铜丝分析改善方案
电工用铜线的性能和提高铜线质量的对策

电工用铜线的性能和提高铜线质量的对策黄崇祺【摘要】2006年我国的铜导体用量已达到354万t,其中电磁线用铜已接近100万t,约占整个电线电缆行业用铜总量的28%,在电缆行业中,对铜线质量要求最高的也是铜电磁线,特别是微细和超微细漆包线,而且还有柔软性的特殊要求.影响铜线质量的链是很长的,从原材料铜的冶炼、制杆、制线、退火(包括拉线退火和漆包退火);合理选材、按铜杆质量分等使用;加强铜杆进出厂检验、铜线生产过程中间检验、采用特殊的可退火性检验方法,以及制订电线电缆行业的铜杆标准和采购规范等都是提高铜线质量的有效对策.【期刊名称】《电线电缆》【年(卷),期】2008(000)003【总页数】7页(P1-7)【关键词】电工;铜杆;铜线;质量;对策【作者】黄崇祺【作者单位】上海电缆研究所,上海,200093【正文语种】中文【中图分类】TM244.11 影响电工用铜线性能的主要因素1.1 铜杆质量是关键在电工铜线生产中铜杆是质量的中心,也是供需双方争议的焦点,也是期货市场中“阴极铜牌号注册”等级评定的依据之一。
影响铜导体生产的质量链是很长的,影响因素很多,互有因果关系(见图1),但技术核心和发展方向就在于要提高铜杆的“可轧性”、“可拉性”和“可退火性”等“三性”。
目前,特别在大量废杂铜直接用于生产电工用铜杆的情况下,“三性”问题就显得比较突出。
用户经常会问连铸连轧低氧铜杆和上引法无氧铜杆有哪些区别?铜杆分等使用的标准、铜杆和铜线的质控预警判别试验方法何在?本文将作概要的研讨,期待制杆厂、拉线厂、电线电缆厂通过实践,积累数据和经验,以求统一,为制订线缆产品的专用标准奠定基础。
1.2 选材不当影响铜线生产的技术经济效果由连铸连轧法生产的光亮低氧铜杆和由上引法生产的光亮无氧铜杆在本质上是有区别的。
因而,对不同质的铜杆应有其最佳的适用范围,并相应地匹配不同的最佳拉线和退火工艺,以取得最佳的技术经济效果。
过去有一种商业性的宣传:“无氧铜杆生产不出柔软的铜线”,从技术发展到今天来看,这种说法是不恰当的。
裸铜线质量缺陷原因分析

裸铜线质量缺陷原因分析一.弯曲:铜料表面出现竹节状或铜料表面具有一定节距的扭转,用手摸起来感到铜料表面不光滑、不平直的现象俗称小弯曲;放线时线打圈引起线打结的现象俗称大弯曲;两种现象统称为弯曲。
产生原因及避免措施:1、张力不稳定、波动较大:报设备部维修、调整张力弹簧、调整张力配重块。
2、模与线不在同一轴线水平线上,造成线材走线不平直:调整模架的位置。
3、模具定径区过短或配模过松:调整模具。
4、拉丝机震动大:报设备部维修。
5、导轮起槽、串动或不灵活:勤检查,定期更换。
6、定速轮压线扎头:停机调整。
二.闪光:表面因状损伤而引起反光亮点的现象.。
阴阳面:拉丝时因出口模的单面磨损引起的铜料表面在光线下呈现出光亮度阴暗不同的两部分的现象。
产生原因及避免措施:1. 模具磨损:更换模具。
2. 导轮起槽、串动或不灵活:勤检查,定期更换。
3. 塔轮起槽:更换塔轮。
4. 毛毡过高:调整毛毡高度。
5. 模架刮伤:调整模架高度或打磨模架。
三.发毛:铜料表面有细小的微料或缺痕,看起来表面泛白,光洁度差的。
产生原因及避免措施:1、具磨损(主要是加工模):更换模具。
2、导轮起槽(过线轮、排线轮):更换起槽导轮。
3、拉丝鼓轮磨损:更换鼓轮。
4、拉丝水润滑不良:调整拉丝水浓度。
5、张力过大:调整张力。
6、线材与鼓轮相对滑差大:调整滑差。
四.翘皮:铜料表面不光滑、开裂起皮的现象。
翘皮主要出现在较大规格的线材,主要是原材料杂质含量过高及轧制不良产生进厂的8mm铜杆因运输过程中的碰撞、磨擦而产生起槽,一些老设备因拉丝鼓轮、模架严重起槽,线材在拉制过程中容易造成损伤,也会产生起槽。
五:擦伤:铜料表面出现单面发毛或连续性的伤痕。
产生原因及避免措施:1、导轮材料粗糙,不光滑:拉制细线时,最好采用进口胶木导轮。
2、导轮转动不灵活:做好维护保养工作,经常检查导轮的运作情况,如有无晃动、串动等,做到定期更换。
3、拉伸塔轮起槽磨损:更换塔轮。
塔轮是价格较高的配件,应做好保护工作,以提高其使用寿命。
铜线拉丝工序中常见问题及解决方法

