【免费下载】冶炼炉渣干法粒化余热回收技术
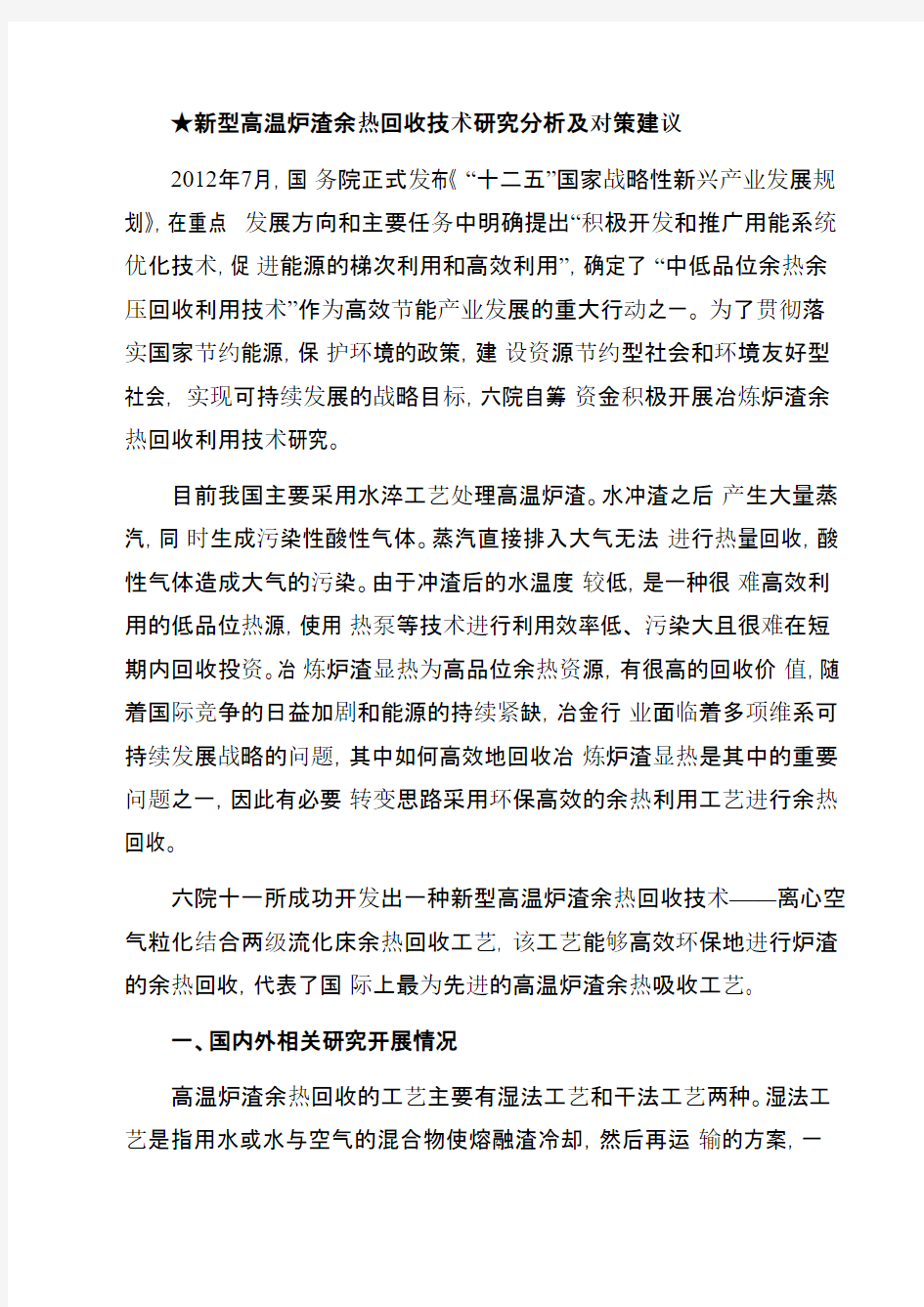
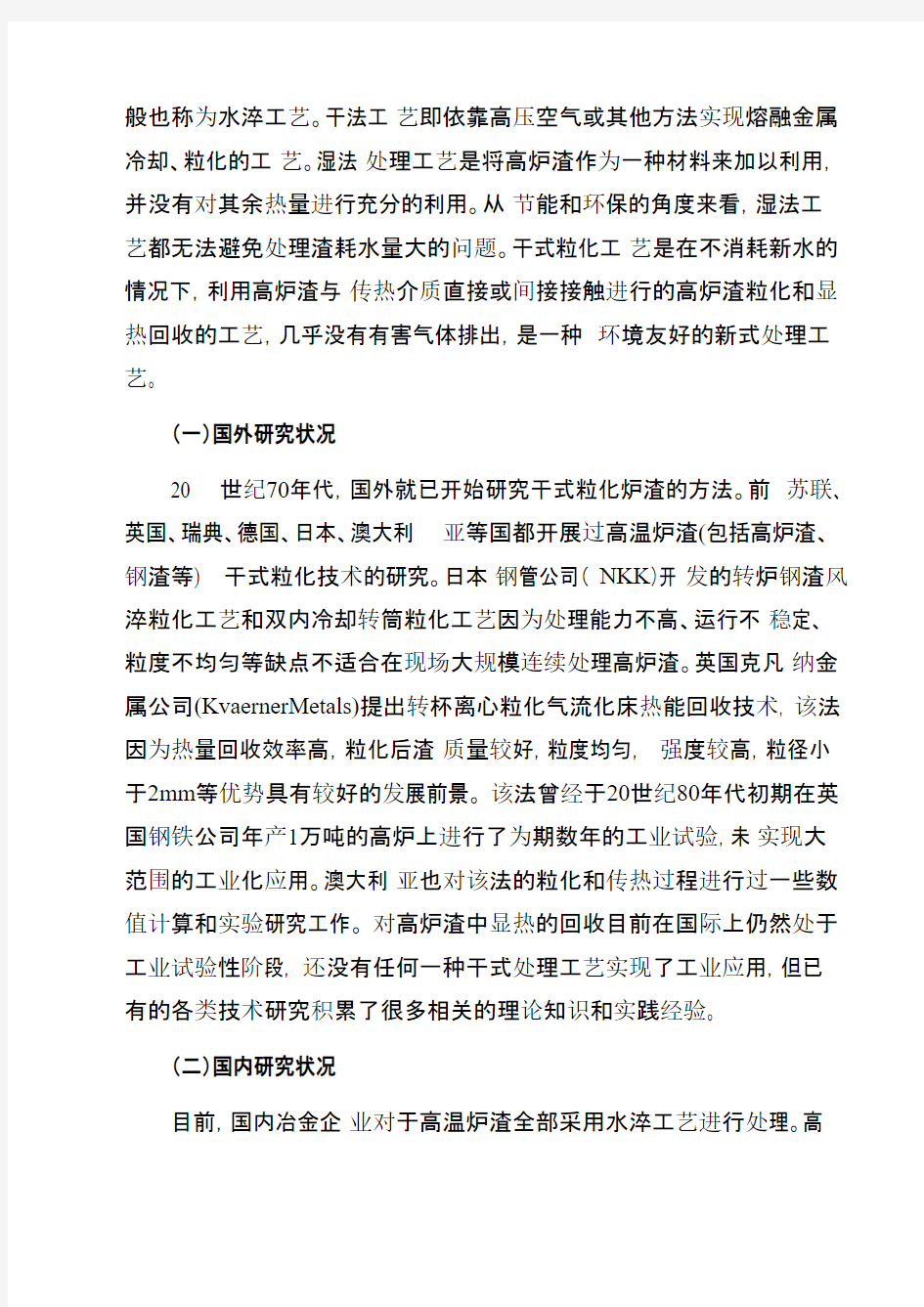
★新型高温炉渣余热回收技术研究分析及对策建议
2012年7月,国务院正式发布《“十二五”国家战略性新兴产业发展规划》,在重点发展方向和主要任务中明确提出“积极开发和推广用能系统优化技术,促进能源的梯次利用和高效利用”,确定了“中低品位余热余压回收利用技术”作为高效节能产业发展的重大行动之一。为了贯彻落实国家节约能源,保护环境的政策,建设资源节约型社会和环境友好型社会,实现可持续发展的战略目标,六院自筹资金积极开展冶炼炉渣余热回收利用技术研究。
目前我国主要采用水淬工艺处理高温炉渣。水冲渣之后产生大量蒸汽,同时生成污染性酸性气体。蒸汽直接排入大气无法进行热量回收,酸性气体造成大气的污染。由于冲渣后的水温度较低,是一种很难高效利用的低品位热源,使用热泵等技术进行利用效率低、污染大且很难在短期内回收投资。冶炼炉渣显热为高品位余热资源,有很高的回收价值,随着国际竞争的日益加剧和能源的持续紧缺,冶金行业面临着多项维系可持续发展战略的问题,其中如何高效地回收冶炼炉渣显热是其中的重要问题之一,因此有必要转变思路采用环保高效的余热利用工艺进行余热回收。
六院十一所成功开发出一种新型高温炉渣余热回收技术——离心空气粒化结合两级流化床余热回收工艺,该工艺能够高效环保地进行炉渣的余热回收,代表了国际上最为先进的高温炉渣余热吸收工艺。
一、国内外相关研究开展情况
高温炉渣余热回收的工艺主要有湿法工艺和干法工艺两种。湿法工艺是指用水或水与空气的混合物使熔融渣冷却,然后再运输的方案,一
般也称为水淬工艺。干法工艺即依靠高压空气或其他方法实现熔融金属冷却、粒化的工艺。湿法处理工艺是将高炉渣作为一种材料来加以利用,并没有对其余热量进行充分的利用。从节能和环保的角度来看,湿法工艺都无法避免处理渣耗水量大的问题。干式粒化工艺是在不消耗新水的情况下,利用高炉渣与传热介质直接或间接接触进行的高炉渣粒化和显热回收的工艺,几乎没有有害气体排出,是一种环境友好的新式处理工艺。
(一)国外研究状况
20 世纪70年代,国外就已开始研究干式粒化炉渣的方法。前苏联、英国、瑞典、德国、日本、澳大利亚等国都开展过高温炉渣(包括高炉渣、钢渣等) 干式粒化技术的研究。日本钢管公司(NKK)开发的转炉钢渣风淬粒化工艺和双内冷却转筒粒化工艺因为处理能力不高、运行不稳定、粒度不均匀等缺点不适合在现场大规模连续处理高炉渣。英国克凡纳金属公司(KvaernerMetals)提出转杯离心粒化气流化床热能回收技术,该法因为热量回收效率高,粒化后渣质量较好,粒度均匀,强度较高,粒径小于2mm等优势具有较好的发展前景。该法曾经于20世纪80年代初期在英国钢铁公司年产1万吨的高炉上进行了为期数年的工业试验,未实现大范围的工业化应用。澳大利亚也对该法的粒化和传热过程进行过一些数值计算和实验研究工作。对高炉渣中显热的回收目前在国际上仍然处于工业试验性阶段,还没有任何一种干式处理工艺实现了工业应用,但已有的各类技术研究积累了很多相关的理论知识和实践经验。
(二)国内研究状况
目前,国内冶金企业对于高温炉渣全部采用水淬工艺进行处理。高
炉渣水淬工艺亦即水渣处理工艺,就是将熔融状态的高炉渣置于水中急速冷却,限制其结晶,并使其在热应力作用下发生粒化。水淬后得到沙粒状的粒化渣,绝大部分为非晶态,是优良的水泥原料。在国内水淬渣处理系统中,水渣比在(8~15):1,高炉渣带走的热量约占高炉总能耗的16%左右,经过各种水淬处理工艺回收的仅为炉渣总热量的10%,其余热量变为水蒸气放入大气,造成资源的极大浪费。国内在干式粒化技术的研究刚刚起步,凤淬法因为在渣粒和空气之间完成的直接换热方式,热回收效率较高是其重要优势,但对炉渣流动性要求较高,处理率有限制。离心粒化法不仅可以回收大量的热能,改善高炉操作,给企业带来可观的经济效益,而且在环保方面的潜力价值是不容低估的,是高炉渣处理利用的发展趋势。在国内,东北大学、青岛理工大学、钢铁研究院对离心粒化法进行了理论和实验研究工作,但是实验所用炉渣流量较小,与生产实际中熔渣流量差距较大,而且未对粒化后渣粒的热量回收工作进行研究。
(三)水淬工艺的缺陷
1.炉渣余热没有回收。用水淬法对1400℃的高炉渣进行降温,会产生大量低压蒸汽以及热水(约80℃),除了极少数企业将热水能量回收用于冬季供暖外,其余能量白白浪费掉了。
2.大量的新水消耗。以钢铁生产过程为例,炼铁工序消耗新水占新水总耗量的1/3左右,是消耗新水最多的工序。在炼铁工序中,冲渣消耗的新水又占到本工序新水消耗总量的50%以上,冲制1吨水渣消耗新水
0.8~1.2吨。
3.产生大气污染。水淬过程中会产生大量的气态硫化物SO2和H2S,
促进酸雨的形成。即使是最环保的水渣工艺——环保型INBA法,吨渣排放硫化物也有5g。
4.额外消耗大量能量。使用水淬法进行急冷得到的固态高炉渣含水量较高,粉磨时必须烘干,需要额外消耗大量能量。
由于存在根本性的缺陷,水淬处理工艺只是适用于特定阶段的过渡性工艺,随着近年来国家对节能减排的重视程度不断提高,高炉渣处理方法必然向着更为节能、环保的方向发展,其中干式粒化工艺就是发展重点方向之一。
二、六院高温炉渣余热回收技术研究的基本情况和进展
2011年6月,十一所与金川集团有限公司签订高温炉渣余热回收工
艺研究课题,拟通过研究开发高效的余热回收工艺,为实现我国整个冶炼行业废渣处理及余热回收工业化应用奠定基础。
(一)十一所进行的工艺流程设计
该余热回收系统工艺流程为第一步采用离心粒化技术将液态的熔渣粒化成大小均匀且粒径为3mm左右的颗粒,根据实际生产中熔渣的流量通过调整粒化装置的关键参数,得到所需粒度范围的高附加值渣粒;第
二步粒化后的颗粒与来自流化床的冷空气直接接触进行换热,在处理过程中颗粒与空气接触面积较大,热交换较为充分,可使得热量回收率大大提高,热空气将炉渣释放出的热量带走出口温度可达600~700℃,到余热锅炉产出蒸汽加以利用。考虑系统的热空气中可能存在酸性气,在系统运行过程中酸性气的浓度需要进行实时测量,如果酸性气浓度不超标则进行循环使用,当酸性气浓度达到处理浓度时转入酸性气脱除装置,保证系统运行过程中的环保性。
余热回收系统原理图
(以沉降电炉和闪速炉为例)
该项目实施分三个阶段,第一阶段进行炉渣基本特性研究和雾化过程研究,第二阶段进行炉渣换热过程和渣粒流态化过程研究,第三阶段进行小型工业化试验研究及产业化建设。
(二)技术优势
炉渣干式粒化工艺应在运行成本和粒化渣质量两方面的指标达到与水渣工艺相当的水平,才能具有竞争力。它必须满足5个条件:能使炉渣粒化到需要的尺寸,粒化过程中炉渣损失的能量少,粒化过程消耗的能量少,能够有效地回收热量,处理后的粒化渣可以有效利用。
离心空气粒化结合两级流化床的余热回收工艺具有单体设备简单、布置紧凑、处理能力大、操作参数少的优点。通过改变转杯的转速即可调
整粒化程度,可获得尺寸小、球形度好、玻璃化程度高的均质高附加值成
