化学工业常见事故及原因分析(正式)
化工火灾事故发生原因

化工火灾事故发生原因一、化工火灾的常见原因1. 人为操作失误化工火灾往往与人为操作失误密切相关。
在化工生产过程中,操作人员可能因疏忽大意、粗心马虎等原因,导致火灾的发生。
比如,在使用电焊、切割等高温作业时没有采取必要的安全措施,导致火灾的发生;未按规定操作,引发了事故等。
2. 设备故障化工生产过程中,设备故障可能是引发火灾的主要原因之一。
化工生产设备往往需要承受高温、高压等极端条件,一旦设备出现故障,可能引发火灾。
设备故障的原因可能是设备老化、维护不当、设计缺陷、材料缺陷等。
3. 火灾隐患在化工厂、仓库等场所,存在各种各样的火灾隐患。
比如:电气设备老化、线路短路;易燃易爆物品存放不当、操作不当等;安全设施不完善、未经定期检查等。
这些火灾隐患如果得不到及时排除,很容易引发火灾事故。
4. 自然灾害自然灾害也是导致化工火灾的原因之一。
比如:雷击引发火灾、地震引发设备故障、暴雨引发地质灾害等。
这些自然灾害在化工生产中可能造成严重后果。
5. 其他原因除了上述常见原因外,化工火灾还可能由其他原因引发,比如:恶意纵火、安全管理不当等。
二、化工火灾的预防措施1.加强安全教育培训为了预防化工火灾的发生,必须加强对操作人员的安全教育培训。
在化工生产过程中,操作人员应该具有一定的安全意识,清楚掌握化工生产操作规程,严格按照操作规程进行操作。
同时,还应不断加强安全知识培训,提高操作人员的安全意识。
2.加强设备检修维护为了减少设备故障引发火灾的可能性,必须加强对设备的检修维护工作。
确保设备具有良好的运行状态,避免因设备故障引发火灾事故。
定期对设备进行检查、维护,及时更换老化、磨损的设备部件。
3. 消防设施齐全化工厂、仓库等场所应该配备完备的消防设施,包括灭火器、消防水源、消防报警器等。
并且,定期对消防设施进行维护保养、演练等,确保在火灾发生时能够及时有效地进行灭火救援。
4. 加强安全管理在化工生产过程中,安全管理工作是至关重要的。
危化品事故多发原因分析及相应对策

危化品事故多发原因分析及相应对策一、发生有关危险化学品事故的原因分析1、企业安全投入不足。
安全投入不足,该更换、维修的设施、设备,没有能够按要求进行及时更换、维修,使化工生产装置出现老化,带病运行。
2、生产装置、设备老化,缺乏本质安全。
化工生产过程常伴有腐蚀性介质,生产设备、装置长期与具有腐蚀性的介质接触,就会造成生产装置、设备的老化,质量降低,加之维修和更新改造不落实,就很难做到本质安全。
3、从业人员安全素质较低。
企业的从业人员素质比较低,尤其在化工企业更为突出。
同时,安全知识和技能培训也不够,操作人员最起码的安全知识和意识都没有。
4、企业安全生产基础薄弱,安全管理有些放松。
企业安全基础差主要表现在事故隐患普遍存在,违规违章作业普遍存在。
一些行之有效的安全管理规章和制度被简化,国家规章不能严格执行。
5、受利益驱动,忽视安全生产。
一些企业为追求经济利益,不顾设备老化和生产装备存在缺陷等问题,开足马力生产化工产品,同时,又没有采取有效安全措施,致使事故多发并相对集中。
从根本上讲,这些事故还有更深层次的原因,一是安全认识不到位,安全意识不强,“安全第一”的思想和“以人为本”的理念还没有真正树立起来,企业重经济效益,轻安全生产,致使国家安全生产的法律法规和要求落实不下去,严不起来;二是安全生产专项整治工作进展不平衡,还存在“死角”。
安全专项整治工作存在要求不严、质量不高的问题,该整的没有整,该关的没有关°还存在以停代整、以停代关、明停暗开的现象;三是监管力度不足,难以保证安全生产法律、法规的有效实施。
二、安全措施及对策1、加大危险化学品安全专项整治的力度。
对不符合国家有关法律、法规和标准规定的安全生产条件的、存在事故隐患的、包括设备老化等,坚决责令停产整改;对整改后仍然达不到标准的,依法予以关闭。
目前化学品国际、国内市场仍处于旺势,更要防止少数企业受经济利益驱动,忽视安全生产,冒险违章蛮干。
化工厂事故案例分析(经典)

化工厂事故案例分析
• 2009年11月23日8时左右,菏泽海润化工有限公司刘喜林 给安全员郭凤田打电话说找到了运输粗苯的车辆,10时30 分左右刘喜林、郭凤田、穆勇敢三人在东明县石油公司油 库集合后,由穆勇敢驾驶运输粗苯的车(鲁R82660)一 起去菏泽海润化工有限公司小井乡黄庄储备库。11时30分 左右到达。他们到达1个多小时以后,运输车辆司机就把 车停到了存储罐前,连接好泵开始从储存罐往罐车里充装 粗苯,装有十五分钟的时候,穆勇敢上到罐车上查看前面 的罐口(罐的前后各有一个开启口),看装满没有。然后 又走到后面的罐口查看了一下,又走回前面的罐口附近对 刘喜林说装的太慢了,也就是在他们说话的同时,大概13 时17分时左右 • 发生了爆燃。然后罐车冒出浓烟。刘喜林从开始装车一直 在罐车上(后罐口附近),郭凤田在控制电泵的闸刀前,看 闸刀。郭凤田见此情况,就立即拉下闸刀,然后跑到储罐 前关掉储罐的阀门。郭凤田立即拨打119、120急救电话, 消防队来后把火扑灭。此次事故造成穆勇敢死亡,刘喜林 受伤。
