声表面波器件工艺原理-3光刻工艺原理
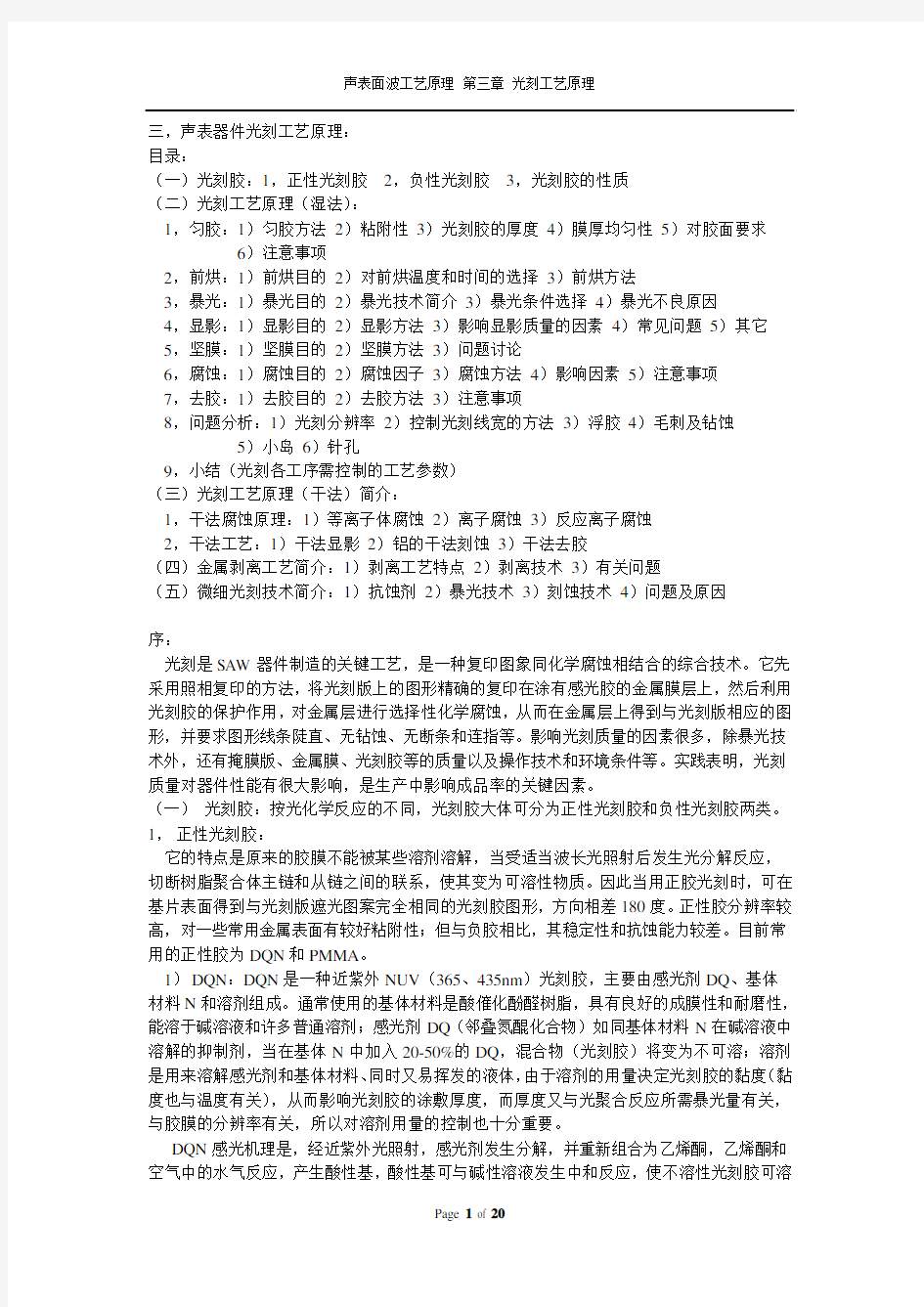

三,声表器件光刻工艺原理:
目录:
(一)光刻胶:1,正性光刻胶2,负性光刻胶3,光刻胶的性质
(二)光刻工艺原理(湿法):
1,匀胶:1)匀胶方法2)粘附性3)光刻胶的厚度4)膜厚均匀性5)对胶面要求6)注意事项
2,前烘:1)前烘目的2)对前烘温度和时间的选择3)前烘方法
3,暴光:1)暴光目的2)暴光技术简介3)暴光条件选择4)暴光不良原因
4,显影:1)显影目的2)显影方法3)影响显影质量的因素4)常见问题5)其它
5,坚膜:1)坚膜目的2)坚膜方法3)问题讨论
6,腐蚀:1)腐蚀目的2)腐蚀因子3)腐蚀方法4)影响因素5)注意事项
7,去胶:1)去胶目的2)去胶方法3)注意事项
8,问题分析:1)光刻分辨率2)控制光刻线宽的方法3)浮胶4)毛刺及钻蚀5)小岛6)针孔
9,小结(光刻各工序需控制的工艺参数)
(三)光刻工艺原理(干法)简介:
1,干法腐蚀原理:1)等离子体腐蚀2)离子腐蚀3)反应离子腐蚀
2,干法工艺:1)干法显影2)铝的干法刻蚀3)干法去胶
(四)金属剥离工艺简介:1)剥离工艺特点2)剥离技术3)有关问题
(五)微细光刻技术简介:1)抗蚀剂2)暴光技术3)刻蚀技术4)问题及原因
序:
光刻是SAW器件制造的关键工艺,是一种复印图象同化学腐蚀相结合的综合技术。它先采用照相复印的方法,将光刻版上的图形精确的复印在涂有感光胶的金属膜层上,然后利用光刻胶的保护作用,对金属层进行选择性化学腐蚀,从而在金属层上得到与光刻版相应的图形,并要求图形线条陡直、无钻蚀、无断条和连指等。影响光刻质量的因素很多,除暴光技术外,还有掩膜版、金属膜、光刻胶等的质量以及操作技术和环境条件等。实践表明,光刻质量对器件性能有很大影响,是生产中影响成品率的关键因素。
(一) 光刻胶:按光化学反应的不同,光刻胶大体可分为正性光刻胶和负性光刻胶两类。1,正性光刻胶:
它的特点是原来的胶膜不能被某些溶剂溶解,当受适当波长光照射后发生光分解反应,切断树脂聚合体主链和从链之间的联系,使其变为可溶性物质。因此当用正胶光刻时,可在基片表面得到与光刻版遮光图案完全相同的光刻胶图形,方向相差180度。正性胶分辨率较高,对一些常用金属表面有较好粘附性;但与负胶相比,其稳定性和抗蚀能力较差。目前常用的正性胶为DQN和PMMA。
1)DQN:DQN是一种近紫外NUV(365、435nm)光刻胶,主要由感光剂DQ、基体
材料N和溶剂组成。通常使用的基体材料是酸催化酚醛树脂,具有良好的成膜性和耐磨性,能溶于碱溶液和许多普通溶剂;感光剂DQ(邻叠氮醌化合物)如同基体材料N在碱溶液中溶解的抑制剂,当在基体N中加入20-50%的DQ,混合物(光刻胶)将变为不可溶;溶剂是用来溶解感光剂和基体材料、同时又易挥发的液体,由于溶剂的用量决定光刻胶的黏度(黏度也与温度有关),从而影响光刻胶的涂敷厚度,而厚度又与光聚合反应所需暴光量有关,与胶膜的分辨率有关,所以对溶剂用量的控制也十分重要。
DQN感光机理是,经近紫外光照射,感光剂发生分解,并重新组合为乙烯酮,乙烯酮和空气中的水气反应,产生酸性基,酸性基可与碱性溶液发生中和反应,使不溶性光刻胶可溶
于碱溶液,而未经暴光的光刻胶仍为不可溶。我们常用的美国AE-1350系列,北化的202、205、212,上试一厂的702,703等都属该类光刻胶。
2)PMMA:主要成分是甲基丙烯酸脂及其衍生物。其感光机理是,PMMA在深紫外光(DUV)照射下,聚合体发生断链降解,分子量迅速降低,变为可被碱溶液溶解的物质,有资料介绍,暴光后的光刻胶在显影时的溶解度几乎十倍于没暴光的光刻胶。PMMA对波长220nm的光最敏感,而对波长大于240nm的光完全不敏感,通过添加光敏剂,如t-丁基苯酸,可使其紫外光谱吸收率增加。PMMA常用于深紫外暴光,电子束光刻、离子束光刻、X射线光刻。
2,负性光刻胶:
它的特点是原来的胶膜可被某些溶剂溶解,当受适当波长照射后,发生光聚合或交联反应,使其键结成高分子聚合物,变为不可溶物质。因此当用负胶光刻时,可在基片表面得到与光刻版遮光图案完全相反的光刻胶图形,方向也相差180度。
负性光刻胶一般由感光剂(光致抗蚀剂)、溶剂和增感剂组成。感光剂是对光敏感的高分子化合物,受光照射后,能吸收一定波长的光能量,发生交联、聚合等光化学反应,使光刻胶改变性质。增感剂在光化学反应时起催化或引发作用,当用适当光源照射时,增感剂分子能在比感光剂响应波长更长一些的光谱范围吸收能量,并与感光剂分子进行能量转移,从而加快感光剂光聚合速度,提高感光度;但是在光刻胶中,感光剂也不宜过多,因为当感光度已达饱和,多余的感光剂会使胶质变脆,减弱胶的抗蚀能力。溶剂是用来溶解感光剂和增感剂、同时又易挥发的液体,其用量与暴光量及胶膜的分辨率密切相关。负性胶有较强的抗蚀能力和稳定性,但因暴光形成的高分子聚合物会吸收显影液引起胶膜溶胀及在聚合过程中所发生的氧化反应的影响,使其分辨率较低。下面介绍几种常用的负性胶。
1)聚肉桂酸脂类:属该类树脂的有聚乙烯醇肉桂酸脂、肉桂酸纤维素等,是线性高分
子聚合物,纤维状固体,能溶于甲苯、氯苯(芳香族溶剂)、丙酮、丁酮(脂肪族溶剂)、环已酮、环乙烷(脂环族溶剂)等溶剂。在紫外线照射下,其分子侧链上的肉桂酸基中的一个双键被打开,与相邻的肉桂酸基相互结合形成交联键,这就是光化学聚合反应,它使线状结构的分子变成三维架桥式的网状结构,成为不溶于有机溶剂也不受酸影响的物质(由于其交联键在强酸强碱作用下易断开,所以该类光刻胶不能经受强酸碱腐蚀)。聚肉桂酸脂类感光树脂的光谱吸收范围在230-340nm,添加增感剂可使其感光波长达到450nm,具有实用价值;常用的增感剂主要是硝基有机化合物,如5-硝基苊等,常用的溶剂是环已酮。聚肉桂酸脂类光刻胶是研究使用最早的光刻胶品种,如北化的103胶,上海化学试剂厂的‘上试1号’,美国柯达光致抗试蚀剂(KPR),日本东京应化光致抗试蚀剂(TPR)等,都是以聚乙烯醇肉桂酸脂为基础的光刻胶。
2)聚脂类:聚脂类感光树脂系二元醇和二元酸的缩聚产物,在这类树脂分子侧链上带
着含有共轭双键的感光性官能团,因此具有较强的感光性;在其分子主链上含有极性基团,因而对二氧化硅、铝有较好粘附性。聚脂类感光树脂的增感作用和光化学反应机理与聚肉桂酸脂相似,其溶剂为氯仿、酮类,增感剂为硝基有机化合物。
3)环化橡胶类(聚烃类-双叠氮系):它主要有天然或人造橡胶制成,主要成分是顺式聚
乙戊二烯。把这种橡胶溶于适当的溶剂(如二甲苯),并加入环化结构催化剂(如氟化硼),加一定温度环化后,链状结构的顺式聚乙戊二烯就变成了环状结构,其耐磨性、粘附性和抗蚀性都得到显著提高。在光照下,环化的橡胶分子通过交联剂(双叠氮化合物,起光化学反应交连作用)交联形成网状分子结构,成为不溶性聚合物。由于在光照时,同时发生的氧化反应是聚合交连的竞争反应,所以该胶具有一定的厌氧性。双叠氮化合物感光范围260-400nm,对常用光源是合适的,添加适宜的增感剂(二苯甲酮),可出现新的吸收峰,使感光度提高。该类光刻胶和金属衬底粘附能力强,耐腐蚀性强,因而得到广泛应用;美国
柯达(KMER),日本应化(OMR),北化302胶都属该类型。
3,光刻胶的性质:
光刻胶性能好坏对光刻质量影响很大,常用感光度、分辨率、抗蚀性、粘附能力和针孔密度等指标来衡量光刻胶的优劣。
1)感光度:是用来表征光刻胶对光敏感度的性能指标。感光度不同,表示它对光的敏
感程度不同,即光化学反应所需暴光量不同。感光度(S)可用暴光时使光刻胶发生光化学反应所需的最小暴光量(E)的倒数表示:
S = k / E (式中为常数,的单位:勒克斯?秒)
暴光量(E)等于光强(I)与暴光时间(t)的乘积,故E又可表示为:
E =k /(I?t)
由于光刻胶对不同波长的光源敏感程度不同,因此感光度与光刻胶的光谱响应、及所用光源的光谱成分有关。为改善光刻胶的感光性,增大其感光范围,往往需要加入适当适量的增感剂。在光刻过程中,当确定了光刻胶后,必须选用合适的光源,才能有满意的效果。
影响感光度的因素很多,与光刻胶本身有关的因素在此不议,这里主要介绍光刻工艺条件对感光度的影响:
a)干燥(前烘)条件的影响:以KPR-2胶为例,在空气中干燥30′,比在100℃ 热板上干燥2′的感光度小许多;在100℃ 热板上干燥2′,感光度即达到最大值,时间再增加,感光度不变。试验说明,当溶剂完全从胶中去除后,感光度即达一定值,感光度与溶剂去除程度有关。因此要仔细控制好前烘,以达最佳感光度。
b)胶膜厚度的影响:胶厚不同,感光度不同。以KTFR胶为例,厚度在12-23μm之间,感光度无变化,当厚度为08-06μm时,感光度显著下降。此外,厚度对感光度的影响还与衬底有无反射、光刻胶对光的吸收等因素有关。
c)暴光的影响:在暴光过程中,光强对感光度通常无影响;但对氧敏感的光刻胶在空气中暴光时,由于氧的影响(胶的氧化会减弱胶的光聚合作用),当用较弱的光暴光时,感光度明显下降。
2)分辨率:它是表示光刻精度的标志之一。它不仅与光刻胶本身有关,还与光刻工艺条件和操作技术等因素有关,如掩膜版的质量,光源的状况,暴光量的大小,暴光光线的平行度,光刻胶的厚度,基片粘附程度,显影液、腐蚀液的配比及显影、腐蚀的温度、时间,前烘、坚膜的温度、时间,以及光的衍射、铝膜的反射等等。分辨率通常是以每毫米最多可容纳的线条数来表示。若可分辨的条宽为W/2 ,而条与条的间距也为W/2 时,则分辨率为1/W (条线/毫米)。
3)留膜率:留膜率直接影响光刻质量,习惯上常用显影前后的光刻胶膜厚之比值表示留膜率。 留膜率(%)= 显影后的胶膜厚度(坚膜后)/ 显影前的胶膜厚度(前烘后)
不同类型的光刻胶,留膜率不同;负性胶一般低于85%,正性胶大于90%。影响留膜率的因素还与光刻工艺条件选择有关,如前烘条件,暴光时间及显影条件(显影液配比、浓度、显影时间)等。
4)针孔密度:单位面积的光刻胶膜上的针孔数。它反应了光刻胶各种外在因素(例如颗粒等)及内在组分,直接影响光刻质量。
5)黏度、固态含有率:温度、黏度和固态含有率是影响涂胶厚度的重要因素。胶黏度越大(即越稠),在相同条件下,所得胶膜越厚;温度高、固态含有率低,胶的黏度变小。此外,固态含有率不仅通过黏度影响胶厚,它本身对膜厚也有直接影响,固态含有率大,胶膜干燥后就厚;但固态含有率增大,影响分辨率的提高,为达到一定分辨率,要求膜厚及前烘条件必须与胶的黏度及固态含有率相适应,以达最佳效果。
6)抗蚀性:是指光刻胶耐酸、碱腐蚀及等离子腐蚀的能力。在湿法腐蚀时,光刻胶膜只
有在针孔密度小、粘附性能好的情况下,才有好的抗蚀能力,对负性胶而言,橡胶系光刻胶性能较优,而正性胶抗湿法腐蚀能力就较差。但在干法等离子腐蚀中,要求光刻胶与被腐蚀物之间有较高的选择比(即被腐蚀材料与胶膜减薄量之比),正性胶就较优。
目前使用的光刻胶,分辨率与抗蚀性常相矛盾;此外同种胶配比不同,两个指标也有差别;应根据需要进行选择。
7)稳定性:要求常温时光刻胶在光(主要是紫外光)屏蔽的情况下,即使加入增感剂也不发生暗反应;若进行烘烤干燥,加热到一定温度时也不发生热交联。一般情况下,负胶稳定性比正胶好。为提高胶的稳定性,可加入一定量的抗氧化剂或能抑制活性基团自发反应能力的稳定剂。
8)粘附能力;光刻胶膜与衬底粘附的牢固程度直接影响光刻精度(如显影时图形尺寸是否变化,腐蚀时是否浮胶和钻蚀)。影响粘附能力的因素很多,它不仅与胶本身性质有关,而且与衬底的性质和表面状态有关(如衬底分子与胶分子相互作用的亲和力,衬底表面的亲、疏水性及清洁程度等)。
以上对光刻胶感光机理及性能作简单描述,不同感光胶性能各异,我们可以根据工艺要求予以选择。
(二) 光刻工艺原理(湿法):
光刻过程中的每一步骤对光刻质量都有直接影响,因此必须选择合适的工艺条件,严格操作,来保证刻蚀图形正确、清晰,无钻蚀、毛刺、小岛等缺陷。
光刻工艺步骤:匀胶—前烘—暴光—烘烤—显影—坚膜—去底膜-腐蚀—去胶。
1,匀胶:
它是将感光胶涂布在待光刻的基片表面。要求涂布的胶层粘附良好,洁净,均匀,无
针孔,胶膜厚度要符合工艺要求。
1)匀胶方法:目前国内外常采用自转涂胶法(转速可在每分钟几千转到每分钟上万转 之间调整)。它是让滴上胶后的基片先低速旋转,使胶在基片表面匀开,紧接着高速旋转(转速要在很短时间内达到设定值,且转速均匀),在离心力及表面张力作用下,胶向四周飞溅,剩余的胶则均匀分布在基片表面,以此得到均匀的具有一定厚度的感光胶层。
2)粘附性:光刻胶与铝膜之间的粘附情况直接影响光刻质量。如边沿钻蚀、针孔,严 重的会造成浮胶,使图形全部损坏。影响粘附性的因素主要有:
a)不同的光刻胶对不同的刻蚀材料的粘附性不同;同类型光刻胶因配比不同,其粘附性 也有差异。如减少光刻胶的固态含有率和在胶中加入适量的表面活性剂,即可改善其粘附性。目前我们常用的环化橡胶类感光胶以及一些正性胶对金属都有较好的粘附性。
b)被刻蚀材料的表面性质影响光刻胶的粘附性。如平整致密的表面有利于胶的粘附(粗糙的表面不利于吸附气体的排除),水接触角小的材料于胶的粘附不利。
C)被刻蚀材料(金属膜)表面的清洁情况直接影响光刻胶的粘附。要尽量避免尘埃、油污、吸附气体对表面的污染。
D)水气对胶的粘附性有较大影响。包括表面吸附的水气和涂胶环境中的水气。一般情况,水滴接触角大于55°时,就能保证粘附良好,为此,人们常采用匀胶前烘烤去气或使用表面处理剂如在表面涂六甲基乙硅氮烷(HMDS),来去除所吸附水分子,使表面由亲水性变为疏水性,改善粘附性。对匀胶环境的湿度要控制在40%以下。(改善粘附性方法还有:如负胶用三氯乙烯/异丙醇1:1浸10秒,室温淋干,烘10分; 正胶用二甲苯/苯基三氯硅烷200:1,5000转/分,30秒等)
