2-加强筋设计规范

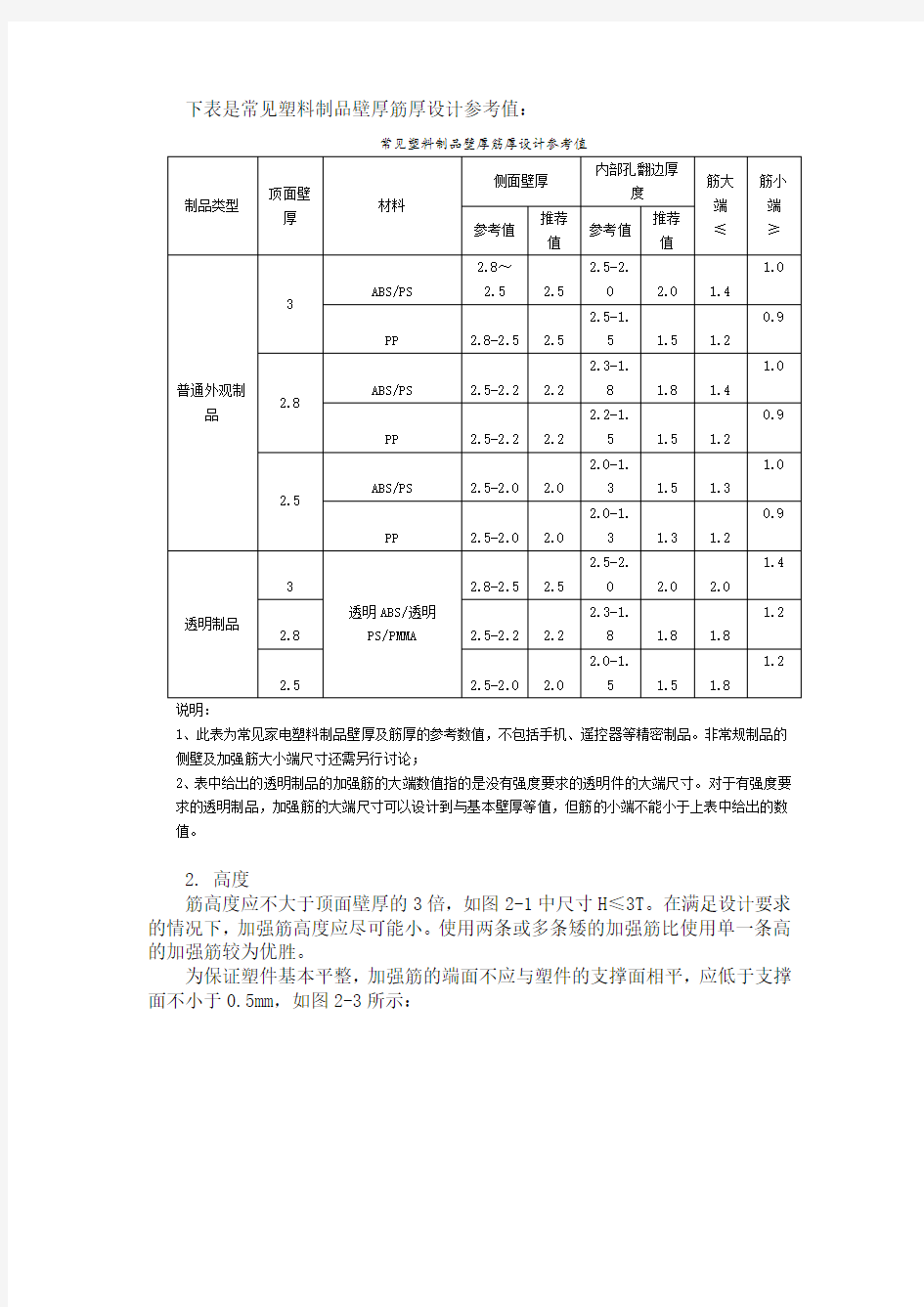
PTC013加强筋设计规范(设计流程节点规范)
一.加强筋应用概述
为了确保塑件的强度和刚性,又不致使塑件的壁厚过厚,可以在塑件的适当部位设置加强筋,以避免塑件的变形。加强筋还起到对装配中元器件的定位,相互配合的部件的对齐,机构的止位和导向的作用,另外,加强筋还可充当内部流道,改善塑件成型过程中塑料流动的情况,有助模腔充填。
二. 加强筋的设计要点
1. 厚度
一般情况下,加强筋大端厚度A应不大于壁厚的1/2,以免引起收缩;筋小端厚度B,PP材料应不小于0.9mm,其他ABS/PS等材料应不小于1.0mm。筋截面如图2-1所示。
T-顶面壁厚
A-筋大端厚度,A≤1/2T
B-筋小端厚度
C-脱模斜度
H-筋的高度
图2-1
增加强度的办法是增加筋的数量,而不是增加筋的厚度。在必须采用较深的加强筋,造成筋大端厚度较厚时,应考虑采取防缩结构,如盘座内壁挂线钩(图2-2所示),或者将容易形成缩痕的部位设计成花纹,来遮盖缩痕。
图2-2
下表是常见塑料制品壁厚筋厚设计参考值:
常见塑料制品壁厚筋厚设计参考值
说明:
1、此表为常见家电塑料制品壁厚及筋厚的参考数值,不包括手机、遥控器等精密制品。非常规制品的
侧壁及加强筋大小端尺寸还需另行讨论;
2、表中给出的透明制品的加强筋的大端数值指的是没有强度要求的透明件的大端尺寸。对于有强度要
求的透明制品,加强筋的大端尺寸可以设计到与基本壁厚等值,但筋的小端不能小于上表中给出的数值。
2. 高度
筋高度应不大于顶面壁厚的3倍,如图2-1中尺寸H≤3T。在满足设计要求的情况下,加强筋高度应尽可能小。使用两条或多条矮的加强筋比使用单一条高的加强筋较为优胜。
为保证塑件基本平整,加强筋的端面不应与塑件的支撑面相平,应低于支撑面不小于0.5mm,如图2-3所示:
图2-3
对于有阶梯的面,在设计加强筋时,应着重考虑筋的位置和高度。如图2-4所示的筋位设计不合理,要保证筋位端面到各支撑面的高度尽量相等。改进方案,可以把筋位的拱形口左移或把拱形口高度抬高。
图2-4
3. 脱模斜度
为方便出模,加强筋应加脱模斜度,一般选取单边0.5°~1°,在允许的情况下,斜度尽量取大值,较深的筋应标注大小端厚度尺寸。
4. 圆角的应用
为提高塑件强度,改善塑件的流动情况及便于脱模,在加强筋的端面设计时,应采用圆弧过度。如图2-5所示的筋位设计不合理,筋位端面应设计成圆角。
图2-5
5.拱形和波形的应用
在加强筋的设计中,要适当考虑拱形和波形的应用。把筋表面制成拱形和波形可以增加筋的强度和刚性,并且可以避免注塑时因料不足而引起的注塑不到位的现象。
6.强度的要求
塑件在跌落过程中会造成特殊部件的断裂,所以设计加强筋时应充分考虑其功能和作用,在强度上达到一定的要求。例如一些受力结构(螺钉柱等)易断裂影响部件的功能,对这类结构考虑与底面的接触面积,要适当增加加强筋的数量,必要时加强筋的底面加圆角以提高强度。
三、加强筋的分类
按照外型及作用的不同,加强筋可分为以下几类,下面分别介绍各类筋应注意的要点。
单向筋
单向筋一般用在薄长型的塑件,只需要单方向刚性的情况。单向筋通常是一系列平行的筋组合使用,设计时应注意系列筋的间距,一般情况下,间距值取不小于壁厚的2倍,如图3-1所示。
T=顶面壁厚
A≤1/2T
H≤3T
L≥2T
C=0.5°~1°
图3-1
若系列筋处有强度要求,如滚筒洗衣机视窗,此处对强度要求比较高,所以系列筋的间距值可不满足上述要求,如图所示。
图3-2
2. 交叉筋
交叉筋就是两个直角相交的筋,其相交处容易形成较厚的截面,如图所示:
图3-3
因此在相交筋接合处设计一个适当尺寸的芯,使筋的厚度保持在1/2壁厚内,以满足加强筋壁厚设计要求,如下图所示。
图3-4
3. 两端相接塑件侧壁的加强筋
加强筋的位置方向最好与胶料熔融充填方向一致,加强筋可两端相接塑件侧壁,长度与塑件长度一致,起增加塑件局部刚性的作用。若筋没有接上塑件侧壁,末端部份不应突然终止,应该渐次地将高度减低,直至完结,从而减少出现困气、填充不满及烧焦痕等问题,这些问题经常发生在排气不足或封闭的位置。
图3-5
4. 与侧壁不垂直的筋
有些筋与侧壁相连时,方向与侧壁不是垂直相交的,而是成一定角度,如图3-6-1所示,筋与侧壁相连处厚度大于侧壁厚度的1/2,为避免收缩,应将筋与侧壁相连处厚度切至壁厚的1/2,或将筋与侧壁相连处改为与垂直相交,如图3-6-2所示。
图3-6-1
图3-6-2
如洗衣机底台底角处的筋,
图3-7
四、成型加强筋的模具设计:
为了降低加工及抛光的成本,模具设计时应注意以下问题: 当筋小端厚度尺寸小于1.2mm时,模具应采用镶拼结构实现;
当筋的深度度大于10mm,筋小端小于1.5mm时,模具应采用镶拼结构实现;
其他情况可根据具体情况确定。
五、典型产品设计举例:
5.1.电视机前壳加强筋的设计:
设计要点:电视机前壳注塑成型采用气辅工艺,避免前脸表面缩水,但对侧壁防缩作用不明显。设计电视机前壳加强筋时,筋的主体壁厚要满足结构强度要求,筋与侧壁相连处的筋的厚度要减薄至前壳壁厚的1/2,以避免侧壁缩水,为了加工方便,应在筋的一侧减胶。
参考产品:21K40三星电视机前壳,模号:7069。
5.1.1.前壳壁厚,如图5-1:
M-前壳主体壁厚度
N-前壳侧壁厚度
图5-1
图5-2
(2)有强度要求的加强筋,如图5-3:
A2-筋大端厚度
