食品生产车间报表模板
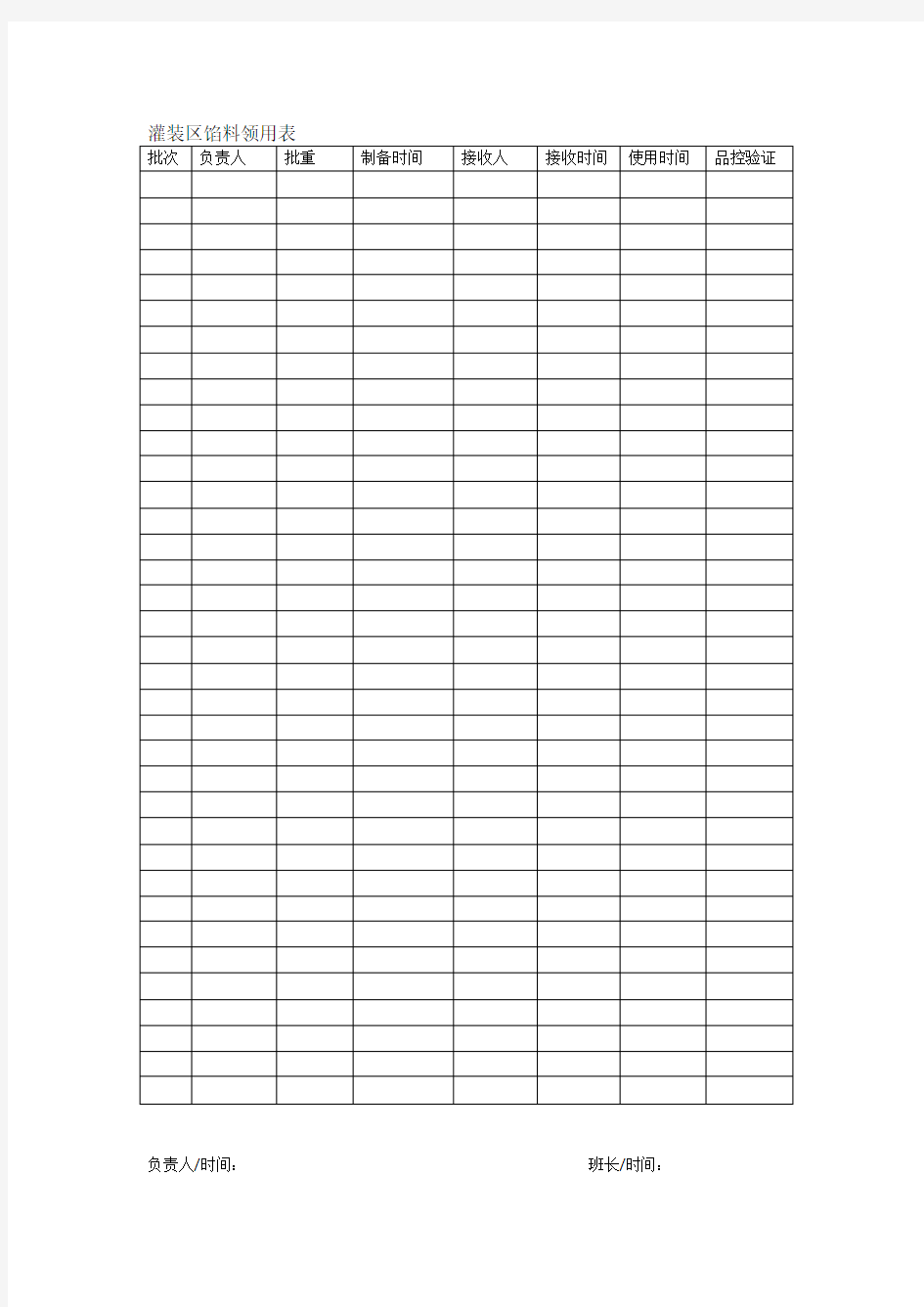
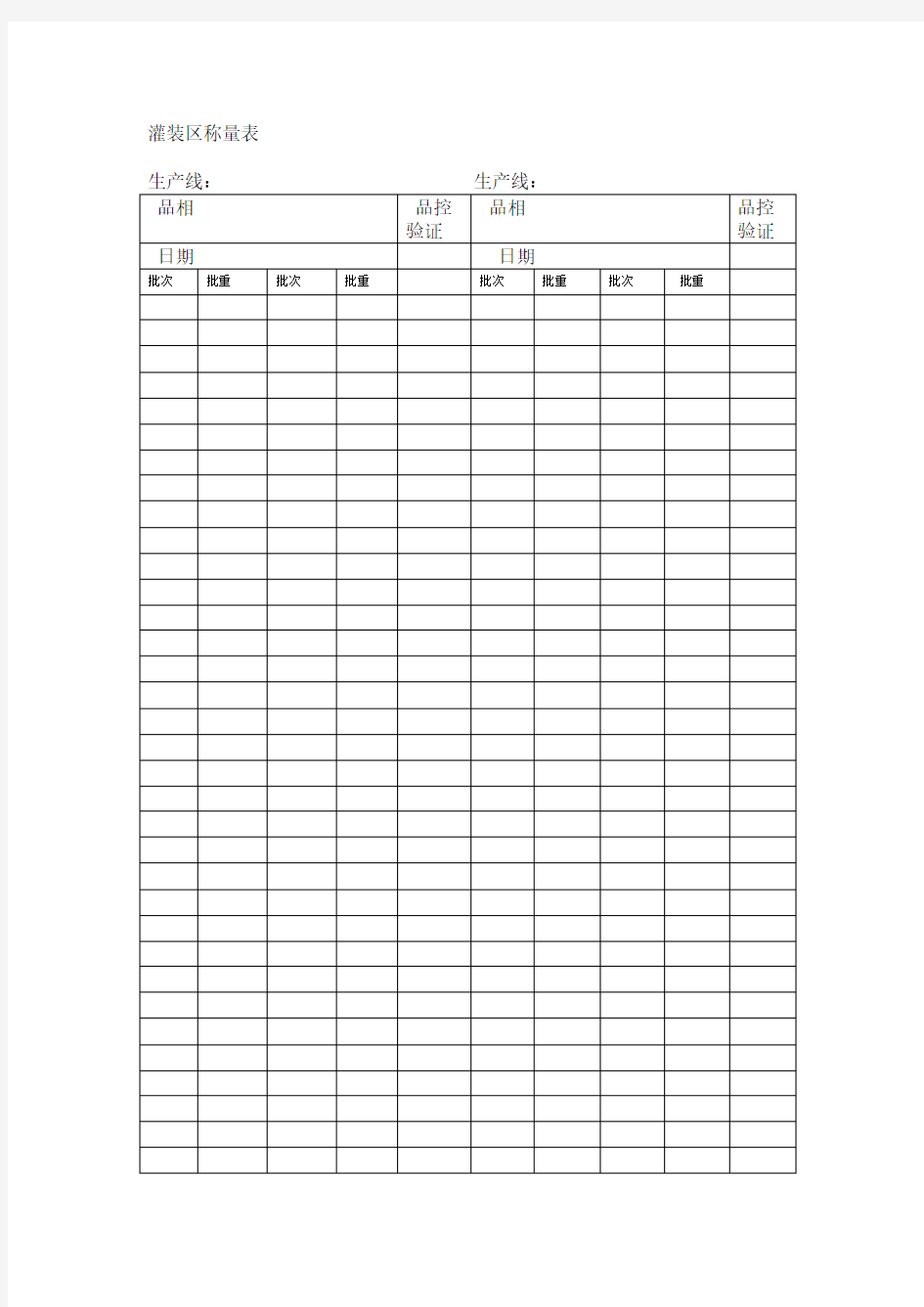
负责人/时间:班长/时间:
灌装区称量表
日期:/班长日期:/称量人
配料监控表
时间:/主任时间:/品控时间:/班长时间:/负责人
熟区报表
班长/时间:
食品标签
品系/ kg 批重/批次月年日制作日期
制作时间制作人
1.车间内统一使用公斤计数。
2.品系为生产品种。
3.批次为生产几锅。
4.产量为当日该品系总产量(为以后几件做准备)。
5.负责人为该生产线负责人,可以称之为线长。
6.成员为该生产线初线长之外其他全部参与劳动人员。
7.开始时间为该批次原料开始生产时刻。
8.结束时间为该批次原料生产结束时刻。
9.品控验证为随机抽检,主要形式为:投料重量、出料温度、操作规程等。每张报表品控次数根据生产批次决定,1~3批次抽检1次,4~6批次抽检2次,7批次及7批次以上抽检3次。
产能分析报告
产能分析报告 一、产能修改记录及主要产品信息 注:产能分析报告——修改记录 1)产能发生变化时以便及时追踪。如进行增产以达到完全生产能力,此时生产线通过一系列步骤可以达到完全生产能力,则应记录下这些变化。填写论证产能时也应同时填写日期。 2)此次产能分析报告均记作初次提交。 注:产品信息 1)完成产能分析报告的首先要明确需要分析的产品的详细信息。包括产品名称、型号、产能概况、客户需求信息等。 2)必要时应完善产品主要零部件供应商信息,以便及时掌握配套商供货情况,平衡零部件供货影响系数。 二、现有设备产能核算 1、预订工作时间标准
注: 1)单班时间:每班总时间-每班的总计可用小时数。 2)班次:表示的是每天每个工艺操作的班次数。 3)作业率:(总工时-无效工时)/总工时。 人员休息-如果在人员休息的时候,机器也停止运转,则输入每班中机器不运转的时间长度。 计划的维修时间-这是计划的每班中机器停机用于维护的时间长度。 4)年出勤时间:年出勤天数-表示的是每年的工艺运作的天数(扣除法定节假日、双休日)。 5)计算举例:每班8小时、每天2班次、作业率80%、年出勤302天,净可用时间=8*2*80%*302=时。 2、代表产品制程/线能力计算
注: 1)代表产品:所谓代表产品指产品制程包含其他所有产品制造过程包含的所有工艺过程;如存在两种以上产品包含不同工艺过程、需分别取各类型产品代表产品制程并进行线能力分析。 2)评价瓶颈工序应排除可用外协、其他生产线可用设备借代等因素影响。 3)每条生产线选取一种或2种产品作为代表说明制程及瓶颈工序即可,其他产品可直接计算毛产能。3、毛产能核算 注: 1)毛产能核算过程没有排除产品合格率、设备故障率、人员负荷等因素对产能的影响,不能作为需求平衡分析的依据,需进一步平衡。 2)其他产品可根据代表产品计算方法计算出出毛产能。
公司产能分析报告模板
公司产能分析报告模板 Revised final draft November 26, 2020
X X公司产能分析报告(模板)产能跟踪分析报告 一、现有设备产能核算 1、预订工作时间标准注: 1)单班时间:每班总时间-每班的总计可用小时数。2)班次:表示的是每天每个工艺操作的班次数。3)作业率:(总工时-无效工时)/总工时。 人员休息-如果在人员休息的时候,机器也停止运转,则输入每班中机器不运转的时间长度。计划的维修时间-这是计划的每班中机器停机用于维护的时间长度。 4)年出勤时间:年出勤天数-表示的是每年的工艺运作的天数(扣除法定节假日、双休日)。 5)计算举例:每班8小时、每天2班次、作业率80%、年出勤302天,净可用时间 =8*2*80%*302=3865.6时。 2、代表产品制程/线能力计算 注: 1)代表产品:所谓代表产品指产品制程包含其他所有产品制造过程包含的所有工艺过程;如存在两种以上产品包含不同工艺过程、需分别取各类型产品代表产品制程并进行线能力分析。 2)评价瓶颈工序应排除可用外协、其他生产线可用设备借代等因素影响。 3)每条生产线选取一种或2种产品作为代表说明制程及瓶颈工序即可,其他产品可直接计算毛产能。 3、毛产能核算 注: 1)毛产能核算过程没有排除产品合格率、设备故障率、人员负荷等因素对产能的影响,不能作为需求平衡分析的依据,需进一步平衡。 2)其他产品可根据代表产品计算方法计算出出毛产能。 4、有效产能(净产能)
