张力调较及故障处理

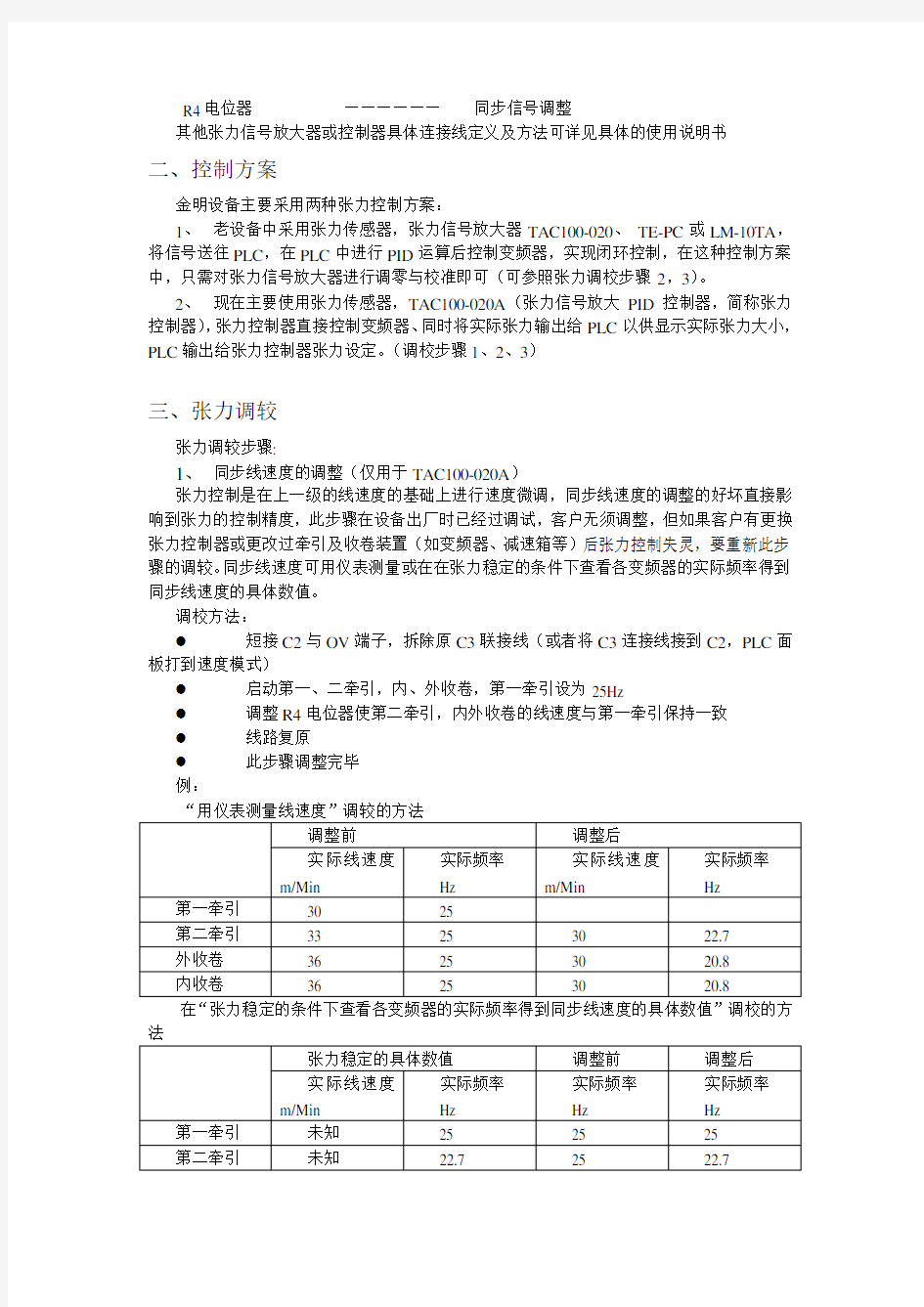
张力控制问题与故障
(广东金明精机股份有限公司吴彦明)
一、张力控制原理及技术参数
金明吹膜收卷中采用张力传感器、张力信号放大器,PLC组成张力控制系统,实现闭环张力控制。
在张力闭环控制中,张力传感采用的是应变片电桥测量原理,采用穿轴式或支座式安装使用,能精确测出薄膜施加在张力辊上的力,根据所受的力的大小,输出与之成正比的电压信号,在吹膜线上采用ZC穿轴式张力传感器或三菱支座式张力传感器。ZC穿轴式张力传感器具有方向性,红点为合力方向。
ZC穿轴式张力传感器技术参数
供电电压6~12V,
输出电阻350欧姆,
灵敏度2mv/V,
电气连接1、电源+,4、电源-,2、信号+,3、信号-,
其他详细技术参数及三菱支座式张力传感器详见相应的说明书。
张力信号放大器与张力传感器配套使用,它为张力传感器提供必要的校准及调零电压,并将传感器的检测信号放大后输出,这些信号通过PID控制器或PLC控制牵引或收卷变频器,实现闭环控制。
TAC100-020及TAC100-020A技术参数:
电源:24V
张力传感器电源:12V
张力传感器输入信号:20mV
其他控制信号输入与输出:0-10V
其他详细技术参数及TE-PC或LM-10TA使用说明详见相应的说明书
TAC100-020A配线端子定义(粗体蓝色部分为控制器信号输出,其他为信号输入) 24V(+)、0V(-)——————电源输入端
VCC(+)、GND(-)——————张力传感器用电源12V
TR1(-)、TR2(+)——————张力传感器(右)信号输入用0-20mV
TL1(-)、TL2(+)——————张力传感器(左)信号输入用
VO(+)、COM(-)——————实际张力输出0-10V
A1(+)、A1(-)——————张力设定值0-10V
A2(+)、A2(-)——————前一级速度信号(同步线速度)0-10V
AP(+)、COM(-)——————控制变频器速度输出0-10V
ZERO电位器——————调零
SPAN电位器——————校准
R1电位器——————积分时间粗调10-250S
R2电位器——————积分时间微调1-50S
R3电位器——————增益调整
R4电位器——————同步信号调整
其他张力信号放大器或控制器具体连接线定义及方法可详见具体的使用说明书
二、控制方案
金明设备主要采用两种张力控制方案:
1、老设备中采用张力传感器,张力信号放大器TAC100-020、TE-PC或LM-10TA,将信号送往PLC,在PLC中进行PID运算后控制变频器,实现闭环控制,在这种控制方案中,只需对张力信号放大器进行调零与校准即可(可参照张力调校步骤2,3)。
2、现在主要使用张力传感器,TAC100-020A(张力信号放大PID控制器,简称张力控制器),张力控制器直接控制变频器、同时将实际张力输出给PLC以供显示实际张力大小,PLC输出给张力控制器张力设定。(调校步骤1、2、3)
三、张力调较
张力调较步骤:
1、同步线速度的调整(仅用于TAC100-020A)
张力控制是在上一级的线速度的基础上进行速度微调,同步线速度的调整的好坏直接影响到张力的控制精度,此步骤在设备出厂时已经过调试,客户无须调整,但如果客户有更换张力控制器或更改过牵引及收卷装置(如变频器、减速箱等)后张力控制失灵,要重新此步骤的调较。同步线速度可用仪表测量或在在张力稳定的条件下查看各变频器的实际频率得到同步线速度的具体数值。
调校方法:
●短接C2与OV端子,拆除原C3联接线(或者将C3连接线接到C2,PLC面板打到速度模式)
●启动第一、二牵引,内、外收卷,第一牵引设为25Hz
●调整R4电位器使第二牵引,内外收卷的线速度与第一牵引保持一致
●线路复原
●此步骤调整完毕
例:
在“张力稳定的条件下查看各变频器的实际频率得到同步线速度的具体数值”调校的方
2、调零和校准
张力传感器属于精密元器件,在使用和运输过程中,由于有可能受到外力的作用或者元器件老化的因素,都会造成张力传感器的轻微变形,因此张力传感器应当定期进行调零与校准工作(建议3个月检测一次)。
在调零与校准工作前,应对张力辊做一下检查:
检查张力传感器的合力方向是否正确,ZC穿轴式张力传感器红点为合力方向。
检查张力辊是否转动灵活。
检查张力传感器插头是否松动。
张力信号放大器或控制器配接线是否断路或短路。
TAC100的调零和校准方法:
●调零
在张力辊不受力(空轴)的情况下,调整ZERO电位器(顺时针输出增大,逆时针输出减少),用电压表检测VO、COM输出电压,使其输出为零。观察PLC操作界面,察看实际张力是否为零。
●校准
在张力辊上按照膜路方向吊挂标准砝码(5Kg),砝码必须在各辊的中心,调整SPAN电位器(顺时针输出增大,逆时针输出减少),用电压表检测VO、COM输出电压,使其输出为相应值。观察PLC操作界面,察看实际张力是否为5Kg。
例:
传感器最大张力=30Kg
标准砝码=5Kg
VO、COM输出最大电压=10V
VO、COM端电压 =VO、COM输出最大电压*砝码重量/传感器最大张力(Kg)
=10*5/30
=1.67(V)
调整VO、COM输出电压为1.67V
●检查
此步骤目的为验证张力传感器的可重复性是否正常。张力辊不受力(空轴)检查检测VO、COM输出电压是否为零,观察PLC操作界面,察看实际张力是否为零。
吊挂标准砝码(5Kg)用电压表检测VO、COM输出电压,使其输出为相应值。观察PLC 操作界面,察看实际张力是否为5Kg左右。
如果检查数值偏差较大,需检查张力辊是否正常?吊挂砝码的方式是否正确?再次校准。
注:其他型号的调零校准方法详见具体的使用说明书
3、测试
测试的目的是检测1、2步的调较是否正确,检测张力控制器是否正常,为正常生产做准备。
●启动第一、二牵引,内、外收卷,第一牵引设为25Hz
●PLC操作界面上设置为张力模式
●设定第二牵引张力为5Kg
●空载时,观察第二牵引实际速度是否高于同步时速度3Hz左右
●对第二牵引张力辊施加外力大于5Kg(用手)
●第二牵引会慢速下降,观察第二牵引实际速度是否低于同步时速度3Hz左右
●内外收卷张力测试同二牵引
●张力检测完毕
例:同步数值可参照调校步骤1方法得到
注:方案一的PLC的速度调节范围比张力控制器的调整范围要大,详见相应的设备使用说明书。
四、张力控制器高级调较
此部分一般为在线调整,出厂已调整好,无须调整,当张力控制失常时,先检查张力传感器、膜路是否正常,排除其他故障依然无法解决时,由专人调整。调整时请注意调整前数值和参数,防止控制继续恶化。
调整前应先进行调校步骤1、2。
调整时先调整张力稳定性,再调整张力偏差。
稳定性主要表现在张力波动较大。
张力偏差主要表现实际张力与设定张力存在偏差,张力稳定但较长时间实际张力无法与设定张力相同。
方案一调整方法
调整PLC参数,当张力波动较大时,先减少P值,再增大I值,直至张力稳定
