表面粗糙度及其影响因素
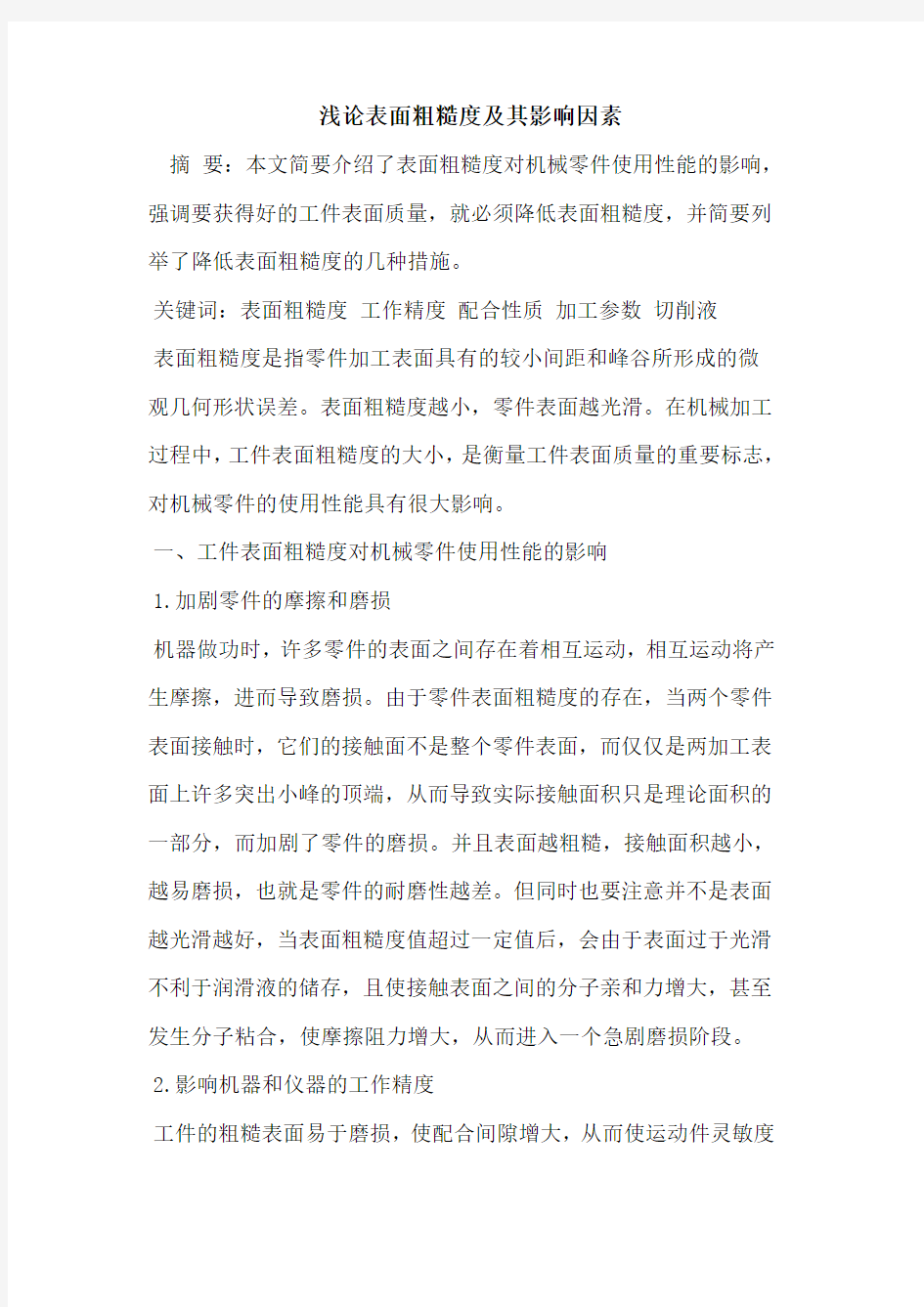

浅论表面粗糙度及其影响因素
摘要:本文简要介绍了表面粗糙度对机械零件使用性能的影响,强调要获得好的工件表面质量,就必须降低表面粗糙度,并简要列举了降低表面粗糙度的几种措施。
关键词:表面粗糙度工作精度配合性质加工参数切削液
表面粗糙度是指零件加工表面具有的较小间距和峰谷所形成的
微观几何形状误差。表面粗糙度越小,零件表面越光滑。在机械加工过程中,工件表面粗糙度的大小,是衡量工件表面质量的重要标志,对机械零件的使用性能具有很大影响。
一、工件表面粗糙度对机械零件使用性能的影响
1.加剧零件的摩擦和磨损
机器做功时,许多零件的表面之间存在着相互运动,相互运动将产生摩擦,进而导致磨损。由于零件表面粗糙度的存在,当两个零件表面接触时,它们的接触面不是整个零件表面,而仅仅是两加工表面上许多突出小峰的顶端,从而导致实际接触面积只是理论面积的一部分,而加剧了零件的磨损。并且表面越粗糙,接触面积越小,越易磨损,也就是零件的耐磨性越差。但同时也要注意并不是表面越光滑越好,当表面粗糙度值超过一定值后,会由于表面过于光滑不利于润滑液的储存,且使接触表面之间的分子亲和力增大,甚至发生分子粘合,使摩擦阻力增大,从而进入一个急剧磨损阶段。2.影响机器和仪器的工作精度
工件的粗糙表面易于磨损,使配合间隙增大,从而使运动件灵敏
各国表面粗糙度对照表
时代涂层测厚仪使用介绍 一、原理 磁性测厚原理:当测头与覆层接触时,测头和磁性金属基体构成一闭合磁路,由于非磁性覆盖层的存在,使磁路磁阻变化,通过测量其变化可计算覆盖层的厚度。 涡流测厚原理:利用高频交电流在线圈中产生一个电磁场,当测头与覆盖层接触时,金属基体上产生电涡流,并对测头中的线圈产生反馈作用,通过测量反馈作用的大小可导出覆盖层的厚度。 二、适用行业 1、电镀、喷涂:这个行业是使用我们仪器最多的,占每年销量相当大的比例,是我们主要用户群体,需要花大的精力去不断挖掘。 2、管道防腐:主要以石化方面的用户比较多,一般防腐层比较厚,TT260配F10探头的用户比较多。 3、铝型材:今年以来受国家实施强制标准,型材企业换发许可证的影响,该行业出现前所未有的好势头,主要测型材上面的氧化膜,据了解生产企业每少镀一微米,一吨型材“节约”150元,非常可观,因此国家强制要求配备包括涂层测厚仪在内的相关检测设备。此举也给我们带来了非常好的机会。这个机会也同样受到竞争对手的关注,他们最大限度的调低了价格,而且采取铺货等多种方式迅速在此行业展开攻势,针对于此唐总、石总也多次指示密切关注对手动向时世采取相应策略,宗旨是让利不让市场。希望分公司同仁也能切实利用好这次机会,充分发挥区域优势,使我们的产品更多进入该行业,也为今后在此行业的销售打下基础。另外,也可以扩大我们的产品在整个市场的影响。 4、钢结构:对于我们的产品这类企业也可以单独划为一个行业。涂层测厚仪在此行业也确实有很大的应用,包括铁塔等厂家最近购买信息也比较多。 5、印刷线路版、及丝网印刷等行业,这类企业相对来讲数特殊行业,购买量目前来看只是来自零星一些厂家, 8月份我们就有两家印刷企业购买。可以看出还是有需求的,需要我们不断做工作,挖掘信息资源,多发现一些新的销售机会。 三、各型号产品介绍: TT220:测量磁性金属上非磁性覆盖层的厚度。如钢、铁、非奥氏不锈钢上基体上的铝、铬、铜、珐琅、橡胶、油漆层的厚度。 TT230:测量非磁性基体上非导电层的厚度。如铜、铝、锌、锡基体上的珐琅、橡胶、油漆、铬、搪瓷、铝阳极氧化层的厚度。 TT240:测量非磁性基体上非导电层的厚度。如铜、铝、锌、锡基体上的珐琅、橡胶、油漆、铬、搪瓷、铝阳极氧化层的厚度。蹶 主要特点: 1、外型美观,且带有橡胶护套便于携带与现场操作; 2、存储数据多达300个测量值; 3、探头与主机的分离使操作稳定性增强,适用范围更广,特别是对于管道内壁,空间狭窄 的工件; 4、可以设定上下限,对界外测量值能自动报警,更大限度满足了用户需求; 5、可以配备通讯软件与PC机接口,便于用户对数据进行进一步的处理,仪器本身档次也 得到提高;
各种材料摩擦系数表分析
各种材料摩擦系数表 摩擦系数是指两表面间的摩擦力和作用在其一表面上的垂直力之比值。它是和表面的粗糙度有关,而和接触面积的大小无关。依运动的性质,它可分为动摩擦系数和静摩擦系数。现综合具体各种材料摩擦系数表格如下。
注:表中摩擦系数是试验值,只能作近似参考
固体润滑材料 固体润滑材料是利用固体粉末、薄膜或某些整体材料来减少两承载表面间的摩擦磨损作用的材料。在固体润滑过程中,固体润滑材料和周围介质要与摩擦表面发生物理、化学反应生成固体润滑膜,降低摩擦磨损。 中文名 固体润滑材料 采用材料 固体粉末、薄膜等 作用 减少摩擦磨损 使用物件 齿轮、轴承等 目录 1.1基本性能 2.2使用方法 3.3常用材料 基本性能 1)与摩擦表面能牢固地附着,有保护表面功能固体润滑剂应具有良好的 成膜能力,能与摩擦表面形成牢固的化学吸附膜或物理吸附膜,在表面附着,防止相对运动表面之间产生严重的熔焊或金属的相互转移。 2)抗剪强度较低固体润滑剂具有较低的抗剪强度,这样才能使摩擦副的 摩擦系数小,功率损耗低,温度上升小。而且其抗剪强度应在宽温度范围内不发生变化,使其应用领域较广。 