炼钢工艺

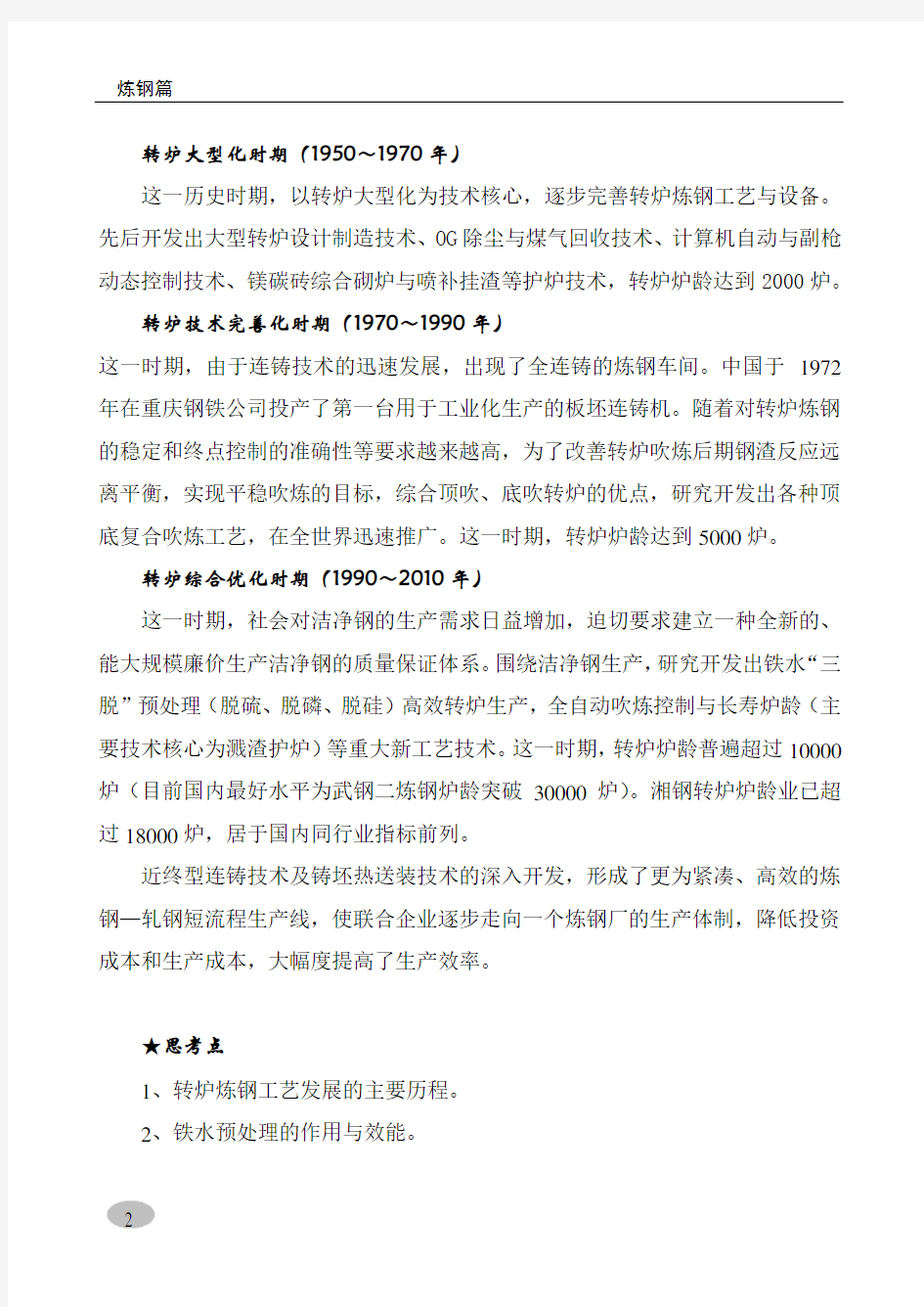
1 炼钢工艺发展概述
亨利·贝塞麦于1855年发明了酸性空气底吹转炉炼钢法,首次解决了用铁水冶炼液态钢的问题,使得炼钢生产的质量、产量实现了跨越性质的提高。相隔10年之后,法国人马丁利用蓄热池原理发明了平炉炼钢法。由于平炉炼钢法适应于各种原材料条件(铁水和废钢可用任何比例),平炉炼钢法长期占居炼钢工艺主导地位,平炉钢占全世界总产钢量的80%以上。湘钢在1999年以前一直处于这种局面:平炉—→模铸—→初轧开坯—→模列式轧机—→普通线材,采用多火成材工艺,成本消耗偏高,多项技术经济指标在全国冶金行业内排名一直靠后。
1940年代,大型空气分离机问世后,能够提供高纯度、大量廉价的氧气,随后诞生了氧气顶吹转炉。1952年在奥地利林茨城和1953年在多纳维茨城先后建成了30吨的转炉车间并投入工业生产。由于转炉生产率高,成本低,质量较高,投资低于平炉,便于实现自动化,因此在世界上发展迅速,并逐步取代了平炉。
回顾二炼钢厂自1996年8月1#转炉投产以来的发展进程及其对于湘钢的生存环境所带来的影响,也印证了这一规律。
自从20世纪开始发展电炉炼钢,该工艺长期以来一直作为熔炼特殊钢和高合金钢的方法。由于质量要求很高和市场需求巨大,伴随电力工业技术进步和供电能力提高,采用超高功率电弧炉和炉外精炼技术已经成为国内外应用日益广泛的冶金生产方式。我国电力建设的大发展,电弧炉炼钢工艺也将逐步改变其目前状况。
氧气转炉炼钢工艺已成为目前世界上最为主要的炼钢方法,即使到21世纪的前期,转炉钢的生产比例仍将保持在60~70%。回顾50年氧气转炉炼钢发展史,可以划分为三个发展时期:
转炉大型化时期(1950~1970年)
这一历史时期,以转炉大型化为技术核心,逐步完善转炉炼钢工艺与设备。先后开发出大型转炉设计制造技术、OG除尘与煤气回收技术、计算机自动与副枪动态控制技术、镁碳砖综合砌炉与喷补挂渣等护炉技术,转炉炉龄达到2000炉。
转炉技术完善化时期(1970~1990年)
这一时期,由于连铸技术的迅速发展,出现了全连铸的炼钢车间。中国于1972年在重庆钢铁公司投产了第一台用于工业化生产的板坯连铸机。随着对转炉炼钢的稳定和终点控制的准确性等要求越来越高,为了改善转炉吹炼后期钢渣反应远离平衡,实现平稳吹炼的目标,综合顶吹、底吹转炉的优点,研究开发出各种顶底复合吹炼工艺,在全世界迅速推广。这一时期,转炉炉龄达到5000炉。
转炉综合优化时期(1990~2010年)
这一时期,社会对洁净钢的生产需求日益增加,迫切要求建立一种全新的、能大规模廉价生产洁净钢的质量保证体系。围绕洁净钢生产,研究开发出铁水“三脱”预处理(脱硫、脱磷、脱硅)高效转炉生产,全自动吹炼控制与长寿炉龄(主要技术核心为溅渣护炉)等重大新工艺技术。这一时期,转炉炉龄普遍超过10000炉(目前国内最好水平为武钢二炼钢炉龄突破30000炉)。湘钢转炉炉龄业已超过18000炉,居于国内同行业指标前列。
近终型连铸技术及铸坯热送装技术的深入开发,形成了更为紧凑、高效的炼钢—轧钢短流程生产线,使联合企业逐步走向一个炼钢厂的生产体制,降低投资成本和生产成本,大幅度提高了生产效率。
★思考点
1、转炉炼钢工艺发展的主要历程。
2、铁水预处理的作用与效能。
2基本知识
2.1钢和生铁
钢和生铁都是铁和碳组成的合金,同属于黑色金属,但其性质有明显的区别:生铁硬而脆,焊接性差;而钢的强度和塑性、韧性等可以在很宽的范围内予以调整,可以进行焊接、轧制和加工成各种形式的产品。
钢和生铁的性能之所以不同,主要是由于碳和其他合金元素的含量不同。通常以含碳量1.7%作为钢和生铁的区分界限:含碳量1.7~4.5%的铁碳合金叫做生铁;含碳量低于1.7%的铁碳合金叫做钢。
生铁主要是由高炉冶炼,分为炼钢生铁、铸造生铁及合金生铁三种。
★思考点
1、钢和铁的区别。
2、叙述钢和铁各自的性能差异。
2.2铁水炉外脱硫
铁水预处理是指铁水进入炼钢炉之前所进行的某种处理,它可以分为普通铁水和特殊铁水的预处理。普通铁水预处理有脱硫、脱硅、脱磷和同时脱磷脱硫等;特殊铁水预处理有脱铬、提钒、提铌和提钨等。
以前炉外处理是作为避免出现号外铁水的补救措施。由于它在技术上合理和经济上优越,逐渐演变为当今用于扩大原材料来源,提高钢材质量,拓宽品种结构和提高技术经济指标的必要生产手段。现代铁水预处理技术的日益成熟,已经构成现代化钢铁厂中的重要组成部分。
炉外脱硫的基本原理是使用与硫的亲合力比铁大的元素或化合物,加入铁水
中以夺取硫化铁中的硫,使之转变为更为稳定的、极少熔解或完全不溶于铁液的硫化物。铁水脱硫的条件比钢水优越得多,脱硫效果比钢水炉外脱硫高约4~6倍,其原因是:铁水当中碳、硅、磷等元素含量高,使硫在渣中的活度系数提高,铁水中含氧量低,有利于脱硫反应的进行。
铁水脱硫剂有碳化钙(CaC2)、氰氨化钙(CaCN2)、石灰(CaO)、苏打粉(Na2CO3)、金属镁等,还有以它们作为主要成份的各种复合脱硫剂。我厂目前使用的铁水脱硫剂为钝化颗粒镁,其中镁的含量大于92%。
按照脱硫剂与铁水之间的混合搅拌方式,铁水炉外脱硫大致可以分为如下几类:
1、铁流搅拌式:它靠铁水流的冲击使铁水与脱硫剂混合搅拌。其优点是设备简单,容易操作,但搅拌不均,混合不充分,因而脱硫效率低,稳定性差。适宜于设备简陋、铁水含硫量高的小钢铁厂。
2、机械搅拌式:靠沉入铁水中的搅拌器或铁水容器运动使铁水与脱硫剂搅拌混合。搅拌时间和搅拌强度均可控制,此方法需要一定的设备,但脱硫效率高,属于这种方式的有摇包法、KR法等,多用于大型钢铁厂。
3、喷吹气体搅拌式:把氮气、氩气、压缩空气等吹入铁水,或者作为运载气源吹入铁水,使铁水与脱硫剂搅拌混合。此类方法具有操作灵活、控制方便、搅拌效果好、脱硫效率高、处理铁水能力大等优点,很适合用于大型钢铁厂。
4、钟罩插入式:靠镁蒸汽从钟罩孔逸出搅动铁水,使铁水与脱硫剂混合。
5、涡流搅拌式:靠电磁搅拌器或涡流装置搅动铁水,使铁水与脱硫剂混合。
目前许多钢厂仍在不断探索,试图研制出新的铁水脱硫方法和廉价、高效率、少污染环境的新脱硫剂。此外还研究适应铁水脱硫使用的高寿命耐火材料,以及脱硫渣的处理和综合利用。
必需指出:渣中的硫含量是铁水中硫含量的1000倍以上。此外,铁水渣的酸性成份影响转炉冶炼终点命中率,降低炉龄。因此,兑入转炉的高炉铁水要实
行扒渣处理,铁水带渣量不得超过0.5%。此外,对于硫含量较高的铁水实施炉外预处理,减轻转炉脱硫负担,不但简化了脱硫操作,而且有利于提高脱硫效果和转炉技术经济指标。但它毕竟增加了炼铁和炼钢之间的工艺环节和操作。当铁水含硫量不高而钢种成份又要求较宽时,无需进行预处理。
★思考点
1、铁水预处理包括哪些工艺流程。
2、经过预处理的回收渣铁对转炉冶炼有何危害?
