管式热裂解反应器出口温度前馈——反馈控制系统设计
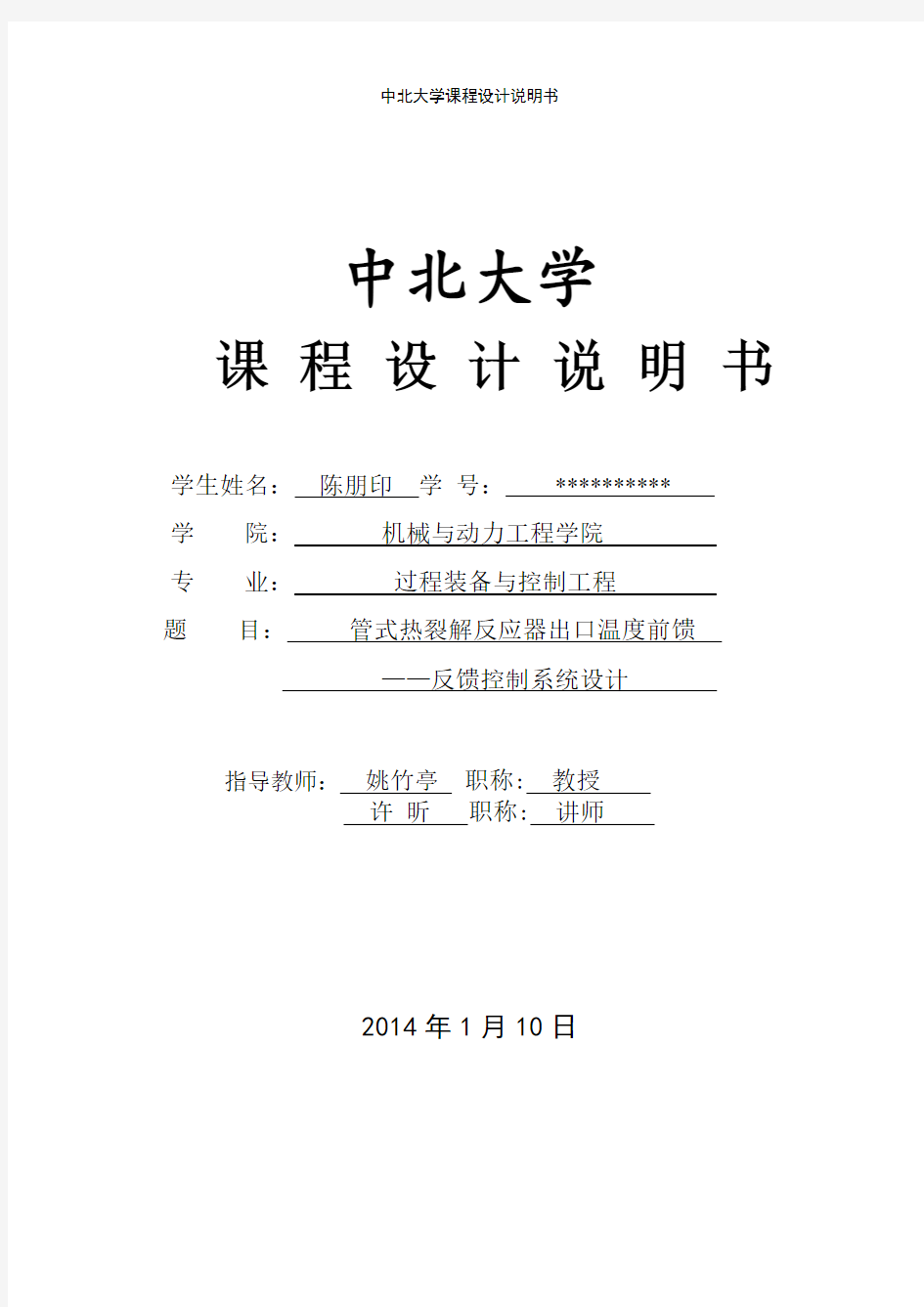
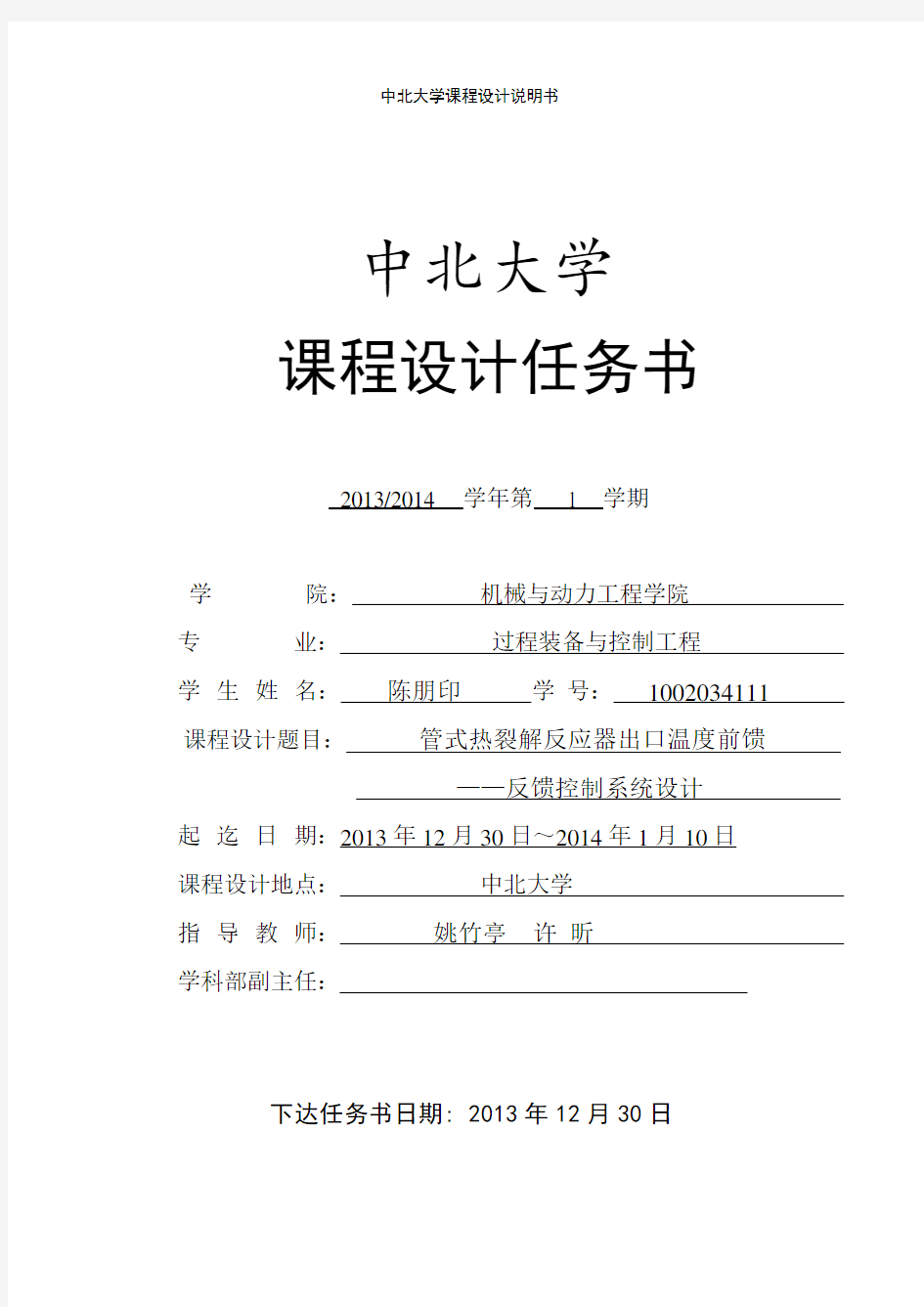
中北大学
课程设计说明书
学生姓名:陈朋印学号:1002034111
学院:机械与动力工程学院
专业:过程装备与控制工程
题目:管式热裂解反应器出口温度前馈
——反馈控制系统设计
指导教师:姚竹亭职称: 教授
许昕职称: 讲师
2014年1月10日
中北大学
课程设计任务书
2013/2014 学年第 1 学期
学院:机械与动力工程学院
专业:过程装备与控制工程
学生姓名:陈朋印学号:1002034111课程设计题目:管式热裂解反应器出口温度前馈
——反馈控制系统设计
起迄日期:2013年12月30日~2014年1月10日
课程设计地点:中北大学
指导教师:姚竹亭许昕
学科部副主任:
下达任务书日期: 2013年12月30日
课程设计任务书
目录
1管式热裂解反应器前馈-反馈控制系统概述 (7)
1.1概述 (7)
1.2 管式热裂解反应器的扰动分析 (7)
1.3 前馈-反馈控制系统 (8)
2 课程设计方案论证 (8)
2.1 控制方案1设计 (8)
2.2 控制方案2设计 (8)
2.3 控制方案3设计 (9)
3 前馈-反馈控制系统设计及器件选择 (10)
3.1 前馈—反馈控制系统设计 (10)
3.2 参数的工程整定 (14)
3.3 前馈—反馈控制系统整定 (17)
4.MATLAB系统仿真 (21)
4.1 matlab的简介 (21)
4.2simulink控制系统仿真 (21)
5 课程设计总结 (23)
6 参考文献 (23)
1 管式热裂解反应器前馈-反馈控制系统概述
1.1概述
管式热裂解反应器是主要用于烃类热裂解的反应装置。烃类热裂解过程是指石油烃类原料(天然气、炼厂气、油田气、汽油和重油)在高温(700-1000℃)、隔绝空气的条件下发生分解反应而生成碳原子数较少、相对分子质量较低的三烯(乙烯、丙烯和丁二烯)、三苯(苯、甲苯和二甲苯)等短裢烃的化学过程。管式反应器从结构上可以分为单管反应器和多管反应器,多管反应器是将多个管式电反应单元并联组装成电反应器;可以是空管,如管式裂解炉,也可以是在管内填充颗粒状催化剂的填充管,以进行多相催化反应,如列管式固定床反应器。管式反应器结构简单、加工方便,耐高压、传热面积大,特别适用于强烈放热和加压下的反应。管式应器还具有容易实现自动控制、节省动力、生产能力高等特点,因此广泛用于气相、均液相、非均液相、气液相、气固相、固相等反应过程。为保证管式反应器内具有良好的传热与传质条件, 使之接近于理想反应器,一般要求流体在管内作高速湍流运动。热裂解的原理:烃类热裂解的过程十分复杂,不仅裂解原料发生反应,而且生成物还会继续反应,同一种烃也会发生不同的反应。按反应进行的先后顺序,可以反应划分为一次反应和二次反应。本次课程设计是要完成管式热裂解反应器出口温度控制系统的设计,采用的是前馈——反馈控制。
1.2 管式热裂解器的扰动分析
管式热裂解反应器温度控系统工艺流程及控制要求管式热裂解反应器的主要任务是把原油或重油加热到一定温度,以保证下一道工序(分馏或裂解)的顺利进行。反应器的工艺流程为燃料油经过蒸汽雾化后在炉膛中燃烧,被加热油料流过炉膛四周的排管中,就被加热到出口温度。在燃料油管道上装设一个调节阀,用它来控制燃油量以达到调节温度的目的。其中燃料油压力和过热蒸汽压力都可以用专门的调节器保持其稳定,所以管式热裂解器的扰动来源于燃油压力与过热蒸汽压力,而过热蒸汽压力是主要扰动。从调节阀动作到温度改变,这中间需要相继通过炉膛、管壁和被加热油料所代表的热容积,因而反应很缓慢。工艺上对出口温度要求不高,一般希望波动范围不超过±1~2%。
1.3 前馈-反馈控制系统
反馈控制系统的输出是偏差的函数,只有出现偏差才进行调节,因此,调节不及时。如果采用某种控制策略,使该控制运算的输出是扰动的函数,则一旦出现扰动,控制系统就有输出,就能在偏差还未出现以前把扰动的影响消除,因此,调节及时。依据预防的控制策略设计的控制系统称为前馈控制系统。
