煤气净化系统工艺的优化与改进
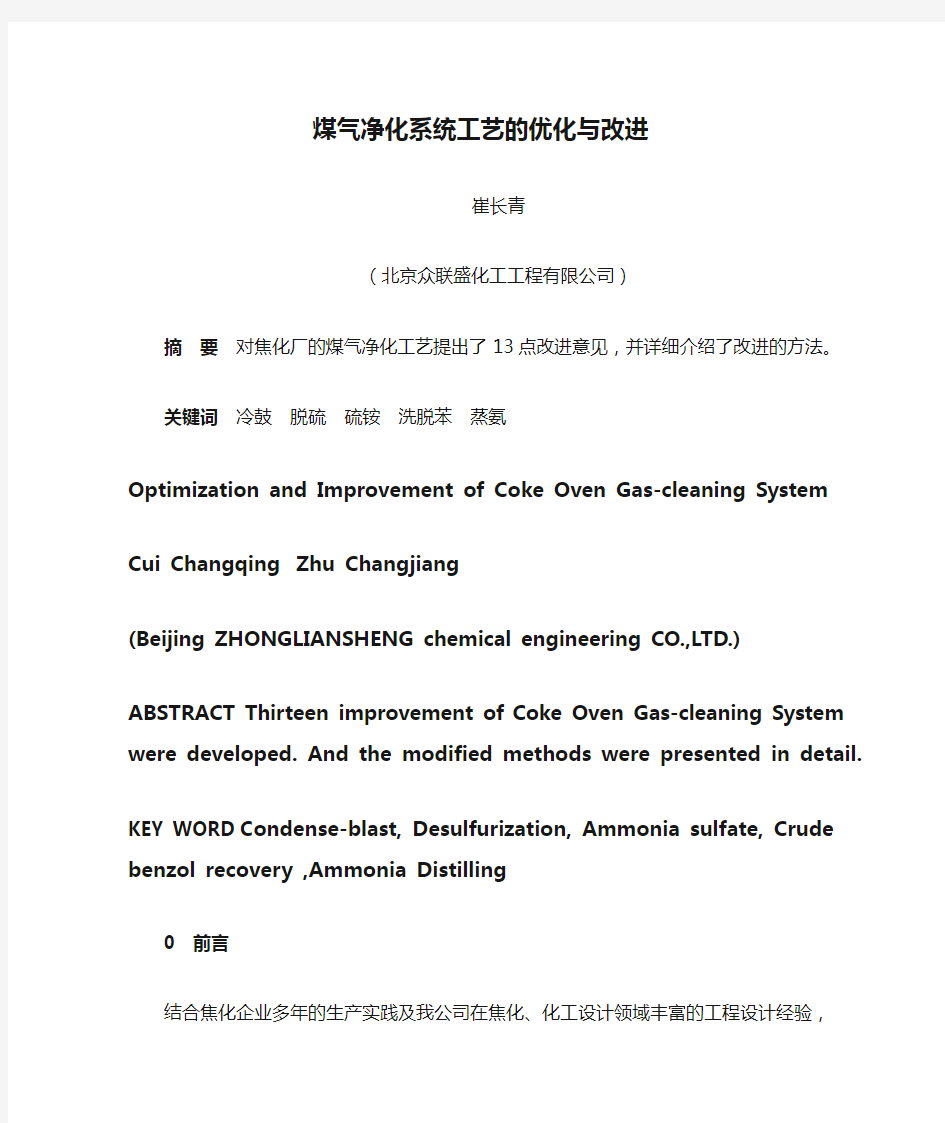

煤气净化系统工艺的优化与改进
崔长青
(北京众联盛化工工程有限公司)
摘要对焦化厂的煤气净化工艺提出了13点改进意见,并详细介绍了改进的方法。
关键词冷鼓脱硫硫铵洗脱苯蒸氨
Optimization and Improvement of Coke Oven Gas-cleaning System
Cui Changqing Zhu Changjiang
(Beijing ZHONGLIANSHENG chemical engineering CO.,LTD.)
ABSTRACT Thirteen improvement of Coke Oven Gas-cleaning System were developed. And the modified methods were presented in detail.
KEY WORD Condense-blast, Desulfurization, Ammonia sulfate,Crude benzol recovery ,Ammonia Distilling
0前言
结合焦化企业多年的生产实践及我公司在焦化、化工设计领域丰富的工程设计经验,我公司在为国内某焦化企业三期100万吨/年焦化工程的设计中,对煤气净化车间的冷鼓、脱硫、硫铵、洗脱苯及蒸氨工段在生产工艺上进行了一些优化设计,得到了业主的一致好评。本文就设计工作中对工艺流程、设备布置进行的修改及其必要性进行详细论述。
1该企业一、二期工艺流程简述
1.1冷鼓工段
自气液分离器来的荒煤气经过初冷器后将煤气温度冷却至22℃,后经电捕焦油器进一步脱除焦油后进入煤气鼓风机,加压后煤气进入后续工段。
气液分离器分离出的液相自流进入机械化氨水澄清槽进行静止分层。上层的氨水溢流至循环氨水槽,由循环氨水泵抽送至荒煤气管冷却荒煤气,并自循环氨水泵后抽取部分氨水至初冷器喷洒冲洗使用。多余的氨水溢流至剩余氨水槽,用剩余氨水泵抽送至蒸氨工段。中层的焦油溢流至焦油中间槽,再次静止分离脱水后泵送至焦油槽贮存、外售。底层的焦油渣定期运往煤场掺混炼焦。
每台初冷器下部设有两台初冷器水封槽(初冷器上、下段各对应一台),煤气冷凝液及初冷器冲洗液经水封槽溢流至上、下段冷凝液循环槽,然后分别由上、下段冷凝液循环泵送至初冷器上下段喷淋,如此循环使用,多余部分由下段冷凝液循环泵送至机械化氨水澄清槽。并在下段冷凝液循环槽内设有蒸汽盘管加热。
1.2脱硫工段
脱硫采用PDS+栲胶为催化剂、煤气中的氨为碱源的湿式氧化法、两级脱硫、再生塔再生、熔硫釜生产硫磺的脱硫工艺。
来自冷鼓工段的粗煤气依次串联进入两个脱硫塔下部与塔顶喷淋下来的脱硫液逆流接触进行洗涤后,煤气经捕雾段除去雾滴后全部送至硫铵工段。
从脱硫塔中吸收了H2S和HCN的脱硫液经脱硫塔液封槽溢流至溶液循环槽,用溶液循
环泵抽送至再生塔下部与空压站来的压缩空气并流再生,再生后的脱硫液返回脱硫塔塔顶循环喷淋脱硫。硫泡沫则由再生塔顶部扩大部分排至硫泡沫槽,再由硫泡沫泵加压后送熔硫釜连续熔硫,生产硫磺外售。熔硫釜内分离的清液送至溶液循环槽循环使用。
1.3硫铵工段
采用喷淋式硫铵饱和器发生产硫铵。
由脱硫工段送来的煤气经煤气预热器后进入硫铵饱和器上段的喷淋室,在此煤气与来自饱和器下段的循环母液充分接触,使其中的氨被母液吸收。煤气经饱和器内的除酸器分离酸雾后送至洗脱苯工段。
在硫铵饱和器内的母液中不断有硫铵晶体生成,用结晶泵将其连同一部分母液送至结晶槽分离,然后经离心机分离、螺旋输送机输送至振动流化床干燥器干燥后入硫铵贮斗贮存、称重、包装即可外售。
1.4洗脱苯工段
该工段分为煤气的冷却、洗苯、脱苯三部分。
来自硫铵工段的粗煤气,经终冷塔间接冷却后从洗苯塔底部入塔,与塔顶喷淋的循环洗油逆流接触,煤气中的苯被循环洗油吸收,再经过塔的捕雾段脱除雾滴后离开洗苯塔。
洗苯塔底富油经富油泵加压后送至粗苯冷凝冷却器,与脱苯塔顶出来的粗苯汽换热,然后至油油换热器与脱苯塔底出来的热贫油换热,最后进入粗苯管式炉被加热至180?C左右,进入脱苯塔。从脱苯塔顶蒸出的粗苯油水混和汽进入粗苯冷凝冷却器分别被从洗苯塔底来的富油和制冷水冷却至30℃,然后进入粗苯油水分离器,分离的粗苯至粗苯回流槽,部分粗苯经粗苯回流泵送至脱苯塔顶作回流,其余部分入粗苯贮槽,定期由粗苯输送泵送至罐区粗苯贮槽,贮存、外售。
脱苯后的热贫油从脱苯塔底流出,自流入油油换热器与富油换热后入贫油槽,并由贫油泵加压送至一、二段贫油冷却器分别被循环水和制冷水冷却至约30?C,送洗苯塔喷淋洗涤煤气。
0.5MPa(表)蒸汽被粗苯管式炉过热至400?C左右,作为洗油再生器和脱苯塔的热源。管式炉所需燃料由引自洗苯后的煤气管道。