3、我厂选择喷吹镁粉脱硫的现实意义。
2.3 炼钢的基本任务
1、脱碳。将生铁中的碳大部分去除,同时随着碳的氧化,2C+O2→2CO↑,在CO气体的排出过程中,同时脱除[H]、[N]。
2、去除杂质。生铁中[S]、[P]含量高,而钢中[S]会造成钢的“热
脆”;[P]造成“冷脆”。通常钢中[S]、[P]愈低愈好。炼钢必须脱除[S]、[P]等有害杂质。
3、升温。铁水温度一般在1250~1350℃,而钢水的出炉温度一般在1600℃以上,才能顺利进行铸锭或铸坯工作。因此炼钢过程也是一个升温过程。
4、合金化。在冶炼过程中,生铁中的[Si]、[Mn]等元素大部分氧化掉了。为了保证成品钢中的规定成份,要向钢水当中加入各种合金元素。
5、脱氧。在炼钢后期钢中氧含量增加,为了将过多的氧去除,就必须完成“脱氧”工作。
2.4 熔渣的性质
炼钢熔渣的性质对炼钢生产的技术经济指标有巨大的影响。熔渣的性质是熔渣结构的外部特征,它包含物理性质和化学性质。化学性质包括碱度和氧化能力。在熔池为碱性的炼钢炉中,炉渣是碱性的,它具有较强的去除[P]和[S]的能力。通常的顶吹转炉炉渣大约有35~45%(CaO),60~65%(CaO+MgO+MnO),5~25%(FeO)和20~25%(SiO2+P2O5+Al2O3)。CaO是含量最多而且碱性又最强的氧化物,SiO2是含量最多而且酸性最强的氧化物,CaO 、SiO2和P2O5三者的含量对炉渣的酸碱性从而对炉渣的去P和去S能力起决定性的作用。炉渣碱度及R常用CaO和SiO2含量的比值来表示:
R=(% CaO)/(% SiO2)
顶吹转炉冶炼过程中R值通常波动在1.5~4.0范围内。
炼钢熔渣的物理性质通常包括如下几点:
①导电性。主要受熔渣的成分和温度影响。
②导热性。炉渣的导热性显著低于金属。
③密度。炉渣密度通常波动在2800~3200kg/m3范围内,温度升高则密度降低,当其中(FeO)和(MnO)增加时密度增大。
④粘度。炉渣粘度是影响炼钢熔池中各类扩散过程的重要因素,受成份和温度的影响很大。由于炼钢熔渣属于多相物质,粘度随碱度的提高而增大。因此提高熔池温度和加入可使炉渣熔点降低的熔剂(如矿石、萤石等)可以降低炉渣粘度。
⑤表面张力。熔渣的表面张力与熔渣的泡沫化、渣—钢之间的乳化、脱氧产物及夹杂物的凝聚上浮、炉衬的侵蚀等冶炼过程多相反应都有重要关系。
2.5 转炉炼钢过程中杂质去除反应
在通常的氧气转炉炼钢过程中,总是要将C、Si、Mn、P、S去除到钢种规定的要求。
溶解在钢液中的碳和氧按如下两个反应进行氧化:
[C]+[O]={CO}
[C]+2[O]={CO2}
[CO2]+[C]=2{CO}
前一反应是钢冶金中最基本的脱碳反应,后一反应在碳氧化中占的比重只是在[%C]<0.05的情况下比较显著,在[%C]>0.1的情况下占的比重很小。
在顶吹转炉中,Si和Mn在吹炼初期进行强烈氧化。Si与O的亲合力显著大于Mn,故Mn的强烈氧化期滞后于Si。Si和Mn的氧化是在钢—渣界面上进行的,属于典型的多相反应,由如下两个环节组成:
(1)渣中氧化铁溶解到金属中(FeO)=[O]+[Fe]
(2)在钢—渣界面上进行Si和Mn的氧化反应
[Si]+2[O]=(SiO2)
[Mn]+[O]=(MnO)
[Mn]+(FeO)=(MnO)+[Fe]
磷的氧化由以下环节组成:
(1)在渣钢界面上5(FeO)=5[Fe]+5[O]
(2)在与渣相邻的金属层中2[P]+5[O]=(P2O5)
(3)在与金属相邻的渣层中(P2O5)+4(CaO)=(4 CaO·P2O5)
总反应式为:2[P]+5(FeO)+4(CaO)=(4 CaO·P2O5)+5[Fe]
铁水含硅量对磷的氧化过程有重要影响:铁水含硅量高,不但要夺取供入熔池的更多的氧,而且也提高了渣中SiO2的活度,并且阻碍石灰的熔解。
脱硫则主要是依靠硫向炉渣的转移。在金属与碱性炉渣接触的情况下,各种脱硫方法的实质可以归结为:使金属中的硫生成在金属液中溶解度很小而能转移入炉渣的硫化物。其在渣相中的反应可以描述为:(RO)+[FeS]=(RS)+(FeO)CaO是RO中最强的脱硫剂之一,MnO是弱脱硫剂,铁水中含[Mn]较高对转炉炼钢过程中的脱硫反应有促进作用。
★思考点
1、叙述炼钢的基本任务。
2、熔渣有哪些物理性质。
3、转炉如何脱磷?
4、转炉如何脱硫?
3炼钢原材料
氧气转炉炼钢常用的主要原料有:铁水、废钢、冷却剂、造渣剂、铁合金、氧气等。
3.1 入炉废钢
对入炉废钢的要求主要有以下几个方面:
1、块度和重量。为保证废钢顺利加入并及时熔化,同时减轻废钢对炉衬的冲击力,确保炉衬寿命,废钢不能过大、过重。
2、成份。废钢成份越单纯越好,因此当废钢成份复杂时,必须加强管理,
以免对产品质量造成不利影响。
3、不允许夹带密闭容器和爆炸物。
4、不得夹有铜、铅、锌、锡等有色金属及橡胶。钢中Cu>0.3%时容易在热加工时产生裂纹;铅的比重很大,沉积之后会损坏炉底,甚至造成漏钢事故;锌蒸发时生成ZnO,会影响烟气回收设备的使用寿命;橡胶则含[S]量高,对钢水质量造成危害。
5、废钢必须保持清洁、干燥,防止装炉时发生爆炸事故。
3.2 造渣材料
3.2.1 石灰
转炉开吹以后,铁水中的Fe、Si、Mn、P等元素被氧化,生成FeO、SiO2、MnO、P2O5等氧化物,形成炉渣。这些氧化物中的SiO2、、P2O5等是酸性氧化物,Fe2O3、Al2O3等是弱酸性氧化物,FeO、MnO是碱性氧化物,因此必须加入石灰造渣,否则会造成下列情形:
1、炉衬侵蚀严重。炉渣中大量的氧化物都呈游离状态存在,当与炉衬中CaO、MgO等碱性物质作用,生成低熔点化合物,在机械冲刷下进入渣中,炉衬被侵蚀破坏。
2、影响有害元素P、S的去除。铁水中P被氧化后生成不稳定的3FeO·P2O5,在高温下容易分解,磷又返回到钢液当中,必须加入足够的石灰去除[P]。硫在冶炼过程中以FeS、MnS、CaS等形式存在,且能够同时溶于渣中,因此,加入足量的石灰,可以使硫化物从钢中转移到渣中,达到从钢中去硫目的。
3、高压氧气流股吹入熔池,会产生严重的金属喷溅,造成金属损失,同时容易造成氧枪烧损,影响炼钢进程。必须保证有一定厚度的渣层覆盖金属液面。
基于上述原因,在开吹后,必须加入适当数量的石灰进行造渣。
我国顶吹转炉石灰质量标准:
石灰本身的物理性质,如体积密度、气孔率、比表面积和晶粒度大小等对石灰熔解速度有重要影响。体积密度小,气孔率高,比表面积大、晶粒细小的活性石灰熔解速度快,反应能力强。这种优质冶金石灰能够提高转炉的生产能力,减少石灰、萤石消耗量和转炉渣量,脱磷、脱硫效果好,减少转炉热损耗,提高炉龄,并且能够提高钢水质量。
石灰是由碳酸钙沉积岩锻烧而成,其反应方程式为:
CaCO3CaO+CO2↑
3.2.2 萤石
萤石的主要成份是CaF2,它的熔点很低,约为930℃。萤石能够使CaO和阻碍石灰熔解的2CaO·SiO2外壳的熔点显著降低,加速石灰熔解,迅速改善炉渣流动性。萤石助熔的特点是作用快、时间短,但大量使用萤石会增加喷溅,加剧炉衬的侵蚀。
3.2.3 白云石
生白云石的主要成份为CaCO3+ MgCO3。近年来国内外氧气转炉采用生白云石或者轻烧白云石代替部份石灰造渣的技术得到广泛应用和发展。大量生产实践证明:采用白云石造渣对减轻炉渣对炉衬的侵蚀,提高炉衬寿命具有明显效果,此外,白云石还有利于促进石灰熔解。转炉用的白云石,对MgO含量有一定要求并具有合适的块度。
3.3 氧气
氧气是转炉炼钢的主要氧源。现代炼钢工业用氧是由空气经氧、氮分离后制取的。氧气纯度应≥99.5%,氧气应脱除水份和肥皂液。
3.4 增碳剂
转炉炼钢常用的增碳剂有焦炭和沥青焦等,沥青焦的质量优于焦炭。
对增碳剂要求其固定碳要高而且稳定,杂质要低,清洁、干燥。
3.5 脱氧剂
我厂常用的脱氧剂有硅铁、锰铁、硅锰和复合脱氧剂如硅钙钡合金、硅铝钡合金、铝锰铁合金等。这些脱氧剂具有如下特点:
与氧的亲和力比铁大,在钢液中扩散的速度快;脱氧产物不溶于钢液且容易上浮;当加入量过大时残留在钢液中的余量对钢质无害;有合适的块度并保持清洁、干燥,不得混有其他杂物。
复合脱氧剂的脱氧效果优于单一脱氧剂。
★思考点
1、转炉用冶金石灰的成份及性能要求。
2、铁水及废钢必须达到哪些要求。
3、白云石和萤石有哪些作用?
