广东某电厂2号锅炉热效率性能试验
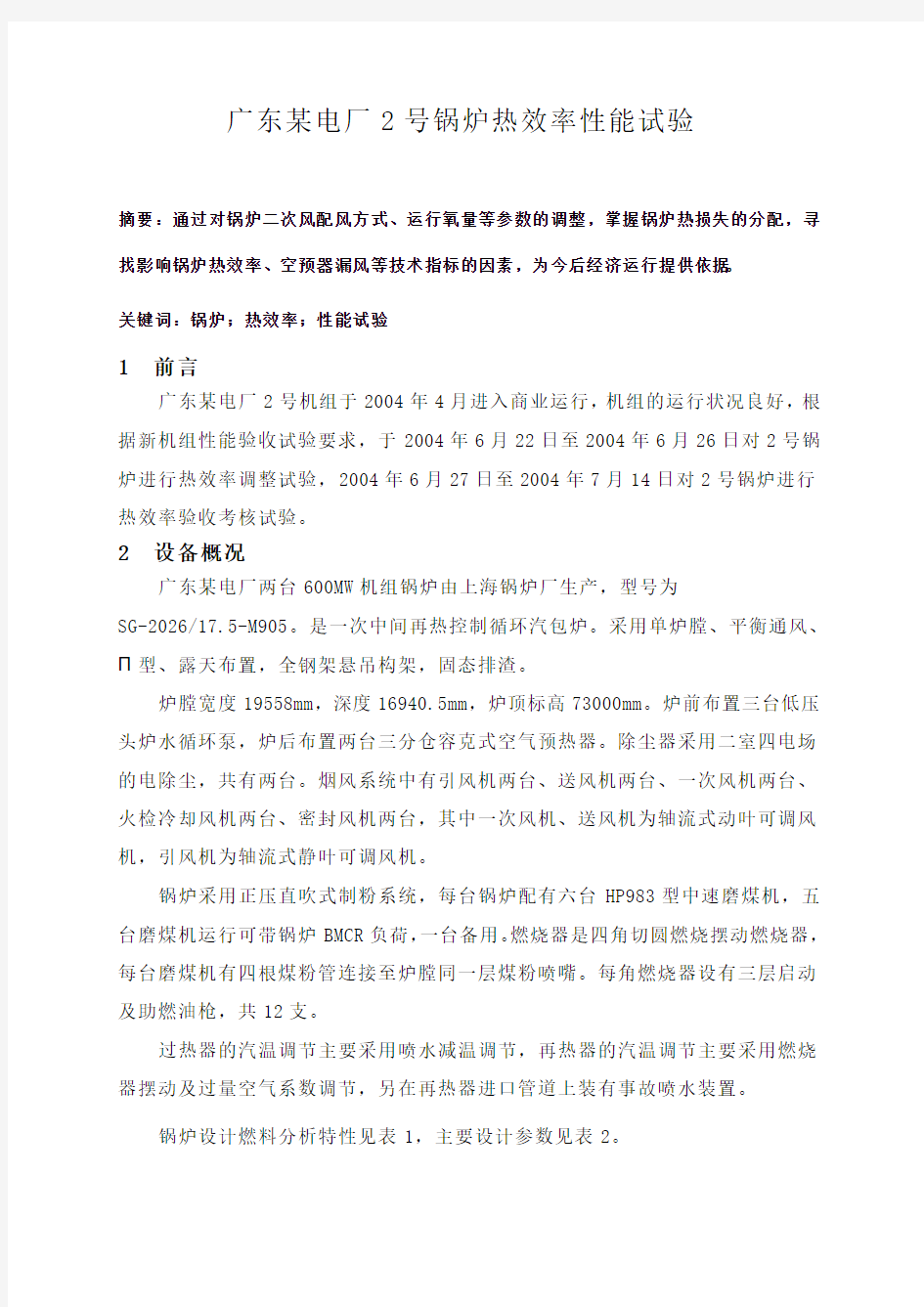

广东某电厂2号锅炉热效率性能试验
摘要:通过对锅炉二次风配风方式、运行氧量等参数的调整,掌握锅炉热损失的分配,寻
找影响锅炉热效率、空预器漏风等技术指标的因素,为今后经济运行提供依据。
关键词:锅炉;热效率;性能试验
1 前言
广东某电厂2号机组于2004年4月进入商业运行,机组的运行状况良好,根据新机组性能验收试验要求,于2004年6月22日至2004年6月26日对2号锅炉进行热效率调整试验,2004年6月27日至2004年7月14日对2号锅炉进行热效率验收考核试验。
2 设备概况
广东某电厂两台600MW机组锅炉由上海锅炉厂生产,型号为
SG-2026/17.5-M905。是一次中间再热控制循环汽包炉。采用单炉膛、平衡通风、П型、露天布置,全钢架悬吊构架,固态排渣。
炉膛宽度19558mm,深度16940.5mm,炉顶标高73000mm。炉前布置三台低压头炉水循环泵,炉后布置两台三分仓容克式空气预热器。除尘器采用二室四电场的电除尘,共有两台。烟风系统中有引风机两台、送风机两台、一次风机两台、火检冷却风机两台、密封风机两台,其中一次风机、送风机为轴流式动叶可调风机,引风机为轴流式静叶可调风机。
锅炉采用正压直吹式制粉系统,每台锅炉配有六台HP983型中速磨煤机,五台磨煤机运行可带锅炉BMCR负荷,一台备用。燃烧器是四角切圆燃烧摆动燃烧器,每台磨煤机有四根煤粉管连接至炉膛同一层煤粉喷嘴。每角燃烧器设有三层启动及助燃油枪,共12支。
过热器的汽温调节主要采用喷水减温调节,再热器的汽温调节主要采用燃烧器摆动及过量空气系数调节,另在再热器进口管道上装有事故喷水装置。
锅炉设计燃料分析特性见表1,主要设计参数见表2。
表1 锅炉设计燃料分析特性
表2 锅炉主要设计参数
2
3 试验目的
3.1 调整试验目的:通过对锅炉二次风配风方式、运行氧量等参数的调整,掌握
锅炉热损失的分配,寻找影响锅炉热效率、空预器漏风等技术指标的因素,为今后经济运行提供依据。
3.2 热效率验收试验目的:在调整试验的基础上,以较经济的运行工况下,测定
在额定负荷下的锅炉热效率、空预器漏风等技术指标,检验和考核技术指标是否达到合同、设计和有关规定的要求。
4 试验所采用的标准
4.1 《火电机组启动验收性能试验导则》电力部文件电综 [1998]179号。
4.2 《电站锅炉性能试验规程》GB10184-88。
4.3 《Fired Steam Generators Performance Test Codes》,ASME PTC4.1(1998年版)。
4.4 《Air Heater Performance Test Codes》,ASME PTC 4.3。
4.5 2号锅炉有关资料。
4.6 合同及技术协议的相关资料。
5 试验条件及试验过程简况
5.1 按合同规定,本次热效率性能验收试验的标准采用《Fired Steam Generators
Performance Test Codes》,ASME PTC4.1(1998年版)。用《电站锅炉性能试验规程 GB 10184-88》对锅炉低位热效率进行复核计算(不涉及合同考核,仅作为机组效率参考)。
5.2 试验条件
5.2.1热效率性能验收试验时锅炉燃用的煤种为设计煤种,试验期间锅炉带额定
电负荷(600MW)。
5.2.2 热效率性能验收试验前,锅炉运行持续时间已大于72小时,正式试验前的
12 小时中,前9小时锅炉负荷不低于试验负荷的75%,后3小时锅炉已维
持试验负荷。
5.2.3 试验期间保持锅炉各参数的稳定,参数稳定范围为:
锅炉负荷:额定蒸汽流量±3%;
主汽温:531 ℃~546 ℃;
主汽压:额定蒸汽压力的±2%;
再热汽温:531 ℃~546 ℃;
给水温度:271±10℃。
5.2.4 试验测试期间,锅炉运行人员不改变氧量、过热汽温、再热汽温、过热汽
压、再热汽压、炉膛风箱压差、燃烧器摆角等参数设置,锅炉不吹灰,不打焦,不排污,试验前后汽包水位相同。
5.2.5 锅炉热效率考核试验期间锅炉投入协调控制系统,空预器密封装置投自动。
5.3 试验过程简况
5.3.1 在试验前校对空预器入口烟温、空预器入口氧量、空预器出口烟温。
5.3.2 在性能验收试验前,先进行了热效率调整,完成配风方式、氧量等因素的
变化对热效率的影响,燃烧器摆角由于有一个角无法调整,因此没有进行燃烧器摆角的调整。此时的原煤样品、飞灰样品、炉渣样品由电厂化验,其结果仅用于《电站锅炉性能试验规程》GB10184-88计算的固体不完全燃烧损
失(q
4)、排烟热损失(q
2
)及作为参考的锅炉热效率。煤粉细度按设计的最
佳煤粉细度预先已调整到位,一、二次风配比保持设计的份额。
5.3.3 由于在DCS上直接修改氧量偏置作用不明显,后来又直接在DCS的送风画
面直接改变风量,进而改变氧量。因此氧量变化的工况是工况2、3、4及工况9、10。测试时间为1.5小时。
5.3.4 二次风以正三角形(工况5)、均匀形(工况6)、缩腰形(工况7)、倒三
4
角形(工况8)等配风方式为变化因素。测试时间为1.5小时。
5.3.5 热效率性能验收试验共进行了两次测试,每次测试时间为4小时。此时的
原煤样品、飞灰样品、炉渣样品由广东发电用煤质量监督检验中心化验,其结果用于ASME PTC4.1计算的高位发热量热效率。
5.3.6 完成100%负荷、75%负荷、50%负荷的试验。测试时间为2小时。此时的
原煤样品、飞灰样品、炉渣样品由广东发电用煤质量监督检验中心化验,其结果用于ASME PTC4.1计算的高位发热量热效率。
6 试验结果与评价
6.1 二次风配风方式对热损失的影响
二次风配风调整试验共进行了正三角形、均匀形、缩腰形和倒三角形四种配风方式,配风方式对热损失的影响如下表3。
表3 二次风配风方式对热损失的影响
在上述四种配风方式中,正三角形配风的热损失最小,缩腰形配风次之,均匀形和倒三角形配风的热损失都比较多。不同的配风方式对煤粉充分燃烧影响不大,对排烟温度有一定的影响。
炉膛温度的测量显示,不同的配风方式下,锅炉燃烧稳定,无火焰偏心的现象。锅炉的轻微烟温偏差也是在允许的范围内。
对于神华煤(高挥发份、低灰分),它属于易燃且稳燃的煤种,即使在不同的
很小。
配风方式下,都能充分燃烧,其固体不完全燃烧损失q
4
单以热效率的角度来分析,正三角形配风的锅炉热效率是最高的,倒三角形配风的热效率最低,但热效率最高的与最低的相比也就相差0.075,差别不大。
建议采用缩腰形配风方式运行,它与锅炉的设计思想(均匀配风)接近,对稳定燃烧更有利,且该配风方式的热效率也较高。
6.2 氧量对热损失的影响
空预器入口氧量调整试验的调整范围为3.0~4.6%(在空预器入口实际测量的数据),氧量对热损失的影响如下表4。