P值为比例调节,越小越稳定,动态性能越差。
I值为积分调节,越大越稳定,数值偏差越慢消除。
方案二调整方法
调整控制器R1、R2、R3,当张力波动较大时,先逆时针调整R2,再逆时针调整R1,如果张力波动还较大,可再逆时针调整R3,直至张力稳定。
张力偏差主要是调校步骤1没有调较好,重复调校步骤1。
R1 时间粗调,数值越大,反应越灵敏,但过大则容易张力振动。
R1 时间微调,数值越大,反应越灵敏,过大则容易张力振动。
R3为增益调整,越小越稳定,动态性能越差。
五、常见张力控制问题
1.Relations between winding tension, winding taper and film width?
收卷张力、收卷椎度与薄膜宽度的关系?
Equipped tension automatic control with the equipment, haul-off tension and winding tension are for film normal needing, if tension is too small, it can not have the enough strength in the bow roller to spreading the film and cause gauffer; if tension oversized, also will cause the film be stretched, (if using gravimetric control will cause the windage between actual thickness and displaying thickness), and reduce film quality.
Tension relation between the second haul-off unit and surface winding, if its adjustment is not good, will cause the winding section stretched or shrink. (if using width measuring unit will cause the windage between actual width and displaying width.
Function of taper control is when the reel diameter increases, gradually attenuating pressure of pressing arm, to keep invariableness of pressure between winding roll and surface roller. Insure the product width will not be reduced when adding reel diameter.
薄膜设备中采用张力自动控制,牵引张力和收卷张力是为了使薄膜正常牵引和收卷之需要,张力过小,不能在弓辊产生足够的力使膜展平而产生皱褶,张力过大,又会使薄膜被拉伸,(如果使用称重控制将产生实际厚度与显示厚度存在偏差的现象),造成薄膜质量下降。
第二牵引的张力与表面收卷的的张力的关系,如果第二牵引张力与表面收卷的张力关系调整不好时,会造成收卷部分拉伸或收缩(如果使用测宽设备将产生实际宽度与显示厚度存在偏差的现象)
锥度控制的作用是当卷径增大时,逐渐衰减压臂的压力,使膜卷与表面辊之间的压力保持恒定。保证在收卷卷径增大时,薄膜成品宽度不减少。
2.第二牵引和收卷张力与锥度如何设定?How to set the taper with the second haul-off and winding tension?
第二牵引和收卷张力设定最小值以不产生薄膜皱褶为准,越小越好。
Setting min. value for the second haul-off and winding tension can take non-film gauffer as standard, more less more better.
当采用单边收卷时,第二牵引张力稍大于收卷张力。
When winding by one side, the tension of second haul-off is bigger than winding.
当采用双边收卷时,第二牵引张力稍大于内外收卷张力之和。
When winding by two sides, the tension of second haul-off is a little bit bigger the sum of inside and outside winding.
设定收卷压力时,大致上1.0Mpa-2.0Mpa之间示情况而定。
When setting winding pressure, it mostly can see the showings between 1.0Mpa-2.0Mpa to decide.
设定锥度时以收卷成品不产生(开始宽度宽、大卷径后宽度窄)的现象为最小值,但注意防止张力衰减到膜卷与表面辊之间无法产生足够的压力,造成收卷跑边等现象。
When setting the taper, use phenomenon of the empty winding reel (starting winding the width is wide, after big winding reel, the width is narrow) as min. value. But have to avoid the tension taper to between the reel film and surface roller can’t produce enough pressure which will make the winding run away.
六、张力控制失常的常见故障、原因排除方法
1、张力控制器无法校零或校准
●检查张力辊是否转动灵活。
●检查张力传感器安装方向,ZC穿轴式张力传感器红点为合力方向。
●校准负载没有按照膜路方向吊挂
●校准负载的膜路上有较大的其他负载,如部分机型的第二牵引,使标准砝码的
无法准确的反应在张力辊上。
●检查张力传感器电源电压,一般为12V
●检查张力传感器输入范围TR1、TR2是否正常,张力传感器信号输入范围为0-20mV,如果超出,则张力传感器损坏
●检查张力信号放大器或控制器电源灯是否点亮,如果张力传感器信号正常,则张力信号放大器或控制器损坏,更换。
2、实际张力一直显示最大值或最小值0Kg
●检查各变频器是否正常工作,输出是否正常
●检查线路是否正常
●检查张力辊及张力传感器轴承是否卡死?
●检查膜路
●检查张力/速度模式是否在张力模式?
