3 m/s;选用链轮2与链轮3之间所需的搓动力为420N 、链轮传动的转速为 200 r /minPd= FV/1000ηa =(420×3)/(1000×0.85)=1.4823529≈1.5 (KW)根据推荐传动比的合理范围,取V带传动的传动比 i1′=2-4;链轮传动的传动比i2′=3-4;则总传动比合理范围为 ia′= 6—16,故电动机转速的可选范围为 nd′= ia′·n=(6--16)×200 =1200—3200 r /min 符合这一范围的同步转速有 1400、1500 r /min,根据容量和转速,由机械设计手册查出适用的电动机型号,因此选定电动机型号为 Y90L-4。
根据资料和《机械设计手册-蔡春源》设计电动机的外形及安装尺寸。
2.1.3 确定电机的型号 初步确定采用Y 系列电动机采用Y90L-4型号的电动机。额定功率Ped=1.5KW 、同步转速1500m in r 、满载时(满载转速1400m in r 、电流
3.65A 、效率79%、功率因数CosФ=0.79)堵转电流/额定电流=6.5A 、堵转转矩/额定转矩=2.2、最大转矩/额定转矩=2.2、转动惯量=0.0027Kg.m 2、噪声67 db(A)、电动机重量27kg 、总传动比
12。参照表11-3各级传动的传动比常用值,可以知道i 带=2-4;i 链=3-4。
3 V 带及带轮的传动设计
3.1 带轮材料的选择
带轮是带传动中的重要零件,它必须满足下列要求:质量分布均匀;安装时对中性好,
转速高时要经过动平衡;铸造和焊接时的内应力小;轮槽工作面要精细加工(表面粗糙度一般为Ra=3.2),以减轻带的磨损;各槽尺寸和角度应保持一定的精度,以使载荷分布较为均匀等。带轮材料主要采用铸铁,常用材料的牌号为HT150或HT200;转速较高时宜采用铸钢(或用钢板冲击后焊接而成);小功率时可用铸铝或塑料。根据电动机的已知参数额定功率Ped=1.5KW 、转速1500m in r 、传动比i0=2、一天运转时间小余10小时。1.)工作情况系数Ka 由表14-7选取经表查出=1.1。 2.)确定计算功率Pca :按所传递的功率P 、载荷性质和每天运转时间等因素来确定计算功率。Pca=KAP (KW) 式中; KA ——— 工作情况系数 , Pca =KAP=5.11.1?=1.65(KW)。
3.2 V 带的设计与计算
表1 V 带的设计与计算
设计计算项目
依据 结果 说明条件 工作情况系数KA
机械设计基础下册 []1 由表14-7 1.1 确定计算功率Pca
Pca=KA .P=1.1×1.5=1.65(KW) 1.65 (KW) 选取V 带型号
机械设计基础下册 图14-12 A 型 初选小带轮直径D1
机械设计基础下册 表14-2 140 mm 可选大值考虑装置问题 大带轮直径D2
D2=i × D1=2×140=280 280 mm 验算带的速度V
V=ЛD1n1/60×1000 10.26 m/s 在10-20m/s 范围内符合要求 初定中心距ɑ0
0.7(D1+D2)≦ɑ0≦2(D1+D2) 294≦a0≦840 350 mm 一般情况下参考实际机器结构确定 初算V 带所需的基准长度L
′d
L ′d=2ɑ0 +Л(D1+D2)/2+(D1+D2)2/4ɑ0 (1464.4 mm ) 1464 mm 选V 带的基准长度Ld
由表14-5 1433 mm 定V 带的公称(内周)长
度Li
由表14-5 1400 mm 定中心距ɑ
ɑ=ɑ0+(Ld-L ′d )/2 (334.3) 334 包角a 1
ɑ1=180˙-(D2-D1)×60/ɑ (154.9˙) 155˙ ≧120˙符合设计要求。 包角系数K a
由表14-8 0.92 长度系数K L
由表14-9 0.96 材质系数K 0.75
目前V 带强力层使用材料主要是棉和人造丝 单根V 带所传递的功率P0 由V=10.26 m/s ,D1=140mm 查表14-6 2.04
单根V 带功率增量ΔP0 ΔP0=0.0001ΔT ·n1 0.154
单根V 带传递扭矩的修正值ΔT 由表14-10 1.1
V 带根数Z Z= Pca/(P0K a K L +ΔP0) ·K 1.124901
取2根
实际带的根数Z ≦5符合 每米V 带质量q
由表14-3
0.1Kg/m
单根V 带的初拉力F0
F0=500·Pca(2.5/K a-1)/ VZ + qV 2 79.57N 80 N 轴上的压力Q Q=2·Z ·F0·sin a/2 310.735N
311 N
计算结果汇总:V 带规格:A 型、V 带的公称长度 1400 mm
V 带根数:Z=2
大小带轮直径:280mm 、140mm ;
中心距:334mm 轴上压力:310.735 N
3.3 带轮的结构设计
