TPS在广汽丰田整车物流系统的应用
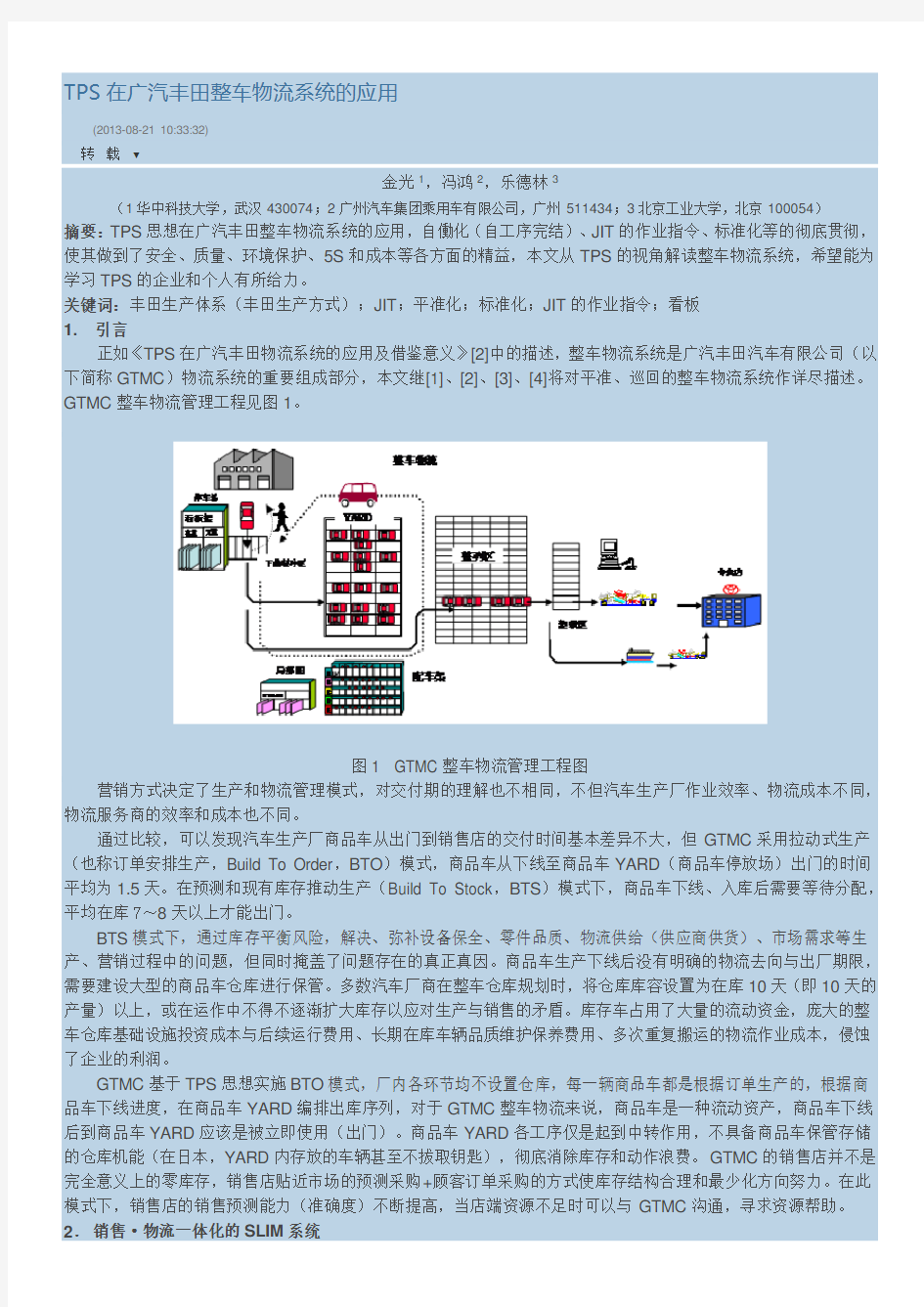
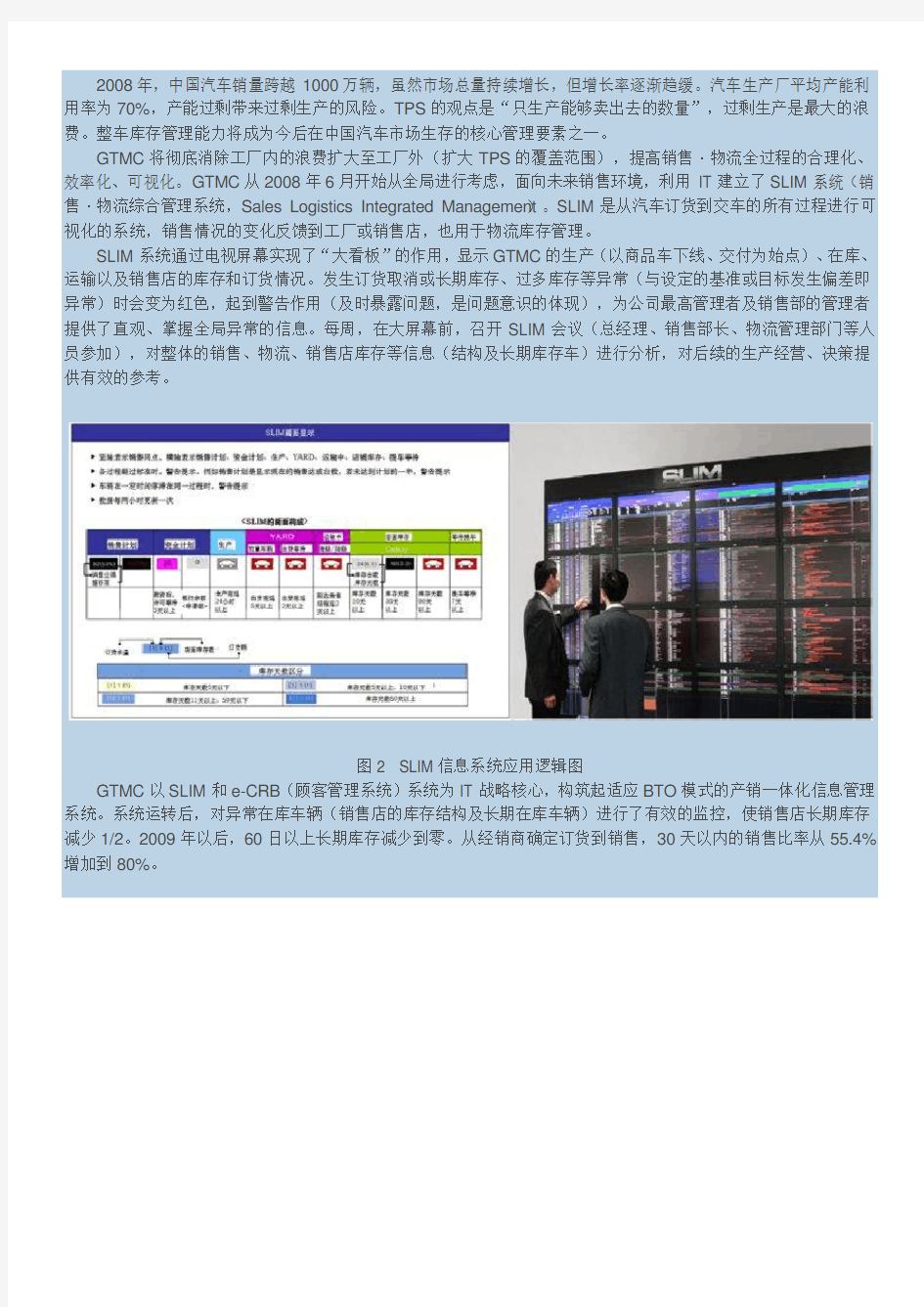
TPS在广汽丰田整车物流系统的应用
(2013-08-21 10:33:32)
转载▼
金光1,冯鸿2,乐德林3
(1华中科技大学,武汉430074;2广州汽车集团乘用车有限公司,广州511434;3北京工业大学,北京100054)
摘要:TPS思想在广汽丰田整车物流系统的应用,自働化(自工序完结)、JIT的作业指令、标准化等的彻底贯彻,使其做到了安全、质量、环境保护、5S和成本等各方面的精益,本文从TPS的视角解读整车物流系统,希望能为学习TPS的企业和个人有所给力。
关键词:丰田生产体系(丰田生产方式);JIT;平准化;标准化;JIT的作业指令;看板
1.引言
正如《TPS在广汽丰田物流系统的应用及借鉴意义》[2]中的描述,整车物流系统是广汽丰田汽车有限公司(以下简称GTMC)物流系统的重要组成部分,本文继[1]、[2]、[3]、[4]将对平准、巡回的整车物流系统作详尽描述。GTMC整车物流管理工程见图1。
图1 GTMC整车物流管理工程图
营销方式决定了生产和物流管理模式,对交付期的理解也不相同,不但汽车生产厂作业效率、物流成本不同,物流服务商的效率和成本也不同。
通过比较,可以发现汽车生产厂商品车从出门到销售店的交付时间基本差异不大,但GTMC采用拉动式生产(也称订单安排生产,Build To Order,BTO)模式,商品车从下线至商品车YARD(商品车停放场)出门的时间平均为1.5天。在预测和现有库存推动生产(Build To Stock,BTS)模式下,商品车下线、入库后需要等待分配,平均在库7~8天以上才能出门。
BTS模式下,通过库存平衡风险,解决、弥补设备保全、零件品质、物流供给(供应商供货)、市场需求等生产、营销过程中的问题,但同时掩盖了问题存在的真正真因。商品车生产下线后没有明确的物流去向与出厂期限,需要建设大型的商品车仓库进行保管。多数汽车厂商在整车仓库规划时,将仓库库容设置为在库10天(即10天的产量)以上,或在运作中不得不逐渐扩大库存以应对生产与销售的矛盾。库存车占用了大量的流动资金,庞大的整车仓库基础设施投资成本与后续运行费用、长期在库车辆品质维护保养费用、多次重复搬运的物流作业成本,侵蚀了企业的利润。
GTMC基于TPS思想实施BTO模式,厂内各环节均不设置仓库,每一辆商品车都是根据订单生产的,根据商品车下线进度,在商品车YARD编排出库序列,对于GTMC整车物流来说,商品车是一种流动资产,商品车下线后到商品车YARD应该是被立即使用(出门)。商品车YARD各工序仅是起到中转作用,不具备商品车保管存储的仓库机能(在日本,YARD内存放的车辆甚至不拔取钥匙),彻底消除库存和动作浪费。GTMC的销售店并不是完全意义上的零库存,销售店贴近市场的预测采购+顾客订单采购的方式使库存结构合理和最少化方向努力。在此模式下,销售店的销售预测能力(准确度)不断提高,当店端资源不足时可以与GTMC沟通,寻求资源帮助。2.销售·物流一体化的SLIM系统
2008年,中国汽车销量跨越1000万辆,虽然市场总量持续增长,但增长率逐渐趋缓。汽车生产厂平均产能利用率为70%,产能过剩带来过剩生产的风险。TPS的观点是“只生产能够卖出去的数量”,过剩生产是最大的浪费。整车库存管理能力将成为今后在中国汽车市场生存的核心管理要素之一。
GTMC将彻底消除工厂内的浪费扩大至工厂外(扩大TPS的覆盖范围),提高销售·物流全过程的合理化、效率化、可视化。GTMC从2008年6月开始从全局进行考虑,面向未来销售环境,利用IT建立了SLIM系统(销售·物流综合管理系统,Sales Logistics Integrated Management)。SLIM是从汽车订货到交车的所有过程进行可视化的系统,销售情况的变化反馈到工厂或销售店,也用于物流库存管理。
SLIM系统通过电视屏幕实现了“大看板”的作用,显示GTMC的生产(以商品车下线、交付为始点)、在库、运输以及销售店的库存和订货情况。发生订货取消或长期库存、过多库存等异常(与设定的基准或目标发生偏差即异常)时会变为红色,起到警告作用(及时暴露问题,是问题意识的体现),为公司最高管理者及销售部的管理者提供了直观、掌握全局异常的信息。每周,在大屏幕前,召开SLIM会议(总经理、销售部长、物流管理部门等人员参加),对整体的销售、物流、销售店库存等信息(结构及长期库存车)进行分析,对后续的生产经营、决策提供有效的参考。
图2 SLIM信息系统应用逻辑图
GTMC以SLIM和e-CRB(顾客管理系统)系统为IT战略核心,构筑起适应BTO模式的产销一体化信息管理系统。系统运转后,对异常在库车辆(销售店的库存结构及长期在库车辆)进行了有效的监控,使销售店长期库存减少1/2。2009年以后,60日以上长期库存减少到零。从经销商确定订货到销售,30天以内的销售比率从55.4%增加到80%。
图3 GTMC产销一体的管理信息系统应用图
从以上表述可以看出,整车物流系统是生产·销售·物流系统的重要组成部分。
3.贯穿始终的看板-“物流管理票”
当商品车下线并经检验合格后即进入整车物流环节,每台车均随车附带一张“物流管理票”(GTMC称之为扩大票)。“物流管理票”的精巧之处在于,从整车下线开始至销售店为止(包括后期的费用结算),在整车物流管理各环节均使用该票。GTMC工厂内整车物流管理工程见图4。
图4 GTMC工厂内整车物流管理工程图
“物流管理票”属于专门定制,分成两大部分。上半部分粘贴于商品车前挡风玻璃中上部,标明车辆身份和物流去向。下半部分有12联,上下部分及每一联用针孔(类似邮票)隔开,为每个物流管理工序进行作业指示。当商品车进入到一个作业环节,该工序操作人员撕开该工序的“物流管理票”的对应联(参考图5、图6)。“物流管理票”是GTMC整车物流系统看板应用的经典,每一辆车通过“物流管理票”明确搬运指示和搬运地点。GTMC 将整车物流管理过程上下工序进行严格区分,每一项工序用“物流管理票”的对应联与车身VIN(车辆识别码)及粘贴于前挡风玻璃的“物流管理票”进行信息的确认。将“物流管理票”中的小票据当作看板使用,使作业内容“JIT、可视化、简单化、循环往复”,不仅使作业人员及时了解作业指示信息,而且能够通过不同工序作业人员扫描“物流管理票”的对应联,将商品车物流状态录入系统,使管理人员和顾客能在IT系统里查询每一辆商品车的物流状态。
图5整车物流作业点
通过“物流管理票”信息与实车一一对应的关系,实现了信息和实物按照1:1的关系同步化,避免出错,提高了作业效率;通过看板管理“物流管理票”(物流管理票清晰显示车辆到达日),实现了先进先出和遵守交货时间【工厂→每一个据点→销售店,出货(车辆)都通过看板实现了先进先出,提高了交货准时率】。