注: 1)设备生产包括机器检修、保养、待料等时间,实际的工作时间达不到计划工时,且生产的产品有不良品,因此有效产能必须是以毛产能为基础,减去因停机和良率以及人员缺口等综合因素所造成的产能损失。2)总体设备利用率计算公式:OEE=设备可用性*性能效率*产品合格率。 根据来自生产验证运转的历史数据来计算总体设备利用率的(OEE)。性能效率的计算是通过计划的所需周期时间来的。如果计算单元显示的是100%或者更高,则该单元用红色进行强调。3)人员负荷率=(现有生产人员/人员配置)*100% 反映了以设备为依据的人员配备情况,这一指标在短期内直接对净产能产生影响。 二、产能需求平衡/预警机制 1、产能负荷率计算 注: 1)产能负荷率反映了企业中长期、短期需求计划对目前净产能比值的柔性指标,其作为产能预警的基础数据,对产能提升计划起指导性作用。 2)当负荷率反映3个月以内需求产能状态时,初步方案采取短期产能提升计划;3-6月以上,采取中长期产能提升计划;超过6个月以上,采取长期产能提升计划。2)预警设置采取红黄蓝三色,具体设置见(三、2)产能预警。 2、产能预警 注: 1)坐标轴纵轴表示产能,横轴为时间进度,两条黑色虚线分别表示长期扩能预警、短期扩能预警,红色实线为需求线(变化情况可参照历史数据)。 2)当需求线在短期扩能预警线以下时显示为蓝色椭圆。不设预警,不需扩能;当需求线在短期扩能预警线与长期扩能预警线之间时,设置黄色预警,采取短期产能提升计划;当红色需求线超过长期扩能预警线,并长时间处于短期最大可获得差能之上,采取红色预警,并策划中长期扩能计划。 三、需求平衡/产能提升策略 1、约束产能的解决对策 通过设置产能预警线,提前对可能产生约束的时间点提出产能扩充的对策建议,并针对各类扩充对策预留实施提前期。
公司产能分析报告范文
2014公司产能分析报告模板 一、产能修改记录及主要产品信息 注:产能 分析报告—— 修改记录 1)产能发生变化时以便及时追踪。如进行增产以达到完全生产能力,此时生产线通过一系列步骤可以达到完全生产能力,则应记录下这些变化。填写论证产能时也应同时填写日期。 2)此次产能分析报告均记作初次提交。 注:产品信息 1)完成产能分析报告的首先要明确需要分析的产品的详细信息。包括产品名称、型号、产能概况、客户需求信息等。 2)必要时应完善产品主要零部件供应商信息,以便及时掌握配套商供货情况,平衡零部件供货影响系数。 二、现有设备产能核算 1、预订工作时间标准
注: 1)单班时间:每班总时间- 每班的总计可用小时数。 2)班次:表示的是每天每个工艺操作的班次数。 3)作业率:(总工时-无效工时)/总工时。 人员休息-如果在人员休息的时候,机器也停止运转,则输入每班中机器不运转的时间长度。 计划的维修时间-这是计划的每班中机器停机用于维护的时间长度。 4)年出勤时间:年出勤天数-表示的是每年的工艺运作的天数(扣除法定节假日、双休日)。 5)计算举例:每班8小时、每天2班次、作业率80%、年出勤302天, 净可用时间=8*2*80%*302=时。 2、代表产品制程/线能力计算 注: 1)代表产品:所谓代表产品指产品制程包含其 他所有产品制造过程包含的所有工艺过程;如存在两种以上产品包含不同工艺过程、需分别取各类型产品代表产品制程并进行线能力分析。 2)评价瓶颈工序应排除可用外协、其他生产线可用设备借代等因素影响。