B2-筋小端厚度
图5-3
5.1.3.与侧壁相连处的薄筋结构
(1)一般情况,如图5-4:
B3-与侧壁相连处的薄筋的小端厚度
B4-主体筋的大端厚度
H1-与侧壁相连处的薄筋的长度
H2-筋渐变处长度
与侧壁相连处的薄筋的小端厚度B3一般取1mm~侧壁厚度的1/2, 与侧壁相连处的薄筋的长度一般取8~12mm
图5-4
此类型的结构模具上一般做镶拼,如图5-4-1,严禁设计成(a)所示的结构,(c)的设计要优于(b)的设计。
图5-4-1
(2)距侧壁15mm以内有其他结构(如螺钉柱、加强筋等)的情况,如图5-5,图5-6:
B3-与侧壁相连处的薄筋的小端厚度
B4-主体筋的小端厚度
图5-5
图5-6
5.1.4.电视前壳加强筋设计技术参数:见表5-1
六、.加强筋设计案例:
6.1.双桶洗衣机箱体下
双桶洗衣机箱体下是洗衣机的主要承重部件,靠近安装电机处的加强筋底部不能设计过宽,则筋根部应力集中,易断裂,倒圆角后断裂现象消除。
图6-1
6.2.洗衣机内桶底下
洗衣机内桶底下的加强筋在设计时,应考虑阶梯面的存在,为了增加筋的强度和刚性,避免各阶梯面受力不均,端面应设计圆角并且拱形口处应加以改进。
图6-2
塑料件结构设计加强筋设计
塑料件结构设计-(5)加强筋设计 浏览发布时间15/05/10基本设计守则 加强筋在塑胶部件上是不可或缺的功能部份。加强筋有效地如『工』字型,增加产品的刚性和强度而无需大幅增加产品切面面积,但没有如『工』字型筋,倒扣结构将难於成型,对一些经常受到压力、扭力、弯曲的塑胶产品尤其适用。此外,加强筋更可充当内部流道,有助模腔充填,对帮助塑料流入部件的支节部份很大的作用。 加强筋一般被放在塑胶产品的非接触面,其伸展方向应跟随产品最大应力和最大偏移量的方向,选择加强筋的位置亦受制於一些生产上的考虑,如模腔充填、缩水及脱模等。加强筋的长度可与产品的长度一致,两端相接产品的外壁,或只占据产品部份的长度,用以局部增加产品某部份的刚性。要是加强筋没有接上产品外壁的话,末端部份亦不应突然终止,应该渐次地将高度减低,直至完结,从而减少出现困气、填充不满及烧焦痕等问题,这些问题经常发生在排气不足或封闭的位置上。 加强筋一般的设计 加强筋最简单的形状是一条长方形的柱体附在产品的表面上,不过为了满足一些生产上或结构上的考虑,加强筋的形状及尺寸须要改变成如以下的图一般。 加强筋的两边必须加上出模角以减低脱模顶出时的摩擦力,底部相接产品的位置必须加上圆角以消除应力过分集中的现象,圆角的设计亦给与流道渐变的形状使模腔充填更为流畅。此外,底部的宽度须较相连外壁的厚度为小,产品厚度与加强筋尺寸的关系图a说明这个要求。图中加强筋尺寸的设计虽然已按合理的比例,但当从加强筋底部与外壁相连的位置作一圆圈R1时,图中可见此部分相对外壁的厚度增加大约50%因此,此部份出现缩水纹的机会相当大。如果将加强筋底部的宽度相对产品厚度减少一半(产品厚度与加强筋尺寸的关系图b),相对位置厚度的增幅即减至大约20%,缩水纹出现的机会亦大为减少。由此引伸出使用两条或多条矮的加强筋比使用单一条高的加强筋较为优胜,但当使用多条加强筋时,加强筋之间的距离必须较相接外壁的厚度大。加强筋的形状一般是细而长,加强筋一般的设计图说明设计加强筋的基本原则。留意过厚的加强筋设计容易产生缩水纹、空穴、变形挠曲及夹水纹等问题,亦会加长生产周期,增加生产成本。(https://www.360docs.net/doc/119030134.html,)
塑胶产品结构设计准则--加强筋篇
产品结构设计准则--加强筋篇 基本设计守则 加强筋在塑胶部件上是不可或缺的功能部份。加强筋有效地如『工』字铁般增加产品的刚性和强度而无需大幅增加产品切面面积,但没有如『工』字铁般出现倒扣难於成型的形状问题,对一些经常受到压力、扭力、弯曲的塑胶产品尤其适用。此外,加强筋更可充当内部流道,有助模腔充填,对帮助塑料流入部件的支节部份很大的作用。 加强筋一般被放在塑胶产品的非接触面,其伸展方向应跟随产品最大应力和最大偏移量的方向,选择加强筋的位置亦受制於一些生产上的考虑,如模腔充填、缩水及脱模等。加强筋的长度可与产品的长度一致,两端相接产品的外壁,或只占据产品部份的长度,用以局部增加产品某部份的刚性。要是加强筋没有接上产品外壁的话,末端部份亦不应突然终止,应该渐次地将高度减低,直至完结,从而减少出现困气、填充不满及烧焦痕等问题,这些问题经常发生在排气不足或封闭的位置上。 加强筋一般的设计 加强筋最简单的形状是一条长方形的柱体附在产品的表面上,不过为了满足一些生产上或结构上的考虑,加强筋的形状及尺寸须要改变成如以下的图一般。
长方形的加强筋必须改变形状使生产更容易 加强筋的两边必须加上出模角以减低脱模顶出时的摩擦力,底部相接产品的位置必须加上圆角以消除应力集过份中的现象,圆角的设计亦给与流道渐变的形状使模腔充填更为流畅。此外,底部的宽度须较相连外壁的厚度为小,产品厚度与加强筋尺寸的关系图a说明这个要求。图中加强筋尺寸的设计虽然已按合理的比例,但当从加强筋底部与外壁相连的位置作一圆圈R1时,图中可见此部份相对外壁的厚度增加大约50%,因此,此部份出现缩水纹的机会相当大。如果将加强筋底部的宽度相对产品厚度减少一半(产品厚度与加强筋尺寸的关系图b),相对位置厚度的增幅即减至大约20%,缩水纹出现的机会亦大为减少。由此引伸出使用两条或多条矮的加强筋比使用单一条高的加强筋较为优胜,但当使用多条加强筋时,加强筋之间的距离必须较相接外壁的厚度大。