动力电池PACK生产线

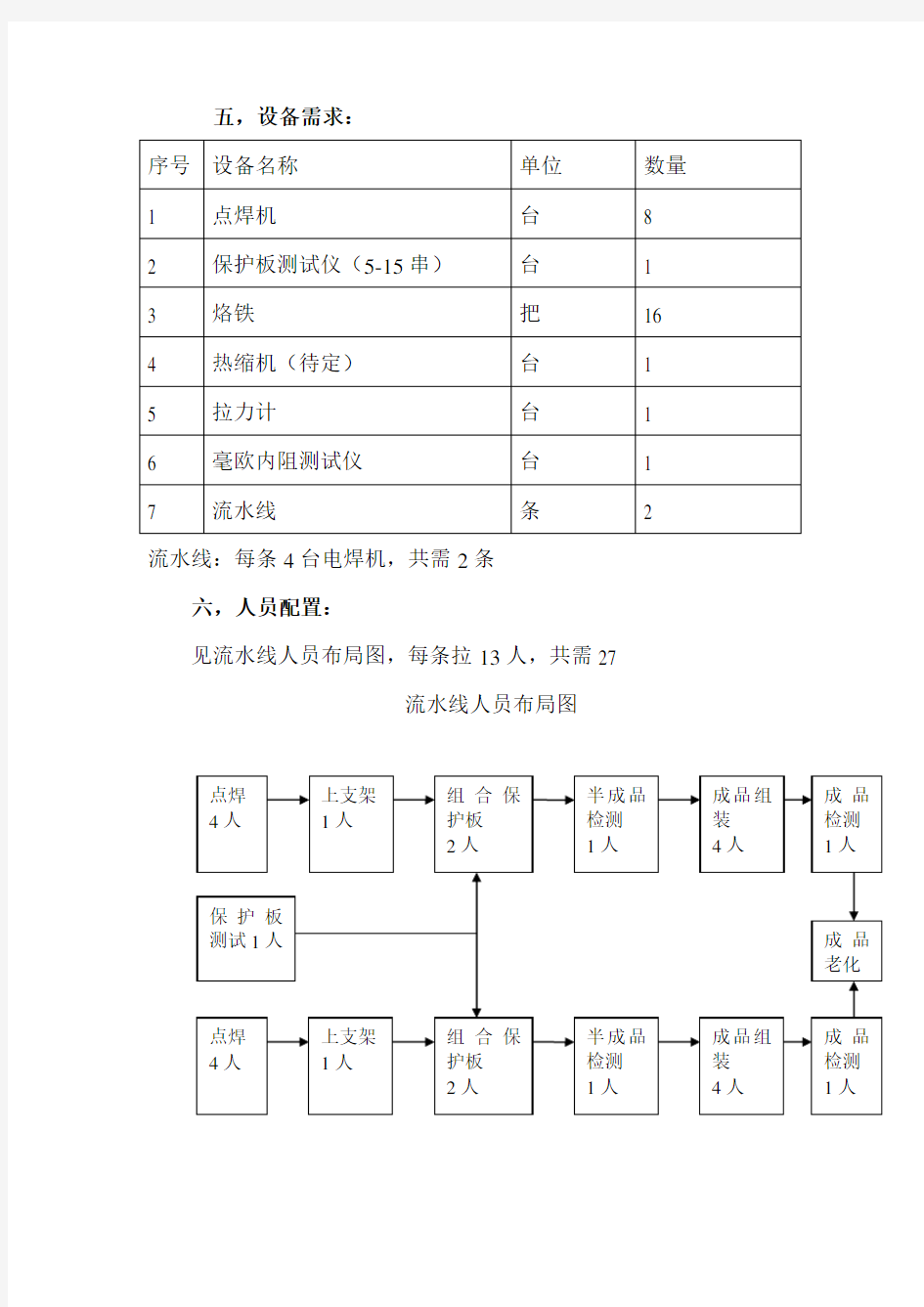
关于筹建动力电池PACK生产线(初稿)
一,动力电池PACK生产线的任务:
负责PT和LEV电池组产品的样品制作及电池组小批量的生产,同时为将来可能的大批量生产做准备。
二,产能规划:
折算成36V/10AH电池组,即100组/天;
折算成6串19.2V/1.1AH电池组,即组/天。
三,工艺流程(讨论):
①LEV:保护板检测(全检)—电池点焊—焊点检测—上支架—焊接保护板—半成品检测—壳体组装—成品老化。
②PT:保护板检测(全检)—电池点焊—焊点检测—焊接保护板—成品检测—成品老化
③相关工艺文件:制定中
四,产能计算:
①以LEV 36V/10AH(3并11串26650)计算:点焊每组需30min,焊接保护板每组需15min,壳体组装每组需30min,所以每台点焊机每天(8小时)能点15组,由此计算共需8台点焊机(产能120组/天)。
②以PT 19.2V/1.1AH(6串18650)计算:点焊每组需7min,焊接保护板每组需5min,所以每台点焊机每天(8小时)能点65组,由此计算8台点焊机的产能520组/天。
五,设备需求:
流水线:每条4台电焊机,共需2条
六,人员配置:
见流水线人员布局图,每条拉13人,共需27
流水线人员布局图
七,PACK产线布局图:见附件“最新布局图”
动力电池pack生产工艺流程
动力电池pack生产工艺流程_动力电池PACK四大工艺介绍 2018-04-17 17:13 ? 885次阅读 动力电池PACK四大工艺 1、装配工艺 动力电池PACK一般都由五大系统构成。 那这五大系统是如何组装到一起,构成一个完整的且机械强度可靠的电池PACK呢?靠的就是装配工艺。 PACK的装配工艺其实是有点类似传统燃油汽车的发动机装配工艺。 通过螺栓、螺帽、扎带、卡箍、线束抛钉等连接件将五大系统连接到一起,构成一个总成。
2、气密性检测工艺 动力电池PACK一般安装在新能源汽车座椅下方或者后备箱下方,直接是与外界接触的。当高压电一旦与水接触,通过常识你就可以想象事情的后果。因此当新能源汽车涉水时,就需要电池PACK有很好的密封性。 动力电池PACK制造过程中的气密性检测分为两个环节: 1)热管理系统级的气密性检测; 2)PACK级的气密性检测; 国际电工委员会(IEC)起草的防护等级系统中规定,动力电池PACK 必须要达到IP67等级。
2017年4月份的上海车展,上汽乘用车就秀出了自己牛逼的高等级气密性防护技术。将充电状态下的整个PACK放到金鱼缸中浸泡7天,金鱼完好无损,且PACK内未进水。 3、软件刷写工艺 没有软件的动力电池PACK,是没有灵魂的。 软件刷写也叫软件烧录,或者软件灌装。 软件刷写工艺就是将BMS控制策略以代码的形式刷入到BMS中的CMU和BMU中,以在电池测试和使用过程中将采集的电池状态信息数据,由电子控制单元进行数据处理和分析,然后根据分析结果对系统内的相关功能模块发出控制指令,最终向外界传递信息。
