铅电解工艺流程图
铅熔炼工艺流程图 (铅系统)

铅烟尘
木质磺酸钙
净 化
干 燥
转 化
压 滤 浇铸锅 滤 液 滤 饼 滤 饼 直线铸锭机 浆 化 氧化渣 1#电铅 阳极泥浆 始极片制备 水 洗 压 滤 铅阴极始极片 洗 水 阳 极 泥 贵金属车间(待定) 阴阳极板排距 铅阳极始极片 污 水 排到污酸污 水车间处理 铅 卷 送铅熔炼系统 薄片机 供锌系统使用
压 滤
吸 收
尾 气
滤 液 排到污水处理站
成品硫酸
外 售
供分厂使用
SO2Байду номын сангаас体
呼伦贝尔驰宏矿业有限公司工艺流程图
离子液吸附
图 名
解 析
铅冶炼工艺流程图
设 计
纯净空气 外 排 纯净的SO 2气体
中国恩菲工程公司
制 图
梁艳辉(技术部)
日 期
审 核
李衍林(技术部)
2012.7.23
铅精矿 硫酸铅渣 石灰石 铅烟尘 铅硫渣 石英石
配 料 套 喷 枪 氧 筒 风 气 风
SO2烟气
水 圆盘制粒
铅精矿 Ausmelt炉氧化阶段熔炼 粗 铅 配 料 氧化后渣 粗 铅 Ausmelt炉还原1阶段熔炼 粗 铅 还原1段后渣 喷枪风 粗 铅 Ausmelt炉还原2阶段熔炼 套筒风 还原2段后渣 铅 松 香 铅锅(火法精炼) 转炉粗铅 合格铅液 铜浮渣 送铜浮渣处理车间 烟 气 终 渣 硫 磺 粗 铅 锌厂运 的冷渣 沉降后渣 粉 煤 锅 焦 粒 电热前床沉降
SO2烟气
块 煤 粉 煤
套 喷 枪 氧 筒 风 气 风
SO2烟气 SO2 烟气
锅炉余热回收
NaOH
残 极
SO2烟气
铅烟尘
静电收尘 烟化炉还原 空 气
铅蓄电池工艺流程

铅蓄电池工艺流程
铅蓄电池工艺流程是指制造铅蓄电池的一系列步骤和工艺操作流程。
下面将详细介绍铅蓄电池的工艺流程。
1. 材料准备:首先需要准备好用于制造铅蓄电池的原材料,主要包括铅板、电极、硫酸等。
2. 板料处理:将铅板进行裁剪、切割等加工处理,使其符合电池制造的要求。
3. 电极制备:将铅板通过一系列的工艺流程进行清洗、酸洗、激活等处理,制备成电池的正负极。
4. 电解液配制:根据设计要求,将硫酸按照一定的比例配制成电解液,以便于后续的工艺操作。
5. 电池组装:将制备好的正负极与隔板等组件进行组装,形成电池的基本结构,并注入电解液。
6. 封装密封:将组装好的电池用专用设备进行密封封装,以确保电池内部不会泄漏。
7. 充电充满:将封装好的电池通过充电设备进行充电,使电池充满电能。
8. 负载测试:将充满电的电池连接到负载设备上,进行负载测试,检测电池的性能和工作状态。
9. 循环充放电:对电池进行循环充放电测试,测试电池的循环寿命和容量。
10. 电池检验:对制造好的电池进行外观检验,检查电池是否存在缺陷,如漏液、变形等。
11. 包装出厂:对检验合格的电池进行包装,贴上标签,然后进行出厂销售。
以上是铅蓄电池工艺流程的基本步骤,每个步骤都需要严格按照标准操作,以确保电池的质量和性能符合要求。
在整个生产过程中,需要注意安全问题,防止发生意外事故,同时也要注意环境保护,尽量减少对环境的污染。
只有通过科学规范的工艺流程,才能制造出高质量的铅蓄电池。
铅生产工艺流程与生产成本概述PPT(34张)

铅精矿 添加物 烟灰、炉渣
配料车间
冶炼车间
LOGO
配料仓
精矿喷嘴
反应塔
用于储存精矿
将精矿均匀喷射
铅精矿燃烧反应
冶炼车间
LOGO
沉淀池
用于沉淀分离
电炉
回收铅
粗铅
用于粗铅精炼
硫化铅精矿
铅生产原料分类
次生氧化铅精矿
再生铅
方铅矿(pbs) 闪锌矿(ZnS) 辉银矿(Ag2S) 黄铁矿(FeS2)
白铅矿(PbCO3) 硫酸铅矿(PbSO4)
铅生产工艺流程与生产成本概述PPT(3 4张)培 训课件 培训讲 义培训 教材工 作汇报 课件PP T
铅生产成本核算
LOGO
铅生产成本=铅精矿+生产能耗+车间管理成本
铅生产工艺流程与生产成本概述PPT(3 4张)培 训课件 培训讲 义培训 教材工 作汇报 课件PP T
