轿车车身异响分析与预防控制
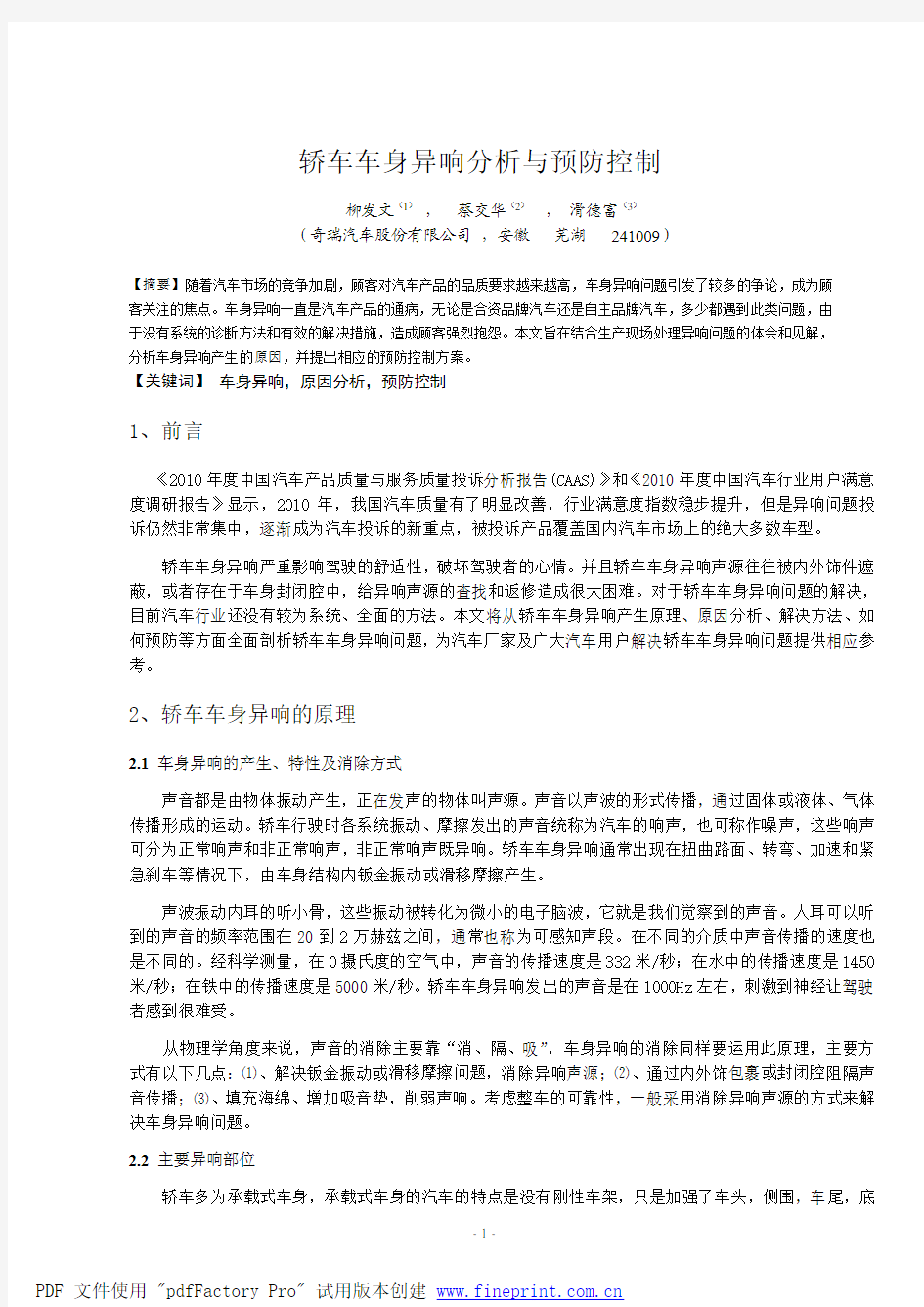
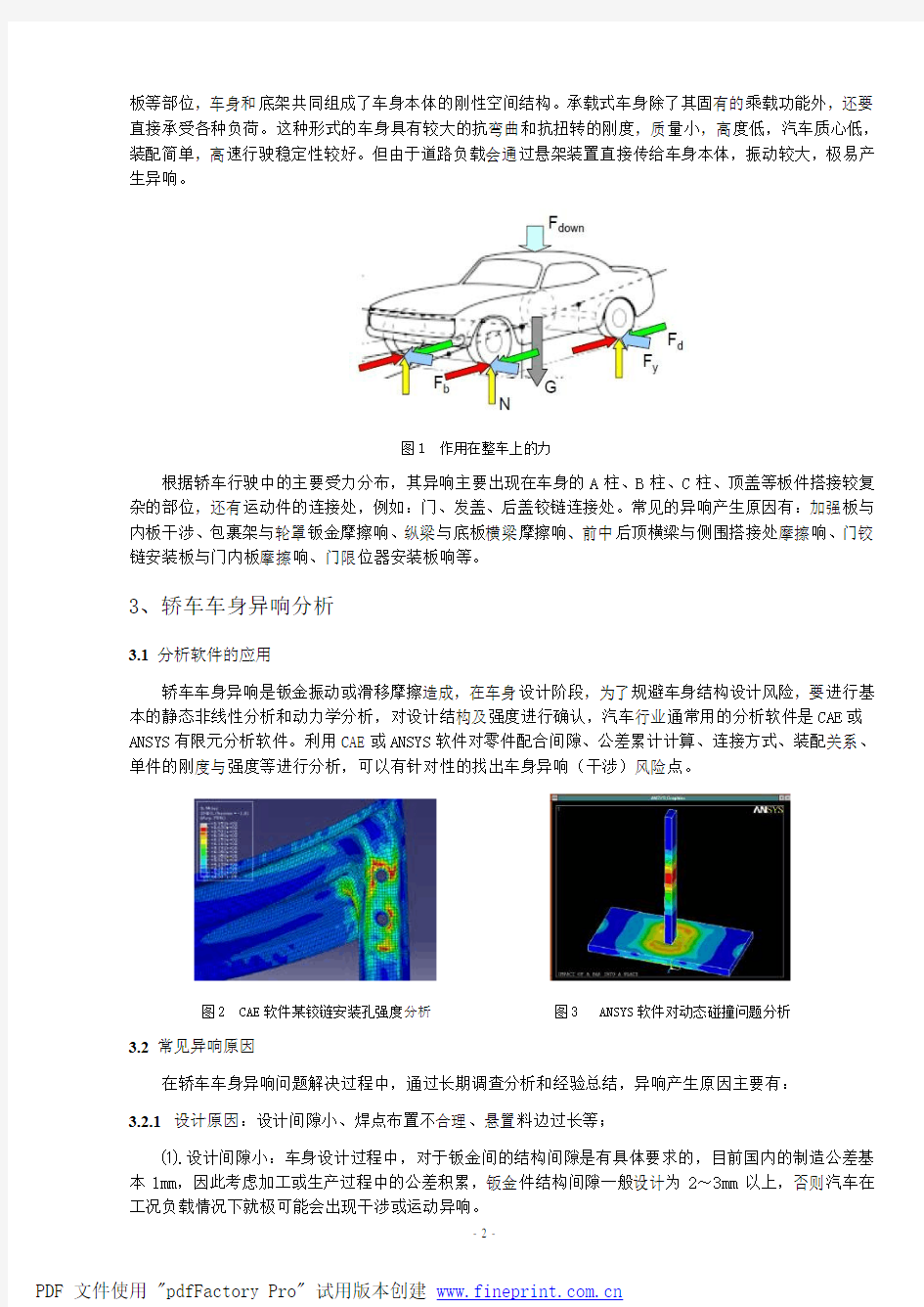
轿车车身异响分析与预防控制
柳发文(1),蔡交华(2),滑德富(3)
(奇瑞汽车股份有限公司,安徽芜湖 241009)
【摘要】随着汽车市场的竞争加剧,顾客对汽车产品的品质要求越来越高,车身异响问题引发了较多的争论,成为顾
客关注的焦点。车身异响一直是汽车产品的通病,无论是合资品牌汽车还是自主品牌汽车,多少都遇到此类问题,由
于没有系统的诊断方法和有效的解决措施,造成顾客强烈抱怨。本文旨在结合生产现场处理异响问题的体会和见解,
分析车身异响产生的原因,并提出相应的预防控制方案。
【关键词】车身异响,原因分析,预防控制
1、前言
《2010年度中国汽车产品质量与服务质量投诉分析报告(CAAS)》和《2010年度中国汽车行业用户满意度调研报告》显示,2010年,我国汽车质量有了明显改善,行业满意度指数稳步提升,但是异响问题投诉仍然非常集中,逐渐成为汽车投诉的新重点,被投诉产品覆盖国内汽车市场上的绝大多数车型。
轿车车身异响严重影响驾驶的舒适性,破坏驾驶者的心情。并且轿车车身异响声源往往被内外饰件遮蔽,或者存在于车身封闭腔中,给异响声源的查找和返修造成很大困难。对于轿车车身异响问题的解决,目前汽车行业还没有较为系统、全面的方法。本文将从轿车车身异响产生原理、原因分析、解决方法、如何预防等方面全面剖析轿车车身异响问题,为汽车厂家及广大汽车用户解决轿车车身异响问题提供相应参考。
2、轿车车身异响的原理
2.1车身异响的产生、特性及消除方式
声音都是由物体振动产生,正在发声的物体叫声源。声音以声波的形式传播,通过固体或液体、气体传播形成的运动。轿车行驶时各系统振动、摩擦发出的声音统称为汽车的响声,也可称作噪声,这些响声可分为正常响声和非正常响声,非正常响声既异响。轿车车身异响通常出现在扭曲路面、转弯、加速和紧急刹车等情况下,由车身结构内钣金振动或滑移摩擦产生。
声波振动内耳的听小骨,这些振动被转化为微小的电子脑波,它就是我们觉察到的声音。人耳可以听到的声音的频率范围在20到2万赫兹之间,通常也称为可感知声段。在不同的介质中声音传播的速度也是不同的。经科学测量,在0摄氏度的空气中,声音的传播速度是332米/秒;在水中的传播速度是1450米/秒;在铁中的传播速度是5000米/秒。轿车车身异响发出的声音是在1000Hz左右,刺激到神经让驾驶者感到很难受。
从物理学角度来说,声音的消除主要靠“消、隔、吸”,车身异响的消除同样要运用此原理,主要方式有以下几点:⑴、解决钣金振动或滑移摩擦问题,消除异响声源;⑵、通过内外饰包裹或封闭腔阻隔声音传播;⑶、填充海绵、增加吸音垫,削弱声响。考虑整车的可靠性,一般采用消除异响声源的方式来解决车身异响问题。
2.2主要异响部位
轿车多为承载式车身,承载式车身的汽车的特点是没有刚性车架,只是加强了车头,侧围,车尾,底
板等部位,车身和底架共同组成了车身本体的刚性空间结构。承载式车身除了其固有的乘载功能外,还要直接承受各种负荷。这种形式的车身具有较大的抗弯曲和抗扭转的刚度,质量小,高度低,汽车质心低,装配简单,高速行驶稳定性较好。但由于道路负载会通过悬架装置直接传给车身本体,振动较大,极易产生异响。
