合成氨装置流程简介
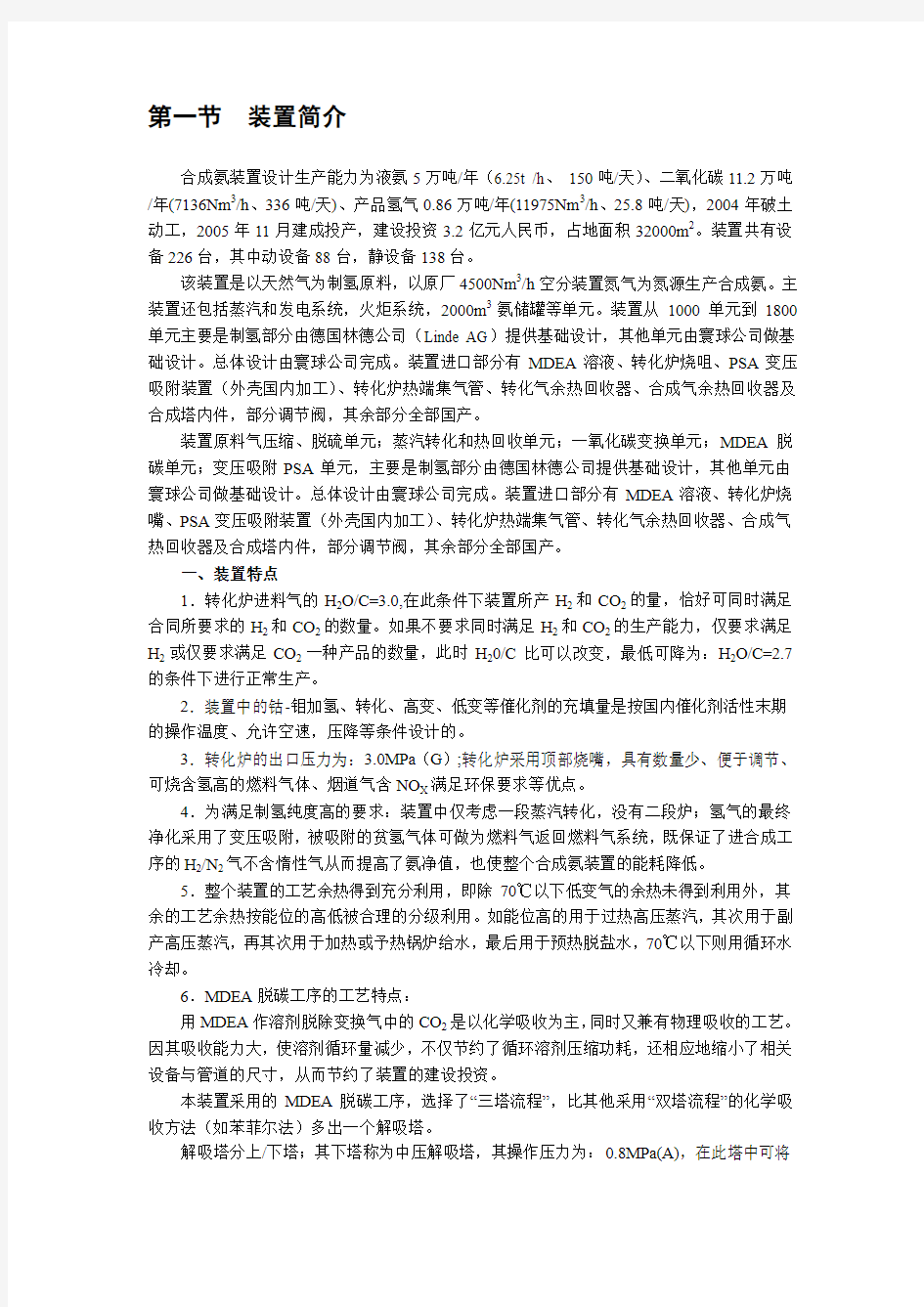

第一节装置简介
合成氨装置设计生产能力为液氨5万吨/年(6.25t /h、150吨/天)、二氧化碳11.2万吨/年(7136Nm3/h、336吨/天)、产品氢气0.86万吨/年(11975Nm3/h、25.8吨/天),2004年破土动工,2005年11月建成投产,建设投资3.2亿元人民币,占地面积32000m2。装置共有设备226台,其中动设备88台,静设备138台。
该装置是以天然气为制氢原料,以原厂4500Nm3/h空分装置氮气为氮源生产合成氨。主装置还包括蒸汽和发电系统,火炬系统,2000m3氨储罐等单元。装置从1000单元到1800单元主要是制氢部分由德国林德公司(Linde AG)提供基础设计,其他单元由寰球公司做基础设计。总体设计由寰球公司完成。装置进口部分有MDEA溶液、转化炉烧咀、PSA变压吸附装置(外壳国内加工)、转化炉热端集气管、转化气余热回收器、合成气余热回收器及合成塔内件,部分调节阀,其余部分全部国产。
装置原料气压缩、脱硫单元;蒸汽转化和热回收单元;一氧化碳变换单元;MDEA脱碳单元;变压吸附PSA单元,主要是制氢部分由德国林德公司提供基础设计,其他单元由寰球公司做基础设计。总体设计由寰球公司完成。装置进口部分有MDEA溶液、转化炉烧嘴、PSA变压吸附装置(外壳国内加工)、转化炉热端集气管、转化气余热回收器、合成气热回收器及合成塔内件,部分调节阀,其余部分全部国产。
一、装置特点
1.转化炉进料气的H2O/C=3.0,在此条件下装置所产H2和CO2的量,恰好可同时满足合同所要求的H2和CO2的数量。如果不要求同时满足H2和CO2的生产能力,仅要求满足H2或仅要求满足CO2一种产品的数量,此时H20/C比可以改变,最低可降为:H2O/C=2.7的条件下进行正常生产。
2.装置中的钴-钼加氢、转化、高变、低变等催化剂的充填量是按国内催化剂活性末期的操作温度、允许空速,压降等条件设计的。
3.转化炉的出口压力为:3.0MPa(G);转化炉采用顶部烧嘴,具有数量少、便于调节、可烧含氢高的燃料气体、烟道气含NO X满足环保要求等优点。
4.为满足制氢纯度高的要求:装置中仅考虑一段蒸汽转化,没有二段炉;氢气的最终净化采用了变压吸附,被吸附的贫氢气体可做为燃料气返回燃料气系统,既保证了进合成工序的H2/N2气不含惰性气从而提高了氨净值,也使整个合成氨装置的能耗降低。
5.整个装置的工艺余热得到充分利用,即除70℃以下低变气的余热未得到利用外,其余的工艺余热按能位的高低被合理的分级利用。如能位高的用于过热高压蒸汽,其次用于副产高压蒸汽,再其次用于加热或予热锅炉给水,最后用于预热脱盐水,70℃以下则用循环水冷却。
6.MDEA脱碳工序的工艺特点:
用MDEA作溶剂脱除变换气中的CO2是以化学吸收为主,同时又兼有物理吸收的工艺。因其吸收能力大,使溶剂循环量减少,不仅节约了循环溶剂压缩功耗,还相应地缩小了相关设备与管道的尺寸,从而节约了装置的建设投资。
本装置采用的MDEA脱碳工序,选择了“三塔流程”,比其他采用“双塔流程”的化学吸收方法(如苯菲尔法)多出一个解吸塔。
解吸塔分上/下塔;其下塔称为中压解吸塔,其操作压力为:0.8MPa(A),在此塔中可将
MDEA溶剂吸收的有效气体(如H2等)自溶剂中先解吸出来并予以回收。它不仅提高了产品CO2的纯度(达99%干基),同时还节约了能耗。解吸塔的上塔被称为低压解吸塔,在此塔中将有部份CO2解吸出来,它与来自再生塔顶并导入低压解吸塔的CO2汇合,一起构成产品CO2,其压力为:0.2MPa(A)。由于产品CO2的压力比“两塔流程”中逸出的CO2压力高约0.1MPa,在出塔温度相等的条件下,压力的提高可减少CO2带出的水蒸汽量;加之溶剂循环量减少等因素,可使再沸器的热负荷降低。除此之外,由于CO2的排出压力提高,也减少了后系统在需用较高压力的CO2时,CO2压缩机的压缩功。再沸器的热负荷降低,CO2压缩机的压缩功减少,使合成氨的吨氨能耗降低。
由于再沸器的热负荷降低,故仅要一台用低变气提供热源的再沸器向再生塔提供热量已能满足工艺的要求;而在苯菲尔工艺中,除要一台用低变气提供热源的再沸器向再生塔提供热量外,还要增加另外一台蒸汽再沸器补充其热量的不足,可见MDEA工艺较苯菲尔工艺节能。
除MDEA工艺节能之外,MDEA溶液比苯菲尔溶液腐蚀性小。
据文献上介绍,把热钾碱工艺(即苯菲尔工艺)脱CO2改为MDEA工艺脱CO2时,其他塔设备不变,仅需增加一台解吸塔,处理能力可提高10%。这也从另一侧面说明了MDEA 工艺的优越性。
二、装置组成
本装置主要有以下几部分组成:
本装置由天然气压缩脱硫、蒸汽转化和热回收、CO变换、MDEA脱碳、变压吸附、合成气压缩、氨合成、氨冷冻、氮气压缩及脱氧、蒸汽发电系统、火炬系统、氨储罐等几部分组成。
三、原料来源
本装置用天然气来自萨喇杏油田配输管系统,原料天然气由萨南、萨中、杏九输气管线经过天然气公司甲醇厂配气站来进行供给。装置所用循环水由给排水车间第二循环水场提供,除盐水由动力车间第三除盐水站供给,氮气由原厂4500 Nm3/h空分装置供给,蒸汽由动力车间锅炉房供给,新鲜水来自全厂新鲜水管网。
(1) 主要产品:合成氨
(2) 副产品:氢气、CO2
四、装置历年来技术改造情况
自装置建成试投产以来进行了部分技术改造,截止至2008年11月份主要改造项目有:转化炉平衡锤改造、合成气机组管系振动改造、装置伴热系统改造、转化静态混合器改造、合成系统氢氮气混合器改造、更新E5114芯子材质、更新E5111材质、合成塔出口管系改造、钴钼反应器加电热器、E1414改造、工艺冷凝液回收项目等。
第二节工艺原理
一、天然气脱硫原理
氧化铁脱硫槽是全装置第一个与天然气接触的脱硫系统,主要进行粗脱硫,保证出口天然气中的达到设计要求的25PPm。氧化铁脱硫剂的组成为αFe2O3.XH2O,反应如下:
Fe(OH)3+3H2S→Fe2S3+6H2O
此反应为不可逆反应,在常温、常压下都可进行反应,并且原料气中含硫量与所脱硫接触时间成正比,因此我们在一般情况下采用串联方法。另外氧化铁脱硫剂还可脱除简单有机
硫化物。
钴钼加氢器是里边装有钴钼催化剂,在有氢气存在时,把天然气中的有机硫转变为无机硫的设备,反应如下:
COS+H2→H2S+H2O
CS2+4H2→2H2S+CH4
RSH+H2→H2S+RH
钴钼催化剂的主要组成是MoO3、CoO,并以Al2O3为载体。催化剂在硫化状态下活性最高,因此,在更换催化剂后要进行硫化,使氧化态的钴钼变成硫化态的钴钼,钴钼加氢器是利用加入原料天然气量3-5%的氢气,在钴钼催化剂的作用下将有机硫转变成无机硫。
R—S—R CO—MO
+ H2 360℃-380℃H2S
R—SH
氧化锌脱硫槽是吸以收H2S和R—SH、R—S—R’的装置,具体有以下的反应:
H2S+ZnO→ZnS+H2S
天然气中的硫对转化镍催化剂、合成铜催化剂的影响非常大,因此在转化炉前要求将天然气中的硫降到0.1PPm以下。
转化催化剂硫中毒是因为天然气中的硫与暴露的镍进行化学吸附,破坏了镍晶体表面的活性中心的催化作用,因此,只要存在PPm级数量的硫就会造成催化剂的中毒,从而转化气中的甲烷含量急剧升高,转化炉管温度也随之升高,影响炉管的使用寿命及安全。此中毒是可逆反应,在大水碳比的情况下,轻微硫中毒可以恢复合成催化剂对硫很敏感,并且硫中毒是不可逆反应,通常认为是硫与铜生成硫化铜及硫化亚铜的缘故。中毒机理如下:Cu+1+O-2+H2S→Cu1SH-1+OH-1。当工艺气体中有H2S时,由触媒表面反应产生Cu+1SH-1及OH-,然后易挥发的硫化物即行挥发进入气相,触媒即由于失去活性中心Cu+1而失活,并且失活是不可逆的,铜触媒发生永久性中毒,且为累积性中毒。脱硫系统运行目标:控制氧化锌脱硫罐出口S≤0.3PPm,保护转化催化剂、合成催化剂不出现中毒情况。提高脱硫温度可提高净化脱硫效果,增加硫容量。
二、天然气蒸汽转化反应原理
天然气与蒸汽混合在镍触媒的作用下进行转化分解,转化反应所需的热量由转化炉辐射段顶部火嘴提供,燃料为PSA吹除气、脱碳系统闪蒸气、天然气、合成冷冻系统驰放气。
CH4+H2O=CO+3H2-Q
CnH2n+(2+n)H2O=nCO+(2n+1)H2-Q
CO+ H2O =CO2+H2+Q
三、高、低变换反应原理
一氧化碳与水蒸汽分子吸附在高、低变催化剂活性表面被活化,活化分子相互作用生成二氧化碳和氢气,生成分子从催化剂表面解析。
CO+ H2O =CO2+H2+Q
四、MDEA溶液脱碳原理
MDEA的主要成分是N-甲基二乙醇胺,在加压和有活化剂存在的条件下,N-甲基二乙醇胺与二氧化碳的反应为:
R2CH3N+CO2+H2O R2′NH R2CH3NH-+HCO3-
MDEA脱碳溶液是一种选择性较好的物理化学吸收剂,对二氧化碳既具有化学吸收性能,又具有物理吸收性能,提高压力,降低温度,有利于二氧化碳气体的溶解,氢气、氮气及其他惰性气体在MDEA溶液中的溶解度很小,而且不发生化学反应,因而在脱碳过程中氢气、氮气损失较少。
