低温光化学装置
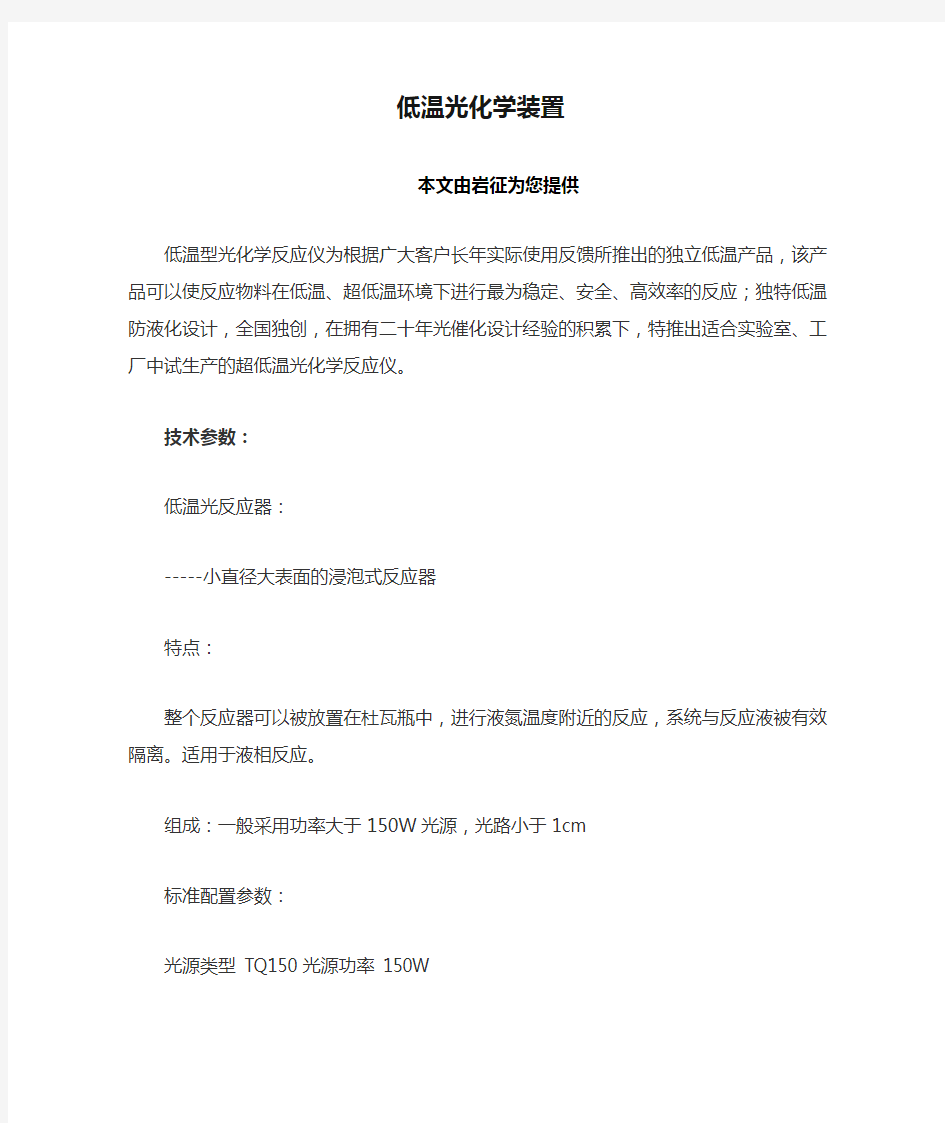

低温光化学装置
本文由岩征为您提供
低温型光化学反应仪为根据广大客户长年实际使用反馈所推出的独立低温产品,该产品可以使反应物料在低温、超低温环境下进行最为稳定、安全、高效率的反应;独特低温防液化设计,全国独创,在拥有二十年光催化设计经验的积累下,特推出适合实验室、工厂中试生产的超低温光化学反应仪。
技术参数:
低温光反应器:
-----小直径大表面的浸泡式反应器
特点:
整个反应器可以被放置在杜瓦瓶中,进行液氮温度附近的反应,系统与反应液被有效隔离。适用于液相反应。
组成:一般采用功率大于150W光源,光路小于1cm
标准配置参数:
光源类型 TQ150 光源功率 150W
附加卤化物(可选) Z1,Z2,Z3 光源长度 384mm
有效弧长 44mm 光源寿命 2000h
反应器体积 600ml 温度范围 -50-40℃
光源材质石英玻璃冷却管材质石英玻璃或硼硅玻璃3.3
主要特点:
光化学反应的应用领域:
1、合成:异构化、加成、置换、聚合、单线态氧化
2、分析:总有机碳(TOC)定量、重金属测量预处理
3、废水处理、超纯水的制备
4、低温杀菌、农药降解
5、制药和化妆品研究:光稳定性测试
6、光生物反应:
特点:
1、选择性强:使分子中某特定位置发生反应的最佳手段。
2、副产物少:用光子为试剂,是“最纯”的试剂,无新的杂质。副反应少:光波长适当,则很低的温度下,反应仍然可以进行,避免原料或产物的热分解。
化学镀镍与电镀镍工艺相互之间的区别
化学镀镍与电镀镍工艺及相互之间的区别 1 电镀镍 电镀是一种电化学过程,也是一种氧化还原过程。电镀镍是将零件浸入镍盐的溶液中作为阴极,金属镍板作为阳极,接通直流电源后,在零件上就会沉积出金属镍镀层。电镀镍的配方及工艺条件见表1。 电镀镍的工艺流程为:①清洗金属化瓷件;②稀盐酸浸泡;③冲净;④浸入镀液; ⑤调节电流进行电镀; ⑥自镀液中取出;⑦冲净;⑧煮;⑨烘干。 表1 电镀镍的配方及工艺条件 成分含量/g/L 温度 /0C PH值电流密度 /A/dm2 硫酸镍硫酸镁硼酸氯化钠 100-170 21-30 14-30 4-12 室温5-6 0.5 电镀镍的优点是镀层结晶细致,平滑光亮,内应力较小,与陶瓷金属化层结合力强。电镀镍的缺点是:①受金属化瓷件表面的清洁和镀液纯净程度的影响大,造成电镀后金属化瓷件的缺陷较多,例如起皮,起泡,麻点,黑点等;②极易受电镀挂具和在镀缸中位置不同的影响,造成均镀能力差,此外金属化瓷件之间的相互遮挡也会造成瓷件表面有阴阳面的现象;③对于形状复杂或有细小的深孔或盲孔的瓷件不能获得较好的电镀表面;④需要用镍丝捆绑金属化瓷件,对于形状复杂、尺寸较小、数量多的生产情况下,需耗费大量的人力。 2 化学镀镍 化学镀镍又称无电镀或自催化镀,它是一种不加外在电流的情况下,利用还原剂在活化零件表面上自催化还原沉积得到镍层,当镍层沉积到活化的零件表面后由于镍具有自催化能力,所以该过程将自动进行下去。一般化学镀镍得到的为合金镀层,常见的是Ni-P合金和Ni-B合金。相较Ni-P合金而言,Ni—B合金的熔焊能力更好,共晶温度高,内应力较小,是一种更为理想的化学镀镍方式。但本文着重讨论的是Ni-P合金镀层。 化学镀镍的配方及工艺条件见表2。 表2化学镀镍的配方及工艺条件 成分含量/g/L 温度 /0C PH值 硫酸镍次磷酸钠柠檬酸钠氯化铵 45-50 45-60 20-30 5-8 85 9.5 化学镀镍的工艺流程为:①清洗金属化瓷件;②冲洗;③活化液浸泡;④冲净; ⑤还原液浸泡;⑥浸入镀液并不时调节pH值;⑦自镀液中取出;⑧冲净;⑨煮;
化学镀工艺流程详解.
化学镀工艺流程 化学镀是一种在无电流通过的情况下,金属离子在同一溶液中还原剂的作用下通过可控制的氧化还原反应在具有催化表面(催化剂一般为钯、银等贵金属离子的镀件上还原成金属,从而在镀件表面上获得金属沉积层的过程,也称自催化镀或无电镀。化学镀最突出的优点是无论镀件多么复杂,只要溶液能深入的地方即可获得厚度均匀的镀层,且很容易控制镀层厚度。与电镀相比,化学镀具有镀层厚度均匀、针孔少、不需直流电源设备、能在非导体上沉积和具有某些特殊性能等特点;但化学镀镀层质量不很好,厚度上不去,且可镀的品种不多,故主要用于不适于电镀的特殊场合。 近年来, 化学镀技术得到了越来越广泛的应用,在各种非金属纤维、微球、微粉等粉体材料上施镀成为研究的热点之一;用化学镀方法可以在非金属纤维、微球、微粉镀件表面获得完整的非常薄而均匀的金属或合金层,而且镀层厚度可根据需要确定。这种金属化了的非金属纤维、微球、微粉镀件具有良好的导电性,作为填料混入塑料时能获得较好的防静电性能及电磁屏蔽性能,有可能部分取代金属粉用于电磁波吸收或电磁屏蔽材料。美国国际斯坦福研究所采用在高聚物基体上化学镀铜来研制红外吸收材料。毛倩瑾等采用化学镀的方法对空心微珠进行表面金属化改性研究,发现改性后的空心微珠具有较好的吸波性能,可用于微波吸收材料、轻质磁性材料等领域。 化学镀所需仪器:电热恒温水浴锅;8522型恒温磁力搅拌器控温搅拌;增力电动搅拌机。化学镀工艺流程:机械粗化→化学除油→水洗→化学粗化→水洗→敏化→水洗→活化→水洗→解胶→水洗→化学镀→水洗→干燥→镀层后处理。 1化学镀预处理 需进行化学镀的镀件一般不溶于水或者难溶于水。化学镀工艺的关键在于预处理,预处理的目的是使镀件表面生成具有显著催化活性效果的金属粒子,这样才能最终在基体表面沉积金属镀层。由于镀件微观表面凸凹不平,必须进行严格的镀前预处理,否则易造成镀层不均匀、密着性差,甚至难于施镀的后果。
铝合金化学镀镍