铅生产工艺流程与生产成本概述PPT(3 4张)培 训课件 培训讲 义培训 教材工 作汇报 课件PP T
铅生产工艺流程与生产成本概述
LOGO
目
录
1 铅生产工艺流程综述 2 铅生产原料分类 3 铅生产工艺分类 4 铅生产成本核算
LOGO
铅生产工艺流程综述
LOGO
❖铅生产工艺流程综述
▪ 1.铅矿的共生性 ▪ 2.生产工艺的分类
铅矿的共生性
LOGO
铅矿
金、银 铜
铊、锡 铋、锑
共生
锌
车间生产图片
LOGO
车间生产图片
LOGO
车间生产图片
LOGO
车间生产图片
LOGO
车间生产图片
LOGO
车间生产图片
铅湿法精炼工艺培训

关键工序及控制点
三、析铅精炼(成品工序) ①经过电解工序后,析出铅中汗其它小金属非常少,但 其中依然有一定量 的杂质金属,达不到GB/T469-2005 的质量要求,故电解后的析出铅必须进行析铅精炼,进 一步除去析铅中的杂质金属,使电铅达到国标一号铅的 标准。 ②氧化精炼:在此过程中,铅液首先氧化为氧化铅, 杂质金属进一步与氧化铅置换成为氧化物,形成浮渣人 工捞出。 在此过程中,杂质金属不能较好的除去,故必 须进行下一步的碱性精炼。此过程温度在420—450℃) ③碱性精炼:由于氧化精炼过程中不能很好的除去杂 质,用强碱进一步除去铅中的杂质金属,使杂质金属同 强碱、氧化铅进一步反应成杂质金属盐从而形成浮渣与 铅液分离。此过程形成的碱渣不再捞出,在铅液表面形 成保护层从而避免铅液被氧化。
电解 阳极泥送贵冶系统 析出铅 析铅精炼、生产电铅 销售
关键工序确认
从生产工艺流程图中可以看出:影响电铅质量的关键点如下 一、阳极板生产(除铜工序) 二、电解过程(电解工序) 三、析铅精炼(成品工序)
关键工序及控制点 一、除铜工序 1、除铜温度:我厂用熔析除铜方法进行除铜。其原理为铜在铅液
中的溶解度随温度的降低而降低。故在生产中对温度的控制很有必要,在生 产实践中总结,除铜一遍分渣的温度一般控制在420~450℃,二遍除铜的温度 控制在400 ℃以下时较为适宜。
关键工序及控制点
析出铅装锅 氧化精炼 碱性精炼 合格铅液 电铅铸锭 除铜工段、熔炼系统 氧化渣
关键工序及控制点
从成品工序工艺流程图可以看出:本工序的关键点在 于析铅的氧化精炼和碱性精炼两个步骤。 ①氧化精炼主要控制铅液温度和氧化精炼的时间,只有温 度、时间控制好,析铅中少量杂质才能充分的氧化,此时 由于铅的纯度较高,形成大量的氧化铅。 ②氧化精炼并不能将杂质金属除去,达不到GB/T469-2005 中99.994牌号铅,就需要进一步用碱进行除去铅中的杂质 金属,此时也一定控制铅液温度与碱性精炼的时间。 ③析铅的氧化精炼与碱性精炼的过程、温度、时间均详细 的记录“铸锭工原始记录”,包括当班生产的铅锭的批号、 吨数、外观质量等,做到产品的可追溯性。 ④电铅每锅为一个批号,有公司质监站到公司检验,合格 后开具“准销证”,方可销售。
铅电解残极洗刷机组技术方案工艺二补充说明[2012.04.05]v2
![铅电解残极洗刷机组技术方案工艺二补充说明[2012.04.05]v2](https://img.taocdn.com/s3/m/5644abe89b89680203d825e8.png)
铅电解残极洗刷机组 技术方案补充说明(二)云南南星科技开发有限公司二O一二年四月1铅电解残极洗刷机组技术方案工艺二补充说明云南南星科技开发有限公司工艺布局 根据工艺及场地要求:铅残极洗刷机组由传统的直线型布置改为直角型布置,整个机组 成直角布置。
阳极板为竖直悬挂放置,则机组成 90°布置后,阳极板在转运过程中也需要随 之旋转 90°。
工艺流程简介 如图 1 所示,洗刷机前段入口输送机保留 1 槽半残极板的长度(场地限制了长度) ,以保 证设备的连续运行;输送链将残阳极板送入洗刷机洗刷后,由洗刷机上的推板装置将洗刷后 的残阳极板推至前出口输送机,输送机前端可设置挡板,将残阳极板收拢,以储备更多的板 作为缓冲;移载机将残阳极板送至旋转机构后,旋转机构旋转 90°后,下位移载机将残阳极 板送入后出口输送机,后出口输送机由于要穿过原阴极线平台的下方,整机长度比原设计有 所加长(大约 20 米) ,这样也可以储备更多的板。