3)稳定性好,包括物理热稳定,化学热稳定和时效稳定,不产生腐蚀及 其他有害的作用物理热稳定是指在没有活性物质参与下,温度改变不会引起相变或晶格的各种变化,因此不致于引起抗剪强度的变化,导致固体的摩擦性能改变。 化学热稳定是指在各种活性介质中温度的变化不会引起强烈的化学反应。要求固体润滑剂物理和化学热稳定,是考虑到高温、超低温以及在化学介质中使用时性能不会发生太大变化,而时效稳定是指要求固体润滑剂长期放置不变质,以便长期使用。此外还要求它对轴承和有关部件无腐蚀性、对人畜无毒害,不污染环境等。 4)要求固体润滑剂有较高的承载能力因为固体润滑剂往往应用于严酷 工况与环境条件如低速高负荷下使用,所以要求它具有较高的承载能力,又要容易剪切。 使用方法 1)作成整体零件使用某些工程塑料如聚四氟乙烯、聚缩醛、聚甲醛、聚 碳酸脂、聚酰胺、聚砜、聚酰亚胺、氯化聚醚、聚苯硫醚和聚对苯二甲酸酯等的摩擦系数较低,成形加工性和化学稳定性好,电绝缘性优良,抗冲击能力强,可以制成整体零部件,若采用环璃纤维、金属纤维、石墨纤维、硼纤维等对这些塑料增强,综合性能更好,使用得较多的有齿轮、轴承、导轨、凸轮、滚动轴承保持架等。
切削加工时表面粗糙度形成的原因及其影响因
切削加工时表面粗糙度形成的原因及其影响因素 简介:1 表面粗糙度产生的原因几何因素由于刀具切削刃的几何形状、几何参数、进给运动及切削刃本身的粗糙度等原因,未能将被加工表面上的材料层完全干净地去除掉(只有当刀具上带有刀具的副偏角kr=0的修光刃、且进给量小于修光刃宽度时,理论上才不产生残留面积),在已加工表面上遗留下残留面积,残留面积的高度构成了表面粗糙度Rz。当f≤2resinkr,残留面积是由圆弧过渡刃构成。此时关键字:刀具夹具切削铣削车削机床测量 1 表面粗糙度产生的原因 几何因素 由于刀具切削刃的几何形状、几何参数、进给运动及切削刃本身的粗糙度等原因,未能将被加工表面上的材料层完全干净地去除掉(只有当刀具上带有刀具的副偏角k'r=0的修光刃、且进给量小于修光刃宽度时,理论上才不产生残留面积),在已加工表面上遗留下残留面积,残留面积的高度构成了表面粗糙度Rz。 当f≤2resink'r,残留面积是由圆弧过渡刃构成。此时 式中:f——进给量,mm/r; re——刀尖圆弧半径。 当2resink'r≤f≤(re/sink'r)[1-cos(kr+k'r],残留面积是由刀尖圆弧过渡刃和直线副切削刃构成。此时 Rz=re[1-sin(k'r+b)]×1,000 sinb=1-(f/re)sink'r 式中kr,k'r——刀具的主偏角、副偏角。 当f>(re/sink'r)[1-cos(kr+k'r)],残留面积是由刀尖圆弧过渡刃和二直线主、副切削刃构成。此时Rz= 1 f-re(tan kr +tan k'r )]×1000 cotkr+k'r 2 2 当re→0时,残留面积是由主、副2条直线切削刃构成。此时Rz= f ×1000 cotkr+k'r 刀具切削刃的粗糙度由于直接复映在加工表面上,所以刀具切削刃的粗糙度值,应低于加工表面要求的粗糙度值。 实际上加工表面的粗糙度总是大于按以上计算的残留面积的高度,只有切削脆性材料或高速切削塑性材料时,实际加工表面的粗糙度才比较接近残留面积的高度,说明影响表面粗糙度的还有其他原因。 积屑瘤
各种材料表面粗糙度
零件表面粗糙度与尺寸公差 一般,我国机械设计和加工技术常用的表面粗糙度标准是轮廓算术均匀偏差Ra 对于Ra,国标GB3508—83有明确的规定。本文仅就Ra在机械零件设计考虑加工情况时的使用作以阐述。 1图纸右上角的表面粗糙度要求留意事项 大多数设计职员在图纸右上角都会标注:其余Ra6.3、Ra1.6,等。这里所指的是,除图样上注明的机械加工面的表面粗糙度要求后,剩余未注明的机械加工面的表面粗糙度Ra的数值为6.3μm或1.6μm。对于这一要求,需留意以下几方面。 1.1对于型钢表面等非本图要求而制作的加工面 在实际工作中,为了减少不必要的加工工作和进步产品质量,可以在图纸右上角处,对用非本图加工手段取得的材料、型材外表加以表面粗糙度要求,然后再对机械加工处的表面进行表面粗糙度要求,如图1。当然,这种对用非本图加工手段取得的材料、型材外表的表面粗糙度要求必须公道,必须不经过原材料工厂特殊加工就可以达到。如,一般热轧型钢的表面粗糙度在Ra25μm~Ra12.5μm;冷拔型钢的表面粗糙度在Ra12.5μm~Ra3.2μm;冷拔铝型钢的表面粗糙度在Ra6.3μm~Ra1.6μm。所以,标注型材等的表面粗糙度要求时,必须留意不能超出以上范围。 1.2对于用铸造、铸造、焊接等本图要求而制作的毛坯件 在使用铸造、铸造、焊接制作毛坯时,尤其是型腔件,对它们的机械加工往往是一部分,而不是全部加工。此时,设计职员一般在图纸右上角处标上:其余Ra6.3。这里的Ra6.3μm仅仅是指对型腔件要求进行机械加工部分,除往图纸上已经有表面粗糙度要求的_部分外表面加以表面粗糙度要求而已,并没有对非机械加工部分(如铸造、铸造)的外表加以表面粗糙度要求。所以,为了不产生混淆,有
光洁度对照表
