发动机缸体

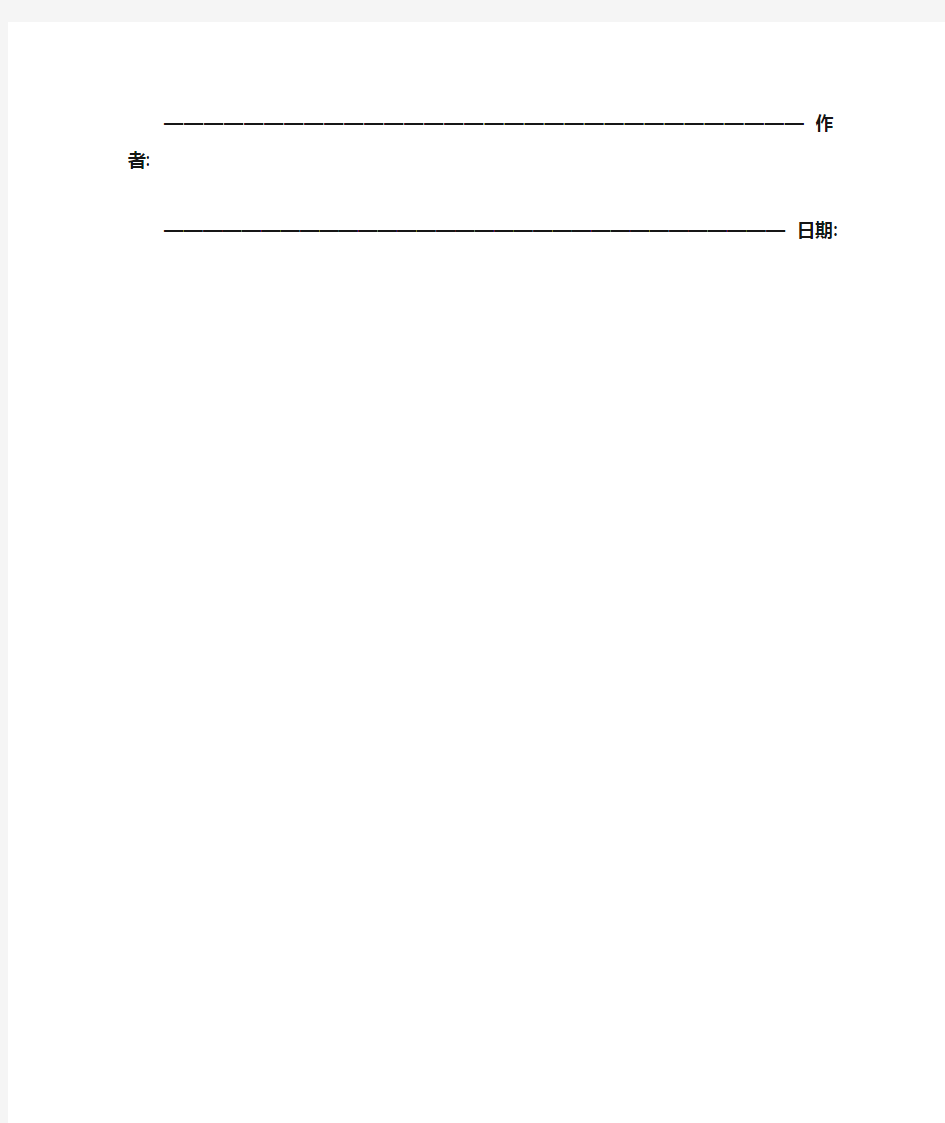
发动机缸体
————————————————————————————————作者: ————————————————————————————————日期:
发动机缸体
[摘要]缸体是汽车发动机乃至汽车中最重要的零件之一,发动机的加工质量直接影响发动机的质量,进而影响到汽车整体的质量,因此发动机缸体的制造加工长期以来一直受到国内外汽车生产企业的重视。[缸体的简单介绍]发动机缸体是发动机的基础零件和骨架,同时又是发动机总装配时的基础零件。缸体的作用是支承和保证活塞、连杆、曲轴等运动部件工作时的准确位置;保证发动机的换气、冷却和润滑;提供各种辅助系统、部件及发动机的安装。汽车发动机的缸体和上曲轴箱常铸成一体,称为缸体——曲轴箱。缸体上部的圆柱形空腔称为气缸,下半部为支承曲轴的曲轴箱,其内腔为曲轴运动的空间。在缸体内部铸有许多加强筋,冷却水套和润滑油道等。根据缸体与油底壳安装平面的位置不同,通常把缸体分为以下三种形式。(1)一般式缸体:其特点是油底壳安装平面和曲轴旋转中心在同一高度。这种缸体的优点是机体高度小,重量轻,结构紧凑,便于加工,曲轴拆装方便;但其缺点是刚度和强度较差(2)龙门式缸体:其特点是油底壳安装平面低于曲轴的旋转中心。它的优点是强度和刚度较好,能承受较大的机械负荷;但其缺点是工艺性较差,结构笨重,加工较困难。(3)隧道式缸体:这种形式的缸体曲轴的主轴承孔为整体式,采用滚动轴承,主轴承孔较大,曲轴从缸体后部装入。其优点是结构紧凑、刚度和强度好,但其缺点是加工精度要求高,工艺性较差,曲轴拆装不方便。为了能够使缸体内表面在高温下正常工作,必须对缸体和缸盖进行适当地冷却。冷却方法有两种,一种是水冷,另一种是风冷。水冷
发动机的缸体周围和缸盖中都加工有冷却水套,并且缸体和缸盖冷却水套相通,冷却水在水套内不断循环,带走部分热量,对缸体和缸盖起冷却作用。现代汽车上基本都采用水冷多缸发动机,对于多缸发动机,气缸的排列形式决定了发动机外型尺寸和结构特点,对发动机机体的刚度和强度也有影响,并关系到汽车的总体布置。按照气缸的排列方式不同,缸体还可以分成单列式、V型和对置式三种。
[缸体的工作条件]缸体通常工作在高温、高载荷、磨损剧烈的条件下,承受较大的压力,受力复杂,同时工作在汽油的沉浸下,工作环境潮湿。
缸体的使用性能要求:缸体的工作条件决定了缸体必须具有高强度、高刚度、高硬度、高耐磨性以及良好的散热性,同时要有很好的密封性、防漏性、减振性等。
[缸体毛坯材料的选择]发动机缸体采用的材料一般是灰铸铁H T150、HT200、HT250,也有采用铸铝或铸钢的。采用灰铸铁可以满足高强度、