断线划痕及毛刺
铜粉污染
利用过滤设备去除铜粉
模具孔堵塞
清除堵塞物
乳化液浓度低
提高乳化液浓度
乳化液温度不合适
调整乳化液温度
拉丝油老化
更换乳化液
乳化液分层或者表面析出物过多
微生物侵害
加入杀菌剂 并补充氢氧化钠溶液或者三乙醇胺
PH过低
补充氢氧化钠溶液或者三乙醇胺
配液用水硬度及无机盐超高
更换配液用水
调整到合适范围
乳化液浓度太低.
提高浓度到正常标准.
乳化液温度不正常
降低温度到正常的35℃~45℃.
铜材附着过多油品
检查成型模的出口是否有拉丝油溢出.
检查羊毛毡及收线设备是否肮脏及吸附油分.
水质不合格
换用合格配液用水
微生物的侵害。
添加适当的杀菌剂。
乳化液保护性能不足
补充抗氧剂 改善车间环境
乳化液混有外来油品
乳化液润滑性差
更换润滑剂
温度不适当
测保持在35℃~45℃为最佳,过高或过低都会影响润滑性
PH低于标准
浓度太低.
添加新油.
长期使用自然降低
添加氢氧化钠溶液或者三乙醇胺,使用适量的杀菌剂.
生物的侵害.
添加杀菌剂.停产时每天循环一小时
混入酸性物质
检查酸性物质来源并补充氢氧化钠溶液或者三乙醇胺
铜材变色
PH太低
铜材拉丝现场
笔者通过现场总结和查找资料,归纳了铜拉丝工序中常见问题,并分析了可能的原因及解决方案,如下:
常见问题
原因
解决方法
塔轮及模具磨损快
润滑液中含有大量的铜粉及其氧化物
捞掉或利用过滤设备过滤.
润滑液循环量少.
2024年铜丝市场分析现状
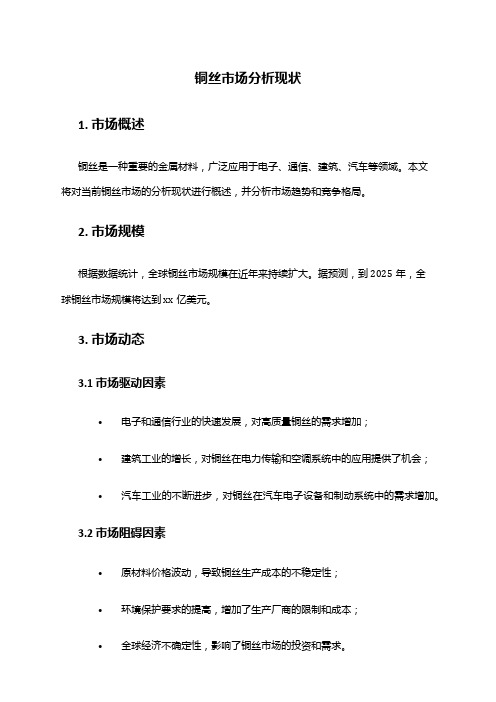
铜丝市场分析现状1. 市场概述铜丝是一种重要的金属材料,广泛应用于电子、通信、建筑、汽车等领域。
本文将对当前铜丝市场的分析现状进行概述,并分析市场趋势和竞争格局。
2. 市场规模根据数据统计,全球铜丝市场规模在近年来持续扩大。
据预测,到2025年,全球铜丝市场规模将达到xx亿美元。
3. 市场动态3.1 市场驱动因素•电子和通信行业的快速发展,对高质量铜丝的需求增加;•建筑工业的增长,对铜丝在电力传输和空调系统中的应用提供了机会;•汽车工业的不断进步,对铜丝在汽车电子设备和制动系统中的需求增加。
3.2 市场阻碍因素•原材料价格波动,导致铜丝生产成本的不稳定性;•环境保护要求的提高,增加了生产厂商的限制和成本;•全球经济不确定性,影响了铜丝市场的投资和需求。
铜丝市场可根据应用领域进行细分,主要包括电子行业、通信行业、建筑行业和汽车行业。
5. 市场竞争铜丝市场竞争激烈,主要厂商包括: - 中国铜业集团 - 贵州铜业集团 - 南方铜业集团 - 日东电工株式会社 - 金川国际集团这些公司通过产品创新、技术研发和市场拓展来竞争市场份额。
6. 市场趋势6.1 智能化应用的增加随着智能手机、物联网等技术的普及,对高质量铜丝的需求将进一步增加。
6.2 可持续发展的重视环境保护和可持续发展已成为全球关注的焦点,铜丝制造商需要采用更环保、节能的生产方式。
6.3 区域市场发展亚洲和欧洲地区的市场增长潜力巨大,中国市场在全球铜丝市场中占据重要地位。
综上所述,铜丝市场具有广阔的发展前景。
随着技术的不断创新和需求的增加,市场规模有望进一步扩大。
然而,市场竞争激烈,企业需要不断提高产品质量、创新能力和市场拓展能力,以保持竞争优势。
5N铜生产中存在的质量问题及改进

文章编号:1007-967X(2009)06-0030-045N铜生产中存在的质量问题及改进3刘庆杰(中冶葫芦岛有色金属集团公司技术中心,辽宁葫芦岛125003)摘 要:介绍了5N铜生产的基本过程和企业质量标准,指出了5N铜存在的主要质量问题是物表质量不稳定及锌超标,分析了影响5N铜质量的原因,提出了改进的措施。
改进的措施实施后,取得了较好的效果。
关键词:5N铜;影响质量因素;改进措施中图分类号:TF804 文献标识码:B 某公司有着多年5N铜生产的历史,其品种有铜片和铜粉。
5N铜广泛地应用在电器、电讯工业、特种高级合金、大型电子管以及化学试剂。
近年来,随着5N铜应用领域的不断扩大,厂家对产品质量的要求越来越严格。
由于种种原因,该公司5N铜产品无论是物理质量还是化学质量都存在诸多问题,远远不能满足客户提出的严格要求。
该公司5N铜质量企业标准见表1。
表1 某公司5N铜质量企业标准牌号化学成份(%)Cu杂质含量不大于,10-4不小于Zn Pb Fe N i Sn Mn A s B i Mg AgCu-0599.9992210.50.50.50.5111 Cu-4.599.995342 1.50.50.50.51111 原因分析生产5N铜的原料为电解一级阴极铜,其化学质量见表2。
5N铜片的生产采取的工艺过程:阴极铜-碱洗-酸洗-水洗-电解-干燥-包装。
5N 铜粉的生产采取的工艺过程:5N铜片-电解-水洗-离心脱水-氢气流中干燥-包装。
5N铜生产中常见的质量问题既有物理质量问题又有化学质量问题,物理质量问题主要是表面长气孔、长粒子和表面氧化变黑,化学质量问题是5N铜产品中锌杂质含量超标。
表2 一级阴极铜化学质量Cu+Ag 不小于杂质含量%(不大于)A s SbB i Fe Pb Sn N i Zn S P99.950.0020.0020.0010.0040.0030.0020.0020.0030.0040.001 1.1 板面长气孔板面长气孔的主要原因是:(1)电解液循环泵存在空转现象。
关于罐式退火铜线变色问题的探讨