此外,光刻胶的涂敷、胶的厚度、前烘、暴光量、显影液配方、坚膜和腐蚀等对光刻胶与基片的粘附也有密切关系。
3)光刻胶的厚度:对于选定的光刻胶而言,胶膜越薄,分辨率越高;在常规工艺中,
对负胶来说,分辨率与暴光波长及胶厚有关,通常分辨率为胶厚的3—4倍。但胶太薄,针孔密度增加,而且当刻蚀深度较大时,需要有较厚的胶膜保护;所以对胶厚要按工艺需要选择。在生产中常从以下几个方面控制胶厚:
a)改变光刻胶浓度:影响胶厚的主要因素是胶的黏度,黏度大,胶膜就厚。通常我们是 用胶的浓度来控制黏度。另外温度、湿度、固态含有率对胶的黏度都有较大影响,工作中不容忽视。
b)用转速控制胶厚:初始转速越快,胶膜越薄。在选定胶厚及黏度时,常以3000-4000 转/分为参考。
c)采用多次涂胶:在多次涂胶时要注意,第一次涂胶后,必须按前烘条件烘烤,然后再二次涂胶,否则会得不到良好胶膜。
d)胶厚与转速及固态含有率关系如下: T = KP2/S-1/2 ,
式中T:胶膜厚度, P:光刻胶固态含有率, S:转速, K:常数。 (在光刻胶说明书中,提供有厚度、温度、黏度、转速的关系曲线,可以参照)
4)膜厚均匀性:由于光刻胶越厚,分辨率越低,所以胶厚均匀性必然影响分辨率,此 外因膜厚不匀,使掩膜不能与片子很好接触,会造成图形失真,在进行细线条光刻时,均匀性尤为重要。 膜厚均匀性主要决定于涂胶方法及设备。一般来说旋转法涂敷转速越大,旋转越平稳,膜厚越均匀。在实际工作中,可观察旋转时片子上光刻胶的干涉条纹,条纹越宽,条数越少,说明膜厚越均匀。通常要求膜厚偏差在±10nm。
5)对胶面要求:胶面洁净是保证光刻图形完整性的关键,尘埃不仅损坏图形,在接触 式暴光中还会损伤光刻版。影响胶面洁净的因素,除光刻胶本身外,主要是要提高生产环境的净化级别,要从细从严作好工艺卫生。如不要让手或其它物体从片子上方经过,不要让滴胶管前次留下的已干燥的胶块掉在片子表面等。
6)注意事项:
a)如条件许可,匀胶台转速要定期测定。
b)由于涂胶前片子表面要保持非常洁净,所以一般情况下,当片子从蒸发台取出或清洗 处理后,应立即匀胶。如确需暂时存放,则应放在干燥洁净的容器中,并在匀胶前要进行热处理。若存放过久或光刻返工,就必须进行清洁处理,对刻铝片,一般采用甲苯、丙酮、乙醇超声,去离子水冲洗、烘干,再行涂胶;或采用丙酮水浴煮15′;或涂胶前将片子放入65℃的10%重铬酸钾溶液中3′;或用发烟硝酸浸泡等;可酌情选用。
C)当使用大片时,低速旋转的速度和时间要选择得当,使滴在片子上的胶先均匀坦敷 在片子表面,然后再高速旋转,否则会影响匀胶质量。
2,前烘:
1)前烘目的:是指对涂敷了光刻胶的片子进行一定温度和时间的烘焙处理。使胶膜干 燥,增加胶膜的粘附性和耐磨性;促使光刻胶膜内溶剂充分挥发,使光刻胶暴光时反应充分,增强其抗蚀能力。此外它对显影速度、线宽控制等也都起一定作用。
2)对前烘温度和时间选择:主要依赖于光刻胶性质和加热方式,具体条件由实验确定。
a)前烘过量(温度高、时间长)的不良影响:
* 温度过高会使光刻胶翘曲硬化,使显影不净、分辨率降低以及图形被破坏。
* 温度过高或时间过长会使光刻胶发黑,失去抗蚀能力。
* 温度过高或时间过长会使光刻胶发生热交连,造成显影不净,影响光刻质量。
* 温度高、时间长会使胶中增感剂挥发过多,影响感光度,延长了暴光时间,严重时, 甚至光刻胶不感光。
* 前烘时不能骤热。因为它会使胶面很快干燥,而内部溶剂没有蒸发,以后会因发泡引起针孔或使图形缺乏均匀性;骤热还会引起胶接触不好,在显影和腐蚀时会发生剥落(在胶膜
厚时尤为显著)。
b)前烘不足(温度低、时间短)除会造成粘版及胶附着力下降外,还有以下不良影响: * 对负胶而言,温度过低或时间过短,由于胶中溶剂没能充分发挥,影响暴光时光刻
胶分子交连,轻则会使显影速度加快,对线宽控制不易;重则因部分胶(指暴光部位的胶)被溶解,会造成浮胶或图形变形。
* 使用正胶时,前烘不足,显影不稳定,时间长,易出现浮胶,甚至胶层全部脱落。
另外前烘不当,有时会出现皱胶。对压电晶片,要特别注意,慢升温慢降温,以免裂片。
c)前烘方法:有:恒温干燥箱烘烤;热板烘烤(将片子直接放在热板上或与热板留1mm 左右间隙);红外烘烤(让红外线从片子背面照射);真空烘箱烘烤(有利于厌氧型光刻胶提高分辨率);真空红外烘烤等。其中热板烘烤(自动匀胶设备配置的热板,温度梯度太大,不宜用于压电晶片)和红外烘烤为目前流行方法,其优点是:光刻胶的干燥是从片子和光刻胶的界面开始,使溶剂逐渐从内部向表面蒸发,前烘效果好。
3,暴光:
1)暴光目的:对已涂敷光刻胶的片子进行选择暴光,使暴光部分发生光化学反应,从 而改变其在显影液中的溶解度,通过显影,在胶膜上显现出与掩膜版相应的图形。 由于声表器件多属一次暴光,只需在暴光前让基片的基准边和波的传播方向(即版上的图形)平行或垂直即可,除特殊要求外,无须套刻,所以在对准方面比IC光刻多次套刻简易许多。
2)暴光技术简介:暴光是光刻中最关键的工艺。当前暴光的主要技术有:光学暴光, 电子束暴光,X射线暴光,离子束暴光等。由于掌握资料有限,对此仅作简单介绍。
a)光学暴光:为提高分辨率,光学暴光波长不断缩小,由全光谱到近紫外NUV(436nm、 365nm),再到深紫外DUV(246nm、193nm),所作最细线宽达0.18微米,一再突破人们预期的光学暴光极限。由于光学暴光的不断创新,使之仍为当前暴光的主流。光学暴光技术包括:接触/接近式紫外暴光技术,紫外投影暴光技术,远紫外(DUV)暴光技术等。
* 接触/接近式紫外暴光技术:接触/接近式紫外暴光是最简单的暴光方法,它是使基片表面的抗蚀剂与掩模版直接接触进行暴光(接触式),或是使抗蚀剂表面与掩膜版保持一定距离(10-50μ)进行暴光(接近式)。近似地取光波波长在抗蚀剂中和空气中一样,两种暴光方式的最小线宽W为: W =(3/2)·[λ(S + d/2)]1/2 ,
其中:λ为暴光波长,S为抗蚀剂表面与掩模的距离,d为抗蚀剂膜厚。 由于受光衍射影响,实际线宽常是理论线宽的2-5倍。 影响暴光线宽的主要因素:除受光的波长和衍射影响外,还受前烘温度、暴光能量、显影时间等影响。
* 紫外投影暴光技术:它是用光学投影方法把光刻版图形投影到基片使光刻胶暴光。其 优点是掩模版不被粘污、不受损伤;对准时不存在景深问题,对准精度高;减少掩模缺陷影响。
·1:1全反射投影暴光:它是有一组凸凹球面反射镜构成的成像系统,光源发出的光线 透过掩模经多次反射在基片的抗蚀剂上成像。由于受光的衍射效应限制,暴光的实际分辨率最小线宽为: w min = λ/1.28(N·A) λ:暴光光源波长, N·A:镜头数值孔径。 1:1全反射投影暴光实用线宽为1.5-2μ,最高分辨率可达1μ。
·缩小投影暴光技术:它是利用光学折射系统把中间掩模图形加以缩小后直接在基片上 分布重复精缩。常用的缩小率有10:1、5:1、4:1等;缩小倍率大时,掩模缺陷对基片图形影响小,但因像场较小,暴光时间长;缩小倍率小时,则相反。采用分布重复办法,在基片局部区域有较好平整度,可允许在小的像场中采用具有较高数值孔径的投影系统。举例: 若N·A = 4,当选用λ=405nm时,能分辨的最小线宽是0.78μm,当选用λ=365 nm时,能分辨的最小线宽是0.55μm。
* 远紫外(DUV)暴光技术:是由波长为200-260nm的远紫外光作光源的亚微米暴光技
术。它的感光机理为,在深紫外光照下,聚合体发生断裂,迅速低分子化,变为可被碱溶液溶解的物质。远紫外线波长短,衍射效应小,采用高分辨率的深紫外抗蚀剂;暴光形式有接触式/接近式及投影式,其中投影式远紫外线暴光最小线宽小于1微米,接触式的远紫外线暴光已能做到0.13μm线条。常用的远紫外线暴光光源有重氢灯,高压水银弧光灯等,由于人造石英对远紫外透光率好(90%),故常被用来制作掩模。
b) 电子束暴光技术:具有一定能量的电子打到光刻胶上同样可以使光刻胶发生化学反应,从而改变光刻胶在显影液中的溶解度。电子束暴光所用抗蚀剂与远紫外暴光同,其感光机理也相同。它具有波长短(不受衍射影响),焦深长(不受表面粗糙程度影响),分辨率高等优点,但设备复杂,造价高。电子束暴光方式主要有扫描型和投影型。这两种形式均可实现亚微米加工,最小线宽可达0.1微米。
* 无掩模扫描电子束暴光:电子由电子枪产生,经加速器使电子获得较大能量,然后这些电子经电磁透镜聚焦,变成了很细的电子束,电子束再经磁偏转系统和通断装置的控制就可以在涂了光刻胶的基片上打出所要求的图形,达到暴光目的。它可直接在基片上做图,易于控制和修改灵活,但生产效率很低,常被用来制作暴光掩模及特殊器件生产。
* 电子束投影暴光:其原理与普通光学缩小投影暴光相似。它是高亮度电子源经电磁透镜聚焦产生电子束,对掩模进行均匀照射(掩模是x倍放大,是在低原子序数材料膜(氮化硅薄膜)上覆盖高原子序数材料层(钨栅)组成),在片子上形成缩小x倍的图形,然后再经过工作台步进实现大面积暴光。投影电子束暴光生产效率高,但掩模制作困难。
c) X射线暴光技术:属接近式暴光;掩模制作在对X射线半透明的衬底上。用聚焦电子束产生的X射线源照射掩模,掩模上用X射线吸收层组成的像投影到抗蚀剂模上,实现图象复印。该暴光技术特点是:分辨率高,最小线宽可达0.03微米;暴光不受衍射、反射干扰;衬底表面状况对结果影响不大。不利因素是:暴光时间长,掩模制作困难。
X射线波长:0.4-1.5nm; X射线源:靶材料有:铜、铝、硅、钼、铑、钯等;
X射线掩模:掩模的吸收模必须很薄(200nm左右),对X射线衰减大。掩模材料常用金。由于硅具有很高的导热性和可加工性,故衬底材料常用硅。
d) 离子束暴光技术:其原理与电子束暴光原理相似,主要区别在于用较重的离子代替电子,离子能量能被光刻胶充分吸收,故其能对多种光刻胶进行有效暴光,并减少了暴光时间;另外由于它质量较重,离子基本不在基片表面产生高能背散射电子,所以其分辨率仅与离子束的直径有关,而与临近效应无关。离子束暴光技术主要包括聚焦离子束暴光技术和离子束缩小投影暴光技术等。
* 聚焦离子束暴光技术:与无掩模扫描电子束暴光相似。它是利用液态镓离子源或气态氢离子源被电离后形成的离子流经电场加速后通过静电透镜聚焦成很细的离子束斑,由计算机控制偏转线圈实现在基片表面上扫描成像。该技术分辨率高,不需掩模,最小线宽为0.03微米,但生产效率低。
*离子束缩小投影暴光技术:它是由气体(氢或氦)离子源发出的离子通过多极静电离 子透镜投照于掩模并将图象缩小后聚焦于涂有抗蚀剂的片子上,进行暴光和步进重复操作。该技术具有分辨率高而焦深长,数值孔径小而视场大,衍射效应小,损伤小,效率高,对抗蚀剂厚度变化不敏感,工艺成本低等特点。目前已有公司用深紫外胶作出0.05微米的间隔线条。由于它是缩小暴光,需要X倍的硅膜镂孔掩模,面临应力和入射离子造成的发热及变形等许多问题需要解决。
3)对暴光条件的选择(光学暴光):暴光条件的选择实质是对暴光量的确定,它标志着 使光照部分的胶膜全部发生交链或分解所需要的能量。暴光量可表示为: E = It ,
其中I:光强,t:时间。
暴光量与光刻胶的种类、胶层厚度、光源(包括光谱、功率等)、光源与片子的距离等因
素有关。在实际操作中,上述因素都基本固定,所以通常是以时间决定暴光量,而时间须经反复实验确定。一般认为短时间强暴光效果较好。
a)暴光量不足(时间短)的危害:对负胶而言,暴光量不足则胶交链不充分,抗蚀性降低。显影时会出现聚合物肿胀,引起图形奇变;有时表面会呈现橘皮状、溶坑、或在边沿引起钻蚀;严重时则部分溶解而失去图形,引起浮胶。对正胶而言,暴光量不足则显影时间长,显影不易干净,严重时会得不到光刻图形。
b)暴光量过度(时间长)的危害:对负胶而言,暴光量过度易产生底膜,分辨率降低, 光刻条变宽,图形交连,严重时会使图形连成一片。对正胶而言,暴光量过度会显影过快,条宽边窄。
c)提醒注意的是,光源在使用后期,由于功率和光谱会发生变化,此时必须增加暴光量 或更换新的光源。(附:当采用负胶时,暴光时间可适当长些;当使用正胶时,暴光时间可适当短些;以抵消横向腐蚀的影响。)
4)引起暴光不良的因素:
a)由于光刻胶对光的强烈吸收造成暴光不足。尤其膜厚时,大部分光能量被上层胶吸收,使下层胶暴光不足。
b)光反射影响:光刻胶所需暴光量与衬底表面是否反射有关。若衬底反射光波长在光
刻胶的吸收范围,则入射光反射光都能对光刻胶暴光;否则反射光对暴光无效,对此要予以注意。同时入射光和反射光会相互干涉,产生驻波效应,使与反射面相接触的光刻胶层可能暴光不足,影响光刻质量;显影前的‘后前烘’能消除驻波的影响,原因是‘后前烘’的热能促使因干涉造成的感光不均衡重新达到平衡。
4,显影:
1)显影目的:显影就是把暴光后的片子用显影液除去应去掉部分的光刻胶。要求显影
彻底,且图形清晰。
2)显影方法:有浸渍法、喷雾法、蒸汽法等。目前多用浸渍法和喷雾法。但无论用什
么方法,都必须保证显影液及所用器皿干净。
a)浸渍法:将暴光后的片子垂直(可减少底膜)或面向上(便于观察)依次放入多杯(两杯以上)显影液中显影,再依次放入多杯(两杯以上)漂洗液中漂洗;显影时要不断晃动片子以利显影,对图形上小部分胶要去掉的,可晃动很些,对图形上小部分胶要保留的,可晃动轻些。显影时间由胶膜厚薄、显影液温度和操作方法决定,该办法均匀性差,重复性差,显影不易控制,操作过程取决于操作者的经验。