加强筋的形状一般是细而长,加强筋一般的设计图说明设计加强筋的基本原则。留意过厚的加强筋设计容易产生缩水纹、空穴、变形挠曲及夹水纹等问题,亦会加长生产周期,增加生产成本。 产品厚度与加强筋尺寸的关系 除了以上的要求,加强筋的设计亦与使用的塑胶材料有关。从生产的角度看,材料的物理特性如熔胶的黏度和缩水率对加强筋设计的影响非常大。此外,塑料的蠕动(creep)特性从结构方面来看亦是一个重要的考虑因数。例如,从生产的角度看,加强筋的高度是受制於熔胶的流动及脱模顶出的特性(缩水率、摩擦系数及稳定性),较深的加强筋要求胶料有较低的熔胶黏度、较低的摩擦系数、较高的缩水率。另外,增加长的加强筋的出模角一般有助产品顶出,不过,当出模角不断增加而底部的阔度维持不变时,产品的刚性、强度,与及可顶出的面积即随着减少。顶出面积减少
河港工程总体设计规范jtj_212-2006
河港工程总体设计规范 JTJ 212-2006 1 总则 1.0.1 为统一河港工程总体设计的技术要求,提高港口的社会效益和经济效益,贯彻国家有关经济和技术政策,适应内河运输事业的发展需要,制定本规范。 1.0.2 本规范适用于内河港口的新建、改建和扩建工程的总体设计。对以潮汐作用为主而停靠内河船舶或海船的河口港、既有河流水文特性又受潮汐影响停靠海船的河港,总体设计可根据不同情况按本规范和现行行、标准《海港总平面设计规范》(JTJ 211)的有关规定执行。 1.0.3 河港工程总体设计应贯彻节约岸线、节约用地、节约能源和安全生产的方针,合理利用资源,保护环境,防治污染。 1.0.4 河港工程总体设计应与江河流域规划、城市总体规划和港口总体规划相协调。改建或扩建工程应重视现有港口的技术改造,充分发挥港口的通过能力。 1.0.5 河港工程总体设计应具备可靠的自然条件资料和社会经济资料等。改建或扩建港口工程还应具备港口现状及运行情况资料等。 1.0.6 河港工程总体设计除应执行本规范规定外,尚应符合国家现行有关标准的规定。 2 港址选择 2.1 一般规定 2.1.1 港址应符合国民经济发展和地区经济开发的需要,结合自然、社会、营运和建设等条件进行综合论证、比较确定。 2.1.2 对适宜建港的水域、岸线及陆域应合理利用,按照深水深用的原则,优先考虑港口建设的需要,并虑适当留有发展余地。 2.1.3 港址应选在河势、河床及河岸稳定少变、水流平顺、水深适当、水域面积足够,并应具备船舶安全营运和锚泊条件的河段。 2.1.4 港址宜具备良好的地质条件。在不良地质条件的地区建港,应进行技术论证。 2.1.5 港址应充分考虑现有的及规划的水库、闸坝、桥梁和其他建筑物对河床冲淤和港区作业条件产生不利影响。 2.1.6 对需要建设专用港区或码头的工矿企业选址时,应同时进行港址选择。 2.1.7 港址选择应充分考虑港口对防洪、航行安全和河道治理等的影响,根据不同的河流类型进行河床演变分析或论证。 2.2 选址原则 2.2.1 港址选择应具备下列主要资料和条件: (1) 水文、气象、河势、地形、地质、地貌和地震; (2) 城市、防洪、交通、枢纽开发的现状及规划,枢纽的功能和调度运行资料,以及历史人文资料; (3) 港口规划、航道、船型和锚地; (4) 水源、电源、通信和地方材料;
产品结构设计准则-加强筋篇
产品结构设计准则--加强筋篇
基本设计守则 加强筋在塑胶部件上是不可或缺的功能部份.加强筋有效地如『工』字铁般增加产品的刚性和强度而无需大幅增加产品切面面积,但 没有如『工』字铁般出现倒扣难于成型的形状问题,对一些经常受到压力,扭力,弯曲的塑胶产品尤其适用.此外,加强筋更可充当内部 流道,有助模腔充填,对帮助塑料流入部件的支节部份很大的作用. 加强筋一般被放在塑胶产品的非接触面,其伸展方向应跟随产品最大应力和最大偏移量的方向,选择加强筋的位置亦受制于一些生产 上的考虑,如模腔充填,缩水及脱模等.加强筋的长度可与产品的长度一致,两端相接产品的外壁,或只占据产品部份的长度,用以局部 增加产品某部份的刚性.要是加强筋没有接上产品外壁的话,末端部份亦不应突然终止,应该渐次地将高度减低,直至完结,从而减少出 现困气,填充不满及烧焦痕等问题,这些问题经常发生在排气不足或封闭的位置上.
加强筋一般的设计 加强筋最简单的形状是一条长方形的柱体附在产品的表面上,不过为了满足一些生产上或结构上的考虑,加强筋的形状及尺寸须要改 变成如以下的图一般.
长方形的加强筋必须改变形状使生产更容易 加强筋的两边必须加上出模角以减低脱模顶出时的摩擦力,底部相接产品的位置必须加上圆角以消除应力集过份中的现象,圆角的设 计亦给与流道渐变的形状使模腔充填更为流畅.此外,底部的宽度须较相连外壁的厚度为小,产品厚度与加强筋尺寸的关系图 a 说明这个
要求.图中加强筋尺寸的设计虽然已按合理的比例,但当从加强筋底部与外壁相连的位置作一圆圈 R1 时,图中可见此部份相对外壁的厚 度增加大约 50%,因此,此部份出现缩水纹的机会相当大.如果将加强筋底部的宽度相对产品厚度减少一半(产品厚度与加强筋尺寸的关系 图 b),相对位置厚度的增幅即减至大约 20%,缩水纹出现的机会亦大为减少.由此引伸出使用两条或多条矮的加强筋比使用单一条高的加 强筋较为优胜,但当使用多条加强筋时,加强筋之间的距离必须较相接外壁的厚度大.加强筋的形状一般是细而长,加强筋一般的设计图 说明设计加强筋的基本原则.留意过厚的加强筋设计容易产生缩水纹,空穴,变形挠曲及夹水纹等问题,亦会加长生产周期,增加生产成 本.