光洁度▽,▽▽,▽▽▽,▽▽▽▽是现在日本和台湾用的。 ▽▽▽▽对应Ra<0.2; ▽▽▽对应Ra=0.2~0.8; ▽▽对应Ra=1.6~6.3; ▽对应Ra=12.5~50。 要求达到▽▽▽▽的表面有:工作时承受较大交变应力作用的重要零件的表面;保证精确定心的锥体表面;液压传动用的孔表面;汽缸套的内表面;活塞销的外表面;仪器导轨面;阀的工作面。 什么加工机械能达到▽▽▽▽,要到达▽▽▽▽至少要研磨,精度更高的话要超级加工。研磨加工是应用较广的一种光整加工。加工后精度可达IT5级,表面粗糙度可达Ra0.1~0.00 6μm。既可加工金属材料,也可以加工非金属材料。研磨加工时,在研具和工件表面间存在分散的细粒度砂粒(磨料和研磨剂)在两者之间施加一定的压力,并使其产生复杂的相对运动,这样经过砂粒的磨削和研磨剂的化学、物理作用,在工件表面上去掉极薄的一层,获得很高的精度和较小的表面粗糙度。 研磨的方法按研磨剂的使用条件分以下三类: 1.干研磨研磨时只需在研具表面涂以少量的润滑附加剂。砂粒在研磨过程中基本固定在研具上,它的磨削作用以滑动磨削为主。这种方法生产率不高,但可达到很高的加工精度和较小的表面粗糙度值(Ra0.02~0.01μm)。 2.湿研磨在研磨过程中将研磨剂涂在研具上,用分散的砂粒进行研磨。研磨剂中除砂粒外还有煤油、机油、油酸、硬脂酸等物质。在研磨过程中,部分砂粒存在于研具与工件之间。此时砂粒以滚动磨削为主,生产率高,表面粗糙度Ra0.04~0.02μm,一般作粗加工用,但加工表面一般无光泽。 3.软磨粒研磨在研磨过程中,用氧化铬作磨料的研磨剂涂在研具的工作表面,由于磨料比研具和工件软,因此研磨过程中磨料悬浮于工件与研具之间,主要利用研磨剂与工件表面的化学作用,产生很软的一层氧化膜,凸点处的薄膜很容易被磨料磨去。此种方法能得到极细的表面粗糙度(Ra0.02~0.01μm)。 我们国家以前也用▽后面加数字表示光洁度(GB1031-1968)有14个等级▽14,▽13,▽12,▽11,▽10,▽9,▽8,▽7,▽6,▽5,▽4,▽3,▽2,▽1,与现在大家用的粗糙度对应(GB1031-1983),*.*,0.012,0.025,0.05,0.10,0.2,0.4,0.8,1.6,3. 2,6.3,12.5,25,50,最后一个没有,请不要将此与日本标准混淆。
机械加工影响表面粗糙度的因素及改善措施
机械加工影响表面粗糙度的因素及改善措施 摘要:零件表面粗糙度是判断一个制造品是否符合工业标准的重要指标,直接决定其能否在机械中发挥正常功能,因此,研究机械加工影响表面粗糙度的因素十分重要,文中结合实际加工经验,探析了哪些因素对零件表面粗糙度有显著影响,并且根据这些影响因素给出合理的解决方案。 关键词:机械加工;表面粗糙度;改善措施 引言 在机械使用过程中,大多因为零件的破损导致其部分功能无法正常使用,工业产品的使用时间,产品质量和产品性能取决于组成零件的加工质量,而零件本身的质量由可靠性,耐磨性,表面粗糙度等因素决定,而其中的重要因素就是表面粗糙度,表面粗糙度即是零件加工表面较小间距和微小峰谷的不平度的表述,波峰和波谷的距离差距会影响机械零件的性能。因此研究表面粗糙度的影响因素十分重要,能够帮助改善零件的性能和机械设备的整体性能。 1.零件表面粗糙度的影响因素分析 1.1切削加工带来的影响 使用刀具给零件加工时,会在表面存留切削的残留面,这种残留面具有微观几何误差,进给量,主副偏角和刀尖圆弧的半径都会对残留面的大小,调整好加工时的进给量,角度就可以减小零件的变形程度和切割面积,另外,加工零件时应该选择符合材质特性的润滑剂和刀具。材料的选择也是至关重要的,因为材料加工发生切屑分离时,会产生塑性变形,这种塑性变形程度是和材料的弹力极限有关系,如果材料不好,残留塑形面积就会扩大,最终导致零件不符合工业标准。刀具的后刀面和已经加工的工件表面的摩擦也会对表面粗糙度产生影响,外力作用增大也会增加表面粗糙度。 1.2磨削加工带来的影响 磨削加工用于机械精细加工,磨粒的硬度很高,具有白锐性,可以用加工各种材料,在加工过程中,磨削转速一般是30到35m/s,转速非常高。但是磨削加工可以获得很高的加工精度和表面粗糙度值。正是因为磨削加工的优势,在具体加工过程中,温度可达1000摄氏度到1500摄氏度,会加深塑性变形,而且磨粒的负前角磨削比较薄,磨削时大多挤压零件表面,面对塑性变形过程,磨粒侧边会产生塑性热流,进而在零件上划出微小粗糙,高温会更近一步加深表面粗糙度。 一般而言,当磨削转速增大时,工件表面磨削度粗糙值减少,因为没有变形的磨粒的厚度会变小,工件转速增加时,磨削表面粗糙度反而会增大,轴方向的
各种材料摩擦系数表
各种材料摩擦系数表文件管理序列号:[K8UY-K9IO69-O6M243-OL889-F88688]
各种材料摩擦系数表 摩擦系数是指两表面间的和作用在其一表面上的垂直力之比值。它是和表面的粗糙度有关,而和接触面积的大小无关。依运动的性质,它可分为动摩擦系数和静摩擦系数。现综合具体各种材料摩擦系数表格如下。
注:表中摩擦系数是试验值,只能作近似参考 固体润滑材料 固体润滑材料是利用固体粉末、薄膜或某些整体材料来减少两承载表面间的摩擦磨损作用的材料。在固体润滑过程中,固体润滑材料和周围介质要与摩擦表面发生、反应生成固体润滑膜,降低摩擦磨损。 中文名 固体润滑材料 采用材料 固体粉末、薄膜等 作????用 减少摩擦磨损 使用物件 齿轮、轴承等 目录 1.1?
