试生产管理程序文件

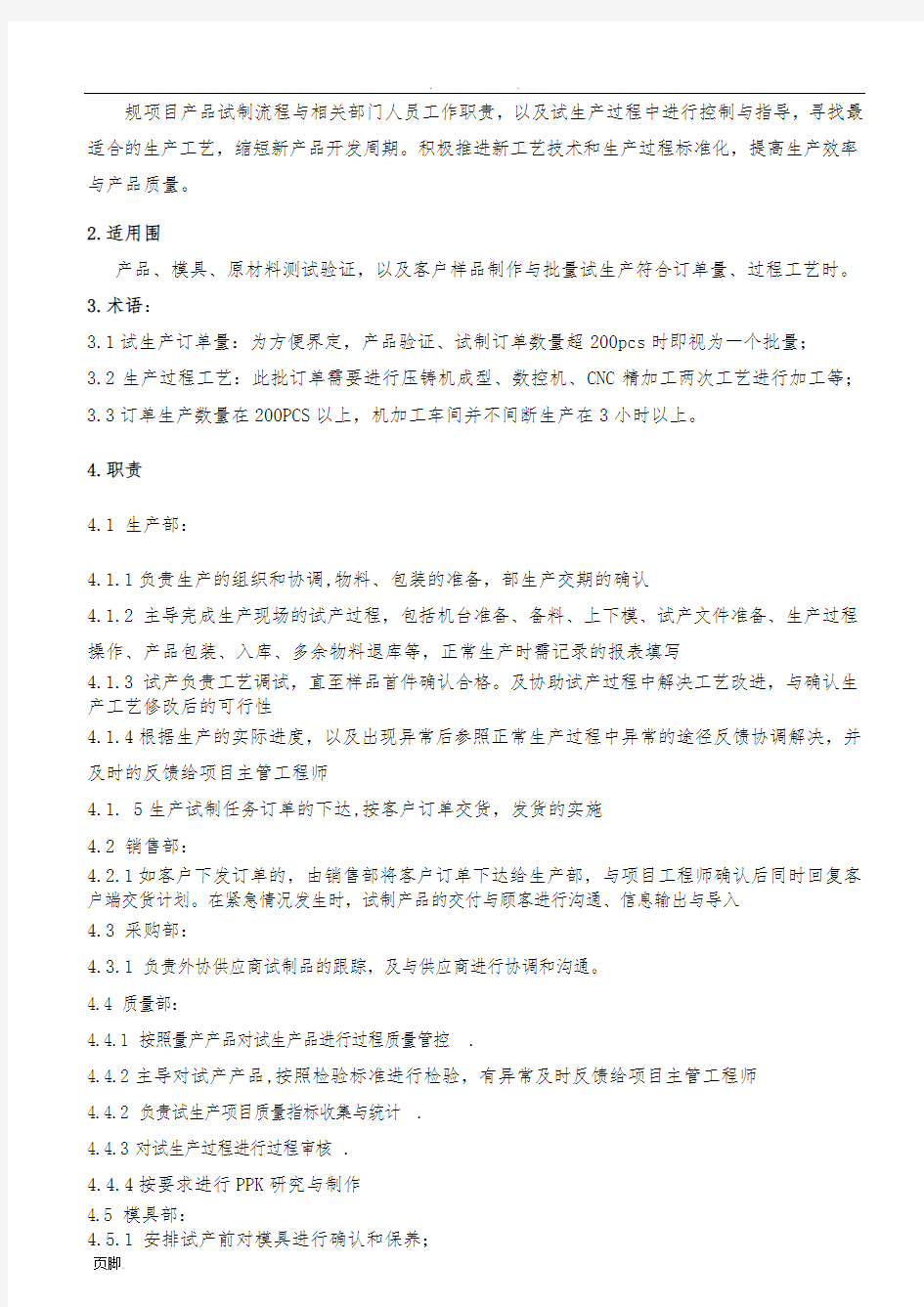
●程序文件批准页
ISO/TS16949:2009质量管理体系文件名称:试生产管理程序
文件号: DH.QP/7.3–03 版本号: A/0
编制:日期:
审核:日期:
批准:日期:
生效日期:受控状态/受控号:
1.目的
规项目产品试制流程与相关部门人员工作职责,以及试生产过程中进行控制与指导,寻找最适合的生产工艺,缩短新产品开发周期。积极推进新工艺技术和生产过程标准化,提高生产效率与产品质量。
2.适用围
产品、模具、原材料测试验证,以及客户样品制作与批量试生产符合订单量、过程工艺时。
3.术语:
3.1试生产订单量:为方便界定,产品验证、试制订单数量超200pcs时即视为一个批量;
3.2生产过程工艺:此批订单需要进行压铸机成型、数控机、CNC精加工两次工艺进行加工等;
3.3订单生产数量在200PCS以上,机加工车间并不间断生产在3小时以上。
4.职责
4.1 生产部:
4.1.1负责生产的组织和协调,物料、包装的准备,部生产交期的确认
4.1.2 主导完成生产现场的试产过程,包括机台准备、备料、上下模、试产文件准备、生产过程操作、产品包装、入库、多余物料退库等,正常生产时需记录的报表填写
4.1.3 试产负责工艺调试,直至样品首件确认合格。及协助试产过程中解决工艺改进,与确认生产工艺修改后的可行性
4.1.4根据生产的实际进度,以及出现异常后参照正常生产过程中异常的途径反馈协调解决,并及时的反馈给项目主管工程师
4.1. 5生产试制任务订单的下达,按客户订单交货,发货的实施
4.2 销售部:
4.2.1如客户下发订单的,由销售部将客户订单下达给生产部,与项目工程师确认后同时回复客户端交货计划。在紧急情况发生时,试制产品的交付与顾客进行沟通、信息输出与导入
4.3 采购部:
4.3.1 负责外协供应商试制品的跟踪,及与供应商进行协调和沟通。
4.4 质量部:
4.4.1 按照量产产品对试生产品进行过程质量管控.
4.4.2主导对试产产品,按照检验标准进行检验,有异常及时反馈给项目主管工程师
4.4.2 负责试生产项目质量指标收集与统计.
4.4.3对试生产过程进行过程审核.
4.4.4按要求进行PPK研究与制作
4.5 模具部:
4.5.1 安排试产前对模具进行确认和保养;
4.5.2 试产过程中对模具的状态进行确认,以及将模具操作的注意事项、保养事项交接给现场作业人员;
4.5.3 持续对模具进行优化的改善
4.6技术部:
4.6.1 试产前项目产品模具的确认,以及试产所需要包材、辅材、工装治具、文件等确认
