煤制氢装置工艺说明书

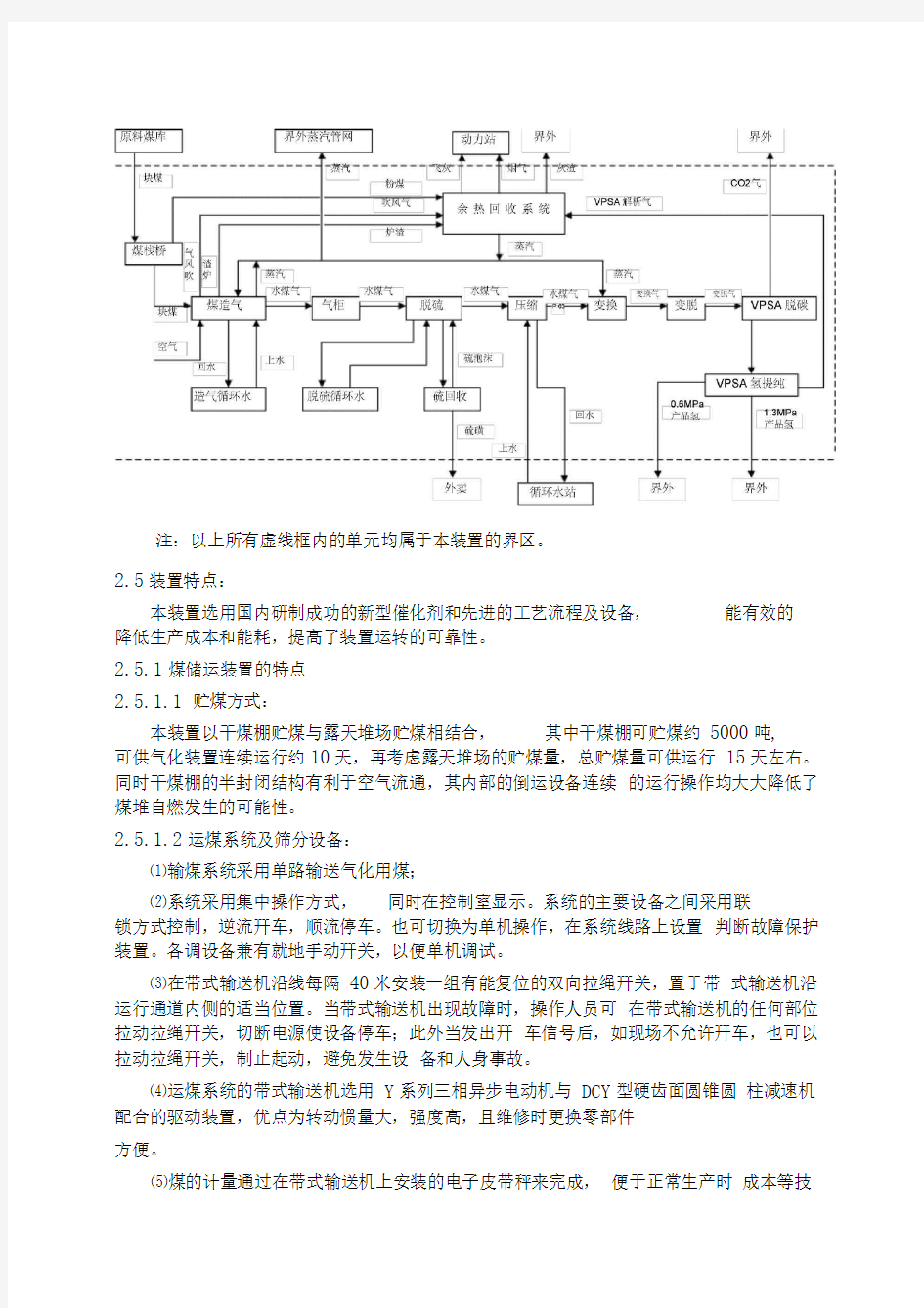
浙江X X X X X X 有限公司
培训教材
煤制氢装置工艺说明书
二。一O年九月
第一章概述
1 设计原则
1.1本装置设计以无烟煤、蒸汽、空气为主要原料生产水煤气,然后经过一系列的净化变换处理生产工业氢气;生产规模:30000Nm3/h 工业氢气。
1.2本装置采用成熟、可靠、先进的技术方案,合理利用能源,降低能耗,节省投资。
1.3认真贯彻国家关于环境保护和劳动法的法规和要求,认真贯彻“安全第一、预防为主”的指导思想,对生产中易燃易爆、有毒有害的物质设置必要的防范措施,三废排放要符合国家现行的有关标准和法规。
1.4采用DCS集散型控制系统。
2 装置概况及特点
2.1装置概况
本装置技术采用固定床煤气发生炉制气、湿法脱硫、全低温变换、变压吸附
VPSA脱碳和(PSA提纯氢气的工艺技术路线,其中的变压吸附脱碳和提氢技术采用上海华西化工科技有限公司的专有技术。
本装置由原料煤储运工序、固定床煤气发生炉制水煤气工序、水煤气脱硫工序、水煤气压缩工序、全低温变换工序、变换气脱硫工序、变压吸附脱碳和提氢工序、造气和脱硫循环水处理工序以及余热回收等部分组成。
2.2装置组成
原料煤储运T造气T气柜T水煤气脱硫T水煤气压缩T全低温变换T变换气脱硫-变压吸附脱碳-变压吸附提氢
2.3生产规模
制氢装置的生产规模为30000NmVh ,其中0.6MPa产品氢7000 Nm3/h , 1.3 MPa 产品氢23000 Nm'/h。装置的操作弹性为30—110%年生产时数为8000小时。
2.4 物料平衡简图
本装置的界区自原料煤库出来的第一条输煤皮带的下料开始,至产品氢出口的最后一个阀门为止。
注:以上所有虚线框内的单元均属于本装置的界区。
2.5装置特点:
本装置选用国内研制成功的新型催化剂和先进的工艺流程及设备,能有效的
降低生产成本和能耗,提高了装置运转的可靠性。
2.5.1煤储运装置的特点
2.5.1.1 贮煤方式:
本装置以干煤棚贮煤与露天堆场贮煤相结合,其中干煤棚可贮煤约5000吨,
可供气化装置连续运行约10天,再考虑露天堆场的贮煤量,总贮煤量可供运行15天左右。同时干煤棚的半封闭结构有利于空气流通,其内部的倒运设备连续的运行操作均大大降低了煤堆自燃发生的可能性。
2.5.1.2运煤系统及筛分设备:
⑴输煤系统采用单路输送气化用煤;
⑵系统采用集中操作方式,同时在控制室显示。系统的主要设备之间采用联
锁方式控制,逆流幵车,顺流停车。也可切换为单机操作,在系统线路上设置判断故障保护装置。各调设备兼有就地手动幵关,以便单机调试。
⑶在带式输送机沿线每隔40米安装一组有能复位的双向拉绳幵关,置于带式输送机沿运行通道内侧的适当位置。当带式输送机出现故障时,操作人员可在带式输送机的任何部位拉动拉绳幵关,切断电源使设备停车;此外当发出幵车信号后,如现场不允许幵车,也可以拉动拉绳幵关,制止起动,避免发生设备和人身事故。