2.2? 3.3? 基本性能 1)与摩擦表面能牢固地附着,有保护表面功能固体润滑剂应具有良 好的成膜能力,能与摩擦表面形成牢固的化学吸附膜或物理吸附膜,在表面附着,防止相对运动表面之间产生严重的熔焊或金属的相互转移。 2)抗剪强度较低固体润滑剂具有较低的抗剪强度,这样才能使摩擦 副的摩擦系数小,功率损耗低,温度上升小。而且其抗剪强度应在宽温度范围内不发生变化,使其应用领域较广。 3)稳定性好,包括物理热稳定,化学热稳定和时效稳定,不产生腐 蚀及其他有害的作用物理热稳定是指在没有活性物质参与下,温度改变不会引起相变或晶格的各种变化,因此不致于引起抗剪强度的变化,导致固体的摩擦性能改变。 化学热稳定是指在各种活性介质中温度的变化不会引起强烈的化学反应。要求固体润滑剂物理和化学热稳定,是考虑到高温、超低温以及在化学介质中使用时性能不会发生太大变化,而时效稳定是指要求固体润滑剂长期放置不变质,以便长期使用。此外还要求它对轴承和有关部件无腐蚀性、对人畜无毒害,不污染环境等。 4)要求固体润滑剂有较高的承载能力因为固体润滑剂往往应用于严 酷工况与环境条件如低速高负荷下使用,所以要求它具有较高的承载能力,又要容易剪切。
各国粗糙度对照表
中美表面粗糙度对照表 中旧标 ( 光洁度 )中新标 ( 粗糙度)Ra美标(微米 ),Ra美国标准 ( 微英寸 ),Ra ▽4 6.3 8.00 3206.30 250 ▽ 5 3.2 5.00 200 4.00 1603.20125 ▽61.62.50 100 2.00 80 1.60 63 ▽ 70.81.25 50 1.00 40 0.8032 ▽ 80.40.63250.50 200.40 16
Ra: 轮廓算术平均偏差在取样长度内轮廓偏距绝对值的算术平均值?Rz:微观不平度十点高度在取样长度内五个最大的轮廓峰高的平均值与五个最大的轮廓谷深的平均值之和。 在设计零件时,表面粗糙度数值的选择,是根据零件在机器中的作用决定的。总的原则是: 在保证满足技术要求的前提下,选用较大的表面粗糙度数值。具体选择时,可以参考下述原则: (1)工作表面比非工作表面的粗糙度数值小。?(2)摩擦表面比不摩擦表面的粗糙度数值小。摩擦表面的摩擦速度愈高,所受的单位压力愈大,则应愈高;滚动磨擦表面比滑动磨擦表面要求粗糙度数值小。 (3)对间隙配合,配合间隙愈小,粗糙度数值应愈小;对过盈配合,为保证连接强度的牢固可靠,?载荷愈大,要求粗糙度数值愈小。一般情况间隙配合比过盈酝合粗糙度数值要小。?(4)配合表面的粗糙度应与其尺寸精度要求相当。配合性质相同时,零件尺寸愈小,则应粗糙度数值愈小;同一精度等级,小尺寸比大尺寸要粗糙度数值小,轴比孔要粗糙度数值小(特别是IT8~IT5的精度)。 (5)受周期性载荷的表面及可能会发生应力集中的内圆角、凹稽处粗糙度数值应较小。 一般零件只要标注Ra(轮廓算术平均偏差)就可以了,对于有密封要求的零件部位,通常须同时标注Ra(轮廓算术平均偏差)和Rz(微观不平度十点高度) 个人认为,通过切削加工的表面标注用Ra,通过抛光等加工方法得到的表面用Rz表示 两者的作用相近, 可相互转化.根据不同国家其使用情况不同. 国内和北美目前采用Ra, 而欧洲国家一般采用R z.? 示意图如下
表面粗糙度与公差等级的关系
机械零件表面粗糙度的选择 表面粗糙度是反映零件表面微观几何形状误差的一个重要技术指标,是检验零件表面质量的主要依据;它选择的合理与否,直接关系到产品的质量、使用寿命和生产成本。 机械零件表面粗糙度的选择方法有3种,即计算法、试验法和类比法。在机械零件设计工作中,应用最普通的是类比法,此法简便、迅速、有效。应用类比法需要有充足的参考资料,现有的各种机械设计手册中都提供了较全面的资料和文献。最常用的是与公差等级相适应的表面粗糙度。在通常情况下,机械零件尺寸公差要求越小,机械零件的表面粗糙度值也越小,但是它们之间又不存在固定的函数关系。例如一些机器、仪器上的手柄、手轮以及卫生设备、食品机械上的某些机械零件的修饰表面,它们的表面要求加工得很光滑即表面粗糙度要求很高,但其尺寸公差要求却很低。在一般情况下,有尺寸公差要求的零件,其公差等级与表面粗糙度数值之间还是有一定的对应关系的。 在一些机械零件设计手册和机械制造专著中,对机械零件的表面粗糙度和机械零件的尺寸公差关系的经验及计算公式都有很多介绍,并列表供读者选用,但只要细心阅来,就会发现,虽然采取完全相同的经验计算公式,但所列表中的数值也不尽相同,有的还有很大的差异。这就给不熟悉这方面情况的人带来了迷惑。同时也增加了他们在机械零件工作中选择表面粗糙度的困难。 在实际工作中,对于不同类型的机器,其零件在相同尺寸公差的条件下,对表面粗糙度的要求是有差别的。这就是配合的稳定性问题。在机械零件的设计和制造过程中,对于不同类型的机器,其零件的配合稳定性和互换性的要求是不同的。在现有的机械零件设计手册中,反映的主要有以下3种类型: 第1类主要用于精密机械,对配合的稳定性要求很高,要求零件在使用过程中或经多次装配后,其零件的磨损极限不超过零件尺寸公差值的10%,这主要应用在精密仪器、仪表、精密量具的表面、极重要零件
尺寸公差、形位公差、表面粗糙度三者的关系