品渣。粒化室内高温渣粒可以采用与空气直接接触的方法吸热,根据国外研制经验,两级流化方法可以使高温炉渣持有的热量较彻底地转化为空气含有的热量,即高效地将炉渣显热转变成为洁净的热能。余热吸收后形成的高温空气可以作为洁净的热源进行多种方法的二次利用,如:
高温空气可以通入余热锅炉进行换热从而产出高压蒸汽,蒸汽直接利用或者推动汽轮机发电;高温空气可以预热进入冶炼炉的助燃空气或者直接进入炉膛参与燃烧,节省冶炼过程燃料的消耗量并提高炉膛内温度。在初始冷却速度足够大的条件下渣粒中玻璃体含量较高,同时由于离心粒化产生的渣粒直径小且分布均匀,渣粒可以直接作为水泥生产的原料,提高产品的附加值。
三、技术综合效益分析
“十二五”期间,我国的高温炉渣产量约23.2亿吨,其中蕴含显热1.35亿吨标煤。若采用离心粒化结合两级流化床余热回收技术,则可以将其中60%的热量进行回收,并可大幅减少酸性气体的排放。该技术既节约
能源,又可保护环境,是资源综合利用的典范,可为企业带来可观的经济效益。如果此项关键技术得到突破,将为该技术的系统工程应用提供直接理论及技术支撑,最终在余热回收领域开拓新技术,形成市场前景较好的产业化项目。
离心空气粒化结合两级流化床余热回收工艺如果能够成功完成技术开发,并逐步完成工业化,未来将替代高温炉渣水冲渣处理工艺。应用此项技术可为该企业节约大量资金和能源,以金川集团公司冶炼厂沉降电炉、闪速炉和铜冶炼炉的炉渣量进行估算,分析企业年节能和环保效益。
采用离心空气粒化工艺后在处理过程中不喷水,每年节省70万吨的
冲渣水,按每吨0.5元,每年可节省水费35万元。基本没有硫化物的排放,对于闪速炉和顶吹炉每年可节省用于中和炉渣中的硫形成的酸水的工业碱液合计1000吨,每吨价格700元,共70万元。若在1350~150 ℃的范围内回收炉渣热量,因成分不同炉渣的放热量约为1500kJ/kg 。若有60 %的热量被回收并有效利用,则实际回收热量0.9GJ/t ,每年可以节约能量折合标煤约6万吨(每吨标准煤为29.27GJ )。整个工艺系统主要耗能装置包括:电机、风机和泵,根据估算可得到该部分能耗占可回收能量的份额小于10%。随着国家环保政策的日益严格,若能将该项目成功开发,推广应用到整个钢铁、冶金企业行业,可对生产过程产生的高温炉渣进行高效环保的热量回收,能够为企业节约大量的资金和能源,效益明显,同时符合国家所倡导的节能环保政策,根据我国目前钢铁和有色金属的产量和增长率,估算可节约的能源具体数据如下表所示。冶金行业综合能效表20112012201320142015总和粗钢产量(亿吨) 6.70007.10207.52817.97988.458637.7685生铁产量(亿吨) 6.2000 6.82007.50208.25229.077437.8516
有色金属产量(亿吨)0.33000.34980.37080.39300.4166 1.8602总产量(亿吨)
13.2314.271815.400916.625017.952677.4804炉渣产量(亿吨) 3.969 4.2815 4.6203 4.9875 5.385823.2441通过管线敷设技术,不仅可以解决吊顶层配置不规范问题,而且可保障各类管路习题到对全部高中资料试卷电气设备,在安装过程中以及安装结束后进行高中资料试卷调整试验;通电检查所有设备高中资料试卷相互作用与相互关系,根据生产工艺高中资料试卷要求,对电气设备进行空载与带负荷下高中资料试卷调控试验;对设备进行电力保护装置调试技术,电力保护高中资料试卷配置技术是指机组在进行继电保护高中资料试卷总体配置时,需要在最大限度内来
显热折算标煤(亿吨)0.23020.24830.26800.28930.3124 1.3482节能60%(亿吨)0.13810.14900.16080.17360.18740.8089推广率20%(亿吨)0.02760.02980.03220.03470.03750.1618
据统计,2010年底,我国粗钢产量为6.27亿吨,占全球粗钢总产量的
44.3%,同比增长9.3%。“十二五”期间我国钢铁工业的发展将由“高速
粗放”型转为“减速精细”型,按较为乐观的8.5亿吨产量峰值计算,年均增速只有6%,较“十一五”期间降低一半左右。钢渣是炼钢过程中的必然副产物,其排出量约为粗钢产量的15%~20%,钢渣目前的利用率只有大约36%,用作建筑材料、烧结溶剂和高炉炼铁熔剂、铁水预处理渣剂等,但都只是一种末端处理方法。
高炉渣是冶炼生铁时产生的废渣,也是冶金行业产生数量最多的一种废渣。2010年,我国生铁产量5.9亿吨,同比增长8.5%,“十二五”期间,增长率继续保持在10%左右。按平均每吨生铁产生0.3t渣来计算,高炉渣产量为1.77亿吨。高炉渣的出炉温度在1400~1500℃,每吨渣含
(1260~1880)x103kJ的显热,相当于60kg标准煤的热值。由于高炉熔渣温度高,产量很大,如果得不到合理的处理和利用,不但是对二次能源及环境会造成很大的污染。
有色金属产量稳步增长,2010年,包括铝、铜、铅、锌等在内的十种有色金属工业产量达到3135万吨,同比增长20.4%,产量消费量占世界三分之一。其中尤以铝为典型,产能超过2100万,增速为16.7%。氧化铝综合能耗为632.4千克标煤/吨,比上年下降3.7%;铜冶炼综合能耗为360.3千克标煤/吨,比上年下降2.4%;铅冶炼综合能耗为453.5千克标煤/吨,比上
年下降4.4%;电解锌综合能耗为946.6千克标煤/吨,比上年下降1.1%。四大主要有色金属节能减排都取得显著成效,这是有色金属行业实现可持续发展的有力保障。按照有色金属行业“十二五”规划草案,到2015年,十种有色金属(铜、铝、铅、锌、镍、锡、锑、镁、海绵钛、汞)产量控制在4100万吨以内,则“十二五”期间有色金属的平均增长率为6%左右。在有色金属“十二五”规划中将明确主要品种产量:粗铜冶炼控制在500万吨以内,电解铜控制在650-700万吨之间,氧化铝控制在410万吨以内,电解铝控制在200万吨以内,铅冶炼控制在550万吨以内,锌冶炼控制在670万吨以内。
按照余热发电的功率计算,年产百万吨渣的冶炼厂可以发电9000万千瓦时,“十二五”我国炉渣总产量为23.2亿吨,如果全部用来余热发电则可以产出2000亿千瓦时电量。如果将余热发电推广到全行业的25%,平均每年发电500亿千瓦时。
四、相关对策建议
1.该技术是通过火箭发动机的高效换热技术转化来的,前期项目研发的经费主要通过自筹解决,关键技术突破后还需要继续开展系统研究工作,希望上级能够给予经费支持。
2.该技术符合国家战略新兴产业政策需求,但对于钢铁和有色金属企业没有直接的吸引力,特别是对已建成的冶炼炉,改造还是需要一定投入。希望上级机关能够呼吁政府部门制定相应标准,引导企业提高环保意识,同时指导企业与研究所进行技术对接,让技术真正转化为生产力,建设资源节约型社会和环境友好型社会,实现可持续发展的战略目标。
(办公室、十一所)
#炉渣利用技术 炉渣利用工艺