图6物流管理票使用方式示意图
4.商品车YARD设置
商品车YARD由掌握TPS思想的广汽丰田物流有限公司(以下简称GTT)完成日常管理和作业。商品车YARD 保管及作业的企划(场地使用、作业流程等)是非常重要的工作。基于自働化和JIT的思想,以标准化管理为起点展开物流停车场的企划,GTMC商品车YARD依据《物流停车场设计标准化手册》进行综合考虑评价,确保物流作业遵循目标,有效地实施,确保“安全”、“品质”的作业,实现标准化的物流作业并按计划顺利地进行。
GTMC工厂每天要制造近千辆商品车,每一辆车在生产线上都已经有了明确的下线时间和物流去向(销售店)。每辆商品车在发运前只有必要的安全等待时间,用于商品车整列排队,使装载数量满足商品车轿运车发运批量。商品车YARD不是仓库,只是发运前一系列商品车搬运和临时停放的缓冲场地的总称。它与零部件厂外物流YARD 功能相同,是一个吸收作业不平准的池子,使整车物流末端作业(拖车运输)平准化。
图7商品车YARD作业示意图
商品车YARD的作用不仅仅有形成批次的缓冲作用,同时也有分类管理的作用【按M在(见后面的说明)、未入金(未付款)、已入金(已付款)、海运、陆运、销售店等规则进行分类】。由于GTMC的车辆是按订单生产及下线的,临时停车场(缓冲区)可以将不同目的地的车辆进行分类停放,这样在入库作业中,作业人员及足车(作业人员的代步车辆)的移动是点到点的移动,减少了人员移动的距离,提高了作业效率。例如海运区域的车辆,不需要区分目的地,可以直接驶入整列道,不拔取钥匙,短时等待后即装载去港口,缩短了商品车在主机厂仓库的物流等待、滞留时间。
商品车YARD极具特色,可称之为棋盘式管理。外部人员看到商品车YARD内的车辆停放,感觉停放的稀疏且没有规律(不同车型交错放置在一起),其实暗含很多规律与信息。GTMC每月编排次月的“停车场使用计划”,指导作业人员按计划操作,各销售店的车辆在YARD停放区域并不是固定不变的,根据上月生产计划、各销售店日均下线台数、配车等待天数等信息,以及销售店的销量比例(在日生产中所占比例),结合配车看板管理,分配次月每个订购商品车的销售店在库区的区域大小及位置。停车区依据经销店分类及权重进行商品车分区摆放,使商品车YARD在库车辆快速周转的同时,也让库位定置可视化。
已经进入商品车YARD的车辆属于待发车,车辆进入停车场,将钥匙和物流管理票中的钥匙管理放入看板袋,然后放置于钥匙看板管理架。物流管理票1联用于配车看板架,将同一销售店的物流管理票1联放入看板架同一格子内(根据拖车凑足6~12台为一板车),扫描后打印“运输指示书”。按照先进先出配车原则,每两小时进行一次,混载不能超过3家销售店;通过配车管理看板,当某个销售店下线的车辆形成批次后,即可下达发运指示。
当形成批次的车辆配车完毕后,即可打印出运输指示,进行整列发运。整列作业人员领取整列看板,进行整列作业。JIT的作业指令(后工序领取作业看板)的好处在此得到完美的体现,运输指示看板分为定期便与临时便,定期便基本确定了每个区域的拖车到场的时间。特殊情况会增加一些临时便,例如某些车辆滞留时间较长,仍未形成批次,需要与其他店进行混载运输出门,或不满载出门。
BTO模式,是实现JIT的前提。GTMC下线前订单与车辆绑定,通过有去向(目的地)的物流管理票的拉动实现JIT物流,入库时按销售店集中停放,从而提高了入、出库的效率。在按订单生产的拉动下,所有的作业均实现了JIT的操作。GTMC平准的物流管理模式下,物流服务商运力组织、调配计划性、操作性更强,车辆和司机的稼动率大幅度提高(例如海运部分的车辆可以每日固定车辆与周转频次),形成GTMC和物流商共赢的良性循环的环境,GTMC的物流成本才得以持续改善与下降。物流商的盈利能力不仅仅是物流企业内部的管理问题,与主机厂的物流模式也有很大的关系。
5.源于标准化的运输品质安全
由于国内大陆型的销售区域分布,整车物流的运输以公路运输为主,运输工具的安全品质水平直接关系到商品车安全品质。GTMC整车物流安全品质从源头做起,开展轿运车标准化(对于轿运车及轿运车司机进行作业标准化
的工作),确保拖车和司机在GTMC内的装载作业安全、规范、高效和在途的安全行驶。这些工作,是自働化(自工序完结)中良品条件和标准作业的具体体现。
根据生产计划、轿运车的标准装载单位及相关信息,预测每月需要的轿运车数量,并制定轿运车标准化检查的年计划、月计划及日计划。初次进入GTMC厂区进行轿运车标准化检查的车与司机信息(身份证、驾驶证、拖车车牌号等)要通知安全保卫科,安全保卫科与实车核对确认信息后,放行轿运车、司机进入GTMC进行轿运车标准化检查,核对司机基础信息,并对轿运车司机的驾驶技能及着装进行考核、确认。驾驶技能考核从理论知识考试和现场实际操作两个方面进行确认。对于标准化检查合格的轿运车,在系统上做确认后,发放《拖车装载许可证》。作业人员对进入GTMC的拖车整备(整理、准备)状况进行检查确认,合格的拖车方可进行装载作业,最大程度地确保作业和商品车的安全。对轿运车辆实施标准化的检查,确保每台轿运车(安全绳、捆绑工具、标识、轮胎、液压升降装载等)在装载时符合要求,确定每台商品车在轿运车上的停放位置(安全距离),确保拖车司机(装载、着装)的作业符合标准。
6.顾客至上的交付过程管理
对于新建销售店,GTMC将物流要求(轿运车进出门的宽度、转弯半径、安全高度、停放场地等)在建店指南中明确提出,对每家新开的销售店,都会在物流方面进行前期调查,并与销售店进行沟通,形成一份原始信息表格。相关信息包括:该店的详细地址,从GTMC到该店的路径(每段路多少公里,每段路的收费标准);接车联络人、联系方式、接车的时间(一年中哪些天不接车、每日接车的时间)、拖车的卸车停放地点(简单的图示)等,制作成《交车场所说明图》。该图随运输指示书打印出来,交给拖车司机,指引其如何到达销售店,在到达前与销售店工作人员联络,及如何进入销售店,拖车停放在何处,卸下商品车停放在何处等最终完成交车工作(如图8)。
图8商品车运输交车场所示意图
为确保物流公司与销售店之间正常、顺利地交接,对接车操作制定了专项基准(规则制定,宣传品的印制,相关规则的宣传、辅导,平时的跟踪管理及落实)。定期对销售店、运输公司进行培训,规范双方的操作。在整车交车过程中,不仅将销售店作为顾客提供标准化服务,而且为运输司机提供明确的作业指示和作业规范。GTMC整车物流建立双向沟通、培训体制,定期收集销售店、承运商的意见及建议,不断地完善交付制度,强化双方的规则意识,提高整体的物流效率。
在交付运输的末端,通过交接标准化和交车场所指示票,避免交接时不必要的纠纷并提高交付效率,在物流终端实现了TPS“顾客至上”(包含内外部顾客,物流服务商、销售店也被视作顾客)的理念。