表4 氧量对热损失的影响
从上表可以看出,氧量3.0~3.5%区间较为合适,在此区间的热损失q2+q4比较小,相应的热效率会较高。
炉膛温度的测量显示,锅炉燃烧稳定,无火焰偏心的现象。锅炉的轻微烟温偏差也是在允许的范围内。
从锅炉设计的燃料燃烧角度来分析,它要求的空预器入口氧量在3.5%左右的区间,此时的过量空气系数约1.2。这主要是考虑到炉膛里的空气浓度场有分布不均匀,需要增加一定裕量的空气,维持炉膛里各处都能有足够的空气支持燃料的充分燃烧,而又不致于带来无谓的排烟热损失。
建议空预器入口氧量维持在3.0~3.5%区间,此时空气量既满足燃烧的需要,又能减少热损失。
6.5 热效率验收与考核值
考核前的准备试验的部分参数为:投入CCS协调控制,电负荷604MW。
第一次热效率测试的部分参数为:投入CCS协调控制,电负荷603MW。测试时间4小时。
第二次热效率测试的部分参数为:投入CCS协调控制,电负荷599MW。测试时间4小时。
热效率计算标准:采用ASME PTC 4.1(1998年版)计算高位发热量热效率。计算干烟气热损失、氢产生水蒸汽热损失、燃料中水份热损失、空气中水分热损
6
失、未完全燃烧热损失、表面辐射及对流散热热损失、不可测量热损失,共7项热损失。
空气预热器漏风指标用漏风率计算,计算标准为ASME PTC 4.3。
不可计量热损失取100%ECR工况时其值为0.3%;表面辐射及对流散热损失取100%ECR工况时其值为0.17%;灰渣比例: 飞灰85%, 炉渣15%。参考基准温度:22.6℃, 基准相对湿度: 81%;空预器进口风温取风机出口风温的风量加权平均值,风量取DCS显示数据。具体参数见下表5。
表5 热效率验收试验参数表
第一次热效率测试的结果为89.96%,第二次热效率测试的结果为89.95%,两者相差为0.01%,符合试验的要求(两次试验效率值偏差不大于1%),故此次热效率测试的结果为两次热效率测试的算术平均值,即89.96%。与考核值89.24%相比,能满足设计要求。
A侧的排烟温度测试结果为两次测试的算术平均值,即135.14℃;B侧的排烟温度测试结果为两次测试的算术平均值,即135.37℃;与考核值132℃相比,不能满足设计要求。
A侧空预器漏风率为两次试验结果算术平均,即5.57%。B侧空预器漏风率为两次试验结果算术平均,即5.48%,满足设计的要求(≤6%)。
炉膛温度的测量显示,锅炉燃烧稳定,无火焰偏心的现象。
为了更深入的了解锅炉热效率,用《电站锅炉性能试验规程 GB 10184-88》对锅炉低位热效率进行计算,其低位热效率不涉及合同考核,仅作为机组效率参考。热效率的结果为两次试验平均值,即锅炉低位热效率为94.38%,修正后的锅炉低位热效率为94.23%。表6为汇总表。
表6 用《电站锅炉性能试验规程 GB 10184-88》计算锅炉低位热效率
6.6 不同负荷下的锅炉热效率
完成100%ECR、75%ECR、50%ECR等不同负荷下锅炉热效率测试,这些负荷下的热效率不涉及厂家考核值,仅仅是对锅炉有一个完整的热效率曲线。
热效率计算标准: 采用ASME PTC 4.1(1998年版)计算高位发热量热效率。空气预热器漏风率计算标准:ASME PTC 4.3。不同负荷的热效率及漏风率见表7。
表7 不同负荷下锅炉热效率及空预器漏风率
从上表可看出,随着负荷降低,锅炉热效率比额定负荷时要高,但空预器的漏风率比额定负荷时增大。炉膛温度的测量显示,在各个负荷段下,锅炉燃烧稳定,无火焰偏心的现象。
7 试验结论
7.1 锅炉热效率测试的结果为89.96%。与合同考核值89.24%相比,能满足设计要求。
7.2 A侧的排烟温度为135.14℃;B侧的排烟温度为135.37℃;与考核值
132℃相比,不能满足设计要求。
7.3 A侧空预器漏风率为5.57%,B侧空预器漏风率为5.48%。与合同考核值6%相比,满足设计要求。
8
锅炉效率计算
单位时间内锅炉有效利用热量占锅炉输入热量的百分比,或相应于每千克燃料(固体和液体燃料),或每标准立方米(气体燃料)所对应的输入热量中有效利用热量所占百分比为锅炉热效率,是锅炉的重要技术经济指标,它表明锅炉设备的完善程度和运行管理水平。锅炉的热效率的测定和计算通常有以下两种方法: 1.正平衡法 用被锅炉利用的热量与燃料所能放出的全部热量之比来计算热效率的方法叫正平衡法,又叫直接测量法。正平衡热效率的计算公式可用下式表示: 热效率=有效利用热量/燃料所能放出的全部热量*100% =锅炉蒸发量*(蒸汽焓-给水焓)/燃料消耗量*燃料低位发热量*100% 式中锅炉蒸发量——实际测定,kg/h; 蒸汽焓——由表焓熵图查得,kJ/kg; 给水焓——由焓熵图查得,kJ/kg; 燃料消耗量——实际测出,kg/h; 燃料低位发热量——实际测出,kJ/kg。 上述热效率公式没有考虑蒸汽湿度、排污量及耗汽量的影响,适用于小型蒸汽锅炉热效率的粗略计算。 从上述热效率计算公式可以看出,正平衡试验只能求出锅炉的热效率,而不能得出各项热损失。因此,通过正平衡试验只能了解锅炉的蒸发量大小和热效率的高低,不能找出原因,无法提出改进的措施。 2.反平衡法 通过测定和计算锅炉各项热量损失,以求得热效率的方法叫反平衡法,又叫间接测量法。此法有利于对锅炉进行全面的分析,找出影响热效率的各种因素,提出提高热效率的途径。反平衡热效率可用下列公式计算。 热效率=100%-各项热损失的百分比之和 =100%-q2-q3-q4-q5-q6 式中q2——排烟热损失,%; q3——气体未完全燃烧热损失,%; q4——固体未完全燃烧热损失,%; q5——散热损失,%; q6——灰渣物理热损失,%。 大多时候采用反平衡计算,找出影响热效率的主因,予以解决。
锅炉热效率测试方案
锅炉热效率测试方案 为了解毛铺酒厂锅炉运行热效率和为确定下步锅炉改造方向,根据《锅炉节能技术监督管理规程》和按照《工业锅炉能效测试与评价规则》对毛铺酒厂3台锅炉进行能效测试。 一、测试方法 锅炉运行工况热效率简单测试采用反平衡法,相关测量要求按照GB/T 10180要求的方法进行测量。 二、测试要求 1.热效率测试应当不少于2次; 2.两次反平衡测试测得的效率之差均应当不大于2%。 三、测试条件 1.锅炉在额定参数下处于安全、热工况稳定的运行状态; 2.辅机与锅炉出力相匹配并运行正常,系统不存在跑、冒、滴现象; 3.测试所用燃料符合设计燃料的要求; 4.锅炉及辅机系统各测点布置满足测试大纲要求。 四、测试项目 1.排烟温度t py,℃; 2.排烟处过量空气系数; 3.排烟处CO含量,%(ppm); 4.入炉冷空气温度t lk,℃; 5.飞灰可燃物含量C fh,%; 6.漏煤可燃物含量C lm,%; 7.炉渣可燃物含量C lz,%; 8.燃料收到基低位发热量Q net.v.ar,kJ/kg;收到基灰分A ar,%; 9.测试开始和结束的时间。 五、正式测试时间 1、锅炉正常燃烧1小时后开始测试; 2、测试时间内至少包括一个完整的燃料添加和出渣周期(分厂应先