主要是根据带轮的基准直径选择结构型式;根据带的型号确定轮槽尺寸(表 14-12);
带轮的其它结构尺寸可参照图14-15所列经验公式计算。确定带轮各部分尺寸后,既可绘制出零件图,并按工艺要求注出相应的技术条件等。V 带两侧面夹角为40°,而轮槽楔角ψ0却是34°、36°、或38°,其原因是V 带在轮上弯曲时,其截面形状发生变化,外边(宽边)受拉而变窄,内边(窄边)受压而变宽,因而使V 带的楔角变小。根据(表 14-12)确定轮槽尺寸:A 型号
表2 带轮的结构
槽型剖面尺寸
m f t S bp δ B φ 38° 数值 12.5 3.5 16 10 11 6 B=(z-1)t+2s
Z 为带的根数 D 125-800 b ' 13.4
带轮1:d1=(1.8-2) d ,d 为轴的直径: D1 =140 mm 基准直径D=200;带宽选择13.4;
B=(z-1) t+2s=(2-1)×16+2×10=36 ,L=(1.5-2)d,当 B<1.5d 时,L=B 因为B<1.5d=1.5
×30=45、所以 L=B=36 ,带轮2:d1=(1.8-2) d=63-70,
mm f D D W 2875.322802=?+=+=,C ’=(1/7-1/4)B=5.14—9;
图2:小带轮
4 链传动设计与计算:
4.1 链轮材料的选择
在设计传动链时链节数以取偶数为宜,这样可以避免使用过渡链节,因为过渡链节会使链的承载能力下降。因为套筒滚子链已经标准化(GB1243·1-83),表15-1列出了单列套筒滚子链的主要尺寸和极限拉伸载荷。选择时可参考《机械设计基础下册-刘长荣р34》。链轮的材料应满足强度和耐磨性的要求。常有用中碳钢和中碳合金钢,热处理后齿面硬度为HRC40-50,或低碳钢,低碳合金钢渗碳并热处理后齿面硬度HRC50-60等。对于齿数较多的从动链轮,在载荷平稳、速度较低时,也可以用强度较高的铸铁链轮制造。小带轮转速1500r/min、小带轮直径140mm;大带轮直径为280mm、大带轮转速为750r/min。
4.2 链轮的基本传动方案
将链轮1与大带轮2一起并列安装在一起安装在轴承座上、再由链轮1传给安装有腰轮的链轮2、由链轮2传给带有鼓轮的链轮3、此时链轮2与链轮3同时反向转动。从而在脱粒时腰轮与鼓轮反向转动作啮合状,对玉米盘进行挤压,使玉米籽之间的间隙有所增大,又由于鼓轮与腰轮的转速不同。腰轮的转速比鼓轮的转速大,使玉米籽与玉米盘之间发生相互搓动,以达到籽盘分离。该设计巧妙的利用腰轮和鼓轮相互转动、利用腰轮和鼓轮轮廓形状迫使玉米盘沿其自身形状产生变形,瓜籽之间的间隙变大的瞬间,进行搓动、使玉米盘在挤压、搓动力的作用下,瓜籽之间的间隙变大的瞬间,进行搓动脱粒,然后净粒,完成整个设计要求任务。
4.3 对链轮的基本要求
滚子能顺利地进入啮合退出啮合,不易发生脱链,能够容许节距有较大的伸长率等。一般链传动的功率P≦100KW,传动比i≦6,链速V≦12-15m/s,效率η=0.92-0.98。设计链传动为多极链传动,参考设计手册联系实际工作原理、对链轮传动做出分析。
4.4 滚子链传动的设计
表3 滚子链传动的设计
小链轮齿数Z1 假定链传动链速 0.6-3 m/s
选取Z1≧Zmin=9;选取Z1=17 Z1≧9 链轮齿数应优先选取下列数列:17,19,
21,23,25,38,57:
传动比选取1.1
大链轮齿数Z2 计算得Z2=18.7 优先选取Z2=19 链轮齿数应优先选取下列数列:17,19,21,23,
25,38,57:
推荐Z2一般超过114
设计功率Pd KW Pd= KA ·P
=1×1.5=1.5 KW
P----传递功率KW
KA----工作情况系数查表8-2-7、8-2-8、8-2-9(р965)查得平稳运转KA =1
特定条件下单排链条传递功率P0KW P0=Pd/ Kz·KL ·Kp=1.5/(0.846
×1.02×1)= 1.74
Kz(Kz′)-----小链轮齿数系数查表15-3;查得
Kz=0.846
KL 链长系数由图15-13查得KL =1.02:(P44)
Kp选单列链,链排数系数由表15-4查得Kp=1
链条节距选
择P mm 根据P0和n1查图8-2-2(A系列)或
图8-2-3(B系列)选用合适的节距P
由表8-2-2查得选用08A链号链节距
12.7(手册P961)
为了保证传动平稳、结构简单紧凑,特别是在高速
下,以选用节距较小的链条,高速、功率大时,可
选用节距小的多排链
初定中心距ɑ0mm 一般取ɑ0=(30-50)P,
初取ɑ0=40·P=40×12.7=508 mm
或取ɑ0=35·P=444.5 对于中心距不可调整的链传动,ɑ0max≈30·P=30
×12.7=381 mm
(链节数)确定链条长度,常用链节数
LP表示LP节LP=2ɑ0/ P+(Z1+ Z2)/2+(P/ɑ