⑷运煤系统的带式输送机选用Y系列三相异步电动机与DCY型硬齿面圆锥圆柱减速机配合的驱动装置,优点为转动惯量大,强度高,且维修时更换零部件
方便。
⑸煤的计量通过在带式输送机上安装的电子皮带秤来完成,便于正常生产时成本等技
术经济指标的统计和核算。
⑹在煤栈桥中转站的筛分楼顶面设置了除尘系统,既改善了现场的操作环境,排放气质量也达到了环保要求。
2.5.2造气装置的特点
2.5.2.1 造气炉炉型:
根据用气量、制氢成本等因素,本装置选择? 2.8米的固定床间歇煤气炉。
9 台炉子(8 开1 备)可满足生产30000Nm3/h 氢气的要求。
2.5.2.2造气流程的选用:
制气工艺流程等同于一般煤化工企业造气流程,九台? 2800 造气炉以四炉为一组,中间位置的5#炉可切换并入任何一个炉组。每个炉组共用一台风机、一台煤气显热回收器(热管式锅炉),水煤气经由显热回收器、煤气总管和洗气塔进入气柜;共三台空气鼓风机,可相互切换替用;共两组油泵站,每炉组配置一套;原料自煤库、筛分装置由输送带送到四楼,经输送带皮带秤计量后入各炉的料仓,由各炉的加煤机加入炉中;气柜采用容积一万方的三节钟罩式的湿式气柜,三节钟罩全升起时气柜静压约400mn水柱。
为提高入炉蒸汽的分解率,降低蒸汽和煤消耗,所有入炉蒸汽均采用过热蒸汽,蒸汽的过热热源来自煤气本身的热量。
2.523造气三位一体DCS综合控制系统的应用
造气工序采用先进的三位一体DCS综合控制系统:
⑴采用“机电一体化自动加煤技术” ,每天可减少因人工加煤造成的单炉停炉时间约60分钟,既增加了造气炉的有效制气时间又减少或避免了造气炉的显热损失,使造气生产的安全得到了保证;同时应用自动加煤后可使造气生产中每个循环减少纯吹风时间约3 秒钟左右,这既能节煤,又能增加产气量。另外机电一体化自动加煤改人工集中大量加煤(1200kg 左右)为每个循环下吹阶段少量加煤(每次75kg 左右),这样使煤燃烧更充分,灰渣的残炭量大幅下降,降低了煤耗。
⑵采用造气生产综合优化控制技术,实现煤造气生产过程的程序控制、阀位检测和报警连锁,实现自动加煤的炭层高度和加煤量控制,实现自动下灰及炉盘转速和下灰量的控制,实现吹风时间及上、下吹制气时间和入炉蒸汽流量及蒸汽分解率的优化控制,实现水夹套及汽包液位自动调节,实现鼓风机和油压系统的管理、报警和联锁,最终达到煤造气整个系统的稳产、高产、低耗和安全,确保了造气炉况的优化与稳定,降低了单位产品的煤耗,节能效果明显。
⑶采用完善可靠的油压控制系统,实现油压控制阀门的快速切换,延长了有效的制气时间,提高了单炉的产气量。
2.5.2.4加煤方式的选择
造气原料煤的输送采用皮带自动输送,上煤输送中转站设置筛分装置,确保造气用煤质量的同时,实现造气煤仓加煤的自动化。考虑到装置的连续稳定运行,同时设计了人工吊碳加煤装置,确保在自动化加煤装置出现故障时能实现制气过程的连续稳定。