产品厚度与加强筋尺寸的关系 除了以上的要求,加强筋的设计亦与使用的塑胶材料有关.从生产的角度看,材料的物理特性如熔胶的黏度和缩水率对加强筋设计的 影响非常大.此外,塑料的蠕动(creep)特性从结构方面来看亦是一个重要的考虑因数.例如,从生产的角度看,加强筋的高度是受制于熔 胶的流动及
《港口工程建设管理规定》解读
《港口工程建设管理规定》解读 新修订的《港口工程建设管理规定》(交通运输部令2018年第2号)已于2018年1 月15日签发,3月1日起正式施行,现将有关内容解读如下: 一、出台的背景和修订过程 《港口工程竣工验收办法》(交通部令2005年第2号)和《港口建设管理规定》(交通部令2007年第5号)颁布实施以来,对规范和加强港口建设管理,保证和提升港口工程质量起到了重要作用。随着近年来党中央、国务院不断推进行政审批制度改革和深化投融资体制改革,港口工程建设管理面临新的形势和要求:一方面,2016年《中共中央国务院关于深化投融资体制改革的意见》、《企业投资项目核准和备案管理条例》和《政府核准的投资项目目录(2016年本)》相继出台,对建设项目的监管方式提出了新的要求,明确管理重心从事前审批转向过程服务和事中事后监管;提出简化建设项目前置条件,建立并联审批、协同监管机制等改革要求;另一方面,《安全生产法》《消防法》《职业病防治法》《建设项目环境保护管理条例》等法律法规对安全、消防、环保、职业病防护设施等在试运行、验收和监管方式等方面进行了较大调整。因此,本着实事求是、问题导向的原则,我部对《港口建设管理规定》《港口工程竣工验收办法》有关内容进行了全面梳理,并进一步优化了规章体系结构,将上述两部规章合并为《港口工程建设管理规定》(以下简称《规定》)。 为做好《规定》制定工作,我部多次组织各地交通运输(港口)主管部门和港航企业进行工作研讨,赴有关单位进行调研;《规定》(征求意见稿)完成后,我部书面征求了有关部门、单位意见,组织行业专家咨询研讨,在部网站和国务院法制办网站进行了公开征求意见,并根据征求意见情况进行了进一步修改完善,于2018年1月10日经第1次部务会审核通过。 二、《规定》的主要内容 《规定》包括总则、建设程序管理、建设实施管理、验收管理、工程信息及档案管理、法律责任、附则共7章76条。主要内容如下: (一)管理范围。《规定》参照《海港总体设计规范》《港口工程基本术语标准》等关于港口区域的表述,明确港口工程界定为在港口规划港区内,为实现港口功能进行新建、改建和扩建的码头工程(含舾装码头工程)及其同时立项的配套设施、防波堤、锚地、护岸等工程。 (二)建设程序。《规定》区分政府投资和企业投资的港口工程对建设程序做了明确规定。 1.工程立项阶段:政府投资项目实行审批管理,应办理项目建议书和工程可行性研究报告审批手续;企业投资项目实行核准或备案管理,需要办理项目核准手续或填写备案信息。
加强筋的设计
为了克服壁厚大可能引起的问题,使用是一种可减少壁厚并能增加刚性的有效方法。 一般来说,部件的刚性可用以下方法增强 ?增加壁厚; ?增大弹性模量(如加大增强纤维的含量); ?设计中考虑。 如果设计用的材料不能满足所需刚性,则应选择具有更大弹性模量的材料。简单的方法是增加塑料中增强纤维的含量。但是,在特定壁厚下,这种方法仅能使刚性呈线性增长。更有效的方法是使用经过优化设计的。由于惯性力矩增大,部件的刚性便会增大。在优化的尺寸时,不但要考虑工程设计应当考虑的问题,还应考虑与生产和外观有关的技术问题。 优化的尺寸 大的惯性力矩可很容易地通过设置又厚又高的来实现。但是对热塑性工程塑料,这种方法常会产生制品表面凹痕、内部空洞和翘曲等问题。而且,如果的高度过高,在负荷下结构将有可能膨胀。出于这种考虑,必须在合理比例内保持的尺寸(见图1)。 图1 为确保带的制品容易顶出,必须设计一个适当的脱模锥度(见图2)。
图2 防止材料堆积 对于表面要求非常高的组件,如汽车轮盖,的尺寸是非常重要的。正确的设计可以减少组件形成表面凹痕的可能,以提高组件的质量。的底部的材料积聚在图1所示的圆中。这个圆的大小与的尺寸相关,应该越小越好,这样才能减小或避免凹痕。如果圆太大,可能会形成内部空洞,制品的机械性能将会非常差。 减少底部的应力 如果给一个有的组件以负载,则的底部可能会产生应力。在这一部位如果没有圆弧,可能会产生非常高的应力集中(见图3),通常会导致组件的断裂和报废。补救措施是建立一个半径足够大的圆弧(图1),使肋底部建立更好的应力分布。 图3 但如果圆弧半径太大,也会增大上文提及的圆的直径,而导致上文已经提及的问题。
加强筋设计原则
加强筋 ( Ribs ) 基本设计守则 加强筋在塑胶部件上是不可或缺的功能部份。加强筋有效地如『工』字铁般增加产品的刚性和强度而无需大幅增加产品切面面积,但没有如『工』字铁般出现倒扣难於成型的形状问题,对一些经常受到压力、扭力、弯曲的塑胶产品尤其适用。此外,加强筋更可充当内部流道,有助模腔充填,对帮助塑料流入部件的支节部份很大的作用。 加强筋一般被放在塑胶产品的非接触面,其伸展方向应跟随产品最大应力和最大偏移量的方向,选择加强筋的位置亦受制於一些生产上的考虑,如模腔充填、缩水及脱模等。加强筋的长度可与产品的长度一致,两端相接产品的外壁,或只占据产品部份的长度,用以局部增加产品某部份的刚性。要是加强筋没有接上产品外壁的话,末端部份亦不应突然终止,应该渐次地将高度减低,直至完结,从而减少出现困气、填充不满及烧焦痕等问题,这些问题经常发生在排气不足或封闭的位置上。 加强筋一般的设计 加强筋最简单的形状是一条长方形的柱体附在产品的表面上,不过为了满足一些生产上或结构上的考虑,加强筋的形状及尺寸须要改变成如以下的图一般。 长方形的加强筋必须改变形状使生产更容易 加强筋的两边必须加上出模角以减低脱模顶出时的摩擦力,底部相接产品的位置必须加上圆角以消除应力集过份中的现象,圆角的设计亦给与流道渐变的形状使模腔充填更为流畅。此外,底部的宽度须较相连外壁的厚度为小,产品厚度与加强筋尺寸的关系图a说明这个要求。图中加强筋尺寸的设计虽然已按合理的比例,但当从加强筋底部与外壁相连的位置作一圆圈R1时,图中可见此部份相对外壁的厚度增加大约50%,因此,此部份出现缩水纹的机会相当大。如果将加强筋底部的宽度相对产品厚度减少一半(产品厚度与加强筋尺寸的关系图b),相对位置厚度的增幅即减至大约20%,缩水纹出现的机会亦大为减少。由此引伸出使用两条或多条矮的加强筋比使用单一条高的加强筋较为优胜,但当使用多条加强筋时,加强筋之间的距离必须较相接外壁的厚度大。加强筋的形状一般是细而长,加强筋一般的设计图说明设计加强筋的基本原则。留意过厚的加强筋设计容易产生缩水纹、空穴、变形挠曲及夹水纹等问题,亦会加长生产周期,增加生产成本。 产品厚度与加强筋尺寸的关系 除了以上的要求,加强筋的设计亦与使用的塑胶材料有关。从生产的角度看,材料的物理特性如熔胶的黏度和缩水率对加强筋设计的影响非常大。此外,塑料的蠕动(creep)特性从结构方面来看亦是一个重要的考虑因数。例如,从生产的角度看,加强筋的高度是受制於熔胶的流动及脱模顶出的特性(缩水率、摩擦系数
