毕业设计=年产2万吨味精工艺设计

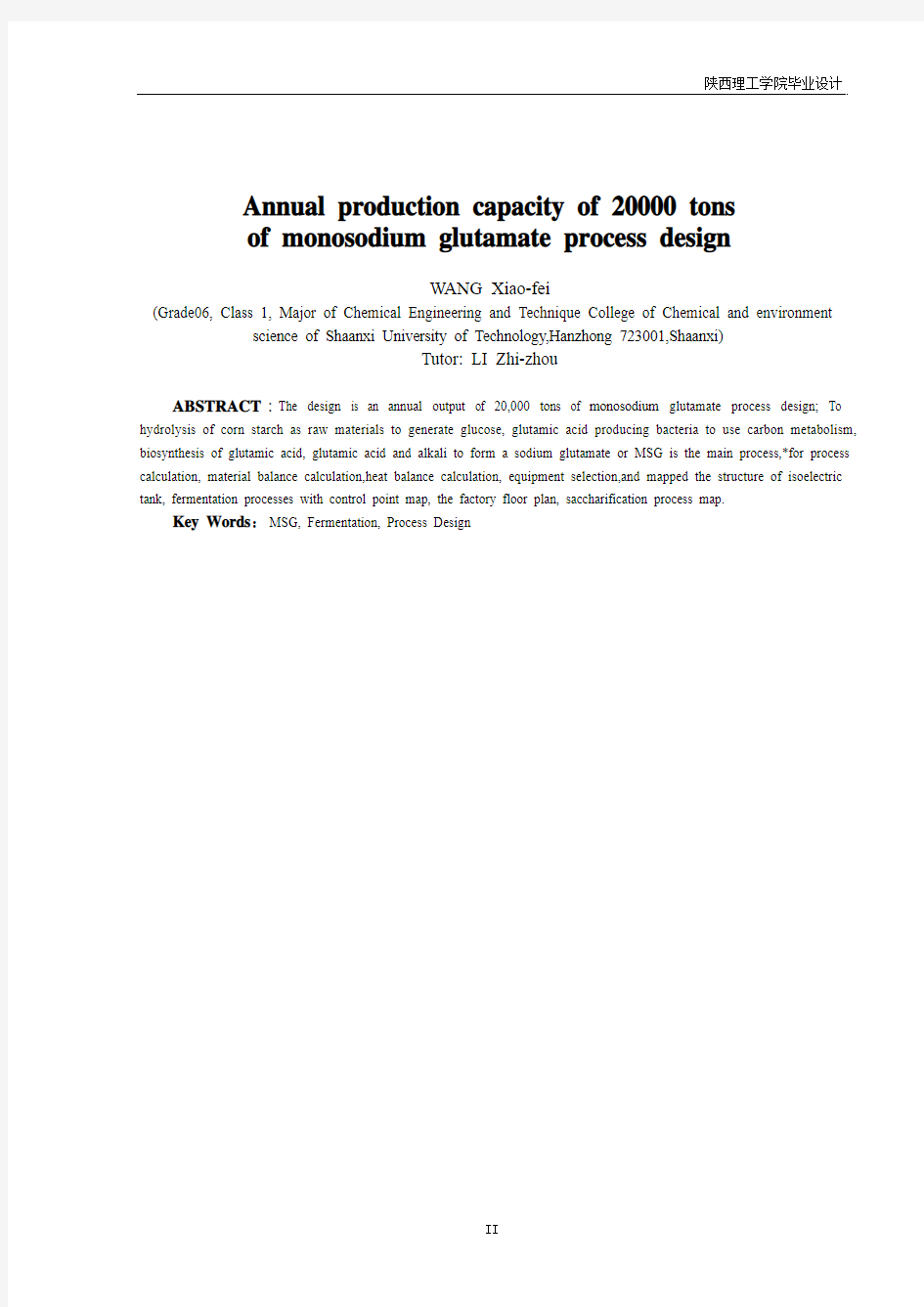
年产2万吨味精工艺设计
XXX
(陕西理工学院化学学院化工专业061班,陕西汉中723001)
指导教师:XXX
[摘要]:本设计是年产2万吨味精工艺设计;以玉米淀粉为原料水解生成葡萄糖、利用谷氨酸生产菌进行碳代谢、生物合成谷氨酸、谷氨酸与碱作用生成谷氨酸一钠即味精为主体工艺,进行工艺计算、物料衡算、热量衡算、设备选型,并绘制了等电罐结构图,发酵工序带控制点图,糖化工序图,工厂平面布置图。
[关键词]:味精;发酵;工艺设计
Annual production capacity of 20000 tons
of monosodium glutamate process design
WANG Xiao-fei
(Grade06, Class 1, Major of Chemical Engineering and Technique College of Chemical and environment science of Shaanxi University of Technology,Hanzhong 723001,Shaanxi)
Tutor: LI Zhi-zhou
ABSTRACT:The design is an annual output of 20,000 tons of monosodium glutamate process design; To hydrolysis of corn starch as raw materials to generate glucose, glutamic acid producing bacteria to use carbon metabolism, biosynthesis of glutamic acid, glutamic acid and alkali to form a sodium glutamate or MSG is the main process,*for process calculation, material balance calculation,heat balance calculation, equipment selection,and mapped the structure of isoelectric tank, fermentation processes with control point map, the factory floor plan, saccharification process map.