3)每条生产线选取一种或2种产品作为代表说明制程及瓶颈工序即可,其他产品可直接计算毛产能。 3、毛产能核算 注: 1)毛产能核算过程没有排除产品合格率、设备故障率、人员负荷等因素对产能的影响,不能作为需求平衡分析的依据,需进一步平衡。 2)其他产品可根据代表产品计算方法计算出出毛产能。 3、有效产能(净产能) 注: 1)设备生产包括机器检修、保养、待料等时间,实际的工作时间达不到计划工时,且生产的产品有不良品,因此有效产能必须是以毛产能为基础,减去因停机和良率以及人员缺口等综合因素所造成的产能损失。 2)总体设备利用率计算公式:OEE=设备可用性*性能效率*产品合格率。 根据来自生产验证运转的历史数据来计算总体设备利用率的(OEE)。性能效率的计算是通过计划的所需周期时间来的。如果计算单元显示的是100%或者更高,则该单元用红色进行强调。 3)人员负荷率=(现有生产人员/人员配置)*100%
XX公司产能分析报告(模板)
产能跟踪分析报告
一、现有设备产能核算 1、预订工作时间标准 注: 1)单班时间:每班总时间-每班的总计可用小时数。 2)班次:表示的是每天每个工艺操作的班次数。 3)作业率:(总工时-无效工时)/总工时。 人员休息-如果在人员休息的时候,机器也停止运转,则输入每班中机器不运转的时间长度。 计划的维修时间-这是计划的每班中机器停机用于维护的时间长度。 4)年出勤时间:年出勤天数-表示的是每年的工艺运作的天数(扣除法定节假日、双休日)。 5)计算举例:每班8小时、每天2班次、作业率80%、年出勤302天,净可用时间=8*2*80%*302=3865.6时。 2、代表产品制程/线能力计算 注: 1)代表产品:所谓代表产品指产品制程包含其他所有产品制造过程包含的所有工艺过程;如存在两种以上产品包含不同工艺过程、需分别取各类型产品代表产品制程并进行线能力分析。
2)评价瓶颈工序应排除可用外协、其他生产线可用设备借代等因素影响。 3)每条生产线选取一种或2种产品作为代表说明制程及瓶颈工序即可,其他产品可直接计算毛产能。3、毛产能核算 注: 1)毛产能核算过程没有排除产品合格率、设备故障率、人员负荷等因素对产能的影响,不能作为需求平衡分析的依据,需进一步平衡。 2)其他产品可根据代表产品计算方法计算出出毛产能。 4、有效产能(净产能) 注: 1)设备生产包括机器检修、保养、待料等时间,实际的工作时间达不到计划工时,且生产的产品有不良品,因此有效产能必须是以毛产能为基础,减去因停机和良率以及人员缺口等综合因素所造成的产能损失。2)总体设备利用率计算公式:OEE=设备可用性*性能效率*产品合格率。 根据来自生产验证运转的历史数据来计算总体设备利用率的(OEE)。性能效率的计算是通过计划的所需周期时间来的。如果计算单元显示的是100%或者更高,则该单元用红色进行强调。 3)人员负荷率=(现有生产人员/人员配置)*100% 反映了以设备为依据的人员配备情况,这一指标在短期内直接对净产能产生影响。 二、产能需求平衡/预警机制 1、产能负荷率计算
生产能力、设备和过程能力分析报告_2010
浙江汽车配件有限公司 设备状况、生产能力及过程能力分析报告 --生产部 Q/YX5.6-02 №:01 本公司总的生产设备有78台,其中A 类设备17 台,B类设备2 台,C类设备59 台。本公司按照2008年度设备维修计划的要求并结合实际出发,对现有的所有设备进行了定期维护保养。各关键设备得到了较好的维护,对关键设备配件、易损件也作最低安全库5套,确保设备故障停机时间降到最低。本公司通过统计分析和潜在失效模式分析对A类设备进行预知性维护,以确保设备的正常运转。从对本公司设备状况的统计结果表明,现阶段设备基本正常,能够满足现行生产需要。 本公司设备从2008.8月份-2009.3月份的质量目标统计结果如下: 这些数据表明,本公司目前的设备是受控的,设备总体趋势良好。 随着本公司对设备和新产品开发的投入,由于受国际金融危机的影响,产量也持续也处于波动状态,从2008.8月份-2009.3月份以来的产量如下: 今年从3月份以来,各车间员工都能按照设备操作规程操作,人身安全意识有很大的提高,针对冲压车间,对危险的工序,必须采用铁夹子操作,焊接车间
