SAP_MM_安全库存详解
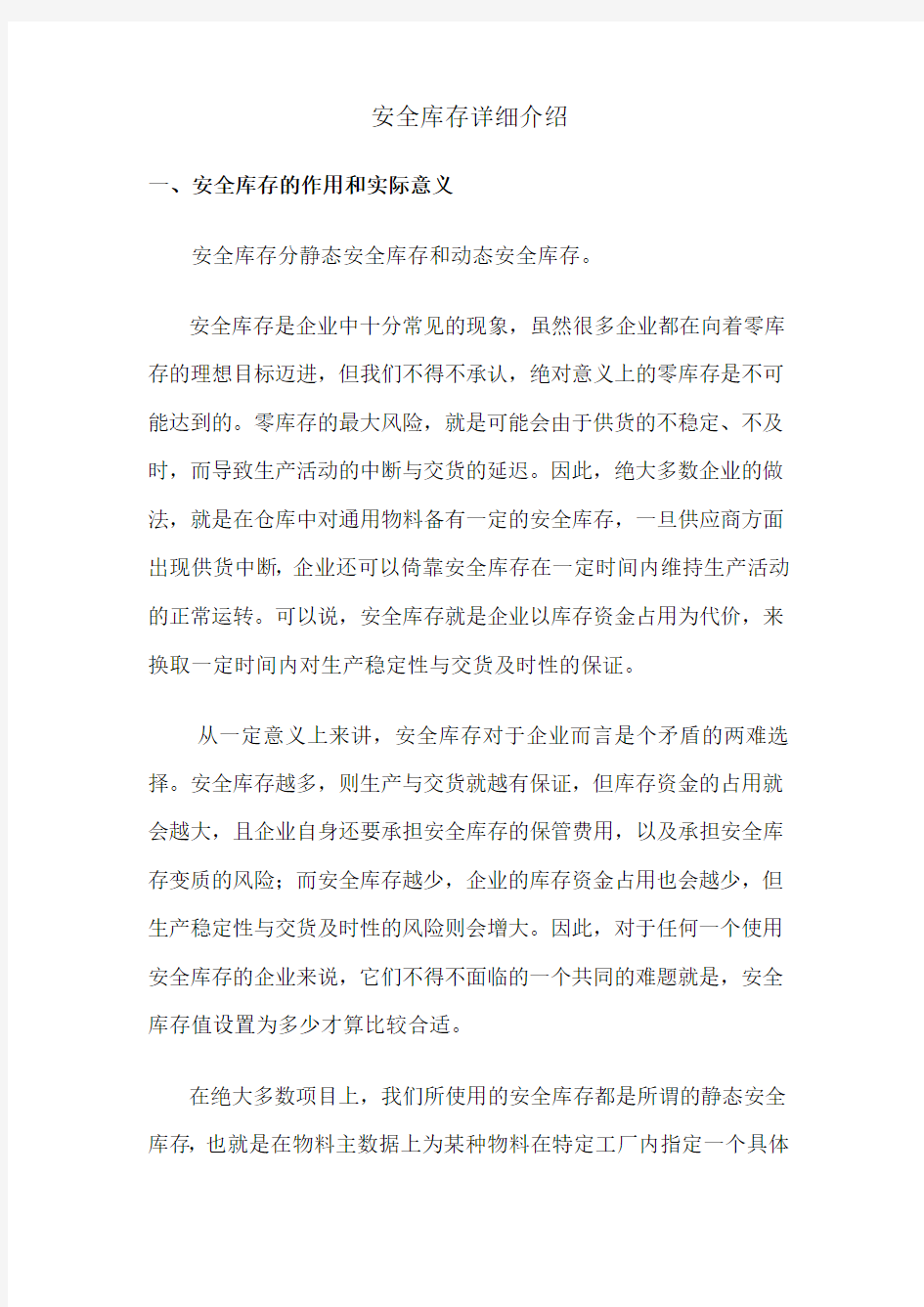
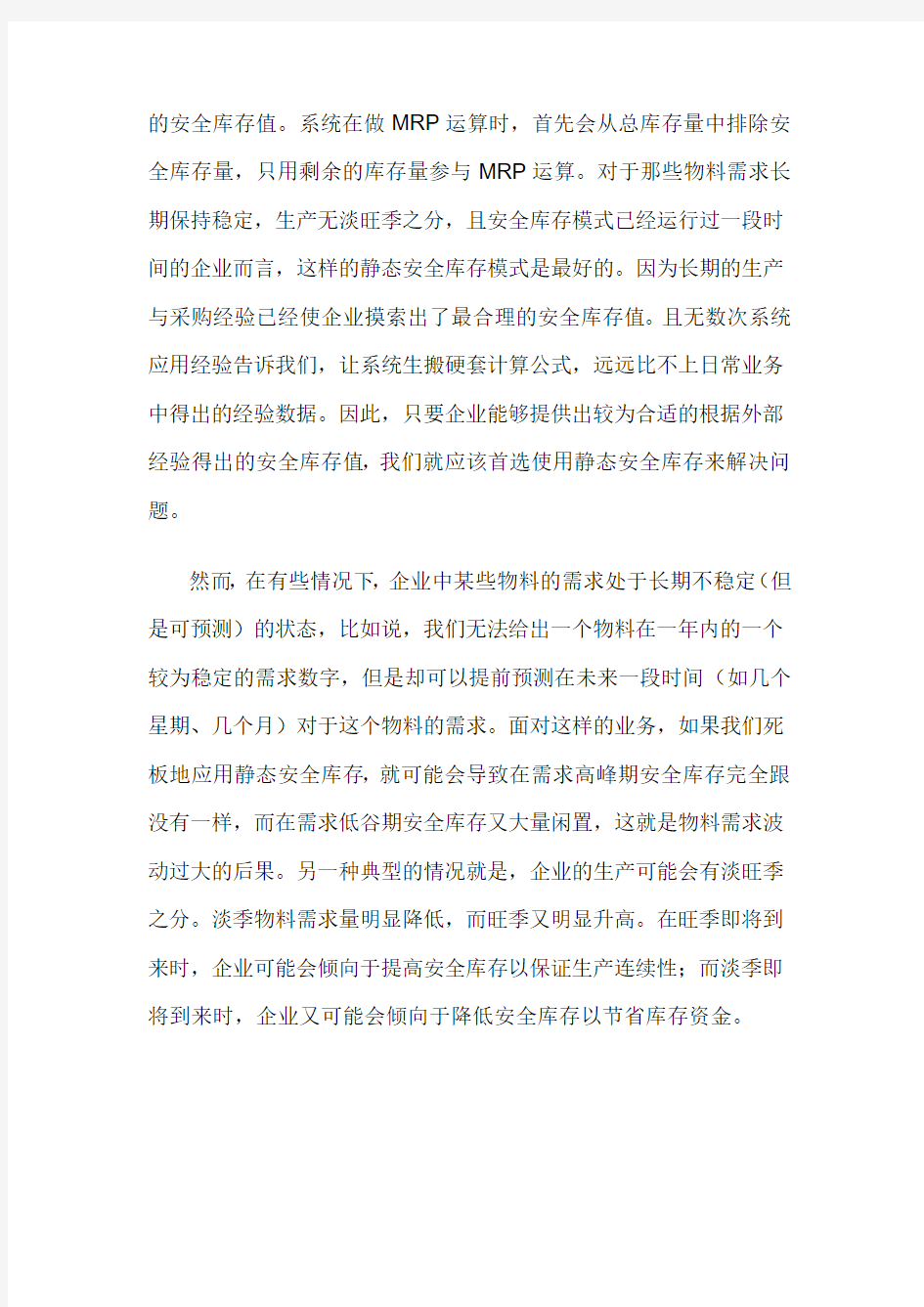
安全库存详细介绍
一、安全库存的作用和实际意义
安全库存分静态安全库存和动态安全库存。
安全库存是企业中十分常见的现象,虽然很多企业都在向着零库存的理想目标迈进,但我们不得不承认,绝对意义上的零库存是不可能达到的。零库存的最大风险,就是可能会由于供货的不稳定、不及时,而导致生产活动的中断与交货的延迟。因此,绝大多数企业的做法,就是在仓库中对通用物料备有一定的安全库存,一旦供应商方面出现供货中断,企业还可以倚靠安全库存在一定时间内维持生产活动的正常运转。可以说,安全库存就是企业以库存资金占用为代价,来换取一定时间内对生产稳定性与交货及时性的保证。
从一定意义上来讲,安全库存对于企业而言是个矛盾的两难选择。安全库存越多,则生产与交货就越有保证,但库存资金的占用就会越大,且企业自身还要承担安全库存的保管费用,以及承担安全库存变质的风险;而安全库存越少,企业的库存资金占用也会越少,但生产稳定性与交货及时性的风险则会增大。因此,对于任何一个使用安全库存的企业来说,它们不得不面临的一个共同的难题就是,安全库存值设置为多少才算比较合适。
在绝大多数项目上,我们所使用的安全库存都是所谓的静态安全库存,也就是在物料主数据上为某种物料在特定工厂内指定一个具体
的安全库存值。系统在做MRP运算时,首先会从总库存量中排除安全库存量,只用剩余的库存量参与MRP运算。对于那些物料需求长期保持稳定,生产无淡旺季之分,且安全库存模式已经运行过一段时间的企业而言,这样的静态安全库存模式是最好的。因为长期的生产与采购经验已经使企业摸索出了最合理的安全库存值。且无数次系统应用经验告诉我们,让系统生搬硬套计算公式,远远比不上日常业务中得出的经验数据。因此,只要企业能够提供出较为合适的根据外部经验得出的安全库存值,我们就应该首选使用静态安全库存来解决问题。
然而,在有些情况下,企业中某些物料的需求处于长期不稳定(但是可预测)的状态,比如说,我们无法给出一个物料在一年内的一个较为稳定的需求数字,但是却可以提前预测在未来一段时间(如几个星期、几个月)对于这个物料的需求。面对这样的业务,如果我们死板地应用静态安全库存,就可能会导致在需求高峰期安全库存完全跟没有一样,而在需求低谷期安全库存又大量闲置,这就是物料需求波动过大的后果。另一种典型的情况就是,企业的生产可能会有淡旺季之分。淡季物料需求量明显降低,而旺季又明显升高。在旺季即将到来时,企业可能会倾向于提高安全库存以保证生产连续性;而淡季即将到来时,企业又可能会倾向于降低安全库存以节省库存资金。
综上所述,在物料需求出现大幅度波动(特别是季节性大幅度波动)的情况下,简单地设置一个静态的安全库存值就显得不太合适了。因此在这种情况下,我们可以考虑应用动态安全库存这一功能。
所谓动态安全库存,指的是我们并不对物料维护一个固定的安全库存值,而是让系统基于未来一段时间内的物料需求量,根据库存量计算公式和一定的公式参数,自动计算出未来一段时间内所需的安全库存值。这一方式最大的特点,就是物料的安全库存值是动态的,是随着需求量的上下波动而上下波动的,也是不断随着时间的推移而循环滚动计算的。
动态安全库存计算所考虑的时间范围可长可短、所考虑的覆盖范围可大可小。但其基本的运算思路是可以确定的,那就是安全库存值=日平均需求*覆盖范围。这里所谓覆盖范围,指的就是安全库存所需供给的需求天数。假设覆盖范围被设置为3天,其含义就是安全库存应该足够独立满足3天的物料需求。或者说通俗一点就是该物料应该可以在完全没有供应商供货的情况下,仅仅依靠安全库存撑过3天(在每天的物料需求都等于日平均需求的情况下)。
通过应用动态安全库存,我们就可以避免静态安全库存的一些缺陷。当安全库存值随着物料需求的变化而上下浮动时,我们就能够避免安全库存值过低或者过高而带来的浪费或者风险了。
二、安全库存的计算
前面已经介绍‘无数次系统应用经验告诉我们,让系统生搬硬套计算公式,远远比不上日常业务中得出的经验数据’,也就是如果能够凭借自己的经验估计安全库存,最好就不要按照下面的公式来计算。安全库存量的大小,主要由顾客服务水平(或订货满足)来决定。所谓顾客服务水平,就是指对顾客需求情况的满足程度,公式表示如下:顾客服务水平(5%)=年缺货次数/年订货次数
顾客服务水平(或订货满足率)越高,说明缺货发生的情况越少,从而缺货成本就较小,但因增加了安全库存量,导致库存的持有成本上升;而顾客服务水平较低,说明缺货发生的情况较多,缺货成本较高,安全库存量水平较低,库存持有成本较小。因而必须综合考虑顾客服务水平、缺货成本和库存持有成本三者之间的关系,最后确定一个合理的安全库存量。
对于安全库存量的计算,将借助于数量统计方面的知识,对顾客需求量的变化和提前期的变化作为一些基本的假设,从而在顾客需求发生变化、提前期发生变化以及两者同时发生变化的情况下,分别求出各自的安全库存量。