Key Words:MSG, Fermentation, Process Design
目录
摘要 ........................................................................................................... I ABSTRACT ................................................................................................ II 1.总论 (1)
1.1项目依据 (1)
1.1.1课题背景及味精概述 (1)
1.1.2味精产业概况 (1)
1.1.3味精需求现状 (2)
1.2设计原则 (2)
1.3设计任务 (3)
1.4厂制概况 (3)
1.4.1工厂组织 (3)
1.4.2工作制度 (3)
1.4.3人员配备 (3)
1.5厂址选择 (3)
1.5.1 建厂依据 (3)
1.5.2 指导方针 (3)
1.5.3 选厂经过 (4)
1.6环境保护剂废物处理 (4)
2.工艺设计 (6)
2.1工艺流程设计 (6)
2.1.1 工艺流程设计的重要性 (6)
2.1.2 工艺流程设计的原则 (6)
2.1.3 工艺流程设计 (6)
2.2玉米制备淀粉工艺 (7)
2.2.1湿法玉米淀粉制备工艺过程 (7)
2.2.2湿法玉米淀粉生产的主要设备 (8)
2.2.3玉米淀粉生产工艺技术指标 (8)
2.3淀粉糖化工艺 (9)
2.3.1概述 (9)
2.3.2一次喷射双酶法制糖工艺流程 (9)
2.3.3一次喷射双酶法制糖工艺控制要点 (9)
2.4发酵工艺 (10)
2.5谷氨酸提取工艺 (10)
2.5.1概述 (10)
2.5.2谷氨酸发酵液的特征和主要成分 (10)
2.5.3等电点—离子交换法提取谷氨酸 (11)
2.6谷氨酸制造味精工艺 (12)
3.物料衡算 (13)
3.1生产过程的总物料衡算 (13)
3.1.2计算指标(以淀粉质为原料) (13)
3.1.3物料衡算 (13)
3.1.4总物料衡算结果 (14)
3.2制糖工序的物料衡算 (14)
3.3发酵工序的物料衡算 (15)
3.4谷氨酸提取车间物料衡算 (17)
3.4.1中和等电工序 (17)
3.4.2离交工序 (18)
3.4.3提取车间物料衡算验算 (18)
3.5精制车间物料衡算 (19)
3.5.1中和脱色工序物料衡算 (19)
3.5.2精制(结晶)工序物料衡算 (20)
3.6精制生产过程物料衡算图 (20)
4.热量衡算 (23)
4.1液化工序热量衡算 (23)
4.1.1液化加热用蒸汽量 (23)
4.1.2液化液冷却用水量 (23)
4.2糖化工序热平衡说明 (23)
4.3连续灭菌和发酵工序热量衡算 (23)
4.3.1培养液连续灭菌用蒸汽量 (23)
4.3.2培养液冷却用水量 (24)
4.3.3发酵罐空罐灭菌用蒸汽量 (24)
4.3.4发酵过程产生的热量及冷却用水量 (25)
4.4谷氨酸提取工序冷量衡算 (25)
4.5谷氨酸钠溶液浓缩结晶过程的热量衡算 (25)
4.5.1热平衡与计算蒸汽加热量 (26)
4.5.2二次蒸汽冷凝所消耗循环冷却水量 (26)
4.6干燥过程的热量衡算 (27)
4.7溴化锂制冷机所用蒸汽量 (28)
4.8生产过程耗用蒸汽衡算汇总 (28)
5.水平衡 (29)
5.1糖化工序用水量 (29)
5.2发酵配料及培养基灭菌后冷却用水量 (29)
5.3发酵过程冷却用水量 (29)
5.4谷氨酸提取工序冷却用水量 (29)
5.5中和脱色工序用水量 (29)
5.6精制工序用水量 (29)
5.7动力工序用水量 (29)
5.8用水量汇总 (29)
6.主要设备选型及计算 (31)
6.1.1发酵罐 (31)
6.1.2种子罐 (33)
6.1.3离子交换柱 (34)
6.1.4尿素罐 (36)
6.1.5等电罐 (36)
6.1.6油罐 (37)
6.2泵的选择 (37)
6.3空气系统选择 (37)
6.3.1流程选择的原则 (37)
6.3.2空气净化设备流程 (37)
6.3.3具体设备要求 (37)
6.4容器、槽的选择 (39)
6.5其他设备的选择 (39)
6.6辅助设备选择 (40)
7.全厂总平面设计 ..................................................... 错误!未定义书签。
7.1总平面设计任务和步骤 (44)
7.1.1总平面设计任务 (44)
7.1.2工厂组织 (44)
7.2总平面布置评述 (44)
7.3工厂布置原则 (45)
7.4竖向布置原则 (45)
7.5设备布置的原则 (46)
7.6厂区管线布置原则 (46)
8.设计结果 (47)
8.1设计成果 (47)
8.2关键设备一览图 (47)
总结 (48)
致谢 (49)
参考文献 (50)
附录 (51)
1.总论
1.1项目依据
1.1.1课题背景及味精概述
(1)味精生产方法概述
味精生产方法一般有水解法、合成法、从甜菜废糖蜜中提取及发酵法等。
最早的生产方法是蛋白质水解法。此方法要耗用大量的含蛋白质的粮食,而且原料来源少,价格高,收率较低,生产周期长,浓盐酸耗最大,设备腐蚀严重,劳动强度大,劳动条件差,成本高;但质量好,收率较稳定。甜菜废糖蜜系综合利用,但原料来源有地区局限性,同时设备庞大,生产工艺复杂,产品是L—型。目前绝大部分生产方法已用发酵法代替。