前馈控制系统根据扰动进行调节;采用开环控制方式;控制器的输入信号只有一个变量,即扰动量;只能克服某个特定扰动的影响;控制器的控制规律是前馈控制规律,它与前馈广义对象特性和扰动通道特性有关,因此,只能近似实现所需控制规律,要实现绝对不变性较困难。前馈控制能及时克服特定扰动的影响,如果合适设计控制规律,可大大消弱扰动对被控变量的影响。
因此,前馈控制往往需要与反馈控制结合起来,构成前馈-控制系统。这样既发挥了前馈控制作用及时的优点,又保持了反馈控制能克服多个扰动和具有对被调节量实行反馈检验的长处。所以前馈-反馈控制是适合于过程控制的较好的方式。 2 课程设计方案论证
2.1 控制方案1设计
所谓静态前馈控制,是指前馈控制器的控制算法为比例控制,即
错误!未找到引用源。
式中,Ko 、Kv 、Km 与Kf 分别是过程控制通道、调节阀、温度变送器静态放大系数以及过程干扰通道的静态放大系数;错误!未找到引用源。,其大小由Ko 、Kv 、Km 、Kf 确定。静态前馈控制的控制目标是使被控参数最终的静态偏差接近于零,而不考虑由于两通道时间常数的不同而引起的动态偏差。由于静态前馈控制非常简单,实施方便。在实际生产中,当干扰通道与控制通道的时间常数相差不大时,应用静态前馈控制可获得较高的控制精度。
2.2 控制方案2设计
静态前馈控制系统结构简单、易于实现,但在扰动影响下动态偏差依然存在。对于扰动频繁且要严格控制动态偏差的生产过程,静态前馈不能满足生产工艺的精度要求,这种情况下宜采用动态前馈控制。
动态前馈控制必须根据过程干扰通道和控制通道的动态特性,其传递函数由式错误!未找到引用源。M v o f
b G G G G G 决定。采用动态前馈控制使扰动对被控
参数的影响在每个时刻都得到补偿,能够极大地提高控制过程的动态品质,是提高控制质量的有效手段。但动态前馈要采用专用控制器,控制规律由上式决定,结构一般比较复杂,往往无法获得精确表达式,也难以精确实现,往往只能近似处理。因此,只有在工艺对控制精度要求较高、其他控制方案又难以满足的情况下,才考虑采用动态前馈控制方案。
2.3 控制方案3设计
为了克服前馈控制的局限性,常把前馈控制和反馈控制结合起来,组成前馈-反馈复合控制系统。这样既发挥了前馈控制及时克服主要扰动对被控参数影响的优点,又保持了反馈控制能抑制各种干扰的优势,同时也降低了对前馈控制器的要求,便于工程上的实现。
当燃油流量F(s)发生变化时,前馈控制器Gb(s)及时发出控制指令,补偿燃油流量F(s)变化对管式热裂解反应器出口温度Y(s)的影响;而燃油压力、过热蒸汽压力等扰动对物料出口温度的影响,则由反馈控制器Gc(s)来克服。前馈控制作用加反馈控制作用,能够很好地克服扰动对出口温度的影响,获得比较理想的控制效果。相对于单纯的前馈控制或反馈控制,复合控制系统具有以下优点:
1.前馈控制与反馈控制组合使用,有利于对主要干扰进行前馈补偿和加其他干扰进行反馈调节,保证控制精度。
2.由于增加了反馈控制回路,降低了对前馈控制器的精度要求,有利于简化前馈控制器的设计和实现。
3.在单纯的反馈控制系统中,提高控制精度与系统稳定性是一对矛盾,往往为保证系统的稳定性而无法实现高精度的控制。而前馈-反馈控制系统既可实现高精度控制,又能保证系统稳定运行,因而在一定程度上解决了稳定性与控制精度之间的矛盾。
由于前馈控制不含时间因子,比较简单,在一般情况下,不需要专用的补偿器,单元组合仪表便可以满足使用要求。而且事实证明,滞后相位差不大的时候,应用静态前馈控制方法可以获得较高的控制精度,相比之下,由于动态前馈控制系统的结构复杂,系统的运行和参数整定过程也比较复杂,需要一套专门的补偿装置。
综上所述,由于本设计主要考虑燃油压力和燃油流量对管式热裂解反应器出口温度的影响,所以采用静态前馈-反馈控制方案。
3 前馈-反馈控制系统设计及器件选择
3.1 前馈—反馈控制系统设计
一、控制器的选择
以单片机89C51为控制器,将温度传感器得到的微弱电信号,经仪表放大器放大后,送入转换器,转化结束后,89C51读取转换结果,当管式热裂解反应器出口温度低于设定温度时,启动加热控制部件,使管式热裂解反应器出口温度升高,以满足现场要求.当管式热裂解反应器出口温度高于设定温度时,实时地切断加热源.采用单片机来对炉温实时控制不仅具有控制方便简单和灵活性大的特点,而且提高了炉温控制精度的技术要求,从而大大提高了产品的质量.