7.整车物流中难以理解或容易误读的课题
GTMC非常重视物流工程上、下工序的衔接,始终贯彻自働化、JIT思想,并强调可视化、简单化和循环往复,对整车物流构筑起高效的作业循环模式。TPS思想指导下的整车物流,下工序在必要的时间去上工序引取必要的整车。首先是实现整车在下线时就完成分类排序功能,使之最终匹配各个销售店及发运装载需要;通过配车架下达JIT
的作业指令,在临时停车场完成无序到有序的转换,实现整车最小库存的缓冲功能,及时、准确的周转搬运强化了物流的流动和分类功能。
有观点认为,从工厂生产线下线后进入库区再对商品车按销售店的需求进行分配,对于销售是比较方便的,资源的调配、变化容易实现。TPS“彻底消除浪费(库存的浪费、动作的浪费)”的观点认为,如果主机厂的生产与销售店之间的订单不进行一对一的绑定,必然导致多余库存与多余的动作(即物流过程中增加的二次分配、移库),一部分生产出来的车辆是没有明确需求的,会带来库存管理和车辆品质维护等问题,而长期库存车的降价处理会造成更大的浪费。
有观点认为GTMC按订单生产,几乎没有整车库存,无法应对零部件品质突发问题,一旦发生品质问题时无法调配合格的整车满足销售店需求。TPS“自働化”的观点认为,全过程自働化的结果是高度一致的产品品质,GTMC 产品纳入不合格率的要求是小于15PPM(百万分之十五),难以想象“某种零部件部分品质异常”这样的说法,任何工序出现品质问题,应该停止生产,彻底解决品质问题,而不是先确保生产,在下工序再处理。库存掩盖品质问题,会导致问题不能彻底解决,并不断重复发生,反而不利于质量管理。
有观点认为GTMC也有不少整车库存,下线后停放在商品车YARD、码头的车辆,这些加起来也有不少库存。JIT的观点认为,整车物流的主要作用是以运输器具为单位(轿运车、船等)将车辆安全、准时地交付给顾客,必要的在途(便于批次形成,方便运输)不是库存,必要的在途之外的才视为库存。
有观点认为预测未来销售趋势向好时,建立必要的库存有明显优势,销售店没有订单临时有需求,则GTMC 的生产体系无法应对。其实也不尽然,GTMC用虚拟订单的形式完成生产储备(在GTMC称之为“M在”),平时严格控制“M在”的比例(月产量的1%~2%),是GTMC主动在供不应求的市场情况下为大客户生产的部分车辆;同时利用区域资源(调配)满足不同店的需求差异。只有在金融风暴和钓鱼岛事件中才被动的产生了一定比例的“M在”。GTMC及时根据订单变化情况调整了生产并产生部分“M在”,虽然对事业计划(经营目标)的完成有一定的影响,但将整个供应链的风险降到了最小。
有观点认为,BTO模式在面对市场波动时响应速度较慢,而BTS模式备有一定量整车库存可以应对市场需求波动则有明显的优势(参考《TPS在广汽丰田物流系统的应用及借鉴意义(下)》关于产销模式的阐述)。诚然,BTS模式在中国过去十年的爆发式汽车市场增长时,确实起到一定的销量扩张和抢占市场作用。可一旦市场回归理性、趋于稳定甚至下滑状态时,BTS库存对应方式的弊端开始显现。尤以2012年钓鱼岛事件为例,突发政治争端对日系车销售冲击直接导致库存激增,给汽车生产厂带来极大的困扰,因为模式不同,本田、日产等在国内的合资企业整车库存(台数、在库时间)远比GTMC高。随着国内经济和汽车销量增速放缓,如何减少库存对车企的现金流影响成为关注焦点。钓鱼岛事件的影响尚未消退之时,东风日产宣布:随着微增长时代的到来,东风日产新十年将用牵引式营销战略应对市场变化。在经历市场剧烈波动后,东风日产开始反思传统产销模式,探索面向BTO 模式下的生产与营销新体制。
有观点认为市场车型需求或车型的不同级别销售情况发生变化,导致部分车型需求提升,GTMC要次月甚至2~3个月(涉及进口件增加时)才能完成响应,理想状态是数日之内响应完毕。笔者认为TPS是站在全局思考的体系,考虑的是整体(整个供应链)的风险与利益(供应商的各种损失,最终都会以各种形式由汽车生产厂承担),快速响应的必要条件是主机厂或供应商有一定的预备库存,而库存是7大浪费的首恶。与快速增产相对立的是快速减产甚至停产,从《TPS在广汽丰田厂外物流系统的应用》的文章可以看出,GTMC整个供应链的响应速度很快,而这正是丰田在日本长期市场低迷中胜出的法宝。
8.结束语
GTMC以TPS思想为基础构筑的整车物流系统是TPS体系的重要组成部分,只有以TPS思想系统地加以理解才能认识整车物流系统。GTMC整车物流系统无处不在的“働
”的案例,可以帮助读者理解其精髓并形成“働”的思想,只有用“働”的思想、TBP的问题意识和解决问题的方法和胸怀服务于一切顾客(不仅消费者是顾客,销售店也是顾客,甚至供应商、物流服务商也是顾客,最终服务到所有的操作工)的心去思考并解决一个个课题,打造以“働”为核心的企业文化,统一每一个员工的价值观、行为规范和思考方法,在正确的工作方法下可以很好地培养员工,并与企业共同进步,长期坚持一定可以取得丰硕的成果、打造百年企业。
[参考文献]
[1]金光.丰田企业文化的剖析及借鉴意义[J].汽车科技,2011(2):5-11.
[2]金光.冯鸿.乐德林.金声.TPS在广汽丰田物流系统的应用及借鉴意义[J].物流技术与应用,2013(2):110-115,
(3):122-127.
[3]金光.金声.乐德林.冯鸿.TPS在广汽丰田零部件厂外物流系统的应用[J].物流技术与应用,2013(4):124-130.
[4]金光.乐德林.冯鸿.金声.TPS在广汽丰田零部件厂内物流系统的应用[J].物流技术与应用,2013(5):122-129.说明:本文发表于2013年第6期《物流技术与应用》,可以在知网或百度文库检索本文
丰田管理模式
丰田管理模式 成立于1937年的丰田汽车公司,自创立以来一直以“通过汽车,创造富裕社会”为基本指导方针,在全世界致力于为用户提供称心如意的汽车。丰田始终坚持全球统一品质标准,在性能和价格两方面,生产富有竞争力的汽车,并以一流的管理、经营理念使其在销售量、销售额、知名度方面均达到世界一流水平。 一、丰田管理的十二要决 在长期的管理中,丰田公司总结出了十二条基本要决。它流传很广,除了日本之外,在世界上许多国家的管理者也都将其默记在心,以便随时指导自己的工作。 第一,所谓管理,就是为下属提供管理上的建议,调整总体的工作,并且借用沟通,协助下属解决工作上所面临的困难,以及畅通无阻地推动管理的循环。 管理并非管制。所以管理者必须是一位建议者、一位计划者、而不是一位监督者和管制者。 此外,管理者所定下的目标是通过下属的工作来实现的。因此,管理者必须提供给下属恰当的建议,并发挥其领导能力,致力于培养下属,并成为最佳建议者。简单地讲,任何事都是一种给与取的关系,不付出就不会获得回报,“尽量地给,否则无理由取!”一语道出了管理者的职责。 第二,所谓管理,就是为了能够更经济地推动管理目标施行,建立不浪费资源的作业体系,同时也为了这些作业体系能够运作得更为有效率而建立了管理制度。
