上海太阳能科技有限公司40MW太阳电池组件全自动生产线项目可行性实施报告
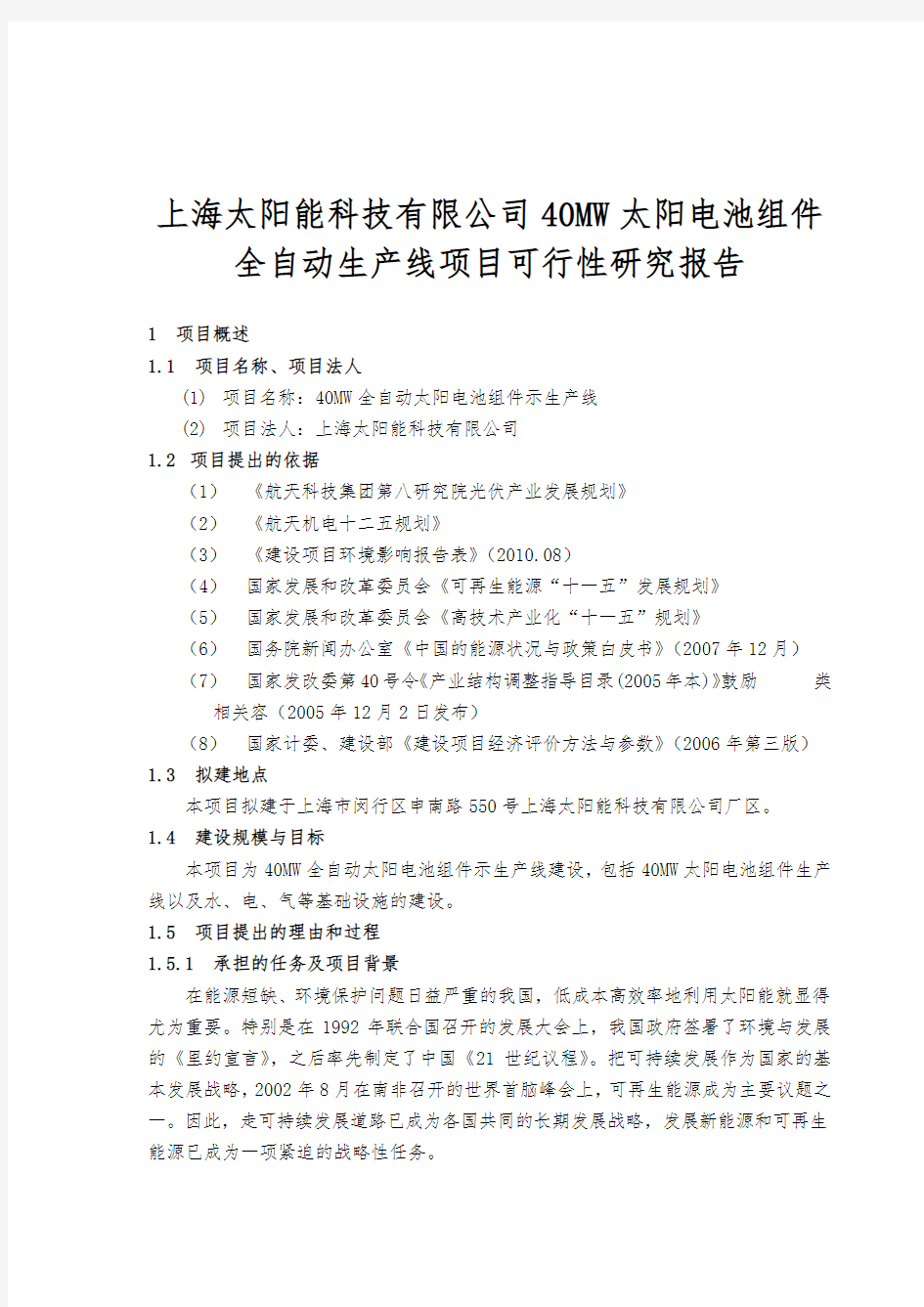

上海太阳能科技有限公司40MW太阳电池组件全自动生产线项目可行性研究报告
1项目概述
1.1 项目名称、项目法人
(1)项目名称:40MW全自动太阳电池组件示生产线
(2)项目法人:上海太阳能科技有限公司
1.2 项目提出的依据
(1)《航天科技集团第八研究院光伏产业发展规划》
(2)《航天机电十二五规划》
(3)《建设项目环境影响报告表》(2010.08)
(4)国家发展和改革委员会《可再生能源“十一五”发展规划》
(5)国家发展和改革委员会《高技术产业化“十一五”规划》
(6)国务院新闻办公室《中国的能源状况与政策白皮书》(2007年12月)(7)国家发改委第40号令《产业结构调整指导目录(2005年本)》鼓励类相关容(2005年12月2日发布)
(8)国家计委、建设部《建设项目经济评价方法与参数》(2006年第三版)1.3 拟建地点
本项目拟建于上海市闵行区申南路550号上海太阳能科技有限公司厂区。
1.4 建设规模与目标
本项目为40MW全自动太阳电池组件示生产线建设,包括40MW太阳电池组件生产线以及水、电、气等基础设施的建设。
1.5 项目提出的理由和过程
1.5.1 承担的任务及项目背景
在能源短缺、环境保护问题日益严重的我国,低成本高效率地利用太阳能就显得尤为重要。特别是在1992年联合国召开的发展大会上,我国政府签署了环境与发展的《里约宣言》,之后率先制定了中国《21 世纪议程》。把可持续发展作为国家的基本发展战略,2002年8月在南非召开的世界首脑峰会上,可再生能源成为主要议题之一。因此,走可持续发展道路已成为各国共同的长期发展战略,发展新能源和可再生能源已成为一项紧迫的战略性任务。
世界光伏组件产量上世纪末最后10年的平均增长率为20%,在各国政府的推动下,目前全球光伏产业年均增长率已高达30%,多年来光伏产业一直是世界增长速度最高和最稳定的领域之一,也成为全球发展最快的新兴行业之一。2010年以前,光伏行业持续30%以上的高速增长,2010~2040年,光伏行业的复合增长率将高达25%,可预见的高速增长将持续40 年以上。光伏产业的发展前景已经被愈来愈多的国家政府所认识,特别是 1997 年以来许多发达国家和地区纷纷制定光伏发展规划,如到2010年,美国计划累计安装4.6GW(含百万屋顶计划);欧盟计划累计安装 6.7GW(可再生能源白皮书);日本计划累计安装5GW(NEDO 日本新阳光计划),预计其它发展中国家1.8GW(估计约10%),预计世界总累计安装18GW。我国光伏产业近几年发展也极其迅速,已成为我国新兴产业。太阳能光伏属高技术光电产业,是国家重点发展的高新技术产品。实施本项目符合我国高新技术产业发展的需要,符合能源发展的需要,符合我国节能减排的大背景。
自2003年以来,航天光伏业务高速发展,但随着欧洲市场的迅速发展,光伏产业的国际化程度越来越高,对企业规模、上下游资源整合能力要求越来越高,因此,鉴于对市场前景的认识和航天光伏产业自身发展的需求,提出本项目的建设,使之成为航天光伏产业的经济增长点。
航天机电下属上海太阳能科技有限公司、神舟新能源有限公司及上海神舟新能源发展有限公司在上海拥有太阳能电池片生产能力和组件封装生产线,组件封装年产能已达到650MW,电池片年产能200MW,此外,航天机电控股的神舟硅业拥有年产3000吨的多晶硅材料的生产线,为整合航天光伏产业链,满足市场发展的需求,通过本项目的实施,一方面实施光伏组件由上海向周边省市实现梯度转移的战略目标,进一步降低生产成本,同时扩大太阳电池组件产量,将完善航天机电产品结构,提高竞争和盈利能力。
在上述组件生产厂区,部分使用全人工生产线和半自动组件生产线,性价比高,但自动化程度不足。目前市场对组件质量和使用寿命要求较高,即对生产过程中的质量控制有很大要求,而半自动线及人工线中人工的使用是不可避免的,这对产品的质量带来的不稳定性,而全自动生产线却能很好的避免这问题。
1.5.2 建设必要性
顺应国家新能源产业规划
在常规能源即将枯竭的二十一世纪,新能源已成为世界经济发展中最具决定力的五大技术领域之一,各国政府都将新能源资源利用作为国家可持续发展战略的重要容。我国的现状主要是煤炭的巨量消费已成为大气污染的主要来源,同时又具有丰富的太阳能、风能、生物质能、地热能和海洋能等新能源和可再生能源资源,因此政府一直采取积极地新能源推动政策。
1995年1月,国家计委、国家科委、国家经贸委制定的《1996-2010年新能源和可再生能源发展纲要》,明确要按社会主义市场经济的要求,加快新能源和可再生能源的发展和产业的建设步伐。2000年8月,国家经贸委资源节约与综合利用司颁布的《2000-2015年新能源和可再生能源产业发展规划》,系统地分析了中国新能源和可再生能源产业化发展的基础、市场开发的潜力、预期效益、制约因素和存在的问题。2002年6月,《中华人民国清洁生产促进法》,提出了清洁生产的概念,以减轻或者消除对人类健康和环境的危害,同时制定了财税激励措施和清洁或不清洁生产的产品目录及标准。2007年10月,《中华人民国节约能源法(修正案)》,旨在健全节能标准体系和监管制度,加大政策激励力度。
2009年8月,发布《可再生能源法修正案(草案)》,此次草案的几项重要修改包括:中国的可再生能源发电将全面获得政府财政补贴,可再生能源发电的上网电价管理也将进一步完善;国家设立政府基金性质的可再生能源发展基金,来源为国家财政年度安排专项资金和征收的可再生能源电价附加等。草案还对可再生能源发电全额保障性收购制度进行了细化:要求国家有关部门制定全国可再生能源发电量的年度收购指标和实施计划,确定并公布对电网企业应达到的全额保障性收购可再生能源发电量的最低限额指标,电网企业应该收购不低于最低限额指标的可再生能源并网发电项目的上网电量。
太阳能是一种清洁、高效和永不衰竭的新能源,而且光伏发电具有无噪声、无污染、制约少、故障率低、维护简单等优点,一直受各国重视。
航天作为创新能力突出、核心竞争力强的国有特大型企业集团,在我国“十一五”收关以及“十二五”战略规划编制的关键年,积极响应我国“倡导节能减排,推进循环经济”是航天义不容辞的企业社会责任。该项目的建设完全符合我国长期的能源战略规划,带来长远的社会和经济效益。
适应市场发展需求
世界光伏组件产量预计在2010年复合增长率将高达25%,可预见的高速增长将持续40年以上。我国光伏产业近几年发展也极其迅速,已成为我国新兴产业。
中国晶硅太阳电池及组件的厂商已经超过了400家。其中十多家已在国外上市,各企业的供货量及销售额2009年上半年虽曾停滞,但下半年迅速好转。2009年,尚德、英利绿色能源、晶澳太阳能、天合光能的产能分别达到704MW、523.3MW、520MW 和399MW。仅这四大厂商的年度出货量就接近2.2GW。为适应市场需求,规模效应势在必行。