●重复调校步骤1、2
●张力传感器损坏
●张力控制器损坏
3、张力波动比较大
●检查薄膜是否在动力辊上是否有打滑现象
●检查二牵引夹棍是否夹紧力太小,间隙过大。
●观察膜泡是否波动很大,膜泡波动大也容易造成张力波动大
●检查膜路及辊
●检查传动装置是否正常
●重复调校步骤1、2、3
●张力控制器高级调较
●张力控制器损坏或调乱,更换或重调
4、张力一直存在偏差
●检查薄膜是否在动力辊上是否有打滑现象
●重复调校步骤1、2、3
联系方式
广东金明精机股份有限公司
吴彦明
10804702@https://www.360docs.net/doc/42739234.html,
张力控制原理介绍
第二章 张力控制原理介绍 2.1 典型收卷张力控制示意图 2
2.2 张力控制方案介绍 对张力的控制有两个途径,一是可控制电机的输出转矩,二是控制电机转速,对应这两个途径,MD330设计了两种张力控制模式。 1、开环转矩控制模式 开环是指没有张力反馈信号,变频器仅靠控制输出频率或转矩即可达到控制目的,与开环矢量或闭环矢量无关。转矩控制模式是指变频器控制的是电机的转矩,而不是频率,输出频率是跟随材料的速度自动变化。 根据公式F=T/R(其中F为材料张力,T为收卷轴的扭矩,R为收卷的半径),可看出,如果能根据卷径的变化调整收卷轴的转矩,就可以控制材料上的张力,这就是开环转矩模式控制张力的根据,其可行性还有一个原因是材料上的张力只来源于收卷轴的转矩,收卷轴的转矩主要作用于材料上。 MD系列变频器在闭环矢量(有速度传感器矢量控制)下可以准确地控制电机输出转矩,使用这种控制模式,必须加装编码器(变频器要配PG卡)。 2、与开环转矩模式有关的功能模块: 1)张力设定部分:用以设定张力,实际使用中张力的设定值应与所用材料、卷曲成型的要求等实际情况相对应,需由使用者设定。张力锥度可以控制张力随卷径增加而递减,用于改善收卷成型的效果。 2)卷径计算部分:用于计算或获得卷径信息,如果用线速度计算卷径需用到线速度输入功能部分,如果用厚度累计计算卷径需用到厚度累计计算卷径相关参数功能部分。 3)转矩补偿部分:电机的输出转矩在加减速时有一部分要用来克服收(放)卷辊的转动惯量,变频器中关于惯量补偿部分可以通过适当的参数设置自动地根据加减速速率进行转矩补偿,使系统在加减速过程中仍获得稳定的张力。摩 3
张力控制变频收卷的控制原理(汇编)
张力控制变频收卷的控制原理本文主要介绍了张力控制变频收卷的控制原理,此技术能够使得在纺织行业中收卷的整个过程很稳定,避免小卷时张力过大;大卷启动时松纱的现象。 一. 前言 : 用变频器做恒张力控制的实质是闭环矢量控制,即加编码器反馈。对收卷来说,收卷的卷经是由小到大变化的,为了保证恒张力,所以要求电机的输出转距要由小到大变化。同时在不同的操作过程,要进行相应的转距补偿。即小卷启动的瞬间、加速、减速、停车,大卷启动时,要在不同卷经时进行不同的转距补偿,这样就能使得收卷的整个过程很稳定,避免小卷时张力过大;大卷启动时松纱的现象。 二.张力控制变频收卷在纺织行业的应用及工艺要求 2.1 传统收卷装置的弊端 纺织机械如:浆纱机、浆染联合机、并轴机等设备都会有收卷的环节。传统的收卷都是采用机械传动,因为机械的同轴传动对于机械的磨损是非常严重的,据了解,用于同轴传动部分的机械平均寿命基本上是一年左右。而且经常要维护,维护的时候也是非常麻烦的,不仅浪费人力而且维护费用很高,给客户带来了很多的不便。尤其是纺织设备基本上是开机后不允许中途停车的,如发生意外情况需要停车会造成很大的浪费。在这种情况下,张力控制变频收卷开始逐渐取代传统的机械传动系统。 2.2 张力控制变频收卷的工艺要求
(1)在收卷的整个过程中都保持恒定的张力。张力的单位为:牛顿或公斤力。 (2)在启动小卷时,不能因为张力过大而断纱;大卷启动时不能松纱。 (3)在加速、减速、停止的状态下也不能有上述情况出现。 (4)要求将张力量化,即能设定张力的大小(力的单位),能显示实际卷径的大小。 2.3 张力控制变频收卷的优点 (1)张力设定在人机上设定,人性化的操作,单位为力的单位:牛顿。 (2)使用先进的控制算法:卷径的递归运算;空心卷径激活时张力的线性递加;张力锥度计算公式的应用;转矩补偿的动态调整等等。 (3)卷径的实时计算,精确度非常高,保证收卷电机输出转矩的平滑性能好。并且在计算卷径时加入了卷径的递归运算,在操作失误的时候,能自己纠正卷径到正确的数值。 (4)因为收卷装置的转动惯量是很大的,卷径由小变大时。如果操作人员进行加速、减速、停车、再激活时很容易造成爆纱和松纱的现象,将直接导致纱的质量。而进行了变频收卷的改造后,在上述各种情况下,收卷都很稳定,张力始终恒定。而且经过PLC的处理,在特定的动态过程,加入一些动态的调整措施,使得收卷的性能更好。 (5)在传统机械传动收卷的基础上改造成变频收卷,非常简便而且造价低,基本上不需对原有机械进行改造。改造周期小,基本上两三天就能安装调试完成。
欧陆590直流调速器调试步骤
欧陆590直流调速器调试步骤 目录 型号说明 (2) 操作面板的使用 (3) 接线 (4) 1、主回路接线 (4) 2、控制端子接线 (5) 3、查看控制端子配置 (7) 默认控制端子基本接线 (8) 必要的修改参数 (10) 浏览内部设置 (11) 系统菜单目录 (13) 通电运行 (15) 中英文对照报警说明 (16) 附录参数表 (24)
一、型号说明
二、操作面板的使用。 面板示意图
三、接线 1、主回路接线 (1)L、N(辅助电流输入。作为控制器控制电源输入)端子接AC220V 为控制电路供电。 (2)L1、L2、L3(三相主电源输入)接AC380V为主电路供电。 (3)A+、A-(电枢输出,A+正极,A-负极)接电枢端口。 (4)F+、F- (励磁输出。F-为负,F+为正。)接励磁端口。 上述端子一般分布图 2、控制端子接线。
(1)、模拟端子 A1 零伏电位,与 B1、C1 同电位,与地线隔离。 A2 模拟输入 1。默认功能为速度输入,可修改。 A3 模拟输入 2。默认功能为辅助速度或电流输入,在默认功能下,由 C8 来切换其输入功能。C8 低态时为速度输入量,C8 高态时为电流量(电流控制方式),不可修改。 A4 模拟输入 3。默认功能为斜坡速度输入,可修改。 A5 模拟输入 4。默认功能为辅助(负)电流箝位,默认功能下由 C6 确定其是否使用。C6 为低态时不使用此功能,C6 为高态时使用其功能来对负电流进行箝位。可修改。 A6 模拟输入 5。默认功能为主电流箝位或辅助(正)电流箝位,默认功能下由 C6 切换其输入功能,C6 为低态时为主电流箝位,同时作用于正负电流的箝位,可修改。 A7 模拟输出 1。默认功能为速度反馈输出,可修改。 A8 模拟输出 2。默认功能为速度给定输出,可修改。 A9 模拟输出 3。默认功能为电流反馈输出,不可修改。 (2)数字端子 B5 数字输出 1,默认功能为电机零速检测,当电机零速时为高态(+24V 输出),当电机运转时为低态(0V 输出)可修改。 B6 数字输出 2,默认功能为控制器正常状态检测,当控制器正常,没有报警或报警复位时为高态(24V 输出),出现报警时为低态(0V 输出)可修改。 B7 数字输出 3,默认功能为控制器准备就绪状态检测,当控制器准备就绪,主电源合闸时为高态(24V 输出),当控制器分闸、停止、出现报警或主电源分闸时为低态(0V 输出),可修改。 C6 数字输入 1 默认功能为电流箝位选择,C6 为低态时为(A6)主电流箝位,C6 为高态时为(A5、A6)双极电流箝位,此时 A5 为负电流箝位,A6 为正电流箝位。可修改。 C7 数字输入 2,默认功能为斜坡保持,当 C7 为高态时,斜坡输出保持在斜坡输入的最后值,此时不管斜坡输入值为多少,输出都一直保持为这个值,当 C7 为低态时,斜坡输出跟踪斜坡输入值。可修改。
调速器故障分析
第一节水轮机调速器的组成和作用 水轮机调节系统是由调节控制器、液压随动系统和调节对象组成的闭环控制系统。通常我们把调节控制器和液压随动系统统称为水轮机调速器 水轮机调速器作用是保证水轮发电机的频率稳定、维持电力系统负荷平衡,并根据操作控制命令完成各种自动化操作,是水电站的重要基础控制设备。 1、调速器的基本作用是: (l) 能自动调节水轮发电机组的转速,使其保持在额定转速允许偏差内运转,以满足电网对频率质量的要求。 (2) 能使水轮发电机组自动或手动快速启动,适应电网负荷的增减,正常停机或紧急停机的需要。 (3) 当水轮发电机组在电力系统中并列运行时,调速器能自动承担预定的负荷分配,使各机组能实现经济运行。 (4) 能满足转桨式、冲击式水轮机双重协联调节的需要。 2、分类; 水轮机调速器的分类方法较多,按调节规律可分为PI和PID调速器;按系统构成分为机械式调速器(机械飞摆式)、电液式调速器及微机调速器; 实际应用中常用是以下几种区分方式: 1、按我国水轮机调速器国家型谱以及调速器行业规范,调速器分为:中、小型调速器;冲击式调速器;大型调速器等。中、小型调速器以