合成法优点不用粮食,采用石油废气,但生产过程中需用高压(200大气压)、高温(120℃以上)、有毒(氯氰酸)、易燃(溶剂)。设备投资大(比发酵法高1倍以上),生产工艺复杂、危险等。半成品消旋谷氨酸还要进行分割,年产量少于5000t者不经济。故生产上很少使用。
当今味精生产的主要方法为发酵法,此方法不仅原料来源广阔,可利用各种淀粉或野生物淀粉、甘蔗、糖蜜、甜菜糖蜜、石油化工产品醋酸、乙醇等。而且设备一般,腐蚀性低,劳动强度小,可自动化、连续化生产、收率高、成本比水解法低30~50%等优点。因此,发酵法是目前生产味精的主要方法[1]。
(2)味精的性质:
味精即谷氨酸钠,是L-谷氨酸的单钠盐,又称味素,学名α-氨基戊二酸钠,含有一分子的结晶水,分子式为NaC5H8O4N·H2O,分子量为187.13。
分子结构如下:
味精和谷氨酸都有旋光性,有D-型及L-型二种光学异构体。当D-型与L-型相等时,发生消旋,称为DL-型。在动植物体中存在的谷氨酸都是L-型,用蛋白质水解法及发酵法生产的谷氨酸钠也都是L-型,而用化学合成法生产的谷氨酸为DL-型。
味精的主要物理性质:
(1)性状味精是无色至白色的柱状晶体或白色的结晶性粉末;
(2)结晶系斜方晶系,柱状八面体。轴角α=β=γ=90o,轴长a≠b≠c;
(3)密度粒子相对密度1.635,视相对密度0.80~0.83;
(4)溶解度及其他不溶于酒精、乙醚及丙酮等有机溶剂,易溶干水,比重为1.65;熔点为195℃;在120℃以上逐渐失去分子中的结晶水;pH为7.0。
味精的主要化学性质是:
(1)与酸作用,生成谷氨酸或谷氨酸盐酸盐;
(2)与碱作用,生成谷氨酸二钠盐,加酸后又生成单钠盐;
(3)长时间受热会引起分子内失去水生成焦谷氨酸钠;
(4)水溶液中解离。
1.1.2味精产业概况
我国味精生产开始于1923年,至今已有80多年历史。它经历了创建、转换和发展三个阶段。
上海天厨味精厂最先用水解法生产味精。之后,1932年沈阳又开始用脱脂豆粕水解生产味精。但在解放前,我国味精工业像其它工业一样,与国外技术与世隔绝,生产长期落后,濒临破产的状态。直到1939年我国味精厂才有沈阳、天津和青岛味精厂三大味精生产家。这些生产家大都以豆粕为原料,工艺采用水解法生产。以上为创建期。
新中国成立后,味精生产如雨后春笋般的成长。1958年有关科研单位、院校和企业合作,进行发酵法制谷氨酸的试验研究工作。1964年上海味精厂和有关科学研究单位协作,开始采用发酵法生
产味精。特别是经过无产阶级文化大革命,味精生产迅速发展。目前全国大部分省(市)都有了味精生产,1967年全国味精产量为1965年产量的5倍。在发酵法生产得到了普遍应用后,在生产用菌种、原材料、发酵工艺、回收提取、以及设备和自动控制等技术方面也都有不少改进和发展。但发展是很不平衡的,距离先进水平还有差距,需要不断地努力。1970~1980年期间,北京等厂用醋酸原料生产味精,后因设备腐蚀等原因而停产;福建、广东、广西等省部分企业用甘蔗糖蜜生产味精。此阶段为转换阶段。
我国味精生产自80年代开始进入高速发展阶段。从量变发展到质变,产量上获得历史性突破。1992年成为世界味精生产的第一大国,产量达34万t。2000年我国味精年产量将近100万t,占世界味精年产量的47﹪。我国味精产量不断增加的同时,生产技术水平也不断得到提高。据了解,现今我国味精生产的各项技术指标比90年代初有了较大的进步。味精生产企业实现了集约化经营。90年代初,我国味精生产企业130家,年产量约30万t。目前仅50家生产企业的年产量就达100多万t。河北梅花味精集团年产味精40万t。河南莲花味精集团有限公司一家企业年产量就达30万t,堪与国际上同类大企业比肩。
1910年日本味之素公司用水解法生产谷氨酸。1936年美国从甜菜废液(司蒂芬废液)中提取谷氨酸。日本1956年开始用糖质原料发酵法,1962年用合成法,1966年以醋酸为原料用发酵法生产味精。1977年,又改用糖蜜为原料发酵法生产谷氨酸。国外味精生产主要分布在日本、东南亚和非洲等地区,其它欧美国家和地区的产量很小,大多依靠外部供给。
1.1.3味精需求现状
1987年,联合国粮农组织和世界卫生组织宣布,取消对味精的食用限量,作为一种增加食品风味的调味料。味精不再需要评价其每日容许摄入量[2]。消费者可以放心食用味精。
(1)国际味精需求市场分析
在国际市场上,味精的消费主要集中在日本、东南亚、非洲等地,最近几年欧洲和南美洲等地的味精需求量也开始出现增长势头,国际市场对味精的需求也不断增加,味精行业的发展平稳向上。日本、韩国、东南亚等国家和地区人均味精消费较高,如日本2007年人均年消费味精1.53kg,香港为1.3kg,而我国仅为0.96kg。
(2)国内味精需求市场的分析
随着我国人民生活水平的提高和膳食结构的改变,以及对味精产品认识的普遍提高,味精的需求量不断增大,人均消费水平逐年提高,华东、中南、东南、西南、华南地区人均年消费量已上升为1.0kg左右。就国内市场来讲,味精的主要消费群体在城市,城市居民年消费量占到总产量的70%以上,农村市场的发展潜力巨大。随着农村人口收入的增加,农民生活水平逐步提高。膳食结构进一步改善,农村市场对味精的需求量会逐步增加。
(3)西北地区味精需求市场的分析