完善产业链布局,提升综合竞争力
随着全球市场的迅速发展,光伏产业的国际化程度越来越高,对企业规模、上下游资源整合能力要求越来越高。
自2003年以来,航天光伏业务高速发展,集团公司十分关注航天光伏产业链的发展。集团公司下属的上市公司航天机电充分依托上海空间电源研究所(811所)的人才和技术优势,积极打造上海太阳能工程技术研究中心为研发平台,以上海航天汽车机电股份有限公司为融资平台,以上海太阳能公司、上海神舟新能源、神舟新能源、神舟硅业等为生产制造平台,以上海申航进出口公司为国际贸易平台的光伏产业发展格局的从硅材料、硅片、电池片到组件、系统、贸易的垂直一体化光伏产业链。
截至到目前,神舟硅业第一期硅料已经正式批产;中环材料、上海神舟新能源等已分别完成了硅片和电池片项目的先期建设。而本项目承建的太阳能电池组件生产线的建设将最终完成航天光伏产业链生产基地布局的宏伟拼图。
本项目全自动生产线的建设,能够提高我们组件生产的技术实力,为今后组件生产技术升级积累经验。
1.5.3 产品研制和生产任务情况
1) 产品研制
本项目研制的主要产品是大面积太阳电池组件,按功率分主要是300W以如190W、240W和280W太阳电池组件,按类型分主要有单晶硅和多晶硅组件,而根据电池片大小分主要是125电池片和156电池片。
2) 生产任务
目标年产能为40MW。
1.6 承担单位概况
1) 上海航天局新能源军转民技术产业化平台
早在上个世纪90年代,由于能源紧缺和环境问题日益严重而导致的世界光伏技术及应用蓬勃发展,上海航天局下属上海空间电源研究所利用自己研究与生产空间太阳电池的技术优势,提出“走出航天、立足航天”的发展思路,结合上海市太阳能发展计划,于2000年与上海航天局控股的上海航天汽车机电股份有限公司以及上海申能新能源投资有限公司合资成立了上海太阳能科技有限公司(SSEC,简称太阳能公司),公司专业从事地面太阳电池技术与应用的发展,是上海航天局实行新能源军转民技术产业化的平台。公司集太阳电池、组件、专用装备以及相关衍生产品的研发、生产、销售和服务为一体,经过几年艰苦创业,充分利用航天技术,并以航天的质量在激烈的市场竞争中站稳了脚跟,并迅速发展成为我国太阳能产品销售量位居前列的基地之一。目前公司也已成为航天科技集团公司新能源产业化基地之一。
2) 公司注册资本、股权结构
3)研发情况
1、研究开发手段与基础设施状况:
(1)研究开发用房建筑面积和开发手段及设施:建筑面积:2000平方米;CAD
设计中心;理化分析中心;机械加工中心;硅、薄膜、化合物太阳电池器件制作圈套
设备;GEF认定太阳电池检测中心;
(2)中试车间建筑面积和主要试验装置及中试条件
中试车间建筑面积为:6000平方米
拥有科技人员75人,研究与试验发展人员36人,博士3人,研究生17人,其
中研究员2人,高级工程师4人,中级工程师10人,形成了一支专业的研发团队。
公司与国外高校、科研院所进行产学研紧密合作,通过产学研合作优化整合与利
用外部科技资源,更好更快的提升公司的技术创新能力。
?依托上海空间电源研究所,与上海交通大学、上海大学、上海电力学院、华东师大学、上海飞乐股份有限公司建立产学研联盟;
?与上海空间电源研究所联合建立上海太阳能工程技术研究中心,集中人力、物力,掌握关键技术;
?与上海大学、华东师大学、上海飞乐股份有限公司合作进行专用装备等项目的研究开发,掌握专用装备核心技术。
4)承担国家、市重点项目情况
依托所拥有的高质专业研发团队,公司还承接了国家级、省部级、市级各类科研
开发、产业化、创新能力建设项目共计13项,其中国家级项目4项,省部级、市级
项目9项。
5)近几年取得的成绩、获奖情况
公司组件产品不断取得国国外认证, 2007年1月30日获得中国CQC-CE认证,
2007年3月30日获得IEC61215认证,2008年8月获得金太阳认证,2010年3月22
日获得德国TUV莱茵认证,2010年10月30日获得意大利Rina认证,2011年1月获
得美国UL认证。
公司产品先后获得国家、集团公司、八院和上海市科技成果奖等各种奖项42项。
其中荣获国家级新产品奖5项,集团公司颁发的1项,八院颁发的5项,上海市优
秀产品奖21项,公司注册商标小火箭获得了2005年度上海名牌产品称号、太阳电池
组件在太阳能并网发电系统上的应用获2005年上海国际工业博览会银奖。
6)知识产权情况
作为一家高科技型企业,太阳能公司十年间着力于科研开发、技术创新,共获得授权专利60件,其中发明专利2件,实用新型专利56件,外观设计专利2件;共申请专利114件,其中发明专利50件,实用新型专利62件,外观设计专利2件;2007年10月,获得了中华人民国国家知识产权局授权《一种具有油加热工作台的太阳电池组件层压机》专利证书,是如今中国电池片组件制造业中各式各样的层压设备的先驱,是国第一台油加热工作台的太阳电池组件层压机。2010年5月,发明了《半导体硅片液态源扩散炉》并获得专利证书,填补了国光伏行业的空白。
7)行业状况或企业在行业中所处的地位
与国同类组件厂家相比,太阳能公司具备别人无法企及的产业链以及综合发展技术能力的优势。公司拥有专业的工程设计、系统集成、系统研发、生产、建设、服务队伍,承担国外大型光伏电站的系统建设工作。2002年5月,公司接下地区的“光明工程”项目。这是公司接下的首个光伏电站系统工程,该项目发电量为1.35兆瓦,产值高达1.3亿元,在42个乡建立42座太阳能电站,为十多万藏族同胞送去了光明。
此后,公司先后接下京沪高速铁路上海虹桥铁路客运站6.572MWp光伏发电项目、上海世博1MW并网项目、神舟光伏电力有限公司5MWp光伏示电站、神舟硅业产业基地1MWp光伏发电项目、国家西部省份送电到乡、中国华电集团新能源发展有限公司华电嘉峪关10MWp太阳能光伏发电工程EPC总承包等重大工程项目,合计完成大型工程项目29.33MWp。充分利用了大型工程项目的契机,带动组件的研发销售,使太阳能公司的组件产品达到了新的高度。
太阳能板制作工艺