1.A/D转换器的选择
ADS774是BRR-BROWN(BB)公司设计生产的主次逼近式模数转换器,4种可选电压范围输入:0~+10V,0~+20V,-5~+5V和-10~+10V,12位或8位可选输出,单一+5V供电。
它采用低功耗COMS工艺和新的电容阵列技术,包含有内部时钟、微处理器接口、三态输出缓冲器以及若干组内部可调阻抗,功率最大为120mv,转换时间为t≤8.5 S。
ADS774可以在2种模式下工作:一种是工作过程由微处理器控制,即所谓非独立方式;一种是独立运行工作模式。
二、执行器的选择
1.调节阀工作区间的选择:正常工况下要求调节阀的开度在15﹪-85﹪之间。
2.调节阀的流量特性选择:
根据生产过程的工艺参数和对控制系统的工艺要求,应选用等百分比流量特性或抛物线流量特性。
3.调节阀的气开、气关作用方式选择:
气开阀即随着控制信号的增加而开度增大,当无压力控制信号时,阀门处于全关闭状态。
由于设计要求当物料进入管式热裂解反应器的时候,有一定的温度,当燃油
流量加大时,温度势必增加,所以阀门控制选择气开式。而当燃油流量增加时,出口温度会增加,所以控制器选择反作用,调节器应选择正作用。
控制阀按其工作能源形式可分为气动、电动和液动三类。气动控制阀用压缩空气作为工作能源,主要特点是能在易燃易爆环境中工作,广泛地应用于化工、炼油等生产过程中;电动控制阀用电源工作,其特点是能源取用方便,信号传递迅速,但难以在易燃易爆环境中工作;液动控制阀用液压推动,推力很大,一般生产过程中很少使用。
三、检测变送器的选择
1.温度检测器
热电偶作为温度传感元件,能将温度信号转换成电动势(mV)信号,配以测量毫伏的指示仪表或变送器可以实现温度的测量指示或温度信号的转换。具有稳定、复现性好、体积小、响应时间较小等优点、热电偶一般用于500°C以上的高温,可以在1600°C高温下长期使用。
热电阻也可以作为温度传感元件。大多数电阻的阻值随温度变化而变化,如果某材料具备电阻温度系数大、电阻率大、化学及物理性能稳定、电阻与温度的关系接近线性等条件,就可以作为温度传感元件用来测温,称为热电阻。热电阻分为金属热电阻和半导体热敏电阻两类。大多数金属热电阻的阻值随其温度升高而增加,而大多数半导体热敏电阻的阻值随温度升高而减少。
采用热电阻法测量温度时,一般将电阻测温信号通过电桥转换成电压,当热电阻的连接导线很长时,导线电阻对电桥的影响不容忽视。为了消除导线电阻带来的测量误差,不管热电阻和测量一边之间的距离远近,必须使导线电阻的阻值符合规定的数值,如果不足,用锰铜电阻丝凑足。同时,热电阻必须用三线接法,热电阻用三根导线引出,一根连接电源,不影响桥路的平衡,另外两根被分别置于电桥的两臂内,使引线电阻值随温度变化对电桥的影响大致抵消。
2.温度变送器
检测信号要进入控制系统,必须符合控制系统的信号标准。变送器的任务就是将检测信号转换成标准信号输出。因此,热电偶和热电阻的输出信号必须经温度变送器转换成标准信号后,才能进入控制系统,与控制器等其他仪表配合工作。
图1给出了温度变送器的原理框图,虽然温度变送器有多个品种、规格,以配合不同的传感元件和不同的量程需要,但他们的结构基本相同。
图1 温度变送器原理框图
MAT-TT系列一体化温度变送器是热电阻、热电偶与变送器的完美结合,以十分简捷的方式把-200~1300℃的温度信号转换为标准4~20mA电流信号实现对温度精确测量与控制。
MAT-TT系列温度变送器可与显示仪、控制系统、记录仪等调节器配套使用,并被广泛应用于石油、化工、发电医药、纺织、锅炉等工业领域。
仪表主要特点:
温度模块内部采用环氧树脂浇注工艺,适应于各种恶劣和危险场所使用。冷端、温漂、非线形自动补偿。液晶、数码管、指针等多种指示功能方便现场适时监控。
技术指标:
(1)基本误差:±1.0%、±0.5%、±0.25% 二线制输出、无需补偿导线。
(2)输出信号:4~20mA 抗干扰能力强、远传性能好。
(3)负载电阻:250Ω允许范围为0~500Ω结构简单、合理安装方便。
(4)供电电源:24V DC 允许范围为18~30VDC 小型化、安全可靠、使用寿命长。
(5)温度漂移:≤0.015%/℃三线制、二线制输入方法通用。
(6)环境温度:-25~60℃、相对湿度:≤95% 液晶显示现场温度,清晰度高,无视觉误差。
3.流量变送器
流量变送器采用LWQ型气体涡轮流量变送器。它吸取了国内外流量仪表先进技术经过优化设计,综合了气体力学、流体力学、电磁学等理论而自行研制开发
的新一代高精度、高可靠性的气体精密计量仪表,具有出色的低压和高压计量性能,多种信号输出方式以及对流体扰动的低敏感性,广泛适用于天然气、煤制气、液化气、轻烃气等气体的计量。该类涡轮流量产品本身不具备现场显示功能,仅将流量信号以电流信号(4-20mA)的方式远传输出。仪表价格低廉,集成度高,体积小巧,特别适用于与二次显示仪、PLC、DCS等计算机控制系统配合使用。且该类涡轮流量计具有防爆功能。
四、控制规律的选择
在控制系统中,主,副控制器起的作用不同。主控制器起定值控制作用,副控制器起随动控制作用,这是选择控制器规律的基本出发点。
主被控参数是工艺操作的主要指标,允许波动范围很小,一般要求无静差,因此,主控制器应选PID控制规律。
副被控参数的设置是为了克服主要干扰对主参数的影响,因而可以允许在一定范围的变化,并允许有静差。为此,副控制器选择P控制规律。
五、前馈—反馈控制系统的控制过程分析
图2所示为精馏塔提馏段温度为主控变量、再沸器蒸汽流量为副被控变量的串级控制系统和进料流量为前馈信号组成的相乘型前馈-反馈控制系统。图中,FC是加热蒸汽流量控制器;TY是乘法器;TC是提馏段温度控制器;FY是前馈控制器。从前馈原理角度看,进料量是扰动变量,反馈信号来自提馏段温度,前馈信号来自进料流量,反馈信号和前馈信号进行相乘运算,运算结果作为再沸器加热蒸汽流量控制器的设定。
其控制器的正、反作用选择如下:
1、主被控变量燃油流量
2、副被控变量过热水蒸气流量
3、控制阀从安全角度考虑,选择气开型控制阀,Kv>0。
4、副被控对象控制阀打开,过热水蒸气流量增加,出口温度也增加,
因此,Kp2>。
5、副控制器为保证负反馈,应满足Kc2KvKp2Km2>0,因Km2>0,应选
Kc2>0,即选用反作用控制器。
6、主被控对象当燃油流量增加时,管式热裂解反应器出口温度升高,
因此,Kp1>0。
7、主控制器为保证负反馈,应满足Kp1Kc1Km1>0,因Km1>0,应选
Kc1>0,即选用反作用控制器。
图3是该控制系统框图。图中,Gy是乘法器,即壁纸控制系统中的比值函数环节;Gff是前馈控制器,即是管式热裂解反应器出口温度控制器;Gc2是副控制器。
图 3 前馈-反馈控制系统框图
3.2 参数的工程整定
一、Kf型前馈控制器
这种模型具有比例特性,实施起来比较容易,用比例控制或比值器等常规仪表就可以实现。Kf可通过现场进行整定。当控制管道的时间常数与干扰通道的时间常数近似相等时,采用这种静态前馈控制,其控制质量将有很大的改善。
二、工程整定
静态参数Kf是前馈控制模型中最基本的参数,它对前馈控制系统中的运行状态影响很大,首先应将整定好。整定方法主要有开环整定和闭环整定。
1.开环整定
就是在系统中做单纯的静态前馈运行下加干扰,Kf值由小到大,直到被控
量回到设定值。此时,所对应的Kf更视为最佳整定值。在进行整定会有较大的误差。另外,由于系统中是处于单纯的前馈运行状态,在整定过程中,被控量失去反馈控制。为了避免Kf过大而导致被控量产生太大的影响甚至发生生产事故,所以Kf由小逐步增大。由于这种方法容易影响生产的正常进行,所以实际中应用越来越少。
2.闭环整定
可以让系统处于前馈反馈运行状态整定Kf,也可以让系统处于反馈运行的状态对Kf进行整定。需要指出的是,使用这种方法整定时,反馈控制器应有积分作用。否则,在干扰作用下,无法消除被控量的静态误差。同时也要求工况稳定,尽量减少其他干扰的影响。
3、PID参数整定
1)PID参数的选取
如果PID参数不合适,PID的调节结果可能比二位式调节的结果还差,例如产生幅度很大的连续振荡,产生长时期不能消除的静差,或者是在系统受扰动后不能尽快复原等,因此,根据被控对象的工况选取合适的PID参数,是用好PID调节仪表的关键。在大多数场合,选择P=5%,I=210秒,D=30秒,就能达到较理想的调节效果。
根据比例带XP1和振荡周期T,查上表后计算出合适的比例带、积分时间、微分时间三个参数的具体数值,再安仪表的设置步骤键入PID参数并稍作微调即可。
概括的说,比例带P设置的数值越大,系统越不会发生振荡,静差也越大;积分时间I设置的数值越大,积分的作用越不明显,消除静差所需的时间也越长,系统越不会发生振荡;微分时间D设置的数值越小,对比例带和积分的作用力越小,系统不会发生振荡,但系统的响应速度也变得迟钝。积分的作用是使系统趋向稳定,而微分的作用是抑制超调,但会使系统趋向不稳定,微分与积分配合的当,就可获得尽快而稳定的调节过程。
在管式热裂解反应器出口温度前馈-反馈控制系统中,设定值为X(s)、干扰F(s)对输出Y(s)的共同影响为
)()()()(1)()()()()()(0()()(1)()()()(s F s G s G s c G S m G s b G s v G s o G S f G s X s o G s v G s o G S o G s v G s c G s Y o v ++++=
3-1
要前馈补偿实现对Y(s)的完全补偿,上式的第二项应当为零,即
0)()()(1)()()()()(=++s o G s v G s c G s m G s b G s v G s o G s f G 3-2
即
0)()()()()(=+s m G s b G s v G s o G s f G 3-3
从而可得
)()()()()(s m G s v G s o G s f G s b G =
3-4
由3-1可知,由于反馈的存在,是干扰F(s)对输出的影响要比开环前馈控制的情况下小)()()(1[s o G s v G s c G +]倍。在系统的通频带内,控制通道往往有很大的放大倍数,即
)
()()(1s o G s v G s c G +》 1
3-5 3-5表明,本来经过开环补偿后,干扰F(s)对被控参数的影响很小,在经过反馈控制进一步减小)()()(1s G s G s G m v c +倍,这充分体现了前馈反馈的优越性。
3.2.1 前馈—反馈的模型分析
按照不变性的条件,球的前馈反馈的传递函数的表达式,即
)()()()
()(s G s G s G s G s G m v b f b -=
实际上,要得到干扰通道特性)(s G f 、控制通道)(s G o 的精确数学模型非常困难,往往无法通过计算球的准确的请按亏反馈模型。实践证明,相当数量的工业工程都具有阻尼特性,因此,常常将被控过程的控制通道和抗扰动通道用一介和