由于后出口输送机连续运行,由下位移载 机运过来的残阳极板会等距离排开,有利于喷淋,后出口输送机将残阳极板送入喷淋工位, 对整个板面做进一步的全面冲洗,使其清洗更彻底;喷淋完成后紧接着进入吹干工位,以吹 干或减少板面残留的液体。
输送机连续运行,把极板运送到末端出口处;在此设置一台链式 提升机,将极板提升到要求的高度,残极底部高于铅锅的平面,同时使极板交到水平运输机 上; 水平运输机为链式运输机, 每六节链条设置一带钩链节 (节距 110mm) , 把极板按 660mm 的间距均匀的分开,从整个工艺尺寸来看,链式运输机上可存放大约 50 片残极板。
运输机把 极板送入端部的横向输送机,横向输送机再把极板分别送入 1-3 号铅锅。
工艺布置示意图如图 1 所示:1铅电解残极洗刷机组技术方案工艺二补充说明云南南星科技开发有限公司入 口 输 送 机 开 卷 机残 极 洗 刷 机洗刷机 前出口过渡机1#铅锅链式运输机链 式 提 升 机 人 行 通 道移载机 后出口输送机 吹 干 喷 淋 移 载 机 旋转机构2#铅锅阴极线平台立模线平台横 向 输 送 机3#铅锅图1工艺布置示意图总图2铅电解残极洗刷机组技术方案工艺二补充说明云南南星科技开发有限公司工艺匹配的要求 由于工艺上的要求, 洗刷速度和入锅速度要求达到同步, 至少是洗刷速度须小于入锅速度, 这样洗刷后的极板才能尽快消化完成,不产生极板的堆积;由于后出口机的加长,使其具有一 定的储板能力,理论上最小能储备 182 片残极板, (按 20 米的长度,极板间距 110mm 计) ,最 大则达到 700 余片(极板收拢) 。
铅冶炼中的火法冶炼与电解冶炼

精炼
将粗铅进行精炼处理,去除其中的杂质,得 到纯度较高的精铅。
火法冶炼的特点
01
02
03
生产效率高
火法冶炼具有较高的生产 效率,能够大规模地生产 铅金属。
适用范围广
火法冶炼适用于各种类型 的铅矿石,尤其是低品位 和高难度的矿石。
环境污染大
火法冶炼过程中会产生大 量的废气、废水和废渣, 对环境造成较大的污染。
在资源条件方面,如果铅矿品位较高且矿石中杂质较少,电 解法是更好的选择,因为它可以提供更高纯度的产品。相反 ,如果铅矿品位较低或矿石中杂质较多,火法冶炼可能更适 合,因为它能够更有效地从矿石中提取铅。
根据环保要求选择
火法冶炼过程中会产生大量的废气、废水和固体废弃物, 对环境造成较大的污染。相比之下,电解法在生产过程中 产生的废弃物较少,对环境的影响较小。
03
火法与电解法炼铅的比较
资源利用率比较
火法炼铅
火法炼铅工艺利用了铅锌矿中的有价元素,通过高温熔炼得到粗铅,再经过一 系列的精炼过程得到纯铅。由于火法炼铅过程中无法有效分离锌和铅,因此资 源利用率相对较低。
电解冶炼
电解冶炼工艺通过电解方式将阳极泥中的铅氧化物转化为硫酸铅,再通过还原 熔炼得到纯铅。该工艺能够有效地分离锌和铅,提高了资源利用率。
在能源供应紧张或能源价格较高的地区,电解法则可能成为更经济的选择。此外 ,对于一些可再生能源丰富的地区,如水电丰富的地区,使用电解法进行铅冶炼 可以充分利用可再生能源,降低生产成本。
THANKS
感谢观看
环保友好
为降低生产过程中的环境污染,电解法炼铅技术正不断改进,以减 少废水和废气排放,同时加强对有价金属的回收利用。
多元化产品开发
铅生产工艺流程与生产成本概述.pptx
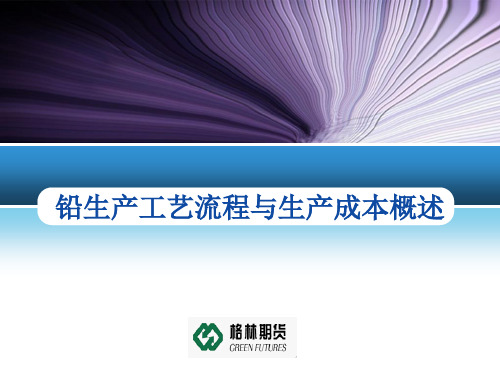
生产能耗(t/标煤--t/粗铅)
0.5 0.35 0.38 0.36 0.49 0.49
铅电解成本
LOGO
铅电解成本核算: 吨铅耗电量为 1040度
铅生产成本核算
LOGO
铅生产成本=铅精矿+生产能耗+车间管理成本
铅冶炼工艺总结
铅冶炼工艺总结 铅冶炼工艺总结
LOGO
料 原
生产工艺
生产成本
铅生产工艺流程与生产成本概述
LOGO