太阳能电池板(组件)生产工艺 组件线又叫封装线,封装是太阳能电池生产中的关键步骤,没有良好的封装工艺,多好的电池也生产不出好的组件板。电池的封装不仅可以使电池的寿命得到保证,而且还增强了电池的抗击强度。产品的高质量和高寿命是赢得可客户满意的关键,所以组件板的封装质量非常重要。 流程: 1、电池检测—— 2、正面焊接—检验— 3、背面串接—检验— 4、敷设(玻璃清洗、材料切割、玻璃预处理、敷设)—— 5、层压—— 6、去毛边(去边、清洗)—— 7、装边框(涂胶、装角键、冲孔、装框、擦洗余胶)—— 8、焊接接线盒—— 9、高压测试——10、组件测试—外观检验—11、包装入库 组件高效和高寿命如何保证: 1、高转换效率、高质量的电池片; 2、高质量的原材料,例如:高的交联度的EVA、高粘结强度的封装剂(中性硅酮树脂胶)、高透光率高强度的钢化玻璃等; 3、合理的封装工艺 4、员工严谨的工作作风; 由于太阳电池属于高科技产品,生产过程中一些细节问题,一些不起眼问题如应该戴手套而不戴、应该均匀的涂刷试剂而潦草完事等都是影响产品质量的大敌,所以除了制定合理的制作工艺外,员工的认真和严谨是非常重要的。 太阳电池组装工艺简介: 工艺简介:在这里只简单的介绍一下工艺的作用,给大家一个感性的认识. 1、电池测试:由于电池片制作条件的随机性,生产出来的电池性能不尽相同,所以为了有效的将性能一致或相近的电池组合在一起,所以应根据其性能参数进行分类;电池测试即通过测试电池的输出参数(电流和电压)的大小对其进行分类。以提高电池的利用率,做出质量合格的电池组件。 2、正面焊接:是将汇流带焊接到电池正面(负极)的主栅线上,汇流带为镀锡的铜带,我们使用的焊接机可以将焊带以多点的形式点焊在主栅线上。焊接用的热源为一个红外灯(利用红外线的热效应)。焊带的长度约为电池边长的2倍。多出的焊带在背面焊接时与后面的电池片的背面电极相连 3、背面串接:背面焊接是将36片电池串接在一起形成一个组件串,我们目前采用的工艺是手动的,电池的定位主要靠一个膜具板,上面有36个放置电池片的凹槽,槽的大小和电池的大小相对应,槽的位置已经设计好,不同规格的组件使用不同的模板,操作者使用电烙铁和焊锡丝将“前面电池”的正面电极(负极)焊接到“后面电池”的背面电极(正极)上,这样依次将36片串接在一起并在组件串的正负极焊接出引线。 4、层压敷设:背面串接好且经过检验合格后,将组件串、玻璃和切割好的EVA 、玻璃纤维、背板按照一定的层次敷设好,准备层压。玻璃事先涂一层试剂(primer)以增加玻璃和EVA的粘接强度。敷设时保证电池串与玻璃等材料的相对位置,调整好电池间的距离,为层压打好基础。(敷设层次:由下向上:玻璃、EVA、电池、EVA、玻璃纤维、背板)。 5、组件层压:将敷设好的电池放入层压机内,通过抽真空将组件内的空气抽出,然后加热使EVA熔化将电池、玻璃和背板粘接在一起;最后冷却取出组件。层压工艺是组件生产的关键一步,层压温度层压时间根据EVA的性质决定。我们使用快速固化EVA 时,层压循环时间约为25分钟。固化温度为150℃。 6、修边:层压时EVA熔化后由于压力而向外延伸固化形成毛边,所以层压完毕应
太阳能电池板的生产工艺流程
太阳能电池板的生产工艺流程 太阳能电池板的生产工艺流程 封装是太阳能电池生产中的关键步骤,没有良好的封装工艺,多好的电池也生产不出好的太阳能电池板。电池的封装不仅可以使电池的寿命得到保证,而且还增强了电池的抗击强度。产品的高质量和高寿命是赢得客户满意的关键,所以太阳能电池板的封装质量非常重要。 (1)流程 电池检测——正面焊接——检验——背面串接——检验——敷设(玻璃清洗、材料切割、玻璃预处理、敷设)——层压——去毛边(去边、清洗)——装边框(涂胶、装角键、冲孔、装框、擦洗余胶)——焊接接线盒——高压测试——组件测试——外观检验——包装入库。 (2)组件高效和高寿命的保证措施 高转换效率、高质量的电池片;高质量的原材料,例如,高的交联度的EVA、高黏结强度的封装剂(中性硅酮树脂胶)、高透光率高强度的钢化玻璃等; 合理的封装工艺,严谨的工作作风, 由于太阳电池属于高科技产品,生产过程中一些细节问题,如应该戴手套而不戴、应该均匀地涂刷试剂却潦草完事等都会严重地影响产品质量,所以除了制定合理的工艺外,员工的认真和严谨是非常重要的。 (3)太阳能电池组装工艺简介 ①电池测试:由于电池片制作条件的随机性,生产出来的电池性能不尽相同,所以为了有效地将性能一致或相近的电池组合在一起,所以应根据其性能参数进行分类;电池测试即通过测试电池的输出参数(电流和电压)的大小对其进行分类。以提高电池的利用率,做出质量合格的太阳能电池组件。如果把一片或者几片低功率的电池片装在太阳电池单体中,将会使整个组件的输出功率降低。因此,为了最大限度地降低电池串并联的损失,必须将性能相近的单体电池组合成组件。 ②焊接:一般将6~12个太阳能电池串联起来形成太阳能电池串。传统上,一般采用银扁线构成电池的接头,然后利用点焊或焊接(用红外灯,利用红外线的热效应)等方法连接起来。现在一般使用60%的Sn、38%的Pb、2%的Ag 电镀后的铜扁丝(厚度约为100~200μm)。接头需要经过火烧、红外、热风、激
太阳能电池组件封装工艺大全
太阳能电池组件封装工艺大全 一、太阳能电池组件封装简介 组件线又叫封装线,封装是太阳能电池板生产中的关键步骤,没有良好的封装工艺,多好的电池片也做不出好的组件板。良好的电池封装不仅可以使电池的寿命得到保证,而且还增强了电池的抗击强度。产品的高质量和高寿命是赢得客户满意的关键,所以太阳能电池板的封装工艺至关重要。 太阳能电池组件封装工艺流程图如下: 太阳能电池组件封装结构图 如何保证太阳能电池组件的高效和高寿命? 1、高转换效率、高质量的电池片
下图是电池的结构示意图: (1)金属电极主栅线;(2)金属上电极细栅线;(3)金属底电极;(4)减反射膜;(5)顶区层(扩散层);(6)体区层(基区层); 2、高质量的封装材料 高耐候性、低水蒸汽透过率、良好电绝缘性等性能优异的太阳能电池背板; 交联度高、耐黄变性能好、热稳定性好、粘接力强等性能优异的EVA胶膜; 高粘结强度、密封性好的封装剂(中性硅酮树脂胶); 高透光率、高强度的钢化玻璃等
3、严谨的工作态度 由于太阳电池组件属于高科技产品,生产过程中一些细节问题,一些不起眼问题如应戴手套而不戴、应均匀的涂刷试剂而潦草完事等都是影响产品质量的大敌,所以除了制定合理的制作工艺外,员工的认真和严谨是非常重要的。 二、太阳能电池组件组装工艺介绍 1、电池分选 由于电池片制作条件的随机性,生产出来的电池片性能不尽相同,所以为了有效的将性能一致或相近的电池片组合在一起,应根据其性能参数进行分类;电池测试即通过测试电池片的输出参数(电流和电压)的大小对其进行分类。以提高电池片的利用率,做出质量合格的太阳能电池组件。 2、单焊 是将汇流带焊接到电池正面(负极)的主栅线上,汇流带为镀锡的铜带,焊带的长度约为电池片边长的2倍。多出的焊带在背面焊接时与后面的电池片的背面电极相连(如下图)。 3、串焊 背面焊接是将N张片电池串接在一起形成一个组件串,电池的定位主要靠一个膜具板,操作者使用电烙铁和焊锡丝将单片焊接好的电池的正面电极(负极)焊接到“后面电池”的背面电极(正极)上,这样依次将N张电池片串接在一起并在组件串的正负极焊接出引线。 4、叠层 背面串接好且经过检验合格后,将组件串、玻璃和切割好的EVA 、太阳能电池背板按照一定的层次敷设好,准备层压。敷设时保证电池串与玻璃等材料的相对位置,调整好电池间的距离,为层压打好基础。(敷设层次:由下向上:玻璃、EVA、电池处、EVA、玻璃纤维、背板)。 5、组件层压 将敷设好的电池组件放入层压机内,通过抽真空将组件内的空气抽出,然后加热使EVA 熔化将电池、玻璃和太阳能电池背板粘接在一起;最后冷却取出组件。层压工艺是太阳能电池组件生产的关键一步,层压温度和层压时间根据EVA的性质决定。我们使用普通的EVA 时,层压循环时间约为21分钟,固化温度为138-140℃。 6、修边 层压时EVA熔化后由于压力而向外延伸固化形成毛边,所以层压完毕应将其切除。 7、装框 类似与给玻璃装一个镜框;给玻璃组件装铝框,增加组件的强度,进一步的密封电池组