二阶的容量滞后模型来近似,必要的时候串联一个纯滞后环节,这样就为前馈控制器的模型具有了通用性创造了条件。假定控制通道特性为
s o o o e s T K s o G τ-+=1
)( 干扰通道特性为
s f f
f f e s T K G τ-+=1
则前馈控制器的模型可归结为如下形式
s b s t s f o o f s
o o s f f
o f b e s T s T K e e T s T K K e s T K e s T K s G s G s G o f o s ττττ-----++-=++-=++=-=11111
1)()()(21 式中b K 静态前馈系数。o f b K K K =;o T T =1,f T T =2,分别为控制通道与
干扰通道的时间常数, τ为干扰通道与控制通道纯滞后的时间差,o f τττ-=。
当o f ττ=时,上式写为
1
1)(21++-=T T K s G b b 若f o T T T T ===21则可改写为
b b K s G -=)(
由此可见,常用前馈控制有b K ,2121++T s T K b ,s b e T T K τ-++2121 3.3 前馈—反馈控制系统整定
前馈反馈控制系统的头动方式有两种。其一,前馈和反馈分别投运,整定后在组合起来;其二,将反馈部分先投运,待整定后,再逐渐加入前馈作用。
在整定前馈反馈控制系统时,反馈回路的前馈控制部分要分别整定。也就是说,当整定反馈回路时,只考虑闭合回路具有适当的稳定余量,而不考虑前馈部分:当整定前馈装置时,不考虑反馈控制引起的稳定性问题。对于具体的整定方法,现已常用的前馈装置2
121++T s T K b 为例,介绍如何确定静态参数b K ,动态参数
1T 和2T 。
3.3.1 b K 的整定
静态参数b K 是前馈模型中最基本的参数,它对前馈控制系统的运行状态影响很大,首先应该将它定好。主要方法有开环和闭环整定。
1)开环整定
所谓开环整定作单纯的静态前馈运行下施加干扰,b K 值由小逐渐增大时,直到被控量回到设定值,此时,所对应的b K 更视为最佳整定值。在进行整定时,应力求工矿稳定,以减小其他扰动对被控量的影响,否则,b K 值有较大误差。另外,由于系统处于单纯前馈控制状态,在整定过程中被控量推动反馈控制。为了避免由于b K 过大而导致被控时产生太大偏差、影响产生甚至发生事故,因此b K 值应由小逐步增大。由于这种方法容易影响生产的正常进行,因而在实际生产过程中应用月俩越少。
2)闭环整定
设待定的系统原理框图如图。可以让系统处于前馈—反馈运行状态整定b K ,也可以让系统处于反馈运行状态对b K 值整定。
①前馈—反馈运行状态整定b K
闭合图中开关K ,使系统处于前馈—反馈运行状态。在反馈控制已整定好的基础上,施加相同的干扰作用,由小到大的逐步改变b K 值,知道获得满意的补偿过程。b K 值对补偿的影响如图4所示,图中(b )曲线为b K 值刚好适当。如此时的b K 值较小,将照成欠补偿所示,如图(a ),所示,若b K 值过大则造成过补偿,如图c
图 4 b K 闭环整定系统框图
a b c
②反馈运行状态整定b K
打开图中的开关K ,使系统处于反馈运行状态。待系统稳定后,记下干扰变送器的输出电流Id0和反馈控制器的输出稳定值Ic0。然后,对干扰 d 施加加一增量△d ,待反馈终止系统在△d 的作用下,被控变量重新回到设定值时,重新记下干扰变送器的输出Id 及反馈控制器的输出Ic ,则前馈控制器的静态放大系数Kb 为: 0
0d d c c b I I I I K --= 式中的物理含义十分的明显。当干扰量为△d 时,由反馈控制器产生的矫校正作用改变了(Ic-Ic0),才能使被控量回到设定值,如果前馈控制器来校正,那么Kb 值也必须满足这一关系式。
需指出的是,在使用这种方法整定Kb 时,反馈控制器应具有积分作用。否则,在干扰作用下,无法消除被控时量的静差。同时,要求工况稳定,尽量减
少其他干扰的影响。
3.3.2 T1,T2的整定
动态参数决定了动态补偿程度,当T1﹥T2时,前馈控制在动态补偿过程中起超前作用,当T1﹤T2时,起之后作用;当T1=T2的时候只有静态前馈作用。因此,常将T1为超前时间,T2称为滞后时间。根据校正作用在世超前或滞后,便可以决定T1、T2的数值。当T1过大时,由于过补偿而使过渡过程曲线反向超调过高,因此从生产安全的角度出发,前馈控制器的动态参数应从欠补偿开始,按照过渡过程曲线变化的趋势,逐渐试凑逼近。也可以在初次实验时,去T1/T2=2或T1/T2=0.5的数值进行,施加干扰观察补偿过程,首先调整T1或T2,使过补偿曲线达到上、下偏差面积相等,然后再调整T1与T2的比值,直到获得平坦的补偿过度曲线。
3.3.3调节器参数整定方法
1) 稳定边界法
其要点是将调节器设置成纯比例作用,将系统投入自动与运行并将比例带由大到小的改变,直到系统产生等振幅震荡为止。这时控制系统处于边界稳定状态,记下此状态下的比例带值,即临界比例带K δ以及振荡周期K T ,然后根据经验公式算出比例调节的各个参数。
2) 衰减曲线法
衰减曲线法是利用比例作用下产生的4:1衰减振荡(75.0=ψ)过程时的调节器比例带s δ及过程衰减周期s T ,或(10:1)衰减振荡过程时调节器比例带s δ及过程上升时间s T ,根据经验公式计算出调节器的各个参数。
3) 响应曲线法
响应曲线法是在系统处于开环状态下,作对象的阶跃扰动实验,根据记录下的节约响应曲线求取一组特征参数ε、β、τ(有自平衡能力的对象),再根据经验公式计算调节器的各个参数。
4)经验法
通过长期实践,人们总结了一套参数整定经验,称之为经验法。经验法可以说是根据经验进行参数试凑得方法,它首先根据经验设置一组调节
基于PLC的温度控制闭环系统
1 绪论 1.1 课题背景 随着现代工业的逐步发展,在工业生产中,温度、压力、流量和液位是四种最常见的过程变量。其中,温度是一个非常重要的过程变量。例如:在冶金工业、化工工业、电力工业、机械加工和食品加工等许多领域,都需要对各种加热炉、热处理炉、反应炉和锅炉的温度进行控制[1]。这方面的应用大多是基于单片机进行PID控制,然而单片机控制的DDC系统软硬件设计较为复杂,特别是涉及到逻辑控制方面更不是其长处,然而PLC在这方面却是公认的最佳选择。 随着PLC功能的扩充在许多PLC控制器中都扩充了PID控制功能,因此在逻辑控制与PID控制混合的应用场所中采用PLC控制是较为合理的,通过采用PLC来对它们进行控制不仅具有控制方便、简单和灵活性大的优点,而且可以大幅度提高被测温度的技术指标,从而能够大大提高产品的质量和数量。因此,PLC对温度的控制问题是一个工业生产中经常会遇到的控制问题。这也正是本课题所重点研究的内容。 1.2 研究的主要内容 本课题的研究内容主要有: 1)温度的检测; 2)采用PLC进行恒温控制; 3)PID算法在PLC中如何实现; 4)PID参数对系统控制性能的影响; 5)温控系统人机界面的实现。
2 基于PLC的炉温控制系统的硬件设计 2.1系统控制要求 本PLC温度控制系统的具体指标要求是:对加热器加热温度调整范围为0℃—150℃,温度控制精度小于3℃,系统的超调量须小于15%。软件设计须能进行人机对话,考虑到本系统控制对象为电炉,是一个大延迟环节,且温度调节范围较宽,所以本系统对过渡过程时间不予要求。 2.2系统设计思路 根据系统具体指标要求,可以对每一个具体部分进行分析设计。整个控制系统分为硬件电路设计和软件程序设计两部分。 系统硬件框图结构如图所示: 图2.1系统硬件框图 被控对象为炉内温度,温度传感器检测炉内的温度信号,经温度变送器将温度值转换成0~10V的电压信号送入PLC模块。PLC把这个测量信号与设定值比较得到偏差,经PID运算后,发出控制信号,经调压装置输出交流电压用来控制电加热器的端电压,从而实现炉温的连续控制。 2.3系统的硬件配置 2.3.1 S7-200PLC选型 S7-200 系列 PLC 是由德国西门子公司生产的一种超小型系列可编程控制器,它能够满足多种自动化控制的需求,其设计紧凑,价格低廉,并且具有良好的可扩展性以及强大的指令功能,可代替继电器在简单的控制场合,也可以用于复杂的自动化控制系统。由于它具有极强的通信功能,在大型网络控制系统中也能充分发挥作用[2] S7-200系列可以根据对象的不同, 可以选用不同的型号和不同数量的模块。并可以将这些模块安装在同一机架上。 SiemensS7-200 主要功能模块介绍: (1)CPU 模块S7-200的CPU 模块包括一个中央处理单元,电源以及数字I/O 点,这些都被集成在一个紧凑,独立的设备中。CPU 负责执行程序,输入部分从现场设备中采集信号,输出部分则输出控制信号,驱动外部负载.从 CPU 模块的功能来看, CPU
自动控制原理课程设计速度伺服控制系统设计样本
自动控制原理课程设计题目速度伺服控制系统设计 专业电气工程及其自动化 姓名 班级 学号 指引教师 机电工程学院 12月
目录一课程设计设计目 二设计任务 三设计思想 四设计过程 五应用simulink进行动态仿真六设计总结 七参照文献
一、课程设计目: 通过课程设计,在掌握自动控制理论基本原理、普通电学系统自动控制办法基本上,用MATLAB实现系统仿真与调试。 二、设计任务: 速度伺服控制系统设计。 控制系统如图所示,规定运用根轨迹法拟定测速反馈系数' k,以 t 使系统阻尼比等于0.5,并估算校正后系统性能指标。 三、设计思想: 反馈校正: 在控制工程实践中,为改进控制系统性能,除可选用串联校正方式外,经常采用反馈校正方式。常用有被控量速度,加速度反馈,执行机构输出及其速度反馈,以及复杂系统中间变量反馈等。反馈校正采用局部反馈包围系统前向通道中一某些环节以实现校正,。从控制观点来看,采用反馈校正不但可以得到与串联校正同样校正效果,并且尚有许多串联校正不具备突出长处:第一,反馈校正能有效地变化
被包围环节动态构造和参数;第二,在一定条件下,反馈校正装置特性可以完全取代被包围环节特性,反馈校正系数方框图从而可大大削弱这某些环节由于特性参数变化及各种干扰带给系统不利影响。 该设计应用是微分负反馈校正: 如下图所示,微分负反馈校正包围振荡环节。其闭环传递函数为 B G s ()=00t G s 1G (s)K s +()=22t 1T s T K s ζ+(2+)+1 =22'1T s 21Ts ζ++ 试中,'ζ=ζ+t K 2T ,表白微分负反馈不变化被包围环节性质,但由于阻尼比增大,使得系统动态响应超调量减小,振荡次数减小,改进了系统平稳性。 微分负反馈校正系统方框图
空调自动化控制原理.
