旧油管判定及分级应用技术规范
套管和油管规范 API
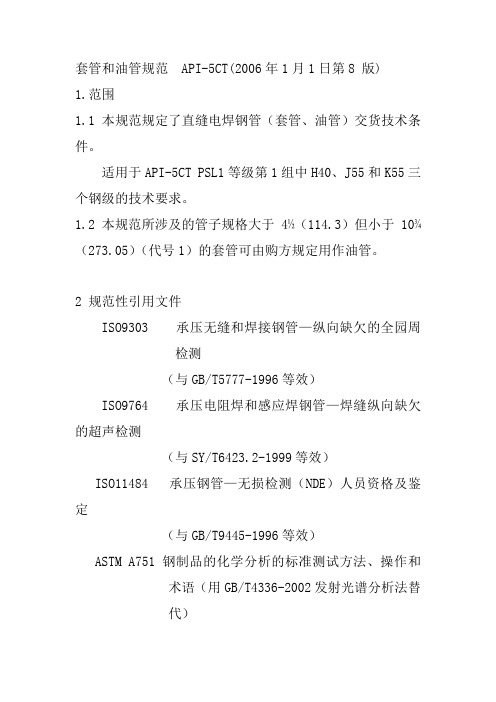
套管和油管规范API-5CT(2006年1月1日第8 版)1.范围1.1 本规范规定了直缝电焊钢管(套管、油管)交货技术条件。
适用于API-5CT PSL1等级第1组中H40、J55和K55三个钢级的技术要求。
1.2本规范所涉及的管子规格大于4½(114.3)但小于10¾(273.05)(代号1)的套管可由购方规定用作油管。
2 规范性引用文件ISO9303 承压无缝和焊接钢管—纵向缺欠的全园周检测(与GB/T5777-1996等效)ISO9764 承压电阻焊和感应焊钢管—焊缝纵向缺欠的超声检测(与SY/T6423.2-1999等效)ISO11484 承压钢管—无损检测(NDE)人员资格及鉴定(与GB/T9445-1996等效)ASTM A751 钢制品的化学分析的标准测试方法、操作和术语(用GB/T4336-2002发射光谱分析法替代)ASTM E23 金属材料缺口冲击试验方法(与GB/T229-1994等效)3 术语、定义3.1套管从地表下入已钻井眼作衬壁的管子。
3.2 缺陷按本规范规定拒收产品所依据的足够大的缺欠。
3.3熔炼分析由炼钢厂报告,对代表一个炉批的化学成分分析。
3.4 油管下入井中用作产液和注液的管子。
3.5 第1组H、J、K、N钢级的所有套管和油管。
3.6 代号1规格或规定外径的无量纲代号,可在订购管子时使用。
3.7代号2单位长度重量的无量纲代号,可在订购管子时使用。
4.符号和缩写CVN—夏比V型缺口J —管子吸收能,焦耳D —管子规定外径d —内径EMI—电磁检验EW—电焊工艺N —全长正火(热处理工艺)NDE —无损检测OD —外径PLS—产品规范等级t —规定壁厚UT—超声检验YS max—规定最高屈服强度,兆帕(Mpa)YS min—规定最低屈服强度,兆帕(Mpa)Mp a—静水压试验压力,兆帕5 购方需提供的资料5.1在订购API5CT套管或油管时,购方应在订单中规定下列要求:1)产品标准: API5CT或ISO11960;2)数量;3)管子类型:套管或油管;4)代号1或规定外径;5)钢级牌号及质量等级;6)长度范围;7)电焊管特殊端部加工要求;8)交货日期和装运说明、购方检验及API5CT 附录B等。
探析旧油管检测及修复技术

探析旧油管检测及修复技术旧油管检测及修复技术是非常重要的一项工作,因为旧油管在使用过程中可能会出现各种各样的问题,如管道老化、漏油、断裂等,这些问题会直接影响油气输送的安全和可靠性。
本文将从旧油管检测和修复两方面进行探析。
1. 无损检测无损检测技术是指通过不破坏物质的情况下,对其内部进行检测和评估的技术手段。
常见的无损检测方法包括超声波检测、磁粉检测、涡流检测、射线检测等。
这些方法可以对油管的内部缺陷进行有效的检测,提供数据支撑和评估依据,可以及时修复油管的问题。
2. 清洗检查清洗检查是指对油管进行内部清洗和外部观察的方法手段。
通过清洗,可以清除管道内的污物和积垢,减少对管道的腐蚀和磨损,同时可以观察管道的内部情况,在有必要的情况下进行维修和修补。
3. 常规检查常规检查是指对油管进行外观、尺寸、连接和支撑状态等的检查。
常规检查最重要的是保证管道的外表和连接处没有任何问题,同时确保管道的支撑状态良好,以确保管道可以长期安全运行。
1. 管道内部修复管道内部修复技术是指通过管内镀膜技术、内覆复合材料等方法对油管内部进行修补的方法。
这种方法可以直接对内部缺陷进行修复,降低了修复难度,同时也可以延长管道使用寿命。
管道外部修复技术是指对油管外部腐蚀和损伤等问题进行修补的方法。
这种方法可以使用热缩套或施工固化材料,将损伤部位进行包裹和修复,使管道仍旧可以正常使用。
3. 管道更换管道更换是指对管道进行彻底更换的方法。
这种方法使用范围广,但是成本更高,适用于严重损坏、断裂等情况。
综上所述,旧油管的检测及修复技术是非常重要的,只有做好这项工作,才能保证油气输送的安全和可靠性。
我们需要不断探索新的技术和方法,使其更加完善和高效。
油管及接头的设计、检验规范

油管及接头的设计、检验规范高压油管及接头的设计、检验规范一:高压油管的设计、检验要求1、外观要求:1)油管的各部分不能有划伤、裂纹、飞边等明显的缺陷。
2)两端的扣压接头螺纹不能有变形、刻痕、刮伤等缺陷。
3)两端的扣压接头的镀层必须是环保白锌。
4)油管必须要有规格标识。
2、清洁度要求:1)油管总成扣压接头两端要有螺纹胶盖保护。
2)管内要求清洁,不能有异物、污垢、生锈现象等。
3、尺寸要求:1)油管总成长度的要求:图纸上应标注油管总成长度及公差。
长度标注方法:使油管总成两端的螺母处于最外端,测量两螺母最外端面之间的长度。