4转炉炼钢工艺
4.1 装入制度
目前国内外顶吹氧气转炉装入制度主要有三种:
4.1.1 定量装入
在整个炉役期间,保持每炉的金属装入总量不变。这种操作方法优点是生产组织简便,能更好地实现过程自动化。
4.1.2 定深装入
这是在一个炉役期内保持每炉的金属熔池深度不变。其优点是氧枪操作稳定,有利于氧气射流在最佳工况下工作,也可充分发挥转炉的生产能力。但这种方法将使装入量及出钢量变化频繁,铁水调度及钢水浇铸都很难配合。
4.1.3 分阶段定量装入
综合上述两种方法的优点,针对炉役不同阶段实行定量装入,这样大体上保持了比较适当的熔池深度,也保持了装入量的相对稳定性。在稳定操作的前提下,充分发挥转炉的生产潜力,既能满足冶炼工艺的要求,又便于组织生产。我厂目前采用这一制度。
目前我厂生产时存在铁水供应不足的矛盾,必须依靠增大废钢比例予以缓解。应当注意在兑完铁水后,应将炉子倒向后侧(即兑铁的相反一侧)使废钢摊平,否则废钢极有可能贴在装料侧的炉衬上,在吹氧后期有可能化不完而留下来,温度低于正常炉次,造成废钢熔化过晚以及倒炉时沸腾。
4.2 供氧制度
供氧是氧气顶吹转炉炼钢最重要的操作,是控制整个吹炼过程的主导因素,
并直接影响冶炼效果和钢的质量。它是保证杂质去除速度、熔池升温速度、造渣速度,控制喷溅和去除钢中气体与夹杂的关键操作。
理论推算,每吨金属所需氧量一般为45~55Nm3。
供氧制度是使氧气流股合理地供给熔解池,创造良好的氧气流股和熔池的物理、化学反应条件。因此,供氧制度的内容包括确定合理的氧枪喷嘴结构,便于在实际生产中调节和控制供氧强度,供氧压力和喷枪高度。合理的供氧制度主要应当根据转炉容量、铁水成份、冶炼钢种等诸多方面统筹确定。
喷头结构确定以后,在一定氧压、氧流量条件下,必须通过合理调节喷枪高度才能获得良好的吹炼指标。而在一炉钢冶炼过程中的枪位要根据铁水成份、温度、炉型、辅助材料及废钢等情况,以及上几炉吹炼枪位及吹炼情况,考虑本炉次冶炼品种等因素确定。
吹炼前期:关键是化好头批渣料。一般要求在3分钟左右化好初期渣,然后将枪压至过程吹炼的高度。头批渣化不好,易导致中期“返干”严重,但头批渣料也不应化得太早、太泡,否则会产生泡沫渣喷溅。
吹炼中期:此段枪位是否合适,直接影响吹炼过程能否顺利进行。
吹炼后期:若铁水含P较高,过程渣子化得不好,“返干”严重,或冶炼中、高碳钢,在终点降枪前要提枪,以保证提高炉渣氧化性,提高渣子流动性,增强炉渣去P效果。
目前,转炉的最佳枪位还难于用计算确定,基本上是凭经验控制。生产上采用的枪位(H,毫米)是以喷头与平静熔池液面的距离来表示,而不考虑实际熔
毫米)的经验计池面的波动。从生产中得到的枪位(H)与喷头喉口直径(d
喉,
算式为:
H=(35~50)*d喉
生产过程中影响枪位控制的因素很多。通常,铁水含硅高,易喷溅,枪位应较低;铁水含硅量低,为了化渣,枪位可适当提高。铁水磷高,应适当提高前期
化渣枪位,以便形成脱磷所需足够的(FeO)。铁水温度低,开吹时应适当降枪提温。反之,则在吹炼前期适当提高枪位,以利化渣。熔池越深,相应渣层越厚,吹炼过程中熔池面上涨越高,为了化渣和避免喷溅,枪位应适当降低。冶炼中、高碳钢时,由于脱磷困难,应采用较高的枪位,尤其是在吹炼后期,在终点前要略微提枪或加入萤石造成泡沫化强、流动性好的炉渣。
4.3 造渣制度
氧气转炉炼钢的冶炼时间很短,因此必须做到快速成渣,使炉渣尽快具有合适的碱度、氧化性和流动性,以便迅速把金属中磷、硫等杂质去除到所炼钢种规格的要求以下。避免炉渣溢出和喷溅,以减少原材料和金属损失,保护炉衬,提高炉衬寿命。
炉渣粘度必须满足冶炼过程的需要:前期要防止炉渣过稀;中期渣粘度要适当;末期炉渣要化透做粘,同时便于溅渣操作。
使用白云石造渣容易出现炉底上涨和粘枪现象。炉底上涨是由于渣况恶化,炉渣中MgO含量过高,炉渣粘度大。粘枪则是由于炉渣粘度大而且形成喷溅造成的。避免炉底上涨和粘枪的关键在于确定合理的白云石加入量,其次是控制好炉渣粘度。
转炉造渣的关键是加速石灰的熔化。在顶吹转炉无后吹的情况下,入炉的石灰的熔化量极少超过80~85%。因此,加速石灰熔化对转炉冶炼有重要意义。
石灰熔化是复杂的多相反应,伴随有传热、传质及其他物理化学过程,可分为三步:
第一步:液相炉渣经过石灰块外部扩散边界层向反应区扩散,并沿气孔向石灰块内部迁移。
第二步:炉渣与石灰在反应区进行化学反应并形成新相,反应在石灰块外表
面及内部气孔表面同时进行。
第三步:反应产物离开反应区向炉渣熔体中转移。
吹炼初期,通常枪位比较高,铁水中的Si、Mn、Fe等元素氧化生成SiO2、MnO、FeO进入炉渣。由于Fe的氧化,使碱度很低的炉渣中氧化铁逐渐提高并促进石灰的熔化。开吹时,渣量的增加主要来源于铁水中Si、Mn、Fe的氧化物,而随后则主要来源于石灰的熔化。此时石灰的熔化速度很快,炉渣温度也比金属熔池温度高约200~300℃,并很快开始形成液滴—炉渣乳化液。
在吹炼中期,通常枪位下降,脱碳反应加速,渣中(FeO)逐渐降低,吹炼中期炉温已较高,石灰进一步熔化,但熔化的速度有所减缓。随着脱碳反应的进行,炉渣泡沫化程度迅速提高。吹炼中期能够最大限度的产生泡沫,并有溢出炉外的趋势。由于脱碳反应大量消耗渣中的FeO,以及有时得不到超过炉渣液相线的正常过热度,导致化渣条件恶化,引起炉渣异相化并出现“返干”现象。
在吹炼末期,脱碳反应速度下降,渣中(FeO)含量再次提高,石灰继续熔化并加快了熔化速度。随着脱碳速度的进一步下降,熔池中的乳化和泡沫现象减
弱并趋于消失。一炉钢吹炼过程中所形成的总渣量可达到金属量的10~16%。
2.14[%Si]
*1000*82(t/炉)
石灰加入量计算公式:W= ——————*R
碱度
(%CaO)有效
在生产实践中,一般根据铁水成份和所炼钢种来确定造渣方法。常用的造渣方法有单渣法、双渣法和双渣留渣法。
1、单渣法。在冶炼过程中只造一次渣,中途不出渣。当铁水中Si、P、S含量较低,钢种对P、S要求不高,或者吹炼低碳钢时,都可以采用单渣操作。单渣操作工艺较为简单,冶炼时间短,劳动条件好。
2、双渣法。在吹炼中途分一次或几次除去约1/2~2/3的炉渣,然后重新加渣料造新渣的操作方法称双渣法。在铁水含硅量较高或含磷量大于0.150%,或者虽然含磷量不高但吹炼优质钢,或吹炼中、高碳钢种时一般都采用双渣操作。其
优点是可以在炉内保持较少的渣量,同时又能获得较高的去除磷、硫的效率,可以消除大渣量引起的喷溅,减轻对炉衬的侵蚀,同时又能减少石灰消耗量。选择掌握倒渣时间是双渣法操作的关键。
3、双渣留渣法。将上炉终点炉渣部分或全部留在炉内供下炉使用的造渣方法称为双渣留渣法。终渣一般有较高的碱度和(FeO)含量,而且温度高,它对铁水具有一定的去磷和去硫能力。这种炉渣留在炉内可以改善下炉吹炼初期的操作,加速初期渣的形成,提高炉子热效率,对于冶炼中、高碳钢具有极大适用价值。
在留渣操作时必须稠化炉渣,防止爆发性喷溅发生安全事故。
通常顶吹转炉渣料多采用分批加入。头批渣料在开吹时加入,加入量为渣料总量的1/2,剩余渣料提倡多批少量加入,且应当控制在供氧时间1/2~2/3前加完。矿石必须在终点前二分钟加完。
★思考点
1、供氧制度的工艺依据。
2、转炉冶炼过程枪位控制要求。
3、造渣方式及其选择依据。
4、转炉造渣的途径及其特点。
4.4 温度控制、终点控制和出钢
4.4.1温度控制
温度控制主要指吹炼的过程温度和终点温度的控制。转炉温度控制的目标是吹炼过程中均衡地升温,吹炼终点时钢水的温度和化学成份同时命中钢种要求的范围。它的内容包括:确定合适的钢种出钢温度,确定熔池富余热量的数值,选择冷却剂并确定其冷却效果和加入量,掌握影响熔池温度变化的因素,及进行温
度控制操作等。
过程温度控制的基本点是:
1、满足快速造渣的需要,保证尽快形成成份和性质符合要求的炉渣;
2、满足去除磷、硫和其它杂质的需要,在特殊情况下还应当满足从金属中提取某些有利元素,同时保留另一些有利元素的要求;
3、满足吹炼过程平稳和顺行的要求。在吹炼的前、中期特别是强烈脱碳期,温度过高或过低都容易产生喷溅;
4、协调熔池的升温和脱碳速度,满足准确控制终点的要求。
4.4.2终点控制
终点控制是转炉吹炼后期的重要操作,主要指终点成份和温度的控制,还包括所有影响钢水的转炉吹炼末期的操作因素和工艺措施的控制。
“拉碳法”和“增碳法”是两种常用的经验控制吹炼终点的方法。
“拉碳法”是指熔池碳含量达到出钢要求时停止吹氧。此时熔池中不但硫、磷和温度符合出钢要求,钢水中的碳也能符合所炼钢种的规格要求。“拉碳法”又分为一次拉碳和高拉一次补吹两种操作。后者是指比出钢含碳量高0.06~0.30%C时停止吹氧,倒炉并取样,再视钢水状况一次补吹后出钢。高拉碳时熔池温度不应高于终点规定温度的上限。
“拉碳法”具有以下优点:
1、终点(FeO)含量较低,金属收得率较高;
2、终点钢水含锰量较高,合金消耗少;
3、钢水含氧量较低,钢中非金属夹杂含量较少;
4、钢中氢和氮含量较低,氧气消耗量少。
“增碳法”是指吹炼平均含碳量≥0.08%的钢种时,均采用吹到0.05~0.06%C 时停吹,然后按照所炼钢种,在钢包内增碳。它具有如下特点:
1、终点容易命中,比“拉碳法”省去中途倒渣、取样、校正成份及温度的
补吹时间,因而生产率高;
2、吹炼结束时炉渣(FeO)含量高,化渣较好,去磷率高,吹炼过程的造渣操作可以简化,有利于减少喷溅,提高供氧强度和稳定吹炼工艺。
3、热量收入较高,有利于增加废钢用量。
4.4.3出钢
国家规范规定:≥50吨的转炉出钢持续时间为3~6分钟。我厂钢包烘烤及管理措施较为完善,已经完全能够做到“红包”出钢。从而为减少温度损失,提升铸机作业稳定水平和产品质量提供了可靠保证。
出钢挡渣已成为一项成熟稳定的工艺技术,目前我厂钢水缶内渣厚H<100mm的炉次比率已经超过90%。这一技术措施的推行,有利于准确控制钢水成份;防止钢水回磷;提高合金收得率;减少钢中夹杂物含量;并且显著地延长钢包寿命。
4.5 脱氧合金化
在转炉吹炼过程中,由于不断向金属熔池吹氧,使吹炼终点金属中残留一定数量的溶解氧,因此在吹炼结束以后,钢必须脱氧,否则就不能顺利浇注,也不能得到结构合理的钢锭。原因在于:
1、氧在钢中的溶解度随温度的降低而减少。同进,钢水在凝固过程中,由于选分结晶的结果,使钢水中[O]、[C]发生偏析而浓聚,引起碳的再次氧化,这会降低钢中的碳含量。另一方面使产生的CO气体有相当部分残留在钢坯内部,破坏了钢坯结构,严重时甚至造成钢水产生沸腾甚至不能浇注。
2、氧在液态钢中溶解度较大,而在固态钢中溶解度很小。钢在冷凝过程中氧将以氧化物析出,分布于晶界上,降低钢的机械性能和特种用途钢的某些性能。
3、钢坯中氧使硫的危害作用加剧,因为FeO与FeS可以生成低熔点共晶物,
使钢在轧制时产生“热脆”。
掌握终点钢水含氧量的定量数据及其变化规律是正确进行脱氧操作的前提。钢中含氧量变化呈如下规律:
1、一般情况下,钢中的含氧量主要受含碳量控制。其变化趋势为:含碳量高则含氧量低,含碳量低时含氧量高。
2、在[C]>0.06%的情况下,实际熔池中碳—氧反应没有达到平衡,钢中实际
含氧量高于碳平衡的含氧量,其差值△[O]=[O]
实际——[O]
碳平
为金属的过剩氧浓
度。
3、在钢中含碳量比较高时,含氧量受含碳量控制。但在含碳量极低的情况下,△[O]有可能出现负值。出现这种变化的原因:主要是含碳量极低时,顶吹转炉熔池搅拌微弱,一次反应区中的碳、氧含量和二次反应区有显著不同。
各类钢的脱氧程度有重要的不同。为了顺利进行脱氧,应该控制好供氧,造渣和终点操作,以期获得需要的钢水氧化性。
向钢中加入一种或几种合金元素,使其达到成品钢成份规格要求的操作过程称为合金化。实际操作多数情况下,脱氧和合金化是同时进行的,脱氧元素收得率受多种因素的影响,主要取决于脱氧前钢水含氧量,终渣氧化性和元素本身的脱氧能力。钢水含氧量越高,终渣氧化性越强及元素脱氧能力越强,则该元素的烧损率越大,收得率越低。在生产条件下,凡是影响终点钢水和炉渣氧化性的因素,在确定脱氧剂加入量时都必须予以考虑。例如:用:“拉碳法”吹炼中、高碳钢时,终点钢水含碳量高氧化性低,脱氧元素烧损少,收得率高。如果钢水温度偏高,则收得率更高。反之,吹炼低碳钢时收得率低。
加入钢中的脱氧剂一部分消耗于钢的脱氧,转化为脱氧产物排出,另一部分则为钢水吸收,起合金化作用,而加入钢中的大多数合金元素,因为其与氧的亲合力比铁强,也必然起一定的脱氧作用,因此实践中脱氧与合金化并非孤立的概念。
[%E]中限—[%E]残余
合金加入量计算方法:W= ————————*出钢量*1000
[%E]合金*η收得率
各类合金应在出钢至1/4左右时开始加入,到2/3左右时加完,注意控制好终点钢水和炉渣氧化性,出钢时尽量少下渣,以便稳定和提高合金收得率。
★思考点
1、什么是终点控制?包括哪些要求?