在洗苯脱苯的操作过程中,循环洗油的质量逐渐恶化,为保证洗油质量采用洗油再生器将部分热贫油再生。洗油再生量为循环洗油量的1~1.5%,用过热蒸汽加热,蒸出的油汽进入脱苯塔,采用干排渣的方式将残渣排入残油池定期送往煤场或外售。
1.5蒸氨工段
采用直接蒸汽为热源的蒸氨方法。
2三期工程设计中对上述工段的改进
2.1冷鼓工段
a、原设计中每台初冷器下部设有两台DN800初冷器水封槽修改为总共设计两台
DN2000的初冷器水封槽;
b、将初冷器基础标高由原设计的POS EL4.000加高为POS EL7.200,初冷器水封槽的基础标高由原设计的POS EL0.600加高为POS EL1.500,机械化氨水澄清槽的基础标高由原设计的POS EL1.860降低为POS EL1.000,同时取消上、下段冷凝液循环槽及上、下段冷凝液循环泵。修改设计后,煤气冷凝液及初冷器冲洗液经水封槽直接溢流至机械化氨水澄清槽。
见附图:
优点:因煤气冷凝液中焦油含量较高,减少中间操作环节后,改善了初冷器平台附近的操作环境;下段冷凝液循环槽中设有蒸汽加热盘管,实际生产中发生过因盘管腐蚀泄漏从而污染蒸汽冷凝液的事件,取消该循环槽,不仅减少蒸汽耗量,而且减少污染事件发生的一个源头;取消上、下段冷凝液循环泵各两台,不仅节省投资,而且减少动力消耗37kW/h。
c、将原设计中的电捕水封槽、鼓风机水封槽由方形结构改为圆形结构,同时取消水封槽顶部的液下泵,冷凝液由原设计的由液下泵直接打入机械化氨水澄清槽改为自流入废液收集槽,然后由废液收集槽液下泵统一打入氨水澄清槽。
优点:方形结构改为圆形结构,使得设备的结构更合理,减少钢材用量;取消液下泵(共四台),节省投资,减少动力消耗11Kw/h,简化操作。
d、剩余氨水送去蒸氨工段前,增加PT963陶瓷管过滤器,除去剩余氨水中绝大部分的焦油后再送往蒸氨工段。
优点:保证蒸氨塔的正常操作,PT963陶瓷管过滤器布置在本工段而非蒸氨工段,主要考虑PT963陶瓷管过滤器反冲洗后得到的焦油可直接排至废液收集槽,后有废液收集槽液下泵统一送往氨水澄清槽;
e、鼓风机煤气入口管设计一段长度为450mm的两端带法兰的直管段,在鼓风机设备安装时,预先同风机入口连接好,为后期煤气管道的安装提供便利。
2.2脱硫工段
a、取消由溶液循环泵出口至再生塔进口的脱硫液液封管道,由止回阀代替。并且在管道设计中,充分考虑止回阀的更换问题。
优点:随着机械加工水平的提高,现有的止回阀质量完全可以满足使用要求,用止回阀代替上U型管道可大大降低安装成本。
b、在进再生塔的两路压缩空气管道上,分别装设调节阀。
优点:保证了再生用压缩空气的稳定,保证再生效果。
c、硫回收生产硫膏,采用卧式螺旋卸料沉降离心机代替传统的三足式自动刮刀下部卸料离心机。
优点:在生产硫膏质量相同的情况下,简化了操作程序,使得生产的自动化水平提高。
d、催化剂配置槽布置在二楼离心机厂房内,将加药方式由间歇加药改为连续加药。
优点:保证了脱硫液中催化剂的均匀,并使药剂能长时间稳定发挥作用,保证了脱硫塔后硫化氢含量的稳定性。
2.3硫铵工段
a、传统设计中硫铵仓库的地坪标高由EL1.000变为EL0.000。
优点:原设计中的硫铵仓库标高主要是为装车方便服务,但随着社会进步,汽车高度也不仅仅局限于原来的高度,因此原设计的地坪1米的标高逐渐失去了原有的作用,取消后不但节省了土建费用,而且在不改变原有层高的前提下,即可满足自动称量包装设备需要的安装高度。
b、在饱和器的下部结晶室增加了结晶母液射流悬浮搅拌系统。
优点:增加了结晶旋转悬浮的速度,使晶膜阻力减少,加快结晶成长并有利于消除硫铵沉积死角;另外,非正常生产时(如突然停电),饱和器下部母液中的硫铵结晶会迅速沉积在饱和器下筒体的底部,晶比高时会造成严重的堵塞,增加该搅拌系统后,启动大母液泵会使结晶堵塞现象迅速消失,使硫铵机组在较短时间内顺利恢复生产运行。
2.4洗脱苯工段
a、在不明显增加洗油消耗量的前提下,将原来的洗油再生器的干法排渣工艺改为湿法
排渣工艺。具体为将排渣温度由220℃降为190℃,通过增加一台齿轮泵将湿渣直
接送至冷鼓工段的氨水澄清槽。
优点:减少了污染排放点,大大改善了工人的操作环境。
2.5 蒸氨工段
a、由原来的直接蒸汽加热修改为通过再沸器的间接蒸汽加热。蒸汽通过再沸器加热后
通过疏水阀对蒸汽冷凝液进行回收。
优点:减少了直接蒸汽损耗约4t/h,同时减少了蒸氨废水的排放量4t/h。
3结束语
近几年来,随着焦化工业的不断发展,各生产企业也对煤气净化系统不断进行优化和改进。因此,各设计单位应该与时俱进,充分发挥设计单位在工程设计中的技术优势,结合各企业现场生产经验以及石化、化工行业的生产经验,不断将新技术在净化工艺中得以应用,使煤气净化工艺得到不断完善。
煤气净化工艺工艺流程..