空调自动化控制原理说明 自动化系统是智能建筑的一个重要组成部分。楼宇自动化系统的功能就是对大厦内的各种机电设施,包括中央空调、给排水、变配电、照明、电梯、消防、安全防范等进行全面的计算机监控管理。其中,中央空调的能耗占整个建筑能耗的50%以上,是楼宇自动化系统节能的重点[1]。由于中央空调系统十分庞大,反应速度较慢、滞后现象较为严重,现阶段中央空调监控系统几乎都采用传统的控制技术,对于工况及环境变化的适应性差,控制惯性较大,节能效果不理想。传统控制技术存在的问题主要是难以解决各种不确定性因素对空调系统温湿度影响及控制品质不够理想。而智能控制特别适用于对那些具有复杂性、不完全性、模糊性、不确定性、不存在已知算法和变动性大的系统的控制。“绿色建筑”主要强调的是:环保、节能、资源和材料的有效利用,特别是对空气的温度、湿度、通风以及洁净度的要求,因此,空调系统的应用越来越广泛。空调控制系统涉及面广,而要实现的任务比较复杂,需要有冷、热源的支持。空调机组内有大功率的风机,但它的能耗很大。在满足用户对空气环境要求的前提下,只有采用先进的控制策略对空调系统进行控制,才能达到节约能源和降低运行费用的目的。以下将从控制策略角度对与监控系统相关的问题作简要讨论。 2 空调系统的基本结构及工作原理 空调系统结构组成一般包括以下几部分[2] [3]:
(1) 新风部分 空调系统在运行过程中必须采集部分室外的新鲜空气(即新风),这部分新风必须满足室内工作人员所需要的最小新鲜空气量,因此空调系统的新风取入量决定于空调系统的服务用途和卫生要求。新风的导入口一般设在周围不受污染影响的地方。这些新风的导入口和空调系统的新风管道以及新风的滤尘装置(新风空气过滤器)、新风预热器(又称为空调系统的一次加热器)共同组成了空调系统的新风系统。 (2) 空气的净化部分 空调系统根据其用途不同,对空气的净化处理方式也不同。因此,在空调净化系统中有设置一级初效空气过滤器的简单净化系统,也有设置一级初效空气过滤器和一级中效空气过滤器的一般净化系统,另外还有设置一级初效空气过滤器,一级中效空气过滤器和一级高效空气过滤器的三级过滤装置的高净化系统。 (3) 空气的热、湿处理部分 对空气进行加热、加湿和降温、去湿,将有关的处理过程组合在一起,称为空调系统的热、湿处理部分。在对空气进行热、湿处理过程中,采用表面式空气换热器(在表面式换热器内通过热水或水蒸气的称为表面式空气加热器,简称为空气的汽水加热器)。设置在系统的新风入口,一次回风之前的空气加热器称为空气的一次加热器;设置在降温去湿之后的空气加热器,称为空气的二次加热器;设置
反应器串级控制系统整定
西华大学课程设计说明书 目录 1 前言 (1) 2 总体方案设计 (2) 2.1 方案比较 (2) 2.2 方案选择 (5) 3 反应器串级控制系统分析 (6) 3.1 被控变量和控制变量的选择 (6) 3.2 主、副回路的设计 (6) 3.3 主、副控制器正、反作用的选择 (8) 3.4 控制系统方框图 (8) 3.5 分析被控对象特性及控制算法的选择 (9) 4 串级控制系统的参数整定 (10) 4.1 参数整定方法 (10) 4.2 参数整定 (11) 4.3 两步法的整定步骤 (12) 5 MATLAB仿真 (14)
5.1 控制系统的MATLAB仿真 (14) 5.2 串级控制系统PID参数整定: (16) 5 结论 (20) 6 总结与体会 (21) 7 参考文献 (22) 1 前言 反应器(或称反应釜)是化工生产中常用的典型设备,种类很多。化学反应器在结构、物料流程、反应机理、传热、传质等方面存在差异,使自控的难易程度相差很大,自控方案差别也比较大。 夹套式反应器是一类重要的化工生产设备,由于化学反应过程伴有许多化学和物理现象以及能量、物料平衡和物料、动量、热量和物质传递等过程,因此夹套反应器操作一般都比较复杂,夹套反应器的自动控制就尤为重要,他直接关系到产品的质量、产量和安全生产。 化工生产过程通常可划分为前处理、化学反应及后处理三个工序。前处理工序为化学反应做准备,后处理工序用于分离和精制反应产物,而化学反应工序通常是整个生产过程的关键,因此在化学反应工序中设计一套比较完善的控制系统是很重要的。 设计夹套式反应器的控制方案应从质量指标,物料平衡和能量平衡,约束条件三个方面考虑(假设在本反应器中反应物为一般性的,无腐蚀,无爆炸的液液反应物)。
51系列单片机闭环温度控制 实验报告
成绩: 重庆邮电大学 自动化学院综合实验报告 题目:51系列单片机闭环温度控制 学生姓名:蒋运和 班级:0841004 学号:2010213316 同组人员:李海涛陈超 指导教师:郭鹏 完成时间:2013年12月
一、实验名称: 51系列单片机闭环温度控制实验 ——基于Protuse仿真实验平台实现 基本情况: 1. 学生姓名: 2. 学号: 3. 班级: 4. 同组其他成员: 二、实验内容(实验原理介绍) 1、系统基本原理 计算机控制技术实训,即温度闭环控制,根据实际要求,即加温速度、超调量、调节时间级误差参数,选择PID控制参数级算法,实现对温度的自动控制。 闭环温度控制系统原理如图: 2、PID算法的数字实现 本次试验通过8031通过OVEN 是模拟加热的装置,加一定的电压便开始不停的升温,直到电压要消失则开始降温。仿真时,U形加热器为红色时表示正在加热,发红时将直流电压放过来接,就会制冷,变绿。T端输出的是电压,温度越高,电压就越高。
8031对温度的控制是通过可控硅调控实现的。可控硅通过时间可以通过可控硅控制板上控制脉冲控制。该触发脉冲想8031用软件在P1.3引脚上产生,受过零同步脉冲后经光偶管和驱动器输送到可控硅的控制级上。偏差控制原理是要求对所需温度求出偏差值,然后对偏差值处理而获得控制信号去调节加热装置的温度。 PID控制方程式: 式中e是指测量值与给定值之间的偏差 TD 微分时间 T 积分时间 KP 调节器的放大系数 将上式离散化得到数字PID位置式算法,式中在位置算法的基础之上得到数字PID 增量式算法: 3、硬件电路设计 在温度控制中,经常采用是硬件电路主要有两大部分组成:模拟部分和数字部分,对这两部分调节仪表进行调节,但都存在着许多缺点,用单片机进行温度控制使构成的系统灵活,可靠性高,并可用软件对传感器信号进行抗干拢滤波和非线性补偿处理,可大大提高控制质量和自动化水平;总的来说本系统由四大模块组成,它们是输入模块、单片机系统模块、计算机显示与控制模块和输出控制模块。输入模块主要完成对温度信号的采集和转换工作,由温度传感器及其与单片机的接口部分组成。利用模拟加热的
(完整word版)基于51单片机的温度控制系统设计
基于51单片机的水温自动控制系统 0 引言 在现代的各种工业生产中 ,很多地方都需要用到温度控制系统。而智能化的控制系统成为一种发展的趋势。本文所阐述的就是一种基于89C51单片机的温度控制系统。本温控系统可应用于温度范围30℃到96℃。 1 设计任务、要求和技术指标 1.1任务 设计并制作一水温自动控制系统,可以在一定范围(30℃到96℃)内自动调节温度,使水温保持在一定的范围(30℃到96℃)内。 1.2要求 (1)利用模拟温度传感器检测温度,要求检测电路尽可能简单。 (2)当液位低于某一值时,停止加热。 (3)用AD转换器把采集到的模拟温度值送入单片机。 (4)无竞争-冒险,无抖动。 1.3技术指标 (1)温度显示误差不超过1℃。 (2)温度显示范围为0℃—99℃。 (3)程序部分用PID算法实现温度自动控制。 (4)检测信号为电压信号。 2 方案分析与论证 2.1主控系统分析与论证 根据设计要求和所学的专业知识,采用AT89C51为本系统的核心控制器件。AT89C51是一种带4K字节闪存可编程可擦除只读存储器的低电压,高性能CMOS 8位微处理器。其引脚图如图1所示。 2.2显示系统分析与论证 显示模块主要用于显示时间,由于显示范围为0~99℃,因此可采用两个共阴的数码管作为显示元件。在显示驱动电路中拟订了两种设计方案: 方案一:采用静态显示的方案 采用三片移位寄存器74LS164作为显示电路,其优点在于占用主控系统的I/O口少,编程简单且静态显示的内容无闪烁,但电路消耗的电流较大。 方案二:采用动态显示的方案 由单片机的I/O口直接带数码管实现动态显示,占用资源少,动态控制节省了驱动芯片的成本,节省了电 ,但编程比较复杂,亮度不如静态的好。 由于对电路的功耗要求不大,因此就在尽量节省I/O口线的前提下选用方案一的静态显示。
反应釜温度过程控制课程设计
过程控制系统课程课题:反应釜温度控制系统 系另I」:电气与控制工程学院 专业:自动化_____________ 姓名: ________ 彭俊峰_____________ 学号:__________________ 指导教师: _______ 李晓辉_____________ 河南城建学院 2016年6月15日
反应器是任何化学品生产过程中的关键设备,决定了化工产品的品质、品种和生产能力。釜式反应器是一种最为常见的反应器,广泛的应用于化工生产的各个领域。釜式反应器有一些非常重要的过程参数,如:进料流量(进料流量比)、液体反应物液位、反应压力、反应温度等等。对于这些参数的控制至关重要,其不但决定着产品的质量和生产的效率,也很大程度上决定了生产过程的安全性。 由于非线性和温度滞后因素很多,使得常规方法对釜式反应器的控制效果不是很理想。本文以带搅拌釜式反应器的温度作为工业生产被控对象,结合PID 控制方式,选用FX2N-PLC 调节模块,同时为了提高系统安全性,设计了报警和紧急停车系统,最终设计了一套反应釜氏的温度过程控制系统。