2、拉碳法和增碳法的优点。
3、过程温度控制的基本要求。
4、为何要挡渣出钢。
5、简述P、S对钢材性能的危害。
6、计算一炉钢的合金加入量。
炼钢工艺的发展历程
炼钢工艺的发展历程 2008年12月8日摘自冶金自动化网 炼钢方法(1) 最早出现的炼钢方法是1740年出现的坩埚法,它是将生铁和废铁装入由石墨和粘土制成的坩埚内,用火焰加热熔化炉料,之后将熔化的炉料浇成钢锭。此法几乎无杂质元素的氧化反应。 炼钢方法(2) 1856年英国人亨利·贝塞麦发明了酸性空气底吹转炉炼钢法,也称为贝塞麦法,第一次解决了用铁水直接冶炼钢水的难题,从而使炼钢的质量得到提高,但此法要求铁水的硅含量大于0.8%,而且不能脱硫。目前已淘汰。 炼钢方法(3) 1865年德国人马丁利用蓄热室原理发明了以铁水、废钢为原料的酸性平炉炼钢法,即马丁炉法。1880年出现了第一座碱性平炉。由于其成本低、炉容大,钢水质量优于转炉,同时原料的适应性强,平炉炼钢法一时成为主要的炼钢法。 炼钢方法(4) 1878年英国人托马斯发明了碱性炉衬的底吹转炉炼钢法,即托马斯法。他是在吹炼过程中加石灰造碱性渣,从而解决了高磷铁水的脱磷问题。当时,对西欧的一些国家特别适用,因为西欧的矿石普遍磷含量高。但托马斯法的缺点是炉子寿命底,钢水中氮的含量高。 炼钢方法(5) 1899年出现了完全依靠废钢为原料的电弧炉炼钢法(EAF),解决了充分利用废钢炼钢的问题,此炼钢法自问世以来,一直在不断发展,是当前主要的炼钢法之一,由电炉冶炼的钢目前占世界总的钢的产量的30-40%。 炼钢方法(6)
瑞典人罗伯特·杜勒首先进行了氧气顶吹转炉炼钢的试验,并获得了成功。1952年奥地利的林茨城(Linz)和多纳维兹城(Donawitz)先后建成了30吨的氧气顶吹转炉车间并投入生产,所以此法也称为LD法。美国称为BOF法(Basic Oxygen Furnace)或BOP法, 如图1所示。 图1 BOF法 炼钢方法(7) 1965年加拿大液化气公司研制成双层管氧气喷嘴,1967年西德马克西米利安钢铁公司引进此技术并成功开发了底吹氧转炉炼钢法,即OBM法(Oxygen Bottom Maxhuette) 。1971年美国钢铁公司引进OBM法,1972年建设了3座200吨底吹转炉,命名为Q-BOP (Quiet BOP) ,如图2所示。 图2 Q-BOP法 炼钢方法(8) 在顶吹氧气转炉炼钢发展的同时,1978-1979年成功开发了转炉顶底复合吹炼工艺,即从转炉上方供给氧气(顶吹氧),从转炉底部供给惰性气体或氧气,它不仅提高钢的质量,而且降低了炼钢消耗和吨钢成本,更适合供给连铸优质钢水,如图3所示。 图3 转炉顶底复合吹炼法 炼钢方法(9) 我国首先在1972-1973年在沈阳第一炼钢厂成功开发了全氧侧吹转炉炼钢工艺。并在唐钢等企业推广应用,如图4所示。
炼钢工艺
炼钢工艺 一、工艺流程图 二、炼钢主要设备 1、公称容量35吨氧气顶吹转炉2座,配35吨钢水包; 2、公称容量600吨混铁炉1座; 3、R6000m连铸机2台,6机6流 三、转炉炼钢用原材料 1主要原料:炼钢用生铁(铁水、铁块)、废钢;
2辅助材料:辅助材料有:增碳剂、脱氧剂、覆盖剂、保护渣等。3造渣剂:石灰、轻烧镁球、石灰石 4铁合金:硅铁、硅锰、锰铁、铝线等。 四、冶炼 1、氧气顶吹转炉的反应 氧气顶吹转炉炼钢的反应过程是氧化反应,反应的机理是物理化学反应,物理化学反应就是在反应的过程中同时进行吸热和放热反应。即是氧化反应就需要氧气,用氧气完成炼钢的一切反应,主要反应是与硅、锰、碳、磷、硫的氧化反应,这些反应都是放热反应,在反应的过程中提高钢水温度,直到满足连铸浇注温度要求。 2、氧气顶吹转炉的生产特点 由于氧气流股的强大动力,将钢和渣击碎,形成液滴,成为球状,球状的表面积最大,炼钢反应又是界面反应,因此反应速度高,冶炼时间短,吹眼时间10~11分钟,冶炼周期25分钟,由此看出氧气顶吹转炉的最大特点是生产效率高。 3、供氧 氧气顶吹转炉通过氧枪向炉内熔池供氧,氧枪喷头由收缩段、过渡段和扩张段构成拉瓦尔喷管,喷头前氧气流股的流速是超音速的,因此具有很强的穿透力,能够将炉内钢水与炉渣充分搅拌起来,形成乳化液,扩大了氧、渣、钢间的反应面积,提高反应速度,降低了冶炼时间。冶炼时间的长短取决于供氧强度(单位时间的供氧量)和氧气纯度,因此要求氧气纯度>99.5%,氧气总管压力≥1.4M pa。 4、炼钢的任务 炼钢的任务是:脱碳脱硅脱气、去除磷硫、去除夹杂、保证温度、保证成分。 5、出钢 当吹氧结束,标志着冶炼结束,将炉中钢水出到钢水包中,进行
炼钢工艺学
冶2007-1、2班《炼钢工艺学》复习题(详见课本和笔记)2010.7.8 (授课教师:刘宇雁) 1.铁水预处理的“三脱”是指脱硅、脱磷、脱硫。 2.铁水预处理指铁水在兑入炼钢炉之前,为除去某种有害成分( 如S、P、Si等)或提取/ 回收某种有益成分(如V、Nb 等)的处理过程。或铁水在兑入转炉之前进行的脱硫、脱磷或脱硅操作。 3.铁水预处理目的及意义:主要是使其中硫、硅、磷含量降低到所要求范围,以简化炼 钢过程,提高钢的质量。 ?有效提高铁水质量;?减轻炼钢负担; ?为优化炼钢工艺,提高钢材质量创造良好条件; ?对特殊铁水预处理而言,可有效回收利用有益元素,实现综合利用。 4.铁水预脱硅技术的目的: ?减少转炉石灰耗量(硅氧化形成的SiO2大大降低渣的碱度),减少渣量和铁损,改善操作和提高炼钢经济技术指标。 ?铁水预脱P的需要,可减少脱磷剂用量、提高脱磷、脱S效率。 当铁水[Si]>0.15%时,脱磷剂用量急剧增大。因此,脱磷处理前需将铁水含[Si]脱至<0.15%,这个值远远低于高炉铁水的硅含量,也就是说,只有当铁水中的硅大部分氧化后,磷才能被迅速氧化去除。所以脱磷前必须先脱硅。 铁水预脱P的最佳[Si] : 初始 ①苏打脱P:[Si] 初始<0.1% ②石灰熔剂脱P:[Si] 初始0.10~0.15% ?对含V或Nb等特殊铁水,预脱Si可为富集V2O5和Nb2O5等创造条件。 5.铁水预脱硫技术迅速发展的原因: ?用户对钢的品种和质量要求提高。 ?连铸技术的发展要求钢中硫含量进一步降低,否则连铸坯容易产生内裂,铁水脱硫可满足冶炼低硫钢和超低硫钢种的要求。 ?铁水中碳、硅、磷等元素的含量高,可提高硫在铁水中的活度系数,而有利于脱硫,同时铁水中的氧含量低,没有强烈的氧化性气氛,有利于直接使用一些强脱硫剂,如电石(CaC2)、金属镁等;故铁水脱硫效率高。 ?铁水脱硫费用低于高炉、转炉和炉外精炼的脱硫费用。其费用比值为:高炉脱硫:铁水预处理脱硫:转炉:炉外精炼=2.6:1:16.9:6.10 ?降低炼铁和炼钢炉脱硫负担; 有利于降低消耗和成本,并增加产量。 ?提高炼铁和炼钢经济技术指标;有效提高钢铁企业铁、钢、材的综合经济效益。 全程脱硫:高炉-铁水炉外-炼钢炉(-精炼炉)→实现铁水深度脱硫,经济有效生产超低S高级优质钢; ?提高钢质、扩大品种、优化工艺(改善转炉炼钢操作); 6.铁水预脱硫优点(铁水脱硫条件比钢水脱硫优越的主要原因) 用优质铁水炼钢,是提高产品质量、扩大品种、增加效益和增强产品市场竞争力的重要条件之一,也是生产低硫洁净钢的基础。铁水炉外脱硫有利于提高炼铁、炼钢技术经济指标。通过比较各种脱硫工艺,铁水脱硫预处理工艺有如下优点: ?铁水中[C]、[Si]较高,fs↑,提高硫的反应能力; ?铁水中[O]较低,提高渣铁之间的硫分配比(Ls↑),脱硫效率高; ?搅拌充分,脱硫剂利用率高,脱硫速度快; ?铁水脱硫可提高炼铁炼钢的生产能力、节约工序能源、降低成本。
炼钢厂生产工艺的设备安全事故分类示范文本
文件编号:RHD-QB-K1052 (安全管理范本系列) 编辑:XXXXXX 查核:XXXXXX 时间:XXXXXX 炼钢厂生产工艺的设备安全事故分类示范文本
炼钢厂生产工艺的设备安全事故分 类示范文本 操作指导:该安全管理文件为日常单位或公司为保证的工作、生产能够安全稳定地有效运转而制定的,并由相关人员在办理业务或操作时进行更好的判断与管理。,其中条款可根据自己现实基础上调整,请仔细浏览后进行编辑与保存。 由于生产组织、工艺设备管理上的不完善,炼钢厂内经常会因为工艺、设备系统发生故障、隐患、事故而引发炼钢的安全事故。 例如: 1)“大喷”:由于工艺控制不合理,如:①低氧压操作;②渣子太稀时若兑入铁水,则炉内氧化反应过于激烈,发生“大喷”。“大喷”时若防护措施不当,可造成人员伤亡。 2)氧枪事故:卡抢、粘枪等设备事故,若处置不当,引发爆炸等严重的安全事故。
3)重大炉壁穿透事故:重大炉壁穿透事故可造成大量高温钢水泄漏。如20xx年2月25日下午1点20分左右,杭州钢铁集团转炉作业区发生重大炉壁穿透事故,造成大量高温钢水泄漏。作业区内的工人已经全部撤离,无人员伤亡。 4)煤气系统事故———泄漏:煤气系统由于存在转炉煤气这种高度危险物质,因而存在火灾、爆炸、急性中毒等重大安全事故的风险。从工艺、设备安全管理的角度分析,最常见的煤气系统事故隐患就是泄漏,由泄漏可引发上述安全事故。在我国冶金行业生产设备事故中,泄漏事故位居前列。 5)漏钢:在连铸生产中,漏钢常造成工人烫伤,漏钢不仅损坏设备、增加废品,还打乱了生产组织。粘结漏钢是连铸生产中出现最为频繁的一种漏钢事故。 6)转炉氧枪、烟道、烟罩等部位漏水引起爆