铝合金化学镀镍 前言:所谓化学镀就是指不使用外电源,而是依靠金属的催化作用,通过可控制的氧化—还原反应,使镀液中的金属离子沉积到镀件上去的方法,因而化学镀也被称为自催化镀或无电镀。化学镀液组成一般包括金属盐、还原剂、络合剂、pH缓冲剂、稳定剂、润湿剂和光亮剂等。当镀件进入化学镀溶液时,镀件表面被镀层金属覆盖以后,镀层本身对上述氧化和还原反应的催化作用保证了金属离子的还原沉积得以在镀件上继续进行下去。目前已能用化学镀方法得到镍、铜、钴、钯、铂、金、银、锡等金属或合金的镀层。化学镀既可以作为单独的加工工艺,用来改善材料的表面性能,也可以用来获得非金属材料电镀前的导电层。化学镀在电子、石油化工、航空航天、汽车制造、机械等领域有着广泛的应用。化学镀具有以下优点:表面硬度高,耐磨性能好;硬化层的厚度及其均匀,处理部件不受形状限制,不变形,特别是适用于形状复杂,深盲孔及精度要求高的细小及大型部件的表面强化处理;具有优良的抗耐蚀性能,在许多酸、碱、盐、氨和海水中具有良好的耐蚀性,其耐蚀性要比不锈钢优越的多;处理后的部件,表面光洁度高,表面光亮,不需要重新的机械加工和抛光,可直接装机使用;镀层与基体的结合力高,不易剥落,其结合力比电镀硬铬和离子镀要高;可处理的基体材料广泛。〔1〕 化学镀分类(广义分类): 1.置换镀(离子交换或电荷交换沉积):一种金属浸在第二种金属的金属盐溶液中,第一种金属的表面上发生局部溶解,同时在其表面自发沉积上第二种金属上。在离子交换的情况下,基体金属本身就是还原剂。 2.接触镀:将欲镀的金属与另一种或另一块相同的金属接触,并沉浸在沉积金属的盐溶液中的沉积法。当欲镀的导电基体底表面与比溶液中待沉积的金属更为活泼的金属接触时,便构成接触沉积。 3.真正的化学镀:从含有还原剂的溶液中沉积金属〔1〕。 日前工业上应用最多的是化学镀镍和化学镀铜。可以使用化学镀进行表面加工的金属及合金有很多,下面以铝合金镀镍为例进行说明,而铝合金化学镀镍属于化学镀的第三种即真正的化学镀。 铝合金简介 铝合金具有机械强度高、密度小、导热导电性好、韧性好、易加工等特点,因而在工业部门,特别是航空航天、国防工业,乃至人们的日常生活中,都有较广泛的应用。铝合金表面覆盖一层致密的氧化膜,它可将铝合金与周围环境隔离开来,避免被氧化。但是这层氧化膜易受到强酸和强碱的腐蚀,同时铝合金易产生晶间腐蚀,表面硬度低,不耐磨。化学镀是赋予铝合金表面良好性能的新型工艺手段之一,它不仅是其抗蚀性、耐磨性、可焊性、和电接触能得到提高,镀层与铝合金机体间结合力好,镀层外观漂亮,而且通过镀覆不同的镍基合金,可以赋予铝合金各种新性能,如磁性能、润滑性等。〔2〕 铝合金化学镀镍原理: 化学镀镍是利用镍盐溶液在强还原剂次亚磷酸钠的作用下,使镍离子还原成金属镍,同时次磷酸钠分解析出磷,因而在具有催化表面的镀件上,获得镍磷合金镀层。 对于次磷酸钠还原镍离子的总反应可以写成: 3NaH 2PO 2 +3H 2 O+NiSO 4 -----3 NaH 2 PO 3 +H 2 SO 4 +2H 2 +Ni 同样的反应可写成如下离子式: 2 H 2PO 2 -+ Ni2++2H 2 O-----2 H 2 PO 3 -+ H 2 +2H++ Ni 或写成另一种形式:Ni 2++H 2 PO 2 -+H 2 O------H 2 PO 3 -+Ni+2H+ 所有这些反应都发生在催化活性表面上,需要外界提供能量,即在较高温度(60≤T≤
化学镀镍工艺
化学镀镍工艺——镀前处理需知 化学镀镍的对象是具体的工件,进厂待镀的工件状况,包括工件材质、制造或维护方法,工件尺寸和最终使用情况是不同的;因此前处理方法应有所不同。在确定正确的前处理工艺流程时,必须对工件善有充分的了解。 合金类型为保证镀层足够的结合力以及镀层质量,必须鉴定基体材质。某些含有催化毒性合金成分的材料在镀前处理时加以表面调整,保证除去这些合金成分后才能进行化学镀镍。例如:铅(含铅钢)、硫(含硫钢)、过量的碳(高碳钢)、碳化物(渗碳钢)等。因为这些物质的残留会产生结合力差和起泡问题。而且,在未除净这些物质的表面、镀层会产生针孔和多孔现象。另一种处理方法是在镀前采用预镀的方法隔离基体才料中有害合金元素的影响。在不清楚待镀工件材质而且又不可能进行材料分析的情况下,必须进行预先试验,试合格后方可处理工作。 工件的制造历史钢件表面状况由于渗碳、渗氮、淬火硬化后提高表面硬度是重要的变化途径之一。通常化学镀镍在硬度范围HRC58-62的铁件表面上镀层的结合力是难以合格的。一方面,上述硬度范围的工件必须进行特别的清洗方法,即在含氰化物的溶液中周期换向电解活化或其它合适的电解清洗,以便溶解除去表面的无机物质诸如碳化物。另一方面,在施镀中产生的表面应力,诸如航天工业用的表面有较高张应力的工件,必须在镀前镀后进行去应力处理,以获得合格的结合力。在制造过程中工件表面大量通讯以除去的机械润滑油和抛光剂等也必须在镀前清除干净。 工件的维修历史工件维修时为除去表面的有机涂层、铁锈或氧化皮,采用喷砂处理,这种工件是化学镀前最难处理的。因为这些工件表面不仅嵌进了残留物质,而且腐蚀产物附着得很牢。在这种情况下,应先采用机械方法清洁表面,以保证后续化学清洗和活化工序的质量。为除去工件表面嵌进的油脂和化学脏污,有时预先烘工件十分有效,尽管这不是唯一的好用的清除方法。 工件的几何尺寸许多工件的几何赃妨碍了采用某前处理技术,如大尺寸的容器以及内表面积很大的管件就是如此。通常清洗和活化钢件应包括电解清洗和活化,在上述情况下,应采用机械清洗、化学清洗和活化更为可行。对于具有盲孔和形状复杂的零件,需要加强清洗工序以解决除去污垢、氢气泡逸出和溶液带出的问题。在工件吊挂和放置方法上也应考虑解决上述问题。 工件非镀面的阻镀问题许多工件要求局部化学镀镍,因此必须彩屏蔽材料将非镀部分保护起来。屏蔽材料可用压敏胶带、涂料、专用塑料夹具等。