将煤斗填平正常燃烧后添加燃煤时必须填平并计量); 3、烟气测量次数不少于5次,每次间隔时间均匀,测试开始、结束各一次(对于排烟温度、排烟处过量空气系数、排烟处CO 含量按测量数据算术平均值作为计算值)。 六、测试项目 1. 排烟热损失(q 2) 2. 气体未完全燃烧热损失(q 3) 3. 固体未完全燃烧热损失(q 4) 4. 散热损失(q 5) 5. 灰渣物理热损失(q 6) 6. 热效率;()65432j 100q q q q q ++++-=η 七、测试报告 1. 锅炉能效测试综合报告 2. 锅炉能效测试项目 3. 锅炉能效测试测点布置及测试仪表说明 4. 能效测试结果汇总表 八、测试小组成员及分工 名称 人员 职责 组长 刘怀臣 测试、督察、分析总协调;为小组工作申请资源保障 综合分析 组 生产技术科设 备组 1、 测试前组织对小组人员进行系统培训; 2、 对测试细节进行全面监督; 3、 对测试数据进行统计分析,并出具相关报告; 4、 对照国家相关规定,寻找不合格项目,并制定锅炉下步改造计划。 检测组 质量科 检验人 员 1、负责飞灰、煤渣、漏煤的取样工作; 2、负责过程中试样的检测工作,并及时反馈至生产技术科设备组 操作、维护 保障组 分厂动力部门 1、 按照操作规程进行规范操作; 2、 按照测试要求对锅炉及其辅机进行全面检修,并保证系统满足测验要求; 生产技术科 二〇一二年二月八日
锅炉热效率计算
1兆帕(MPa)=10巴(bar)=9.8大气压(atm)约等于十个大气压,1标准大气压=76cm汞柱=1.01325×10^5Pa=10.336m水柱约等于十米水柱,所以1MPa大约等于100米水柱,一公斤相当于10米水柱 水的汽化热为40.8千焦/摩尔,相当于2260千焦/千克.一般地:使水在其沸点蒸发所需要的热量五倍于把等量水从一摄氏度加热到一百摄氏度所需要的热量. 一吨水=1000千克每千克水2260千焦 1000千克就是2260 000千焦 1吨蒸汽相当于60万千卡/1吨蒸汽相当于64锅炉马力/1锅炉马力相当于8440千卡热。 用量是70万大卡/H 相当于1.17吨的锅炉 以表压力为零的蒸汽为例,每小时产一吨蒸汽所具有的热能,在锅内是分两步吸热获得的,第一步是把20度的一吨给水加热到100度的饱和水所吸收的热能,通常这部分热能为显热,其热能即为1000×(100-20)=8万/千卡时。 第二步则是将已处于饱和状态的热水一吨加热成饱和蒸汽所需要吸收的热能,这部分热为潜热,其热能即为1000×539=53.9万/千卡时。 把显热和潜热加起来,即是一吨蒸汽(其表压力为零时)在锅内所获得的热能, 即:53.9+8=61.9万/千卡时。这就是我们通常所说的蒸汽锅炉每小时一吨蒸发量所具有的热能,相当于热水锅炉每小时60万/大卡的容量。 天然气热值 天燃气每立方燃烧热值为8000大卡至8500大卡,1千卡/1大卡/1000卡路里(kcal)=4.1868千焦(kJ),所以每立方米燃烧热值为33494.4—35587.8KJ 产地、成分不同热值不同,大致在36000~40000kJ/Nm3,即每一标准立方米天然气热值约为36000至40000千焦耳,即36~40百万焦耳。 天燃气每立方燃烧热值为8000大卡至8500大卡,1千卡/1大卡/1000卡路里(kcal)=4.1868千焦(kJ),所以每立方米燃烧热值为33494.4—35587.8KJ。而1度=1kW*h=3.6*10^6J=3.6*10^3KJ。即每立方燃烧热值相当于9.3—9.88度电产生的热能, 3.83<1.07*9.3 OR 9.88 天然气价格: 天然气的主要成分是甲烷,分子式是CH4,分子量是12+4*1=16. 在1标准大气压下,1mol气体的体积是22.4升,1立方米的气体有
能效测试报告(电站锅炉)
报告编号: 锅炉能效测试报告 项目名称: 测试方法: 锅炉型号: 委托单位: 测试地点: 测试日期: 有限公司 注意事项 1.报告书应当由计算机打印输出,涂改无效。 2.本报告书无检验、审核、批准人签字无效。 3.本报告书无检验专用章或公章及骑缝章无效。 4.本报告书一式三份,由检测机构和使用单位分别保存。 5.测试结论是在本报告所记载的测试依据和测试条件下得出的。 6.受检单位对本报告结论如有异议,请在收到报告书之日起15日内, 向测试机构提出书面意见。 地址: 电话: 邮编: 传真:
锅炉能效测试报告目录 报告编号: 序号检验项目页码附页、附图一锅炉能效测试综合报告 二锅炉能效测试项目 三锅炉能效测试点布置及测试仪表说明 四测试数据综合表 五测试锅炉数据综合表 六能效测试结果汇总表
一、锅炉能效测试综合报告 设备品种锅炉型号 总图号产品编号 制造单位 使用证号注册代码 使用单位联系人联系电话 通讯地址邮政编码 测试地点测试日期 测试类型 测试依据1.《锅炉节能技术监督管理规程》(TSG G0002-2010);2.《电站锅炉性能试验规程》GB/T 10184-2015;3.《工业锅炉热工性能试验规程》GB/T 10180-2003;4.相应标准或者其他要求。 测试说明1.测试用燃料主要参数,符合性:2.实际测试的运行状况: 3.燃料、灰、渣系统: 4.其他需要说明的内容: 测试结果 锅炉出力 kg/h 蒸汽压力MPa 炉体表面温 度℃ 炉渣含碳 量% 飞灰含碳量%漏煤含碳量%排烟温度℃ 入炉冷空气温 度℃ 过量空气系数锅炉效率% 结论 分析 下次测试日期 测试人员: 测试负责人:年月日 (检验专用章)编制:年月日 审核:年月日 批准:年月日 二、锅炉能效测试项目
锅炉热效率
锅炉热效率试验 1热效率试验的标准 《GB10184-88 电站锅炉性能试验规程》 2本课程的适用范围 火力发电厂燃煤锅炉。 基于燃用煤、不包括其它的燃料。 热效率是锅炉的一项重要经济指标。 3热效率的计算方式 3.1 输入-输出法 又称:直接法或正平衡法。 即直接测量锅炉输入和输出热量求得热效率。 3.2 热损失法 又称:反平衡法。 即由确定各项热量损失求得热效率。 4概念的介绍 4.1 输入热量 随每千克煤输入锅炉能量平衡系统的总热量。 4.1.1 煤的收到基低位发热量 4.1.2 物理显热 4.1.3 用外来热源加热燃料或空气时所带入的热量 4.2 输出热量 相对每千克煤,工质在锅炉能量平衡系统中所吸收的总热量。 4.3 各项热损失 4.3.1 包括5项损失 4.3.2 排烟热损失 锅炉排烟热损失为末级热交换器后排出烟气带走的物理显热占输入热量的百分率