关于罐式退火铜线变色问题的探讨摘要:本文结合笔者多年的工作经验,主要对罐式退火铜线变色问题进行了探讨分析,可供大家参考。
关键词: 铜丝退火;操作要点;原因分析;处理措施铜丝退火可以连拉连退,也可以采用罐式退火。
采用罐式退火生产方式,铜丝性能比较稳定,延伸率大,电阻率较小,一般中小企业和布电线产品采用的较多。
但在生产过程中,经常会出现退火铜丝表面发黑或放置后变色现象,严重影响产品质量,需引起生产企业的重视。
1、铜丝退火开机步骤及操作要点1.1 开机前的准备(1)准备好生产用的量具及工具,并检查校对计量器具是否准确。
(2)检查吊车,真空泵,仪器,仪表等生产设备是否完好正常,还应检查退火炉中的发热元件有否损坏,如有损坏应及时修理。
(3)铜单线退火时,应检查退火钢罐是否漏气。
如有漏气应清理密封槽及密封胶圈。
1.2 操作要点(1)将检验好的铜单线用起吊铁钩吊起,缓慢地吊入退火钢罐中,防止碰伤导体。
(2)将铜单线装满罐后,盖上罐盖,拧紧罐盖螺栓。
(3)启动真空泵,把真空软管接上退火钢罐阀门,抽真空使真空压力表指示到工艺要求压力时关上阀门,再关真空泵取下软管,再接上二氧化碳软管,打开阀门充二氧化碳使真空压力表指示在工艺要求压力为止。
充气时先开气瓶低压阀,后开气瓶高压阀。
关气时应先关高压阀,后关低压阀。
(4)将充好气体的退火钢罐吊入电热炉中,按工艺要求温度进行加热,并接上罐盖冷却水管打开水制,在加热过程中要检查炉温和气压。
升温至工艺要求的退火温度后,必须继续保温,保温时间按工艺规定执行。
(5)在退火过程中如发现罐内的气压不是逐步上升,而是逐步下降时,说明钢罐漏气,必须采取充二氧化碳等补救措施。
在加热过程中若气压上升超过0.3Mpa必须放气至0.3Mpa。
以防气压过大使钢罐变形。
(6)将退火钢罐从电热炉中吊出置于地面,让其在空气中冷却至到达工艺要求的自然冷却时间再放入水池中冷却,按工艺要求的浸水时间进行浸水,到达时间后开罐出线,出线要小心轻放,防止碰伤铜线。
铜拉丝生产管理解决方案(一)
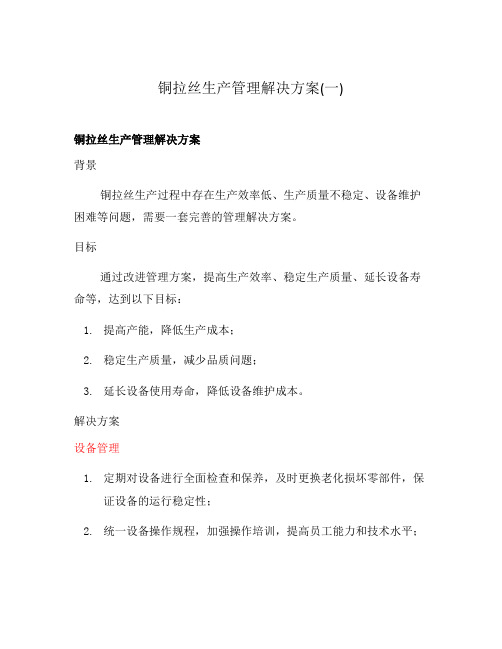
铜拉丝生产管理解决方案(一)铜拉丝生产管理解决方案背景铜拉丝生产过程中存在生产效率低、生产质量不稳定、设备维护困难等问题,需要一套完善的管理解决方案。
目标通过改进管理方案,提高生产效率、稳定生产质量、延长设备寿命等,达到以下目标:1.提高产能,降低生产成本;2.稳定生产质量,减少品质问题;3.延长设备使用寿命,降低设备维护成本。
解决方案设备管理1.定期对设备进行全面检查和保养,及时更换老化损坏零部件,保证设备的运行稳定性;2.统一设备操作规程,加强操作培训,提高员工能力和技术水平;3.建立设备运行数据统计和分析体系,及时发现设备故障和异常情况,加以解决。
生产管理1.建立完善的生产计划和调度管理体系,提高生产效率和产量;2.加强原材料和生产流程的质量控制,减少品质问题;3.建立生产数据统计和分析体系,及时发现生产异常情况,加以解决。
员工管理1.加强员工培训,提高技术能力和工作效率;2.建立员工绩效考核制度,激励员工主动参与生产管理,并持续改进。
预期效果通过上述综合管理措施,预计可以取得以下效果:1.产量提高10%,生产成本降低5%;2.品质问题率下降20%;3.设备使用寿命延长15%。
总结综合各方面因素,对铜拉丝生产管理进行全面优化,有利于提高企业生产效率和质量水平,为企业发展奠定坚实基础。
实施方案1.确定项目领导和团队,明确目标、时间表和工作计划;2.对设备进行全面检查和保养,及时更换老化损坏零部件,确保设备运行安全;3.建立设备运行数据统计和分析体系,及时发现设备故障和异常情况,制定合理的解决方案;4.建立生产计划和调度管理体系,确保生产计划的顺利实施,提高生产效率和产量;5.加强原材料和生产流程的质量控制,降低品质问题率;6.建立生产数据统计和分析体系,及时发现生产异常情况,制定改进措施;7.定期进行员工培训,提高员工技能和工作效率;8.建立员工绩效考核制度,激励员工积极参与生产管理。
风险控制1.对于生产计划和调度管理,定期进行评估和分析,及时调整生产计划和流程,防止生产延误和浪费;2.对于设备管理,建立完善的保养和检修制度,赋予设备管理人员足够的操作权限,避免因人为因素造成设备故障;3.加强员工培训,提高员工技能和工作效率,确保员工都能够熟练掌握操作技巧,降低品质问题率。
集线异常分析及改善