当然市场上现在有商品的阻镀涂料(或叫保护漆)出售,并且高级一点的,可以镀后轻松除去,用专用溶剂溶解后可以反复使用。 化学清洗浸洗是化学镀前处理的重要步骤之一,其重要的功能在于清除工件表面的污垢,为保证清洗效果,通常使用清洗剂、机械搅拌和加温。采用碱性清洗剂时必须加热至60-80℃,以便彻底清洗污垢,大多数碱性清洗采取浸洗并且强力搅拌,也可以采用喷淋清洗方式。市售的浸洗清洁剂的质量和去污能力差异很大,因此根据工件污染程度选用清洁剂是很重要的。 电解清洗电解清洗化学镀镍活化处理前的末道清洗方法,多适用于精密零件。直流电解清洗即阻极电解清洗的优点在于工件表面产生大量的氢气增加了洗涤效果;其缺点在于工件带负电,因而吸附清洗溶液中的铜、锌和其它金属离子、皂类和某些胶体物质,在工件上形成疏松的电极泥以致带去。电解清洗时采用周期换向电注,当工件为阳极时,迫使工件表面带正电荷的离子和污垢脱离。而且工件表面生成的氧气有利于有效地洗涤掉嵌牢在工件上的污垢,由清洗溶液中的清洁剂去润湿污垢,乳化转换掉污垢。
化学仪器装置图大全
化学仪器装置图大全 一、成套装置.......................................................................................................错误!未定义书签。 1.制氯气:................................................................................................错误!未定义书签。 2.实验室制乙烯:....................................................................................错误!未定义书签。 3.蒸馏、分馏............................................................................................错误!未定义书签。 4.氢气还原氧化铜:................................................................................错误!未定义书签。 5.制SO3 ......................................................................................................错误!未定义书签。 6.喷泉........................................................................................................错误!未定义书签。 7.酯化........................................................................................................错误!未定义书签。 8.制Fe(OH)2 ...............................................................................................错误!未定义书签。 @ 9.合成无水三氯化铁: ...............................................................................错误!未定义书签。 10.合成无水四氯化锡: .............................................................................错误!未定义书签。 11.其它......................................................................................................错误!未定义书签。 12.原电池、电解池..................................................................................错误!未定义书签。 二、组合装置.......................................................................................................错误!未定义书签。 1.两通管加热............................................................................................错误!未定义书签。 2.固~固加热,制气................................................................................错误!未定义书签。 3.固~液、液~液加热,制气................................................................错误!未定义书签。 4.固~液不加热,制气............................................................................错误!未定义书签。 5.启普发生器............................................................................................