图1油管总成长度标注方法油管总成长度公差按表1选取,对于长度要求严格油管总成可适当提高公差要求:表1 油管总成长度公差油管总成总长mm 公称内径油管总成长度公差25 25公称内径50 50630 +7mm -3mm +12mm -4mm +25mm-6mm630总长1250 +12mm -4mm +20mm -6mm1250总长2500 +20mm -6mm +25mm -6mm2500总长8000 +% %mm8000 +3% -1%mm2)密封锥度要求: 美制37和公制243)油管两端扣压接头的通径要求:①美制螺纹JIC 37锥密封(ISO 8434-2)表2 美制螺纹JIC37°锥扣管接头通径参考数值螺纹规格(M)扣压接头通径(D)/mm 通径公差/mm 旋母扭矩建议值/要求能承受扭矩值/9/16—18UNF 7 24-18 40 3/4—16UNF 10 49-53 70 7/8—14UNF 12 77-85 110②公制螺纹24D_Dd______________________螺纹规格(M)扣压接头通径(D)/mm公差/mm 旋母扭矩建议值/ 要求能承受扭矩值/ M14 4 20-25 40 M16 6 25-40 60M18 7 30-45 70M22 10 40-70 90M26 13 60-100 1304、油管的技术要求表4 油管通径、外径、最大工作压力机最小弯曲半径参考数值油管通径(mm)油管外径(mm)最大工作压力(MPa)最小爆破压力(MPa)最小弯曲半径(mm)64016050 8163514055 10331326511090 1625100100 1986120注:以上油管均为两层钢丝超软型。
井下作业施工油管修复技术操作规程
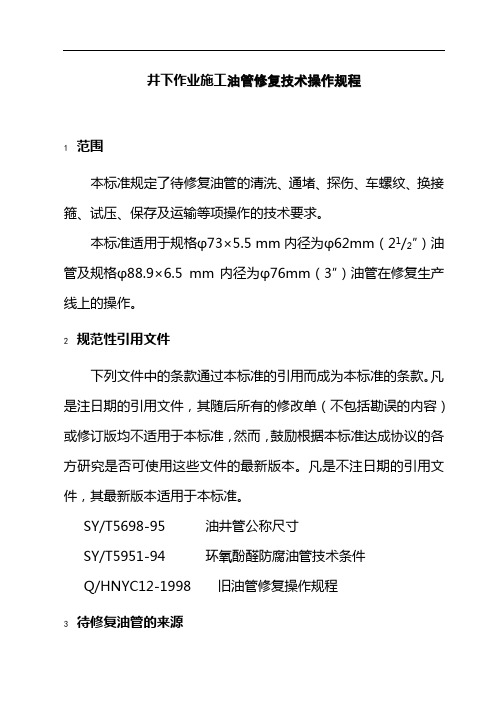
井下作业施工油管修复技术操作规程1 范围本标准规定了待修复油管的清洗、通堵、探伤、车螺纹、换接箍、试压、保存及运输等项操作的技术要求。
本标准适用于规格φ73×5.5 mm内径为φ62mm(21/2″)油管及规格φ88.9×6.5 mm内径为φ76mm(3″)油管在修复生产线上的操作。
2 规范性引用文件下列文件中的条款通过本标准的引用而成为本标准的条款。
凡是注日期的引用文件,其随后所有的修改单(不包括勘误的内容)或修订版均不适用于本标准,然而,鼓励根据本标准达成协议的各方研究是否可使用这些文件的最新版本。
凡是不注日期的引用文件,其最新版本适用于本标准。
SY/T5698-95 油井管公称尺寸SY/T5951-94 环氧酚醛防腐油管技术条件Q/HNYC12-1998 旧油管修复操作规程3 待修复油管的来源在各种井下作业过程中更换下来的规格φ73×5.5 mm内径为φ62mm(21/2″)油管及φ88.9×6.5 mm内径为φ76mm(3″)油管。
4 筛选4.1 对待修复的各种型号的旧油管进行人工筛选。
剔除严重扭曲(扭曲点一处以上者),严重弯曲(弯曲度≥10mm)、严重变形、严重腐蚀(腐蚀坑点≥3mm)等不能修复的油管。
4.2 剔除不能在该生产线上修复的其他管材,如:内径≠φ62mm 的油管及内径≠φ76mm的油管。
4.3 剔除油管内有卡死抽油杆、充满泥沙的油管(确认油管内充满原油的除外)5 浸泡(一部)5.1 将人工筛选后含油多的油管放入油管浸泡池中浸泡。
浸泡池温度≥95℃,浸泡时间≥20min.5.2 浸泡后的油管起出时,须在浸泡池上方停留控干油管内的积水。
6 高压外清洗(一部)6.1 把挑选后的油管用行吊吊到准备架上,依次上线。
6.2 上线后的油管经辊轮传动,依次经过高压外冲洗装置。
6.3 滑轮传动速度控制在10m/min。
6.4 高压外清洗压力不低于50MPa。
管道类别、级别划分(可编辑修改word版)
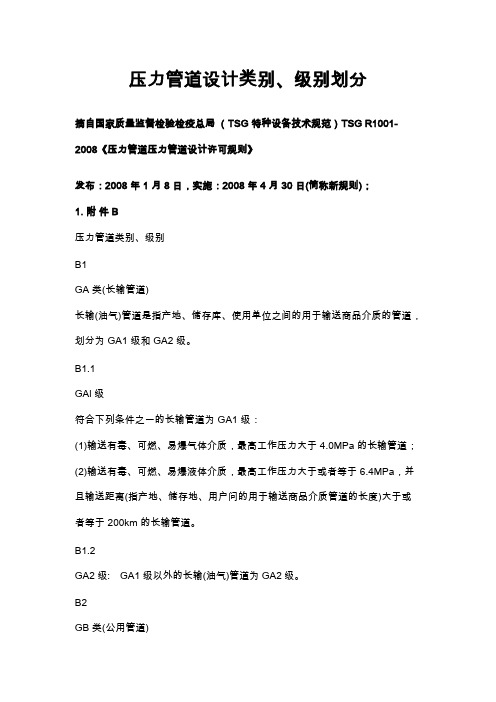
压力管道设计类别、级别划分摘自国家质量监督检验检疫总局(TSG 特种设备技术规范)TSG R1001- 2008《压力管道压力管道设计许可规则》发布:2008 年 1 月 8 日,实施:2008 年 4 月 30 日(简称新规则);1. 附件 B压力管道类别、级别B1GA 类(长输管道)长输(油气)管道是指产地、储存库、使用单位之间的用于输送商品介质的管道,划分为 GA1 级和 GA2 级。
B1.1GAl 级符合下列条件之一的长输管道为 GA1 级:(1)输送有毒、可燃、易爆气体介质,最高工作压力大于 4.0MPa 的长输管道;(2)输送有毒、可燃、易爆液体介质,最高工作压力大于或者等于 6.4MPa,并且输送距离(指产地、储存地、用户问的用于输送商品介质管道的长度)大于或者等于 200km 的长输管道。
B1.2GA2 级: GA1 级以外的长输(油气)管道为 GA2 级。
B2GB 类(公用管道)公用管道是指城市或乡镇范围内的用于公用事业或民用的燃气管道和热力管道,划分为 GBl 级和 GB2 级。
B2.1GBl 级城镇燃气管道。
B2.2GB2 级城镇热力管道。
B3GC 类(工业管道)工业管道是指企业、事业单位所属的用于输送工艺介质的工艺管道、公用工程管道及其他辅助管道,划分为 GCl 级、GC2 级、GC3 级。
B3.1GCl 级符合下列条件之一的工业管道为 GC1 级:(1)输送 GB 5044—85《职业接触毒物危害程度分级》中规定的毒性程度为极度危害介质、高度危害气体介质和工作温度高于标准沸点的高度危害液体介质的管道;(2)输送 GB 50160-1999 《石油化工企业设计防火规范》及 GB 50016-2006《建筑设计防火规范》中规定的火灾危险性为甲、乙类可燃气体或甲类可燃液体(包括液化烃),并且设计压力大于或者等于 4.0MPa 的管道;(3)输送流体介质并且设计压力大于或者等于 10.0MPa,或者设计压力大于或者等于 4.0MPa,并且设计温度大于或者等于 400℃的管道。
QSH0180-2008修复油管质量要求

