炼钢部分各种计算公式汇总
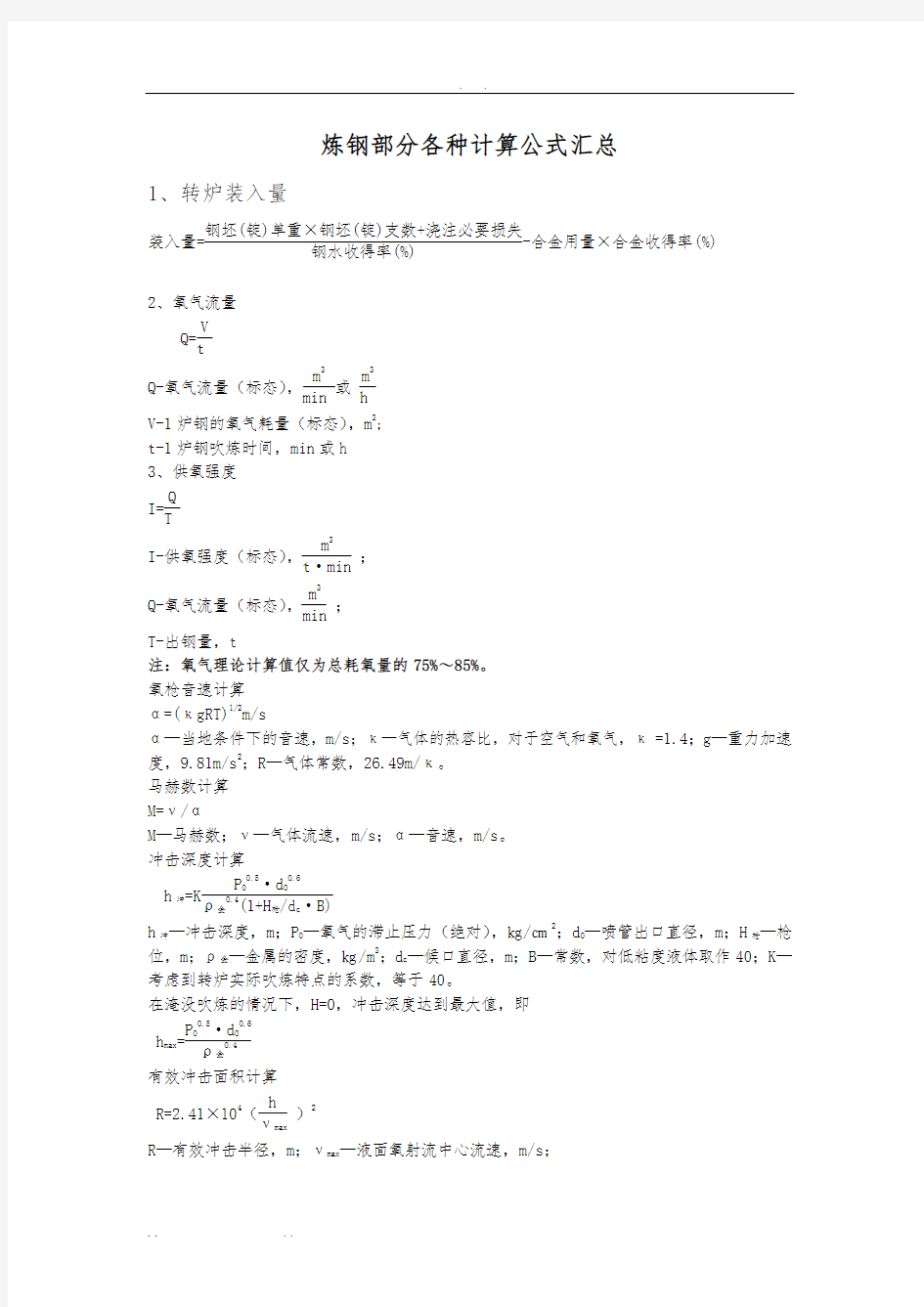

炼钢部分各种计算公式汇总
1、转炉装入量
装入量=钢坯(锭)单重×钢坯(锭)支数+浇注必要损失
钢水收得率(%)-合金用量×合金收得率(%)
2、氧气流量
Q=V t
Q-氧气流量(标态),m 3
min 或 m
3
h
V-1炉钢的氧气耗量(标态),m 3
; t-1炉钢吹炼时间,min 或h 3、供氧强度 I=Q T
I-供氧强度(标态),m
3
t ·min ;
Q-氧气流量(标态),m
3min
;
T-出钢量,t
注:氧气理论计算值仅为总耗氧量的75%~85%。 氧枪音速计算
α=(κgRT)1/2
m/s
α—当地条件下的音速,m/s ;κ—气体的热容比,对于空气和氧气,κ=1.4;g —重力加速
度,9.81m/s 2
;R —气体常数,26.49m/κ。 马赫数计算 M=ν/α
M —马赫数;ν—气体流速,m/s ;α—音速,m/s 。 冲击深度计算
h 冲=K P 00.5
·d 0
0.6
ρ金0.4
(1+H 枪/d c ·B)
h 冲—冲击深度,m ;P 0—氧气的滞止压力(绝对),㎏/㎝2
;d 0—喷管出口直径,m ;H 枪—枪
位,m ;ρ金—金属的密度,㎏/m 3
;d c —候口直径,m ;B —常数,对低粘度液体取作40;K —考虑到转炉实际吹炼特点的系数,等于40。
在淹没吹炼的情况下,H=0,冲击深度达到最大值,即 h max =P 00.5
·d 0
0.6
ρ金0.4
有效冲击面积计算 R=2.41×104
(
h νmax
)2
R —有效冲击半径,m ;νmax —液面氧射流中心流速,m/s ;
νmax =ν出d 出H ·P 0
0.404
ν出—氧射流在出口处的流速,m/s 。
金属-氧接触面积计算
在淹没吹炼时,射流中的金属液滴重是氧气重量的3倍,吹入1m3氧气的液滴总表面积(金属-氧气的接触面积): S Σ=3G 金r 平均·ρ金
G 金—1标米3
氧气中的金属液滴重量=3×1.43㎏;r 平均—液滴的平均半径,m ;ρ金—金属
液的密度,7×103㎏/m 3
。 金属-熔渣接触面积计算 S 渣=3V 渣
r 渣
V 渣—乳化渣的总体积,m 3
;r 渣—渣滴半径,m 。 氧气高度计算 H=bPD e
H —氧枪喷头端面距熔池液面的高度,㎜;b —系数,随喷孔数而变化,四孔喷头b=45~60;P —供氧压力,MPa ;D e —喷头出口直径,㎜。 4、石灰的加入量(㎏/t ) 当铁水P <0.30%时,
石灰加入量(㎏/t )= 2.14[Si]×R ×1000
ω(CaO,石灰)-R ×ω(SiO2,石灰)
每千克矿石补加石灰量(㎏)= R ×ω(SiO2,矿)
ω(CaO,石灰)-R ×ω(SiO2,石灰)
当铁水P >0.30%时,
石灰加入量(㎏)=(2.14[Si]+2.29[P])×R ×1000
ω(CaO,石灰)-R ×ω(SiO2,石灰)
石灰加入量(㎏/t )=(2.14[Si]+η×2.29[P])×R ×1000
ω(CaO,石灰)-R ×ω(SiO2,石灰)
