铣刀加工工艺参数表
各种铣刀直壁加工规格参数表表全
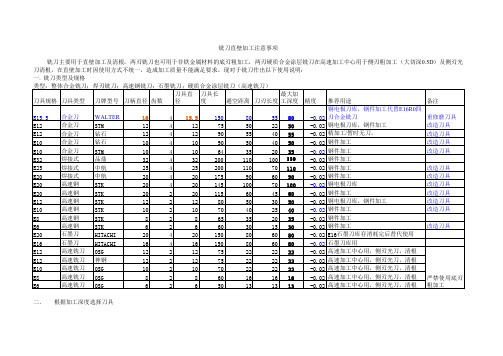
铣刀直壁加工注意事项铣刀主要用于直壁加工及清根,两刃铣刀也可用于非铁金属材料的底刃粗加工,两刃硬质合金涂层铣刀在高速加工中心用于侧刃粗加工(大切深0.5D )及侧刃光刀清根,在直壁加工时因使用方式不统一,造成加工质量不能满足要求。
现对于铣刀作出以下使用说明:一. 铣刀类型及规格类型:整体合金铣刀;焊刃铣刀;高速钢铣刀;石墨铣刀;硬质合金涂层铣刀(高速铣刀)刀具规格刀具类型刀牌型号刀柄直径齿数刀具直径刀具长度避空距离刀刃长度最大加工深度精度推荐用途备注E15.5合金刀WALTER 16415.5150805580-0.02铜电极刀库,钢件加工代替E16R0四刃合金铣刀重修磨刀具E12合金刀STM 1241275502250-0.02铜电极刀库,钢件加工改造刀具E12合金刀钻石1241290554055-0.02精加工/暂时无刀。
改造刀具E10合金刀钻石1041090504050-0.02钢件加工改造刀具E10合金刀STM 1041064352035-0.02钢件加工改造刀具E32焊接式品鼎32432200110100110-0.02钢件加工E25焊接式中航2542520011070110-0.02钢件加工改造刀具E20焊接式中航20420175906090-0.02钢件加工改造刀具E20高速钢STK 2042014510070100-0.02铜电极刀库改造刀具E20高速钢STK 20220115604560-0.02钢件加工改造刀具E12高速钢STK 1221280503050-0.02铜电极刀库,钢件加工改造刀具E10高速钢STK 1021070402540-0.02钢件加工改造刀具E8高速钢STK 82865352035-0.02钢件加工E6高速钢STK 62660301530-0.02钢件加工改造刀具E20石墨刀HITACHI 20420150806080-0.02E16石墨刀库存消耗完后替代使用E16石墨刀HITACHI 16416150806080-0.02石墨刀库用E12高速铣刀OSG 1221275222222-0.02高速加工中心用,侧刃光刀,清根严禁使用底刃粗加工E12高速铣刀神钢1221275222222-0.02高速加工中心用,侧刃光刀,清根E10高速铣刀OSG 1021070222222-0.02高速加工中心用,侧刃光刀,清根E8高速铣刀OSG 82860161616-0.02高速加工中心用,侧刃光刀,清根E6高速铣刀OSG62650131313-0.02高速加工中心用,侧刃光刀,清根二. 根据加工深度选择刀具优先选用大直径刀具,但要考虑刀具刃长,避免刀刃上下不等量磨损加工直壁40mm以內深度用D10;加工直壁40-50mm深度用D12;加工直壁50-80mm深度用D15.5;加工直壁60-90mm深度优选用D20;加工直壁70-100mm深度用D25;加工直壁100-110mm深度用D32;三.刀加工直壁注意事项:1.考虑刀具刃长,加工须分段加工,每次切深不能超过刀刃长度,推荐值为1.5D;2.程序编制要求刀路顺铣;3.精加工前,操作工须准确在机测刀并进行补偿;4.加工时优先选用风冷(干式切削),尽管切削液在润滑的情况下能获得更好的表面质量,但也存在让刀问题造成难以加工到位;5.严禁侧面底面同时加工,加工侧面深度让出底面0.05~0.1mm;6.侧面加工刀具刀刃可能有0.5x45°倒角,如须清出R0角请特殊注明。