炼钢生产流程详细讲解
钢铁生产工艺主要包括:炼铁、炼钢、轧钢等流程。 (1)炼铁:就是把烧结矿和块矿中的铁还原出来的过程。焦炭、烧结矿、块矿连同少量的石灰石、一起送入高炉中冶炼成液态生铁(铁水),然后送往炼钢厂作为炼钢的原料。 (2)炼钢:是把原料(铁水和废钢等)里过多的碳及硫、磷等杂质去掉并加入适量的合金成分。 (3)连铸:将钢水经中间罐连续注入用水冷却的结晶器里,凝成坯壳后,从结晶器以稳定的速度拉出,再经喷水冷却,待全部凝固后,切成指定长度的连铸坯。 (4)轧钢:连铸出来的钢锭和连铸坯以热轧方式在不同的轧钢机轧制成各类钢材,形成产品。 炼钢工艺总流程图
炼焦生产流程:炼业是将焦煤经混合,破碎后加入炼焦炉经干馏后产生热焦碳及粗焦炉气之制程。
烧结生产流程:烧结作业系将粉铁矿,各类助熔剂及细焦炭经由混拌、造粒后,经由布料系统加入烧结机,由点火炉点燃细焦炭,经由抽气风车抽风完成烧结反应,高热之烧结矿经破碎冷却、筛选后,送往高炉作为冶炼铁水之主要原料。 高炉生产流程:高炉作业是将铁矿石、焦炭及助熔剂由高炉顶部加入炉,再由炉下部鼓风嘴鼓入高温热风,产生还原气体,还原铁矿石,产生熔融铁水与熔渣之炼铁制程。
转炉生产流程:炼钢厂先将熔铣送前处理站作脱硫脱磷处理,经转炉吹炼后,再依订单钢种特性及品质需求,送二次精炼处理站(RH真空脱气处理站、Ladle Injection盛桶吹射处理站、VOD真空吹氧脱碳处理站、STN搅拌站等)进行各种处理,调整钢液成份,最后送大钢胚及扁钢胚连续铸造机,浇铸成红热钢胚半成品,经检验、研磨或烧除表面缺陷,或直接送下游轧制成条钢、线材、钢板、钢卷及钢片等成品。 连铸生产流程:连续铸造作业乃是将钢液转变成钢胚之过程。上游处理完成之钢液,以盛钢桶运送到转台,经由钢液分配器分成数股,分别注入特定形状之铸模,开始冷却凝固成形,生成外为凝固壳、为钢液之铸胚,接着铸胚被引拔到弧状铸道中,经二次冷却继续凝固到完全凝固。经矫直后再依订单长度切割成块,方块形即为大钢胚,板状形即为扁钢胚。此半成品视需要经钢胚表面处理后,再送轧钢厂轧延.
炼钢工艺流程
炼钢工艺流程 造渣:调整钢、铁生产中熔渣成分、碱度和粘度及其反应能力的操作。目的是通过渣——金属反应炼出具有所要求成分和温度的金属。例如氧气顶吹转炉造渣和吹氧操作是为了生成有足够流动性和碱度的熔渣,以便把硫、磷降到计划钢种的上限以下,并使吹氧时喷溅和溢渣 的量减至最小。 出渣:电弧炉炼钢时根据不同冶炼条件和目的在冶炼过程中所采取的放渣或扒渣操作。如用单渣法冶炼时,氧化末期须扒氧化渣;用双渣法造还原渣时,原来的氧化渣必须彻底放 出,以防回磷等。 熔池搅拌:向金属熔池供应能量,使金属液和熔渣产生运动,以改善冶金反应的动力学条件。熔池搅拌可藉助于气体、机械、电磁感应等方法来实现。 电炉底吹:通过置于炉底的喷嘴将N2、Ar、CO2、CO、CH4、O2等气体根据工艺要求吹入炉内熔池以达到加速熔化,促进冶金反应过程的目的。采用底吹工艺可缩短冶炼时间,降低电耗,改善脱磷、脱硫操作,提高钢中残锰量,提高金属和合金收得率。并能使钢水成分、温度更均匀,从而改善钢质量,降低成本,提高生产率。 熔化期:炼钢的熔化期主要是对平炉和电炉炼钢而言。电弧炉炼钢从通电开始到炉料全部熔清为止、平炉炼钢从兑完铁水到炉料全部化完为止都称熔化期。熔化期的任务是尽快将 炉料熔化及升温,并造好熔化期的炉渣。 氧化期和脱炭期:普通功率电弧炉炼钢的氧化期,通常指炉料溶清、取样分析到扒完氧化渣这一工艺阶段。也有认为是从吹氧或加矿脱碳开始的。氧化期的主要任务是氧化钢液中的碳、磷;去除气体及夹杂物;使钢液均匀加热升温。脱碳是氧化期的一项重要操作工艺。为了保证钢的纯净度,要求脱碳量大于0.2%左右。随着炉外精炼技术的发展,电弧炉的氧 化精炼大多移到钢包或精炼炉中进行。 精炼期:炼钢过程通过造渣和其他方法把对钢的质量有害的一些元素和化合物,经化学反应选入气相或排、浮入渣中,使之从钢液中排除的工艺操作期。 还原期:普通功率电弧炉炼钢操作中,通常把氧化末期扒渣完毕到出钢这段时间称为还原期。其主要任务是造还原渣进行扩散、脱氧、脱硫、控制化学成分和调整温度。目前高功 率和超功率电弧炉炼钢操作已取消还原期。 炉外精炼:将炼钢炉(转炉、电炉等)中初炼过的钢液移到另一个容器中进行精炼的炼钢过程,也叫二次冶金。炼钢过程因此分为初炼和精炼两步进行。初炼:炉料在氧化性气氛的炉内进行熔化、脱磷、脱碳和主合金化。精炼:将初炼的钢液在真空、惰性气体或还原性气氛的容器中进行脱气、脱氧、脱硫,去除夹杂物和进行成分微调等。将炼钢分两步进行的好处是:可提高钢的质量,缩短冶炼时间,简化工艺过程并降低生产成本。炉外精炼的种类很多,大致可分为常压下炉外精炼和真空下炉外精炼两类。按处理方式的不同,又可分为钢 包处理型炉外精炼及钢包精炼型炉外精炼等。 钢液搅拌:炉外精炼过程中对钢液进行的搅拌。它使钢液成分和温度均匀化,并能促进
炼钢连铸工艺流程介绍
连铸工艺流程介绍 将高温钢水浇注到一个个的钢锭模内,而是将高温钢水连续不断地浇到一个或几个用强制水冷带有“活底”(叫引锭头)的铜模内(叫结晶器),钢水很快与“活底”凝结在一起,待钢水凝固成一定厚度的坯壳后,就从铜模的下端拉出“活底”,这样已凝固成一定厚度的铸坯就会连续地从水冷结晶器内被拉出来,在二次冷却区继续喷水冷却。带有液芯的铸坯,一边走一边凝固,直到完全凝固。待铸坯完全凝固后,用氧气切割机或剪切机把铸坯切成一定尺寸的钢坯。这种把高温钢水直接浇注成钢坯的新工艺,就叫连续铸钢。
【导读】:转炉生产出来的钢水经过精炼炉精炼以后,需要将钢水铸造成不同类型、不同规格的钢坯。连铸工段就是将精炼后的钢水连续铸造成钢坯的生产工序,主要设备包括回转台、中间包,结晶器、拉矫机等。本专题将详细介绍转炉(以及电炉)炼钢生产的工艺流程,主要工艺设备的工作原理以及控制要求等信息。由于时间的仓促和编辑水平有限,专题中难免出现遗漏或错误的地方,欢迎大家补充指正。? 连铸的目的: 将钢水铸造成钢坯。?将装有精炼好钢水的钢包运至回转台,回转台转动到浇注位置后,将钢水注入中间包,中间包再由水口将钢水分配到各个结晶器中去。结晶器是连铸机的核心设备之一,它使铸件成形并迅速凝固结晶。拉矫机与结晶振动装置共同作用,将结晶器内的铸件拉出,经冷却、电磁搅拌后,切割成一定长度的板坯。?连铸钢水的准备 一、连铸钢水的温度要求: 钢水温度过高的危害:①出结晶器坯壳薄,容易漏钢;②耐火材料侵蚀加快,易导致铸流失控,降低浇铸安全性;③增加非金属夹杂,影响板坯内在质量;④铸坯柱状晶发达;⑤中心偏析加重,易产生中心线裂纹。 钢水温度过低的危害:①容易发生水口堵塞,浇铸中断;②连铸表面容易产生结疱、夹渣、裂纹等缺陷; ③非金属夹杂不易上浮,影响铸坯内在质量。 二、钢水在钢包中的温度控制: 根据冶炼钢种严格控制出钢温度,使其在较窄的范围内变化;其次,要最大限度地减少从出钢、钢包中、钢包运送途中及进入中间包的整个过程中的温降。 实际生产中需采取在钢包内调整钢水温度的措施: 1)钢包吹氩调温 2)加废钢调温 3)在钢包中加热钢水技术 4)钢水包的保温 中间包钢水温度的控制
炼钢工艺流程图
炼钢工艺流程 1炼钢厂简介 炼钢厂主要将铁水冶炼成钢水,再经连铸机浇铸成合格铸坯。现有5座转炉,5台连铸机,年设计生产能力为500万吨,现年生产钢坯400万吨。其中炼钢一分厂年生产能力达到240万吨;炼钢二厂年生产能力为160万吨。 2炼钢的基本任务 钢是以Fe为基体并由C、Si、Mn、P、S等元素以及微量非金属夹杂物共同组成的合金。 炼钢的基本任务包括:脱碳、脱磷、脱硫、脱氧去除有害气体和夹杂,提高温度,调整成分,炼钢过程通过供氧造渣,加合金,搅拌升温等手段完成炼钢基本任务,“四脱两去两调整”。 3氧气转炉吹炼过程 氧气顶吹转炉的吹氧时间仅仅是十分钟,在这短短的时间内要完成造渣,脱碳、脱磷、脱硫、去气,去除非金属夹杂物及升温等基本任务。 由于使用的铁水成分和所炼钢种的不同,吹炼工艺也有所区别。氧气顶吹转炉炼钢的吹炼过程,根据一炉钢吹炼过程中金属成分,炉渣成分,熔池温度的变化规律,吹炼过程大致可以分为以下3个阶段: (1)吹炼前期。(2)吹炼中期。(3)终点控制。 炼好钢必须抓住各阶段的关键,精心操作,才能达到优质、高产、低耗、长寿的目标。 装入制度 装入制度是保证转炉具有一定的金属熔池深度,确定合理的装入数量,合适的铁水废钢比例。