0)·[(Z2- Z1)/2Л]2=98 节
LP=98节
LP应圆整为整数,并宜取偶数,以避免使用过渡链
节(有过渡链节的奇数节链条,其极限拉伸载荷为
正常值的80%)
确定链条长
度L m L= LP·P/1000 =(98×
12.7)/1000=1.2446
计算中心距ɑC mm 当Z1≠Z2 时
ɑC = P·(2 LP- Z1- Z2)·K a =12.7
×(2×98-17-19)×0.25= 508
当Z1=Z2=Z 时
ɑC = P(LP-Z)/2
LP---取圆整成整数后的链节数;
Ka---系数查表 8-2-12;由表查得Ka= 0.25
(P966)
对于中心距不可调整和没有张紧装置时,ɑC值计算
精确到小数点后2位
实际中心距ɑmm ɑ=ɑC -Δɑ =508-0.003×
508=506.476
通常:Δɑ=(0.002-0.004)ɑC 为了保证链条松边有一个合理的安装垂度f即:f
=(0.01-0.02)ɑ;
对于中心距不可调整和没有张紧装置的链传动,Δɑ取较小值,中心距可调整时,Δɑ取较大值。
验算链速v m/
s V =( Z1·n1·P)/(60·1000)=(17×
750×12.7)/(60×1000)= 2.69875≈3
m/s
V ≦0.6 m/s 为低速传动
V 〉0.6-8 m/s 为中速传动
V 〉8 m/s 为高速传动显然此例为中速传动。通
常情况下链传动的链速V≦12-15m/s 符合链传动
的实际工作要求。
验算小链轮轮毂孔径(即轴孔直径)d k mm d k≦d kmax d k -----由支承轴的设计确定;
d kmax-----链轮轮毂孔的最大许用直径查表
8-2-13;
当不能满足要求时,可增大Z1 或 P,重新验算。
有效圆周力 F N F=1000·P/ v =(1000×1.5)/3=500N
或F=1000·P/ v=(1000×1.5)
/2.69875 = 555.8129
作用在轴上
的力FQ
(Q
)
N 对水平传动和倾斜传动FQ≈
(1.15-1.2)·K A·F
因载荷平稳FQ≈1.2×1×500=600 N
对接近垂直的传动:FQ=1.05· K A·F
润滑方式根据节距P与链速V见图8-2-4(设
计手册-蔡春源)械设计基础-刘长荣》由图15-12 查出选取润滑方式为滴油润滑
[]2
图3:链轮1
4.5 链轮3的传动与设计
计算并设计第三个带有鼓轮的链轮3 在设计时使链轮2的速度高于链轮3的速度,以使链轮2与链轮3 转速不同相互反向转动从而产生搓动力,按照链传动的二级传动设计与计算:
表4 链轮3的传动与设计
计算与设计项目符号单位计算公式及参考选定说明
链轮2的齿数Z2 由上步已知得出 Z2=19
链轮3的齿数Z3 假定链轮2的速度是链轮3的一倍初步
确定其传动比为i=2
Z3=38 在设计时使链轮2的速度高于
链轮3的速度
设计功率Pd KW Pd= KA ·P
=1×1.5=1.5 KW
P----传递功率KW
KA----工作情况系数查表
8-2-7、8-2-8、8-2-9(р965)查得平稳运转KA =1
链条节距选择P mm 同上一步选用08A链号链节距12.7(手
册P961)为了保证传动平稳、结构简单紧凑,特别是在高速下,以选用节距较小的链条。高速、功率大时,可选用节距小的多排
链
初定中心距ɑ0min mm ɑ0min=0.2·Z2·(i+1) ·P=0.2×19×3
×12.7=144.78≈145 在实际设计中链轮3的包角大
于
120?,且大小链轮传动是不
会相碰
(链节数)确定链条长度常用链节数LP表示LP节LP=2ɑ0min / P+(Z1+ Z2)/2+(P/ɑ
0min)·[(Z2- Z1)/2Л]2=52.13637 节,
LP=52节
LP应圆整为整数,并宜取偶
数,以避免使用过渡链节(有
过渡链节的奇数节链条,其极
限拉伸载荷为正常值的80%)
特定条件下单排链条传递功率P0KW P0=Pd/ Kz·KL ·Kp=1.5/(1×0.83×
1)= 0.83
Kz(Kz′)-----小链轮齿数系
数(Z2)查表15-3;查得Kz=1
KL 链长系数由图15-13查
得KL =0.83:(P44)Kp选单
列链,链排数系数由表15-4
查得Kp =1
确定链条长度 L m L = LP ·P/1000 =(52×12.7)/1000=
0.6604
验算链速 v m/s
V =( Z2·n2·P)/(60·1000)=(19×
681.8182×12.7)/(60×1000)=
2.69875≈3 m/s V ≦0.6 m/s 为低速传动 V 〉0.6-8 m/s 为中速传动 V 〉8 m/s 为高速传动 显然此例为中速传动通常情况下链传动的链速V ≦12-15m/s 符合链传动的实际工作要求。 验算小链轮轮毂