任何一个部门都会同时存在作业和管理的问题。一方面,管理者以人、物、设备为对象,建立一套减少浪费的作业体系来提高生产力;另一方面,管理者又必须时常为提升部、料、组而思考如何在管理上建立一套体系。只有如此这般,才能提高整体组织的工作效率,并且达到降低成本的效果。 其方法有以下几种: (1)制定一套以人、物、设备为对象,不浪费人力资源的生产流程,并且运用工业工程的方法来提高劳动生产力。 (2)运用提升整体效率的系统工程方法可以有计划地改革、改善部门的运作制度或组织的体制。 第三,所谓管理,就是为了要达到所设定的目标值,选择应当优先处理的重点项目,根据实际的分析数据,并且清楚地了解项目的背景,以重点导向来积极推动管理循环。 工作不分领域,总会存在形形色色、大小各异的项目。然而经营就必须讲究效率,不能随便选择。因此需要依据目的将资料做分门别类、层层递进的分析,根据结果,依据质量、成本、交货期的种类,选定优先的重点项目。而且,最重要的是重点施行选定的项目,以及将其施行效果反映到经营目的上。 第四,所谓管理,并不是一种简单的表面现象管理,例如将计划执行所产生不良现象的结果加以纠正,而是探求这一现象的真正原因并加以排除的管理。 纠正不良现象的善后管理是一种着重于表面现象的管理方法,缺乏效率,它导致成本长期持续的损失,但管理者若能够从根本上找出其产生不良现象的真正原因且能解决,将其转变为注重原因的管理方法,那么只需投入一次,便可以一劳永逸。以长期的眼光看来,这是非常有效率的。而管理者本来的职责就是真正地了解企业的基本理念,发挥其领导能力,督促下属实践该理念。
图解丰田生产方式读后感
《图解丰田生产方式》 结合自己的本职工作以及现在工厂涉及的TPS业务中存在的疑惑,读了《图解丰田生产方式的密码》一书,进一步加深了对丰田生产方式的理解,这套生产方式是作者大野耐一先生经过在丰田公司多年的实践和创新总结出来的。而且,它已经被证实是一套先进的、高效的生产方式。 丰田生产方式的体系及基本思想——杜绝浪费。 本书的第一章介绍的就是如何可以让企业有竞争力,经济生产力发展到今天,对于汽车这样消费品而言,消费者有很多的选择,面对这种竞争的压力,作为企业,‘价格=成本+利润’的定价方式早已不能适用。在丰田生产方式中从成本意识出发对利润有了全新的解释‘利润=价格-成本’虽然只是简单的公式变换但其中的内涵有着天壤的差别,其中给我印象最深刻的就是价格的定义,那就是售价必须在客户所期望的销售价格以下!这就说明企业经营者要想在同行内获得订单、提高竞争力,降低成本成为不二之选。而降低成本的最主要途径就是——杜绝浪费。 在我们工厂,浪费也大量的存在,从大方面说,散片库存积压、整车成品在调试工段进行返修、员工的流失、设备的停顿等等。往小的地方说,如生产线周围散落的螺钉、辅料的浪费、零部件不合格的替换,这些都存在于生产的方方面面。如果我们能够杜绝和消除,那么我们的生产效率可能提高几倍。 丰田生产方式的两大支柱——准时化、自働化。 本书的第二章及第三章介绍的是丰田作为汽车行业的巨头所具有的独特管理方式,准时化就是以市场为龙头在合适的时间生产合适的数量和高质量的产品。是在以拉动式生产为基础,以平准化为条件下进行的,在去年的赴日研修过程中,我有幸亲身感受到准时化生产现场的状态,在参观奥德克斯工厂时,他们的内部生产指示系统完全按照18分钟的循环开展工作,每一个人按照同样的节拍开展工作而且每日持续的坚持,实在是令人钦佩。 自働化是指在生产过程中,充分利用人员与设备的有机配合,达到简化生产,消除浪费的目的,还有另外一种说法就是将设备赋予人的智慧,即当机器发生异常情况就会停止运做,等到工作人员把异常排除之后才能重新启动机器。目视化管理是自働化能够实现的重要环节,只有将各个环节的生产状态进行目视,才能第一时间发现存在的问题,这就杜绝了现场中过量制造的无效劳动,防止生产不合格品的产生,也让企业更好的解决生产中的难题。 建立在尊重人的基础上的企业文化——持续改善 丰田生产方式旨在作为一种由员工的贡献和创造性所促进的动态过程,而不是一套固定不变的生产方法,它是不断地寻找更好的生产方法的指南。各部门的领导干部不可能看到和知道一切事情,而工人每天在工作时能够观察和了解到。断断续续地征询员工的想法远不如制订一项规定员工的建议如果得到采用,将会给予现金奖励的正式政策更有效。今天丰田在全球的所有部门都采用提建议制度,每年作出改进的总数成千上万条。平均每个员工11条,其中99%以上得到采纳。对比工厂现在每个员工1.98条的提案,差距还是比较大的,通常员工把精力主要放在看起来似乎微不足道的事上,例如建议在制造现场制作工具存储盒,使生产更方便,建议改变器具存放方向,方便拿取零部件。但是在这些年来实行的许多建议,例如,在汽车里改造可升降的座椅,或者在装配线上部分造好的
(丰田管理)丰田人力资源管理模式
丰田模式+当地环境+目标=成功 一、我们的目标是什么? 作为一个企业,丰田也希望赚钱,但这不是公司所追求的终极目标。丰田存在的目标是满足消费者的需求,为社会做贡献,并且实现所有员工和事业伙伴的长期共同繁荣。 虽然员工也期望最起码的工资和利益,但是同时也希望在积极的环境里实现个人事业的发展,希望能够不断学习、培养新的能力,在能够对社会产生积极影响的公司里工作。 如果把双方的利益集合在一起,其共同目标就是实现员工、公司和社会的长期共同繁荣。
二、塑造优秀员工,造就优质产品 一个优秀的员工应该是可塑的,能够在一个小组中工作,遵循并改进标准,受企业文化和目标的鼓舞,对家庭和社区做出积极的贡献。 丰田的优秀员工及其强大的文化凝聚力无处不在。丰田像生产零瑕疵产品那样为培养优秀员工做出了巨大努力。其结果是培养出了大批优秀员工,他们在塑造和支撑着丰田模式文化。 2.1优秀员工造就优质产品 人力系统模型假设:投资于优秀员工价值流能获得竞争优势和长期的共同繁荣。这表明形成适当的文化是经营成功的必要条件。 丰田的人力价值流信念:以正确的方式投资于员工培训将产生正确的结果。 跟踪并实现S(安全:safety)Q(质量:quality)C(成本:cost)D(交期:delivery)M(士气:morale)的目标是丰田文化的中心,也是人力价值流与产品价值流的结合点。从一开始公司就提醒每一个员工,如果紧密合作他们就能实现这些目标,为实现长期的共同繁荣他们将采取进一步的措施。 2.2追求质量的新文化 在工厂建立之初,就关注质量。无论员工还是经理不仅要执行标准作业,而且还要检查每个产品以避免出现影
(丰田管理)丰田人力资源管理模式
(丰田管理)丰田人力资源管理模式