加强筋含凸台、角撑设计说明
加强筋(含凸台、角撑) 1.5.1 加强筋的作用 (1) 在不加大制品壁厚的条件下,增强制品的强度和刚性,以节约塑料用量,减轻重量,降低成本。 (2) 可克服制品壁厚差带来的应力不均所造成的制品歪扭变形。 (3) 便于塑料熔体的流动,在塑料制品本体某些壁部过薄处为熔体的充满提供通道。 1.5.2 加强筋的形状及尺寸 塑料制品上加强筋和凸台的形式和应用如图2-9,图2-10所示。 加强筋尺寸参数如图2-11,图2-12所示。
凸台的形状及尺寸参数如图2-13~图2-15所示。 角撑位于制品边缘,支撑制品壁面,以增加强度及刚度,尺寸参数如图2-16所示。
注意:角撐的高度應比制品的側壁高度低0.5mm以上,以免妨礙制品與其它零件的配合 1.5.3 加强筋的设计要点 (1) 用高度较低、数量稍多的筋代替高度较高的单一加强筋,避免厚筋底冷却收缩时产生表面凹陷、部空洞和翘曲,如果高度过高,在负荷下结构将有可能膨胀,(图2-17、图2-18)。当筋的背面出现凹陷影响美观时,如果外觀允許,可采用图2-19所示的装饰结构予以遮掩。
(2) 筋的布置方向最好与熔料的充填方向一致(见表2-12中示例)。 (3) 筋的根部用圆弧过渡,以避免外力作用时产生应力集中而破坏。但根部圆角半径过大则会出现凹陷。
(4) 一般不在筋上安置任何零件。 (5) 位于制品壁的凸台不要太靠近壁,以避免凸台局部熔体充填不足(图2-20)。 加强筋在防止制品变形、增加制品刚性方面的应用如图2-21~图2-22所示 6)制品底部的加強肋,若結構允許,採用錯位式,而非交叉式,如下圖所示。
冲压件设计
冲压(Stamping) 冲压是在常温下利用压力机并依靠模具对金属材料剪切,使之变形获得所需形状的工艺。 压力机属于锻压机的一类,冷冲压的压力机有机械压力机和液压压力机,常用的是机械压力机(冲床)。 冲压工艺(Stamping Process) (1)落料Cutting 落料:从材料上沿着封闭轮廓分离出工件初胚的工艺。 (2)冲孔Punching 冲孔:从工件上沿着封闭轮廓分离出废料,获得所需要的带孔零件的工序。 (3)压凸/压筋Embossing 压凸/压筋:用凸模挤入工件的一面,迫使材料流入对面凹坑以形成凸起的一种冲压工序。 用途:a)增强产品强度b)代替其他子件 (4)弯曲Bending 弯曲:弯曲是把板材加工成具有一定的角度和形状的零件成形方法,材料在模具的作用下产生弯曲变形。 (5)卷边和翻边Revolving and Hemming 卷边: 对板、圆筒或圆形容器或圆形容器的端部进行圆形卷边的加工。 翻边: 翻边是沿外形曲线周围将材料翻成侧立短边的一种冲压工序。
(6)冲沉孔Chamfering 冲沉孔: 可借助模具在零件孔侧压出锥形沉孔或圆柱形沉孔, 一般用于装配沉头螺丝或去除毛刺。 (7)翻孔Turns Hole 翻孔: 沿内圆孔周围将材料翻成侧立凸缘的冲压工序,一般用于薄片攻螺纹孔。
(8)切舌与切开/冲桥位Part Cutting & Bridge Forming 切舌: 将材料沿轮廓局部而不是完全分离的一种冲压工序。被局部分离的材料,具有工件所要求的一定位置,不再位于分离前所处的平面上。 切开/冲桥位: 将材料沿敞开轮廓局部而不是完全分离的一种冲压工序。被切开而分离的材料位于或基本位于分离前所处的平面。 (9)拍披锋Deburring 拍披锋: 利用模具清除剪切带来的锋利毛刺。
2-加强筋设计规范
PTC013加强筋设计规范(设计流程节点规范) 一.加强筋应用概述 为了确保塑件的强度和刚性,又不致使塑件的壁厚过厚,可以在塑件的适当部位设置加强筋,以避免塑件的变形。加强筋还起到对装配中元器件的定位,相互配合的部件的对齐,机构的止位和导向的作用,另外,加强筋还可充当内部流道,改善塑件成型过程中塑料流动的情况,有助模腔充填。 二. 加强筋的设计要点 1. 厚度 一般情况下,加强筋大端厚度A应不大于壁厚的1/2,以免引起收缩;筋小端厚度B,PP材料应不小于0.9mm,其他ABS/PS等材料应不小于1.0mm。筋截面如图2-1所示。 T-顶面壁厚 A-筋大端厚度,A≤1/2T B-筋小端厚度 C-脱模斜度 H-筋的高度 图2-1 增加强度的办法是增加筋的数量,而不是增加筋的厚度。在必须采用较深的加强筋,造成筋大端厚度较厚时,应考虑采取防缩结构,如盘座内壁挂线钩(图2-2所示),或者将容易形成缩痕的部位设计成花纹,来遮盖缩痕。 图2-2
下表是常见塑料制品壁厚筋厚设计参考值: 常见塑料制品壁厚筋厚设计参考值 说明: 1、此表为常见家电塑料制品壁厚及筋厚的参考数值,不包括手机、遥控器等精密制品。非常规制品的 侧壁及加强筋大小端尺寸还需另行讨论; 2、表中给出的透明制品的加强筋的大端数值指的是没有强度要求的透明件的大端尺寸。对于有强度要 求的透明制品,加强筋的大端尺寸可以设计到与基本壁厚等值,但筋的小端不能小于上表中给出的数值。 2. 高度 筋高度应不大于顶面壁厚的3倍,如图2-1中尺寸H≤3T。在满足设计要求的情况下,加强筋高度应尽可能小。使用两条或多条矮的加强筋比使用单一条高的加强筋较为优胜。 为保证塑件基本平整,加强筋的端面不应与塑件的支撑面相平,应低于支撑面不小于0.5mm,如图2-3所示:
壁厚与加强筋的关系