孔径(即轴孔直
径) d k mm
d k ≦d kmax d k -----由支承轴的设计确定; d kmax-----链轮轮毂孔的最大许用直径查表8-2-13;当不能满足要求时,可增大Z1 或 P,重新验算。 有效圆周力
F N F=1000·P/ v =(1000×1.5)/2.74=547N 有效圆周力 作用在轴上的力 FQ
(Q) N 对水平传动和倾斜传动FQ ≈(1.15-1.2)·K A ·F 因载荷平稳FQ ≈1.2
×1×547=656 N 对接近垂直的传动:
FQ=1.05· K A ·F
作用在轴上的力 润滑方式 根据节距P 与链速V 《机械设计基础-刘长荣》[]1 查出选取润滑方式为滴油润滑
4.6 链轮4的传动与设计
链轮4 的选用与计算:链轮1(顺时针转动)→ 链轮2(顺时针转动)→ 链轮3(逆
时针转动)→ 链轮4 (顺时针转动)→ 链轮1(顺时针转动),为了使设计结构合理性使链轮3反向转动,需要在链轮3的下方安装一个链轮4 。这样传递运动,由链轮4传递给链轮1 ,从而构成一个封闭的链传动。结合实际工作要求,此时要求链轮3与链轮4的中心距不宜过大。选取小链轮齿数Z4≧Zmin=9;假定链传动链速0.6-3 m/s ,选取小链轮齿数Z4=17,Z3=38;i= Z3/ Z4=38/17=2.2。通常i ≦7,推荐选用i=2-3.5。初定中心距ɑ0min=0.2·Z4·(i+1) ·P=0.2×17×3.2×12.7=144.78≈138.18
确定链条长度---常用链节数LP 表示:LP =2ɑ0min / P+(Z1+ Z2)/2+(P/ɑ0min )·[(Z2- Z1)/2Л]2 =50 (LP 应圆整为整数,并宜取偶数,以避免使用过渡链节(有过渡链节的奇数节链条,其极限拉伸载荷为正常值的80%)。确定链条长度:L = LP ·P/1000 =(50×12.7)/1000=0.64 ,n3=340.91 r/min n4=2.2×340.91=750.002≈750 r/min 此结果与链轮1的转速相同,所以构成一个封闭的链传动,符合设计要求。验算链速:V =( Z4·n4·P)/(60·1000)=(17×750×12.7)/(60×1000)= 2.699≈3 m/s
有效圆周力:F=1000·P/ v =(1000×1.5)/3=500 N 。作用在轴上的力:对水平传动和倾斜传动FQ ≈(1.15-1.2)·K A ·F; 因载荷平稳FQ ≈1.2×1×500=600 N 。
滚
子
图4 链链轮的基本参数和主要尺寸
图5 链轮1
4.7 链轮1的设计
4.7.1链轮1的计算见表5
表5 链轮1的计算
名称符号计算公式说明条件
链轮齿数Z1Z1=17 由以上条件可知
配用链条的节距P 节距:P=12.7
滚子外径:d1=7.95
A系列查表8-2-2 可知
分度圆直
径d d=P/[sin(180?/Z1)]=12.7/[sin(180?
/17)]= 69.12≈70
齿顶圆直
径da damax= d + 1.25·P- d1 =69.12+1.25×
12.7- 7.95= 77.05≈77
damin=d+(1-1.6/z)P-d1=69.12+(1-1.6/1
7) ×12.7-7.95 =72.67≈73
可在damax和damin 范围内选取,但当选用时,应
注意用展成法加工时有可能发生顶切
齿根圆直
径
df df =d- d1=70-7.95=62.05≈62
分度圆弦
齿高ha hamax=(0.625+0.8/Z)P-0.5d1=4.56
hamin=0.5(P-d1)=0.5 ·(12.7-7.95)=
2.375
Ha是为简化放大齿形图的绘制而引入的辅助设计
尺寸,hamax相应于damax; hamin相应于damin
齿侧凸缘(或排间槽)直径dg dg < P·cot(180?/z)-1.04·h2-0.76
=54.6322≈55
h2-----内链板高度 h2=12.07
A 系列查表 8-2-2
注意:da、dg 值取整数,其它尺寸精确到 0.01 mm 。
4.7.2 滚子链链轮1
表6 齿槽形状参数
名称符号单位计算公式
最大齿槽形状最小齿槽形状
齿面圆弧半
径re mm remin=0.008d1(Z12+180)=0.008×7.95×(172
+180) =29.8284≈30
remax=0.12 d1(z+2)=0.12×
7.95×19=18.126
齿沟圆弧半
径ri mm rimax=0.505d1+0.069˙3d1=0.505×
7.95+0.069×1.996=4.152474≈4.2
rimin=0.505·d1=4.01475=4
齿沟角ɑ˙ɑmin=120?-90?/Z1=120?-90?/17
=114.7059?=115?