图1 作用在整车上的力
根据轿车行驶中的主要受力分布,其异响主要出现在车身的A柱、B柱、C柱、顶盖等板件搭接较复杂的部位,还有运动件的连接处,例如:门、发盖、后盖铰链连接处。常见的异响产生原因有:加强板与内板干涉、包裹架与轮罩钣金摩擦响、纵梁与底板横梁摩擦响、前中后顶横梁与侧围搭接处摩擦响、门铰链安装板与门内板摩擦响、门限位器安装板响等。
3、轿车车身异响分析
3.1分析软件的应用
轿车车身异响是钣金振动或滑移摩擦造成,在车身设计阶段,为了规避车身结构设计风险,要进行基本的静态非线性分析和动力学分析,对设计结构及强度进行确认,汽车行业通常用的分析软件是CAE或ANSYS有限元分析软件。利用CAE或ANSYS软件对零件配合间隙、公差累计计算、连接方式、装配关系、单件的刚度与强度等进行分析,可以有针对性的找出车身异响(干涉)风险点。
图2 CAE软件某铰链安装孔强度分析图3 ANSYS软件对动态碰撞问题分析
3.2常见异响原因
在轿车车身异响问题解决过程中,通过长期调查分析和经验总结,异响产生原因主要有:
3.2.1设计原因:设计间隙小、焊点布置不合理、悬置料边过长等;
⑴.设计间隙小:车身设计过程中,对于钣金间的结构间隙是有具体要求的,目前国内的制造公差基本1mm,因此考虑加工或生产过程中的公差积累,钣金件结构间隙一般设计为2~3mm以上,否则汽车在工况负载情况下就极可能会出现干涉或运动异响。
同时在产品数据校核时,往往对典型截面或特定结构进行分析,从而忽略了弧面与平面、点与面、面与面配合、线与面配合的配合间隙,导致配合间隙过小,甚至干涉。弧面与平面、点与面的配合在尽量避免,实在无法避免此类的配合时,要考虑设定较大的间隙或CO2工艺。面与面配合或线与面配合时,尽量设计成平行状态,如无法避免两个面或线与面的倾斜,在考虑间隙时,必须以最小处间隙为准,一般大于
2.5mm 。
图4 某结构钣金配合间隙小
⑵.焊点布置不合理:焊点布置不合理是造成焊接失效的主要原因。焊点布置在圆角拐弯处或不平整处,由于焊钳在焊接时的压力比较大,易在圆角拐角处或不平整的部位产生焊接变形。
另外,一般情况下,采用三层板或者三层以上的焊接结构,若没有通过使用工艺缺口以进行二层板焊接来代替三层板,三层板等直径通孔使用CO2塞焊易造成虚焊。
图5 某车型结构弧面焊点布置间距大
⑶.悬置料边过长:为了满足车身安全要求,同时降低车重,对于车身工况下应力分布集中部位,设计人员会尽量考虑采用整体多层次构架、局部加强的设计方式。这样就导致车身内外板、各加强板等搭接结构复杂。车身钣金搭接边设计时,易有长距离料边悬置(无任何连接),长距离料边悬置可能振动异响或与周围结构摩擦异响。下面这种设计结构就属于这种情况
:
图7 某车型B 柱加强板悬臂过长
3.2.2制造原因:冲压件制件不合格、装焊偏差累计等造成的冲焊件尺寸形状偏差问题
1.13mm
Z 向剖面图
L=200mm ,此种
结构存在很大异
响风险
X 向剖面图
冲压件制件过程中通常存在尺寸毛刺、翻边不到位、回弹变形量等制造缺陷。车身焊接过程中一般存在定位销磨损、夹具设计不合理等造成公差累计的不良因素。具体详见图8.