煤气净化工艺工艺流程及主要设备煤气净化设施 1概述 煤气净化车间生产规模按2×65 孔5.5m 捣固焦炉焦炉年产130万t 干全焦配套设计。焦炉煤气处理量为75300m3/h(标况)。 煤气净化车间由冷凝鼓风工段、脱硫工段、硫铵工段(含蒸氨系统)、终冷洗涤及粗苯蒸馏工段、油库及其相关的生产辅助设施组成。 2设计原则 对煤气净化车间本着经济、实用、可靠的原则,在满足国家环保、 职业卫生与安全、能源等法规要求的前提下,尽量简化工艺流程,并 合理配备工艺装备,以节省投资和工厂用地。 3设计基础数据 a)煤气量基础数据 焦炉装煤量(干基):206.98t/h 煤气产量:340Nm3/t(干煤) b) 煤气净化指标 表1 煤气净化指标表 序号指标名称单位净化前指标净化后指标 1 NH3g/m36~8 ≤0.05 2 H2S g/m35~7 ≤0.2 3 苯g/m324~40 ≤4 4 焦油g/m3≤0.02 5 萘g/m3≤0.3 4原材料及产品指标
4.1焦油——符合YB/T5075-2010 2号指标 序号指标名称质量指标 1 密度(20℃),g/cm3 1.13~1.22 2 甲苯不溶物(无水基),% ≤9 3 灰分,% ≤0.13 4 水分,% ≤4.0 5 粘度(E80) ≤4.2 6 萘含量(无水基),% ≥7.0(不作考核指标) 4.2硫酸铵—符合GB535-1995一级品 序号指标名称质量指标 1 氮N含量(以干基计),% ≥21 2 含水,% ≤0.3 3 游离酸含量,% ≤0.05 4.3粗苯—符合YB/T5022-1993 序号指标名称质量指标(溶剂用) 1 密度(20℃),g/ml ≤0.900 2 75℃前馏出量(重),% ≤3 3 180℃前馏出量(重),% ≥91% 室温(18~25℃)下目测无可见的不 4 水分: 溶解的水 4.4洗油指标 序号指标名称指标 1 密度(20℃),g/ml 1.03~~1.06 2 馏程(大气压760mmHg),%
焦炉煤气净化工艺流程的选择
焦炉煤气净化工艺流程的选择 (2011-01-24 13:14:42) 标签: 分类:焦化类 煤化工 杂谈 笑看人生 摘要:本文对我国煤气净化工艺的发展进行了回顾,提出了我国焦炉煤气净化工艺发展的方向以及选择工艺流程的原则。并推荐采用的焦炉煤气净化工艺流程以及各单元中应采用的行之有效的环保、节能技术。 1 焦炉煤气净化工艺的历史回顾 我国焦炉煤气净化发展是与炼焦工业的发展紧密相连的。建国以前,我国焦化工业几乎是一片空白。建国以来,随着炼焦工业的发展,煤气净化工艺从无到有,蓬勃发展,技术水平和装备水平得到了不断提高。概括起来,大体上经历了三个阶段。第一个阶段是从20世纪50年代末到60年代中期,我国焦化厂的焦炉煤气净化工艺主要是以50年代从原苏联引进的工艺为基础、消化翻板饱和器法生产硫铵的老流程,以当时的武钢焦化厂、包钢焦化厂、鞍钢化工总厂、太钢焦化厂、马钢焦化厂等一批大型厂为代表。但该工艺存在流程陈旧、能耗高、环保措施不健全、装备水平低等问题。主要表现在初冷采用立管冷却器,冷却效率低;硫铵装置设备庞大,煤气阻力大,产品质量差,设备腐蚀严重;没有配套建设脱硫装置,终冷系统不能闭路,对大气和水体污染严重;在粗苯蒸馏系统采用蒸汽法,不但耗用大量蒸汽,产品质量也得不到保证。第二阶段是从60年代中期至70年代末期,随着我国自行设计的58型焦炉不断推广及炭化室高5.5米焦炉的诞生,对煤气净化工艺开展了与石油、化工行业找差距进行技术革新的阶段。在广大技术人员的努力下,在此期间我们将初冷流程改为二段冷却;开发了多种油洗萘代替终冷水洗萘;研制成功了终冷水脱氰生产黄血盐,解决了终冷水的污
焦炉煤气知识问答
精心整理 焦炉煤气知识问答 1. 荒煤气的组成有哪些?占多大的比例? 煤在炭化室内炼焦产生的没有经过净化处理的黄色粗煤气叫荒煤气。荒煤气的组成大致是(克/米3):水蒸气250-450、焦油气80-120、粗苯30-45、氨8-16、硫化氢6-30、氰化物1.0-2.5、轻吡啶盐基0.4-0.6、萘10、其它2-2.5 2. 3. 5.5-74. 炼焦干煤的重量%计): 煤气15-19、焦油3-4、粗苯0.9-1.2、氨0.2-0.3 5. 城市煤气有哪些要求? 各国对城市煤气的质量均有严格要求,对杂质含量都作出明确规定。中国规定的指标与工业发达国家基本相似,具体要求为:(1)低发热值大于14654kJ/m 3;(2)杂质
允许含量(mg/m3):焦油和灰尘小于10,硫化氢小于20,氨小于50(冬季)和100(夏季):(3)含氧量小于1%(体积)。 6.焦炉煤气有那些性质? 焦炉煤气性质主要有如下几个方面:(1)焦炉煤气是一种无色(在没有回收化学产品时呈黄色)有毒气体(约含6%的CO);(2)发热值较高(16720-18810kJ/m3), (3) ℃);(5 7. %以上。 8. 9. 焦炉煤气中硫化氢含量主要取决于配合煤的含硫量。煤在高温炼焦时,煤中的硫约有25-30%转入到煤气中。我国煤含硫量较低,焦炉煤气中硫化氢含量一般为:洗苯塔前为4.5-6.0克/米3,洗苯塔后为4-4.5克/米3。 10.焦炉煤气为什么要脱除硫化氢? 焦炉煤气中硫化氢是一种有害物质,它腐蚀化学产品回收设备及煤气储存输送设
备。含硫化氢高的焦炉煤气用于炼钢,会降低钢的质量;用于合成氨生成,会使催化剂中毒和腐蚀设备;用作城市煤气时,硫化氢燃烧产生的二氧化硫有毒,因而破坏了环境卫生,影响人的健康。因此,焦炉煤气净化过程脱除硫化氢是非常重要的。 11.为什么在焦炉煤气的净化过程中要除氨? 工业生产中所以要除去煤气中氨,主要有三点原因:(1)氨是一种较好的农业肥料。(23)氨 12.煤 600-650 13.什 (2 14.什 15.焦炉煤气煤气的爆炸极限是多少?为什么规程规定煤气中含氧量不大于2%? 焦炉煤气的爆炸极限是5.5-30%。是指空气中煤气的体积含量;简单的数学演算可知空气进入煤气中的量要达到70-94.5%时,才能引起爆炸,低于70%或高于94.5%都不会引起爆炸,即是煤气含氧量14.7%-19.85%时才能引起爆炸。为了保险起见,煤气规程规定含氧量不大于2%。
煤气净化工艺工艺流程..
煤气净化工艺工艺流程及主要设备 煤气净化设施 1概述 煤气净化车间生产规模按2×65 孔5.5m 捣固焦炉焦炉年产130万t 干全焦配套设计。焦炉煤气处理量为75300m3/h(标况)。 煤气净化车间由冷凝鼓风工段、脱硫工段、硫铵工段(含蒸氨系统)、终冷洗涤及粗苯蒸馏工段、油库及其相关的生产辅助设施组成。 2设计原则 对煤气净化车间本着经济、实用、可靠的原则,在满足国家环保、 职业卫生与安全、能源等法规要求的前提下,尽量简化工艺流程,并 合理配备工艺装备,以节省投资和工厂用地。 3设计基础数据 a)煤气量基础数据 焦炉装煤量(干基):206.98t/h 煤气产量:340Nm3/t(干煤) b) 煤气净化指标 表1 煤气净化指标表 序号指标名称单位净化前指标净化后指标 1 NH3g/m36~8 ≤0.05 2 H2S g/m35~7 ≤0.2 3 苯g/m324~40 ≤4 4 焦油g/m 3 ≤0.02 5 萘g/m 3 ≤0.3 4原材料及产品指标 4.1焦油——符合YB/T5075-2010 2号指标 序号指标名称质量指标 1 密度(20℃),g/cm3 1.13~1.22