高刚度以及高耐磨性的要求,而且工艺性能、减振性、切削加工性能优良,同时成本较低,但是会增加缸体的重量,增加发动机的负担;采用铸钢材料,可以使缸体承受更大的冲击载荷;采用铝合
金材料最大的好处是可以减轻缸体的重量,顺应了汽车轻量化的趋势,因此最近采用铸铝材料的缸体越来越多。每种材料都有自身的特点,优劣共存,我们需要根据不同缸体产品的不同质量要求来确定相应的生产材料。
[毛坯制造方法的选择]铸造、锻压、焊接、粉末冶金和非金属材料成形等方法都可以作为机械零件毛坯的制造方法,但它们的制造成本、生产条件等都有差异,再加上实际生产中零件毛坯生产批量的不同,我们对制造方法的选择必然也会不同,正确的方法是:结合生产实际,综合考虑毛坯的使用要求、生产经济性要求,同时兼顾环境保护,最终达到制造方法与实际生产条件相适应。对于缸体这种形状复杂、尺寸较大、有不规则的外形和内腔、壁厚不均的箱体类零件,通常采用铸造(砂型铸造)的方法,(缸盖制造如
图)
采用铸造的方法不但可以满足缸体的使用性能要求,而且生产成本较低。砂型铸造流程:准备炉料→熔炼金属→浇注→凝固冷却→落砂清理→检验→合格铸件。
[缸体毛坯的技术要求]对非加工面不允许有裂纹、冷隔、疏松、气孔、砂眼等铸造缺陷。缸体毛坯质量对加工的影响:加工余量过大,会增加机床的负荷,影响机床和刀具的使用寿命,成本变高;飞边过大,直接影响刀具使用寿命;由于冷热加工基准不统一,毛坯各部分相互间的偏移会造成机械加工时余量不均匀。
[缸体制造工艺]缸体的工艺特点是:结构、形状复杂;加工的平面、孔多;壁厚不均;加工精度要求高,属于典型的箱体类加工零件。加工平面一般采用刨、铣削等方法加工,加工孔主要采用镗削,加工小孔多用钻削。由于缸体结构复杂,因此如何保证各表面的相对位置精度是加工中的一个重要问题。选择合理的加工工艺基准,直接关系到能否保证零件的加工质量。一般来说,工艺基准可分为粗基准和精基准。粗基准对于上线的毛坯,其粗基准的选择尤为重要,粗基准选择不合理会造成加工余量分布不均匀,加工面偏移,产生废品。在缸体的生产中,我们一般采用侧面为粗基准。精基准对于发动机缸体这种箱体零件来说,一般采用“一面两销”为全线的统一基准。对于较长的自动生产线系统,由于定位销孔在使用过程中的磨损造成定位不准确,因此,将定位销孔分为2~3段使用。在缸体定位销孔的加工中,我们采用以侧面、底面和主轴孔定位,在加工中心上加工。加工阶段的划分缸体需要加工的表面许多,不同表面的加工精度也不同。因此,在