4、电性能检测工艺 电性能检测工艺是在上述三个工艺完成后,即产品下线之前必做的检测工艺。 电性能检测分三个环节: 1)静态测试: 绝缘检测、充电状态检测、快慢充测试等; 2)动态测试; 通过恒定的大电流实现动力电池容量、能量、电池组一致性等参数的评价。 3)SOC调整; 将电池PACK的SOC调整到出厂的SOC SOC:StateOfCharge,通俗的将就是电池的剩余电量。 关于电池PACK的电性能检测参数,每个公司其实都有自己定义的标准,都不一样。但是国家对于新能源汽车动力的电性能要求是有规定的,国标如下: 《GB/T31484-2015电动汽车用动力蓄电池循环寿命要求及试验方法》《GB/T31486-2015电动汽车用动力蓄电池电性能要求及试验方法》
动力电池组PACK流水线生产方案
动力电池组PACK流水线生产方案一、锂电芯PACK生产流程 二、电池组加工工序
三、设备清单 工序机器名称型号单价机器数工位人参考图片备注
量 数 电芯分选 (人工)内阻仪 DH-R308 1500 4 4 效率慢,建议选择分选机 自动分选机 FX-105 35000 1 1 高效率高精度 点焊 气动点焊机 DH-2018 17000 2-4 2-4 人工点焊 单面自动点焊机 DH-10000 65000 1-2 1-2 自动点焊效率高 双面自动点焊机 DH-20000 130000 1-2 1-2 效率是单面自动点焊的两倍 焊锡 人工 人工 2-3 焊BMS 人工 人工 1-2 焊连接线 人工 人工 1-2 半成品测试 电池综合测试仪 DH-6030 16000 1 支持60V30A 电池测试(可定制) 套PVC 人工 人工 1 PVC 吹塑 人工 人工 1 收缩机 热缩机 3千瓦 3800 1 1 可代替人工 PVC 吹塑
成品老化电池老化柜60V20A600011根据情况选择购买数量 方案一: 工厂产量要求不高,出始投入较低,大部分采用人工操作。流水线机器配置如下:4台内阻仪+4台点焊机+1成品检测综合测试仪+成品老化柜(3-4个点),设备投入大概12万-13万,可建成一条标准的电池组流水线。人员配置约16-18个人 方案二: 工厂生产需求大,可大部分采用自动化机器.流水线自动化机器配置如下:自动分选机1台(五通道)+1台点焊机+单面自动点焊机1台+(或者1台双面自动点焊机)+热缩膜机+ 1成品检测综合测试仪+1成品老化柜(8-10个点,根据实际需求购买),设备投入大概15万-25万(如果选双面自动点焊机大概25万),人员配置约10-12人。 方案三: 初步打样阶段,主要为客户制作样品,小批量试产,设备清单如下: 电池精密内阻仪一台,8通道分容柜一台,气动储能动力电池点焊机1台,60V20A动力电池老化机一台,总投入在3万以内,如果对电池品质要求高,可选配加多一台动力电池综合测试仪一套,1.8万左右。
中国第一条汽车动力电池PACK生产线