序号指标名称质量指标 2 甲苯不溶物(无水基),% ≤9 3 灰分,% ≤0.13 4 水分,% ≤4.0 5 粘度(E80) ≤4.2 6 萘含量(无水基),% ≥7.0(不作考核指标)4.2硫酸铵—符合GB535-1995一级品 序号指标名称质量指标 1 氮N含量(以干基计),% ≥21 2 含水,% ≤0.3 3 游离酸含量,% ≤0.05 4.3粗苯—符合YB/T5022-1993 序号指标名称质量指标(溶剂用) 1 密度(20℃),g/ml ≤0.900 2 75℃前馏出量(重),% ≤3 3 180℃前馏出量(重),% ≥91% 4 水分:室温(18~25℃)下目测无可见的不 溶解的水 4.4洗油指标 序号指标名称指标 1 密度(20℃),g/ml 1.03~~1.06 2 馏程(大气压760mmHg),% 230℃前馏出量(容),% ≥3.0 300℃前馏出量(容),% ≥90.0 3 酚含量(容),% ≤0.5 4 萘含量(重),% ≤8 5 水分≤1.0
焦炉煤气净化工艺的有关思考
龙源期刊网 https://www.360docs.net/doc/3b14089055.html, 焦炉煤气净化工艺的有关思考 作者:郭晓林 来源:《中国化工贸易·中旬刊》2018年第07期 摘要:焦炉煤气装置主要包括煤气脱苯、煤气脱硫、煤气脱氮等几个环节,不同工序具 有不同的施工工艺。在全球环保法规日益严格的背景下,以往煤气净化技术弊端逐渐凸显。而焦炉煤气中含有的HCN、H2S及其他燃烧后废料对大气也造成了严重的影响。因此本文根据现阶段焦炉煤气净化主要工序特点,对焦炉煤气净化工艺进行了优化分析,以便为焦化工业的可持续发展提供有效地借鉴。 关键词:煤炉;煤气;净化 某焦化厂主要包括4座4.2m焦炉、1座6.2m焦炉,其设计煤气处理能力为 125000Nm3/h。随着该焦化企业生产规模拓展,在2017年建成投产后,年度设计生产能力由 以往的210万t焦炭上升到300万t焦炭,同时焦炉煤气总发生量也由以往的120000Nm3/h上升到150000Nm3/h。这种情况下,实际生产系统指标就出现不匹配风险。本文对该焦化企业焦炉煤气净化工艺进行了优化分析。 1 焦炉煤气净化工艺主要工序 ①焦炉煤气脱氮:在焦炉干馏环节,大多数氮可转化为以氨根离子为基础的含氮化合物,在煤气粗提取环节也存在6-8g/m3的氮。由于氨具有腐蚀性质,因此在实际处理过程中,需要采用氨水焦油分离装置将其分层分离。 ②焦炉煤气脱苯:焦炉中煤气脱苯主要依据理论脱苯标准,依次通过冷冻、吸附、洗涤等工序进行处理。在焦化工业生产过程中,依据焦油来源共分为石油洗油洗苯、焦油洗油洗苯两种类型。在粗焦油加工系统的大规模焦化企业,大多选择自产焦油洗油洗涤模式。 ③焦炉煤气脱硫:在焦炉煤气中存在着少量的硫化氢及氰化氢气体。现阶段我国煤气脱硫方式主要包括干式氧化、湿式吸收、湿式氧化等几种类型。其中干式氧化主要采用氧化铁箱法,整体使用较普遍。 2 焦炉煤气净化工艺的改进 2.1 环保技术 焦炉煤气净化工艺根据净煤气质量指标及焦化产业市场标准,具有不同的工艺流程。而系统工艺改进则是通过物料流、能源流、信息流、资金流等各个环节设计控制及优化组织,结合环保技术的合理应用,实现过程分析优化。
焦炉荒煤气净化工艺
焦炉荒煤气净化工艺 焦炉荒煤气中一般含硫化氢为4~8 g/m3、含氨为4~9 g/m3、含氰化氢为0.5~1.5 g/m3。硫化氢(H2S)及其燃烧产物二氧化硫(SO2)对人身均有毒性,氰化氢的毒性更强。氰化氢和氨在燃烧时生成氮氧化物(NOx)。二氧化硫(SO2)与氮氧化物(NOx)都是形成酸雨的主要物质,煤气的脱硫脱氰洗氨主要是基于环境保护的需要。此外在冶金工厂,高质量钢材的轧制,对其使用的燃气含硫也有较高的要求。随着科学技术的进步和焦化工业的发展,产生了众多各具特色的煤气脱硫洗氨净化工艺。 HPF 法脱硫属湿式催化氧化法脱硫工艺,是PDS 脱硫工艺的改进工艺,两者的区别在于所使用的催化剂略有差异:前者使用对苯二酚加PDS 及硫酸亚铁的复合催化剂(HPF),后者使用PDS 催化剂。HPF 催化剂在脱硫和再生过程中均有催化作用,是利用焦炉煤气中的氨做吸收剂,以HPF 为催化剂的湿式氧化脱硫。煤气中的H2S 等酸性组分由气相进入液相与氨反应,转化为硫氢化铵等酸性铵盐,再在空气中氧的氧化下转化为硫。HPF 法脱硫选择使用HPF(醌钴铁类)复合型催化剂,可使焦炉煤气的脱硫效率达到99%左右。 HPF 法脱硫工艺置于喷淋式饱和器法生产硫铵的工艺之后。从鼓风冷凝工段来的温度约55 ℃的煤气,首先进入直接式预冷塔与塔顶喷洒的循环冷却水逆向接触,被冷至30~35 ℃;然后进入脱硫塔。 工艺特点 (1)以氨为碱源、HPF 为催化剂的焦炉煤气脱硫脱氰新工艺,具有较高的脱硫脱氰效率(脱硫效率99%,脱氰效率80%),而且流程短,不需外加碱,催化剂用量小,脱硫废液处理简单,操作费用低,一次性投资省。 (2)硫磺收率一般为60%,硫损失约为40%,其废液量约为300~500 kg/(103m3·h),废液回兑至配煤中,对焦碳的质量有一定的影响。 (3)硫膏产品质量不理想,外观多为暗灰色,纯度90%左右,产品销售难度大。若后续能再配置硫膏生产硫酸的工艺,硫酸用于硫铵生产,则HPF工艺不失为一种完善的工艺。
焦炉煤气净化技术现状
焦炉煤气净化技术现状 在2004年国家公布的《焦化准入条件》中,明确规定新建或改造焦炉要同步配套建设煤气净化设施。至2006年底,经国家发改委核准的厂家仅108家,这些家的产能之合仅占当年焦炭总产能的30%左右。还有大量企业未被核准,其主要原因之一就是煤气净化设施配套不完善。煤气净化设施主要包括冷凝鼓风装置、脱硫脱氰装置、氨回收装置及苯回收装置。所谓配套不完善,是指缺某个或某些装置,特别是缺脱硫脱氰装置。 主流工艺技术 我国焦炉煤气净化工艺通过不断引进国外先进技术和创新发展,已经步入世界先进行列;煤气净化工艺已基本涵盖了当今世界上较为先进的各种工艺流程。目前,年产焦炭100万t以上的大型焦化厂全部设有煤气净化系统,对来自炼焦炉的荒煤气进行净化处理,脱除其中的硫化氢、氰化氢、氨、焦油及萘等各种杂质,使之达到国家或行业标准,供给工业或民用用户使用;同时,对化工副产品进行回收利用。 煤气净化工艺采用的主要技术包括:焦炉煤气的冷凝冷却及排送、焦油氨水分离、焦油、萘、硫化氢、氰化氢、氨等杂质的脱除以及粗苯的回收等。 焦炉煤气的冷凝冷却 焦炉煤气的冷凝冷却,即初步冷却,普遍采用了高效横管间冷工艺。其特点是:煤气冷却效率高,除萘效果好;当煤气温度冷却至20~22℃,煤气出口含萘可降至0.5g/m3,不需另设脱萘装置即可满足后续工艺操作需要。