调速功大小来区分,冲击式调速器以喷针及折向器数目来区分,大型调速器以主配压阀名义直径来区分。 调速器分类表 2、微机调速器依据调节器(电气部分)及机械液压系统(机械部分)的不同形式,有以下区分: 2.1按调节器的硬件构成有单片机、工控机、可编程控制器三大类调节器。其中单片机、单版机构成的调节器由于可靠性差、故障率高等多方面原因,已趋于淘汰。目前可编程控制器以其高度的可靠性成为调节器构成首选。 2.2机械液压系统依据电液转换电液转换方式分为:电液转换器类、电机类、比例伺服阀类、数字阀类。其中电液转换器类已基本为市场淘汰,其他几种均有不同厂家生产。 3、按照调速器的适用机组类型分为:冲击式调速器、单调、双调。冲击式调速器适用于冲击式水轮发电机组;单调适用于无轮叶调节的混流式、轴流定桨式等水轮发电机组;双调适用于有轮叶调节的轴流转桨式、灯泡贯流式水轮发电机组。 第二节调速器的操作 一、调速器的基本参数 1、调速器型号;DFWSF-100-6.3-STARS 2、主配压阀直径;100mm
什么是张力控制
什么是张力控制? 最佳答案 1.什么是张力控制:所谓的张力控制,通俗点讲就是要能控制电机输出多大的力,即输出多少牛顿。反应到电机轴即能控制电机的输出转距。 2.真正的张力控制不同于靠前后两个动力点的速度差形成张力的系统,靠速度差来调节张力的实质是对张力的PID控制,要加张力传感器。而且在大小卷启动、停止、加速、减速、停车时的调节不可能做到象真正的张力控制的效果,张力不是很稳定。肯定会影响生产出产品的质量。 用变频器做恒张力控制的实质是死循环矢量控制,即加编码器反馈。对收卷来说,收卷的卷经是由小到大变化的,为了保证恒张力,所以要求电机的输出转距要由小到大变化。同时在不同的操作过程,要进行相应的转距补偿。即小卷启动的瞬间,加速,减速,停车,大卷启动时,要在不同卷经时进行不同的转距补偿,这样就能使得收卷的整个过程很稳定,避免小卷时张力过大;大卷启动时松纱的现象。 二.张力控制变频收卷在纺织行业的应用及工艺要求 1.传统收卷装置的弊端 纺织机械如:浆纱机、浆染联合机、并轴机等设备都会有收卷的环节。传统的收卷都是采用机械传动,因为机械的同轴传动对于机械的磨损是非常严重的,据了解,用于同轴传动部分的机械平均寿命基本上是一年左右。而且经常要维护,维护的时候也是非常麻烦的,不仅浪费人力而且维护费用很高,给客户带来了很多的不便。尤其是纺织设备基本上是开机后不允许中途停车的,如发生意外情况需要停车会造成很大的浪费。在这种情况下,张力控制变频收卷开始逐渐取代传统的机械传动系统。 2.张力控制变频收卷的工艺要求 * 在收卷的整个过程中都保持恒定的张力。张力的单位为:牛顿或公斤力。 * 在启动小卷时,不能因为张力过大而断纱;大卷启动时不能松纱。 * 在加速、减速、停止的状态下也不能有上述情况出现。 * 要求将张力量化,即能设定张力的大小(力的单位),能显示实际卷径的大小。 3.张力控制变频收卷的优点 * 张力设定在人机上设定,人性化的操作,单位为力的单位:牛顿. * 使用先进的控制算法:卷径的递归运算;空心卷径激活时张力的线性递加; 张力锥度计算公式的应用;转矩补偿的动态调整等等. * 卷径的实时计算,精确度非常高,保证收卷电机输出转矩的平滑性能好。并且
dcm-直流调速器快速调试汇编
SINAMICS DCM 简明调试指南 SINAMICS DCM Commissioning Guide User Guide Edition (2012年6 月) 摘要 本文介绍了SINAMICS DCM 的选型,基本调试步骤。 关键词 SINMICS DCM, 6RA80,选型,调试 Key Words SINMICS DCM, 6RA80,Selection, Commissioning 目录 1 DCM 介绍 1.1 DCM介绍 1.2 SINAMICS DCM选型和接线 2 调试 2.1 BOP20 调试 2.2 Starter 配置和调试 3 DCM 功能介绍
3.1 优化 3.2 数据组 3.3 参数复位和存储 3.4 第二块CUD 3.5 自由功能块和DCC 1 DCM 介绍 1.1 DCM介绍 SINAMICS DCM 是 SINAMICS家族中的直流驱动装置,包含直流驱动装置和控制模块两种产品。直流驱动装置功率范围从15-3000A,超过3000A可以用装置并联实现。 控制模块主要用来替代原来的SIMOREG CM系列产品,实现设备的改造。 其型谱如图1: 图1 SINAMICS DCM 型谱
1.2 SINAMICS DCM选型和接线 1.2.1 控制单元选件 ?标配的DCM包含以下部分: ?控制单元电子板CUD ?标准面板BOP20 ?三相晶闸管全控桥(2Q和4Q); ?单相励磁模块 ?风扇(125A及以下装置自冷) DCM上有两个控制单元电子板插槽(左槽和右槽)。左槽为整个驱动装置发出控制指令,右槽的CUD的主要功能可以扩展端子数量,增加计算能力(如DCC 的编程),增加选件插槽(如CBE20)等功能。 控制单元CUD分成两类: Standard CUD 和 Advanced CUD (选件G00),其接线如图1-2所示:
柴油机调速器故障的诊断与排除
柴油机调速器故障的诊断与排除 [摘要]本文就柴油机调速器故障的诊断与排除进行的较为详尽的介绍。 【关键词】柴油机;调速器;故障;诊断排除 一、转速过高 1.故障现象 发动机空转时最大转速超出最高额定转速。 2.故障原因 2.1最大转速限制螺钉调整不当。有些机手为提高速度,自己拧动高速限制螺钉,一些小型拖拉机上为提高车速拉直调速弹簧; 2.2调速器的调速弹簧预紧度过大; 2.3供油拉杆不灵活,使供油拉杆卡住; 2.4调速g8加油过多,使飞球甩出受阻而影响到控制油量的灵敏度; 2.5调速器内的连接杆系有卡滞现象。 3.检查判断 3.1当减小油门时,若发动机转速不能下降应检查油门摇臂或杆系的连接处是否有卡滞现象,若无卡滞现象,可检查供油拉杆移动是否灵活。如不灵活,可进一步查找供油拉杆是否卡住,或柱塞咬住,或柱塞弹簧折断卡住;若拉杆移动灵活,可检查其连接杆系是否有卡滞现象。同时,也应检查供油拉杆上的调节叉固定螺钉是否松脱。 3.2当减小油门时,发动机转速随之下降,可检查高速螺钉是否调整不当。若经过调整高速限制螺钉无效,可放松调速弹簧预紧力,再检查试验;若转速还降不下来,只有将喷油泵连同调速器一同卸下,再上试验台检查调试。 二、怠速过高 1.故障现象 1.1发动机在低速运转时稳不住。 1.2发动机怠速动转时转速超过400-600转/分钟。 2.故障原因 2.1调速弹簧过软、折断或调整不当; 2.2调速器怠速调节螺钉调整不当,使调速弹簧预紧力过大; 2.3供油拉杆调整不当,或者油门传动杆系的连接节处卡滞; 2.4调速器游隙过大,使调速杠杆位置向增大供油量方向移动; 2.5调速器内积油过多。当调速器内加注机油过多或输油泵及泵盖(指柱塞套肩胛面与泵盖支承面间)漏油过多时,调速器的飞块浸在油液中,运动时的阻力随之增大,致使怠速时向外移动的行程减小,传动板在调速器弹簧弹力的作用下,使油泵拉杆向增大油量方向移动。 3.故障检查 3.1一般发动机的怠速转速为400-600转/分钟,若怠速转速过高,可在发动机熄火后,连续踏几次脚油门踏板,如果油门踏板不返回原位,即为油门回位弹簧过软或传动杆系有卡滞之处,应进一步查找。若油门能自己回位,说明原拉杆调整过长,应调至合适的长度; 3.2检查调速器内润滑油是否合适,若过多,应放出润滑油使油面至合适位置;
张力控制解释