尺寸公差、形位公差、表面粗糙度三者的关系 A.尺寸公差、形位公差、表面粗糙度数值上的关系 1、形状公差与尺寸公差的数值关系 当尺寸公差精度确定后,形状公差有一个适当的数值相对应,即一般约以50%尺寸公差值作为形状公差值;仪表行业约20%尺寸公差值作为形状公差值;重型行业约以70%尺寸公差值作为形状公差值。由此可见.尺寸公差精度愈高,形状公差占尺寸公差比例愈小所以,在设计标注尺寸和形状公差要求时,除特殊情况外,当尺寸精度确定后,一般以50%尺寸公差值作为形状公差值,这既有利于制造也有利于确保质量。 2、形状公差与位置公差间的数值关系 形状公差与位置公差间也存在着一定的关系。从误差的形成原因看,形状误差是由机床振动、刀具振动、主轴跳动等原因造成;而位置误差则是由于机床导轨的不平行,工具装夹不平行或不垂直、夹紧力作用等原因造成,再从公差带定义看,位置误差是含被测表面的形状误差的,如平行度误差中就含有平面度误差,故位置误差比形状误差要大得多。因此,在一般情况下、在无进一步要求时,给了位置公差,就不再给形状公差。当有特殊要求时可同时标注形状和位置公差要求,但标注的形状公差值应小于所标注的位置公差值,否则,生产时无法按设计要求制造零件。 3、形状公差与表面粗糙度的关系 形状误差与表面粗糙度之间在数值和测量上尽管没有直接联系,但在一定的加工条件下两者也存在着一定的比例关系,据实验研究,在一般精度时,表面粗糙度占形状公差的1/5~1/4。由此可知,为确保形状公差,应适当限制相应的表面粗糙度高度参数的最大允许值。 在一般情况下,尺寸公差、形状公差、位置公差、表面粗糙度之间的公差值具有下述关系式:尺寸公差>位置公差>形状公差>表面粗糙度高度参数 从尺寸、形位与表面粗糙度的数值关系式不难看出,设计时要协调处理好三者的数值关系,在图样上标注公差值时应遵循:给定同一表面的粗糙度数值应小于其形状公差值;而形状公差值应小于其位置公差值;位置各差值应小于其尺寸公差值。否则,会给制造带来种种麻烦。可是设计工作中涉及最多的是如何处理尺寸公差与表面粗糙度的关系和各种配合精度与表面粗糙度的关系。 一般情况下按以下关系确定: 1、形状公差为尺寸公差的60%(中等相对几何精度)时,Ra≤0.05IT; 2、形状公差为尺寸公差的40%(较高相对几何精度)时,Ra≤0.025IT; 3、形状公差为尺寸公差的25%(高相对几何精度)时,Ra≤0.012IT; 4、形状公差小于尺寸公差的25%(超高相对几何精度)时,Ra≤0.15Tf(形状公差值)。 最简单的参考值:尺寸公差是粗糙度的3-4倍,这样最为经济。
尺寸公差形位公差、表面粗糙度数值上的关系
尺寸公差、形位公差、表面粗糙度数值上的关系 一、尺寸公差、形位公差、表面粗糙度数值上的关系 1、形状公差与尺寸公差的数值关系 当尺寸公差精度确定后,形状公差有一个适当的数值相对应,即一般约以50%尺寸公差值作为形状公差值;仪表行业约20%尺寸公差值作为形状公差值;重型行业约以70%尺寸公差值作为形状公差值。由此可见.尺寸公差精度愈高,形状公差占尺寸公差比例愈小所以,在设计标注尺寸和形状公差要求时,除特殊情况外,当尺寸精度确定后,一般以50%尺寸公差值作为形状公差值,这既有利于制造也有利于确保质量。 2、形状公差与位置公差间的数值关系 形状公差与位置公差间也存在着一定的关系。从误差的形成原因看,形状误差是由机床振动、刀具振动、主轴跳动等原因造成;而位置误差则是由于机床导轨的不平行,工具装夹不平行或不垂直、夹紧力作用等原因造成,再从公差带定义看,位置误差是含被测表面的形状误差的,如平行度误差中就含有平面度误差,故位置误差比形状误差要大得多。因此,在一般情况下、在无进一步要求时,给了位置公差,就不再给形状公差。当有特殊要求时可同时标注形状和位置公差要求,但标注的形状公差值应小于所标注的位置公差值,否则,生产时无法按设计要求制造零件。 3、形状公差与表面粗糙度的关系 形状误差与表面粗糙度之间在数值和测量上尽管没有直接联系,但在一定的加工条件下两者也存在着一定的比例关系,据实验研究,在一般精度时,表面粗糙度占形状公差的1/5~1/4。由此可知,为确保形状公差,应适当限制相应的表面粗糙度高度参数的最大允许值。 在一般情况下,尺寸公差、形状公差、位置公差、表面粗糙度之间的公差值具有下述关系式:尺寸公差>位置公差>形状公差>表面粗糙度高度参数 从尺寸、形位与表面粗糙度的数值关系式不难看出,设计时要协调处理好三者的数值关系,在图样上标注公差值时应遵循:给定同一表面的粗糙度数值应小于其形状公差值;而形状公差值应小于其位置公差值;位置各差值应小于其尺寸公差值。否则,会给制造带来种种麻烦。可是设计工作中涉及最多的是如何处理尺寸公差与表面粗糙度的关系和各种配合精度与表面粗糙度的关系。 一般情况下按以下关系确定: 1、形状公差为尺寸公差的60%(中等相对几何精度)时,Ra≤0.05IT; 2、形状公差为尺寸公差的40%(较高相对几何精度)时,Ra≤0.025IT; 3、形状公差为尺寸公差的25%(高相对几何精度)时,Ra≤0.012IT; 4、形状公差小于尺寸公差的25%(超高相对几何精度)时,Ra≤0.15Tf(形状公差值)。 最简单的参考值:尺寸公差是粗糙度的3-4倍,这样最为经济。
表面粗糙度等级对照表
表面粗糙度级别对照及应用国际标注Rz N12 N11 N10 N9 N8 N7 N6 N5 N4 N3 N2 N1200 100 25Ra 50 25 6.3粗糙面表面形状特征 明显可见刀痕 可见刀痕
微见刀痕 可见加工痕迹 微见加工痕迹 看不见加工痕迹 可辨加工痕迹的方向 光面微辨加工痕迹的方向 不可辨加工痕迹的方向 暗光泽面 亮光泽面 镜状光泽面 雾状镜面 镜面精磨、研磨、抛光、超精磨、 镜面磨削等研磨、金刚石车刀的精车、精绞、冷拉、拉刀加工、抛光等加工方法举例锯断、粗车、粗铣、粗刨、钻孔以及用粗纹锉刀、粗砂 轮等加工冷拉、精车、精绞、粗绞、粗磨、刮削、粗拉刀加 工等5012.5 12.53.2半光面 6.31.6 6.30.8 3.20.4 1.60.2