1系统工艺过程及被控对象特性选取 被控对象的工艺过程 本设计以工业常见的带搅拌釜式反应器(CSTR)为过程系统被控对象。 反应器为标准3盆头釜,反应釜直径1000mm,釜底到上端盖法兰高度1376mm, 反应器总容积,耐压。为安全起见,要求反应器在系统开、停车全过程中压力不超过。反应器压力报警上限组态值为。反应器的工艺流程如图1-1所示。 S8Q A a珑厲娜口 图1-1釜式反应器工艺流程图 该装置主要参数如表1-1所示。各个阀门的设备参数如表1-2所示,其中,D g为阀门公称直径、K v为国际标准流通能力。 表1-1主要测控参数表
自动控制系统概要设计
目录 1引言 (3) 1.1编写目的 (3) 1.2背景 (3) 1.3技术简介 (4) https://www.360docs.net/doc/2c4947166.html,简介 (4) 1.3.2SQL Server2008简介 (5) 1.3.3Visual Studio2010简介 (5) 1.4参考资料 (6) 2总体设计 (8) 2.1需求规定 (8) 2.2运行环境 (8) 2.3数据库设计 (8) 2.3.1数据库的需求分析 (9) 2.3.2数据流图的设计 (9) 2.3.3数据库连接机制 (10) 2.4结构 (11) 2.5功能需求与程序的关系 (11) 3接口设计 (12) 3.1用户接口 (12) 3.2外部接口............................................................................................错误!未定义书签。 3.3内部接口............................................................................................错误!未定义书签。4运行设计.....................................错误!未定义书签。 4.1运行模块组合....................................................................................错误!未定义书签。 4.2运行控制............................................................................................错误!未定义书签。 4.3运行时间............................................................................................错误!未定义书签。5测试 (13)
空调自控系统方案设计(江森自控)
沈阳利源轨道交通设备有限公司暖通空调自控系统项目 HVAC暖通空调自控系统 技术方案设计书
一. 总体设计方案 根据用户对项目要求,并结合沈阳建筑智能化建筑现状,沈阳利源轨道交通装备有限公司暖通空调自控系统项目是屹今为止整个沈阳所有建筑物厂区当中智能化程度要求较高的。沈阳利源轨道交通装备有限公司暖通空调自控系统项目里面分布着大量的暖通空调机电设备。 ?如何将这些暖通空调机电设备有机的结合起来,达到集中监测和控制,提高设备的无故障时间,给投资者带来明显的经济效益; ?如何能够使这些暖通空调机电设备经济的运行,既能够节能,又能满足工作要求,并在运行中尽快的将效益体现出来; ?如何提高综合物业管理综合水平,将现代化的的计算机技术应用到管理上提高效率。 这是目前业主关心的也是我们设计所侧重的。 沈阳利源轨道交通装备有限公司暖通空调楼宇自动化控制系统的监测和控制主要包括下列子系统: 冷站系统 空调机组系统 本暖通空调楼宇自动化控制系统之设计是依据沈阳利源轨道交通设备有限公司暖通空调自控系统项目的设计要求配置的,主体的设计思想是结合招标文件及设计图纸为准。 1.1冷站系统 (1)控制设备内容 根据项目标书要求,暖通自控系统将会对以下冷站系统设备进行监控:监控设备监控内容 冷却水塔(2台)启停控制、运行状态、故障报警、手 自动状态。 冷却水泵(2台)启停控制、运行状态、故障报警、手
自动状态、水流开关状态; 冷却水供回水管路供水温度、回水温度, 冷水机组(2台)启停控制、运行状态、故障报警、手 自动状态; 冷冻水泵(2台)启停控制、运行状态、故障报警、手 自动状态、水流开关状态; 冷冻水供回水管路供水温度、回水温度、回水流量; 分集水器分水器压力、集水器压力、压差旁通 阀调节; 膨胀水箱高、低液位检测; 有关系统的详细点位情况可参照所附的系统监控点表。 (2)控制说明 本自控系统针对冷站主要监控功能如下: 监控内容控制方法 冷负荷需求计算根据冷冻水供、回水温度和回水流量测量值,自动计算建筑空 调实际所需冷负荷量。 机组台数控制根据建筑所需冷负荷自动调整冷水机组运行台数,达到最佳节 能目的。 独立空调区域负荷计算根据Q=C*M*(T1-T2) T1=分回水管温度,T2=分供水总管温度, M=分回水管回水流量 当负荷大于一台机组的15%,则第二台机组运行。 机组联锁控制启动:冷却塔蝶阀开启,冷却水蝶阀开启,开冷却水泵,冷冻 水蝶阀开启,开冷冻水泵,开冷水机组。停止:停冷水机组, 关冷冻泵,关冷冻水蝶阀,关冷却水泵,关冷却水蝶阀,关冷 却塔风机、蝶阀。 冷却水温度控制根据冷却水温度,自动控制冷却塔风机的启停台数,并且自
温度自动控制系统的设计毕业设计论文
北方民族大学学士学位论文论文题目:温度自动控制系统的设计 北方民族大学教务处制
毕业设计(论文)原创性声明和使用授权说明 原创性声明 本人郑重承诺:所呈交的毕业设计(论文),是我个人在指导教师的指导下进行的研究工作及取得的成果。尽我所知,除文中特别加以标注和致谢的地方外,不包含其他人或组织已经发表或公布过的研究成果,也不包含我为获得及其它教育机构的学位或学历而使用过的材料。对本研究提供过帮助和做出过贡献的个人或集体,均已在文中作了明确的说明并表示了谢意。 作者签名:日期: 指导教师签名:日期: 使用授权说明 本人完全了解大学关于收集、保存、使用毕业设计(论文)的规定,即:按照学校要求提交毕业设计(论文)的印刷本和电子版本;学校有权保存毕业设计(论文)的印刷本和电子版,并提供目录检索与阅览服务;学校可以采用影印、缩印、数字化或其它复制手段保存论文;在不以赢利为目的前提下,学校可以公布论文的部分或全部内容。 作者签名:日期:
学位论文原创性声明 本人郑重声明:所呈交的论文是本人在导师的指导下独立进行研究所取得的研究成果。除了文中特别加以标注引用的内容外,本论文不包含任何其他个人或集体已经发表或撰写的成果作品。对本文的研究做出重要贡献的个人和集体,均已在文中以明确方式标明。本人完全意识到本声明的法律后果由本人承担。 作者签名:日期:年月日 学位论文版权使用授权书 本学位论文作者完全了解学校有关保留、使用学位论文的规定,同意学校保留并向国家有关部门或机构送交论文的复印件和电子版,允许论文被查阅和借阅。本人授权大学可以将本学位论文的全部或部分内容编入有关数据库进行检索,可以采用影印、缩印或扫描等复制手段保存和汇编本学位论文。 涉密论文按学校规定处理。 作者签名:日期:年月日 导师签名:日期:年月日
化学反应器自动控制系统设计
目录 摘要.............................................................................................................................III 1 关于化学反应 (1) 2 关于化学反应器 (2) 2.1 反应器的类型 (2) 2.2 反应器的性能指标 (2) 2.3 反应器的控制要求 (2) 3 反应器的控制方案 (4) 3.1 反应器常用的控制方式 (4) 3.2 温度被控变量的选择 (5) 3.3 控制系统的选择 (6) 4 反应器串级系统的控制原理 (9) 4.1 系统方框图 (9) 4.2 系统原理分析 (9) 5 反应器的部分实现 (11) 5.1 原料的比值控制 (11) 5.2 仪器仪表的选择 (12) 6 设计总结与展望 (13) 参考文献 (14)
化学反应器自动控制系统设计 1 关于化学反应 化学反应的本质是物质的原子、离子重新组合,使一种或者几种物质变成另一种或几种物质。化学反应过程具备以下特点: 1) 化学反应遵循物质守恒和能量守恒定律。因此,反应前后物料平衡,总热量也平衡; 2) 反应严格按反应方程式所示的摩尔比例进行; 3) 化学反应过程中,除发生化学变化外,还发生相应的物理等变化,其中比较重要的有热量和体积的变化; 4) 许多反应应需在一定的温度、压力和催化剂存在等条件下才能进行。 此外,反应器的控制方案决定于化学反应的基本规律: 1.化学反应速度 化学反应速度定义为:单位时间单位容积内某一部分A 生成或反应掉的摩尔数,即 t A A Vd dn r 1± = (1-1) 若容积V 为恒值,则有 dt dC dt V dn r A A A ±=± =/ (1-2) 式中 r A ——组分A 的反应速度,mol/m 3·h ; n A ——组分A 的摩尔数,mol ; C A ——组分A 的摩尔浓度,mol/m 3; V ——反应容积,m 3。 2.影响化学反应速度的因素 实验和理论表明,反应物浓度(包括气体浓度,溶液浓度等)对化学反应速度有关键作用。温度对化学反应速度影响较为复杂,最普遍的是反应速度与温度成正比。而对于气相反应或有气相存在的反应,增大压力(压强)会加速反应的进行。化学反应还受催化剂,反应深度等因素的影响,这些都是要在设计反应器是需要考虑的。
5.2 闭环电子控制系统的设计与应用(1)