b)喷雾法:有槽式喷淋和自转喷雾。槽式喷淋每次可显多片,显影液循环使用并通过滤膜过滤(滤膜孔径视光刻线条宽度而定)。自转喷雾法多在自动显影机上采用。需要注意的是:在自转喷雾显影时,如喷雾量小,时间短或自转速度不合适,会显影不净,在表面留下底膜;若一次不净,再显时,底膜会加重,这是因为氧或光的作用使残留的胶不易被溶解;所以尽量不要多次显影。
c)显影后检查:显影后必须检查以确保显影质量。一般应检查:图形是否对准,暴光条件是否合适,图形边沿是否整齐,有无皱纹和胶面发黑,有无浮胶和表面划伤。如有不合格必须返工。
3)影响显影质量的因素:显影质量主要表现于显影彻底,图形边沿整齐。在没感光处(正胶)或感光处(正胶),显影后不能残留光刻胶,否则在坚膜或腐蚀时,因感光(包括热感光)增加抗蚀性而影响腐蚀;而边沿不整齐在腐蚀时会产生钻蚀现象。
a)对显影液的选择:不同光刻胶所用显影液不同。对显影液选择原则是,应对暴光后
需去掉部分的抗蚀剂溶解的快,且溶解度大;对需保留部分的抗蚀剂溶解度极小。另外要求显影液有害杂质少,毒性小。
b)温度影响:显影液温度高,显影速度快,正胶表现更明显;但也有温度高而显影速度慢的胶,如AZ-1350,OFPR等。要注意胶的使用说明。
c)浓度影响:负胶采用有机溶剂或专用显影液,不存在浓度变化问题,但要注意按时
更换显影液,以免其中溶解光刻胶过多,影响显影速度。正胶采用碱性水溶液对显影速度影响较大,必须按规定配比,否则显影速度不宜控制。
d)时间影响:显影时间随抗蚀剂种类、胶膜厚度和显影液种类及显影液温度不同而不同,而且一杯显影液使用前期和后期显影时间也不同。所以要根据实际情况选择和调整时间。* 显影时间太短:会使显影不足。在没感光(负胶)和感光(正胶)面积内留下一层
不易观察出的光刻胶膜,在腐蚀时起保护作用,使腐蚀不彻底,会留下“小岛”铝层,若继续腐蚀,会引起铝条钻蚀。此外显影不足还会出现图形边沿厚度递减,影响光刻质量。
* 显影时间过长:由于显影时光刻胶发生软化、膨胀,显影液从基片表面向图形边沿渗透,发生钻溶,使图形边沿变坏。有时会出现浮胶,胶膜皱起呈橘皮状,严重时则大片剥离,形成脱胶。
4)常见问题:
a)底膜:
* 在窄间距图形负胶光刻中,如暴光时间稍长,显影易产生底膜;若时间过长,底膜加重,同时条宽变宽。
* 正胶光刻时,暴光不足,会显影不净产生底膜。
* 当选用OMR-83等类厌氧性负性胶时,若暴光不是在氮气中进行,易产生底膜。
* 喷雾显影时,若喷雾条件不当,需多次显影时,易产生底膜。
* 显影不足,如温度低,时间短,易产生底膜。
b)图形尺寸不合要求:当暴光过度及显影过度时,对正胶光刻,会造成条宽变细,严
重则断条;对负胶光刻,条宽变粗,严重则连条。暴光不足的负胶显影后胶面不光亮,图形变细,边沿毛刺,严重时会胶面发皱或图形变形;暴光不足的正胶显影后图形变粗,严重时甚至不出图形。
c)浮胶:由涂胶、前烘、暴光、显影等工序引起的浮胶原因有:涂胶时表面太脏或环
境湿度太大,前烘不足或过度,暴光不足,显影时间太长或多次显影等。
5)其它:
a)在显影小图形时,常发现边沿粗糙不整齐现象,若在显影前用正丁醇对片子做两次
漂洗,然后显影,可减少边沿不整齐现象;原因是正丁醇可使光刻胶略有收缩。
b)将25-50%的碳酸二丙酯加于显影液中,可以起到防止胶膜泡胀和增强胶粘附作用。c)对窄线条光刻,如暴光后再前烘一次,然后显影,有利于对条宽的控制。这是因为 烘烤的热能能促使因光干涉引起的胶层感光不匀最后达到平衡。
5,坚膜:
1)坚膜目的:显影后,由于显影液使光刻胶膜发生软化、膨胀,使胶膜与衬底的粘附
性变差,耐蚀性降低,因此必须在一定温度下烘烤,以除去胶膜中的显影液和水分,从而提高其粘附性和抗蚀性。
2)坚膜方法:一种是烘箱坚膜,一种是红外坚膜(用红外灯从片子背面照射)。因不同的胶,有不同的工艺要求,所以具体坚膜温度、时间要实验确定。
3)问题讨论:
a)坚膜过度(温度高、时间长):会引起光刻胶部分炭化或使光刻胶因热膨胀发生翘曲和剥离,腐蚀时产生钻蚀或脱胶,有时也会引起聚合物发生一些分解,产生低分子产物,影响粘附和抗蚀能力。另外由于铝有较强的反光性,与光刻胶粘附能力较强,因此坚膜时间可稍短,以免光刻后去胶困难。
b)坚膜不足:胶膜没洪透,膜不坚固,腐蚀时会产生侧蚀及负胶现象。
c)坚膜时应缓慢升温和自然冷却,这样会使胶膜更坚固,而且可以防止胶的细小裂纹,所造成的毛刺。对一些有特殊要求的光刻,也可采用长时间低温坚膜。
d)坚膜温度的确定:高聚合物在玻璃化温度范围内会产生微量的塑性留动,如果衬底
与胶的粘附力较强,而不致因这种微量的塑性流动使图形变形,则这种流动能改善光刻胶与衬底的粘附。光刻胶聚合物的玻璃化温度不是一个确定值,而是一个范围,当温度高于这个范围,则会发生教大的塑性流动,使图形变形,低于这个范围,则不会发生塑性流动,若坚膜温度在玻璃化温度范围上限以下5-10℃,即:使胶极微量塑性流动又不变形,这样就能达到增强粘附能力的目的。各种胶的坚膜温度时间,在光刻胶说明书中都有说明。
6,腐蚀:
1)腐蚀目的:腐蚀是光刻技术中的重要工序,通过该工序,要按照光刻胶膜已显现出
的图形,完整、清晰、准确地刻蚀出金属膜图形。腐蚀有干、湿法之分。干法腐蚀对正胶更合适,因为正胶抗干法腐蚀能力强。湿法腐蚀是用适当的腐蚀液将无光刻胶膜覆盖的金属膜腐蚀掉,而将有光刻胶膜覆盖的区域保留下来。其腐蚀的三步骤是:(a)反应物扩散到被刻蚀物表面。(b)反应物与被刻蚀薄膜反应。(c)反应生成物从被刻蚀表面扩散到溶液中,并随溶液排出。湿法腐蚀有各向同性的缺点,但设备简单,操作易行。由于被腐蚀材料及厚薄各不相同,光刻胶的粘附性及耐蚀性也各不相同,因此选择腐蚀液(对腐蚀液的要求是:对铝要有很好的溶解性,对光刻胶浸蚀要尽量小)和腐蚀条件,十分重要。
2)腐蚀因子:腐蚀时,腐蚀液不仅纵向腐蚀,还横向腐蚀;胶膜与金属膜粘附性好,
横向腐蚀就小。横向腐蚀是我们不希望出现的,腐蚀时要尽量避免侧向腐蚀及胶层损坏。我们常用腐蚀因子F来衡量腐蚀好坏。 F = 纵向腐蚀深度 / 横向腐蚀宽度。F可用光学比较器测定。F大,表明腐蚀效果好,F值一般在0.5-2.5之间,当F > 1时,即可用于生产。3)腐蚀方法:目前多采用浸渍法,即将片子放于腐蚀液进行腐蚀,此法横向腐蚀较大,但简单易行。此外还有喷射腐蚀法,该法腐蚀均匀,横向腐蚀小。下面主要介绍浸渍法。a)去除光刻胶底膜:显影后底膜厚一般为200-300A°,为保证腐蚀顺利进行,不分干法湿法,都要在腐蚀前去除在腐蚀窗口所残留的光刻胶,去除办法可采用等离子去胶(见光刻干法工艺),去胶功率为300W左右、时间2-3′,去胶不净是因通氧量不够,一般应达到10-2mmHg ;另外也可采用去胶剂去底膜或发烟硝酸去底膜,具体条件由实验确定。原则是既要去净残留的胶,又尽量少损伤要保留的胶。下面介绍几种湿法腐蚀常用的铝腐蚀液。b)磷酸腐蚀液:浓磷酸与铝反应产生溶于水的酸式磷酸铝,使铝膜溶除。反应如下:2AI + 6H3PO4(85%) = 2AI(H2PO4)3 + 3H2↑
加温腐蚀:水浴加温至70度,铝与浓磷酸反应激烈,会有气泡不断冒出。为消除气泡, 可在浓磷酸中加入无水乙醇(15-20%);也可用毛笔轻轻抹去气泡。要注意控制好腐蚀时间,既要腐蚀干净又不腐蚀过度。
超声腐蚀:水浴加温至70度,加超声振动(能量不能太大,否则铝易剥离),并不断把片子放入无水乙醇中去除气泡;因超声波能将腐蚀时产生的气泡震碎,故腐蚀均匀,铝条边沿陡直。在腐蚀硅铝膜(硅:1-2%)时要适当加大超声能量,并在腐蚀铝后去除表面上的硅;方法是用等离子腐蚀多晶硅的办法,时间5-10秒;或硝酸:氢氟酸 = 98:2漂洗。
磷酸使用时间过长,酸度下降,铝与磷酸会生成难溶的磷酸铝白色沉淀淀积在片子表面,对铝腐蚀不利,因此要定期更换新磷酸。
c)高锰酸钾腐蚀液:KmnO4:NaOH:H2O = 16克:5克:300毫升, 腐蚀温度25-30度,该腐蚀液优点是,因室温下腐蚀,铝条边沿整齐。缺点是,因高锰酸钾是强氧化剂,当
腐蚀时晃动不够或拿出观察时,易使反应生成的黄色二氧化锰淀积在铝表面,影响腐蚀。此时可将片子放入25%的亚硫酸钠(内加1-2滴硫酸)溶液中漂洗,溶除二氧化锰。(当铝条
间距小时,不易采用高锰酸钾腐蚀液)
d)三酸腐蚀液:硝酸:磷酸:醋酸:水(也可不加)=1:16:1:1,反应方式是:由硝酸和铝生成氧化铝,再由磷酸和水分解氧化铝; 腐蚀温度35-60度。 若用丙乙酸代替醋酸时,可用两份;若硝酸用0.5份时,腐蚀时间应梢长;溶液组成比例及温度不同,以及是否搅拌,均会影响铝的刻蚀速率;常用速率1000-3000A0/min。腐蚀液配好后,应放置一天后使用,要盖好瓶盖,以免挥发。腐蚀时要尽量做到一次腐蚀干净,若一次腐蚀不净,必须重新坚膜后再腐蚀。
e)其它:目前许多厂家生产有各种成品铝腐蚀液,可根据工艺要求选用。
4)影响腐蚀的因素:
a)温度影响:温度越高腐蚀速度越快。温度高,尺寸不易控制,严重时易发生钻蚀、断条、浮胶等现象;温度低,胶膜长时间在腐蚀液中浸泡,易出现针孔增多、浮胶等问题。b)时间影响:时间短,腐蚀不净,会出现连条、小岛,甚至模糊一片。时间长,易出现钻蚀、细条、断条、浮胶等现象。
c)腐蚀方法和腐蚀液的影响:不同的腐蚀方法和腐蚀液,腐蚀结果不同;腐蚀条件掌握不当或腐蚀液配比和浓度发生变化,都会影响腐蚀结果。
d)其它:如铝膜厚度不均匀。搅拌方法不当,不能使气泡尽快逸离腐蚀窗口,让新鲜腐蚀液不断与待腐蚀铝层接触,因而造成腐蚀不匀等。
5)注意事项:
a)腐蚀前要先试一片,确定工艺条件。
b)超声腐蚀时,片子不要垂直放置,以免因能量差异,腐蚀不均。
c)需再腐蚀时,要把片甩干,以免窗孔有水,影响腐蚀质量。
d)对腐蚀后的片子进行检查时,要先用水冲净甩干,免得残余的腐蚀液继续腐蚀。
7,去胶:
1)去胶目的:腐蚀结束,光刻胶已完成它的作用,去胶是为下工序提供一个清洁、无污染的表面。
2)去胶方法:去胶方法有溶剂去胶,氧化去胶,干法去胶(见光刻干法工艺)。
a)溶剂去胶:把带有光刻胶的基片浸泡在相应的有机溶剂(溶剂要加热到所需温度,并将片子浸泡一定时间)中,使聚合物溶解而把胶去掉;然后用去离子水冲洗甩干。去胶剂一般是含氯的烃化物(例如三氯乙烯等),并含有表面湿润剂。目前对各类光刻胶都有较高质量的去胶剂,可选择购用。
b)氧化去胶:常用的适用于铝的氧化去胶剂是发烟硝酸。具体做法是,把腐蚀后的片子用去离子水冲洗并甩干,然后放入发烟硝酸中浸泡,时间5-10′,取出后用去离子水迅速将片上的残液冲净甩干。
c)对去胶后的片子要进行检查,以便发现胶膜是否去净和了解本次光刻质量。
3)注意事项:
a)不同的去胶剂适用于不同的光刻胶,选购时要对号入座。
b)氧化去胶时要作到,去胶前片子干燥,去胶后要迅速冲净残液,以免片子表面的水份使发烟硝酸稀释为硝酸,而造成局部铝膜被腐蚀。
c)对去胶后的片子要进行检查,以便发现胶膜是否去净和了解本次光刻质量。
8,问题分析:
1)光刻分辨率:
a)影响分辨率的原因:
* 受掩模版分辨率的影响:
* 受光刻胶分辨率的影响:光刻胶分辨率随其种类不同而不同,一般来说聚合度大的胶
抗蚀能力强,但分辨率低;光刻胶中的杂质对分辨率也有影响,这些杂质常是在生产和使用光刻胶的过程中被带入。
* 光刻胶膜的质量和厚度影响:由于光线在胶膜中的散射,产生侧向光聚合反应,形
成图形边沿的过渡区,胶膜越厚,过渡区就越宽,分辨率就越低。光刻胶的固态含有率高,光线散射严重,分辨率也低。就散射所造成的影响而言,负胶比正胶严重。
* 衍射对分辨率的影响:光通过细小间隙的图形边沿,会引起衍射现象,使应遮蔽部
分胶膜感光(这种反应不完全),显影后,会留下薄的胶膜(负胶),在腐蚀时形成厚度递减区,使分辨率降低。由于光通过比波长的一半还小的物体时会产生衍射,所以用光学法暴光,其分辨率的极限为暴光波长的一半。当光刻版与胶膜接触不良时对分辨率影响很大,接触不良的原因有:片子不平或表面有凸物、灰尘,胶膜厚度不均,定位设备不良等。
* 暴光光线的平行度:在接触暴光时暴光光线应成平行光束,并与光刻版和胶膜表面
垂直,否则光刻图形将变形或模糊。
* 暴光时间和显影时间的影响:由于光的散射和衍射,暴光时间越长,分辨率越低(但暴光不足,光聚合不充分,也影响光刻质量);而显影不足会出现底膜,显影时间过长会发生钻蚀,都影响分辨率。
* 腐蚀对分辨率的影响:腐蚀时间长,横向腐蚀大,分辨率就低;。我们常用腐蚀因子表述纵向、横向腐蚀的关系,腐蚀因子越大,或刻蚀图形越浅,分辨率就越高。
* 衬底反射的影响:不同的衬底对光的反射强度不同。由于反射会使光线紊乱,造成暴光不匀而影响分辨率。
b)提高线宽分辨率的一些方法:(亦适用于微细光刻)
* 采用高分辨率光刻胶;胶要经超微过滤;胶层厚度要均匀。
* 采用高平整度、高分辩率掩膜版;晶片表面要平整洁净。
* 要滤除光源中的长波长紫外光、红外光、可见光。
* 采用蝇眼透镜等措施减少干涉效应的影响;保证光源均匀性。
* 暴光后用前烘温度烘10分钟再显影,可减少光衍射效应的影响。
* 采用百级净化工作间。严格工艺要求等。
2)控制光刻条宽的一些方法:
a)由于制版时会引起尺寸误差,因此在设计版时,要根据光刻胶的类型,提出不同要求,如对负胶,设计掩膜尺寸时可适当偏小,而正胶则相反。
b)对暴光时间的控制:由于暴光过度,显影后负胶条宽变宽,正胶条宽变窄;因此在暴光时可适当调整时间,达到控制线宽的目的。
c)显影后,如线条变宽,适当过腐蚀也可达到控制条宽的目的。
3)浮胶:
在显影或腐蚀时胶膜皱起或大片脱落。出现该现象说明胶与片表面粘附不好,须认真查明原因,去净胶膜,进行返工。(铝与胶膜粘附较好,浮胶现象不多)
a)显影时浮胶的原因:
* 匀胶前片子表面不洁净,有油污、水汽、灰尘等,或在空气中放置过久;环境湿度大。* 光刻胶配置有误或胶陈旧不洁净及存有颗粒等;胶化学反应性能不好;与铝膜结合能力差;胶膜不均匀或过厚,引起胶粘附不良。
* 前烘温度不足(膜内溶剂不能充分挥发)或过度(胶感光性能变坏)。
* 暴光不足,光硬化反映不彻底。
* 显影时间太长。
b)腐蚀时浮胶的原因:
* 坚膜不足,固化不充分。(坚膜时间太长,不易去胶)
* 腐蚀液配比失误。
* 腐蚀温度太低(腐蚀时间太长,腐蚀液会穿透或从底部渗入胶膜,引起浮胶)或太高(腐蚀液太活泼)。
4)毛刺及钻蚀:
腐蚀时腐蚀液渗入胶膜边沿,会使图形边沿局部腐蚀,破坏铝条的完整性。当腐蚀较轻时铝条会变窄;中度腐蚀,图形尺寸明显变化,边沿会出现针刺状的局部破坏,常称毛刺;情况严重时,图形边沿会出现锯齿状或绣花球似的破坏。产生原因除产生浮胶的原因外,还有光刻版有毛刺,片子表面有异物,在暴光时与版无法贴紧等。
5)小岛:
是指在腐蚀后,条之间残留有铝点、铝斑,它们会使器件绝烟电阻降低,甚至短路报废。产生小岛的原因如下:
a)版质量不好。用负胶时,在遮光区有针孔或损伤,用正胶时,在透光区有小岛。
b)暴光过度,或显影不彻底,在光刻窗口留有底膜。
c)腐蚀液不纯,粘有阻碍腐蚀的污物。腐蚀铝时要及时排除气泡,清除附着在片子表
面的反应生成物,定期更换腐蚀液。
6)针孔:
由于光刻胶膜掩蔽不完整,存在一些小孔,经腐蚀后在铝膜上会出现小的空洞,即为针孔。针孔当很小时对声表器件无大危害,但当针孔大时,必须重视。针孔产生原因如下:a)光刻版透光区有黑斑(负胶),遮光区有亮点(对正胶),造成胶被溶解,铝被腐蚀。b)胶含有杂质颗粒,显影时剥落,引起针孔;工艺卫生差,当灰尘颗粒落在片子表面、涂胶表面,会引起针孔。
c)胶层太薄,产生针孔;可降低匀胶速度,或两次匀胶,以减少针孔。
d)对负胶暴光不足,交联不充分;对正胶暴光过分,使胶层减薄,影响抗蚀性,都会
引起针孔。
e)腐蚀液配比不当,使腐蚀速度过快,易引起针孔。
9,小结(光刻各工序需控制的工艺参数):
在半导体领域,光刻工艺是一种重要的基本工艺。由于它涉及复杂的光化学反应和物理过程及许多外部条件,所以影响其结果的因素十分复杂,如除光刻工艺本身外,还有光刻版质量、光刻胶质量、基片及镀膜质量、工作环境的净化、温度、湿度等。一般的光刻工艺都需经如下工序:匀胶、前烘、暴光、显影、坚膜、刻蚀、去胶。
* 涂胶可用浸涂法、喷涂法、印刷法、旋转法等,常用自旋转法。涂胶后的胶膜厚度是需要控制的工艺参数。常通过胶的黏度、自旋转转速及温度等予以控制。
* 前烘是为了去除胶内溶剂(有利光交联),增加胶膜耐磨性及与基片粘附性。前烘方法有烘箱烘烤、铁板烘烤、红外烘烤等,前烘效果用温度和时间控制(注意控制升、降温速)。 * 暴光是为了让胶膜充分吸收光能进行光化学反应;其关键控制参数是暴光量(暴光强度和暴光时间)。暴光方法有光学暴光、电子束暴光、离子束暴光、X射线暴光等,一般工艺要求,多采用光学暴光。
* 暴光后的胶膜需在相应的显影液中,经合适的显影时间才能显出清晰图形。其中显影液的浓度、温度和显影时间都是需要控制的参数。
* 坚膜是为坚固因显影而软化、膨胀的胶膜。控制参数为坚膜温度和时间(要慢升降温)。 * 刻蚀分干法和湿法两种。对湿法刻蚀,相应的腐蚀液浓度、温度和腐蚀时间为需控制的工艺参数;对干法刻蚀,刻蚀时间、射频功率、基片温度、气体压力等是需控制的参数。 * 去胶是去除用于屏蔽的胶膜,得到所需要的光刻图形,并为下工序提供一个洁净表面。生产上常采用氧等离子去胶,去胶主要控制射频功率、去胶时间、氧气压力等工艺参数。
(三) 光刻工艺原理(干法)简介:
湿法显影时因抗蚀剂受显影液浸泡,使抗蚀剂图形发生膨胀和收缩,影响尺寸精度;湿法腐蚀时因各向同性,会造成严重的侧向腐蚀,且坚膜时又常会引起图形变形等;以上原因都严重影响湿法工艺的加工精度。另外大量化学试剂的使用不仅污染器件,同时污染环境。因此作为精细加工技术之一的干法工艺受到日益重视和发展。干法工艺包括:干法清洗,干法显影,干法刻蚀,干法去胶,其基本原理都是利用气体在高频作用下电离产生的等离子体,轰击或腐蚀基片表面以达到去除欲去除材料的目的;只是因不同的工艺有不同的要求,所以采用的腐蚀气体及腐蚀方法不同。等离子体与固体表面的反应包括纯化学作用的等离子体腐蚀、纯物理作用的离子腐蚀及同时具有化学、物理作用的反应离子腐蚀。
1,干法腐蚀原理:
1)等离子体腐蚀:在低压(13-1300Pa)下对气体施加高频电场时,气体原子或分子与
具有一定能量的电子发生碰撞,电离产生由离子、电子及中性原子和分子组成的等离子体;这种低温等离子体的电离度小,相当部分是处于激发态的原子和分子,具有很强的化学活泼性,当与被腐蚀物接触时,就发生化学反应生成挥发性物质,达到腐蚀目的。由于在低温(50-200℃)等离子腐蚀中,离子动能小,主要是活性物质(活性基)的化学反应,几乎无轰击作用。另外因等离子体中的活性物质自由程较小,可以认为到达欲腐蚀面上各处离子的碰撞几率大致相同,因而腐蚀各向同性;采用具有平行板电极结构等离子反应器,电场均匀分布在平行极板间,在电场中的离子垂直片子表面作定向运动,使腐蚀具有各向异性的特点。2)离子腐蚀:是一种纯物理加工。它是利用辉光放电将气体,如氩气,电离成带正电的离子,在低压(0.13-13Pa)中加偏压将离子加速,轰击基片表面;通过高能惰性气体离子和基片表面原子间的能量交换达到去除被腐蚀材料原子的目的。离子腐蚀具有纯度高,定向性好,均匀性好,重复性好的特点,有很高的刻蚀分辨率(0.01μ),并可通过对离子入射角的控制来实现对腐蚀剖面的控制。缺点是腐蚀速度慢,刻蚀选择性差,刻蚀时会产生再淀积现象。
3)反应离子腐蚀(RIE):是在等离子腐蚀基础上发展起来的一种腐蚀方式,它是在比
等离子腐蚀更低的压力(1.3-130 Pa)下进行的,反应气体通过放电产生各种活性等离子体,靠射频溅射使活性离子作固有的定向运动,既获得高选择比;又产生各向异性腐蚀;同时活性离子在电场作用下破坏了被刻蚀物质的原子键及清除了反应面上的生成物或聚合物,因而加速了化学反应过程。这种腐蚀既有化学作用又有物理作用,有良好的腐蚀效果。
2,干法工艺:
1)干法显影:(等离子体腐蚀)
采用负胶的干法显影机理:经匀胶-前烘-暴光后,再进行后暴光烘烤(温度时间与前烘同),此时没经暴光的抗蚀剂由于溶剂的挥发,其厚度减少40-50%,而经暴光的抗蚀剂由于光聚合不再挥发,故厚度不变;再因氧等离子体对没暴光抗蚀剂的腐蚀速率比对暴光抗蚀剂的腐蚀速率高5倍,所以当将片子放入氧等离子体中显影时,由于抗蚀剂和腐蚀速率的差异,在暴光部分抗蚀剂减薄前,没暴光区域的抗蚀剂已被腐蚀干净。当选择合适的压力(氧)、功率、温度、时间等显影条件,显影留膜率可大于85%。
采用正胶(PMMA)的干法显影机理:匀胶-前烘,用
CF4+O2等离子体处理5-15′(表面经此氟化处理后可增强
对氧等离子体的耐蚀性),用深紫外光或电子束暴光,然后
用氧等离子体显影。由于氧等离子体对暴光的PMMA比没
暴光的PMMA腐蚀速率快2-5倍,所以只要适当选择暴光
剂量、氧等离子体处理时间等条件,即可达到70%的留膜率。
2)铝的干法刻蚀:(反应离子腐蚀)
A)RIE刻蚀设备:
它包括一个高真空反应室,反应压力范围在1.3-130 Pa,室内有2个平板状电极,阳极与腔壁接地,基片放置在加有高频(13.56MHz)的阴极上,承片电极加负偏置电压。加高频电场使通入的反应气体电离,刻蚀除利用活性离子与薄膜反应外,还利用高能量离子轰击薄膜表面,引起表面原子溅射,并去除再淀积的反应物或聚合物,加速反应进行,同时达到异向腐蚀的目的。
B)铝刻蚀工艺:
a)反应机理及常添加气体:在铝的刻蚀中,刻蚀气体常采用CCl4,BCl3,它们在高频电场中被理解为:CCl4→CCl3* + Cl*,BCl3→BCl2 *+ Cl* ,与铝反应为:Al + 3 Cl*→AlCl3↑。Cl*是腐蚀Al的主要活性基,反应生成易挥发的AlCl3 (刻蚀温度为70度时,利于AlCl3的挥发)。为避免残留的铝造成绝缘电阻下降,可适当过腐蚀。为提高腐蚀速率,可在反应中加入适量Cl2 。为增加腐蚀的可控性和均匀性,可在反应中加入适量He。另外为增进异向刻蚀,除适当的离子轰击外,常添加气体如Si Cl4、C Cl4、CHF3、CH Cl3等,它们与胶中的C反应生成聚合物,沉积在金属上,可保护侧壁不受离子轰击。
b)Al2O3的影响:在刻蚀过程中,铝表面的自生氧化物Al2O3(30-50A0)会影响刻蚀进行;另外当空气中的水气进入反应室和反应物AlCl3反应,也会生成难以刻蚀的Al2O3 。为此常采用:(1)两步腐蚀法,即先加大功率,在纯铝快露出时,再降低功率。(2)在反应室前端加装进出片的予真空室(即连锁装置),采用予真空、反应室封闭法,可以减少空气中水气的影响。(3)添加气体BCl3。这是因为BCl3极易与氧和水反应,故可吸收反应室中的水气和氧气;并且BCl3还可将铝表面的Al2O3还原。具体反应如下:
O + BCl3→2Cl + B O Cl 。
c)后腐蚀现象:在干法腐蚀后的片子表面,我们常看到铝的后腐蚀现象,这是因残留在片子表面的AlCl3吸收了空气中的水,分解成盐酸造成。我们可通过如下方法改进:* 加装予真空室连锁装置。* 对取出的片子用大量的水迅速冲洗和用无水乙醇脱水。* 在正常的腐蚀后即通入适量的CF4,将残余的Cl置换为F,生成不与水反应的AlF3,隔绝Al 与Cl的接触。* 在正常腐蚀后,当基片尚未从真空室取出即用氧离子将抗蚀剂去除,并在铝表面形成Al2O3,保护铝不再被腐蚀。
d) SAW器件工艺的特殊性:
* SAW器件制作采用的是高压电材料,在受热时,表面会产生电荷,不同切向的基片电荷不同。电荷的累加会对刻蚀产生影响,在刻蚀过程中到达放置芯片的离子带正电荷,如果芯片表面也带正电,由于同性相斥,使到达阴极的离子能量降低,在刻蚀的开始阶段会降低离子的溅射作用;如果芯片表面带负电,因异性相吸,会加速离子溅射,同时削弱化学反应过程。所以在刻蚀前应先去除表面电荷,以保证工艺稳定性。
* 刻蚀均匀性:由于刻蚀后的铝条宽度对器件性能影响很大,对于批生产而言,为保证每个芯片上的管芯性能尽可能一致,常采用单片刻蚀结构,通过控制工艺条件的一致性来保证批生产的一致性。
* 离子损伤:在刻蚀过程中,高能离子的轰击会引起基片晶格损伤;在增加离子密度的同时,也增加了离子能量,将加剧其损伤,对SAW器件的影响,通常表现为损耗变大。为此我们通过:(1)在反应室加入网状第三极,通过对第三极电位的调整,可使阴极感应的自偏压降低,抑制离子轰击的损伤。(2)及时调整工艺:即当终点检测显示,金属膜厚接近零时,降第三极电压。(3)高温退火处理减少损伤(300℃、N2保护2h)。
* 选择比问题:在干法刻蚀中,选择比是很重要的特性,它的物理意义是,在相同条件下,被刻蚀材料的腐蚀速率与抗蚀剂腐蚀速率之比。选择比越大,刻蚀中损失的抗蚀剂越少,这将更有利于保证SAW器件制作中对指条相对宽度的特殊要求。反应气体的成分、流量,
RF功率、气压大小和抗蚀剂的种类都对刻蚀速率和选择比产生影响;因此必须要通过不断实验,才能取得一个良好的选择比。(因反应离子刻蚀中到达阴极的正离子有很强的能量和指向阴极的方向性,所以它的溅射作用强,但选择比小;而等离子刻蚀选择比大,但因各向同性,无法刻蚀亚微米线条)。
e)影响干法刻蚀的因素:每一种材料的腐蚀速率都与工艺条件的选择密切相关。
* 射频功率的影响:功率越大,腐蚀速率越大。但过高的功率会降低抗蚀剂的耐蚀性,使腐蚀的可控性变差。(频率越低,阴极感应的自偏压越高,离子溅射能量越大,会使选择比变差,化学腐蚀减弱,基片损伤加大;但频率过高,离子溅射作用会越小。)
* 气体流量的影响:增加流量,即增加活性离子浓度,腐蚀速率相应增大。但流量过大,会导致反应压力增高,使电子自由程缩短,气体离化率变低,腐蚀速率反而下降。
* 温度影响:反应时释放的热量会使腐蚀速率加快。为保证腐蚀的重复性,需精确控制腐蚀时的功率和温度。
* 腐蚀气体的种类对腐蚀速率影响至关重要。
f)介绍干法腐蚀终点检测:进行干法腐蚀终点检测可确保腐蚀精度,提高腐蚀重复性,监控腐蚀过程,实现刻蚀自动化。光学反射法是常用的有效方法,它是利用一束单色光(如He-Ne 激光)照射在样品上,根据被腐蚀材料与衬底材料反射率的差别,产生反射光强度的变化来确定腐蚀终点。如当腐蚀铝膜时,得到的是具有恒定幅度的反射信号强度,随着薄膜腐蚀完毕,反射强度迅速变小,即显示出腐蚀终点。
3)干法去胶(等离子体腐蚀)
a)反应机理:在干法去胶工艺中,氧是主要腐蚀气体。它在低压(1.3-13Pa)反应室中受高频(13.56MHz)电场作用,电离产生氧离子、游离态氧原子O*、氧分子和电子等混合的等离子体,其中具有强氧化能力的游离态氧原子O*(约占10-20%)在高频电压作用下与光刻胶膜反应:O2→O*+ O*,C x H y + O*→CO2↑+ H2O↑。反应后生成的CO2和H2O,随即被抽走。
b)操作方法:将待去胶片插入石英舟并平行气流方向,推入真空室两电极间,抽真空到1.3 Pa,通入适量氧气,保持反应室压力在1.3-13Pa,加高频功率,在电极间便产生淡紫色辉光,通过调节功率、流量等工艺参数,可得不同去胶速率,当胶膜去净时,辉光消失。c)影响因素:
* 频率选择:频率越高,氧越易电离形成等离子体。频率太高,以至电子振幅比其平
均自由程还短,则电子与气体分子碰撞几率反而减少,使电离率降低。一般常用频率为13.56MHz。
* 功率影响:对于一定量的气体,功率大,等离子体中的的活性粒子密度也大,去胶速度也快;但当功率增大到一定值,反应所能消耗的活性离子达到饱和,功率再大,去胶速度则无明显增加。由于功率大,基片温度高,所以应根据工艺需要调节功率。