过去由于西北地区人们的饮食习惯,人均年消费水平不足0.1kg克,,随着西部地区经济的不断发展,东西部经济、文化的交流,饮食结构日趋多样化,人均年消费也已增长到现在的人均0.5kg 克左右。
总的来看,我国及全世界的味精消费量都在逐年增加。味精行业在食品工业中将占据重要的地位。
1.2设计原则
(1)遵守国家法则,贯彻党的基本建设方针,实事求是,因地制宜;
(2)合理利用国家资源和财产,最大限度的发挥硬件设施的内在潜力,节约土地,减少投资,降低成本,以获得最大的经济效益;
(3)采用成熟的,先进的工艺流程、设备,学习先进的生产技术,努力实现自动化、现代化,提高产品的科技含量,提高产品的国际竞争力;
(4)轻化工业产品批量小、品种多的特点,努力做到“一钱多用,一钱多能”,是本厂的宗旨;
尽可能创造出良好的劳动环境,以利于劳动工人的身心健康。
1.3设计任务
味精厂的设计范围:生产工艺及装置的设计;各车间、辅助生产车间、生活服务、办公设施等的建筑、结构设计;总平面设计;三废治理设计;热能动力、供电照明、给排水、采暖通风等设计。其中,味精生产的工艺流程布置及设计,主要设备的计算和选型为本次设计的主要内容。此外,还根据实际要求画出等电罐结构图,发酵工序带控制点图,工厂总平面布置图,糖化工序图等。
1.4厂制概况
1.4.1工厂组织
本厂职工按工作性质分为:生产性人员和非生产性人员。生产人员占全长职工的70%左右,非生产人员占全厂人员的30%左右。在非生产性人员中:50%为科研人员(兼职行政人员),6%为保安人员,10%为勤杂人员,其他的为34%。
1.4.2工作制度
法定假日和星期假日采用轮换倒班制度,连续工作制:
工作日=365-设备维修日
=365-45
=320(天)
1.4.3人员配备
根据工厂不同部门的工作性质要求,本工厂的人员配置见表1.1。
表1.1 劳动定员表
序号部门管理
人员
技术
人员
生产
人员
辅助生
产人员
服务
人员
合计
比例
/%
1 主要生产部门10 15 600 ——625 69.4
2 辅助生产部门
3 3 —140 —146 16.2
3 管理及服务部门50 55 ——2
4 130 14.4
3.1 管理部门50 55 —— 3 108 12
3.2 服务部门————21 22 2.4
4 合计63 73 600 140 24 900 —
5 各类人员所占比例/% 7 8.1 66.7 15.5 2.7 —100
1.5厂址选择
1.5.1 建厂依据
工厂选址和生产规模决策是企业长期战略决策的重要内容,它关系到企业的近期投资和未来的生产运作成本。根据各行业发展的需求,以及国际市场的需求,经省政府及市政府有关部门的批准,新建厂的厂址拟选在陕西省榆林市。新建厂的主要原料,经上级主管部门的批准,直接榆林市及其附近省市取原料,节省经费,并且能够做到产品统一规格。
1.5.2 指导方针
(1)遵守国家的政策规定;
(2)符合城市规划和工业布局;
(3)利于生产,便于生活;
(4)对环境不会造成威胁;
(5)合理利用资源;
(6)带动当地经济发展;
(7)节约投资,留有余地。
1.5.3 选厂经过
厂址选择是味精厂建设中的一个重要环节[3],是一项政策性、技术性很强,牵涉范围很广,关系到工厂投产后生存与发展的综合性工作。因此新建味精厂必须重视厂址选择工作。
选择味精厂厂址的基本原则:
(1)厂址选择必须符合国家工业布局和城市规划的要求,遵守国家有关法律、法规。所选厂址要满足生产需要,尽量不占或少占良田,节约用地,但要留有发展余地。
(2)厂址应靠近水量充足、水质良好的水源地。水质应符合《生活饮用水卫生标准》和味精生产的要求。
(3)厂址应尽可能靠近热电供应地,要有可靠的供应保证。对于中小型味精厂应尽可能利用社会热电站的蒸汽热电站,以减少新建工厂在热力方面的投资,对于较大型味精厂应考虑热电联产,建自备热电站,合理利用能源,降低生产成本。
(4)厂址周围应有良好的卫生环境,周边空气质量良好,无污染源,以保证味精生产,尤其是发酵工序对空气的质量要求。应远离居民密集区、文物风景区、机场以及散发大量粉尘和有害空气的工厂、仓储、堆场等区域。如不能远离有严重空气污染区时,则应位于其最大频率风向上风侧,或全年最小频率风向的下风侧。
(5)厂址应具满足建设工程需要的过程地质条件和水文地质条件。建厂厂址的基地应该有较高的承载力和稳定性,应避免在地震断层地区基本烈度为9度以上地区,易受洪水、泥石流、滑坡、土崩等危害的地区建厂。
(6)厂址应有便利的交通运输条件,味精生产用原料、燃料及成品等物质吞吐量较大,应尽可能靠近原有的交通运输线路,如铁路、公路、码头,以减少建设投资。
(7)厂址宜靠近原料、燃料基地及产品主要销售地区,尽量缩短运距。并靠近储运、机修、公用工程和生活设施等方面有良好基础和协作条件的地区。
(8)厂址附近应有生产污水、生活污水、废渣等排放的可靠排除地,并应保证新建工厂不给当地环境造成不良影响和危害。
1.6 环境保护剂废物处理
现代工业的发展虽然创造了巨大的财富,使人类的环境又为它付出了巨大的代价。随着世界特别是我国环境的明显恶化,国民的环境保护意识逐步提高,人类从严酷的事实中提高了对人类活动与环境之间关系的认识。为了防止环境质量的进一步恶化,为了我们自己,为了我们的子孙后代,必须保护环境。
味精工厂主要产生的“三废”及处理措施[4-5]:
(1)废气
现有味精企业除少数由热电站供给蒸汽外,多数企业自备锅炉,其烟尘排放基本上可以达标。主要通过加高烟囱高度和采用旋风除尘器、电除尘和布袋除尘等干式除尘和麻石水膜湿式除尘的办法来解决。