QSH0180-2008修复油管质量要求ICS 75.180.10 E 92Q/SH修复油管质量要求Quality requirements of tubing repair中国石油化工集团公司发布标准分享网 免费下载Q/SH 0180—2008目次前言 (III)1 范围 (1)2 规范性引用文件 (1)3 初选报废条件 (1)4 修复工艺 (1)5 修复质量 (1)6 储存和运输 (3)I标准分享网 免费下载Q/SH 0180—2008前言本标准由中国石油化工集团公司油田企业经营管理部提出。
本标准由中国石油化工股份有限公司科技开发部归口。
本标准起草单位:中原油田分公司采油三厂。
本标准主要起草人:白连庆、鲁延峰、张寿根、张祥兆、李增仁、李济民、迟延东。
III标准分享网 免费下载Q/SH 0180—2008修复油管质量要求1 范围本标准规定了修复油管过程中初选报废条件、修复工艺和修复质量的要求。
本标准适用于油管修复工艺和修复工序质量的检查验收。
2 规范性引用文件下列文件中的条款通过本标准的引用而成为本标准的条款。
凡是注日期的引用文件,其随后所有的修改单(不包括勘误的内容)或修订版均不适用于本标准,然而,鼓励根据本标准达成协议的各方研究是否可使用这些文件的最新版本。
凡是不注日期的引用文件,其最新版本适用于本标准。
SY/T 6194—2003 石油天然气工业油气井套管或油管用钢管API RP 5A3 管用螺纹脂3 初选报废条件具备下列条件之一的油管直接按报废处理:——管体螺旋形弯曲;——弯曲半径小于100 mm;——内孔严重堵塞;——管体变形2处以上;——管壁腐蚀穿孔破裂;——火烧过的油管、涂料油管。
4 修复工艺修复油管应开展的修复工艺包括:初选、校直、清洗、探伤、试压、修扣、换接箍、检验、储存和运输等工艺。
5 修复质量5.1 校直5.1.1 应具备能够校直油管的设备及配套的生产线。
5.1.2 所有校直油管应进行外观检查,直线度的测试应符合SY/T 6194—2003中8.9的要求。
隔热油管修复与报废技术条件执行标准

《隔热油管修复与报废技术条件执行标准》一、前言隔热油管是工业生产中常见的设备,它具有隔热、保温的作用,对于保障生产过程中的安全和效率起着重要的作用。
然而,随着设备的使用和老化,隔热油管也会出现一些问题,比如破损、老化等。
隔热油管的修复与报废技术条件执行标准显得尤为重要。
二、隔热油管的常见问题1. 破损:隔热油管在运行过程中可能会受到外部冲击或者其他因素的影响而导致破损。
2. 老化:隔热油管长时间的使用会导致其材料老化,从而影响隔热效果。
以上问题都需要及时修复或者报废,以免对生产过程造成影响。
三、隔热油管修复技术条件执行标准在修复隔热油管时,我们需要遵循一定的技术条件执行标准:1. 严格执行操作规程:修复隔热油管需要遵循严格的操作规程,包括清洁、检测、焊接等步骤。
2. 选择合适的修复材料:修复隔热油管需要选择耐高温、耐腐蚀的材料,以保证修复效果和使用寿命。
所有的修复工作都需要在符合相关标准下进行,以保证修复的质量和安全性。
四、隔热油管报废技术条件执行标准当隔热油管达到报废标准时,需要进行合理的报废处理,同时也需要遵循一定的技术条件执行标准:1. 对隔热油管进行全面检测:需要对隔热油管进行全面的检测,确定是否可以修复,如果无法修复则需要及时报废。
2. 按照安全要求进行拆卸:在报废处理过程中,需要按照安全要求进行拆卸,以避免因为拆卸不当而带来的安全隐患。
报废处理同样需要遵循相关标准,以保证设备的安全和环保要求。
五、隔热油管修复与报废的个人观点对于隔热油管的修复与报废,我认为在实际操作过程中需要严格遵循相关标准和规程,以保证修复和报废的质量和安全性。
也需要重视设备的定期检测和维护,以延长设备的使用寿命,提高生产效率。
总结回顾:在隔热油管修复与报废技术条件执行标准方面,我们需要重视相关标准和规程的执行,保证修复和报废工作的质量和安全性。
我个人也认为定期的检测和维护对于设备的使用寿命和生产效率至关重要。
以上是我对《隔热油管修复与报废技术条件执行标准》的一些个人理解和观点,希望能够对您有所帮助。
探析旧油管检测及修复技术

探析旧油管检测及修复技术
旧油管检测及修复技术,在原油、天然气输送中具有至关重要的作用。
下面,我们将
从以下三个方面探析旧油管检测及修复技术。
旧油管检测技术主要是为了保障输油管道运营的安全,防止事故的发生。
其主要的检
测方法包括:回声检测、磁粉探伤、管道内检测及无损检测等。
其中,无损检测是较为常
用的一种方法。
无损检测是指对金属材料进行的不破坏性检测,其主要目的是检测钢管本身的质量及
管道缺陷,例如管壳腐蚀、裂纹、变形等问题。
无损检测技术的应用包括:超声波检测、
磁流检测、射线检测等。
旧油管修复技术可以分为在线修复和离线修复两种,其中在线修复指的是在油管导管
内进行的修复,而离线修复则是针对损坏管段进行更换。
旧油管修复技术的选择,首先要考虑到其实际的应用环境、材料特性和管道损伤情况。
常用的修复技术包括:环氧涂层修复、管道绕包抗拉带更换、环氧粘结材料修复、修复套
管及夹层修复等。
旧油管检测及修复技术的影响因素包括:管道使用年限、管道设计、操作及维护水平、输送介质类型等。
在这些因素的作用下,针对不同的损伤情况使用不同的修复方案,可以
延长油管使用寿命、提高油管输送效率和安全性。
总之,旧油管检测及修复技术对于保障输油管道的安全运营至关重要。
只有通过科学
的检测及修复技术,才能够实现油气运输的高效、安全和稳定。
探析旧油管检测及修复技术

探析旧油管检测及修复技术摘要:针对油田单位中旧油管的检测及修复问题,结合我国油田中旧油管的检测修复现状,首先对旧油管检测修复作业的基本技术要求进行简单介绍,对检测修复过程中的多种关键技术进行深入研究,为我国油田单位中旧油管的检测修复技术应用奠定基础。
