精益生产管理
精益生产管理理念

精益生产管理理念精益生产管理(Lean Production Management)是一种以提高效率、降低浪费和实现持续改进为目标的商业运营理念和管理方法。
它起源于日本的丰田汽车公司,通过简化流程、减少库存、增加产品质量和提高员工参与度来提高企业的竞争力。
精益生产管理不仅仅在制造业中有应用,它也成为了一种在服务行业和其他组织中普遍使用的管理方法。
精益生产管理的核心理念是尽可能减少浪费并实现持续改进。
浪费是指任何不会增加产品或服务的价值,但会增加成本或时间的活动。
精益生产管理方法通过以下几个步骤来减少浪费:第一步是优化价值流。
价值流是指从原材料到最终产品或服务交付的整个过程。
通过剖析整个价值流,可以找到并消除其中的浪费,以提高效率。
例如,通过精确控制库存并与供应商密切合作,可以减少库存的积压和浪费。
第二步是实施精准生产。
这意味着根据产品的需求量进行生产,最大限度地降低库存和成本。
不仅如此,还要通过制定合理的生产计划,确保产品能够按时交付给客户,以提高客户满意度。
第三步是实施标准化工作。
标准化工作是指制定和遵循一套标准化的工作方法和程序,以确保质量和效率。
通过标准化工作,可以降低错误和重新工作的发生率,并提高产品和服务的一致性。
第四步是提高员工参与度和团队合作。
精益生产管理鼓励员工主动参与和贡献,倡导员工团队合作和共同学习。
通过培养员工的创新能力和问题解决能力,可以不断改善工作流程和提高整体效率。
除了以上步骤,精益生产管理还强调持续改进和追求卓越。
持续改进是指以持续性的方式不断寻找并解决问题,从而不断提高业务和流程的效率和质量。
追求卓越是指以超越竞争对手的高标准和目标为导向,不断追求卓越。
通过持续改进和追求卓越,企业可以不断提高其竞争力和市场份额。
精益生产管理的优势是显而易见的。
它可以帮助企业降低成本、提高效率和质量,以及增加客户满意度。
通过减少浪费和提高流程效率,企业可以实现更高的盈利能力和持续改进。
精益生产管理
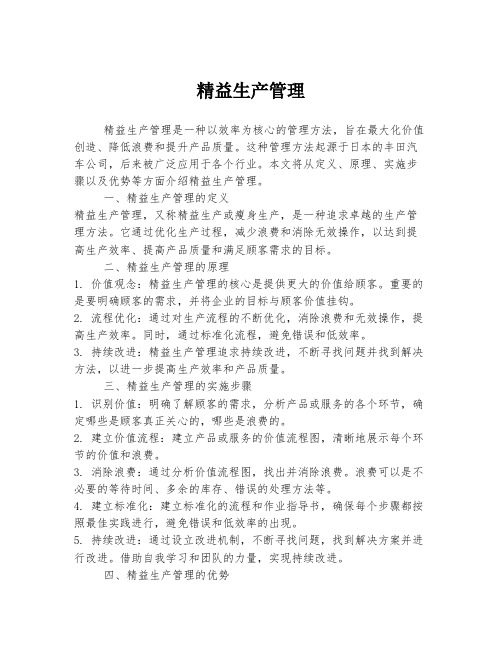
精益生产管理精益生产管理是一种以效率为核心的管理方法,旨在最大化价值创造、降低浪费和提升产品质量。
这种管理方法起源于日本的丰田汽车公司,后来被广泛应用于各个行业。
本文将从定义、原理、实施步骤以及优势等方面介绍精益生产管理。
一、精益生产管理的定义精益生产管理,又称精益生产或瘦身生产,是一种追求卓越的生产管理方法。
它通过优化生产过程,减少浪费和消除无效操作,以达到提高生产效率、提高产品质量和满足顾客需求的目标。
二、精益生产管理的原理1. 价值观念:精益生产管理的核心是提供更大的价值给顾客。
重要的是要明确顾客的需求,并将企业的目标与顾客价值挂钩。
2. 流程优化:通过对生产流程的不断优化,消除浪费和无效操作,提高生产效率。
同时,通过标准化流程,避免错误和低效率。
3. 持续改进:精益生产管理追求持续改进,不断寻找问题并找到解决方法,以进一步提高生产效率和产品质量。
三、精益生产管理的实施步骤1. 识别价值:明确了解顾客的需求,分析产品或服务的各个环节,确定哪些是顾客真正关心的,哪些是浪费的。
2. 建立价值流程:建立产品或服务的价值流程图,清晰地展示每个环节的价值和浪费。
3. 消除浪费:通过分析价值流程图,找出并消除浪费。
浪费可以是不必要的等待时间、多余的库存、错误的处理方法等。
4. 建立标准化:建立标准化的流程和作业指导书,确保每个步骤都按照最佳实践进行,避免错误和低效率的出现。
5. 持续改进:通过设立改进机制,不断寻找问题,找到解决方案并进行改进。
借助自我学习和团队的力量,实现持续改进。
四、精益生产管理的优势1. 提高生产效率:通过消除浪费和优化流程,可以提高生产效率,减少生产时间和成本。
2. 提升产品质量:通过建立标准化流程和作业指导书,可以降低错误率,保证产品质量。
3. 提升员工参与度:精益生产管理重视员工参与和创新,可以激发员工积极性,并增强团队合作精神。
4. 提高顾客满意度:精益生产管理以顾客价值为导向,通过不断改进和提升产品质量,满足顾客需求,提高顾客满意度。
精益生产管理

精益生产管理精益生产(Lean Production Management),简称“精益”,是衍生自丰田生产方式的一种管理哲学。
概念精益生产管理,是一种以客户需求为拉动,以消灭浪费和不断改善为核心,使企业以最少的投入获取成本和运作效益显著改善的一种全新的生产管理模式.它的特点是强调客户对时间和价值的要求,以分类不增值尚难以消除的活动、不增值可立即消除的活动。
精益生产将所的效率改善而忽视向非增值活动的挖潜。
研究表明,物资从进厂到出厂,只有10%的时间是增值的,精益生产成功秘诀就在于将提高效率的着眼点转移到占90%时间的非增值活动上去.价值效满足。
停滞精益生产将所有的停滞视为浪费,要求促进停滞物流转运行,跟流动。
传统的职能分工和大批量生产方式,往往阻断了本应动起来的用率降低、管理成本增大、批次质量风险等等.过早过量精益生产认为过早生产、过量生产均是浪费,应以需求拉动原则使顾客能精确的在需要的时间得到需要的产品,如同在超市的货架上选取所需要的东西,而不是把用户不太想要的东西强行推给用户.拉动原则由于生产和需求直接对接,消除了过早、过量的投入,而减少精益生产要求人们要识别价值流,采用JIT(准时化)、一件流等产等方法为价值流动提供支持和保障。
精益生产的实施是永无止境的过程,其改进结果必然是浪费的不断消除以及价值的不断挖掘。
精益生产追求完美的持续改善,改善是以需求为基础的,要求工作人员并不只做会做的事,更要向应该做的事挑战,成为改善者而不是被改善者,对于被改善的事件彻底追究事件真相,改善设备之前先进行员工作业改善,保证其对改善的适应性,而在改善方案确定之后,首先确认安全和质量,否则改善也将成为一种浪费。