0.80.1 0.40.05 0.20.025最光面 0.10.012 0.05 表面特征 明显可见刀痕 微见刀痕 看不见加工痕迹,微辩加工方向暗光泽面 雾状镜面0.012 镜状光泽面0.025 亮光泽面0.05 暗光泽面0.1 不可见加工痕迹的方向0.2 可见加工痕迹方向0.8 微见加工痕迹方向0.4 看不清加工痕迹方向1.6 微见加工痕迹方向3.2 可见加工痕迹方向6.3 微见刀痕12.5
可见刀痕25 明显可见刀痕50表面粗糙度(Ra)数值 Ra100、Ra50、Ra25、 Ra12.5、Ra6.3、Ra3.2、 Ra1.6、Ra0.8、Ra0.4、 Ra0.2、Ra0.1、Ra0.05、加工方法举例 粗车、粗刨、粗铣、钻孔精车、精刨、精铣、粗铰、粗磨精车、精磨、精铰、研磨研磨、珩磨、超精磨、抛光镜面0.006微米
摩擦系数及其计算
达芬奇1508年提出假设,摩擦系数一般为0.25 阿芒汤1699年,摩擦系数0.3 比尤里芬格1730年,摩擦系数0.3 库伦,十八世纪,确定压力对摩擦系数的影响,并求出几种材料配合的摩擦系数的不同数值。 俄国,科捷利尼科夫、彼得罗夫,十九世纪中叶,摩擦偶件的摩擦系数并非不变摩擦系数影响因素: 1材料本性及摩擦表面是否有膜(润滑油、氧化物、污垢) 2静止接触的延续时间 3施加载荷的速度 4摩擦组合件的刚度及弹性 5滑动速度 6摩擦组合件的温度状态 7压力 8物体的接触特性,表面尺寸,重叠系数 9表面质量及粗糙度 A Static Friction Model for Elastic—Plastic Contacting Rough Surfaces. 形状误差对过盈联接摩擦力的影响分析及其修正 摩擦分类: 1动摩擦力,对应于很大的、不可逆的相对位移,相对位移大小与外施力无关。2非全静摩擦力,对应于很小的、局部可逆的相对位移,位移大小与外施力成正比,称为初位移,微米级。 3全静摩擦力,对应于初位移的极限值,初位移转变成相对位移。 根据运动学特征划分 滑动摩擦、旋转摩擦(变相的滑动摩擦)、滚动摩擦 根据表面状态,是否润滑的特征 1纯净摩擦,无吸附膜、氧化物等 2干摩擦,表面间无润滑油、污垢等 3边界摩擦,表面被一层润滑油分开,润滑油极薄(<0.1微米) 4液体摩擦 5半干摩擦 6半液体摩擦 静摩擦系数,克服两物体的接触耦合、使之摆脱静止状态所耗费的最大切向力对应接触物体所受压力载荷的比率。 滑动摩擦系数,克服两物体相对移动的阻力(超出初位移的范围以外)所耗费的切向力对应接触物体所受压力载荷的比率。 滚动阻力系数,··· 库伦方程,采用的滚动摩擦系数 T——滚动摩擦力,r——圆柱体的半径,P——接触物体所受压力 接触面积、粗糙度、载荷的影响 由于固体表面的粗糙度及波纹度,使得两个固体表面总是在个别的点上发生接触。
摩擦系数及其计算
精心整理达芬奇1508年提出假设,摩擦系数一般为0.25 阿芒汤1699年,摩擦系数0.3 比尤里芬格1730年,摩擦系数0.3 库伦,十八世纪,确定压力对摩擦系数的影响,并求出几种材料配合的摩擦系数的不同数值。 俄国,科捷利尼科夫、彼得罗夫,十九世纪中叶,摩擦偶件的摩擦系数并非不变 摩擦系数影响因素: 1材料本性及摩擦表面是否有膜(润滑油、氧化物、污垢) 2静止接触的延续时间 3施加载荷的速度 4 5 6 7压力 8 9 1 2 3 1 2 3 4 5 6 滑动摩擦系数,克服两物体相对移动的阻力(超出初位移的范围以外)所耗费的切向力对应接触物体所受压力载荷的比率。 滚动阻力系数,··· 库伦方程,采用的滚动摩擦系数 T——滚动摩擦力,r——圆柱体的半径,P——接触物体所受压力 接触面积、粗糙度、载荷的影响 由于固体表面的粗糙度及波纹度,使得两个固体表面总是在个别的点上发生接触。 两个相互叠合的表面只是在其某些凸部发生接触,而这些凸部的总接触面积只占接触轮廓所限定的总表面面积的极小部分。随着压力增大,接触面积增大。凸部的直径几分之一微米至30~50微米(高度小于80微米)。
载荷增大,各点的直径增大,随后面积的增大主要是由于接触点数目的增多。 名义(几何)接触面积——由接触物体的外部尺寸描绘出来. 轮廓接触面积——由物体的体积压皱所形成的面积;真实面积即轮廓接触面上;轮廓接触面积与压力载荷有关。 真实(物理)接触面积——物体接触的真实微小面积总和,也是压力载荷的函数,并且在名义面积尺寸的1/100000至1/10的范围内变化,由接触表面的机械性能及粗糙度而定。 接触点的总数目及每一个接触点的尺寸随着载荷的增大而增大,但当载荷继续增大时,接触面积的增大主要是依靠接触点的数目的增加,尺寸几乎不再变化。 对于粗糙表面来说,需要耗费更大的力,使凸部变形,从而获得一定的接触面积;光滑表面,凸部变形不大时,就能获得很大的接触面积(试验知,光滑表面的接触点上的应力约为材料硬度的一半,粗糙表面的接触点应力为硬度的2-3倍)。 L a =δ=若认为第三个量度中所有凸部具有相同的截面轮廓,则lb S ?=,b ——被研究表面的宽度。但若凸部具有球形,则单个接触面积相应的等于2l π?。若认为接触点具有相同的半径,则2S r n ?π=。 为得出真实面积,除总宽度外,必须有个别点的半径方面的数据, 在第一种和第二种情况下,真实接触面积与互相接近程度成正比。 令()S x ??=,当0x =,()P x S ?=;当x h =,()0x ?=。 S P ——轮廓投影图的基础面积,称为计算接触面积,但x ——棒的高度,相对于经过最短的棒 的零位截面而言的。 令棒上的单位载荷q 为绝度压缩(x-a )的函数,即