关键词:旧油管;检测修复;技术;机械性能1 旧油管检测修复技术要求旧油管检测修复过程中的基本技术要求主要包含四点:①机械性能要求,由于不同级别的油管都具有不同的机械性能,主要的机械性能包括其韧性以及强度等,只有当旧油管修复到相应的机械性能以后,其才能再次投入使用;②联接性能要求,在油管使用的过程中,需要多根油管配合作业才能达到原油开采的要求,在油管相互配合的过程中,需要将其进行联接,反复的联接可能会使得联接部位产生一定的磨损,但是油管在使用的过程中又有密封性的要求,如果联接部位的磨损较为严重,则油管也将无法使用,因此,在检测修复的过程中,其联接性能也必须达到一定的要求后才能投入使用;③通过性能要求,油管最主要的作用就是完成原油的输送作业,如果油管内产生了大量的蜡沉积使其管径减小,则将无法满足使用要求,因此,在进行油管修复的过程中,也需要对其通过能力进行修复,防止影响原油开采效率;④表明状态要求,油管在使用的过程中,不可避免的会出现各种类型的内外腐蚀问题,进而产生了大量的凹坑,这些缺陷的存在会对原油的使用安全产生直接影响,因此,在油管检测修复的过程中,也十分需要对其表明状态进行一定的修复,进而使其满足安全要求。
2 旧油管检测修复重要技术2.1 清洗技术在进行油管检测修复作业之前,首先需要对其进行清洗处理,目前常见的油管清洗技术主要可以分为两种类型,分别是物理方面的清洗和化学方面的清洗。
所谓化学方面的清洗就是将旧油管放置于含有一定量的化学物质的溶液中,在高温的作用下,对油管上的一定沉积物或腐蚀产物进行清除,该种方法的清洗效果以及效率都相对较高,但是该种技术的应用成本也相对较高。
废旧油管杆、抽油泵的修复与再利用问题思考
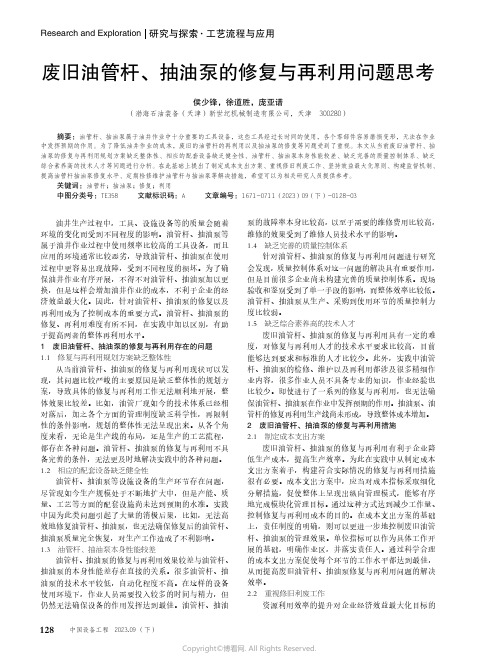
128研究与探索Research and Exploration ·工艺流程与应用中国设备工程 2023.09 (下)油井生产过程中,工具、设施设备等的质量会随着环境的变化而受到不同程度的影响。
油管杆、抽油泵等属于油井作业过程中使用频率比较高的工具设备,而且应用的环境通常比较恶劣,导致油管杆、抽油泵在使用过程中更容易出现故障,受到不同程度的损坏。
为了确保油井作业有序开展,不得不对油管杆、抽油泵加以更换,但是这样会增加油井作业的成本,不利于企业的经济效益最大化。
因此,针对油管杆、抽油泵的修复以及再利用成为了控制成本的重要方式。
油管杆、抽油泵的修复、再利用难度有所不同,在实践中加以区别,有助于提高两者的整体再利用水平。
1 废旧油管杆、抽油泵的修复与再利用存在的问题1.1 修复与再利用规划方案缺乏整体性从当前油管杆、抽油泵的修复与再利用现状可以发现,其问题比较严峻的主要原因是缺乏整体性的规划方案,导致具体的修复与再利用工作无法顺利地开展,整体效果比较差。
比如,油管厂现如今的技术体系已经相对落后,加之各个方面的管理制度缺乏科学性,再限制性的条件影响,规划的整体性无法呈现出来。
从各个角度来看,无论是生产线的布局,还是生产的工艺流程,都存在各种问题。
油管杆、抽油泵的修复与再利用不具备完善的条件,无法更及时地解决实践中的各种问题。
1.2 相应的配套设备缺乏健全性油管杆、抽油泵等设施设备的生产环节存在问题,尽管现如今生产规模处于不断地扩大中,但是产能、质量、工艺等方面的配套设施尚未达到预期的水准。
实践中因为此类问题引起了大量的消极后果,比如,无法高效地修复油管杆、抽油泵,也无法确保修复后的油管杆、抽油泵质量完全恢复,对生产工作造成了不利影响。
1.3 油管杆、抽油泵本身性能较差油管杆、抽油泵的修复与再利用效果较差与油管杆、抽油泵的本身性能差存在直接的关系。
很多油管杆、抽油泵的技术水平较低,自动化程度不高。
油管性能基本要求

API油管螺纹锥度测头尺寸
量规类型
每英寸螺 纹牙数
螺纹类型
球形测头直径
in
mm
锥度规
8
圆螺纹 0.072
1.83
锥度规
10
圆螺纹 0.057
* 公差±0.002in(±0.05mm)。
1.45
外螺纹锥度应使用外螺纹锥度量规。
外螺纹锥度量规的使用方法:
a)将量规的调节臂调至被测外螺纹的规格,检查仪表的灵 活性和测头的直径;
--夏比V型缺口冲击试验 --取样取向、尺寸,试验温度(除了第1组,J55和K55
钢级应在21℃试验外,其它所有组的试验温度应为0℃。 )
--各钢级管体和接箍的规定最小值
材料要求—晶粒度 --仅对抗硫材料C90、T95 --大于等于5级。 材料要求—硫化物应力开裂试验(SSC) --针对抗硫材料C90、T95 --以ANSI-NACE(美国腐蚀工程师协会 )
b)量规测量爪上的固定球形测头置于首牙完整螺纹的牙槽 内,另一测量爪上活动测杆上的球形测头置于直径相对 侧同一螺纹的牙槽内;
c)固定的测头保持不动,测杆上的触头做小圆弧摆动。调 节指示表,使零位与最大读数重合;
d)以同样的方法,沿同一条圆锥母线在规定的间距内进行 连续测量;
e)连续测量之差值即为该段螺纹的锥度。完整螺纹的最后 间距内的锥度也应测量。
质量控制:以油管技术标准为基础
油管主要技术标准包括:
API SPEC 5CT, API SPEC 5B, API RP 5C1, API BUL 5C2, API TR 5C3, API RP 5C5, API RP 5A3。
API SPEC 5CT规定了油、套管及附件的技术 条件,为管体生产控制及交货检验标准;