1)干烟气带走的热量 2)烟气中含水蒸气的显热 4.3.3 可燃气体未完全燃烧热损失 该项热损失由排烟中的未完全燃烧产物(CO、H2、CH4和C m H n)的含量决定,系指这些可燃气体成分未放出其燃烧热而造成的热量损失占输入热量的百分率4.3.4 固体未完全燃烧热损失 燃煤锅炉的固体未完全燃烧热损失,即灰渣可燃物造成的热量损失和中速磨煤机排出石子煤的热量损失占输入热量的百分率 4.3.5 散热损失 锅炉散热损失q5,系指锅炉炉墙、金属结构及锅炉范围内管道(烟风道及汽、水管道联箱等)向四周环境中散失的热量占总输入热量的百分率。热损失值的大小与锅炉机组的热负荷有关。 4.3.6 灰渣物理热损失 灰渣物理热损失,即炉渣、飞灰与沉降灰排出锅炉设备时所带走的显热占输入热量的百分率 4.4 锅炉的额定蒸发量(ECR) 锅炉在额定蒸汽参数、额定给水温度、燃用设计煤种并保证效率时所规定的蒸发量。 4.5 锅炉的最大蒸发量(BMCR) 锅炉在额定蒸汽参数、额定给水温度、燃用设计煤种,安全连续运行时能达到的最大蒸发量。 4.6 基准温度 指各项输入与输出能量的起算点。 规定为锅炉送风机入口处空气温度。一般可认为是冷空气温度。 4.7 燃料分析 燃料的工业分析和元素分析。 5锅炉机组热平衡系统
锅炉热效率计算
一、锅炉热效率计算 10.1 正平衡效率计算 10.1.1输入热量计算公式: Qr=Qnet,v,ar+Qwl+Qrx+Qzy 式中: Qr__——输入热量; Qnet,v,ar ——燃料收到基低位发热量; Qwl ——加热燃料或外热量; Qrx——燃料物理热; Qzy——自用蒸汽带入热量。 在计算时,一般以燃料收到基低位发热量作为输入热量。如有外来热量、自用蒸汽或燃料经过加热(例: 重油)等,此时应加上另外几个热量。 10.1.2饱和蒸汽锅炉正平衡效率计算公式: 式中:η1——锅炉正平衡效率; Dgs——给水流量; hbq——饱和蒸汽焓; hgs——给水焓; γ——汽化潜热; ω——蒸汽湿度; Gs——锅水取样量(排污量); B——燃料消耗量; Qr_——输入热量。 10.1.3过热蒸汽锅炉正平衡效率计算公式: a. 测量给水流量时: 式中:η1——锅炉正平衡效率; Dgs——给水流量; hgq——过热蒸汽焓; hg——给水焓; γ——汽化潜热; Gs——锅水取样量(排污量); B——燃料消耗量; Qr——输入热量。 b. 测量过热蒸汽流量时: 式中:η1——锅炉正平衡效率; Dsc——输出蒸汽量; Gq——蒸汽取样量; hgq——过热蒸汽焓; hgs——给水焓; Dzy——自用蒸汽量;
hzy——自用蒸汽焓; hbq——饱和蒸汽焓; γ——汽化潜热; ω——蒸汽湿度; hbq——饱和蒸汽焓; Gs——锅水取样量(排污量); B——燃料消耗量; Qr——输入热量。 10.1.4 热水锅炉和热油载体锅炉正平衡效率计算公式 式中:η1——锅炉正平衡效率; G——循环水(油)量; hcs——出水(油)焓; hjs——进水(油)焓; B——燃料消耗量; Qr——输入热量。 10.1.5电加热锅炉正平衡效率计算公式 10.1.5.1电加热锅炉输-出饱和蒸汽时公式为: 式中:η1——锅炉正平衡效率; Dgs——给水流量; hbq——饱和蒸汽焓; hgs——给水焓; γ——汽化潜热; ω——蒸汽湿度; Gs——锅水取样量(排污量); N——耗电量。 10.1.5.2电加热锅炉输-出热水(油)时公式为: 式中:η1——锅炉正平衡效率; G——循环水(油)量; hcs——出水(油)焓; hjs——进水(油)焓; B——燃料消耗量; Qr_——输入热量 二、锅炉结焦的危害、原因及预防方法是什么? 在炉子的燃烧中心,火焰温度高达1450~1600℃,因此煤灰基本上处于溶化状态。当与受热面碰撞后,溶渣就会粘附在管道或炉墙上,这就叫结焦。 如果炉内结了焦,炉膛部分的吸热量就要减少,到过热器部分的烟温就会增高,而造成个别管子的外壁温度超过它的允许范围,引起爆管,同时还会使主汽温度超温。结焦严重时,会使吸热量的减少而减负荷,甚至停炉。结焦还会使排烟热损失q2和机械热损失q4及风机耗电增加。
广东某电厂2号锅炉热效率性能试验
广东某电厂2号锅炉热效率性能试验 摘要:通过对锅炉二次风配风方式、运行氧量等参数的调整,掌握锅炉热损失的分配,寻 找影响锅炉热效率、空预器漏风等技术指标的因素,为今后经济运行提供依据。 关键词:锅炉;热效率;性能试验 1 前言 广东某电厂2号机组于2004年4月进入商业运行,机组的运行状况良好,根据新机组性能验收试验要求,于2004年6月22日至2004年6月26日对2号锅炉进行热效率调整试验,2004年6月27日至2004年7月14日对2号锅炉进行热效率验收考核试验。 2 设备概况 广东某电厂两台600MW机组锅炉由上海锅炉厂生产,型号为 SG-2026/17.5-M905。是一次中间再热控制循环汽包炉。采用单炉膛、平衡通风、П型、露天布置,全钢架悬吊构架,固态排渣。 炉膛宽度19558mm,深度16940.5mm,炉顶标高73000mm。炉前布置三台低压头炉水循环泵,炉后布置两台三分仓容克式空气预热器。除尘器采用二室四电场的电除尘,共有两台。烟风系统中有引风机两台、送风机两台、一次风机两台、火检冷却风机两台、密封风机两台,其中一次风机、送风机为轴流式动叶可调风机,引风机为轴流式静叶可调风机。 锅炉采用正压直吹式制粉系统,每台锅炉配有六台HP983型中速磨煤机,五台磨煤机运行可带锅炉BMCR负荷,一台备用。燃烧器是四角切圆燃烧摆动燃烧器,每台磨煤机有四根煤粉管连接至炉膛同一层煤粉喷嘴。每角燃烧器设有三层启动及助燃油枪,共12支。 过热器的汽温调节主要采用喷水减温调节,再热器的汽温调节主要采用燃烧器摆动及过量空气系数调节,另在再热器进口管道上装有事故喷水装置。 锅炉设计燃料分析特性见表1,主要设计参数见表2。
锅炉性能测试方案精编版
锅炉性能测试方案公司标准化编码 [QQX96QT-XQQB89Q8-NQQJ6Q8-MQM9N]
锅炉性能测试方案 1.目的 为进一步推进锅炉系统精益管理能效提升工作,对锅炉系统运行工况进行测试,试验锅炉经济运行工况及参数,提高锅炉运行效率。 2 测试依据 GB/T 10184-88 《电站锅炉性能试验规程》 》 GB/T 10180-2003《工业锅炉热工性能试验规程》山东 GB/T17954-2007《工业锅炉经济运行》 TSG0002-2010《锅炉节能技术监督管理规程》 TSG0003-2010《工业锅炉能效测试与评价规则》 DB37/T 842-2007《电站锅炉节能监测方法》 DB37/T 100-2007《工业锅炉节能运行管理》 DB37/T 116-2007《工业锅炉热能利用监测规范》 3试验前的准备工作 测点完好可用;试验仪器及测试系统安装调试结束;试验人员就位。 机组主辅设备及系统无重大缺陷,确保机组能安全、稳定运行。 主要运行表计(蒸汽流量、煤气流量、给水流量、减温水量、主汽温度、主汽压力、引送风机电流、电量等表计)经过校验,投运正常,指示正确有效;经过仪表维护人员前期检查确认。 阀门控制系统运行可靠,具备条件的提前2-3天进行试运。