• 3.防范措施 • (1)进一步完善建设项目安全许可工作,严格 按照"三同时"要求,落实各项规范要求,设计、 施工、试生产等各个阶段应严格按规范执行。 • (2)严格按照规范、标准要求开展日常设备的 监督检验工作,及时发现设备腐蚀等隐患。 • (3)严格按照技术规范进行操作,严禁超过工 艺规程允许范围运行。 • (4)进一步规范评价单位的评价工作,提高安 全评价报告质量,切实为企业提供安全保障。
化工行业安全事故案例分析报告

化工行业安全事故案例分析报告化工行业安全事故案例分析报告一、案例概述该案例是发生在某化工公司的一起重大安全事故。
事故发生在某年某月某日,造成了重大人员伤亡和财产损失。
事故的起因是某操作工不按规程操作,导致化学反应错误,再加上相关设备的故障,最终引发了一系列爆炸和火灾。
二、事故原因分析1.操作工不按规程操作:事故发生时的操作工因为工作经验不足和对操作规程不熟悉,没有按照规定的步骤进行操作,导致了化学反应的错误。
2.设备故障:与操作工的错误操作相结合,事故中发生了设备故障,导致反应条件的控制失效,反应产生的能量无法得到及时和有效的排放,进而引发了爆炸和火灾。
3.安全管理不到位:化工公司在工艺设计、设备维修和人员培训等方面的安全管理措施不到位。
工艺设计中应该有考虑设备的安全性和稳定性,并设置合适的技术和管理措施。
设备维修应及时维护,确保设备运行的正常和安全。
人员培训应强调工作流程和操作规程,确保员工对于化工操作的安全意识和操作能力。
三、事故影响及教训1.人员伤亡:事故导致多名员工和附近居民受伤,其中包括数名员工重伤和一些居民中毒。
这是一起十分严重的人身伤害事故,提醒我们在化工行业安全管理中,更要重视人身安全。
2.财产损失:事故导致了大量的生产设备损坏和化工品泄漏,造成了巨大的经济损失。
这一点提醒我们在安全管理中注重资源的保护和风险的控制。
3.环境污染:爆炸和火灾导致了大量的有毒气体和废水的排放,对周边的土壤、水源和空气环境造成了严重的影响。
化工行业必须要考虑环境保护和可持续发展,确保生产过程中不对环境造成不可逆转的损害。
四、防范措施和对策1.完善安全管理制度:加强安全管理,建立健全的安全管理制度和工艺管控体系,明确责任划分和操作规程,确保员工按照规定进行操作,减少人为失误的发生。
2.提高员工技能和安全意识:加强员工培训,提高员工的操作技能和安全意识,确保操作人员具备足够的知识和技能,理解危险源及应对方法。
化学品事故的原因分析与预防措施
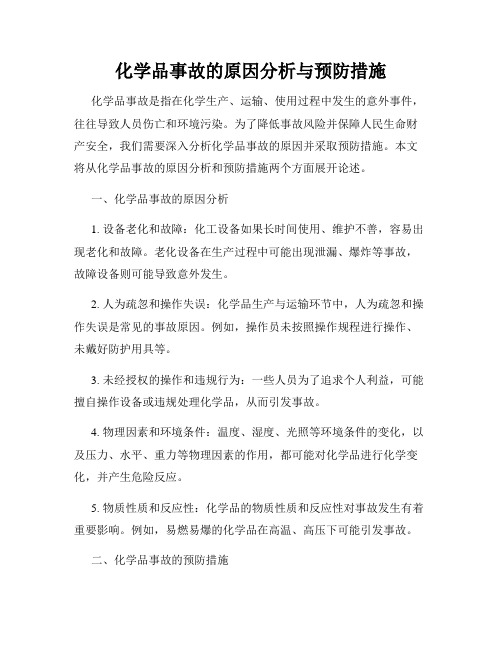
化学品事故的原因分析与预防措施化学品事故是指在化学生产、运输、使用过程中发生的意外事件,往往导致人员伤亡和环境污染。
为了降低事故风险并保障人民生命财产安全,我们需要深入分析化学品事故的原因并采取预防措施。
本文将从化学品事故的原因分析和预防措施两个方面展开论述。
一、化学品事故的原因分析1. 设备老化和故障:化工设备如果长时间使用、维护不善,容易出现老化和故障。
老化设备在生产过程中可能出现泄漏、爆炸等事故,故障设备则可能导致意外发生。
2. 人为疏忽和操作失误:化学品生产与运输环节中,人为疏忽和操作失误是常见的事故原因。
例如,操作员未按照操作规程进行操作、未戴好防护用具等。
3. 未经授权的操作和违规行为:一些人员为了追求个人利益,可能擅自操作设备或违规处理化学品,从而引发事故。
4. 物理因素和环境条件:温度、湿度、光照等环境条件的变化,以及压力、水平、重力等物理因素的作用,都可能对化学品进行化学变化,并产生危险反应。
5. 物质性质和反应性:化学品的物质性质和反应性对事故发生有着重要影响。
例如,易燃易爆的化学品在高温、高压下可能引发事故。
二、化学品事故的预防措施要防范化学品事故,我们应该采取以下预防措施:1. 加强设备维护和更新:定期检查和维护化工设备,更新老化设备,确保设备的安全可靠性。
2. 健全安全管理制度:建立严格的安全管理制度,包括安全标准、操作规程等,明确各岗位职责和安全操作要求。
3. 加强人员培训与教育:对从事化学品生产、运输和使用的人员进行全面的培训与教育,提高其安全意识和操作技能,减少人为疏忽和操作失误。
4. 建立应急预案和演练:制定科学合理的应急预案,明确事故发生时的应急措施和处理方法,并定期组织演练,提高应对突发事件的能力。
5. 加强监测与检测:建立完善的监测与检测体系,对化学品生产过程中的关键环节进行实时监测,发现异常情况及时采取措施。
6. 推广使用安全工艺和技术:引进和推广先进的安全工艺和技术,减少事故发生的可能性。
化工安全事故案例介绍及分析讨论

化工安全事故案例介绍及分析讨论化工安全事故是指在化工生产过程中突发的、意外的、造成人员伤亡、财产损失、环境污染等严重后果的事件。
化工行业的安全事故往往具有严重性、复杂性和多样性。
下面将介绍一起典型的化工安全事故案例,并进行分析和讨论。
案例:美国蒙塔纳州安那科达化工厂爆炸事故安那科达化工厂是美国最大的液化石油气生产厂家之一,2024年夜晚,该工厂发生了一次重大爆炸事故。
这起事故造成了8人死亡,数十人受伤,工厂设备损毁严重,导致巨额财产损失。
分析:1.原因分析:经过调查发现,该次爆炸事故是由于工厂压力容器内积存的液化石油气泄漏引起的。
事故发生前,工厂在检修、维护和管理等方面存在一系列问题,如设备老化、维护不到位、员工培训不到位等。
2.安全管理不到位:该化工厂事故的发生暴露了安全管理不到位的问题。