1.需求发生变化,提前期为固定常数的情形
先假设需求的变化情况符合正态分布,由于提前期是固定的数值,因而我们可以直接求出在提前期的需求分布的均值和标准差。或者可以通过直接的期望预测,以过去提前期内的需求情况为依据,从而确定需求的期望均值和标准差。这种方法的优点是能够让人容易理解。
当提前期内的需求状况的均值和标准差一旦被确定,利用下面的公式可获得安全库存量SS。
σ
SS=Z L
D
σ---在提前期内,需求的标准方差;
其中:D
L---提前期的长短;
Z ---一定顾客服务水平需求化的安全系数(见下表)
顾客服务水平及安全系数表
例:
某饭店的啤酒平均日需求量为10加仑,并且啤酒需求情况服从标准方差是2加仑/天的正态分布,如果提前期是固定的常数6天,试问满足95%的顾客满意的安全库存存量的大小?
解:由题意知:
σ=2加仑/天,L=6天,F(Z)=95%,则Z=1.65, D
σ=1.65*2.* 6=8.08
从而:SS=Z L
D
即在满足95%的顾客满意度的情况下,安全库存量是8.08加仑。
2.提前期发生变化,需求为固定常数的情形
如果提前期内的顾客需求情况是确定的常数,而提前期的长短是
随机变化的,在这种情况下:SS为
dσ
SS=Z L
其中:Lσ---提前期的标准差;
Z ----一定顾客服务水平需求化的安全系数;
d ----提前期内的日需求量;
例:
如果在上例中,啤酒的日需求量为固定的常数10加仑,提前期是
随机变化的,而且服务均值为6天、标准方差为1.5的正态分的,试
确定95%的顾客满意度下的安全库存量。
解:由题意知:Lσ=1.5天,d=10加仑/天,F(Z)=95%,则
Z=1.65,
dσ=1.65*10.*1.5=24.75
从而:SS= Z L
即在满足95%的顾客满意度的情况下,安全库存量是24.75加仑。
3.需求情况和提前期都是随机变化的情形
在多数情况下,提前期和需求都是随机变化的,此时,我们假设顾客的需求和提前期是相互独立的,则SS 为 SS=Z 22
2L D d L σσ+ 其中: Z ----一定顾客服务水平下的安全系数;
L σ---提前期的标准差;
D σ---在提前期内,需求的标准方差;
d ----提前期内的平均日需求量;
L ---平均提前期水平;
例:
如果在上例中,日需求量和提前期是相互独立的,而且它们的变化均严格满足正态分布,日需求量满足均值为10加仑、标准方差为2加仑的正态分布,提前期满足均值为6天、标准方差为1.5天的正态分布,试确定95%的顾客满意度下的安全库存量。
解:由题意知:D σ=2加仑,L σ=1.5天,d =10加仑/天,L =6天,F(Z)=95%,则Z=1.65,从而:SS=Z
22
2L D d L σσ+=1.65*2225.1*106*2+=26.04 即在满足95%的顾客满意度的情况下,安全库存量是26.04加仑
三、静态安全库存实际使用
首先我们创建3个物料:物料333662设置有安全库存,物料333663没有设置安全,注意两个物料在测试过程中的区别
步骤一:对333662 和333663 初始化库存,均为10(TCODE:MB1C)
步骤二:创建物料BOM(TCODE:CS01)
步骤三:创建成品333661的独立需求为10(TCODE:MD61)
注意:成品的需求是10,成品和组件的比例是1:2,那么对2种原料的需求均为20
步骤四:运行MRP(TCODE:MD01/MD02/MD03)
比较
运行MRP后,对333662产生了20的计划单,对333663产生了10的计划单。因为物料333662设置了安全库存,安全库存的数量为10。
四、动态安全库存实际使用
动态安全库存是在运行MRP时才被计算。SAP系统计算动态安全库存的公式:平均日需求* 覆盖范围
注释:覆盖范围指在没有货物供应的情况下,靠库存来维持正常生产的天数。
求平均日需求的公式:特定时期内的总需求/ 除以特定时期内的工作天数
使用安全库存的前提是:
在MRP2中维护‘覆盖参数文件’
配置该参数文件:IMG—>生产—>物料需求计划→计划→MRP计算→定义覆盖范围参数文件(动态安全库存)
A.平均日需求:
为计算平均日需求,必须维护下面的字段:
期间标识、期间数、期间长度类型,每个期间天数<可选> 说明:
B .定义覆盖范围:你可以为每期定义一个目标覆盖天数,图中第一期的目标覆盖天数为3。你也可以定义一个范围,也就是指定其最小值 和 最大值。在运行MRP 时,系统会采用‘库存可用量/平均日需求’来计算覆盖天数。如果计算出来的覆盖天数没在定义的覆盖范围内,则系统以定义‘目标覆盖天数’来计算安全库存
C .计算动态安全库存:下面以一个例子来讲解。
第一步:配置覆盖范围参数(略)--见前面的图
第二步:在MRP2中设置参数文件(略)--见前面的图
第三步:创建成品333661的需求 TCODE : MD61