运行参数历史趋势记录存盘正常运行。 试验稳定负荷期间,锅炉主要运行参数必须在规定波动范围。 试验前锅炉定排完毕,关闭锅炉定排、连排阀门,隔离非生产系统用汽,确保锅炉汽水系统无外漏现象。 风烟系统严密无泄漏。 煤气系统压力与品质成分稳定,无大幅波动,确保锅炉热工况稳定。 正式试验前由各单位组织岗位进行预备试验。 试验过程中司炉等操作人员经验丰富,责任心强。 4测试内容及要求 60%、80%、100%额定负荷下的热效率。 60%、80%、100%额定负荷下的漏风率、漏风系数。 燃料成分及热值测试。 各负荷下的烟气成分检测(含氧量、一氧化碳等); 各负荷下的运行参数测试,风燃比变化情况下的燃烧效率。 试验器材(在线仪表、测温仪、热电偶、烟气分析仪、气压表、u型管、湿度计、对讲机等;应急器材:CO报警仪、氧气报警仪、空气呼吸器等) 5 试验测试项目及方法(测试点的选取) 锅炉反平衡效率、漏风率 5.1.1 排烟温度测量 测量方法:利用现有温度测点测量锅炉排烟温度,两个温度测点测试结果在误差允许范围内。测试期间数据记录周期为每5分钟一次。
锅炉性能测试方案
锅炉性能测试方案 1.目的 为进一步推进锅炉系统精益管理能效提升工作,对锅炉系统运行工况进行测试,试验锅炉经济运行工况及参数,提高锅炉运行效率。 2 测试依据 GB/T 10184-88 《电站锅炉性能试验规程》 DL/T 469-2004 《电站锅炉风机现场性能试验》 GB/T 10180-2003《工业锅炉热工性能试验规程》山东 GB/T17954-2007《工业锅炉经济运行》 TSG0002-2010《锅炉节能技术监督管理规程》 TSG0003-2010《工业锅炉能效测试与评价规则》 DB37/T 842-2007《电站锅炉节能监测方法》 DB37/T 100-2007《工业锅炉节能运行管理》 DB37/T 116-2007《工业锅炉热能利用监测规范》 3试验前的准备工作 3.1测点完好可用;试验仪器及测试系统安装调试结束;试验人员就位。 3.2机组主辅设备及系统无重大缺陷,确保机组能安全、稳定运行。 3.3主要运行表计(蒸汽流量、煤气流量、给水流量、减温水量、主汽温度、主汽压力、引送风机电流、电量等表计)经过校验,投运正常,指示正确有效;经过仪表维护人员前期检查确认。 3.4阀门控制系统运行可靠,具备条件的提前2-3天进行试运。 3.5运行参数历史趋势记录存盘正常运行。
3.6试验稳定负荷期间,锅炉主要运行参数必须在规定波动范围。 3.7试验前锅炉定排完毕,关闭锅炉定排、连排阀门,隔离非生产系统用汽,确保锅炉汽水系统无外漏现象。 3.8风烟系统严密无泄漏。 3.9煤气系统压力与品质成分稳定,无大幅波动,确保锅炉热工况稳定。 3.10正式试验前由各单位组织岗位进行预备试验。 3.11试验过程中司炉等操作人员经验丰富,责任心强。 4测试内容及要求 4.1 60%、80%、100%额定负荷下的热效率。 4.2 60%、80%、100%额定负荷下的漏风率、漏风系数。 4.3 燃料成分及热值测试。 4.4 各负荷下的烟气成分检测(含氧量、一氧化碳等); 4.5 各负荷下的运行参数测试,风燃比变化情况下的燃烧效率。 4.6 试验器材(在线仪表、测温仪、热电偶、烟气分析仪、气压表、u型管、湿度计、对讲机等;应急器材:CO报警仪、氧气报警仪、空气呼吸器等) 5 试验测试项目及方法(测试点的选取) 5.1 锅炉反平衡效率、漏风率 5.1.1 排烟温度测量 测量方法:利用现有温度测点测量锅炉排烟温度,两个温度测点测试结果在误差允许范围内。测试期间数据记录周期为每5分钟一次。 测点位置:空气预热器出口烟道
火电机组启动验收性能试验导则
中华人民共和国电力工业部 火电机组启动验收性能试验导则 一九九八年三月
火力发电厂机组启动蒸汽吹管系统的设计附录 编写说明 为贯彻落实《火力发电厂基本建设工程启动及竣工验收规程(1996年版)》(以下简称《新启规》)关于机组性能试验的有关要求,规范火电机组在试生产期间的性能试验工作,提高机组性能试验的水平,保证机组安全、稳定、经济运行、在试生产期结束时按《火电机组移交生产达标考核评定办法(1998年版)》考核实现达标投产,根据国家标准和有关行业标准制定本导则。 本导则编审部门:电力工业部工程建设协调司 主审:梁兵段喜民 本导则主编部门:华北电力科学研究院 执笔:梁燕钧 编写人:黄安平余元张清峰 游永坤李学尧黄乃民 孙丽燕严冬华
目录 1 总则 2 试验目的 3 试验项目及要求 4 试验准备 5 性能试验内容及要求 5.1 锅炉热效率试验 5.2 锅炉最大出力试验 5.3 锅炉额定出力试验 5.4 锅炉断油(气)最低出力试验 5.5 制粉系统出力试验 5.6 磨煤单耗试验 5.7 机组热耗试验 5.8 机组轴系振动试验 5.9 汽机最大出力试验(VWO工况) 5.10 汽机额定出力试验 5.11 机组RB功能试验 5.12 机组供电煤耗测试 5.13 污染物排放测试 5.14 机组噪音(声)测试 5.15 机组散热测试 5.16 机组粉尘测试 5.17 除尘器效率试验 6 试验技术报告 7 参考标准 8 附录(略)
1.总则 1.0.1 本导则适用于按《新启规》的有关要求完成机组满负荷试运行并移交试生产的国产200MW及以上容量的火力发电机组。200MW以下火力发电机组若安排试生产期可参照执行。凡合同规定的机组性能考核试验项目,按合同的规定进行试验,其结果视同本导则规定的相应性能试验项目的结果;合同未规定的项目,可执行本导则的有关条款。 1.0.2 火电机组的性能试验应由建设单位(即项目法人,下同)组织,具体的试验工作由有关单位协商确定的试验单位负责,设备制造厂、电厂、设计、安装等单位配合。全部性能试验工作应在试生产期结束前完成,有些项目可在机组整套启动试运期间进行。 1.0.3 机组的性能试验是考验机组各主、辅机及系统是否达到设计性能的主要依据。 1.0.4 机组的性能试验应执行国际标准、国家标准或有关行业标准,暂无国际标准、国家标准和行业标准的项目执行本导则。 1.0.5 在机组初步设计阶段就应确定性能试验的负责单位,试验单位应确定试验负责人。在设计联络会上由试验负责人负责,会同建设、设计、制造等单位确定试验采用的标准、试验测点位置、测点型式、规格尺寸,并确定测点制造、安装单位。 1.0.6 设备供货合同确定的机组性能等与性能试验有关的技术资料,在设备订货合同正式签定后由建设单位提供给试验负责单位。 1.0.7 本导则自颁布之日起实施,解释权在国家电力公司。 2.试验目的 2.0.1 检验与考核机组的各项技术经济指标是否达到合同、设计和有关规定的要求。 2.0.2 在机组的辅机以不同方式编组情况下,试验确定机组的最大负荷和最低不投助燃燃料稳燃负荷。 2.0.3 考验机组自动装置的性能,在发生RB工况(指有此功能的机组)时维持机组安全稳定运行的能力。 2.0.4 考验机组环保设施的使用效果,测试环保设备及设施的性能是否达到合同(或设计)要求,测定机组运行中污染物的排放。 2.0.5 测试机组各工作场所劳动保护条件是否达到要求。 3.试验项目及要求 3.0.1 机组性能试验一般在机组完成168h(或72+24h)满负荷试运移交试生产后进行;条件具备时,部分项目可在机组整套试运期间进行;所有试验应于试