2.2追求质量的新文化 在工厂建立之初,就关注质量。无论员工还是经理不仅要执行标准作业,而且还要检查每个产品以避免出现影响用户的任何可能缺陷。不仅要通过管理者的言行来强调质量第一,而且要到问题现场,训练小组和团队领导解决问题的方法,强调任何时候都不要让有“质量嫌疑”的产品进入消费者手中。 2.3暂停生产线是每个人的责任 生产线的暂停警示着工厂里的每个人,所有合适的资源都汇集到流程中来解决这个问题。所有的团队领导回去后都将这重要的一课与整个团队一起分享。丰田建立的文化能够使得员工放心地拉安灯线,尽管这样做会导致整个工厂都停下来,因为事实上如果他们不拉安灯线,存在的问题持续出现,最终仍然会导致整个工厂的生产暂停。 2.4按部就班 只有在每个人对产品质量的全心关注成为一种文化后,才开始期望其他关键性指标的成长,如提高生产效率和降低成本等问题。 成熟的持续改进流程最终要涉及生产系统的所有方面。一个团队活一家工厂在实现了安全、质量和停工期的目标(在成熟流程中需要再用一年)之后,面临的新挑战就是减少需要的流程数,以减少制造产品所需要的团队
成员数,从而降低生产成本。改进后的流程又要需要近两年的时间去融入到文化中,其中一半的时间用来指导团队成员进行团队合作,去发现并杜绝浪费,另一半时间则是让他们相信“每个人只有在工作中才能得到提高。” 三、对组织的投入 丰田文化植入新工厂时所需的3个关键性投入因素:丰田的理念和价值观、生产系统原则以及丰田对即将雇用的合格员工的影响方式。 3.1理念和价值观 相互尊重和持续改善是丰田模式建立的基础,而这些承诺则是相互尊重和持续改善的根本性理念和价值观,当然其他的一些理念和价值观对丰田文化也很重要,例如,从长期的角度对待供应商和员工关系,每一名员工都是检查员,每名团队成员都是专家、主管是为其他成员服务,等等,这些理念或价值观共同构成了丰田文化。丰田文化起源于它的领导者,他们信守并传播自己的理念。丰田所有的管理者必须接受正式的课堂训练和在职指导来加强对丰田模式价值观的理解。然后这些管理者成为其下属的导师和教练,其中包括管理层和计时人员之间起关键作用的小组领导。 3.2生产系统原则 新员工进入丰田时都要有经验丰富的关键领导者的教导,还需要熟悉由一组操作原则定义的操作。
JIT-丰田管理模式
JIT-丰田管理模式 丰田的生产和管理系统长期以来一直是丰田公司的核心竞争力和高效率的源泉,同时也成为国际上企业经营管理效仿的榜样,例如,作为丰田生产管理一大特 点的看板管理已被世界各地的企业所采用。如今,世界很多大型企业都在学习 丰田管理模式的基础上,建立了各自的管理系统,以试图实现标杆超越,像通 用电气公司、福特公司、克莱斯勒公司等世界著名企业都加入了这一行列。但是,令人惊异的是,尽管丰田管理模式已为全球所认同和接受,真正成功的企 业却并不多,如今位于日本的丰田公司每天都要接受数以万计的企业高级管理 者参观,这些参观者将他们看到的管理方式带到本国后,并没有得到意想的效果,为此,很多人认为丰田管理模式的成功根源于其独特的文化因素。但事实 并非如此,例如同是日本公司的尼桑和本田却并没有达到丰田的标准,而丰田 本身却将其独特的管理模式带到了全世界,这其中的代表就是位于美国肯塔基 州的丰田乔治城汽车生产厂,该厂自1988年7月开始在1300英亩的厂址上进 行批量生产,年生产能力为200000辆Camry轿车,相当于以往美国从日本进 口同类型轿车的总量,1991年秋天丰田美国公司引入了全新的Camry 轿车,1992 年该类型车的供应量为40000辆,销售额将增加20%。新的Camry轿车 属于中等家庭车系列,占有美国所有轿车市场l/3的市场份额,价格平均为$18500,税前平均利润为17%,显然,其经营绩效是十分瞩目的。 由此看来,丰田管理模式并不是因为其独特的日本文化而难以为其它国家的企业所学习,之所以存在管理方法难以移植的情况,主要原因在于参观者所看到的丰田管理模式只是其外在的东西,诸如它的活动、连接和生产流等都是较为固定、甚至死板的东西,但是,在这些看似简单的活动和流程后面,却蕴含着丰田公司巨大的柔性和适应性,正是这些看似简单、却颇具柔性的管理特点,造就了丰田公司举世瞩目的经营业绩,也使得他的柔性化生产管理方式--TPS (Toyota Production System)成为管理中的精髓,并使大规模定制模式下的敏捷产品开发和生产成为现实。以下从纵(历史发展)、横(管理特点)两个方面来揭示丰田公司JIT管理的奥秘。 的"Just in Time"这一理念的具体体现。
TPS管理模式
TPS管理模式 丰田的生产和管理系统长期以来一直是丰田公司的核心竞争力和高效率的源泉,同时也成为国际上企业经营管理效仿的榜样。世界很多大型企业都在学习丰田管理模式的基础上,建立了各自的管理系统,以试图实现标杆超越,像通用电气公司、福特公司、克莱斯勒公司等世界著名企业都加入了这一行列。中国第一汽车集团公司和东风公司也都推行了JIT和“一个流”,取得了一定成效。 但是,令人惊异的是,尽管丰田管理模式已为全球所认同和接受,但学习者和模仿者与丰田公司始终存在差距。其原因除了环境差别之外,主要是未能把握丰田生产方式的实质,因此只能做到“形似”,而不能做到神似。以下从纵(历史发展)、横(管理特点)两个方面来揭示丰田公司JIT管理的奥秘。 一、 JIT生产方式 JIT(Just In Time,简称JIT)生产方式的基本思想是"只在需要的时候,按需要的量,生产所需的产品",也就是追求一种无库存,或库存达到最小的生产系统。JIT的基本思想是生产的计划和控制及库存的管理。 JIT生产方式以准时生产为出发点,首先暴露出生产过量和其他方面的浪费,然后对设备、人员等进行汰淘、调整,达到降低成本、简化计划和提高控制的目的。在生产现场控制技术方面,JIT的基本原则是在正确的时间,生产正确数量的零件或产品,即准时生产。它将传统生产过程中前道工序向后道工序送货,改为后道工序根据"看板"向前道工序取货,看板系统是JIT生产现场控制技术的核心,但JIT不仅仅是看板管理。 JIT的目标是彻底消除无效劳动和浪费,具体要达到以下目标: 1.废品量最低(零废品)。JIT要求消除各种引起不合理的原因,在加工过程中每一工序都要求达到最好水平。 2.库存量最低(零库存),JIT认为,库存是生产系统设计不合理、生产过程不协调、生产操作不良的证明。
TPS丰田生产体系