Q/YX5.6-02 №:02 针眼睛有危害的工序,采用戴防护眼镜,到目前为止公司没有发现一次安全事故; 在生产工装管理方面,各车间基本都能按照文件所规定的要求进行运作,只有个别的由于场地小,车间主管的意识欠缺,出现现场管理不够处于比较混乱的现象,针对此问题,由责任部门对其采取的纠正和预防措施,现已基本达到要求,现将2008年8月份至2009年2月份的工装情况统计结果如下: 至09年2月份由于全国经济不景气,造成公司员工流动性相对比较大,对新进员工对公司地各项制度不是很清楚,对公司的TS16949标准体系理解不够,出现目标偏低情况,后来通知体系不断的改进和完善,现已有较大的变化,具体情况如下: CPK均在1.33以上,完全满足顾客要求,能够适应任何顾客的需求。 生产部: 2010年3月20日
如何提高装配车间生产能力报告.doc
关于实现400台套产能报告 在这120多天的车间管理过程中,让我更进一步了解到周密的工作计划对工作指导的重要性。为了全面完成400/月台套以上的产量及各项工作指标,实现轻伤以上事故为零;根据我们农机目前的生产情况,我主要从以下几个方面分析问题: 一、数字分析。 1、各部装现场实测产量记录表I 附表I 2、部装实际操作分析 ①割台部装:共有25个零件需要装配,其中4LBA02-0331001左调节盒、4LBA02-0349300防草圈焊件、4LBA02-0310000机壳总成、4LBA02-0333002梳脱带等需要打磨装配;平均每台打磨耗费时间大概为62分钟。 ②分禾器部装:共有37个零件需要装配,主要部件4LBA02-04091208支杆焊件 I、连接板与送禾轮间隙不符合图纸要求需要打磨装配;平均每台套打磨耗费时间大概为30分钟。 ③操作架体:共有90多个零件需要装配,其中4LBA02-0752000g面板焊件与
4LBA02-0750008h操作台前罩、4LBA02-0762000f座位支架与4LBA02-0760002e 座椅罩子等需要打磨配装;平均每台打磨耗费时间大概为24分钟。 3、岗位工位器具、工具、工装等满足不了工作需要。 如割头部装标准件有17种,其中有42颗螺钉需要拧紧如果用气动板手装配速度会提高原来的2倍以上;某些零部件需要专用的工位器具来存放如提升螺旋、出谷螺旋、二次脱粒滚筒等。 二、现场生产情况 1、本岗位装配人员的技术知识不够硬,装配工艺不完善,缺少岗位作业指导书,无法统一装配工序标准。 2、生产连续性和节奏性差,不论外协还是内部提供都缺乏成套作业,若某一环节出了问题就会造成停工形成内部物流的堵塞,在相同时间间隔内不能提供生产数量相同的产品,不能均衡地完成生产,经常出现时松时紧或某一环节松散现象。 3、生产节奏太慢,主要是整机无法定型,工艺不够明确,精准,造成产量居下不上。 4、员工的积极性和主动性比较消极,主要是车间生产计划执行力度不够,整体规划缺乏周密,要一样做一样,想要什么就下什么,导致操作人员工作心情烦躁。 5、生产链不能实现一环扣一环,部门对接经常脱节,主要是生产环节控制监督不力。 6、车间没有真正实现流水线作业,造成员工容易钻空子;员工缺少专业培训。 8、职责不分明,一个人不可能实现无边界作业,一个公司有可能实施无边界化管理,但这种管理方式就会使一些人过于依赖另一个人来完成自己的职责,没有明确的分工就不会有正规化的管理,弄得一些人飞不飞,落不落,自己的事情没有处理好,相关的事情又出现了。 