炉渣利用技术炉渣利用工艺 1 用于流化床锅炉的链带式排渣控制冷却器 2 高炉水碎炉渣或其粒度调整物的防凝结剂及防凝结方法 3 高炉铁水渣铁分离装置 4 烟道灰、炉渣活化剂 5 高效利用工业炉熔渣显热的新一步法矿棉技术 6 一种电炉炼钢吹氧喷粉氧燃助熔及造泡沫渣工艺 7 钢包炉用脱氧造渣剂 8 用气、水反冲高炉水渣滤层的方法 9 旋风炉炉渣生产岩棉热衔接工艺及所采用的补热炉 10 用于液体炉渣脱铬和/或脱镍的方法 11 一种电渣炉控制系统 12 用锅炉废渣灰制水硬性凝固剂方法 13 粉煤灰炉渣砼小型空心砌块 14 炼钢电弧炉泡沫渣控制方法 15 危险废弃物及医疗垃圾处理用的溶渣焚烧炉及工艺方法 16 用于氧化处理炼钢厂炉渣的方法及所得到的LD渣 17 一种控制转炉炉底上涨溅渣的方法 18 一种用镍熔炼炉渣和钢渣的混合渣炼铁的方法 19 型煤炉正块缓漏卸双向分离排渣器 20 转炉出钢用挡渣锥 21 一种冶金炉风口、渣口表面强化的方法 22 用含钛高炉渣制备光催化材料的方法 23 一种以炉渣为基料的合成材料及其生产工艺 24 轻质隔声炉渣混凝土建筑板材 25 炉渣冷却机 26 利用沸腾炉渣制造泡沫型隔热防水保温材料 27 利用电厂炉渣生产水泥的方法 28 粒化高炉矿渣水泥砂浆 29 防御液态排渣炉析铁熔蚀的金属陶瓷涂层 30 转炉溅渣护炉方法 31 造气炉渣运用煅烧石灰的方法 32 一种石灰质碳化煤球(棒)造气炉渣的新用途 33 直流电弧电渣加热钢包炉及其控制方法 34 一种利用石灰质碳化煤球造气炉渣生产的路面砖及其方法 35 用于沸腾炉的层燃式灰渣燃烬冷却床 36 用浓盐酸高温高压处理锅炉灰渣浸取其中三氧化二铝的综合利用方法 37 稀土精矿渣电弧炉冶炼稀土中间合金 38 稀土精矿球团(或块)矿热炉制备稀土精矿渣和含铌磷铁 39 低温干馏、炉渣再燃、刮板传动式锅炉 40 用喷粉方法处理熔渣生产高价值炉渣制品 41 促进粒状炉渣脱水用的混合剂和使用方法
冶炼烟气余热回收—余热发电技术
冶炼烟气余热回收—余热发电技术 一、所属行业:有色金属行业 二、技术名称:冶炼烟气余热回收—余热发电技术 三、适用范围:有色金属、钢铁、水泥等行业 四、技术内容: 1.技术原理 利用强制循环余热锅炉回收冶炼烟气余热,生产中压饱和蒸汽,配套饱和蒸汽汽轮机组,发电机组抽汽供热,实现供热、电联产,最大限度提高余热蒸汽利用效率。 2.关键技术 国内自行设计制造的耐高温腐蚀性、粘结性冶炼烟气余热锅炉。 工艺流程 原水→脱盐→除氧→余热锅炉→汽轮发电机组→凝结水→余热锅炉。 五、技术指标: 1.节能技术相关生产环节的能耗现状: 有色行业冶炼高温烟气余热损耗占较大比率,有色系统余热锅炉应用率不高,而配套余热发电站的企业更少,余热利用水平较低。 2.技术指标: 余热锅炉蒸汽量5-100t/h,工作压力3.0-5.0MPa,蒸汽温度一般为饱和温度(236-265℃)。汽轮发电机入口压力3.0-5.0MPa,抽汽压力0.5-1.0MPa,排气压力 0.008-0.03 MPa,电站容量0.5-15MW。 六、技术鉴定及应用情况: 本技术已在云南铜业股份有限公司等多家企业投入商业运行,尚没有进行过技术鉴定。 在云南铜业股份有限公司、云南冶金集团驰宏锌锗股份公司、云南锡业股份有限公司、白银有色金属公司等多家企业投入运行,取得良好经济效益。 七、典型用户及投资效益: 应用典型案例一:云南铜业股份有限公司 余热电站规模9470kW,汽轮发电机组1台,另配套ISA炉余热锅炉1台,转炉余热锅炉2台、阳极炉余热锅炉2台。总蒸汽量55-85t/h,蒸汽压力4.2MPa,蒸汽温度253℃。
建设期为1年,节能技改投资额为6232万元(不包括余热锅炉系统投资)。年发电量达到68752MWh,年供热量573772GJ。年创产值约为2539万元,新增利润总额1531万元,投资回收期4.8年。 应用典型案例二:云南锡业股份有限公司 国产汽轮发电机组1台,功率6000kW,电压6kV,进汽压力2.5MPa,蒸汽量30t/h;余热锅炉3台。建设期为1年,余热发电站投资为2456万元(不包括余热锅炉系统投资)。年发电量达到39600MWh,年创产值约为1660万元,新增利润总额880万元。投资回收期3年。 八、推广前景和节能潜力: 本技术可用于有色行业的各个大、中型冶炼厂,其余热锅炉蒸汽量大于5t/h,压力大于1.0MPa。也可用于钢铁、水泥等相关行业。 “十一五”期间,该技术在大、中型企业推广率可达85%以上,需要总投入约为2-3亿元,可取得总节能量444100吨标煤/年(按中等容量估算)。 九、推广措施及建议: 1.在项目立项和实施过程中,将冶炼烟气余热回收-余热发电同步立项,同步实施余热利用也应热电联产,提高余热利用效率。 2.政府部门给予优惠贷款、提高上网电价。 3.鼓励企业发展余热电站,取消某些地方存在的限制上网的规定。
炉渣的的回收与再利用分析
炉渣的回收与综合利用分析 姓名:杜国震学号: 08L0101203 学院:理工学院专业:化学工程与工艺 班级:化工L082 指导教师:刘老师 2011--11--13
炉渣的的回收与再利用分析 摘要:许多炉渣都是完全燃烧的灰烬与不完全燃烧的煤块组成的混合物。它既不能用作燃料,也不能用作水泥的填料。造成环境的污染和浪费。选矿工艺将这部分分成可燃的炉渣与不可燃的炉渣,不论可燃与不可燃的都将能回收与再利用是我的文章要论述的内容。 关键字:炉渣回收再利用 1.炉渣的产生及现状。 工业生产中的炉渣一般不经过煤洗的原煤直接作燃料产生,也有经过洗过的灰分较高的中煤。这样除了造成严重的空气和粉尘污染外,大量的煤渣也造成了,环境的污染和煤矿资源的浪费,产生了固体废弃物。有来自中国矿业大学学报,报道每一百万吨燃烧,有超过二十万吨的炉渣,由于燃烧不完全煤渣中含有一定的可燃物质。如果不经过回收再利用而是当做废渣堆弃或是填充低地,就造成里环境的严重污染和资源的巨大浪费,因此回收与利用部分炉渣也就成了挖掘潜能措施,同时也成为了保护环境的有效手段。同时,也带来了一样的经济效益。可见回收与再次利用燃烧不完全的煤渣的意义与重要性。不单单是环境的要求也是保护资源的迫切要求。 就我国煤炭工业来说,由于国内的洗选能力与技术不足,不得不烧原煤的现状真是个遗憾。 2.炉渣的成分及用途 炉渣又称为熔渣。根据冶金过程的不同,炉渣可分为熔炼渣,精炼渣,混合渣。根据炉渣性质又分为碱性渣,酸性渣和中性渣。许多炉渣有重要的作用,如高炉渣可做水泥的原料,高磷渣可做肥料,含有钒,钛的炉渣可作为提取钒,钛的原料。还有些炉渣可以制炉渣水泥,炉渣砖,炉渣玻璃等。煤在锅炉燃烧室里的熔融物,由煤灰组成,可以作为砖,瓦的原料。 3.高炉渣的产生及回收与利用 高炉渣是冶炼生铁时从高炉中排除的废物,当炉温达到1400—1600时,炉料熔融,矿石中的脉石,焦炭中的煤灰和助溶剂和其他不能进入生铁中的杂质形成以硅酸盐,铝酸盐为主的浮
典型有色金属冶炼烟气余热回收利用研究