张力控制变频收卷的控制原理 2007年7月23日 中国工业设备网 本文主要介绍了张力控制变频收卷的控制原理,此技术能够使得在纺织行业中收卷的整个过程很稳定,避免小卷时张力过大;大卷启动时松纱的现象。 一. 前言 : 用变频器做恒张力控制的实质是闭环矢量控制,即加编码器反馈。对收卷来说,收卷的卷经是由小到大变化的,为了保证恒张力,所以要求电机的输出转距要由小到大变化。同时在不同的操作过程,要进行相应的转距补偿。即小卷启动的瞬间、加速、减速、停车,大卷启动时,要在不同卷经时进行不同的转距补偿,这样就能使得收卷的整个过程很稳定,避免小卷时张力过大;大卷启动时松纱的现象。 二.张力控制变频收卷在纺织行业的应用及工艺要求 2.1 传统收卷装置的弊端 纺织机械如:浆纱机、浆染联合机、并轴机等设备都会有收卷的环节。传统的收卷都是采用机械传动,因为机械的同轴传动对于机械的磨损是非常严重的,据了解,用于同轴传动部分的机械平均寿命基本上是一年左右。而且经常要维护,维护的时候也是非常麻烦的,不仅浪费人力而且维护费用很高,给客户带来了很多的不便。尤其是纺织设备基本上是开机后不允许中途停车的,如发生意外情况需要停车会造成很大的浪费。在这种情况下,张力控制变频收卷开始逐渐取代传统的机械传动系统。 2.2 张力控制变频收卷的工艺要求
(1)在收卷的整个过程中都保持恒定的张力。张力的单位为:牛顿或公斤力。 (2)在启动小卷时,不能因为张力过大而断纱;大卷启动时不能松纱。 (3)在加速、减速、停止的状态下也不能有上述情况出现。 (4)要求将张力量化,即能设定张力的大小(力的单位),能显示实际卷径的大小。 2.3 张力控制变频收卷的优点 (1)张力设定在人机上设定,人性化的操作,单位为力的单位:牛顿。 (2)使用先进的控制算法:卷径的递归运算;空心卷径激活时张力的线性递加;张力锥度计算公式的应用;转矩补偿的动态调整等等。 (3)卷径的实时计算,精确度非常高,保证收卷电机输出转矩的平滑性能好。并且在计算卷径时加入了卷径的递归运算,在操作失误的时候,能自己纠正卷径到正确的数值。 (4)因为收卷装置的转动惯量是很大的,卷径由小变大时。如果操作人员进行加速、减速、停车、再激活时很容易造成爆纱和松纱的现象,将直接导致纱的质量。而进行了变频收卷的改造后,在上述各种情况下,收卷都很稳定,张力始终恒定。而且经过PLC的处理,在特定的动态过程,加入一些动态的调整措施,使得收卷的性能更好。 (5)在传统机械传动收卷的基础上改造成变频收卷,非常简便而且造价低,基本上不需对原有机械进行改造。改造周期小,基本上两三天就能安装调试完成。 (6)克服了机械收卷对机械磨损的弊端,延长机械的使用寿命。方便维护设备。
调速器故障处理与调试
调速器故障处理与调试 1油泵、压油罐及导水机构最低操作油压试验 待油压装置及调速器装配完毕后,安全阀调整螺栓松出,用手盘 动油泵与电动机的联轴器,转动应均匀,且压油罐的供油阀,排气、排油阀均开启,主接力器处于全关锁定位置。此时启动油泵电动机,启动应平稳无杂音,使油泵在空载状况下进行1小时试运转,(压油罐排气阀有油冒出时,即行关闭),以检查油泵转动部分是否发热,油泵运转 情况是否良好。油温应低于50℃, 油泵轴承、外壳、及电动机轴承温度应低于60℃,外壳振动幅值小于0.05mm。 待油泵运转正常后,就可关闭排油、气阀,调整安全阀,使压油罐油压保持额定油压的16%或稍低。打开供油总阀,操作接力器,此时导水机构应能在无水状态下作全行程的移动。关闭供排油阀,调节安全阀,依次按额定油压值的25%、50%、75%、100%(为了安全,必须先排尽油罐顶部的空气)进行升压试验,各连续运20分钟,同时仔细检查 补气阀,中间油罐,压油罐附件、接头,以及所有焊缝处的渗漏情况。在无压时作相应处理,无油时作焊补处理。 上述试验合格后,再调整安全阀,使压油罐内的油压达1.25倍的额定油压保持30分钟。检查压油罐各部位有无渗漏现象,压力表读数有无明显下降。然后降至额定油压,用0.5kg的小锤沿焊缝周围70mm 处轻轻锤击焊缝处应无渗漏现象。然后打开排油阀排油,至压力为零。
关闭排油与排气阀,由排油阀口充入干净的压缩空气后,关闭排油阀,启动油泵供油至油面计上部刚能看出一点空气时止。按此时的压力整定好电接点压力表的上限值,再降低0.1MPa~0.2MPa后整定好下限值,同时将集油槽内的补气阀吸气管调至集油槽油面以上(待油气比及油压合格后,再将管口调至油面下),再慢慢调整压油罐排油阀至合适的开度。压油罐经过不断排油——补气——供油后,罐上部空气逐渐增加,在相同油压的情况下,油面就渐渐下降。待油下降到油面计上稍能看清油面时,即应将电接点压力表的上、下限指示值向上移一相同数值,使油泵停止时,从油面计上部刚能看到空气即可。这样逐步提高压油罐内的压力,至油压达额定值2.3MPa~2.5MPa,油气比为1∶2左右即可关闭排油阀,使压油罐内保持额定油压和正常油位。记录好油压及油位,经24小时后,检查油压和油位的变化,此时油压下降值不应大于0.1MPa,油面下降不准超过15mm,如油位正常而压力下降,则表明排气阀漏气。当油压下降太大,远超过上述允许值时,则应根据压力和油面下降的情况及对排气阀的检查,综合判断是漏油为主,还是漏气为主,然后再采取相应的处理措施。 2压力信号器与安全阀的整定 2.1启动工作油压的整定方法 将油泵电动机的电源开关置于自动位置。当压油罐油压正常时,打开排油阀。调整电接点压力表下限指针,使压油罐内油压下降到比额定工作油压上限值低0.2MPa~0.25MPa时,油泵电动机应能准确可靠地启动供油。随后关闭好排油阀。
速度控制与张力控制
速度控制与张力控制 Document serial number【KKGB-LBS98YT-BS8CB-BSUT-BST108】
张力控制 1.什么是张力控制:所谓的张力控制,通俗点讲就是要能控制电机输出多大的力,即输出多少牛顿。反应到电 机轴即能控制电机的输出转距。 2. 3. 2.真正的张力控制不同于靠前后两个动力点的速度差形成张力的系统,靠速度差来调节张力的实质是对张力 的PID控制,要加张力传感器。而且在大小卷启动、停止、加速、减速、停车时的调节不可能做到象真正的张力控制的效果,张力不是很稳定。肯定会影响生产出产品的质量。 4. 5.用变频器做恒张力控制的实质是死循环矢量控制,即加编码器反馈。对收卷来说,收卷的卷经是由小到大变 化的,为了保证恒张力,所以要求电机的输出转距要由小到大变化。同时在不同的操作过程,要进行相应的转距补偿。即小卷启动的瞬间,加速,减速,停车,大卷启动时,要在不同卷经时进行不同的转距补偿,这样就能使得收卷的整个过程很稳定,避免小卷时张力过大;大卷启动时松纱的现象。 6. 7.二.张力控制变频收卷在纺织行业的应用及工艺要求 8. 9.1.传统收卷装置的弊端 10.纺织机械如:浆纱机、浆染联合机、并轴机等设备都会有收卷的环节。传统的收卷都是采用机械传动,因为 机械的同轴传动对于机械的磨损是非常严重的,据了解,用于同轴传动部分的机械平均寿命基本上是一年左右。而且经常要维护,维护的时候也是非常麻烦的,不仅浪费人力而且维护费用很高,给客户带来了很多的不便。尤其是纺织设备基本上是开机后不允许中途停车的,如发生意外情况需要停车会造成很大的浪费。在这种情况下,张力控制变频收卷开始逐渐取代传统的机械传动系统。 11. 12.2.张力控制变频收卷的工艺要求 13.* 在收卷的整个过程中都保持恒定的张力。张力的单位为:牛顿或公斤力。 14.* 在启动小卷时,不能因为张力过大而断纱;大卷启动时不能松纱。 15.* 在加速、减速、停止的状态下也不能有上述情况出现。 16.* 要求将张力量化,即能设定张力的大小(力的单位),能显示实际卷径的大小。 17. 18.3.张力控制变频收卷的优点 19.* 张力设定在人机上设定,人性化的操作,单位为力的单位:牛顿. 20.* 使用先进的控制算法:卷径的递归运算;空心卷径激活时张力的线性递加; 21.张力锥度计算公式的应用;转矩补偿的动态调整等等. 22.* 卷径的实时计算,精确度非常高,保证收卷电机输出转矩的平滑性能好。并且 23.在计算卷径时加入了卷径的递归运算,在操作失误的时候,能自己纠正卷径到正确的数值。 24.* 因为收卷装置的转动惯量是很大的,卷径由小变大时。如果操作人员进行加速、 25.减速、停车、再激活时很容易造成爆纱和松纱的现象,将直接导致纱的质量。 26.而进行了变频收卷的改造后,在上述各种情况下,收卷都很稳定,张力始终恒 27.定。而且经过PLC的处理,在特定的动态过程,加入一些动态的调整措施, 28.使得收卷的性能更好。 29.* 在传统机械传动收卷的基础上改造成变频收卷,非常简便而且造价低,基本 30.上不需对原有机械进行改造。改造周期小,基本上两三天就能安装调试完成。 31.* 克服了机械收卷对机械磨损的弊端,延长机械的使用寿命。方便维护设备。 32.