错误!未定义书签。 【 6.水浴加热................................................................................................错误!未定义书签。 7.洗气瓶....................................................................................................错误!未定义书签。 8.干燥装置................................................................................................错误!未定义书签。 9.集气装置................................................................................................错误!未定义书签。 10.量气装置..............................................................................................错误!未定义书签。 11.尾气吸收..............................................................................................错误!未定义书签。 三、容器...............................................................................................................错误!未定义书签。 1.试管........................................................................................................错误!未定义书签。 2.烧杯........................................................................................................错误!未定义书签。 3.烧瓶、蒸馏瓶........................................................................................错误!未定义书签。 — 4.锥形瓶....................................................................................................错误!未定义书签。 5.试剂瓶....................................................................................................错误!未定义书签。 6.U形管 .....................................................................................................错误!未定义书签。 7.干燥类....................................................................................................错误!未定义书签。 8.冷凝管、牛角管....................................................................................错误!未定义书签。 9.漏斗........................................................................................................错误!未定义书签。 10.水槽.........................................................................................................错误!未定义书签。 11.计量类..................................................................................................错误!未定义书签。 12.加热类..................................................................................................错误!未定义书签。 13.导管......................................................................................................错误!未定义书签。 · 14.橡管、塞、活塞、接口......................................................................错误!未定义书签。 15.其它......................................................................................................错误!未定义书签。