API SPEC 5CT:2011新旧对照
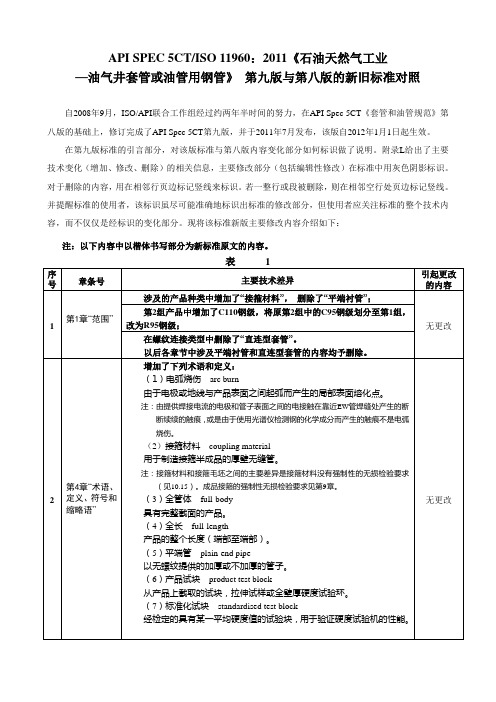
API SPEC 5CT/ISO 11960:2011《石油天然气工业—油气井套管或油管用钢管》第九版与第八版的新旧标准对照
自2008年9月,ISO/API联合工作组经过约两年半时间的努力,在API Spec 5CT《套管和油管规范》第八版的基础上,修订完成了API Spec 5CT第九版,并于2011年7月发布,该版自2012年1月1日起生效。
在第九版标准的引言部分,对该版标准与第八版内容变化部分如何标识做了说明。
附录L给出了主要技术变化(增加、修改、删除)的相关信息,主要修改部分(包括编辑性修改)在标准中用灰色阴影标识。
对于删除的内容,用在相邻行页边标记竖线来标识。
若一整行或段被删除,则在相邻空行处页边标记竖线。
并提醒标准的使用者,该标识虽尽可能准确地标识出标准的修改部分,但使用者应关注标准的整个技术内容,而不仅仅是经标识的变化部分。
现将该标准新版主要修改内容介绍如下:
注:以下内容中以楷体书写部分为新标准原文的内容。
表 1。
探析旧油管检测及修复技术

探析旧油管检测及修复技术旧油管检测及修复技术是一项非常重要的技术,它能够帮助我们及时发现并修复旧油管的各种问题,确保其正常使用,可以延长旧油管的使用寿命,提高其工作效率,并减少对环境的影响。
本文将探讨旧油管检测及修复技术的原理、方法和应用。
一、旧油管检测技术的原理和方法旧油管检测技术主要是通过检测管道内部及其周围的状态来判断其是否存在问题。
其中,主要有以下几种检测方法:1. 外观检测:这种方法是通过肉眼观察油管的外观来判断其是否存在问题,如是否有明显的损坏、裂缝、变形等。
这种方法的优点是简单易行,但缺点是无法发现隐形的问题。
2. 磁粉检测:这种方法是将磁粉涂在油管表面,然后经过加热,使用磁探头扫描,可以发现油管表面存在裂缝或裂纹的区域。
这种方法的优点是可以检测出许多隐形问题,但缺点是该方法只适用于铁制品。
3. 超声波检测:这种方法是将超声波发射到油管内部,并通过接收回波来判断油管是否存在问题。
使用超声波可以检测到油管内部的裂缝、疼痛、破损等问题,同时也可以检测出油管周围的变形和腐蚀。
这种方法可以适用于所有类型的油管,但需要专业操作。
4. X射线检测:这种方法是使用X射线透过油管来获得其内部和周围的图像,从而检测出其中的问题。
这种方法可以检测到油管内部的污垢、疏松、灰化、腐蚀、疼痛、裂缝等问题,但需要专业的设备和技术。
1. 补焊:当油管出现部分破裂,或者存在缺损时,可以使用补焊方法来实现修复。
该方法是通过焊接来将油管的损坏部分填补起来,使其恢复原状。
但需要注意的是,补焊质量需要经过专业检测,以确保其安全可靠。
2. 射流喷涂:这种方法是将高速喷射的氧化铝、碳化硅等硬质材料粘附在油管表面,以强化其表面硬度。
该方法可以有效地延长油管的使用寿命,但需要专业技术并且费用较高。
3. 内衬涂层:这种方法是在油管内部涂上一层特殊的涂层,以降低摩擦力、减少油管内部的腐蚀。
该方法可以有效地延长油管的使用寿命,但需要专业操作并且费用较高。
内衬油管通用技术条件(QSH1020 1889-2011)
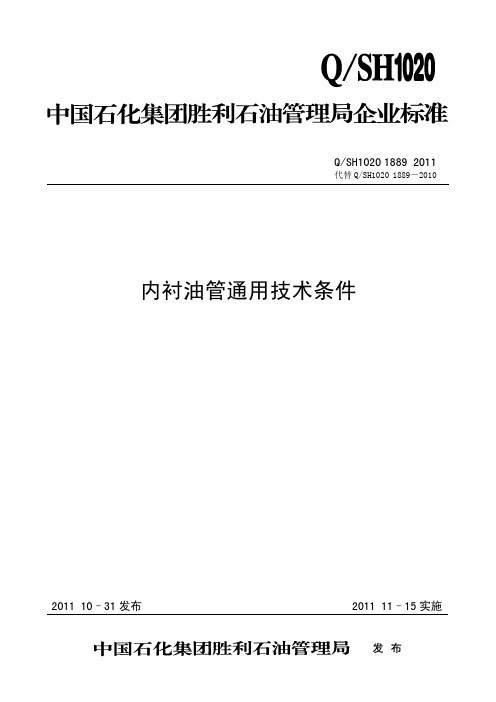
图 2 衬管结合性能检测方法示意图 5.8 通径检测
采用通径规进行全长检测,通径规尺寸见表 6,两端倒圆角不小于 R3。 表 6 内衬油管用通径规尺寸
单位为毫米
序号
代号
通径规直径
通径规长度
1
2 7/8
51
1200
2
3 1/2
64
1200
3
4 1/2
86
6 检验规则
6.1 取样规则
内衬油管出厂检验按生产批次进行抽检,抽样方案见表 7。
Q/SH1020 1889-2011
代替 Q/SH1020 1889-2010
内衬油管通用技术条件
2011-10–31 发布
2011-11–15 实施
Q/SH1020 1889-2011
前言
本标准代替 Q/SH1020 1889—2010《内衬抗磨抗腐油管通用技术条件》。 本标准与 Q/SH1020 1889—2010 相比,除编辑性修改外主要技术变化如下: ——标准名称由《内衬抗磨抗腐油管通用技术条件》改为《内衬油管通用技术条件》; ——范围中“本标准适用于油田采油、注水井用内衬油管的制造和验收”改为“本标准适用于油田
内衬油管在运输过程中应轻吊轻放,防止油管变形和损伤。其它运输要求应符合 GB/T 17745 的规定。 7.4 贮存
内衬油管应按内衬类型及油管尺寸规格分类存放,存放处应通风。应尽量避免阳光的长期照射, 在空气中的存放时间不宜超过 12 个月。其它贮存要求应符合 GB/T 17745 的规定。 8 质量合格证
无缝钢管
钢级 J55
重量代号 6.50
规格代号 2 7/8
2009 年 7 月生产
API 会标标志
作业过程油管使用规定
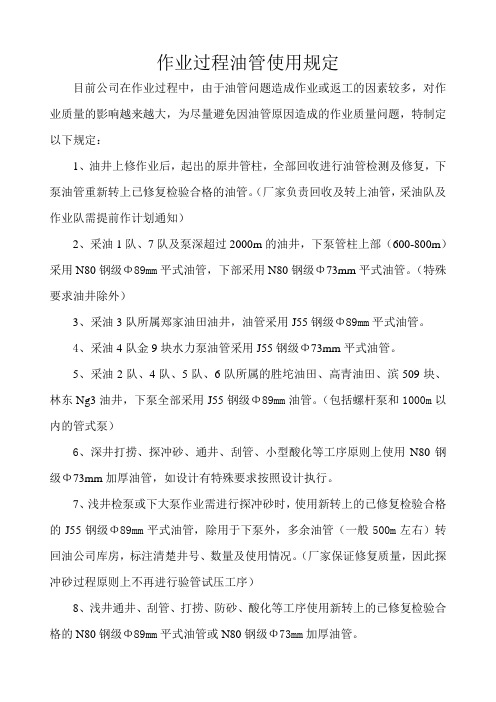
作业过程油管使用规定目前公司在作业过程中,由于油管问题造成作业或返工的因素较多,对作业质量的影响越来越大,为尽量避免因油管原因造成的作业质量问题,特制定以下规定:1、油井上修作业后,起出的原井管柱,全部回收进行油管检测及修复,下泵油管重新转上已修复检验合格的油管。
(厂家负责回收及转上油管,采油队及作业队需提前作计划通知)2、采油1队、7队及泵深超过2000m的油井,下泵管柱上部(600-800m)采用N80钢级Φ89mm平式油管,下部采用N80钢级Φ73mm平式油管。