调速器常见故障处理
水轮机微机调速器常见故障的处理所谓常见故障是指调速器投运前或大修后经过调整、试验合格,能投入正常运行,在以后的正常运行中,由于调速器部件产品质量问题,机构松脱变位、机械杂质堵塞、参数设置改变等原因引起的故障。为帮助运行人员迅速判断故障原因和故障部位及时排除故障,本节列举了可编程调速器运行时可能发生的故障及处理措施。 (一)开机、并网及空载运行时常见故障 1.上电后出现电气故障无法开机 该故障的可能原因有: (1)可编程控制器的运行开关未置于“RUN”位置,“RUN”灯未亮,可编程没有投入运行,可能导致电气故障灯亮。 (2)可编程控制器故障,此时可编程故障灯亮。导致可编程控制器故障有多种原因,主要的有模块故障,程序运行超时,状态RAM故障,时钟故障等。此时应先切手动,暂停运行,过一会儿再重新启动,一般即可恢复正常。如果是常驻性故障,应检查相关模块运行指示灯是否正常,对不正常的模块应进行更换。 (3)“电气故障”继电器接点粘连或继电器损坏。此时可检查可编程控制器“电气故障”端子是否有“电气故障”的信号输出(即观察可编程对应输出端口指示灯是否亮)即可判断是否继电器的问题。 (4)测频故障导致“电气故障”灯亮,观察显示屏是否显示“机频故障”。 2.手动开机并网,切至自动后导叶全关 (1)水机自动屏/LCU的停机令未复归。 (2)电气部分连线接触不良、元件损坏。如PLC的调节输出电压未送至综合放大板,功率管损坏短路,或调节阀的线圈与控制信号线接触不良等。 (3)若调节器输出有开机信号,则可能是电液转换部件卡在关机侧,清除电液转换部件故障。 3.发开机令后调速器不响应 (1)调速器没有切为自动状态。手动状态时,切除了电气部分对机械部分的控制,上位机指令不起作用。 (2)紧急停机电磁阀没有复归。由于采用具有定位功能的两位置电磁换向阀,紧急停机信号解除后,电磁换向阀保持在原紧停位置,必须在复位线圈通电后,紧急停机功
调速器知识
一调节系统参数 1 水流惯性时间常数 w T 水流惯性时间常数是指在额定工况下,表征过水管道中水流惯性的特征时间, 其表达式为 22 3580 r r a r r J GD n T M N ω ==r w r r LV Q L T gH S gH == ∑ ∑ 式中 w T为水流惯性时间常数, Q r 为水轮机设计流量, H r 为水轮机设计水头, S为每段过水管道的截面面积, L为相应每段过水管道的长度, V为响应每段过水管道的流速, G为重力加速度 w T表示过水管道水流的惯性,它是水轮机主动力矩变化存在滞后的主要原因, 也是造成调节系统不稳定和动态品质恶化的主要因素。在其他条件不变时, w T越大,水流惯性越大,水击作用越显着,则调节过程的振幅越大,振荡次数越多,调节时间越长,以至最后超出稳定范围。 2 机组惯性时间常数 机组惯性时间常数是指机组在额定转速时的动量矩与额定转矩之比。其表达式为 式中T a 为机组惯性时间常数, Jω r 为额定转速时机组的动量矩, GD2为机组飞轮力矩,
M r 为机组额定转矩, N r 为发电机额定功率, n r 为机组额定转速 T a 的物理意义是:在与发出额定功率相当的额定转矩下,机组由静止达到额定转速所需要的时间。T a 越大,越有利于调节系统的稳定,而且在调节过程中能够见效转速的偏差和减缓转速的变化,但有可能使调节时间变长。若T a 过小,将使调节系统难以稳定。 3永态转差系数b p 、永态调差系数e p 调节系统的静特性有两种情况:图1(a )为无差静特性,表示机组出力不论 为何值,调节系统均保持机组转速n 0,即静态误差为零。图1(b )为有差静特性,当机组出力增大时,调节系统将保持较低的机组转速,即静态误差不为零,永态调差系数e p 定义为调速系统静特性曲线图上某一规定点的斜率的负数。(反馈为功率反馈) 图1(c )也为有差静特性,它以接力器行程Y 为横坐标,以机组转速n 为纵坐标 (反馈为导叶反馈)。永态转差系数b p 为 max x f b p 图1(b) 有差静特性 r x f e p 图1(c) 有差静特性 永态转 差系数b p 是电力系统各机组负荷分配的关键参数,根据电厂在系统的作用不同,各电厂调速器的b p 有所不同。当系统负荷变化时,首先由b p 小的机组承当变化后的负荷,再由b p 大的机组承当变化后的负荷。一般担任调峰、调频的机组比非调
张力控制
力控制变频收卷方案 1.传统收卷装置的弊端 纺织机械如:浆纱机、浆然联合机等设备都会有收卷的环节。传统的收卷都是采用机械传动,因为机械的同轴传动对于机械的磨损是非常严重的,据了解,用于同轴传动部分的机械平均寿命基本上是一年。而且经常要维护, 维护的时候也是非常麻烦的,不仅浪费人力而且维护费用很高,给很多客户带来了很多不便。尤其是纺织设备基本上是开机后不允许中途停车的,如发生意外情况需要停车会造成很大的浪费。在这种情况下,张力控制变频收卷开始逐渐取代传统的机械传动。 2.张力控制变频收卷的优点 * 张力设定在人机上设定,人性化的操作。 * 使用先进的控制算法:卷径的递归运算;空心卷径启动时张力的线性递加;张力锥度计算公式的应用;转矩补偿的动态调整等等. * 卷径的实时计算,精确度非常高,保证收卷电机输出转矩的平滑性能好。并且在计算卷径时加入了卷径的递归运算,在操作失误的时候,能自己纠正卷径到正确的数值。 *因为收卷装置的转动惯量是很大的,卷径由小变大时。如果操作人员进行加速、减速、停车、再启动时很容易造成爆纱和松纱的现象,将直接导致纱的质量。而进行了变频收卷的改造后,在上述各种情况下,收卷都很稳定,张力始终恒定。而且经过PLC的处理,在特定的动态过程,加入一些动态的调整措施,使得收卷的性能更好。 * 在传统机械传动收卷的基础上改造成变频收卷,非常简便而且造价低,基本上不需对原有机械进行改造。改造周期小,基本上两三天就能安装调试完成。 * 克服了机械收卷对机械磨损的弊端,延长机械的使用寿命。方便维护设备。 二. 变频收卷系统构成 1.系统框图
2.变频收卷的控制原理 * 卷径的计算原理:根据V1=V2来计算收卷的卷径。因为V1=ω1*R1,V2=ω2*Rx.因为在相同的时间内由测长辊走过的纱的长度与收卷收到的纱的长度是相等的。即 L1/Δt=L2/ΔtΔn1*C1=i*Δn2*C2(Δn1---单位时间内牵引电机运行的圈数、Δn2---单位时间内收卷电机运行的圈数、C1---测长辊的周长、C2---收卷盘头的周长、i---减速比) Δn1*π*D1=Δn2*π*D2/iD2=Δn1*D1*i/Δn2,因为Δn2=ΔP2/P2(ΔP2---收卷编码器产生的脉冲数、P2---收卷编码器的线数).Δn1=ΔP1/P1取Δn1=1,即测长辊转一圈,由霍尔开关产生一个信号接到PLC.那么D2=D1*i*P2/ΔP2,这样收卷盘头的卷径就得到了. * 收卷的动态过程分析 要能保证收卷过程的平稳性,不论是大卷、小卷、加速、减速、停车、启动都能保证张力的恒定.需要进行转矩的补偿.整个系统要启动起来,首先要克服静摩擦力所产生的转矩,简称静摩擦转矩,静摩擦转矩只在启动的瞬间起作用;正常运行时要克服滑动摩擦力产生的滑动摩擦转矩,滑动摩擦转矩在运行当中一直都存在,并且在低速、高速时的大小是不一样的。需要进行不同大小的补偿,系统在加速、减速、停车时为克服系统的惯量,也要进行相应的转矩补偿,补偿的量与运行的速度也有相应的比例关系.在不同车速的时候,补偿的系数是不同的。即加速转矩、减速转矩、停车转矩、启动转矩;克服了这些因素,还要克服负载转矩,通