图8 车身异响中制造过程问题
4. 轿车车身异响的现场解决步骤
4.1异响声源的查找
车身异响声源查找没有什么系统的方法,较为先进的是利用异响诊断仪等听诊器具,直接抵在产生异响的大概部位进行听诊,确定异响声源的具体位置。在没有设备辅助的情况下,主要采用一听、二看、三触摸的方法来查找异响声源。听是指通过人的听觉,确定异响源的大致位置。看,主要是观察异响大致区域零部件的装配关系,是否有明显的钣金接触。触摸是根据异响震动的频率高低来寻找异响源。
图9 某汽车异响探测仪
异响诊断仪应用声振原理,通过传感器收集信息频率来分辨主要异响并确定异响的部位。
4.2原因查找及验证
在判断出异响声源大致位置后,需要对该位置区域的装配关系、工艺要求、单件状态、配合公差等进行分析,主要通过以下步骤:
⑴.数模校核及CAE分析
数模校核主要是针对车身异响大致区域,检查数模设计中是否存在的明显错误,例如板件配合间隙小,结构的工艺、装配关系不合理等现象。
CAE分析则是对异响区域的相关件进行刚度、强度分析,了解单件在负载情况下的变形情况,便于根据配合处实际间隙,判断是否存在干涉并产生异响的风险。
⑵.利用工艺文件对工艺确认
在确认装配关系、刚度等没有问题后,利用现场工艺文件,确认异响区域结构的焊接是否符合工艺要求,主要查看焊点或焊缝数量、涂胶情况、搭接边状态等。
⑶.单件检具测量或白光扫描
利用检具或白光扫描,对异响区域的单件或总成件进行尺寸、型面的确认。
⑷.采用排除法、模拟法进行实验验证
通过以上步骤仍然找不到具体异响原因,可以采用排除法、模拟法进行实验验证。验证方法有两种:一是拉大声源震体的距离、二是让声源震体紧密贴合,通过这两种方法来破环声源,达到排除或故障重现的目的,以便更直观的找出异响源。
5、轿车车身异响的预防控制
5.1完善车身设计
⑴.A/B/C柱内板、加强板搭接,钣金结构复杂,车身钣金搭接边设计时,不要有长距离料边悬置(无任何连接),一般不超过150mm,搭接通常可以采用翻边连接或搭接。翻边接头的边宽一般取6t+8mm最佳,t为板料厚度;
⑵.车身钣金配合时,避免弧面与平面,点与平面的配合。在无法避免此类的配合时,要考虑设定较大的间隙或CO2工艺。点与面的配合,在车身工况产生扭矩时,很可能会产生摩擦,造成车身异响;
⑶.面与面配合或线与面配合时,尽量设计成平行状态。如无法避免两个面或线与面的倾斜,在考虑间隙时,必须以最小处间隙为准,一般大于2.5mm;
⑷.缺口与翻边配合时,间隙设计需要考虑翻边的R角处在冲压成型的过程中产出生凸起或翻进余量,以保证设计要求在生产中能得到满足;
⑸.目前国内的钣金件结构间隙一般设计为3mm以上,否则汽车过扭曲路时就很可能会出现干涉或运动异响,并且静刚度试验检测表明A、B、C柱附近测点的最大位移量为0.2~0.7mm,钣金之间的间隙如果在0~1.0mm,对于车身异响来说就是可疑点,很可能造成钣金异响;
⑹.设计车身结构时,要充分考虑冲压件尺寸公差及回弹变形量、车身装配尺寸偏差等,适当补偿,避免误差积累吸收设计间隙;
⑺.设计时充分考虑点焊或CO2焊的可执行性与可靠性。
⑻.设计点焊间距要求:焊点间距越小,焊点数自然增多,当然能提高被焊接件的联接强度。但是在能保证联接强度的条件下,焊点间距应以加大好,这不仅能减少焊点,提高生产率,而且也减少点焊时的分流,提高焊接质量。因此在设计时必须选一个适当点距。
表1 焊接点距参考
一个焊接件的厚度(mm) 0.3 1.0 2.0 3.0 4.0 6.0
焊二层板时最小点距(mm) 12 15 25 30 40 60
在实际设计中,当焊接小的零、总件时,可以参考上表数据,在焊接大的零、总件时,点距可以适加大,一般不小于35~50mm。在有些非受力的部位,则焊点的距离还可以加大到70~80mm。
⑼.焊点不应布置在圆角拐弯处或不平整处,由于焊钳在焊接时的压力比较大,易在圆角拐角处或不平整的部位产生焊接变形。对于无法用点焊连接的弧形搭接面,必须考虑涂点焊密封胶或补CO2焊点;
⑽、一般情况下,尽可能少的采用三层板或者三层以上的焊接结构,最好能够通过使用工艺缺口以进行二层板焊接来代替三层板,三层板等直径通孔若用CO2塞焊易造成虚焊,设计时应尽量避免,无可避免时将焊接面的孔径稍做扩大,便于焊接。
5.2提高生产过程保证能力
⑴.冲压材料应具有良好的塑性,即有较高的伸长率和断面收缩率,较低的屈服强度和较高的抗拉强度。这样,允许的变形程度大,有利于冲压工序的稳定性和变形的均匀性,提高了制品的成形尺寸精度。
⑵.避免分离工序中断口缺陷、制件整体缺陷所造成的飞边、毛刺、尺寸超差、位置不准等缺陷;
⑶.避免弯曲件圆角半径过大。过大时因受弹复的影响,弯曲件的精度不易保证,容易产生形变。弯曲工件的工序增多时,选择相同的定位可减少零件的偏差。此外,工序前后安排顺序不同,也会对精度有很大的影响。例如,对于有孔的弯曲件,先弯曲后冲孔时,孔的精度比先冲孔后弯曲时孔的位置精度要高得多;
⑷.及时检查和调整模具间隙,保证冲载件的断面质量、形状精度和尺寸精度。当间隙较小时,冲裁件往往出现弹胀现象,即材料压缩变形。冲裁后的弹性恢复,使落料件外形尺寸增大(大于凹模尺寸);使冲孔尺寸缩小(小于凸模尺寸);当间隙过大时,拉应力的作用又超过压应力的作用,冲裁过程中有拉伸现象,冲裁后又有反向回弹,因而使落料件尺寸缩小(小于凹模尺寸),使冲孔件尺寸增大(大于凸模尺寸)。
⑸.多采取整修、挤光、负间隙冲裁、小间隙圆角刃口冲裁、对向凹模冲裁、精密冲裁等工艺。
⑹.员工操作时必须执行合理的焊接方法和焊接工艺(焊接顺序),控制稳定的焊接规范,以减少焊接变形;
⑺.零件在运输过程中,以及在一系列装夹取放的过程中,由于员工的熟练程度、劳动态度方面的影响,都会不可避免的使工件产生一定的变形,造成装焊误差,这种装焊误差一般属于随机误差,要尽量避免。
5.3工艺方法弥补
对于异响问题点的处理,只有两种方式,一是将相互干涉、摩擦的钣金进行固定,消除异响源;二是增加异响问题点相互配合的间隙,使其在工况下不至于干涉、摩擦产生异响。具体对应以下两类工艺方法:
⑴.增加焊点、涂点焊密封胶或填充隔振胶
针对焊点布置不合理、悬置料边过长等问题,通常采用增加焊点的方式来解决。对于无法用点焊连接的弧形搭接面,必须考虑涂点焊密封胶或补CO2焊点。如异响源在封闭内腔中,最直接、最简单的办法就是向异响源处填充隔振胶。
⑵.合理加大配合间隙
针对设计间隙小、冲压制件不合格、公差累计等问题,一般没有焊接边、焊接空间可供焊接,主要采用的工艺方法就是改进单件,合理加大配合间隙来解决异响问题。
5.4新工艺、新技术的应用
⑴.激光拼焊板技术:激光拼焊板是将几块不同材质、不同厚度、不同涂层的钢材焊接成一块整体板。
激光拼焊板的应用将减少结构件数量、提高制件质量,避免复杂结构下,钣金公差累计造成的钣金干涉、摩擦异响。
图10 激光拼焊工艺与传统工艺对比
⑵.热成型技术:热成型技术是将原材料加热到再结晶温度以上某一适当温度,使板料在奥氏体状态
成形。热成型材料可以优化集成,并且没有回弹,可广泛用于车身的A、B、C柱等处。
图11 热冲压成形与冷冲压成形对比
⑶.机器人焊接技术:机器人焊接是一种稳定、高效的车身焊接和控制方法,能够对各关键点的焊接
和尺寸提供有效保证,增提高车身各结构的稳定性,减少焊接过程公差累计。
⑷.车身结构模块化:车身结构模块化能够简化车身设计结构、降低工艺要求、提高配合精度。
6、总结
车身异响涉及的因素非常多,在问题处理过程中难度系数大,很多异响问题只能做到具体问题具体分析,更值得关注的是,在预防车身异响方面目前还没有一套完善的检测方法,只有等到问题发生后再去寻求问题产生的原因。以上分析及解决办法只是工作中的经验积累,缺乏一定的理论科学依据,仅仅为我们提供一些车身异响诊断及解决方面的参考。虽然每款车型车身结构不同,但车身异响的原理是相同的,在工作中,设计人员及现场技术人员需要不断的总结归纳,把我们的经验进行沉淀,并实现经验共享。产品开发设计结合SE工程,在调试、生产等一系列环节和过程,都必须进行综合的控制,这样异响问题才能得到改善,整车质量也能彻底得到提升。
参考文献:
[1] 奇瑞汽车股份有限公司汽车研究院. 汽车动力学基础(1)[R]. 2005年.
[2] 奇瑞汽车股份有限公司培训课件. 冲压工艺学[R]. 2010年9月.
[3] 奇瑞汽车股份有限公司规划院. 焊接基础知识[R]. 2008年.
