车刀几何角度选择
车刀种类和角度选择原则详解
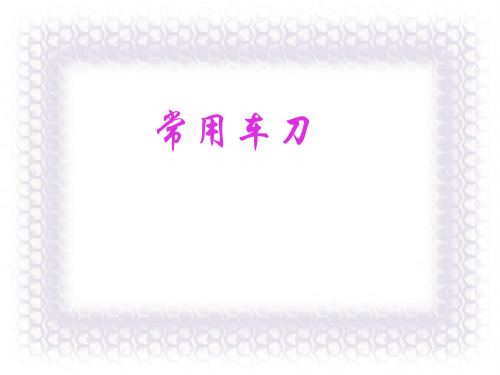
车刀不对准工件中心对角度的影响
五、车刀刃磨
无论硬质合金车刀(焊接)或高速钢 车刀,在使用之前都要根据切削条 件所选择的合理切削角度进行刃磨 ,一把用钝了的车刀,为恢复原有 的几何形状和角度,也必须重新刃 磨。
重 要 性
三分手艺、七分刀 徒弟的手、师傅的刀
1.磨刀步骤(图a~d)
⑴磨前刀面 把前角和刃倾角磨正确。 ⑵磨主后刀面 把主偏角和主后角磨正确。 ⑶磨副后刀面 把副偏角和副后角磨正确。 ⑷磨刀尖圆弧 圆弧半径约0.5~2mm左右。 ⑸研磨刀刃 车刀在砂轮上磨好以后,再用油石加些机油研磨车 刀的前面及后面,使刀刃锐利和光洁。这样可延长车刀的使用寿命。 车刀用钝程度不大时,也可用油石在刀架上修磨。硬质合金车刀可 用碳化硅油石修磨。
前角γo
——在主切削刃选定点的正交平面po内, 前刀面与基面之间的夹角
。
后角αo
——在正交平面po内,主后刀面与切削 平面之间的夹角。
主偏角κr
——主切削刃在基面上的投影与进给方 向的夹角。
刃倾角λs ——在切削平面ps内,主切削刃与 基面pr的夹角。
其他角度:
副前角γoˊ、 副后角αoˊ、 副偏角κrˊ、 刃倾角λsˊ
3.主偏角、副偏角的选择 (1)主偏角的选择 A、主偏角κr的增大或减小对切削加工有利的一 面 在背吃刀量ap与进给量f 不变时,主偏角κr减小 将使切削厚度hD减小,切削宽度bD增加,参加 切削的切削刃长度也相应增加,切削刃单位长度 上的受力减小,散热条件也得到改善。 主偏角κr减小时,刀尖角增大,刀尖强度提高, 刀尖散热体积增大。 所以,主偏角κr减小,能提高刀具耐用度。
(4)良好的工艺性和经济性
如何合理的选取车刀的几何角度

如何合理的选取车刀的几何角度
1、前角γ0(在正交面的上测量的前刀面与基面之间的夹角)。
它表示前刀面的倾斜程度。
前角越大,刀刃越锋利,切削时就越省力。
但前角过大会削弱刀头强度,影响刀具的寿命。
前角的选取决定于工件材料、刀具材料和加工性质。
硬质合金车刀γ0通常取-5º~+25º。
2、后角α0。
在正交平面上测量的主后刀面与切削平面之间的夹角。
它表示主后刀面的倾斜程度。
后角的作用主要是减少刀具与加工表面之间的摩擦,后角越大,摩擦越小,但后角过大会削弱切削刃的强度及耐用度。
一般取α0为60~120。
3、主偏角k r。
主切削刃在基面上的投影与进给方向之间的夹角。
主偏角能影响主切削刃和刀头受力情况及散热情况。
加工强度、硬度较高的材料时,应选较小的主偏角,以提高刀具的耐用度。
加工细长工件时,应选较大的主偏角,以减少径向切削力引起工件的变形和振动。
一般取k r为300~900。
4、副偏角k r'。
副切削刃在基面上的投影与进给反方向之间的夹角。
副偏角的作用是减少副切削刃与工件已加工表面之间的摩擦。
副偏角越大,摩擦越小。
但k r过大,又会增大已加工表面的粗糙度。
一般取k r为50~150。
车刀的几何角度:。
数控车刀的几何参数.