如图分别创建了1-6月的独立需求,因为在后面配置中‘期间标识’为M ,‘期间数’为2,所以1、2月为第一期;3、4月为第二期;5、
6月为第三期,同时第一期的目标覆盖天数为3,第二期的目标覆盖天数为5;第三期的目标覆盖天数为6。
注意:图中的划分看上去好像正确,其实是错误的划分。因为图中定义的产品独立需求,在本文中我们只给原料333662设置了安全库存。
D.运行MRP TCODE :MD02
注意:成品的自制天数为10天。
我们来分析这个图:(验证动态安全计算是否正确)
A.验证1月这里的总需求为1月的需求+ 2月的需求
1月成品的计划是500,所以对333662原料的需求为1000。
平均日需求= 特定时期的总需求/ 特定时期内的工作日= (1000 + 2000 +3000)/ (2*5) =600
第一期的覆盖天数为3
所以动态安全库存为600 * 3=1800
因为需求为1000,安全库存为1800,现有库存为10 所以还需采购1000+1800 – 10=2790.于是产生了2790的采购计划。
B.验证2月,这里的总需求为2月的需求+ 3月的需求
平均日需求= 特定时期的总需求/ 特定时期内的工作日= (3000 + 1000)/ (2 * 5) = 400
第二期的覆盖天数为5
所以动态安全库存为400 * 5 = 2000
实际需求是3000 本月的动态库存为2000,可以库存为1800 所以还需采购3000+2000 -1800 = 3200
于是产生3200的采购计划。
……………..
C.验证5月,这里的总需求为5月的需求+ 6月的需求,因为没创建6月的需求,所以6月的需求为0
平均日需求=特定时期的总需求/ 特定时期内的工作日= (1200 + 0)/ (2 * 5)=120
该期的覆盖天数为6天
实际需求为1200 本月的动态安全库存为720 可用库存为1920 所以还需采购1200+ 720 – 1920 =0
因此5月不需要产生采购计划。
根据我们的分析分析结果和系统运行出来的结果完全一样,根据上面的分析可以发现安全库存在不同时期,其安全库存数量也在变化,这就叫动态安全库存。
附件:动态安全(英文参
考资料)。本文关于动态安全库存的配置和操作,都是
参考该资料
(完整word版)安全库存管理制度
安全库存管理制度 1.目的: 为规范本公司生产需要的零部件库存管理,保证供应安全,便于生产有序开展,特制订本制度。 2.范围: 适用于公司所需零部件及耗材等(包括辅助用品、设备配件等)的管理储备。 3.权责: 3.1仓库作为公司安全库存管理工作的实物管理部门,负责根据技术部牵头制定的标准数据及时对安全库存的设置进行更新;负责监控已设置了安全库存物料的库存情况; 3.2采购部负责根据各部门提出的申购单,采购零部件保障外部的供应;3.3标准件设计的库存量由技术部牵头确定,由标准件专员负责与设计、生管以及仓库核对数据,根据生产任务、销售预测等需求设置安全库存;并负责完成审批流程; 3.4制造部生管参与安全库存的设定,并负责内制件外发加工的审请和转变申请; 3.5技术部经理负责新增标准件的安全库存量初次设置以及库存件减量审批。 3.6 生产副总负责安全库存数量的增量审批以及内制转外发件的最终审批。 3.7 制造部生管以及仓库有责任对运行中的库存量提出变更申请,以保障稳定供应。 4.名词定义:
4.1安全库存:指为了防止由于不确定因素(如突发性大量订货或供应商延期交货)影响订货需求而准备的缓冲库存,安全库存用于满足生产基本需求,提前准备零部件。 4.2采购周期:采购周期是指采购方决定订货并下订单-供应商确认-供应商生产-发运到货(含第三方物流)的整个周期时间。 5.作业内容:设置安全库存、变更安全库存及取消安全库存的审批要求5.1新标准件库存设置:设计科负责标准件设计,由标准件专员提出零部件安全库存上限、下限,技术部门负责人审批后,书面发送仓库及关联部门,更新安全库存物料清单; 5.1.1安全库存标准设置的基本原则: 5.1.1.1临时性测试验证:以备件形式下发,安全库存上限、下限在30-50件范围; 5.1.1.2验证合格的标准件:按不同物料规格,制定1.5个月的平均用量为下限,上限为不超过两倍的下限值,如果高价值和大体积的物料,以下限1.5倍的数量作为上限(例如电机);用量大、小价值且小体积的外购国标件,可以放宽到3个月的上限库存量(例如螺钉)。 5.1.1.3根据采购周期的不同,考虑供应的连续性,对于采购周期大于两周的材料或者零件,安全库存的下限数量要大于两倍采购周期内的使用量。上限取下限数量的1.5倍进行控制。 5.2为了提高生产效率节约公司成本,各部门在了解到外制成本质量更优于内制时,可由生管申请将内制件转换为外购物料,或者将外购零件转换为内制零件,需生产副总最终批准。仓库接到书面批准单据后,按照安全库存的
安全库存管理办法