工厂在检修维护过程中,没有及时发现设备的存在问题并采取相应措施,导致液化石油气泄漏。
此外,工厂员工的安全意识和应急响应能力也存在缺陷,无法及时有效地应对事故。
3.环境污染问题:事故发生后,大量的液化石油气在厂区周围泄漏,引发了严重的环境污染。
该地区的空气和水源受到污染,给当地居民的健康造成了威胁。
讨论:该案例中的化工安全事故具有以下几个值得注意的问题:1.安全管理:化工企业在日常生产中应该加强安全管理,对设备进行定期检修和维护,并进行员工培训,提高员工的安全意识和应急响应能力。
此外,还应建立完善的安全管理制度和监督机制,确保安全管理工作的有效性。
2.风险评估:化工企业应在生产过程中进行全面的风险评估和控制,充分了解和掌握各个环节的风险点,并采取相应的防范措施。
在备份设备、应急措施、防范措施等方面进行科学规划和布局,以减少事故的发生和扩大。
3.环境保护:化工企业在生产过程中要严格遵守环境保护相关法律法规,使用环保技术和设备,控制污染物的排放,减少对环境的影响。
当事故发生时,应立即采取紧急措施,包括封锁泄漏源、清理污染物等,以避免进一步扩大事故影响。
化工厂事故案例分析
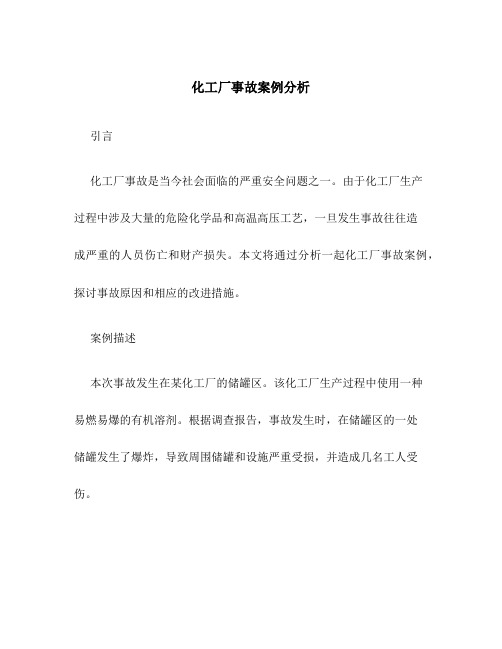
化工厂事故案例分析引言化工厂事故是当今社会面临的严重安全问题之一。
由于化工厂生产过程中涉及大量的危险化学品和高温高压工艺,一旦发生事故往往造成严重的人员伤亡和财产损失。
本文将通过分析一起化工厂事故案例,探讨事故原因和相应的改进措施。
案例描述本次事故发生在某化工厂的储罐区。
该化工厂生产过程中使用一种易燃易爆的有机溶剂。
根据调查报告,事故发生时,在储罐区的一处储罐发生了爆炸,导致周围储罐和设施严重受损,并造成几名工人受伤。
事故原因分析经过事故调查,我们可以得到以下事故原因:1.设备老化:事故发生的储罐在爆炸前存在较长时间的使用历史,其安全性能可能受到设备老化的影响。
2.操作失误:据工人回忆,储罐区在事故发生前没有进行预防性维护和检查,可能存在人为操作失误,比如没有正确关闭阀门。
3.通风不良:储罐区没有良好的通风系统,导致有机溶剂在储罐区内积聚,增加了爆炸的风险。
4.应急响应不足:事故发生后,化工厂的应急响应机制没有迅速启动,导致事故扩大。
改进措施为了避免类似的事故再次发生,化工厂应采取以下改进措施:1.定期检查和维护设备:对化工厂储罐等设备进行定期检查和维护,及时更换老化设备,确保其安全可靠运行。
2.严格操作规程:制定并强制执行操作规程,确保工人正确操作设备,如关闭和锁定阀门等。
3.完善通风系统:加强储罐区通风系统的设计和改造,确保有机溶剂不会积聚在储罐区内,减少爆炸的风险。
4.建立应急响应机制:建立健全的化工厂应急响应机制,包括事故报警和紧急疏散等程序,以及培训员工的应急处理技能。
5.安全培训和教育:加强对化工厂工人的安全培训和教育,提高他们的安全意识和应急处理能力。
结论化工厂事故的发生给人们的生命财产安全带来了巨大的威胁,因此,化工厂应始终将安全放在首位,采取必要措施防范和减少事故的发生。
本文通过分析一起化工厂事故案例,总结出了一些改进措施,希望能够对化工厂事故防范和安全管理提供一定的参考和借鉴价值。
化工企业安全事故原因分析及预防措施探讨

化工企业安全事故原因分析及预防措施探讨
一、原因分析
(一)设备设施技术滞后
当前,国内一些化工企业的生产设备设施仍存在技术滞后的现象,尤
其是涉及到有毒有害物质生产的企业,严重影响企业安全生产。
首先,民
用技术落后,许多企业都会采用老旧技术,而这种技术带来的风险也是显
而易见的;其次,生产技术滞后,由于一些企业生产的产品技术滞后,也
会对安全生产带来一定的风险。
(二)安全保障系统不完善
由于当前国内一些化工企业安全保障制度未建立,安全管理体系也欠缺,使得企业的安全保障系统不健全,本质上是设备设施技术未达到要求,管理技术也不行,仅仅依靠安全措施设备是无法保障企业安全的。
因此,
企业在安全保障过程中,需要牢牢建立安全责任制,加强安全培训,建立
完善的安全管理体系,以期能够真正的保障企业安全。
(三)操作不当
二、安全预防措施
(一)加强安全管理
企业在进行安全预防工作时,要加强安全管理,要牢牢建立安全责任制。
案例分析39、化工厂发生事故分析事故原因和预防措施[最终版]
![案例分析39、化工厂发生事故分析事故原因和预防措施[最终版]](https://img.taocdn.com/s3/m/8720edc29f3143323968011ca300a6c30c22f1d7.png)
案例分析39、化工厂发生事故分析事故原因和预防措施[最终版]第一篇:案例分析39、化工厂发生事故分析事故原因和预防措施[最终版]案例分析39、化工厂发生事故分析事故原因和预防措施天津创业化工厂是一家生产六溴—2,4—二硝基苯胺的村办企业。
该厂只有一座大厂房,内分3个车间;东车间生产中间产品2,4—二硝基苯胺,中间车间为备料车间,堆放着一袋袋强氧化剂氯酸钠、溴化物和2,4—二硝基苯胺。
1996半1月26日下午4时,有人发现该厂厂房中部的窗户冒出黑烟,大声喊救火,正在厂办公室的厂长和宿舍里的职工以及附近村民都赶来救火。