高效横管间冷工艺通常分为二段式或三段式初冷工艺。当上段采用循环冷却水,下段采用低温冷却水对煤气进行冷却时,称为二段式初冷工艺。为回收利用荒煤气的余热,通常在初冷器上部设置余热回收段,即构成三段初冷工艺。采用三段初冷工艺,回收的热量用作冬季采暖或其它工艺装置所需的热源,不仅可以回收利用荒煤气的余热,同时也可节省大量循环冷却水,节能效果显著,应大力倡导采用。 除上述普遍采用的横管间冷工艺外,焦炉煤气的冷凝冷却也可采取先间冷,后直冷的“间直冷工艺”对焦炉煤气进行冷却。间直冷工艺的优点在于煤气在通过直冷塔冷却的同时,可对煤气中夹带的煤粉进行洗涤、净化,使去后续装置的煤气更加洁净;缺点是工艺流程较长,运行费用高,脱萘效果差,一般需单独设置后续脱萘装置。 焦炉煤气的排送 焦炉煤气的排送由煤气鼓风机完成。从焦炉来的荒煤气经初冷工艺冷凝冷却后,通常经电捕焦油器(当电捕设在负压侧)进入煤气鼓风机,由煤气鼓风机加压后,送至后续装置。 目前,国内焦化厂煤气鼓风机较多采用电动离心式煤气鼓风机,其流量调节通常采用液力偶合器调速、电机变频调速或鼓风机前导向技术完成上述三种煤气鼓风机流量调节技术均可根据煤气输送负荷的变化,对煤气流量进行自动调节、降低鼓风机的电能消耗、降低运行费用;其中,变频技术由于技术成熟,节能效果显著,在工业生产中应用广泛,因此值得广泛采用。 除电动煤气鼓风机外,蒸汽透平驱动的煤气鼓风机在国内外煤气排送工艺中也常采用。由于同电动鼓风机相比,汽动鼓风机具有能源利用率更高,更加节能
焦炉煤气净化工艺流程的评述
作者:范守谦时间:2008-7-8 10:25:53 焦炉煤气净化工艺流程的评述 范守谦(鞍山焦化耐火材料设计研究院) 焦炉煤气净化工艺流程的选择,主要取决于脱氨和脱硫的方法。众所周知,在炼焦过程中,煤中约有30%的硫进入焦炉煤气,95%的硫以硫化氢的形式存在。焦炉煤气中一般含有硫化氢6~8g /m3 , 氰化氢 1. 5~2g/m'。若不事先脱除,就有50%的氰化氢和10%~40%的硫化氢进入氨、苯回收系统,加剧了设备的腐蚀,还会增加外排污水中的酚、氰含量。含有硫化氢和氰化氢的煤气作为燃料燃烧时, 会生成大量SO 2和NO x 而污染大气。为了防止氨对煤气分配系统、煤气主管以及煤 气设备的腐蚀和堵塞,在煤气作为燃料使用之前必须将其脱除。20世纪70年代以前,由于焦炉煤气主要供冶金厂作工业燃料,因此,大部分焦化厂的煤气净化工艺都没有设置脱硫装置,而回收氨的装置几乎全采用半直接法饱和器生产硫铵流程。 随着国民经济的发展以及我国环保法规的不断完善和日益严格,在焦炉煤气净化工艺过程设置脱硫脱氰装置和改进脱氨工艺就势在必行。进入80年代以后,改革开放逐步深入,我国焦化行业和煤气行业相继从国外引进了多种煤气净化装置,国内科技人员在原有基础上也开发研制了新型脱硫工艺,大大推动了我国焦炉煤气净化工艺的发展。现将几种脱氨和脱硫方法作扼要介绍和论述。 1 氨的脱除 1.1 硫铵工艺 生产硫铵的工艺是焦炉煤气氨回收的传统方法,我国在20世纪60年代以前建成的大中型焦化厂均采用半直接法饱和器生产硫铵,该工艺的主要缺点是设备
腐蚀严重,硫铵质量差,煤气系统阻力大。随着宝钢一期工程的建设,我们引进了酸洗法生产硫铵工艺,该工艺由酸洗、真空蒸发结晶以及硫铵离心、干燥、包装等三部分组成。与饱和器法相比,由于将氨吸收和硫铵结晶操作分开,可获得优质大颗粒硫铵结晶。酸洗塔为空喷塔,煤气系统的阻力仅为饱和器法的1/4,可大幅度降低煤气鼓风机的电耗。采用干燥冷却机将干燥后的硫铵进一步冷却,以防结块,有利于自动包装。我院开发的酸洗法工艺也已成功地用于天津煤气二厂。随着宣钢、北焦的建设,我们还引进了间接法饱和器生产硫铵工艺,该工艺是从酸性气体中回收氨,其产品质量要比饱和器法好,但因在较高温度(100℃左右)下操作,对设备和管道材质要求高,加之饱和器尺寸并不比半直接法小,因此投资高于半直接法。鞍钢二回收还从法国引进了喷淋式饱和器以代替半直接法的饱和器。喷淋式饱和器的特点是煤气系统阻力小,设备尺寸也相应减小,硫铵质量有所提高。但是,不管采用那种生产硫铵的工艺,从经济观点分析,其共同的致命缺点是回收硫铵的收入远远不够支付其生产费用。 1.2 无水氨工艺 另一种可供选择的脱氨方法是用弗萨姆法生产无水氨。弗萨姆工艺是由美钢联开发的,它可以从焦炉煤气中吸收氨(半直接法),也可以从酸性气体中吸收氨(间接法)。 宝钢二期工程是从美国USS公司引进的从焦炉煤气中吸收氨的弗萨姆装置,焦炉煤气导入吸收塔,,体气体xn磷酸铵溶液与煤气直接接触,吸收煤气中的氨,然后经解析、精馏制取产品无水氨。该工艺主要是利用磷酸二氢铵具有选择性吸收的特点,从煤气中回收氨,并精馏制得纯度高达99. 98 %的无水氨。但由于介质具有一定的腐蚀性,且解吸、精馏操作要求在较高的压力下进行,故对设备材质要求较高。但该工艺的经济性受生产规模影响较大,规模过小时,既不经济也不易操作。 攀钢焦化厂在引进AS法脱硫的同时引进了间接法弗萨姆法无水氨装置,将脱酸塔顶的酸性气体引入间接法弗萨姆装置的吸收塔,用磷酸溶液吸收酸性气体中的氨。由于不与煤气直接接触,几乎不产生酸焦油,与半直接法相比,可大大简化分离酸焦油的处理设施。弗萨姆装置生产的无水氨纯度高,产值也较高,经济效益较好,但储运不方便。 1.3 氨分解工艺
煤气净化车间工艺流程
1.煤气净化车间 3.1概述 本煤气净化车间是与年产2×96万吨冶金焦的焦炉配套的,煤气处理量为115590 m3/h。其组成为:冷凝鼓风工段、脱硫工段、硫铵工段(含剩余氨水蒸氨装置)、终冷洗苯工段、粗苯蒸馏工段、油库工段。 3.2设计基础数据 3.2.1 净化前煤气中杂质含量 杂质成分NH3H2S HCN 苯 含量g/m3 6 6 1.5 34 3.2.2净化后煤气中杂质含量 杂质成分焦油NH3H2S HCN 苯萘含量g/m30.05 0.05 0.02 0.3 4 0.3 3.2.3产品产率 焦油 3.5%(对干煤) 硫铵0.84%(对干煤) 粗苯 1.0%(对干煤) 3.2.4焦油——符合YB/T5075-93 密度(20?C) 1.15~1.21g/cm3 甲苯不溶物(无水基) 3.5~7% 灰分不大于0.13% 水分不大于4.0%
粘度(E80) 不大于4 3.2.5硫磺: 含硫≥90% 3.2.6硫铵——符合GB535-1995 氮(N)含量(以干基计)≥21.0% 水分(H2O)含量≤0.3% 游离酸H2SO4含量≤0.05% 3.2.7粗苯——符合YB/T5022-93 外观黄色透明液体 密度(20?C) 0.871~0.900g/cm3馏程: 180℃前馏出量(重)不小于93% 水分室温(18~25℃)下目测无可见的不溶解的水 3.3煤气净化工艺流程、特点及主要操作指标 3.3.1冷凝鼓风工段 a)工艺流程 来自焦炉~80?C的荒煤气,与焦油和氨水沿吸煤气管道流至气液分离器,气液分离后的荒煤气由分离器上部出来,进入四台并联操作的横管初冷器上部,在此用32?C的循环水将煤气冷却至~35?C;由横管初冷器下部排出的煤气,进入直冷塔下部,用直冷塔循环水喷洒煤气,将煤气冷却至~22?C;由直冷塔上部排出的煤气,进入三台并联操作的电捕焦油器,捕集煤气中夹带的焦油,再由煤气鼓风机压
2020年焦炉煤气知识问答题库答案大全汇总