数控车刀的几何参数一、刀具几何参数刀具的切削性能主要是由刀具材料的性能和刀具几何参数两方面决定的。
刀具几何参数的选择是否合理对切削力、切削温度及刀具磨损有显著影响。
选择刀具的几何参数要综合考虑工件材料、刀具材料、刀具类型及其他加工条件(如切削用量、工艺系统刚性及机床功率等)的影响。
刀具组成部分如图1-1所示。
图1-1主偏角κr——主切削刃在基面上的投影与进给方向的夹角。
刃倾角λs——在切削平面ps内,主切削刃与基面pr的夹角。
还有:副前角γoˊ、副后角αoˊ、副偏角κrˊ、副倾角λsˊ图1-2二、刀具几何参数对加工精度的影响在数控加工中,为降低加工工件表面粗糙度,减缓刀具磨损、提高刀具使用寿命、选择适宜的切削力等因素,通常车刀会存在刀尖圆弧半径r,主偏角kr,车刀刀尖距零件中心高的偏差等刀具几何参数的影响,必定引起被加工零件的轴向尺寸误差和径向尺寸误差由此使得加工的运行轨迹与被加工零件的形状产生差异。
因被加工零件表面形状各异,所以引起的差异也各不相同。
下面依次分析车削加工各类零件表面形状引起的差异以及采取的措施。
1.车刀刀尖圆弧半径对加工圆柱类零件表面的影响众所周知,被加工零件表面的成形是由车刀与零件表面接触见切点的运行轨迹保证的,对于主偏角kr=90°的车削加工,参见图1.1示,被加工零件表面的轴向尺寸由刀尖圆弧半径点A保证。
图1.1当(D-d)/2=ap>r时,由图可知,由刀尖圆弧半径引起的轴向尺寸变化量△a为△a=b-a=r式中:b——零件轴向尺寸;a——实际轴向位移量;r——刀尖圆弧半径.此时,刀具实际轴向位移是长度a为:a=b-△a=b-r(D-d)/2=ap△a=BC=2pp22a-ra2)(r=--par此时,刀具实际轴向位移长度a=b-Δa=22yyarab--对于主偏角KF<90°的车削加工,当完成轴向加工即处于图1.1c位置时,被加工零件的已加工表面部由车刀刀尖A保证,零件的加工表面由刀具型面AC 和CE形成。
怎样选择车刀的几何角度

怎样选择车刀的几何角度合理选择车刀几何角度,有利于改善加工条件,提高被加工工件质量,延长刀具与设备的使用寿命,本文从车刀几何角度对切削力、切削热和刀具耐用度影响等角度,分析车刀几何角度选择的一般原则.车刀几何角度是指车刀切削部分各几何要素之间,或它们与参考平面之间构成的两面角或线、面之间的夹角.它们分别决定着车刀的切削刃和各刀面的空间位置。
根据“一面二角”理论可知,车刀的独立标注角度有六个,它们分别是:确定车刀主切削刃位置的主偏角Kr和刃倾角λs;确定车刀前刀面Ar与后刀面Aa的前角ro和后角ao;确定副切削刃及副后刀面Aa′的副偏角Kr′和副后角ao′.这些几何角度对车削过程影响很大,其中尤其以主偏角Kr、前角ro、后角ao和刃倾角λs 的影响更为突出,科学合理地选择车刀的几何角度,对车削工艺的顺利实施起着决定性作用。
下面就从车刀几何角度对切削力、切削热和刀具的耐用度的影响分析着手,本着使切削轻便、质量稳定,延长刀具使用寿命的宗旨,确定科学的车刀几何角度的一般性原则.一、车刀几何角度对切削力的影响在金属切削时,刀具切入工件,将多余材料从工件上切除会产生强烈的力的作用,这些力统称为切削力。
切削力主要来源于被加工材料在发生弹性和塑性变形时的抗力和刀具与切屑及工件表面之间的摩擦作用。