MDEA与二氧化碳反应生成不稳定的碳酸氢盐,加热后容易再生。MDEA在加压时对二氧化碳的溶解度大,在减压闪蒸时解吸出的二氧化碳完全,因此,MDEA脱碳工艺是一种低能耗脱碳工艺。
五、PSA制氢原理
PSA变压吸附是以物理吸附为基础,利用不同气体组份在相同压力下在吸附剂上的吸附能力不同和同一气体组份在不同压力下在吸附剂上的吸附容量有差异的特性,来实现对混合气中某一组份的分离提纯。高挥发性、低极性分子氢气与其它组份二氧化碳、甲烷、氮气、一氧化碳相比是非吸附性的,因此含氢混合气中的杂质组份能够被选择吸附而获得纯净的氢气。
六、合成反应原理
氨的合成反应为可逆的放热反应,其化学反应方程式为:
铁系催化剂
N2(g)+ 3H2(g) 2NH3 (g) + Q
由于该反应为可逆放热反应,仅有一部分H2和N2合成为NH3,而且反应后体积缩小,因此低温、高压下是有利于反应平衡向右进行的,即低温、高压下操作可提高转化率。
第三节生产工艺流程简述
一、脱硫1000单元
本装置脱硫系统包括三部分:氧化铁粗脱硫系统、钴钼脱硫系统、氧化锌脱硫系统
1、流程叙述
自界区外来压力0.3MPa(g)、流量9240 Nm℃/h(最大10101 Nm3/h)、总硫≤100PPm的天然气首先进入天然气油水分离器D1004,经油水分离后进入E1016经0.5 MPa(g)190℃的低压蒸汽加热至30℃进入两台串联的、内部装有氧化铁脱硫剂的脱硫反应器(R1003A/B)进行脱硫。这两台反应器的其中任何一台都可以做为第一反应器;也可以只使用一台反应器进行正常生产,并对另一台反应器进行脱硫剂的更换,经氧化铁脱硫后总硫降至PPm。脱硫后天然气经除尘过滤器S1001一股作为燃料天然气,减压进入燃料系统,作为一段炉的燃料;另一股是作为原料天然气。
原料天然气首先进入原料气压缩机,压缩到约1.7 MPa(g)后,在压缩机二段配入一小股来自变压吸附单元的氢气226 Nm3/h,混合后再入原料气压缩机,进一步压缩到3.7 MPa(g)。
3.7 MPa(g)的原料气,首先进入原料气预热器(E1015),被高变气预热到380℃,再进钴-钼加氢反应器(R1002)。通过加氢反应,天然气中的有机硫转化为H2S。
热的原料天然气在钴-钼加氢反应器(R1002)反应后,通过两台串联的、内部装有氧化锌脱硫剂的ZnO脱硫反应器(R1001A/B)进行脱硫。这两台反应器的使用与氧化铁脱硫罐相同。脱硫后的天然气总硫降至0.1PPm,脱硫后的气体去转化部分。
氧化锌脱硫的方式是按如下反应进行:
H2S + ZnO——→H2O + ZnS
二、蒸汽转化和余热回收1100单元
脱硫后的原料气体与来自透平发电机组的一级抽汽,即3.7MPa(g)的中压蒸汽混合,水碳比控制为3.0,然后进入置于蒸汽转化炉对流段中的原料气加热器I/II(E1115A/B)加热。为了防止在转化炉进气总管和转化炉管内结碳,必须控制在对流段预热的原料气温度小于600℃,因此采用两组原料气预热器串联,并且将部分热量用高压汽包移走的温度控制方式。具体说明如下:进原料气加热器II(E1115B)的进料气温度为356℃,被加热到473℃后离开E1115B,其中约16%的473℃的进料气通过温度控制阀的控制,被送到高压汽包(D1131)内的盘管冷却到332℃后,与未冷却的进料气混合后,送入原料气加热器I(E1115A)加热到580℃送到转化管。加热到580℃后,进入蒸汽转化炉(F1101)的转化管内与水蒸汽进行烃类转化反应。
其主要反应方程式为:
CH4 + H2O——→CO + 3H2
CO + H2O——→CO2 +H2
转化反应需要的热量由燃烧来自PSA单元的吹除气、脱碳系统的解析气、燃料天然气和一部分合成驰放气提供。如果出PSA单元的H2产品暂时没有用户,也可以将其一部分作为燃料。
蒸汽转化炉内依传热方式的不同而分辐射段和对流段。辐射段的传热方式主要为辐射传热,装有催化剂的转化管,是置于辐射段内。出转化管的气体温度为850℃、压力3.0MPa(g),残余甲烷约6.75%(mol%干基)。从转化管出来的热气体被收集到热集气管、冷集气管后,送到转化气余热回收器(E1122)被迅速冷却到340℃,并副产8.15 MPa(g)高压饱和蒸汽,然后进入CO变换工序。
烟道气离开转化炉辐射段后进入对流段,依次与原料气加热器II/I(E1115B/A),蒸汽过热器(E1116),蒸汽发生器(E1118),燃烧空气预热器(E1121)换热后,温度降到151℃,并通过烟道气引风机(C1107)排入烟囱(Y1191)放空。
蒸汽转化炉烧嘴用燃烧空气由空气鼓风机(C1109)供给。
三、CO变换1200单元
出转化气余热回收器(E1122)的转化气CO含量为13 % (mol%干基),进入高温变换反应器(R1202)。在高变催化剂上发生变换反应,其反应方程式如下:
CO + H2O——→H2 + CO2
变换反应是放热反应,转化气进入装有铁-铬催化剂的高温变换反应器(R1202)后,温度由340℃升到406℃;出高温变换反应器的变换气中的CO含量被降到:3.2%(干基)。
高变气首先经过原料气预热器(E1015)回收热量,然后进入锅炉给水加热器II(E1212)加热部分锅炉给水,高变气的温度降为195℃后进入低温变换反应器(R1204)。
在低温变换反应器(R1204)中,装有铜系催化剂,高变气在催化剂床上继续发生变换反应,出低温变换反应器的低变气中的CO含量降到0.37%(干基),温度升高到217℃。
变低气再经锅炉给水预热器I(E1221)、MDEA脱碳单元的再生塔再沸器(E1412)和脱盐水预热器(E1214)回收热量后,去低变气冷凝液分离器I(D1231)分出工艺冷凝液。然后气体经低变气水冷器(E1216)冷却,进入低变气冷凝液分离器II(D1232)分出冷凝液。出低变气冷凝液分离器II的气体被送入MDEA脱碳部分。
出低变气冷凝液分离器I(D1231)和低变气冷凝液分离器II(D1232)的工艺冷凝液经
工艺冷凝液泵升压后在工艺冷凝液汽提塔T1201中进行汽提,使氨含量降至大约30ppm,CO2含量降至几乎为零,甲醇降至5ppm。汽提后的冷凝液中含有大约2.5ppm的金属。汽提后的工艺冷凝液经冷却后送出界区。
工艺冷凝液的处理是在一台填料塔T1201中用一部分中压工艺蒸汽进行汽提。工艺冷凝液在E1217中经汽提塔排出液预热后自塔顶进入塔内,汽提蒸汽从塔底进入。蒸汽和工艺冷凝液在填料段逆流接触,汽提出工艺冷凝液中易挥发组份和溶解的气体,汽提后的工艺冷凝液只含微量的氨和甲醇。塔顶排出的蒸汽用作工艺蒸汽。汽提后的冷凝液在E1217中回收热量,再经E1218冷却,然后送入界区回收利用。
四、MDEA脱碳1400单元
采用BASF的专利技术,是一种低能耗的MDEA脱碳工艺。它为两段吸收、两段再生流程。
来自变换工序的变换气送入CO2吸收塔(T1401)下段,大量CO2在此段被MDEA半贫液吸收,剩余CO2在上段用MDEA贫液吸收。工艺气出塔前,在吸收塔的顶部,用锅炉给水洗下气流中夹带的微量MDEA。出吸收塔的工艺气温度约为50℃,CO2含量小于1000ppm。
脱碳后的工艺气经净化气水冷却器(E1417)冷却到40℃后,在净化气冷凝液分离器(D1430)中分离出水份,然后送到变压吸附工序。
自CO2吸收塔(T1401)下段引出的吸收了CO2的富液,经半贫液泵透平(X1409)回收能量后,降压到0.85MPa(g)送到中压解吸塔(T1402),在此解吸出的大部分H2和少量的CO2从塔顶引出并作为燃料送到蒸汽转化炉。
中压解吸塔(T1402) 塔底溶液进一步减压,送到低压解吸塔(T1403),在0.11 MPa(g)下继续解吸出CO2,其余部分CO2则由来自再生塔(T1404)顶部的CO2饱和蒸气气提得到。低压解吸塔(T1403)塔顶得到的CO2产品,经产品CO2气水冷器(E1415)及产品CO2气氨冷器(E1416)冷却后,送到产品CO2气冷凝液分离器(D1431)分离出冷凝液后,得到10℃,纯度约99%(干基)的产品CO2送出界区。产品CO2气冷凝液分离器(D1431)分离出的冷凝液由低压解吸塔顶冷凝液泵(P1473A/B)将部分凝液打回流到低压解吸塔(T1403)塔顶,用以洗下解吸CO2气中所夹带的微量MDEA;另一部分与净化气冷凝液分离器(D1430)分出的冷凝液合并后作为污水,送污水处理装置。
低压解吸塔(T1403)塔底的排出液分成两部分;一部分由半贫液泵(P1471A/B)加压并作为半贫液送到CO2吸收塔(T1401)下段,另一部分由再生塔给料泵(P1472A/B)经贫液/半贫液换热器(E1413)加热后送再生塔(T1404)继续再生。
在再生塔(T1404)塔底,由再沸器(E1412)提供热源,使溶液中的CO2解吸并从塔顶逸出,送到低压解吸塔(T1403)作为气提气,气提出部分的CO2产品。再生后的贫液从塔底排出并送到贫液/半贫液换热器(E1413)与半贫液换热后,送贫液水冷却器(E1414)冷却后,经贫液泵(P1474A/B)加压送到CO2吸收塔(T1401)上段。其中部分贫液经贫液第一过滤器(S1451)、贫液第二过滤器(S1452)、贫液第三过滤器(S1453),滤下固体颗粒、杂质和容易引起发泡及设备堵塞的物质等。