目
录
1 铅生产工艺流程综述 2 铅生产原料分类 3 铅生产工艺分类 4 铅生产成本核算
LOGO
铅生产工艺流程综述
LOGO
❖铅生产工艺流程综述
▪ 1.铅矿的共生性 ▪ 2.生产工艺的分类
铅矿的共生性
LOGO
铅矿
金、银 铜
铊、锡 铋、锑
共生
锌
车间生产图片
LOGO
• 17、一个人如果不到最高峰,他就没有片刻的安宁,他也就不会感到生命的恬静和光荣。下午4时0分3秒下午4时0分16:00:0320.9.27
谢谢观看
铅精矿 添加物 烟灰、炉渣
配料车间
冶炼车间LOGO配 Nhomakorabea仓精矿喷嘴
反应塔
用于储存精矿
将精矿均匀喷射
铅精矿燃烧反应
冶炼车间
LOGO
沉淀池
用于沉淀分离
电炉
回收铅
粗铅
用于粗铅精炼
硫化铅精矿
铅生产原料分类
次生氧化铅精矿
再生铅
方铅矿(pbs) 闪锌矿(ZnS) 辉银矿(Ag2S) 黄铁矿(FeS2)
白铅矿(PbCO3) 硫酸铅矿(PbSO4)
电解铅工艺介绍

书山有路勤为径,学海无涯苦作舟
电解铅工艺介绍
电解铅的冶炼工艺流程
铅冶金是白银生产的最佳载体:一般铅对金银的捕集回收率都在95%以上,因此金银的回收是与铅的生产状况直接相关的。
现在世界上约有80%的原生粗铅是采用传统的烧结一鼓风炉熔炼工艺方法生产的。
传统法技术成熟,较完善可靠,其不足之处在于脱硫造块的烧结过程中,烧结烟气的SO2 浓度较低,硫的回收利用尚有一定难度,鼓风炉熔炼需要较昂贵的冶金焦炭。
为了解决上述问题,冶金工作者进行了炼铅新工艺的研究。
八十年代以来,相继出现了QSL 法、闪速熔炼法、TBRC 转炉顶吹法、基夫赛特汉和艾萨熔炼法等新的炼铅方法。
其中,QSL 法是德国鲁奇公司七十年代开发的直接炼铅新工艺,加拿大、韩国和我国虽然先后购买了此专利建厂,但生产效果不甚理想;闪速熔炼法尚未实现工业化生产;TBRC 法是瑞典波里顿公司所创,但此法作业为间断性的,且炉衬腐蚀严重;基夫赛特法由原苏联有色金属研究院研究成功,现已有多个厂家实现了工业化生产,是一种各项指标先进、技术成熟可靠的炼铅新工艺,但采用该法单位投资大,只有用于较大生产规模的工厂时,才能充分发挥其效益。
艾萨炼铅技术基于由上方插入的赛罗浸没喷枪将氧气喷射入熔体。
产生涡动熔池,让强烈的氧化反应或者还原反应迅速发生。
在第一段,熔炼炉产出的高铅渣经过流槽送还原炉,氧化脱硫所产的烟气经除尘后送制酸系统。
在第二段还原炉中,所产粗铅和弃渣从排放口连续放出,并在传统的前床中分离,所产烟气进行除尘处理后经烟囱排放。
艾萨法熔炼流程。
该工艺流程先进,对原料适应性广、生产规模可大可小,比较灵活、指标先进、SO2 烟气浓度高,可解决生产过程中烟气污染问题;同。
铅电解精炼的工艺控制

铅电解精炼的工艺控制(1)电解液。
以氢氟酸作为原料,加石英粉搅拌制成硅氟酸,质量浓度可达到350g/L,再加黄丹与硅氟酸反应制成硅氟酸铅。
不同工厂对电解液中铅和硅氟酸浓度控制的范围存在一定差异,另有少量从阳极溶解的杂质,如Zn,Fe、Cd、Co、Ni等。
为了改善阴极沉积物的电结晶结构,还要加入少量添加剂,如骨胶、木质素黄酸钠以及P-萘酚等。
一般来说,随电流密度的提高,电解液中铅和酸的浓度也应该相应增大。
(2)电解液温度。
电解液温度受电流密度、气温及散热状况等条件的影响,一般波动在30~45之间。
电解液温度的高低对其比电阻有较大的影响。
温度越高,电解液比电阻越小,但电解液蒸发损失增大,同时硅氟酸分解加快,消耗增加,又具有毒性。
但若温度过低,电解液导电性差,槽电压升高,电耗增大。
(3)电解液的循环。
为了使槽内电解液成分均匀、温度分布均匀,必须使电解液循环流通。
电解液的循环方式与铜电解精炼过程极为相似,一般采取上进液,下出液的循环方式,这样有利于悬浮的阳极泥颗粒沉降。
电解液循环速度决定于电流密度、阳极成分和阳极泥层厚度(4)电流密度。
铅电解精炼的电流密度一般为140~230。
(5)同名极距。
同名极距通常在80~120mm范围内选取。