如图所示是JN6201集成电路鸡蛋孵化温度控制器电路图,根据该原理图完成1~3题。 1.该电路图作为控制系统的控制(处理)部分是IC JN6201,当JN6201集成输出9脚长时间处于高电平,三极管V2处于截止状态,继电器释放,电热丝通电加热。 2.安装好调试时,先将温度传感器Rt1放入37℃水中,调整电位器Rp1,使继电器触点J-2吸合,再将温度传感器Rt2放入39℃水中,调整Rp2,使继电器触点J-2释放。 3.调试时发现,不管电位器Rp1和Rp2怎么调,继电器J 始终吸合,检查电路元器件安装和接线都正确,用万用表测三极管V2集电极电位,在不同的调试状态分别为2.8V 和0V ,可知电路发生故障的原因是( B ) A.二极管V6内部断路 B.三极管V3内部击穿(短路) C.电阻R4与三极管V3基极虚焊 D.继电器线圈内部短路 如图所示是运算放大器鸡蛋孵化温度控制器电路图,根据该原理完成4~6题。 4.该电路作为控制系统的输出部分是继电器J 、电热丝等,当电路中集成运放2脚的电位低于3脚的电位,三极管V3处于饱和状态,继电器J 吸合,电热丝通电加热。 上限 V2饱和导通时候Uce 电压降0.2V ,所以留下来给集电极2.8V ,截止时候0V
5.安装好后调试时,将温度传感器Rt 放入39℃水中,调R4,使电压U2=U3,集成运放输出端6脚的电压为0V ,电路实现39℃单点温度控制。 6.调试时发现,将温度传感器Rt 放入高于39℃水中,继电器吸合;将温度传感器Rt 放入低于39℃水中,继电器释放,出现该故障现象的原因可能是( A ) A.集成运放2脚与3脚接反 B.二极管V4接反 C.电阻R2断路 D.三极管V3损坏 如图所示是晶体管组成的水箱闭环电子控制系统电路,根据该原理图完成7~9题。 7.该电路作为控制系统被控对象的是水箱内的水,水箱的水位从a 点降到b 点的过程中,三极管V1处于饱和状态,三极管V2处于截止状态,继电器触点J-1处于吸合状态。 8.安装调试时,将三个水位探头按图中的高低放入空玻璃杯中,如果电路正常,电路通电后,继电器J 吸合;向玻璃杯中加水,到达a 点时,继电器J 释放;接着将玻璃杯中的水排出,水位降到b 点以上时,继电器J 释放;水位降到b 点以下时,继电器J 吸合。 9.调试时发现,玻璃杯中的水位在b 点以下时,继电器J 就吸合;水位加到b 点,继电器J 就释放。出现该故障现象的原因是( D ) A.继电器J 没用 B.三极管V1损坏 C.二极管V3接反 D.电路没接J-1触点,b 点直接接到了电阻R1 如图所示是555集成电路组成的水箱水位闭环电子控制系统电路图, (第4~6题) (第7~9题) R4 10k ?R5 4.7k R3 4.7k
液位自动控制系统设计与调试
液位自动控制系统设计 与调试 Company number:【WTUT-WT88Y-W8BBGB-BWYTT-19998】
课程设计 2016年6月17日
电气信息学院 课程设计任务书 课题名称液位自动控制系统设计与调试 姓名专业班级学号 指导老师沈细群 课程设计时间2016年6月6日~2016年6月17日(第15~16周) 教研室意见同意开题。审核人:汪超林国汉 一.课程设计的性质与目的 本课程设计是自动化专业教学计划中不可缺少的一个综合性教学环节,是实现理论与实践相结合的重要手段。它的主要目的是培养学生综合运用本课程所学知识和技能去分析和解决本课程范围内的一般工程技术问题,建立正确的设计思想,掌握工程设计的一般程序和方法。通过课程设计使学生得到工程知识和工程技能的综合训练,获得应用本课程的知识和技术去解决工程实际问题的能力。 二. 课程设计的内容 1.根据控制对象的用途、基本结构、运动形式、工艺过程、工作环境和控制要求,确定控制方案。 2.绘制水箱液位系统的PLC I/O接线图和梯形图,写出指令程序清单。 3.选择电器元件,列出电器元件明细表。 4.上机调试程序。 5.编写设计说明书。 三. 课程设计的要求 1.所选控制方案应合理,所设计的控制系统应能够满足控制对象的工艺要求,并且技术先进,安全可靠,操作方便。
2.所绘制的设计图纸符合国家标准局颁布的GB4728-84《电气图用图形符号》、GB6988-87《电气制图》和GB7159-87《电气技术中的文字符号制定通则》的有关规定。 3.所编写的设计说明书应语句通顺,用词准确,层次清楚,条理分明,重点突出,篇幅不少于7000字。
太阳能热水器自动温度控制器设计_王彤
接启动一个拨号服务器。然后,在计算机B 中的pc Anywhere 软件中启动一个通过拨号连接的Clinet (客户端),拨通计算机A ,建立起连 接以后,就可以进行通信了 。 图1被控端计算机的屏幕显示在主控端上 图2主控端搜索被控端计算机A 图3在计算机C 中渐入A 的IP 地址 当需要多台计算机终端进行协同交互时,(比如有三台计算机A ,B ,C )。首先启动A 为Host ,B 为Clinet ,建立A 和B 的连接,在重新启动一个计算机B 上的pc Anywhere 被设为Host ,C 为Clinet 。建立C 与B 的hos t 之间的联系。这样A ,B ,C 三台计算机上同时显示计算机A 屏幕上的内容,三台计算机之间即可进行交互工作。 5总 结 综上所述,远程监控技术随着Internet 的不断发展而得到广泛应用,同时,随着控制、计算机、通信及网络技术的发展,信息交换沟通的领域正在迅速覆盖控制应用的现场设备、控制及管理的各个层次。信息技术的飞速发展,引发了自动化结构的深刻变革,逐步形成了以网络集成自动化系统为基础的信息系统。目前在过程自动化、制造自动化、楼宇、家庭及交通等领域得到了广泛的应用。 值得提出的是近年来,随着远程控制技术发展的日趋成熟,黑客技术也在不断发展,对网络安全造成了极大的威胁,黑客的主要攻击手段之一,就是使用远程控制技术,渗透到对方的主机系统里。从而实现远程操作目标主机。其破坏力之大,决不容忽视的。因此,我们必须加强安全意识,合理安全的应用远程控制技术。 参 考 文 献 [1]何牧泓.轻松玩转远程控制.重庆出版社,2002. [2]崔彦锋,许小荣.VB 网络与远程控制编程实例教程.北京希望出版社, 2002.[3]王 达.计算机网络远程控制.清华大学出版社,2003.作者简介:樊丽萍,女,硕士研究生,研究方向:计算机控制及应用,通信地址:大连铁道学院303#(116028)E -mail :xiao fanshi wo @https://www.360docs.net/doc/2c4947166.html, ;袁爱进,男,研究生导师,研究方向:现场总线技术。作者注:辽宁省教育厅重大项目“工业现场智能化设备的嵌入式软件构件平台研究” 文章编号:1671-1041(2004)05-0029-02 太阳能热水器自动温度控制器设计 王 彤 (丹东电子研究设计院有限责任公司,辽宁丹东118000) 摘要:介绍了太阳能热水器的自动控制器的功能和组成,阐述了控制系统的 工作原理,硬件和软件设计及相关技术问题,实际应用表明该系统可靠性高、操作简单,具有良好的经济和社会效益。关键词:自动控制;单片机中图分类号:T P273 文献标识码:A The design of automatic temperature controller of solar heater W ANG Tong (Dandong Electronic research &Design institute Co .,Ltd .Dandong 118000China ) Ab stract :Fu nctio n an d co mpo sitio n o f au to matic temp era tu re co ntr olle r of so la r h e ate r a re in trod uce d in th is p a pe r .Also d escribe s t he wo rk p rinciple o f th e co nt rol syste m ,t he ha rd wa re d esign ,t he sof twa re d esig n a nd corre lative t ech niq ue pro b -le m .Th e pra ctical a p plica tion h a s sh ow n th at th is system is o f go od re lia blity a nd e as y op e ratio n ,a n d sig nifican t eco no mic an d so cia l be n efit .Ke y Wo rds :a u toma tic con tro l ;sin gle -chip micr ocomp u ter 收稿日期:2004-04-23 电子邮件来稿 目前,市场上销售的太阳能热水器大多没有自动控制功能,使用 起来不灵活方便,为此,为太阳能热水器加装自动控制功能,具有广泛的市场。 1自动控制系统技术要求 (1)设定温度的范围为25℃至65℃。 (2)输入信号为水温传感器产生的温度信号;水位传感器产生的水量信号。 (3)输出信号为控制水温电信号(控制加热电热管)和控制水流量调节阀信号(控制加水电磁阀)。 (4)配有输入功能键盘:完成自动/手动、手动加水键、手动加热键、温度设定键、水位档选择键。 (5)具有两位LED 数码显示电路,显示温度设定值、实际温度测量值,六个发光二极管指示六档水位(10%、30%、50%、70%、90%、100%)。 2系统硬件设计及原理 太阳能热水器加装自动控制功能,主要是加装一个数据采集系 统和一个电脑控制板。根据太阳能热水器的技术要求及经济方面的考虑,我们选用89C51单片机为核心控制器[1],组成热水器温度控制系统。系统由89C51单片机、数据采集系统、水位选择电路、温度显 29 仪器仪表用户 科研设计与成果 欢迎订阅欢迎撰稿欢迎发布广告产品信息
基于PLC的大棚温度自动控制系统设计
清华大学 毕业设计(论文) 题目基于PLC的大棚温度自动控制 系统设计 系(院)自动化系 专业电气工程与自动化班级2009级3班 学生姓名雷大锋 学号2009022321 指导教师王晓峰 职称副教授 二〇一三年六月二十日