4.6.2 试产前BOM、工序加工工艺卡、工艺管控参数、工序加工图纸/控制计划的完成
4.6.3 员工的作业方法的培训与指导
4.6.4 试产过程中产品异常信息的主导解决
4.6.5 对试产过程的审核和各指标达成的汇总,并完成试产报告存档
4.7 动力部:
4.7.1负责组织关键设备的及时维修
4.7.2负责关键设备明细的制定、修改和更新,紧急情况水、电、气等公用设施维修与及时处理。
5.试制作业流程:
5.1 试产订单接收与评价
5.1.1 在接收到订单后,先需确认信息有否同时知会到项目工程师与业务员,如没有知会完整,需将信息进行部门共享。
5.1.2 由销售部经理进行评审,回复客户
5.2试生产通知:
5.2.1 项目工程师根据销售业务试制订单,或根据技术部部项目的进度要求安排试生产(如
没订单的,项目工程师主导项目小组讨论安排部样品试产)。
凡安排试产的产品,必须确认BOM、工序加工工艺卡、工序加工图纸、检验标准、成型工艺管控参数、模具、机加工装、治具、量具等均需要准备到位。
5.2.2 试生产需求确定后, 项目工程师下发《试生产-制造计划》给生产部,并且特别标注明
材料损耗需求,以备应对试产断料突发情况;另数量也可按实际需要安排合理的数量。
5.2.3 生产计划确定准确的试产时间与机台,回签《试生产-制造计划》给项目,并安排生产
计划予车间,进行材料准备。
5.2.4 如果试产因为异常中断或取消需通知各相关部门,采购、销售、技术对应进行关闭处
理。
5.3 试生产要求:
5.3.1 试生产要求:
(1) 公司定义要求:生产数量在200模以上,并不间断生产在3小时以上;
(2) 参照客户要求。
5.3.2 试生产过程要求:
(1) 过程审核符合率≥80%;
(2) PPK值≥1.67;(如果新产品没有要求计算PPK的,由项目工程师在试产启动
会上明确1-2个重点尺寸进行PPK分析)
(3) 如客户要求有特殊要求的,参照客户要求执行。
5.4 试生产准备阶段:
5.4.1 生产部在编制试生产计划时,应考虑该项目安排在原试模的同类型压铸机台(如吨
位、机型);
5.4.2 质量部工程师、检验主管对本部门QC,生产班长、调试员、操作工进行产品质量
要求的培训,确保人员具备识别产品不良缺陷的能力,并形成《培训签到记录表》。
5.4.3 项目部项目工程师对车间主任、生产班长、调试员,操作工进行工序工艺卡、工序
加工图纸、工艺特殊参数、客户要求等进行培训,确保相关人员具备操作此产品的
能力,并形成《培训签到记录表》。
5.4.4 模具部装配主管接生产部计划表时,应指定对应装配模具师傅负责对模具状态进行