汽车维护检测诊断技术规范
汽车维护检测诊断 技术规范
中华人民共和国国家标准 GB/T 18344— 汽车维护、检测、诊断技术规范 Specification for the inspection and Maintenance of motor vehicle
-03-26 发布 -12-01 实施 国家质量技术监督局发布 GB/T18344-
前言 为规范在用汽车维护、检测、诊断作业,使汽车保持良好的技术状况,减少汽车故障,保证行车安全,延长车辆使用寿命,有效地控制汽车排放污染物,特制定本标准。 本标准是在总结了行业标准JT/T201-1995《汽车维护工艺规范》经验的基础上,扩大了适用范围,使标准更加完善。 本标准的附录A为提示的附录。 本标准由中华人民共和国交通部提出。 本标准由全国汽车维修标准化技术委员会归口。 本标准主要起草单位:交通部公路科学研究所、南京市汽车维修管理处、天津市交通局、北京市汽车维修管理处、云南省交通厅、辽宁省交通厅公路运输管理局。 本标准主要起草人:冯桂芹、韩国庆、谢素华、孟秋、蔡团结、徐通法、刘亚平、刘林、金诚仁。 本标准由全国汽车维修标准化技术委员会负责解释。
中华人民共和国国家标准 汽车维护、检测、诊断技术规范GB/T 18344- Specification for the inspection and Maintenance of motor vehicle 1 范围 本标准规定了汽车日常维护、一级维护、二级维护的周期,作业内容和技术规范。 本标准适用于所有在用汽车。 2 引用标准 下列标准所包含的条文,经过在本标准中引用而构成为本标准的条文。本标准出版时,所示版本均为有效。所有标准都会被修订,使用本标准的各方应探讨使用下列标准最新版本的可能性。 GB7258-1997机动车运行安全技术条件 3 定义 本标准采用下列定义 3.1 日常维护 routine maintenance 以清洁、补给和安全检视为作业中心内容,由驾驶员负责执行的车辆维护作业。 3.2 一级维护 elementary maintenance 除日常维护作业外,以清洁、润滑、紧固为作业中心内容。并检查有关
汽车车身结构与设计试题
一、填空(25分) 1、汽车的主要部件由()、()、()、()四部分组成。 2、单排座汽车的总质量=()。 3、汽车模型雕塑是()中一个必不可少的环节。 4、汽车车身形式按车身壳体受力情况可分为()、()、()三种。 5、汽车车身形式按驾驶室发动机的相对位置可分为()、()、()、()四种。 6、车架的结构形式归纳起来主要有()、()、()三种。 7、汽车门锁按其结构形式分为()式、()式和()式。 8、升力在汽车行驶方向的分力为()。 9、零件图的尺寸标注应满足()、()、()等基本要求。 10.空气阻力有()、()、()、()、()五种。 四、简答题(20分) 1、说明车身的作用。 2、说明承载式车身的特点。 3、说出车身结构主要包括哪些部件。 4、说明非承载式车身的特点。 填空 1.发动机、底盘、车身、电气部件 2.整备质量+允许最大载重量+驾驶员及随员质量 3.汽车外形设计 4.承载式、半承载式、非承载式 5.长头式、短头式、平头式、偏置式 6.框式、脊背式、综合式 7.舌簧、转子和钩簧 8.诱导阻力 9.清晰、完整、合理 10.形状阻力、诱导阻力、摩擦阻力、干涉阻力、内部阻力 简答题 1.答:车身的主要作用是保证驾驶员便于操纵以及为他和乘客提供安全舒适的乘坐环境,隔绝振动和噪音,不受恶劣气候的影响。 2.答:汽车没有车架,用车身完全代替车架承受全部载荷,车身就作为发动机和底盘各总成的安装基础。 3.答:主要包括车身壳体、车门、车前钣件、车窗等,货车和专用车还包括车厢。 4.答:汽车有单独的车架,车身与车架通过弹簧或橡胶垫作柔性连接。 一、填空(25分) 1.汽车车身形式按驾驶室发动机的相对位置可分为()、()、()、()四种。 2. 空气阻力有()、()、()、()、()五种。 3. 零件图的尺寸标注应满足()、()、()等基本要求。 4.汽车车身形式按车身壳体受力情况可分为()、()、()三种。 5. 汽车的主要部件由()、()、()、()四部分组成。 6.车架的结构形式归纳起来主要有()、()、()三种。 7.汽车门锁按其结构形式分为()式、()式和()式。 8.升力在汽车行驶方向的分力为()。 9. 汽车模型雕塑是()中一个必不可少的环节。 10. 单排座汽车的总质量=()。 四、简答题(20分)
汽车维修技术标准
汽车维修技术标准 文稿归稿存档编号:[KKUY-KKIO69-OTM243-OLUI129-G00I-FDQS58-
汽车维修技术标准 GB5624---------85 汽车维修术语 GB3730.3--------83 汽车和挂车的术语及其定义车辆尺寸GB4094----------------94 汽车操纵件、指示器及信号装置的标志 GB3798----------------83 汽车大修竣工出厂技术条件 GB3799----------------83 汽车发动机大修竣工技术条件 GB3800----------------83 汽车车架修理技术条件 GB3801----------------83 汽车发动机气缸体与气缸盖修理技术条件 GB3802----------------83 汽车发动机曲轴修理技术条件 GB3803---------------83 汽车发动机凸轮轴修理技术条件修理技术条件 GB5336----------------85 大客车车身修理技术条件 GB5372----------------85 汽车变速器修理技术条件 GB8823----------------88 汽车前桥及转向系修理技术条件GB8824----------------88 汽车传动轴修理技术条件 GB8825----------------88 汽车驱动桥修理技术条件 GB10830---------------89 汽车制动液使用技术条件 GB/T13094------------91 客车通用技术条件 GB/T8028--------------94 汽油机油换油指标 GB7607-----------------87 汽车柴油机润滑油换油指标
平衡车平衡控制算法
平衡车平衡控制算法.txt /* ******************************************************************************* * @函数名称: f_ContrlBanlance_Ctrl * @摘 要: 平衡车平衡控制算法 * @输 入: 无 * @输 出: 无 ******************************************************************************* */ static void f_ContrlBanlance_Ctrl(void) { float kp,kd; int_32 speed; uint_8 direction; int_16 encoder_left,encoder_right; // 平衡比例系数 kp = 50.0; // 平衡微分系数 kd = 15.0; // 平衡控制算法参数 speed = banlance_angle*kp+banlance_gyro[0]*kd; // 速度控制算法(可选) encoder_left = -f_HardwareEncoder_Read(2); encoder_right = f_HardwareEncoder_Read(3); banlance_motion = f_ContrlBanlance_Motion(encoder_left, encoder_right); speed = speed+banlance_motion; // 增加转速差,实现左右转动控制(可选) speed_left = speed+10-speed_diff; speed_right = speed+10+speed_diff; // 根据得到的转速驱动马达 f_ContrlBanlance_SetSpeed(); } 第 1 页
白车身模态分析作业指导书(修改)
文件编号: YJY·P ·0020·A1-2004 文件名称:白车身模态分析作业指导书 编制:日期: 审核:日期: 批准:日期:
发布日期:年月日实施日期:年月日 前言 为使本公司白车身模态分析规范化,参考国内外白车身模态分析的技术,结合本公司已经开发车型的经验,编制本分析作业指导书。意在对本公司分析人员在做白车身模态分析的过程中起指导作用,让不熟悉或者不太熟悉该分析的员工有所依据,提高工作效率和精度。本作业指导书将在本公司所有白车身模态分析中贯彻,并将在实践中进一步提高完善。 内容包括:前处理模型;分析软件的使用;工程载荷及求解的设置;分析结果后处理和评价标准等。 本标准于2004年9月起实施。 本标准由上海同济同捷科技股份有限公司技术总监室提出。 本标准由上海同济同捷科技股份有限公司技术总监室负责归口管理。 本标准主要起草人:谢颖、邓文彬
白车身模态分析流程 1、适用范围 任何车型的白车身。 2、分析的目标及意义 本分析旨在分析白车身的振动固有频率和振型,得到的数据可为车身结构设计和振动噪声分析提供参考。 3、前处理建模 3.1白车身模型(只包括焊接总成,不包括门、玻璃、内饰等螺栓紧固件),焊点用RBE2(6个自由度)模拟,焊点布置应符合实际情况,边界条件为自由。 3.2 网格大小和注意事项如下。 3.2.1建模标准(所有项均在HYPERMESH中检测)表1 在网格划分之前,一定要充分考虑该零件与其它零部件之间的连接关系。 3.2.2在hypermesh中注意事项: 3.2.2.1 单元网格总体要求:连续、均匀、美观,过渡平缓。
3.2.2.2 对于倒角,倒角两端点距离小于5mm时可删去(命令:geom\distance)。当倒角两端点距离大于5mm时,测一下倒角的弧长(命令:geom\length),如弧长小于10mm时划分一个单元,大于10mm,划分两排单元,如难以满足单元长度要求,可将倒角的一边toggle掉。对于孔,半径小于5mm时可删去,同时删去小于5mm的凸台和沉孔。 3.2.2.3对于对称件,只划分一个件的网格,另一个件使用镜像方法生成。对于一个单个零件如果是左右对称的,可将它从中间切开,划分一半即可(使用splitbody命令),对于单个零件判断其是否是左右对称的,可将切开的另一半镜像过去(使用transform命令),渲染后看是否重合 3.2.2.4对于一些比较小的零部件(比如小螺栓)根据其位置和尺寸及对分析目标的重要性可不进行网格划分 3.2.2.5 B柱之前的零件网格尺寸控制在10-15mm,对于B柱之后c柱之前的零件,可适当增大网格尺寸,定在15-20mm,c柱之后20-35mm划分时可根据具体情况进行调整(如对一些连接处可划分细一些); 3.2.2.6原则上存在焊点的翻边必须划分两排单元,识别焊边可察看各总成数模、或者是看参考车型以及去设计部门的相关负责人联系。在焊点的翻边上,如翻边长度小于10mm,在保证最小单元长度要求下,可适当将翻边加长。大于10mm 时,考虑划分两排单元,对不符合长度要求的单元进行必要的调整(如将翻边的边界toggle掉)。 原则上焊点位置由设计部门确定,在设计部门已提供焊点位置的情况下,采取以下操作步骤:1)在UG中检查焊点位置,若发现分布不合理的焊点,须与车身相关设计人员确认;2)将零件导入HYPERMESH,其中应包含该零件的焊点信息――点和圆圈线(导入前需确认在UG里已经将点、线、面分层);3)将含圆线圈的COMP隐藏,只显示零件和焊点,然后用GEOM CLEANUP/FIXED POINTS/ADD命令将焊点变成零件面上的硬点;4)划分网格并按标准检查好单元质量后,文件先以HM格式进行保存(须包含所有点、线、面和单元),然后将网格输出成*.bdf文件,再将焊点和圆圈线输出成*.igs(该文件的命名方法:在bdf文件名前加w。如:bdf文件53-01.bdf,则igs文件w53-01.igs);5)在PATRAN里装配时,将
汽车维修技术标准
汽车维修技术标准 (一)汽车大修竣工出厂技术提条件(国家标准GB3798-83) 1.一般技术要求 (1)装配的零件、部件、总成和附件应符合相应的技术条件。各项装备应齐全,并按原设计的装配技术要求安装。允许在汽车大修中按经规定程序批准的技术文 件改变某些零件、部件的设计,但其性能不得低于原设计(注)要求。 (2)主要结构参数应符合原设计规定。由于经修理而增加的自重,不得超过原设计自重的3%。 (3)驾驶室、客车楔应形状正确、曲面圆顺、转角处无折绉、蒙皮平整、无松弛、污垢及机械操作等缺陷。 注:原设计是指汽车制造厂或按照规定程序批准的改造、改装的技术文件(下同)(4)喷漆颜色协调、均匀、光亮、漆层无裂纹、剥落、起泡、流痕和皱纹等现象。 不需涂漆的部位,不得有漆痕。刷漆部位允许有不明显的流痕和刷纹。 (5)驾驶室、客车厢、货箱及翼子板左右对称。各对称部位离地面高度差:驾驶室、翼板/客车厢不大于10mm,货箱不大于20mm。 (6)座椅颜色的形状、尺寸、座间距及调节装置应符合原设计要求。 (7)门窗启闭灵活,关闭严密,锁卡可靠,合缝匀称,不松旷。挡风玻璃透明,不眩目。 (8)转向机机构各连接部位不松旷,锁卡可靠。方向盘自由行程(代转向助力器的除外),总重不小于4.5t的汽车不大于30o,总重小于4.5t汽车不大于15o。 (9)离合器踏板、制动踏板的自由行程和驻车制动的有效行程应符合原设计要求。 (10)仪表、灯光、信号和标志齐全,工作正常。 (11)轮胎充气气压应符合原设计要求。 (12)限速装置应铅封。 (13)各部润滑应符合原设计要求。 (14)各部件运行温度正常,各处无漏油、漏水和漏电现象。但润滑油、冷却水密封结合面处允许有不致形成滴状的浸渍。
线控两轮平衡车的建模与控制研究
线控两轮平衡车的建模 与控制研究 文稿归稿存档编号:[KKUY-KKIO69-OTM243-OLUI129-G00I-FDQS58-
线性系统理论 上机实验报告 题目:两轮平衡小车的建模与控制研究 完成时间:2016-11-29 1.研究背景及意义 现代社会人们活动范围已经大大延伸,交通对于每个人都十分重要。交通工具的选择则是重中之重,是全社会关注的焦点。 随着社会经济的发展,人民生活水平的提高,越来越多的小汽车走进了寻常百姓家。汽车快捷方便、省时省力,现代化程度高,种类繁多的个性化设计满足了不同人的需求。但它体积大、重量大、污染大、噪声大、耗油大、技术复杂、使用不便、价格贵、停放困难,效率不高,而且还会造成交通拥堵并带来安全隐患。相比之下,自行车是一种既经济又实用的交通工具。中国是自行车大国,短距离出行人们常选择骑自行车。自行车确实方便,但在使用之前需要先学会骑车,虽然看似简单,平衡能力差的人学起来却很困难,容易摔倒,造成人身伤害。另外,自行车毕竟不适宜长距离的行驶,遥远的路程会使人感到疲劳。 那么,究竟有没有这样一种交通工具,集两者的优点于一身呢?既能像汽车一样方便快捷又如自行车般经济简洁,而且操作易于掌握,易学又易用。两轮自平衡车概念就是在这样的背景下提出来的。 借鉴目前国内外两轮自平衡车的成功经验,本文提出的研究目标是设计一款新型的、结构简单、成本低的两轮自平衡车,使其能够很好地实现自平衡功能,同时设计结果通过MATLAB进行仿真验证。
2.研究内容 自平衡式两轮电动车是一个非线性、强耦合、欠驱动的自不稳定系统,对其控制策略的研究具有重大的理论意义。我们通过分析两轮平衡车的物理结构以及在平衡瞬间的力学关系,得到两轮车的力学平衡方程,并建立其数学模型。运用MATLAB 和SIMULINK 仿真系统的角度θ、角加速度? θ、位移x 和速度的? x 变化过程,对其利用外部控制器来控制其平衡。 3.系统建模 两轮平衡车的瞬时力平衡分析如图1所示。下面将分析归纳此时的力平衡方程[1-3],并逐步建立其数学模型。 对两轮平衡车的右轮进行力学分析,如图2所示。 依据图2对右轮进行受力分析,并建立其平衡方程: =R R R R M X f H ? - (1) R R R R J C f R ??? =- (2) 同理,对左轮进行受力分析,并建立其平衡方程: =R L L L M X f H ? - (3) L L L L J C f R ??? =- (4) 两轮平衡车摆杆的受力分析如图3所示,由图3可以得到水平和垂直方向的平衡方程以及转矩方程。 水平方向的平衡方程: H H x R L p m +=? ? (5) 其中θsin L x x m p +=,则有:
轿车车身结构及其设计解析