安全库存管理办法 一、目的 为规范安全库存管理工作,保证公司各部门正常工作的开展,特制订本制度。 二、适用范围 适用于公司所需主要原辅材料和其他一般性耗材(包括辅助用品、设备配件、办公用品等)的物料储备。 三、内容 安全库存:指为了防止由于不确定因素(如突发性大量订货或供应商延期交货)影响订货需求而准备的缓冲库存,安全库存用于满足提前期需求。 采购周期:采购周期是指采购方决定订货并下订单-供应商确认-供应商生产-发运到货(有时为第三方物流)的整个周期时间。 四、职责 (一)储运部作为公司安全库存管理工作的直接承担者,负责录入各类相关数据,保证数据的准确性、及时性;对安全库存的设置进行计算;负责每季度组织生产部、销售部、采购部对安全库存的设置进行更新;负责监控设置了安全库存物料的库存情况; (二)采购部负责根据库房提供的和自身记录的各类数据,根据请购单实施采购活动; (三)其他部门负责根据生产任务、销售预测等需求提出安全库
存需求; (四)财务部负责对安全库存的设定进行监管。 (五)库房、生产、销售、采购共同对安全库存的设置和变更做会签。 五、设置安全库存、变更安全库存及取消安全库存的审批要求 (一)安全库存物料项目的增加 1、当出现以下情况时,仓库负责填制《安全库存物料变更表》以增加安全库存项目,并负责完成审批流程: 2、某物料连续三个月使用量递增或稳定; 3、需求部门提出增加安全库存项目; (二)增加安全库存项目的审批人及审批内容: 1、储运部:负责审核由各库房提供的需设置安全库存项目的物料的连续三个月的使用量,并确定设置安全库存上、下限数量及安全库存数量; 2、生产经理:负责审核涉及生产使用的需要新增安全库存项目的物料,并审核该物料的名称、规格、型号、安全库存上、下限、安全库存数量是否符合生产活动的实际需要; 3、技术经理:负责审核涉及生产使用的需要新增安全库存项目的物料,并审核该物料的名称、规格、型号是否适当,并能够满足生产加工的技术要求; 4、采购经理:负责审核所有新增安全库存项目的物料、确定采购周期并审核该安全库存物料设置数量是否适当(最小起订量、最小
SAP四种安全库存的设置
安全库存只是一个笼统的说法,本文归纳了SAP四种安全库存(时间)的设置,用于增加 计划过程中库存数量(时间)的弹性。为何安全库存能增加计划的弹性呢?因为在净需求计 算(Net Requirements Calculation ) 中,Quantity available = Fixed receipts + Stock available for planning - Safety stock - requirements,若可用数量小于零,则报缺料,视为短缺数量(Shortage quantity )或需求数量(Net requriements),将用于批量计算并得出最终的获取建议。 Safety stock Safety stock partially available Dyn amic safety stock Safety time 一、Safety stock 这就是安全库存”了,安全库存的数量在计划中是不可用的。MRP中,若物料的数量低于安全库存水平,就会产生计划订单。安全库存在物料主数据MRP2视图设置。 二、Safety stock partially available 如果设置了安全库存,一低于该水平就会产生补货的请求,哪怕只是缺了一点,这增加了计 划的工作量。为了弥补这个不足,我们可以在MRP Group中设置一个百分比,只有安全库 存低于该百分比,补货请求方会产生。 三、Dynamic safety stock 动态安全库存就更加厉害了,它根据平均的日需求(Average daily requirements )数量,来确定未来几个时期的安全库存水平(数量等于若干个平均日需求) :最小库存、目标库存、最 大库存。若小于最小库存,产生补货请求至目标库存;若大于最大库存,系统将提示例外信息。若同时设置了安全库存,将累加。该配置称为Range of Coverage Profile,在MRP2 视图分配,配置在IMG: Production - MRP - Planning - MRP Calculation - Define Range of Coverage Profile (Dynamic Safety Stock)。 四、Safety time 前面三种方案都是对安全库存数量上的设置,Safety time则是设置时间上的余量。物料的补 货提议时间将提前于实际的需求时间,提前日期在MRP2视图中配置。考虑到物料可能用 在产品的不同层次,为了避免重复提前,可以在MRP2视图的Safety time indicator栏位设 置安全时间有效于所有需求还是仅相关需求,或者干脆无效。而考虑到不同时期对安全时间 的长度要求不同,可以在后台定义Period Profile,IMG: Production - MRP - Planning - MRP Calculation - Define Period Profile for Safety Time/Actual Range of Coverage ,并在MRP2 视图 分配给物料。 注意:百分比是根据MPR组设置的,在后台:Define Safety Stock Availability 。 从我的测试结果来看,系统计算的顺序是:Safety Stock --------------- >实际需求---- 〉Dynamic Safety
