Removed_100吨电炉及精炼炉除尘方案

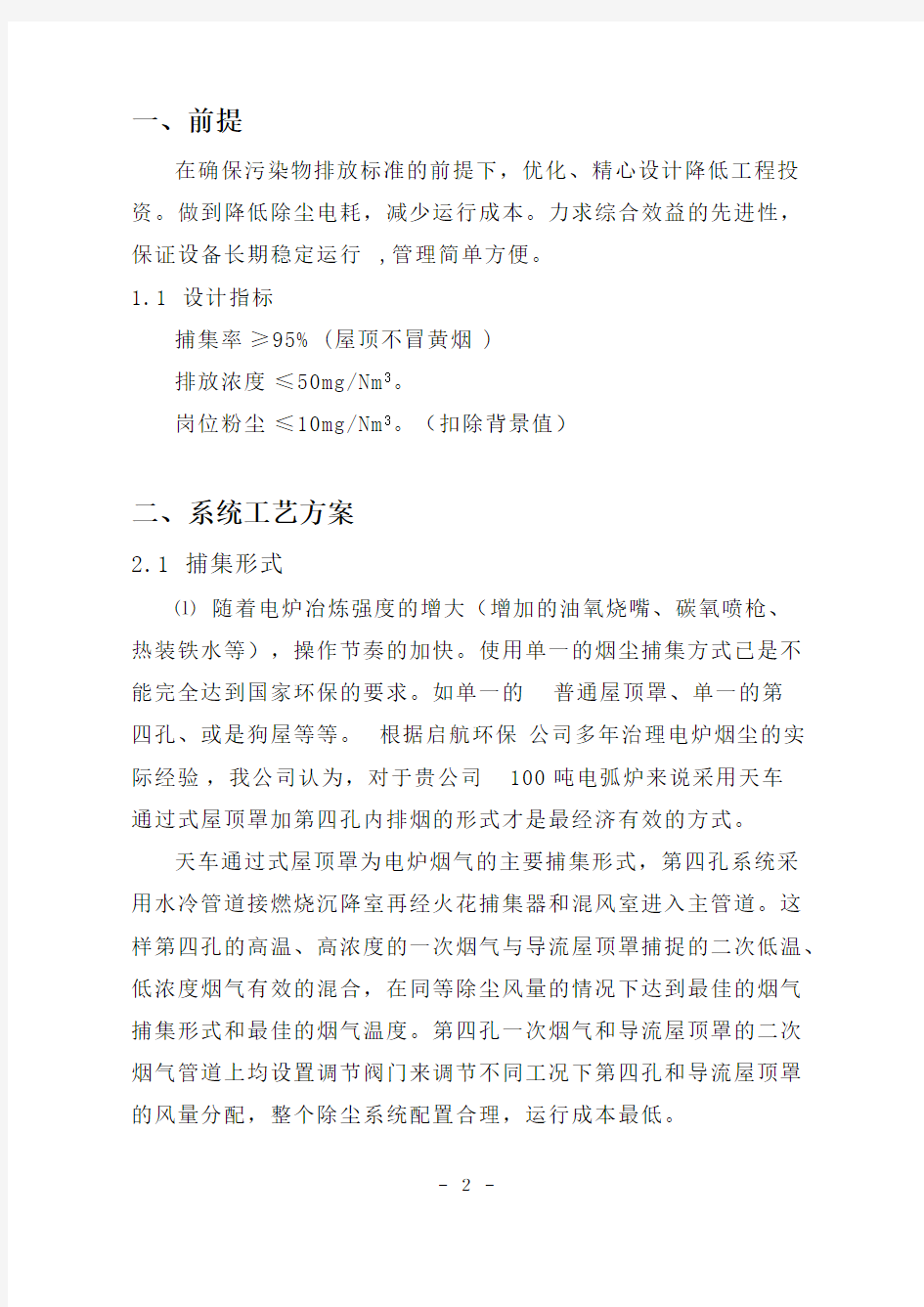
100吨电弧炉及精炼炉除尘系统
初
步
方
案
二零一三年七月十八日
一、前提
在确保污染物排放标准的前提下,优化、精心设计降低工程投资。做到降低除尘电耗,减少运行成本。力求综合效益的先进性,保证设备长期稳定运行,管理简单方便。
1.1 设计指标
捕集率≥95% (屋顶不冒黄烟)
排放浓度≤50mg/Nm3。
岗位粉尘≤10mg/Nm3。(扣除背景值)
二、系统工艺方案
2.1 捕集形式
⑴随着电炉冶炼强度的增大(增加的油氧烧嘴、碳氧喷枪、
热装铁水等),操作节奏的加快。使用单一的烟尘捕集方式已是不能完全达到国家环保的要求。如单一的普通屋顶罩、单一的第
四孔、或是狗屋等等。根据启航环保公司多年治理电炉烟尘的实际经验,我公司认为,对于贵公司100吨电弧炉来说采用天车
通过式屋顶罩加第四孔内排烟的形式才是最经济有效的方式。
天车通过式屋顶罩为电炉烟气的主要捕集形式,第四孔系统采
用水冷管道接燃烧沉降室再经火花捕集器和混风室进入主管道。这样第四孔的高温、高浓度的一次烟气与导流屋顶罩捕捉的二次低温、低浓度烟气有效的混合,在同等除尘风量的情况下达到最佳的烟气捕集形式和最佳的烟气温度。第四孔一次烟气和导流屋顶罩的二次烟气管道上均设置调节阀门来调节不同工况下第四孔和导流屋顶罩的风量分配,整个除尘系统配置合理,运行成本最低。
⑵ 100吨精炼炉则采用半密闭罩排烟。
⑶天车通过式屋顶罩
我公司将屋顶罩设计成多腔吸烟区域,分为主烟气收集区,散
烟气收集区。并据烟气流向及分布有效地捕集电炉烟气,实现用最
小的烟气吸风量,取得较高的捕集烟能力,并使得炼钢电炉烟气在
吸入罩体前与适量的冷空气充分混合,烟气温度均匀冷却,烟气捕
集率>95%。
根据电炉烟气的特点,罩体设计成双层结构形成主、副吸口,
使其更适宜气体流动的顺畅,防止涡流的发生。大大提高了对电炉
烟气的捕集能力。
在电炉平台上设计了移动式导流罩,在电炉周围形成密闭空间,移动罩上设排烟导流口,主要目的是最大限度地减少外部横向气流
对电炉烟柱的影响,使烟气尽可能地进入屋顶罩体。同时移动罩一
定程度上也起到隔音作用。炉前移动导流罩设计不影响电炉操作工艺。
2.2 流程简述
100吨电炉和100吨精炼炉合为一个除尘系统。100吨电炉烟
气的捕集形式采用第四孔加天车通过式屋顶罩;100吨精炼炉
烟气的捕集形式采用的是半密闭集烟罩。
100吨电弧炉产生的一次烟气通过电炉第四孔水冷弯管引入燃
烧室,在燃烧室内大颗粒烟尘沉降,并使烟气中的CO完全燃烧;高温烟气经水冷烟道冷却到500℃左右进入火花捕集器经混风室
二次冷却到400℃左右与总管汇合;100吨电炉产生的二次烟尘则在电炉周边移动导流罩的导流下进入屋顶罩,捕集后的烟气进入主
烟气管道与一次烟气混合,混合后的烟气通过总管道进入一台
LMC 脉冲布袋除尘器净化,净化后的洁净空气通过引风机送入排气筒。而100吨精炼炉产生的烟气则由半密闭罩捕集后通过另一条管道并入电炉烟气总管混合后进入同一台除尘器净化。