他们发现是备料车间的氯酸钠冒烟,于是从离厂房约十几米的废水塘里拎水灭火,泼了几桶后无效,厂长便叫人赶快运沙子灭火,没等沙子运到,只听两声巨响,一股黑烟直冲天空,面积约500平方米的厂房被夷为平地,前来救火的工人和村民死亡19人,受伤14人,直接经济损失120万元。
请分析事故原因以及应采取的预防措施。
参考答案:这是一起因企业未按规定储存化工物料,救火措施不当所造成的特大伤亡事故。
氯酸钠是一种强氧化剂,要用干燥牢固的铁桶外包装,里面还要加一层塑料袋和牛皮纸进行防潮。
强氧化剂单独存在并不会自燃,但如果把它和有机物放在一起,便会发生分解反应释放出热量。
本案例中,创业化工厂的氯酸钠的包装是里面一个塑料袋,外面加一个编织袋。
工人在用铁锹铲料时,难免把氯酸钠散落在外面。
发生事故的前几天,天津持续高温,26日室外温度33℃,厂房房顶是石棉瓦,隔热性差,厂房内温度达40cC,塑料袋和编织袋本身就是有机物,于是强氧化剂与有机物在高温下发生氧化反应放热,热量又加速了氧化反应,导致编织袋燃烧,引燃了旁边堆放的木头,冒出黑烟。
由于厂长和工人用废水塘里呈酸性的水灭火,强氧化剂氯酸钠遇酸反应产生大量氯酸,氯在40℃下就会发生爆炸,第一声巨响就是氯酸遇热发生的爆炸。
又由于备料车间同时堆放着2,4—二硝基苯胺,它遇高温高压气体冲击发生爆炸,产生第二声巨响,造成厂毁人亡。
化工安全管理中的事故案例与教训总结
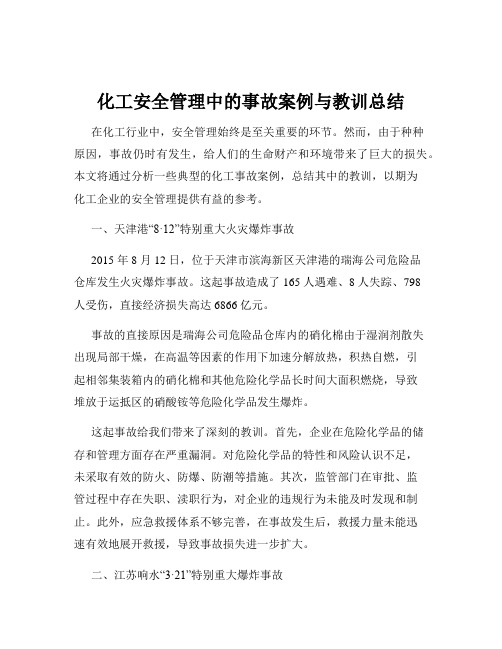
化工安全管理中的事故案例与教训总结在化工行业中,安全管理始终是至关重要的环节。
然而,由于种种原因,事故仍时有发生,给人们的生命财产和环境带来了巨大的损失。
本文将通过分析一些典型的化工事故案例,总结其中的教训,以期为化工企业的安全管理提供有益的参考。
一、天津港“8·12”特别重大火灾爆炸事故2015 年 8 月 12 日,位于天津市滨海新区天津港的瑞海公司危险品仓库发生火灾爆炸事故。
这起事故造成了 165 人遇难、8 人失踪、798人受伤,直接经济损失高达 6866 亿元。
事故的直接原因是瑞海公司危险品仓库内的硝化棉由于湿润剂散失出现局部干燥,在高温等因素的作用下加速分解放热,积热自燃,引起相邻集装箱内的硝化棉和其他危险化学品长时间大面积燃烧,导致堆放于运抵区的硝酸铵等危险化学品发生爆炸。
这起事故给我们带来了深刻的教训。
首先,企业在危险化学品的储存和管理方面存在严重漏洞。
对危险化学品的特性和风险认识不足,未采取有效的防火、防爆、防潮等措施。
其次,监管部门在审批、监管过程中存在失职、渎职行为,对企业的违规行为未能及时发现和制止。
此外,应急救援体系不够完善,在事故发生后,救援力量未能迅速有效地展开救援,导致事故损失进一步扩大。
二、江苏响水“3·21”特别重大爆炸事故2019 年 3 月 21 日,江苏省盐城市响水县陈家港镇化工园区内的江苏天嘉宜化工有限公司发生特别重大爆炸事故,造成 78 人死亡、76 人重伤,640 人住院治疗,直接经济损失达 19863507 万元。
事故的直接原因是天嘉宜公司长期违法贮存的硝化废料持续积热升温导致自燃,燃烧引发爆炸。
从这起事故中,我们可以看到企业安全意识淡薄,为了追求经济利益,无视安全生产法规和标准,违规储存危险化学品。
同时,地方政府和相关部门在安全监管方面存在宽松软的问题,对企业的违法违规行为监管不力。
此外,企业在安全风险评估和隐患排查治理方面存在严重不足,未能及时发现和消除潜在的安全隐患。
化工事故案例分析
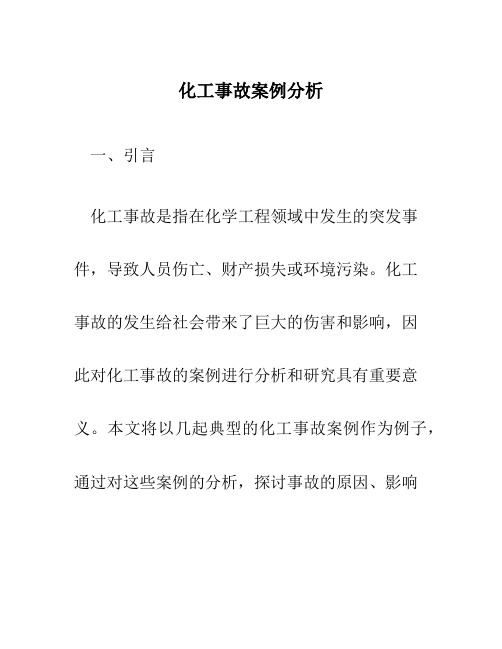
化工事故案例分析一、引言化工事故是指在化学工程领域中发生的突发事件,导致人员伤亡、财产损失或环境污染。
化工事故的发生给社会带来了巨大的伤害和影响,因此对化工事故的案例进行分析和研究具有重要意义。
本文将以几起典型的化工事故案例作为例子,通过对这些案例的分析,探讨事故的原因、影响以及相应的防范措施,以期提高人们对化工事故的认识和预防能力。
二、案例一:2005年美国得克萨斯州蒙塔瓦炼油厂爆炸1. 案例背景2005年3月23日,美国得克萨斯州蒙塔瓦炼油厂发生了一起严重的爆炸事故,该事故导致15人死亡,上百人受伤,造成巨大的财产损失。
该炼油厂是该地区最大的炼油厂,也是臭氧层破坏物质的主要制造商之一。
2. 事故原因分析经过调查,事故的原因主要有以下几个方面:(1)操作失误:操作人员未按照规定操作程序进行操作,导致了事故的发生。
操作人员在进行装载燃料过程中没有及时检查和修理卸油软管,最终导致了油气泄漏和爆炸。
(2)设备故障:事故中使用的设备存在一定的故障和缺陷。
在事故发生前,该炼油厂的监测系统未能及时发现油气泄漏,导致事故无法及时预警。
3. 事故影响及防范措施该次事故导致了严重的人员伤亡和财产损失,同时对环境产生了严重的污染。
为防止类似事故再次发生,可以从以下几个方面采取相应的防范措施:(1)加强操作培训:化工企业应加强对操作人员的培训,提高他们的操作能力和安全意识,确保操作规程得到严格执行。
(2)完善监测系统:加强对设备故障及时发现的能力,建立完善的监测系统,确保事故能够及时预警并进行相应的应对措施。
三、案例二:2015年中国天津港爆炸事故1. 案例背景2015年8月12日晚间,中国天津港发生了一起重大爆炸事故,该事故导致173人死亡,数百人受伤。