为回收能量,其中一台半贫液泵(P1471A)是由半贫液泵透平(X1409)和电机联轴驱动的,设计时,电机的驱动功率按泵消耗功率的100%考虑。另一台半贫液泵(P1471B)由电机驱动。
为防止MDEA溶液发泡,由消泡剂系统(Y1491)往再生塔(T1404)的进料管线及贫
液泵(P1474A/B)入口管线间断地加入消泡剂。
在MDEA溶液贮罐(D1432)中贮存有溶剂,用溶液输送泵(P1475)往系统里补充。
如果长期停车,所有塔和管路中的MDEA溶液都可以排放到MDEA溶液贮罐(D1432)中。贮罐中装有MDEA溶液加热器(E1420),用于冬季加热、以防溶液结晶或结冻。
五、变压吸附1800单元
变压吸附工序共有6台吸附器(A1831~A1836)内装吸附剂,其吸附器的数目是根据装置规模及操作条件等因素确定的。本工序将用于进一步脱除脱碳工序送来的工艺气中所含有的CO,CO2,CH4,及H2O等杂质。在高压下,这些杂质被吸附而得到温度为:40℃、压力为:2.58MPa(g)、纯度为:99.99 vol%的H2产品。
通过一系列减压和用H2吹除等步骤,使CO、CO2、CH4及H2O等杂质脱吸,使吸附剂得以再生。吸附器排出的脱吸气体、经过PSA脱吸气收集罐(D1848)收集后,送到一段炉的燃料气系统,脱吸气体中除含CO、CO2、CH4及H2O外,还含有大量的H2。
吸附器按下列步骤进行操作:
在产品操作压力下吸附净化气中的杂质,得到工艺要求的产品H2。
经一系列减压步骤,使一台吸附器的压力降低到再生压力,用膨胀气加压另一台已完成再生的吸附器,然后再送去把第二个处于低压状态的吸附器加压到某个压力中间值,最后吹扫第三个吸附器,直至膨胀到最低压力,送入吹除气管线。
用来自另一个处于低压状态下的吸附器的膨胀气,吹扫此降低到再生压力的吸附器。
再用来自其他吸附器的膨胀气加压此吸附器,并用H2产品气加压到最终操作压力。
在此循环过程中的任何一个阶段,系统中仅一台吸附器处于操作状态(即吸附状态),其余的五台吸附器将处于不同状态下的再生状态(即脱吸状态)。
用一个可编程逻辑控制器(PLC)来实现对PSA系统的操作控制,以使得PSA系统可以高效运转。PLC可以根据制氢装置的负荷变化、净化气中的杂质含量,相应地调节PSA 系统。
吹除气被送到PSA脱吸气收集罐(D1848)中,从而可使吹除气组成、压力稳定(即:使燃料气总管的压力、热值不会波动),这对转化炉燃料系统的稳定操作十分重要。
净化后出PSA系统的H2压力约2.58MPa(g),一部分送氨合成工序,另一部分作为产品外输。
六、合成气压缩5000单元
来自变压吸附单元的氢气和来自氮气压缩机的氮气,按氢、氮摩尔比3:1混合后,最终形成压力为2.55 MPa(g)的新鲜气。它被导入合成气压缩机(C5001A/B)进一步的被压缩到12.2 MPa(g),再与来自合成回路冷交换器(E5115)的27℃、12.2MPa(g)循环气混合,再返回压缩机,继续压缩到12.9 MPa(g),经滤油器,除去夹带的微量油后,送入合成回路。合成气压缩机为二台往复式压缩机,其中一开一备。合成气压缩机出口设计油含量最大不超过
0.2mg/Nm3
七、氨合成5100单元
反应为可逆的放热反应,其化学反应方程式为:
催化剂
N2(g)+ 3H2(g) 2NH3 (g)+ Q
由于该反应为可逆放热反应,仅有一部分H2和N2合成为NH3,而且反应后体积缩小,因此低温、高压是有利于反应平衡向右进行的,即低温、高压下操作可提高转化率。但是由
于该反应速度较慢,保证一定的反应温度和压力尤为重要。
出合成气压缩机(C5001A/B)温度39.5℃、压力12.9 MPa(g)的合成气进入热交换器(E5113),在此它与出塔气换热,温度升至242 ℃,然后进入氨合成塔(R5101),入塔气中氨含量为:5.59 %(vol)。氨合成塔的操作压力为:12.8 MPa(g)。
氨合成塔采用Casale拥有专利技术的轴、径向均流合成塔内件,该塔为立式,并由高压外壳和催化剂筐两部分构成。催化剂筐内有三层催化剂床,床内装有颗粒较小的铁系催化剂(1.5~3.0mm)。在三个床层内既有径向流也有轴向流,使得床层达到充分地利用。在第二床层还设有换热器,以通过间接换热移去氨合成的反应热。
合成气由合成塔顶部进入,沿外壳和内筐之间的环隙空间向下流到底部,使外壳温度保持为300℃以下,以保护合成塔外壳。然后气体在底部折流上升,流过贯穿第三催化剂床层的中心管后,再向上穿过换热器的管程,与来自第二床层的合成气换热升温。然后流过贯穿第一催化剂床层的中心管到达塔顶后进入第一床层,工艺气体沿径向和轴向穿过第一床层,开始反应,温度升高;工艺气体从第一床层出来后,加入冷激气降温后进入第二床层,然后进入到换热器壳程,与进入塔内没有反应的工艺气体换热,温度降低。在换热器壳程被冷却后的工艺气体,继续进入第三床层,在第三床层同样沿径向和轴向穿过催化剂层,进一步进行氨的合成反应,反应后的气体由合成塔底部离开合成塔,出口气体含氨达18.33 % (vol),温度约为429℃。
第一、二床层入口温度可以由副线和冷激线的工艺气体来控制。
合成塔入口惰性气体(氩,甲烷等)的浓度,初期工况下约为0.186%(mol),末期工况下约为0.16%(mol)。
氨合成塔壳内设有一台电加热器,用于开车时催化剂的升温和还原。
离开合成塔的429?C的合成气,先经过合成气冷却器(E5111)回收反应热,副产8.15MPa(g)的高压饱和蒸汽。再经热交换器(E5113)加热入塔合成气而被冷却后,进入水冷器(E5114)冷却到40?C。
然后,合成反应气经下列步骤进一步冷却、冷凝并分离出液氨产品:
——在冷交换器(E5115)中,合成气与从氨分离器(D5131)顶部出来的冷循环气换热,在管程,合成气被冷却到约35?C,在此有部分液氨被冷凝下来,分离出少量的液氨。
——反应气进一步在氨冷器(E5116)中冷却,并与来自冷交换器(E5115)的液氨混合,然后进入氨分离器(D5131)。氨分离器(D5131)分离出的气体进入冷交换器(E5115)的壳程回收冷量。
由冷交换器出来的循环气返回合成气压缩机三段,与新鲜合成气混合并进一步压缩后,再次循环进入氨合成塔。
由氨分离器(D5131)分离出的高压液氨,经减压阀排放到氨闪蒸槽(D5132)。氨闪蒸槽(D5132)的压力约为2.60 MPa(g),液氨中的溶解气体被释放出来,送至合成气压缩机(C5001A/B)入口,压缩后进入循环系统。
生产的液氨由液位控制系统控制送入氨贮罐(D5501)。
八、氨冷冻5200单元
来自氨受槽(D5234)的液氨作为以下三个换热器的制冷剂:弛放气冷却器(E5213)、氨冷器(E5116)、产品CO2气氨冷器(E1416)。液氨在换热器中蒸发制冷,气氨进入氨压缩机入口缓冲罐(D5231),其压力为0.41 MPa(g),然后进入氨压缩机压缩,升压至约1.58 MPa(g)后,进入最终水冷器(E5211)被循环水冷却、冷凝。冷凝下来的40℃,1.53 MPa(g)
的液氨流回氨受槽(D5234)。
另外,氨球罐(D5501)内的气氨和少量不凝气体被送入氨压缩机入口缓冲罐(D5231),然后进入氨压缩机。
氨冷冻系统的液氨可由氨闪蒸槽(D5132)补充或送出,而多余的液氨经氨受槽(D5234)的液位控制系统流入氨球罐(D5501)。
氨受槽中的气体,经弛放气冷却器(E5213)冷却,将其中的氨冷凝下来流回氨受槽(E5234)。未凝的弛放气送至燃料气系统,以作为转化炉(F1101)的燃料气。
九、氨球罐5500单元
新装置在原罐区新增一台直径15.7m,容积2000m3的氨球罐(D5501),用于储存产品液氨。从氨闪蒸罐来的液氨用其自身的压力直接压入氨球罐内。为防止球罐超压,球罐内闪蒸出的气氨和少量惰性气体送入氨压缩机缓冲罐而进入氨冷冻系统。
另外配置了氨输送泵(P5501A/B),将其产品液氨送出界区。
本装置氨产品储存能力与储存周期见下表。本装置液氨产品除4万吨/年由管道送至邻近大庆炼化公司外,其余1万吨液氨产品汽运。罐区贮存按14天2086吨贮量设计,罐区原贮存能力1062吨,新建氨球罐贮量约1024吨。
十、蒸汽发电系统8000单元
蒸汽的发生:来自界区的脱盐水经过脱盐水预热器(E1214)预热到85℃后送到脱氧器(D8031)。通过低压蒸汽脱氧,化学加药,调节PH值后,作为锅炉给水,通过锅炉给水泵送到装置内的各用户。一部分锅炉给水送到高压汽包(D1131),通过转化气余热回收器(E1122)和蒸汽发生器(E1118)产生8.15MPa(g)高压饱和蒸汽。另一部分锅炉给水送到合成气冷却器(E5111)也产生8.15MPa(g)高压饱和蒸汽。两部分高压蒸汽混合,在一段炉对流段蒸汽过热器(E1116)中过热至450℃后,送入蒸汽发电系统(Y8099)。
蒸汽发电机组是以供热为主、发电为辅,以热定电。来自蒸汽过热器(E1116)的高压过热蒸汽,经抽汽、背压式蒸汽透平发电机组的高压段后,一部分中压蒸汽被抽出,作为蒸汽转化所需工艺蒸汽,其余中压蒸汽全部进入蒸汽透平低压段,出蒸汽透平低压段的低压蒸汽被送入低压蒸汽管网。
本装置蒸汽系统共有三个压力等级的蒸汽:
高压过热蒸汽:压力7.9 MPa,温度450℃