典型有色金属冶炼烟气余热回收利用研究 发表时间:2017-11-17T10:51:16.700Z 来源:《基层建设》2017年第24期作者:陈伍平 [导读] 摘要:近年来,典型有色金属冶炼烟气余热回收利用研究得到了业内的广泛关注,研究其相关课题有着重要意义。本文首先对相关内容做了概述,分析了有色金属冶炼烟气余热回收处理必要性,并结合相关实践经验,分别从多个角度与方面就有色金属冶炼烟气余热回收处理技术的应用展开了研究,阐述了个人对此的几点看法与认识,望有助于相关工作的实践。 新疆众和股份有限公司新疆维吾尔自治区 830013 摘要:近年来,典型有色金属冶炼烟气余热回收利用研究得到了业内的广泛关注,研究其相关课题有着重要意义。本文首先对相关内容做了概述,分析了有色金属冶炼烟气余热回收处理必要性,并结合相关实践经验,分别从多个角度与方面就有色金属冶炼烟气余热回收处理技术的应用展开了研究,阐述了个人对此的几点看法与认识,望有助于相关工作的实践。 关键词:有色金属冶炼;烟气;余热;回收 1 前言 如何在有色金属冶炼过程中,实现其烟气余热的回收利用,对于更好地开展有色金属冶炼工作意义重大。毋庸置疑,在当前的有色金属冶炼过程中,受多方面因素的制约与影响,烟气余热回收利用工作还存在着多方面的问题,因此探讨其回收利用技术十分关键。 2 概述 锅炉余热资源的回收利用是节约能源的重要措施,工业锅炉排烟余热所占锅炉热量的比重较大,尤其对于燃气锅炉。在天然气锅炉热损失中,主要为排烟热损失。通常燃气锅炉的排烟温度较高,一般在160~240℃。烟气中含大量过热态水蒸气,是烟气热量的主要携带者,约为55%~75%。天然气锅炉尾部增设烟气冷凝换热装置,可回收利用排烟显热与烟气凝结潜热,并减少有害气体排放量,烟气冷凝水可经简单处理后回收利用。 烟气凝结换热包括水蒸气凝结和烟气中的不凝结气体对流换热2个过程。烟气在流经换热器时,由于水蒸气的凝结造成了烟气的组成成分发生变化,使得换热过程比较复杂。当冷凝换热器的表面温度低于水蒸气露点温度时,烟气中水蒸气释放潜热后,开始凝结,换热器表面形成凝结液膜包围,同时在该液膜外还存在一层不凝结气体。 3 对有色金属冶炼烟气余热回收处理必要性 在我国,电能有72%都是来自燃煤发电。我们日常生活中每多用一度电,发电厂就要燃烧更多的煤进行发电。煤的燃烧会产生一氧化氮、一氧化硫等有毒气体,这些有毒气体排到空气中导致空气固体粉粒增多,污染空气。再者煤的再生产需要历经一个世纪以上的时间,因此现存的煤量一旦同完,我们的日常生活、工业发展等都会受到影响。 3.1国家高度重视工业锅炉节能 在最近90年里,很多资本主义国家已经完成本国的工业建设,世界上的煤资源被资本主义国家的工业建设消耗得所剩无几。我国是全球处于正在发展的国家中最大的发展国,在工业化的道路上飞速前进,发展是建立在消耗大量能源的基础上。据调查显示,我国在2009年煤总量比2008年少了6.8%,能源消耗位居世界第三,消耗速度极其迅速。按这样的发展形势下去,我国煤资源很快就会消耗完。节能行动迫在眉睫。国家颁布条令,必须加强节约能源的工作,科学进行生产发展,降低能源消耗,节约能源,特别是针对锅炉锅炉烟气余热回收,并且颁布相应对策,将节能作为基本国策去落实。全国各省各市高度重视,积极落实节能减排工作。 3.2工业锅炉消耗能源巨大 全国人民都在为节能减排共同努力:随手关灯、出门坐公车、低碳烹饪、水资源循环利用、家用电器的节能使用等等。为缓解我国能源紧张的局势做出一份贡献,努力创造一个节约能源的新型社会。但是工业的锅炉生产方面存在很大的浪费和污染问题,这些问题亟待解决。工业锅炉的尾气温度很高,工业锅炉在燃煤运作的时候,锅炉后边会排除大量浓烟,烟的温度高至250-400℃,热能源高。大多工厂并不注重对浓烟的循环使用,而是直接任其排到空气中,不仅造成浪费还对大气造成污染。一般重型CFB锅炉的旁边都设置筑铁管道及防止腐蚀的节煤机器,用以帮助气体燃烧和对锅炉内的水进行加热。但煤等燃烧物质的化学成分中有硫,在燃烧的过程中会有二氧化硫、一氧化硫等有毒气体产生,和空气中的水分子进行反应成硫酸。当硫酸的温度比CFB底部铁壁温度高时,硫酸就由气态形式变成液态。时间久了就会对锅炉造成侵蚀,导致漏洞等现象。锅炉就会潜在危险因素。现在大多使用的工业CFB锅炉都选择升高烟气热度,减少硫酸对锅炉的侵蚀。但这又会造成新的问题,高温度的烟气转换成热能散播在空气中,造成污染、浪费。因此必须对锅炉尾部烟气余热进行回收,只有节能才能保障我国工业持续正常发展,因为工业一旦瘫痪,整个社会秩序就无法正常运行 4 有色金属冶炼烟气余热回收处理技术应用 烟气余热是燃料燃烧后被释放到空气中,未能得到充分利用的热能,也是能量资源中的一种。余热形式有很多种,比如烟气高温热量、烟气中的水分和氮氢气反应产生的化学能量、热能反应产生的余热、燃料残渣热能等等。而余热回收技术的作用就是一用科学技术,回收这些热量,降低能源浪费。同时锅炉烟气余热回收处理技术是一种节能对策。通过对整个锅炉烟气余热的排放循环过程进行研究,运用科学技术,结合经济条件和环保知识,充分考虑资源消耗、结构材料、使用过程等方面的问题,创造出最可行的锅炉烟气回收方案。从而达到加高效率、降低浪费、节约能源的作用。 4.1锅炉烟道中安装节能设备 锅炉燃烧排出的烟气大部分都是水分,含量占烟气所有化学物质成分的19%。若将其直接排放到空气中,会造成很大的能源浪费。同时燃料在锅炉中燃烧,通过锅炉尾部排放出一氧化硫、一氧化氮等污染环境的有毒气体。解决这些问题的办法很多,可以通过在锅炉烟道中安装节能器对其加之利用。节能器将这些化学物质同水蒸气结合在一起,吸收这些污染物,减少排放量,从而达到环保作用。降低能源消耗的同时能够减少工业投资,既环保又经济。 4.2安装冷凝装置回收锅炉烟气余热 大部分的锅炉排放出的烟气气温高达172~260℃,烟气的水分温度过高,导致沸腾,无法凝聚为流动的水状释放热量。材料燃烧散发出来的热量最低值就是锅炉的工作效率,材料燃烧能够释放热能的最高值和最低值之间存在一定差距,这个差距以锅炉烟气余热的形式被消耗浪费。根据调查发现,普通的锅炉热能功率在79%~86%之间上下浮动,造成约21%~14%的浪费。安装冷凝装置,能将锅炉排放烟
高炉渣与转炉渣综合利用
高炉渣与转炉渣综合利用 摘要:转炉炼钢过程中的主要副产品是转炉渣,目前我国转炉渣的利用率仅为10%。为提高转炉渣的利用率,应按照分析成分、制定利用方案、综合处理、分级利用 4 个主要步骤,根据当地的实际情况,建立不同适应性的阶梯利用方式,以实现最好的社会效益、环境效益和经济效益。介绍了当前国内外高炉渣综合回收与利用现状,对比分析了高炉渣各种处理工艺的优点和不足,展望了高炉渣回收与利用的发展趋势。 关键词:普通高炉渣;含钛高炉渣;综合利用转炉渣;综合处理;利用;分析 1高炉渣处理工艺与综合利用 高炉渣是冶炼生铁过程中从高炉中排出的副产品,是我国现阶段最主要的冶炼废渣。在20世纪70年代以前,一直作为工业废弃物堆放。随着钢铁工业的发展,各种高炉渣的堆积量日益增大,高炉渣的堆积不仅对环境造成了严重污染,也是一种资源的严重浪费,随着世界范围资源的日益贫乏,对高炉渣进行综合利用,变废为宝已刻不容缓。 1.1高炉渣的化学成分 高炉渣有普通高炉渣和含钛高炉渣。普通高炉渣的化学成分与普通硅酸盐水泥类似,主要为CaO、MgO、SiO2、Al2O3和MnO。含钛高炉渣中除含有上述物质外,还含有大量的TiO2。见表1 表 1 高炉渣的化学成分 高炉渣的处理工艺可分为水淬粒化工艺、干式粒化工艺和化学粒化工艺。在我国工业生产中,主要以水淬粒化工艺作为高炉渣的处理工艺,但水渣处理工艺存在以下问题 : 新水消耗量大、熔渣余热没有回收、系统维护工作量大、冲渣产生的二氧化硫和硫化氢等气态硫化物带来空气污染。粉磨时,水渣必须烘干,要消耗大量能源。因此,利用干法将高炉渣粒化作为水泥原料,同时高效利用炉渣显热,减少对环境的污染,是高炉渣处理的发展趋势。 1.2国内外高炉渣处理工艺概况 1.2.1 水淬粒化工艺 水淬粒化工艺就是将熔融状态的高炉渣置于水中急速冷却,限制其结晶,并使其在热应力作用下发生粒化。水淬后得到沙粒状的粒化渣,绝大部分为非晶态。其主要方法有:底滤法、因巴法、图拉法、拉萨法等。水淬粒化工艺处理的高炉渣,玻璃质(非晶体)含量超过95%,可以用作硅酸盐水泥的部分替代品,生产普通酸盐水泥。但此法不可避免地释放出大