思想内涵精益生产的思想内涵可概括为五点,分别是顾客确定价值、识别思想原则,就掌握了精益生产的成功秘诀。
管理原则原则1:消除八大浪费企业中普遍存在的八大浪费涉及:过量生产、等待时间、运输、库存、过程(工序)、动作、产品缺陷以及忽视员工创造力。
精益生产管理(完整版)

第一章精益生产的思想和方法企业经营的目的是向社会提供产品和服务,同时为企业创造利润。
为达到这一目的,企业必须投入人员、材料、设备、资金等资源,并通过对它们的有效使用和优化组合制造出社会所需要的产品。
而利润的高低取决于投入和有效产出1的比例,即生产效率,班组是使产品增值的基本单元,是提高生产效率的主战场。
提高生产效率有以下三种途径:1.投入不变,产出增加;2。
产出不变,投入减少;3。
投入减少,产出增加。
第一种途径适用于产品的成长期2,即市场对该产品的需求呈上升趋势的阶段;第二种途径适用于产品的成熟期或衰退期,即市场对该产品的需求渐趋稳定或下降的阶段;第三种途径显然是最理想的,因而难度也是最大的。
但是,市场竞争的结果最终将导致第一和第二种途径的失效,从而使企业的经营状况步入低谷。
要避免这种状况,就必须采用第三种途径。
精益生产的成功有力地证明了这一途径的优越性和有效性.第一节精益生产的诞生及其特点精益生产方式是继单件生产方式和大量生产方式之后在日本丰田汽车公司诞生的全新生产方式。
精益的“精"就是指更少的投入,而“益"指更多的产出。
本世纪中叶,当美国的汽车工业处于发展的顶峰时,以大野耐一为代表的丰田人对美国的大量生产方式进行了彻底的分析,得出了两条结论:1。
大量生产方式在削减成本方面的潜力要远远超过其规模效应所带来的好处2。
大量生产方式的纵向泰勒制3组织体制不利于企业对市场的适应和职工积极性、智慧和创造力的发挥基于这两点认识,丰田公司根据自身面临需求不足、技术落后、资金短缺等严重困难的特点,同时结合日本独特的文化背景,逐步创立了一种全新的多品种、小批量、高效益和低消耗的生产方式。
这种生产方式在1973年的石油危机中体现了巨大的优越性,并成为80年代日本在汽车市场竞争中战胜美国的法宝,从而促使美国化费500万美元和5年时间对日本的生产方式进行考察和研究,并把这种生产方式重新命名为精益生产(LEAN PRODUCTION)。
精益生产的五项管理精髓
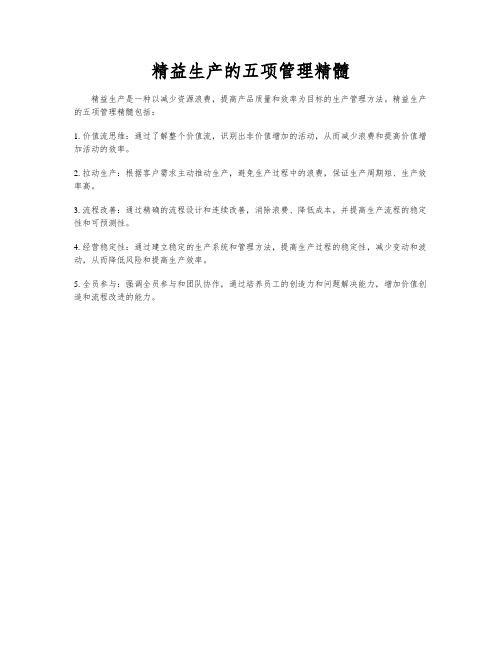
精益生产的五项管理精髓
精益生产是一种以减少资源浪费,提高产品质量和效率为目标的生产管理方法。
精益生产的五项管理精髓包括:
1. 价值流思维:通过了解整个价值流,识别出非价值增加的活动,从而减少浪费和提高价值增加活动的效率。
2. 拉动生产:根据客户需求主动推动生产,避免生产过程中的浪费,保证生产周期短、生产效率高。
3. 流程改善:通过精确的流程设计和连续改善,消除浪费、降低成本,并提高生产流程的稳定性和可预测性。
4. 经营稳定性:通过建立稳定的生产系统和管理方法,提高生产过程的稳定性,减少变动和波动,从而降低风险和提高生产效率。
5. 全员参与:强调全员参与和团队协作,通过培养员工的创造力和问题解决能力,增加价值创造和流程改进的能力。
精益生产管理的11种方法
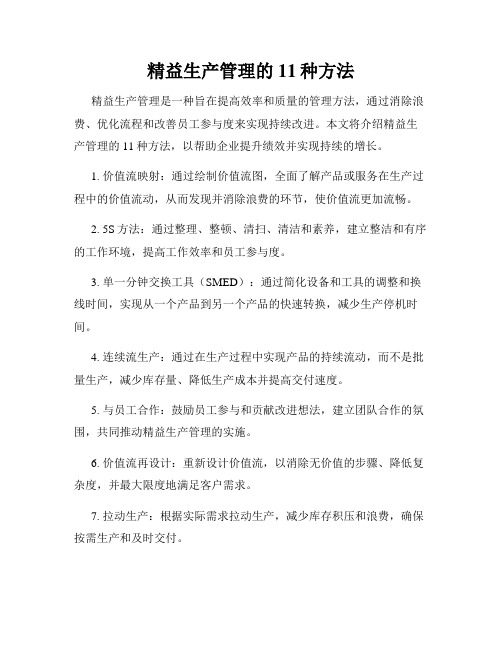
精益生产管理的11种方法精益生产管理是一种旨在提高效率和质量的管理方法,通过消除浪费、优化流程和改善员工参与度来实现持续改进。
本文将介绍精益生产管理的11种方法,以帮助企业提升绩效并实现持续的增长。
1. 价值流映射:通过绘制价值流图,全面了解产品或服务在生产过程中的价值流动,从而发现并消除浪费的环节,使价值流更加流畅。
2. 5S方法:通过整理、整顿、清扫、清洁和素养,建立整洁和有序的工作环境,提高工作效率和员工参与度。
3. 单一分钟交换工具(SMED):通过简化设备和工具的调整和换线时间,实现从一个产品到另一个产品的快速转换,减少生产停机时间。
4. 连续流生产:通过在生产过程中实现产品的持续流动,而不是批量生产,减少库存量、降低生产成本并提高交付速度。
5. 与员工合作:鼓励员工参与和贡献改进想法,建立团队合作的氛围,共同推动精益生产管理的实施。
6. 价值流再设计:重新设计价值流,以消除无价值的步骤、降低复杂度,并最大限度地满足客户需求。
7. 拉动生产:根据实际需求拉动生产,减少库存积压和浪费,确保按需生产和及时交付。
8. 持续改进:将改进作为一种持续性的活动,通过设立改进目标、定期检查和评估,并及时采取纠正措施,不断提高工作流程和绩效。
9. 供应链管理:与供应商建立稳定的伙伴关系,建立有效的供应链管理体系,以实现产品的高质量、低成本和及时交付。
10. 错误防治:采用错误防治方法,如Poka-Yoke(防误装置)和错误预防分析,减少错误发生的可能性,确保产品质量。
11. 生产线平衡:通过平衡各个工作站的工作量,避免生产线上的瓶颈和积压,确保生产过程的平稳进行。
以上是精益生产管理的11种方法,它们帮助企业实现高效、高质量的生产,减少浪费并提升利润。
企业可以根据自身情况选择和结合适合自己的方法,并持续改进以不断提升绩效,实现持续增长。
精益生产管理的11种方法

精益生产管理的11种方法精益生产是通过系统结构、人员组织、运行方式和市场供求等方面的变革,使生产系统能很快适应用户需求不断变化,并能使生产过程中一切无用、多余的东西被精简,最终达到包括市场供销在内的生产的各方面最好结果的一种生产管理方式。
与传统的大生产方式不同,其特色是“多品种”,“小批量”。