焦炉煤气知识问答题库答案大全汇总 1. 荒煤气的组成有哪些?占多大的比例? 煤在炭化室内炼焦产生的没有经过净化处理的黄色粗煤气叫荒煤气。 荒煤气的组成大致是(克/米3):水蒸气250-450、焦油气80-120、粗苯30-45、氨8-16、硫化氢6-30、氰化物1.0-2.5、轻吡啶盐 基0.4-0.6、萘10、其它2-2.5 2. 为什么荒煤气必须净化? 煤在炭化室内炼焦产生的煤气(荒煤气)含有大量各种化学产品,其 中焦油、萘容易凝结挂霜堵塞管道,影响煤气的输送。另外,荒煤气 中还含有硫化物、氰化物等有毒成份,并且对煤气设备有腐蚀性。所 以这种煤气不经加工处理,或者说不经精制是不能作为气体燃料使用的,煤气净化的目的是除去荒煤气中的焦油雾、氨、苯类、轻油、硫 化物、氰化物、萘、煤气中的液体(即冷凝氨水),最后获得以氢、 甲烷等不凝性气体为主的精制焦炉煤气。
3. 净焦炉煤气组成有哪些?净煤气(经回收化学产品后的煤气,又称回炉煤气)的组成大致是(体积%):氢气54-59、甲烷23-28、其它烃类2-3、一氧化碳5.5-7、二氧化碳1.5-2.5、氧气0.3- 0.7、氮气3-5 4. 荒煤气净化后主要分离出哪几种产品?产率都是多少? 荒煤气经冷凝回收处理后,分离出煤气、焦油、粗苯和氨他们的煤产 率如下(按炼焦干煤的重量%计): 煤气15-19、焦油3-4、粗苯0.9-1.2、氨0.2-0.3 5. 城市煤气有哪些要求? 各国对城市煤气的质量均有严格要求,对杂质含量都作出明确规定。 中国规定的指标与工业发达国家基本相似,具体要求为:(1)低发热 值大于14654kJ/m3;(2)杂质允许含量(mg/ m3):焦油和灰尘小于10,硫化氢小于20,氨小于50(冬季)和100(夏季):(3)含氧量小于1%(体积)。
焦炉煤气精处理方法的优化方案
冶金动力 2018年第10期总第期 引言 燃气蒸汽联合循环发电(简称CCPP)是目前最为先进、成熟的发电技术。以焦炉煤气为燃料的航改型燃气轮机发电为CCPP 发电技术的一种,但要求进燃机焦炉煤气洁净度非常高,经过焦化车间净化工序、焦炉煤气精制装置后仍无法满足要求。目前我国现有焦炉煤气轻型燃气轮机在投产初期,燃气轮机的运行都遇到了焦油含量高的困扰,频繁停机更换滤芯,原因即是焦炉煤气中含有少量苯、萘、焦油等杂质成分,这些杂质在管道经过过滤器时,流速降低,或焦炉煤气温度降低时,有一部分会冷凝析出堵塞燃机自带的入口装置滤芯。如何降低燃机入口焦炉煤气中焦油含量成为燃机安全稳定运行的关键。 1目前焦炉煤气精处理方法 针对燃机入口焦炉煤气过滤器频繁堵塞的情 况,现有的处理方法都是在燃机焦炉煤气过滤器前进行整改,通过对精过滤器前焦炉煤气冷却、过滤、加热脱除焦炉煤气中的苯、萘、焦油等杂质成分。 现有的技术方法一: 如图1中所示为现有焦炉煤气蒸汽联合循环发电工艺流程图,焦化工艺精制焦炉煤气首先进入压缩机进行四级压缩,压缩后的高温焦炉煤气经冷却、分离进入过滤阶段,主要包括粗过滤和精过滤两个 阶段将煤气中颗粒物脱除,最后进入燃汽轮机。 图1焦炉煤气精处理技术方法一 现有的技术方法二: 如图2中所示的流程是基于图1中的焦炉煤气蒸汽联合循环发电工艺流程发展起来的,其主要特点是在焦炉煤气过滤后利用蒸汽对焦炉煤气进行加热,使焦炉煤气中杂质保持气态进入燃机。 图2焦炉煤气精处理技术方法二 2现有焦炉煤气精处理方法优缺点 图1中的技术方案,利用了焦炉煤气的物理特性对煤气进行净化处理,但在设备运行中还是出现 了精过滤器频繁堵塞的现象。其主要原因是压缩后 的焦炉煤气经过冷却后温度降低,虽然在冷却后设置了气水分离装置,但由于分离后的煤气温度依旧保持在煤气中苯、萘等杂质的结晶露点以下,使得各 焦炉煤气精处理方法的优化方案 张晓凯,曹韦韦,张荣宇,李海英 (中冶京诚工程技术有限公司,北京 100176) 【摘要】针对当前焦炉煤气CCPP 项目中焦炉精处理系统,提出了优化的处理方案,即用高温未净化焦 炉煤气加热净化后的焦炉煤气,减少冷却水量消耗的同时也降低了蒸汽加热器蒸汽量的消耗。 【关键词】焦炉煤气;CCPP;精处理;热法【中图分类号】TQ546.5 【文献标识码】B 【文章编号】1006-6764(2018)10-0017-02 Optimization Program of the Precision Treatment Method for Coking Gas ZHANG Xiaokai,CAO Weiwei,ZHANG Rongyu,LI Haiying (Capital Engineering &Research Incorporation Limited,Beijing 100176,China) 【Abstract 】The paper provides an optimized treatment program for current coke oven precision treatment system in coking gas CCPP project that is to use high-temperature unpuri-fied coking gas to heat purified coking gas,which can reduce the steam consumption of the steam heater as well as reduce cooling water consumption. 【Keywords 】coking gas;CCPP;precision treatment;hot process
焦炉煤气净化文章
焦炉煤气净化文章 1. 焦炉煤气净化技术现状及探讨 1.1. 焦炉煤气净化的作用 焦炭是冶金工业炼铁的主要原料。全国共有焦化企业200余家,其中约10%生产能力超过100万t/a ,总生产能力超过亿t/a ,中国焦炭产量居世界第一位,焦化产品百余种。炼焦用煤在复杂的地质状况下含有上百种成分,在焦炉中成焦时,其中多种成分随煤气一起进入随后的工序。在炼焦过程中原料煤中约30%~35%的硫转化成H S 等含量一般为5g ~8g/m ,HCN 的含量为1g/m ~2.5g/m 。而H S 和HCN 具有很强的腐蚀性、毒性,在空气中含有.1%的S 就能使人毒,会严重污染环境,所以煤气作为燃料使用之前必须进行净化。1792年苏格兰人发明用铁罐干馏烟煤以来,煤气制造技术发展较快。法国、德国、英国、荷兰先后建立起能够回收化学产品的焦炉,并以奥托——霍夫曼型焦炉最为著名,从此炼焦工业不仅生产焦炭,同时也生产净煤气。 硫化物,与N H 和HCN 等一起形成煤气中的杂质,煤气中的H S 的/m 0H 致命,当焦炉煤气最终用作燃料时,硫化氢及燃烧产物二氧化硫均有