在除尘器入口主风管适当位置设置紧急野风阀,来防止突发性高温烟气对布袋产生不利影响。
2.3 工艺流程
第四孔水冷烟道
脉冲气源
2.4 系统配置
① 主风机: Y4-73-11 NO29.5D 2台并联
设计点压头: 4500 Pa
设计点风量: 65.0 ×104 m 3/h
② 主电机 Y630-8 N=1250KW n=740r/min 2台③ 液力偶合器 YoTcs —1150 2台④ 除尘器 LMC18000 1台
主风机排气筒
除尘器过滤面积: 19200 m2
过滤风速≤ 1.128 m/min
除尘器阻力≤ 1300 Pa
2.5 风量分配
根据电炉和精炼炉的不同工况和冶炼强度,对于100吨电炉和100吨精炼炉配置总风量130×104米3/小时,其中100吨电炉第四孔18×104米
3/小时,屋顶罩92×104米3/小时,100吨精炼炉风量20×104米3/小时。
风量分配根据电炉和精炼炉不同的冶炼工况来调节各自管道阀门以达到最佳烟气捕集效果。
2.6 风机的调速
为节约运行能耗,对大型的主风机均采用调速装置,而采用液力偶合器调速是国内除尘系统中常用的一种调速系统,技术较为成熟。
三、除尘器
3.1 除尘器选型
本设计选用目前除尘系统常用的启航LMC脉冲大布袋除尘器,其主要优点有:可离线清灰,阻力低、脉冲清灰效果好,所有除尘器的灰尘均采用埋刮板机输送方式输送进入集中灰仓,经加湿机加湿后卸灰装车。
LMC除尘器为中进中出,袋仓两边排列的布置形式。除尘器在宽
度方向分为三部分,即进出气流通道和仓室,烟气流从除尘器一端进入进气通道,进气通道截面积依通道内流量递减速率(分别进入了布袋仓)设计成递减截面,烟气流通过通道与布袋仓相通的布袋仓进气门进入左右各个布袋仓,经布袋过滤后的净化空气从布袋上方汇集至布袋仓出气门通至净化气过渡通道,经过过渡通道的离线清灰阀进入除尘器出气通
道而从除尘器的另一端排出。
吸附在布袋外的烟尘由压缩空气反吹进行清灰工作,清灰周期在调试时定时设定,并进行压差监控,并不断调整,直至清灰周期适合除尘器的积灰速度。清灰采用离线清灰方式,即在分室轮流清灰时,正在清灰的室的离线清灰阀关闭,切断上部的负压源,以使布袋上的积灰在自重力作用下落至仓底的灰仓内,清灰结束后离线清灰阀打开,该室进入净化状态,下一室则进入清灰状态。
3.2 脉冲气源
气源处理对除尘器运行稳定性有直接影响。在工厂提供的洁净压缩空气基础上,气源首先经气包一级滤除去气源过饱和水分,再由冷冻干燥机二级处理最后经气源管路三大件滤除气中的主要水和油份进入脉冲喷吹系统使用。
四、电气控制
4.1 电气配置
⑴主风机电机采用6KV/10KV高压等级
配进线柜 KGN-6KV/10KV 1套
开关柜KGN-6KV/10KV 1套
⑵半密闭罩及移动导流罩等传动电机和其它电机:星型卸灰阀电机,均采用380V 。
低压控制柜(PLC控制柜) 1套
现场操作箱 1套
4.2 自动化控制
电炉、精炼炉除尘系统采用西门子S7-300 PLC和一台上位微机控制