* 对真空度的选择:适当提高真空度,可使电子运动的平均自由程变大,因而从电场获得的能量就大,有利电离。另外当氧气流量一定时,真空度高,则氧的相对比例就大,产生的活性粒子浓度也就大。但若真空度过高,活性粒子浓度反而减小。
* 氧气流量的影响:氧气流量大(反应室压力大),活性粒子密度大,去胶速率加快;但流量太大,则离子的复合几率增大,电子运动的平均自由程缩短,电离强度反而下降。若反应室压力不变,流量增大,则被抽出的气体量也增加,其中尚没参加反应的活性粒子抽出量也随之增加,因此流量增加对去胶速率的影响也就不甚明显。
d)其它:
* 不同的抗蚀剂在相同条件下,去胶速率不同。去胶速率一般常控制在>300nm/min。
* 当在氧气中加入少量CF4(1-2%),可提高去胶速度,而又不会引起衬底过腐蚀。
去胶后,抗蚀剂中不挥发杂质可能残留在基片表面,造成产品性能不良;所以要尽量选择含杂质少的光刻胶,或用其它方法去除表面残留物。另外对去胶终点的控制要恰到好处,去胶时间短,会有残胶存留,时间长,会使铝膜氧化。
(四) 剥离工艺简介:
1, 剥离工艺的特点:
利用剥离技术制作微细金属图形具有设备投资少,剥离过程无物理和化学损伤,基片表面不易污染等优点。剥离技术的工艺流程是:清洗→涂胶→前烘→暴光→后前烘→显影→坚膜→蒸发→剥离。它是首先在洁净的晶片上涂上一层或多层光刻胶,进行暴光、烘烤、显影、坚膜等工艺处理,在基片上得到呈倒“八”字形光刻胶侧剖面几何图形,然后通过蒸发,在基片表面获得不连续的金属层,最后剥离掉光刻胶掩模层及其上的金属层,而与基片紧密接触的金属层则保留下来。
由于金属图形线宽尺寸完全由光刻胶暴光显影后的窗口区域决定,而不是由干法刻蚀或湿法腐蚀决定,所以在亚微米范围内可以实现精确的掩模图形转移和优良的线宽控制。为能有效剥离,剥离光刻掩模层必须满足以下要求:
1)要有良好的金属图形层沉积在光刻胶掩断开区域
内,而光刻胶掩模上的金属层与膜断开区域内的金属层
要相互分离,这就要求光刻胶掩模层厚度一定要比金属
层厚。
2)光刻胶要有高分辨率;在烘烤、蒸发等环境下,
胶膜的膨胀率要小,热稳定性要好,变形小,易剥离。
3)光刻掩膜层图形侧剖面要呈倒“八”字形,这是
剥离成功的关键。
4)脆性金属材料(如铝)比延展性金属材料(如金)
易剥离。
在剥离技术中,金属图形线条的粗细受光刻分辩率的限制。事实上,金属层图形尺寸是由掩模图形尺寸决定,而掩模图形尺寸是由暴光掩模版尺寸、暴光量和显影等参数及工艺决定。在亚微米工艺中,光刻胶层很薄,但为了有利剥离,胶层又不能太薄;因此使用剥离技术还有许多工作要作。
2,剥离技术:
正性胶具有灵敏度高,膨胀形变小,形成图形稳定性好等优
点;但若制作1μ以下线条,用接触性暴光会十分困难,此时则
应选用相应的暴光技术。常用的剥离技术有氯苯浸泡法、图象
反转法、多层掩模剥离法及负性光刻胶法等。
1)氯苯浸泡法:
a)基本原理:AZ系列正性胶在氯苯中浸泡易被除去某些低
分子量物质,使光刻胶表层被浸泡部分在显影液中几乎不溶,
而表层下的光刻胶仍保持原来的溶解度。显影时,当暴光部分
的胶被向下溶解的同时,光刻窗口的侧面也发生横向溶解,由
于表层胶受氯苯浸泡不被溶解,而表层下的胶仍保持原来的溶
解度,所以只要控制好“过显影”时间,就可在显影后的光刻
窗口得到一个“凸沿”,使光刻掩膜层图形侧剖面呈倒“八”字型,使蒸发时的金属膜在“凸沿”处分离。
b)氯苯浸泡工艺:在洁净基片表面涂AZ系列正性胶→90℃烘箱烘烤10-15min → 通 过掩膜版暴光 → 将基片放在氯苯溶液中浸泡10-15min(时间长短取决于对“凸沿”厚度
要求)→ 90℃烘箱烘烤30min → 浸泡显影并轻微晃动(此时,在光刻胶掩膜层暴光部分侧面产生暗刻蚀,“凸沿”形成)→清洗烘干,电子束镀膜→ 在丙酮或去膜剂中超声去胶(完成光刻胶掩膜溶解和基片上不需要金属的物理剥离)。
c)其它:在实际操作中需要注意如下问题:
* 光刻胶掩膜层要有足够伸出的“凸沿”,其下面侧壁的斜
度和其厚度(强度)等是应考
虑的重要因素。这两种性能应保证:在电子束蒸发时,“凸沿”
不变形,不塌陷;金属层不会沿“凸沿”下部斜面堆积成翼尖
状,以至于与“凸沿”上的金属相连。
*“凸沿”厚度由氯苯浸泡时间和显影决定。
* 喷雾显影会破坏“凸沿”的形成。
* 氯苯有毒,注意通风保护。
2)图象反转法:
a)基本原理:首先光刻胶膜经近紫外(NUV)暴光产生潜
在的正性图形,然后图形经反转烘烤,已暴光的光刻胶发生新
的交连反应,在显影液中变为不可溶;接着通过大面积泛暴光,
使还没暴光区域暴光,变为显影可溶;最后通过碱性显影得到
高质量的负胶图形。由于首次暴光形成的正潜影图形侧剖面呈倒“八”字型,当烘烤转性后所得到的负胶图形也就自然呈倒“八”字型。
b)工艺步骤:AZ5200E系列光刻胶为适应于亚微米工艺图
象反转用光刻胶。涂AZ5200E系列光刻胶→予烘烤→掩膜暴光→图形反转烘烤→泛暴光→显影→烘烤→电子束镀膜→剥离。
3)负性光刻胶法:
a)基本原理:负性光刻胶在紫外光照射下产生光化反
应,使高分子化合物交连成不溶于
显影液的分子结构,而未被光照射的部分溶于显影液被显
影。因在暴光时,胶膜上层光化反应强于下层,因此,在
显影后留在基片上的光刻胶剖面开口区域自然成“八”字
型(掩膜层图形侧剖面呈倒“八”字型),即有利于剥离
的侧剖面。
b)对负性光刻胶的要求:一般紫外用负性胶以环化橡胶或聚肉桂皮酸等为基质。膜厚在1μ时分辨率≤1.5μ,该类胶可塑性变化较大,易膨胀、软
化,不能用于亚微米剥离。由于负胶比正胶耐热性差,当采
用负胶剥离时,要尽量选用膨胀系数小的负性胶。
目前,日本用以酚醛树脂为基质的负性胶(热膨胀系数很
小),采用接触式深紫外暴光,已用剥离法制作出4.5G滤波
器,线宽0.2μ。
4)多层掩膜剥离法:
a)基本原理:利用多层掩膜剥离的方法很多,通常为双
层结构。通过对底层胶的柔性烘
烤(或泛暴光)和对上层胶的选择性暴光,然后在单一或多
种显影液中显影,即可得到适合于剥离的具有暗刻蚀侧剖面
的掩膜图形;在该剥离法中,形成图形的关键在于上层胶,
因为它确定了金属图形的尺寸;底层胶显影尺寸略大于上
层,并提供了掩膜层和金属层之间的厚度差,因而可消除金属台阶覆盖,使掩膜上的金属层与和基片接触的金属层分离,确保顺利剥离。
b)介绍两个实例:
* 有公司用AZ2400和AZ1350J进行剥离。工艺流程如下:
涂AZ1350J光刻胶→泛暴光→用CF4/O2等离子体处理(为
阻止两层胶相互混合)→涂AZ2400光刻胶→掩蔽暴光。由于两层胶在给定显影液中溶解度有较大差异,用单步显影工艺即可得到适合剥离的掩膜图形。
* 希普列公司推出LOL1000和LOL2000剥离层。将LOL
涂在基片表面,柔性烘烤后,涂正性胶,作选择性暴光层;LOL产品可兼容g线和i线光刻胶,两层间不会产生混合,并兼容KOH、NaOH、TMAH(四甲基氢氧化胺)显影液,在亚微米工艺中应用,可对其侧向暗刻蚀溶解速率进行有效控制,生产中批之间有良好一致性;若严格工艺条件,用此技术可作出0.3μ的金属线条。其工艺流程如下:
涂LOL(厚应为金属膜厚的1.5-2倍,或视情况而定)→柔性烘烤(140-170℃,10-15′)→涂正性胶并柔性烘烤(胶厚与光刻条宽有关,具体请参考“镀膜工艺原理”)→对上层正性胶(g线或i线)暴光→用LOL专用显影液(MIF或MIB)显影→镀膜金属→用去膜液剥离光刻胶、LOL和多余金属。
3,有关问题:
1)在剥离技术中,最关键最重要的是形成有利于剥离成功的光刻胶掩膜倒“八”字或有暗刻蚀的侧剖面,并且能精确控制。
2)由于LT、LN、水晶等压电晶片均为半透明晶片,暴光光束入射到晶片表面会引起反射、透射和吸收,并在晶片背面形成慢散射,导致光刻线宽失真。为防止上述现象,常采用方法有:a)在正面和背面涂防反射层。不同的暴光波长及不同的图形分辨率应选用不同的防反射涂层及不同的涂层厚度。防反射涂层的最佳厚度D = λ/4n (其中λ为暴光波长,n为防反射涂层的折射率)。b)用化学淀积、溅射或蒸发的办法,在晶片背面生长一定厚度的SiO x。C)通过对LT、LN晶片进行化学还原处理,使晶片呈黑色,压电效应无衰减,热释电效应基本消失,光透过率明显下降,晶片对紫外光吸收明显加强。
3)为保证图形精度,镀膜时,根据图形尺寸,金属粒子必须以一定的角度入射光刻窗口,而在所有的成膜方法中,只有电子束镀膜可以满足要求,具体请参看“镀膜工艺原理”。4)在镀膜前,要注意清除光刻窗口内残余有机物。
(五)微细光刻技术简介:随着电子技术的发展,光刻线宽已进入亚微米数量级,通常称光刻线宽< 1μ 的光刻技术为亚微米光刻技术,以下从几方面作简单介绍:
1,对光刻胶的要求:
1)分辨率高,厚-宽比大,反差和留膜率高。
2)合适的暴光和显影时间,合适的灵敏度。
3)最佳的光学吸收系数,在长波长区急速切断。
4)和衬底粘附性好,涂层厚度均匀。
5)缺陷密度小,抗蚀剂和显影液微粒< 0.2μ,金属杂质含量< 0.5ppm。
6)具有和亚微米光刻技术相适应的化学、物理性质(如耐酸性、等离子刻蚀等)
2,暴光技术:根据需要,可选择如下方法:
暴光技术暴光方式及线宽(μm)备注
紫外暴光接触式:1μm,缩小投影式< 1μm
远紫外暴光(200-260nm)接触式:0.2μm,缩小投影式< 1μm
电子束暴光扫描式(直写):0.1μm
投影式 < 0.5μm 直接暴光,不需掩模,效率低。掩模制作困难。
离子束暴光聚焦式:0.03μm
缩小投影式 < 0.1μm 直接暴光,不需掩模,效率低。掩模制作困难。
X射线暴光
(4-15A0)
接近式:0.05μm掩模制作困难。
3,铝刻蚀技术:
对微细光刻,铝刻蚀必须采用干法刻蚀或金属剥离技术。对其优劣作简单对比:
设备工艺
难易暴光
影响
过刻蚀对基片
伤害程度
对微粒敏
感程度
精度控制最小线
宽
干法刻蚀设备
价高
复杂
工艺
复杂
正面
反射
光
过刻蚀及残余
气体易对表面
造成伤害导致
频偏。
大,易造成
断路。
控制线宽好,线
条边缘好,但影
响精度因素多。
可得到
窄的线
宽
金属剥离简单易掌
握
背面
散射
光
不易产生
金属残余
和形成短
路。
控制线宽好,线
条边缘好,易处
理厚金属
受局限
4,问题及原因:
问题原因
图形尺寸比掩膜图形尺寸大1)暴光时间过长。2)显影液配比不当,浓度过高。3)显影液温度过高,显影时间过长。4)前烘温度过低或时间太短。5)腐蚀不当,时间过长或温度过高。6)掩膜尺寸错误。
微细线条显影不出1)暴光时间不足(或暴光灯失效)。2)前烘温度过高或时间过长。3)片子(版)不平整或表面脏。4)接触暴光时,片与版压力不当。5)胶过厚或不均匀。
微细线条不均匀1)光源不均匀。2)胶厚不均匀或有赃物。3)接触暴光时,片与版压力不均匀。4)片子不平整或表面脏。5)版图形尺寸不均或表面有赃物。
线条边沿不整齐1)暴光不足。2)接触暴光时,片与版压力不够。3)显影或腐蚀时晃动方向不规则。4)显影时间不够。4)版图形边沿不整齐,过渡区大。6)坚膜温度太高。7)腐蚀时间不够。
浮胶或钻蚀1)片子表面呈亲水性。2)环境湿度大或温度低。3)前烘或坚膜温度低,或时间不够。4)腐蚀温度高或时间长。
编者:杜文玺 duwenxiabc@https://www.360docs.net/doc/613788939.html,
声表面波滤波器原理和应用
声表面波滤波器原理及应用 1.声表面波滤波器(SAWF)的结构和工作原理 声表面波滤波器(SAWF)是利用压电材料的压电效应和声特性来工作的。具有压电效应的材料能起到换能器的作用,它可以将电能转换成机械能,反之亦然。压电效应包括正压电效应和反压电效应。所谓正压电效应是指压电材料受力变形产生电荷,因而产生电场的效应,即由机械能转换为电能,反压电效应是指压电材料在外加电场的作用下,产生机械形变的效应,也即由电能转换为机械能。 声表面波滤波器(SAWF)的结构如图2—12所示。这种滤波器的基片是由压电材料(如铌酸锂或石英晶体)制成,在基片上蒸镀两组“叉指电极”,一般由金属薄膜用光刻工艺刻成。左侧接信号源的一组称为发送换能器,右侧接负载的一组称为接收换能器,图中a、b分别为电极宽度和极间距离,W为相邻叉指对的重叠长度,称为“叉指孔径”。当交变的电信号u s 加到发送换能器的两个电极上时,通过反压电效应,基片材料就会产生弹性形变,这个随信号变化的弹性波,即“声表面波”,它将沿着垂直于电极轴向(图中x方向)向两个方向传播,一个方向的声表面波被左侧的吸声材料吸收,另一方向的声表面波则传送到接收换能器,由正压电效应产生了电信号,再送到负载R L。但叉指换能器的形状不同时,滤波器对不同频率信号的传送与衰减能力就会不一样。
图2—12 声表面波滤波器结构示意图 为了简便起见,仅分析“均匀”型叉指换能器的频率特性。所谓“均匀”型就是指图2—12中各叉指对的参数a、b、W 都相同,设换能器有n+1个电极,并把换能器分为n节或N个周期(N=n/2),各电极将激发出相同数量的声表面波,声表面波的波长由指装点基的宽度a和间隔b决定,声表面波的频率与传播速度有关,其自然谐振频率(或机械谐振频率)为 v是声表面波的传播速度,约为3×103m/s,比光速小很多,比声速高9倍多。在f0一定,速度v低时(a+b)就可以小,所以声表面波器件的尺寸可以做得很小,但f0很低,则(a+b)就增大,SAWF的尺寸就增大,因此它适合工作在高频或超高频段。 叉指换能器的尺寸决定后,换能器的f0就固定了,当外加信号的频率等于f0时,换能器各节电极所激发的声表面波同相叠加,振幅最大,即所激发出的声表面波幅值最大;当外加信号的频率偏离f0时,换能器各节电极所激发的声表面波振