1·引言 塑料与钢铁、水泥、木材并称为四大工程材料。随着科学技术的进步,塑料的应用也愈加广泛。从事机械设计的工程技术人员应具有一定的塑料构件的设计知识。笔者总结了注塑成型塑料件结构设计的若干要点,这对设计相关产品有借签作用。 2·结构设计要点 2.1壁厚合理 从成型质量的角度来看,塑料件的壁厚过大,在成型的过程中容易产生凹陷、缩孔等缺陷;壁厚太小,则会造成进胶困难,不易充满型腔而造成缺料。塑料件的壁厚应尽可能均匀,可采取缓和的形式过渡,也可采用局部挖空的结构,使壁厚变的均匀,避免成型过程中产生翘曲变形等缺陷。 2.2加强筋结构的设计原则 在塑料件上设置加强筋,可提高塑料件的强度和刚度,防止塑料件的翘曲变形。选择恰当的加强筋位置可改善塑料融体的流动性。 加强筋的尺寸一般遵循以下原则:①筋的壁厚一般为主体厚度t的0.4倍,最大不超过 0.6倍;②筋之间的间距大于4t,筋的高度低于3t; ③螺钉柱的加强筋至少低于柱子表面 1.0mm;④加强筋应低于零件表面或分型面至少1.0mm。多条加强筋相交,要注意相交带来的局部材料堆积问题。 其改进方法是:①将加强筋错位;②加强筋交叉部位设计成空心结构。 细长的加强筋,如受力,应尽量使其承受拉力,避免承受过大的压力。因为塑料材料的弹性模量很低,容易出现失稳问题。这与我们在进行金属铸件设计时所遵循的优先受压原则相反,需要特别注意。 2.3避免应力集中 塑料件的结构设计要特别注意避免尖锐棱角的产生。棱角处几何形状的过渡不连续,此处会产生应力集中现象,从而会产生裂纹。 塑料材料的强度通常很低,应力集中的地方更易损坏。避免应力集中主要的措施是改善构件的尖锐棱角部位的结构形式。例如,在尖角部位增加倒角、倒圆角或以平缓的过渡段代替。当因构件功能的需要而不可直接增加倒角、倒圆角时,可通过在尖角处减小局部结构强度,向内掏出圆角的办法降低应力集中,参照图1所示直线导轨的改进设计方案。塑料螺纹的牙形应优先采用圆形和梯形,避免三角形、矩形,这样可以减低缺口效应,提高螺纹的承载能力。 2.4设计合适的拔模斜度
螺柱通用设计规范
1. 目的 2. 实用范围 3. 术语\定义\名词解释 4 螺丝、螺母的基本介绍 螺丝的分类 螺丝的主要参数 螺母的分类与基本介绍 5. 常见的螺丝柱类型 自攻牙螺丝柱 嵌入螺母型螺丝柱 钣金翻边螺丝柱 钣金铆接螺丝柱 压铸件螺丝柱 6. 螺丝柱的基本设计原则 6.1塑胶类螺丝柱的设计 (1)自攻牙型螺丝柱(2)嵌入螺母型螺丝柱 6.2钣金件螺丝柱的设计 (1)钣金件翻边攻牙(2)钣金件的铆接螺丝柱 6.3压铸件螺丝柱的设计 (1)压铸件的自攻牙螺丝柱设计(2)压铸件的机牙螺丝柱设计 7. 螺丝柱的配合设计原则 螺丝的种类: 自攻螺丝的螺纹分为粗牙和细牙,一般称为typeA和typeAB,绝大多数都用AB牙。自攻螺丝不需要与内螺纹配合,只需有预制孔,攻入时自动产生配合螺纹,多用在木材、塑胶等质地较软的材料上面。自攻螺丝属于非标。 机螺丝与自攻螺丝的区别一是他们的螺纹。机螺纹一般多用粗牙,需与相应标准的内螺纹配合缩紧,一般多为螺母或着有螺纹的金属件。机螺纹主要有公制标准、美制标准、英制标准,公制标准和美制标准螺纹角为60度,英制为55度。公制标准以螺距表示、美制和英制标准 则以一英寸多少牙来表示。 螺丝的主要参数 螺纹 1、大径d(D) 螺纹的最大直径,即外螺纹的牙顶(或内螺纹的牙底),相重合的假想的圆柱面的直径,也叫螺纹的公称直径。 2、小径d1(D1)螺纹的最小直径,即与外螺纹牙底(或内螺纹牙顶)相重合的假想圆柱面的直径
3、中径d2(D2)一个假想圆柱面的直径,其母线通过牙型上牙厚和牙间宽相等圆柱面的直径 4、螺距P 相邻两牙在中径上的对应两点间轴向距离。 5、导程S 同一条螺旋线上的相邻两牙在中径上对应两点间的轴向距离。 6、螺纹升角φ在中径圆柱上螺旋线的切线与垂直于螺纹轴线的平面间夹角。 7、牙型角α轴向剖面内螺纹牙型两侧面的夹角。 8、牙型斜角β轴向剖面内螺纹牙型一侧边与螺纹轴线的垂线间的夹角。 螺丝头的形状 螺丝头的槽型
塑料件结构设计 加强筋设计
塑料件结构设计-(5)加强筋设计 浏览?发布时间?15/05/10基本设计守则 ??? 加强筋在塑胶部件上是不可或缺的功能部份。加强筋有效地如『工』字型,增加产品的刚性和强度而无需大幅增加产品切面面积,但没有如『工』字型筋,倒扣结构将难於成型,对一些经常受到压力、扭力、弯曲的塑胶产品尤其适用。此外,加强筋更可充当内部流道,有助模腔充填,对帮助塑料流入部件的支节部份很大的作用。 ??? 加强筋一般被放在塑胶产品的非接触面,其伸展方向应跟随产品最大应力和最大偏移量的方向,选择加强筋的位置亦受制於一些生产上的考虑,如模腔充填、缩水及脱模等。加强筋的长度可与产品的长度一致,两端相接产品的外壁,或只占据产品部份的长度,用以局部增加产品某部份的刚性。要是加强筋没有接上产品外壁的话,末端部份亦不应突然终止,应该渐次地将高度减低,直至完结,从而减少出现困气、填充不满及烧焦痕等问题,这些问题经常发生在排气不足或封闭的位置上。 加强筋一般的设计 ??? 加强筋最简单的形状是一条长方形的柱体附在产品的表面上,不过为了满足一些生产上或结构上的考虑,加强筋的形状及尺寸须要改变成如以下的图一般。 ??? 加强筋的两边必须加上出模角以减低脱模顶出时的摩擦力,底部相接产品的位置必须加上圆角以消除应力过分集中的现象,圆角的设计亦给与流道渐变的形状使模腔充填更为流畅。此外,底部的宽度须较相连外壁的厚度为小,产品厚度与加强筋尺寸的关系图a说明这个要求。图中加强筋尺寸的设计虽然已按合理的比例,但当从加强筋底部与外壁相连的位置作一圆圈R1时,图中可见此部分相对外壁的厚度增加大约50%因此,此部份出现缩水纹的机会相当大。如果将加强筋底部的宽度相对产品厚度减少一半(产品厚度与加强筋尺寸的关系图b),相对位置厚度的增幅即减至大约20%,缩水纹出现的机会亦大为减少。由此引伸出使用两条或多条矮的加强筋比使用单一条高的加强筋较为优胜,但当使用多条加强筋时,加强筋之间的距离必须较相接外壁的厚度大。加强筋的形状一般是细而长,加强筋一般的设计图说明设计加强筋的基本原则。留意过厚的加强筋设计容易产生缩水纹、空穴、变形挠曲及夹水纹等问题,亦会加长生产周期,增加生产成本。
机架设计准则
机架设计准则 1、工况要求:即任何机架的设计首先必须保证机器的特定工作要求。例如,保证机架上安装的零部件能顺利运转,机架的外形或内部结构不致有阻碍运动件通过的突起;设置执行某一工况所必需的平台;保证上下料的要求、人工操作的方 便及安全等。 2、刚度要求:在必须保证特定的外形条件下,对机架的主要要求是刚度。如果基础部件的刚性不足,则在工作的重力、夹紧力、摩擦力、惯性力和工作载荷等的作用下,就会产生变形,振动或爬行,而影响产品定位精度、加工精度及其它性能。例如机床的零部件中,床身的刚度则决定了机床的生产率和加工产品的精 度。 3、强度要求:对于一般设备的机架,刚度达到要求,同时也能满足强度的要求 4、稳定性要求:对于细长的或薄壁的受压结构及受弯-压结构存在失稳问题,某些板壳结构也存在失稳问题或局部失稳问题。失稳对结构会产生很大的破坏,设 计时必须校核。 5、美观:目前对机器的要求不仅要能完成特定的工作,还要使外形美观。 6、其它:如散热的要求,防腐蚀及特定环境的要求。 机架设计的一般要求 在满足机架设计准则的前提下,必须根据机架的不同用途和所处环境,考虑下列 各项要求,并有所偏重。 1、机架的重量轻,材料选择合适,成本低。 2、结构合理,便于制造。 3、结构应使机架上的零部件安装、调整、修理和更换都方便。 4、结构设计合理,工艺性好,还应使机架本身的内应力小,由温度变化引起的 变形应力小。 5、抗振性能好。 6、耐腐蚀,使机架结构在服务期限内尽量少修理。 7、有导轨的机架要求机架导轨面受力合理,耐磨性良好。 设计步骤