集线异常分析及改善一、 目的:加强品质管理,建立作业员自主品质管理观念,有效防止不良品的发生以确保产品品质。
二、 常见异常资料收集:1.混料2.铜线少条3.铜线走股4.铜线打顿5.排线不良6.线径偏差7.绞距出错 8.毛刺9.标签与实物不符三、 原因分析及改善对策:1.混料原因分析:作业者换线前未预计备料导致测量线径不确实(或根本未测量)。
改善对策:(1)作业者依实际生产之规格於上线前预计备料、识别颜色规格标签(目视)(2)预计换料前剪下一小段铜线测量线径,并把实测值、换料时间对号记录于《集线工程上线/下轴自主检测表》,以备抽察。
(3)卸轴前所剪下1米之样品,必须自行确认其条数,测量线径,并记录于《集线工程上线/下轴检查记录表》上。
(4)若发现实测值超出管制的公差范围值时,立即停机查明原因,排除异常后方可继续开要生产。
2.铜线少条原因分析:(1)断线后断线器未感应到而造成机器仍未停。
(2)断线后操作者未将少条部份清除干净。
(3)换规格时未确认铜线的总条数。
(4)操作者未巡视机台,造成外部断线后未被及时发现的情况发生。
改善对策:(1)检查以下项目;A开机前,检查断线控制开关是否打开;B检查断线连接线的镙丝是否脱离,手试断线装置是否感应灵敏;C内外部断线控制装置须每天保养,用砂布打磨增加其感应灵敏度;D内部断线控制装置与铜线的缠绕距离不能低於绕线轮3毫米;E走动巡视机台是否正常运转。
(2)发生外部断线少条时,将单芯铜丝缠绕在原股上并保留15毫米左右作痕迹。
剪断时确认铜线条数,若有少条的部分须将其全部清除,确认无误后方可作总接。
3铜线走股:原因分析:A单根铜线张力太松。
改善对策:作业过程中,用张力计检查外部单根铜线张力,若有张力太松则增加太阳丝。
4铜线打顿原因分析:A传动装置出现故障 B卷取张力失调,造成张力太松。
改善对策:A调妥卷取张力后,用手转动钢板,若收线铁轴不转动,则检查传动齿轮有无故障,若有故障需修复试机OK后,并清除打顿铜线方可开机作总接。
铜丝铜渣改善专案报告

二.现况把握
厂内检验状况
月份 铜丝铜渣 生产总数 不良率 3.00% 2.50% 2.00% 1.50% 1.00% 0.50% 0.00% 1 2 3 4 5 6 7 8 9 10 1.33% 1.45% 1.55% 1.32% 1.44% 1.35% 1.11% 1.34% 2.33% 1 16329 2 9109 3 20041 4 28010 5 19728 6 17245 7 17070 8 39814 9 16906 10 35452 Ave 21970.4
四.不良原因查找----现场稽查
*經稽核現場及廠內銅絲銅渣不良現象收集,銅絲銅渣主要產生 源於防焊制程
7
五.不良原因分析
人员操作
检修铜屑残留 人员动作不标准 砂纸打磨不净 搬运时板边撞伤 暂存台缓冲失效
机器设备
前处理磨刷残留
基板原物料
板边毛刺
铜粉回收及水洗 过滤效果不佳 板边撞伤掉屑 板边流胶
报废标记 位置残铜
对策执行 过程监控
对策点检——checklist
12
八.效果確認
改善前後, 廠內數據對比
2013年
月份 项目 铜丝铜渣 生产总数 铜丝铜渣不良率
2014年 8
39814
1
16329
2
9109
3
20041
4
28010
5
19728
6
17245
7
17070
9
16906
10
35452
Ave
219704
11
缓冲胶垫偏移破损
印刷插框板边 与框架摩擦
印刷底板未蚀 刻或蚀铜不净 印刷台面及底 板清洁不及时 印刷后预烤 前叠框静置
半孔残铜改善报告

半孔残铜改善报告作为关于半孔残铜改善的报告,我们将分析当前的情况并提出一些建议,以改善我们所面临的问题。
一、问题分析半孔残铜是一种在金属冶炼中常见的问题。
它可能导致工艺失效、产品质量下降等严重后果。
半孔残铜可能是由于工艺参数不当、设备故障、原料问题等多种因素引起的。
当前,我们公司也在生产过程中遇到了半孔残铜的问题。
通过对现有情况进行分析,我们找到了以下几个主要问题:1. 工艺参数不稳定。
在生产过程中,我们发现工艺参数经常波动,导致产品质量不稳定。
2. 设备老化故障。
部分生产设备已经达到了使用年限,出现了频繁的故障,影响了生产效率和产品质量。
3. 原料质量不稳定。
我们发现,有时采购到的原料质量不稳定,包含了一些影响产品质量的杂质。
二、改善方案为了解决半孔残铜的问题,我们提出以下改善方案:1. 优化工艺参数。
我们将对生产工艺进行精细化调整,确保参数稳定,提高产品质量。
2. 更新设备。
对于老化故障的设备,我们将对其进行维护和更新,确保设备的正常运行,提高生产效率和产品质量。
3. 优化原料采购。
我们将加强对原料供应商的管理,确保原料质量稳定可靠,避免影响产品质量的杂质。
三、实施计划为了有效实施上述改善方案,我们制定了以下实施计划:1. 工艺参数优化。
成立由生产、技术、质量等部门组成的工艺改进小组,共同制定并实施工艺参数优化方案,并定期进行检查和调整。
2. 设备更新维护。
安排专业维护团队,对老化故障设备进行定期检查和维护,并逐步更新部分设备,提高生产线设备的整体性能。
3. 原料采购改善。
加强原料供应商的质量管理,与供应商建立长期稳定的合作关系,确保原料质量的稳定可靠性。
四、预期效果通过以上改善方案的实施,我们预期可以取得以下效果:1. 产品质量稳定。
通过工艺参数优化和原料采购改善,产品质量将得到稳定提高,减少半孔残铜问题的出现。
2. 生产效率提高。
设备更新维护和工艺参数优化将提高生产效率,降低生产成本。
3. 客户满意度提高。
铜材车间分条工艺流程战略改善报告