根据切削力产生的作用效果的不同,可将切削力分解成三个相互垂直方向的分力.它们分别是:主切削力Fz,进给抗力Fx和切深抗力Fy,其中Fz是切削总力Fr沿主运动切向分解而得,是计算车刀强度,设计机床零件,确定机床功率的主要依据;Fx也叫轴向力,它是Fr沿工件轴向的分力,是设计进给机构,计算车刀进给功率所必需的;Fy也叫径向力,它是Fr沿着工件径向的分力,它不消耗机床功率,但是当机床或工艺系统刚度不足时,易引起振动.(一)前角ro对切削力的影响前角ro增大,剪切角Φ随着增大,金属塑性变形减小,变形系数ξ减小,沿前刀面的摩擦力减小,因此切削力减小。
解释车刀的主要几何角度,并说明对车削加工的影响

在车削加工中,车刀的主要几何角度对加工效果和加工质量有着重要的影响。
在本文中,我将从深度和广度上对车刀的几何角度进行全面评估,并探讨它们对车削加工的影响。
1. 切削角:切削角是指车刀切削刃上的主切削刃与前方切削方向的夹角。
切削角的大小直接影响着切屑的形成和流动。
当切削角较大时,切削力减小,但切削刃容易磨损;当切削角较小时,切削力增大,但切削刃磨损减小。
选择适当的切削角对于保证加工质量和提高加工效率至关重要。
2. 后角:后角是指车刀主切削刃与切削方向之间的夹角。
后角的大小影响着车刀的进给力和阻力。
当后角增大时,进给力增大,加工效率提高;但阻力也会增大,对车刀和工件的刚性要求也会增加。
合理选择后角是为了在保证加工效率的尽可能减小刀具和工件的损耗。
3. 主偏角:主偏角是指车刀主切削刃与工件表面的夹角。
主偏角的大小直接影响着工件的表面质量和加工精度。
一般来说,主偏角越小,加工表面的质量越好,但车刀的刚度和稳定性要求也越高。
在实际应用中需要根据工件的要求和加工条件选择合适的主偏角。
4. 副偏角:副偏角是指车刀副切削刃与工件表面的夹角。
副偏角的大小影响着切削刃与工件的接触面积和切削力的大小。
合理选择副偏角可以有效减小切削力,提高车削加工的效率和质量。
车刀的几何角度对车削加工有着重要的影响,其合理选择可以有效提高加工效率和加工质量。
在实际应用中,需要根据具体的加工要求和工件材料来选择合适的几何角度,以达到最佳的加工效果。
个人观点和理解:车刀的几何角度是车削加工中的关键参数,合理选择和调整这些角度对于提高加工质量和效率至关重要。
在实际应用中,需要综合考虑工件材料、加工条件和车刀性能等因素,进行合理的选择和调整,以达到最佳的加工效果。
以上是对“解释车刀的主要几何角度,并说明对车削加工的影响”的文章撰写,希望能帮助你更深入地理解这一主题。
在车削加工中,车刀的几何角度对加工效果和加工质量有着重要的影响。
除了切削角、后角、主偏角和副偏角外,还有其他几何角度也对车削加工起着重要作用,比如前角、刀尖半径等。
车工15-车刀几何角度的初步选择
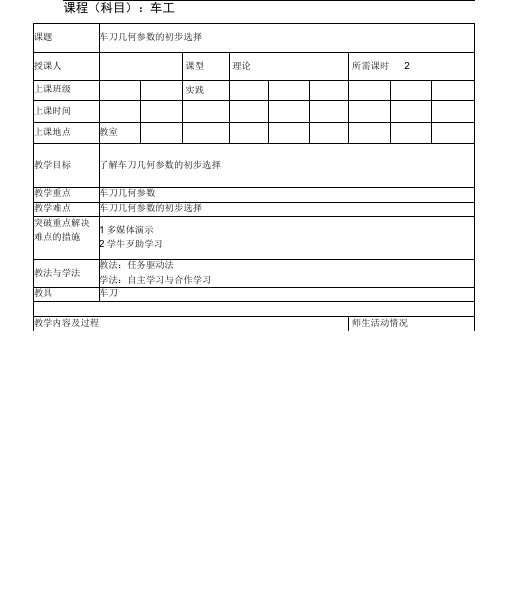
课程(科目):车工车刀前角的参考数值见表1工件材料刀具材料咼速钢硬质合金前角(丫0 )数值灰铸铁HT1500°〜5 c5°〜10。
咼碳钢、合金钢((T15°〜25°5°〜10。
b=800 〜1000MPa)中碳钢、中碳合金钢25°〜30°10°〜15°((Tb=600〜800 MPa )低碳钢30 °〜40°25 〜30°铝及镁的轻合金35°〜45°30°〜35°④工艺系统的刚性较差或机场精度不足时应取较大的前角⑤成形刀具或齿轮刀具等为了防止齿形误差常取很小的前角,甚至是零度的前角O前角的作用:前角大,刃口锋利,切削层的塑性变形和摩擦阻力小,切削力和切削热减小。
但前角过大将使切削刃的强度降低,散热条件变差,刀具的使用寿命降低,甚至会造成崩刃的现象。