化学镀镍工艺
化学镀镍工艺 化学镀镍机理: 1)原子氢析出机理。原子氢析出机理是1946年提出的,核心是还原镍的物质是原子氢,其反应过程如下: H2P02-+H20→HP032-+H++2H Ni2++2H→Ni+2H+ H2P02-+H++H→2H20+P 2H→H2 水和次磷酸根反应产生了吸附在催化表面上的原子氢,吸附氢在催化表面上还原镍离子。同时,吸附氢在催化表面上也产生磷的还原过程。原子态的氢相互结合也析出氢气。2)电子还原机理(电化学理论)电子还原机理反应过程如下: H2P02-+H20→HP032-+H++2e Ni2++2e→Ni H2P02-+2H++e→2H20+P 2H++2e→H2 酸性溶液中,次磷酸根与水反应产生的电子使镍离子还原成金属镍。在此过程中电子也同时使少部分磷得到还原。 3)正负氢离子机理。该理论最大特点在于,次磷酸根离子与磷相连的氢离解产生还原性非常强的负氢离子,还原镍离子、次磷酸根后自身分解为氢气。 H2P02-+H20→HP032-+H++H- Ni2++2H-→Ni+H2 H2P02-+2H++H-→2H20+P +1/2H2 H-+H+→H2 分析上述机理,可以发现核心在于次磷酸根的P-H键。次磷酸根的空间结构是以磷为中心的空间四面体。空间四面体的4个角顶分别被氧原子和氢原子占据,其分子结构式为: 各种化学镀镍反应机理中共同点是P-H键的断裂。P-H键吸附在金属镍表面的活性点上,在镍的催化作用下,P-H键发生断裂。如果次磷酸根的两个P-H键同时被吸附在镍表面的活性点上,键的断裂难以发生,只会造成亚磷酸盐缓慢生成。对于P-H键断裂后,P-H间共用电子对的去向,各种理论具有不同的解释。如电子在磷、氢之间平均分配,这就是原子氢析出理论;如果电子都转移至氢,则属于正负氢理论;而电子还原机理则认为电子自由游离出来参与还原反应。因此,可以根据化学镀镍机理的核心对各种宏观工艺问题进行分析解释。 化学镀镍工艺过程 化学镀镍前处理工艺 一:除油:
化学气相沉积设备与装置
化学气相沉积设备与装置 化学气相沉积设备与装置 136 化学工程与装备 ChemicalEngineering&Equipment 2011年第3期 2011年3月 化学气相沉积设备与装置 韩同宝 (中国石油集团东方地球物理勘探有限责任公司敦煌经理部,甘肃敦煌736200) 摘要:本文介绍了化学气相沉积设备的系统组成与典型装置,讨论了几种典型装置特点对化学气相沉积 过程的影响,分析和总结了典型装置的维护对沉积参数控制精度及沉积过程的 影响. 关键词:化学气相沉积;设各:装置 前言 化学气相沉积(CvD)技术是一种新型的材料制备方法, 它可以用于制各各种粉 体材料,块体材料,新晶体材料,陶瓷纤维,半导体及金刚石薄膜等多种类型的材料,广泛应用于宇航工业上的特殊复合材科,原子反应堆材料,刀具材料, 耐热耐磨耐腐蚀及生物医用材料等领域.同传统材料制各技术相比,Cv1)技术具有以下优点:(1)可以在远低于材科熔点的温度进行材料合成:(2)可以控制合成材料的元素组成, 晶体结构,微观形貌(粉末状,纤维状,技状,管状,块状 等):(3)不需要烧结助剂,可以高纯度合成高密度材料;(4) 可以实现材料结构 微米级,亚微米级甚至纳米级控制:(5) 能够进行复杂形状结构件及图层的制备;(6)能够制备梯度复合材料及梯度涂层和多层涂层:(7)能够进行亚稳态物质
及新材料的合成.目前,CVD己成为大规模集成电路的铁电材料,绝缘材料,磁性 材料,光电子材料,高温热结构陶瓷基复合材料及纳米粉体材料不可或缺的制备技术. 关于CVD技术的热力学,动力学,各种新型CVD方法及制各粉体,薄膜,纤维,块体,复合材料的研究已经有了大量的报道.然而,关于CVD设备与装置的系统报道却 很少见. 本文对CVD设备的系统组成,典型装置与仪器及其维护进行了分析和总结. 1CvD设备系统的构成 任何一种CVD系统都需要满足以下四个最基本的需求: 传输和控制先驱体气体,载气和稀释气体进入反应室:提供激发化学反应的能量源:排除和安全处理反应室 的副产物废气:精确控制反应参数,温度,压力和气体流量.对于大规模的生产,还 必须考虑一些其它的需求,如生产量,经济, 安全和维修等. 基于以上的这些要求.CVD设备系统通常要包括一些一些子系统: (1)气体传输系统.用于气体传输和混合:(2)反应 室,化学反应和沉积过程在其中进行:(3)进装科系统,用于装,出炉和产品在反 应室内的支捧装置;(4)能量系统, 为激发化学反应提供能量源;(5)真空系统.用于 捧除反应废气和控制反应压力,包括真空泵,管道和连接装置;(6) 工艺自动控制系统,计算机自动控制系统用于测量和控制沉积温度,压力,气体流量和沉积时间:(7) 尾气处理系统. 用于处理危害和有毒的尾气和柱子,通常包括冷阱,化学阱, 粉尘阱等. 2CvD设备系统的典型装置 2.I反应气体传输装置 CVD的反应物有气体,固体和液体三种形态.反应物为 气态的直接通入或通过载气传送近反应室内.反应物为固体的通过加热变为气 态或溶于无污染溶剂中变为液态经载气传输进反应室内.反应物为液态的可通过直 接蒸发,载气携带和鼓泡方式载入反应室内.气态反应物可通过气体减压器和流量
化学镀镍配方汇编