一、精益生产管理包含的方法有以下11种:1、5S与目视控制“5S”是整理(Seiri)、整顿(Seiton)、清扫(Seiso)、清洁(Seikeetsu)和素养(Shitsuke)这5个词的缩写“5S”,起源于日本。
5S是创建和保持组织化,整洁和高效工作场地的过程和方法,可以教育、启发和养成良好“人性”惯,目视管理可以在瞬间识别正常和异常状态,又能快速、正确的传递讯息。
2、准时化生产(JIT)准时生产方式是起源于XXX,其基本思想是“只在需要的时候,按需要的量生产所需的产品”。
这种生产方式的核心是追求一种无库存的生产系统,或使库存达到最小的生产系统。
3、看板管理(Kanban)XXX是个日语名词,表示一种挂在或贴在上或一批零件上的标签或卡片,或流水线上各类颜色的信号灯、电视图象等。
看板是可以作为交流厂内生产管理信息的手段。
看板卡片包含相当多的信息并且可以反复使用。
常用的看板有两种:生产看板和运送看板。
4、零库存管理工厂的库存管理是供应链的一环,也是最基本的一环。
就制造业而言,加强库存管理,可缩短并逐步消除原材料、半成品、成品的滞留时间,减少无效作业和等待时间,防止缺货,提高客户对“质量、成本、交期”三大要素的满意度。
5、全面生产维护(TPM)TPM起源于日本,是以全员参与的方式,创建设计优良的设备系统,提高现有设备的利用率,实现安全性和高质量,防止故障发生,从而使企业达到降低成本和全面生产效率的提高。
6、运用价值流图来识别浪费生产过程中到处充斥着惊人的浪费现象,价值流图(Value Stream Mapping)是实施精益系统、消除过程浪费的基础与关键点。
精益生产管理体系及三大要点

精益生产管理体系及三大要点精益生产管理体系(Lean Production Management System)是一种提升生产效率、降低成本和提高质量的管理方法和理念。
它是在日本丰田生产方式(Toyota Production System)的基础上发展起来的,旨在通过消除浪费、优化流程和提高员工参与度来实现持续的改善和精益化生产。
精益生产管理体系的三大要点是:1. 消除浪费(Eliminate Waste):精益生产管理体系的核心是消除浪费。
浪费是指任何不会增加产品或服务价值的活动或过程。
常见的浪费包括等待、过产、运输、库存、生产缺陷等。
通过识别和消除浪费,企业可以提高效率、降低成本并提高产品质量。
消除浪费需要全员参与,通过改进工作流程和制度来减少浪费的发生,从而达到提升整体生产效率和竞争力的目标。
2. 规范化流程(Standardize Processes):精益生产管理体系强调规范化的工作流程。
通过制定明确的工作规范和流程,可以减少变动和不确定性,提高生产过程的稳定性和一致性。
规范化流程可以减少错误和缺陷的发生,提高产品质量,并减少员工在执行任务时的不确定性和错误率。
通过标准化工作流程,企业还可以更好地掌握生产情况,及时调整和改进,实现持续改善。
3. 培养员工参与意识(Cultivate Employee Involvement):精益生产管理体系强调员工的积极参与和持续改进的文化。
企业需要鼓励员工参与生产过程的改善,并提供相关的培训和支持。
员工参与意识的培养可以激发员工的创新和贡献,促进团队合作和沟通,并建立起持续改进的机制。
员工是生产线上最了解实际情况的人,他们的参与和反馈可以帮助企业改善工作环境、流程和产品质量,从而提高整体生产效率。
总之,精益生产管理体系是一种通过消除浪费、规范化流程和培养员工参与意识来提升生产效率和产品质量的管理方法。
企业可以通过积极实施精益生产管理体系,不断改进和优化生产过程,提高竞争力和市场份额。
精益生产管理手册
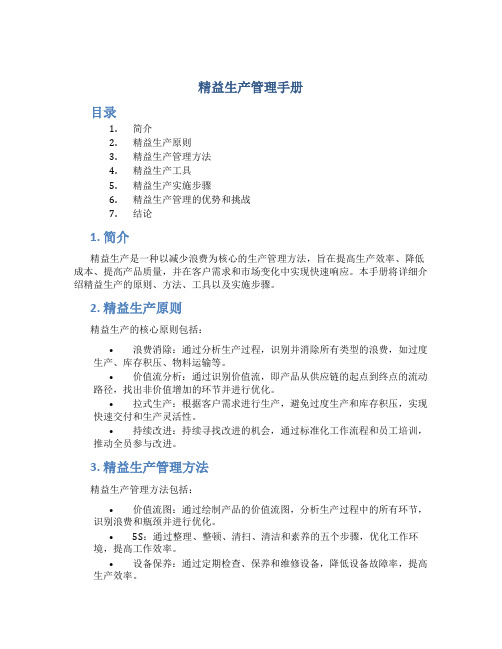
精益生产管理手册目录1.简介2.精益生产原则3.精益生产管理方法4.精益生产工具5.精益生产实施步骤6.精益生产管理的优势和挑战7.结论1. 简介精益生产是一种以减少浪费为核心的生产管理方法,旨在提高生产效率、降低成本、提高产品质量,并在客户需求和市场变化中实现快速响应。
本手册将详细介绍精益生产的原则、方法、工具以及实施步骤。
2. 精益生产原则精益生产的核心原则包括:•浪费消除:通过分析生产过程,识别并消除所有类型的浪费,如过度生产、库存积压、物料运输等。
•价值流分析:通过识别价值流,即产品从供应链的起点到终点的流动路径,找出非价值增加的环节并进行优化。
•拉式生产:根据客户需求进行生产,避免过度生产和库存积压,实现快速交付和生产灵活性。
•持续改进:持续寻找改进的机会,通过标准化工作流程和员工培训,推动全员参与改进。
3. 精益生产管理方法精益生产管理方法包括:•价值流图:通过绘制产品的价值流图,分析生产过程中的所有环节,识别浪费和瓶颈并进行优化。
•5S:通过整理、整顿、清扫、清洁和素养的五个步骤,优化工作环境,提高工作效率。
•设备保养:通过定期检查、保养和维修设备,降低设备故障率,提高生产效率。
•产能平衡:根据市场需求和生产能力,调整生产线的平衡,提高生产效率和产品质量。
•Just-In-Time (JIT) 生产:根据客户需求精确控制物料、零部件和成品的库存,避免过度生产和库存积压。
•持续改进:通过持续的改进活动,提高工作流程、生产效率和产品质量。
4. 精益生产工具精益生产使用多种工具来支持管理和改进活动,包括:•流程图:用于描述生产过程中的各个步骤和环节。
•Gantt 图:用于规划和跟踪项目进度。
•帕累托图:用于识别主要问题和优先解决。
•5W1H 分析:通过回答问题谁、何时、何地、为什么、如何和多少来分析问题的根本原因。
•根本原因分析:通过追溯问题的根本原因,找到解决问题的有效措施。
•PDCA 循环:通过计划、执行、检查和行动的循环,持续改进工作流程和活动。
精益生产生产车间现场管理