一、前言 我国在新能源汽车方面投入力度很大,列为科技部重大专项课题,目前已有多种混合动力新能源汽车样车问世,许多汽车企业陆续发布新车上市时间表,国务院近期出台了鼓励发展新能源汽车的扶持政策,显然,发展新能源汽车是国际共识,中国各地都在下大力气研发建设,如天津的电动汽车生产基地,深圳比亚迪的双模铁电池混合汽车,不久前合肥电动汽车已下线上路行驶,当地政府大力支持并特别颁发了上路牌照,此外还有浙江准备大力推出适合农村市场需要的微型电动汽车,价格不到万元人民币,在专家们还在争论我国到底发展哪种新能源结构车型时,各地方政府及企业已经因地制宜、实事求是地发展自己的新能源汽车产业了。 无论是何种新能源汽车,几乎都不排斥电池的作用,包括油电混合动力汽车、燃料电池汽车以及纯电动汽车,而在汽车动力电池方面,除了低成本的铅酸电池外,现在开始使用镍氢电池,近期将陆续推出锂动力电池,锂动力电池的综合性能目前最符合混合动力汽车的要求,世界各国,尤其汽车强国日本和美国,都在大力发展锂电池生产技术规模,我国也一哄而上,生产锂动力电池的企业不下百家。 锂动力电池目前的技术瓶颈是如何提高成品率从而降低成本,在保证单体电芯安全性的前提下实现大规模成组的动态充放电一致性,在足够功率放电的同时具有足够的循环使用寿命。现有的生产设备、工艺流程、电池管理系统均存在缺陷,换句话说,目前企业尚不能稳定生产合格的锂动力电池组,至少国内企业是这样,有专家明确指出,我国现在还没有一条真正的汽车动力电池PACK生产线,如果不能快速解决这个问题,不但上百家电芯生产企业发展受阻,而且也会严重影响我国相关新能源汽车产业发展,反之,如果实现产业化,不但能满足国内整车市场的需要,更能解决国际庞大的市场之需,业内预计,新能源汽车专用锂动力电池每年需求上亿块,产值数万亿,谁也吃不下,与太阳能电池产业类似,将数年呈供不应求态势,而且订单只会向少数技术拥有企业过分集聚。 我们辛苦钻研八年之久,终于在锂动力电池的生产、控制方面取得了一系列技术突破,并拥有完全自主知识产权,可以整合现有的国内外单体电芯生产技术资源,突出解决电芯与整车用户之间的PACK问题,与地方政府和投资商一起,共同建立我国第一条汽车锂动力电池组PACK生产线。
锂电池pack生产线可行性报告
年产值3000万锂离子电池pack生产线项目 可行性研究报告 编制: 审核: 批准: 日期:2015-4-10 1.总论 1.1项目名称 年产3000万元锂电pack生产线项目 1.2项目概况 1.2.1建设目标 本项目建设的目标是:到2017年建成年产值3000万元的锂电pack生产线,本项目分三期完成,一期2015年拟建成年产值500万元的锂电PACK生产线,二期到2016年拟建成年产值1000万元的锂电pack生产线,三期到2017年拟建成年产值3000万元的锂电pack生产线,通过外购电芯,自行检测包装组合,再到市场推广,逐步积累经验、培养人才、最后形成市场口碑、优质客户等,为公司进入锂电池的电芯制造打下良好的基础。 1.2.2产品线以及拟建规模 建设期产品名称拟建规模 一期圆柱(18650) 普通型年产值500万 二期软包装普通型年产值500万 三期圆柱(18650) 动力型+普通型年产值1000万