光伏组件(太阳能电池板)规格表
光伏组件(太阳能电池板)规格表如本页不能正常显示,请点击刷新 型号材料 峰值 功率 Pm (watt) 峰值 电压 Vmp (V) 峰值 电流 Imp (A) 开路 电压 Voc (V) 短路 电流 Isc (A) 尺寸 (mm) APM18M5W27x27单晶硅 5 8.75 0.57 10.5 0.66 265*265*25 APM36M5W27x27单晶硅 5 17.5 0.29 21.5 0.32 265*265*25 APM18P5W27x27多晶硅 5 8.75 0.57 10.5 0.66 265*265*25 APM36P5W27x27多晶硅 5 17.5 0.29 21.5 0.32 265*265*25 APM36M8W36x30单晶硅8 17.5 0.46 21.5 0.52 301*356*25 APM36P8W36x30多晶硅8 17.5 0.46 21.5 0.52 301*356*25 APM36M10W36x30单晶硅10 17.5 0.57 21.5 0.65 301*356*25 APM36P10W36x30多晶硅10 17.5 0.57 21.5 0.65 301*356*25 APM36M15W49x29单晶硅15 17.5 0.86 21.5 0.97 287*487*25 APM36P15W43x36多晶硅15 17.5 0.86 21.5 0.97 356*426*28 APM36M20W63x28单晶硅20 17.5 1.14 21.5 1.29 281*627*25 APM36P20W58x36多晶硅20 17.5 1.14 21.5 1.29 356*576*28 APM36M25W48x54单晶硅25 17.5 1.43 21.5 1.61 536*477*28 APM36P25W68x36多晶硅25 17.5 1.43 21.5 1.61 356*676*28 APM36M30W48x54单晶硅30 17.5 1.71 21.5 1.94 536*477*28 APM36P30W82x36多晶硅30 17.5 1.71 21.5 1.94 356*816*28 APM36M35W62x54单晶硅35 17.5 2.00 21.5 2.26 537*617*40
太阳能电池组件的封装(精华)
太阳能电池组件的封装(精华) 导读:单件电池片由于输出功率太小,难以满足常规用电需求,因此需要将其封装为组件以提高其输出功率。封装是太阳能电池生产中的关键步骤,没有良好的封装工艺,再好的电池也生产不出好的组件。电池的封装不仅可以使电池的寿命得到保证,而且还增强了电池的抗击强度。产品的高质量和高寿命是赢得客户满意的关键,所以组件的封装质量非常重要。 具有外部封装及内部连接、能单独提供直流电输出的最小不可分割的太阳能电池组合装置,叫太阳能电池组件,即多个单体太阳能电池互联封装后成为组件。太阳能电池组件是太阳能发电系统中的核心部分,也是太阳能发电系统中最重要的部分。 1.防止太阳能电池破损。晶体硅太阳能电池易破损的原因:晶体硅呈脆性;硅太阳能电池面积大;硅太阳能电池厚度小。 2.防止太阳能电池被腐蚀失效。太阳能电池的自然抗性差:太阳电池长期暴露在空气中会出现效率的衰减;太阳电池对紫外线的抵抗能力较差;太阳电池不能抵御冰雹等外力引起的过度机械应力所造成的破坏;太阳电池表面的金属化层容易受到腐蚀;太阳电池表面堆积灰尘后难以清除。 3.满足负载要求,串联或并联成一个能够独立作为电源使用的最小单元。由于单件太阳电池输出功率难以满足常规用电需求,需要将它们串联或者并联后接入用电器进行供电。 太阳能电池组件的种类较多,根据太阳能电池片的类型不同可分为晶体硅(单、多晶硅)太阳能电池组件、非晶硅薄膜太阳能电池组件及砷化镓电池组件等;按照封装材料和工艺的不同可分为环氧树脂封装电池板和层压封装电池组件;按照用途的不同可分为普通型太阳能电池组件和建材型
太阳能电池组件。其中建材型太阳能电池组件又分为单面玻璃透光型电池组件、双面夹胶玻璃电池组件和双面中空玻璃电池组件。由于用晶体硅太阳能电池片制作的电池组件应用占到市场份额的85%以上,在此就主要介绍用晶体硅太阳能电池片制作的电池组件。 单晶硅组件 多晶硅组件 非晶硅组件 第一代室温硫化硅橡胶封装 第二代聚乙烯醇缩丁醛 (PVB )封装 第三代乙烯-醋酸乙烯共聚物(EVA )封
太阳能电池组件生产的主要工艺流程
太阳能电池组件生产的主要工艺流程:测试分选T单片焊接T串联焊接T叠层T中间测试T层压T装框注胶T清洗T最终测试 (1)测试分选 电池片分选主要是为了检出不合格的电池片,同时,电池片的颜色一般呈蓝褐色、蓝紫色、蓝色、浅兰色等几种不同档次的蓝色,对电池片进行颜色分选并分档放置,保证单个组件所用到的电池片为同档次的颜色,从而使单个组件生产出来后颜色外观美观,各电池单片之间无明显色差现象。若电池片不经过色差分选就直接做组件,做出来的组件外表颜色“参差不齐” ,不美观。因此,为了保证电池片的质量、外观和生产顺利高效率的运行,通过初选将缺角、栅线印刷不良、裂片、色差等电池片筛选出来。 在标准测试环境(温度25 ±2 C、湿度w 60%RH、光强1000 士 50W )下,绘制I-V曲线图,根据电池片的开路电压Voc、短路电流Isc、工作最佳功率Pm、工作最佳电压Vm、工作最佳电流Im、填充因子FF、转换效率n等指标把电池电性参数相近的电池分到一类,之后根据生产、工艺的数据分析要求,和客户的分档要求,对电池片进行测试并分档。 (2)单片焊接单片焊接将汇流带焊接到电池正面(负极)的主栅线上,从上至 下,匀速焊接。单片焊接的目的是将连接带(锡铜合金带)平直地焊接到电池片的主栅线上,要求保证电气和机械连接良好,外观光亮;焊带
的长度约为电池边长的2倍,多出的焊带在串联焊接时与后面的电池片的背面电极相连。 ⑶串联焊接 背面焊接是将电池片接在一起形成一个电池片的串组,电池的定位主要靠一个膜具板,上面有放置电池片的凹槽,槽的大小和电池的大小相对应,槽的位置已经是设计好的,不同规格的组件使用不同的模板,操作者使用电烙铁和连接带(锡铜合金带)将单片焊接好的电池片的正面电极(负极)焊接到另一片的背面电极(正极)上,以此类推,依次将电池片串接在一起,并在组件串的正负极焊接出为叠层时准备的引线。 串接结构示意图 (4)叠层 背面串接好且经过检验合格后,将电池片串、钢化玻璃和切割好的EVA、背板(TPT)按照一定的层次敷设好,玻璃事先涂一层试剂(primer )以增加玻璃和EVA的粘接强度。敷设时保证电池串与玻璃等材料的相对位置,调整好电池间的距离,为层压打好基础。(敷设层次:由下向上:钢化玻璃、EVA、电池片、EVA、背板)。叠层 是将电池片串按照所设计的方案进行排列,为下面的工序层压做准备,叠层的主要目的还是在于对组件中电池片位置的控制(假设在层压过程中电池片不发生移动)。