调速器调试试验
调速器调试试验 文件管理序列号:[K8UY-K9IO69-O6M243-OL889-F88688]
[键入文档标题] [键入作者姓名] 2013/10/15 目录
1实验目的 为了检验调速器性能的优劣,在正式投入运行前必须进行一系列调整实验,合理的选择整定调速器的各种调节参数,使其具有良好的静、动态特性,从而保证水轮发电机组安全可靠运行。 2静态实验(无水实验) 2.1 试验前的检查 2.1.1 电气柜、机械柜安装 电气柜安装于电站屏柜布置层,不得与大电流、大功率设备,如励磁系统安装在一起。柜体安装牢固,采用螺钉(或焊接方式)固定与基础板上,柜体包括柜体活动部分(前后门)必须可靠接地。 2.1.2 线路检查 安装单位电缆接线已经结束,安装检查工作已经结束。 调速器交、直流220V输入电源线由独立电缆线输入,进入指定接线端子。核实LCU输入调速器的离散量接点(开机令、停机令、增减负荷
令、紧急停机令)、来自锁锭位置的接点和机组出口断路器接点必须为无源接点。 调速器信号输入屏蔽线按照要求接入,电缆屏蔽线应单边接入调速器接地端子,并且不得与动力线同用一根电缆。 2.1.3 安全检查 发电机开关跳开、闸刀已拉开。 工作门全关、闸门落下(或蝴蝶阀已经全关),压力钢管处于无水状态。 水车室、转轮室内不得有人工作。 调速器静态试验工作票已开。 有关人员确认调试人员可以开始工作。 油压装置处于正常自动运行状态 2.1.4 上电检查 上电前,断开调速器柜内主设备电源输入端(位移传感器电源、接近开关电源等)。 通入交直流220V电压,测量上一步骤中断开各端电源电压是否正确,并记录当前工作电源的电压值。 在开度传感器侧测量与传感器接线电缆电源值(与设计传感器电源相同)。 检查完毕,断开电源,恢复线路。
张力控制原理教程
10本文从应用的角度阐述了当前技术条件下,矢量变频技术在卷取传动中运用和设计的方法和思路。有较强的实用性和理论指导性。 关键词: 张力变频矢量转矩卷径 引言: 在工业生产的很多行业,都要进行精确的张力控制,保持张力的恒定,以提高产品的质量。诸如造纸、印刷印染、包装、电线电缆、光纤电缆、纺织、皮革、金属箔加工、纤维、橡胶、冶金等行业都被广泛应用。在变频技术还没有成熟以前,通常采用直流控制,以获得良好的控制性能。随着变频技术的日趋成熟,出现了矢量控制变频器、张力控制专用变频器等一些高性能的变频器。其控制性能已能和直流控制性能相媲美。由于交流电动机的结构、性价比、使用、维护等很多方面都优于直流电动机,矢量变频控制正在这些行业被越来越广泛的应用,有取代直流控制的趋势。 张力控制的目的就是保持线材或带材上的张力恒定,矢量控制变频器可以通过两种途径达到目的:一、通过控制电机的转速来实现;另一种是通过控制电机输出转矩来实现。 速度模式下的张力闭环控制 速度模式下的张力闭环控制是通过调节电机转速达到张力恒定的。首先由带(线)的线速度和卷筒的卷径实时计算出同步匹配频率指令,然后通过张力检测装置反馈的张力信号与张力设定值构成PID闭环,调整变频器的频率指令。 同步匹配频率指令的公式如下: F=(V×p×i)/(π×D) 其中:F 变频器同步匹配频率指令V 材料线速度p 电机极对数(变频器根据电机参数自动获得)i 机械传动比D 卷筒的卷径 变频器的品牌不同、设计者的用法不同,获得以上各变量的途径也不同,特别是材料的线速度(V)和卷筒的卷径(D),计算方法多种多样,在此不一一列举。 这种控制模式下要求变频器的PID调节性能要好,同步匹配频率指令要准确,这样系统更容易稳定,否则系统就会震荡、不稳定。这种模式多用在拉丝机的连拉和轧机的连轧传动控制中。若采用转矩控制模式,当材料的机械性能出现波动,就会出现拉丝困难,轧机轧不动等不正常情况。 转矩模式下的张力控制 一、转矩模式下的张力开环控制
调速器调试方案
1#发电机调速器调试方案 1、一般性检查: 1.1、调试前工作准备 调试设备: (1)计算机、万用表、频率发生器、调压器、调速器图纸、交直流电源、安装工具、编程电缆、兆欧表。 (2)机械设备已质检结束,符合机械电气联调要求。 (3)工作场地整洁,柜体摆放符合要求,调试电缆满足走向要求。 1.2、控制回路检查 (1)检修工作已经结束,安装自检工作结束。 (2)在调速器端子排测量急停阀、与复归阀线圈电阻。 急停阀线圈电阻:Ω 复归阀线圈电阻:Ω (3)调速器信号输入屏蔽线按照要求接入,电缆屏蔽线应单边接入调速器接地端子。 (4)绝缘回路检查: 1.3、安全检查 (1)调速器所有空气开关处于OFF位置。 (2)断开PLC、触摸屏、开度传感器、接近开关电源。 (3)调速器机械调试工作已经结束,具备试验条件。 (4)油压装置处于正常自动运行状态,油系统已投入运行。 1.4、上电检查 交、直流电源已输入调速器 (1)上电前,断开调速器柜内主设备电源输入端(位移传感器电源、接近开关电源等等)。 (2)通入交、直流220V电压,测量上一步骤中断开各端电源电压是否正确,并记录当前工作电源的电压值。记录如下: AC220V: V DC220V: V(极性) DC24V : V (极性) DC5V : V(极性) 以上电压值要求在±10%为正常值 (3)上电后,观察10分钟,无明显烧焦、异味、放电声等等。 2、调速器油压装置试验 2.1、压力油罐耐压试验 (1)用油压装置的油泵按下述步骤向压力罐送油 a、在压力罐的排气孔上安装排油管并接至回油箱; b、开启油泵截止阀和压力表针阀,其余阀门全部关闭 C、用手转动油泵,检查是否灵活,然后通电检查油泵转动方向是否正确 将油泵注满气轮机油,然后以手动方式启动油泵向压力罐送油
台达张力控制变频收卷的控制原理