η-脱磷率,单渣法取90%,双渣法为90%~95%; 石灰加入量(㎏/t )= 2.2([%Si]+[%P])
ω(CaO,有效)-R ×ω(SiO2,石灰)×R ×1000
当生成3CaO ·P 2O 5时,
石灰加入量(㎏)= ωCaO -1.18 ω P2O5
ω(CaO,石灰)-R ×ω(SiO2,石灰)
当生成4CaO ·P 2O 5时,
石灰加入量(㎏)=ωCaO
ωSiO +0.634ωP2O5
4CaO ·P 2O 5和3CaO ·P 2O 5在炼钢高温下都是稳定的化合物,生产时放出大量的热,3CaO ·P 2O 5比4CaO ·P 2O 5生成时放出的热量多。只有当渣中P 2O 5的质量分数ω(P2O5)>3%时才有可能形成3CaO ·P 2O 5。实际生产中P 2O 5的质量分数一般不会超过1%。 吨钢石灰的加入量(㎏)
=
2.14(ω[Si],铁水×铁水量+ ω[Si],废钢×废钢量+ ω[Si],生铁块×生铁块量)×R ×1000
(ω(CaO,石灰)-R ×ω(SiO2,石灰)
铁水带渣带入的SiO 2应考虑铁水渣中CaO 相当的SiO 2量
ω(SiO2有效,铁水渣)= ω(SiO2,铁水渣)-ωCaO
R
则辅原料及铁水带渣所需石灰用量(㎏) =
R ×(ωSiO2,矿×矿石量+ ωSiO2,萤石×萤石量+ ωSiO2有效,铁水渣×铁水带渣量)
ω(CaO,石灰)-R ×ω(SiO2,石灰)
5、渣量计算
渣量可以用元素平衡法计算。Mn 和P 两元素,从渣料和炉衬中的来源很少,其数量可以忽略不计。因而可以用Mn 或P 的平衡来计算渣量。 用Mn 平衡计算渣量 设渣量为X,
终渣中氧化锰的含量已知为A%;,则渣中锰含量= A%×55
55+16
=B%;
锰来源量=铁水带锰量+废钢带锰量
=铁水装入量×铁水中锰含量%+废钢装入量×废钢中锰含量% 锰支出量=钢水带锰量+炉渣带锰量
=出钢钢水量×终点残锰量%+炉渣渣量×炉渣中锰含量% 根据质量守恒定律,锰来源量=锰支出量
铁水装入量×铁水中锰含量%+废钢装入量×废钢中锰含量%=出钢钢水量×终点残锰量%+炉渣渣量×炉渣中锰含量% 用P 平衡计算渣量 设渣量为Y
终渣中氧化锰的含量已知为A%;,则渣中锰含量= A%×62
62+80
=B%;
P 来源量=铁水带P 量+废钢带P 量
=铁水装入量×铁水中P 含量%+废钢装入量×废钢中P 含量% P 支出量=钢水带P 量+炉渣带P 量
=出钢钢水量×终点钢水中P 量%+炉渣渣量×炉渣中P 含量% 根据质量守恒定律,P 来源量=P 支出量
铁水装入量×铁水中P 含量%+废钢装入量×废钢中P 含量%=出钢钢水量×终点钢水中P 量%+炉渣渣量×炉渣中P 含量% 6、白云石加入量计算 白云石加入量
石灰带入的MgO 的量=石灰加入量×石灰中MgO 含量%=A (㎏)
1t 装入量炉衬熔损带出的MgO 的量=1000×熔损的含量%×炉衬中MgO 的含量%=B (㎏) 1t 装入量终渣MgO 的量=1000×渣量占金属装入量的量%×终渣成分中MgO 含量%=C (㎏) 白云石的加入量=(终渣要求MgO 的量C-石灰带入的MgO 的量A-炉衬熔损带出的MgO 的量B )/白云石中MgO 的含量% =D (㎏) 白云石需补加石灰用量