ɑ
max=140?-90?/z=134.7059=135
4.7.3整体式小链轮Z1主要结构尺寸
表7 小链轮结构尺寸
名称符号结构尺寸及(参考)
轮毂厚度h h =K + d k/6 + 0.01d =3.2+35/6+0.01×70≈9
常数k; 式中d k max为链轮轮毂孔的最大许用直径,查表8-2-13;由节距P查出(当
Z1=17、dk≦dkmax =34,dk为轴孔直径按轴的尺寸确定,dk取35;)(P 966).(当
Z2=19、dk≦dkmax =41)
d <50 50-100 100-150 >150
K 3.2 4.8 6.4 9.5 轮毂长度l l =3.3h=3.3×9=29.7≈30;lmin=2.6·h=2.6×9=23.4≈23
轮毂直径dh dh = d k+2 h=35+2×9=48
dhmax< dg , dg 见表8-2-19
齿宽b f齿宽计算公式
单排p≦12.7p>12.7
0.93 b10.95 b1
当p>12.7时,经制造厂同意,亦可使用p≦12.7时的齿宽
b1----内链节内宽见表8-2-2 ——表8-2-4 查得 b1=7.85 齿宽b f1b f1=0.93×7.85=7.3005≈7.3
倒角宽b a ba=(0.1-0.15) p=0.15×12.7=1.905≈2倒角半径rx rx rx≧P
rx≧P=12.7
齿侧凸缘(圆角半
径)
R R=0.04·p=0.04×12.7=0.508≈0.5
腹板厚度t 由表8-2-24查得当P=12.7时,t=9.5 (P973)
图6 链轮2
4.8 链轮2的设计
4.8.1 链轮2的计算
表8 链轮2的计算
名称符号计算公式说明条件
链轮齿数Z2Z2=19 由以上条件可知
配用链条的
节距P 节距:P=12.7
滚子外径:d1=7.95
A系列查表8-2-2 可知
分度圆直径 d d=P/[sin(180?/Z2)]=12.7/[sin(180?/19)
]= 77.15928≈77
齿顶圆直径da damax= d + 1.25·P-d1=77+1.25×12.7-
7.95= 84.925≈85
damin=d+(1-1.6/Z2)P-d1=77+(1-1.6/19)
×12.7-7.95 =80.680526≈81可在damax和damin 范围内选取,但当选用时,应注意用展成法加工时有可能发生顶切
齿根圆直径df df =d- d1=77-7.95=69.05≈69
分度圆弦齿
高ha hamax=(0.625+0.8/ Z2)P-0.5d1=4.5
hamin=0.5(P-d1)=0.5 ·(12.7-7.95)=
2.375
Ha是为简化放大齿形图的绘制而引入的辅助设
计尺寸,hamax相应于damax; hamin相应于
damin
齿侧凸缘(或排间槽)直径dg dg < P·cot(180?/ Z2)-1.04·h2-0.76
=62.826289=63
h2-----内链板高度 h2=12.07
A 系列查表 8-2-2
注意:da、dg 值取整数,其它尺寸精确到 0.01 mm 。
4.8.2 滚子链链轮2齿槽形状参数表9 链链轮2齿槽形状参数
名称符
号单
位
计算公式
最大齿槽形状最小齿槽形状
齿面圆弧半
径re mm remin=0.008d1(Z22+180)=0.008
×7.95×(192+180) =34.4076≈34
remax=0.12 d1(Z2+2)=0.12×7.95×21=
20.034
齿沟圆弧半
径ri mm rimax=0.505d1+0.069 ˙
3d1=0.505×7.95+0.069×
1.996=4.152474≈4.2
rimin=0.505·d1=4.01475=4
齿沟角ɑ˙ɑmin=120?-90?/Z2=120?-90?/19
=115.26316?=115?