生产中使用的工艺过程中产生HCl、H2S、NH3、H2SO3等气体通过使设备密闭、脱硫措施及使用液体石蜡与空气隔离等措施防止其逸出。
(2)废渣
味精企业的废渣即锅炉灰渣和回收的粉煤灰随生产运出厂外,其炉渣和粉煤灰可用于铺路和作建筑保温材料。有些工厂的大米渣、糖渣售出作饲料,灰渣可回收利用。
(3)噪声
味精生产主要噪声来源于发酵罐、空压机、鼓风机、引风机以及设有大功率的搅拌设备等,以发酵罐的噪声最大。100 m3发酵罐的噪声达到70~80Db。
(4)废水
味精企业的废水可分为高低浓度的有机废水。其中,刷罐水、生活污水、蒸发冷水等是低浓度废水。味精生产的主要污染物为高浓度有机废水,为谷氨酸母液。20世纪80年代后,各厂采取多种措施解决污染问题,已取得诸如废液生产复混合肥料、饲料酵母,通过浓缩—喷浆—干燥—造粒-
包装,变废为宝,厌氧、曝气处理废水等成果。但就全国味精行业来看,问题相当严重。进入21世纪,很多味精企业已采取浓缩制肥的办法,使高浓度废水得到彻底根治,但还有部分企业没有解决。此外每年还向环境排出大约400万吨的低浓度废水,可见排放的污染物负载量是十分惊人的。在国家环保法公布和味精工业污染物排放标准公布之后,企业今后通过清洁生产地管理和综合治理,坚决实行节能排放,坚决使废水达到排放标准,改善环境,促进生产。味精行业对废水治理展开较早并做了大量研发工作,提出不少治理方案。其中主要有:高浓度废液浓缩制生物发酵肥法;废液制取饲料酵母(SCP)法;厌氧—好氧二段生化法;生物转盘法;氧化塘(沟)法等。很多方法已经在生产中应用并取得很好的效果。对污染源、废水、废气、废渣、噪音粉尘烟等的具体防止和处理方法主要依据《环境保护法》及相应的可行性研究、环保报告和初审意见来确定。
2.工艺设计
2.1工艺流程设计
2.1.1 工艺流程设计的重要性
(1)生产工艺流程设计是工艺设计的基础,所涉及面很广,是味精工厂设计的核心和重要部分。在设计中必须做到技术先进、经济合理、成熟可靠;在保证产品质量条件下,力求工艺流程简化,生产管理方便;把各个生产过程按一定顺序、要求组合起来,编制成工艺流程图等来完成工艺流程设计。因为工艺流程设计的质量直接决定车间的生产产品质量、生产能力、操作条件、安全生产、三废治理、经济效益等一系列根本性问题。
(2)工艺流程设计图是物料衡算、设备选型的基础。从其他角度来说,工艺流程设计是定性分析工作阶段,物料衡算是定量计算阶段。一般来说,先定性后定量,所以,工艺流程设计是物料衡算的前提和基础。
2.1.2 工艺流程设计的原则
(1)先进性
工艺流程的先进性从两个方面考虑:一方面是技术的先进;一方面是经济上的合理。两方面同等重要,缺一不可。
(2)可靠性
所设计的工艺流程必须可靠即经过实验室、工业小试、中试,证明技术是成熟的,生产安全可靠,才可以设计选用。
(3)结合国情,因地制宜
工艺流程的选择从技术角度来说,应尽量采用新工艺、新技术,单从具体情况考虑,并不必选择国外的先进的技术。因为国外的技术往往价格较高,技术保密性强,实用价值不大。所以,结合实际,选择自己易于掌握和改进的技术要方便、实用。
2.1.3 工艺流程设计
味精工艺流程图2.1如下。
图2.1 味精生产工艺流程图
2.2玉米制备淀粉工艺
2.2.1湿法玉米淀粉制备工艺过程
玉米在我国广泛种植,产量高,与其他淀粉原料相比,具有易于储存、工厂可以全年生产、不受季节限制、淀粉质量高等优点。因此玉米成为我国制造淀粉最重要的原料,玉米淀粉占我国淀粉总产量的90%以上,卫生发酵行业需要的糖源大都来自玉米。
玉米淀粉的制备分干法和湿法两种[6]。所谓干法是指靠磨碎筛分风选的方法,分出胚芽和纤维,而得到低脂肪的玉米粉。湿法是指“一浸二磨三分”,即将玉米温水浸泡、粗磨、细磨,分离胚芽、纤维素和蛋白质,而得到高纯度的淀粉。一般为获得高纯度的玉米淀粉都采用封闭式湿法工艺进行。封闭式流程只在最后的淀粉洗涤时用新水,其他用水工序都用工艺水,因此新水用量少,干物质损失少,污染大为减轻。本设计采用湿法制备淀粉。
湿法玉米淀粉生产工艺流程如图3.1所示。
图2.2 湿法玉米淀粉生产工艺流程图
1.玉米储存
玉米的储存一般采取立筒仓或平仓。储存玉米应备有相应的输送设备,装设测温仪表,同时注意通风、发热、发霉、虫害、防爆等问题,保证玉米质量。
2.玉米净化
玉米粒中混有砂石、铁片、木片、尘土等杂物,在加工之前要先将其去除,常采用带有吸尘(风力)的振动筛、比重除石器、除尘器等去除大小杂质,电磁分离机去除铁片,然后将玉米采用水力输送到浸泡罐,同时将灰分除去。水力输送的速度为0.9~1.2m/s,玉米和输送水的比例为1:(2.5~3.0),水温35~40℃。
3.玉米浸泡
玉米浸泡时亚硫酸浓度为0.15%~0.35%,浸泡温度48~50℃,浸泡时间40~50h。浸泡过程要严格控制亚硫酸浓度,过高过低对玉米浸泡都不利。
4.破碎与胚芽分离
浸泡的玉米经齿轮磨破碎后,用泵送至一次旋液分离器,底流物经曲筛虑去浆料,筛上物进入二道齿轮磨。经二次破碎的浆料泵入二次旋液分离器,分离出的浆料经二次曲筛得到粗淀粉乳与一次曲筛分离出的淀粉乳混合。两次旋液分离器分离的胚芽料液进入胚芽分离器分离出胚芽,得到的稀浆料进入细磨工序。进入一次和二次旋液分离器的淀粉悬乳液浓度为7~9°Bé,压力为0.45~0.55MPa,胚芽分离过程的物料温度不低于35℃。
5.细磨