1、初步确定机架的形状和尺寸。根据设计准则和一般要求,初步确定机架结构 的形状和尺寸,以保证其内外部零件能正常运转。 2、根据机架的制造数量、结构形状及尺寸大小,初定制造工艺。例如非标准设 备单件的机架、机座、可采用焊接代替铸造。 3、分析载荷情况,载荷包括机架上的设备重量、机架本身重量、设备运转的动 载荷等。 4、确定结构的形式,例如采用桁架结构还是板结构等。再参考有关资料,确定 结构的主要参数(即高、宽、板厚与材料等)。 5、画出结构简图。 6、参照类似设备的有关规范、规程,确定本机架结构所允许的挠度和应力。 7、进行计算,确定尺寸。 8、有必要时,进行详细计算并校核或做模型试验,对设计进行修改,确定最终 尺寸。 综上所述:注塑机机架设计要符合机架设计的准则与一般要求,并要注意以下几 点: 1、应根据锁模结构在容模量最大时及射移行程最大的状态确定机架的长度,并兼顾油箱及电机油泵的布局具体确定。根据锁模、射台、油箱、电箱及电机油泵布局确定机架的宽度与高度,高度要考虑人机工程学,适当时候要考虑用高低机 架结构。 2、机架结构的主要构件是梁。梁分纵梁与端梁。注塑机中的梁可以是型材(角钢、槽钢、方通、工字钢、H型钢等),也可以的折弯板材焊接梁,也可以是型材与 折弯板组焊梁。 3、机架结构还有另一主要构件是柱。焊接柱按外形分为实腹柱和格构柱。实腹柱分为型钢实腹柱和钢板实腹柱两种,前者焊缝少,应优先选用。后者适应性强,可按使用要求设计成各种大小尺寸。当腹板的计算高度h与腹板厚度δ之比大于80时,应有横向隔板加强,间距不得大于3h;柱腹外伸自由宽度b不宜超过15t,箱形柱的两腹板间宽度b也不宜超过40t(t为板厚)。 4、梁和柱的连接有铰接和刚性连接两种。以焊接连接为主,很少用螺钉或铆接。 焊接方法可参看有关焊接规范和手册。 5、油箱的设计 油箱在系统中的功能,主要是储油和散热,也起着分离油液中的气体及沉淀物的 作用。
模具设计原则和核心以及注意事项
模具设计原则和核心以及注意事项 一、 开模方向和分型线 每个注塑产品在开始设计时首先要确定其开模方向和分型线,以保证尽可能减少抽芯滑块机构和消除分型线对外观的影响。 1、 开模方向确定后,产品的加强筋、卡扣、凸起等结构尽可能设计成与开模方向一致,以避免抽芯减少拼缝线,延长模具寿命。 2、 开模方向确定后,可选择适当的分型线,避免开模方向存在倒扣,以改善外观及性能。 二 、脱模斜度 1 、适当的脱模斜度可避免产品拉毛(拉花)。光滑表面的脱模斜度应≥0.5度,细皮纹(砂面)表面大于1度,粗皮纹表面大于1.5度。 2 、适当的脱模斜度可避免产品顶伤,如顶白、顶变形、顶破。 3、 深腔结构产品设计时外表面斜度尽量要求大于内表面斜度,以保证注塑时模具型芯不偏位,得到均匀的产品壁厚,并保证产品开口部位的材料强度。 三、 产品壁厚 1 、各种塑料均有一定的壁厚范围,一般0.5~4mm,当壁厚超过4mm时,将引起冷却时间过长,产生缩印等问题,应考虑改变产品结构。
2、壁厚不均会引起表面缩水。 3 、壁厚不均会引起气孔和熔接痕。 四、加强筋 1、 加强筋的合理应用,可增加产品刚性,减少变形。 2、 加强筋的厚度必须≤ (0.5~0.7)T产品壁厚,否则引起表面缩水。 3、 加强筋的单面斜度应大于1.5°,以避免顶伤。 五、圆角 1、 圆角太小可能引起产品应力集中,导致产品开裂。 2、圆角太小可能引起模具型腔应力集中,导致型腔开裂。 3、 设置合理的圆角,还可以改善模具的加工工艺,如型腔可直接用R刀铣加工,而避免低效率的电加工。 4 、不同的圆角可能会引起分型线的移动,应结合实际情况选择不同的圆角或清角。 六、 孔 1 、孔的形状应尽量简单,一般取圆形。 2 、孔的轴向和开模方向一致,可以避免抽芯。
产品部件之设计准则——壁厚篇(1)
壁厚 (Wall Thickness) 基本设计守则 壁厚的大小取决於产品需要承受的外力、是否作为其他零件的支撑、承接柱位的数量、伸出部份的多少以及选用的塑胶材料而定。一般的热塑性塑料壁厚设计应以4mm为限。从经济角度来看,过厚的产品不但增加物料成本,延长生产周期”冷却时间〔,增加生产成本。从产品设计角度来看,过厚的产品增加引致产生空穴”气孔〔的可能性,大大削弱产品的刚性及强度。 最理想的壁厚分布无疑是切面在任何一个地方都是均一的厚度,但为满足功能上的需求以致壁厚有所改变总是无可避免的。在此情形,由厚胶料的地方过渡到薄胶料的地方应尽可能顺滑。太突然的壁厚过渡转变会导致因冷却速度不同和产生乱流而造成尺寸不稳定和表面问题。 对一般热塑性塑料来说,当收缩率”Shrinkage Factor〔低於0.01mm/mm时,产品可容许厚度的改变达;但当收缩率高於0.01mm/mm时,产品壁厚的改变则不应超过。对一般热固性塑料来说,太薄的产品厚度往往引致操作时产品过热,形成废件。此外,纤维填充的热固性塑料於过薄的位置往往形成不够填充物的情况发生。不过,一些容易流动的热固性塑料如环氧树脂”Epoxies〔等,如厚薄均匀,最低的厚度可达0.25mm。 此外,采用固化成型的生产方法时,流道、浇口和部件的设计应使塑料由厚胶料的地方流向薄胶料的地方。这样使模腔内有适当的压力以减少在厚胶料的地方出现缩水及避免模腔不能完全充填的现象。若塑料的流动方向是从薄胶料的地方流向厚胶料的地方,则应采用结构性发泡的生产方法来减低模腔压力。 平面准则 在大部份热融过程操作,包括挤压和固化成 型,均一的壁厚是非常的重要的。厚胶的地 方比旁边薄胶的地方冷却得比较慢,并且在 相接的地方表面在浇口凝固後出现收缩痕。 更甚者引致产生缩水印、热内应力、挠曲部 份歪曲、颜色不同或不同透明度。若厚胶的 地方渐变成薄胶的是无可避免的话,应尽量 设计成渐次的改变,并且在不超过壁厚3:1的 比例下。下图可供叁考。 转角准则 壁厚均一的要诀在转角的地方也同样需要,以免冷却时间不一致。冷却时间长的地方就会有收缩现象,因而发生部件变形和挠曲。此外,尖锐的圆角位通常会导致部件有缺陷及应力集中,尖角的位置亦常在电镀过程後引起不希望的物料聚
结构设计原则之加强筋
结构设计原则之加强筋