ɑmax=140?-90?/Z2=135.26316=135.3
4.8.3 整体式小链轮Z2主要结构尺寸
表10 小链轮Z2结构尺寸
名称符号结构尺寸及(参考)
轮毂厚度h h =K + dk/6 + 0.01d =3.2+35/6+0.01×77=9.08≈9
常数k; 式中dkmax为链轮轮毂孔的最大许用直径,查表8-2-13;由节距P查出(当
Z1=17、dk≦dkmax =34,dk为轴孔直径按轴的尺寸确定,dk取35;)(P 966)
(当Z2=19、dk≦dkmax =41)
d <50 50-100 100-150 >150
K 3.2 4.8 6.4 9.5 轮毂长度l l =3.3h=3.3×9=29.7≈30
lmin=2.6·h=2.6×9=23.4≈23
轮毂直径dh dh = dk+2 h=35+2×9=53
dhmax< dg , dg 见表8-2-19
齿宽bf 见表8-2-22 (P972)
齿宽计算公式
单排p≦12.7 p>12.7
0.93 b1 0.95 b1
当p>12.7时,经制造厂同意,亦可使用p≦12.7时的齿宽
b1----内链节内宽见表8-2-2 ——表8-2-4 查得 b1=7.85 齿宽bf1 bf1=0.93×7.85=7.3005≈7.3
倒角宽ba ba=(0.1-0.15) p =0.15×12.7=1.905≈2 倒角半径rx rx rx≧P
rx≧P=12.7
齿侧凸缘(圆角半
径)
R R=0.04·p=0.04×12.7=0.508≈0.5
腹板厚度t 由表8-2-24查得当P=12.7时,t=9.5 (P973)
图7 链轮3
4.9 链轮3的设计
4.9.1链轮3的计算
表11 链轮3的计算
名称符号计算公式说明条件
链轮齿数Z3Z3=38 由以上条件可知
配用链条的
节距P 节距:P=12.7
滚子外径:d1=7.95
A系列查表8-2-2 可知
分度圆直径 d d=P/[sin(180?/Z3)]=12.7/[sin(180?
/38)]= 153.79148≈154
齿顶圆直径da damax= d + 1.25·P- d1 =154+1.25×12.7-
7.95= 161.925≈162
damin=d+(1-1.6/Z2)P-d1=154+(1-1.6/38)
×12.7-7.95 =158.21526≈158可在damax和damin 范围内选取,但当选用时,应注意用展成法加工时有可能发生顶切
齿根圆直径df df =d- d1=154-7.95=146.05≈146
分度圆弦齿
高ha hamax=(0.625+0.8/ Z2)P-0.5d1=4.2
hamin=0.5(P-d1)=0.5 ·(12.7-7.95)=
2.375
Ha是为简化放大齿形图的绘制而引入的辅助设
计尺寸,hamax相应于damax; hamin相应于damin
齿侧凸缘(或排间槽)直径dg dg < P·cot(180?/ Z3)-1.04·h2-0.76
=62.826289=140.0651≈140
h2-----内链板高度 h2=12.07
A 系列查表 8-2-2
注意:da、dg 值取整数,其它尺寸精确到 0.01 mm 。
4.9.2滚子链链轮3齿槽形状参数
表12 链轮3齿槽形状参数
名称符号单位
计算公式
最大齿槽形状最小齿槽形状
齿面圆弧半径re mm
remin=0.008d1(Z32+180)=0.008×7.95×
(382+180) =103.2864≈103
remax=0.12 d1(Z3+2)=0.12×7.95×40=
38.16=38
齿沟圆弧半径ri mm
rimax=0.505d1+0.069 ˙3d1=0.505×
7.95+0.069×1.996=4.152474≈4.2
rimin=0.505·d1=4.01475=4
齿沟角ɑ(˙)ɑmin=120?-90?/Z3=120?-90?/38
=117.63158?=118?
ɑ
max=140?-90?//Z3=134.7059=137.63158
=138
4.9.3整体式钢制小链轮Z3主要结构尺寸
表13 小链轮Z3主要结构尺寸
名称符号结构尺寸及(参考)
轮毂厚度h h =K + d k/6 + 0.01d =3.2+35/6+0.01×70≈9
常数k; 式中d k max为链轮轮毂孔的最大许用直径,查表8-2-13;由节距P查出(当
Z1=17、dk≦dkmax =34,dk为轴孔直径按轴的尺寸确定,dk取35;)(P 966),
(当Z2=19、dk≦dkmax =41)
d <50 50-100 100-150 >150
K 3.2 4.8 6.4 9.5 轮毂长度l l =3.3h=3.3×9=29.7≈30
lmin=2.6·h=2.6×9=23.4≈23
轮毂直径dh dh = d k+2 h=35+2×9=53
dhmax< dg , dg 见表8-2-19
齿宽b f见表8-2-22 (P972)
齿宽计算公式
单排p≦12.7p>12.7
0.93 b10.95 b1
当p>12.7时,经制造厂同意,亦可使用p≦12.7时的齿宽
b1----内链节内宽见表8-2-2 ——表8-2-4 查得 b1=7.85 齿宽b f1b f1=0.93×7.85=7.3005≈7.3
倒角宽b a ba=(0.1-0.15) p =0.15×12.7=1.905≈2倒角半径rx rx rx≧P
rx≧P=12.7
圆角半径R R=0.04·p=0.04×12.7=0.508≈0.5
腹板厚度t 由表8-2-24查得当P=12.7时,t=9.5 (P973)
图8 链轮4
4.10 链轮4的设计
4.10.1 链轮4的计算
表14 链轮4的计算
名称符号计算公式说明条件
链轮齿数Z4Z4=17 由以上条件可知
配用链条的节距P 节距:P=12.7
滚子外径:d1=7.95
A系列查表8-2-2 可知
分度圆直
径d d=P/[sin(180?/Z4)]=12.7/[sin(180?