及监测整个系统的工作过程。人机界面生动、简洁、直观。
4.3 该除尘系统设置:
(1)除尘器烟气温度测量
(2)除尘器差压测量
(3)水冷管道前、后温度测量
(4)野风阀前、后温度测量
(5)主电机前后轴温测量
(6)电机定子三相温度检测
(7)液偶油温检测
(8)液偶油压检测
(9)主风机前后轴承测温
10风门开度显示及控制
五、说明
本设计与国内同类工程比较,综合技术经济指标是先进的,捕集烟尘能力强,不影响工艺操作,实用可靠,能耗低,投资省等,各项技术指标均能达到有关标准及规定要求。
六、电炉高温烟气余热回收方案(仅作参考)
一、电炉炼钢设备余热回收系统方案
随着能源的日趋紧张及能源价格上涨,节能工作成为各企业一项重要工作。如何挖掘企业自身潜力,节能增效,成为各部门普遍关注的话题。钢铁企业是能源消耗大户,能源浪费相对较大,其中有相当大部分是由于燃烧废气及冷却废气带走的,因此采用何种方式有效回收这部分废气显热就成为科技工作者研究的课题。
电炉炼钢是钢铁生产的重要环节,其中电炉烟气(第四孔)中的热能绝大部分被水冷烟道或机力冷却器带走了,因此,回收利用电炉废气带走的显热成为炼钢工序节能的一个重要环节。如何通过回收这部分显热,降低企业的生产成本,就成为电炉炼钢工作者及节能工作者关注的话题。
电炉炼钢设备的烟气温度呈同期性变化,最高烟温可以达到1300℃。原有第四孔烟气降温装置主要是通过汽化冷却烟道、燃烧沉降室、水冷壁烟道、风机冷却后进入布袋除尘后排空。这一流程的主要问题是冷却水循环量大,从沉降室后面出来的高温烟气中的热能全部被浪废掉了。造成运行成本高。且水冷烟管易粘灰产生灰阻,维修不方便。
二、热管工作原理
无机传热技术是在80年代末研究、开发的一项新型传热技术,无机热管是该项技术的专利产品。目前,无机热管技术在我国石油、化工、化肥和电力工业等领域的20多家不同企业中的换热设备或热能回收装置中得到了成功的应用。实践证明,它是具有极强生命力和竞争力的节能降耗、高效传热的高新技术。与普通的热管相比,其传热能力、高温工作性能更具优越性。
无机热管的传热原理与普通热管的传热原理类似,其区别在与内部
工质是一种稳定的无机化合物,在工作状态下无相变现象,稳定性好;具有良好的导热性,使用寿命长,热通量大;特别是它的高温性能是普通热管无法比拟的。正因为如此,无机热管技术越来越受到人们的重视,其应用领域也越来越广。
无机热传导元件的优越性:
1、启动迅速,导热速度快,热阻小(导热系数是白银的2.5-3.2万倍)。
2、均热性好(温差每米<0.1℃),传热能力强。
3、适用温度范围广,工质工作温度-60℃~1000℃。
4、传热多向性,与材料相容性好,操作压力低,无爆管现象。
5、形式多样,如管式结构、板式结构及各种结构组合。
6、效率高,使用寿命长(无机工质寿命达11万小时以上)。
7、适用行业面广,如石油化工、冶金、电力、电子、建材等行业都有应用,主
要应用于空预器、省煤器、煤气预热器、余热锅炉、燃油燃气锅炉、原油加热器、
水加热器、干燥器、散热器、电子电器元件散热器、太阳能热水器等。