精益生产车间现场管理:提升效率与品质的关键策略一、现场布局优化,提升空间利用率1. 合理规划生产线布局,减少物料搬运距离。
根据生产流程,将相关工序紧密排列,降低在制品的移动次数,提高生产效率。
2. 采用流线型设计,确保生产流程顺畅。
通过分析生产过程中的瓶颈环节,优化设备布局,使物料流动更加顺畅。
3. 创设整洁、有序的现场环境。
定期清理现场,消除不必要的物品,确保生产空间宽敞,降低安全事故发生的概率。
二、标准化作业,确保生产稳定性1. 制定详细的生产作业指导书,明确各工序操作规程。
让员工按照标准作业,减少人为失误,提高产品质量。
2. 开展技能培训,提高员工操作水平。
针对不同岗位需求,组织专业培训,提升员工技能,降低生产过程中的不良品率。
3. 落实岗位责任制,强化员工责任心。
明确各岗位职责,确保每位员工都能认真负责地完成本职工作。
三、目视化管理,提高现场透明度1. 利用颜色、标识等手段,对现场进行分区、定置。
使员工一目了然,快速找到所需物品,提高工作效率。
2. 设立看板系统,实时展示生产进度、质量状况。
让员工了解生产现状,便于及时调整生产计划。
3. 建立异常反馈机制,鼓励员工发现问题、解决问题。
通过目视化管理,让问题无处藏身,确保生产顺利进行。
四、持续改善,推动现场管理不断提升1. 开展全员参与的质量管理活动,激发员工潜能。
鼓励员工提出合理化建议,不断优化生产流程。
2. 定期组织现场巡查,查找问题根源。
针对发现的问题,制定改进措施,落实整改。
3. 建立持续改善的长效机制,将现场管理纳入日常工作中。
通过持续改进,不断提升车间现场管理水平。
五、库存控制,减少浪费提高响应速度1. 实施准时制生产(JIT),减少在制品和成品库存。
通过精确的需求预测和订单管理,降低库存成本,提高资金周转率。
2. 推行看板管理系统,实现按需生产。
根据生产线的实际消耗情况,动态调整物料供应,避免过量生产。
3. 建立库存预警机制,及时发现潜在问题。
如何进行精益生产管理
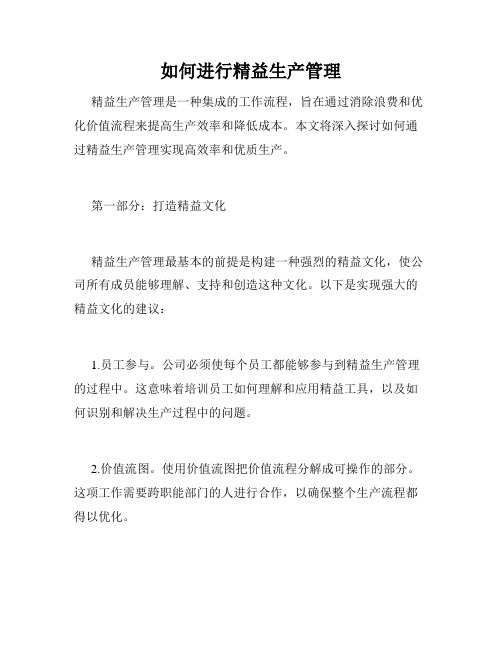
如何进行精益生产管理精益生产管理是一种集成的工作流程,旨在通过消除浪费和优化价值流程来提高生产效率和降低成本。
本文将深入探讨如何通过精益生产管理实现高效率和优质生产。
第一部分:打造精益文化精益生产管理最基本的前提是构建一种强烈的精益文化,使公司所有成员能够理解、支持和创造这种文化。
以下是实现强大的精益文化的建议:1.员工参与。
公司必须使每个员工都能够参与到精益生产管理的过程中。
这意味着培训员工如何理解和应用精益工具,以及如何识别和解决生产过程中的问题。
2.价值流图。
使用价值流图把价值流程分解成可操作的部分。
这项工作需要跨职能部门的人进行合作,以确保整个生产流程都得以优化。
3.连续改进。
将精益生产文化视为一个循环过程,并不断进行改进。
运用持续改进和5S原则,不断寻找生产流程中的改进机会。
第二部分:精细化生产计划一个成功的精益生产管理系统需要可靠的生产计划,并利用所有可用的技术和资源。
以下是精细化生产计划的建议:1.材料控制。
精益生产管理让公司能够提前规划材料的采购和安排,避免过早或过晚采购造成的浪费。
生产成品前需要准备好所有所需材料。
2.在制品控制。
精益生产管理需要确保在制品被按时制造出来。
一个成功的计划应该考虑到精益生产管理的所有要素,从原材料的时效性到零部件和成品的最终装配时间。
3.人员调度。
生产计划需要考虑到所有能力的员工,以及他们在不同部门的使用情况。
第三部分:精益的生产流程通过精益生产管理,公司能够提高生产效率,消除浪费,并减少工作时间的浪费。
以下是优化生产流程的建议:1. 5S的严格实施。
5S的原则是严格遵守的,以确保工作区域的生产流程保持整洁、有序、清晰,从而使得员工更有效率、自信。
2.整合将流程中更多的价值化。
产生流程中的所有活动都必须产生价值或者直接为产生价值,否则就是浪费。
一个成功的精益生产管理系统能够找到并消除掉这种浪费。
3.标准化生产。
标准化确保了在减少浪费和版本差异的同时,保证了一致性和可重复性,可以实现松散耦合状态的组合。
精益生产管理

精益生产管理精益生产管理(Lean Production Management)是一种以提高生产效率和质量为目标的管理方法。
其核心理念是通过减少浪费和增加价值创造来优化生产流程,以达到提高企业竞争力的目的。
一、精益生产管理的基本原则1. 精益生产管理的基本原则是价值流动。
价值流动是指从原材料采购到产品交付给客户的整个生产过程中,能够创造价值的活动。
企业需要识别和优化这些价值活动,以消除非价值活动的浪费。
2. 浪费的八种形式。
精益生产管理中,通常将浪费分为八种形式,即过产、过程、过运输、过库存、过作业、过加工、过检查和过修正。
这些浪费会导致生产成本的增加和效率的降低,因此需要通过精益生产管理的手段进行改善。
3. 价值流图的绘制。
价值流图是精益生产管理中的一项重要工具,用于分析和改进生产流程。
通过绘制价值流图,可以清晰地展示价值流动的整个过程,找出其中的浪费点,并制定相应的改进计划。
二、精益生产管理的实施步骤1. 识别价值和非价值活动。
首先,需要对生产过程中的各个环节进行调查和分析,确定哪些活动是创造价值的,哪些活动是浪费的。
在这个过程中,可以借助价值流图等工具,以确保准确地识别出价值和非价值活动。
2. 优化生产流程。
在识别出非价值活动后,需要对其进行改进,从而优化生产流程。
这可以通过减少不必要的工序、缩短生产周期、优化物料流动等方式来实现。
同时,应该注重提高生产的灵活性和自适应性,以应对市场需求的变化。
3. 建立标准化作业。
为了确保生产流程的稳定和可控,需要制定标准化作业操作程序,并确保员工按照这些程序进行操作。