1.2.煤气净化的内容及技术现状 煤气净化主要是脱除煤气中有害成分,具体包括冷却和输送出炉 H H 煤气、脱除煤气中S,HCN等酸性气体和N 类碱性气体、脱除及回收煤气中焦油类、苯类等物质以及萘等。因此一般的净化工艺包括鼓冷、洗涤、解析、后处理等主要工序内容。 1.2.1煤气的初冷 煤气的初冷是指出炉煤气通过集气管喷洒氨水和设置初冷器将 出炉煤气由650~800℃降至25℃左右的处理过程。初冷器冷却方法通常有间接式、直接式、间直结合式3种。冷却设备有直冷式喷淋塔、立管式初冷器和横管式初冷器。间接式煤气冷却过程冷却水不与煤气接触,通过换热器完成两相传热。由于冷却介质——水没有受到煤气中有害介质的污染,循环使用次数多。间冷式适用于大多数缺水地区的焦化厂。由于煤气初冷时有大量萘的结晶析出,所以采用立管式初冷器的工艺要求初冷器后集合温度不低于25℃,以防冷凝液管堵塞。而在采用横管多级喷洒洗萘初冷器的工艺中,由于喷洒液对萘的吸收而大大降低了萘结晶堵塞管道。直冷煤气设备通常采用塔,由煤气与冷介质的逆相直接接触,完成热量和物质传递,因此煤气直接冷却,不但冷却了煤气,而且具有净化的效果。据测定,在直冷过程中可有效除去煤气中90%以上的焦油、80%左右的氨、60%的萘、80%的H S 等。鉴于间、直冷各自优点,多数厂家采用间——直冷结合方式, 即煤气先在间接初冷器中冷却至45℃后,再进入直接冷却器进一步冷
焦炉煤气知识问答
焦炉煤气知识问答 1.荒煤气的组成有哪些?占多大的比例? 煤在炭化室内炼焦产生的没有经过净化处理的黄色粗煤气叫荒煤气。荒煤气的组成大致是(克/米3):水蒸气250-450、焦油气80-120、粗苯30-45、氨8-16、硫化氢6-30、氰化物1.0-2.5、轻吡啶盐基0.4-0.6、萘10、其它2-2.5 2.为什么荒煤气必须净化? 煤在炭化室内炼焦产生的煤气(荒煤气)含有大量各种化学产品,其中焦油、萘容易凝结挂霜堵塞管道,影响煤气的输送。另外,荒煤气中还含有硫化物、氰化物等有毒成份,并且对煤气设备有腐蚀性。所以这种煤气不经加工处理,或者说不经精制是不能作为气体燃料使用的,煤气净化的目的是除去荒煤气中的焦油雾、氨、苯类、轻油、硫化物、氰化物、萘、煤气中的液体(即冷凝氨水),最后获得以氢、甲烷等不凝性气体为主的精制焦炉煤气。 3.净焦炉煤气组成有哪些?净煤气(经回收化学产品后的煤气,又 称回炉煤气)的组成大致是(体积%):氢气54-59、甲烷23- 28、其它烃类2-3、一氧化碳5.5-7、二氧化碳1.5-2.5、氧气 0.3-0.7、氮气3-5 4.荒煤气净化后主要分离出哪几种产品?产率都是多少? 荒煤气经冷凝回收处理后,分离出煤气、焦油、粗苯和氨他们的煤产率如下(按炼焦干煤的重量%计): 煤气15-19、焦油3-4、粗苯0.9-1.2、氨0.2-0.3
5.城市煤气有哪些要求? 各国对城市煤气的质量均有严格要求,对杂质含量都作出明确规定。中国规定的指标与工业发达国家基本相似,具体要求为:(1)低发热值大于14654kJ/m3;(2)杂质允许含量(mg/ m3):焦油和灰尘小于10,硫化氢小于20,氨小于50(冬季)和100(夏季):(3)含氧量小于1%(体积)。 6.焦炉煤气有那些性质? 焦炉煤气性质主要有如下几个方面:(1)焦炉煤气是一种无色(在没有回收化学产品时呈黄色)有毒气体(约含6%的CO);(2)发热值较高(16720-18810 kJ/m3),含惰性气体少(氮气约4%),含氢气较多(近60%),燃烧速度快,火焰短;(3)爆炸范围大(5-30%),遇空气易形成爆炸性气体;(4)易着火,燃点低(600℃);(5)煤气较脏时,管道易被焦油、萘堵塞,煤气中冷凝液还会腐蚀管道。 7.焦炉煤气中的硫化氢是怎样形成的? 在炼焦过程中,配合煤中的一部分硫在高温作用下,主要形成无机物的硫化氢和少许部分有机硫化物(二氧化硫、噻吩等)。有机硫化物在较高温度作用下继续发生反应,几乎全部转化为硫化氢,煤气中硫化氢所含硫约占煤气中总含硫量的90%以上。 8.硫化氢有哪些主要物理性质? 硫化氢在常温下是一种带刺激臭味的气体,其密度为 1.539千克/米3,燃烧时能生成二氧化硫和水,有毒,在空气中含0.1%时就能使人死亡。同时硫化氢对钢铁设备有严重的腐蚀性。
煤气净化作业指导书
化产操作规程 鼓冷岗位 1工艺流程 4.1煤气初冷单元简述 从焦炉来的荒煤气以及氨水、焦油,经初冷器前的气液分离器分离,荒煤气去横管初冷器,液体流入机械化澄清槽。在初冷器内,煤气自上而下从管间流过初冷器,冷却水自下而上经过冷却水管内。横管初冷器分三段冷却,下段用低温水,中段用循环水,上段用采暖水,同时混合液(轻质焦油)在初冷器内分中、下两段喷洒,除去荒煤气中的萘,初冷器上段设有热氨水喷洒管道,定期对初冷器进行喷洒,以清洗初冷器器体,保持初冷器阻力稳定在工艺范围之内。 离开焦炉的荒煤气冷凝下来的氨水、焦油等,以及初冷器、电捕等设备的冷凝液均进入机械化焦油氨水澄清槽,它们按密度不同在机械化焦油氨水澄清槽中分为三层;底部为焦油渣,用连续运转的刮板刮出;中间部分为焦油,靠压差自流入焦油分离器中加热,再用泵送到焦油中间槽;最上部为氨水,满流到循环氨水槽后,一部分送焦炉作循环氨水使用,一部分作为高压氨水供装煤除尘或集气道清扫使用,一部分作为剩余氨水经气浮除油机除油后自流入剩余氨水槽,由泵送入陶瓷过滤器处理,分离出的焦油自流入焦油分离器内。
4.3煤气捕雾工艺简述 初冷器冷凝后的煤气进入电捕焦油器下部,捕去焦油雾的煤气从顶部出来进入脱硫工序。 电捕焦油器为蜂窝式,强直流电在电晕极(负极)和沉淀极(正极)之间形成不均匀的高压电场,当煤气通过此高压电场时,夹带于煤气中的焦油雾和灰尘颗粒被荷电化,并沉淀于正极上(沉淀极),棸集成大颗粒焦油雾滴后,靠自身重力沉积于电捕焦油器底部,最终由电捕焦油器底部流出,经水封槽再流到鼓风地下池并送往鼓冷机械化焦油氨水槽。当电极需要清洗时,可用热氨水或蒸汽清扫。当安装在煤气管道上的氧分析仪检测出的氧含量超过1.0%(体积)时,电捕焦油器会发出报警,当氧含量超过2.0%(体积)时,电捕焦油器会自动断电,电源恢复手动进行。 4.4鼓风机单元简述 鼓风系统共有三台D1800-1.28/0.96型离心式鼓风机,分别由电机、液力耦合器、变速箱、风机本体组成,鼓风机输送介质为煤气,煤气在风机中为绝热压缩,煤气的压力是在转子的各个叶轮作用下,并经过压头转换被提高的。转子旋转的速度愈大,煤气的密度愈大,离心力愈大,煤气沿工作叶轮运动的速度也愈大,离开工作叶轮后的静压头就愈高。在输送过程中,煤气中的部分焦油、水被冷凝下来。并通过风机排液系统排出,为化产品的回收,风机的安全运行,煤气的正常输送创造良好的条件。 2主要工艺指标控制 5.1温度指标(℃) 初冷器前煤气温度≤78-82 初冷器循环水上水温度≤32 初冷器循环水下水温度≤45 初冷器低温水上水温度≤18 初冷器低温水下水温度≤30 初冷器煤气出口温度 20~25 两台初冷器煤气出口温差≤3~5 电捕绝缘箱温度 90~120 鼓风机及主电机机体温度<85
焦炉煤气净化工艺流程的评述