在电解过程中缩短同极距可提高单槽产量,降低槽电压;但极距过小会使短路增多,电流效率下降。
(6)阴极、阳极使用周期。
为了减少短路和提高电流效率,阴极使用周期不宜过长,一般为2~6d。
采用一次电解,阳极使用周期与阴极使用周期相同。
若采用二次电解,阳极使用周期为阴极使用周期的2倍。
大型工厂多采用二次电解。
中国冶金行业网电解精炼时,阳极金属溶解、阴极析出金属。
然而,由于液相传质迟缓,使得阳极附近溶液中金属离子浓度增大,而阴极附近溶液中金属离子浓度却减小。
按照能斯脱公式,必然导致阳极的极化电位变正、而阴极的极化电位变负,这就是浓差极化产生的根本原因。
电化学极化主要决定于电极过程的本身性质。
铅电解精炼

铅电解精炼铅电解精炼旨在获得纯精度高的工业用铅,并回收伴生的铋和稀贵金属,有时尚回收锡。
我国铅电解的原料大部分为矿产粗铅,其余为再生粗铅和炼锡的副产粗铅。
粗铅在进行电解精炼前,需经火法精炼预先除去粗铅中的铜或锡,并调整锑含量,然后铸成阳极板去电解。
铅电解精炼目前都采用硅氟酸盐电解法,意大利圣.加维诺厂曾一度用氨基磺酸盐电解法,但由于电解液导电性差、电流密度低和槽电压高等缺点,又改用硅氟酸盐电解法。
铅电解精炼工艺本身变化不大,但在机械化程度方面发生了显著的变革,从而提高了劳动生产率,减轻了劳动强度和改善了劳动条件。
1)阳极铸型阳极铸型机组采用液压并采用微机控制。
将过去人工控制铅液量、手工起板、平板和排板等工序变为铅液定容量浇铸、链钩起板、液压平整,再按同极距要求均匀的放置在排板机上,装槽时用桥式起重运输机直接吊入电解槽内。
2)精铅铸锭机组电解阴极铅须熔化或进一步精炼除锡后铸成电铅方能销售。
原先各工序(浇注、打印、起锭和码垛)均为手工作业,精铅铸锭机除能完成上述各道工序外,尚能将码成垛的铅锭运送至桥式起重运输机工作范围内。
3)始极片制造机组原先制造始极片的各道工序如舀铅、制片、缺口和平整均系手工作业,始极片装槽也是手工作业,机组除取消了手工作业外,尚能将始极片按同级等距要求置于排板机上,再用桥式起重运输机把他们直接吊装入电解槽。
机制始极片比过去厚了,从而使周转的阴极铅量和煤(气)耗稍有增加;但是厚一些的始极片不易起翘,短路机会减少,并有助于提高电流效率和降低电耗。
4)阳极泥过滤洗涤阳极泥的液固分离和洗涤已成功地用压滤代替渗滤和离心过滤。
除劳动条件显著改善外,且由于压滤机生产能率高,电解槽清理时排出的阳极泥浆可及时地压滤掉,故电解槽清理极易安排。
5)电解液冷却在我国南方地区,每到夏季由于气温高,电解液温度往往超过要求,如无经济的地下水冷却,而采用冷冻水作冷煤时,则既不经济且冷却效果不堪理想,只能安排在夏季最热的月份内停产检修。
粗铅精炼

第六章粗铅的精炼目的要求:要求同学们掌握粗铅的火法与电解两种精炼工艺。
重点难点:1、铅的火法精炼;2、铅的电解精炼。
6.1 概述粗铅中一般含有1-4%的杂质成份,如金、银、铜、铋、砷、铁、锡、锑、硫等,见表6-1:粗铅需经过精炼才能广泛使用。
精炼目的:一是除去杂质。
由于铅含有上述杂质,影响了铅的性质,使铅的硬度增加,韧性降低,对某些试剂的抗蚀性能减弱,使之不适于工业应用。
用这样的粗铅去制造铅白、铅丹时,也不能得到纯净的产品,因而降低了铅的使用价值。
所以,要通过精炼,提高铅的纯度。
二是回收贵金属,尤其是银。
粗铅中所含贵金属价值有时会超过铅的价值,在电解过程中金银等贵金属富集于阳极泥中。
粗铅精炼的方法有两类,第一类为火法精炼,第二类为先用火法除去铜与锡后,再铸成阳极板进行电解精炼。
目前世界上火法精炼的生产能力约占80%。
采用电解精炼的国家主要有中国、日本、加拿大等国。
我国大多数企业粗铅的处理均采用电解法精炼。
火法精炼的优点是设备简单、投资少、占地面积小。
含铋和贵金属少的粗铅易于采用火法精炼。
火法精炼的缺点是:铅直收率低、劳动条件差、工序繁杂,中间产品处理量大。
电解精炼的优点是能使铋及贵金属富集于阳极泥中,有利于综合回收,因此金属回收率高、劳动条件好,并产出纯度很高的精铅。