各种材料摩擦系数表
各种材料摩擦系数表
各种材料摩擦系数表 摩擦系数是指两表面间的摩擦力和作用在其一表面上的垂直力之比值。它是和表面的粗糙度有关,而和接触面积的大小无关。依运动的性质,它可分为动摩擦系数和静摩擦系数。现综合具体各种材料摩擦系数表格如下。
注:表中摩擦系数是试验值,只能作近似参考 固体润滑材料 固体润滑材料是利用固体粉末、薄膜或某些整体材料来减少两承载表面间的摩擦磨损作用的材料。在固体润滑过程中,固体润滑材料和周围介质要与摩擦表面发生物理、化学反应生成固体润滑膜,降低摩擦磨损。中文名 固体润滑材料 米用材料 固体粉末、薄膜等 作用 减少摩擦磨损 使用物件 齿轮、轴承等 目录 1.1基本性能 2.2使用方法 3.3常用材料 基本性能 1)与摩擦表面能牢固地附着,有保护表面功能固体润滑剂应具有良好的成膜能力,能与摩擦表面形成牢固的化学吸附膜或物理吸附膜,在表面附 着,防止相对运动表面之间产生严重的熔焊或金属的相互转移。 2)抗剪强度较低固体润滑剂具有较低的抗剪强度,这样才能使摩擦副的 摩擦系数小,功率损耗低,温度上升小。而且其抗剪强度应在宽温度范围内不发生变化,使其应用领域较广。 3)稳定性好,包括物理热稳定,化学热稳定和时效稳定,不产生腐蚀及其他有害的作用物理热稳定是指在没有活性物质参与下,温度改变不会引起相变或晶格的各种变化,因此不致于引起抗剪强度的变化,导致固体的摩擦性能改变。 化学热稳定是指在各种活性介质中温度的变化不会引起强烈的化学反应。要求固体润滑剂物理和化学热稳定,是考虑到高温、超低温以及在化学介质中使用时性能不会发生太大变化,而时效稳定是指要求固体润滑剂长期放置不变质,以便长期使用。此外还要求它对轴承和有关部件无腐蚀性、对人畜无毒害,不污染环境等。 4)要求固体润滑剂有较高的承载能力因为固体润滑剂往往应用于严酷工况与环境条件如低速高负荷下使用,所以要求它具有较高的承载能力,又要容易剪切。使用方法 1)作成整体零件使用某些工程塑料如聚四氟乙烯、聚缩醛、聚甲醛、聚碳酸脂、聚酰胺、聚砜、聚酰亚胺、氯化聚醚、聚苯硫醚和聚对苯二甲酸酯等的摩擦系数较低,成形加工性和化学稳定性好,电绝缘性优良,抗冲击能力强,可以制成整体零部件,若采用环璃纤维、金属纤维、石墨纤维、硼纤维等对这些塑料增强,综合性能更好,使用得较多的有齿轮、轴承、导轨、凸轮、滚动轴承保持架等。 2)作成各种覆盖膜来使用通过物理方法将固体润滑剂施加到摩擦界面或表面,使之成为具有一定自润滑性能的干膜,这是较常用的方法之一。成膜的方法很多,
各国表面粗糙度对照表
時代塗層測厚儀使用介紹 一?原理 磁性測厚原理:當測頭與覆層接觸時,測頭和磁性金屬基體構成一閉合磁路,由於非磁性覆蓋層的存在,使磁路磁阻變化,通過測量其變化可計算覆蓋層的厚度? 渦流測厚原理:利用高頻交電流在線圈中產生一個電磁場,當測頭與覆蓋層接觸時,金屬基體上產生電渦流,並對測頭中的線圈產生回饋作用,通過測量回饋作用的大小可匯出覆蓋層的厚度? 二、適用行業 1?電鍍?噴塗:這個行業是使用我們儀器最多的,占每年銷量相當大的比例,是我們主要使用者群體,需要花大的精力去不斷挖掘? 2?管道防腐:主要以石化方面的用戶比較多,一般防腐層比較厚,TT260配F10探頭的用戶比較多? 3?鋁型材:今年以來受國家實施強制標準,型材企業換發許可證的影響,該行業出現前所未有的好勢頭,主要測型材上面的氧化膜,據瞭解生產企業每少鍍一微米,一噸型材“節約”150元,非常可觀,因此國家強制要求配備包括塗層測厚儀在內的相關檢測設備?此舉也給我們帶來了非常好的機會?這個機會也同樣受到競爭對手的關注,他們最大限度的調低了價格,而且採取鋪貨等多種方式迅速在此行業展開攻勢,針對于此唐總?石總也多次指示密切關注對手動向時世採取相應策略,宗旨是讓利不讓市場?希望分公司同仁也能切實利用好這次機會,充分發揮區域優勢,使我們的產品更多進入該行業,也為今後在此行業的銷售打下基礎?另外,也可以擴大我們的產品在整個市場的影響? 4?鋼結構:對於我們的產品這類企業也可以單獨劃為一個行業?塗層測厚儀在此行業也確實有很大的應用,包括鐵塔等廠家最近購買資訊也比較多? 5?印刷線路版?及絲網印刷等行業,這類企業相對來講數特殊行業,購買量目前來看只是來自零星一些廠家, 8月份我們就有兩家印刷企業購買?可以看出還是有需求的,需要我們不斷做工作,挖掘資訊資源,多發現一些新的銷售機會? 三?各型號產品介紹: TT220:測量磁性金屬上非磁性覆蓋層的厚度?如鋼?鐵?非奧氏不銹鋼上基體上的鋁?鉻?銅?琺瑯?橡膠?油漆層的厚度? TT230:測量非磁性基體上非導電層的厚度?如銅?鋁?鋅?錫基體上的琺瑯?橡膠?油漆?鉻?搪瓷?鋁陽極氧化層的厚度? TT240:測量非磁性基體上非導電層的厚度?如銅?鋁?鋅?錫基體上的琺瑯?橡膠?油漆?鉻?搪瓷?鋁陽極氧化層的厚度?蹶 主要特點: 1、外型美觀,且帶有橡膠護套便於攜帶與現場操作; 2、存儲資料多達300個測量值; 3、探頭與主機的分離使操作穩定性增強,適用範圍更廣,特別是對於管道內壁,空間狹窄的工 件; 4、可以設定上下限,對界外測量值能自動報警,更大限度滿足了用戶需求; 5、可以配備通訊軟體與PC機介面,便於使用者對資料進行進一步的處理,儀器本身檔次也 得到提高; 6、兩節AA型鹼性電池,在使用過程中突然斷電時可以隨時更換無需等待? 7、顯示解析度達到0.1um,尤其對於測量鋁型材氧化膜更有優勢?