安全库存管理制度最新版
安全库存管理制度 1、目的 为防止可知和不可知因素的影响,设定安全库存,以保证生产的如期正常进行。 2、适用范围 适用于公司所需主要原辅材料和其他一般性耗材(包括辅助用品、设备配件、办公用品等)的物料储备。 3、术语 安全库存:指为了防止由于不确定因素(如突发性大量订货或供应商延期交货)影响订货需求而准备的缓冲库存,安全库存用于满足提前期需求。 采购周期:采购周期是指采购方决定订货并下订单-供应商确认-供应商生产-发运到货(有时为第三方物流)的整个周期时间。 4、职责 (1)库房负责录入各类相关数据,保证数据的准确性、及时性,为采购部做关于安全库存的各种决策提供准确的数据支持;对安全库存的设置进行计算;负责每月/每季度①组织生产部、销售部、采购部对安全库存的设置进行更新;负责监控设置了安全库存物料的库存情况; (2)采购部负责根据库房提供的和自身记录的各类数据,根据请购单实施采购活动; (3)其他部门负责根据生产任务、销售预测等需求提出安全库存需求; (4)生产经理负责对安全库存的设定进行监管。 5、工作流程 (1)库房按照现有数据对部分库存物料设置安全库存; (2)库房及时、准确录入各类数据; (3)库房根据一段时期内(一般以月度/季度为周期)的物料使用情况、公司各部门的预测或申报(如销售部的市场预测、工程部对设备零配件的需求等)对安全库存的限额进行调整,并报送副总经理审核; (4)副总经理审核;
(5)执行批准后新的安全库存标准,并重复第2-6项工作。 6、安全库存制定标准 (1)标准计算方法为: 安全库存=日平均消耗量×一定服务水平下的前置期标准差 (2)受实际情况限制,我司目前暂时采用以下计算方法: 安全库存=日平均消耗量×采购周期×调整系数 其中:日平均消耗量由库房提供数据;采购周期、调整系数由采购部测算。 7、安全库存物料项目的增加和删减 (1)安全库存物料项目的增加 当某一物料连续3个月的使用量递增或维持在一定水平上时,库房填写《安全库存物料变更表》,提出将此物料的安全库存限额提高或由非安全库存物料变为安全库存物料的建议,以下为审批流程: (2)安全库存物料项目的删减 当遇到以下情况之一时,由库房填写《安全库存物料变更表》,提出将此物料安全库存额度降低或由安全库存物料转为按需采购物料的建议:某一物料连续3个月的使用量递减或很小; 生产、技术、工程、行政等部门对某一物料给出使用量减小或停止采购的正式指令(可以是书面指令、腾讯通对话等,口头通知无效); 以下为审批流程:
安全库存管理办法
安全库存管理办法 1、目的 为规范安全库存管理工作,保证公司各部门正常工作的开展,特制订本制度。 2、适用范围 适用于公司所需主要原辅材料和其他一般性耗材(包括辅助用品、设备配件、办公用品等)的物料储备。 3、术语 安全库存:指为了防止由于不确定因素(如突发性大量订货或供应商延期交货)影响订货需求而准备的缓冲库存,安全库存用于满足提前期需求。 采购周期:采购周期是指采购方决定订货并下订单-供应商确认-供应商生产-发运到货(有时为第三方物流)的整个周期时间。 4、职责 4.1库房作为公司安全库存管理工作的直接承担者,负责录入各类相关数据,保证数据的准确性、及时性;对安全库存的设置进行计算;负责每季度组织生产部、销售部、采购部对安全库存的设置进行更新;负责监控设置了安全库存物料的库存情况; 4.2采购部负责根据库房提供的和自身记录的各类数据,根据请购单实施采购活动; 4.3其他部门负责根据生产任务、销售预测等需求提出安全库存需求; 4.4生产事业部总经理负责对安全库存的设定进行监管。 4.5 库房、生产、销售、采购、计划部共同对安全库存的设置和变更做会签。 5、设置安全库存、变更安全库存及取消安全库存的审批要求 5.1安全库存物料项目的增加 5.1.1当出现以下情况时,库房负责填制《安全库存物料变更表》以增加安全库存项目,并负责完成审批流程: 5.1.1.1某物料连续三个月使用量递增或稳定; 5.1.1.2需求部门提出增加安全库存项目; 5.1.2增加安全库存项目的审批人及审批内容:
5.1.2.1库房经理:负责审核由各库房提供的需设置安全库存项目的物料的连续三个月的使用量,并确定设置安全库存上、下限数量及安全库存数量; 5.1.2.2生产经理:负责审核涉及生产使用的需要新增安全库存项目的物料,并审核该物料的名称、规格、型号、安全库存上、下限、安全库存数量是否符合生产活动的实际需要; 5.1.2.3技术经理:负责审核涉及生产使用的需要新增安全库存项目的物料,并审核该物料的名称、规格、型号是否适当,并能够满足生产加工的技术要求; 5.1.2.4总经办主任:负责审核办公用品、劳保用品的新增安全库存项目的物料,并审核该物料是否需要设置安全库存、设置的数量是否适当; 5.1.2.5采购经理:负责审核所有新增安全库存项目的物料、确定采购周期并审核该安全库存物料设置数量是否适当(最小起订量、最小包装、)、确定采购周期; 5.1.2.6生产事业部总经理:负责审核生产用料增加安全库存项目的审批; 5.1.2.7计划运营部总监:负责审核所有《安全库存物料变更申请单》; 5.2变更安全库存上限及安全库存量 5.2.1发生以下情况时,可对安全库存上限及安全库存量进行变更 5.2.1.1设置安全库存的物料使用量连续三个月发生递增或递减,由库房发起变更流程; 5.2.1.2需求部门提出增加或减少安全库存上限、安全库存量的要求; 5.2.1.3当发生生产工艺改变而需要增加或减少安全库存上限、安全库存量时,由生产部门发起变更流程; 5.2.2增加或减少安全库存上限、安全库存量的审批人及审批内容: 5.2.2.1库房经理:负责审核由各库房提供的需设置安全库存项目的物料的连续三个月的使用量,并确定变更后的安全库存上、下限数量及安全库存数量; 5.2.2.2生产经理:负责审核涉及生产使用的需要变更安全库存上、下限、安全库存数量的主要辅料及原材料,并审核该物料的名称、规格、型号、安全库存上限、安全库存数量是否符合生产活动的实际需要; 5.2.2.3总经办主任:负责审核办公用品、劳保用品的变更安全库存上限、安全库存数量的物料,并审核该物料是否需要变更安全库存、及变更的数量是否适
安全库存设置流程
目的:规范和指导安全库存设置流程,确保安全库存合理、严谨 适用范围:所有零件 流程 1.PFEP及时提供零件现场最大库存; 2.安全库存计算原则: 国产件安全库存=PIECE BANK+HOUR BANK 进口件安全库存=WEEKLY BANK 注:2.1 应充分考虑LOC存放空间,合理取值。 2.2 PIECE BANK 2.2.1 国产物料 ●依据生产计划,所有物料取1天需求 ●二级底料,1天需求+1个包装 ●若为大包装零件,取现场最大库存数量和3天需求中的最大值 2.2.2 进口物料 ●C KD零件按照单价不同进行分类。根据单价不同,结合不同的 标准包装数量以及不同零件的特殊故事最终确定PIECE BANK和 WEEKLY BANK。 ●例如, ●单价>50元的CKD零件。令A=周末1.2周,B=包装(订货包装) *2,X=特殊故事的零件需要增加的PIECE BANK。计算方法为: 如果A+X >B,保留WEEKLY BANK=A 取值和PIECE BANK=X 取值; 反之,PIECE BANK取值为B-A,WEEKLY BANK=A 取值不变。 ●
●另外,如果在未来按日历日有放假等原因停产,在CKD件MRD到 达该停产日前,增加weekly bank:停产日为N,周工作日为M, N/M=增加weekly bank周数。CKD件MRD过了停产日后,减掉增 加的weekly bank数。 2.3 HOUR BANK 2.3.1 国产物料 ●A类外地物料取1天 ●B/C类取2天 ●底料相应增加1天 2.3.2 进口物料 ●价值在1RMB以下,周初3周 ●价值在1-5RMB,周初2.5周 ●价值在5-25RMB,周初2.4周 ●价值在25-50RMB,周初2.3周 ●价值在50RMB以上,周初2.2周 2.4 物料需求取当月产量的平均值。 2.5 安全库存设置以计算结果为参考值。 3.断点新旧零件安全库存设置(参见《断点控制流程》) 3.1 据断点预测期定期盘点旧零件库存。 3.2 F/U发布旧零件最后一张PUS时,设置新零件安全库存,并保证断点新零 件的安全库存在断点使用前已建立。 4.安全库存需要更改,由F/U填写《安全库存更改申请单》,经物料计划股主 管和生产计划与控制室经理批准签字,由Scheduler导入SAP系统,同时存档更改的相关凭证; 5.安全库存设置必须保持严谨合理,设置后应注意观察其引起的库存及需求
安全库存管理流程规定
安全库存管理规定版本版次A/0 页码共2页第1页生效日期2013年4月24日 1.目的 为了保证零部件的及时供应,建立完善的安全库存管理体系,特制订本规定。2.范围 适用于公司各仓库用于生产的自制件半成品和成品、外购件以及外协件。 3.职责 3.1 计划科负责编制《月度采购计划》,采购科根据附件一《零部件采购周期/安全库存汇总表》进行审核,如实际采购周期与附件一发生冲突,则通知计划科按实际情况进行修改; 3.2各仓库根据附件一《零部件采购周期/安全库存汇总表》定期核定安全库存的零部件,当零部件库存量低于1000台安全库存预警线时,仓库立即报采购科,当低于600台安全库存预警线时,仓库立即报计划科; 3.3采购科和计划科在接到各仓库安全库存预警申报后,应立即采取补货或调货的措施并跟催到货情况。 4.绩效考核 4.1在执行过程中,如果因相关责任仓库管理员没有及时核定并告知采购科、计划科某零部件库存量低于安全库存预警线,因此造成后续生产出现断料、停工等影响,相关责任仓库管理员应承担相应责任; 4.2在执行过程中,如果因采购科、计划科在接到仓库管理员某零部件库存量低于安全库存预警通知后,未采取有效措施进行补货或调货,而造成后续生产出现断料、停工等影响,采购科、计划科主管责任人应承担相应责任。 5.附则 本规定自发布之日起实施