简述电镀槽液加料方法与溶液密度测定方法 1.电镀生产现场工艺管理的主要内容: 1)控制各槽液成分在工艺配方规范内。遵守规定的化学分析周期。 2)保持电镀生产的工艺条件。如温度、电流密度等。 3)保持阴极与阳极电接触良好。 4)严格的阴极与阳极悬挂位置。 5)保持镀液的清洁和控制镀液杂质。 6)保持电镀挂具的完好和挂钩、挂齿良好的电接触。 2.电镀槽液加料方法:加料要以“勤加”“少加”为原则。 2.1固体物料的补充,某些有机固体料先用有机溶剂溶解,再慢慢加入以提高增溶性。若直接加入往往会使镀液混浊。一般的固体物料,可用镀槽中的溶液来分批溶解。即取部分电镀液把要加的料在搅拌下慢慢加入,待静止澄清,把上层清液加入镀槽。未溶解的部分,再加入镀液,搅拌溶解。这样反复作业,直到全部加完。在不影响镀液总体积的情况下,也可以用去离子水或热的去离子水搅拌溶解后加入镀槽。有些固体料易形成团状,影响溶解过程。可以先用少量水调成稀浆糊状,逐步冲稀以避免团状物的形成。 2.2液体物料的补充,可以用去离子水适当稀释或用镀液稀释后在搅拌下慢慢加入。严禁将添加剂光亮剂的原液加入镀槽。 2.3补充料的时机,加料最好是在停镀时进行。加入后经过充分搅匀再投入生产。在生产中加料,要在工件刚出槽后的“暂休”时段加入。可在
循环泵的出液口一方加入,加入速度要慢,药料随着出液口的冲击力很快分散开来。 2.4加料方法不当可能造成的后果: 2.4 1)如果加入的是光亮剂,则易造成此槽工件色泽差异。 2.4.2)如果加入的是没有溶解的固体料,则易造成镀层毛刺或粗糙。 2.4.3)如果是加入酸调节pH,会造成槽液内部pH不均匀而局部造成针孔。 3.镀液及其它辅助溶液密度的测试方法: 3.1要经常测定溶液的密度,新配制的镀液或其它辅助液,都要测定它的密度并作为档案保存起来供以后对比。镀液的密度一般随着槽龄增加而增加。这是由于镀液中杂质离子、添加剂分解产物等积累的结果,因此可以把溶液密度与溶液成分化验数据一起综合进行分析,判断槽液故障原因以利排除。 3.2溶液密度测定方法,在电镀生产中,常用密度计或波美计测试溶液密度。密度与波美度可以通过下列公式转换。对重于水的液体密度 =145/(145-波美度),波美度=(145x145)/密度,在用波美计测试时,其量程要从小开始试测,若波美计量程选择不当,会损坏波美计。 测试密度不要在镀槽内进行,应取出部分镀液在槽外进行。在镀槽中测试,当比重计或波美计万一损坏,镀液会被铅粒污染。应将待测液取出1.5L左右(用2000mL烧杯),热的溶液可用水浴冷却。然后将样液转移至1000mL直形量筒中,装入量为距筒口约20mm处,就可用比重计测量。 脉冲电镀电源使用须知
实验指导书-化学气相沉积上课讲义
实验指导书-化学气相 沉积
化学气相沉积技术实验 一、实验目的 1.了解化学气相沉积制备二硫化钼的基本原理; 2.了解化学气相沉积方法制备二硫化钼薄膜材料的基本流程及注意事项; 3.利用化学气相沉积方法制备二硫化钼薄膜材料。 二、实验仪器 该实验中用到的主要实验仪器设备以及材料有:干燥箱、CVD生长系统、电子天平、超声清洗机,去离子水机等,现将主要设备介绍如下: 1.CVD生长系统 本实验所用CVD生长系统由生长设备,真空设备,气体流量控制系统和冷却设备四部分组成,简图如下 图1 CVD设备简图 2.电子天平 本实验所用电子天平采用电磁力平衡被称物体重力原理进行称量,特点是称量准确可靠、显示快速清晰并且具有自动检测系统、简便的自动校准装置以及超载保护等装置。在本实验中电子天平主要用于精确称量药品,称量精度可精确到小数点后第五位。 三、实验原理
近年来,各国科学工作者对化学气相沉积进行了大量的研究,并取得一定的显著成果。例如,从气态金属卤化物(主要是氯化物)还原化合沉积制取难熔化合物粉末及各种涂层(包括碳化物、硼化物、硅化物、氮化物)的方法。其中化学沉积碳化钛技术已十分成熟。化学气相沉积还广泛应用于薄膜制备,主要为Bchir等使用钨的配合物Cl4 (RCN)W(NC3H5)作为制备氮化钨或者碳氮共渗薄膜的原料—CVD前驱体;Chen使用聚合物化学气相沉积形成的涂层提供了一个有吸引力的替代目前湿法化学为主的表面改善方法。同时,采用CVD方法制备CNTS的研究也取得很大的进展和突破,以及通过各种实验研究了不同催化剂对单壁纳米碳管的产量和质量的影响,并取得了一定的成果。 一、化学气相沉积法概述 1、化学沉积法的概念 化学气相沉积(Chemical vapor deposition,简称CVD)是反应物质在气态条件下发生化学反应,生成固态物质沉积在加热的固态基体表面,进而制得固体材料的工艺技术。它本质上属于原子范畴的气态传质过程。与之相对的是物理气相沉积(PVD)。 化学气相沉积是一种制备材料的气相生长方法,它是把一种或几种含有构成薄膜元素的化合物、单质气体通入放置有基材的反应室,借助空间气相化学反应在基体表面上沉积固态薄膜的工艺技术。 2、化学气相沉积法特点 (1) 在中温或高温下,通过气态的初始化合物之间的气相化学反应而形成固体物质沉积在基体上。
最新高中化学实验装置图汇总
人教版高中化学实验装置图汇总(必修一) 章节名 称实验名称实验原理 实验装置仪器药品清单备注 第一章第一节: 化学实验基本方法过滤 固体与液体混合 物的分离 仪器:漏斗、烧 杯、玻璃板、铁 架台(带铁圈)、 滤纸 药品:固液混合 物 操作要 点:“一 贴二低 三靠”蒸发 分离溶剂中的溶 质 仪器:蒸发皿、 酒精灯、玻璃 棒、铁架台 药品:食盐水溶 液 注意: 蒸发过 程中要 不断搅 拌,在 加热至 有大量 固体析 出时要 用余温 加热 蒸馏 混合物中各组分 的沸点不同 仪器:蒸馏烧 瓶、酒精灯、铁 架台、冷凝管、 锥形瓶 药品:液体混合 物 加热前 一定要 检验装 置的气 密性 萃取 物质在互不相容 的溶剂里的溶解 度不同,用一种溶 剂把物质从它与 另一种溶剂所组 成的溶液里提取 出来 分液漏斗、烧 杯、铁架台(带 铁圈) 进行分 液操作 之前一 定要进 行检漏