冷凝燃气锅炉烟气余热回收利用研究
冷凝燃气锅炉烟气余热回收利用研究 摘要近些年来,随着经济社会的快速发展,国家对环境保护、节约资源、能源综合利用等提出了较高的要求。在北京市集中供热系统中,燃气锅炉得到了广泛的应用,而燃气锅炉所排放的烟气具有较高的温度,可以采取有效措施来降低烟气排放温度,并实现对烟气余热的有效回收,其不仅可以使燃气锅炉的供热效率得到有效提升,而且还可以达到比较理想的节能效果。本文将会以北京市某热源厂为例来对冷凝燃气锅炉烟气余热回收利用技术进行探究。 关键词冷凝燃气锅炉;烟气余热;回收利用 如今,随着燃气锅炉在供热行业中的广泛应用,与燃煤锅炉相比具有热效率更高、污染更小等特点。在锅炉中天然气燃烧过程中,将会有大概92%左右能量转化为热量、7%左右为排烟热损失、1%左右表面散热损失掉。因此,做好烟气余热回收利用工作就显得尤为重要。通常情况下,很大一部分烟气中的余热存在于水蒸气中,在回收显热、降低烟气温度的同时,会有效回收烟气中的水蒸气潜热,从而实现烟气全热的正回收。烟气余热回收利用主要是以天然气为驱动源,借助回收型热泵机组,就能够使锅炉排烟从80℃降至30℃,从而使大量的水蒸气冷凝潜热被回收,这样既可以达到节省燃气锅炉燃气耗量的目的,而且还可以降低PM2.5雾霾形成物的排放,达到节能减排的双重效果。 1 冷凝燃气锅炉烟气余热回收利用技术 1.1 利用换热器烟气余热回收技术 在烟气余热回收利用技术中,换热器是比较常用的设备,对其进行科学、合理的选择尤为关键,根据换热方式的差异,可以将烟气余热回收利用方式划分为直接接触式换热型、间接接触式换热型[1]。 (1)直接接触式换热器。直接接触式换热通常是以直接接触的方式来实现两种介质相互传热传质的过程。通常情况可以根据接触结构的不同划分为折流盘型、多孔板鼓泡型和填料型如图1所示。因为我国供热供回水温度相对比较高,导致直接接触式换热型换热器在烟气余热回收利用过程中并未得到广泛的应用。(2)间接接触式换热器。间接换热通常是指在被壁面分隔来的空间里冷热介质可以实现独立流动,并通过壁面来使实现冷热介质的换热。在烟气余热回收利用技术中,常用的间接接触式换热器有热管换热器、翅片管换热器和板式换热器. 1.2 利用热泵回收烟气余热技术 在燃气锅炉中,天然气燃烧过程中所产生的烟气露点在55—65℃之间,在进行回收烟气冷凝余热阶段,一般要求供热回水温度在烟气露点温度范围以内。一旦供热回水温度超过了烟气露点温度,则需要借助热泵回收烟气冷凝余热来实现预热供热回水。目前,在烟气余热回收利用过程中,吸收式热泵回收烟气余热
余热回收利用
余热回收利用(S-CO2)动力循环-应用海运 业 摘要 船舶动力的主要来源是柴油机,它已经发展成为一种高效的发电装置,用于推进和辅助用途。然而,只有小于50%的燃料能源转化为有用的工作,其余的损失。这是公认的,约占总能量的转换在30%型柴油机是在排拒天然气。最近授权的EEDI [ 1 ]系统大型船舶归功于任何可回收的能源设计的船。而一些节能的设备正在酝酿,利用风能和太阳能发电研究中,它被公认为从发动机废气和冷却水的余热回收仍然可以利用,以产生能量,从而提高能源效率的工厂。从废气中回收热能的方法之一是将热量传递给一个能量回收的介质。在大型船舶上,所用的是水和蒸汽,从而产生了我用于加热燃料油或用于涡轮机的电能生产。本文提出了一种替代流体(超临界二氧化碳)作为一种手段,通过一个碳回收的能量闭环循环燃气轮机(布雷顿循环)它明显在较低的温度和无腐蚀性,无毒,不易燃,热稳定。在超临界状态下,S-CO2已高密度的结果,如涡轮机的部件的尺寸减小。超临界二氧化碳气体涡轮机可以在一个高的循环热效率,即使在温和的温度下产生的功率对550℃。周期可以在宽范围的操作压力为20。在一个典型的发动机安装在近海供应船的排气气体的能量回收量的案例研究,提出了理论计算的热量进行的UT的功率可由发动机的超临界CO2气轮机厂产生的废气和提取 . 关键词:余热,S-CO2布雷顿循环,水, 一、引言 今天的大多数船舶使用柴油发动机的推进和电力生产。通常被认为具有实际应用潜力的热排阻式柴油机为了浪费热量恢复是排气和外套冷却液。热通常是从一个以蒸汽的形式大型海轮主推进发动机的废气是最优选的介质用于燃料和货物加热,包括国内服务所需的加热。冷却水的热量通常以新鲜水的形式回收。从辅助余热回收辅助发动机,直到最近,没有考虑经济实用的除的情况下,大型客运船舶或船舶电力推进系统的操作。国际海事组织和国际海
余热回收设计方法
恒昌焦化 焦炉烟气余热回收项目 设计方案 唐山德业环保设备有限公司 二〇一二年三月 一、焦化工艺概述: 备煤车间送来的配合煤装入煤塔,装煤车按作业计划从煤塔取煤,经计量后装入炭化室内。煤料在炭化室内经过一个结焦周期的高温干馏制成焦炭并产生荒煤气。 炭化室内的焦炭成熟后,用推焦车推出,经拦焦车导入熄焦车内,并由电机车牵引熄焦车到熄焦塔内进行喷水熄焦。熄焦后的焦炭卸至凉焦台上,冷却一定时间后送往筛焦工段,经筛分按级别贮存待运。 煤在炭化室干馏过程中产生的荒煤气汇集到炭化室顶部空间,经过上升管、桥管进入集气管。约800℃左右的荒煤气在桥管内被氨水喷洒冷却至84℃左右。荒煤气中的焦油等
同时被冷凝下来。煤气和冷凝下来的焦油等同氨水一起经过吸煤气管送入煤气净化车间。 焦炉加热用的焦炉煤气,由外部管道架空引入。焦炉煤气经预热后送到焦炉地下室,通过下喷管把煤气送入燃烧室立火道底部与由废气交换开闭器进入的空气汇合燃烧。燃烧后的废气经过立火道顶部跨越孔进入下降气流的立火道,再经蓄热室,又格子赚把废气的部分显热回收后,经过小烟道、废气交换开闭器、分烟道、总烟道、烟囱排入大气。 对于其中经总烟道进入烟囱热烟气的仍有较大的余热回收价值。 二、余热回收工艺流程图 技术方案如下:该系统由热管蒸气发生器、软水预热器、汽包、上升管、下降管、外连管路和控制仪表等组成,并且互相独立。 主要技术特点: 1、地下烟道开孔技术:如何实现地下主烟道在焦炉正常行产情况下在线开孔,是本项目成功实施的第一关键。我公司根据多次地下烟道的开孔经验,成功总结出一套行之有效施工方案。 地下烟道路截面尺寸如上图所示。
烟气余热回收技术方案样本
烟气余热回收技术 方案
烟气余热回收利用改造项目 技术方案 ***节能科技有限公司 二O一二年