安全库存管理规定 版本版次 A/0 页 码 共2页 第2页 生效日期 2013年4月24日 6.流程图 注:YES/NO ——表示供应商是否可以按期到货或完成订单; 编制 审核 批准 日期 日期 日期 会签 发放 仓库定期核定 安全库存 采购科 执行未完成订单 YES NO 计划科 跟催采购计划订单 需求计划不足,下达增补计划 低于1000台 低于600台 2个工作日内,汇报上级领导
安全库存管理规范(含表格)
安全库存管理规范 (ISO9001-2015) 1、目的 为规范安全库存管理工作,保证公司各部门正常工作的开展,特制订本制度。 2、适用范围 适用于公司所需主要原辅材料和其他一般性耗材(包括辅助用品、设备配件、办公用品等)的物料储备。 3、术语 安全库存:指为了防止由于不确定因素(如突发性大量订货或供应商延期交货)影响订货需求而准备的缓冲库存,安全库存用于满足提前期需求。 采购周期:采购周期是指采购方决定订货并下订单-供应商确认-供应商生产-发运到货(有时为第三方物流)的整个周期时间。 4、职责 4.1库房作为公司安全库存管理工作的直接承担者,负责录入各类相关数据,保证数据的准确性、及时性;对安全库存的设置进行计算;负责每季度组织生产部、销售部、采购部对安全库存的设置进行更新;负责监控设置了安全库存物料的库存情况; 4.2采购部负责根据库房提供的和自身记录的各类数据,根据请购单实施采购活动;
4.3其他部门负责根据生产任务、销售预测等需求提出安全库存需求; 4.4生产事业部总经理负责对安全库存的设定进行监管。 4.5 库房、生产、销售、采购、计划部共同对安全库存的设置和变更做会签。 5、设置安全库存、变更安全库存及取消安全库存的审批要求 5.1安全库存物料项目的增加 5.1.1当出现以下情况时,库房负责填制《安全库存物料变更表》以增加安全库存项目,并负责完成审批流程: 5.1.1.1某物料连续三个月使用量递增或稳定; 5.1.1.2需求部门提出增加安全库存项目; 5.1.2增加安全库存项目的审批人及审批内容: 5.1.2.1库房经理:负责审核由各库房提供的需设置安全库存项目的物料的连续三个月的使用量,并确定设置安全库存上、下限数量及安全库存数量; 5.1.2.2生产经理:负责审核涉及生产使用的需要新增安全库存项目的物料,并审核该物料的名称、规格、型号、安全库存上、下限、安全库存数量是否符合生产活动的实际需要; 5.1.2.3技术经理:负责审核涉及生产使用的需要新增安全库存项目的物料,并审核该物料的名称、规格、型号是否适当,并能够满足生产加工的技术要求; 5.1.2.4总经办主任:负责审核办公用品、劳保用品的新增安全库存项目的物料,并审核该物料是否需要设置安全库存、设置的数量是否适当;
安全库存管理流程规定
编号:SY-AQ-05967 ( 安全管理) 单位:_____________________ 审批:_____________________ 日期:_____________________ WORD文档/ A4打印/ 可编辑 安全库存管理流程规定 Safety stock management process
安全库存管理流程规定 导语:进行安全管理的目的是预防、消灭事故,防止或消除事故伤害,保护劳动者的安全与健康。在安全管理的四项主要内容中,虽然都是为了达到安全管理的目的,但是对生产因素状态的控制,与安全管理目的关系更直接,显得更为突出。 安全库存管理规定 文件编号 FD/PD-0401R 版本版次 A/0 页码 共2页第1页 生效日期 2013年4月24日 1.目的 为了保证零部件的及时供应,建立完善的安全库存管理体系,特制订本规定。 2.范围
适用于公司各仓库用于生产的自制件半成品和成品、外购件以及外协件。 3.职责 3.1计划科负责编制《月度采购计划》,采购科根据附件一《零部件采购周期/安全库存汇总表》进行审核,如实际采购周期与附件一发生冲突,则通知计划科按实际情况进行修改; 3.2各仓库根据附件一《零部件采购周期/安全库存汇总表》定期核定安全库存的零部件,当零部件库存量低于1000台安全库存预警线时,仓库立即报采购科,当低于600台安全库存预警线时,仓库立即报计划科; 3.3采购科和计划科在接到各仓库安全库存预警申报后,应立即采取补货或调货的 措施并跟催到货情况。 4.绩效考核 4.1在执行过程中,如果因相关责任仓库管理员没有及时核定并告知采购科、计划科某零部件库存量低于安全库存预警线,因此造
安全库存概念和计算方法