中压蒸汽:压力3.7 MPa,温度358℃(从界区外来的备用中压蒸汽的压力为3.9 MPa(g),温度为410℃)
低压蒸汽:压力0.5 MPa,温度190℃
7.9 MPa(g),450℃高压过热蒸汽的用户主要为蒸汽透平发电机组。
3.7 MPa(g),358℃中压蒸汽主要作为蒸汽转化用的工艺蒸汽。
0.5 MPa(g),190℃的低压蒸汽的使用主要有三处:一处是用于脱氧器(D8031)脱氧、一处用于氧化铁入口天然气预热(E1016)和冬季时送入燃烧空气除霜器(E1127)加热燃烧空气;剩余部分送至界区。
十一、火炬系统9000单元
本装置设有两个火炬系统,用于处理本装置正常、事故及紧急情况下排放的可燃性废气。为防止二氧化碳和氨反应生成氨基甲酸胺结晶,将含氨火炬气和不含氨火炬气分开处理。
装置各排放点排放的可燃性气体由总支管,经分液罐分离液体后,汇入火炬总管,通过火炬总管送至火炬系统。火炬系统包括水封罐、火炬筒体(配有分子密封器)、火炬头(配
有长明灯、蒸汽喷射器等)、自动电点火设施、点火火焰探测器,支撑结构、和其它公用工程设施等。可燃性排放气经火炬总管先后通过水封罐,沿火炬筒体上升至高架的火炬头,燃烧后排入大气。
制氢和净化装置火炬气最大排放量为27.38吨/小时,火炬系统按此排放量设计。采用二路蒸汽助燃无烟火炬头,蒸汽最大用量2.5吨/小时,尽量做到无烟燃烧,减少环境污染。火炬头公称直径DN600;含氨火炬气最大排放量为13.82吨/小时,火炬系统按此排放量设计。采用带伴热燃烧器火炬头,以确保氨的燃烧,火炬头公称直径DN400。
设高空点火系统和地面点火系统两种点火系统。地面点火系统由火炬头的长明灯和一台地面内传焰点火器组成,两火炬共用一台地面内传焰点火器,采用现场手动操作,作为火炬的备用点火方式;高空点火系统由高空点火装置和PLC仪表控制系统组成,制氢火炬设三台高空点火装置,氨火炬采用两台高空点火装置。
制氢、净化装置火炬和含氨火炬气处理火炬均高80m,以火炬为中心,120米半径范围内,无其他设施。满足热辐射强度要求。火炬系统设有严格的分液设施,确保进入火炬的火炬气不含任何可燃液体。
十二、冷凝液回收单元
含微量氨、CO2及甲醇、高级醇的工艺冷凝液经工艺冷凝液泵升压后在工艺冷凝液汽提塔E101中进行汽提,使氨含量降至大约30ppm,CO2含量降至几乎为零,甲醇降至5ppm。汽提后的冷凝液中含有大约2.5ppm的金属。汽提后的工艺冷凝液经冷却后送出界区。
工艺冷凝液的处理是在一台填料塔T1201中用一部分中压工艺蒸汽进行汽提。工艺冷凝液在E1217中经汽提塔排出液预热后自塔顶进入塔内,汽提蒸汽从塔底进入。蒸汽和工艺冷凝液在填料段逆流接触,汽提出工艺冷凝液中易挥发组份和溶解的气体,汽提后的工艺冷凝液只含微量的氨和甲醇。塔顶排出的蒸汽用作工艺蒸汽。汽提后的冷凝液在E1217中回收热量,再经E1218冷却,然后送入界区回收利用。
浮雕施工组织设计
.. 目录 1. 工程概况 2. 施工前准备 .. 错误!未定义书签。 3. 室干挂材墙面工艺流程框图错误!未定义书 3.1施工工艺流程图:错误!未定义书签。 4. 干挂材墙面施工工艺错误!未定义书签。4.1测量放线 (5) 4.2龙骨加工 (6) 4.3竖向主龙骨安装 (8) 4.4水平次龙骨安装 (8) 4.5材加工 (8) 4.6镶挂黄锈材板 (8) 4.7材擦缝、墙面清理、验收 (9) 5.质量保证项目 (10) 专业资料
1.工程概况: 工程名称:金道城项目一期三标段 建设单位:金道房地产开发有限公司 设计单位:中国东北设计研究院 监理单位:新佳城工程管理有限公司 施工单位:上海市第五建筑有限公司 本工程位于市浑南新城白塔路与桃仙大街交汇处,东临本大道,生活办公区位于白塔路西侧。该工程总建筑面积为168957.04m2,多层部分的建筑总面积约为47275 m2,包括一个转角合院、一个合院和一个单体住宅组成,结构形式为框架剪力墙结构,浮雕安装总面积为260M2.。 2. 施工前准备: 2.1 浮雕:本项目材料为甲供材,进场前应确定浮雕的品种、颜色、花纹和尺寸规格及雕刻深度,并格控制、检查其抗折。抗拉及抗压强度,吸水率、耐冻融循环等性能。浮雕在运抵工地后,不得随意拆箱,并放置于施工干扰少,无重物坠落的平整场地保管。 2.2 合成树脂胶粘剂:用于粘贴材背面的柔性背衬材料,要求具有防水和耐老化性能。 2.3 膨胀螺栓、连接铁件、连接不锈钢针等配套的铁垫板、垫圈、螺帽及与骨架固定的各种设计和安装所需要的连接件的质量,必须符合要求。 3. 施工主要机具:
3.1 水平仪、经纬仪、无齿切割锯、冲击钻、手枪钻、力矩扳手、开口扳手、嵌缝枪、专用手推车、长卷尺、盒尺、锤子、各种形状的钢凿子、靠尺、铝制水平尺、尺、多用刀、铅丝、弹线用的粉线包、墨斗、小白线、笤帚、铁锹、开刀、灰槽、灰桶、工具袋、手套、红铅笔等。 3.2 施工主要辅材 主要辅材示例图片 膨胀螺栓 AB混合胶 云胶
-合成氨原料气的制备方法
年产五十万吨合成氨的原料气制备工艺筛选 合成氨生产工艺流程简介 合成氨因采用的工艺不同其生产流程也有一定的差别,但基本的生产过程都大同小异,基本上由原料气的生产、原料气的净化、合成气的压缩以及氨合成四个部分组成。 ●原料气的合成 固体燃料生产原料气:焦炭、煤 液体燃料生产原料气:石脑油、重油 气体燃料生产原料气:天然气 ●原料气的净化 CO变换 ●合成气的压缩 ●氨的合成 工业上因所用原料制备与净化方法不同,而组成不同的工艺流程,各种原料制氨的典型流程如下: 1)以焦炭(无烟煤)为原料的流程 50年代以前,世界上大多数合成氨厂采用哈伯-博施法流程。以焦炭为原料的吨氨能耗为88GJ,比理论能耗高4倍多。 我国在哈伯-博施流程基础上于50年代末60年代初开发了碳化工艺和三催化剂净化流程: ◆碳化工艺流程将加压水洗改用氨水脱除CO2得到的碳酸氢铵经结晶,分离后作 为产品。所以,流程的特点是气体净化与氨加工结合起来。 ◆三催化剂净化流程采用脱硫、低温变换及甲烷化三种催化剂来净化气体,以替代 传统的铜氨液洗涤工艺。 2)以天然气为原料的流程 天然气先要经过钴钼加氢催化剂将有机硫化物转化成无机硫,再用脱硫剂将硫含量脱除到以下,这样不仅保护了转化催化剂的正常使用,也为易受硫毒害的低温变换催化剂应用提供了条件。 3)以重油为原料的流程 以重油作为制氨原料时,采用部分氧化法造气。从气化炉出来的原料气先清除炭黑,经CO耐硫变换,低温甲醇洗和氮洗,再压缩和合成而得氨。 二、合成氨原料气的制备方法简述 天然气、油田气、炼厂气、焦炉气、石脑油、重油、焦炭和煤,都是生产合成氨的原料。除焦炭成分用C表示外,其他原料均可用C n H m来表示。它们呢在高温下与蒸汽作用生成以H2和CO为主要组分的粗原料气, 这些反应都应在高温条件下发生,而且为强吸热反应,工业生产中必须供给热量才能使其进行。 按原料不同分为如下几种制备方法: ●以煤为原料的合成氨工艺 各种工艺流程的区别主要在煤气化过程。 典型的大型煤气化工艺主要包括固定床碎煤加压气化工艺、德士古水煤浆加压气化工艺以及壳牌干煤粉加压气化工艺。 ①固定床碎煤气化
合成氨工艺流程
合成氨工艺流程标准化管理部编码-[99968T-6889628-J68568-1689N]
将无烟煤(或焦炭)由炉顶加入固定床层煤气发生炉中,并交替向炉内通入空气和水蒸汽,燃料气化所生成的半水煤气经燃烧室、废热锅炉回收热量后送入气柜。 半水煤气由气柜进入电除尘器,除去固体颗粒后依次进入压缩机的Ⅰ、Ⅱ、Ⅲ段,加压到~,送入脱硫塔,用溶液或其他脱硫溶液洗涤,以除去硫化氢,随后,气体经饱和塔进入热交换器,加热升温后进入一氧化碳变换炉,用水蒸汽使气体中的一氧化碳变为氢。变换后的气体,返回热交换器进行降温,并经热水塔的进一步降温后,进入变换器脱硫塔,以除去变换时产生的硫化氢。然后,气体进入二氧化碳吸收塔,用水洗法除去大部分二氧化碳。脱碳后的原料进入压缩机Ⅳ、Ⅴ段,升压到压缩机~后,依次进入铜洗塔和碱洗塔,使气体中残余的一氧化碳和二氧化碳含量进一步降至20(ppm)以下,以满足合成氨的要求。 净化后的原料气进入压缩机的最后一段,升压到~MPa进入滤油器,在此与循环压缩机来的循环气混合,经除油后,进入冷凝塔和氨冷器的管内,再进入冷凝塔的下部,分离出液氨。分离出液氨后的气体进入冷凝塔上部的管间,与管内的气体换热升温后进入氨合成塔。在高温高压并有催化剂存在的条件下,将氮氢气合成氨。出合成塔的气体中,约含氨10~20%,经水冷器与氨冷器将氨液化并分离后,其气体进入循环压缩机循环使用。分离出的液氨进入液氨贮槽。 原料气的制备:制备氢氮比为3:1的半水煤气 即造气。将无烟煤(或焦炭)由炉顶加入固定床层煤气发生炉中,并交替向炉内通入空气和水蒸汽,燃料气化后生成氢氮比为3:1的半水煤气。整个生产过程由煤气发生炉、燃烧室、废热锅炉、气柜等设备组成。 固定床半水煤气制造过程由吹风、上吹制气、下吹制气、二次上吹、空气吹净等5个阶段构成,为了调节氢氮比,在吹风末端要将部分吹风气吹入煤气,这个过程通常称为吹风回收。 吹风阶段:空气从煤气炉的底部吹入,使燃料燃烧,热量贮存于燃料中,为制气阶段碳与水蒸汽的反应提供热量。吹风气经过燃烧室和废热锅炉后放空。上吹制气阶段:从煤气炉的底部通入混有适量空气的水蒸汽,和碳反应生成的半水煤气经过炉的顶部引出。向水蒸汽中加入的空气称为加氮空气。 下吹制气阶段:将水蒸汽和加氮空气由炉顶送入,生成的半水煤气由炉底引出。二次上吹制气阶段:水蒸汽和加氮空气自下而上通过燃料层,将炉底残留的半水煤气排净,为下一步送入空气创造安全条件。 空气吹净阶段:从炉底部吹入空气,所得吹风气为半水煤气中氮的主要来源,并将残留的半水煤气加以回收。 以上五个阶段完成了制造半水煤气的主过程,然后重新转入吹风阶段,进入下一个循环。原料气的净化:除去原料气中的硫化氢、二氧化碳等杂质,将一氧化碳转化为氢气本阶段由原料气脱硫、一氧化碳变换、水洗(脱除二氧化碳)、铜洗(脱除一氧化碳)、碱洗(脱除残余二氧化碳)等几个工段构成,主要设备有除尘器、压缩机、脱硫塔、饱和塔、热水塔、一氧化碳变换炉、二氧化碳吸收塔、铜洗塔、碱洗塔等。 脱硫:原料气中硫化物的存在加剧了管道及设备的腐蚀,而且能引起催化剂中毒,必须予以除去。脱硫方法可分为干法脱硫和湿法脱硫两大类。干法脱硫是用固体硫化剂,当气体通过脱硫剂时硫化物被固体脱硫剂吸附,脱除原料气中的少量硫化氢和有机硫化物。一般先进行湿法脱硫,再采用干法脱硫除去有机物和残余硫化氢。湿法脱硫所用的硫化剂为溶液,当含硫气体通过脱硫剂时,硫化物被液体剂吸收,除去气体中的绝大部分硫化氢。