拟定工艺顺序时,要抓住“加工精度高的表面”这个主要矛盾,合理安排工序。安排工艺顺序的原则是:先粗后精,先面后孔,先基准后其它。1)粗加工阶段:在发动机缸体的机械加工过程中,安排粗加工工序,对毛坯全面进行粗加工,切去大部分余量,以保证生产效率。2)半精加工阶段:在发动机缸体的机械加工中,为了保证一些重要表面的加工精度,安排一些半精加工工序,将精度和表面粗糙度要求中等的一些表面加工完成,而对要求较高的表面进行半精加工,为以后的精加工做准备。3)精加工阶段:对精度和表面粗糙度要求高的表面进行加工。4)次要小表面的加工:一些表面(如螺纹孔表面)可以在精加工主要表面后进行,一方面工时对工件变形影响不大,同时废品率也会降低;另外,如果表面加工出现差错时,那么这些小表面也就不必加工了,这样即避免了人力、物力、资金的浪费。但是要注意的是,如果小表面的加工容易造成主要表面损伤的话,那么就应该将小表面加工放在主要表面的精加工之前。5)妥善安排辅助工序:这类工序(如检验工序)在零件粗加工阶段之后、关键工序加工前后零件全部加工完毕后,都要适当安排。对加工阶段进行划分的优点是:一是可以在粗加工之后采取措施消除工件内应力,保证精度;二是将精加工放在后面可以避免在运输过程中损坏工件已加工好的表面;三是先粗加工各表面可以及时发现毛坯缺陷并及时处理,以免工时不必要的浪费。需要注意的是,在粗加工和精加工之前应分别加上预备热处理和最终热处理的工序。
[热处理的作用]对材料进行热处理是改善金属材料性能的一种常见的方法,它能够使材料的组织结构发生变化,从而达到改善加工工艺性能和强化力学性能的目的。对于缸体这种力学性能要求较高的零件,合理安排热处理工序非常重要。
[热处理工序]对于铸铁材料的缸体而言,通常的热处理工艺为:预备热处理(去应力退火+正火+去应力退火)→最终热处理(淬火+高温回火,又称调质处理+表面淬火)预备热处理安排在粗加工阶段之前,其目的是:消除残余内应力,防止工件变形、开裂;改善组织,细化晶粒;调整硬度,改善切削性能。退火工艺规范为:加热温度500~550℃,加热速度60~120℃/h,经一定时间保温后,炉冷到150~220℃出炉空冷。正火工艺规范:将铸件加热到880~920℃,保温1~3h,然后出炉空冷。正火后,为了消除正火时铸件产生的内应力,通常还要进行去应力退火。最终热处理安排在精加工阶段之前,其目的是:使材料具有使用时的所有力学性能。调质处理的工艺规范为:将工件加热至860~900℃,保温后油淬,然后在550~600℃回火2~4h。调质处理后对零件进行适当的表面淬火,这样可以使缸体具有较高的硬度和耐磨性。
参考文献
[1] 中国机械工程学会铸造分会. 铸造工艺手册( 第二版) [M].北京: 机械工业出版社, 2003.
[2] 赵书城 ,《汽车发动机缸体铸造技术》
[3]黄政,《汽车发动机缸体的制造工艺》