9、配送物料不按时,导致安排的工作易混乱,白天活少,晚上还得加班。 三、自身管理问题。我总是急急忙忙地处理一些日常性的杂事以及别的组别或部门的生产协调工作。在车间管理方面我不得不承认我是一个失败者,因为:1、车间管理实际上注重一个“检”字,多“检查、监督”,其关键在于动态管理。随时了解各车间生产进度和完成情况,当时我只注重现场零件装配问题的处理。 2、生产安排没有严密的计划性和监督性,使带班人员不知道自己的工作量和完成时间。车间管理混乱分析其原因和结果,其责任主要在我的身上,因为几个月以来我对生产管理就有所松懈,对其他管理人员存在一种依赖,觉得安排好工作
生产日报表管理规定
朔州丰泰实业有限公司生产日报表管理规定 版本号: 制定部门:安全生产部 批准日期:年月日 发布日期:年月日
生产日报表管理规定 一、目的 各生产车间按时、准确地上报生产日报,保证公司领导和相关管理部门了解掌握各车间生产情况和根据生产情况及时准确做出有关部署、调整。 二、适用范围 丰泰实业有限公司各车间 三、职责 1.安全生产部负责制定生产日报管理规定。 2.各车间负责依照生产日报管理规定按时完成生产日报。 四、规定内容 1.各车间每日上午9点之前将生产日报上报至公司安全生产部统计员,统计员在收集汇总后报相关人员。如不能按时上报,请提前通知安全生产部统计员。 2.各车间主任为各车间生产日报的第一责任人,机台班长或班长为日报表的实际负责人,负责生产日报的及时性、准确性和填写上报, 3. 公司的生产日报使用统一格式,未经同意不能随意更改(详见附件各车间《生产日报统计表》)。 4. 每月的最后一张生产日报上报后,生产部与财务、销售等部门核对数据一致后上报月度报表。 5. 设备报表中,由于设备自身原因造成的停机都需填写在机械影响或电气影响中,其他非设备原因造成的停机填写在其他原因中并备注停机原因,故障时机修确认后才可生效。(详见附件《生产设备运行日报表》)。
6.各车间的各种交接表单、记录表单、生产部统计的各种数据表单都在管理范围内。 五、考核办法 无故未按规定执行的人员每次处罚相关责任人、负责人各50元,数据不准确的处罚相关班组每一处30元。 六、本规定解释权归安全生产部,自签发之日起施行。 朔州丰泰实业有限公司 安全生产部 2014年7月3日 附件1:生产日报统计表 附件2:生产设备运行日报表
产能分析报告详解
产能规划 产能规划的步骤 1.估计未来能力需求 在进行产能规划时,首先要进行需求预测。 由于能力需求的长期计划不仅与未来的市场需求有关,海域技术变化,竞争关系以及生产率提高等多种因素有关,因此必须综合考虑。所预测的时间段越长,预测的误差可能性就越大。 在制造业企业中,企业能力经常是可以利用的设备数来表示的,在这种情况下,管理人员必须把市场需求(通常是产品产量)转变为所需的设备数。 将这些设备信息输入APS,通过APS可快速实现未来能力的评估。 2.计算需求与现有能力之间的差 当预测需求与现有能力之间的差为正数时,就需要扩大产能,当一个生产运作系统包括多个环节或多个工序时,能力扩大必须考虑到各个工序能力的平衡。当企业的生产环节很多,设备多种多样时,各个环节的所拥有的生产能力往往不一致,既有富余有瓶颈的环节。而富余的和瓶颈的环节又随着产品品种和制造工艺的改变而变化。从这个意义上来说,企业的整体生产能力是由瓶颈环节的能力所决定的,这个制定能力计划时必须注意的一个关键问题。否则的话,就会形成一种恶性循环,即,某瓶颈工序能力紧张——增加该工序能力——未增加能力的其他工序又变为瓶颈工序。 利用APS可快速发现瓶颈环节,方便企业管理者决策。 3.制定候选方案 处理能力与需求之差的方法可有多种。最简单的一种是:不考虑能力扩大,任由这部分顾客或订单失去。其他方法包括能力扩大规模和时间的多种方案,包括积极策略,消极策略或者中间策略的选择,也包括新设施地点的选择,还包括是否考虑使用加班,外包等临时措施,等等。