(特殊要求油井除外)3、采油3队所属郑家油田油井,油管采用J55钢级Φ89mm平式油管。
4、采油4队金9块水力泵油管采用J55钢级Φ73mm平式油管。
5、采油2队、4队、5队、6队所属的胜坨油田、高青油田、滨509块、林东Ng3油井,下泵全部采用J55钢级Φ89mm油管。
(包括螺杆泵和1000m以内的管式泵)6、深井打捞、探冲砂、通井、刮管、小型酸化等工序原则上使用N80钢级Φ73mm加厚油管,如设计有特殊要求按照设计执行。
7、浅井检泵或下大泵作业需进行探冲砂时,使用新转上的已修复检验合格的J55钢级Φ89mm平式油管,除用于下泵外,多余油管(一般500m左右)转回油公司库房,标注清楚井号、数量及使用情况。
(厂家保证修复质量,因此探冲砂过程原则上不再进行验管试压工序)8、浅井通井、刮管、打捞、防砂、酸化等工序使用新转上的已修复检验合格的N80钢级Φ89mm平式油管或N80钢级Φ73mm加厚油管。
9、水平井完井下泵使用J55钢级Φ89mm平式油管,但其他如通井、刮管、射孔、探冲砂、防砂、封堵、打丢封等工序,原则上必须使用新转上的已修复检验合格的N80钢级Φ89mm平式油管或N80钢级Φ73mm加厚油管,进入造斜点后油管必须45度倒角,设计有特殊要求按照设计执行。
10、新井投产作业及完井必须全部为新油管,新油管规格型号按以上深井和浅井要求执行。
探析旧油管检测及修复技术

探析旧油管检测及修复技术1. 引言1.1 背景介绍旧油管是石油工业中广泛使用的重要设备,其质量对整个生产过程的稳定性和安全性至关重要。
由于长期使用和外部环境的影响,旧油管往往会出现各种损坏情况,导致其性能下降甚至发生泄漏事故。
为了确保油管运行的正常和安全,旧油管的检测和修复技术显得尤为重要。
目前,随着科技的不断进步和工艺的日益完善,旧油管检测及修复技术也在不断改进和完善,为旧油管的安全运行提供了更加可靠的保障。
通过对旧油管的定期检测与及时修复,可以及早发现并解决潜在问题,延长油管的使用寿命,提高生产效率,降低维修成本,也可以减少对环境的影响,实现资源的最大化利用。
研究旧油管的检测及修复技术具有重要的理论和实践意义。
1.2 研究意义旧油管检测及修复技术的研究意义在于解决旧油管存在的安全隐患问题,保障石油运输系统的正常运行和安全性。
随着石油资源的逐渐枯竭,对于旧油管的修复和维护显得尤为重要。
传统的旧油管检测和修复技术存在一定局限性,需要更加高效和可靠的新技术来替代。
通过深入研究旧油管检测及修复技术,可以提高修复效率、降低修复成本,减少石油泄漏事故的发生,保护环境,维护能源安全。
该研究还有利于推动相关技术的创新和发展,推动石油行业向智能化、自动化方向发展。
研究旧油管检测及修复技术具有十分重要的意义,对避免环境破坏、保障石油运输安全和提高经济效益都具有积极的促进作用。
1.3 目的目的是对旧油管检测及修复技术进行深入探究,以探讨如何有效地延长旧油管的使用寿命,提高油管输送效率,减少资源浪费和环境污染。
通过对旧油管的检测方法、常见的油管损坏情况、修复技术、材料与成本分析以及修复效果评估的综合分析,探讨优化修复方案,提高修复效果,降低修复成本,为油管使用和维护提供科学依据。
通过研究旧油管检测及修复技术的应用前景、对环境和经济的影响以及未来的研究方向,为相关领域的研究和实践提供借鉴和指导。
旨在促进油管行业的可持续发展,实现资源的有效利用和环境的保护。
废旧油管处置方案设计依据
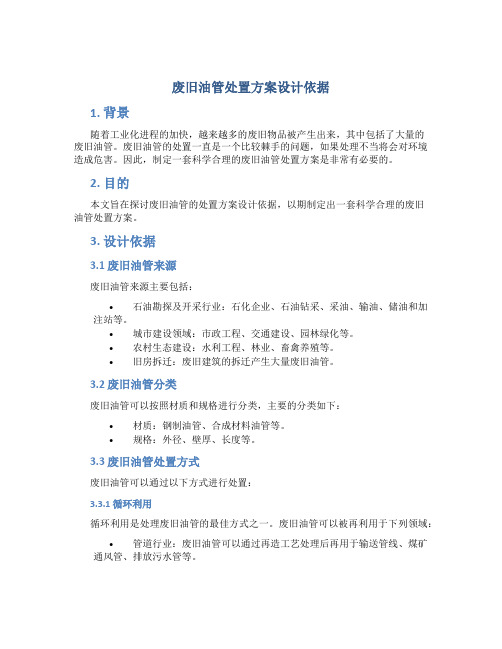
废旧油管处置方案设计依据1. 背景随着工业化进程的加快,越来越多的废旧物品被产生出来,其中包括了大量的废旧油管。
废旧油管的处置一直是一个比较棘手的问题,如果处理不当将会对环境造成危害。
因此,制定一套科学合理的废旧油管处置方案是非常有必要的。
2. 目的本文旨在探讨废旧油管的处置方案设计依据,以期制定出一套科学合理的废旧油管处置方案。
3. 设计依据3.1 废旧油管来源废旧油管来源主要包括:•石油勘探及开采行业:石化企业、石油钻采、采油、输油、储油和加注站等。
•城市建设领域:市政工程、交通建设、园林绿化等。
•农村生态建设:水利工程、林业、畜禽养殖等。
•旧房拆迁:废旧建筑的拆迁产生大量废旧油管。
3.2 废旧油管分类废旧油管可以按照材质和规格进行分类,主要的分类如下:•材质:钢制油管、合成材料油管等。
•规格:外径、壁厚、长度等。
3.3 废旧油管处置方式废旧油管可以通过以下方式进行处置:3.3.1 循环利用循环利用是处理废旧油管的最佳方式之一。
废旧油管可以被再利用于下列领域:•管道行业:废旧油管可以通过再造工艺处理后再用于输送管线、煤矿通风管、排放污水管等。
•建筑行业:废旧油管可以用于构建雨水收集系统、雨水利用系统、太阳能集热器等。
3.3.2 再制造废旧油管可以通过再制造进行处理,加工成符合标准的新油管。
3.3.3 废旧油管回收废旧油管可以由专业机构回收再处理。
废旧油管回收可通过拍卖、出售方式变废为宝。
3.3.4 科学填埋如果无法进行循环利用、再制造和回收,则可以采用科学填埋的方式进行处理。
废旧油管必须进行分类处理,进行专门的油管填埋。
废旧油管填埋应遵照国家相关标准要求。
4. 结论制定一套科学合理的废旧油管处置方案非常有必要,为此本文提出了废旧油管处置方案设计依据。
具体包括废旧油管来源、分类及处理方式。