三、余热回收装置系统介绍
我院开发研制的电炉余热回收装置,减少了检修成本,保证了除尘器
的工艺要求,回收了大量的余热能源,提供了炼钢炉的效率。以下简单介绍该系
统:
该系统按最高烟气温度范围的平均值和最多烟气量设计,这样可以保证
锅炉在最高温度和流量工况运行时的排烟温度低于180℃,以确保锅炉后部除尘
器的安全工作。
有可靠的除尘和清除积灰的手段,不会因为积灰而影响系统的运行和余
热回收效果。
锅炉对变工况的适应能力要强,当进入锅炉的烟气温度和流量变化时,
锅炉有很好的适应能力。
该余热系统为卧式烟道型,沿烟气流向主要由水冷沉降室、蒸发管束和
热管省煤器三部分组成。并设有汽水分离器和除氧器,其中热管省煤器中的水为强制循环,水冷沉降室。蒸发管束与汽水分离器之间为自然循环。
1.水冷沉降室是本余热锅炉烟气流程的第一通道,其主要功能是吸收烟
气的高温余热,并以重力分离和惯性分离的形式降低烟气中的含尘。
2.蒸发管束为双集箱立式光管受热面管组,上下联箱和受热面由无缝管
制作。沿烟气流向,将蒸发管束分成若干单元,各段高度依次降低,即采用了等流速设计。这种结构方式可使烟气流经各段受热面的速度基本一致,烟气冲刷均匀,减轻锅炉的磨损,降低流动阻力,自吹灰能力强。
3.本余热锅炉采用了热管省煤器。烟气侧位于省煤器的下部,水侧位于
省煤器的上部,垂直布置。
4.汽水分离器为纵置式,汽水分离器上设有安全阀、压力表、放空阀管
座,还设有主汽、副汽、水位表、给水、加药、连续排污、紧急放水,在主汽管接头内设有饱和蒸汽取样器。
5.水冷沉降室、蒸发管束和热管省煤器底部设集灰斗,集灰斗由钢板和
型钢框架构成,每个集灰斗下部设锁气器、锁气器下接输灰系统。
四、本余热锅炉性能特点:
1、有可靠的清灰手段
设置了特殊结构的水冷沉降室,以重力+惯性的方式分离烟气中的灰分;
水冷沉降室还可将部分飞灰变为固态,便于沉降分离。采用了合适的烟气速度,靠烟气的自吹灰作用减轻积灰。
清灰降尘措施完善,不会因为积灰而影响锅炉工作。热管省煤器结构合理,个别热管损坏时,不影响锅炉运行。
2、沉降室、蒸发管束为自然循环,循环回路设计合理,水循环安全可靠。
3、锅炉为卧式布置,烟道结构重心低,稳定性强,抗震,抗风能力强。
4、有自身蓄热能力
在炼钢炉工作的60分钟内,系统运行压力1.6MPa,靠减压阀将蒸汽压力降至1MPa供汽。炼钢炉停运时,靠蓄热向外供汽。
5、锅炉检修检查更换方便,热管省煤器采用了便于拆卸的结构。制造、安
装、检修方便。
6、运行费用低
与强制循环余热锅炉相比,本系统不设强制循环泵,设备不但安全可靠,而且自耗电少,运行成本低。
五、热管式余热锅炉设计制作依据的主要标准及规范
1)余热锅炉的设计、制造、检验遵循《蒸汽锅炉安全技术监察规程》进行监督、检查。
2)锅筒的设计、制造、验收符合JB/T1609-93《锅炉锅筒技术条件》。
3)水压试验按照JB/T1612-94《锅炉水压技术条件》执行。
4)锅炉受压元件的焊接符合JB/T1613-93《锅炉受压元件焊接技术条件》。