这些都是制定能力计划方案所要考虑到内容。所考虑的重点不同,就会形成不同的候选方案。一般来说,至少应给出3-5个候选方案。 利用APS模拟排程,制定多种可供选择方案。 4.评价每个方案 评价包括两个方面:定量评价和定性评价。定量评价主要是从财务的角度,以所要进行的投资为基准,比较各种方案给企业带来的收益以及投资回收清况。这里,可使用净现值法,盈亏平衡分析法,投资回收率法等不同方法。定性评价主要是考虑不能用财务分析来判断的其他因素,例如,是否与企业的整体战略相符,与竞争策略的关系,技术变化因素,人员成本等等,这些因素的考虑,有些实际
公司生产成本分析报告
XXXX公司生产成本分析报告 根据我公司情况,现将生产、主营利润、成本进行初步分析。 一、基本情况 1、产量及其变化情况 2008年3月我公司产量为XX吨,比上年同期减产。其中,本月产量XX吨,比上年同期减产XX,本月产量XX吨,比上年同期减产XX,割板本月产量XX,比上年同期减产XX,来料加工本月生产XX吨,比上年同期减产XX%,工具本月产量XX,比上年同期减产XX%。 公司本年产量及其变化见下表 产量变化情况表 2、产品销售收入及其变化情况 2008年3月我公司实现销售收入XX元,比上年同期增长XX%。其中,公司本月生产销售收入XX元,比上年同期减少XX;其他业务收入XX元,比上年同期增长XXX。 公司本年销售收入及变化见下表 收入变化情况表 3、主营业务利润 2008年3月我公司生产实现主营业务利润XX元,比上年同期减少XX。 公司本年主营业务利润及变化见下表 利润变化情况表
4、生产成本 2008年3月我公司产品生产成本为XX元,比上年同期增长XX。 成本变化情况表 二、本月成本分析 2008年3月,我公司生产销售收入为XX元,生产成本为XX元,生产亏损XX元。其中,锻件亏损XX元,模块盈利XX元,割板盈利XX元,来料加工盈利XX元。。 1、产品总成本分析 对于产品总成本的分析,一般来说,分为按成本项目和按产品种类来分析。我们采按成本项目进行本公司的成本分析。 产品的成本由材料、人工、制造费用三部分构成。结合我公司的实际情况,便于公司管理层对成本的控制,我公司的产品成本构成可分为:直接材料、辅料、电、煤、人工、废品损失、制造费用七部分。 2008年3月我公司成本构成比率为:直接材料成本比率XX,辅料成本比率XX、电成本比率XX、煤成本比率XX、人工成本比率XX、制造费用成本比率XX、XX。2月份构成比率为:直接材料为XX、辅料为XX、电为XX、煤为XX、人工成本为XX、制造费用为XX、废品损失为XX。根据上面各项构成比率可以看出,本月构成比上月有较大变动,由于2008年2月,我国的传统节日--春节--发生在当月,造成比率有较大的变动,我们采用2008年1月为对比对象。2008年1月,我公司成本构成比率为:直接材料XX、辅料为XX、电为XX、煤为XX、人工为XX、制造费用为XX、废品损失为XX。通过3月与1月对比,可以看出本月比1月有较大变动,应当进一步查明这些变动的原因以及变动是否合理。通过对比,我们发现直接材料比率比1月增加XX,其他成本构成比率均比1月减少,甚至有些比率变动不大。我们对其中变动较大的构成比率进行分析。我公司2008年3月产量为XX吨,领用原材料XX吨,均比1月的产量为XX吨和领用的原材料XX吨多XX,而导致材料成本比率上升。因此,我们认为,材料成本的变动时不合理的。 3月的制造费用比1月减少XX,其原因为工资、修理费、劳防用品费用的减少。因此,我们认为这些变动是合理的。 在实际工作中,我们可以通过计算两个性质不同而又相关的指标的比率,来反映企业经济效益的好坏,称之为相关指标比率分析。一般来说,我们通过产值成本率、销售收入成本率、成本利润率三个比率来反映。产值成本率和销售收入成本率高的企业经济效益差,这两种比率低的企业经济效益好。而成本利润率则与之相反,成本利润率高的企业经济效益好,成本利润率低的企业经济效益差。