软包装普通型+动力型年产值1000万合计(三期建成后) 年产值3000万建设期内容时间 一期编制一期设备清单2015.4.20前厂房规划2015.4.25前设备调研2015.5.10前设备采购2015.6.1前设备安装调试2015.7.1前人员培训2015.7.5前 二期编制二期设备清单2016.1.30前厂房规划2016.2.5前设备调研2016.2.20前设备采购2016.3.15前设备安装调试2016.4.20前人员培训2016.4.25前 三期编制三期设备清单2017.2.15前厂房规划2017.2.25前设备调研2017.3.25前设备采购2017.4.30前设备安装调试2017.6.10前人员培训2017.6.15前 (1)一期设备投资预计 类别名称型号用途 单台产 能支 /10h 数 量 / 台 总产 能支 /10h 单价 /万元 价格 /万元 生圆柱锂离子盈创容量检测1500 3 4500 3 9
动力电池PACK制造四大工艺的简介
动力电池PACK制造四大工艺的简介整车制造有四大工艺,分别是:冲压、焊接、喷涂和总装。动力电池PACK也有四大工艺。分别是: 1、装配工艺; 2、气密性检测工艺; 3、软件刷写工艺; 4、电性能检测工艺; 下面简单介绍下动力电池PACK的制造四大工艺。 一、装配工艺 动力电池PACK一般都由五大系统构成。 那这五大系统是如何组装到一起,构成一个完整的且机械强度可靠的电池PACK呢?靠的就是装配工艺。 PACK的装配工艺其实是有点类似传统燃油汽车的发动机装配工艺。 通过螺栓、螺帽、扎带、卡箍、线束抛钉等连接件将五大系统连接到一起,构成一个总成。 二、气密性检测工艺 动力电池PACK一般安装在新能源汽车座椅下方或者后备箱下方,直接是与外界接触的。当高压电一旦与水接触,通过常识你就可以想象事情的后果。因此当新能源汽车涉水时,就需要电池PACK有很好的密封性。 动力电池PACK制造过程中的气密性检测分为两个环节: 1)热管理系统级的气密性检测; 2)PACK级的气密性检测; 国际电工委员会(IEC)起草的防护等级系统中规定,动力电池PACK必须要达到IP67等级。 三、软件刷写工艺 没有软件的动力电池PACK,是没有灵魂的。 软件刷写也叫软件烧录,或者软件灌装。 软件刷写工艺就是将BMS控制策略以代码的形式刷入到BMS中的CMU和BMU中,以在电池测试和使用过程中将采集的电池状态信息数据,由电子控制单元进行数据处理和分析,然后根据分析结果对系统内的相关功能模块发出控制指令,最终向外界传递信息。 四、电性能检测工艺 电性能检测工艺是在上述三个工艺完成后,即产品下线之前必做的检测工艺。
动力电池pack生产工艺流程