标准化作业可以帮助企业减少变异和错误,提高产品质量和生产效率。
4. 实施持续改进。
精益生产管理并非一次性的改进活动,而是一个持续的过程。
企业应该建立起持续改进的机制,通过不断地检查和分析生产数据,找出问题,并及时采取纠正措施。
只有坚持持续改进,才能不断提高生产效率和质量。
三、精益生产管理的优势与挑战1. 优势:(1)降低生产成本。
精益生产管理有哪些方法
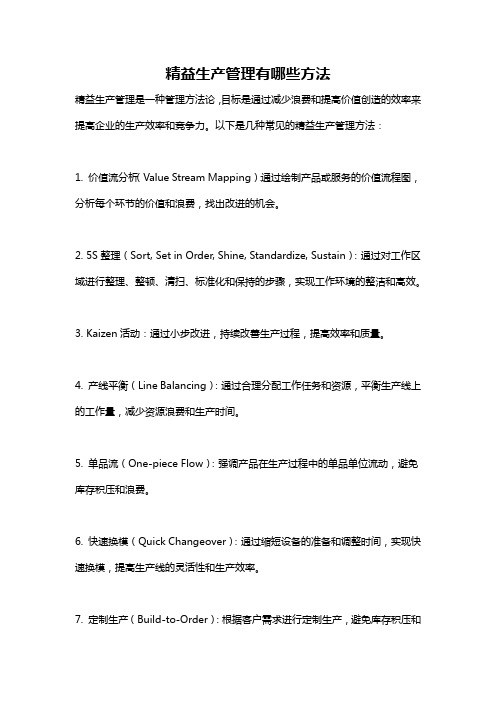
精益生产管理有哪些方法
精益生产管理是一种管理方法论,目标是通过减少浪费和提高价值创造的效率来提高企业的生产效率和竞争力。
以下是几种常见的精益生产管理方法:
1. 价值流分析(Value Stream Mapping):通过绘制产品或服务的价值流程图,分析每个环节的价值和浪费,找出改进的机会。
2. 5S整理(Sort, Set in Order, Shine, Standardize, Sustain):通过对工作区域进行整理、整顿、清扫、标准化和保持的步骤,实现工作环境的整洁和高效。
3. Kaizen活动:通过小步改进,持续改善生产过程,提高效率和质量。
4. 产线平衡(Line Balancing):通过合理分配工作任务和资源,平衡生产线上的工作量,减少资源浪费和生产时间。
5. 单品流(One-piece Flow):强调产品在生产过程中的单品单位流动,避免库存积压和浪费。
6. 快速换模(Quick Changeover):通过缩短设备的准备和调整时间,实现快速换模,提高生产线的灵活性和生产效率。
7. 定制生产(Build-to-Order):根据客户需求进行定制生产,避免库存积压和
浪费。
8. 质量管理(Quality Management):通过建立质量控制和质量改进的制度,降低不良品率和质量成本,提高产品质量和顾客满意度。
以上是几种常见的精益生产管理方法,不同企业可以根据自身情况选择和结合使用。
精益生产管理个人总结5篇

精益生产管理个人总结5篇篇1一、背景随着市场竞争日益激烈,企业为了提升自身竞争力,对生产管理的要求越来越高。
精益生产作为一种追求卓越的管理理念和手段,在现代企业中得到了广泛应用。
我在这段时间里,深入参与了精益生产管理的实践,现就个人参与精益生产管理的工作经历进行如下总结。
二、精益生产管理理念认知1. 精益求精:我认识到精益生产强调不断优化生产过程,消除浪费,提高效率。
从原材料的采购到产品的生产、存储、配送等各个环节,都需要细致入微地分析和改进。
2. 顾客需求导向:精益生产强调以顾客需求为中心,生产符合市场需求的产品。
我体会到,在生产过程中始终要关注市场变化,及时调整生产策略,确保满足客户需求。
3. 团队协作与沟通:在实践过程中,我深刻体会到跨部门协作的重要性。
只有加强团队间的沟通与协作,才能及时发现并解决问题,推动精益生产的实施。
三、个人参与精益生产管理的实践经历1. 生产流程优化:我参与了生产流程的分析和改进工作。
通过深入生产线,对工艺流程进行详细观察和分析,找出存在的浪费现象。
针对这些问题,提出改进措施并付诸实践,取得了显著的效果。
2. 精益培训与推广:我积极参与了公司组织的精益生产培训活动,通过学习掌握了更多的精益生产知识和工具。
同时,我还负责将培训的内容推广到生产一线,提高员工对精益生产的认知和应用能力。
3. 生产数据分析和改进:我负责收集和分析生产数据,通过数据分析找出生产过程中的瓶颈和问题。
针对这些问题,我提出改进措施并跟踪实施效果,确保改进措施的有效性。
4. 跨部门协作与沟通:我积极与生产、研发、采购、销售等部门沟通协作,共同推进精益生产的实施。
通过跨部门合作,解决了许多实际问题,提高了生产效率和质量。
四、取得的成果与收获1. 提高生产效率:通过实施精益生产管理,生产效率得到显著提高,生产周期缩短,交付速度加快。
2. 降低生产成本:通过消除浪费、优化流程和提高生产效率,生产成本得到有效控制。
精益生产七大管理方法

精益生产七大管理方法
一、精益生产管理(Lean Production Management)
1、最小化过程(Minimizing Processes)
这一管理方法就是要努力将生产流程及时间简化,争取将各个工序的时间降到最低,从而加快产品的出厂速度。
2、适当设计流程(Designing Appropriate Processes)
这一管理方法是要求企业意识到,要想提高生产产能,就必须根据要生产的产品或工序的要求,进行适当的设计和安排,以达到理想的生产效果。
3、库存控制(Inventory Control)
这一管理方法要求企业在生产过程中,采取有效的库存控制,以改善工作流程,降低库存成本。
4、流程分析(Process Analysis)
这一管理方法要求企业对自己的生产流程进行分析,看看存在哪些不足及问题,指出其解决方式,从而改善工作流程,提高生产效率。
5、投入产出平衡(Input-Output Balance)
这一管理方法是要求企业要保证每一项投入,都能得到较高的产出,以达到平衡和优化,使生产效率和成本更加合理。
6、质量保证(Quality Assurance)
关于质量保证管理方法,重点是要坚持自动化化、全面化、实时化管理,满足内部和外部客户的需求,以确保产品质量,提高企业的市场竞争力。
7、人力资源开发(Human Resources Development)
这一管理方法强调要重视人力资源开发,大力提升员工专业技能和工作能力,从而提高企业的综合效益和市场竞争力。
精益生产管理的十大方法和实施步骤

精益生产管理的十大方法和实施步骤
精益生产是一种业务流程改进方法,旨在最大化价值并最小化浪费。
以下是实施精益生产的十大方法和步骤:
1. 制定计划:明确目标、收集数据、制定计划并规划资源。
2. 准确评估当前状态:识别问题、流程步骤和价值流、收集数据和测量结果。
3. 访问现场:了解如何实际操作,寻找改进机会。
4. 保持流程简单:消除不必要的复杂性,消除非必要的步骤。
5. 建立标准化流程:明确流程步骤,消除浪费,保证过程标准化。
6. 实施自动化:使用自动化技术改善生产流程、降低成本。
7. 打破固有思维定式:跳出固有思维定式,创新思维。
8. 实施“5S”:整理、整顿、清扫、标准化和纪律化。
9. 持续改进:持续反思改进策略,适应生产变化。
10. 培训员工:确保员工能够理解和支持生产过程。
实施精益生产管理需要长期的、有针对性的改进。
然而,通过实施这些方法和步骤,组织可以增加生产效率、降低成本、提高产品质量,并以最低的成本满足客户需求。
精益生产与管理

精益生产与管理一、精益生产精益生产是一种生产理念,旨在通过最小化浪费来提高生产效率和质量。
这种理念源于日本的丰田生产系统,并在全球范围内得到了广泛应用。
1.1 七种浪费精益生产的核心概念是减少浪费。
除了常见的浪费,如物料、时间和人力资源外,七种浪费也是精益生产中最常见的减少浪费的方法。
这七种浪费是:1. 过度生产2. 运输3. 途中库存4. 处理缺陷5. 过度加工6. 坏货处理7. 等待1.2 价值流映射为了提高生产效率,必须了解生产过程中的所有环节和活动。
价值流映射是一种工具,用于把整个生产过程分解成特定的步骤和活动。
这种工具可以帮助生产工程师发现浪费和瓶颈,从而改进整个生产流程。
1.3 连续流生产精益生产倡导按需生产,而不是过度生产。
连续流生产是一种生产准则,将生产过程分解为小的生产单元,并使物料在生产过程中连续流动。
这种方法可减少浪费和缩短生产时间。
二、精益管理精益管理是一种管理哲学,旨在提高效率和质量。
与精益生产一样,精益管理也源于日本的丰田生产系统,并在世界各地得到了广泛应用。
2.1 Kaizen精益管理的核心概念是不断改进。
Kaizen是一种日本管理哲学,这种哲学强调持续不断的小改进,以提高效率和质量。
这种方法的目的是使每个员工都参与到不断改进的过程中。
2.2 5S方法5S是一种管理方法,旨在提高生产环境的清洁和有序性。
这种方法分为五个步骤:1. 整理2. 整顿3. 清洁4. 清理5. 培养通过这些步骤,5S方法可以建立一种高效且有序的生产环境,减少浪费和错误。
2.3 价值流映射价值流映射不仅适用于生产领域,还适用于管理领域。
对于管理人员来说,价值流映射可以帮助他们发现管理中的浪费和瓶颈,并改进管理过程。
2.4 限制精益管理倡导消除浪费,尤其是物料和时间的浪费。
为了实现这一目标,精益管理强调限制。
通过对生产和管理过程的限制,管理人员可以使员工花更多的时间和精力在真正为公司创造价值的事情上。
精益生产管理

一、什么是精益生产管理二、精益生产管理咨询能对公司产生什么作用和效益1、作用①降低库存②关注流程,提高总体效益③建立无间断流程以快速应变④消除八大浪费⑤全过程的高质量,一次做对⑥顾客需求才生产⑦标准化与工作创新⑧尊重员工,给员工授权⑨满足顾客需要⑩精益供应链⑪“自我反省”和“现地现物”⑫团队工作2、优势分析①人力资源利用优势②产品的质量更高③新产品开发周期短④在制品库存极少⑤厂房的空间小三、如何用精益生产管理辅导企业四、精益生产管理的特点五、精益生产实施原则一、什么是精益生产管理精益生产管理,是一种以客户需求为拉动,以消除浪费和不断改善为核心,使公司以最少的投入获取成本和运作效益显著改善的一种全新的生产管理模式。
它的特点是强调客户对时间和价值的要求,以科学合理的制造体系来组织为客户带来增值的生产活动,缩短生产周期,从而显著提高公司适应市场万变的能力。
精益生产管理辅导公司就是控制浪费、降低成本的最有效的一种生产管理方式。
二、精益生产管理咨询能对公司产生什么作用和效益1、作用①降低公司库存精益生产管理是一种追求无库存生产,或使库存降低到极小的生产系统。
降低库存的目的就是为了解决问题和降低成本,而且低库存是需要高效的流程、稳定可靠的品质来保证的。
有很多的公司在实施精益生产时,以为精益生产就是零库存,不先去改造流程、提高品质,就一味的要求下面降低库存,结果可想而知,成本不但没有降低反而急剧上升,于是就以此说,精益生产不适合我的行业、我的公司,这种误解是需要极力避免的。
②关注流程,提高总体效益什么样的流程就产生什么样的绩效。
改进流程要注意目标是提高总体的效益,而不是提高局部的部门的效益,为了公司的总体效益即使牺牲局部的部门的效益也在所不惜,所以,在精益生产管理辅导中,流程管理很重要。
流程管理好了,对整体的效益提高是相当大的。
③建立无间断流程以快速应变建立无间断流程,将流程当中不增值的无效时间尽可能压缩以缩短整个流程的时间,从而快速应变客户的需要,这点对于精益生产辅导是很重要的④消除八大浪费公司中普遍存在的八大浪费涉及:过量生产、等待时间、运输、库存、过程(工序)、动作、产品缺陷以及忽视员工创造力,只有从根本上消除这些,那么公司就会快速发展起来了。
精益生产管理

精益生产管理精益生产管理(Lean Production Management)是一种旨在通过消除浪费、提高效率和质量的管理理论和方法。
它起源于日本的丰田生产系统(Toyota Production System),并在全球范围内被广泛应用。
精益生产管理的核心思想是追求价值流和流程的最大化优化。
它通过减少无用的非价值增加环节,例如等待、库存和不必要的运输,从而提高整个价值链的效率。
这种管理方法还着重关注员工参与和持续改进的理念,鼓励员工发现问题并提出解决方案,以实现持续的生产效率提升。
精益生产管理的实施需要识别并消除浪费。
这种浪费可能包括过度生产、缺陷、过度处理、不必要的运输和运动、无用的等待、库存和运输等等。