焦炉煤气净化工艺流程的评述 时间:2012-1-10 | 点击:79 | 字体:大小 范守谦(鞍山焦化耐火材料设计研究院) 焦炉煤气净化工艺流程的选择,主要取决于脱氨和脱硫的方法。众所周知,在炼焦过程中,煤中约有30%的硫进入焦炉煤气,95%的硫以硫化氢的形式存在。焦炉煤气中一般含有硫化氢6~8g /m3 , 氰化氢 1. 5~2g/m'。若不事先脱除,就有50%的氰化氢和10%~40%的硫化氢进入氨、苯回收系统,加剧了设备的腐蚀,还会增加外排污水中的酚、氰含量。含有硫化氢和氰化氢的煤气作为燃料燃烧时,会生成大量SO2和NOx而污染大气。为了防止氨对煤气分配系统、煤气主 管以及煤气设备的腐蚀和堵塞,在煤气作为燃料使用之前必须将其脱除。20世纪70年代以前,由于焦炉煤气主要供冶金厂作工业燃料,因此,大部分焦化厂的煤气净化工艺都没有设置脱硫装置,而回收氨的装置几乎全采用半直接法饱和器生产硫铵流程。 随着国民经济的发展以及我国环保法规的不断完善和日益严格,在焦炉煤气净化工艺过程设置脱硫脱氰装置和改进脱氨工艺就势在必行。进入80年代以后,改革开放逐步深入,我国焦化行业和煤气行业相继从国外引进了多种煤气净化装置,国内科技人员在原有基础上也开发研制了新型脱硫工艺,大大推动了我国焦炉煤气净化工艺的发展。现将几种脱氨和脱硫方法作扼要介绍和论述。 1 氨的脱除 1.1 硫铵工艺 生产硫铵的工艺是焦炉煤气氨回收的传统方法,我国在20世纪60年代以前建 成的大中型焦化厂均采用半直接法饱和器生产硫铵,该工艺的主要缺点是设备腐蚀严重,硫铵质量差,煤气系统阻力大。随着宝钢一期工程的建设,我们引进了酸洗法生产硫铵工艺,该工艺由酸洗、真空蒸发结晶以及硫铵离心、干燥、包装等三部分组成。与饱和器法相比,由于将氨吸收和硫铵结晶操作分开,可获得优质大颗粒硫铵结晶。酸洗塔为空喷塔,煤气系统的阻力仅为饱和器法的1/4,可 大幅度降低煤气鼓风机的电耗。采用干燥冷却机将干燥后的硫铵进一步冷却,以防结块,有利于自动包装。我院开发的酸洗法工艺也已成功地用于天津煤气二厂。随着宣钢、北焦的建设,我们还引进了间接法饱和器生产硫铵工艺,该工艺是从酸性气体中回收氨,其产品质量要比饱和器法好,但因在较高温度(100℃左右)下操作,对设备和管道材质要求高,加之饱和器尺寸并不比半直接法小,因此投资高于半直接法。鞍钢二回收还从法国引进了喷淋式饱和器以代替半直接法的饱和器。喷淋式饱和器的特点是煤气系统阻力小,设备尺寸也相应减小,硫铵质量有所提高。但是,不管采用那种生产硫铵的工艺,从经济观点分析,其共同的致
焦炉煤气净化工艺流程的选择复习课程
焦炉煤气净化工艺流 程的选择
焦炉煤气净化工艺流程的选择 (2011-01-24 13:14:42) 分类:焦化类 标签: 煤化工 杂谈 笑看人生 摘要:本文对我国煤气净化工艺的发展进行了回顾,提出了我国焦炉煤气净化工艺发展的方向以及选择工艺流程的原则。并推荐采用的焦炉煤气净化工艺流程以及各单元中应采用的行之有效的环保、节能技术。 1 焦炉煤气净化工艺的历史回顾 我国焦炉煤气净化发展是与炼焦工业的发展紧密相连的。建国以前,我国焦化工业几乎是一片空白。建国以来,随着炼焦工业的发展,煤气净化工艺从无到有,蓬勃发展,技术水平和装备水平得到了不断提高。概括起来,大体上经历了三个阶段。第一个阶段是从20世纪50年代末到60年代中期,我国焦化厂的焦炉煤气净化工艺主要是以50年代从原苏联引进的工艺为基础、消化翻板饱和器法生产硫铵的老流程,以当时的武钢焦化厂、包钢焦化厂、鞍钢化工总厂、太钢焦化厂、马钢焦化厂等一批大型厂为代表。但该工艺存在流程陈旧、能耗高、环保措施不健全、装备水平低等问题。主要表现在初冷采用立管冷却器,冷却效率低;硫铵装置设备庞大,煤 仅供学习与交流,如有侵权请联系网站删除谢谢2
气阻力大,产品质量差,设备腐蚀严重;没有配套建设脱硫装置,终冷系统不能闭路,对大气和水体污染严重;在粗苯蒸馏系统采用蒸汽法,不但耗用大量蒸汽,产品质量也得不到保证。第二阶段是从60年代中期至70年代末期,随着我国自行设计的58型焦炉不断推广及炭化室高5.5米焦炉的诞生,对煤气净化工艺开展了与石油、化工行业找差距进行技术革新的阶段。在广大技术人员的努力下,在此期间我们将初冷流程改为二段冷却;开发了多种油洗萘代替终冷水洗萘;研制成功了终冷水脱氰生产黄血盐,解决了终冷水的污染问题;推广采用了溶剂脱酚和生物脱酚装置;以管式炉脱苯代替蒸汽脱苯,开发了双塔、单塔脱苯新工艺;在个别焦化厂设置了改良ADA脱硫装置(如:梅山焦化厂、北京焦化厂等)。除此之外,为了适应当时国内硫酸供应紧张的情况,开发和推广了一大批采用氨水流程的焦化厂(如:济钢、莱钢、邯钢、杭钢、安钢、攀钢等)。当时,我国生产浓氨水的厂家曾占了整个焦化厂总数的三分之一。但是,氨水流程也存在着设备腐蚀、堵塞严重、浓氨水产品质量低劣、产品滞销、开工率低等致命问题。 因此,虽然经过我国工程技术人员的不断努力,焦炉煤气净化工艺有了一些进展,而从环保、能耗、技术水平、工艺装备、产品质量等方面来看,仍然未能摆脱落后的局面。第三阶段从改革开放以来算起,随着宝钢工程的建设,我国6米大容积焦炉的诞生,焦化厂的规模不断扩大,以及通过与国外技术交流,联合设计、技术引进等方式,先后引进了各种规模、不同工艺的多套装置,我国工程技术人员基本上掌握了全负压煤气净化工艺、AS洗涤脱硫工艺、脱酸蒸氨工艺、氨分解硫回收工艺、无饱和器法硫铵工艺、FRC法和T-H法脱硫脱氰工艺、索尔菲班法脱硫工艺、真空空碳酸盐法脱硫工艺、冷法和热法弗萨姆无水氨工艺以及与之相配套的生产浓仅供学习与交流,如有侵权请联系网站删除谢谢3
关于焦炉煤气净化回收的方案
焦炉煤气净化回收方案 山西天柱山化工有限公司
关于焦炉煤气净化回收的方案 随着企业的发展壮大,节能降耗的工作日益重要。为了搞好节能降耗工作,使企业实现效益最大化,同时满足日益严格的环保要求,使我公司实现循环经济,针对我公司化产回收系统目前存在的问题,特提出本方案。 一、总则 1、化产回收的运行具有连续性强、工段之间协调性强的特点,一个工段的条件变化会引起全系统的变化,因此,对它要从初冷器开始进行系统性的通盘考虑,才能实现良性运转。 2、尽可能挖掘现有系统的潜力,从运行管理、工艺调整实现系统的最佳运行。 3、目前严重制约系统正常运转但通过现有装置的工艺调整无法达到优化的问题,考虑用最小的投资完善装置来实现工艺的良性运行。 4、净焦炉气含氢50%以上,焦炉自身无法完全利用焦炉煤气,被迫排放,既是对环境的污染,更是能源的浪费。因此,考虑投资焦炉煤气提氢装置,既利用价值很高的有效氢,又为废气零排放创造了条件。 二、目前状况及存在问题 1、目前系统整体配置 系统工艺具体流程如下:
⑴煤气主要流程 来自初冷器22~25℃ 38~44℃净焦的焦炉煤气→罗茨风机→电捕焦→两台脱硫塔→洗氨→洗苯→ 含H2S 6~8g/m3 15~18KPa ↑↓炉煤气含NH3 4~6g/m3 贫液泵富液槽﹙255 m3﹚↓ ↑↓﹙经富液泵加压﹚↓ 贫液槽←再生槽排放←↓ ↑↓ 补来自蒸氨系统回炉利用 的浓氨水﹙约60℃﹚ ⑵蒸氨主要流程 放空 约90℃↑ 60℃ 蒸汽分缩器→气液分离器→换热器→送脱硫蒸氨废水↓↑↓ 回系统利用←↓约105℃↓ 约70℃↑↓↑↓ 来自 68℃↓ 98℃↑液体回流 原料氨水→换热器→换热器→蒸氨塔到蒸氨塔 槽的氨水↓↑ 0.5%左右↑约105℃蒸氨废水↓↑ ↑↓蒸汽 2、存在问题 从目前整体运行看,系统整体运行连续性差,只有洗氨、洗苯连续运行,脱硫系统处于断断续续运行状态,蒸氨浓氨水无法回收。 脱硫系统运行时,可以消耗蒸氨系统部分浓氨水,但从脱硫系统本身存在脱硫效率低、动力消耗高、硫膏产量低的问题,同时引出脱硫后煤气温度上升,影响洗苯效果的问题。另外,因脱硫系统需补来自蒸氨的浓氨水,蒸氨系统分缩器、氨水冷却器的运行导致全系统循环水温度上升,全系统工艺指标中温度呈现严重超标,不仅脱硫差,粗苯产量也下降,形成恶性循环运行状态。现将具体情况汇总如下: ⑴循环水系统