什么是安全库存 安全库存(又称保险库存,德文:Sicherheitsbestand)是指当不确定因素(订货期间需求增长、到货延期等)已导致更高的预期需求或导致完成周期更长时的缓冲存货,安全库存用于满足提前期需求。在给定安全库存的条件下,平均存货可用订货批量的一半和安全库存来描述。 安全库存的确定是建立在数理统计理论基础上的。首先,假设库存的变动是围绕着平均消费速度发生变化,大于平均需求量和小于平均需求量的可能性各占一半,缺货概率为50%。 安全库存越大,出现缺货的可能性越小;但库存越大,会导致剩余库存的出现。应根据不同物品的用途以及客户的要求,将缺货保持在适当的水平上,允许一定程度的缺货现象存在。安全库存的量化计算可根据顾客需求量固定、需求量变化、提前期固定、提前期发生变化等情况,利用正态分布图、标准差、期望服务水平等来求得。 安全库存的原则 1、不缺料导致停产(保证物流的畅通); 2、在保证生产的基础上做最少量的库存; 3、不呆料。 怎么确定哪些物料需要定安全库存[1] 运用A.B.C分析法确定了物料的A,B,C等级后根据A,B,C等级来制订库存: A类料:一般属于成本较高,占整个物料成本的65%左右,可采用定期定 购法,尽量没有库存或只做少量的安全库存.但需在数量上做严格的控制。 B类料:属于成本中等,占整个物料成本的25%左右,可采用经济定量采 购的方法,可以做一定的安全库存。 C类料:其成本最少,占整个物料成本的10%左右,可采用经济定量采购 的方式,不用做安全库存,根据采购费用和库存维持费用之和的最低点,订出一次的采购量。 怎么降低“安全”库存 1、订货时间尽量接近需求时间. 2、订货量尽量接近需求量 3、库存适量
SAP四种安全库存的设置
安全库存只是一个笼统的说法,本文归纳了SAP 四种安全库存(时间)的设置,用于增加 计划过程中库存数量(时间)的弹性。为何安全库存能增加计划的弹性呢?因为在净需求计 算(Net Requirements Calculation )中,Quantity available = Fixed receipts + Stock available for planning - Safety stock - requirements ,若可用数量小于零,则报缺料,视为短缺数量(Shortage quantity )或需求数量(Net requriements),将用于批量计算并得出最终的获取建议。 Safety stock Safety stock partially available Dynamic safety stock Safety time 一、Safety stock 这就是“安全库存”了,安全库存的数量在计划中是不可用的。MRP 中,若物料的数量低于 安全库存水平,就会产生计划订单。安全库存在物料主数据MRP2 视图设置。 二、Safety stock partially available 如果设置了安全库存,一低于该水平就会产生补货的请求,哪怕只是缺了一点,这增加了计划的工作量。为了弥补这个不足,我们可以在MRP Group 中设置一个百分比,只有安全库存低于该百分比,补货请求方会产生。 三、Dynamic safety stock 动态安全库存就更加厉害了,它根据平均的日需求(Average daily requirements )数量,来确定未来几个时期的安全库存水平(数量等于若干个平均日需求):最小库存、目标库存、最 大库存。若小于最小库存,产生补货请求至目标库存;若大于最大库存,系统将提示例外信息。若同时设置了安全库存,将累加。该配置称为Range of Coverage Profile ,在MRP2 视图分配,配置在IMG: Production - MRP - Planning - MRP Calculation - Define Range of Coverage Profile (Dynamic Safety Stock) 。 四、Safety time 前面三种方案都是对安全库存数量上的设置,Safety time 则是设置时间上的余量。物料的补货提议时间将提前于实际的需求时间,提前日期在MRP2 视图中配置。考虑到物料可能用 在产品的不同层次,为了避免重复提前,可以在MRP2 视图的Safety time indicator 栏位设置安全时间有效于所有需求还是仅相关需求,或者干脆无效。而考虑到不同时期对安全时间的长度要求不同,可以在后台定义Period Profile ,IMG: Production - MRP - Planning - M RP Calculation - Define Period Profile for Safety Time/Actual Range of Coverage ,并在MRP2 视图分配给物料。 注意:百分比是根据MPR 组设置的,在后台:Define Safety Stock Availability 。 从我的测试结果来看,系统计算的顺序是:Safety Stock——〉实际需求——〉Dynamic Safety Stock,然后提前Safety Time 的时间来产生相应采购申请