通过精确地定义价值流和深入分析流程步骤,管理者能够识别并消除这些浪费,使生产过程更加高效。
此外,精益生产管理鼓励实施一种持续改进的文化。
通过定期会议和讨论,员工被鼓励提出问题并寻找改进的机会。
这种文化鼓励员工主动解决问题,促进团队合作和创新。
精益生产管理的好处是显而易见的。
首先,它能够降低成本和提高生产效率。
通过消除浪费,管理者能够更好地控制成本,并提高整个生产过程的效率。
其次,这种管理方法还可以提高质量。
通过减少缺陷和浪费,精益生产管理有助于提高产品和服务的质量水平。
最后,它还能提高员工参与度和满意度。
精益生产管理强调员工的主动参与和改进,这有助于增强员工的工作动力和满意度。
综上所述,精益生产管理是一种重要的管理理论和方法,它可以帮助组织提高效率、降低成本、提高质量和促进员工的参与度和满意度。
通过消除浪费和持续改进,组织能够更好地适应市场需求,增强竞争力,取得长期可持续发展。
精益生产管理(Lean Production Management)是一种以提高效率、质量和客户价值为核心的管理理论和方法。
它被广泛认可为一种优化资源利用、降低浪费和最大化生产价值的方法,并被许多组织应用于日常运营和生产流程中。
- 1、下载文档前请自行甄别文档内容的完整性,平台不提供额外的编辑、内容补充、找答案等附加服务。
- 2、"仅部分预览"的文档,不可在线预览部分如存在完整性等问题,可反馈申请退款(可完整预览的文档不适用该条件!)。
- 3、如文档侵犯您的权益,请联系客服反馈,我们会尽快为您处理(人工客服工作时间:9:00-18:30)。
压支架 人数:10 CT:7 SHIFT:1 C/O:0 周期:H LOT:1800
包装 人数:14 CT:7.6 9 1H SHIFT:1 C/O:0 周期:5H LOT:不定 8
2 4H
1 1天
3 4H
4 1H
5 1H
6 5H
绕粗线 7天 人数:11 CT:10.3 1 SHIIFT:1(8) C/O:60 周期:2H
单位五十只
数值
比率
单位五十只
数值 139 19 56 55 9
比率
总 时 间 3453.6min 有效时间 暂停时间 搬运时间 检验时间 677.5min 2638min 43.6min 94.5min 19.6% 76.4% 1.3% 2.7%
总工序数 有效工序 暂停工序 搬运工序 检验工序
13.7% 40.3% 39.6% 6.5%
精益生产概述
唯晓成事之规律 方持不灭改善心
---大野耐一
大野耐一,1912年出生于中国大连,1932年毕 业于名古屋高等工业学校机械科,同年进入丰田纺织公司, 1943年调入丰田汽车工业公司,1949年任该公司机 械厂厂长,后来历任总公司工厂厂长、董事、常务董事和专 务董事,1975~1978年出任丰田汽车工业公司副总 经理。
生产方式的变革主要原因
1、十九世纪前 市场特点: 需多供少---手工作坊 生产特点: 产量低、品质不能保证、技能要求高
进入20世纪顾客需求量增大对品质要求高
2、十九世纪~二十世纪 市场特点: 供需两旺 生产特点: 以流水线为主体的大规模生产,产量大、品质提高
20世纪后期,顾客需求个性化突出
3、二十一世纪 市场特点:多品种,小批量,变化快。 生产方式: 一种适应顾客定制的“多品种”“小批量”生产 生产特点:产量和品种能快速对应市场变化柔性生产
价值流分析认识浪费
信息流 物流 供应商 配套部 采购订单 库房 生产 计划部 日计划 临时计划 旬计划 客户
本地 3天 外地 7天内 日 计 划(生产部)
外地 2天
本地 1天 成品库 15天 10 5H
推进式物控 结构套件 五金 橡胶 1天 杂件 漆包线 7天 绕细线 人数:15 CT:52 SHIFT:2(8+6) C/O:180 周期:4H 焊接组 人数:15 CT:10/6 SHIFT:1 C/O:0 周期:4H LOT:100PCS 烘烤 人数:14 CT:3 SHIFT:3 C/O:0 周期:1H LOT:400PCS 高温灌封 人数:14 CT:13.3/4 SHIFT:3 C/O:0 周期:20min LOT:400PCS 高温烘烤 人数:14 CT:2.25 SHIFT:3 C/O:0 周期:5H LOT:1600PCS 准备组 人数:10 CT:2.4 SHIFT:1 C/O:0 周期: LOT:不定 0.6D 3S 5.6S 0.25D 装配组 人数:10 CT:5.6/6 SHIFT:1 C/O:0 周期:1H LOT:不定
6 5H
2 2H
7 1H
8 1H 测试 人数:4 CT:2.25 SHIFT:1 C/O:0 周期:1H LOT:2000 0.25D
何为浪费
o 实体上改变了物品的活动才能在生产过程中增加价值。 o 加工/组装/油漆/包装? o 点数/库存/质量检验, 增加价值? o 搬运不仅不增加价值,反而可能会减少价值。 o 资源等超过了“绝对最少”的界限。
价值流分析认识浪费
增值比率 =
增值时间(Value added time) 制造周期(Manufacturing cycle time) ×100%
零浪费
¾ ¾ ¾ ¾ ¾ ¾
精益生产概述 生产方式变革历史 精益生产体系 精益生产基础 – 5S 认识浪费 (制造7大浪费) 精益生产的方法
柔性生产线 周转批量大小设定 转产时间与中间库存的关系 工业工程(IE)
¾ 精益六西格码介绍(ห้องสมุดไป่ตู้EAN-SIGMA)
¾ ¾ ¾ ¾ ¾ ¾
精益生产概述 生产方式变革历史 精益生产体系 精益生产基础 – 5S 认识浪费 (制造7大浪费) 精益生产的方法
柔性生产线 周转批量大小设定 转产时间与中间库存的关系 工业工程(IE)