爆炸造成的巨大冲击波摧毁了大量附近的建筑物。
2. 事故原因分析经过调查,事故的原因主要有以下几个方面:(1)危险化学品储存不当:事故发生地点附近的仓库储存了大量危险化学品,包括硝酸铵等易燃易爆物品。
化学工业常见事故及原因分析
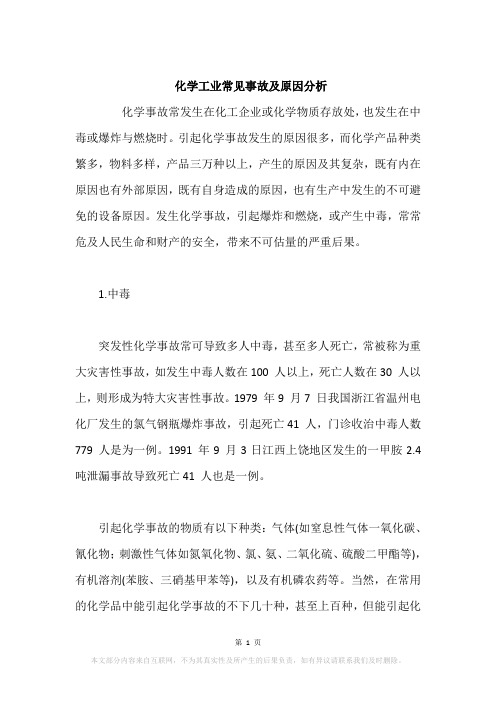
化学工业常见事故及原因分析
化学事故常发生在化工企业或化学物质存放处,也发生在中毒或爆炸与燃烧时。
引起化学事故发生的原因很多,而化学产品种类繁多,物料多样,产品三万种以上,产生的原因及其复杂,既有内在原因也有外部原因,既有自身造成的原因,也有生产中发生的不可避免的设备原因。
发生化学事故,引起爆炸和燃烧,或产生中毒,常常危及人民生命和财产的安全,带来不可估量的严重后果。
1.中毒
突发性化学事故常可导致多人中毒,甚至多人死亡,常被称为重大灾害性事故,如发生中毒人数在100 人以上,死亡人数在30 人以上,则形成为特大灾害性事故。
1979 年9 月7 日我国浙江省温州电化厂发生的氯气钢瓶爆炸事故,引起死亡41 人,门诊收治中毒人数779 人是为一例。
1991 年9 月3日江西上饶地区发生的一甲胺2.4 吨泄漏事故导致死亡41 人也是一例。
引起化学事故的物质有以下种类:气体(如窒息性气体一氧化碳、氰化物;刺激性气体如氮氧化物、氯、氨、二氧化硫、硫酸二甲酯等),有机溶剂(苯胺、三硝基甲苯等),以及有机磷农药等。
当然,在常用的化学品中能引起化学事故的不下几十种,甚至上百种,但能引起化
第 1 页
本文部分内容来自互联网,不为其真实性及所产生的后果负责,如有异议请联系我们及时删除。
化工安全事故案例介绍及分析讨论
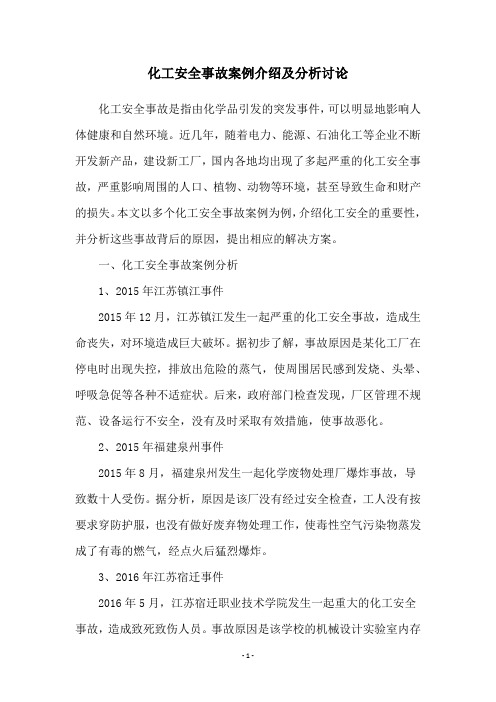
化工安全事故案例介绍及分析讨论化工安全事故是指由化学品引发的突发事件,可以明显地影响人体健康和自然环境。
近几年,随着电力、能源、石油化工等企业不断开发新产品,建设新工厂,国内各地均出现了多起严重的化工安全事故,严重影响周围的人口、植物、动物等环境,甚至导致生命和财产的损失。
本文以多个化工安全事故案例为例,介绍化工安全的重要性,并分析这些事故背后的原因,提出相应的解决方案。
一、化工安全事故案例分析1、2015年江苏镇江事件2015年12月,江苏镇江发生一起严重的化工安全事故,造成生命丧失,对环境造成巨大破坏。
据初步了解,事故原因是某化工厂在停电时出现失控,排放出危险的蒸气,使周围居民感到发烧、头晕、呼吸急促等各种不适症状。
后来,政府部门检查发现,厂区管理不规范、设备运行不安全,没有及时采取有效措施,使事故恶化。
2、2015年福建泉州事件2015年8月,福建泉州发生一起化学废物处理厂爆炸事故,导致数十人受伤。
据分析,原因是该厂没有经过安全检查,工人没有按要求穿防护服,也没有做好废弃物处理工作,使毒性空气污染物蒸发成了有毒的燃气,经点火后猛烈爆炸。
3、2016年江苏宿迁事件2016年5月,江苏宿迁职业技术学院发生一起重大的化工安全事故,造成致死致伤人员。
事故原因是该学校的机械设计实验室内存放大量可燃烧的易燃液体,但学校没有采用有效的安全防护措施,基本上没有任何消防设备。
当实验人员使用电锯时,电锯切割出的火花引爆了室内气体,造成大火灾。
二、化工安全问题分析从上述事故案例可以看出,化工安全事故对世界各地的人、物和环境都有极大的危害,每起事故都会带来极大的损失和伤害。
然而,这些事故大多是由于化学品管理不严格,监管不完善,政府机构缺乏整体的安全规划,以及人们缺乏安全意识所致。
为了解决化工安全事故问题,我们必须加强政策措施,进一步完善安全法规,建立和完善化学品管理制度,及时开展安全风险评估,加强安全技术监督,定期对安全管理人员进行培训,提高公众的安全意识,加强安全防范措施,及时发现和处理有潜在安全隐患的化学污染现象,以及推行有效的应急救援措施。
化工厂事故案例分析
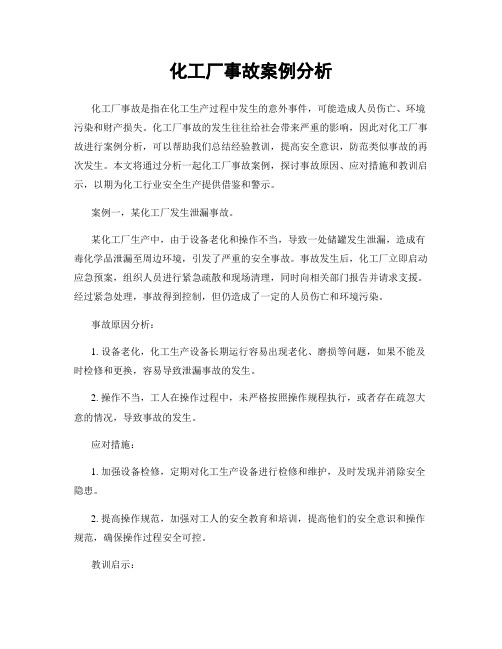
化工厂事故案例分析化工厂事故是指在化工生产过程中发生的意外事件,可能造成人员伤亡、环境污染和财产损失。
化工厂事故的发生往往给社会带来严重的影响,因此对化工厂事故进行案例分析,可以帮助我们总结经验教训,提高安全意识,防范类似事故的再次发生。
本文将通过分析一起化工厂事故案例,探讨事故原因、应对措施和教训启示,以期为化工行业安全生产提供借鉴和警示。
案例一,某化工厂发生泄漏事故。
某化工厂生产中,由于设备老化和操作不当,导致一处储罐发生泄漏,造成有毒化学品泄漏至周边环境,引发了严重的安全事故。
事故发生后,化工厂立即启动应急预案,组织人员进行紧急疏散和现场清理,同时向相关部门报告并请求支援。
经过紧急处理,事故得到控制,但仍造成了一定的人员伤亡和环境污染。
事故原因分析:1. 设备老化,化工生产设备长期运行容易出现老化、磨损等问题,如果不能及时检修和更换,容易导致泄漏事故的发生。
2. 操作不当,工人在操作过程中,未严格按照操作规程执行,或者存在疏忽大意的情况,导致事故的发生。
应对措施:1. 加强设备检修,定期对化工生产设备进行检修和维护,及时发现并消除安全隐患。
2. 提高操作规范,加强对工人的安全教育和培训,提高他们的安全意识和操作规范,确保操作过程安全可控。