晶体硅太阳能电池组件清理工艺规范
电池组件生产工艺 目录 太阳能电池组件生产工艺介绍 (1) 晶体硅太阳能电池片分选工艺规范 (3) 晶体硅太阳能电池片激光划片工艺规范 (4) 晶体硅太阳能电池片单焊工艺规范 (6) 晶体硅太阳能电池片串焊工艺规范 (8) 晶体硅太阳能电池片串焊工艺规范 (9) 晶体硅太阳能电池片叠层工艺规范 (10) 晶体硅太阳能电池组件层压工艺规范 (12) 晶体硅太阳能电池组件装框规范 (14) 晶体硅太阳能电池组件测试工艺规范 (15) 晶体硅太阳能电池组件安装接线盒工艺规范 (16) 晶体硅太阳能电池组件清理工艺规范 (17)
太阳能电池组件生产工艺介绍 组件线又叫封装线,封装是太阳能电池生产中的关键步骤,没有良好的封装工艺,多好的电池也生产不出好的组件板。电池的封装不仅可以使电池的寿命得到保证,而且还增强了电池的抗击强度。产品的高质量和高寿命是赢得可客户满意的关键,所以组件板的封装质量非常重要。 1流程图: 电池检测——正面焊接—检验—背面串接—检验—敷设(玻璃清洗、材料切割、玻璃预处理、敷设)——层压——去毛边(去边、清洗)——装边框(涂胶、装角键、冲孔、装框、擦洗余胶)——焊接接线盒——高压测试——组件测试—外观检验—包装入库; 2组件高效和高寿命如何保证: 2.1高转换效率、高质量的电池片 2.2高质量的原材料,例如:高的交联度的EVA、高粘结强度的封装剂(中性硅酮树脂胶)、 高透光率高强度的钢化玻璃等; 2.3合理的封装工艺; 2.4员工严谨的工作作风; 由于太阳电池属于高科技产品,生产过程中一些细节问题,一些不起眼问题如应该戴手套而不戴、应该均匀的涂刷试剂而潦草完事等都是影响产品质量的大敌,所以除了制定合理的制作工艺外,员工的认真和严谨是非常重要的。 3太阳电池组装工艺简介: 3.1工艺简介: 在这里只简单的介绍一下工艺的作用,给大家一个感性的认识,具体内容后面再详细介绍: 3.1.1电池测试: 由于电池片制作条件的随机性,生产出来的电池性能不尽相同,所以为了有效的将性能一致或相近的电池组合在一起,所以应根据其性能参数进行分类;电池测试即通过测试电池的输出参数(电流和电压)的大小对其进行分类。以提高电池的利用率,做出质量合格的电池组件。 3.1.2正面焊接: 是将汇流带焊接到电池正面(负极)的主栅线上,汇流带为镀锡的铜带,我们使用的焊接机可以将焊带以多点的形式点焊在主栅线上。焊接用的热源为一个红外灯(利用红外线的热效应)。焊带的长度约为电池边长的2倍。多出的焊带在背面焊接时与后面的电池片的背面电极相连。 3.1.3背面串接: 背面焊接是将36片电池串接在一起形成一个组件串,我们目前采用的工艺是手动的,电池的定位主要靠一个膜具板,上面有36个放置电池片的凹槽,槽的大小和电池的大小相
太阳能电池板参数
太阳能电池板的一组参数 最大标称功率Wp max (W), 峰值电压Vmp(V):峰值电压是在强光时的最高电压 峰值电流Imp(A) 开路电压V oc(V):开路电压是电池板空载电压 工作电压:是电池板带上负荷时测得的电压 短路电流Isc(A) 尺寸Size(mm) 重量Weight(KGS) (峰值电压最高、开路电压次之、工作电压最低) 直流接线盒: 采用密封防水、高可靠性多功能ABS 塑料接线盒,耐老化防水防潮性能好;连接端采用易操作的专用公母插头,使用安全、方便、可靠。 工作温度:-40℃~+90℃ 使用寿命可达20 年以上,衰减小于20%。 问题集锦: 1、什么是太阳能电池? 答:太阳能电池是基于半导体的光伏效应将太阳辐射直接转换为电能的半导体器件。 现在商品化的太阳能电池主要有以下几种类型:单晶硅太阳能电池、多晶硅太阳能电池、非晶硅太阳能电池,目前还有碲华镉电池、铜铟硒电池、纳米氧化钛敏化电池、多晶硅薄膜太阳能电池及有机太阳能电池等。 晶体硅(单晶、多晶)太阳能电池需要高纯度的硅原料,一般要求纯度至少是99. 99998%,也就是一千万个硅原子中最多允许2 个杂质原子存在。硅材料是用二氧化硅(SiO2,也就是我们所熟悉的沙子)作为原料,将其熔化并除去杂质就可制取粗级硅。从二氧化硅到太阳能电池片,涉及多个生产工艺和过程,一般大致分为:二氧化硅—> 冶金级硅—>高纯三氯氢硅—>高纯度多晶硅—>单晶硅棒或多晶硅锭—>硅片—>太阳能电池片。 2、什么是单晶硅太阳能电池板? 答:单晶硅太阳能电池片主要是使用单晶硅来制造,与其他种类的太阳能电池片相比,单晶硅电池片的转换效率最高。在初期,单晶硅太阳能电池片占领绝大部份市场份额,在1998 年后才退居多晶硅之后,市场份额占据第二。由于近几年多晶硅原料紧缺,在2004 年之后,单晶硅的市场份额又略有上升,现在市面上看到的电池有单晶硅居多。单晶硅太阳能电池片的硅结晶体非常完美,其光学、电性能及力学性能都非常的均匀一致,电池的颜色多为黑色或深色,特别适合切割成小片制作成小型的消费产品。单晶硅电池片在实验室实现的转换效率为24.7%.普通商品化的转换效率为10%-1 8%。单晶硅太阳能电池片因为制作工艺问题,一般其半成硅锭为圆柱进,然后经过切片->清洗->扩散制结->去除背极->制作电极->腐蚀周边->蒸镀减反射膜等工蕊制成成品。一般单晶硅太阳能电池四个角为圆角。单晶硅太阳能电池片的厚度一般为200uM- 350uM 厚,现在的生产趋势是向超薄及高效方向发展,德国太阳能电池片厂家已经证实40uM 厚的单晶硅可达到20%的转换效率。 3、什么是多晶硅太阳能电池板? 答:在制作多晶硅太阳能电池时,作为原料的高纯硅不是再提纯成单晶,而是熔化浇铸成正方形的硅锭,然后再加工单晶硅一样切成薄片和进行类似的加工。多晶硅从其表面很容易进行辨认,硅片是由大量不同大小的结晶区域组成(表面有晶体结晶状),其发电机制与单晶相同,但由于硅片由多个不同大小、不同取向的晶粒组在,其晶粒界面处光电转换易受到干扰,因而多晶硅的转换效率相对较低,同时,多晶硅的光
太阳能电池组件的封装
太阳能电池组件的封装
太阳能电池组件的封装 (二)组件的封装结构 (三)组件的封装材料 1上盖板2黏结剂3底板4边框(四)组件封装的工艺流程 不同结构的组件有不同的封装工艺。平板式硅太阳能电池组件的封装工艺流程,如图17所示。可将这一工艺流程概述为:组件的中间是通过金属导电带焊接在一起的单体电池,电池上卞两侧均为EVA膜,最上面是低铁钢化白玻璃,背面是PVF复合膜。将各层材料按顺序叠好后,放人真空层压机内进行热压封装。最上层的玻璃为低铁钢化白玻璃,透光率高,而且经紫外线长期照射也不会变色。EVA膜中加有抗紫外剂和固化剂,在热压处理过程中固化形成具有一定弹性的保护层,并保证电池与钢化玻璃紧密接触。PVF复合膜具有良好的耐光、防潮、防腐蚀性能。经层压封装后,再于四周加上密封条,装上经过阳极氧化的铝合金边框以及接线盒,即成为成品组件。最后,要对成品组件进行检验测试,测试内容主要包括开路电压、短路电流、填充因