一、运行现状 锅炉房配备2.1MW锅炉2台(一用一备),供热面积5万m2;**炉配备2.1MW锅炉2台(一用一备),供热面积4.5万m2。经监测,**锅炉房2台锅炉正常运行排烟温度在150--170℃,平均热效率在89%,**锅炉房2台锅炉正常运行排烟温度在160-180℃,平均热效率在88%,(标准应不高于160℃)。锅炉系统运行进出水温差较小,排烟热损失较大,同时影响锅炉热效率的提高,回收利用潜力明显。 二、技术介绍 烟气冷凝回收利用技术是国家第一批特种设备节能技术推荐目录中的成熟技术。有着显著的节能效益。主要原理:1m3天然气燃烧后会放出9450kcal的热量,其中显热为8500kcal,水蒸气含有的热量(潜热)为950kcal。对于传统燃气锅炉可利用的热能就是8500kcal的显热,供热行业中常规计算天然气热值一般以8500kcal/nm3为基础计算。这样,天然气的实际总发热量9450kcal与天然气的显热8500kcal比例关系以百分数表示就为:111%,其中显热部分占100%,潜热部分占11%,因此对于传统燃气锅炉来说还是有很多热量白白浪费掉。 普通天然气锅炉的排烟温度一般在120--250℃,这些烟气含有8%--15%的显热和11%的水蒸气潜热。加装烟气冷凝器的主要
目的就是经过冷凝器把烟气中的水蒸气变成凝结水,最大限度地回收烟气中含有的潜热和显热,使回收热量后排烟温度可降至100℃左右,同时烟气冷却后产生的凝结水得到及时有效地排出(1 nm3天然气完全燃烧后,可产生1.66kg水),而且大大减少了co2、co、nox等有害物质向大气的排放,起到了明显的节能、降耗、减排及保护锅炉设备的作用。从而达到节能增效的目的。 三、改造方案 3.1、设备选型 烟气余热回收器选用瑞典爱瑞科(AIREC)板式烟气热回收器。 瑞典AIREC公司是世界上唯一一家 钎焊式模块化非对称流量板式换热器的 专业生产制造商,凭借独到的设计理 念,雄厚的产品开发能力和多年行业丰 富的实践经验使AIREC成为在非对称流量换热领域的真正领导者。 irCross21由多块板片重叠冲压在一起,在真空和高温的环境下,板片用铜或镍焊接在一起,具有很高的机械强度,更大的传热面积,更高的效率,更轻便小巧。AIREC经过继承CBE(钎焊式换热器)的技术特点,独特的换热器设计板纹,气体/液体应用
炉渣处置与应用
垃圾焚烧发电炉渣处置与应用 ●垃圾焚烧灰渣的现状 目前,随着政府对生活垃圾处理减量化、无害化和资源化的加强管理,生活垃圾处理已经成为城市管理和公共服务的重要组成部分,根据中国国情和相关技术,生活垃圾焚烧处理无疑成为目前最好的垃圾处理方式。焚烧灰渣是城市垃圾焚烧过程中一种必然的副产物,如何处理好灰渣,是当前生活垃圾焚烧处理的一大问题。 垃圾焚烧产生的灰渣包括从焚烧炉的底灰(Bottom Ash,BA),由烟气净化产生的空气污染控制残渣(Air Pollution Control Residues,APCR)两种。主要是不可燃的无机物以及部分未燃尽的可燃有机物。根据垃圾组成的不同,灰渣的数量一般为垃圾焚烧前总重量的5%-20%。灰渣特别是飞灰中含有一定量的有害物质,若重金属未经处理直接排放,将会污染土壤和地下水,对环境造成危害。另一方面,由于灰渣中含有一定数量的铁、铜、锌、铬等重金属物质,有回收利用价值,故又可作为一种资源开发利用。因此,焚烧灰渣既有它的污染性,又有其资源特性。焚烧灰渣的处理是城市垃圾焚烧工艺的一个必不可少的组成部分。 ●炉渣 1.炉渣的组成 底灰(即炉渣)是灰渣的主要部分,呈黑褐色,大约占灰渣总质量的80%-90%。炉渣含水率10.5%~19.0%,热灼减率1.4%~3.5%,低热灼减率反映出其良好的焚烧效果。底灰是由熔渣、玻璃、陶瓷类物
质碎片、铁和其他金属、及其他一些不可燃物质,以及没有燃烧完全的有机物所组成的不均匀混合物。大颗粒炉渣(>20mm)以陶瓷/砖块和铁为主,两种物质的质量百分比随着粒径的减小而减小;小颗粒炉渣(<20mm)则主要为熔渣和玻璃其含量随着粒径的减小而增多,这主要是由于这些物质的物理性质和在炉排中移动时所受的撞击力不同而造成的。 因焚烧 1t生活垃圾约产生 200~250kg 炉渣,以日处理量为1200t的重庆同兴垃圾焚烧发电2厂为例,1年约产生8~11万t 左右的炉渣。 2.炉渣的分拣工艺 炉渣中铁的总含量在5%~8%,目前国内的炉渣分拣主要是分拣炉渣中的铁。 炉排中燃尽的炉渣掉落到除渣机中,通过水的降温,液压式除渣机将冷却后的炉渣沥干后送入皮带输送机,在皮带输送机的转换端头加装多级除铁器,利用磁铁将金属铁分拣出来,为进一步提高分拣效果,工厂中一般在炉渣输送过程中配置振动装置和破碎装置,加大分拣力度。 3.炉渣的资源化利用 3.1炉渣的性质 炉渣粒径分布主要集中在 2~ 50mm的范围内(占61.1%~77.2%),基本符合道路建材(骨料、级配碎石或级配砾石等)的级配要求。炉渣溶解盐量较低,仅为 0.8%~1.0%,因此炉渣处理处置时因溶解盐污染地下水的可能性较小。炉渣pH 缓冲能力较强,初始 pH 值(蒸馏水浸出,液固比为5:1)在11.5以上,能有效抑制重金属的浸出[2]。
电炉烟气余热回收装置及应用
电炉烟气余热回收装置及应用 发表时间:2015-02-10T10:15:21.547Z 来源:《科学与技术》2014年第12期下供稿作者:付继刚[导读] 电炉烟气余热回收装置的回收,完全符合国家“十二五”规划关于“节能减排、余热回收”的指导方针。其在钢铁厂的成功应用 中冶华天工程技术有限公司付继刚摘要:本文介绍了电炉烟气余热回收装置的发展现状、系统组成、工艺流程、热管的传热原理及特点等以及电炉烟气余热回收装置在国内某钢厂的实际应用情况。 关键词:电炉;热管;余热回收1 前言随着经济社会发展,资源短缺与环境恶化问题日益显现,资源与环境问题已成为全球共同关注的问题。专家指出经济发展与资源、环境相协调,科技进步是最佳的解决方案。企业通过技术创新,走节约型企业发展新路,提高了企业的生命力,实现了资源节约与环境友好,促进了经济社会的和谐发展。 在电炉冶炼过程中产生的含尘烟气最高温度可达1300℃,其携带的热量约为电炉输入总能量的10%,如这部分烟气的余热不予以回收,则造成热量的巨大浪费。 目前国内多数钢厂均采用水冷烟道的方式冷却烟气。电炉烟气从炉盖第四孔抽出,经过水冷弯头、水冷滑套加上吸入大量空气,然后进入二次燃烧沉降室,进入水冷烟道后,再进入强制通风冷却器冷却后,烟气温度降至约300℃,最后和来自电炉狗屋、大屋顶罩温度约60℃的二次烟气相混合,混合以后的烟气温度低于150℃,直接进入布袋除尘器除尘,达标后经风机、烟囱直接排空。电炉烟气的水冷烟道冷却方式,冷却水温度升高只有3~4℃,不但没有回收到烟气中的大量高温显热,需要大量循环,而且消耗了大量电能。 2 系统组成及工艺流程2.1 系统组成整个余热回收系统设备包括余热回收本体、汽包、自动控制系统、除氧器、蓄热器、取样器(给水、炉水、蒸汽)、软水箱、加药器、输灰系统、清灰系统、汽水管路及阀门管件、支撑钢结构及平台爬梯等。 其中余热回收本体包括:中压蒸发器、中压省煤器、低压蒸发器共三组受热面以及中压汽包、低压汽包、蓄热器。 