二次旋流分离出的筛上物进入冲击磨(针磨)进行细磨,最大限度地使与纤维素联结的淀粉分
离出来,细磨后的浆料进入纤维素槽洗涤。
6.纤维分离
细磨后的浆料与洗涤纤维素水依次泵入六级压力曲筛进行逆流洗涤,纤维素从最后一级曲筛筛面排出,第一级曲筛筛下物为粗淀粉乳进入淀粉分离工序。细磨后的浆料浓度为5~7°Bé,压力曲筛进料压力为0.25~0.30MPa,洗涤用水温度45℃,可溶物不超过1.5%,纤维素洗涤用水量(210~230L)/100kg干玉米。
7.淀粉蛋白质分离
粗淀粉乳经除砂器、回转过滤器,进入分离麸质和淀粉的主离心机,第一级旋流分离器顶流的澄清液作为主离心机的洗涤水。顶流分离出麸质水,浓度为1%~2%,送浓缩分离机,底流为淀粉乳,浓度为19~20°Bé,送十二级旋流分离器进行逆流洗涤。洗涤用新鲜水,水温为40℃。经十二级旋流分离器洗涤后的淀粉含水60%,蛋白质含量低于0.35%。
8.淀粉的脱水干燥
洗涤后的淀粉乳可以用来直接制备淀粉糖,也可以经自动刮刀离心机等进行脱水,得到含水34%~38%的湿淀粉,再用气流干燥机干燥后得到成品淀粉。
2.2.2湿法玉米淀粉生产的主要设备
湿法生产玉米淀粉的主要设备如表2.1所示。
表2.1 湿法生产玉米淀粉的主要设备
工序主要设备
玉米浸泡浸泡罐
玉米破碎凸齿磨
胚芽分离旋流分离器
胚芽洗涤曲筛
细磨针磨
纤维分离压力曲筛货锥型离心筛
淀粉与蛋白质分离碟片分离机
淀粉洗涤12级旋流分离器
麸质浓缩碟片分离机
麸质回收转股式真空吸虑机或板框式压滤机
淀粉脱水卧式刮刀离心机
淀粉干燥一级负压或正压二级气流干燥机
湿纤维胚芽干燥管束干燥机
麸质干燥气流干燥机或管束干燥机
2.2.3玉米淀粉生产工艺技术指标
(1)计算依据
a.年产2万吨味精需商品淀粉3万t,以年产商品淀粉(含水)3万t为基准进行计算。
b.玉米质量含淀粉≥70%,碎玉米及杂质≤3%,蛋白质8%~11%,脂肪4%~6%,含水14%。
(2)主副产品产量。
a.年产商品淀粉(含水14%):3万t。
b.副产品(年产量)。
蛋白粉(含蛋白质60%,含水10%):2680t;
麸质饲料(含蛋白质21%,含水12%):7430t;
麸质饲料由玉米浆2000t+玉米纤维4000t+胚芽油饼1430t组成;
玉米米油:1248t。
c.原料
年耗用原料玉米(含水14%):46722t;
年耗用净化玉米(含水14%):45357t;
年耗用干玉米:39007t。
(3)生产及辅助用水
生产用水比列:
玉米:输送水=1:3;
亚硫酸:玉米=(1.20~1.25):1;
胚芽洗涤水:玉米=1.2:1;
纤维洗涤水:玉米=2.0:1;
淀粉洗涤水(软水):玉米(干物)=2.5:1。
由此可以看出,如全部用新水生产1t淀粉需用水10t以上,耗水量很大,年产1万t淀粉,用水十几万t,排放污水也有近10万t,环保压力很大。
2.3淀粉糖化工艺
2.3.1概述
将淀粉质原料(如玉米、大米、小麦、木薯等淀粉)转化为葡萄糖的过程称作糖化工艺,其糖化液称淀粉糖或淀粉水解糖。淀粉是由葡萄糖单元通过α-1,4和α-1,6糖苷键连接而成的多糖,α-1,4和α-1,6糖苷键在酸或酶的作用下会断裂,形成葡萄糖单元。淀粉糖化按使用催化剂的不同可以分为酸解法、酶酸法和双酶法三种。双酶法生产的糖液产品质量高,杂质含量低而具有较大的优势,在味精行业已广泛应用,酸法和酶酸法已被企业淘汰。双酶法制糖工艺可根据升温方式的不同分为升温液化法、喷射液化法。喷射液化法又依所用加热设备的不同可分为一次喷射液化法和二次喷射液化法。一次喷射液化法由于能耗低,设备少,糖液质量好而获得了广泛的应用。本设计采用一次喷射双酶法制糖工艺。
2.3.2一次喷射双酶法制糖工艺流程
一次喷射双酶法制糖工艺流程如下:
酶、调pH Na2CO3
↓↓淀粉乳→调浆→喷射液化→高温维持→闪蒸→层流液化→降温→糖化→升温灭酶→过滤→糖液↑↓
调pH(盐酸或石灰水/ Na2CO3)、酶糖渣→饲料
2.3.3一次喷射双酶法制糖工艺控制要点
调浆配料:根据需要,将淀粉乳调节15~20°Bé(加自来水调节),用盐酸或石灰水/ Na2CO3调pH6.0~6.2。加入适量耐高温α-淀粉酶(20000标准活力/mL),每吨干淀粉0.5~0.6L。
糊化:将调好的淀粉乳,用泵送入水热器,利用水热器加热至108~110℃(玉米淀粉在100~160℃高温蒸煮下,才能正真溶解),然后进入高温维持罐(维持罐压力0.08~0.10MPa),通过压力维持把料液送入闪蒸罐,达到汽液分离,迅速降温至98~99℃以下。通过高温维持,温度混合均匀,淀粉颗粒充分润胀,初步水解淀粉,降低料液的黏度,达到理想的糊化效果。同时通过减压打开淀粉分子的网状结构,温度降至酶的最佳温度反应区间,以利于酶的进一步作用。
液化:料液经闪蒸后温度降至98~99℃,进入层流罐保温液化100~120min,液化结束后通过换热器降温至60~62℃,进入糖化罐。
糖化:液化液加盐酸/H2SO4调pH4.2~4.4,糖化温度(60±1)℃,加入糖化酶进行糖化。高效糖化酶的加量按1.0~1.5kg/t干基物计(以10万单位/mL为例),糖化时间36~40h,糖化结束用无水乙醇滴定检查无白色为终点。用稀碱水调节蛋白质等电点至pH4.8~5.0,然后升温至82~85℃灭酶,维持15min后降温至65℃。
过滤:灭酶后的糖化液通过动力输送到高位槽或直接上板框压滤机压滤,滤去蛋白质、糖渣,糖液透光率达到90%以上(用721分光光度计测),糖液打入贮糖罐(保温不低于60℃)供发酵用。