数控铣削加工工艺范围及铣削方式

页脚内容1数控铣削加工工艺范围及铣削方式铣削是铣刀旋转作主运动,工件或铣刀作进给运动的切削加工方法。
铣削的主要工作及刀具与工件的运动形式如图所示。
在铣削过程中,根据铣床,铣刀及运动形式的不同可将铣削分为如下几种:(1)根据铣床分类根据铣床的结构将铣削方式分为立铣和卧铣。
由于数控铣削一个工序中一般要加工多个表面,所以常见的数控铣床多为立式铣床。
(2)根据铣刀分类根据铣刀切削刃的形式和方位将铣削方式分为周铣和端铣。
用分布于铣刀圆柱面上的刀齿铣削工作表面,称为周铣,如图6-2(a )所示;用分布于铣刀端平面上的刀齿进行铣削称为端铣,如图6-2(b )所示。
图中平行于铣刀轴线测量的切削层参数ap 为背吃刀量。
垂直于铣刀轴线测量的切削层参数ac 为切削宽度,fz是每齿进给量。
单独的周铣和端铣主要用于加工平面类零件,数控铣削中常用周、端铣组合加工曲面和型腔。
(3)根据铣刀和工件的运动形式公类根据铣刀和工作的相对运动将铣削方式分为顺铣和逆铣。
铣削时,铣刀切出工件时的切削速度方向与工件的进给方向相同,称为顺铣如图(6-3)a 所示;铣削时,铣刀切入工件时的切削速度方向与工件进给方向相反,称为逆铣,如图(6-3)b所示。
顺铣与逆铣比较:顺铣加工可以提高铣刀耐用度2~3倍,工件表面粗糙度值较小,尤其在铣削难加工材料时,效果更加明显。
铣床工作台的纵向进给运动一般由丝杠和螺母来实现,采用顺铣法加工时,对普通铣床首先要求铣床有消除进给丝杠螺母副间隙的装置,避免工作台窜动;其次要求毛坯表面没有破皮,工艺系统有足够的刚度。
如果具备这样的条件,应当优先考虑采用顺铣,否则应采用逆铣。
目前生产中采用逆铣加工方式的比较多。
数控铣床采用无间隙的滚球丝杠传动,因此数控铣床均可采用顺铣加工。
数控铣削主要特点(1)生产率高(2)可选用不同的铣削方式(3)断续切削(4)半封闭切削数控铣削主要加工对象(1)平面类零件页脚内容2加工面平行或垂直水平面,或加工面与水平面的夹角为定角的零件为平面类零件。
t型刀铣槽切削参数

T型刀铣槽切削参数引言切削加工是现代制造业中常见的一项工艺,其中T型刀铣槽切削是一种常见的切削方式。
本文将详细探讨T型刀铣槽切削参数的选择,包括刀具选择、切削速度、进给速度、切削深度等。
刀具选择选择适合的刀具对于T型刀铣槽切削非常重要,常用的刀具有整体硬质合金铣刀和可转位式硬质合金铣刀。
整体硬质合金铣刀整体硬质合金铣刀具有高硬度、高韧性和耐磨性的特点,适合加工硬质材料。
常用的整体硬质合金铣刀有柱铣刀、球铣刀和盘铣刀等。
可转位式硬质合金铣刀可转位式硬质合金铣刀由刀柄和刀片组成,具有可更换刀片的优势,因此适用于多种加工需求。
可转位式硬质合金铣刀分为高速钢刀片和硬质合金刀片两种,选择时需要考虑材料的硬度和加工要求。
切削速度切削速度是指刀具在切削过程中的线速度,通常用Vc表示。
切削速度的选择直接影响到切削效率和切削质量。