子以及最大输出功率等。 硅片划片切割工艺概况 1用激光来划片切割硅片是目前最为先进的,它使用精度高、而且重复精度也高、工作稳定、速度快、操作简单、维修方便。 2激光最大输出≧50W(可调)、激光波长为1.064μm、 切割厚度≦1.2mm、光源是用Nd:YAG晶体组成激光器、是单氪灯连续泵浦、声光调Q、并用计算机控制二维工作台可预先设定的图形轨迹作各种精确运动。 ± 部件分析: 1操作可分为外控与内控。 2计算机操作系统-有专用软件设立工作台划片步骤实现划片目标。 3电源控制盒-供应激光电源、Q电源驱动、水冷系统的输入电源进行分配及自控,当循环水冷系统出现故障时,自动断开激光电源及Q电源驱动盒的供电。 4激光电源盒-点燃氪灯的自动引燃恒流电源。 5 Q电源驱动盒-产生射频信号并施加到Q开
太阳能电池组件规定
太阳能电池组件规定 1、电池组件方阵概况 1.1电站容量20MW,均采用多晶硅太阳能电池组件,为固定式17°倾角安装。 1.2太阳能方阵由太阳能组件经串联、并联组成。光伏电池组件串联的数量由并网逆变器的最高输入电压、最低工作电压、太阳能电池组件的最大系统电压以及当地气候等条件确定;组串并联的数量由逆变器的额定容量确定。 1.3 组件方阵:每22块电池组件串为一个支路,12条支路进入一个汇流箱,每8或9个汇流箱进入一个直流柜,由两台直流柜分别分配电能到两台500kW的逆变器,2个逆变器(500kW)和1台1000KV A箱变组成一个发电单元(1MW),共20个发电单元;每10MW的联合单元进入一个进线柜,2个10MW联合单元构成总容量为:20MW。
2 、太阳能电池组件型号及参数 序号名称 单 位 型号备注1 太阳电池种类多晶硅 2 光伏组件尺寸 结构1650mm×992mm×40mm 3 光伏组件重量kg 19.0 4 组件效率% 14.98 5 最大输出功率Wp 255 6 最大功率偏差% ±3% 7 开路电压 (V oc) V 38.1 8 短路电流 (Isc) A 8.78 9 最佳工作电压V 31.5 10 最佳工作电流 A 8.13
序号名称 位 型号备注11 最大系统电压V 1000 序号名称 单 位 型号备注1 太阳电池种类多晶硅 2 光伏组件尺寸 结构1650mm×992mm×40mm 3 光伏组件重量kg 19.0 4 组件效率% 14.98 5 最大输出功率Wp 250 6 最大功率偏差% ±3% 7 开路电压 (V oc) V 37.8 8 短路电流 (Isc) A 8.72
详解太阳能电池组件中逆变器的工作原理
太阳能电池组件中逆变器的工作原理逆变器的概念通常,把将交流电能变换成直流电能的过程称为整流,把完成整流功能的电路称为整流电路,把实现整流过程的装置称为整流设备或整流器。与之相对应,把将直流电能变换成交流电能的过程称为逆变,把完成逆变功能的电路称为逆变电路,把实现逆变过程 逆变器的概念 通常,把将交流电能变换成直流电能的过程称为整流,把完成整流功能的电路称为整流电路,把实现整流过程的装置称为整流设备或整流器。与之相对应,把将直流电能变换成交流电能的过程称为逆变,把完成逆变功能的电路称为逆变电路,把实现逆变过程的装置称为逆变设备或逆变器。 现代逆变技术是研究逆变电路理论和应用的一门科学技术。它是建立在工业电子技术、半导体器件技术、现代控制技术、现代电力电子技术、半导体变流技术、脉宽调制(PWM)技术等学科基础之上的一门实用技术。它主要包括半导体功率集成器件及其应用、逆变电路和逆变控制技术3大部分。 逆变器的分类 逆变器的种类很多,可按照不同的方法进行分类。
1.按逆变器输出交流电能的频率分,可分为工频逆变器、中频逆器和高频逆变器。工频逆变器的频率为50~60Hz的逆变器;中频逆变器的频率一般为400Hz到十几kHz;高频逆变器的频率一般为十几kHz 到MHz。 2.按逆变器输出的相数分,可分为单相逆变器、三相逆变器和多相逆变器。 3.按照逆变器输出电能的去向分,可分为有源逆变器和无源逆变器。凡将逆变器输出的电能向工业电网输送的逆变器,称为有源逆变器;凡将逆变器输出的电能输向某种用电负载的逆变器称为无源逆变器。 4.按逆变器主电路的形式分,可分为单端式逆变器,推挽式逆变器、半桥式逆变器和全桥式逆变器。 5.按逆变器主开关器件的类型分,可分为晶闸管逆变器、晶体管逆变器、场效应逆变器和绝缘栅双极晶体管(IGBT)逆变器等。又可将其归纳为“半控型”逆变器和“全控制”逆变器两大类。前者,不具备自关断能力,元器件在导通后即失去控制作用,故称之为“半控型”普通晶闸管即属于这一类;后者,则具有自关断能力,即无器件的导 通和关断均可由控制极加以控制,故称之为“全控型”,电力场效应晶体管和绝缘栅双权晶体管(IGBT)等均属于这一类。
太阳能电池组件生产工序中英文
中文:太阳能电池组件生产工艺 组件线又叫封装线,封装是太阳能电池生产中的关键步骤,没有良好的封装工艺,多好的电池也生产不出好的组件板。电池的封装不仅可以使电池的寿命得到保证,而且还增强了电池的抗击强度。产品的高质量和高寿命是赢得可客户满意的关键,所以组件板的封装质量非常重要。 工艺流程如下: 1、电池检测—— 2、正面焊接—检验— 3、背面串接—检验— 4、敷设(玻璃清洗、材料切割、玻璃预处理、敷设)—— 5、层压—— 6、去毛边(去边、清洗)—— 7、装边框(涂胶、装角键、冲孔、装框、擦洗余胶)—— 8、焊接接线盒—— 9、高压测试——10、组件测试—外观检验—11、包装入库; 1.2工艺简介: 在这里只简单的介绍一下工艺的作用,给大家一个感性的认识,具体内容后面再详细介绍:1、电池测试:由于电池片制作条件的随机性,生产出来的电池性能不尽相同,所以为了有效的将性能一致或相近的电池组合在一起,所以应根据其性能参数进行分类;电池测试即通过测试电池的输出参数(电流和电压)的大小对其进行分类。以提高电池的利用率,做出质量合格的电池组件。 2、正面焊接:是将汇流带焊接到电池正面(负极)的主栅线上,汇流带为镀锡的铜带,我们使用的焊接机可以将焊带以多点的形式点焊在主栅线上。焊接用的热源为一个红外灯(利用红外线的热效应)。焊带的长度约为电池边长的2倍。多出的焊带在背面焊接时与后面的电池片的背面电极相连。(我们公司采用的是手工焊接) 3、背面串接:背面焊接是将36片电池串接在一起形成一个组件串,我们目前采用的工艺是手动的,电池的定位主要靠一个膜具板,上面有36个放置电池片的凹槽,槽的大小和电池的大小相对应,槽的位置已经设计好,不同规格的组件使用不同的模板,操作者使用电烙铁和焊锡丝将“前面电池”的正面电极(负极)焊接到“后面电池”的背面电极(正极)上,这样依次将36片串接在一起并在组件串的正负极焊接出引线。 4、层压敷设:背面串接好且经过检验合格后,将组件串、玻璃和切割好的EVA 、玻璃纤维、背板按照一定的层次敷设好,准备层压。玻璃事先涂一层试剂(primer)以增加玻璃和EVA的粘接强度。敷设时保证电池串与玻璃等材料的相对位置,调整好电池间的距离,为层压打好基础。(敷设层次:由下向上:玻璃、EVA、电池、EVA、玻璃纤维、背板)。 5、组件层压:将敷设好的电池放入层压机内,通过抽真空将组件内的空气抽出,然后加热使EVA熔化将电池、玻璃和背板粘接在一起;最后冷却取出组件。层压工艺是组件生产的关键一步,层压温度层压时间根据EVA的性质决定。我们使用快速固化EVA时,层压循环时间约为25分钟。固化温度为150℃。 6、修边:层压时EVA熔化后由于压力而向外延伸固化形成毛边,所以层压完毕应将其切除。 7、装框:类似与给玻璃装一个镜框;给玻璃组件装铝框,增加组件的强度,进一步的密封电池组件,延长电池的使用寿命。边框和玻璃组件的缝隙用硅酮树脂填充。各边框间用角键连接。 8、焊接接线盒:在组件背面引线处焊接一个盒子,以利于电池与其他设备或电池间的连接。 9、高压测试:高压测试是指在组件边框和电极引线间施加一定的电压,测试组件的耐压性和绝缘强度,以保证组件在恶劣的自然条件(雷击等)下不被损坏。