磨漆画制作工艺流程和制作材料
磨漆画制作工艺流程和制作材料 一、木工工艺一般漆器漆画家具的用材和生产工艺与其它木器家具生产工艺基本相同。高档漆器漆画产品的框架需采用楠木、红木、紫檀等名贵材种,雕刻以各种精美的图案花纹。80年代初,屏风木坯由拼木工艺改为夹板压制工艺。 二、髹漆工艺涂灰上灰髹漆 1、木胚涂灰:涂灰是进行装饰工艺和增加坯胎强度的一道重要工序。灰料分生漆灰、猪血灰和合成灰三种。70年代以前均使用猪血灰,80年代以后大部改用聚乙烯醇合成灰。 漆灰料制作 (1)生漆灰:用生漆和石膏或瓦灰,加适量的水及少量煤油调和而成。 (2)猪血灰:以新鲜猪血加适量生石灰搅拌成熟后,再加入不同细度的瓦灰而成。分粗灰(60目)、细灰(160目)、浆灰(200目)三种,习称"宝塔灰"。 (3)漆画合成灰:在聚乙烯醇内加入一定数量的清水,煮沸。另以松香、清漆(或桐油)和煤油混合加热溶解,然后两者相和,经搅拌制成合成胶。用合成胶加入不同细度的瓦灰、土子灰、老粉等调成粗、细两种合成灰。 2、上灰 (1)对漆画干木坯表面进行去污处理。 (2)上粗灰:用刮板将灰料均匀刮附于木坯上,以日光或远红外灯烘干。高档产品一般用生漆灰。 (3)打抹、刮裂:刮去干粗灰上的毛刺。 (4)布布、布麻:用料灰将夏布、麻丝贴实于木坯接缝处,以增加接缝处的牢固度。 (5)上细灰:要求刮得平整,厚薄均匀,并达到一定厚度。镶嵌工艺除底灰外,还要上一次细灰。 (6)上浆灰:阴干。 (7)清灰:用砂纸或砂轮打磨,达到平整,无波浪纹,平磨螺细产品要加水打磨,将图案磨显出来。
(8)刮浆:用薄灰料将灰坯孔隙刮平(镶嵌螺细产品,发现脱落之处,要及时补上)。 (9)砂磨:用细号水砂纸细磨。 3、髹漆:漆器漆画产品多用天然漆。有大木漆、小木漆之分。生漆主要来源于湖北省的恩施、利川、来凤、建始、兴山,湖南省的凤凰、武当,贵州省的黔西、恩南、渭泽,四川省的万县、大宁、宜宾,陕西省的平利、石泉、汉中,山西省的洪洞,河南省的高南,浙江省的桐庐,以及安徽、云南、广东等省。各地出产的漆质不同,制漆时要根据各地不同漆性,制成各种不同用漆,如推光漆、熟漆等。 (1)制漆经过滤去杂质后的生漆,在经加温、搅拌,去水份,即为推光漆。腰果漆是腰果壳油加溶剂及其它化学材料,经反应釜加热化合,即成合成腰果漆。 (2)上漆用推光漆或腰果漆,均匀地刷涂(或喷涂、淋涂)于制好的灰坯上(刷涂时要先上后下,再由左向右依次涂刷),下窨房阴干。待实干后,在由砂纸砂磨。然后根据需要再进行髹涂第二次、第三次......方法相同。 (3)推光漆器制作完成后,需对其表面进行推光处理。大件漆器用机动布盘蘸出光粉或上光腊抛光。小件漆器用布、棉花蘸浆灰、出光粉、菜油反复推擦 漆艺的技法 漆画装饰技法有很多种,变化万千,其主要技法有: ①、镶嵌镶嵌装饰采用螺铀、金、银、锡、铝、铜等金属线或薄片蛋壳以及经选择的玉石做为材料,用漆拈贴在画面所需要的位置,结合其它装饰工艺经过髹漆研磨后,可产生不同的材料质感、纹理、色彩等独特的效果。 ②、罩明即用透明的漆罩于不同的漆地上,因底漆色相不同,又有“罩黄”、“罩朱”等。此法光明莹彻,若在银下变涂肌理,经细心打磨,可显现丰富多彩的效果,这也是漆画主要的技法语言。 ③、莳绘即莳粉彩漆。莳粉包括金银凡粉与干漆粉,以推光漆或彩漆做为底漆,趁湿撒上所需之莳粉,干后罩透明或不透明彩漆研磨而成。 ④、彩绘分平绘与研磨彩绘。平绘仅在完成的底板上进行彩绘,绘完也就完工,研磨彩绘所髹彩漆有一定的厚度,经罩漆干燥后,研磨显出所画花纹。 ⑤变涂使用不同的材料、工具,在髹漆未干时,制作随意的有规律的变化的自然肌理、纹样,主要有:纹漆、变涂斑漆、汽油变涂。 ⑥堆漆用漆或漆灰堆出花纹,有如浮雕明显的高低起伏。分为高堆和平堆 ⑦雕填 ⑧针刻 ⑨晕金 5、漆画工艺制作程序 一、底层绘制程序
合成氨工艺简介模板
合成氨工艺简介模板 1
合成氨工艺控制方案总结 一合成氨工艺简介 中小型氮肥厂是以煤为主要原料, 采用固定层间歇气化法制造合成氨原料气。从原料气的制备、净化到氨的合成, 经过造气、脱硫、变换、碳化、压缩、精炼、合成等工段。工艺流程简图如下所示: 该装置主要的控制回路有: ( 1) 洗涤塔液位; ( 2) 洗涤气流量; ( 3) 合成塔触媒温度; ( 4) 中置锅炉液位; ( 5) 中置锅炉压力; ( 6) 冷凝塔液位; ( 7) 分离器液位; ( 8) 蒸发器液位。 其中触媒温度控制可采用全系数法自适应控制, 其它回路采用PID 控制。 2
二主要控制方案 ( 一) 造气工段控制 工艺简介: 固定床间歇气化法生产水煤气过程是以无烟煤为原料, 周期循环操作, 在每一循环时间里具体分为五个阶段; (1)吹风阶段约37s; (2)上吹阶段约39s; (3)下吹阶段约56s; (4)二上吹阶段约12s; (5)吹净阶段约6s. l、吹风阶段 此阶段是为了提高炉温为制气作准备的。这一阶段时间的长短决定炉温的高低, 时间过长, 炉温过高; 时间过短, 炉温偏低而且都影响发气量, 炉温主要由这一阶段控制。 般工艺要求此阶段的操作时间约为整个循环周期的18%左右。2、上吹加氮制气阶段 在此阶段是将水蒸汽和空气同时加入。空气的加入增加了气体中的氮气含量, 是调节 H2/N2的主要手段。可是为了保证造气炉的安全该段时间最多不超过整个循环周期的26%。 3、上吹制气阶段 该阶段与上吹加氯制气总时间为整个循环的32%, 随着上吹制气的进行下部炉温逐渐下降, 为了保证炉况和提高发气量, 在此 3
浮雕工艺制作流程精编版
浮雕工艺制作流程精编 版 MQS system office room 【MQS16H-TTMS2A-MQSS8Q8-MQSH16898】
浮雕工艺制作流程 A、设计? B、泥稿制作 C、制作模具 D、树脂产品制作 E、合模 F、抛光打磨 G、安装 H、上效果? 一、根据主题来设计稿子。泥塑稿的话主要需要解决的问题就是设计的构成元素和背景之间的层次要处理好。这个层次的处理是十分关键的。还要解决的是图案所要表达的整体气氛是怎样的及其表现形式的确定。这些问题的解决和确定与砂岩浮雕所要放置的地方、以及环境和使用的材料都有着很重要的关系。 二、根据之前确定的浮雕的尺寸,先制作一块浮雕板。制作的时候浮雕板用架子把它竖直,然后再上面堆上泥巴,泥巴要堆得厚一点。而后在制作浮雕的画面,在制作浮雕画面之前要先将浮雕的涉及的各个比例先画好,在这些比例画好之后。把之前的的泥巴中的在轮廓外面的泥巴给去掉。这一层作为浮雕的基本层,为了保证浮雕的层次,那么就需要将高处的再加一些,抵触的就再往里面挖一些。这样的话就很有距离感和层次感了。为了保证浮雕的感觉。泥搞制作完成后?再进行抛光,抛光完进行下一步,石膏模具制作。 三、制作石膏模 制作阴型雕刻图案的石膏模具:(一)将石膏粉、水按质量份100:35的比例混合均匀,调成糊状,浇灌在放有雕刻图案的泥质模型的木格内,浇灌时放入适量玻璃纤维增加石膏强度;(二)阴干1~2小时,再继续慢干2~24小时,待石膏干燥后,使雕刻图案的泥质模型与石膏模具分离,进行清洗和修补有瑕疵的石膏模具,制成具有阴型雕刻图案的石膏模具;石膏模具完成。
四、利用石膏模生产树脂产品。 ???????(一)把树脂与石英粉按质量份100:60的比例混合,边加边搅拌,搅拌均匀形成树脂A粉料,然后在树脂A粉料中按质量份100:15的比例加浓度为1600pg/ml的促进剂搅拌均匀制成混合物B,在混合物B中按质量份按100:15的比例加入固化剂,搅拌均匀10~20分钟,制成C料;(二) 用软毛刷将滑石粉刷在阴型雕刻图案的石膏模具内壁上,然后注入调匀的C 料,在最薄处厚度达到20mm时,铺上纤维网格布以增加强度; (三) 对加入阴型雕刻图案的石膏模具的C料进行手工处理,使模型的背面更加平整;(四) 在室温下,阴干1~2小时,再继续慢干2~48小时,干燥后,从阴型雕刻图案的石膏模具中取出,且用角磨机去除浮雕多余的边缘部分制成树脂浮雕成品. ?五、合模 ????? 把制作好的若干块树脂浮雕成品进行组合成整体,调整各个幅面形成整体树脂浮雕模型 六、修补、打礳。 ????? 修补处理、打磨:对整体树脂浮雕模型的一块树脂浮雕模型与另一块树脂浮雕模型的接缝处及瑕疵部分用C料进行修补和调式平行,并先用80目到120目砂纸进行粗磨,粗磨完成再进行细补完成后,再用240目的砂纸进行细磨,细部处理浮雕无缝成品的成型。对整体树脂浮雕模型进行至少一次喷砂处理,制得仿砂岩浮雕大型无缝壁画成品。 七、安装 ??浮雕板块干挂前要进行检查清理,搭建铁架,将浮雕板块运至安装处,用吊机将浮雕板块逐一传递给架上的安装工,并用冲击钻打孔,放膨胀胶,用膨胀螺丝固定墙体,树脂封闭钉口,待检查挂牢后用树脂密封。安装时,左右、上下的偏差不