教训启示:1. 安全意识不可忽视,化工生产是高风险行业,企业和员工都需要高度重视安全意识,时刻保持警惕,严格执行操作规程。
2. 应急预案要健全,化工企业应建立完善的应急预案,定期组织演练,确保在事故发生时能够迅速、有效地处置。
通过对以上化工厂事故案例的分析,我们可以看到,化工生产事故的发生往往是由于设备老化、操作不当等多种因素叠加所致。
因此,化工企业在安全生产方面需要加强设备检修和维护,提高员工的安全意识和操作规范,健全应急预案,以期减少类似事故的发生,保障生产安全和人员健康。
同时,政府部门也需要加强对化工企业的监管和指导,推动化工行业安全生产工作的持续改进和提升。
化工事故分析报告
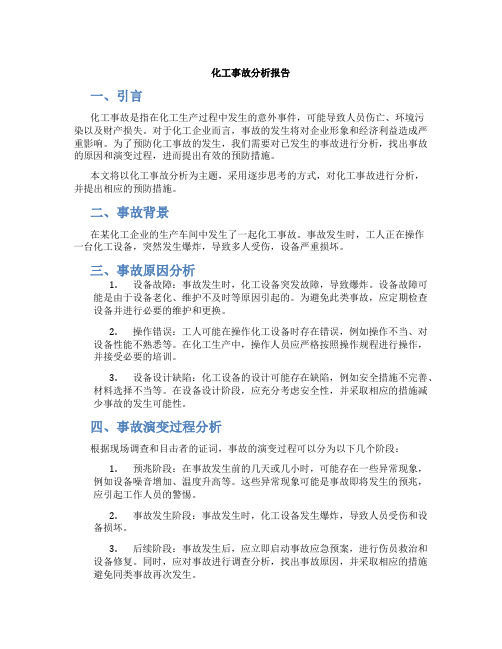
化工事故分析报告一、引言化工事故是指在化工生产过程中发生的意外事件,可能导致人员伤亡、环境污染以及财产损失。
对于化工企业而言,事故的发生将对企业形象和经济利益造成严重影响。
为了预防化工事故的发生,我们需要对已发生的事故进行分析,找出事故的原因和演变过程,进而提出有效的预防措施。
本文将以化工事故分析为主题,采用逐步思考的方式,对化工事故进行分析,并提出相应的预防措施。
二、事故背景在某化工企业的生产车间中发生了一起化工事故。
事故发生时,工人正在操作一台化工设备,突然发生爆炸,导致多人受伤,设备严重损坏。
三、事故原因分析1.设备故障:事故发生时,化工设备突发故障,导致爆炸。
设备故障可能是由于设备老化、维护不及时等原因引起的。
为避免此类事故,应定期检查设备并进行必要的维护和更换。
2.操作错误:工人可能在操作化工设备时存在错误,例如操作不当、对设备性能不熟悉等。
在化工生产中,操作人员应严格按照操作规程进行操作,并接受必要的培训。
3.设备设计缺陷:化工设备的设计可能存在缺陷,例如安全措施不完善、材料选择不当等。
在设备设计阶段,应充分考虑安全性,并采取相应的措施减少事故的发生可能性。
四、事故演变过程分析根据现场调查和目击者的证词,事故的演变过程可以分为以下几个阶段:1.预兆阶段:在事故发生前的几天或几小时,可能存在一些异常现象,例如设备噪音增加、温度升高等。
这些异常现象可能是事故即将发生的预兆,应引起工作人员的警惕。
2.事故发生阶段:事故发生时,化工设备发生爆炸,导致人员受伤和设备损坏。
3.后续阶段:事故发生后,应立即启动事故应急预案,进行伤员救治和设备修复。
同时,应对事故进行调查分析,找出事故原因,并采取相应的措施避免同类事故再次发生。
五、预防措施建议基于对事故原因和演变过程的分析,我们提出以下预防措施建议:1.加强设备检修和维护:对化工设备进行定期检查、维护和更换,确保设备的正常运行和安全性。
2.加强操作人员培训:对操作人员进行专业培训,提高他们的操作技能和安全意识,确保他们能够正确、安全地操作化工设备。
化工安全事故典型案例分析

氯乙酸氯化岗位玻璃冷却器爆炸事故1. 事故经过:2007年10月25日上午10:30分,某化工厂氯乙酸工段C1氯化釜系统玻璃冷却器突然发生爆炸。
其中C1氯化釜三楼九节玻璃冷却器全部炸坏,炸坏后的碎片造成附近D2 、E1 、E2等三台氯化釜共七节玻璃冷却器不同程序的损坏。
爆炸发生后,当班人员迅速关闭氯化系统相关阀门,氯化岗位做紧急停车处理,氯乙酸其他结晶、离心包装等岗位未受到影响,生产保持正常运行。
经维修人员紧急检查、抢修后,氯化岗位于11:00部分氯化釜恢复开车(4主4副),下午18:30分氯化系统开满正常。
这次事故由于设备造成的直接经济损失约为2万余元,并且爆炸后形成的酸雾向周围弥散,造成极坏的影响。
2. 事故调查:1)C1氯化釜停用前后的情况调查:根据查看相关记录,该氯化釜最后一次投料使用时间为10月13日下午15:36,到14日21:00转为主釜,在15日15:00氯化反应中期发现釜体穿孔后停用。
停用后,工段组织人员对通氯阀、进出水阀等进行了关闭,并对釜内料液进行了抽空处理。
2)化验室人员对氯乙酸氯化系统相关气体及该氯化釜釜内残液(约500㎏)等进行了化验分析,具体结果如下:a)主釜尾气组成:HCl:64.5%;Cl2:1.75%;H2/Cl2:3.17%;b)副釜尾气组成:HCl:73%;H2/Cl2:3.15%;c)氯化釜釜内残液:HAc 34.55%;HCl 2.10%;另外氯化釜残液内含有大量Fe2+离子。
3)维修人员对该氯化釜分配台通氯胶囊阀、釜上通氯玻璃阀及釜上DN100气相大阀进行检查,发现以上氯气和气相阀门关不死,存在内漏现象。
4)维修人员对氯化釜水洗处理后,打开釜盖后进行了仔细检查,发现氯化釜内穿孔两处,距离釜底圆弧以上400mm处(方向分别为西南侧一处,孔径φ8mm),同时发现穿孔处上下共约600mm宽的釜体出现一周脱瓷。
3. 事故原因分析:1)由于该氯化釜几处通氯阀门内漏,造成氯气进入氯化釜系统内。
化工常见事故案例及原因分析【最新资料】

化工常见事故及原因分析一、分析化工常见事故原因的意义在经济全球化的浪潮中,化学工业的发展十分迅速,在我国工业经济结构中起着十分重要的作用。
但同时我们也应看到,化工生产面临的安全和环境问题十分严重,化工生产的原料和产品范围广、种类多,且大部分属易燃易爆,有毒有害物质。