太阳能电池(组件)生产工艺
太阳能电池(组件)生产工艺 组件线又叫封装线,封装是太阳能电池生产中的关键步骤,没有良好的封装工艺,多好的电池也生产不出好的组件板。电池的封装不仅可以使电池的寿命得到保证,而且还增强了电池的抗击强度。产品的高质量和高寿命是赢得可客户满意的关键,所以组件板的封装质量非常重要。 流程: 1、电池检测—— 2、正面焊接—检验— 3、背面串接—检验— 4、敷设(玻璃清洗、材料切割、玻璃预处理、敷设)—— 5、层压—— 6、去毛边(去边、清洗)—— 7、装边框(涂胶、装角键、冲孔、装框、擦洗余胶)—— 8、焊接接线盒—— 9、高压测试——10、组件测试—外观检验—11、包装入库 组件高效和高寿命如何保证: 1、高转换效率、高质量的电池片; 2、高质量的原材料,例如:高的交联度的EVA、高粘结强度的封装剂(中性硅酮树脂 胶)、高透光率高强度的钢化玻璃等;
3、合理的封装工艺; 4、员工严谨的工作作风; 由于太阳电池属于高科技产品,生产过程中一些细节问题,一些不起眼问题如应该戴手套而不戴、应该均匀的涂刷试剂而潦草完事等都是影响产品质量的大敌,所以除了制定合理的制作工艺外,员工的认真和严谨是非常重要的。 太阳电池组装工艺简介: 工艺简介:在这里只简单的介绍一下工艺的作用,给大家一个感性的认识。 1、电池测试:由于电池片制作条件的随机性,生产出来的电池性能不尽相同,所以为了有效的将性能一致或相近的电池组合在一起,所以应根据其性能参数进行分类;电池测试即通过测试电池的输出参数(电流和电压)的大小对其进行分类。以提高电池的利用率,做出质量合格的电池组件。 2、正面焊接:是将汇流带焊接到电池正面(负极)的主栅线上,汇流带为镀锡的铜带,我们使用的焊接机可以将焊带以多点的形式点焊在主栅线上。焊接用的热源为一个红外灯(利用红外线的热效应)。焊带的长度约为电池边长的2倍。多出的焊带在背面焊接时与后面的电池片的背面电极相连。
太阳能电池组件制造原理详细介绍
前言 太阳能光电池需要被连接(普通为串联),然后层迭封装起来,以防止受到损坏,这就是所谓的模块化封装,同时,该模块制程一般将依据电池种类和模块应用型态来决定。 一、电池串联 当制造太阳能光电模块时,太阳能电池首先必须以串联的方式(电池串行)连接,这是因为每单一硅晶太阳电池的各别电能输出是很低的。在串接程序里,每一个电池的前端接点将被焊接到下一个电池的后端接点之上,以便将每一个电池的前端负极连接到下一个电池的后端正极,也就是将若干电池作串联式的连接(图 1 )。 然后,每一串序的开始和结束再向外延伸,以用于随后的电力连接。在大量生产时,所谓的” Tabber-Stringers” 机器经常被使用于自动化焊接。但是,顾客量身定作的电池产品则通常以手工制作。硅晶电池系一个接一个地在独立的制造工作站被连接;相反地,薄膜电池则借着独立层中沟槽的切割来予以完成,同时,电力连接则是电池组装的一主要部分;通常,雷射或机械线切被使用,将该材料切割成大约 1 公分宽的电池长条。
图 2 表示当电池被配置在前侧时,该组装之序列。此方式系使用在碲化镉(CdTe) 模块和大部分的非晶硅模块上面。首先,透明氧化物导电 (TCO) 层被分离成平行的长条状,然后太阳能电池层沈积在上面。接着,第二切段(太阳能电池层)有点偏离第一切段 (TCO) 来制作,但是仍然与后者平行。最后,再切割与制作第三切段后接点(金属层)。此方式制造了从一电池的后接点至下一电池的前接点之间的电力连接,使得各别电池长条能以串联的方式作相互的连接。参见图 3 ,该结构系以相类似的方式来成型:从后接点开始,铜铟硒 (CIS) 电池和非晶硅薄膜电池系以相反的顺序装配。 二、电池封装 为了保护电池对抗机械应力、曝晒和湿气,串接的电池被嵌进一透明的封装材料内,该封装材料同时能对该电池产生电绝缘的作用。为了结构上的稳定,该封装系统应用一覆板 (superstrate) 。大部分的案例系使用玻璃,但同时也可使用压克力、金属或塑料薄片。视制程而定,太阳电池可放在覆板材料之上、之后或之间。在太阳电池光感面之上的覆盖物以透明材料来制造是很重要的,因为越透明的材料能使更多的太阳能量投射在太阳电池之上。基于这个理由,低铁玻璃常当作前覆板来使用,因为它能够让 91% 的光线通过。该玻璃系经过回火处理的,以便强化其对抗高热能应力的特性。最近所开发的抗反射玻璃,使用烧熔制程或浸染涂布,因而具有抗反射涂层,能达成 96% 之光穿透率。使用此抗反射玻璃的太阳电池模块所吸收的能量比使用普通玻璃者多出约 3.5% 。目前使用较普遍的封装方式有三种: ?乙烯醋酸乙烯共聚物 (EVA) 封装 ?铁氟龙( Teflon R )封装 ?铸造树脂封装 ■乙烯醋酸乙烯聚合物 (EVA) 封装 当以 EVA 封装时,该电池串行在真空腔内系以正负压加温的方式进行层迭制程(真空层迭制程)。该 EVA 在此制程里被熔解,并将整个太阳电池包围起来。该 EVA 在正面需要抗紫外线的功能。在大部分的应用例中,这是一片高透明白色的回火玻璃(太阳玻璃),而其背榇可为一传统的硬化玻璃薄片或不透明薄膜。 EVA 封装大部分使用于制造标准和特殊之模块,最大所能装配的尺寸为2 公尺乘 3 公尺。随着模块尺寸的加大,在迭层期间该等电池将开始漂浮,这将使得在该等电池之间的间隙很难保持相等。然而,不同基板的使用将能够装配不同的迭层构型。(请参考图 4-7 )
光伏组件
光伏组件 光伏组件 单体太阳电池不能直接做电源使用。作电源必须将若干单体电池串、并联连接和严密封装成组件。光伏组件(也叫太阳能电池板)是太阳能发电系统中的核心部分,也是太阳能发电系统中最重要的部分。其作用是将太阳能转化为电能,或送往蓄电池中存储起来,或推动负载工作。 光伏组件 1.组成结构: 又称太阳电池组件( Solar Cell module),是指具有封装及内部联结的,能单独提供直流电输出的,最小不可分割的光伏电池组合装置。 [1] 光伏组件(俗称太阳能电池板)由太阳能电池片(整片的两种规格125*125mm、156*156mm、124*124mm等)或由激光切割机机或钢线切割机切割开的不同规格的太阳能电池组合在一起构成。由于