燃煤电厂综合升级改造机组性能测试技术要求
附件2:燃煤电厂综合升级改造机组性能测试技术要求 一、锅炉性能试验及修正 (一)锅炉性能试验应执行最新版《电站锅炉性能试验规程》(GB/T 10184)或《锅炉机组性能试验规程》(ASME PTC 4.1)、《磨煤机试验规程》(ASME PTC 4.2)、《空气预热器试验规程》(ASME PTC 4.3)等规程,原则上执行高标准规程。 (二)锅炉性能试验应优先采用反平衡法,在额定工况下至少开展两次,在修正到相同条件后,两次试验结果(锅炉热效率)的偏差不大于0.35个百分点。 (三)改造前后锅炉性能试验煤种,原则上应采用设计煤种。采用其他煤种时,改造前后试验煤种收到基低位发热量(Q net.ar)偏差不超过1200kJ/kg、收到基挥发分(V daf)偏差不大于3个百分点、收到基灰分(A ar)偏差不大于5个百分点。变更设计煤种的综合升级改造,改造前后锅炉性能试验煤种应分别采用对应的设计煤种。 (四)锅炉性能试验结果应按相应规程修正。若进行空气预热器、省煤器、低温省煤器等改造,应通过试验确定改造后锅炉排烟温度、空气预热器漏风率、锅炉热效率和供电煤耗变化量。若进行制粉系统、燃烧器等改造,应通过试验确定改造后磨煤机出力、制粉单耗、锅炉飞灰和底渣可燃物、锅炉排烟温度、锅炉热效率和供电煤耗变化量。 二、汽轮机性能试验及修正 (一)汽轮机性能试验执行最新版《汽轮机热力性能验收试验规程的第1部分:方法A —大型凝汽式汽轮机高准确度试验》(GB/T 8117.1)、第2部分:方法B—各种类型和容量的汽轮机宽准确度试验》(GB/T 8117.2)。原则上执行高标准规程。 (二)汽轮机性能试验应在额定工况下开展,不明泄漏量不大于新蒸汽流量的0.3%,试验结果不确定度不大于0.5%;汽轮机性能试验应开展两次,在修正到相同条件后,两次试验结果(汽轮机热耗率)的偏差不大于0.25%。 (三)汽轮机性能试验结果原则上应合理修正主蒸汽压力、主蒸汽温度、再热蒸汽温度、再热器减温水流量(或过热减温水流量)和凝汽器压力(或凝汽器入口循环水温度)等参数。变更设计主蒸汽压力、主蒸汽温度、再热蒸汽温度、再热器减温水量(或过热器减温水流量)的综合升级改造,可不修正相应参数。汽轮机冷端系统改造,可参考相应标准,通过试验确定凝汽器压力及循环水泵功耗变化后,再确定供电煤耗变化,并计算节能量。
锅炉性能试验方案
2t/h实验炉性能测试 实验方案 2016年10月
目录 1前言 (1) 2设备概述 (1) 3实验目的 (3) 4实验依据 (4) 5试验工况设置 (4) 6测量项目及方法 (5) 7实验仪器、仪表校验 (6) 8实验条件及要求 (6) 9实验内容及方法 (7) 附表1实验所需仪器及材料 (8) 附表2电脑记录数据清单 (9)
1前言 哈尔滨华氏海德科技发展有限公司在哈尔滨工业大学煤污染物节能减排实验室新建2t/h蒸汽试验锅炉,锅炉为双锅筒纵置链条炉,采用D形布置,尾部受热面采用铸铁空气预热器及热管相变换热器,单炉膛单侧送风,室内布置,固态排渣。设计煤种:二类烟煤。采用垂直提升机和刮板机上煤。 本方案为锅炉性能试验的指导性文件,制定了试验的方法及为确保测试精度所应采取的测试手段。 2设备概述 2.1本工程装设1台2t/h蒸汽锅炉。锅炉为双锅筒纵置链条炉,采用D形布置, 尾部受热面采用铸铁空气预热器及热管相变换热器,单炉膛单侧送风,室内布置固态排渣。设计煤种:二类烟煤。采用垂直提升机和刮板机上煤。 2.2锅炉出口蒸汽参数为0.7MPa/300℃锅炉主要参数见下表 表1 锅炉主要特性汇总
表2 燃料分析 表3 燃料分析
表4 各烟道烟气特性 3实验目的 性能试验的目的是为了考核锅炉的性能是否达到计算值的标准,主要试验以下内容: 在下述工况条件下,锅炉保证热效率82.89%(按低位发热量) 1)燃用设计煤种 2)大气温度不低于10℃ 3)过热蒸汽温度应在280℃~320℃之间 4)蒸汽品质合格,压力不小于0.55MPa。
4实验依据 4.1GB/T10180-2003工业锅炉热工性能试验规程4.2GB13271-2014锅炉大气无污染物排放标准4.3有关会议纪要 5试验工况设置 依据实验内容拟安排表5所示的试验工况。 表5 试验工况设置
燃煤锅炉热效率效率计算
燃煤锅炉热效率效率计算
————————————————————————————————作者:————————————————————————————————日期:
燃煤锅炉的热效率热效率计算 根据《关于发展热电联产的规定》(计基础〔2000〕1268号)文件,热效率=(供热量+供电量×3600千焦/千瓦时)/(燃料总消耗量×燃料单位低位热值) ×100%,供热量就是热力产品(热水、蒸汽)根据供热流量、压力、温度的参数进行焓值计算后得出的焦耳热值当量年度产量,加上年发电量换算成焦耳热值当量(kWh乘以3600),二者的和就是热电厂年产品总量(电+热)。 分母是热电厂的燃料消耗,如果是燃煤电厂,就用所耗煤种的低位热值(可以查到)*年耗煤吨量;如果是燃气电厂,就用天然气的热值*年耗气量。 电厂出口的总产品热值比上输入的各种一次能源消耗热值,就是热效率。 如何求解热效率 当前,能源日逐紧张。如何节能,如何提高能源的利用效率已是摆在人们面前的一个突出而现实的问题。热效率的计算也成为中考热点问题。如何求解热效率,下面通过一些典例进行分析归纳。 一、燃具的效率 例1、小明学习了热学的有关知识后,他想估算一下自己家煤炉的效率是多少。于是小明仔细记录了他家每天烧水、煮饭、炒菜需要的时间,并把它折算成了烧水的时间,相当于每天将30Kg20℃的水烧开。小明家实际平均每天需要烧4块蜂窝煤,按每块蜂窝煤含煤0.5Kg算,他家每天实际用煤2Kg.普通煤的热值为3×107J/Kg,则他家煤炉的效率是多少? [分析与解]:煤炉烧水,化学能转化为内能,水吸收的热量是有用能量,完全燃烧煤所放出的热量是总的能量。煤炉的效率可用η=Q有用/Q总×100%=cmΔt/m'q×100%计算。 Q有用=cmΔt=4.2×103×30×(100-20)J=1.008×107J Q总=mq=2×3×107J=6×107J η=Q有用/Q总×100%=1.008×107J/6×107J=16.8% 二热机的效率 例2、小兵同学想知道一辆小汽车的实际效率是多少。他从驾驶员那了解到:该汽车行驶100Km的耗油量约7Kg。从书上查得汽油的热值q=4.6×107J/Kg。他又测出在平直公路上,用644N的水平拉力可使汽车匀速前进。若空气阻力不计,试求该小汽车的效率是多少? [分析与解]:小汽车行驶,化学能转化为内能后又转化为机械能,对汽车做功是有用的能量,完全燃烧汽油放出的能量是总能量。小汽车的效率可用η=Q 有用/Q总×100%=FS/mq×100%计算。 Q有用=FS=644×105J=6.44×107J Q总=mq=7×4.6×107J=3.22×108J