《公差配合及表面粗糙度》选择题
1.一孔尺寸的要求为φ30+0052,我们在加工时最理想的目标值是( D ) A.30 B.30.052 C.30.040 D.30.026 2.下列标准公差中,精度最低的是( D ) A.ITO B.IT01 C.IT10 D.IT18 3.某轴段标注尺寸为,现对四个完工零件进行测量,得到的数据分别为φ55.000mm,φ5 4.998mmφ5 5.042mm,φ55.023mm,则合格的零件有( A ) A1个 B.2个 C.3个 D.4个 4.已知某轴的公称尺寸为φ50加工后测得的实际尺寸为φ50.022mm,则实际偏差为( D ) A.0.051mm B.0.050mm C.0.025mm D.0.022mm 5.关于φ20R6、φ20R7、φ20R8三个公差带,下列说法正确的是( C ) A,上、下极限偏差均不相同 B.上、下极限偏差均相同 C.上极限偏差相同,但下极限偏差不同
D.上极限偏差不同,但下极限偏差相同 6.表面结构中,加工纹理呈两斜向交叉且与视图所在的投影面相交的是( C ) 7.表面结构中,加工纹理垂直于视图所在的投影面的是( B ) 8.以下不属于表面粗糙度对零件的使用性能影响的主要表现是( C ) A.对配合性质的影响 B对耐磨性的影响奥面 C.对材料塑性变形的影响 D.对抗腐蚀性的影响 9.Ra值测量最常用的方法是( C ) A.样板比较法 B.显微镜比较法,度 C电动轮廓仪比较法D.光切显微镜测量法工眼 10.表面粗糙度是( )误差。( B ) A.宏观几何形状 B.微观几何形状 C.宏观相互位置 D.微观相互位置 11选择表面粗糙度评定参数值时,下列论述不正确的有( A ) A.同一零件上工作表面应比非工作表面参数值大 B摩擦表面应比非摩擦表面的参数值小 C配合质量要求高,表面粗糙度参数值应小 D.受交变载荷的表面,表面粗糙度参数值应小
尺寸公差、形位公差、表面粗糙度数值上的关系
一、尺寸公差、形位公差、表面粗糙度数值上的关系 1、形状公差与尺寸公差的数值关系 当尺寸公差精度确定后,形状公差有一个适当的数值相对应,即一般约以50%尺寸公差值作为形状公差值;仪表行业约20%尺寸公差值作为形状公差值;重型行业约以70%尺寸公差值作为形状公差值。由此可见.尺寸公差精度愈高,形状公差占尺寸公差比例愈小所以,在设计标注尺寸和形状公差要求时,除特殊情况外,当尺寸精度确定后,一般以50%尺寸公差值作为形状公差值,这既有利于制造也有利于确保质量。 2、形状公差与位置公差间的数值关系 形状公差与位置公差间也存在着一定的关系。从误差的形成原因看,形状误差是由机床振动、刀具振动、主轴跳动等原因造成;而位置误差则是由于机床导轨的不平行,工具装夹不平行或不垂直、夹紧力作用等原因造成,再从公差带定义看,位置误差是含被测表面的形状误差的,如平行度误差中就含有平面度误差,故位置误差比形状误差要大得多。因此,在一般情况下、在无进一步要求时,给了位置公差,就不再给形状公差。当有特殊要求时可同时标注形状和位置公差要求,但标注的形状公差值应小于所标注的位置公差值,否则,生产时无法按设计要求制造零件。 3、形状公差与表面粗糙度的关系 形状误差与表面粗糙度之间在数值和测量上尽管没有直接联系,但在一定的加工条件下两者也存在着一定的比例关系,据实验研究,在一般精度时,表面粗糙度占形状公差的1/5~1/4。由此可知,为确保形状公差,应适当限制相应的表面粗糙度高度参数的最大允许值。 在一般情况下,尺寸公差、形状公差、位置公差、表面粗糙度之间的公差值具有下述关系式:尺寸公差>位置公差>形状公差>表面粗糙度高度参数 从尺寸、形位与表面粗糙度的数值关系式不难看出,设计时要协调处理好三者的数值关系,在图样上标注公差值时应遵循:给定同一表面的粗糙度数值应小于其形状公差值;而形状公差值应小于其位置公差值;位置各差值应小于其尺寸公差值。否则,会给制造带来种种麻烦。可是设计工作中涉及最多的是如何处理尺寸公差与表面粗糙度的关系和各种配合精度与表面粗糙度的关系。 一般情况下按以下关系确定: 1、形状公差为尺寸公差的60%(中等相对几何精度)时,Ra≤0.05IT; 2、形状公差为尺寸公差的40%(较高相对几何精度)时,Ra≤0.025IT;
表面粗糙度对照表
国内表面光洁度与表面粗糙度Ra、Rz数值换算表(单位:μm)
另附:粗糙度仪新旧标准参数变化对照表现将TR200粗糙度仪依据新标准更改参数的情况列表如下,如有问题,由时代公司负责解释。本表还适用于公司TR1系列粗糙度仪。修改后可测量参数的总数没有变化,仍为13个参数,只是显示在不同的标准中,也就是说:时代粗糙度仪产品参数:涵盖新旧标准参数!(详见表)
另附:表面粗糙度国际标准加工方法 表面粗糙度参数及其数值(Surface Roughness Parameters and their Values)常用的3个分别是:轮廓算数平均偏差(Ra)--arithmetical mean deviation of the profile; 微观不平度十点高度(Rz)--the point height of irregularities; 轮廓最大高度(Ry)--maximum height of the profile。
Ra--在取样长度L内轮廓偏距绝对值的算术平均值。 Rz--在取样长度内5个最大的轮廓峰高的平均值与5个最大的轮廓谷深的平均值之和。 Ry--在取样长度L内轮廓峰顶线和轮廓谷底线之间的距离。 如果图面没标注粗糙度选用Ra /Rz /Ry 的情况下默认为Ra。 表面粗糙度是指加工表面具有的较小间距和微小峰谷不平度。其两波峰或两波谷之间的距离(波距)很小(在
1mm以下),用肉眼是难以区别的,因此它属于微观几何形状误差。表面粗糙度越小,则表面越光滑。表面粗糙度的大小,对机械零件的使用性能有很大的影响,主要表现在以下几个方面: ①表面粗糙度影响零件的耐磨性。表面越粗糙,配合表面间的有效接触面积越小,压强越大,磨损就越快。 ②表面粗糙度影响配合性质的稳定性。对间隙配合来说,表面越粗糙,就越易磨损,使工作过程中间隙逐渐增大;对过盈配合来说,由于装配时将微观凸峰挤平,减小了实际有效过盈,降低了联结强度。 ③表面粗糙度影响零件的疲劳强度。粗糙零件的表面存在较大的波谷,它们像尖角缺口和裂纹一样,对应力集中很敏感,从而影响零件的疲劳强度。 ④表面粗糙度影响零件的抗腐蚀性。粗糙的表面,易使腐蚀性气体或液体通过表面的微观凹谷渗入到金属内层,造成表面腐蚀。 ⑤表面粗糙度影响零件的密封性。粗糙的表面之间无法严密地贴合,气体或液体通过接触面间的缝隙渗漏。 此外,表面粗糙度对零件的外观、测量精度也有影响。 粗糙度:0.012、0.025、0.050、0.100、0.20、0.40、0.80、1.6、3.2、6.3、12.5、25、50、100 6.3:半精加工表面。用于不生要的零件的非配合表面,如支柱、轴、、支架、外壳、衬套、盖等的端面;螺钉、螺栓各螺母的自由表面;不要求定心和配合特性的表面,如螺栓孔、螺钉通孔、铆钉孔等;飞轮、带轮、离合器、联轴节、凸轮、偏心轮的侧面;平键及键槽上下面、花键非定心表面、齿顶圆表面;所有轴和孔的退刀槽;不重要的连接配合表面;犁铧、犁侧板、深耕铲等零件的摩擦工作面;插秧爪面等。1、外观的光滑与摩擦是一个矛盾问题,总的来说,既要光滑美观,又要有相当的摩擦, 以方便安装,以下是常见的一些粗糙度数值: 2、粗糙度0.8以下:抛光 3、粗糙度0.8:用磨床加工的面 4、粗糙度1.6—3.2:车床、铣床加工面 5、粗糙度3.2—12.5:一般性的常规加工 6、一般而言,既要光滑美观,又要有相当的摩擦,以方便安装的话,粗糙度0.8可以,既显得美观高档,手感也可以的 7、如果手拧部分需要减低等级的话也可以的,建议选择粗糙度1.6—3.2,但是,好看吗?会不会影响外观的美感呢? 8、如果需要重视手拧的功能,最好是做滚花处理,滚花有“直纹”和“网纹”两种,图纸上的标注:网纹0.8(用箭头指明需要滚花的部位,再写上文字) 如有侵权请联系告知删除,感谢你们的配合!