第六章轿车车身结构及其设计 第一节轿车车身结构及其分类 1.1 轿车定义 GB3730.1-88 轿车是用于载送人员及随身物品,且座位布置在两轴之间的四轮汽车。 轿车车身的作用是能为乘员提供一个较舒适的乘坐环境以及一定的安全保护措施,它包括白车身及其附件,并与底盘、发动机、电子电器设备一起构成轿车的四大总成。由于它是轿车上载人的容器,因此要求轿车车身应具有良好的舒适性和安全性。此外,轿车车身又是包容整车的壳体,能够最直观地反映轿车外观形象的特点,从而决定了现代轿车车身设计非常注重外部造型以符合人们对轿车外形的审美要求,更好的开创轿车市场。 1.2 轿车车身结构 早期轿车沿用马车车身,并没有自身独立的车身,被人们称作“没有马的马车”,随着时代的进步,轿车车身成为了轿车的一个重要组成部分。轿车车身由以下几个部分组成:车身本体、车身外装件、内装件和车身电气附件等。 1.2.1车身本体 1—1 三厢式轿车车身结构图 1、发动机盖 2、前档泥板 3、前围上盖板 4、前围板 5、车顶盖 6、前柱 7、上边梁 8、顶盖侧板 9、后围上盖板10、行李箱盖11、后柱12、后围板13、后翼子板14、中柱15、车门16、下边梁17、底板18、前翼子板19、前纵梁20、前横梁21、前裙板22、散热器框架23、发动机盖前支撑板车身本体即白车身,它包含车身的骨架结构,由车身结构件和车身覆盖件组合而成,是主要承载构件的骨架件,其截面形状、受力方向、力如何传递、力矩的位置都是设计时应注意的问题,如图1-1所示为三厢式轿车车身的结构图。 车身结构件主要是车身结构中的梁和支柱,用来支撑车身覆盖件,并通过焊接而成车
某商用车驾驶室白车身模态分析
龙源期刊网 https://www.360docs.net/doc/5418533439.html, 某商用车驾驶室白车身模态分析 作者:谢小平,韩旭,陈国栋,周长江 来源:《湖南大学学报·自然科学版》2010年第05期 摘要:以某商用车驾驶室白车身为原型,利用模态分析方法对其动力学特征参数进行分析.在理论(正问题)和实验(反问题)两个互补的模态分析过程中,利用有限元模型进行理论模态分析,为实验模态分析的实施打下良好基础.分别采用最小二乘复指数法(LSCE)和最小二乘复频域法(LSCF)进行实验模态分析,得到各阶模态振型并对理论分析的结果进行修正.经过两种结果的比较和分析,最终得出准确的模态分析结果并对白车身原型提出改进意见.生产厂商依据改进意见进行工艺改进,通过用户实际使用证实了改进方案的有效性和正确性. 关键词: 商用车驾驶室;白车身;有限元;实验模态分析;LSCE;LSCF 中图分类号:TH113.1文献标识码:A Modal Analysis of Commercial Vehicle Cab’s Body-in-White XIE Xiao-ping+, HAN Xu, CHEN Guo-dong, ZHOU Chang-jiang (State Key Laboratory of Advanced Design and Manufacturing for Vehicle Body, Faculty of Mechanical and Vehicle Engineering, Hunan University, Changsha, 410082) Abstract: The theory modal analysis (TMA, forward problem) and experimental modal analysis(EMA, inverse problem) methods are both used to analysis dynamics characteristic parameters of one commercial vehicle cab’s body-in-white. Finite element modal analysis is carried out to get mode shape and lay down well basis to experimental modal analysis in TMA process. In EMA process, LSCE(Least Squares Complex exponent method) and LSCF (Least Squares Complex Frequency Domain method) methods are used to get mode shape and modify TMA results. With comparison to all results, the accurate conclusion can be reached and improvement opinion is brought forward to the prototype. The improvement projection was proved to be effective by consumers’utilization after manufacturer put it into applications. Keywords: commercial vehicle cab’s bod y-in-white; finite element method; experimental modal analysis; LSCE; LSCF 车辆在行使的过程中常因路面不平,车速和运动方向的变化,车轮、发动机和传动系的振动激励,以及齿轮的冲击等各种外部和内部激励,极易引起整车和局部振动。当外界激振频率与系统固有频率接近时,将产生共振[1]。
汽车维护检测诊断技术规范
汽车维护、检测、诊断技术规范GBT18344 来源:技术处时间:2013-01-07 前言 为规范在用汽车维护、检测、诊断作业,使汽车保持良好的技术状况,减少汽车故障,保证行车安全,延长车辆使用寿命,有效地控制汽车排放污染物,特制定本标准。 本标准是在总结了行业标准JT/T201-1995《汽车维护工艺规范》经验的基础上,扩大了适用范围,使标准更加完善。 本标准的附录A为提示的附录。 本标准由中华人民共和国交通部提出。 本标准由全国汽车维修标准化技术委员会归口。 本标准主要起草单位:交通部公路科学研究所、南京市汽车维修管理处、天津市交通局、北京市汽车维修管理处、云南省交通厅、辽宁省交通厅公路运输管理局。 本标准主要起草人:冯桂芹、韩国庆、谢素华、孟秋、蔡团结、徐通法、刘亚平、刘林、金诚仁。 本标准由全国汽车维修标准化技术委员会负责解释。? 1?范围? 本标准规定了汽车日常维护、一级维护、二级维护的周期,作业内容和技术规范。 本标准适用于所有在用汽车。? 2?引用标准
下列标准所包含的条文,通过在本标准中引用而构成为本标准的条文。本标准出版时,所示版本均为有效。所有标准都会被修订,使用本标准的各方应探讨使用下列标准最新版本的可能性。GB7258-1997机动车运行安全技术条件。? 3?定义 本标准采用下列定义 3.1?日常维护?routine maintenance 以清洁、补给和安全检视为作业中心内容,由驾驶员负责执行的车辆维护作业。 3.2?一级维护?elementary maintenance 除日常维护作业外,以清洁、润滑、紧固为作业中心内容。并检查有关制度、操纵等安全部件,由维修企业负责执行的车辆维护作业。? 3.3?二级维护?complete maintenance 除一级维护作业外。以检查、调整转向节、转向摇臂、制动蹄片、悬架等经过一定时间的使用容易磨损或变形的安全部件为主,并拆检轮胎,进行轮胎换位,检查调整发动机工作状况和排气污染控制装置等,由维修企业负责执行的车辆维护作业。 4?汽车维护分级和周期 4.1?汽车维护的分级:日常维护,一级维护,二级维护。 4.2?汽车维护的周期 4.2.1?日常维护的周期 出车前,行车中,收车后。 4.2.2?一级维护、二级维护的周期?
基于单片机的两轮自平衡车控制系统设计
基于单片机的两轮自平衡车控制系统设计 摘要 两轮自平衡车是一种高度不稳定的两轮机器人,就像传统的倒立摆一样,本质不稳定是两轮小车的特性,必须施加有效的控制手段才能使其稳定。本文提出了一种两轮自平衡小车的设计方案,采用重力加速度陀螺仪传感器MPU-6050检测小车姿态,使用互补滤波完成陀螺仪数据与加速度计数据的数据融合。系统选用STC 公司的8位单片机STC12C5A60S2为主控制器,根据从传感器中获取的数据,经过PID算法处理后,输出控制信号至电机驱动芯片TB6612FNG,以控制小车的两个电机,来使小车保持平衡状态。 整个系统制作完成后,小车可以在无人干预的条件下实现自主平衡,并且在引入适量干扰的情况下小车能够自主调整并迅速恢复至稳定状态。通过蓝牙,还可以控制小车前进,后退,左右转。 关键词:两轮自平衡小车加速度计陀螺仪数据融合滤波 PID算法 Design of Control System of Two-Wheel Self-Balance Vehicle based on Microcontroller Abstract Two-wheel self-balance vehicle is a kind of highly unstable two-wheel robot. The characteristic of two-wheel vehicle is the nature of the instability as traditional inverted pendulum, and effective control must be exerted if we need to make it stable. This paper presents a design scheme of two-wheel self-balance vehicle. We need using gravity accelerometer