2.5.2.5造气装置安全设施设计技术的综合利用
⑴造气装置最大的危险是系统中氧含量高。系统工作时处于正压状态,氧含量高的原因只能是制气工序阀门内漏窜气、罗茨机抽负、压缩机抽负。为了防止阀门内漏造成氧高,设计了油压安全联锁的吹风防过氧阀和下行防过氧阀,排除了因设备故障造成氧高的安全隐
患。
⑵造气装置采用安全可靠、性能稳定的液压驱动阀门,主要液压阀都采用阀门阀位监测装置,同时油压系统采用油压和油位报警装置。
⑶造气除尘器各排灰口油压圆盘阀设计为手控油压阀控制,操作位置在一楼,防止出灰时因联络出错而发生误操作。
⑷与共用煤气总管相连的煤气总阀和与共用吹风气总管相连的吹风气回收阀都采用双阀,保证安全和维修时切断的方便。
⑸造气水夹套给水汽包和煤气显热回收器给水汽包还设置过低液位连锁停炉保护措施,确保锅炉系统运行的本质安全。
⑹气柜设置高度高低位报警装置,并设计高位自动放空装置,防止气柜过高冒顶;同时实现气柜高度过低连锁停机保护系统。仪表形式上选用三选二仪表,最大限度地提高气柜运行时的安全系数。
⑺在装置的相应部位设置了安全阀、防爆板、置换放空管等安全装置元件。
2.5.2.6 造气装置附属设备的选用
⑴上行煤气除尘器:
采用高效铸铁除尘器,利用精确铸造的旋涡结构保证旋风分离的气体速度,改善除尘效果,除尘器本体采用渐扩式结构有利于灰渣的分离和沉降。
⑵显热回收器
在造气水煤气显热回收器结构形式的选择上,采用RLG型组合式热管锅炉,
其中热管式蒸汽过热器阻力仅为管壳式的1/3~1/4, 系统阻力下降,保证了制气强度的提高;热管表面渗入镍铬合金,大耐高温和冲刷、耐腐蚀,热能回收效率高,既可增加蒸汽产量,又可降低煤气洗涤冷却水耗量。
⑶水煤气气柜
煤气气柜的作用主要是储存煤气,考虑到造气工序造气炉的间歇特性和投资、占地等因素,为确保为后工序正常供气,煤气气柜采用1个10000m3规格的
直升直降式湿式气柜。
2.5.3 余热回收装置的特点
本装置采用一套三废混燃炉余热回收系统。三废混燃炉不仅回收造气吹风气中约9%可燃组分的化学热及物理显热(250C)、变压吸附提氢装置解析气中约50%可燃组分的化学热,还燃烧掉约含14%残C量的造气炉所产生的全部炉渣(造气炉渣与含C 约75%的无烟粉煤末以2:1 的比例进行配比,制成热值约为
2900kcal/kg 的混合料在三废炉底进行燃烧),真正做到对造气废物的“榨尽吃干”同时生产出2.5MPa?G 280C的过热蒸汽约40t/h,除能满足整个煤制氢装置的用汽需求,多余的蒸汽还能输送给外界的蒸汽总管,经济效益显著;同时避免了吹风气、提氢解析气、造气灰渣直接外排对环境的污染,环保效果显著。
三废流化混燃炉是第三代造气吹风气回收装置,和第二代吹风气回收装置相比有很大的优势,主要体现在以下几点:
⑴安全性能高:三废流化混燃炉是以造气炉渣(或煤)为点火源,炉内始终长明火,爆炸的因素已排除,彻底改变了造气吹风气回收运行的不安全状态,克服了造气吹风气回收的爆炸现象。
⑵一炉多用、减少投资、便于管理:综合煤化工企业,一台三废流化混燃炉就能达到全厂蒸汽自给。
⑶从三废混燃炉底出来的炉渣含C量仅为3%灰分含量占97% 一天所产生的炉渣量有
70 多吨,可送水泥厂、砖瓦厂做建材;三废混燃炉炉顶出来的高温烟气组分主要是CO、N2及HbO气,另外含有少量的SO及夹带的粉尘,烟气经锅炉装置回收热量后,由布袋除尘器除尘(除尘效率可达99%),再送动力站脱硫,
达标后排放,解决了造气生产废气、废渣、废灰综合治理的难题,保护了环境,治理了现场。同时还可将制氢等生产过程中其它工序的低热值废气一起处理掉,实现循环经济和环保效益的最佳配置。
⑷燃烧系统阻力低、不积灰、提高造气吹风效率。
⑸三废流化混燃炉是隔离燃烧,集中分离,集中热量回收,根本不存在锅炉排管的磨损和冷热不均产生应力而导致设备损坏的问题,因此三废流化混燃炉运行周期较长,生产稳定性突出,节能效果明显。
2.5.4 脱硫装置的特点
2.5.4.1流程的优化
因脱硫系统是粗煤气初步净化的过程,系统中含有大量的煤灰及焦油、硫磺、富盐等多种杂质,为确保煤制氢装置的长周期连续稳定运行,脱硫系统采用两套双塔串联流程装置,正常作业方式为并联运行,单套装置的设计负荷按总负荷的75%设计;开双塔时可脱高硫,开单塔可脱低硫,这样既可以有计划的按作业周期的长短安排每套装置的检修和系统清理,又可以提高整个装置的操作弹性。由于设计中采用了双塔串联流程,可以脱除用高硫煤制取的水煤气H2S至设
计指标,使该装置对煤种的适应性较强,另外高硫煤与低硫煤之间存在一定的差价,可以节约原料成本,具有较好的经济效益。
2.5.4.2PDS —600脱硫的工艺特点
⑴脱硫原理:
气体中的HbS溶于脱硫液后,首先与脱硫液中的碱反应
H2S + Na2CO3 == NaHS + NaHCO3
在催化剂作用下,生成的NaHS又与溶液中的氧发生氧化析硫反应,生成单质硫和碳酸钠。在脱硫塔内由于煤气中氧含量不足,溶液中生成的单质硫是不多的,所以当溶液吸收了足量的H2S 后,溶液就失去了继续吸收的能力。
⑵再生原理:
为恢复溶液吸收H2S 的能力,就必须对溶液进行再生,再生过程主要发生氧化析硫反应:NaHS + NaHCO 3 == S + Na 2CO + H2O。同时,由于气(空气)
液相的相对剧烈运动,使析出的单质硫相互凝聚,并随上升气流浮出,离开循环脱硫液,从而使脱硫液双重新具有吸收HS的能力。
⑶催化原理:
在脱硫过程中PDS—600 催化剂最本质的作用是将气体或液体中的氧迅速地结合在催化剂分子上,同时又迅速地促使结合的氧与液体中的硫氢化钠反应,使化合态的硫转化成单质硫。由于催化剂的这一作用,大大降低了化学反应的活化能,从而极大地加快了化学反应速度。