混床操作流程
混床 混床是通过离子交换的方法制取去离子水。当阴阳树脂吸附饱和后,分别用一定浓度的NaOH和HCl再生。本系统双柱混床再生方式采用酸碱分步再生方式。 1工艺参数 a.运行:运行流速15-30米/小时,出水水质达不到设计指标即为运行终点。 b.分层:反洗流速10米/小时,反洗时间15分钟。 c.进碱:碱用量120-160克/升树脂,再生液浓度3~5%,再生液流速3~5米/小时,时间约为30分钟。 d.置换:流速同再生流速,时间为30分钟,至出水pH与进水pH相同为止。 e.进酸:盐酸用量120-160克/升树脂,再生液浓度4~6%,再生液流速3~5米/小时,时间约为30分钟。 f.快冲洗:流速为20米/小时,至排水与进水pH接近为止。 g.混合:压缩空气压力0.1~0.15MPa,气量2.5~3.0米3/米2〃分,混合时间为1~5分钟。 h.正洗:正洗流速为15~30米/小时,以排水符合出水水质指标为终点,正洗结束后转入运行。 2混床操作步骤 ①运行:
a.混床运行前先进行排气,排气时开启上进阀、排气阀,当排气 管路出水时,排气完毕。 b.排气完毕后,打开下排阀,同时关闭排气阀,当柱子下排出水 符合指标,开启出水阀,同时关闭下排阀,混床投入运行。 ②反洗分层 当混床出水水质达不到指标时,树脂就要再生。再生之前,先要进行反洗分层,反洗分层根据阴、阳树脂的比重不同,通过树脂沉降来实现的。 a.开启上排阀,逐渐调节下进阀,以缓慢增大下进流量,直至下 进流速10米/小时左右。使树脂得到充分展开,树脂碎粒、悬 浮物从塔顶部排掉。 b.约15分钟后,逐渐降低下进流量。使树脂颗粒逐步沉降。 分层效果可根据树脂沉降后界面是否清晰来判断,如果一次操作未达到要求,可重复操作直至分层清晰,都仍未达到要求,则须采取强迫失效方法。 ③失效 树脂分层不清是由于阳、阴树脂失效程度不同造的,遇到这种情况可用进碱的方法强制树脂失效。 a.打开下排阀、排气阀,将水排至树脂层上150mm左右。 b.关闭下排阀,打开进碱阀,碱喷水阀,吸碱阀,压力水阀,下 排阀,开启中间增压泵,调节下排阀,使混床进出碱量平衡, 此时碱液自上而下流经整个树脂层,使阳树脂失效。
声表面波简介
声表面波简介 声表面波技术是六十年代末期才发展起来的一门新兴科学技术,它是声学和电子学相结合的一门边缘学科。由于声表面波的传播速度比电磁波慢十万倍,而且在它的传播路径上容易取样和进行处理,因此,用声表面波去模拟电子学的各种功能,能使电子器件实现超小型化和多功能化。同时,由于声表面波器件在甚高频和超高频波段内以十分简单的方式提供了其它方法不易得到的信号处理功能,因此,声表面波技术在雷达、通信和电子对抗中得到了广泛的应用。 声表面波是沿物体表面传播的一种弹性波。早在九十多年前,人们就对这种波进行了研究。1885 年,瑞利根据对地震波的研究,从理论上阐明了在各向同性固体表面上弹性波的特性。但由于当时的科学技术水平所限,这种弹性表面波一直没有得到实际上的应用。直到六十年代,由于半导体平面工艺以及激光技术的发展,出现了大量人造压电材料为声表面波技术的发展提供了必要的物质和技术基础。 1949 年,美国贝尔电话实验室发现了LiNbO3单晶。1964 年产发表了激发弹性表面波平面结构换邹器的专利。特别应该指出的是,1965 年,怀特(R . M.white)和沃尔特默(F.W.voltmer )在应用物理杂志上发表了题为“一种新型表面波声-电换能器― 叉指换能器”的论文,从而取得了声表面波技术的关键性突破。 声表面波器件的基本结构和工作原理 声表面波器件是在压电基片上制作两个声一电换能器―叉指换能器。所谓叉指换能器,就是在压电基片表面上形成形状像两只手的手指交叉状的金属图案,它的作用是实现声一电换能。声表面波器件的工作原理是,基片左端的换能器(输入换能器)通过逆压电效应将愉入的电信号转变成声信号,此声信号沿基片表面传播,最终由基片右边的换能器(输出换能器)将声信号转变成电信号输出。整个声表面波器件的功能是通过对在压电基片上传播的声信号进行各种处理,并利用声一电换能器的待性来完成的。 声表面波技术有如下的特点: 第一,声表面波具有极低的传播速度和极短的波长,它们各自比相应的电磁波的传播速度的波长小十万倍。在VHF 和UHF 绳段内,电磁波器件的尺寸是与波长相比拟的。同理,作为电磁器件的声学模拟声表面波器件,它的尺寸也是和信号的声波波长相比拟的。因此,在同一频段上,声表面波器件的尺寸比相应电磁波器件的尺寸减小了很多,重量也随之大为减轻。例如,用一公里长的微波传愉线所能得到的延迟,只需用传输路径为1 。m 的声表面波延迟线即可完成。这表声表面波技术能实现电子器件的超小型化。 第二,由于声表面波系沿固体表面传播,加上传播速度极慢,这使得时变信号在给定瞬时可以完全呈现在晶体基片表面上。于是当信号在器件的输入和输出端之间行进时,就容易对信号进行取样和变换。这就给声表面波器件以极大的灵活性,使它能以非常简单的方式去.完成其它技术难以完成或完成起来过于繁重的各种功能。比如脉冲信号的压缩和展宽,编码和译码以及信号的相关和卷积。一个实际例子是1976 年报道的一个长为一英寸的声表面波卷积器,它具有使两个任意模拟信号进行卷积的功能,而它所适应的带宽可达100MHz ,时带宽积可达一万。这样一个卷积器可以代替由几个快速傅里叶变换(FFT )链作成的数字卷积器,即实际上可以代替一台专用卷积计算机。此外,在很多情况下,声表面波器件的性能还远远超过了最好的电磁波器件所能达到的水平。比如,用声表面波可以作成时间-带宽乘积大于五千的脉冲压缩滤波器,在UHF 频段内可以作成Q 值超过五万的谐振腔,以及可以作成带外抑制达70dB 、频率达1 低Hz 的带通滤波器。 第三,由于声表面波器件是在单晶材料上用半导体平面工艺制作的,所以它具有很好的一致性和重复性,易于大量生产,而且当使用某些单晶材料或复合材料时,声表面波器件具有极高的温度稳定性。 第四,声表面波器件的抗辐射能力强,动态范围很大,可达100dB 。这是因为它利用的是晶体表面的弹性波而不涉及电子的迁移过程。
光刻工艺流程
光刻工艺流程 Lithography Process 摘要:光刻技术(lithography technology)是指集成电路制造中利用光学—化学反应原理和化学,物理刻蚀法,将电路图形传递到单晶表面或介质层上,形成有效图形窗口或功能图形的工艺技术。光刻是集成电路工艺中的关键性技术,其构想源自于印刷技术中的照相制版技术。光刻技术的发展使得图形线宽不断缩小,集成度不断提高,从而使得器件不断缩小,性能也不断提利用高。还有大面积的均匀曝光,提高了产量,质量,降低了成本。我们所知的光刻工艺的流程为:涂胶→前烘→曝光→显影→坚膜→刻蚀→去胶。 Abstract:Lithography technology is the manufacture of integrated circuits using optical - chemical reaction principle and chemical, physical etching method, the circuit pattern is transferred to the single crystal surface or the dielectric layer to form an effective graphics window or function graphics technology.Lithography is the key technology in integrated circuit technology, the idea originated in printing technology in the photo lithographic process. Development of lithography technology makes graphics width shrinking, integration continues to improve, so that the devices continue to shrink, the performance is also rising.There are even a large area of exposure, improve the yield, quality and reduce costs. We know lithography process flow is: Photoresist Coating → Soft bake → exposure → development →hard bake → etching → Strip Photoresist. 关键词:光刻,涂胶,前烘,曝光,显影,坚膜,刻蚀,去胶。 Key Words:lithography,Photoresist Coating,Soft bake,exposure,development,hard bake ,etching, Strip Photoresist. 引言: 光刻有三要素:光刻机;光刻版(掩模版);光刻胶。光刻机是IC晶圆中最昂贵的设备,也决定了集成电路最小的特征尺寸。光刻机的种类有接触式光刻机、接近式光刻机、投影式光刻机和步进式光刻机。接触式光刻机设备简单,70年代中期前使用,分辨率只有微
声表面波器件工艺原理-9倒装焊工艺原理
九,声表器件倒装焊工艺原理 序:倒装芯片(FC)技术,是在芯片的焊接区金属上制作凸焊点,然后将芯片倒扣在 外壳基座上,以实现机械性能和电性能的连接,由于FC是通过凸焊点直接与底座相连,因此与其它互连技术相比,FC具有最高的封装密度、最小的封装尺寸(线焊可焊的最小陶瓷外壳为3×3mm,而FC可以作到芯片级)、最好的高频性能(电感小)、最小的高度、最轻的重量,以及产品高可靠、生产高工效等。倒装焊工艺:主要由UBM的形成、凸点的制作、倒装焊接三部分组成。 (一)UBM的形成: 当凸焊点材料与芯片上的焊接区金属不能很好浸润粘附时(或接触电阻大,或热匹配差,或两种材料间易形成会导致键合强度降低的金属间化合物),需要在凸焊点与芯片压焊块之间置入一层既能与芯片焊接区金属良好粘附、又能与凸焊点良好浸润、还能有效阻挡两者之间相互反应扩散的金属膜(UBM),因我们无法找到可同时满足上述要求的材料,所以通常UBM由多层金属膜组成。(说明:与凸点连接的还有底座上相应的焊接点,由于在底座制作时该部位已镀有多层金属,能满足要求,固在此不于讨论。) 1,对UBM的各层要求及材料选择: 1)粘附层:要求与铝膜及钝化层间的粘附性好,低阻接触,热膨涨系数接近,热应力小。常选用材料有:Cr、Ti、Ti-W、Al、V等,因它们与Al浸润性很好,固该层可较薄。2)扩散阻挡层:能有效阻挡凸焊点材料与铝间的相互扩散,以免形成不利的金属间化合物,特别是金凸焊点,在高温下与铝可生成Al2Au、AlAu、AlAu2、Al2Au5等脆性金属间化合物及在接触处相互扩散形成空洞,导致键合强度降低甚至失效。该层常用材料有:Ti、Ni、Cu、Pd、Pt、Ti-W等。(当用软焊料如PbSn作凸点时,由于其回流时会吃掉浸润层,直接与阻挡层接触;此时阻挡层应足够厚,且与凸点相浸润,不反应产生有害物) 3)浸润层:要求一方面能和凸焊点材料良好浸润,可焊性好,且不会形成不利于键合 的金属间化合物;另一方面还能保护粘附层和阻挡层金属不被氧化、粘污。该层常选用薄的金膜、金的合金膜或较厚的铜膜(用于焊料凸焊点)。 2,UBM的制作: 1)UBM的组合选择:对于金凸焊点,常选用的UBM为:Cr/Ni/Au、Ti/Ni/Au、Ti/Pt/Au、Ti-W/Au等;对于PbSn凸焊点,常选用的UBM有:Ti-W/Cu、Ti-W/Au/Cu、Cr/Cr-Cu/Cu、Al/Ni-V/Cu、Ti/Cu、Ti-W/Cu/化学镀Ni等。 2)UBM的制作方法:UBM的制作是凸焊点制作的关键工艺,其质量好坏直接影响凸焊点质量、倒装焊接的成功率和封装后凸焊点的可靠性。由于UBM是多层金属,为防止薄膜间形成氧化膜夹层,对UBM的制作基本上都是采用溅射或电子束蒸发,在高真空腔内一次完成(当需要制作厚金属膜时,则采用电镀或化学镀)。为防止多层金属腐蚀时造成凸点脱落,可采用剥离技术(电镀法制凸点除外),既可解决腐蚀不易控制,又可简化工艺,提高芯片凸点可靠性;这对换能器裸露于芯片表面的声表器件尤其适宜。 (二)凸焊点制作: 1,凸焊点常用材料: 要具有电阻率小、延展性好、化学性能稳定等特点,同时凸点(包括UBM)材料还要能承受器件在加工、使用、老化、可靠性实验等过程中所需承受的条件。 1)Au:由于金浸润性好,延展性好,内应力小,接触电阻小,化学性能稳定,因此是 高频、高可靠器件常用的凸点材料。现在已可作节距为20μ,直径为20μ,高为15μ的金凸点。对小尺寸、高密度的金凸点的制作主要是用厚金电镀技术,低密度的金凸点可用金丝球焊切尾制作。目前国内无氰电镀金凸点剪切强度已达11.8 mg/μm2,高度容差±1.4μm(优于美国公司标准:剪切强度>8.7mg/μm2,高度容差:管芯内±1.5μm,圆片内±2.5μm)。
混床操作详细-很有用