汽车电子稳定程序系统
浅谈汽车电子稳定程序 前言 随着汽车行驶速度的提高,道路行车密度的增大,汽车行驶安全性已经受到了高度关注。汽车的行驶安全性能要求不断提高,汽车安全系统已经成为汽车研究发展的重要部分。 汽车安全性包括主动安全性和被动安全性两大类。汽车主动 安全是指事故发生前的安全,即实现事故预防和事故回避,防止 事故发生。主动安全性是指通过事先预防,避免或减少事故发生 的能力。被动安全性是指汽车在发生意外事故时对乘员进行有效 保护的能力。汽车的主动安全性因其防患于未然,所以越来越受 到汽车厂商和消费者的重视,越来越多的先进技术也被应用到汽 车主动安全装置上。主动安全性的好坏决定了汽车产生事故发生概率的多少,而被动安全性的好坏主要决定了事故后车内成员的受伤严重程度。 目前广泛运用的汽车主动安全性系统主要有防抱死制动系统(ABS)、驱动防滑系统〔ASR〕、牵引力控制系统 (TCS)、汽车电子稳定程序系统(ESP),汽车电子制动力分配系统(EBD), 紧急刹车辅助系统 (EBA)、汽车自适应巡航速度控制系统(ACC)等,保证汽车在危险状况下行驶的安全性。上述这些系统具有智能化的控制作用,根据车辆的行驶状况,自动地完成对汽车制动性能、转向辅助等的控制,无需人的主动性操作,可见汽车安全系统已经向智能型方向发展。
摘要 本文探讨了ESP系统的原理、发展和现状。简要讨论汽车 ESP 系统的结构及关键技术。介绍新奥迪 A4轿车 ESP系统的组成、电控系统、液压单元及工作过程。 关键词:电子稳定程序,主动安全性,操纵稳定性,模糊控制传感器液压控制单元电子控制单元 ESP系统实际是一种牵引力控制系统,与其他牵引力控制系统比较,ESP不但控制驱动轮,而且可控制从动轮。如后轮驱动汽车常出现的转向过多情况,此时后轮失控而甩尾,ESP便会刹慢外侧的前轮来稳定车子;在转向过少时,为了校正循迹方向,ESP则会刹慢内后轮,从而校正行驶方向。 ESP系统是汽车上一个重要的系统,通常是支持ABS及ASR 的功能。它通过对从各传感器传来的车辆行驶状态信息进行分析,然后向ABS、ASR发出纠偏指令,来帮助车辆维持动态平衡。ESP可以使车辆在各种状况下保持最佳的稳定性,在转向过度或转向不足的情形下效果更加明显。ESP一般需要安装转向传感器、车轮传感器、侧滑传感器、横向加速度传感器等。 ESP系统包含ABS(防抱死刹车系统)及ASR(驱动防滑转系统),是这两种系统功能上的延伸。因此,ESP称得上是当前汽车
线控-两轮平衡车的建模及控制研究
线性系统理论 上机实验报告 题目:两轮平衡小车的建模与控制研究
完成时间:2016-11-29 1.研究背景及意义 现代社会人们活动围已经大大延伸,交通对于每个人都十分重要。交通工具的选择则是重中之重,是全社会关注的焦点。 随着社会经济的发展,人民生活水平的提高,越来越多的小汽车走进了寻常百姓家。汽车快捷方便、省时省力,现代化程度高,种类繁多的个性化设计满足了不同人的需求。但它体积大、重量大、污染大、噪声大、耗油大、技术复杂、使用不便、价格贵、停放困难,效率不高,而且还会造成交通拥堵并带来安全隐患。相比之下,自行车是一种既经济又实用的交通工具。中国是自行车大国,短距离出行人们常选择骑自行车。自行车确实方便,但在使用之前需要先学会骑车,虽然看似简单,平衡能力差的人学起来却很困难,容易摔倒,造成人身伤害。另外,自行车毕竟不适宜长距离的行驶,遥远的路程会使人感到疲劳。 那么,究竟有没有这样一种交通工具,集两者的优点于一身呢?既能像汽车一样方便快捷又如自行车般经济简洁,而且操作易于掌握,易学又易用。两轮自平衡车概念就是在这样的背景下提出来的。 借鉴目前国外两轮自平衡车的成功经验,本文提出的研究目标是设计一款新型的、结构简单、成本低的两轮自平衡车,使其能够很好地实现自平衡功能,同时设计结果通过MATLAB进行仿真验证。
2.研究容 自平衡式两轮电动车是一个非线性、强耦合、欠驱动的自不稳定系统,对其控制策略的研究具有重大的理论意义。我们通过分析两轮平衡车的物理结构以及在平衡瞬间的力学关系,得到两轮车的力学平衡方程,并建立其数学模型。运用MATLAB和SIMULINK仿真系统的角度θ、角加速度?θ、位移x和速度的?x变化过程,对其利用外部控制器来控制其平衡。 3.系统建模 两轮平衡车的瞬时力平衡分析如图1所示。下面将分析归纳此时的力平衡方程[1-3],并逐步建立其数学模型。 对两轮平衡车的右轮进行力学分析,如图2所示。
电气自动化专业的行业分析报告
电气自动化专业的行业分析报告 电气1401 任翀 专业概念及特点 电气工程及其自动化专业是电气信息领域的一门新兴学科,但由于和人们的日常生活以及工业生产密切相关,发展非常迅速,现在也相对比较成熟。已经成为高新技术产业的重要组成部分,广泛应用于工业、农业、国防等领域,在国民经济中发挥着越来越重要的作用。其触角伸向各行各业,小到一个开关的设计,大到宇航飞机的研究,都有它的身影。本专业生能够从事与电气工程有关的系统运行、自动控制、电力电子技术、信息处理、试验技术、研制开发、经济管理以及电子与计算机技术应用等领域的工作,是宽口径“复合型”高级工程技术人才。该领域对高水平人才的需求很大。据估计,随着国外大企业的进入,在这一专业领域将出现很大缺口,那时很可能出现人才供不应求的现象。 控制理论和电力网理论是电气工程及自动化专业的基础,电力电子技术、计算机技术则为其主要技术手段,同时也包含了系统分析、系统设计、系统开发以及系统管理与决策等研究领域。该专业还有一些特点,就是强弱电结合、电工电子技术相结合、软件与硬件相结合,具有交叉学科的性质,电力、电子、控制、计算机多学科综合,使毕业生具有较强的适应能力,是“宽口径”专业。(摘自《电气自动化-百度百科》) 发展现状 我国电气自动化专业开始发展于20世纪50年代初,国家对该专业进行几次调整,但由于该专业所覆盖的行业领域广,适用性大,到现在仍然焕发着勃勃生机。全国各大高校都相继开设该专业,并发展迅速。学习该专业的大学生和研究生数量迅速增大,社会上从业人员也迅速增加。高校电气自动化专业大学生也随之增加。 本专业产生于19世纪70年代,首先在英国的牛津大学,首次实现的是直流电的控制方式,那时候执行元件的驱动电压是直流的,控制电压也是直流的,自动化系统的工作方式是很简单、粗糙的,精度也很低。但直流的控制方式由于其历史的久远而被人们所熟知,自然而然的人们想到了用直流电去控制交流执行元件。随着晶体管、大功率晶体管、场效应管等大功率的电子器件的出现和成熟、以及建立在场的理论上、以现代数学、矩阵代数为理论依据的弱电强电控制系统更使电子技术与自动化达到新的历史高度。至此,本专业得到了广泛的发展,日本、美国、英国及其他国家的大学也纷纷设立了本专业,在这一时期的成果也并不少,诸如完成数控机床,车间厂房自动控制的工作已经是新的课题。电子技术与自动化、计算机的有机结合,赋予电子工程及自动化专业以全新的内涵。无人操纵,系统简化,格局合理,即插即用型的产品成为新宠。
汽车车身结构与设计
第一章:车身概论 1.车身包括:白车身和附件。 白车身通常系指已经焊装好但尚未喷漆的白皮车身,此处主要用来表示车身结构和覆盖件的焊接总成,此外尚包括前、后板制件与车门,但不包括车身附属设备及装饰等。 2.按承载形式之不同,可将车身分为非承载、半承载式和承载式三大类。 非承载车身的优点:①除了轮胎与悬架系统对整车的缓冲吸振作用外,挠性橡胶垫还可以起到辅助缓冲、适当吸收车架的扭转变形和降低噪声的作用,既延长了车身的使用寿命,又提高了舒适性。②底盘和车身可以分开装配,然后总装在一起,这样既可简化装配工艺,又便于组织专业化协作。③由于车架作为整车的基础,这样便于汽车上各总成和部件安装,同时也易于更改车型和改装成其他用途车辆,货车和专用车以及非专业厂生产的大客车之所以保留有车架,其主要原