虽然前角和前刀面的作用各不相同,但是它们之间有着密切的联系。
前刀面的形状有平面型、曲面型和带带倒棱型三种。
平面型又可以分成正前角平面型、负前角平面型和负前角双面型;曲面型又可分为弧曲面、波纹曲面和其他形式曲面;带倒棱型又可分为平面带倒棱型和曲面带倒棱型两种。
如下图所示°a)b)c)图1前刀面平面型a)正前角平面型b)负前角单面型c)负前角双面型图2曲面型图3带倒棱型(1)后角(a o)后角太大,会降低切削刃和刀头的强度;后角太小,会增加后刀面与工件表面的磨擦,选择后角主要诊所以下几个原则:①粗加工时,应取较小的后角(硬质合金车刀:a o =5。
〜7。
;高速钢车刀:ao=6°〜8。
);精加工是时,应取较大的后角(硬质合金车刀:ao =8°〜10°;高速钢车刀:ao=8°〜12°)②工件材料较硬,后角宜取小值;工件材料较软,则后角取大值。
车刀前角和后角的参考值副后角(a J)—般磨成与后角(ao )相等但在等特殊情况下,为了保证刀具的强度,副后角应该取较小的数值。
车刀的几何角度及选择原则

车刀的几何角度及选择原则newmaker为了决定车刀刃口的锋利程度及其在空间的位置,必须建立一个坐标系,该坐标系由三个基准平面构成。
下面以外圆车刀为例,介绍车刀的几何角度。
如图所示。
基面:过主切削刃选定点的平面,此平面在主切削刃为水平时包含主刀刃并与车刀安装底面即水平面平行,此平面主要作为度量前刀面在空间位置的基准平面。
切削平面:过主切削刃选定点与主切削刃相切,并与基面相垂直的平面。
此平面主要作为度量主后刀面在空间位置的基准面。
主剖面:过主切削刃选定点并同时垂直于基面和主切削平面的平面。
(1)、前角γ0 前刀面与基面的夹角,在主剖面中测量。
前角的大小影响切削刃锋利程度及强度。
增大前角可使刃口锋利,切削力减小,切削温度降低,但过大的前角,会使刃口强度降低,容易造成刃口损坏。
取值范围为:-8°到+15°。
选择前角的一般原则是:前角数值的大小与刀具切削部分材料、被加工材料、工作条件等都有关系。
刀具切削部分材料性脆、强度低时,前角应取小值。
工件材料强度和硬度低时,可选取较大前角。
在重切削和有冲击的工作条件时,前角只能取较小值,有时甚至取负值。
一般是在保证刀具刃口强度的条件下,尽量选用大前角。
如硬质合金车刀加工钢材料时前角值可选5°-15°。
(2)、主后角α0 主后刀面与切削平面间的夹角,在主剖面中测量。
其作用为减小后刀面与工件之间的摩擦。
它也和前角一样影响刃口的强度和锋利程度。
选择原则与前角相似,一般为0到8°。
(3)、主偏角κ r 主切削刃与进给方向间的夹角,在基面中测量。
其作用体现在影响切削刃工作长度、吃刀抗力、刀尖强度和散热条件。
主偏角越小,吃刀抗力越大,切削刃工作长度越长,散热条件越好。
选择原则是:工件粗大刚性好时,可取小值;车细长轴时为了减少径向切削抗力,以免工件弯曲,宜选取较大的值。
常用在15°到90°之间。
(4)、副偏角κ 'r 副切削刃与进给反方向间的夹角,在基面中测量。
车刀切削部分几何参数的选择

教学过程
威海工业技术学校
加工塑性材料和精加工—取大后角( 选择:
0
)
加工脆性材料和粗加工—取小后角( 0 )
后角( 0)只能是正的。
精加工: 0= 80~120 粗加工: 0= 40~80
11
教学过程
3 . 主偏角(kr)
威海工业技术学校
作用: 改善切削条件,提高刀具寿命。
根据加工条件.工件材料性能. 工艺系统刚性 (例.细长轴)工件表面形状来合理选择.