/17)]= 69.12≈70
齿顶圆直
径da damax= d + 1.25·P- d1 =69.12+1.25×
12.7- 7.95= 77.05≈77
damin=d+(1-1.6/Z4)P-d1=69.12+(1-1.6/
17) ×12.7-7.95 =72.67≈73
可在damax和damin 范围内选取,但当选用时,应
注意用展成法加工时有可能发生顶切
齿根圆直
径
df df =d- d1=70-7.95=62.05≈62
分度圆弦齿高ha hamax=(0.625+0.8/Z4)P-0.5d1=4.56
hamin=0.5(P-d1)=0.5 ·(12.7-7.95)=
2.375
Ha是为简化放大齿形图的绘制而引入的辅助设计
尺寸,hamax相应于damax; hamin相应于damin
齿侧凸缘(或排间槽)直径dg dg < P·cot(180?/ Z4)-1.04·h2-0.76
=54.6322≈55
h2-----内链板高度 h2=12.07
A 系列查表 8-2-2
注意:da、dg 值取整数,其它尺寸精确到 0.01 mm 。
4.10.2 滚子链链轮4齿槽形状参数
表15 链轮4齿槽形状参数
名称符号单位计算公式
最大齿槽形状最小齿槽形状
齿面圆弧半
径re mm remin=0.008d1(Z42+180)=0.008×7.95×(172
+180) =29.8284≈30
remax=0.12 d1(Z4+2)=0.12×
7.95×19=18.126
齿沟圆弧半
径ri mm rimax=0.505d1+0.069 ˙3d1=0.505×
7.95+0.069×1.996=4.152474≈4.2
rimin=0.505·d1=4.01475=4
齿沟角ɑ˙ɑmin=120?-90?/Z4=120?-90?/17
=114.7059?=115?
ɑ
max=140?-90?/Z4=134.7059=135
4.10.3整体式钢制小链轮Z4主要结构尺寸
表16 小链轮Z4结构尺寸
名称符号结构尺寸及(参考)
轮毂厚度h h =K + d k/6 + 0.01d =3.2+35/6+0.01×70≈9
常数k; 式中d k max为链轮轮毂孔的最大许用直径,查表8-2-13;由节距P查出(当
Z1=17、dk≦dkmax =34,dk为轴孔直径按轴的尺寸确定,dk取35;)(P 966)(当
Z2=19、dk≦dkmax =41)
d <50 50-100 100-150 >150
K 3.2 4.8 6.4 9.5 轮毂长度l l =3.3h=3.3×9=29.7≈30
lmin=2.6·h=2.6×9=23.4≈23
轮毂直径dh dh = d k+2 h=30+2×9=48
dhmax< dg , dg 见表8-2-19
齿宽b f见表8-2-22 (P972)
齿宽计算公式
单排p≦12.7p>12.7
0.93 b10.95 b1
当p>12.7时,经制造厂同意,亦可使用p≦12.7时的齿宽
b1----内链节内宽见表8-2-2 ——表8-2-4 查得 b1=7.85 齿宽b f1b f1=0.93×7.85=7.3005≈7.3
倒角宽b a ba=(0.1-0.15) p =0.15×12.7=1.905≈2倒角半径rx rx rx≧P
rx≧P=12.7
圆角半径R R=0.04·p=0.04×12.7=0.508≈0.5
腹板厚度t 由表8-2-24查得当P=12.7时,t=9.5 (P973)
4.11 链传动的失效形式
4.11.1 链条铰链的磨损链轮与链条进入啮合和脱离啮合过程中,由于铰链的销轴与套筒间承受较大的压力和有相对转动,因而导致承压面发生磨损,使链的实际节距变长,啮合点沿齿高外移,最终产生跳齿和脱链现象。它是开式齿轮传动的主要形式。
4.11.2 链的疲劳破坏链在传动过程中,紧边和松边的拉力是不相等的,再加上传动中的动载荷,使得它的各元件都是在变应力的作用下工作,在中、低速时,经过一定循环次
数后,链板首先产生疲劳破坏;高速时由于滚子进入啮合时的冲击载荷剧增,套筒或滚子先于链板产生冲击疲劳破坏。
4.11.3 多次冲击破断链条在反复启动、反转、制动时所产生的巨大惯性冲击作用下,销轴、套筒、滚子等元件不到疲劳时就产生破断。它的载荷较疲劳破坏允许的载荷要大,但较一次冲击破断载荷要小。它的应力总循环次数一般在104以内。
4.11.4 链条的胶合高速和润滑不良的传动,销轴、套筒的工作面会因温度过高而发生胶合。