合成氨工艺简介
合成氨工艺简介 标准化文件发布号:(9312-EUATWW-MWUB-WUNN-INNUL-DQQTY-
摘要 煤气化法是我国合成氨的主要制气方法,也是未来更替天然气和石油资源所必将采用的制气方法。即利用无烟煤、蒸汽和空气在碳发生炉内生产合成氨所需要的气体,俗称半水煤气。在已制得的半水煤气中,除了含有按合成工艺所需要的氮气和氢气外,还含有许多杂质和有害气体。由于这些杂质和有害气体很容易使合成触媒中毒而降低触媒效能。为保护触媒,延长其使用寿命,保证合成氨生产的正常进行,半水煤气中的杂质和有害气体必须在合成之前得以及时清除,这就需要对混合气体进行净化处理,并且要求连续性作业,以达到化学反应稳定进行,从而构成了合成氨工艺流程错综复杂和连续性强的生产特点。 一合成氨的生产方法简介 氨的合成,必须制备合成氨的氢、氮原料气。氮可取之于空气或将空气液化分离而制得,氮气或使空气通过燃料层汽化将产生CO或CO2转化为原料气。氢气一般常用含有烃类的各种燃料制取,亦通过焦碳,无烟煤,重油等为原料与水作用的方法制取。由于我国煤储量丰富,所以以煤为原料制氨在我国工业生产中广泛使用。 合成氨的过程一般可分为四个步骤: 1.造气:即制备出含有氮一定比例的原料气。 2.净化:任何制气方法所得的粗原料气,除含有氢和氮外,还含有硫化氢、有机硫、一氧化碳、二氧化碳和少量氧,这些物质对氨合成催化剂均有害,需进行脱除,直至百万分之几的数量级为止。在间歇式煤气炉制气流程中,脱硫置于变换之前,以保护变换催化剂的活性。 3.精炼:原料气的最终精炼包括清除微量一氧化碳、二氧化碳、氧、甲烷和过量氮,以确保氨合成催化剂活性和氨合成过程的经济运行。 4.合成:将合格的氢氮混合气体压缩到高压,在催化剂作用下合成氨气。 二合成氨反应的基本原理 1. 造气:合成氨的原料——氢氮可以用下列两种方法取得 (1)以焦碳与空气、水蒸气作用 (2)将空气分离制取氮,由焦炉气分离制氢 采用煤焦固定床间歇式汽化法。反应方程如下: C+H2O=CO +H2 (1) CO+O2=CO2 (2) 2.脱硫:无论以固体煤作原料还是以天然气、石油为原料制备氢氮原料气都含有一定成分的硫元素,无机硫主要含有硫化氢;有机硫主要含有二硫化碳、硫化氧碳等等。 硫化氢对合成氨生产有着严重危害,但不能与铁反应生成硫化亚铁,而且进入变换及合成系统能使铁催化剂中毒,进入铜洗系统使铜液的低价铜生成硫化亚铜的低价沉淀,使操作恶化,铜耗增加。所以半水煤气总的无机碳化物和有机硫化物必须在进入变换、合成系统前除去。
浮雕工程施工设计方案
目录 1. 工程概况 2. 施工前准备 .. 错误!未定义书签。 3. 室干挂石材墙面工艺流程框图错误!未定义 3.1施工工艺流程图:错误!未定义书签。 4. 干挂石材墙面施工工艺错误!未定义书签。 4.1测量放线 (5) 4.2龙骨加工 (6) 4.3竖向主龙骨安装 (8) 4.4水平次龙骨安装 (8) 4.5石材加工 (8) 4.6镶挂黄锈石石材板 (8) 4.7石材擦缝、墙面清理、验收 (9) 5.质量保证项目 (10)
1.工程概况: 工程名称:金道城项目一期三标段 建设单位:金道房地产开发 设计单位:中国东北设计研究院 监理单位:新佳城工程管理 施工单位:市第筑 本工程位于市浑南新城白塔路与桃仙大街交汇处,东临本大道,生活办公区位于白塔路西侧。该工程总建筑面积为168957.04m2,多层部分的建筑总面积约为47275 m2,包括一个转角合院、一个方合院和一个单体住宅组成,结构形式为框架剪力墙结构,浮雕安装总面积为260M2.。2. 施工前准备: 2.1 浮雕:本项目材料为甲供材,进场前应确定浮雕的品种、颜色、花纹和尺寸规格及雕刻深度,并严格控制、检查其抗折。抗拉及抗压强度,吸水率、耐冻融循环等性能。浮雕在运抵工地后,不得随意拆箱,并放置于施工干扰少,无重物坠落的平整场地保管。 2.2 合成树脂胶粘剂:用于粘贴石材背面的柔性背衬材料,要求具有防水和耐老化性能。 2.3 膨胀螺栓、连接铁件、连接不锈钢针等配套的铁垫板、垫圈、螺帽及与骨架固定的各种设计和安装所需要的连接件的质量,必须符合要求。 3. 施工主要机具:
3.1 水平仪、经纬仪、无齿切割锯、冲击钻、手枪钻、力矩扳手、开口扳手、嵌缝枪、专用手推车、长卷尺、盒尺、锤子、各种形状的钢凿子、靠尺、铝制水平尺、方尺、多用刀、铅丝、弹线用的粉线包、墨斗、小白线、笤帚、铁锹、开刀、灰槽、灰桶、工具袋、手套、红铅笔等。 3.2 施工主要辅材 主要辅材示例图片 膨胀螺栓 AB混合胶 云石胶
(工艺技术)合成氨工艺简介
合成氨工艺控制方案总结 一合成氨工艺简介 中小型氮肥厂是以煤为主要原料,采用固定层间歇气化法制造合成氨原料气。从原料气的制备、净化到氨的合成,经过造气、脱硫、变换、碳化、压缩、精炼、合成等工段。工艺流程简图如下所示: 该装置主要的控制回路有:(1)洗涤塔液位; (2)洗涤气流量; (3)合成塔触媒温度; (4)中置锅炉液位; (5)中置锅炉压力; (6)冷凝塔液位; (7)分离器液位; (8)蒸发器液位。 其中触媒温度控制可采用全系数法自适应控制,其他回路采用PID控制。 二主要控制方案 (一)造气工段控制 工艺简介: 固定床间歇气化法生产水煤气过程是以无烟煤为原料,周期循环操作,在每一循环时间里具体分为五个阶段;(1)吹风阶段约37s;(2)上吹阶段约39s;(3)下吹阶段约56s;(4)二上吹阶段约12s;(5)吹净阶段约6s. l、吹风阶段 此阶段是为了提高炉温为制气作准备的。这一阶段时间的长短决定炉温的高低, 时间过长,炉温过高;时间过短,炉温偏低并且都影响发气量,炉温主要由这一阶段控制。般工艺要求此阶段的操作时间约为整个循环周期的18%左右。 2、上吹加氮制气阶段 在此阶段是将水蒸汽和空气同时加入。空气的加入增加了气体中的氮气含量,是调节H2/N2的主要手段。但是为了保证造气炉的安全该段时间最多不超过整个循环周期的26%。 3、上吹制气阶段 该阶段与上吹加氯制气总时间为整个循环的32%,随着上吹制气的进行下部炉温逐渐下降,为了保证炉况和提高发气量,在此阶段蒸汽的流量最好能得以控制。 4、下吹制气阶段 为了充分地利用炉顶部高温、提高发气量,下吹制气也是很重要的一个阶段。这段时间
石雕、铜雕施工工艺流程
石雕雕塑工程施工工艺流程 一、工程特征 本雕塑工程采用圆雕及高浮雕雕刻手法,雕塑材料采用花岗岩和红砂岩。 二、石雕设计要求 雕塑制作是个复杂的过程,雕塑作品艺术含量高,对作品制作的艺术要求较高,施工时药考虑艺术品的特殊性,注意施工过程中的技术处理问题。 1、整体雕塑创作设计制作安装流程 创作设计阶段: 创作构思→平面效果图→泥塑小样创作→泥塑定型 模型制作阶段: 按尺寸要求制作大泥塑→制作玻璃钢→合模卸模 石雕雕刻阶段: 选材→石雕初稿→细部刻画→艺术总监指导修饰→验收 运输阶段: 包装→装车→运输→卸车 安装阶段: 前期准备→基础验收→安装→调整→清理→验收
2、技术及艺术品位质量控制要点 ①先作泥塑小样,因泥塑小样是平面效果图的立体表现形式,便于对整体效果的把握,小样制作时应充分考虑平面的透视效果,按适当比例制作注重表现手法。 ②泥塑大样为成品的1:1稿样,以小样按比例准确放大,必须通过泥塑制作作为成品雕塑的参照模型,这是艺术家作品区别于民间工艺作坊的分水岭,制作时要准确把握制作比例,充分体现设计理念,对各部分的刻画细致,特别明显,必须由艺术家监理。 ③石膏模是将泥塑转变为玻璃钢样品的中间环节,而玻璃钢样品是石雕制作的模型,此工序直接影响到雕塑的作品质量,故应认真细致制作。 三、石雕塑工程的重点、难点部分 经对设计施工图的认真阅读及仔细研究,精心制作玻璃钢模型,结合雕塑意图及实际情况,本工程重点、难点如下: 1、重点性分析 ①选材:因为整体雕塑结构美观大方,为了减少接缝所用的原材料为大方料石且质地须均匀。 ②雕塑构件拆分与拼接:认真研究拆分位置,尽量选择在横直线条上进行拼接。 ③包装运输:因大部分雕塑构建都有雕刻图案。 ④构件安装:雕塑构件安装是从图纸变为现实,使设计理想得以体现的重要环节。
合成氨生产工艺介绍