19
威海工业技术学校
20
11 醉翁亭记
1.反复朗读并背诵课文,培养文言语感。
2.结合注释疏通文义,了解文本内容,掌握文本写作思路。
3.把握文章的艺术特色,理解虚词在文中的作用。
4.体会作者的思想感情,理解作者的政治理想。一、导入新课范仲淹因参与改革被贬,于庆历六年写下《岳阳楼记》,寄托自己“先天下之忧而忧,后天下之乐而乐”的政治理想。实际上,这次改革,受到贬谪的除了范仲淹和滕子京之外,还有范仲淹改革的另一位支持者——北宋大文学家、史学家欧
文本举例表并列
1.蔚然而深秀者;2.溪深而鱼肥;3.泉香而酒洌;4.起坐而喧哗者表递进
1.而年又最高;2.得之心而寓之酒也表承接
1.渐闻水声潺潺,而泻出于两峰之间者;2.若夫日出而林霏开,云归而岩穴暝;3.野
芳发而幽香,佳木秀而繁阴;4.水落而石出者;5.临溪而渔;6.太守归而宾客从也;7.人知从太守游而乐表修饰
学说说本文读来有哪些特点,为什么会有这些特点。(1)句法上大量运用骈偶句,并夹有散句,既整齐又富有变化,使文章越发显得音调铿锵,形成一种骈散结合的独特风格。如“野芳发而幽香,佳木秀而繁阴”“朝而往,暮而归,四时之景不同,而乐亦无穷也”。(2)文章多用判断句,层次极其分明,
- 1、下载文档前请自行甄别文档内容的完整性,平台不提供额外的编辑、内容补充、找答案等附加服务。
- 2、"仅部分预览"的文档,不可在线预览部分如存在完整性等问题,可反馈申请退款(可完整预览的文档不适用该条件!)。
- 3、如文档侵犯您的权益,请联系客服反馈,我们会尽快为您处理(人工客服工作时间:9:00-18:30)。
Page 1 of 2
查看文章 合理选择车刀几何角度
2009-01-06 23:41
摘要:合理选择车刀几何角度,有利于改善加工条件,提高被加工工件质量,延长刀具与设备的使用寿命,本文从车刀几何角度对切削力、切削热 和刀具耐用度影响等角度,分析车刀几何角度选择的一般原则。关键词:几何角度;切削力;切削热; 车刀几何角度是指车刀切削部分各几何要素之间,或它们与参考平面之间构成的两面角或线、面之间的夹角。它们分别决定着车刀 的切削刃和各刀面的空间位置。根据“一面二角”理论可知,车刀的独立标注角度有六个,它们分别是:确定车刀主切削刃位置的主偏角Kr和刃倾 角λs;确定车刀前刀面Ar与后刀面Aa的前角ro和后角ao;确定副切削刃及副后刀面Aa′的副偏角Kr′和副后角ao′。 这些几何角度对车削过程影响很大,其中尤其以主偏角Kr、前角ro、后角ao和刃倾角λs的影响更为突出,科学合理地选择车刀的几何角 度,对车削工艺的顺利实施起着决定性作用。下面就从车刀几何角度对切削力、切削热和刀具的耐用度的影响分析着手,本着使切削轻便、质量稳 定,延长刀具使用寿命的宗旨,确定科学的车刀几何角度的一般性原则。 一、车刀几何角度对切削力的影响 在金属切削时,刀具切入工件,将多余材料从工件上切除会产生强烈的力的作用,这些力统称为切削力。切削力主要来源于被加工材料 在发生弹性和塑性变形时的抗力和刀具与切屑及工件表面之间的摩擦作用。根据切削力产生的作用效果的不同,可将切削力分解成三个相互垂直方 向的分力。它们分别是:主切削力Fz,进给抗力Fx和切深抗力Fy,其中Fz是切削总力Fr沿主运动切向分解而得,是计算车刀强度,设计机床零件, 确定机床功率的主要依据;Fx也叫轴向力,它是Fr沿工件轴向的分力,是设计进给机构,计算车刀进给功率所必需的;Fy也叫径向力,它是Fr沿着 工件径向的分力,它不消耗机床功率,但是当机床或工艺系统刚度不足时,易引起振动。 (一)前角ro对切削力的影响 前角ro增大,剪切角Φ随着增大,金属塑性变形减小,变形系数ξ减小,沿前刀面的摩擦力减小,因此切削力减小。但对于脆性材料而 言,前角ro的变化则不会对车削力产生较大的影响,这是因为脆性材料在车削时,切屑变形和加工硬化都很小,变形抗力自然会随之减小。同时, 实验还证明,前角ro的增大,对切削分力Fx、Fy的影响程度也不一样,当主偏角Kr较大时,对Fx的影响较明显,而当主偏角Kr较小时,则对Fy的降 低幅度更大些。 (二)主偏角Kr对切削力的影响 主偏角Kr的改变,使得切削面积的形状和切削分力Fxy的作用方向改变,从而使切削力也随之变化。实验证明,主偏角Kr增大,切削厚 度也随之增大,切削变厚,切削层的变形减小,因此主切削力也随之减小,如图3所示。但当Kr增大到60°-75°后,Fz又随着Kr的增大而有所回 升,这是因为此时刀尖圆弧所占的切削工作比例增大,使切屑变形和排屑阻力增大,又使主切削力Fz增大。根据切削力分解公式:Fy=FxycosKr; Fx=FxysinKr可知,主偏角Kr增大,使Fy减小,Fx增大,这有利于减轻工件的变形和系统的振动。因此,在工程上我们往往采用较大主偏角的车刀 切削细长轴类零件,来减小径向分力Fy。 (三)刃倾角λs对切削力的影响 刃倾角λs对主切削力Fz影响很小,但对进给抗力Fx和切深抗力Fy的影响较大。当λs减小时,使刀具受到的正压力的方向发生了变化, 从而改变了切削合力Fr及其分力Fxy的作用方向,使Fy增大,Fx减小。由此可见,从切削力角度分析,切削时不宜选用过大的负刃倾角,否则会增 大Fy的作用而产生振动。 二、车刀几何角度对切削热的影响 车削过程所消耗的能量,除了极少部分用以形成新表面和潜藏能以外,绝大部分都转换为热能,以切削热的形式表现出来,使工艺系统 的温度升高。分析可知,车削时热量主要来源于切屑的变形功和前、后刀面的摩擦功。这些热量产生后又将通过切屑、工件、刀具和周围介质传 出,使产热与散热达到动态平衡状态,此时工艺系统的切削温度就是稳态切削温度。影响切削热与切削温度的因素很多,这里分析车刀几何角度对 其产生的影响。 (一)前角ro对切削温度的影响 前角增大,使切削力下降,切屑的变形和工艺系统的摩擦减轻,使产生的切削热减少,从而降低了切削温度。事实上,切削温度的高低 不仅取决于工艺系统产生热量的多少,还受工艺系统散热条件的影响。实验证明,当车工的前角增大到16°左右时,由于车刀的楔角减少后使刀具 的散热条件变差,切削温度反而有一些回升。 (二)主偏角Kr对切削温度的影响 主偏角Kr减小时,使切削宽度增大,切削厚度减小,切削变形和摩擦减轻,同时,切削宽度增大后,散热条件改善,又有利于降低切削 温度。因此,当工艺系统刚性足够时,采用小的主偏角切削,是降低切削温度、提高刀具的耐用度的一个重要措施,尤其是切削难加工材料时效果 更显著。 三、车刀几何角度对刀具耐用度的影响 车刀在切削加工过程中,受切屑和工件表面的摩擦,使用一段时间后,它就会钝化,从而失去其切削的能力,这时就要对刀具进行重磨 或更换刀片。刀具的耐用度就是用来衡量刀具连续切削时间长短的参量。它是指刀具从开始使用至达到磨损限度为止所用的切削时间,它是衡量刀 具切削性能的重要指标。由于刀具几何角度对耐用度的影响较大,合理选择刀具几何角度,可以大幅度提高刀具的耐用度,因此刀具的耐用度也是 衡量刀具几何角度先进与否的重要标志。 (一)前角ro对刀具耐用度的影响 适当增大前角,有利于减少切削力,降低切削温度,使刀具的耐用度提高。