3.1.1装入量的确定 装入量是指转炉冶炼中每炉次装入的金属料总重量,它主要包括铁水和废钢量。目前国内外装入制度大体上有三种方式: (1)定深装入;(2)分阶段定量装入;(3)定量装入 3.2.2装入次序 目前永钢的操作顺序为,钢水倒完后进行溅渣护炉溅渣完后装入废钢,然后兑入铁水。 为了维护炉衬,减少废钢对炉衬的冲击,装料次序也可以先兑铁水,后装废钢。若采用炉渣预热废钢,则先加废钢,再倒渣,然后兑铁水。如果采用炉内留渣操作,则先加部分石灰,再装废钢,最后兑铁水。 供氧制度 制订供氧制度时应考虑喷头结构,供氧压力,供氧强度和氧枪高度控制等因素。 3.2.1氧枪喷头 转炉供氧的射流特征是通过氧枪喷头来实现的,因此,喷头结构的合理选择是转炉供氧的关键。氧枪有单孔,多孔和双流道等多种结构。永钢使用的是4孔拉瓦尔喷头形式喷枪。 3.2.2氧气压力控制 氧气压力控制受炉内介质和流股马赫数的影响。经测定,炉内介质压力一般为—,流股马赫数在—之间。因此目前在转炉上使用的工作压力为—,视各种扎容量而定。一般说来,转炉容量大,使用压力越高。 3.2.3氧气流量和供氧强度 (1)氧气流量:
炼铁炼钢工艺流程
1.3 企业基本情况 新绛县祥益工贸有限公司根据山西省发展和改革委员会(晋发改备案【2007】146号)批文,建设450m3高炉,并配套建设90m3带式烧结机等。 新绛县祥益工贸有限公司位于运城市新绛县煤化工业园区,厂址距新绛县城10km,距离同蒲铁路侯马北货站10km,距大运高速公路出口2.5km,距晋韩高速公路出口3km,交通运输十分便利,地理位置非常优越。 新绛县祥益工贸有限公司占地面积约28万m2,目前拥有职工600余人,其中中层管理人员20人,各类专业技术人员40余人(其中高级技术人员3人,中级技术人员20人),职工队伍稳定,职工素质普遍提高。公司紧紧依托当地丰富的矿产资源优势,艰苦创业,我稳步发展。 新绛县祥益工贸有限公司始终坚持质量第一、信誉为本的宗旨,依靠全体员工团结拼搏、积极开拓、艰苦创业、自强不息的努力,企业迅速发展壮大,为新绛县经济发展做出贡献。 1.4 高炉生产工艺简述 高炉冶炼用的焦炭、含铁原料、溶剂在原料厂和烧结厂加工处理合格后,用皮带机运至料仓贮存使用。 各种炉料在仓下经二次筛分、计量后,按程序由仓下皮带机送到高炉料坑,由料车将炉料至炉顶加入炉内进行冶炼。 高炉冶炼的热源主要来源于焦炭和煤粉的燃烧。各种原料在炉内进行复杂的理化反应,炉内承受着高温高压作用。为此,高炉内要砌耐火材料,并在高温区和重要部位设冷却壁,确保高炉安全生产。 高炉冶炼用风由鼓风机站供给,冷风以热风炉加热后送入高炉。 高炉冶炼主要产品是生铁,副产品为煤气、炉渣、炉尘等。 高炉的铁水用铁水罐拉至铸铁机进行铸铁,或用汽车将铁水罐直接送至铸铁机进行铸铁,或用汽车将铁水罐直接送至炼钢厂进行炼钢。 高炉煤气经除尘、净化后一部分供热风炉烧炉,余下部分供烧结机、喷煤和6000kw发电机组。 高炉炉渣在炉前进行水冲渣,水渣送至建材厂制砖,或送至水泥厂作为制作水泥的原料。 高炉产生的各种原料、重力除尘拉到烧结厂进行配料烧结,煤气除尘的布袋拉到建材厂进行综合利用。 高炉生产工艺流程见图二。 1.6烧结生产工艺简述 90m3烧结机主要包括烧结机及相应配套的原料系统、配料系统、混料系统、破碎、筛分系统、鼓风冷却系统、成品贮存系统以及供风、供水、供电等辅助设施。 该工程主要由生产设施、辅助设施和生活设施三大部分组成,其中生活设施由建设单位同意考虑,故本设计只考虑生产设施和辅助设施。 生产设施包括原料及配料系统,主烧结室、带冷几室、风机房、烟卤,一混合室、二混合室、成品中间仓等。 辅助设施包括原料及配料系统除尘及配套风机,机头除尘室及配套风机、烟卤,机尾布袋出尘室及配套风机、变配电室、水泵房等。 生产设施的总图布置为带冷机室在、主烧结室东西方向布置,除尘室的南侧。原料上料及配料系统布置在主烧机室的东侧,一混合室、二混合室布置在主烧机室的南侧。成品中间仓布置在带冷机室的南侧,距高炉储矿槽100余米,由成品皮带将成品烧结矿送至高炉储矿槽上。 烧结生产工艺流程见图三。 1.8 高炉喷煤生产工艺简述 高炉喷煤配套工程,是节约焦炭、降低高炉炼铁生产成本的重要措施。自从六十年代我国鞍钢、首钢高炉喷煤会的成功以来很快在国内普遍推广应用,并且高炉喷煤在工艺及其相关技术得到了迅速发展。尤其是近几年发展的富氧大喷煤技术(宝钢喷煤煤比打达到≥200kg/Tfe水平)给高炉生产注入县的生机。国内炼铁生产规模不断扩大与高炉生产效率的提高,对焦炭需求量业日趋增加,由于国内
炼钢工艺流程
【导读】:转炉炼钢是把氧气鼓入熔融的生铁里,使杂质硅、锰等氧化。在氧化的过程中放出大量的热量(含1%的硅可使生铁的温度升高200摄氏度),可使炉内达到足够高的温度。因此转炉炼钢不需要另外使用燃料。炼钢的基本任务是脱碳、脱磷、脱硫、脱氧,去除有害气体和非金属夹杂物,提高温度和调整成分。归纳为:“四脱”(碳、氧、磷和硫),“二去”(去气和去夹杂),“二调整”(成分和温度)。采用的主要技术手段为:供氧,造渣,升温,加脱氧剂和合金化操作。本专题将详细介绍转炉炼钢生产的工艺流程,主要工艺设备的工作原理以及控制要求等信息。由于时间的仓促和编辑水平有限,专题中难免出现遗漏或错误的地方,欢迎大家补充指正。 转炉冶炼目的:将生铁里的碳及其它杂质(如:硅、锰)等氧化,产出比铁的物理、化学性能与力学性能更好的钢。 【相关信息】钢与生铁的区别:首先是碳的含量,理论上一般把碳含量小于2.11%称之钢,它的熔点在1450-1500℃,而生铁的熔点在1100-1200℃。在钢中碳元素和铁元素形成Fe3C固熔体,随着碳含量的增加,其强度、硬度增加,而塑性和冲击韧性降低。钢具有很好的物理、化学性能与力学性能,可进行拉、压、轧、冲、拔等深加工,其用途十分广泛。 转炉冶炼原理简介: 转炉炼钢是在转炉里进行。转炉的外形就像个梨,内壁有耐火砖,炉侧有许多小孔(风口),压缩空气从这些小孔里吹炉内,又叫做侧吹转炉。开始时,转炉处于水平,向内注入1300摄氏度的液态生铁,并加入一定量的生石灰,然后鼓入空气并转动转炉使它直立起来。这时液态生铁表面剧烈的反应,使铁、硅、锰氧化 (FeO,SiO2 , MnO,) 生成炉渣,利用熔化的钢铁和炉渣的对流作用,使反应遍及整个炉内。几分钟后,当钢液中只剩下少量的硅与锰时,碳开始氧化,生成一氧化碳(放热)使钢液剧烈沸腾。炉口由于溢出的一氧化炭的燃烧而出现巨大的火焰。最后,磷也发生氧化并进一步生成磷酸亚铁。磷酸亚铁再跟生石灰反应生成稳定的磷酸钙和硫化钙,一起成为炉渣。当磷与硫逐渐减少,火焰退落,炉口出现四氧化三铁的褐色蒸汽时,表明钢已炼成。这时应立即停止鼓风,并把转炉转到水平位置,把钢水倾至钢水包里,再加脱氧剂进行脱氧。整个过程只需15分钟左右。如果氧气是从炉底吹入,那就是底吹转炉;氧气从顶部吹入,就是顶吹转炉。 转炉冶炼工艺流程简介:
转炉炼钢工艺流程介绍
转炉炼钢工艺流程介绍 ---- 冶金自动化系列专题 【导读】:转炉炼钢是把氧气鼓入熔融的生铁里,使杂质硅、锰等氧化。在氧化的过程中放出大量的热量(含1%的硅可使生铁的温度升高200摄氏度),可使炉内达到足够高的温度。因此转炉炼钢不需要另外使用燃料。炼钢的基本任务是脱碳、脱磷、脱硫、脱氧,去除有害气体和非金属夹杂物,提高温度和调整成分。归纳为:“四脱”(碳、氧、磷和硫),“二去”(去气和去夹杂),“二调整”(成分和温度)。采用的主要技术手段为:供氧,造渣,升温,加脱氧剂和合金化操作。本专题将详细介绍转炉炼钢生产的工艺流程,主要工艺设备的工作原理以及控制要求等信息。由于时间的仓促和编辑水平有限,专题中难免出现遗漏或错误的地方,欢迎大家补充指正。【发表建议】 转炉冶炼目的:将生铁里的碳及其它杂质(如:硅、锰)等氧化,产出比铁的物理、化学性能与力学性能更好的钢。 【相关信息】钢与生铁的区别:首先是碳的含量,理论上一般把碳含量小于2.11%称之钢,它的熔点在1450-1500℃,而生铁的熔点在1100-1200℃。在钢中碳元素和铁元素形成Fe3C固熔体,随着碳含量的增加,其强度、硬度增加,而塑性和冲击韧性降低。钢具有很好的物理、化学性能与力学性能,可进行拉、压、轧、冲、拔等深加工,其用途十分广泛。 [查看全文] 转炉冶炼原理简介: 转炉炼钢是在转炉里进行。转炉的外形就像个梨,内壁有耐火砖,炉侧有许多小孔(风口),压缩空气从这些小孔里吹炉内,又叫做侧吹转炉。开始时,转炉处于水平,向内注入1300摄氏度的液态生铁,并加入一定量的生石灰,然后鼓入空气并转动转炉使它直立起来。这时液态生铁表面剧烈的反应,使铁、硅、锰氧化 (FeO,SiO2 , MnO,) 生成炉渣,利用熔化的钢铁和炉渣的对流作用,使反应遍及整个炉内。几分钟后,当钢液中只剩下少量的硅与锰时,碳开始氧化,生成一氧化碳(放热)使钢液剧烈沸腾。炉口由于溢出的一氧化炭的燃烧而出现巨大的火焰。最后,磷也发生氧化并进一步生成磷酸亚铁。磷酸亚铁再跟生石灰反应生成稳定的磷酸钙和硫化钙,一起成为炉渣。当磷与硫逐渐减少,火焰退落,炉口出现四氧化三铁的褐色蒸汽时,表明钢已炼成。这时应立即停止鼓风,并把转炉转到水平位置,把钢水倾至钢水包里,再加脱氧剂进行脱氧。整个过程只需15分钟左右。如果氧气是从炉底吹入,那就是底吹转炉;氧气从顶部吹入,就是顶吹转炉。 [查看全文] 转炉冶炼工艺流程简介:
钢铁行业生产流程及主要设备介绍
钢铁行业 一.我国钢铁行业简介 我国是世界上最早进行钢铁冶炼的国家之一,在公元前6世纪前后,中国就发明了生铁冶炼技术,到春秋战国时期,基本掌握了块炼铁、铸铁和炼钢技术。 进入工业大革命时期以后,随着工业发展需要和电炉炼钢,连铸技术的发展,钢铁冶炼技术大大提高,全球钢铁产钢量大幅度提高。建国后,我国先后从西德和日本引进大量的先进的冶炼设备和工艺,从而改善了国内钢铁冶炼落后的形势,到20009年国内生产粗钢5.65亿吨,连续10年居世界之首。 我国有大小钢铁企业几百家,主要的钢铁企业有:宝钢、首钢、鞍本、武钢、河北钢铁、山东钢铁、沙钢、包钢、攀钢、马钢、太钢等等。 和分类 二. 钢铁的定义 钢铁的定义和分类 钢铁从本质上都是铁和碳的化合物,其中还有微量的磷、硫、硅和锰等元素。生铁、熟铁和钢的主要区别在于含碳量上,含碳量超过2%的铁,叫生铁;含碳量低于0.05%的铁,叫熟铁;含碳量在0.05%-2%当中的铁,称为钢。 钢铁的分类方式很多,常用分类如下。 (1) 按品质分类:普通钢(P≤0.045%,S≤0.050%);优质钢(P、S均≤0.035%);高级优质钢(P≤0.035%,S≤0.030%)。
(2)按化学成份分类:①碳素钢【低碳钢C≤0.25%)、中碳钢(C≤0.25~0.60%)、高碳钢(C≤0.60%)】②合金钢:【低合金钢(合金元素总含量≤5%)、中合金钢(合金元素总含量>5~10%)、高合金钢(合金元素总含量>10%)】。 (3)按成形方法分类:锻钢、 铸钢、 热轧钢、冷拉钢。 (4)按钢的用途分:结构钢、工具钢、特殊钢、专业用钢。 三. 钢铁的冶炼钢铁的冶炼流程流程流程和主要设备和主要设备 一般来说,钢铁的冶炼大致分为四个过程:炼铁、炼钢、热轧、冷轧。 宝钢钢铁产品冶炼工艺流程
炼钢工艺
1 炼钢工艺发展概述 亨利·贝塞麦于1855年发明了酸性空气底吹转炉炼钢法,首次解决了用铁水冶炼液态钢的问题,使得炼钢生产的质量、产量实现了跨越性质的提高。相隔10年之后,法国人马丁利用蓄热池原理发明了平炉炼钢法。由于平炉炼钢法适应于各种原材料条件(铁水和废钢可用任何比例),平炉炼钢法长期占居炼钢工艺主导地位,平炉钢占全世界总产钢量的80%以上。湘钢在1999年以前一直处于这种局面:平炉—→模铸—→初轧开坯—→模列式轧机—→普通线材,采用多火成材工艺,成本消耗偏高,多项技术经济指标在全国冶金行业内排名一直靠后。 1940年代,大型空气分离机问世后,能够提供高纯度、大量廉价的氧气,随后诞生了氧气顶吹转炉。1952年在奥地利林茨城和1953年在多纳维茨城先后建成了30吨的转炉车间并投入工业生产。由于转炉生产率高,成本低,质量较高,投资低于平炉,便于实现自动化,因此在世界上发展迅速,并逐步取代了平炉。 回顾二炼钢厂自1996年8月1#转炉投产以来的发展进程及其对于湘钢的生存环境所带来的影响,也印证了这一规律。 自从20世纪开始发展电炉炼钢,该工艺长期以来一直作为熔炼特殊钢和高合金钢的方法。由于质量要求很高和市场需求巨大,伴随电力工业技术进步和供电能力提高,采用超高功率电弧炉和炉外精炼技术已经成为国内外应用日益广泛的冶金生产方式。我国电力建设的大发展,电弧炉炼钢工艺也将逐步改变其目前状况。 氧气转炉炼钢工艺已成为目前世界上最为主要的炼钢方法,即使到21世纪的前期,转炉钢的生产比例仍将保持在60~70%。回顾50年氧气转炉炼钢发展史,可以划分为三个发展时期:
转炉大型化时期(1950~1970年) 这一历史时期,以转炉大型化为技术核心,逐步完善转炉炼钢工艺与设备。先后开发出大型转炉设计制造技术、OG除尘与煤气回收技术、计算机自动与副枪动态控制技术、镁碳砖综合砌炉与喷补挂渣等护炉技术,转炉炉龄达到2000炉。 转炉技术完善化时期(1970~1990年) 这一时期,由于连铸技术的迅速发展,出现了全连铸的炼钢车间。中国于1972年在重庆钢铁公司投产了第一台用于工业化生产的板坯连铸机。随着对转炉炼钢的稳定和终点控制的准确性等要求越来越高,为了改善转炉吹炼后期钢渣反应远离平衡,实现平稳吹炼的目标,综合顶吹、底吹转炉的优点,研究开发出各种顶底复合吹炼工艺,在全世界迅速推广。这一时期,转炉炉龄达到5000炉。 转炉综合优化时期(1990~2010年) 这一时期,社会对洁净钢的生产需求日益增加,迫切要求建立一种全新的、能大规模廉价生产洁净钢的质量保证体系。围绕洁净钢生产,研究开发出铁水“三脱”预处理(脱硫、脱磷、脱硅)高效转炉生产,全自动吹炼控制与长寿炉龄(主要技术核心为溅渣护炉)等重大新工艺技术。这一时期,转炉炉龄普遍超过10000炉(目前国内最好水平为武钢二炼钢炉龄突破30000炉)。湘钢转炉炉龄业已超过18000炉,居于国内同行业指标前列。 近终型连铸技术及铸坯热送装技术的深入开发,形成了更为紧凑、高效的炼钢—轧钢短流程生产线,使联合企业逐步走向一个炼钢厂的生产体制,降低投资成本和生产成本,大幅度提高了生产效率。 ★思考点 1、转炉炼钢工艺发展的主要历程。 2、铁水预处理的作用与效能。
碱性电弧炉炼钢工艺流程
碱性电弧炉炼钢工艺流程 碱性电弧炉氧化法炼钢工艺过程主要包括原材料准备、补炉、配料及装料、熔化期、氧化期、还原期及出钢等7个阶段。 一、原材料准备 废钢是电弧炉炼钢的主要材料,废钢质量的好坏直接影响钢冶的质量、成本和生产率,因此,对废钢质量有如下几点要求。 1)废钢表面应清洁少锈,因废钢中沾有的泥沙等杂物会降低炉料的导电性能,延长熔化时间,还会影响氧化期去鳞效果及侵蚀炉衬。废钢锈蚀严重或沾有油污时还会降低钢和合金元素的收得率,并增加钢中的含氢量。 2)废钢中不得混有铅、锡、砷、锌和铜等有色金属。铅的密度大,熔点低,不溶于钢液,易沉积在炉底缝隙中造成漏钢事故;锡、砷和铜易引起钢的热脆。 3)废钢中不得混有密封容器,以及易燃、易爆物和有毒物,以保证安全生产。 4)废钢化学成分应明确,且需按成分分类存放,硫、磷含量不宜过高。 5)废钢外形尺寸不能过大(截面积不宜超过300mm×300mm,最大长度不宜超过350mm)。 二、补炉 一般情况下,每炼完一炉钢后,在装料前要进行补炉,其目的是修补炉底和被侵蚀的渣线及被破坏的部位,以维持正常的炉体形状,从而保证冶炼的正常进行和安全生产,补炉的要点如下:
1)出钢后立即检查炉衬,需填补炉底时,应先将炉底残渣全部扒出,然后进行填补。补炉的原则是高温、快补、薄补,维护炉膛原状。 2)补炉料要提前半个小时混合均匀,补炉后放下电极烘烤30min,若补镁砂量较大,应酌情延长烘烤时间。 三、配料及装料 配料是电炉炼钢工艺中不可缺少的组成部分,配料是否合理关系到炼钢工能否按照工艺要求正常地进行冶炼操作。合理的配料能缩短冶炼时间。配料时应注意以下几点:一是必须正确地进行配料计算和准确地称量炉料装入量;二是炉料的大小要按比例搭配,以达到好装、快速熔化的目的;三是各类炉料应根据钢液的质量要求和冶炼方法搭配使用;四是配料成分必须符合工艺要求。 装料前应先在炉底铺上一层石灰,其重量约为炉料重量的2%,以便提前造好熔化渣,有利于早期去磷,减少钢液吸气和加速升温。 装料时应将小料的一半放入底部,小料的上部、炉子中心区放入全部大料、低碳废钢和难熔炉料,大料之间放入小料,中型料装在大料的上面及四周,大料的最上面放入小料。凡在配料中使用的电极块应砸成50~lOOmm,装在炉料下层,且要紧实,装好的炉料为半球形,二次加料不使用大块料及湿料。 四、熔化期 在电弧炉炼钢工艺中,从通电开始到炉料全部熔清为止称为熔化期。熔化期的任务是将固体炉料迅速熔化成钢液,并进行脱磷,减少钢液吸收气体和金属的挥发。熔化期的操作工艺如下: 1)启弧阶段。通电启弧时炉膛内充满炉料,电弧与炉顶距离很近,如果输入功率过大、电压过高,炉顶容易被烧坏,因此一般选用中级电压和输入变压器额定功率的2/3左右。
某钢铁厂主要生产流程及设备简介
钢铁厂主要生产工艺及设备简介 烧结厂 烧结厂目前有1#—6#烧结机(主要工艺流程如图),其中1#、2#的烧结机属于平烧,3#、4#、5#、6#属于带烧。 1、1#、2#烧结主要设备参数如下: 10个原料料仓,一次混合机(? 2.8×12m×1台),二次混合机(?2.8×12m×1台),平滚布料器(2台),烧结机(50m2×2台),助燃风机(4台),单辊破碎机(1台),链板机(IS125—15—M速比250×2台),1545振动筛(1.2×2.4m×2台)。 2、3#、4#、5#烧结主要设备参数如下: 31个原料料仓,一次混合机(? 3.2×13m×2台),二次混合机(?3.8×15m×2台),梭式布料器(48×1.2m×2台),烧结机(180m2×3台),助燃风机(9-19-7.1D×6台),抽风机(2台),单辊破碎机(2X3.74m×1台,3.23×1.8m×2台),环冷(170m2×48车×3台),椭圆等厚振动筛(IDLS3075×3台,IDLS 2060×3台)。