加强肋 理想的设计 为了克服壁厚大可能引起的问题,使用是一种可减少壁厚并能增加刚性的有效方法。 一般来说,部件的刚性可用以下方法增强 ?增加壁厚; ?增大弹性模量(如加大增强纤维的含量); ?设计中考虑。 如果设计用的材料不能满足所需刚性,则应选择具有更大弹性模量的材料。简单的方法是增加塑料中增强纤维的含量。但是,在特定壁厚下,这种方法仅能使刚性呈线性增长。更有效的方法是使用经过优化设计的。由于惯性力矩增大,部件的刚性便会增大。在优化的尺寸时,不但要考虑工程设计应当考虑的问题,还应考虑与生产和外观有关的技术问题。 优化的尺寸 大的惯性力矩可很容易地通过设置又厚又高的来实现。但是对热塑性工程塑料,这种方法常会产生制品表面凹痕、内部空洞和翘曲等问题。而且,如果的高度过高,在负荷下结构将有可能膨胀。出于这种考虑,必须在合理比例内保持的 尺寸(见图1)。图1 为确保带的制品容易顶出,必须设计一个适当的脱模锥度(见图2)。 图2
防止材料堆积 对于表面要求非常高的组件,如汽车轮盖,的尺寸是非常重要的。正确的设计可以减少组件形成表面凹痕的可能,以提高组件的质量。的底部的材料积聚在图1所示的圆中。这个圆的大小与的尺寸相关,应该越小越好,这样才能减小或避免凹痕。如果圆太大,可能会形成内部空洞,制品的机械性能将会非常差。减少底部的应力 如果给一个有的组件以负载,则的底部可能会产生应力。在这一部位如果没有圆弧,可能会产生非常高的应力集中(见图3),通常会导致组件的断裂和报废。补救措施是建立一个半径足够大的圆弧(图1),使肋底部建立更好的应力分布。 图3 但如果圆弧半径太大,也会增大上文提及的圆的直径,而导致上文已经提及的问题。 图4 在塑料设计中,十字结构是最好的,因为它能应付许多不同的负荷排列变化(图4)。正确设计的可承受预期应力的十字结构,可以确保在整个制品上的应力均匀分布。在的十字交叉处形成的节点(图5)代表材料的积聚,但可以将节点中心挖空,以防止产生问题。还必须注意,不要在交叉处和组件的边相交的地方形成材料积聚(图6)。
产品的结构设计注意事项(塑胶类)
塑胶结构篇 塑料的外观要求:产品表面应平整、饱满、光滑,过渡自然,不得有碰、划伤以及缩孔等缺陷。产品厚度应均匀一致,无翘曲变形、飞边、毛刺、缺料、水丝、流痕、熔接痕及其它影响性能的注塑缺陷。毛边、浇口应全部清除、修整。产品色泽应均匀一致,表面无明显色差。颜色为本色的制件应与原材料颜色基本一致,且均匀; ?需配颜色的制件应符合色板要求。 ?上、下壳外形尺寸大小不一致,即面刮(面壳大于底壳)或底刮(底壳大于面 ?壳)。可接受面刮<0.15mm,可接受底刮<0.1mm。所以在无法保证零段差时,尽量 ?使产品:面壳>底壳。 ?一般来说,上壳因有较多的按键孔,成型缩水较大,所以缩水率选择较大, ?一般选0.5%,底壳成型缩水较小,所以缩水率选择较小,一般选0.4%。 结构设计的一般原则:力求使制品结构简单,易于成型;壁厚均匀;保证强度和刚度;根据所要求的功能决定其形状尺寸外观及材料,当制品外观要求较高时,应先通过外观造型在设计内部结构。 尽量将制品设计成回转体或对称形状,这种形状结构工艺性好,能承受较大的力,模具设计时易保证温度平衡,制品不以产生翘曲等变形。应考虑塑料的流动性,收缩性及其他特性,在满足使用要求的前提下制件的所有转角尽可能设计成圆角或用圆弧过渡。 塑料件设计要点 开模方向和分型线 每个塑料产品在开始设计时首先要确定其开模方向和分型线,以保证尽可能减少抽芯机构和消除分型线对外观的影响; 开模方向确定后,产品的加强筋、卡扣、凸起等结构尽可能设计成与开模方向一致,以避免抽芯减少拼缝线,延长模具寿命。 脱模斜度 脱模斜度的要点 脱模角的大小是没有一定的准则,多数是凭经验和依照产品的深度来决定。此外,成型的方式,壁厚和塑料的选择也在考虑之列。一般来讲,对模塑产品的任何一个侧壁,都需有一定量的脱模斜度,以便产品从模具中取出。脱模斜度的大小可在0.2°至数度间变化,视周围条件而定,一般以0.5°至1°间比较理想。具体选择脱模斜度时应注意以下几点: a. 取斜度的方向,一般内孔以小端为准,符合图样,斜度由扩大方向取得,外形以大端为准,符合图样,斜度由缩小方向取得。如下图1-1。 b. 凡塑件精度要求高的,应选用较小的脱模斜度。
压铸件结构设计规范
压铸件结构设计 压铸件结构设计是压铸工作的第一步。设计的合理性和工艺适应性将会影响到后续工作的顺利进行,如分型面选择、内浇口开设、推出机构布置、模具结构及制造难易、合金凝固收缩规律、铸件精度保证、缺陷的种类等,都会以压铸件本身工艺性的优劣为前提。 1、压铸件零件设计的注意事项 ⑴、压铸件的设计涉及四个方面的内容: a、即压力铸造对零件形状结构的要求; b、压铸件的工艺性能; c、压铸件的尺寸精度及表面要求; d、压铸件分型面的确定; 压铸件的零件设计是压铸生产技术中的重要部分,设计时必须考虑以下问题:模具分型面的选择、浇口的开设、顶杆位置的选择、铸件的收缩、铸件的尺寸精度保证、铸件内部缺陷的防范、铸孔的有关要求、收缩变形的有关要求以及加工余量的大小等方面; ⑵、压铸件的设计原则是: a、正确选择压铸件的材料; b、合理确定压铸件的尺寸精度; c、尽量使壁厚分布均匀; d、各转角处增加工艺园角,避免尖角。 ⑶、压铸件分类 按使用要求可分为两大类,一类承受较大载荷的零件或有较高相对运动速度的零件,检查的项目有尺寸、表面质量、化学成分、力学性能(抗拉强度、伸长率、硬度);另一类为其它零件,检查的项目有尺寸、表面质量及化学成分。 在设计压铸件时,还应该注意零件应满足压铸的工艺要求。压铸的工艺性从分型面的位置、顶面推杆的位置、铸孔的有关要求、收缩变形的有关要求以及加工余量的大小等方面考虑。合理确定压铸面的分型面,不但能简化压铸型的结构,还能保证铸件的质量。 ⑷、压铸件结构的工艺性: 1)尽量消除铸件内部侧凹,使模具结构简单。 2)尽量使铸件壁厚均匀,可利用筋减少壁厚,减少铸件气孔、缩孔、变形等缺陷。 3)尽量消除铸件上深孔、深腔。因为细小型芯易弯曲、折断,深腔处充填和排气不良。 4)设计的铸件要便于脱模、抽芯。 5)肉厚的均一性是必要的。 6)避免尖角。 7)注意拔模角度。 8)注意产品之公差标注。 9)太厚太薄皆不宜。 10)避免死角倒角(能少则少)。 11)考虑后加工的难易度。 12)尽量减少产品内空洞。 13)避免有半岛式的局部太弱的形状。 14)太长的成形孔,或太长的成形柱皆不宜。 2、压铸件零件设计 ⑴、压铸件的形状结构 a、消除内部侧凹; b、避免或减少抽芯部位; c、避免型芯交叉;合理的压铸件结构不仅能简化压铸型的结构,降低制造成本,同时也改善铸件质量。 ⑵、壁厚 压铸件的壁厚对铸件质量有很大的影响。以铝合金为例,薄壁比厚壁具有更高的强度和良好的致密性。因此,在保证铸件有足够的强度和刚性的条件下,应尽可能减少其壁厚,并保持壁厚均匀一致。