切削速度的计算切削速度的计算公式为Vc=π×D×n,其中Vc为切削速度,D为刀具直径,n为主轴转速。
切削速度的选择切削速度的选择需要考虑材料的硬度、刀具材料和加工要求等因素。
一般来说,对于硬度较高的材料应选择较低的切削速度,同时也需要根据刀具材料和加工要求合理选择切削速度。
进给速度进给速度是指刀具在每转完一圈时,进给到工件上的距离,通常用f表示。
进给速度的选择与切削速度密切相关,对于同一切削速度下,进给速度越大,切削深度越小。
进给速度的计算进给速度的计算公式为f=fz×Z×n,其中f为进给速度,fz为每齿切削进给量,Z 为刀具齿数,n为主轴转速。
进给速度的选择进给速度选择需要考虑切削质量和加工效率的平衡。
进给速度过大容易导致刀具磨损加剧,切削质量降低;进给速度过小则会降低加工效率。
因此,合理选择进给速度是保障切削质量和提高加工效率的关键。
切削深度切削深度是指刀具在一次切削中,与工件表面的相对距离,通常用ap表示。
切削深度的选择对切削过程中的切削力、切削温度和切削质量都有重要影响。
锯片铣刀切削速度计算【干货经验】
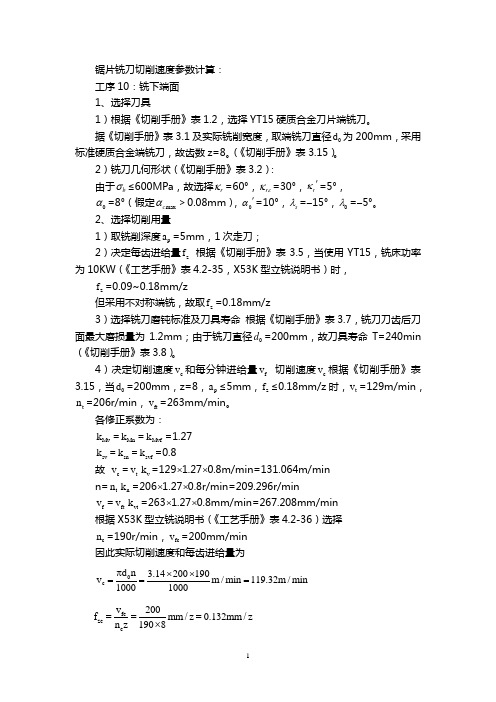
锯片铣刀切削速度参数计算: 工序10:铣下端面 1、选择刀具1)根据《切削手册》表1.2,选择YT15硬质合金刀片端铣刀。
据《切削手册》表3.1及实际铣削宽度,取端铣刀直径0d 为200mm ,采用标准硬质合金端铣刀,故齿数z=8。
(《切削手册》表3.15)。
2)铣刀几何形状(《切削手册》表3.2):由于b σ≤600MPa ,故选择r κ=60°,r εκ=30°,r κ'=5°,0α=8°(假定max c α>0.08mm ),0α'=10°,s λ=-15°,0λ=-5°。
2、选择切削用量1)取铣削深度p a =5mm ,1次走刀;2)决定每齿进给量z f 根据《切削手册》表3.5,当使用YT15,铣床功率为10KW (《工艺手册》表4.2-35,X53K 型立铣说明书)时,z f =0.09~0.18mm/z但采用不对称端铣,故取z f =0.18mm/z3)选择铣刀磨钝标准及刀具寿命 根据《切削手册》表3.7,铣刀刀齿后刀面最大磨损量为1.2mm ;由于铣刀直径0d =200mm ,故刀具寿命T=240min (《切削手册》表3.8)。
4)决定切削速度c v 和每分钟进给量f v 切削速度c v 根据《切削手册》表3.15,当0d =200mm ,z=8,p a ≤5mm ,z f ≤0.18mm/z 时,t v =129m/min ,t n =206r/min ,ft v =263mm/min 。
各修正系数为:Mv k =Mn k =Mvf k =1.27 sv k =sn k =svf k =0.8故 c v =t v v k =129⨯1.27⨯0.8m/min=131.064m/min n=t n n k =206⨯1.27⨯0.8r/min=209.296r/minf v =ft v vt k =263⨯1.27⨯0.8mm/min=267.208mm/min 根据X53K 型立铣说明书(《工艺手册》表4.2-36)选择c n =190r/min ,fc v =200mm/min 因此实际切削速度和每齿进给量为0c