铜材车间分条工艺流程战略改善报告
对于铜材分条车间的工艺流程,我们针对现有的操作流程进行了分析,并提出了以下改进建议:
1. 增加检测环节:在分条过程中,铜材经过多次加工,容易产生裂纹和变形等不良现象,如果这些产品不及时检测,将影响下一步加工的质量。
因此,我们建议在分条工艺中增加第一次抽头进行非破坏性探伤,对于探测结果不合格的产品进行返工或者废料处理,以减小后续产品的质量风险。
2. 调整分条顺序:传统的分条工艺流程是先进行大面积分条,再进行小面积分条。
我们认为这种分条方式容易产生变形并难以避免,因此我们建议修改工艺流程,先进行小面积分条,再进行大面积分条,以便更好地控制过程中的变形。
3. 优化润滑条件:在分条过程中,润滑剂对铜材的质量和分条效果影响很大,因此我们建议对现有的润滑剂进行优化,选取更适合分条的润滑剂,同时对润滑参数进行严格的控制。
4. 强化设备维护:设备的维护对于工艺的稳定性和产品的质量有着至关重要的作用,因此我们建议设立专门的维修保养岗位,强化设备的维护和保养,定期检查机器的机械部分以及液压、气动部分的连接情况。
通过以上几个方面的改进,我们相信可以提高分条工艺的效率、产品质量的稳定性和可靠性,从而提高整个车间的效益和竞争力。
铜丝跟进报告

主题:电镀铜丝跟进报告一、背景:10月19日AOI反馈电镀铜丝比例偏高,整个板面铜丝数量达到几十个点,AOI PNL 良率只有20%,严重影响AOI生产。
为改善电镀铜丝问题,我部和药水供应商一起跟进查找产生原因并加以改善。
二、问题描述:此次AOI反馈的铜丝所表现出来的症状与一般的铜粒铜丝有所不同,以往因为电镀药水所产生的铜丝在蚀刻后铜丝与铜面是结合在一起的,用砂纸打磨很难去除干净,需用修板刀或是磨刷板面来处理干净。
而这次出现的铜丝在过VRS机检修时,操作人员用1500目的砂纸轻轻打磨即可处理干净,并且铜面也未见有凹凸不平的现象。
板面铜丝见下图:三、试验与分析::由上述试验得出,产生铜丝的原因有可能为外层显影后板面存在问题,而显影后板面存在问题主要为显影线保养不到位等问题。
经现场查看外层显影线发现确实存在有保养不到位的问题,以下为显影缸保养前后图片对比图: 保养前 保养后在外层进行仔细、有效的保养后,按铜槽槽号跟进一批板到AOI统计各槽铜丝坏点,从数据来看有较明显改善,以下为保养前后的数据对比:保养后从以上数据及图表可以看出在保养过后各缸铜丝的不良已经有非常明显的好转,只是8#槽相比它铜槽稍严重些。
因为二铜在10月份已经开始做碳处理此次刚好从8#往1#开始做的(10月19日已经做到3#槽)。
碳处理时对缸底和阳极铜球都会进行清洗;对药水会进行处理和过滤。
从理论上来说铜丝应该比1—3#各缸产生铜丝的几率要低,而从以上铜丝数据来看却没有低,反而较偏高。
在检查8#槽时发现过滤棉芯有严重的掉棉丝异常现象: 使用后:10.99.510.88.212.110.812.61.62.02.63.12.92.67.90.02.0 4.0 6.0 8.0 10.0 12.0 14.0 03060901201501802102#3#4#5#6#7#8#保养后铜丝数据保养前铜丝数据保养前每PNL 铜丝(平均)保养后每PNL 铜丝(平均)8#过滤机内的棉芯(有较明显的掉丝现象) 其它过滤机的棉芯(正常)异常棉芯使用前图片正常棉芯使用前图片》在通知采购联系棉芯供应商时,供应商的解释为:他们的原材料换了供货商。
铜丝铜渣改善专案总结汇报

不良率 1.33% 1.45% 1.55% 2.33% 1.32% 1.44% 1.35% 1.11% 1.34% 2.40% 1.50%
3.00% 2.50% 2.00% 1.50% 1.00% 0.50% 0.00%
2.33%
不良率
2.40%
1.33%
1.45%
1.55%
1.32%
1.44%
1.35%
9
六.對策擬定
10
六.對策擬定
11
七.防止再發
对策实施,并进行过程监控,建立标准化管理,防止不良再发。
项目
板边流胶 板边毛刺
板边撞伤
印刷插框 摩擦掉屑
粘尘纸更 换不及时
标准化附件
《PTH进料 《暂存台胶垫 检验记录》 使用标准》
《调框及插框作 业标准》
《印刷作业重 点注意事项》
对策执行 过程监控
生产总数
1229247 628419 1293188 1200530 1489345 1195979 1267960 3575686 1261205 1478928 14620487 1291881 1349121 1284187 3925189
铜丝铜渣不良率 1.33% 1.45% 1.55% 2.33% 1.32% 1.44% 1.35% 1.11% 1.34% 2.40% 1.50% 0.93% 0.47% 0.32% 0.57%
备注:数据来自明冠客户端上件统计不良
4
二.现况把握
厂内检验状况
月份
1
2
3
4
5
6
7
8
9
10
Ave
铜丝铜渣 16329 9109 20041 28010 19728 17245 17070 39814 16906 35452 21970.4
孔口铜丝问题的原因分析与改善