化工生产过程复杂,工艺多样,操作控制标准严格,但部分企业片面的追求经济效益,忽视企业的生产安全,减少安全方面的资金投入和人员安排,从而导致很多事故的发生,给国家人民的生命财产安全带来了极大的危害。
在消防部队的火灾和应急救援战例中,化工事故占了很大比重。
一名基层中队的指挥员,应当掌握一定的化工技术知识,具备一定的处臵常见化工事故的能力,才能在接警出动后迅速的将事故的危害降到最低,防止事态的扩大和蔓延,妥善的进行人员救护和现场处理,圆满的完成作战任务。
因此,讨论化工常见事故及发生的原因,将有助于提高基层指挥员应对和处臵此类事件的能力,在目前化工安全形势严峻的情况下,是十分必要的。
二、化工企业存在的消防安全隐患经验总结认为化工企业有以下消防安全隐患:(1)企业的火灾危险性级别高,极易造成重大人员伤亡和财产损毁。
(2)企业使用、存放的危险化学物品种类、数量繁多,发生化工事故易造成环境污染和火灾发生。
(3)厂房车间设计复杂,危险物品的储罐星罗棋布,运输管线纵横交错,对被困人员和消防官兵的生命安全构成巨大威胁,加大了灭火救援的难度。
另外,化工火灾不但火情复杂,蔓延迅速,往往还会有层出不穷的次生灾害,如有毒气体、液体的泄漏、扩散会严重威胁到被困人员和消防官兵的生命安全;腐蚀性物质会损坏个人防护装备、灼伤救援人员,还会损坏救援器材,使之难以发挥作用;建筑物倒塌会造成人员被埋,发生群死群伤的严重后果。
这些都给消防部队执行灭火救援任务带来了巨大的难度。
因此,消防部队在处臵化工事故时,应当全面掌握现场的化学危险品情况,及时的采取关阀断料、堵漏等措施,防止爆炸、火灾及有毒物品泄漏,将其对人员财产及环境的危害降到最低。
化工安全事故的常见原因分析及预防措施
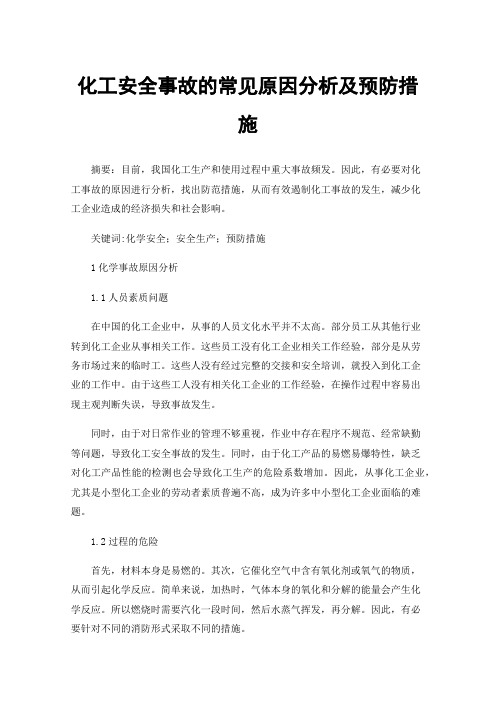
化工安全事故的常见原因分析及预防措施摘要:目前,我国化工生产和使用过程中重大事故频发。
因此,有必要对化工事故的原因进行分析,找出防范措施,从而有效遏制化工事故的发生,减少化工企业造成的经济损失和社会影响。
关键词:化学安全;安全生产;预防措施1化学事故原因分析1.1人员素质问题在中国的化工企业中,从事的人员文化水平并不太高。
部分员工从其他行业转到化工企业从事相关工作。
这些员工没有化工企业相关工作经验,部分是从劳务市场过来的临时工。
这些人没有经过完整的交接和安全培训,就投入到化工企业的工作中。
由于这些工人没有相关化工企业的工作经验,在操作过程中容易出现主观判断失误,导致事故发生。
同时,由于对日常作业的管理不够重视,作业中存在程序不规范、经常缺勤等问题,导致化工安全事故的发生。
同时,由于化工产品的易燃易爆特性,缺乏对化工产品性能的检测也会导致化工生产的危险系数增加。
因此,从事化工企业,尤其是小型化工企业的劳动者素质普遍不高,成为许多中小型化工企业面临的难题。
1.2过程的危险首先,材料本身是易燃的。
其次,它催化空气中含有氧化剂或氧气的物质,从而引起化学反应。
简单来说,加热时,气体本身的氧化和分解的能量会产生化学反应。
所以燃烧时需要汽化一段时间,然后水蒸气挥发,再分解。
因此,有必要针对不同的消防形式采取不同的措施。
1.3安全漏洞目前,随着中国经济的快速发展,企业之间的竞争日益激烈。
为了在激烈的市场竞争中取得有利地位,必须加大设备更新和技术研究,同时加强现有生产设备和硬件,严格控制成本,以增加公司的经济效益。
很多化工企业只注重经济效益,经常出现一些以次充好的现象。
很多企业的安全管理设施达不到相关法律法规的要求,造成很大的危险性和不安全性。
而很多公司的管理者,因为没有足够的安全意识,即使发现了安全漏洞也不及时解决,造成很多安全隐患。
此外,化工企业的安全漏洞大多是由于安全管理不到位、生产法律法规不健全、相关部门监管不到位、安全投入不足等原因造成的,都是事故的安全隐患。
化工火灾事故及分析

化工火灾事故及分析化工行业是一种高危行业,由于其生产过程中频繁使用化学物质,容易引发火灾事故。
化工火灾事故不仅造成人员伤亡和财产损失,还对环境造成了不可逆转的影响。
因此,对化工火灾事故进行全面的分析和探讨,有助于减少事故发生的概率,提高化工行业的安全水平。
一、化工火灾事故概述1. 化工火灾事故的定义化工火灾事故是指在化工生产或储存过程中,由于各种原因引起的火灾事故。
这种事故不仅会造成人员伤亡和财产损失,而且还会对周围环境产生严重的污染和危害。
2. 化工火灾事故的发生原因(1)生产过程中使用的化学物质易燃易爆,一旦泄漏或混合,就会引发火灾事故。
(2)生产设备老化、维护不当,导致设备故障,从而引发火灾事故。
(3)人为操作不当,违反安全操作规程或经验,容易引发火灾事故。
(4)自然灾害等外部因素也可能导致化工火灾事故的发生。
3. 化工火灾事故的危害(1)人员伤亡:化工火灾会造成人员伤亡,给员工和周围群众带来不可逆转的伤害。
(2)财产损失:化工火灾会造成建筑物、设备和原料的损失,给企业造成巨大的经济损失。
(3)环境污染:化工火灾会释放大量的有害气体和污染物,严重影响周围环境的质量,对生态环境造成长期的危害。
4. 化工火灾事故的应对措施(1)加强安全生产教育培训,提高员工对安全生产的重视和认识。
(2)对生产设备进行定期检查、维护和更新,确保设备的正常运行。
(3)加强日常巡检和管理,及时发现潜在的安全隐患,采取措施消除隐患。