d n 3.14200190v m /min 119.32m /min 10001000π⨯⨯=== fc zc c v 200f mm /z 0.132mm /z n z 1908===⨯5)校验机床功率 根据《切削手册》表3.23,当b σ<560MPa ,e a ≤138mm ,p a ≤5.9mm ,0d =200mm ,z=8,f v =200mm/min ,近视为cc P =7.8KW根据X53K 型立铣说明书(《工艺手册》表4.2-35),机床主轴允许的功率为cM P =10⨯0.85KW=8.5KW故cc P <cM P ,因此所选择的切削用量可以采用,即p a =5mm ,f v =200mm/min ,n=190r/min ,c v =119.32m/min ,z f =0.132mm/z 。
各材料常用刀具转速进给参数对照表

各材料常用刀具转速进给参数对照表在机械加工领域,刀具的转速和进给参数对于加工质量、效率和成本都有着至关重要的影响。
不同的材料具有不同的物理和机械性能,因此需要根据材料的特性来选择合适的刀具转速和进给参数。
下面是一份常见材料的刀具转速进给参数对照表,希望能为您的加工工作提供一些参考。
一、铝合金铝合金是一种广泛应用于航空航天、汽车制造和电子工业等领域的轻质材料。
由于其良好的导热性和较低的强度,加工时需要较高的转速和较快的进给速度。
1、粗加工刀具:硬质合金立铣刀转速:3000 5000 rpm进给速度:800 1500 mm/min切削深度:2 5 mm切削宽度:刀具直径的 70% 80%2、半精加工刀具:硬质合金立铣刀转速:5000 8000 rpm进给速度:500 1000 mm/min切削深度:05 15 mm切削宽度:刀具直径的 50% 60%3、精加工刀具:硬质合金球头铣刀转速:8000 12000 rpm进给速度:200 500 mm/min切削深度:01 03 mm切削宽度:刀具半径的 20% 30%二、钢材钢材是机械加工中最常见的材料之一,其种类繁多,性能各异。
以下是常见钢材的加工参数。
1、低碳钢粗加工刀具:硬质合金涂层立铣刀转速:1500 2500 rpm进给速度:300 600 mm/min切削深度:3 6 mm切削宽度:刀具直径的 60% 70%半精加工刀具:硬质合金涂层立铣刀转速:2500 4000 rpm进给速度:200 400 mm/min切削深度:1 2 mm切削宽度:刀具直径的 40% 50%精加工刀具:硬质合金涂层球头铣刀转速:4000 6000 rpm进给速度:100 200 mm/min切削深度:01 02 mm切削宽度:刀具半径的 15% 20% 2、中碳钢粗加工刀具:硬质合金涂层立铣刀转速:1000 1800 rpm进给速度:200 400 mm/min切削深度:2 4 mm切削宽度:刀具直径的 50% 60%半精加工刀具:硬质合金涂层立铣刀转速:1800 3000 rpm进给速度:150 300 mm/min切削深度:05 10 mm切削宽度:刀具直径的 30% 40%精加工刀具:硬质合金涂层球头铣刀转速:3000 5000 rpm进给速度:80 150 mm/min切削深度:005 015 mm切削宽度:刀具半径的 10% 15% 