过滤压力先低后高,最高不超过0.25MPa。
2.4发酵工艺
以淀粉、大米水解糖为原料。利用发酵法生产谷氨酸的基本要素是采用优良的菌株和控制合适的环境条件。要使谷氨酸稳定与高产,必须认识与掌握谷氨酸生产菌活动的规律,根据混种性能和发酵特点,用发酵条件来控制过程中化学及生物反应的方向和速度[7-8]。
微生物本身有多种代谢途径,当条件及环境因素发生改变时。必然影响控制代谢有关的酶的合成及其活性,从而产生不同的发酵产物。
谷氨酸发酵过程可分为三个阶段,长菌阶段,长菌型细胞向产菌型细胞的转移阶段与产酸阶段。
发酵条件的控制一般包括:发酵过程温度的控制,pH控制,种龄和种量控制,泡沫控制,排气CO2控制等。对温度的控制,谷氨酸产菌的最适温度为30~34℃,谷氨酸生产菌产生谷氨酸的最适温度是35~37℃,谷氨酸发酵在不同阶段的要求不同,需要分别加以控制。在正常情况下,为了保证足够的氮源,满足谷氨酸合成的需要,发酵前期控制pH为7.2左右,中期7.0~7.2,后期6.9~7.0,在将近放罐时,为了后续工段提起谷氨酸,pH6.5~6.8为好。对于种龄来说,一般一级种子种龄9~12h,二级种子种龄为7~8h,而种量在10%左右。在谷氨酸发酵中,由于通气搅拌与菌体代谢产生的CO2而使培养液产生大量的泡沫,消除泡沫的方法可以是物理消泡,机械消泡和化学消泡等方法。对于CO2一般为10%左右,发酵开始4~5h,排气中CO2迅速上升至10%以上,加大通风量,以保持在10%,在发酵中期至后期通风需下降,才能保持在10%左右。
发酵工序:过滤的滤液冷却到32℃,进入发酵罐发酵,用冷却水调温,每隔12小时升温1~2℃,当发酵时间接近34h时,温度升至37℃。加水使糖化液浓度为14%,发酵时间为34h,发酵菌种的产酸量与葡萄糖量之比为50%。发酵完的料液进行离心分离后进入谷氨酸提取工序。这一工序中包括传热,离心分离。
2.5谷氨酸提取工艺
2.5.1概述
从发酵液中提取谷氨酸必须要了解谷氨酸理化特性和发酵液的主要成分及特征,以利用它们之间物性差异,达到分离和提纯的目的[9]。从发酵液中分离谷氨酸的方法较多,有等电点法、离子交换法、等电点—离子交换法、连续等点—转晶法、锌盐法、钙盐法、溶剂萃取法、电渗析法等。国内味精生产厂采用的提取工艺主要是:等电点—离交法、连续等电—转晶法、离子交换法等。谷氨酸的分离方法应考虑工艺简单,收率高,产品纯度好,色泽低,操作安全,劳动强度小,设备简单,各种原辅材料价格低廉,来源广易,并应考虑清洁生产等方面的原则。本设计采用等电点—离交法提取工艺。
2.5.2谷氨酸发酵液的特征和主要成分
特征:
(1)正常发酵液放罐时的pH为6.8~7.2,温度在34~36℃,呈乳白色或淡黄色,有谷氨酸发酵的特殊气味。
(2)发酵液中有3%~5%湿菌体,折干菌体为0.8%~1.2%左右。细菌的相对密度为1.04,其大小为(0.7~1.0)μm×(1.0~3.0)μm。菌体内核酸(RNA)含量为7%~8%。
(3)谷氨酸发酵液中的菌体与其他胶体物质均以悬浮状存在,若把菌体在发酵液中视为一种胶体,它是属于S-型亲水性的。
主要成分:
(1)谷氨酸含量10%~13%。
(2)湿菌体含量2%~5%。
(3)乳酸、琥珀酸等有机酸含量<0.8%。
(4)酮酸0.06%左右。
(5)残糖0.5%以下。
(6)铵离子0.6%~0.8%。
(7)核酸和核苷酸类物质、腺嘌呤化合物0.02%~0.05% ,尿嘧啶化合物0.01%~0.03% 。
(8)残留的阴阳离子微量。阴离子:SO42-、Cl-、PO43-;阳离子:K+、Na+、Ca2+等。
(9)有机色素少量。
(10)残留的消泡剂和其他培养基杂质。
(11)少量的谷氨酸类似物质谷氨酰胺、焦谷氨酸等。
(12)其他氨基酸丙氨酸、丝氨酸、亮氨酸等,总量为0.7%~0.9%。
2.5.3等电点—离子交换法提取谷氨酸
原理:该方法是发酵液经等电点法提取谷氨酸以后,再采用单柱或串柱法,将等电点母液通过离子交换树脂进行交换然后用氨水洗脱树脂上的谷氨酸,收集高流分,将其酸化后调下批发酵液等电点,提取谷氨酸。
工艺流程:工艺流程见图2.3。
图2.3 等电点—离子交换法提取谷氨酸工艺流程图
2.6谷氨酸制造味精工艺
从谷氨酸发酵液中提取的谷氨酸,加水溶解,用碳酸钠或氢氧化钠中和,经脱色,除铁、钙、镁等离子,再经蒸发、结晶、分离、干燥、筛选等单元操作,得到高纯度的晶体或粉体味精,经过包装则成为商品味精。
谷氨酸制造味精的生产工艺流程如图2.4所示。
图2.4 谷氨酸制造味精的生产工艺流程图
3.物料衡算
3.1生产过程的总物料衡算
3.1.1生产能力
年生产商品味精(99%)20000t,折算为100%味精为19800t/a。
日生产商品味精(99%):20000/320=62.5(t/d),折算为100%味精为62t/d。
3.1.2计算指标(以淀粉质为原料)
计算指标[10]见表3.1。
表3.1 计算指标
项目指标
淀粉糖化转化率98.5%
发酵产酸率(浓度)11%
发酵对糖转化率60%
培养菌种耗糖为发酵耗糖的 1.5%
谷氨酸提取收率96%
精制收率95%
商品淀粉中淀粉含量86%
发酵周期(含辅助时间)40h
全年工作日320d
3.1.3物料衡算
(1)1000kg纯淀粉理论上产100%MSG量
1000×1.11×81.7%×1.272=1153.5kg