孔口铜丝问题的原因分析与改善孔化与电镀 & 印制电路信息 .子口铜丝问题的原因分析与改善戴勇陈家逢邓峻袁国东王颇臣深圳市崇达电路技术股份有限公司,广东深圳摘要电镀工艺能够增加面铜厚度并实现不同层次的导电连接而被广泛的应用于行业。
然而,针对该工艺的品质保证绝非易事。
电镀工艺受钻孔效果、沉铜前处理、电镀参数等因素的影响,在品质上容易出现铜丝铜粒等不良问题本文从电镀基本原理出发,初步分析了电镀工艺铜丝的产生原因,并通过试验验证了铜丝产生的原因,得出了有效的改善措施。
关键词线路板;电镀;钻孔;铜丝中图分类号: 文献标识码: 文章编号: ?】 ? ? ? ?. , . , ,. ..;;;因,并通过试验验证了铜丝产生的原 ,得出了有线路板的制造工艺,随着电子设备的高功能化和小型化而飞速发展。
电镀工艺是制造流程中非效的改善措施,以增加对高密度多层次线路板电镀的了解。
常重要的一个环节,为增加面铜厚度,实现不同层次的导电金属提供电连接,需要在面铜及通孔上电电镀铜原理镀导电性良好的金属铜。
随着终端产品日趋激烈的竞争,势必对产品的可靠性提出更高的要求,而镀铜溶液的主要成分是硫酸铜和硫酸,在直流对电镀工艺中铜层的性能保证则成为可靠性保证电压的作用下,在阴、阳极上发生如下反应:的重要项日阴极:受钻孔效果、沉铜『处理、电镀参数等素的阳极: 一 ?影响,线路板电镀时极易出现品质问题,其中板面电解液中的金属离了或其络合离子在阴极还原铜丝是影响产品品质的最大问题之一。
本文从电镀沉积出铜镀层的过程叫电结晶。
在形成金属晶体时基本原理出发,初步分析了电镀工艺铜丝的产生原分为结晶核的生成与成长两个步骤进行。
这两个过....印制电路信息 . 孔化与电镀 &程的速度决定着金属结晶的粗细程度】。
当晶核的生成速度快而晶核成长的速度慢的时候,晶粒长大缓慢使得镀层的结晶细致、致密;当晶核的生成速度慢而晶核成长的速度快的时候,即单位面积的电镀电流过大时,则使电镀层粗糙,产生“过烧”现象。
电线整改方案

电线整改方案一、背景说明电线在日常生活和工作中起到了重要的作用,但不合格的电线可能存在安全隐患。
为了保障人身财产安全,确保电线的质量和安全性,我公司制定了电线整改方案,以解决旧电线质量问题和确保新电线质量达到标准要求。
二、问题分析1. 电线质量问题:旧电线有可能因受潮、老化等原因导致绝缘层损坏,存在断线或短路的风险。
2. 安全隐患:电线老化、质量不合格等问题会增加火灾、漏电等事故发生的风险,严重威胁到人身财产安全。
三、整改方案1. 建立整改小组:选派专业技术人员和管理人员组成电线整改小组,负责制定整改计划、监督执行和后续检查。
2. 制定整改计划:整改小组根据已发现的问题和需求,制定详细的整改计划。
整改计划应包括改造范围、时间节点、质量要求等,并确保整改工作落实到位。
3. 更新电线标准:根据相关标准,更新电线的规格和要求。
确保所有使用的电线都符合最新的标准,并严格按照标准进行采购和安装。
4. 更换老旧电线:对经过检测发现老化、质量不合格的电线,及时更换。
5. 加强巡检和维护:制定巡检计划,定期检查电线的使用情况和安装质量,并进行维护和保养。
四、整改措施1. 确保电线采购的质量:选择合格的供应商,确保所有采购的电线符合国家和行业标准,严禁使用假冒伪劣产品。
2. 强化施工监督:加强对电线施工的监督,确保安装质量达到标准要求。
对存在安装质量问题的电线,责令整改或进行重装。
3. 动态管理电线使用寿命:建立电线使用档案,对电线的使用寿命进行动态管理,提前预防老化问题,并制定相应的更新计划。
4. 安全培训和教育:针对电线使用人员进行相关安全培训和教育,提高他们的安全意识和应急能力。
五、整改效果评估1. 编制整改效果评估表,通过定期的检查、测试和评估,全面了解电线整改后的情况,确保整改效果符合预期目标。
2. 根据检查结果,对发现的问题进行整改和改进,确保电线使用的安全和质量。
六、总结通过制定和实施严格的电线整改方案,我们公司将有效地解决电线质量问题和安全隐患,提高人身财产的安全保障水平,预防事故的发生,推动公司的可持续发展。
5n铜生产中存在的质量问题及改进
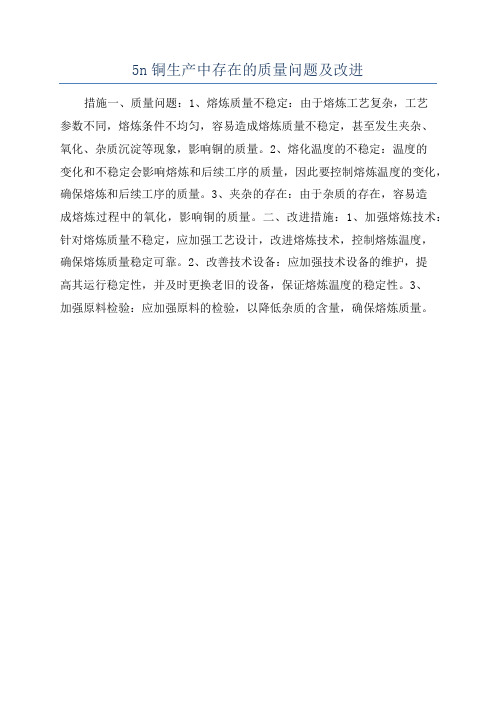
5n铜生产中存在的质量问题及改进
措施一、质量问题:1、熔炼质量不稳定:由于熔炼工艺复杂,工艺
参数不同,熔炼条件不均匀,容易造成熔炼质量不稳定,甚至发生夹杂、
氧化、杂质沉淀等现象,影响铜的质量。
2、熔化温度的不稳定:温度的
变化和不稳定会影响熔炼和后续工序的质量,因此要控制熔炼温度的变化,确保熔炼和后续工序的质量。
3、夹杂的存在:由于杂质的存在,容易造
成熔炼过程中的氧化,影响铜的质量。
二、改进措施:1、加强熔炼技术:针对熔炼质量不稳定,应加强工艺设计,改进熔炼技术,控制熔炼温度,
确保熔炼质量稳定可靠。
2、改善技术设备:应加强技术设备的维护,提
高其运行稳定性,并及时更换老旧的设备,保证熔炼温度的稳定性。
3、
加强原料检验:应加强原料的检验,以降低杂质的含量,确保熔炼质量。
铜针刮出锡丝改善报告