TPS丰田生产体系 TPS丰田生产体系编辑 丰田式生产管理(Toyota Management),或称丰田生产体系(Toyota Production System,TPS)由日本丰田汽车公司的副社长大野耐一创建,是丰田公司的一种独具特色的现代化生产方式。它顺应时代的发展和市场的变化,经历了20多年的探索和完善,逐渐形成和发展成为今天这样的包括经营理念、生产组织、物流控制、质量管理、成本控制、库存管理、现场管理和现场改善等在内的较为完整的生产管理技术与方法体系。 目录 1简介 2由来 3理论框架 4关键原则 5实施条件 6T存在问题7管理特征1简介编辑丰田生产方式又称精细生产方式,或精益生产方式。 美国《商业周刊》2003年第一期评选出世界十五位最杰出经理人,日本首家税前盈余超过1兆日元(87.4亿美元)的企业———丰田,其社长张富士夫(Fujio Cho)名列榜上。在日本经济被人形容为“处在黑洞看不见曙光”之际,张富士夫此时能获选,具有典范的意义与价值。 张富士夫认为,日本要脱离困境,无论是制造、服务业或者是政府,唯一的良方就是打破传统产业(部门)藩篱,也就是要改变僵固思维模式,引进“丰田式生产管理”。 通过塑造丰田式生产管理的企业文化,张富士夫领导这家世界第三大的汽车厂,建立全球制造和销售系统,成绩亮丽,创下净利达46亿美元,销售额比前一年同期增长15.4%为657亿美元,并满怀信心宣示:“要实现全球年销售量600万辆的目标”,“要从现在全球10%占有率提升至15%”。 2由来编辑20世纪后半期,世界汽车工业进一个市场需求多样化的新阶段,而对质量的要求也越来越高,这就给制造业提出了这样一个新课题:只有有效地组织多品种、小批量生产,避免生产过剩所引起的设备、人员、库存、资金等一系列资源浪费,以保持企业竞争能力。在这种历史背景下,从丰田相佐诘开始,经丰田喜一郎及大野耐一等人的共同努力,综合了单件生产和批量生产的特点和优点,创造了一种多品种、小批量混合生产条件下高质量、低消耗的生产方式。 追根溯源,从理论渊源上看,它是美国企业管理理论与日本本土企业实践”嫁接”的产物。2O 世纪50年代初,朝鲜战争爆发,美军为了解决后勤军需问题,就近在日本下订单,采购军需品。但从朝鲜前线反馈回来的信息表明,从日本采购的电话机质量不稳定,问题较多。麦克阿瑟将军到日本去视察,发现日本企业完全是手工作坊式的装配,没有明确的分工和作业流程,更别提流水作业了。于是,麦克阿瑟将军请美国国防部的军需官,为日本企业起草了MTP (中级管理技术)和JIS(基层督导员相当于主任或班组长)两套培训教材,借助这两套教材,日本企业开始了从模仿外国产品到学习外国管理的转型过程,把美式管理中的技术层面同日本文化结合起来,从而诞生了TPS。 3理论框架编辑丰田式生产管理哲理的理论框架包含“一个目标”、“两大支柱”和“一大基础”。 “一个目标”是低成本、高效率、高质量地进行生产,最大限度地使顾客满意。 “两大支柱”是准时化与人员自觉化。
图解丰田生产方式
《图解丰田生产方式》——初赛竞赛试题A 一、必答题单元 1、以下答案中,制造成本包括:(ABC) A 材料费 B 劳务费 C 经费 D 员工工资 2、以下属于看板种类的是:(BD) A 信息看板 B 生产指示看板 C 现品票看板 D 搬运看板 3、三现主义是:(ACD) A 现场 B 现品 C 现物 D 现实 4、以下哪一项不属于生产过剩的浪费生产的原因是:(D) A 设备过剩 B 大批量生产 C 生产效率提高 D 表面作业 5、丰田思想中,有一个3MU的概念,以下哪个不是属于3MU的范畴: (D) A 超负荷 B 浪费 C 不均衡 D 低效率 6、下列哪一项不属于“可视化”的手段:(C) A 指示灯 B 星型表 C 五色图 D 看板 7、我们可以通过各种各样的探测来防止错误,以下哪一项不属于防止 错误的探测分类:(B) A 接触式探测 B 抽样式探测 C 定数式探测D标准动作异常探测 8、在丰田生产方式中,下道工序会把什么信息反馈给前道工序:(B) A 工序拉动 B 加工前检查 C 自主检查 D 加工后检查 9、上世纪80年代,丰田公司在美国汽车配送中心开始将代销商的“每 周提货”改为“每日提货”。请问,以下哪一项不是丰田公司用来补 偿“每日提货”增加的费用:(D) A节约存货成本B消灭加急送货费用C简化提货过程D给代销商提价 10、丰田喜一郎曾说,“产品的各部分及时被安装好是很重要的”,请问这 句话体现了丰田生产方式的什么思想:(B) A 均衡化 B 准时化 C 标准化 D 流程化 11、just in time (准时化)不成功的原因,以下正确的是:(ABCD) A 顾客要求没有被均衡化B减少机械设备故障的TPM体制不够完善 C 不能够灵活对应小批量生产 D 作业人员不具备迅速解决问题的能力 12、后道工序领取的好处是:(ABC) A 减少中间品的库存 B 减少空间浪费 C 减少搬运浪费 D 增加节拍时间 13、丰田解决问题的根本思想是:(A) A 三现主义 B 降低成本 C 提高效率 D 发现浪费 14、以下对5S中“整顿”解释正确的是:(C) A 将不必要的东西清除掉的技术 B 瞄准目标彻底实施的技术 C 确保必要的东西在必要的时候能够立即使用的技术 D 发现浪费的技术 15、与丰田生产方式的目的无关的是:(C) A 浪费 B 高收益 C 高速度 D 高质量 16、哪种情况更贴切拉动式生产:(D) A 手工作坊 B 食盐生产 C 石油炼制 D 超级市场销售
1 2图解丰田生产方式学习要点1 2
《1-2图解丰田生产方式》学习1-2 要点. 《图解丰田生产方式》1、2章学习要点 1、3MU:muri(超负荷的人员或设备)、muda(浪费)、mura(不均衡) 2、效率:效率=生产数量/人数 3、作业分类:浪费作业;纯作业;附加作业。浪费作业指只使成本增加而不产生附加价值的作业,比如停工等活、搬运、寻找工具等;纯作业指能够产生附加价值的作业,如组装零部件;附加作业指不产生附加价值但又必须伴随着纯作业一起实施的作业,如换模。
4、七种浪费:生产过剩、制造不良品、停工等活、动作上、搬运、加工本身、库存。 5、处理7种浪费的步骤:JIT的思想;消除不合格产品;消除停工等活;减少工时数要谨慎;搬运距离和搬运次数上优 化;识别加 工过程中不产生附加价值的动作;最后阶段消除库存浪费。 6、丰田认为,生产过剩是罪恶之源,生产过剩中还包括提前生产。瞄准“零库存”战略的企业,首先应该从消除生产过剩开始。如果机器经常发生故障或更换作业上花费太多时间,则无望实现。库存多,则绝大部分问题都被掩盖。 7、零库存前提条件:不产生不合格品、不发生机器故障、帐实相符、活用看板和库存管理方法(经济订货批量、定期补货等) 8、零库存从提高库存精度开始:出现误差的企业无论盘点多少次,其结果都一样。因此,需查找误差的真正原因。 9、丰田生产方式概要:自动化和准时化两大支柱,准时化指在必要的时候生产必要数量的必要产品。即后道工序在必要的时候到前工序去取需要数量的产品或零件,前工序只生产需要领取的部分产品或零件,不会产生不必要的库存。这种方式以均衡化生产为前提。 10、自动化是人性化的自动化,把人的智慧和机械设备有机结合。当生产不合格品时,机器会停止操作,从而消除后工序可能得麻烦;如果不包含人的因素,及时在发生异常时,机器会继续运转,从而生产大量不合格品,甚损坏机器设备。 11、准时化:也就是JIT,以均衡化生产为前提,由生产的流程化、确定符合需求数量的节拍时间、后道工序在必要的