(4)建立健全的安全管理体系,严格执行安全操作规程,加强事故应急预案的制定和演练。
二、化工火灾事故的分析1. 化工火灾事故的类型化工火灾事故可分为火灾、爆炸和泄露,其中火灾是最常见的一种。
火灾:火灾是指由于化学反应、设备故障或人为因素等引起的火焰的事故。
火灾会造成建筑物、设备和物资的损失,严重时还会造成人员伤亡和环境污染。
爆炸:爆炸是指在气体、液体或固体物料中发生的瞬间剧烈放热、释放能量的现象。
- 1、下载文档前请自行甄别文档内容的完整性,平台不提供额外的编辑、内容补充、找答案等附加服务。
- 2、"仅部分预览"的文档,不可在线预览部分如存在完整性等问题,可反馈申请退款(可完整预览的文档不适用该条件!)。
- 3、如文档侵犯您的权益,请联系客服反馈,我们会尽快为您处理(人工客服工作时间:9:00-18:30)。
编订:__________________
单位:__________________
时间:__________________
化学工业常见事故及原因
分析(正式)
Deploy The Objectives, Requirements And Methods To Make The Personnel In The Organization Operate According To The Established Standards And Reach The Expected Level.
Word格式 / 完整 / 可编辑
文件编号:KG-AO-4889-59 化学工业常见事故及原因分析(正
式)
使用备注:本文档可用在日常工作场景,通过对目的、要求、方式、方法、进度等进行具体、周密的部署,从而使得组织内人员按照既定标准、规范的要求进行操作,使日常工作或活动达到预期的水平。
下载后就可自由编辑。
化学事故常发生在化工企业或化学物质存放处,也发生在中毒或爆炸与燃烧时。
引起化学事故发生的原因很多,而化学产品种类繁多,物料多样,产品三万种以上,产生的原因及其复杂,既有内在原因也有外部原因,既有自身造成的原因,也有生产中发生的不可避免的设备原因。
发生化学事故,引起爆炸和燃烧,或产生中毒,常常危及人民生命和财产的安全,带来不可估量的严重后果。
1.中毒
突发性化学事故常可导致多人中毒,甚至多人死亡,常被称为重大灾害性事故,如发生中毒人数在100 人以上,死亡人数在30 人以上,则形成为特大灾害性事故。
1979 年9 月7 日我国浙江省温州电化厂发
生的氯气钢瓶爆炸事故,引起死亡41 人,门诊收治中毒人数779 人是为一例。
1991 年9 月3日江西上饶地区发生的一甲胺2.4 吨泄漏事故导致死亡41 人也是一例。
引起化学事故的物质有以下种类:气体(如窒息性气体一氧化碳、氰化物;刺激性气体如氮氧化物、氯、氨、二氧化硫、硫酸二甲酯等),有机溶剂(苯胺、三硝基甲苯等),以及有机磷农药等。
当然,在常用的化学品中能引起化学事故的不下几十种,甚至上百种,但能引起化学事故的物质一定要有基本条件,即毒物易弥散,而散发时有较多的人接触。
从实际发生的情况看,化学事故多集中在某几种化学物质上:氯气、氨气、氮氧化物、二氧化碳、硫化氢、硫酸二甲酯、光气等,主要由刺激性气体和窒息性气体组成,占全部中毒事故的75%以上。
而其中氯气、一氧化碳、氨气三类化合物所致的化学事故占55%左右。
这些毒物所占比例如此之高是不难理解的,首先,它们是化学工业中的化肥、氯碱、合成纤维、炼油、染料、医药、
军工生产中最基本的原料,也是产品和副产品。
在化工、石油化工、石油等产业中应用和接触十分广泛和密切的也是常见的有害气体。
其次,由于刺激性气体遇水即可生成酸或碱,腐蚀性很强,常使设备、管线损坏,发生跑、冒、滴、漏,外逸的气体极易通过呼吸道进入人体而导致人体中毒。
2.爆炸和燃烧
爆炸和燃烧是化学事故中另一重要的原因,1949~1984 年全国石油化工企业发生的化学事故5899 起,设备原因占很大比重。
从大量的化工设备发生的爆炸与燃烧事故可以看出以下特点。
①爆炸事故屡见不鲜。
1979~1988 年10 月间,据全国28 个省市化肥、化工、炼油行业的不完全统计,共发生化工设备与机器的爆炸事故252 起,占全部事故的45.7%,多是由于违章指挥与操作、设备缺陷、操作人员素质低而造成。
②相同事故接连不断,同台设备连续发生相同事
故。
例如:煤气发生炉水夹套超压爆炸;停车检修前,未予置换或置换不合格,盲目动火;未与生产设备隔绝,动火引起爆炸。
③重大恶性事故时有发生。
1989 年8 月29 日,辽宁本溪市某化工厂聚氯乙烯车间设备人孔和轴处大量泄漏,引起燃烧爆炸,死亡12 人,伤5 人。
1972 年4 月15 日,山西省某化肥厂运输氨罐车在途中发生爆炸,死亡21 人,重伤56 人,轻伤99 人。
④设备缺陷问题严重。
a.在设备缺陷中,因设计问题而导致的设备缺陷,特别是致燃烧和爆炸屡见不鲜,1982~1986 年压缩机因设计而致的事故约占50%左右。
b.材质不符要求,铸造、焊接质量低劣,阀门质量不佳导致事故的比比皆是。
c.因设计、制造缺陷原因而发生汽缸开裂次数占全部汽缸的64%。
请在这里输入公司或组织的名字
Enter The Name Of The Company Or Organization Here。