补加石灰量=R ×ωSiO2×白云石加入量D
ω(CaO,石灰)-R ×ω(SiO2,石灰)
= F (㎏)
白云石相当的石灰量
白云石相当的石灰量=白云石的加入量D ×白云石中MgO 的含量%
ω(CaO,石灰)-R ×ω(SiO2,石灰)
=E (㎏)
∴石灰的加入总量=石灰加入量-补加石灰量-白云石相当的石灰量=G (㎏) 1炉钢渣量总量简单计算
炉渣总量/炉=石灰加入量+白云石×(1-白云石中烧碱含量%)+矿石加入量×(1-矿石中全铁含量%)+装入量×入炉金属料硅含量%×1000×60÷28
入炉金属料硅含量=装入量×铁水所占比例×铁水硅含量%+装入量×生铁块所占比例×生铁块硅含量%+装入量×废钢所占比例×废钢硅含量%
炼钢温度下分配系数常以渣中氧化物含量和元素的比值表示 L M =ω(M)ω[M] =αω(M x O y )ω[M]
根据脱磷效果确定硅、渣量计算
转炉炼钢脱磷能力较强,去磷量可达90%以上,在FeO%=14%时,脱磷指数为L p =(P)[P]
炉渣碱度下脱磷指数L p =(P)
[P]
的最大值
实际脱磷指数只能达到最大值的50%~80%之间。
ω渣=([P]铁水-[P]钢水)×1000/[P]钢水L 实
ω渣=
([P]铁水-[P]钢水)×1000
[P]钢水L 实
=A
L 实=0.436L p +0.3717
以100㎏炉料为例,磷的平衡关系为: 炉料中磷量=钢中磷量+渣中磷量 100ω[P]%料=Q 钢ω[P]%料+Q 渣ω(P )%
∵ω(P )%=0.437ω(P 2O 5)%,ω(P 2O 5)%=L p ω[P]% 100ω[P]%料=Q 钢ω[P]%料+0.437Q 渣L p ω[P]% ω[P]%= 100ω[P]%料/ (Q 钢+0.437Q 渣L p ) ω[P]%料—炉料中磷的质量百分数; Q 钢—钢水重量,㎏; Q 渣—炉渣重量,㎏。
炼钢铁水的最佳硅质量分数
渣量既要保证脱磷效果,又要考虑成本。炼钢碱度一般取3.5,炉渣中CaO 和SiO 2占总渣量的50%~60%左右。假定CaO+ SiO 2为渣量的55%,渣中CaO 含量为B%,渣中SiO 2含量为C%则
石灰的加入量(㎏/t )=渣量×渣中CaO 含量%/石灰有效氧化钙 =A ×B%
ω(CaO,石灰)-R ×ω(SiO2,石灰)
铁水硅含量计算
渣中SiO 2的量(㎏/t )=渣量×渣中SiO 2含量%=A ×C%=D ㎏
每吨铁水的Si 含量 ω(Si)=渣中SiO 2的量/1000×28/60×100%=E% =渣中SiO 2的量×28×100%
60×1000
=D ×28×100%
1000×60
∴铁水中的ω(Si)与ω(P) 的关系为:
Si%=(P%铁水-P%出钢)×1000×100%×渣中SiO 2含量%×28×100%)/(L 实×P%出钢×60×1000) Si%=(P%铁水-P%出钢)×1000×100%×渣中SiO 2含量%×28×100%L 实×P%出钢×60×1000
L 实=0.436L p +0.3717 还原性脱磷方案:
硅钙合金脱磷,要求用一定压力的氩气作为载流气体,将Ca —Si 合金粉喷入钢液之中;电石脱磷,要求钢液温度为1575~1680℃、钢中碳的活度在0.02~0.30之间,脱磷率ηp 可达50%以上;CaC 2—CaF 2合成渣脱磷,钢水温度在1575~1680℃,CaC 2—CaF 2渣系中CaF 2的配比控制在10%~25%为好。 温度为1570~1680℃,ω(CaO )>24%时脱磷计算
lg
ω(P)%ω[P]% =22350
T
-16+2.5lg Σω(FeO)%+0.08ω(CaO )% 当硫在渣、钢间的分配系数Ls 一定时,钢液硫含量取决于炉料硫含量和渣量的计算
Σω(S)%=ω[S]%+ω(S)%·Q Ls=ω(S)%/ ω[S]%
则ω[S]%= Σω(S)%/(1+Ls ·Q )
Σω(S)%—炉料带入熔池的总硫量,%;ω[S]%—钢液中硫的质量百分数; ω(S)%—炉
渣中硫的质量百分数;Q —渣量,%.
7、转炉热效率计算 总热效率=有效热×100%
总热量
8、出钢温度的计算
出钢温度=凝固温度(T 凝)+过热度(α)+出钢过程温降(Δt 1)+出钢完毕至精炼开始之前的温降(Δt 2)+钢水精炼过程的温降(Δt 3)+钢水精炼完毕至开浇之前的温降(Δt 4)+钢水从钢包至中间包的温降(Δt 5) 常用的凝固温度计算公式
T n =1536-(78ω[C]+7.6ω[Si]+4.9ω[Mn]+34ω[P]+30ω[S]+5.0ω[Cu]+3.1ω[Ni]+2.0ω[Mo]+2.0ω[V]+1.3ω[Cr]+18ω[Ti]+3.6ω[Al]+ 80ω[B]+ 80ω[O] +90ω[N] +1300ω[H]) 过热度-与钢种、坯型有关,方坯一般取20-30℃,板坯一般取15-25℃ 9、冷却剂的冷却效应计算 Q 冷=Q 物+Q 化
1㎏矿石的冷却效应
Q 矿(kj/㎏)=1×(矿石热熔×(前期熔池温度-常温)+矿石熔化潜热+矿石中Fe 2O 3含量×112/160×还原铁吸收热量+矿石中FeO 含量×56/72×还原铁吸收热量)
Q 矿(kj/㎏=1×C 矿×Δt+λ矿+1×(ω(e 2O 3)矿×112/160×6456+ω(FeO)矿×56/72×4247) Q 矿=1×(1.016×(1350-25)+209+矿石中Fe 2O 3含量×112/160×6459+矿石中FeO 含量×112/160×4249) 1㎏废钢的冷却效应 Q 废(kj/㎏)=1×((废钢固态热熔×(废钢熔化温度-常温)+废钢熔化潜热+液态热熔×(出钢温度-废钢熔化温度))
Q 废(kj/㎏)=1×[(C 固×(t 熔-25))+λ废+C 液(t 出-t 熔)] Q 废=1×(0.699×(1500-25)+272+0.837×(出钢温度-1500)) 冷却剂用量确定
如果选择矿石为装入量的A%,则需要设废钢用量,设废钢用量χ㎏ Q 余=A%(100+χ)×Q 矿+χ×Q 废
温度降低计算
T 降℃=冷却效应
(钢水量×液态热熔)+(炉渣×炉渣热熔)
T 降℃=冷却效应
(钢水量×0.837)+(炉渣×1.247)
假定设定废钢的冷却效应为1,则常用冷却剂的冷却效应换算值换算
加入1%冷却剂时降温的经验数据