3、6#烧结主要设备参数如下: 16个原料料仓,一次混合机(? 3.8×15m×1台),二次混合机(?4.0×20m×1台),梭式布料器(41×1.2×1台),烧结机(265m2×1台),助燃风机(9-19-7.1D×2台),单辊破碎机(2X3.74m×1台),环冷(280m2×60车×1台),椭圆等厚振动筛(TDLS3090×2台)。 球团厂 球团厂主要有3个竖炉(主要工艺流程如图),由老区1#,新区2#、3#竖炉组成。 老区1#竖炉主要设备参数如下: 6个原料料仓,烘干机(?2.4X14×1台),润磨机(?3.5X6.2m×1台),圆盘给料机(PQ1600mm×5台),造球机(?4.5m×5台),圆辊筛分机(TS-C型?102X1420X34辊X 1台),竖炉本体(1m2×1台),热链板机(1台),带冷机(30m2×1台)。 老区2#、3#竖炉主要设备参数如下:
炼钢生产工艺流程
炼钢、连铸工艺
转炉炼钢工艺简介 黑龙江建龙钢铁有限公司建于双鸭山岭西区长胜乡新兴村东部,东北距双鸭山市区7km。场地南、北部为完达山山脉,东、西向为马蹄河河谷。 建设规模与产品 主要设备配置:1×900吨混铁炉、2×60吨转炉、2×R8m六机六流方坯连铸机, 及其相关公辅设施。形成年产钢200万吨规模。 生产的钢种有:普通碳素结构钢、优质碳素结构钢。代表钢种:Q195-235、20MnSiV、20MnSi、铸坯断面:150x150mm,定尺:4.2-12m 装备水平 1、炉倾动机构采用全悬挂,四点传动,三点球面支承、扭力杆平衡式、水冷炉 口、炉帽上部和托圈进行水冷。 2、氧枪采用双小车、双卷扬,能实现自动换枪。 3、转炉采用顶底复合吹炼技术。 4、转炉自动化控制系统,采用电、仪一体化的基础自动化和过程计算机,并留 有与上位机接口。 5、转炉炉前、炉后挡火门采用铸铁板式、维护方便,并能节约用水。 6、转炉出钢采用挡渣球挡渣,减少流入钢水罐中的钢渣量。 7、采用R8m六机六流高效方坯连铸机。 原材料
车间组成 —主厂房主要包括:混铁炉间、加料跨、转炉跨、钢水接受跨、炉渣跨。—公用辅助设施包括:10k V开关站、转炉一烟气净化系统、二次烟气净化系统(包含混铁炉烟气除尘、散状材料上料系统除尘)、转炉浊循环水泵站及转炉污水处理设施。转炉净循环水泵站和连铸水处理、转炉煤气柜及加压站、机修设施、检化验系统、通讯设施、制氧站、空压站、铁合金仓库、耐火材料库、总图及运输设施,各种散料仓库或堆场设施等由公司另行安排设计。 厂房工艺布置
主要生产工艺流程 高炉铁水900吨混铁炉保存通过铁水罐用天车兑入转炉用废钢斗把废钢同时装入转炉下枪吹炼过程中通过高位料仓加入造渣剂达到终点倒炉出钢出钢过程中加入合金、脱氧剂、增碳剂在出钢过程中对钢水进行底吹氮(氩)气处理对部分钢种进行LF炉钢包精炼处理或钢包吹氩喂丝处理钢水处理合格后用天车吊到连铸回转台打开大包水口钢水进入中间包通过结晶器、拉矫机拉出150方的连铸坯。 铁水供应 铁水用65t高炉铁水罐车运输,到达混铁炉间后用100/32t吊车将高炉铁水罐吊起兑入900t混铁炉储存保温待用。当转炉需要铁水时,再从900t混铁炉倒入炉下铁水罐车上的80t转炉铁水罐中,经称量后,铁水罐车开出到加料跨,用加料跨125/40t吊车吊起直接兑入转炉炼钢。当混铁炉检修或有故障时,可在混铁炉间用100/32t吊车将铁水从65t高炉铁水罐中直接翻罐到80t转炉铁水罐,然后由过跨车运送到加料跨,再兑入转炉炼钢。 废钢供应 废钢用汽车运入主厂房加料跨废钢区,在废钢区进行配料。废钢料槽置于废钢料槽电子秤上,利用16/3t电磁吊车进行配料,配好料的料槽由20/20t吊车吊
炼钢连铸工艺流程的介绍
连铸工艺流程介绍 将高温钢水浇注到一个个得钢锭模内,而就是将高温钢水连续不断地浇到一个或几个用强制水冷带有“活底”(叫引锭头)得铜模内(叫结晶器),钢水很快与“活底”凝结在一起,待钢水凝固成一定厚度得坯壳后,就从铜模得下端拉出“活底”,这样已凝固成一定厚度得铸坯就会连续地从水冷结晶器内被拉出来,在二次冷却区继续喷水冷却。带有液芯得铸坯,一边走一边凝固,直到完全凝固。待铸坯完全凝固后,用氧气切割机或剪切机把铸坯切成一定尺寸得钢坯。这种把高温钢水直接浇注成钢坯得新工艺,就叫连续铸钢。 【导读】:转炉生产出来得钢水经过精炼炉精炼以后,需要将钢水铸造成不同类型、不同规格得钢坯。连铸工段就就是將精炼后得钢水连续铸造成钢坯得生产工序,主要设备包括回转台、中间包,结晶器、拉矫机等。本专题将详细介绍转炉(以及电炉)炼钢生产得工艺流程,主要工艺设备得工作原理以及控制要求等信息。由于时间得仓促与编辑水平有限,专题中难免出现遗漏或错误得地方,欢迎大家补充指正。
连铸得目得:将钢水铸造成钢坯。 将装有精炼好钢水得钢包运至回转台,回转台转动到浇注位置后,将钢水注入中间包,中间包再由水口將钢水分配到冬个结晶器中去。结甜器就是连铸机得核心设备之一,它使铸件成形并迅速凝固结晶。拉矫机与结晶振动裝置共同作用,将结晶器内得铸件拉出,经冷却、电磁搅拌后,切割成一定长度得板坯。 连铸钢水得准备 一、连铸钢水得温度要求: 钢水温度过高得危害:①出结晶器坯壳薄,容易漏钢;②耐火材料侵蚀加快,易导致铸流失控,降低浇铸安全性;③增加非金属夹杂,影响板坯内在质量;④铸坯柱状晶发达;⑤中心偏析加重,易产生中心线裂纹。 钢水温度过低得危害:①容易发生水口堵塞,浇铸中斯;②连铸表面容易产生结疱、夹渣、裂纹等抉陷;③非金属夹杂不易上浮,影响铸坯內在质量。 二、钢水在钢包中得温度控制: 根据洽炼钢种严格控制出钢温度,使其在较窄得范围内变化;其次,要最大限度地减少从出钢、钢包中、钢包运送途中及进入中间包得整个过程中得温降。 实际生产中需釆取在钢包内调整钢水温度得措施: 1)钢包吹氨调温 2)加废钢调温 3)在钢包中加热钢水技术 4)钢水包得保温 中间包钢水温度得控制—、浇铸温度得确定
炼钢简单工艺流程
炼钢的工艺流程 7月8日上午听了苏教授给我们讲的关于炼钢的工艺流程,我对我们的专业课有了初步的了解与认识。 炼钢就是将铁水冶炼成钢水,而钢与铁的区别就在于含碳量不同,只要将铁里边的含碳量降低到一定程度就是我们所需要的钢了,所以要想炼钢首先便要炼铁。这里一般有两个流程: 长流程:选矿→烧结(球团)→高炉→铁水预处理→转炉→精炼→连铸→轧钢短流程:废钢→电炉→精炼→连铸→轧钢 这里说的选矿,烧结,球团,是高炉冶炼的原料准备阶段,当完成烧结,造球后进入高炉利用高炉内的还原性环境将铁水从铁矿石从还原出来,为下一阶段的炼钢提供原料供给。而接下来的铁水预处理就是脱去硫等杂质。接着就是利用转炉内的氧化性环境将铁水中过量的碳氧化成一氧化碳和二氧化碳,达到钢水要求的碳含量。转炉出钢后的钢水精炼(LF或LF+RH或LF+VD,VOD等),完成精炼后用行车调运至连铸机的大包回转台,进行连铸浇铸的工序环节,为后续的轧钢厂提供钢坯原料。 实际中,整个联合钢铁厂的工艺流程为:原料码头(各种原料集中卸载存放区域)——烧结(矿石造块或造球团)——高炉(炼铁)——炼钢(铁水预处理-转炉或电炉-精炼-连铸)-轧钢。其流程图如下:
现在普遍使用的是转炉炼钢法,这种炼钢法使用的氧化剂是氧气。把空气鼓入熔融的生铁里,使杂质硅、锰等氧化。在氧化的过程中放出大量的热量(含1%的硅可使生铁的温度升高200摄氏度),可使炉内达到足够高的温度。因此转炉炼钢不需要另外使用燃料。 转炉炼钢是在转炉里进行。转炉的外形就像个梨,内壁有耐火砖,炉侧有许多小孔(风口),压缩空气从这些小孔里吹炉内,又叫做侧吹转炉。开始时,转炉处于水平,向内注入1300摄氏度的液态生铁,并加入一定量的生石灰,然后鼓入空气并转动转炉使它直立起来。这时液态生铁表面剧烈的反应,使铁、硅、锰氧化 (FeO,SiO2 , MnO,) 生成炉渣,利用熔化的钢铁和炉渣的对流作用,使反应遍及整个炉内。几分钟后,当钢液中只剩下少量的硅与锰时,碳开始氧化,生成一氧化碳(放热)使钢液剧烈沸腾。炉口由于溢出的一氧化炭的燃烧而出现巨大的火焰。最后,磷也发生氧化并进一步生成磷酸亚铁。磷酸亚铁再跟生石灰反应生成稳定的磷酸钙和硫化钙,一起成为炉渣。 当磷于硫逐渐减少,火焰退落,炉口出现四氧化三铁的褐色蒸汽时,表明钢已炼成。这时应立即停止鼓风,并把转炉转到水平位置,把钢水倾至钢水包里,再加脱氧剂进行脱氧。整个过程只需15分钟左右。如果空气是从炉低吹入,那就是低吹转炉。 随着制氧技术的发展,现在已普遍使用氧气顶吹转炉(也有侧吹转炉)。这种转炉吹如的是高压工业纯氧,反应更为剧烈,能进一步提高生产效率和钢的质量。 应用较多的除了转炉之外还有平炉,平炉炼钢使用的氧化剂是通入的空气和炉料里的氧化物(废铁,废钢,铁矿石)。反应所需的热量是由燃烧气体燃料(高炉煤气,发生炉煤气)或液体燃料(重油)所提供。平炉的炉膛是一个耐火砖砌成的槽,上面有耐火砖制成的炉顶盖住。平炉的前墙上有装料口,装料机就从这里把炉料装进去。熔炼时关上耐火砖造成的门。炉膛的两端都筑有炉头,炉头各有两个孔道,供导入燃料与热空气,或从炉里导炉气之用。平炉炼钢所用的原料有废钢、废铁、铁矿石和溶