1、合成氨生产工艺介绍 1)造气工段 造气实质上是碳与氧气和蒸汽的反应,主要过程为吹风和制气。具体分为吹风、上吹、下吹、二次上吹和空气吹净五个阶段。原料煤间歇送入固定层煤气发生炉内,先鼓入空气,提高炉温,然后加入水蒸气与加氮空气进行制气。所制的半水煤气进入洗涤塔进行除尘降温,最后送入半水煤气气柜。 造气工艺流程示意图 2)脱硫工段 煤中的硫在造气过程中大多以H2S的形式进入气相,它不仅会腐蚀工艺管道和设备,而且会使变换催化剂和合成催化剂中毒,因此脱硫工段的主要目的就是利用DDS脱硫剂脱出气体中的硫。气柜中的半水煤气经过静电除焦、罗茨风机增压冷却降温后进入半水煤气脱硫塔,脱除硫化氢后经过二次除焦、清洗降温送往压缩机一段入口。脱硫液再生后循环使用。
脱硫工艺流程图 3)变换工段 变换工段的主要任务是将半水煤气中的CO在催化剂的作用下与水蒸气发生放热反应,生成CO2和H2。河南中科化工有限责任公司采用的是中变串低变工艺流程。经过两段压缩后的半水煤气进入饱和塔升温增湿,并补充蒸汽后,经水分离器、预腐蚀器、热交换器升温后进入中变炉回收热量并降温后,进入低变炉,反应后的工艺气体经回收热量和冷却降温后作为变换气送往压缩机三段入口。
变换工艺流程图 4)变换气脱硫与脱碳 经变换后,气体中的有机硫转化为H2S,需要进行二次脱硫,使气体中的硫含量在25mg/m3。脱碳的主要任务是将变换气中的CO2脱除,对气体进行净化,河南中科化工有限责任公司采用变压吸附脱碳工艺。来自变换工段压力约为1.3MPa左右的变换气,进入水分离器,分离出来的水排到地沟。变换气进入吸附塔进行吸附,吸附后送往精脱硫工段。 被吸附剂吸附的杂质和少量氢氮气在减压和抽真空的状态下,将从吸附塔下端释放出来,这部分气体称为解析气,解析气分两步减压脱附,其中压力较高的部分在顺放阶段经管道进入气柜回收,低于常 压的解吸气经阻火器排入大气。
浮雕工艺制作流程
浮雕工艺制作流程公司内部编号:(GOOD-TMMT-MMUT-UUPTY-UUYY-DTTI-
浮雕工艺制作流程 A、设计 B、泥稿制作 C、制作模具 D、树脂产品制作 E、合模 F、抛光打磨 G、安装 H、上效果 一、根据主题来设计稿子。泥塑稿的话主要需要解决的问题就是设计的构成元素和背景之间的层次要处理好。这个层次的处理是十分关键的。还要解决的是图案所要表达的整体气氛是怎样的及其表现形式的确定。这些问题的解决和确定与砂岩浮雕所要放置的地方、以及环境和使用的材料都有着很重要的关系。 二、根据之前确定的浮雕的尺寸,先制作一块浮雕板。制作的时候浮雕板用架子把它竖直,然后再上面堆上泥巴,泥巴要堆得厚一点。而后在制作浮雕的画面,在制作浮雕画面之前要先将浮雕的涉及的各个比例先画好,在这些比例画好之后。把之前的的泥巴中的在轮廓外面的泥巴给去掉。这一层作为浮雕的基本层,为了保证浮雕的层次,那么就需要将高处的再加一些,抵触的就再往里面挖一些。这样的话就很有距离感和层次感了。为了保证浮雕的感觉。泥搞制作完成后再进行抛光,抛光完进行下一步,石膏模具制作。 三、制作石膏模 制作阴型雕刻图案的石膏模具:(一)将石膏粉、水按质量份100:35的比例混合均匀,调成糊状,浇灌在放有雕刻图案的泥质模型的木格内,浇灌时放入适量玻璃纤维增加石膏强度;(二)阴干1~2小时,再继续慢干2~24小时,待石膏干燥后,使雕刻图案的泥质模型与石膏模具分离,进行清洗和修补有瑕疵的石膏模具,制成具有阴型雕刻图案的石膏模具;石膏模具完成。 四、利用石膏模生产树脂产品。 (一)把树脂与石英粉按质量份100:60的比例混合,边加边搅拌,搅拌均匀形成树脂A粉料,然后在树脂A粉料中按质量份100:15的比例加浓度为1600pg/ml 的促进剂搅拌均匀制成混合物B,在混合物B中按质量份按100:15的比例加入固化剂,搅拌均匀10~20分钟,制成C料;(二) 用软毛刷将滑石粉刷在阴型雕刻
合成氨生产工艺简介
合成氨生产工艺简介 目前国内生产合成氨的工艺大同小异,忽略各自的设备差异和工艺上的微小不同,我们可以将氨的生产过程,粗略的讲可分成一下几步:造气;脱硫;变换;变换后脱硫;铜洗;氨合成几个步骤,如下是此类流程的一个极简示意图: 图1 合成氨的极简化流程 1造气工段 造气实质上是碳与氧气和蒸汽的反应,原料煤间歇送入固定层煤气发生炉内,先鼓入空气,提高炉温,然后加入水蒸气与加氮空气进行制气。所制的半水煤气(主要成分为CO和H2,另有其他杂质气体)进入洗涤塔进行除尘降温,最后送入半水煤气气柜。 造气工段脱 硫 工 段 变 换 工 段 煤块水蒸汽 CO, N2, H2 H2S等其他杂质 CO, N 2 , H 2 变 换 气 脱 硫 工 段 CO2, N 2 , H 2 H2S等其他杂质 甲 醇 合 成 工 段 少量CO, CO 2 , N 2, H 2 精 炼 工 段 N 2 , H 2 极少量CO X等其他杂质 氨 合 成 工 段 N 2 , H 2 冷 冻 工 段 NH 3液氨
图2 造气工艺流程示意图 2脱硫工段 煤中的硫在造气过程中大多以H2S的形式进入气相,它不仅会腐蚀工艺管道和设备,而且会使变换催化剂和合成催化剂中毒,因此脱硫工段的主要目的就是利用DDS脱硫剂脱出气体中的硫。气柜中的半水煤气经过静电除焦、罗茨风机增压冷却降温后进入半水煤气脱硫塔,脱除硫化氢后经过二次除焦、清洗降温送往压缩机一段入口。脱硫液再生后循环使用。 图3 脱硫工艺流程图 3变换工段 气体从脱硫工艺中处理过后,已不含H2S等有毒气体。变换工段的主要任务是将半水煤气中的CO在催化剂的作用下与水蒸气发生放热反应,生成CO2和H2。经过两段压缩后的半水煤气进入饱和塔升温增湿,并补充蒸汽后,经水分离器、预腐蚀器、热交换器升温后进入中变炉回收热量并降温后,进入低变炉,反应后的工艺气体经回收热量和冷却降温后作为变换气送往压缩机三段入口。 说明:合成气的中的CO(一氧化碳)经蒸汽转换成CO2(二氧化碳)与H2,转换后气体称为“变换气”。
合成氨工艺流程
工艺流程说明: 将无烟煤(或焦炭)由炉顶加入固定床层煤气发生炉中,并交替向炉内通入空气和水蒸汽,燃料气化所生成的半水煤气经燃烧室、废热锅炉回收热量后送入气柜。 半水煤气由气柜进入电除尘器,除去固体颗粒后依次进入压缩机的Ⅰ、Ⅱ、Ⅲ段,加压到1.9~2.0Mpa,送入脱硫塔,用A.D.A.溶液或其他脱硫溶液洗涤,以除去硫化氢,随后,气体经饱和塔进入热交换器,加热升温后进入一氧化碳变换炉,用水蒸汽使气体中的一氧化碳变为氢。变换后的气体,返回热交换器进行降温,并经热水塔的进一步降温后,进入变换器脱硫塔,以除去变换时产生的硫化氢。然后,气体进入二氧化碳吸收塔,用水洗法除去大部分二氧化碳。脱碳后的原料进入压缩机Ⅳ、Ⅴ段,升压到压缩机12.09~13.0Mpa后,依次进入铜洗塔和碱洗塔,使气体中残余的一氧化碳和二氧化碳含量进一步降至20(ppm)以下,以满足合成氨的要求。 净化后的原料气进入压缩机的最后一段,升压到30.0~32.0 MPa进入滤油器,在此与循环压缩机来的循环气混合,经除油后,进入冷凝塔和氨冷器的管内,再进入冷凝塔的下部,分离出液氨。分离出液氨后的气体进入冷凝塔上部的管间,与管内的气体换热升温后进入氨合成塔。在高温高压并有催化剂存在的条件下,将氮氢气合成氨。出合成塔的气体中,约含氨10~20%,经水冷器与氨冷器将氨液化并分离后,其气体进入循环压缩机循环使用。分离出的液氨进入液氨贮槽。 原料气的制备:制备氢氮比为3:1的半水煤气 即造气。将无烟煤(或焦炭)由炉顶加入固定床层煤气发生炉中,并交替向炉内通入空气和水蒸汽,燃料气化后生成氢氮比为3:1的半水煤气。整个生产过程由煤气发生炉、燃烧室、废热锅炉、气柜等设备组成。 固定床半水煤气制造过程由吹风、上吹制气、下吹制气、二次上吹、空气吹净等5个阶段构成,为了调节氢氮比,在吹风末端要将部分吹风气吹入煤气,这个过程通常称为吹风回收。 吹风阶段:空气从煤气炉的底部吹入,使燃料燃烧,热量贮存于燃料中,为制气阶段碳与水蒸汽的反应提供热量。吹风气经过燃烧室和废热锅炉后放空。 上吹制气阶段:从煤气炉的底部通入混有适量空气的水蒸汽,和碳反应生成的半水煤气经过炉的顶部引出。向水蒸汽中加入的空气称为加氮空气。 下吹制气阶段:将水蒸汽和加氮空气由炉顶送入,生成的半水煤气由炉底引出。 二次上吹制气阶段:水蒸汽和加氮空气自下而上通过燃料层,将炉底残留的半水煤气排净,为下一步送入空气创造安全条件。 空气吹净阶段:从炉底部吹入空气,所得吹风气为半水煤气中氮的主要来源,并将残留的半水煤气加以回收。 以上五个阶段完成了制造半水煤气的主过程,然后重新转入吹风阶段,进入下一个循环。原料气的净化:除去原料气中的硫化氢、二氧化碳等杂质,将一氧化碳转化为氢气本阶段由原料气脱硫、一氧化碳变换、水洗(脱除二氧化碳)、铜洗(脱除一氧化碳)、碱洗(脱除残余二氧化碳)等几个工段构成,主要设备有除尘器、压缩机、脱硫塔、饱和塔、热水塔、一氧化碳变换炉、二氧化碳吸收塔、铜洗塔、碱洗塔等。 脱硫:原料气中硫化物的存在加剧了管道及设备的腐蚀,而且能引起催化剂中毒,必须予以除去。脱硫方法可分为干法脱硫和湿法脱硫两大类。干法脱硫是用固体硫化剂,当气体通过脱硫剂时硫化物被固体脱硫剂吸附,脱除原料气中的少量硫化氢和有机硫化物。一般先进行湿法脱硫,再采用干法脱硫除去有机物和残余硫化氢。湿法脱硫所用的硫化剂为溶液,当含硫气体通过脱硫剂时,硫化物被液体剂吸收,除去气体中的绝大部分硫化氢。 CO变换:一氧化碳对氨催化剂有毒害,因此在原料气进入合成氨工序之前必须将一氧
浮雕工艺制作流程