台达张力控制变频收卷的控制原理 一、前言: 用变频器做恒张力控制的实质是闭环矢量控制,即加编码器反馈。对收卷来说,收卷的卷经是由小到大变化的,为了保证恒张力,所以要求电机的输出转距要由小到大变化。同时在不同的操作过程,要进行相应的转距补偿。即小卷启动的瞬间、加速、减速、停车,大卷启动时,要在不同卷经时进行不同的转距补偿,这样就能使得收卷的整个过程很稳定,避免小卷时张力过大;大卷启动时松纱的现象。 二、张力控制变频收卷在纺织行业的应用及工艺要求 2.1 传统收卷装置的弊端 纺织机械如:浆纱机、浆染联合机、并轴机等设备都会有收卷的环节。传统的收卷都是采用机械传动,因为机械的同轴传动对于机械的磨损是非常严重的,据了解,用于同轴传动部分的机械平均寿命基本上是一年左右。而且经常要维护,维护的时候也是非常麻烦的,不仅浪费人力而且维护费用很高,给客户带来了很多的不便。尤其是纺织设备基本上是开机后不允许中途停车的,如发生意外情况需要停车会造成很大的浪费。在这种情况下,张力控制变频收卷开始逐渐取代传统的机械传动系统。 2.2 张力控制变频收卷的工艺要求 (1)在收卷的整个过程中都保持恒定的张力。张力的单位为:牛顿或公斤力。 (2)在启动小卷时,不能因为张力过大而断纱;大卷启动时不能松纱。 (3)在加速、减速、停止的状态下也不能有上述情况出现。 (4)要求将张力量化,即能设定张力的大小(力的单位),能显示实际卷径的大小。 2.3 张力控制变频收卷的优点 (1)张力设定在人机上设定,人性化的操作,单位为力的单位:牛顿。 (2)使用先进的控制算法:卷径的递归运算;空心卷径激活时张力的线性递加;张力锥度计算公式的应用;转矩补偿的动态调整等等。 (3)卷径的实时计算,精确度非常高,保证收卷电机输出转矩的平滑性能好。并且在计算卷径时加入了卷径的递归运算,在操作失误的时候,能自己纠正卷径到正确的数值。 径时加入了卷径的递归运算,在操作失误的时候,能自己纠正卷径到正确的数值。 (4)因为收卷装置的转动惯量是很大的,卷径由小变大时。如果操作人员进行加速、减速、停车、再激活时很容易造成爆纱和松纱的现象,将直接导致纱的质量。而进行了变频
张力控制原理介绍
第二章张力控制原理介绍 2.1 典型收卷张力控制示意图 浮动辊 F 牵引辊 收卷 图2 带浮动辊张力反馈 收卷 F 牵引辊 图1 无张力反馈 3 2.2 张力控制方案介绍 对张力的控制有两个途径,一是可控制电机的输出转矩,二是控制电机转速,对应这两个途径,MD330 设计了两种张力控制模式。 1、开环转矩控制模式 开环是指没有张力反馈信号,变频器仅靠控制输出频率或转矩即可达到控制目的,与开环矢量或闭环矢量无关。转矩控制模式是指变频器控制的是电机的转矩,而不是频率,输出频率是跟随材料的速度自动变化。根据公式F=T/R(其中F 为材料张力,T 为收卷轴的扭矩,R 为收卷的半径),可看出,如果能根据卷径的变化调整收卷轴的转矩,就可以控制材料上的张力,这就是开环转矩模式控制张力的根据,其
可行性还有一个原因是材料上的张力只来源于收卷轴的转矩,收卷轴的转矩主要作用于材料上。MD 系列变频器在闭环矢量(有速度传感器矢量控制)下可以准确地控制电机输出转矩,使用这种控制模式,必须加装编码器(变频器要配PG 卡)。 2、与开环转矩模式有关的功能模块: 1)张力设定部分:用以设定张力,实际使用中张力的设定值应与所用材料、卷曲成型的要求等实际情况相对应,需由使用者设定。张力锥度可以控制张力随卷径增加而递减,用于改善收卷成型的效果。2)卷径计算部分:用于计算或获得卷径信息,如果用线速度计算卷径需用到线速度输入功能部分,如果用厚度累计计算卷径需用到厚度累计计算卷径相关参数功能部分。 3)转矩补偿部分:电机的输出转矩在加减速时有一部分要用来克服收(放)卷辊的转动惯量,变频器中关于惯量补偿部分可以通过适当的参数设置自动地根据加减速速率进行转矩补偿,使系统在加减速过程中仍获得稳定的张力。摩4擦补偿可以克服系统阻力对张力产生的影响。 3、闭环速度控制模式 闭环是指需要张力(位置)检测反馈信号构成闭环调节,速度控制模式是指变频器根据反馈信号调节输出频率,而达到控制目的,速度模式变频器可工作在无速度传感器矢量控制、有速度传感器矢量控制和V/F 控制三种方式中的任何一种。 该控制模式的原理是通过材料线速度与实际卷径计算一个匹配频率
调速器无水试验方案
调速器无水调试试验方案 一、试验条件及注意事项 1水轮机和调速器系统各部位检修完毕; 2机组进水口闸门和尾水闸门处于关闭状态; 3发电机与主系统可靠断开; 4在导叶和桨叶操作机构动作过程中,确保在水车室和转轮室内,导叶和桨叶操作机构周围无人和物件; 5保证通讯畅通,出现异常情况及时汇报终止试验。 二、试验项目 1、导叶传感器零点检查调整 (1)现地手动控制开关导叶5 个来回,将接力器内空气排完。 (2)将导叶手动关到全关位置(接力器活塞杆无法再伸长)的位置记录为传感器零点。 (3)将导叶手动开到全开位置(接力器活塞杆无法再回收)的位置记录导叶全开行程; 2、桨叶传感器零点检查 (1)现地手动控制开关桨叶5 个来回,将接力器内空气排完; (2)将桨叶手动关到全关位置记录为传感器零点; (3)将桨叶手动开到全开位置记录导叶全开行程; 3、导叶开关机时间检查及调整 (1)现地手动将导叶开到全开位置。 (2)LCU强制动作急停阀,记录导叶关机时间是否满足调保计算时间(第一段5S、第二段8S)以及拐点位置是否为40% (3)将急停阀复归,记录导叶开机时间。 (4)事故配动作试验时,记录导叶关闭时间及拐点情况。 4、调速器冗余配置切换实验 (1)将调速器现地手动方式下开到10%开度,用信号发生器在调速器柜后(端子XI:23和XI:24)上加50Hz频率信号,然后短接并网信号(端子X1:2 和X1:6)将调速器切自动,模拟并网负载工况。 (2)进行调速器自动、手动方式切换,观察调速器导叶开度变化情况。
(3)拉开调速器交流电源开关,观察调速器导叶开度变化情况。 (4)合上调速器交流电源开关,拉开调速器直流电源开关,观察调速器导 叶开度变化情况。 (5)进行调速器A、B 套切换,观察调速器导叶开度变化情况。 (6)在程序中进行调速器运行模式切换,观察调速器导叶开度变化情况。 5、模拟并网运行下各种信号消失试验 (1)将调速器现地手动方式下开到10%开度,用信号发生器在调速器柜后 (端子X1: 23和X1: 24)上加50Hz频率信号,然后短接并网信号(端子X1:2 和X1:6)将调速器切自动,模拟并网负载工况。 (2)将频率信号撤掉(信号发生器在端子X1:23和X1:24的接线解 掉), 记录频率消失时的导叶开度曲线,然后复归频率信号。 (3)将功率信号解掉,记录功率信号消失时的导叶开度曲线,然后复归 功率信号。 (4)先解开调速器A套导叶开度反馈传感器正信号线(X4: 3 ), 观察有无 传感器故障告警信号及导叶开度变化情况,再解开调速器柜后B套导叶开度反馈传 感器接线(X4:17),观察有无调速器事故信号及导叶开度变化情况。 6、调速器静特性实验 (1 )将调速器导叶控制方式切至现地手动,桨叶自动。 (2)将调速器现地手动方式下开到50%开度,用继保仪在调速器柜 后(端子XI:23和XI:24)上加50Hz频率信号。 (3)在调速器柜后短接并网信号(端子X1:2 和X1:6)将调速器导叶控制方式切自动。 (4)将调速器切频率运行模式,同时将导叶开度限制放开,原Bp=4 Bt=45 Td=10 Tn=0.3 修改为Bp =6 Bt=5 Td=2 Tn=0 。 (5)用继保仪升高或降低频率使导叶接力器关全或全开,调整频率信号 值,使之按一个方向逐次升高或降低,在导叶接力器每次变化稳定后,记录该次信号频率值及相应的导叶接力器行程,分别绘制频率升高或降低的静态特性曲线。每条曲线在导叶接力器行程10~90%的范围内, 测点不少于8 点。