3、高碳钢粗加工刀具:硬质合金涂层立铣刀转速:800 1200 rpm进给速度:100 200 mm/min切削深度:1 3 mm切削宽度:刀具直径的 40% 50%半精加工刀具:硬质合金涂层立铣刀转速:1200 2000 rpm进给速度:80 150 mm/min切削深度:03 08 mm切削宽度:刀具直径的 20% 30%精加工刀具:硬质合金涂层球头铣刀转速:2000 3500 rpm进给速度:50 100 mm/min切削深度:003 008 mm切削宽度:刀具半径的 8% 12%三、不锈钢不锈钢具有良好的耐腐蚀性和耐磨性,但加工难度较大,需要较低的转速和较慢的进给速度。
铣扁加工机的操作工艺流程、参数14.7
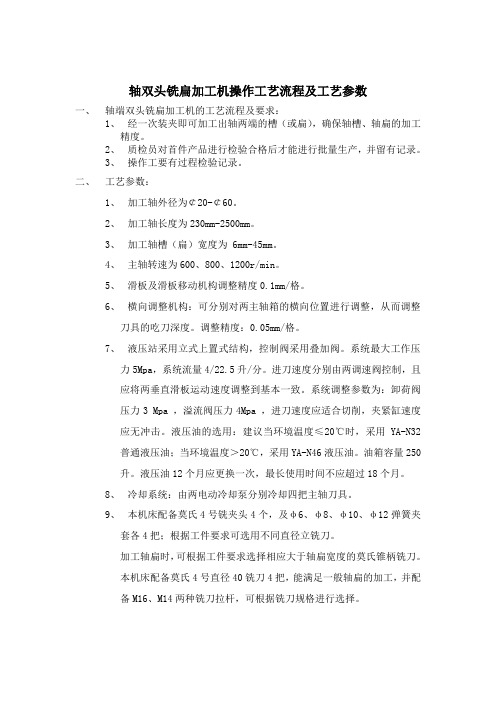
轴双头铣扁加工机操作工艺流程及工艺参数一、轴端双头铣扁加工机的工艺流程及要求:1、经一次装夹即可加工出轴两端的槽(或扁),确保轴槽、轴扁的加工精度。
2、质检员对首件产品进行检验合格后才能进行批量生产,并留有记录。
3、操作工要有过程检验记录。
二、工艺参数:1、加工轴外径为¢20-¢60。
2、加工轴长度为230mm-2500mm。
3、加工轴槽(扁)宽度为 6mm-45mm。
4、主轴转速为600、800、1200r/min。
5、滑板及滑板移动机构调整精度0.1mm/格。
6、横向调整机构:可分别对两主轴箱的横向位置进行调整,从而调整刀具的吃刀深度。
调整精度:0.05mm/格。
7、液压站采用立式上置式结构,控制阀采用叠加阀。
系统最大工作压力5Mpa,系统流量4/22.5升/分。
进刀速度分别由两调速阀控制,且应将两垂直滑板运动速度调整到基本一致。
系统调整参数为:卸荷阀压力3 Mpa ,溢流阀压力4Mpa ,进刀速度应适合切削,夹紧缸速度应无冲击。
液压油的选用:建议当环境温度≤20℃时,采用YA-N32普通液压油;当环境温度>20℃,采用YA-N46液压油。
油箱容量250升。
液压油12个月应更换一次,最长使用时间不应超过18个月。
8、冷却系统:由两电动冷却泵分别冷却四把主轴刀具。
9、本机床配备莫氏4号铣夹头4个,及φ6、φ8、φ10、φ12弹簧夹套各4把;根据工件要求可选用不同直径立铣刀。
加工轴扁时,可根据工件要求选择相应大于轴扁宽度的莫氏锥柄铣刀。
本机床配备莫氏4号直径40铣刀4把,能满足一般轴扁的加工,并配备M16、M14两种铣刀拉杆,可根据铣刀规格进行选择。
数控加工工艺过程卡

数控加工工艺过程卡数控加工是一种通过数控机床实现零件加工的技术,它具有高精度、高效率、高稳定性等优点,在现代制造业中得到广泛应用。
而数控加工工艺过程卡是对数控加工过程的描述和规范,它包含了零件的工艺流程、机床设备的参数设置、刀具的选用和刀具路径规划等信息。