铜针刮出锡丝改善报告
尊敬的[报告对象]:
我谨向您提交关于铜针刮出锡丝问题的改善报告。
一、问题描述
在我们的生产过程中,发现使用铜针刮出锡丝的操作存在一些问题。
具体表现为刮出的锡丝不够均匀,容易出现断裂和残留,导致产品质量不稳定。
二、原因分析
经过仔细调查和分析,我们发现问题主要出在以下几个方面:
1. 铜针的材质和制造工艺不够理想,导致刮出的锡丝不够均匀。
2. 刮锡的速度和力度控制不当,容易造成锡丝断裂和残留。
3. 锡丝的质量不稳定,也会影响刮锡的效果。
三、改善措施
针对以上问题,我们提出了以下改善措施:
1. 优化铜针的材质和制造工艺,提高铜针的硬度和耐磨性,确保刮出的锡丝更加均匀。
2. 加强对刮锡速度和力度的控制,通过培训和操作规范,提高操作人
员的技能水平。
3. 加强对锡丝质量的管控,选择质量稳定的供应商,并定期进行质量检测。
四、实施计划
为了确保改善措施的有效实施,我们制定了以下实施计划:
1. [具体时间]前,完成铜针材质和制造工艺的优化。
2. [具体时间]前,完成对操作人员的培训和操作规范的制定。
3. [具体时间]前,完成对锡丝供应商的评估和选择,建立锡丝质量检测制度。
通过以上改善措施的实施,我们相信能够有效解决铜针刮出锡丝不够均匀的问题,提高产品质量和生产效率。
感谢您对我们工作的支持和关注!
此致
敬礼!
[姓名]
[日期]。
铜合金件生产整改措施