确认,确保模具型腔的清洁并按时将模具放到待试模区,同时通知项目工程师,由
项目工程师将信息落实到生产;
5.4.5 生产部门压铸冷室车间主任接到生产计划表时,应及时安排物料员领取正确的原材
料,并从模具部领模具到试产机台,依产品要求准备辅材,并确认对应的作业文件。
5.5试生产过程控制:
5.5.1 试产开始时,项目工程师负责协调该项目的相关人员到场确认;
5.5.2 第一次试产生产部在压铸模具、机加工夹具、机台清理准备好后,由车间主任或车
间主任指定工艺人员负责调试,生产技术人员现场参与学习,直至首件合格后交给
生产技术人员;
5.5.3 质量部QC在产品试生产过程,按照工艺加工卡、加工图纸对产品进行判定,并按
照QE要求收集试产过程中相关数据,以及相关缺陷不良品、PPK取样与分析;
5.5.4 QE在试生产过程,参照《产品过程审核控制》与项目工程师一起进行试生产过程审
核;
5.6 试生产后确认:
5.6.1 试生产过程信息,由生产车间当班领班在一个工作日填写【试生产报告】及试产《生
产参数工艺卡》交车间主任审核确认后交项目部项目工程师审核。
5.6.2 质量部2个工作日将试生产的过程审核结论、产品符合性(合格率、尺寸、性能、
外观等)、PPK分析报告、过程稳定性(MSA)填写于【试生产报告】交项目部项目
工程师
5.6.3 生产计划员需反馈试生产效率数据给项目工程师
5.6.4 项目工程师对【试生产报告】进行确认,并在试生产后1周组织召开试产总结会议,
按以下结论办理:
(1) 验收确认合格后,开出【量产批准书】将模具移交生产,项目资料移交质保部
档案室。
(2) 有条件验收合格,即允许在整改完成问题后,开出【量产批准书】将模具、夹
具移交生产车间,项目资料移交技术部档案。注:不会影响到产品的量产性的
问题才许可有条件验收。
(3) 验收不合格后,对本次试产反馈情况组织对应部门确定具体改进方案及确定下
次试生产时机。
注:试产总结会议按《项目开发目标实现情况》的标准模板展开。
5.6.5 试产后的产品,经质量部确认合格后,由生产部门根据生产计划数入库,并由项
目订单计划根据销售订单要求安排发货。如试产产品确认不合格,则由质量部开
【不合格品评审单】按照《不合格品控制程序》评审处理。
6. 相关记录:
6.1 试生产-制造计划书
6.2 试生产报告
6.3 项目开发目标实现情况
6.4 PPAP资料清单
6.5 PPAP检查表
6.6 最终产品包装评价报告
6.7 MSA报告
6.8 PPK报告
6.9不合格品评审单
6.10过程审核表
6.11产品审核表
7. 相关文件:
7.1 过程审核控制程序7.3 不合格品控制程序