只有采取科学的方法和措施,才能更好地处理废旧油管,减少环境和人群健康的影响。
- 1、下载文档前请自行甄别文档内容的完整性,平台不提供额外的编辑、内容补充、找答案等附加服务。
- 2、"仅部分预览"的文档,不可在线预览部分如存在完整性等问题,可反馈申请退款(可完整预览的文档不适用该条件!)。
- 3、如文档侵犯您的权益,请联系客服反馈,我们会尽快为您处理(人工客服工作时间:9:00-18:30)。
旧油管判定及分级应用技术规范(征求意见稿)1范围本标准适用于中国石化西北油田分公司旧油管修复过程中分级判定、修复工艺和修复质量的要求。
2规范性引用文件本技术协议引用以下标准。
提倡使用下列标准的最新版本。
API SPEC 5CT套管和油管规范API SPEC 5B套管、油管和管线管螺纹加工和检验规范API RP 5B1套管、油管和管线管螺纹测量和检验的推荐作法中国石油化工股份有限公司《油管和套管采购技术规范》(第1部分:普通油管和套管)试行中国石化西北油田分公司《套管和油管采购要求》3 分级条件本标准以旧油管内外表面缺陷深度为主要依据,结合旧油管剩余长度,油管分级准则为:一级油管a) 缺陷深度≤10%标准壁厚;b) 管体内壁不允许存在线性轴向磨损缺陷;c) 管体长度符合API SPEC 5CT表所列范围2的要求。
二级油管a) 10%标准壁厚<缺陷深度<30%标准壁厚;b) 管体内壁存在壁厚损失<%的线性轴向磨损缺陷;c) 管体长度符合API SPEC 5CT表所列范围1或范围2的要求,用户可根据需要进行选择。
报废油管:具备下列条件之一的油管直接判为报废油管a) 壁厚损失≥30%标准壁厚;b) 管体内壁存在壁厚损失≥%的线性轴向磨损缺陷;c) 管体弯曲;d) 内孔严重堵塞;e) 管体变形2处以上;f) 管体长度小于用户所选API SPEC 5CT表所列长度范围要求。
4 修复工艺旧油管应开展修复工艺包括:清洗、通径、外观检验、打磨、探伤、分级判定、更换接箍、螺纹修理、试压、标识、检验、螺纹保护等项目。
P110和110S及特殊钢级油管不允许进行矫直。
5 修复质量清洗和通径5.1.1 应具备清洗油管的设备及配套的生产线。
5.1.2 修复油管清洗后,应达到内外壁无明显油污、蜡和结垢,内壁无锈蚀掉块等卡挂井下工具的残留物质,油管内外壁应能够满足探伤对管体表面的要求。
5.1.3 每根修复油管都应进行全长通径试验。
5.1.4 通径棒尺寸应符合API SPEC 5CT套管和油管规范中的技术要求。
5.1.5 通径试验不合格的油管,应在相应的缺陷位置涂一条环绕的蓝色色带,在管端0°和180°方向分别作出×形蓝色标识。
5.1.6 每个班在生产前和连续生产4h以后,应检查通径棒一次。
外观检验和打磨5.2.1 初步目测分类检查的项目应包括:有无裂纹、裂缝、麻点、凹坑、内外表面腐蚀损伤、内外表面钢丝绳损伤(纵向)、外表面卡瓦和大钳咬伤、内表面抽油杆磨损、管体弯曲、接箍外观及螺纹、公端螺纹损伤情况等。
5.2.2 对造成壁厚损失的各类缺陷进行测量,按照分级标准进行判定。
5.2.3对卡瓦和大钳咬伤等缺陷可以进行打磨,打磨后应对剩余壁厚进行测量并按照分级条件做出判定。
5.2.4管子两端内壁腐蚀坑和管体内壁偏磨是旧油管的常见缺陷,需要重点检查。
探伤和壁厚检测5.3.1 设备和人员5.3.1.1应具备一定精度的自动无损检测设备和壁厚测量设备自动化无损检测设备工作时对工件的重复覆盖率必须大于等于120%。
5.3.1.3 探伤设备的信噪比大于8dB。
5.3.1.4 自动化设备必须由具有计量认证资质的单位对设备进行三年一次的认证和一年一次的计量。
5.3.1.5无损检测的人员必须经过相应无损检测机构培训,并取得一级或一级以上的资质。
5.3.1.6 二级油管分级检测:a) 无损检测人员取得二级或二级以上的资质;b) 设备应经过相应考核后,能承担旧油管分级检测任务。
无损检测方法(新增)无损检测的方法见附表1所示。
表1 无缝管、接箍坯料和焊管管体无损检测方法修改原因:引用自API 5B标准中的无损检测方法,对5.3.1.1的设备提出准确要求。
5.3.2 探伤样管5.3.2.1一级油管样管:作为评判的参考标样尺寸应符合API SPEC 5CT表所述L2验收等级的尺寸要求,参考标样应与被检油管具有相同的直径、壁厚、钢级和材质。
5.3.2.2 二级油管样管:作为评判的参考标样尺寸选用Φ的通孔样管,参考标样应与被检油管具有相同的直径、壁厚、钢级和材质。
5.3.3 探伤和壁厚检测5.3.3.1通则a) 进行探伤和壁厚检测前应在每根旧油管上打上钢印号作为唯一标识;b) 探伤和壁厚检测前应逐根登记钢印号;c) 工厂的每个班在进行探伤和测厚检测前和连续探伤和测厚4小时后,应对探伤仪器和测厚仪器进行校准并保存校准记录。
5.3.3.2 探伤a) 探伤前使用相应级别的样管对探伤仪进行标定;b) 符合一级油管探伤要求的判定为一级油管,不符合一级油管探伤标准的进行二级油管探伤。
一级油管按照第条进行标识;c) 符合二级油管探伤要求的判定为二级油管,不符合二级油管探伤标准的应判定为报废油管。
二级和报废油管按照第条进行标识;d) 本标准规定的自动无损检验操作中,管子两端可能存在一小段不能被检测到。
在这种情况下,未经检验的管端区域应进行至少与自动无损检验具有相同检验程度的手工检验。
修改建议:将“一小段”修改为“盲区”修改原因:管子两端可能存在一小段不能被检测到的就是油管通过自动探伤设备的“盲区”,对“一小段”进行了名词替换。
5.3.3.3 壁厚检测。