混床操作维护手册 1、结构形式 设备本体是带上下碟形封头的圆柱形钢结构,内壁衬5mm耐酸耐碱硬橡胶防 腐;设备内部中排装置由不锈钢管、不锈钢缠绕管焊制而成;集水装置为衬胶多 孔板配滤水帽。进水配水采用喇叭口布水。设备本体内装填强酸强碱型树脂。 成套设备的本体外部装配有各种控制阀门并留有各种仪表接口,便于用户现 场装接和实现水站正常运行。 床内装填料高度: 混床:阳树脂 001x7 600 mm 阴树脂 201x7 1200 mm 混床的运行、再生专门配置了UPVC操作屏。 2、操作说明 2.1 正洗 打开混床进水阀一、排气阀,水流自上而下,当水充满设备时打开下排阀, 关闭排气阀,正洗流速同制水流速,当出水电阻率大于出水要求时,转入制水。 2.2 制水 正洗结束,打开出水阀,关闭下排阀,稳定制水流量,直至出水电阻率小于 要求时,制水周期结束。 2.3 再生 2.3.1 反洗预分层 打开混床反洗阀、反洗排放阀,控制反洗分层流速10 m/h左 右,以树脂充分膨胀流动,且正常颗粒树脂不被水冲出为最佳控 制流速,以阴阳树脂基本分层为反洗终点。 2.3.2 沉降 打开排气阀,使反洗预分层后展开的树脂自然、均匀地沉降下 来,而后打开下排阀,使容器内液面降至树脂层面以上10~20cm 处,避免进再生液时不必要的稀释。 2.3.3 失效 打开混床进碱阀、进水阀二、下排阀,浓度按4%左右控制,并注意当喷射 混床操作屏示意图
器进水流量发生变化时, NaOH吸入量也会发生变化,要加以调整; 进碱时间45分钟左右。 2.3.4 反洗分层 打开混床反洗阀、反洗排放阀,控制反洗分层流速10 m/h左右,以树脂充分膨胀流动,且正常颗粒树脂不被水冲出为最佳控制流速,以阴阳树脂分层界限分明为反洗终点。反洗结束时应缓慢关闭反洗阀,使树脂颗粒逐步沉降,以达到最佳分层效果。如一次操作未达要求,可重复操作以达到满意的效果。 2.3.5 沉降 打开排气阀,使反洗分层时展开的树脂自然沉降下来,并打开中排阀,使容器内液面降至树脂层面以上10~20 cm处,避免进再生液时不必要的稀释。 2.3.6 再生:采取分步再生 ①进碱 打开混床进碱阀、中排阀、反洗进水阀,进碱阀进碱与反洗进水阀进水同步进行,碱、水从中排口排出。再生液浓度、再生时间同“失效”步骤相同。 ②进酸: 打开混床进酸阀、进水阀二、反洗进水阀,进酸阀进酸与进水阀进水同步进行,酸、水从中排口排出。再生液浓度按4%左右控制,并注意当喷射器进水流量发生变化时,HCl吸入量也会发生变化,要加以调整;进酸时间30分钟左右。 2.3.7 置换清洗 由进酸、进碱阀中吸入适量清水(混床出水),由中排阀排出,然后打开混床进水阀二、反洗进水阀,以上下等量水流量进行清洗。清洗时间为半小时或以排水基本中性为终点。 2.3.8 混合 ①排水 打开排气阀、中排阀,将容器内积水排至树脂层面以上10~20 cm处,使树脂层有充分的混合空间。 ②混合 打开反洗排水阀、排气阀、进气阀,氮气(或压缩空气、真空抽气等)压力:1~1.5 kg/cm2,混合时间为10分钟左右,或以容器内两种树脂充分混合而定。 ③排水
声表面波器件工艺原理-3光刻工艺原理
三,声表器件光刻工艺原理: 目录: (一)光刻胶:1,正性光刻胶2,负性光刻胶3,光刻胶的性质 (二)光刻工艺原理(湿法): 1,匀胶:1)匀胶方法2)粘附性3)光刻胶的厚度4)膜厚均匀性5)对胶面要求6)注意事项 2,前烘:1)前烘目的2)对前烘温度和时间的选择3)前烘方法 3,暴光:1)暴光目的2)暴光技术简介3)暴光条件选择4)暴光不良原因 4,显影:1)显影目的2)显影方法3)影响显影质量的因素4)常见问题5)其它 5,坚膜:1)坚膜目的2)坚膜方法3)问题讨论 6,腐蚀:1)腐蚀目的2)腐蚀因子3)腐蚀方法4)影响因素5)注意事项 7,去胶:1)去胶目的2)去胶方法3)注意事项 8,问题分析:1)光刻分辨率2)控制光刻线宽的方法3)浮胶4)毛刺及钻蚀5)小岛6)针孔 9,小结(光刻各工序需控制的工艺参数) (三)光刻工艺原理(干法)简介: 1,干法腐蚀原理:1)等离子体腐蚀2)离子腐蚀3)反应离子腐蚀 2,干法工艺:1)干法显影2)铝的干法刻蚀3)干法去胶 (四)金属剥离工艺简介:1)剥离工艺特点2)剥离技术3)有关问题 (五)微细光刻技术简介:1)抗蚀剂2)暴光技术3)刻蚀技术4)问题及原因 序: 光刻是SAW器件制造的关键工艺,是一种复印图象同化学腐蚀相结合的综合技术。它先采用照相复印的方法,将光刻版上的图形精确的复印在涂有感光胶的金属膜层上,然后利用光刻胶的保护作用,对金属层进行选择性化学腐蚀,从而在金属层上得到与光刻版相应的图形,并要求图形线条陡直、无钻蚀、无断条和连指等。影响光刻质量的因素很多,除暴光技术外,还有掩膜版、金属膜、光刻胶等的质量以及操作技术和环境条件等。实践表明,光刻质量对器件性能有很大影响,是生产中影响成品率的关键因素。 (一) 光刻胶:按光化学反应的不同,光刻胶大体可分为正性光刻胶和负性光刻胶两类。1,正性光刻胶: 它的特点是原来的胶膜不能被某些溶剂溶解,当受适当波长光照射后发生光分解反应,切断树脂聚合体主链和从链之间的联系,使其变为可溶性物质。因此当用正胶光刻时,可在基片表面得到与光刻版遮光图案完全相同的光刻胶图形,方向相差180度。正性胶分辨率较高,对一些常用金属表面有较好粘附性;但与负胶相比,其稳定性和抗蚀能力较差。目前常用的正性胶为DQN和PMMA。 1)DQN:DQN是一种近紫外NUV(365、435nm)光刻胶,主要由感光剂DQ、基体 材料N和溶剂组成。通常使用的基体材料是酸催化酚醛树脂,具有良好的成膜性和耐磨性,能溶于碱溶液和许多普通溶剂;感光剂DQ(邻叠氮醌化合物)如同基体材料N在碱溶液中溶解的抑制剂,当在基体N中加入20-50%的DQ,混合物(光刻胶)将变为不可溶;溶剂是用来溶解感光剂和基体材料、同时又易挥发的液体,由于溶剂的用量决定光刻胶的黏度(黏度也与温度有关),从而影响光刻胶的涂敷厚度,而厚度又与光聚合反应所需暴光量有关,与胶膜的分辨率有关,所以对溶剂用量的控制也十分重要。 DQN感光机理是,经近紫外光照射,感光剂发生分解,并重新组合为乙烯酮,乙烯酮和空气中的水气反应,产生酸性基,酸性基可与碱性溶液发生中和反应,使不溶性光刻胶可溶
光刻工艺简要流程介绍
光刻工艺是半导体制造中最为重要的工艺步骤之一。主要作用是将掩膜板上的图形复制到硅片上,为下一步进行刻蚀或者离子注入工序做好准备。光刻的成本约为整个硅片制造工艺的1/3,耗费时间约占整个硅片工艺的40~60%。 光刻机是生产线上最贵的机台,5~15百万美元/台。主要是贵在成像系统(由15~20个直径为200~300mm的透镜组成)和定位系统(定位精度小于10nm)。其折旧速度非常快,大约3~9万人民币/天,所以也称之为印钞机。光刻部分的主要机台包括两部分:轨道机(Tracker),用于涂胶显影;扫描曝光机(Scanning ) 光刻工艺的要求:光刻工具具有高的分辨率;光刻胶具有高的光学敏感性;准确地对准;大尺寸硅片的制造;低的缺陷密度。 光刻工艺过程 一般的光刻工艺要经历硅片表面清洗烘干、涂底、旋涂光刻胶、软烘、对准曝光、后烘、显影、硬烘、刻蚀、检测等工序。 1、硅片清洗烘干(Cleaning and Pre-Baking) 方法:湿法清洗+去离子水冲洗+脱水烘焙(热板150~2500C,1~2分钟,氮 气保护) 目的:a、除去表面的污染物(颗粒、有机物、工艺残余、可动离子);b、除去水蒸气,是基底表面由亲水性变为憎水性,增强表面的黏附性(对光刻胶或者是 HMDS-〉六甲基二硅胺烷)。 2、涂底(Priming) 方法:a、气相成底膜的热板涂底。HMDS蒸汽淀积,200~2500C,30秒钟;优点:涂底均匀、避免颗粒污染; b、旋转涂底。缺点:颗粒污染、涂底不均匀、HMDS 用量大。
目的:使表面具有疏水性,增强基底表面与光刻胶的黏附性。 3、旋转涂胶(Spin-on PR Coating) 方法:a、静态涂胶(Static)。硅片静止时,滴胶、加速旋转、甩胶、挥发溶剂(原光刻胶的溶剂约占65~85%,旋涂后约占10~20%); b、动态(Dynamic)。低速旋转(500rpm_rotation per minute)、滴胶、加速 旋转(3000rpm)、甩胶、挥发溶剂。 决定光刻胶涂胶厚度的关键参数:光刻胶的黏度(Viscosity),黏度越低,光刻胶的厚度越薄;旋转速度,速度越快,厚度越薄; 影响光刻胶厚度均运性的参数:旋转加速度,加速越快越均匀;与旋转加速的时 间点有关。 一般旋涂光刻胶的厚度与曝光的光源波长有关(因为不同级别的曝光波长对应不 同的光刻胶种类和分辨率): I-line最厚,约0.7~3μm;KrF的厚度约0.4~0.9μm;ArF的厚度约0.2~ 0.5μm。 4、软烘(Soft Baking) 方法:真空热板,85~120℃,30~60秒; 目的:除去溶剂(4~7%);增强黏附性;释放光刻胶膜内的应力;防止光刻胶 玷污设备; 边缘光刻胶的去除(EBR,Edge Bead Removal)。光刻胶涂覆后,在硅片边缘的正反两面都会有光刻胶的堆积。边缘的光刻胶一般涂布不均匀,不能得到很好的图形,而且容易发生剥离(Peeling)而影响其它部分的图形。所以需要去除。
混床离子交换器的优点和工作原理
混床离子交换器就是阳、阴两种离子交换树脂,互相充分地混合在一个离子交换器内,同时进行阳、阴离子交换的设备。简称混床。所谓混床,就是把一定比例的阳、阴离子交换树脂混合装填于同一交换装置中,对流体中的离子进行交换、脱除。由于阳树脂的比重比阴树脂大,所以在混床内阴树脂在上阳树脂在下。一般阳、阴树脂装填的比例为1:2,也有装 填比例为1:1.5的,可按不同树脂酌情考虑选择。混床也分为体内同步再生式混床和体外再生式混床。同步再生式混床在运行及整个再生过程均在混床内进行,再生时树脂不移出设备以外,且阳、阴树脂同时再生,因此所需附属设备少,操作简便。 一、混床离子交换器的优点 (1)出水水质优良,出水pH值接近中性。 (2)出水水质稳定,短时间运行条件变化(如进水水质或组分、运行流速等)对混床出水水质影响不大。 (3)间断运行对出水水质的影响小,恢复到停运前水质所需的时间比较短。 混床设备比较好用一点的还是有机玻璃柱的那种,因为分层的时候比较容易看得清楚。 操作起来,再生效果好。以前我用的那种A3钢的,有个视孔,操作起来真的好麻烦,分层都看不到。 二、混床离子交换器的工作原理 混床床离子交换法,就是把阴、阳离子交换树脂放置在同一个交换器中,在运行前将它们均匀混合,所以可看着是由无数阴、阳交换树脂交错排列的多级式复床,水中所含盐类的阴、阳离子通过该项交换器,则被树脂交换,而得到高度纯水。在混合床中,由于阴、阳树脂是相互混匀的,所以其阴、阳离子交换反应几乎同时进行,或者说,水的阳离子交换和阴离子交换是多次交错进行的,经H型交换所产生的H+和经过OH型交换所产生的OH-都不能积累起来,基本上消除反离子的影响,交换进行得比较彻底。由于进入混合床的初级纯水质较好,交换器的负载较轻,树脂的交换能力很长时间才被子耗竭。本混合床采用体内再生法,再生时首先利用两种树脂的比重不同,用反洗使用权阴、阳离子交换树脂完全分离,阳树脂沉积在下,阴树脂浮在上面,然后阳树脂用盐酸(或硫酸)再生,阴树脂用烧碱再生。 三、混床离子交换器的结构 1、再生装置:阴离子交换树脂再生碱液在高于阴离子交换树脂面300毫米处母管进液(Φ400、500、600采用单母管进液,Φ800、2500采用双母管进液),管上小孔布液,管外采用塑料窗纱60目尼龙网布包覆。阳离子交换树脂再生酸性由底部排水装置的多孔板上排水帽进入。 2、中排装置:中排装置设置在阴、阳树脂的分界面上,用于再生排泄酸、碱还原液和冲洗型,型式分为双母管或支母管式,管子小孔外包覆塑料窗纱及60目尼龙网各一层。 3、排水装置:采用多孔板上装设PB2-500型叠片式排水帽,或宝塔式ABS型排水帽,多孔板材质按设备规格不同而异。(Φ400、500、600型采用硬聚氯乙烯多孔,Φ800、2500型采用钢衬胶多孔板)。
声表面波标签工作原理及应用
声表面波标签 1、声表面波射频标签 声表面波是沿物体表面传播的一种弹性波,其声速仅为电磁波速的十万分之一,传播衰耗很小。 2、声表面波射频标签的工作原理 SAW标签采用反射调制方式完成射频标签信息向阅读器的传送,主要由压电基片、叉指换能器、反射栅和天线组成,在压电基片上以平面电极结构制作叉指换能器和反射栅。声表面波标签通过天线接收到高频脉冲信号,该信号传至叉指换能器,由于基片的逆压电效应,换能器激发出同频的SAW,该SAW沿基片表面传播,到达一系列紧密排列编码的反射栅后,部分能量可以反射到叉指换能器,通过基片的压电效应再次转变成电磁波由天线发射回来。如果将反射器组按某种特定的规律设计,使其反射信号表示规定的编码信息,那么阅读器接收到的反射高频电脉冲串就带有该物品的特定编码。通过解调与处理,达到识别标签的目的。 3、声表面波射频标签的应用 在各式各样的电子产品及无线通讯产品中,都会牵涉到信号的接收与发射。为了确保信号的质量,在系统设计时,会使用到数量不一的滤波器。滤波器的种类很多,有陶瓷滤波器、LC滤波器等,各依所对应之频率范围、频率响应特性、价格之不同而在使用上有所分别。SAW滤波器是利用电磁波与声波的特性进行传播的。