单片太阳能电池片的电流和电压都很小,然后我们把他们先串联获得高电压,再并联获得高电流后,通过一个二极管(防止电流回输)然后输出。 并且把他们封装在一个不锈钢、铝或其他非金属边框上,安装好上面的玻璃及背面的背板、充入氮气、密封。 整体称为组件,也就是光伏组件或说是太阳电池组件。 2.制作流程: 组件制作流程经电池片分选-单焊接-串焊接-拼接(就是将串焊好的电池片定位,拼接在一起)-中间测试(中间测试分:红外线测试和外观检查)-层压-削边-层后外观-层后红外-装框(一般为铝边框)-装接线盒-清洗-测试(此环节也分红外线测试和外观检查.判定该组件的等级)-包装. 3.组件的生产工艺流程 第一步单片焊接:将电池片焊接互联条(涂锡铜带),为电池片的串联做准备. 第二步串联焊接:将电池片按照一定数量进行串联。 第三步叠层:将电池串继续进行电路连接,同时用玻璃、EVA胶膜、TPT背板将电池片保护起来。 第四步层压:将电池片和玻璃、EVA胶膜、TPT背板在一定的
太阳能电池组件生产工艺流程
太阳能电池组件生产工艺介绍 太阳能光伏组件生产制造过程主要是将单片太阳能电池片进行串联和并联连接后严密封装,以保护电池片表面电极和互联线等不受到腐蚀,另外封装也避免了电池片的碎裂,所以太阳能电池组件生产过程其实就是组件的封装过程,因此组件线又叫封装线,封装是太阳能电池生产中的关键步骤,没有良好的封装工艺,多好的电池也生产不出好的组件板。 1、太阳能电池组件生产步骤和工艺流程: 电池片的检测分选—激光机划片—正面焊接—检验—背面串接—检验—叠层铺设(玻璃清洗、材料切割、玻璃预处理、敷设)——层压——去毛边(去边、清洗)—终检—装边框(涂胶、装角键、冲孔、装框、擦洗余胶)——装接线盒——高压测试——清洗—抽检--贴标签—包装入库 2、 各生产步骤简介 (1)电池片的分选:由于电池片制作条件的随机性, 生产出来的电池性能不尽相同,为了有效的将性能一致或 相近的电池组合在一起,所以应根据其性能参数进行分类; 电池测试即通过测试电池的输出参数(电流和电压)的大 小对其进行分类。以提高电池的利用率,生产出质量合格 的电池组件。 (2)激光机划片:就是利用激光划片机将整片的电 池片根据需要切割成组件需要的规格尺 寸。在激光切片前要设计好切线的线路, 编号切割程序,充分利用电池片的边角 料,以节省材料。 (3)电池片单焊:将互联条焊接 到电池片正面的负极主栅线上,要求平直、牢固。焊带 的产股度约为 电池片的宽度 的2倍。 (4)电池片串焊:串焊也称背面 焊,是将单焊好的电池片串焊在一起, 形电池片分选仪 https://www.360docs.net/doc/036722344.html, 单焊、串焊设备
成电池串,然后再用汇流条将串焊好的电池串进行串联或并联焊接,最后汇流条的两端引出正负极。 (5)中检:也称为中测,是将串焊好的电池串放在组件测试仪上进行检测,通过检测可以发现电池片的 虚焊及电池片本身的裂纹等。 (6)叠层铺设:将检测合 格好的电池串与面板玻璃及裁 好的EVA 胶膜、PTP 背板按照一 定的顺序铺设好准备层压。铺设 前要对面板玻璃进行清洗,做好 EVA 胶膜与电池片的相对位置, 一般胶膜的尺寸要大于面板玻璃周边各20mm 。铺设的顺序由下向上一次为:玻璃-EVA 胶膜-电池片-EVA 胶膜 -PTP 背板。 (7)层压:将铺设好的光 伏组件放在层压机内,通过抽真空 将组件内的空气抽出,然后加热使 EVA 胶膜融化并加压,使熔化的 EVA 胶在流动中充满玻璃、电池片、 和PTP 背板膜之间的间隙,同时排 出间隙中的气泡,将组件紧密粘合 在一起。最后降温、固化后取出。 (8)终检:将层压好的光 伏组件放在组件检测仪上进行检 测,不仅要检测组件在层压过程中 的各种参数是否变化,还要观察组 件内电池片的位置是否发生偏移, 是否有裂纹,组件内是否有斑点、 碎渣、异物等。 (9)装边框:就是给终测 好的组件安装铝合金边框,这个在 自动组框机上进行。安装边框进一 步密封光伏组件,延长电池的使用 寿命。边框与组件的缝隙用硅胶密深圳聚光能提供 层压机 组框机
太阳能电池组件生产工艺
太阳能电池组件生产工艺 组件线又叫封装线,封装是太阳能电池生产中的关键步骤,没有良好的封装工艺,多好的电池也生产不出好的组件板。电池的封装不仅可以使电池的寿命得到保证,而且还增强了电池的抗击强度。产品的高质量和高寿命是赢得可客户满意的关键,所以组件板的封装质量非常重要。 工艺流程如下: 1、电池检测—— 2、正面焊接—检验— 3、背面串接—检验— 4、敷设(玻璃清洗、材料切割、玻璃预处理、敷设)—— 5、层压—— 6、去毛边(去边、清洗)—— 7、装边框(涂胶、装角键、冲孔、装框、擦洗余胶)—— 8、焊接接线盒—— 9、高压测试——10、组件测试—外观检验—11、包装入库; 工艺简介: 在这里只简单的介绍一下工艺的作用,给大家一个感性的认识,具体内容后面再详细介绍: 1、电池测试:由于电池片制作条件的随机性,生产出来的电池性能不尽相同,所以为了有效的将性能一致或相近的电池组合在一起,所以应根据其性能参数进行分类;电池测试即通过测试电池的输出参数(电流和电压)的大小对其进行分类。以提高电池的利用率,做出质量合格的电池组件。 2、正面焊接:是将汇流带焊接到电池正面(负极)的主栅线上,汇流带为镀锡的铜带,我们使用的焊接机可以将焊带以多点的形式点焊在主栅线上。焊接用的热源为一个红外灯(利用红外线的热效应)。焊带的长度约为电池边长的2倍。多出的焊带在背面焊接时与后面的电池片的背面电极相连。(我们公司采用的是手工焊接) 3、背面串接:背面焊接是将36片电池串接在一起形成一个组件串,我们目前采用的工艺是手动的,电池的定位主要靠一个膜具板,上面有36个放置电池片的凹槽,槽的大小和电池的大小相对应,槽的位置已经设计好,不同规格的组件使用不同的模板,操作者使用电烙铁和焊锡丝将“前面电池”的正面电极(负极)焊接到“后面电池”的背面电极(正极)上,这样依次将36片串接在一起并在组件串的正负极焊接出引线。 4、层压敷设:背面串接好且经过检验合格后,将组件串、玻璃和切割好的EVA 、玻璃纤维、背板按照一定的层次敷设好,准备层压。玻璃事先涂一层试剂(primer)以增加玻璃和EVA的粘接强度。敷设时保证电池串与玻璃等材料的相对位置,调整好电池间的距离,为层压打好基础。(敷设层次:由下向上:玻璃、EVA、电池、EVA、玻璃纤维、背板)。 5、组件层压:将敷设好的电池放入层压机内,通过抽真空将组件内的空气抽出,然后加热使EVA熔化将电池、玻璃和背板粘接在一起;最后冷却取出组件。层压工艺是组件生产的关键一步,层压温度层压时间根据EVA的性质决定。我们使用快速固化EVA时,层压循环时间约为25分钟。固化温度为150℃。 6、修边:层压时EVA熔化后由于压力而向外延伸固化形成毛边,所以层压完毕应将其切除。