以下是一个关于数控加工工艺过程卡的示例,供参考:零件名称:薄壁零件材料:铝合金6061加工精度:0.01mm加工工艺:铣削、钻孔、螺纹加工设备:数控铣床、数控钻床刀具:铣刀、钻孔刀、螺纹攻丝刀1.工艺流程:1.1首先根据图纸进行零件的准备和标记1.2将工件夹紧于数控铣床工作台1.3调整数控铣床的零点和坐标轴1.4选择合适的铣刀,装夹在数控铣床刀柄上1.5设置加工参数,确定切削速度和进给速度1.6进行主体加工,包括铣削外形和加工孔位1.7检验零件尺寸和形状是否满足要求2.设备参数设置(数控铣床):2.1设置工件夹具和工作台的夹紧力2.2调整数控铣床的零点和坐标轴2.3根据刀具类型和材料确定切削速度和进给速度2.4调整刀具的位置和切削深度2.5检查数控铣床的润滑系统是否正常运行3.刀具选用:3.1铣削外形:选择合适的面铣刀,刀径根据零件尺寸确定3.2钻孔:选择合适的钻孔刀,直径根据零件需求确定3.3螺纹加工:选择合适的螺纹攻丝刀,根据螺纹尺寸和规格确定4.刀具路径规划:4.1铣削外形:根据零件几何形状和加工要求,确定铣刀的切削路径和铣削方向4.2钻孔:根据孔位和孔径确定钻孔的位置和顺序4.3螺纹加工:根据螺纹的要求,确定攻丝刀的加工路径和攻丝顺序5.加工注意事项:5.1在加工过程中,保持加工液的供给和润滑系统的正常工作5.2在加工过程中,及时清理切削屑和切屑槽,以保证切削效果和切屑排出5.3加工前要检查工具刀具是否完好,并及时更换磨损或损坏的刀具通过对数控加工工艺过程的规范和描述,可以确保零件的加工质量和生产效率,提高工艺流程的标准化和规范化,为企业的生产制造提供有力的支持。
螺纹铣削工艺参数

螺纹铣削工艺参数螺纹铣削是一种常见的金属加工方法,用于在工件表面加工出螺纹。
螺纹铣削工艺参数的选择对于加工质量和效率至关重要。
本文将介绍螺纹铣削工艺参数的几个关键要素,并提供一些实用的参考建议。
1. 刀具选择螺纹铣削常用的刀具有螺纹铣刀和螺纹铣刀柄。
螺纹铣刀的选择应考虑工件材料、螺纹类型和加工要求等因素。
常见的螺纹铣刀有高速钢刀具、硬质合金刀具和立铣刀等。
根据工件材料的硬度和加工要求,选择合适的刀具材料和形状。
2. 加工参数螺纹铣削的主要加工参数包括切削速度、进给速度和切削深度。
切削速度是指刀具在单位时间内相对于工件表面的移动速度,一般使用米/分钟(m/min)作为单位。
进给速度是指刀具在单位时间内相对于工件表面的移动距离,一般使用毫米/转(mm/rev)作为单位。
切削深度是指刀具在每次切削中所削去的金属层的厚度,一般使用毫米(mm)作为单位。
针对不同的工件材料和螺纹要求,可以通过试切和实验确定合适的加工参数。
一般来说,切削速度和进给速度要根据工件材料的硬度和刀具的耐磨性来选择,切削深度要根据螺纹的要求和工件的强度来确定。
3. 切削液选择切削液在螺纹铣削中起到冷却、润滑和清洁的作用,能够提高加工质量和刀具寿命。
常见的切削液有液体切削油和乳化液等。
对于不同的工件材料和加工要求,选择合适的切削液是十分重要的。
切削液的选择要考虑到切削液的冷却性能、润滑性能和防锈性能等因素。
4. 夹具设计螺纹铣削过程中,夹具的设计对于工件的稳定性和加工精度有重要影响。
夹具应能够牢固固定工件,并保证工件与刀具的相对位置关系。
夹具的设计要考虑到工件的形状、尺寸和加工要求,以及加工过程中的力和振动等因素。
5. 工艺优化螺纹铣削的工艺参数选择不仅要满足加工要求,还要考虑到加工效率和经济性。
通过工艺优化,可以提高加工效率、降低成本和改善加工质量。
工艺优化的方法包括试切和实验、刀具磨损监测和切削力测量等。
总结起来,螺纹铣削工艺参数的选择需要综合考虑刀具选择、加工参数、切削液选择、夹具设计和工艺优化等因素。