其缺点是基建投资大,且电解精炼仍需要火法精炼除去铜锡等杂质6.2 粗铅的火法精炼6.2.1 粗铅火法精炼的工艺流程无论是火法精炼还是电解精炼,在精炼前通常都需除去粗铅中的铜和砷、锑、锡。
如是电解精炼,阳极板要含0.3—0.8%锑,此时要对阳极板含锑进行调整。
粗铅的火法精炼工艺流程如图6-1:铜浮渣精炼渣银锌壳精炼渣含铋浮渣精铅图6-16.2.2 粗铅除铜精炼除铜精炼的一般原理A、熔析除铜基本原理:熔析除铜的基本原理是基于铜在铅液中的溶解度随着温度的下降而减少,当含铜高的铅液冷却时,铜便成固体结晶析出,由于其比重较铅小(约为9),因而浮至铅液表面,以铜浮渣的形式除去。
7从废铅蓄电池生产再生铅
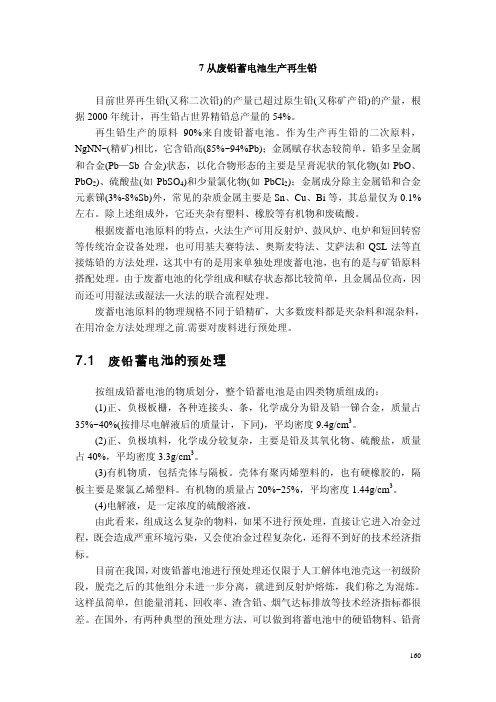
图 7—1 重介质分选预处理废铅蓄电池工艺流程
自生重介质分选处理废蓄电池的工艺流程如图 7—1 所示。没有解体的废蓄 电池先经锤式破碎机破碎,将破碎后的物料进行湿式筛分,分为三种粒级的产物: 细粒部分(-1mm),中粗部分(-4mm 至 1mm)和粗块部分(+4mm 至-60mm)。细物料
7.3 废 铅 蓄电 池的鼓风 炉 熔炼
鼓风炉熔炼适合处理团矿或块状物料,细粒物料则需先压团或烧结成块。鼓 风炉熔炼最大的优点是生产能力大,过程能连续进行。鼓风炉熔炼废铅蓄电池的 工艺流程如图 7—4。
废铅蓄电池的细粒物料包括正、负极填料(俗称铅膏或膏泥)和粒度小于 10mm 的板栅碎屑等。这类物料的烧结较铅精矿烧结简单,靠碎焦燃烧维持高温, 因为只需结块,不需脱硫,但要求比烧结块有较高强度和透气性。由于高铅炉料, 尤其是金属态的铅的熔化,会降低烧结块强度。在配料时,要严格控制炉料含铅 在 30%~35%的范围,因此炉料要添加鼓风炉水淬渣以稀释铅。在生产中烧结配 料的比例(%)一般是:含铅的粉料 22,水淬炉渣 16,黄铁矿烧渣 5,焦粉 2,返 粉 55。配好的炉料在烧结前须加水润湿并在混料圆筒中混匀,炉料在烧结时因 水分蒸发而提高炉料的透气性。在烧结过程中,2PbO·SiO2 的生成量取决于烧 结温度和配料中的含铅量,低铅(29%~33%)配料烧结时,2PbO·SiO2 部分占 25%~35%。烧结块成分(%)一般为 22 ~ 32Pb,19 ~22 SiO2 ,19~24FeO,
164
部连接烟气冷却和收尘系统,以便余热利用并收集铅尘。
反射炉熔炼加铁屑和煤粉作还原剂,其炉料配比一般是废蓄电池(去壳):煤 粉:铁屑=100:2~3:10~12。熔炼温度不低于 1200℃。熔炼过程中需不断搅拌 熔池以保证反应完全。
【电解铅生产工艺】 【还原铅、再生铅和铅精矿区别
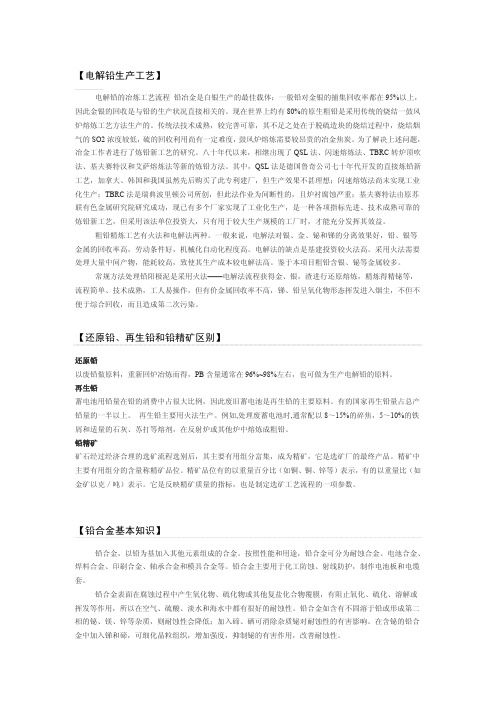
【电解铅生产工艺】电解铅的冶炼工艺流程铅冶金是白银生产的最佳载体:一般铅对金银的捕集回收率都在95%以上,因此金银的回收是与铅的生产状况直接相关的。
现在世界上约有80%的原生粗铅是采用传统的烧结一鼓风炉熔炼工艺方法生产的。
传统法技术成熟,较完善可靠,其不足之处在于脱硫造块的烧结过程中,烧结烟气的SO2浓度较低,硫的回收利用尚有一定难度,鼓风炉熔炼需要较昂贵的冶金焦炭。
为了解决上述问题,冶金工作者进行了炼铅新工艺的研究。
八十年代以来,相继出现了QSL法、闪速熔炼法、TBRC转炉顶吹法、基夫赛特汉和艾萨熔炼法等新的炼铅方法。
其中,QSL法是德国鲁奇公司七十年代开发的直接炼铅新工艺,加拿大、韩国和我国虽然先后购买了此专利建厂,但生产效果不甚理想;闪速熔炼法尚未实现工业化生产;TBRC法是瑞典波里顿公司所创,但此法作业为间断性的,且炉衬腐蚀严重;基夫赛特法由原苏联有色金属研究院研究成功,现已有多个厂家实现了工业化生产,是一种各项指标先进、技术成熟可靠的炼铅新工艺,但采用该法单位投资大,只有用于较大生产规模的工厂时,才能充分发挥其效益。
粗铅精炼工艺有火法和电解法两种。
一般来说,电解法对银、金、铋和锑的分离效果好,铅、银等金属的回收率高,劳动条件好,机械化自动化程度高。