660MW机组脱硫性能考核试验方案(A版)
x x x电厂2×660M W机组脱硫性能考核试验方案 西安热工研究院有限公司 2011年5月
西安热工研究院有限公司技术方案 版本更新记录
目录 1前言 .................................... 错误!未定义书签。2设备概述 ................................ 错误!未定义书签。3性能保证值 .............................. 错误!未定义书签。4试验依据 ................................ 错误!未定义书签。5试验条件及要求 .......................... 错误!未定义书签。6试验内容及测量方法 ...................... 错误!未定义书签。7试验工况设置 ............................ 错误!未定义书签。8试验测点 ................................ 错误!未定义书签。9试验仪器、仪表校验 ...................... 错误!未定义书签。10试验方法 ................................ 错误!未定义书签。11试验数据处理 ............................ 错误!未定义书签。12试验组织机构 ............................ 错误!未定义书签。附件 1 试验测点清单....................... 错误!未定义书签。附件 2 试验所需仪器及材料................. 错误!未定义书签。 2
电厂锅炉性能试验大纲1
电厂#1机组锅炉性能考核试验方案 1 试验目的 电厂#1机组将于今年移交试生产,为考核机组的各项技术经济指标是否达到合同、设计和有关规定的要求,电厂委托安徽省电力科学研究院,进行#1机组锅炉性能考核试验。 2 试验项目 锅炉性能考核试验项目如下: ●锅炉机组热效率试验; ●锅炉最大出力试验; ●锅炉额定出力试验; ●空气预热器漏风率试验 ●锅炉最低不投油稳燃负荷试验; ●制粉系统出力试验; ●磨煤机单耗试验; 3 试验方案编制依据 本试验方案依据以下文件及规程编制: ●电厂2×600MW超临界燃煤发电机组锅炉技术合同附件; ●电厂2×600MW超临界燃煤发电机组调试、性能考核试验技术服务合同; ●《火力发电厂基本建设工程启动及竣工验收规程(1996年版)及相关规程》; ●《火电机组达标投产考核标准(2001年版)及其条文解释》; ●《火电机组启动验收性能试验导则》; ●GB10184-88《电站锅炉性能试验规程》; ●DL/T 467—2004《磨煤机试验规程》; 4 锅炉设备概况(略) 5 试验前准备 5.1 测点布置 为了保证锅炉性能考核试验的顺利进行,试验前锅炉各部分测点安装完成。 5.2试验燃料 试验前两个星期电厂应准备好试验用煤,试验燃用的煤种应质量稳定,煤质特性分析
应尽可能接近合同规定的设计煤种,以保证性能考核试验能够顺利进行。 锅炉验收试验时使用的设计煤种,其工业分析的允许变化范围为: 干燥无灰基挥发份Δ=±5%(绝对值) 收到基全水份Δ=±4%(绝对值) 收到基灰份Δ=+5%(绝对值) -10% 收到基低位发热量Δ=±10%(绝对值) 灰的变形温度(校核煤种)Δ=-50℃ 当试验条件偏离设计值时,锅炉热效率按GB10184-88予以修正。 5.3 锅炉设备 ,以使锅炉达到最佳的状态。 5.3.3 六台磨煤均可投用。 6 试验准则 6.1试验期间锅炉机组应按试验要求的负荷稳定运行,如遇特殊情况应通知试验负责人员,经试验负责人员同意后,方可进行运行操作,否则不得调节运行条件(危机机组安全的除外)。 6.2试验结束后将煤样、灰、渣样破碎后缩分成2个样品,一个样品在试验结束后送有检定资质的单位化验分析,一个样品电厂留存。 6.3所有试验仪器在使用前需经有检定资质的单位检验合格。 6.4 电厂应派专人协助试验负责单位进行试验前的准备工作和测试工作。 7. 锅炉性能考核试验 7.1 锅炉热效率及空气预热器漏风率试验 7.1.1 试验目的 考核锅炉在设计运行条件下,燃用设计煤种,带额定负荷BRL工况下运行时,锅炉保证热效率不低于93.25%(按低位发热值)。 考核锅炉在BMCR工况时,燃用设计煤种及校核煤种,空气预热器的漏风率(单台)是否达到设计指标。 7.1.2 试验条件 锅炉在BRL 负荷稳定运行。
锅炉测试报告
锅炉热工试验报告 湖南省特种设备检测中心 年月日
锅炉热工试验报告 1.任务及目的要求 根据《特种设备安全监察条例》的要求,受XXXXXX 公司的委托,湖南省特种设备检测中心于年月日对该公司使用的型锅炉(产品编号:)进行热工测试。 测试要求:根据中华人民共和国国务院第549号令,关于修改《特种设备安全监察条例》的决定已于2009年1月24日颁布,并于2009年5月1日正式实施。对高耗能的特种设备,按照国务院的规定实行节能审查和监管。国家质量监督检验检疫总局发布国质检特函〔2008〕264号文《关于推进高耗能特种设备节能监管工作的指导意见》,要求对所有在用工业锅炉实际运行能效状况进行普查,并客观记录相关数据。 测试目的:通过对锅炉热效率的测试,掌握在用锅炉的热效率和能耗情况,评介该锅炉是否满足设计及相关标准要求。 2.试验依据 a)GB/T10180-2003《工业锅炉热工性能试验规程》 b)设计及相关标准要求。 3.项目概况 4.锅炉设计参数及实际燃料特性 锅炉设计相关参数见表1 实际燃料特性见表2
表1 锅炉设计基本参数