余热回收设备采取立式布置,分成受热部分和公用部分。 热管换热器分成热管联箱、热管支架、和灰斗等组件。灰斗位于换热管正下方。 公用部分分成三层设置,均为钢结构。一层布置出灰装置;二层布置中压蒸发器(共4 组)、中压省煤器、低压蒸发器(共2 组);三层布置中压汽包、低压汽包。 水处理间布置中压给水泵、软水泵,软水箱、汽水取样分析装置和锅内磷酸盐加药装置。 2.2 工艺流程高温烟气从电炉炉顶(第四孔)抽出,经水冷烟道,在绝热燃烧沉降室(烟气在燃烧沉降室一方面充分燃烧,同时大颗粒灰尘沉积在沉降室底部)充分燃烧,然后烟气继续流经高温烟道,混风后温度降至约850℃,再经过热管蒸汽发生器和热管省煤器后混风烟气温度降至约150℃,与二次烟气混合送至除尘系统净化达标后排入大气(见图1)。 图1 电炉烟气余热回收工艺流程图2.3 热管的传热原理及特点2.3.1 热管的传热原理将一根封闭的管壳抽成真空,内部充装一定比例的液体工作介质(工质),即构成了热管。热管放在热源部分的称之为蒸发段(热端),放在冷却部分的称之为冷凝段(冷端)。在管内压差作用下,汽体携带潜热由蒸发段流到冷凝段,把热量传递给管外的冷流体,放出凝结潜热,管内工质又由汽体凝为液体,在重力作用下,又回到蒸发段,继续吸热汽化。如此周而复始,将热量不断地由热流体传给冷流体。 2.3.2 热管的特点(1)极高的导热性:金属、非金属材料本身的导热速率取决于材料的导热系数、温度梯度。以金属银为例,其值为429W/m·K。经测定,随管内工质的不同,热管的传热系数可以达到106 W/m·K,是银的数千倍。故热管又有超导体之称。 (2)优良的等温性:由于热管内的传热过程是相变过程,而且工质的纯度很高,因此热管内蒸汽温度基本上保持恒温,经测定:热管两端的温差不超过5℃,与其它传热元件相比,热管具有良好的等温性能。一根直径12.7mm,长1000mm 的紫铜棒,两端温差100℃时传输30W 的热量;而一根同样直径和长度的热管传输100W 的热量,两端温差只需几度。 (3)适应温度范围广:热管能适应的温度范围与热管的具体结构、采用的工作流体及热管的环境工作温度有关。按照热管管内工作温度区分,热管可分为低温热管(-273~0℃)、常温热管( 0~250℃)、中温热管( 250~450℃)、高温热管(450~1000℃)等[1]。 3 电炉烟气余热回收装置的实际应用国内某钢厂一期新建1 座100t 电炉炼钢连铸车间,年产钢水72.5×104t,连铸坯63×104t,铸锭7×104t。为节能降耗,减少吨钢能耗指标,提高全厂循环经济效益,与之配套新建1 套电炉汽化冷却烟气余热回收装置。 3.1 电炉工艺原始数据电炉公称容量100t,平均出钢量100t,最大出钢量120t,铁水兑入率35%,冶炼周期56min,年作业时间300天。电炉第四孔炉气参数:炉气设计流量87000m3/h,炉气设计温度:max 1600℃。 3.2 余热回收系统主要技术指标余热回收系统参数:额定烟气量348000m3/h,烟道入口额定烟气温度1300℃。氧化初期烟气最高温度为850℃,热管余热回收设备出口烟气温度≤150℃,设备进出口烟气压损1.2~1.5kPa,除氧器工作压力0.03MPa,汽包工作压力1.6MPa,外送蒸汽压力0.8~1.2MPa,冶炼周期余热回收平均蒸汽流量12t/h。 4 结束语电炉烟气余热回收装置的回收,完全符合国家“十二五”规划关于“节能减排、余热回收”的指导方针。其在钢铁厂的成功应用,能降低国内电炉炼钢的吨钢能耗指标,为企业及社会带来切实的利益,为国内电炉炼钢进一步开展综合利用,提高企业的经济效益,开拓了一条新途径。
《铜冶炼炉渣回收铜》国家标准
《铜冶炼炉渣回收铜》国家标准 编制说明 铜陵有色金属集团控股有限公司 2010年8月
《铜冶炼炉渣回收铜》国家标准编制说明 1、任务来源 根据中色协综字[2010]015号文件,关于下达2009年第二批有色金属国家、行业标准制(修)订项目计划通知,《铜冶炼炉渣回收铜》由铜陵有色金属集团控股有限公司负责起草,参加起草单位大冶有色金属集团控股有限公司。负责起草单位接到通知后立即成立标准编制小组。经过半年的相关准备,制定出本讨论稿。 2、铜冶炼炉渣回收铜产品简介 目前国内铜冶炼所采用的主要是熔炼和吹炼二道炼铜工艺,以往第一道工艺所产生的熔炼渣由于含铜量较低基本上作为废料丢弃,也有部分作为建筑行业添加剂销售。第二道工艺所产生的吹炼渣由于含铜量相对较高,有的厂家返回上道工序使用,有的采用选矿富集再利用。 由于近年来铜价较高,不少厂家对含铜量较低熔炼渣在投入和产出比进行了测算;同时,随着选矿回收技术的提高,各冶炼厂纷纷上马选矿厂回收熔炼渣中铜金属。 无论是熔炼渣还是吹炼渣所回收的铜,与井下和地表开采的铜矿物所选的铜精矿相比除含硫品位较低和粒度较细外,其性质基本相同,各冶炼厂都是把该产品与铜精矿配料使用。 3、标准编制前期工作 在编制标准期间,首先,进行了相关信息和资料的搜集。标准编制小组于今年6月至7月,先后前往云南铜业公司、大冶有色金属控
股公司、江西铜业公司、金川有色金属公司、中条山有色金属集团公司、祥光铜业公司、铜陵有色稀贵金属公司、铜陵有色金口岭矿业公司、铜陵有色天马山矿业公司进行实地考察调研,收集了大量的相关数据和资料,并取样进行了分析。 通过调研,基本掌握国内铜冶炼炉渣回收铜的生产和需求厂家的情况,覆盖面达到90%以上,应当说具有广泛的代表性。具体收集和分析的相关数据见附表。 4、标准编制原则 4.1本标准格式按照GB/T1.1-2009最新版本要求编写。 4.2本标准参考YS/T 318-2007《铜精矿》标准进行编写。 4.3本标准编制遵循“先进性、实用性、统一性、规范性”的原则,使标准制定具有可操作性。 4.4本标准充分考虑了使用单位的意见和建议。 5、标准中主要内容确定 5.1关于标准名称 标准的名称有三个可采用:“铜冶炼炉渣回收铜”、“铜冶炼炉渣回收铜精矿”、“铜冶炼炉渣渣精矿”,我们建议采用“铜冶炼炉渣回收铜”作为该产品的标准名称。该产品名称确定是为了区别于井下或地表开采铜矿物所选的铜精矿,来源于铜冶炼中。 5.2关于产品分类 根据调研所收集和取样分析的资料,按照精矿含铜品位高低不同确定为三个品级,三级品含铜品位不小于15%,一级品含铜品位不小
烟气余热回收装置的利用(2021年)
Enhance the initiative and predictability of work safety, take precautions, and comprehensively solve the problems of work safety. (安全管理) 单位:___________________ 姓名:___________________ 日期:___________________ 烟气余热回收装置的利用(2021 年)