因也基于此。④发生碰撞事故时,车架对车身起到一定的保护作用。非承载车身的缺点:①由于计算设计时不考虑车身承载,故必须保证车架有足够的强度和刚度,从而导致自重增加。②由于车身和底盘之间装有车架,使整车高度增加。③车架是汽车上最大而且质量最大的零件,所以必须具备有大型的压床以及焊接、工夹具和检验等一系列较复杂昂贵的制造设备。 3.承载式车身分为基础承载式和整体承载式。 基础承载式特点:①该结构由截面尺寸相近的冷钢杆件所组成,易于建立较符合的有限元计算模型,从而可以提高计算精度。②容许设法改变杆件的数量和位置,有利于调整杆件中的应力,从而达到等强度的目的。③作为基础承载的格栅底架具有较大的抗扭刚性,可以保证安装在其上的各总成的相对位置关系及其正常工作。④提高材料利用率,简化构件的成型过程,节省部分冲压设备,同时也便于大客车的改型和系列化,为多品种创造了条件。 4.“三化”指的是产品系列化、零部件通用化以及零件设计标准化。第二章:车身设计方法
汽车车身模态分析研究综述
汽车车身模态分析研究综述 北京信息科技大学研1202班姓名:曹国栋学号:2012020045 摘要:车身是汽车的关键总成。它的构造决定了整车的力学特性,对白车身进行模态分析不仅能考察车身结构的整体刚度特性,而且可以指导人们对车身结构进行优化以及响应分析。因此,研究车身模态分析具有重要的意义。本文综述了近几年国内外在车身模态分析领域内的研究,总结了研究理论和试验方法,并进行归纳。最后,对未来的研究工作提出了一些展望。 关键词:车身;模态分析;有限元模态;试验模态;结构优化 0 前言 随着计算机技术的发展和仿真技术、有限元分析技术的提高,计算机辅助设计和分析技术几乎涵盖了涉及汽车性能的所有方面,如刚度、强度、疲劳寿命、振动噪声、运动与动力性分析、碰撞仿真和乘员保护、空气动力学特性等,各种计算机辅助设计软件为汽车设计提供了一个工具平台,极大地方便了汽车的设计。 车辆在行驶过程中,车身结构在各种振动源的激励下会产生振动,如发动机运转、路面不平以及高速行驶时风力引起的振动等。如果这些振源的激励频率接近于车身整体或局部的固有频率,便会发生共振现象,产生剧烈振动和噪声,甚至造成结构破坏。为提高汽车的安全性、舒适性和可靠性,就必须对车身结构的固有频率进行分析,通过结构设计避开各种振源的激励频率。 车身结构模态分析是新车型开发中有限元法应用的主要领域之一,是新产品开发中结构分析的主要内容。尤其是车身结构的低阶弹性模态,它不仅反映了汽车车身的整体刚度性能,而且是控制汽车常规振动的关键指标,应作为汽车新产品开发的强制性考核内容。有限元模态分析和试验模态分析方法是辨识汽车结构动态性能的一种有效的手段,在汽车车身动态性能研究中得到了广泛应用。采用有限元方法对白车身进行模态分析,识别出车身结构的模态参数,并通过模态试验验证了有限元模型的正确性,为改型设计提供参考依据,是汽车开发设计与优化的一般流程。 因此,研究车身结构模态分析,进行车身轻量化设计和优化,对于提高国产轿车的自开发与科技创新能力,具有重要的理论意义和工程实用价值。 1 车身模态分析的一般理论 1.1 模态分析基本理论 模态分析的经典定义即以模态矩阵作为变换矩阵,将线性定常系统振动微分方程组中的物理坐标进行坐标转换变到模态坐标上,从而使系统在原来坐标下的耦合方程变成一组互相独立的二阶常微分方程进而成为一组以模态坐标及模态参数描述的独立方程[1]。 在实际的结构动力分析中,一般将连续结构离散化为一个具有n个有限自由
汽车维护、检测、诊断技术规范
中华人民共和国国家标准 GB/T 18344—2001 汽车维护、检测、诊断技术规范 Specification for the inspection and Maintenance of motor vehicle 2001-03-26 发布 2001-12-01 实施 国家质量技术监督局发布 GB/T18344-2001
前言 为规范在用汽车维护、检测、诊断作业,使汽车保持良好的技术状况,减少汽车故障,保证行车安全,延长车辆使用寿命,有效地控制汽车排放污染物,特制定本标准。 本标准是在总结了行业标准JT/T201-1995《汽车维护工艺规范》经验的基础上,扩大了适用范围,使标准更加完善。 本标准的附录A为提示的附录。 本标准由中华人民共和国交通部提出。 本标准由全国汽车维修标准化技术委员会归口。 本标准主要起草单位:交通部公路科学研究所、南京市汽车维修管理处、天津市交通局、北京市汽车维修管理处、云南省交通厅、辽宁省交通厅公路运输管理局。 本标准主要起草人:冯桂芹、韩国庆、谢素华、孟秋、蔡团结、徐通法、刘亚平、刘林、金诚仁。 本标准由全国汽车维修标准化技术委员会负责解释。 中华人民共和国国家标准 汽车维护、检测、诊断技术规范GB/T 18344-2001 Specification for the inspection and Maintenance of motor vehicle 1 范围 本标准规定了汽车日常维护、一级维护、二级维护的周期,作业内容和技术规范。 本标准适用于所有在用汽车。 2 引用标准 下列标准所包含的条文,通过在本标准中引用而构成为本标准的条文。本标准出版时,所示版本均为有效。所有标准都会被修订,使用本标准的各方应探讨使用下列标准最新版本的可能性。
汽车车身主要构成部分
汽车知识: 汽车车身主要构成部分 汽车车身是由发动机盖、车顶盖、行李箱盖、翼子板、前围板等几部分构成的。 发动机盖 发动机盖(又称发动机罩)是最醒目的车身构件,是买车者经常要察看的部件之一。对发动机盖的主要要求是隔热隔音、自身质量轻、刚性强。 发动机盖的在结构上一般由外板和内板组成,中间夹以隔热材料,内板起到增强刚性的作用,其几何形状由厂家选取,基本上是骨架形式。发动机盖开启时一般是向后翻转,也有小部分是向前翻转。 向后翻转的发动机盖打开至预定角度,不应与前档风玻璃接触,应有一个约为10毫米的最小间距。为防止在行驶由于振动自行开启,发动机盖前端要有保险锁钩锁止装置,锁止装置开关设置在车厢仪表板下面,当车门锁住时发动机盖也应同时锁住。 车顶盖 车顶盖是车厢顶部的盖板。对于轿车车身的总体刚度而言,顶盖不是很重要的部件,这也是允许在车顶盖上开设天窗的理由。从设计角度来讲,重要的是它如何与前、后窗框及与支柱交界点平顺过渡,以求得最好的视觉感和最小的空气阻力。 当然,为了安全车顶盖还应有一定的强度和刚度,一般在顶盖下增加一定数量的加强梁,顶盖内层敷设绝热衬垫材料,以阻止外界温度的传导及减少振动时噪声的传递。 行李箱盖 行李箱盖要求有良好的刚性,结构上基本与发动机盖相同,也有外板和内板,内板有加强筋。一些被称为“二厢半”的轿车,其行李箱向上延伸,包括后
档风玻璃在内,使开启面积增加,形成一个门,因此又称为背门,这样既保持一种三厢车形状又能够方便存放物品。 如果采用背门形式,背门内板侧要嵌装椽胶密封条,围绕一圈以防水防尘。行李箱盖开启的支撑件一般用勾形铰链及四连杆铰链,铰链装有平衡弹簧,使启闭箱盖省力,并可自动固定在打开位置,便于提取物品。 翼子板 翼子板是遮盖车轮的车身外板,因旧式车身该部件形状及位置似鸟翼而得名。按照安装位置又分为前翼子板和后翼子板,前翼子板安装在前轮处,因此必须要保证前轮转动及跳动时的最大极限空间,因此设计者会根据选定的轮胎型号尺寸用“车轮跳动图”来验证翼子板的设计尺寸。 后翼子板无车轮转动碰擦的问题,但出于空气动力学的考虑,后翼子板略显拱形弧线向外凸出。现在有些轿车翼子板已与车身本体成为一个整体,一气呵成。但也有轿车的翼子板是独立的,尤其是前翼子板,因为前翼子板碰撞机会比较多,独立装配容易整件更换。有些车的前翼子板用有一定弹性的塑性材料(例如塑料)做成。塑性材料具有缓冲性,比较安全。 前围板 前围板是指发动机舱与车厢之间的隔板,它和地板、前立柱联接,安装在前围上盖板之下。前围板上有许多孔口,作为操纵用的拉线、拉杆、管路和电线束通过之用,还要配合踏板、方问机柱等机件安装位置。 为防止发动机舱里的废气、高温、噪声窜入车厢,前围板上要有密封措施和隔热装置。在发生意外事故时,它应具有足够的强度和刚度。对比车身其它部件而言,前围板装配最重要的工艺技术是密封和隔热,它的优劣往往反映了车辆运行的质量。 汽车车身结构从形式上说,主要分为非承载式和承载式两种。 非承载式车身的汽车有刚性车架,又称底盘大梁架。车身本体悬置于车架上,用弹元件联接。车架的振动通过弹性元件传到车身上,大部分振动被减弱或消除,发生碰撞时车架能吸收大部分冲击力,在坏路行驶时对车身起到保护