丰田公司TPS管理模式
丰田公司的TPS管理模式 丰田的生产和管理系统长期以来一直是丰田公司的核心竞争力和高效率的源泉,同时也成为国际上企业经营管理效仿的榜样,例如,作为丰田生产管理一大特点的看板管理已被世界各地的企业所采用。如今,世界很多大型企业都在学习丰田管理模式的基础上,建立了各自的管理系统,以试图实现标杆超越,像通用电气公司、福特公司、克莱斯勒公司等世界著名企业都加入了这一行列。但是,令人惊异的是,尽管丰田管理模式已为全球所认同和接受,真正成功的企业却并不多,如今位于日本的丰田公司每天都要接受数以万计的企业高级管理者参观,这些参观者将他们看到的管理方式带到本国后,并没有得到意想的效果,为此,很多人认为丰田管理模式的成功根源于其独特的文化因素。但事实并非如此,例如同是日本公司的尼桑和本田却并没有达到丰田的标准,而丰田本身却将其独特的管理模式带到了全世界,这其中的代表就是位于美国肯塔基州的丰田乔治城汽车生产厂,该厂自1988年7月开始在1300英亩的厂址上进行批量生产,年生产能力为200000辆Camry轿车,相当于以往美国从日本进口同类型轿车的总量,1991年秋天丰田美国公司引入了全新的Camry轿车,1992年该类型车的供应量为40000辆,销售额将增加20%。新的Camry轿车属于中等家庭车系列,占有美国所有轿车市场l/3的市场份额,价格平均为$18500,税前平均利润为17%,显然,其经营绩效是十分瞩目的。 由此看来,丰田管理模式并不是因为其独特的日本文化而难以为其他国家的企业所学习,之所以存在管理方法难以移植的情况,主要原因在于参观者所看到的丰田管理模式只是其外在的东西,诸如它的活动、连接和生产流等都是较为固定、甚至死板的东西,但是,在这些看似简单的活动和流程后面,却蕴含着丰田公司巨大的柔性和适应性,正是这些看似简单、却颇具柔性的管理特点,造就了丰田公司举世瞩目的经营业绩,也使得他的柔性化生产管理方式--TPS (Toyota Production System)成为管理中的精髓,并使大规模定制模式下的敏捷产品开发和生产成为现实。以下从纵(历史发展)、横(管理特点)两个方面来揭示丰田公司JIT管理的奥秘。 一、JIT生产方式 透视丰田生产方式,会发现三位杰出的人物:丰田佐吉、其子丰田喜一郎和一名生产工程师大野耐一。 佐吉的儿子喜一郎于1927年完成了’即时到位’的生产思想和方法,即彻底完备各种专用工作机器和加工组装工具,并统一它们的规格,与此同时,对零部件进行提前喷漆和辅助安装,然后供给组装工厂的流水作业形式,这就是后来成为’丰田生产方式’另一大支柱的’准时化生产’体系。 喜一郎远赴美国学习了亨利福特的生产系统。归国时,他已经完全掌握了福特的传送带思想并下定决心在日本的小规模产量汽车生产中加以改造应用。喜一郎的办法是,在装配生产线的各工序,只在必要的时候,提供必要数量的必要零件。因此,每一道工序只是在下一道工序需要的时候,才生产所需种类和数量的零部件。生产和输送在整条生产线上,同时协调进行,在每一工序中和不同工序间都是如此。喜一郎就这样奠定了’just in time’(零部件应在正好的时间到达正好的位置的准时生产片)的基础。
丰田生产方式
《丰田生产方式》读后感 12级工商管理辅修江凌峰3115503011 读完《丰田生产方式》一书之后,我更全面系统的了解了这一先进生产方式的基本理念及具体实施办法。这套生产方式是作者大野耐一经过在丰田公司多年的实践和创新总结出来的。而且,在丰田,它已被证实是一套先进的、高效的生产方式。所以,这种生产方式才会风靡全球,各国企业纷纷学习效仿。 本书通过清晰的概念、具体的方法、生动的实例全面阐述了丰田生产方式,每个章节都是至关重要的精华,缺一不可。这里,我就从其基本思想――“彻底杜绝浪费”这一角度谈谈自己的认知。 经济生产力发展到今天,消费者几乎对任何一种商品都有很多选择权。正如书中所说,做为企业,“成本+利润=价格”的定价方式早已不能适用。企业经营者要想在同行业内获得订单、提高竞争力,降低成本自然是不二之眩降低成本的最主要途径就是――杜绝浪费。 我们不妨先来看看浪费的危害性。以书中的例子来说:假设库存零件超过了需求量,首先是对公司资金的积压,如果库存量超过了工厂现有的容纳量,还得重新建厂房仓库,建好以后,又得请工人把这些多余零件搬到新的仓库。零件(特别机械企业的金属加工件零件)存放在仓库里,为了防止生锈损坏和管理库存,就得再请仓库保管员。尽管如此,库存的产品依然不可避免的会损坏,等到用的时候还得有人去除锈,修理。或者,库存过多的零件可能会因为设计的更新而不能再使用,只能白白扔掉。而且,存入仓库的产品,就要经常掌握其各种数据,为此,仓库管理者就要花费更多的工时及办公设备。更糟的是,一旦因为库存过多而无法清楚掌握这些库存品的情况,就会发生部分零件缺货,进而可能会认为是生产力不足而去再增加设备,增加生产人员,然后则会生产更多的库存品。这种恶性循环的浪费是非常巨大的。由此可见,仅仅因为生产了过量的不需求零件,会派生出多少的浪费。同理,过多的人员,过多的设备,过多的材料,都会产生惊人的浪费。使企业的成本增加。 只有充分认识到浪费的危害性,才会重视这个问题,在企业的生产过程中,
丰田模式(TPS)学习心得
丰田模式(TPS)心得体会通过学习了解到。TPS的本质要求公司不断进步,并提升公司的作法。因此TPS亦被称为“一套帮助人们持续提高他们的工作的工具”。全书丰田模式的14原则可以分成四个部分:1)长远的理念,2)正确的步骤会产生正确的结果,3)通过提升你的员工增加企业的价值。4)不断解决根本问题会促进整体学习。 通过学习丰田的生产模式让我了解到丰田以一线员工为主来开发他们的潜能,找出问题点的所在,激励员工以提案的方式来改善种种不足。任何人可以在发生问题时喊“停”。丰田给员工提供机会与自主,同时也同我们QC活动持续改进的目的相辅相成。这样不仅是给员工的鼓励,更是一个自信心积累过程。因为他发现这个流程的错误,得以及时改善而没有造成严重后果。自然得到的是奖励,能够体会到成功的喜悦,从而更加投入工作。相反,如果认为他发现流程错误是他的本质工作,理所当然的事,没有及时给予鼓励及恳定,不加以赞许,就得不到十足的员工士气。 我认为只有具备发现问题的能力,才会更好地去解决问题,同样丰田对每一位新员工也很重视,由专职人员来教导,并传授他们经验与寻找问题的方法及解决问题的方法。当然,首先要学会独立,不能依靠他人来完成自己的事,若是这样永远不会成长。 丰田非常重视方法。无论是生产还是在原物料上,他们都会想方设法去降低一切能降低的成本。如:丰田帮助供应商找到流程的上错