在自动测厚过程中,发现不符合或接近相应级别油管剩余壁厚标准的部位,应当进行周向与纵向人工复检,找到剩余壁厚最小值。
5.3.4 油管探伤和壁厚检测后,一、二级油管进入螺纹修复工序。
螺纹修复和更换接箍5.4.1 螺纹检查和判定5.4.1.1对于内外表面存在腐蚀缺陷的油管,需要卸开接箍,对其工厂端螺纹以及现场端螺纹根部的腐蚀情况进行检查,切头后对管端起100mm范围内的内外表面腐蚀情况进行重点检查。
5.4.1.2公端螺纹存在锈蚀、粘扣、破坏螺纹连续性及严重腐蚀坑的应切头重新车扣。
5.4.1.3接箍螺纹存在锈蚀、粘扣、破坏螺纹连续性的各种缺欠应更换接箍。
5.4.1.4接箍外表面存在腐蚀缺陷、端面损伤缺陷以及超过表1所列缺欠,应更换接箍。
表1 接箍外表面缺欠允许深度单位:mm修改建议:增加适用于二级油管的接箍外表面缺欠允许深度数据表格。
修改原因:表1中的数据引自API标准,适用于一级油管。
随着油管的降级使用,接箍外表面缺欠也随之增加,接箍外表面缺欠允许深度若仍引用一级油管的标准,维修过程中会引起大批更换接箍的情况,存在成本浪费的问题,技术层面也存在一定的漏洞,同时缺乏数据的支持。
因此完井测试管理中心建议通过实验得出数据,增加适用于二级油管的接箍外表面缺欠允许深度数据表格,避免上述情况的出现。
5.4.2 修扣5.4.2.1 应具备管子螺纹加工车床及配套设备,并具备满足生产需要的专用量具和螺纹规。
5.4.2.2 修复管子螺纹质量应符合中石化《油管和套管采购技术规范》和西北油田分公司企业标准《套管和油管采购要求》以及生产厂家提供的验收标准要求。
注:TP-JC扣型的二级油管,在Lc范围内最后3牙齿顶,允许存在因腐蚀坑造成的点状缺欠。
修改建议:将“注:TP-JC扣型的二级油管,在Lc范围内最后3牙齿顶,允许存在因腐蚀坑造成的点状缺欠”删去。
工厂应在线100%检验每根油管螺纹的各项参数,离线抽检比例不低于30%,并保存检验记录。
修改建议:工厂在生产线上每根油管螺纹各项参数检验方法执行油管厂家检验标准,工厂在成品检验时的抽检比例不低于30%,并保存检验记录。
更换接箍5.4.3.1 应具备机械上卸接箍的设备及相关设施。
5.4.3.2 管子接箍应是无缝的,应具有与管子相同的钢级和类型、相同或更高的PSL,并经过与管子相同的热处理,符合中石化《油管和套管采购技术规范》和西北油田分公司企业标准《套管和油管采购要求》以及生产厂家提供的验收标准要求。
5.4.3.3 接箍上紧前,应在管子螺纹与接箍整个结合表面涂上螺纹脂,螺纹脂应符合SY/T 5199《套管、油管和管线管用螺纹脂》要求,特殊扣用螺纹脂应符合生产厂家的要求。
5.4.3.4 油管接箍应采用机械方式上紧,上扣扭矩参照附录2执行,建议将上扣扭矩控制在最佳扭矩与最大扭矩之间。
油管试压5.5.1 应具备静水压试验生产线及配套设施。
5.5.2 所有修复油管都应进行静水压试验。
5.5.3 一级油管试压5.5.3.1试验压力45MPa,全压试验状态保持时间应不得少于10s。
5.5.3.2 每批应有5%的油管静水压试验压力达到69MPa,全压试验状态保持时间应不得少于10s。
5.5.4 二级油管试压,试验压力69MPa,全压试验状态保持时间应不得少于10s。
5.5.5 工厂在试压过程中应注意对螺纹的保护,在试压完成后应对螺纹外观进行检查,如果造成螺纹损伤,应重新修理和试压。
涂层与保护5.6.1 经过修复的油管管体和接箍应有外涂层,以防止运输储存过程中生锈,应采取措施使涂层光滑、致密,并尽可能不脱落,涂层的等级应具有保护管子至少3个月的能力。
5.6.2完全完成加工的螺纹应装上外螺纹和内螺纹保护器。
螺纹保护器的设计、材料和机械强度应能保护螺纹和管端避免在正常装卸和运输中受损。
外螺纹保护器应覆盖管子螺纹全长,内螺纹保护器应覆盖等于螺纹总长度的内螺纹。
在运输与正常的库存期间,螺纹保护器的设计和材料应能保证在正常装卸和运输中使螺纹隔绝脏物和水。
正常的库存时间应约为一年。
螺纹保护器的螺纹形状应不损伤产品的螺纹。
5.6.3螺纹保护器的材料不应含有能引起螺纹腐蚀或促使螺纹保护器与产品螺纹粘结的成分,并能适用于-46℃~+66℃的服役温度。
标识5.7.1 一、二级油管的管体标识5.7.1.1 为便于追溯和识别,修复完毕的所有一、二级油管应做好标识,标识方法和位置见第条,建议采用漆模印方法,标识内容包括加工厂名称或商标、钢级、壁厚、外径、扣型、静水压试验压力、是否更换接箍等。
5.7.1.2 漆模印标记要求:漆模印标记印在每根管子的外表面上,且在距接箍端不小于米处开始。
标记顺序为:加工厂标记管子外径×壁厚钢级扣型静水压试验压力是否更换接箍(更换标记为G,未更换为N)级别(一级油管标注Ⅰ,二级油管标注Ⅱ),如图1所示。
5.7.1.3 钢印标记要求:钢印标记印在每个管子距公端500mm处,标记顺序为:加工厂标记钢级扣型静水压试验压力是否更换接箍(更换标记为G,未更换为N)级别(一级油管标注Ⅰ,二级油管标注Ⅱ)。
5.7.2色标5.7.2.1 API油管:一级油管管体与接箍的色标,按照API标准相应条款执行;二级油管管v1.0 可编辑可修改体与接箍的色标,在原一级油管色标后另外喷涂一条约50mm宽环绕的绿色带。
5.7.2.2 非API油管:一级油管110S钢级管体在工厂端不小于米处的管体上喷涂两条约50mm宽环绕管体的黄色带,接箍外表面喷涂白漆后喷涂一条约50mm宽环绕接箍的黄色带;在原一级油管色标后另外喷涂一条约50mm宽环绕的绿色带。