生产车间产能分析报告(模板)-生产车间产能表格
产能跟踪分析报告 一、现有设备产能核算 1、预订工作时间标准 注: 1)单班时间:每班总时间-每班的总计可用小时数。 2)班次:表示的是每天每个工艺操作的班次数。 3)作业率:(总工时-无效工时)/总工时。 人员休息-如果在人员休息的时候,机器也停止运转,则输入每班中机器不运转的时间长度。 计划的维修时间-这是计划的每班中机器停机用于维护的时间长度。 4)年出勤时间:年出勤天数-表示的是每年的工艺运作的天数(扣除法定节假日、双休日)。 5)计算举例:每班8小时、每天2班次、作业率80%、年出勤302天,净可用时间=8*2*80%*302=3865.6时。 2、代表产品制程/线能力计算 注: 1)代表产品:所谓代表产品指产品制程包含其他所有产品制造过程包含的所有工艺过程;如存在两种以上产
品包含不同工艺过程、需分别取各类型产品代表产品制程并进行线能力分析。 2)评价瓶颈工序应排除可用外协、其他生产线可用设备借代等因素影响。 3)每条生产线选取一种或2种产品作为代表说明制程及瓶颈工序即可,其他产品可直接计算毛产能。 3、毛产能核算 注: 1)毛产能核算过程没有排除产品合格率、设备故障率、人员负荷等因素对产能的影响,不能作为需求平衡分析的依据,需进一步平衡。 2)其他产品可根据代表产品计算方法计算出出毛产能。 4、有效产能(净产能) 注: 1)设备生产包括机器检修、保养、待料等时间,实际的工作时间达不到计划工时,且生产的产品有不良品,因此有效产能必须是以毛产能为基础,减去因停机和良率以及人员缺口等综合因素所造成的产能损失。 2)总体设备利用率计算公式:OEE=设备可用性*性能效率*产品合格率。 根据来自生产验证运转的历史数据来计算总体设备利用率的(OEE)。性能效率的计算是通过计划的所需周期时间来的。如果计算单元显示的是100%或者更高,则该单元用红色进行强调。 3)人员负荷率=(现有生产人员/人员配置)*100% 反映了以设备为依据的人员配备情况,这一指标在短期内直接对净产能产生影响。 二、产能需求平衡/预警机制 1、产能负荷率计算
生产日报表管理规定
生产日报表管理规定 TYYGROUP system office room 【TYYUA16H-TYY-TYYYUA8Q8-
朔州丰泰实业有限公司生产日报表管理规定 版本号: 制定部门:安全生产部 批准日期:年月日 发布日期:年月日
生产日报表管理规定 一、目的 各生产车间按时、准确地上报生产日报,保证公司领导和相关管理部门了解掌握各车间生产情况和根据生产情况及时准确做出有关部署、调整。 二、适用范围 丰泰实业有限公司各车间 三、职责 1.安全生产部负责制定生产日报管理规定。 2.各车间负责依照生产日报管理规定按时完成生产日报。 四、规定内容 1.各车间每日上午9点之前将生产日报上报至公司安全生产部统计员,统计员在收集汇总后报相关人员。如不能按时上报,请提前通知安全生产部统计员。 2.各车间主任为各车间生产日报的第一责任人,机台班长或班长为日报表的实际负责人,负责生产日报的及时性、准确性和填写上报, 3. 公司的生产日报使用统一格式,未经同意不能随意更改(详见附件各车间《生产日报统计表》)。 4. 每月的最后一张生产日报上报后,生产部与财务、销售等部门核对数据一致后上报月度报表。 5. 设备报表中,由于设备自身原因造成的停机都需填写在机械影响或电气影响中,其他非设备原因造成的停机填写在其他原因中并备注停机原因,故障时机修确认后才可生效。(详见附件《生产设备运行日报表》)。
6.各车间的各种交接表单、记录表单、生产部统计的各种数据表单都在管理范围内。 五、考核办法 无故未按规定执行的人员每次处罚相关责任人、负责人各50元,数据不准确的处罚相关班组每一处30元。 六、本规定解释权归安全生产部,自签发之日起施行。 朔州丰泰实业有限公司 安全生产部 2014年7月3日 附件1:生产日报统计表 附件2:生产设备运行日报表