电解法的缺点是基建投资较火法高。
采用火法需要处理大量中间产物,能耗较高,致使其生产成本较电解法高。
鉴于本项目粗铅含银、铋等金属较多。
常规方法处理铅阳极泥是采用火法——电解法流程获得金、银,渣进行还原熔炼,精炼得精铋等,流程简单、技术成熟,工人易操作,但有价金属回收率不高,锑、铅呈氧化物形态挥发进入烟尘,不但不便于综合回收,而且造成第二次污染。
【还原铅、再生铅和铅精矿区别】还原铅以废铅做原料,重新回炉冶炼而得,PB含量通常在96%~98%左右,也可做为生产电解铅的原料。
再生铅蓄电池用铅量在铅的消费中占很大比例,因此废旧蓄电池是再生铅的主要原料。
铅蓄电池生产工艺流程
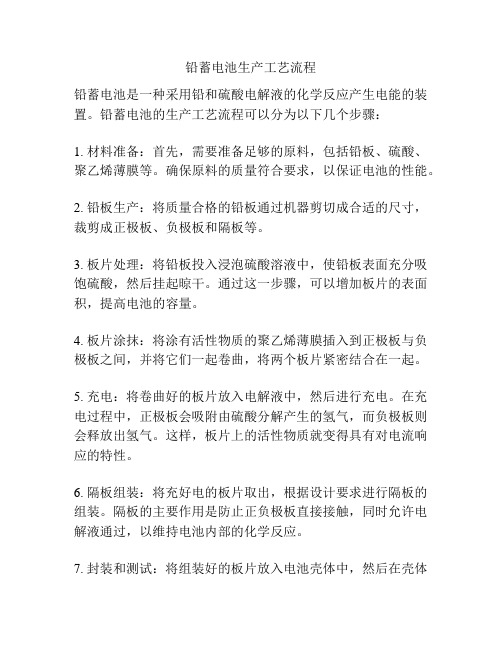
铅蓄电池生产工艺流程铅蓄电池是一种采用铅和硫酸电解液的化学反应产生电能的装置。
铅蓄电池的生产工艺流程可以分为以下几个步骤:1. 材料准备:首先,需要准备足够的原料,包括铅板、硫酸、聚乙烯薄膜等。
确保原料的质量符合要求,以保证电池的性能。
2. 铅板生产:将质量合格的铅板通过机器剪切成合适的尺寸,裁剪成正极板、负极板和隔板等。
3. 板片处理:将铅板投入浸泡硫酸溶液中,使铅板表面充分吸饱硫酸,然后挂起晾干。
通过这一步骤,可以增加板片的表面积,提高电池的容量。
4. 板片涂抹:将涂有活性物质的聚乙烯薄膜插入到正极板与负极板之间,并将它们一起卷曲,将两个板片紧密结合在一起。
5. 充电:将卷曲好的板片放入电解液中,然后进行充电。
在充电过程中,正极板会吸附由硫酸分解产生的氢气,而负极板则会释放出氢气。
这样,板片上的活性物质就变得具有对电流响应的特性。
6. 隔板组装:将充好电的板片取出,根据设计要求进行隔板的组装。
隔板的主要作用是防止正负极板直接接触,同时允许电解液通过,以维持电池内部的化学反应。
7. 封装和测试:将组装好的板片放入电池壳体中,然后在壳体上进行密封。
接着,对电池进行外观和性能的测试,以确保电池的质量和可靠性。
8. 充放电循环:将新生产的电池进行充放电循环测试,以提高电池的性能和品质。
9. 包装和仓储:最后,对产品进行包装,将其储存到仓库中,等待出货。
总结起来,铅蓄电池的生产工艺流程主要包括材料准备、铅板生产、板片处理、板片涂抹、充电、隔板组装、封装和测试、充放电循环,以及最后的包装和仓储。
通过这些步骤,可以制造出质量优良的铅蓄电池产品。
铅
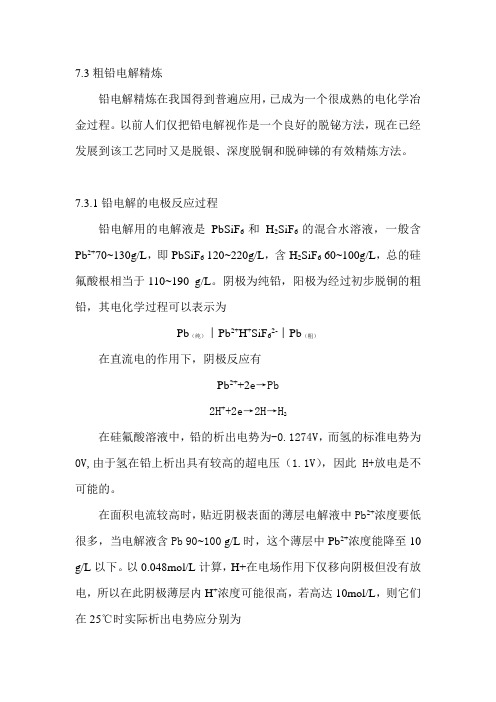
(1)阳极铸型阳极铸型机组采用液压并采用微机控制。将过去人工控制铅液量、手工起板、平板和排版等工序变为铅液定容量浇铸、链钩起板、液压平整,再按同极距要求均匀地放置在排板机上,装槽时用桥式起重运输机直接吊入电解槽内。
电解产出的阴极铅,用水洗涤后进行熔化,并视所含杂质情况进行氧化精炼或碱性精炼以除净残留的锡、砷、锑、然后铸成锭出售。小部分阴极铅熔化后制成始极片。残极取出后,洗净附着的阳极泥,送往熔铅锅重新熔化铸成阳极板。为了降低阳极泥中酸、铅含量,阳极泥需经压滤、洗滤。滤后阳极泥送稀、贵金属回收工序,洗水经澄清后返回电解系统。
Pb(纯)︱Pb2+H+SiF62-︱Pb(粗)
在直流电的作用下,阴极反应有
Pb2++2e→Pb
2H++2e→2H→H2
在硅氟酸溶液中,铅的析出电势为-0.1274V,而氢的标准电势为0V,由于氢在铅上析出具有较高的超电压(1.1V),因此H+放电是不可能的。
在面积电流较高时,贴近阴极表面的薄层电解液中Pb2+浓度要低很多,当电解液含Pb 90~100g/L时,这个薄层中Pb2+浓度能降至10 g/L以下。以0.048mol/L计算,H+在电场作用下仅移向阴极但没有放电,所以在此阴极薄层内H+浓度可能很高,若高达10mol/L,则它们在25℃时实际析出电势应分别为
电解液成分,g/L Pb99~128 H2SiF6 75~85 As1~1.4 Fe 4~5 Ag 0.001 Cu 0.002氨基乙酸40.8~59.5