¾ 精益六西格码介绍(LEAN-SIGMA)
何为浪费
什么是浪费: ◇不增加价值的活动,是浪费; ◇尽管是增加价值的活动,所用的资源超过了“绝对最少”的界 限,也是浪费。 NO 1 2 3 4 5 6 7 精 益 生 产 的 七 大 浪 费 过多制造的浪费(Overproduction) 库存的浪费 (Inventory) 搬运的浪费 (Movement) 不良品的浪费(defective products) 加工的浪费 (Processing) 动作的浪费 (Motion) 等待的浪费 (Waiting) 如果认为是 如果认为是 浪费谁都会 浪费谁都会 积极杜绝, 积极杜绝, 问题是本来 问题是本来 是浪费却不 是浪费却不 认为是浪 认为是浪 费,这才是 费,这才是 个大问题。 个大问题。
不 断 暴 露 问 题 , 不 断 改 善
消除浪费降低成本
尊 重 人 性 , 发 挥 人
作业标准 OS
全面质量管理 防呆防错体系 POKAYOKE
低成本简易 自动化 LCIA
多能工 作业员
的 作 用
全员参与的改善和合理化活动(IE) 企业教育、开发、人力资源、5S
标准化
精益生产体系的八大支柱
快速转产与设备维护 (SMD&TPM)
生产方式变革的历史
手工生产的弊端
• 生产成本高 – 产量与成本的反比关系不明显; – 只有富人才能买的起; • 实际上,每辆汽车是一个样车 – 可靠性低; – 一致性差; – 汽车的主人和司机不得不进行“路试”; • 小作坊缺乏基本的创新资源; – 真正的改进需要系统的研究而决非修补;
生产方式变革的历史
Henry Ford 和大量生产
• Ford 对“大”生产的创新; – 装配流水线; – 通用的计量系统和在线检测; – 可互换性部件; – 可维修的设计; • Ford 系统的益处 – 更高的劳动生产率; – 对员工“技能”的要求降低; – 成本大幅度降低;
生产方式变革的历史
大量生产的弊端
• 启动需要高的资本投入; – 庞大的、高容量的设备被用作单一产品的生产; – 许多设备需要满负荷运行; • 生产切换的响应速度缓慢 – 高度专业化工具的更换,需要熟练工人花费冗长的时间; • 部件的备件库存很高 – 高的库存成本; – 很多部件在发现缺陷之前已经被制成; • 工厂的衡量是基础成品率和质量 – 成品率是指:汽车的实际产量/汽车的计划产量; – 质量:出厂质量,并不计入在线的修复;
¾ ¾ ¾ ¾ ¾ ¾
精益生产概述 生产方式变革历史 精益生产体系 精益生产基础 – 5S 认识浪费 (制造7大浪费) 精益生产的方法
柔性生产线 周转批量大小设定 转产时间与中间库存的关系 工业工程(IE)
¾ 精益六西格码介绍(LEAN-SIGMA)
生产方式变革的历史
手工生产作坊式生产
• 19世纪90年代汽车生产主要是由工匠来完成: – 这些工匠在设计、机器操作和安装方面具有极 丰富的经验和高超的水平; – 生产组织极度分散:大部分零件来自于小的加 工作坊。汽车的总成直接是由业主与各个零件 的制造者相互联系、协调来完成; – 通用的工艺设备通常是:钻床、磨床和其它一 些用来加工金属和木材的装备; – 产量非常低 — 每年大约1,000辆,且只有一小 部分汽车的设计是一致的。因为工匠手艺存在 波动,因此没有二辆完全一致的汽车; – 一些现代的“工匠”型汽车公司至今仍然活跃 在市场中。
品质保证与自动化 (TQM)
柔性生产系统
均衡化与同步化 (LOB)
现代 IE作业改善
生产计划与物流系统 产品开发设计系统
意识改革·5S ·3定·现场改善
追求“零”浪费的极限目标
精益企业
精益生产的核心
核心:消除一切浪费,追求精益求精和不断改善。精简并撤除一 切不增值的岗位。精简产品开发设计、生产、管理中一切不产 生附加值的工作,以最优品质、最低成本和最高效率对市场需 求作出最迅速的响应。同时,精益生产把责任下放到组织结构 的各个层次,采用小组工作法,充分调动全体职工的积极性和 聪明才智,把缺陷和浪费及时地消灭在每一个岗位。
¾ 精益六西格码介绍(LEAN-SIGMA)
精益生产概述
零浪费的生产
精益生产(Lean Production)是美国麻省理工学院数位国际汽车计 划组织(IMVP)的专家对日本“丰田丰田汽车JIT(Just In Time)生产 方式”的赞誉之称; JIT:Just in time 准时化生产 只在必要的时间 针对必要的产品 生产必要的数量 精,即少而精,不投入多余的生产要素,只是在适当的时间生产必要 数量的市场急需产品(或下道工序急需的产品); 益,即所有经营活动都要有益有效,具有经济性。
生产方式变革的历史
进入精益生产的时代 精益生产起源于20世纪50年代丰田汽车公司,而 在80年代中期被欧美企业纷纷采用。 随着微利个性化消费时代的来临,精益生产成为 企业竞争的有力武器。
卓越的研究开发,可使新产品进入市场 依赖卓越的生产活动,才能立足于市场
生产方式变革的历史
进入精益生产的时代
当美国的汽车工业处于发展的顶峰时,以大野耐一为代表的丰田 人对美国的大量生产方式进行了彻底的分析,得出了两条结论: – 大量生产方式在削减成本方面的潜力要远远超过其规模效应所带 来的好处 – 大量生产方式不利于企业对市场的适应和职工积极性、智慧和创 造力的发挥 基于这两点认识,丰田公司根据自身面临需求不足、技术落后、 资金短缺等严重困难的特点,同时结合日本独特的文化背景,逐步创立 了一种全新的多品种、小批量、高效益和低消耗的生产方式。 这种生产方式在1973年的石油危机中体现了巨大的优越性,并成 为80年代日本在汽车市场竞争中战胜美国的法宝,从而促使美国花费500 万美元和5年时间对日本的生产方式进行考察和研究,并把这种生产方式 重新命名为精益生产(LEAN PRODUCTION)。