第一章 第二节:化学计量在实验中的应用配制一定 量浓度的 溶液 C=n/V 仪器:容量瓶、 量筒、烧杯、玻 璃棒、胶头滴 管、托盘天平 药品:氯化钠固 体、蒸馏水 容量瓶 在使用 之前一 定要检 漏 第二章 第一节:物质的分类丁达尔效 应 当一束光线透过 胶体,从入射光的 垂直方向可以观 察到胶体里出现 的一条光亮的“通 路” 仪器:激光笔、 烧杯 药品:某种胶体 第三章 第一节:金属的化学性 质加热金属 钠 钠受热后,与氧气 剧烈反应,发出黄 色火焰,生成一种 淡黄色固体,过氧 化钠 仪器:小刀、铁 架台(带铁圈)、 酒精灯药品: 金属钠 注意安 全 金属钠和 水的反应 活泼金属和水的 剧烈反应 仪器:小刀、烧 杯 药品:蒸馏水、 金属钠、酚酞 注意观 察实验 现象 铝与盐酸 和氢氧化 钠溶液的 反应 铝是两性金属,既 能和酸反应又能 和碱反应 仪器:试管、架 子 药品:盐酸溶 液、氢氧化钠溶 液 注意检 查生成 的气体 第三章 第二节:几种重要的金属化合 物过氧化钠 和水的反 应 过氧化钠可以与 水反应生成氧气 仪器:试管、火 柴 药品:过氧化 钠、蒸馏水、 注意检 验生成 的气体
镀镍工艺
镀镍工艺 一、镀镍概述 在零件上镀镍可以使零件具有优良的耐蚀性、耐磨性、可焊性以及高硬度等优点,满足零件的使用要求,提高零件的使用寿命。 镀镍通常可以采用化学镀镍,也可以采用电镀或刷镀。化学镀与电镀相比具有显著的优点:1.具有广泛的覆盖能力,对于复杂零件的各个部位可以得到较均匀的镀层;2.具有比电镀优良得多的深镀能力,可以大大地减少镀件盲孔、深孔内的无镀层现象。 刷镀是最近几年发展起来的一种新工艺,它的最大优点是不用镀槽,而且沉积速度较快。由于它设备筒单,操作方便,可以选择多种镀层,而且具有较高的结合强度等优点,所以在航空、船舶、铁路、电子及机械和各种车辆的维修中广泛应用,是目前国家推广的一种新工艺。 但是,刷镀在很多场台下,如修理大批量、大面积镀层的一些零件,生产率显然不是很高,而且同化学镀相比较,刷镀的镀层深镀也明显不如化学镀。而且化学镀镍层具有比电镀和刷镀优良得多的耐蚀性、耐磨性、可焊性以及镀层厚度均匀、硬度高等优点。 化学镀镍通常是在高温(70?90C)下操作,虽然镍的沉积速度较快,但工艺控制困难,能耗高,镀液易挥发、稳定性差,次亚磷酸盐的利用率低;同时高温操作对软化点低和高温下易变形的材料(如塑料等)施镀,会引起基体的变形和改性,这就限制了它的进一学镀镍研究的重要方向之一,也是一个备受重视的课题。 二、化学镀镍的特点 低温化学镀镍与高温化学镀镲的基础镀液大致相同,但由于温度的降低,根据Arrhenius 方 程,镍的沉积速度将大为降低,因此,低温化学镀镍须在碱性条件下进行,这是低温化学镀镍的一个特点,同时,加速剂显得更为重要,因为在碱性条件下,Ni极易与0H形成溶度积较小的Ni(0H)2沉淀,因而,对络合剂的选择相对高温化学镀
化学镀镍一般工艺
化学镀镍一般工艺 Company number:【WTUT-WT88Y-W8BBGB-BWYTT-19998】
化学镀镍一般工艺 在化学镀镍前,金属制品表面前处理包括:研磨抛光、除油、除锈、活化等过程,化学镀镍中经常使用的金属前处理方法与电镀工艺中的类似。研磨、抛光等物理方法,我们不做讨论。下面主要介绍一些化学处理方法。 1、除油 除油方法可分为有机溶剂除油、化学除油。 有机溶剂除油的特点是除油速度快,不腐蚀金属,但除油不彻底,需用化学法或电化学方法进行补充除油,常用的有机溶剂有:汽油、煤油、苯类、酮类、某些氯化烷烃及烯烃。有机溶剂除油还有一个优点即经除油后的溶剂还可回收再利用。有机溶剂一般属易燃品,使用时要格外小心。 化学除油是利用碱溶液的皂化作用和表面活性物质对非皂化性油脂的乳化作用,除去工件表面上的各种油污的。化学除油的温度通常取在60-80度之间,工件除油效果一般为目测,即工件表面能完全被水润湿就是油污完全除尽的标志。一般的除油液由氢氧化钠、碳酸钠、磷酸三钠、水玻璃、乳化剂等组成。 电化学除油分阴极除油和阳极除油,在相同的电流下,阴极除油产生的氢气比阳极除油产生的氧气多一倍,气泡小而密,乳化能力大,除油效果更好。但容易造成工件氢脆和杂质在阴极析出的现象。阳极除油虽没有这些缺点但可能造成工件表面氧化和溶解。目前常用正负极交换的化学除油法。电化学除油液配方与化学除油的配方相似。 2、除锈? 除锈方法有机械法、化学法和电化学法。 机械法除锈是对工件表面进行喷砂、研磨、滚光或擦光等机械处理,在工件表面得到整平的同时除去表面锈层。 化学法除锈是用酸或碱溶液对金属制品进行强浸蚀处理使制品表面的锈层通过化学作用和浸蚀过程所产生氢气泡的机械剥离作用而除去。 电化学除锈是在酸或碱溶液中对金属制品进行阴极或阳极处理除去锈层。阳极除锈是化学溶解、电化学溶解和电极反应析出的氧气泡的机械剥离作用而去除。阴极除锈是化学溶解和阴极析出氢气的机械剥离作用而去除。 用于化学镀镍前处理除锈工艺基本与电镀的除锈工艺相同。 3、活化? 活化是使零件能获得充分活化的表面,这种酸蚀对于不同材质的零件所用的酸液是不同的。 一般钢铁件的活化可用10%的硫酸或1:1的盐酸进行,活化的标准一般为工件表面冒出细小均匀的气泡。不锈钢件的活化可加大酸的浓度,并且加热进行酸蚀。严格讲,不锈钢的化学镀镍应该进行闪镀后再进行化学镀镍,也就是先打一个电解镍或电解铜的底层。
化学镀镍相关知识.doc