4.11.5 过载拉断链条所受载荷超过了链条静强度而被拉断。
5 轴的结构设计
5.1 轴材料的选择
轴的材料主要采用碳钢和合金钢,也可采用球墨铸铁。碳钢有足够的强度,对应力集中不太敏感,便于进行机械加工和热处理,价格低廉,应用广泛。一般机器的轴,可用30、40、50等牌号的优质中碳钢,其中最常用的为45号钢。为了改善机械性能,应进行正火或调制处理。对于轻载或不重要的轴,一般不需要进行热处理,可采用A3、A4、A5等普通碳素钢。合金钢的机械性能(强度、耐磨性、硬度)更高,多用于制造高速重载及受力大而又要求尺寸小、重量轻的轴。对于在高温、低温、或由腐蚀介质条件下工作的轴,则更宜用合金钢来制造。轴的材料应根据轴的工作状况、重要性和结构复杂程度、生产批量、材料供应情况、加工可能性以及经济性等因素,综合考虑、合理选取。
5.2 轴结构的基本要求
设计轴的基本要求是保证轴具有:1.足够的强度和刚度。即所要求设计的轴具有足够的承载能力,以保证轴在预期寿命内能正常的工作。2.合理的结构。即要求所设计的轴便于加工,疲劳强度高,轴上的零件便于拆装,并且相对于轴有可靠的固定方式。
轴的结构设计应满足的要求:1)轴及轴上的零件要有确定的工作位置;2)轴上零件应便于拆装和调整;3)轴具有良好的制造及装配工艺性;4)有利于提高轴的强度、刚度,有利于节约材料和减轻重量。
根据脱粒机的工作要求和机构特性查表确定轴的材料及其机械性能:
表17 轴的材料及其机械性能
材料牌号热处
理毛坯
直径
(mm)
硬度(HBS)拉伸强度极
限δB
拉伸屈服极
限δs
弯曲疲劳极
限δ-1
剪切疲劳极
限ζ-1
备注
45号钢调制≦200 217-255 (MPa)应用
最为
广泛
650 360 300 155
5.3 初步确定轴1的各段直径和长度
根据以上的计算数据来计算轴的传递功率P : V=ЛDn/60×1000(3.14×280×750)/(60
×1000) =10.99 有效圆周力F=500 P=FV/1000=(500×10.99)/1000=5.495kw 。估算轴端直径按表 18-2 轴常用的几种材料的[τ]T 及A0 值: 当轴的材料为 45 号钢时
[τ]T=30-40、A0=118-107,(因轴端受弯矩,A0去平均值)所以 A0=110,轴的转速为750 r/min 。
5.3.1 估算轴的最小直径 从而可以计算出轴的最小直径为:d ≧A0 3n P =110×3750495.5=21.36mm 。为了保证安装强度与安装尺寸,根据表18-3 标准直径系列 选择轴的最小直径dmin=35mm 。
图9 轴1结构
5.3.2 拟定轴上零件的装配方案 从右到左的顺序为带轮2、套筒、链轮1、套筒、滚动轴承和轴承支座;轴的右端直径为35,根据带轮2的宽度B ,从而确定装带轮的端轴长为36 ,为了使带轮2能够很好的定位需在带轮2的左端设计成一个套筒,套筒长度为10mm,厚度为5mm ,套筒直径为45mm 。在套筒的左端需安装链轮1,链轮1与带轮2一起安装在同一根轴上。根据以上整体式小链轮Z1主要结构尺寸的计算:轮毂长度 L=23,所以安装在链轮1的轴长为23mm ,轴径为35mm ,链轮1 的左端的定位依靠套筒来实现,套筒厚度5mm ,套筒处的轴径为45mm ,长度为10mm 。左端设计成一段长轴轴径为40mm ,长度为360mm 。左端设计成轴径为35mm ,根据机械设计手册查得轴径为35mm 时的轴承型号,初步选择角接触球轴承7307。(P711—GB292--83)D=80、D1=6
6.1、B=21、d=35mm 、d1=49.9;所以轴承长度为21mm 。为了使轴承很好的固定左端用开口的止推弹簧圈来固定,以保证止推弹簧圈与轴承的紧密配合。装配止推弹簧圈的那段轴设计为宽为5mm,深度为5mm,根据轴的结构设计将止推弹簧圈的厚度设计成10mm,宽度设计为5mm ,厚度为10mm. 左端轴长为10mm.
5.3.3 轴上零件的轴向定位 带轮2与轴的周向定位采用楔键联接,根据带轮轴的直径d6-7=35mm,《机械设计手册》GB 1054-79;(P291)查的楔键的剖面尺寸为:b ×h ×l=10×8×22,键槽用铣刀加工。链轮1与轴的周向定位联接用普通平键联接。根据轴的直径d4-5=38 《机械设计手册》GB 1096-79;(P286)查的普通平键的剖面尺寸为:b ×h ×l=10
×8×18。同时为了保证带轮与轴配合有良好的对中性,故选从动带轮与轴的配合为6
7t H 。角接触球轴承与轴的周向定位也是借配合来保证的,此处初选6
7s H 。