烟气余热回收装置的利用(2021年)导语:根据时代发展的要求,转变观念,开拓创新,统筹规划,增强对安全生产工作的主动性和预见性,做到未雨绸缪,综合解决安全生产问题。文档可用作电子存档或实体印刷,使用时请详细阅读条款。 [摘要]文章主要介绍锅炉排烟余热回收的必要性和利用方向,当今国内外烟气回收装置的应用情况,从设计角度提出设置烟气余热回收装置(烟气冷却器)需要考虑的问题,并列举工程设计方案及其预期的节能效果。 [关键词]烟气余热回收;低温腐蚀;节能 [作者简介]梁著文,广东省电力设计研究院,广东广州,510000 [中图分类号]TM621.2[文献标识码]A[文章编号]1007-7723(2010)10-0111-0003 一、引言 在火电厂的运行中,煤炭燃烧及各种用能设备、热能换热设备产生了大量的余热,然而这些能量多数都被浪费了。近些年来,在国家大力倡导“节能减排”能源利用政策的大环境下,国内某些电厂成功地设计安装了余热回收利用装置,给电厂带来很好的经济效益。 对火力发电厂讲,锅炉热损失中最大的是排烟热损失。对小型锅
冶炼炉渣干法粒化余热回收技术
★新型高温炉渣余热回收技术研究分析及对策建议 2012年7月,国务院正式发布《“十二五”国家战略性新兴产业发展规划》,在重点发展方向和主要任务中明确提出“积极开发和推广用能系统优化技术,促进能源的梯次利用和高效利用”,确定了“中低品位余热余压回收利用技术”作为高效节能产业发展的重大行动之一。为了贯彻落实国家节约能源,保护环境的政策,建设资源节约型社会和环境友好型社会,实现可持续发展的战略目标,六院自筹资金积极开展冶炼炉渣余热回收利用技术研究。 目前我国主要采用水淬工艺处理高温炉渣。水冲渣之后产生大量蒸汽,同时生成污染性酸性气体。蒸汽直接排入大气无法进行热量回收,酸性气体造成大气的污染。由于冲渣后的水温度较低,是一种很难高效利用的低品位热源,使用热泵等技术进行利用效率低、污染大且很难在短期内回收投资。冶炼炉渣显热为高品位余热资源,有很高的回收价值,随着国际竞争的日益加剧和能源的持续紧缺,冶金行业面临着多项维系可持续发展战略的问题,其中如何高效地回收冶炼炉渣显热是其中的重要问题之一,因此有必要转变思路采用环保高效的余热利用工艺进行余热回收。 六院十一所成功开发出一种新型高温炉渣余热回收技术——离心空气粒化结合两级流化床余热回收工艺,该工艺能够高效环保地进行炉渣的余热回收,代表了国际上最为先进的高温炉渣余热吸收工艺。 一、国内外相关研究开展情况 高温炉渣余热回收的工艺主要有湿法工艺和干法工艺两种。湿法工艺是指用水或水与空气的混合物使熔融渣冷却,然后再运输的方案,一
般也称为水淬工艺。干法工艺即依靠高压空气或其他方法实现熔融金属冷却、粒化的工艺。湿法处理工艺是将高炉渣作为一种材料来加以利用,并没有对其余热量进行充分的利用。从节能和环保的角度来看,湿法工艺都无法避免处理渣耗水量大的问题。干式粒化工艺是在不消耗新水的情况下,利用高炉渣与传热介质直接或间接接触进行的高炉渣粒化和显热回收的工艺,几乎没有有害气体排出,是一种环境友好的新式处理工艺。 (一)国外研究状况 20 世纪70年代,国外就已开始研究干式粒化炉渣的方法。前苏联、英国、瑞典、德国、日本、澳大利亚等国都开展过高温炉渣(包括高炉渣、钢渣等) 干式粒化技术的研究。日本钢管公司(NKK)开发的转炉钢渣风淬粒化工艺和双内冷却转筒粒化工艺因为处理能力不高、运行不稳定、粒度不均匀等缺点不适合在现场大规模连续处理高炉渣。英国克凡纳金属公司(KvaernerMetals)提出转杯离心粒化气流化床热能回收技术,该法因为热量回收效率高,粒化后渣质量较好,粒度均匀,强度较高,粒径小于2mm等优势具有较好的发展前景。该法曾经于20世纪80年代初期在英国钢铁公司年产1万吨的高炉上进行了为期数年的工业试验,未实现大范围的工业化应用。澳大利亚也对该法的粒化和传热过程进行过一些数值计算和实验研究工作。对高炉渣中显热的回收目前在国际上仍然处于工业试验性阶段,还没有任何一种干式处理工艺实现了工业应用,但已有的各类技术研究积累了很多相关的理论知识和实践经验。 (二)国内研究状况 目前,国内冶金企业对于高温炉渣全部采用水淬工艺进行处理。高
炉渣废物处理与应用
炉渣废物处理与应用 关键词:炉渣城市生活垃圾炉渣的处理与综合利用 摘要:焚烧法处理城市生活垃圾的特点是减量化效果显著,体积可减少90%,但仍有20%~30%的质量留在了焚烧灰渣中。焚烧灰渣主要包括飞灰和炉渣,飞灰因其可浸出重金属含量高,且含有二噁英等有机污染物,属于危险废物。炉渣是灰渣的主要部分,占80%左右,在我国是属于没有毒性的一般废物,可直接进行填埋或作建筑材料加以利用。随着垃圾焚烧工艺在我国应用越来越广泛和对污染控制的愈加严格,焚烧炉渣内重金属的活性及在资源化利用过程中的环境安全性应引起足够重视。近年来,我国在垃圾焚烧处理方面已积累了一定的经验,对焚烧工艺和焚烧过程产生的二次污染物也做了大量的研究工作. 正文:炉渣与飞灰这两种焚烧灰渣,不仅在数量上差别很大,而且性质也有显著差异,炉渣中可浸出的重金属的量明显低于飞灰,且在标准范围之内。因此,城市生活垃圾焚烧炉渣不在欧盟委员会规定的有害废物之列,而城市生活垃圾焚烧飞灰被欧盟委员会列为19.01.03号和19.01.07号废物(R.bI么efizetal.,2000)。日本1992年修订《废物处置和公共清扫法》规定新建的垃圾焚烧炉须分别收集飞灰和炉渣(KyUng一JinHong,加oo)。生活垃圾焚烧飞灰在比利时也被认为是有害物质(.P、傲nHeerk,2000)。因此,应该将炉渣从飞灰中分离出来以便于利用炉渣和处理飞灰;将余热回收灰和控制空气污染残余物一起来管理。目前,英国、德国、法国、荷兰、丹麦、
加拿大以及日本等国大部分的生活垃圾焚烧厂,其炉渣和飞灰都是分别收集、处理和处置的:而在美国,炉渣和飞灰是混合收集、处理和处置的,因此被称作混合灰渣。我国《生活垃圾焚烧污染控制标准》(GB18485一2001)明确规定“焚烧炉渣与除尘设备收集的焚烧飞灰应分别收集、贮存和运输,焚烧炉渣按一般固体物处理,焚烧飞灰应按危险废物处理”。生活垃圾焚烧炉渣的处理是一个重要的环境生态问题。我国,炉渣属于一般废物,可直接填埋或作建材利用。但是,由于焚烧的垃圾组成复杂,炉渣中可能含有多种重金属、无机盐类物质,如铅、锡、铬、锌、铜、汞、镍、硒、砷等,在炉渣填埋或利用过程中有害成分会浸出而污染环境(0.Hjelm,ar1996)。因为包括土壤酸性、酸雨、充满COZ的水等都会把不可溶的重金属氢氧化物转化成为易溶的碳酸盐,甚至是含水碳酸盐。Dugenest等人(1999)的研究发现焚烧炉渣的TCLP浸出毒性测试中Pb、Cd超出有害废弃物限定标准。Pb、Zn、Cu的浸出成为炉渣资源化利用的潜在威胁(J.M.Chimenosetal,2000)。欧盟标准委员会第12920条法规规定城市生活垃圾焚烧灰渣如果不进行前处理,将不能填埋或资源化利用(H.A.确nderSlootetal.,2001)。欧美等发达国家早己开始采用卫生填埋方式来处理焚烧炉渣,以避免其中含有的可溶有害成分进入土壤。然而,由于卫生填埋的维护费用极高,这样进而增加了整个焚烧过程的费用,因此这种方法在我国现阶段是不可行的。炉渣引起的环境污染问题是其不能直接填埋的主要原因。另外,填埋场地急剧减少的客观现实也限制了焚烧炉渣的填埋处理。焚烧炉渣成分复杂,且含