一、化学镀镍溶液的成分分析 为了保证化学镀镍的质量,必须始终保持镀浴的化学成分、工艺技术参数在 最佳范围(状态),这就要求操作者经常进行镀液化学成分的分析与调整。 1.Ni2+浓度 镀液中镍离子浓度常规测定方法是用EDTA络合滴定,紫脲酸胺为指示剂。 试剂 (1)浓氨水(密度:0.91g/ml)。 (2)紫脲酸胺指示剂(紫脲酸胺:氯化钠=1:100)。 (3)EDTA容液0.05mol,按常规标定。 分析方法: 用移液管取出10ml冷却后的化学镀镍液于250ml的锥形瓶中,并加入100ml蒸馏水、15ml浓氨水、约0.2g指示剂,用标定后的EDTA溶液滴定, 当溶液颜色由浅棕色变至紫色即为终点。 镍含量的计算: C Ni2+= 5.87 M·V (g/L) 式中M——标准EDTA溶液的摩尔浓度; V——耗用标准EDTA溶液的毫升数。 2.还原剂浓度 次亚磷酸钠NaH2PO2·H2O浓度的测定 其原理是在酸性条件下,用过量的碘氧化次磷酸钠,然后用硫代硫酸钠溶液反滴定自剩余的碘,淀粉为指示剂。 试剂 (1)盐酸1:1。 (2)碘标准溶液0.1mol按常规标定。 (3)淀粉指示剂1%。 (4)硫代硫酸钠0.1mol按常规标定。 分析方法: 用移液管量取冷却后的镀液5ml于带盖的250mL锥形瓶中;加入盐酸 25mL碘标准溶液于此锥形瓶中,加盖,置于暗处0.5h(温度不得低于25℃); 打开瓶盖,加入1mL淀粉指示剂,并用硫代硫酸钠标准溶液滴定至蓝色消 失为终点。 计算: C NaH2PO2·H2O = 10.6(2M1V1-M2V2) (g/L) 式中M1——标准碘溶液的摩尔浓度; V1——标准碘溶液毫升数;
MOCVD有机金属化学气相沉积
原理:金属有机化学气相沉积系统(MOCVD)是利用金属有机化合物作为源物质的一种化学气相淀积(CVD)工艺,其原理为利用有机金属化学气相沉积法metal-organic chemical vapor deposition.MOCVD是一种利用气相反应物,或是前驱物precursor和Ⅲ族的有机金属和V族的NH3,在基材substrate表面进行反应,传到基材衬底表面固态沉积物的工艺。 优缺点:MOCVD设备将Ⅱ或Ⅲ族金属有机化合物与Ⅳ或Ⅴ族元素的氢化物相混合后通入反应腔,混合气体流经加热的衬底表面时,在衬底表面发生热分解反应,并外延生长成化合物单晶薄膜。与其他外延生长技术相比,MOCVD技术有着如下优点:(1)用于生长化合物半导体材料的各组分和掺杂剂都是以气态的方式通入反应室,因此,可以通过精确控制气态源的流量和通断时间来控制外延层的组分、掺杂浓度、厚度等。可以用于生长薄层和超薄层材料。(2)反应室中气体流速较快。因此,在需要改变多元化合物的组分和掺杂浓度时,可以迅速进行改变,减小记忆效应发生的可能性。这有利于获得陡峭的界面,适于进行异质结构和超晶格、量子阱材料的生长。(3)晶体生长是以热解化学反应的方式进行的,是单温区外延生长。只要控制好反应源气流和温度分布的均匀性,就可以保证外延材料的均匀性。因此,适于多片和大片的外延生长,便于工业化大批量生产。(4)通常情况下,晶体生长速率与Ⅲ族源的流量成正比,因此,生长速率调节范围较广。较快的生长速率适用于批量生长。(5)使用较灵活。原则上只要能够选择合适的原材料就可以进行包含该元素的材料的MOCVD生长。而可供选择作为反应源的金属有机化合物种类较多,性质也有一定的差别。(6)由于对真空度的要求较低,反应室的结构较简单。(7)随着检测技术的发展,可以对MOCVD 的生长过程进行在位监测。 MOCVD技术的主要缺点大部分均与其所采用的反应源有关。首先是所采用的金属有机化合物和氢化物源价格较为昂贵,其次是由于部分源易燃易爆或者有毒,因此有一定的危险性,并且,反应后产物需要进行无害化处理,以避免造成环境污染。另外,由于所采用的源中包含其他元素(如C,H等),需要对反应过程进行仔细控制以避免引入非故意掺杂的杂质。 基本结构和工作流程:通常MOCVD生长的过程可以描述如下:被精确控制流量的反应源材料在载气(通常为H2,也有的系统采用N2)的携带下被通入石英或者不锈钢的反应室,在衬底上发生表面反应后生长外延层,衬底是放置在被加热的基座上的。在反应后残留的尾气被扫出反应室,通过去除微粒和毒性的尾气处理装置后被排出系统。MOCVD工作原理如图所示。
化学气相沉积CVD
化学气相沉积 1 前言 化学气相沉积CVD(Chemical Vapor Deposition)是利用加热,等离子体激励或光辐射等方法,使气态或蒸汽状态的化学物质发生反应并以原子态沉积在置于适当位置的衬底上,从而形成所需要的固态薄膜或涂层的过程。 一般地说,化学气相沉积可以采用加热的方法获取活化能,这需要在较高的温度下进行;也可以采用等离子体激发或激光辐射等方法获取活化能,使沉积在较低的温度下进行。另外,在工艺性质上,由于化学气相沉积是原子尺度内的粒子堆积,因而可以在很宽的范围内控制所制备薄膜的化学计量比;同时通过控制涂层化学成分的变化,可以制备梯度功能材料或得到多层涂层。在工艺过程中,化学气相沉积常常在开放的非平衡状态下进行,根据耗散结构理论,利用化学气相沉积可以获得多种晶体结构。在工艺材料上,化学气相沉积涵盖无机、有机金属及有机化合物,几乎可以制备所有的金属(包括碳和硅),非金属及其化合物(碳化物、氮化物、氧化物、金属间化合物等等)沉积层。另外,由于气态原子或分子具有较大的转动动能,可以在深孔、阶梯、洼面或其他形状复杂的衬底及颗粒材料上进行沉积。为使沉积层达到所需要的性能,对气相反应必须精确控制。 正是由于化学气相沉积在活化方式、涂层材料、涂层结构方面的多样性以及涂层纯度高工艺简单容易进行等一系列的特点,化学气相沉积成为一种非常灵活、应用极为广泛的工艺方法,可以用来制备各种涂层、粉末、纤维和成型元器件。特别在半导体材料的生产方面,化学气相沉积的外延生长显示出与其他外延方法(如分子束外延、液相外延)无与伦比的优越性,即使在化学性质完全不同的衬底上,利用化学气相沉积也能产生出晶格常数与衬底匹配良好的外延薄膜。此外,利用化学气相沉积还可生产耐磨、耐蚀、抗氧化、抗冲蚀等功能涂层。在超大规模集成电路中很多薄膜都是采用CVD方法制备。经过CVD 处理后,表面处理膜密着性约提高30%,防止高强力钢的弯曲,拉伸等成形时产生的刮痕。