浮雕工艺制作流程 A、设计 B、泥稿制作 C、制作模具 D、树脂产品制作 E、合模 F、抛光打磨 G、安装H 、上效果 一、根据主题来设计稿子。泥塑稿的话主要需要解决的 问题就是设计的构成元素和背景之间的层次要处理好。这个层次的处理是十分关键的。还要解决的是图案所要表达的整体气氛是怎样的及其表现形式的确定。这些问题的解决和确 定与砂岩浮雕所要放置的地方、以及环境和使用的材料都有着很重要的关系。 二、根据之前确定的浮雕的尺寸,先制作一块浮雕板。 制作的时候浮雕板用架子把它竖直,然后再上面堆上泥巴,泥巴要堆得厚一点。而后在制作浮雕的画面,在制作浮雕画面之前要先将浮雕的涉及的各个比例先画好,在这些比例画好之后。把之前的的泥巴中的在轮廓外面的泥巴给去掉。这一层作为浮雕的基本层,为了保证浮雕的层次,那么就需要将高处的再加一些,抵触的就再往里面挖一些。这样的话就很有距离感和层次感了。为了保证浮雕的感觉。泥搞制作完成后再进行抛光,抛光完进行下一步,石膏模具制作。 三、制作石膏模 制作阴型雕刻图案的石膏模具:(一)将石膏粉、水按质量份100:35的比例混合均匀,调成糊状,浇灌在放有雕刻图案的泥质模型的木格内,浇灌时放入适量玻璃纤维增加石膏强度;(二)阴干1?2小时,再继续慢干2?24小时,待石膏干燥后,使雕刻图案的泥质模型与石膏模具分离,进行清洗和修补有
瑕疵的石膏模具,制成具有阴型雕刻图案的石膏模具;石膏模具完成。 四、利用石膏模生产树脂产品。 (一)把树脂与石英粉按质量份100:60的 比例混合,边加边搅拌,搅拌均匀形成树脂A粉料,然后在 树脂A粉料中按质量份100:15的比例加浓度为1600pg/ml 的促进剂搅拌均匀制成混合物B,在混合物B中按质量份按100:15的比例加入固化剂,搅拌均匀10?20分钟,制成C 料;(二)用软毛刷将滑石粉刷在阴型雕刻图案的石膏模具内壁上,然后注入调匀的C料,在最薄处厚度达到20mm寸, 铺上纤维网格布以增加强度;(三)对加入阴型雕刻图案的 石膏模具的C料进行手工处理,使模型的背面更加平整;(四)在室温下,阴干1?2小时,再继续慢干2?48小时,干燥后,从阴型雕刻图案的石膏模具中取出,且用角磨机去除浮雕多余的边缘部分制成树脂浮雕成品 五、合模 把制作好的若干块树脂浮雕成品进行组合成整 体,调整各个幅面形成整体树脂浮雕模型 六、修补、打礳。 修补处理、打磨:对整体树脂浮雕模型的一块树脂浮雕模型与另一块树脂浮雕模型的接缝处及瑕疵部分用C料进行修补和调式平行,并先用80目到120目砂纸进行粗磨,粗磨完成再进行细补完成后,再用240目的砂纸进 行细磨,细部处理浮雕无缝成品的成型。对整体树脂浮雕模型进行至少一次喷砂处理,制得仿砂岩浮雕大型无缝壁画成品。 七、安装
自然浮雕釉制作方法和工艺流程
自然浮雕釉制作方法和工艺流程 集萃印花网2008-11-19 【集萃网观察】1、引言 在陶瓷生产实践中,由于某些工序操作不当,一般会导致釉烧产品出现局部或大面积缩釉,从而严重影响产品质量和经济效益。然而,就是这种“不良现象”却给了我们一个意外的收获:利用“缺陷”人为塑造“自然浮雕”美感,研制出了一种在陶瓷釉面上形成自然浮雕的方法用其所使用的陶瓷釉(文中简称“自然浮雕釉”),并于2005年9月由国家知识产权局授予发明专利权。 2、技术背景 要使陶瓷表面形成凹凸分明的浮雕且具有立体美感,传统方法是采用雕刻,堆填或转印等手段在陶瓷素坯上人为而成。但这样产生的效果很不理想———凹陷部位积釉较厚,凹凸不明显,棱角模糊,缺乏立体感,况且工艺复杂,成本昂贵。而自然浮雕方法更简单易行,产生的浮雕效果十分明显,其线条流畅,纹理清晰,釉面光滑细腻,富有很强的观赏性和适用性。因此,通过釉面装饰产生自然浮雕的方法应该拥有广阔的市场前景。 3、技术原理浅析 通过在陶瓷生坯或素烧坯上施一定厚度的自然浮雕釉,在干燥过程中由于缩水干裂而产生裂痕,经釉烧使釉玻化,控制温度使釉具有适当流动性,釉自身表面张力在裂纹处分断并各自聚集成滴,从而产生自然的凸起浮雕效果。 4、配方与做法 4.1(浮雕釉的制配 4.1.1所需矿石及其百分比含量(见表) 钾长石38-42% 大理石26-30% 滑石10-15% 高岭土3-5%
粘土6-10% 磷酸钙6-18% 4.1.2制配方法与步骤 按配方组成所需量的原矿石,经粉碎再过260目筛,搅拌均匀后倒入球磨容器中,加1:1等重量干净水,加盖密封,球磨50小时,所得釉浆即是“浮雕釉”。 4.1.3 雕釉的矿物成分和含量(见右表) 5、工艺流程 5.1自然浮雕釉的装饰方式 5.1.1一般装饰 首先,将陶瓷生坯或素烧坯清理干净,适当补水; 其次,在不要釉面形成浮雕的部位如器皿瓷内壁施以通常的透明釉或色釉; 再次,运用传统的转印印花工艺在必要的区域形成五彩缤纷的图案,花纹以及人物鸟兽。 最后,在需要形成的部位或区域如器皿瓷的外表壁,扁平瓷的外边沿采用喷涂,刷涂或浸泡醮取方式施釉,干燥后釉层厚度最好保证0.6—0.8mm,均匀平滑,以便在干燥过程中因干裂而产生大量裂纹,釉层被裂纹分割成无数小块,形成浮雕的雏形。
合成氨生产工艺介绍样本
1、合成氨生产工艺简介 1)造气工段 造气实质上是碳与氧气和蒸汽反映,重要过程为吹风和制气。详细分为吹风、上吹、下吹、二次上吹和空气吹净五个阶段。原料煤间歇送入固定层煤气发生炉内,先鼓入空气,提高炉温,然后加入水蒸气与加氮空气进行制气。所制半水煤气进入洗涤塔进行除尘降温,最后送入半水煤气气柜。 造气工艺流程示意图 2)脱硫工段 煤中硫在造气过程中大多以H2S形式进入气相,它不但会腐蚀工艺管道和设备,并且会使变换催化剂和合成催化剂中毒,因而脱硫工段重要目就是运用DDS脱硫剂脱出气体中硫。气柜中半水煤气通过静电除焦、罗茨风机增压冷却降温后进入半水煤气脱硫塔,脱除硫化氢后通过二次除焦、清洗降温送往压缩机一段入口。脱硫液再生后循环使用。
脱硫工艺流程图 3)变换工段 变换工段重要任务是将半水煤气中CO在催化剂作用下与水蒸气 发生放热反映,生成CO2和H2 。河南中科化工有限责任公司采用是中变串低变工艺流程。通过两段压缩后半水煤气进入饱和塔升温增湿,并补充蒸汽后,经水分离器、预腐蚀器、热互换器升温后进入中变炉回收热量并降温后,进入低变炉,反映后工艺气体经回收热量和冷却降温后作为变换气送往压缩机三段入口。
变换工艺流程图 4)变换气脱硫与脱碳 经变换后,气体中有机硫转化为H2S,需要进行二次脱硫,使气体中硫含量在25mg/m3。脱碳重要任务是将变换气中CO2脱除,对气体进行净化,河南中科化工有限责任公司采用变压吸附脱碳工艺。来自变换工段压力约为1.3MPa左右变换气,进入水分离器,分离出来水排到地沟。变换气进入吸附塔进行吸附,吸附后送往精脱硫工段。 被吸附剂吸附杂质和少量氢氮气在减压和抽真空状态下,将从吸附塔下端释放出来,这某些气体称为解析气,解析气分两步减压脱附,其中压力较高某些在顺放阶段经管道进入气柜回收,低于常压解吸气经阻火器排入大气。
合成氨工艺
合成氨工艺 合成氨的介绍 基本简介: 生产合成氨的主要原料有天然气、石脑油、重质油和煤(或焦炭)等。 ①天然气制氨。天然气先经脱硫,然后通过二次转化,再分别经过一氧化碳变换、二氧化碳脱除等工序,得到的氮氢混合气,其中尚含有一氧化碳和二氧化碳约0.1%~0.3%(体积),经甲烷化作用除去后,制得氢氮摩尔比为3的纯净气,经压缩机压缩而进入氨合成回路,制得产品氨。以石脑油为原料的合成氨生产流程与此流程相似。 ②重质油制氨。重质油包括各种深度加工所得的渣油,可用部分氧化法制得合成氨原料气,生产过程比天然气蒸气转化法简单,但需要有空气分离装置。空气分离装置制得的氧用于重质油气化,氮作为氨合成原料外,液态氮还用作脱除一氧化碳、甲烷及氩的洗涤剂。 ③煤(焦炭)制氨。随着石油化工和天然气化工的发展,以煤(焦炭)为原料制取氨的方式在世界上已很少采用。 用途氨主要用于制造氮肥和复合肥料,氨作为工业原料和氨化饲料,用量约占世界产量的12%。硝酸、各种含氮的无机盐及有机中间体、磺胺药、聚氨酯、聚酰胺纤维和丁腈橡胶等都需直接以氨为原料。液氨常用作制冷剂。
贮运商品氨中有一部分是以液态由制造厂运往外地。此外,为保证制造厂内合成氨和氨加工车间之间的供需平衡,防止因短期事故而停产,需设置液氨库。液氨库根据容量大小不同,有不冷冻、半冷冻和全冷冻三种类型。液氨的运输方式有海运、驳船运、管道运、槽车运、卡车运。直接合成氨。于1908年申请专利,即“循环法”,在此基础上,他继续研究,于1909年改进了合成,氨的含量达到6%以上。这是目前工业普遍采用的直接合成法。反应过程中为解决氢气和氮气合成转化率低的问题,将氨产品从合成反应后的气体中分离出来,未反应气和新鲜氢氮气混合重新参与合成反应。 合成氨反应式如下:N2+3H2≒2NH3(该反应为可逆反应,等号上反应条件为:“高温高压”,下为:“催化剂”) 合成氨的主要原料可分为固体原料、液体原料和气体原料。经过近百年的发展,合成氨技术趋于成熟,形成了一大批各有特色的工艺流程,但都是由三个基本部分组成,即原料气制备过程、净化过程以及氨合成过程。 氨是重要的无机化工产品之一,在国民经济中占有重要地位。除液氨可直接作为肥料外,农业上使用的氮肥,例如尿素、硝酸铵、磷酸铵、氯化铵以及各种含氮复合肥,都是以氨为原料的。合成氨是大宗化工产品之一,世界每年合成氨产量已达到1 亿吨以上,其中约有80%的氨用来生产