铜合金件生产整改措施第一篇:铜合金件生产整改措施铜合金件生产整改措施一原材料原因及存在的问题分析我厂近年来一直由小型铜材生产企业提供货源,这些企业产品的缺点是质量控制水平低,质量稳定性差。
优点是可小批量订货、供货及时、能垫付资金,减小我厂生产资金的压力。
我厂目前铜材验收检验只能化验四种主要元素,而对性能影响较大的其它五种元素靠外协。
对杂质元素无内控标准,特别是铅的含量。
材料存在的问题:锻造用铜合金材料按TB2073-2002标准要求应为挤制棒材。
目前,供应的材料均为拉制棒,对于关键受力零件加工,材料锻压比不够。
化学成份不稳定、材料表面存在微裂,材料端头切除不够,内外表杂质等缺陷较多。
2 纠正预防措施1)对关锻受力零件,如定位线夹、吊弦线夹、接头线夹、终锚线夹等材料选用国内大型企业的产品,如洛铜、西北铜等。
2)增加本厂化验设施,确保能按GB5231-2001标准所列的项目进行分析。
如增加光谱分析仪或原子吸收分光光度计。
3)加强对铜材表面裂纹和端头缩孔的检查,可采用浸酸、宏观分析或电气仪表测试等手段。
二下料方式原因及存在的问题分析我厂因考虑大批量生产的原因,对直径小于30mm棒材一直采用冲切下料方式,对于铝青铜类较脆性的材料来说,易在下料端头形成冲切裂纹,锻造时,若坯料放置不当,易将裂纹带入到产品中。
2 纠正预防措施对于青铜类材料在下料时,改为锯切下料。
三锻造过程控制原因及存在的问题分析此阶段存在的主要问题为:始锻和终锻温度不能严格保证,若采用在线淬火,淬火温度不能严格保证,人为控制影响因素大,原设备上的自动推料和实时测温系统得不到应用。
易造成零件的过热、过烧、开裂。
锻后冷却消除脆性措施得不到保证。
2 纠正预防措施1)完善加热设备自动推料和实时测温系统,进行工艺试验,确定每种产品的加热工艺参数(电流和生产节拍)。
2)对于在线淬火,应在锻锤上增加红外温度监测仪,测量锻后淬火温度。
3)每个锻锤处增加适合的冷却水槽,确保锻后零件能有效冷却。
- 1、下载文档前请自行甄别文档内容的完整性,平台不提供额外的编辑、内容补充、找答案等附加服务。
- 2、"仅部分预览"的文档,不可在线预览部分如存在完整性等问题,可反馈申请退款(可完整预览的文档不适用该条件!)。
- 3、如文档侵犯您的权益,请联系客服反馈,我们会尽快为您处理(人工客服工作时间:9:00-18:30)。
Ξ操鞯凵 '~'¨η丬 通 告到期彐筵锸椐谖厂…乙 镇涵适型
郭 生 (PE)、
孙生
ˉ—
SU歇 镧篮分耕畿蔷窟爨
、背景: 铜丝 问题对公司品质及 出货将会造成严重 困扰 ,过 往 的品质表现显示铜丝 问 题流到客户处的现象也比较频繁,大 幅度降低客户对公司的满意度,故 铜丝 问题是我司要重点控制的品质项 目 (主要图片如下)。
inch(特殊情况另论) 2.烂板边调出来砂纸打磨 3.外层工序监督卡关,禁止烂板边问题
流入下工序 1.改善手套掉毛问题,将涂布手套更换
成无硫手套 2.每天抽查 1.边条只能使用机器切,不能手掰 2.小桐球退仓处理 3.光剂添加桶 3 月清洗 1 次 4.鼓风机过滤网,维修每月更换 1 次 5.铜缸 3 月倒缸 6.更换 PCM 光剂
负责人
PROD 梁初 QA: 邱树平 ME: 王大鹏 PE:段正华
PROD 李志华 QC 张和杨 ME 林森
PROD 邵荣辉 维修 赵明国 ME 林森
1.单只报废打报废孔板需过电镀幼磨处 理后才能出货到后工序
QC QA
张和杨 邱树平
粘上去的铜
绿油工序
丝
1.控制高压水洗正常运行及水洗 2 个小 时检查 1 次
铜丝 经过综合评估 初步确定 PCM 光剂对铜丝改
善较明显
实验证明绿油 工序磨刷能将 线路边缘的铜 磨卷起来产生
铜丝
改善内容
建议更换成 240#320#磨刷(白井 是 240#/320#)其他厂也是
将电镀 B 拉更换成 PCM 光剂 将电镀 A 拉更换成 2001 光剂
( 跟白井一样)
建议将 500#磨刷更换成 800#磨 刷
一
表 格 编 号 :QAI-DCCBG01ˉ
ZI/0
介定文件:QAIˉ DCC01
版本号:弭 ˉ0
科 惠镍 路有 限公 司
TECH阳 河 sE CRCuTs COL·
IPAH¥ L1RiIITm·
J
辽建 滔 化 工 彝 田 戚 员 l
地址〓番淹吊畀rJ Ⅱ番忱斜早 目丑 =朝 钭 技大逍 皮+=啦 诤 汝大理 -座 -俚
2.氧化铝缸大保养 2 周 1 次 3.建议更换 800#磨刷,避免将线路边缘
的铜磨卷起来
PROD 陈益红 ME 梅正中 QA 邱树平
FQC 工序 铜丝铜屑漏 出管控
1.培训员工重点检查及执行到位
FQC:王响亮
4.2.工艺改良方面
工序 沉铜前粗磨
机
电镀工序
绿油工序
现象描述 目前使用 180# 及 240#磨刷, 铜面较粗,电 镀时容易形成
Tm.oog5:-zs丁
Ⅰg9zε 苎 V口叮|00g日 Ξ~7吕了丁g吕吾5
第 1觅 共 丘页
mE部 文件
文 件 编 号 :TTG肌 1’ olV丬 丨°Tc,0 发 文 日 期 :⒛ 14。Q1.10
适用范围 □ 科惠各厂 (TW, □ 惠阳
(Ⅱ 盯 ) □
有效期限 ?014.4.19
科 惠 白井 (TsF)
目前进度
计划中
预计 3-4 月 待 B 拉更换 PCM 稳定后
预定中
负责人 ME 林森 ME 林森 ME 梅正中
二、 目的:
分析铜丝产生的根源加 以控制:
1 制定工序相应的控制点降低铜丝产生。
2
工艺上遂步优化减弱铜丝问题。
3
有效堵截铜丝问题的流出。
三、产生铜丝工序分析:
3.1.压板(烂板边)
小结:压板过程中板边缺胶导致空洞,铜箔与基材未贴合密实,在后工序的生产过程中 铜屑容易掉到缸里。
3.2.电镀前毛毛丝(干菲林涂布手套掉毛)
图电后
图电后切片
显影后
手套
图电后
图电后
小结:以上图片显示 DF 手套掉毛造成电镀后毛毛丝,图电后切片毛毛丝位置镀铜包住。
3.3.电镀铜丝(电镀工序产生)
小结:电镀过程中有机物或异物(导体或半导体)随着镀铜的进行,粘附于线路之间逐步 形成条状铜丝。
3.4.打报废孔铜丝。
小结:报废孔边缘较多铜屑,带到绿油工序掉落到缸中粘附到板子线路上。
3.5.绿油磨板产生铜丝(磨刷将线路边缘的铜磨卷起来)。 3.6 绿油绿油黏上去的铜丝
小结:绿油在印油过程中掉落到板面上的铜丝。
四、控制及改善:
4.1.生产控制方面
工序
控制项目
压板工序 烂板边
显影后执 漏
毛毛丝
电镀工序 电镀铜丝
MRB/蚀检
打报废孔铜 丝
代表图片
改善内容 1.开料尺寸比成型尺寸尽量保证大 0.2
科惠佛 冈 (FTC)
拟文 : ME:林 森
收 文 部 丨1∶ PROD(电
IWF、 镀 )、 压 合 、 矽 F、 蚀 检 、
FQC、 PE、 QA、 PWl收
文 者 :/+生 (QA)、 郝 生 (PROD)、
刘 生 (ME)、 卓 生 (PR∞ )、 张 小 姐 (QC)、