误,来降低自己的原物料成本。不但降低了供应商自己的成本,也降低了自己的成本。大多企业都不会去做这样的事情,认为我帮他来解决问题降低成本谁为帮我解决问题降低成本啊?而丰田却相反主动极枳去帮助供应商解决问题来达到降低自己的原物料成本。 丰田重视过程管理。让生产设备具有发现问题并能立即停止生产的能力。同时设置一种视觉系统以警示团队或计划领导者某部机器或某个流程需要协助。如汽车生产线的“安东”系统。如果员工只是做上级指派的工作,你就会在生产线的终点不断看到有瑕疵。我们希望员工超越自己接收到的指示,并发挥创意,在流程内建立品质。追出问题根源是至高的指导原则,从基层员工到高层主管,所有人都要落实。丰田文化极枳鼓励较低层的员工向主管指出问题所在,而且会对此给予公开表扬。 丰田的执行力强,员工的思维模式自由奔放,以致于提出更好的改善。联系实际我的工作与相差太远了,我要学习丰田生产模式的原则与方法。我认为应该提供机会让人去探索无限的可能性,鼓励员工要超越工作职掌,并希望创造出无限的可能性。平时工作时多给予组员鼓励与支持,对每位组员提出的问题认真的对待与解决,并寻找问题根源,落实执行,不能怕失败。 当前正在推进精益生产的企业许多使用了丰田生产方式的各种工具。个人认为,部分企业只依循丰田模式中的少数几项原则,其结果可能是绩效指标在短期跃升,但无法持久。相反,若企业确确实实地实行整套的丰田模式原则,将会自然而然地遵循丰田生产方式,那
TPS丰田式生产管理新简介
TPS豐田式生產管理簡介 講師﹕劉協理 2006年6月12日 一、前言 『自需要出發』,如何在低成長中生存下去,且企業能賺錢是當前迫切課題 二、背景分析 1〃自行車供過於求,市場呈飽和狀態,客戶普徧庫存多 2〃原材料﹐有色金屬。汽油大幅度上漲﹐產品單价無法做有效的反應 3〃商業型量販店興起,形成低價競爭﹐微利的時代 4〃商品成熟化,產業差異化縮小,大陸組車、零件廠興起,形成低價要性競爭 5〃同業新的專業強勁對手掘起,有SR、RST、MOZO、ROCKSHOK 6〃商品研發力、品牌力、技術力弱,品級、市場無法突破國際化行銷
~1~ 三、TPS和HPS定義
~2~ 四〃TPS豐田式生產管理架構 4-1架構圖 TPS目的
~3~ 4-2 T PS生產方式與品質管理 ⊙及時化四大實施戰術
~4~ 五、TPS生產方式意義 將豐田生產方式加予分解﹐則首先是[豐田式流線化生產]﹐就是將生產現場變成一個流佈置,過去的車床﹑銑床都是分別集中在一處。現在則改為依照製造過程先車床﹑次銑床﹑後鑽床一台一臺地照順序排列的方式來佈置﹐生產物件則照制程順序在流動。由於這樣作法將原來一人負責操作一台﹐移轉到了一人負責多台機器﹐正確地說是一人負責多項制程過程﹐藉以提高了生產力。 第二項是[超市化生產]之應用﹐這是為了實行[豐田式生產管理]中之[及時化]生產的一個手段﹐其精神就是達到必要的時候,能適時供給必要的產品﹐必要數量的目標。不提早生產或是過量生產,重點是在降低原材料、在製品及成品的庫存。 當超市料架上的物品被取走後,在架子上的數量,當然也跟著下降了,當降到某一數量(訂購點)時,店員就會定時的拿取一張補貨單傳票,登記料架欠缺商品數量,由倉庫補貨進來,這時大倉庫內貨源也會跟著減少,但減到某一個訂購點的數量時,倉 庫管理員會自動向供應商發出訂購單,補貨進來.這就是超級市場的運作方式.由後制 程的消費者開始,向前制程取貨,所以也稱為[後補充生產方式]或簡稱為[後拉式生產] [看板]扮演了傳達物料流動之[領用情報]或[搬運指示情報]或作為生產過程內之[作業指示情報]而有效發揮了生產指示情報回饋功能。 第三項重點是『安定化生產』,當流線化生產後,生產線會陸續暴露更多的潛在問題,機械故障多、不良品發生、人員流動、產品更換時間長等等管理的問題相繼產生。因此,如何使生產線安定下來,就有下列五大課題要做改善。 (1) 人員的安定:取決於『標準作業』 (2) 機器的安定: 取決於『可動率的提升』 (3) 品質的安定: 取決於『零不良的追求與保證』 (4) 物量的安定(經濟生產) : 取決於『一個接著一個流、快速切換』 (5) 管理的安定: 取決於『公司標準、目標,計劃確立及人的管理』 ~5~
丰田精益生产模式介绍(TPS)
丰田精益生产模式介绍(TPS) 丰田精益生产方式(TPS-Toyota Production Sys tem)是由日本丰田汽车公司的副社长大野耐一创建的,是丰田公司的一种独具特色的现代化生产方式。它顺应了时代的发展和市场的变化,其间经历了20多年的探索和完善,逐渐形成和发展成为一套完整的生产管理技术与方法体系。 丰田生产方式使得丰田汽车在全世界获得成功。通和认为:从更高的意义上说,丰田生产方式代表了一种崇尚创新的企业文化和企业精神,丰田生产方式是一场意识革命。那么,中国企业就很有必要需要了解其TPS这种具有东方文化背景的管理模式的特点、核心、内涵等特征。下面我们就主要从TPS精益生产模式和中国企业在推行TPS方面存在的显著问题、解决途径以及企业精益化之路等方面进行重点阐述,相信一定会对我国企业的现代化管理具有极强的参考和借鉴作用。 一、TPS由来的简单回顾20世纪后半期,世界汽车工业进入一个市场需求多样化的新阶段,而对质量的要求也越来越高,这就给制造业提出了这样一个新课题:只有有效地组织多品种、小批量生产,避免生产过剩所引起的设备、人员、库存、资金等一系列资源浪费,以保持企业竞争能力。在这种历史背景下,从丰田相佐诘开始,经丰田喜一郎及大
野耐一等人的共同努力,综合了单件生产和批量生产的特点和优点,创造了一种多品种、小批量混合生产条件下高质量、低消耗的生产方式,这就是精益生产,其核心是追求消灭包括库存在内的一切“浪费”。 二、TPS生产管理哲学的理论框架 丰田式生产管理哲学的理论框架包含“一个目标”、“两大支柱”和“一大基础”。 “一个目标”是低成本、高效率、高质量地进行生产,最大限度地使顾客满意;“两大支柱”是准时化(JIT)与人员自觉化; “一大基础”是指改善,改善是丰田式生产管理的基础。 这里的改善是指这样的含义: (1)从局部到整体永远存在着改进与提高的余地。(2)消除一切浪费。(3)连续改善(Continuous Improvement)。 三、精益生产的特点 精益生产作为一种从环境到管理目标都全新的管理思想,并在实践中取得成功,并非简单地应用了一、二种新的管理手段,而是一套与企业环境、文化以及管理方法高度融合的管理体系,因此精益生产自身就是一个自治的系统。精益生产与大批量生产方式管理思想相比较而言,主要在优 化范围、对待库存的态度、业务控制观、质量观以及对人的态度方面有很大的不同。而精益生产在管理方法上的特点主