四PACK生产工艺流程_动力电池动力电池pack大工艺介绍 2018-04-17 17:13 ? 885次阅读 动力电池PACK四大工艺 1、装配工艺 动力电池PACK一般都由五大系统构成。 那这五大系统是如何组装到一起,构成一个完整的且机械强度可靠的电池PACK呢?靠的就是装配工艺。 PACK的装配工艺其实是有点类似传统燃油汽车的发动机装配工艺。 通过螺栓、螺帽、扎带、卡箍、线束抛钉等连接件将五大系统连接到一起,构成一个总 成。. 、气密性检测工艺2一般安装在新能源汽车座椅下方或者后备箱下方,直PACK 动力电池
接是与外界接触的。当高压电一旦与水接触,通过常识你就可以想象事情PACK 有很好的密封性。的后果。因此当新能源汽车涉水时,就需要电池PACK制造过程中的气密性检测分为两个环节:动力电池)热管理系统级的气密性检测; 1 PACK级的气密性检测;2)PACKIEC)起草的防护等级系统中规定,动力电池国际电工委员会( 等级。IP67必须要达到. 2017年4月份的上海车展,上汽乘用车就秀出了自己牛逼的高等级气密性防护技术。将充电状态下的整个PACK放到金鱼缸中浸泡7天,金鱼完好无损,且PACK内未进水。 3、软件刷写工艺 没有软件的动力电池PACK,是没有灵魂的。 软件刷写也叫软件烧录,或者软件灌装。 软件刷写工艺就是将BMS控制策略以代码的形式刷入到BMS中的CMU和BMU中,以在电池测试和使用过程中将采集的电池状态信息数据,由电子控制单元进行数据处理和分析,然后根据分析结果对系统内的相关功能模块发出控制指令,最终向外界传递信息。
4、电性能检测工艺 电性能检测工艺是在上述三个工艺完成后,即产品下线之前必做的检测工艺。电性能检测分三个环节: 1)静态测试: 绝缘检测、充电状态检测、快慢充测试等; 2)动态测试; 通过恒定的大电流实现动力电池容量、能量、电池组一致性等参数的评价。3)SOC调整; 将电池PACK的SOC调整到出厂的SOC SOC:StateOfCharge,通俗的将就是电池的剩余电量。 关于电池PACK的电性能检测参数,每个公司其实都有自己定义的标准,都不一样。但是国家对于新能源汽车动力的电性能要求是有规定的,国标如下:《GB/T31484-2015电动汽车用动力蓄电池循环寿命要求及试验方法》 电动汽车用动力蓄电池电性能要求及试验方法》GB/T31486-2015《
浅谈锂电池模组与PACK系列
浅谈锂电池模组与PACK系列---两大市场形态 自1990年问世以来,因其能量密度高、电压高、环保、寿命长以及可快速充电等优点,深受3C数码、动力工具等行业的追捧,特别是对新能源汽车行业的贡献尤为突出。作为提供新能源汽车动力来源的市场潜力巨大,不仅仅是国家战略发展的重要一环,预计未来5到10年,其产业链将实现行业生态的自我 完善和发展,产业规模有望突破1600亿元。 众所周知,从锂电池单体电芯到自动化模组再到PACK生产线的整个过程中,组装线的自动化程度是决定产品质量与生产效率的重要因素。近几年,随着经验的增加和自动化集成能力的提升,国内高端智能装备制造企业在打造动力电池全自动/ 半自动组装线、自动化设备集成、信息采集与传输(MES)、无人化车间软硬件管理系统等方面大展拳脚并占据一席之地。