生产实践表明,应用周期反向电解,当电解液含酸120~140g/L、含铅90~110g/L、电流密度160~180A/m2时,可获得结晶致密的阴极铅;极间短路减少,劳动强度减轻;消除了浓差极化,槽电压下降;电流效率稳定在93%以上。
铅渣处理粗铅火法精炼粗铅电解精炼
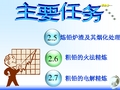
造渣除去。分离As、Sb、Sn后的粗铅开始变软,所以将除As、
Sb、Sn的粗铅精炼称为软化精炼,精炼后的铅称为软铅。
24
—铅冶金—
氧化精炼虽然设备简单,操作容易,投资少;但 其缺点是铅的损失大,直接回收率低,作业时间长,
劳动条件差,燃料消耗高,精炼后残锑高,故很少采
用。 碱性精炼的主要优点是作业可在较低温度下进行, 金属损失小,燃料消耗少,操作条件好,终点产品含 砷、锑、锡比较低,试剂NaOH和NaCl可部分再生; 缺点是过程所产生的各种碱渣处理比较麻烦,试剂消 耗大。目前大多数精炼厂采用碱性精炼除砷、锑、锡。
成 分
—铅冶金—
2. 5.2 烟化炉处理炉渣
液态熔炼炉渣周期地加入烟化炉,
烟化炉处理炉渣 的原理与过程
再往熔渣中鼓入空气和粉煤进行吹炼,
熔渣中的铅、锌、锗等金属被还原挥
发,金属蒸汽在炉子上部空间和前部 废热利用装置里,被三次风口吸入 的 空气氧化,变成氧化物再予以回收。
2
烟化炉主要尺寸实例
—铅冶金—
2 [Pb] +S2= 2[PbS]
被硫化,但是由于硫对铜的亲和力比对铅大,故按式:
[PbS]+2[Cu]=[Pb]+ (Cu2S)
形成Cu2S。
15
—铅冶金—
Pb Cu2 S K 2 PbS Cu
由于Cu2S不溶于铅,且铅的浓度可视为不变。上式可变为:
1 Cu K PbS
18
—铅冶金—
19
—铅冶金—
粗铅除铜实例
20
有的工厂采用连续除铜作业,其操作是在一个较深熔池
—铅冶金—
(1.2 ~ 1.8m)的炉中进行的。在深熔池中,熔体自上而下温 度逐步降低,形成一定的温度梯度,粗铅液加入熔池上部,低
铅电解精炼法简介
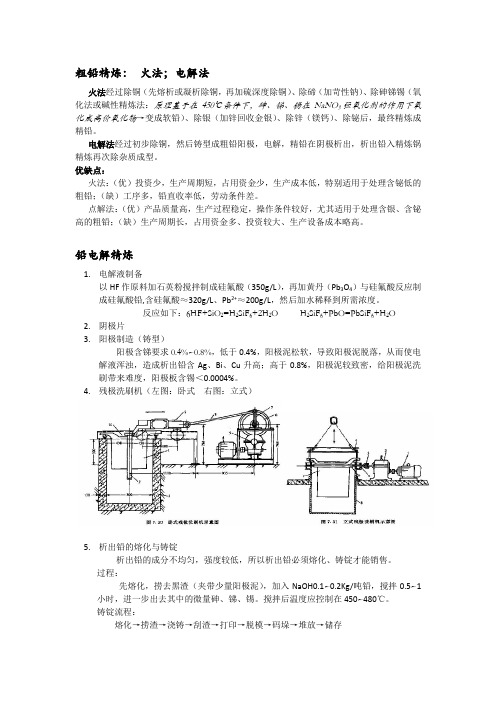
粗铅精炼:火法;电解法火法经过除铜(先熔析或凝析除铜,再加硫深度除铜)、除碲(加苛性钠)、除砷锑锡(氧化法或碱性精炼法:原理基于在450℃条件下,砷、锑、锡在NaNO3强氧化剂的作用下氧化成高价氧化物→变成软铅)、除银(加锌回收金银)、除锌(镁钙)、除铋后,最终精炼成精铅。
电解法经过初步除铜,然后铸型成粗铅阳极,电解,精铅在阴极析出,析出铅入精炼锅精炼再次除杂质成型。
优缺点:火法:(优)投资少,生产周期短,占用资金少,生产成本低,特别适用于处理含铋低的粗铅;(缺)工序多,铅直收率低,劳动条件差。
点解法:(优)产品质量高,生产过程稳定,操作条件较好,尤其适用于处理含银、含铋高的粗铅;(缺)生产周期长,占用资金多、投资较大、生产设备成本略高。
铅电解精炼1.电解液制备以HF作原料加石英粉搅拌制成硅氟酸(350g/L),再加黄丹(Pb3O4)与硅氟酸反应制成硅氟酸铅,含硅氟酸≈320g/L、Pb2+≈200g/L,然后加水稀释到所需浓度。
反应如下:6HF+SiO2=H2SiF6+2H2OH2SiF6+PbO=PbSiF6+H2O2.阴极片3.阳极制造(铸型)阳极含锑要求0.4%~0.8%,低于0.4%,阳极泥松软,导致阳极泥脱落,从而使电解液浑浊,造成析出铅含Ag、Bi、Cu升高;高于0.8%,阳极泥较致密,给阳极泥洗刷带来难度,阳极板含锡<0.0004%。
4.残极洗刷机(左图:卧式右图:立式)5.析出铅的熔化与铸锭析出铅的成分不均匀,强度较低,所以析出铅必须熔化、铸锭才能销售。
过程:先熔化,捞去黑渣(夹带少量阳极泥),加入NaOH0.1~0.2Kg/吨铅,搅拌0.5~1小时,进一步出去其中的微量砷、锑、锡。
搅拌后温度应控制在450~480℃。
铸锭流程:熔化→捞渣→浇铸→刮渣→打印→脱模→码垛→堆放→储存。