独创声明 本人郑重声明:所呈交的毕业设计(论文),是本人在指导老师的指导下,独立进行研究工作所取得的成果,成果不存在知识产权争议。据我所知,除文中已经注明引用的内容外,本设计(论文)不含任何其他个人或集体已经发表或撰写过的作品成果。对本文的研究做出重要贡献的个人和集体均已在文中以明确方式标明。 本声明的法律后果由本人承担。 作者签名: 年月日 毕业设计(论文)使用授权声明 本人完全了解滨州学院关于收集、保存、使用毕业设计(论文)的规定。 本人愿意按照学校要求提交学位论文的印刷本和电子版,同意学校保存学位论文的印刷本和电子版,或采用影印、数字化或其它复制手段保存设计(论文);同意学校在不以营利为目的的前提下,建立目录检索与阅览服务系统,公布设计(论文)的部分或全部内容,允许他人依法合理使用。 (保密论文在解密后遵守此规定) 作者签名: 年月日
基于PLC的大棚温度自动控制系统设计 摘要 大棚温度自动控制系统是一种为作物提供最好环境、避免各种棚内外环境变化对其影响的控制系统。该系统采用FX2N系列PLC作为下位机,PC机作为上位机,采用三菱D-720通用变频器,采用温度、湿度、光照传感器采集现场信号,这些模拟量经PLC转化为数字信号,把转化来的数据与设定值比较,PLC经处理后给出相应的控制信号使环流风机、遮阴帘、微雾加湿机等设备动作,大棚温度就能实现自动控制。这种技术不但实现了生产自动化,而且非常适合规模化生产,劳动生产率也得到了相应的提高,通过种植者对设定值的改变,可以实现对大棚内温度的自动调节。 关键词:大棚,温度控制,PLC
夹套式反应器温度串级控制课程设计
课程设计任务书
中北大学 课程设计说明书 学院:机械与动力工程学院 专业:过程装备与控制工程 题目:夹套式反应器温度串级控制系统设计指导教师:吕海峰职称: 副教授
中北大学课程设计说明书 目录 1、概述 (1) 1.1化学反应器基本介绍 (1) 1.2夹套式反应器控制要求 (2) 2、被控对象特性研究 (3) 2.1建立动态数学模型 (3) 2.2被控变量与控制变量的选择 (6) 2.3夹套式反应器扰动变量 (6) 3、控制系统方案确定 (7) 3.1主回路的设计 (8) 3.2副回路的设计 (8) 4、过程检测仪表的选型 (9) 4.1测温检测元件及变送器 (9) 4.2主、副控制器正、反作用的选择 (12) 4.3控制系统方框图 (13) 5、系统仿真,分析系统性能 (13) 5.1各个环节传函及参数确定 (13) 5.2控制系统的仿真及参数整定 (14) 5.3 系统性能分析 (17) 6、课程设计总结 (18) 7、参考文献 (19)
1 概述 1.1化学反应器的基本介绍 反应器(或称反应釜)是化工生产中常用的典型设备,种类很多。化学反应器在结构、物料流程、反应机理、传热、传质等方面存在差异,使自控的难易程度相差很大,自控方案差别也比较大。 化学反应器可以按进出物料状况、流程的进行方式、结构形式、传热情况四 个方面分类: 一、按反应器进出物料状况可分为间歇式和连续式反应器 通常将半连续和间歇生产方式称为间歇生产过程。间歇式反应器是将反应物 料分次获一次加入反应器中,经过一定反应时间后取出反应中所有的物料,然后重新加料在进行反应。间歇式反应器通常适用于小批量、多品种、多功能、高附加值、技术密集型产品的生产,这类生产反应时间长活对反应过程的反应温度有严格程序要求。 连续反应器则是物料连续加入,化学反应连续不断地进行,产品不断的取出,是工业生产最常用的一种。一些大型的、基本化工产品的反应器都采用连续的形式。 二、从物料流程的进行方式可分为单程与循环两类 物料在通过反应器后不再进行循环的流程称为单程,当反应的转化率和产率都较高时,可采用单程的排列。如果反应速度较慢,祸首化学平衡的限制,物料一次通过反应器转化不完全,则必须在产品进行分离后,把没有反应的物料与新鲜物料混合后,再送送入反应器进行反应。这种流程称为循环流程。 三、从反应器结构形式可分为釜式、管式、塔式、固定床、流化床、移动床反应器等。 四、从传热情况可分为绝热式反应器和非绝热式反应器[1]。 绝热式反应器与外界不进行热量交换,非绝热式反应器与外界进行热量交换。一般当反应过程的热效应大时,必须对反应器进行换热,其换热方式有夹套式、蛇管式、列管式等。如今用的最广泛的是夹套传热方式,且采用最普通的夹套结构居多。随着化学工业的发展,单套生产装置的产量越来越大,促使了反应设备的大型化。也大大促进了夹套反应器的反展。 夹套式反应器是一类重要的化工生产设备,由于化学反应过程伴有许多化学和物理现象以及能量、物料平衡和物料、动量、热量和物质传递等过程,因此夹套反应器操作一般都比
单闭环温度恒值控制
单闭环温度恒值控制 姓名: 学号: 班级: 实验指导老师: 一、实验目的 1.理解温度控制的基本原理。 2.了解温度传感器的使用方法。 3.学习温度PID控制参数的配置。 二、实验设备 1.THBCC-1型信号与系统控制理论及计算机控制技术实验平台。 2.THBXD数据采集卡一块(含37芯通信线、16芯排线和USB电缆线各1根)。 3.PC机1台(含软件“THBCC-1”)。 三、实验内容 1.设计并实现具有一个积分环节的二阶系统的最少拍控制。 2.设计并实现具有一个积分环节的二阶系统的最少拍无纹波控制,并通过混合仿真实验,观察该闭环控制系统输出采样点间纹波的消除。 四、实验原理 1.温度驱动部分 该实验中温度的驱动部分采用了直流15V的驱动电源,控制电路和驱动电路的原理与直流电机相同,直流15V经过PWM调制后加到加热器的两端。 2.温度测量端(温度反馈端) 温度测量端(反馈端)一般为热电式传感器,热电式传感器式利用传感元件的电磁参数随温度的变化的特性来达到测量的目的。例如将温度转化成为电阻、磁导或电势等的变化,通过适当的测量电路,就可达到这些电参数的变化来表达温度的变化。 在各种热电式传感器中,已把温度量转化为电势和电阻的方法最为普遍。其中将温度转换成为电阻的热电式传感器叫热电偶;将温度转换成为电阻值大小的
热电式传感器叫做热电阻,如铜电阻、热敏电阻、Pt 电阻等。 铜电阻的主要材料是铜,主要用于精度不高、测量温度范围(-50℃~150℃)不大的的地方。而铂电阻的材料主要时铂,铂电阻物理、化学性能在高温和氧化性介质中很稳定,它能用作工业测温元件和作为温度标准。铂电阻与温度的关系在0℃~630.74℃以内为 Rt=R0(1+at+bt2) 式中Rt――温度为t ℃时的温度;R0――温度为0℃时的电阻; t――任意温度;a、b――为温度系数。 该实验系统中使用了Pt100作为温度传感器。 在实际的温度测量中,常用电桥作为热电阻的测量电阻。在如图15-1中采用铂电阻作为温度传感器。当温度升高时,电桥处于不平衡,在a,b两端产生与温度相对应的电位差;该电桥为直流电桥。 3.温度控制系统与实验十三的直流电机转速控制相类似,虽然控制对象不同,被控参数有差别,但对于计算机闭环控制系统的结构,却是大同小异,都有相同的工作原理,共同的结构及特点。 五、温度测量及放大电路图和温度控制系统的框图
水温自动控制系统
《电子技术综合设计》 设计报告 设计题目:水温自动控制系统 组长姓名:学号: 专业与班级:工业自动化14-16班 姓名:学号: 专业与班级:工业自动化14-16班 姓名:学号: 专业与班级:工业自动化14-16班 时间: 2016 ~ 2017 学年第(1)学期指导教师:陈烨成绩:评阅日期:
一、课题任务 设计并制作一个水温自动控制系统,对1.5L净水进行加。水温保持在一定范围内且由人工设定。 细节要求如下: 1.温度设定范围为40℃~90℃,最小分辨率为0.1℃,误差≤1℃。 2.可通过LCD显示屏显示温度目标值与实时温度。 3.可以通过键盘调整目标温度的数值。 二、方案比较 1.系统模块设计 为完成任务目标,可以将系统分为如下几个部分:5V直流电供电模块、测温模块、80C52单片机控制系统、键盘控制电路、温度显示模块、继电器控制模块、强电加热电路。通过各模块之间的相互配合,可以完成水温检测、液晶显示、目标值设置、水温控制等功能。 系统方框图如下:
2.5V直流电供电模块 方案一:直接用GP品牌的9v电池,然后接通过三端稳压芯片7805稳压成5伏直流电源提供给单片机系统使用,接两个5伏电源的滤波电容后输出。 方案二:通过变压器,将220v的市电转换成9v左右的交流电,变压器输出端的9V电压经桥式整流并电容滤波。要得到一个比较稳定的5v电压,在这里接一个三端稳压器的元件7805。 由于需要给继电器提供稳定的5V电压,而方案一中导致电池的过度损耗,无法稳定带动继电器持续工作,所以我们选用能够提供更加稳定5v电源的方案二。 3.测温模块 经查阅资料,IC式感温器在市场上应用比较广泛的有以下几种: AD590:电流输出型的测温组件,温度每升高1 摄氏度,电流增加1μA,温度测量范围在-55℃~150℃之间。其所采集到的数据需经A/D 转换,才能得到实际的温度值。 DS18B20:内含AD转换器,所以除了测量温度外,它还可以把温度值以数字的方式(9 B i t ) 送出,因此线路连接十分简单,它无需其他外加电路,直接输出数字量,可直接与单片机通信,读取测温数据。它能够达到0.5℃的固有分辨率,使用读取温度暂存寄存器的方法还能达到0.0625℃以上精度,温度测量范围在-55℃~125℃之间,应用方便。 SMARTEC感温组件:这是一只3个管脚感温IC,温度测量范围在 -45℃~13℃,误差可以保持在0.7℃以内。 max6225/6626:最大测温范围也是-55~+125℃,带有串行总线接口,测量温度在可测范围内的的误差在4℃以内,较大,故舍弃该方案。 本设计选用DS18B20感温IC,这是因其性能参数符合设计要求,接口简单,内部集成了A/D 转换,测温更简便,精度较高,反应速度快,且经过市场考察,该芯片易购买,使用方便。 下面是DS18B20感温IC的实物和接口图片