本文将从国内电池模组与PACK 设备特点和市场需求出发,抛砖引玉,浅析当前市场形态。 电池模组 是由几颗到数百颗电池芯经由并联及串联所组成的多个模组,除了机构设计部分,再加上电池管理系统和热管理系统就可组成一个较完整的锂电池包系统。一般而言,不管是软包、方形、圆柱还是18650型电池,模组的自动化组装工艺流程都是从电芯上料开始。来料可以是原供应商提供的包装,也可以是厂家经过检测后统一整理好的专用托盘。上料过程可以是人工操作,也可以通过传送带自动上料,然后通过机器人经由抓手抓取。上料的同时还会进行电芯的读码(采集单个电芯的身份数据信息)、电芯极性检测(有无放反方向)、电芯分选及配组,并将不良品剔除。来料通过初检和分选之后,根据模组和工艺要求的不同会分别进行诸如激光清洁-涂胶-电芯堆叠-电池盒组装-极耳裁切整形-模组壳激光焊接-模组激光打码-打螺丝-模组检测-连接片激光焊接-BMS系统连接-模组终检测-模组下料等 锂电池模组 目前,由于市场上各家汽车厂商的要求不同,几乎没有一家的模组和生产工艺是一样的,而这也对自动化产线提出了更多的要求。好的自动化生产线除了满足以上硬件配置和工艺要求以外,还需要重点关注兼容性和“整线节拍”。由于模组的不固定,故来料的电芯、壳体、PCB板、连接片等都可能发生变化,产线
动力电池PACK制造四大工艺的简介
动力电池PACK制造四大工艺的简介 整车制造有四大工艺,分别是:冲压、焊接、喷涂和总装。动力电池PACK也有四大 工艺。分别是: 1、装配工艺; 2、气密性检测工艺; 3、软件刷写工艺; 4、电性能检测工艺; 下面简单介绍下动力电池PACK的制造四大工艺。 一、装配工艺 动力电池PACK一般都由五大系统构成。 那这五大系统是如何组装到一起,构成一个完整的且机械强度可靠的电池PACK呢? 靠的就是装配工艺。 PACK的装配工艺其实是有点类似传统燃油汽车的发动机装配工艺。 通过螺栓、螺帽、扎带、卡箍、线束抛钉等连接件将五大系统连接到一起,构成一个 总成。 二、气密性检测工艺 动力电池PACK一般安装在新能源汽车座椅下方或者后备箱下方,直接是与外界接触的。当高压电一旦与水接触,通过常识你就可以想象事情的后果。因此当新能源汽车涉水时,就需要电池PACK有很好的密封性。 动力电池PACK制造过程中的气密性检测分为两个环节: 1)热管理系统级的气密性检测; 2)PACK级的气密性检测; 国际电工委员会(IEC)起草的防护等级系统中规定,动力电池PACK必须要达到 IP67等级。 三、软件刷写工艺 没有软件的动力电池PACK,是没有灵魂的。 软件刷写也叫软件烧录,或者软件灌装。 软件刷写工艺就是将BMS控制策略以代码的形式刷入到BMS中的CMU和BMU中,以在电池测试和使用过程中将采集的电池状态信息数据,由电子控制单元进行数据处理和 分析,然后根据分析结果对系统内的相关功能模块发出控制指令,最终向外界传递信息。四、电性能检测工艺 电性能检测工艺是在上述三个工艺完成后,即产品下线之前必做的检测工艺。