式中81.7%——谷氨酸对糖的理论转化率
1.272——
纯味精相对分子质量
纯谷氨酸相对分子质量
=
184
147
=1.272
(2)1000kg纯淀粉实际产100%MSG量
1000×1.11×98.5%×60%×(100%-1.5%)×96%×95%×1.272=749.6kg (3)1000kg商品淀粉(含量86%的玉米淀粉)产100% MSG量
749.6×86%=644.7 kg
(4)淀粉单耗
①1t100%MSG消耗纯淀粉量
1000
749.6
=1.334t/t
②1t100%MSG实耗商品淀粉量
1000
644.7
=1.5511 t/t
③1t100%MSG理论上消耗纯淀粉量
1000
1153.5
=0.8669 t/t
④1t100%MSG理论上消耗商品淀粉量
0.8669
86%
=1.008 t/t
(5)总收率可按以下两种方法计算
①
)749.6
)
1153.5
100%100%64.98%kg kg ??实际产量(理论产量(=
=
② 98.5%60%98.5%96%95%
100%64.98%81.7%
?????=
(6)淀粉利用率
1.008100%65%1.5511
?=
(7)生产过程总损失
100%-65%=35%
(8)原料及中间品计算
①商品淀粉或淀粉乳用量:日产100%味精62t ,单耗商品淀粉1.5511t ,日耗商品淀粉量
62×1.5511=96.17t/d
相当日耗100%淀粉: 96.17×86%=82.7 t/d 如使用15.2°Bé,含淀粉30.113g/dL 的淀粉乳,日耗量为
82.7/30%=275.67m 3/d (30.113g/dL ≈30%)
②糖化液量:日产纯糖量
96.17×86%×1.11×98.5%=90.43 t/d
只算为30%或34g/dL 的糖液
90.43301.43t 30%=;90.43
265.9734
= m 3
③发酵液量:发酵液中纯谷氨酸量
90.43×60%×(100%-1.5%)=53.44 t/d
折算为谷氨酸11g/dL 的发酵液量
53.44
485.8211
= m 3/d 485.82×1.07=519.83 t/d(1.07为发酵液相对密度)
④提取谷氨酸量:产纯谷氨酸
53.44×96%=51.3 t/d
折算为90%湿谷氨酸量
51.3/90%=57 t/d
3.1.4总物料衡算结果
总物料衡算结果汇总见表3.2。
原料 规格 玉米淀粉原料
生产1t100%MSG
日(耗)产量(t/d )
玉米淀粉/t 86% 1.5511 96.17 糖液/t 30% 4.862 301.43 谷氨酸/t 90% 0.9197 57 味精/t
100%
1.0
62
3.2制糖工序的物料衡算
(1)淀粉浆量及加水量 淀粉加水比例为1:1.8,1000kg 工业淀粉产淀粉浆
1000×(1+1.8)=2800kg
加水量为1800kg 。
(2)粉浆干物质浓度
100086%
100%30.7%2800
??=
(3)液化酶量 使用耐高温α-淀粉酶(液体,20000U/mL ),加酶量10 U/g 干淀粉。1000kg 干淀粉加酶量
1000100010
500mL 0.5L 2000
??==
0.5L 液化酶质量约为0.6kg 。
(4)CaCl 2量 一般加量为干淀粉的0.15%,即1000kg 干淀粉加CaCl 2
1000×0.15%=1.5kg
(5)糖化酶量 一般加糖化酶量为120 U/g 干淀粉,如液体糖化酶为100000 U/mL ,则每1000kg 干淀粉加糖化酶量
10001000120
1200mL 1.2L 100000
??==
1.2L 糖化酶质量约为1.5kg 。
(6)糖液产量
100086% 1.1198.5%
3134kg 30%
???=
30%的糖液相对密度1.1321,相当于1.1321×30%=34g/dL
3134/1.1321=2768L
(7)过滤糖渣量 湿渣(含水70%)10kg ,折干渣量
10×(1-70%)=3kg
(8)生产过程进入的蒸汽冷凝水及洗水量
3134+10-3.6-2800=340.4kg
(9)衡算结果(年产2万吨味精) 根据总物料衡算,按日投入商品淀粉96.17t ,物料衡算汇总见表3.3。
表3.3 制糖车间物料衡算汇总表
项目 物料比例/kg
日投料量/t 项目 物料比例/kg
日产料量/t 商品淀粉 1000 96.17 30%糖液 3134 300.86 配料水 1800 172.8 滤渣 10 0.96 液化酶 0.6 0.0576 CaCl 2 1.5 0.144 糖化酶 1.5 0.144 蒸汽冷凝水及
洗水量
340.4 32.68 累计
3144
301.82
3144
301.82
3.3发酵工序的物料衡算
(1)发酵培养基和用糖量 1000kg 商品淀粉,可产100%糖量
1000×86%×1.11×98.5%=940kg
其中初始发酵定容用糖占53%,即940×53%=498kg (100%糖);流加补量用糖占47%,即940×47%=442kg (100%糖)。初糖用30%的糖液配料:
4981660kg 30%=,即498
1465L 34g/dL
= 初糖配13g/dL ,初定V =
498kg 3831L 13g/dL
=,13g/dL 糖液相对密度1.05,则
3831×1.05=4023kg