产能分析报告及指标明细
产能分析报告及指标明细 The document was prepared on January 2, 2021
产能分析报告模板及指标明细 一、产能修改记录及主要产品信息 注:产Array能分析 报告— —修改 记录 1) 产能发 生变化 时以便 及时追踪。如进行增产以达到完全生产能力,此时生产线通过一系列步骤可以达到完全生 产能力,则应记录下这些变化。填写论证产能时也应同时填写日期。 2)此次产能分析报告均记作初次提交。 注:产品信息 1)完成产能分析报告的首先要明确需要分析的产品的详细信息。包括产品名称、型号、产能概况、客户需求信息等。 2)必要时应完善产品主要零部件供应商信息,以便及时掌握配套商供货情况,平衡零部件供货影响系数。 二、现有设备产能核算
1、预订工作时间标准 注:Array 1)单班 时间:每 班总时间 -每班的 总计可用 小时数。 2)班 次:表示 的是每天 每个工艺操作的班次数。 3)作业率:(总工时-无效工时)/总工时。 人员休息-如果在人员休息的时候,机器也停止运转,则输入每班中机器不运转的时间长度。 计划的维修时间-这是计划的每班中机器停机用于维护的时间长度。 4)年出勤时间:年出勤天数-表示的是每年的工艺运作的天数(扣除法定节假日、双休日)。 5)计算举例:每班8小时、每天2班次、作业率80%、年出勤302天,净可用时间 =8*2*80%*302=时。 2、代表产品制程/线能力计算
1)代 表产 品:所 谓代表 产品指 产品制 程包含 其他所 有产品 制造过 程包含 的所有 工艺过 程;如 存在两种以上产品包含不同工艺过程、需分别取各类型产品代表产品制程并进行线能力分析。2)评价瓶颈工序应排除可用外协、其他生产线可用设备借代等因素影响。 3)每条生产线选取一种或2种产品作为代表说明制程及瓶颈工序即可,其他产品可直接计算毛产能。 3、毛产能核算
产能分析报告及指标明细
产能分析报告模板及指标明细 一、产能修改记录及主要产品信息 注:产Array能分析 报告— —修改 记录 1) 产能发 生变化 时以便 及时追踪。如进行增产以达到完全生产能力,此时生产线通过一系列步骤可以达到完全生 产能力,则应记录下这些变化。填写论证产能时也应同时填写日期。 2)此次产能分析报告均记作初次提交。 注:产品信息 1)完成产能分析报告的首先要明确需要分析的产品的详细信息。包括产品名称、型号、产能概况、客户需求信息等。 2)必要时应完善产品主要零部件供应商信息,以便及时掌握配套商供货情况,平衡零部件供货影响系数。
二、现有设备产能核算 1、预订工作时间标准 注:Array 1)单班时 间:每班 总时间- 每班的总 计可用小 时数。 2)班次: 表示的是 每天每个 工艺操作的班次数。 3)作业率:(总工时-无效工时)/总工时。 人员休息-如果在人员休息的时候,机器也停止运转,则输入每班中机器不运转的时间长度。计划的维修时间-这是计划的每班中机器停机用于维护的时间长度。 4)年出勤时间:年出勤天数-表示的是每年的工艺运作的天数(扣除法定节假日、双休日)。5)计算举例:每班8小时、每天2班次、作业率80%、年出勤302天,净可用时间 =8*2*80%*302=3865.6时。 2、代表产品制程/线能力计算
1)代表 产品: 所谓代 表产品 指产品 制程包 含其他 所有产 品制造 过程包 含的所 有工艺 过程; 如存在 两种以上产品包含不同工艺过程、需分别取各类型产品代表产品制程并进行线能力分析。 2)评价瓶颈工序应排除可用外协、其他生产线可用设备借代等因素影响。 3)每条生产线选取一种或2种产品作为代表说明制程及瓶颈工序即可,其他产品可直接计算毛产能。 3、毛产能核算