但是,如果前角增大到一定值以后,会使刀刃强度下降,散 热条件逐渐变差,而且刀刃易于产生破损,耐用度反而会下降。因此前角ro对刀具耐用度的影响呈山峰状,它的峰顶处前角值使刀具的耐用度最 高,切削不同的材料时,刀具的耐用度达到最高时的前角值也不相同。 (二)主偏角Kr对刀具耐用度的影响 主偏角减小,增加了刀具强度,改善了刀具的散热条件,使刀具的耐用度升高。另外,适当减小副偏角Kr′还能降低摩擦,提高刀具强 度,改善散热条件,使刀具耐用度升高。当然,随着主偏角Kr和副偏角Kr的减小,会使系统的切深抗力Fy增大,当系统刚性不足时,会引起振动而 影响加工质量。 四、如何选择科学合理的几何参数评价车刀的几何角度对车削工艺过程的影响,应该用辩证的观点去分析,同时还应该综合考虑车刀几 何角度对切削过程中的切削力、切削热和刀具耐用度的影响,选择科学合理的几何参数。 (一)车刀前角选择原则 前角主要影响切削过程中的变形和摩擦、刀具强度,改变散热条件,影响刀具的耐用度。选择前角时,应该综合考虑材料和加工工艺的 要求。一般认为,在刀具强度允许的条件下,尽量选用大前角。例如,高速钢的强度高、韧性好,硬质合金脆性大、怕冲击,因此,高速钢刀具的 前角可比硬质合金刀具的前角大5°左右,陶瓷刀具的脆性更大,前角不能太大。另外,如果被加工的材料导热系数低,应该选择小前角车刀,以改 善系统的散热效果,提高车刀的耐用度。特别需要说明的是,在加工高强度材料时,为了防止车刀的破损,常采用负前角,以提高车刀的使用寿 命。
/lishiguang007/blog/item/8804941388bc11055aaf53c7.html
2009-10-9
合理选择车刀几何角度_流金岁月
Page 2 of 2
(二)车刀后角的选择原则 后角主要影响切削时的摩擦和刀具强度。当工件材料的强度、硬度较高时,宜取较小后角,以提高刀具强度;当工艺系统刚性较差时, 应适当减小后角,防止系统产生振动;当加工精度要求较高时,应采用小后角。 (三)主偏角的选择原则 主偏角主要影响刀具强度、耐用度和工艺系统加工的稳定性。一般认为,在工艺系统刚性不足时,常取较大主偏角,以减小切削力。加 工高强度、高硬度材料时,取较小主偏角以提高刀具的耐用度。副偏角影响工件的表面质量和刀具强度,在系统不易产生振动和摩擦的条件下,应 选择较小的副偏角。 (四)车刀刃倾角的选择原则 刃倾角主要影响切屑的倾向和刀具的强度及其锋利程度。在无冲击的正常车削时,刃倾角一般取正值,如果切削时有间断冲击,选择负 刃倾角能提高刀头强度,保护刀尖。当系统刚性不足时,不宜采用负刃倾角,否则会因为切深抗力Fy的增大,引起系统的振动而影响加工质量。 类别:数控学习 | 添加到搜藏 | 浏览(1128) | 评论 (2) 上一篇:数控技术常用术语大全 下一篇:数控刀具的选择
相关文章:
• •
最近读者:
车刀几何角度如何测量 自动车床之车刀的几何角度及选择...
•
车刀几何参数的综合选择
登录后,您就出 现在这里。 haxbel 4993036160 wq69171225 jcj1983 zqm5309 hexi5200 44411434166 hefeibinbin 23
网友评论:
1
2009-02-21 13:06 | 回复
kbsakb 2 匿名网友
很好的知识! 2009-04-25 13:07 | 回复 很好,很详细!
发表评论:
姓
名:
注册 | 登录 (选填) 插入表情 闪光字
验证码:
请点击后输入四位验证码,字母不区分大log/item/8804941388bc11055aaf53c7.html
2009-10-9