5.试验工况说明及结果分析 1. 试验条件 本次热工测试在 XXXXX锅炉车间现场进行,测试期间锅炉运行正常,负荷稳定,燃烧良好。试验在锅炉正常运行状况下进行。 1.1本次试验以燃料低位发热量为基准。 1.2根据现场的实际情况,本次试验采用正、反平衡法来测定锅炉热效率。 2. 试验内容 年月日对本台锅炉进行了热工测试,试验共进行了2个试验工况。根据《工业锅炉热工性能试验规程(GB/T10180-2003)》的要求,2次试验测得的正、反平衡效率之差应不大于5%,2次试验测得的正平衡效率之差应不大于3%,2次试验测得的反平衡效率之差应不大于4%,最终结果取两个试验工况的平均值。 试验期间锅炉燃烧稳定,设备运行正常。试验期间各主要参数维持稳定。试验期间主要进行了以下项目的测量: 2.1 烟气成分分析:利用烟气分析仪测量空气预热器出口烟气中的RO2、O2、CO含量,每15~20分钟进行一次分析。 2.2 排烟温度测量: 在省煤器出口烟道上用烟气分析仪上热电偶测量锅炉的排烟温度。 2.3 进行燃料取样分析:有输送皮带的锅炉在进料口前的输送皮带上取样,无输送皮带的在炉前煤斗或试验煤堆中取样,并进行燃料元素成份及低位发热量的分析。 2.4 飞灰取样:在尾部烟道气流稳定的适当直段处利用飞灰取样器进行取样,条件不允许的,也可在除尘器排灰口处进行取样,每个试验工况的灰样混合后缩分为一个分析样,进行飞灰可燃物含量分析。 2.5 炉渣取样:可从渣流中连续接取,或定期从渣槽(池、斗)内掏取,同时保证炉渣具有代表性,进行炉渣可燃物含量分析。
煤电机组性能测试及能效指标修正规范.doc
附件2: 燃煤电厂综合升级改造机组性能测试技术要求 一、锅炉性能试验及修正 (一)锅炉性能试验应执行最新版《电站锅炉性能试验规程》(GB/T 10184)或《锅炉机组性能试验规程》(ASME PTC 4.1)、《磨煤机试验规程》(ASME PTC 4.2)、《空气预热器试验规程》(ASME PTC 4.3)等规程,原则上执行高标准规程。 (二)锅炉性能试验应优先采用反平衡法,在额定工况下至少开展两次,在修正到相同条件后,两次试验结果(锅炉热效率)的偏差不大于0.35个百分点。 (三)改造前后锅炉性能试验煤种,原则上应采用设计煤种。采用其他煤种时,改造前后试验煤种收到基低位发热量(Q net.ar)偏差不超过1200kJ/kg、收到基挥发分(V daf)偏差不大于3个百分点、收到基灰分(A ar)偏差不大于5个百分点。变更设计煤种的综合升级改造,改造前后锅炉性能试验煤种应分别采用对应的设计煤种。 (四)锅炉性能试验结果应按相应规程修正。若进行空气预热器、省煤器、低温省煤器等改造,应通过试验确定
改造后锅炉排烟温度、空气预热器漏风率、锅炉热效率和供电煤耗变化量。若进行制粉系统、燃烧器等改造,应通过试验确定改造后磨煤机出力、制粉单耗、锅炉飞灰和底渣可燃物、锅炉排烟温度、锅炉热效率和供电煤耗变化量。 二、汽轮机性能试验及修正 (一)汽轮机性能试验执行最新版《汽轮机热力性能验收试验规程的第1部分:方法A—大型凝汽式汽轮机高准确度试验》(GB/T 8117.1)、第2部分:方法B—各种类型和容量的汽轮机宽准确度试验》(GB/T 8117.2)。原则上执行高标准规程。 (二)汽轮机性能试验应在额定工况下开展,不明泄漏量不大于新蒸汽流量的0.3%,试验结果不确定度不大于0.5%;汽轮机性能试验应开展两次,在修正到相同条件后,两次试验结果(汽轮机热耗率)的偏差不大于0.25%。 (三)汽轮机性能试验结果原则上应合理修正主蒸汽压力、主蒸汽温度、再热蒸汽温度、再热器减温水流量(或过热减温水流量)和凝汽器压力(或凝汽器入口循环水温度)等参数。变更设计主蒸汽压力、主蒸汽温度、再热蒸汽温度、再热器减温水量(或过热器减温水流量)的综合升级改造,可不修正相应参数。汽轮机冷端系统改造,可参考相应标准,通过试验确定凝汽器压力及循环水泵功耗变化后,再
热电公司锅炉检修前性能试验报告书
2×210MW#7机组 SY-PDRD-JN-012 平顶山平东热电有限责任公司 #7锅炉A级检修前性能实验报告 中电投河南电力有限公司技术中心 二O一一年四月
批准: 审核: 编写:陈玉良 (章)
工程名称:平顶山平东热电有限公司 #7锅炉A级检修前性能实验 实验时间:2011年4月13日 工程负责:陈玉良 中电投河南电力有限公司技术中心:陈玉良郎勇 冯坤 平顶山平东热电有限公司:李成忠王恒张士豪戚光宇 郝文辉王玉盘杨青春李丽 娅当值运行人员等
目录 摘要3 1 实验目的6 2 实验依据6 3 设备简况7 4.实验测点布置、主要工程测量方法及实验仪器12 5 数据处理方法13 6 实验结果与分析15 7 结论20 8 耗差分析20
摘要 平顶山平东热电有限公司#7锅炉为哈尔滨锅炉厂生产的超高压、自然循环、单炉膛四角切圆燃烧一次中间再热、平衡通风、固态排渣、“ ”型布置汽包锅炉,型号为HG-670/13.7-YM型,为了获取锅炉在不同负荷下主要经济指标,了解本炉运行状况,分析其存在的问题,并为A级检修前评估提供依据。中电投河南公司技术中心于2011年4月13日对该炉进行性能实验、空预器漏风率实验。 实验得到平顶山平东热电有限公司的大力支持,在此表示衷心的感谢! 本次机组实验负荷分别为210MW、3VWO、170MW、130MW,对应锅炉效率依次为87.09%、88.11%、90.71%、91.49%,修正后的锅炉热效率依次为87.09%、88.03%、90.62%、91.49%;机组在210MW工况时,修正后锅炉效率比设计值93.71%降低了6.62%。 机组在210MW工况时,A、B侧空预器两侧漏风率分别为7.65%和19.61%,空预器平均漏风率为13.63%。 机组在210MW、3VWO工况运行时,锅炉热效率偏低的主要原因: 1、飞灰、炉渣可燃物含量高。机组在210MW、3VWO工况时,飞灰可燃物含量分别 为7.48%、6.45%,炉渣可燃物含量分别为17.78%、12.61%。 2、空预器漏风率较大,造成排烟热损失增大。 3、由于DCS内空预器入口氧量比实际值偏高,造成实际炉膛出口氧量偏小,使飞 灰可燃物含量升高,机械不完全燃烧热损失增大,锅炉效率降低。 4、煤粉细度较高。210MW负荷工况下,A、B、C、D粗粉分离出口煤粉细度分别为 27.6%、32%、18%、26.4%,平均煤粉细度为26.00%,比设计值20%偏高6%,造 成飞灰、炉渣可燃物含量升高,机械不完全燃烧热损失增大,锅炉效率降低。 5、入炉煤煤质较差。210MW负荷工况下,入炉煤收到基灰分为40.45%,比设计值 29.45%,偏高11%,收到基低位发热量为17.615 MJ/kg,比设计值20.62 MJ/kg 偏低3.005MJ/kg,造成机械不完全燃烧热损失升高。 6、一、二次风配风有待完善。 存在问题: 1、机组在210MW负荷工况时,DCS内A、B侧空预器入口氧量分别为4.820%、5.13%,