表面声波是一种独特的机械波,它沿着晶体表面行进时,在垂直晶体表面的方向,能量会以指数形式衰减(就是说衰减非常非常快),而当其深入超过一个波长深度时,能量密度则降为在表面时的十分之一,因此这种波在晶体表面行进时,最主要的优点就是能量能够集中于表层。这种独特的性质,使得声表面波元件可以很容易地运用其所携带之能量。 早期应用雷达、广播 作为六十年代末期(85后父母一代哦)才发展起来的一门新兴科学技术,声表面波技术是声学和电子学相结合的一门边缘学科。由于声表面波的传播速度是电磁波的十万分之一(最快的飞机1000Km/h,它的1/100000是10m/h,比蜗牛似乎快一点?),在它的传播路径上容易取样和进行处理,因此,用声表面波去模拟电子学的各种功能,能使电子器件实现超小型化和多功能化。同时,由于声表面波器件在甚高频和超高频波段内以十分简单的方式提供了其它方法不易得到 的信号处理功能,因此,声表面波技术在雷达、通信和电子对抗中得到了广泛的应用。声表面波的应用最早是在军用雷达、广播领域作频率稳定的滤波器之用。军方的需求推动了SAW技术的发展。 第一个繁荣期彩电 八十年代后期到本世纪初,彩色电视机对SAW器件的大量需求,引导了声表面波器件的一个繁荣期。回忆一下,最初的彩色电视机价格是不是很贵?为什么呢?因为在当时,一个其中的声表面波器件就
声表面波器件工艺原理-1清洗工艺原理
一,声表器件清洗工艺原理 序: 声表器件制作工艺中的清洗技术及洁净度是影响器件合格率、器件性能和可靠性的重要因素。杂质污染主要来源于晶片加工过程、环境污染、水(包括纯水)污染、试剂污染、工艺气体污染、生产用设备、器皿、工具及易耗品污染、人体污染和工艺过程造成的污染。由于表面污染是通过污染物与表面间的作用力引起(主要是化学力和分子间力),清洗就是为破坏这种作用力,除去由上述污染源所带来的有机物、微粒、金属原子(离子)及微粗糙。(一)对基片表面的清洗: 由于有机物会遮盖部分基片表面,影响对微粒和金属的清洗,所以清洗的一般思路是:先除去表面的有机污染,然后再去除微粒和金属杂质。 1,对有机物的清洗: 基片上的有机污染主要有油膜、残余的蜡膜胶膜、不纯有机溶剂挥发后的残膜,以及微生物的有机残渣、手油等。这些杂质分子与基片表面的接触通常是依靠分子间力维持,多属物理吸附,吸引力较弱,且随分子间距的增加很快削弱,。基片表面上的有机物除影响清洗效果外,工艺上主要影响金属膜的粘附和光刻质量。清洗有机物常用方法主要有: a)擦洗:当基片表面有微粒、有机残渣或残膜时常用擦片办法,它是靠人工(或机械)作用及有机溶剂溶解作用去除表面大块污物,根据有机溶剂结构相似相溶原理,可依次用甲苯、丙酮、无水乙醇棉球在基片表面沿同一方向轻轻擦拭,然后用纯水超声5-10分钟,最后用纯水冲洗、甩干。操作中注意,不可将溶剂顺序颠倒或打乱,擦片要无划伤、不留液渍。 b)等离子体清洗(干法清洗):等离子体是部分电离的气体,由电子、离子、自由基(以氧为例,指游离态氧原子)及其它中性粒子组成,是物质的第四态。等离子体清洗机理主要是依靠等离子体中的活性粒子(电子、离子和自由基)的活化作用达到去除表面污渍的目的。其反应过程包括:无机气体被激发为等离子态;气相物质被吸附在固体表面;被吸附基团与固体表面分子反应生成产物分子;产物分子解析形成气相;反应残余物脱离表面。 按反应类型分类:等离子体与固体表面反应可以分为物理反应(离子轰击)化学反应及物理化学反应。物理反应机制是,活性离子轰击待清洗表面,使污染物脱离表面并最终被真空泵抽走;其优点是,自身无化学反应,表面不留氧化物,腐蚀作用各向异性;缺点是,使表面在分子级范围内变的粗糙,对被清洗表面的各种不同物质选择性差,热效应大,腐蚀速度低。化学反应机制是,各种活性的粒子和污染物反应生成易挥发性物质,然后由真空泵吸走;其优点是,清洗速度高,选择性好,对清除有机污染比较有效,缺点是会在表面产生氧化物。物理化学反应机制是,两种反应都起重要作用,并互相促进;离子轰击使被清洗表面产生损伤,削弱其化学键或者形成原子态,使其容易吸收反应剂,离子碰撞使被清洗物加热,使之更容易发生反应,其效果是既有好的选择性、清洗效率、均匀性,又有好的方向性。 按激发频率分类:等离子态密度n(cm-3)和激发频率v(Hz)有如下关系: n =1.2425×108v2 ,由上式见,频率越高,等离子态密度越大,列表说明其分类: 频率 等离子体类型 自偏压 反应类型 应用 40KHz 超声等离子体 1000V 物理反应 对表面影响大,易造成二次污染 13.56MHz 射频等离子体 250V 物理化学反应 去除表面污染物、有机物、氧化物(氢)等 2.45GHz 微波等离子体 几十伏 化学反应 去除表面污染物、有机物、氧化物(氢)等 典型的等离子体化学清洗工艺是氧等离子体清洗。在低压系统中通入少量氧,受高频电场作用,氧被激励成游离态氧原子,使有机物氧化成挥发性物质CO2 和H2O,达到清除目的(但不能去掉碳和其它非挥发性金属或金属氧化物)。工艺要求的真空度、高频频率、通氧量、功率、时间可参照设备说明或由实验确定。具体反应如下: O2—→O* + O* C x H y + O*—→C O2↑+ H2 O↑ 典型的等离子体物理清洗工艺是氩等离子体清洗。在镀膜前,抽高真空到5×10-3Pa,充
混床用户使用手册
一、关键词 1、混床:在同一个交换器内,将阴、阳离子交换树脂按照一定的体积比例进行填装,在均匀混合状态下,进行阴、阳离子交换,从而除去水中的盐分,称为混合床除盐处理。 2、脱碳器:装有填料、通过鼓风机送风去除水中的CO2(即去除HCO3-)的设备 3、再生:树脂经过一段运行后,失去了其交换离子的能力,此时需不同的树脂通过不同的盐液、碱液、酸液等再生液进行浸泡,脱除树脂所吸附的离子,让树脂重新恢复其交换能力的过程叫再生。再生过程包括反洗、进再生液、置换、正洗等步骤。 4、置换:树脂被再生液浸泡,盐液中的Na+、碱液中的OH-、酸液中的H+分别与不同树脂所吸附的离子进行交换,此过程叫置换。 5、两步法再生:分别进酸、碱,依次对阴、阳树脂进行再生。 6、同步法再生:分别同时进酸、碱通过阴、阳树脂,从中间排管排出混合再生废液,然后,分别同时进水对阴、阳树脂进行置换与清洗。 7、反洗:与运行时,水通过的方向相反。 8、正洗:与运行时,水通过的方向一致。 9、工作压力:进入系统各设备前的压力。 10、压差:系统各设备进、出口之间的压力差值。 11、工作温度:树脂进行交换可承受的温度。
二、工作原理 1、混床脱盐: 在同一个交换器内,将阴、阳离子交换树脂按照一定的体积比例进行填装,在均匀混合状态下,进行阴、阳离子交换,从而除去水中的盐分,称为混合床除盐处理。 1.1工作过程: 其工作原理可用下列反应式表示: ++= R +H 2O 1.2再生过程: 混床经过一定的周期制水后,阴、阳树脂就会失去交换作用。当混床工作至电导率增加到一定界限或二氧化硅超标时,就得对阴、阳树脂进行交换再生,重新恢复阴、阳树脂的工作交换能力。 阳树脂再生交换反应式为: R = RH + OH R /-????????????????????- ---+ + ++HSiO HCO CL SO K Na Mg Ca 3 3242221 212 1? ?? ??? ?? ?+???????? ???- - - -++++HSiO HCO CL SO K Na Mg Ca R 3 3 24/2221 2 121 -++???????????++ ++CL H K Na Mg Ca 222 121 -++++ +???????+CL K Na Mg Ca RH 221 22 1
混床
混床 一、基本介绍 混床是混合离子交换柱的简称,是针对离子交换技术所设计的设备。所谓混床,就是把一定比例的阳、阴离子交换树脂混合装填于同一交换装置中,对流体中的离子进行交换、脱除。由于阳树脂的比重比阴树脂大,所以在混床内阴树脂在上阳树脂在下。一般阳、阴树脂装填的比例为1:2,也有装填比例为1:1.5的,可按不同树脂酌情考虑选择。混床也分为体内同步再生式混床和体外再生式混床。同步再生式混床在运行及整个再生过程均在混床内进行,再生时树脂不移出设备以外,且阳、阴树脂同时再生,因此所需附属设备少,操作简便。 混床处理工艺的设备包括混合离子交换器和体外再生设备。其中体外再生设备主要包括树脂分离器、阴(阳)树脂再生器、树脂贮存塔、混杂树脂塔和酸碱再生设备。国内混床处理工艺主要特点体现在树脂分离再生工艺上。树脂的分离再生工艺有三种。 二、设备优点 1、出水水质优良,出水pH值接近中性。 2、出水水质稳定,短时间运行条件变化(如进水水质或组分、运行流速等)对混床出水水质影响不大。 3、间断运行对出水水质的影响小,恢复到停运前水质所需的时间比较短。 4、回收率达到100% 三、结构性能 混床外壳制作材质有玻璃钢、有机玻璃、不锈钢、碳钢、防腐等,外型为圆柱型,直径Φ200—2500mm,产水量从0.5t/h—98t/h。阳床装载强酸阳离子交换树脂,阴床装载强碱阴离子交换树脂,装载高度一向在1000—2400 mm,小型滤帽式设备底部没有承托层,中大型设备底部有粒度不同多级别石英砂承托层(现不建议这样做,因为酸洗的时候石英砂和
酸会产生化学反应,对水质造成影响),逆流再生固定床树脂顶层有200 mm厚压脂层树脂(特殊的树脂用来覆盖下面的树脂)。有机玻璃柱运行压力≤0.15MPa,其他材质的设备运行压力≤0.6MPa。阳床配备有酸箱、酸泵再生系统,阴床配备有碱箱、碱泵再生系统。 四、再生步骤 反洗 关闭进水阀、产水阀;打开反洗进水阀、反洗排放阀,以10m/h反洗15min。然后,关闭反洗进水阀、反洗排放阀。静置,沉降5~10min。开排气阀、中排阀,部分排水至树脂层表面上10cm左右,关闭排气阀、中排阀。 再生 开进水阀、加酸泵、进酸阀、中排阀,以5m/s、200L/h对阳树脂进行再生,用反渗透产水对阴树脂进行清洗,维持柱内液面在树脂层表面上10cm。对阳树脂再生30min后,关进水阀、加酸泵、进酸阀,开反洗进水阀、加碱泵、进碱阀,以5m/s、200L/h对阴树脂进行再生,用反渗透产水对阳树脂进行清洗,维持柱内液面在树脂层表面上10cm,再生30min。 置换、混脂、冲洗 关加碱泵、进碱阀,开进水阀,上下同时进水对树脂进行置换、清洗。30min后,关进水阀、反洗进水阀、中排阀,开反洗排放阀、进气阀、排气阀,以压力0.1~0.15MPa,气量2~3m3/(m2·min),混合树脂0.5~5min。关反洗排放阀、进气阀,沉降1~2min。开进水阀、正洗排放阀,调节排气阀,灌水至柱内无空气后,关排气阀,对树脂冲洗。当电导率达到要求时,开产水阀,关正洗排放阀,开始制水。 五、应用范围 混床一般放置在电渗析器或反渗透装置之后(或直接应用于含盐量较低的水),对水进一步脱盐可制取较高纯水,广泛使用在电子、化工、医药、原子能、电力等行业。 六、EDI模块 1、概述 EDI(Elcctrodeionization)是一种将离子交换技术、离子交换膜技术和离子电迁移技术相结合的纯水制造技术。它巧妙的将电渗析和离子交换技术相结合,利用两端电极高压使水中带电离子移动,并配合离子交换树脂及选择性树脂膜以加速离子移动去除,从而达到水纯化的目的。在EDI除盐过程中,离子在电场作用下通过离子交换膜被清除。同时,水分子在电场作用下产生氢离子和氢氧根离子,这些离子对离子交换树脂进行连续再生,以使离子交换树脂保持最佳状态。
简述去离子水设备原理及工艺描述
简述去离子水设备原理及工艺描述去离子水设备是水处理设备的一种,通过阴、阳离子交换树 脂对水中的各种阴、阳离子进行置换的一种传统水处理工艺,阴、阳离子交换树脂按不同比例进行搭配可组成离子交换阳床系统,离子交换阴床系统及离子交换混床系统,而混床系统又通常是用在反渗透等水处理工艺之后用来制取超纯水,高纯水的终端工艺,它是目前用来制备超纯水、高纯水不可替代的手段之一。其出水电导率可低于1uS/cm以下,出水电阻率达到1MΩ.cm以上,根 据不同的水质及使用要求,出水电阻率可控制在1~18MΩ.cm之间。被广泛应用在电子、电力超纯水,化工,电镀超纯水,锅炉补给水及医药用超纯水等工业超纯水,高纯水的制备上。 离子交换树脂系统工作原理 采用离子交换方法,可以把水中呈离子态的阳、阴离子去除,以氯化钠(NaCl)代表水中无机盐类,水质除盐的基本反应可以用下列方程式表达:去离子水设备 1、阳离子交换树脂:R—H+Na+ R—Na+H+ 2、阴离子交换树脂:R—OH+Cl- R—Cl+OH-
阳、阴离子交换树脂总的反应式即可写成: RH+ROH+NaCl——RNa+RCL+H2O 由此可看出,水中的NaCl已分别被树脂上的H+和OH-所取代,而反应生成物只有H2O,故达到了去除水中盐的作用去离子水设备主要工艺 去离子水的工艺大致可分为四种: 第一种:采用阳阴离子交换树脂取得的去离子水,一般通过之后,出水电导率可降到10us/cm以下,再经过混床就可以达到 1us/cm以下了。但是这种方法做出来的水成本极高,而且颗粒 杂质太多,达不到理想的要求。目前已较少采用了。 第二种:预处理(即砂碳过滤器+精密过滤器)+反渗透+混床 工艺 这种方法是目前采用最多的,因为反渗透投资成本也不算高,可以去除90%以上的水中离子,剩下的离子再通过混床交换除去,这样可使出水电导率:0.06左右。这样是目前最流行的方法。 第三种:采用两级反渗透方式其流程如下: 自来水→多介质过滤器→活性炭过滤器→软化水器→中间 水箱→低压泵→精密过滤器→一级反渗透→PH调节→混合器→
光刻工艺流程及未来发展方向
集成电路制造工艺 光刻工艺流程 作者:张少军 陕西国防工业职业技术学院电子信息学院电子****班 24 号 710300 摘要:摘要:光刻(photoetching)是通过一系列生产步骤将晶圆表面薄膜的特定部分除去 的工艺,在此之后,晶圆表面会留下带有微图形结构的薄膜。被除去的部分可能形状是薄膜内的孔或是残留的岛状部分。 关键词:光刻胶;曝光;烘焙;显影;前景 Abstract: photoetching lithography (is) through a series of steps will produce wafer surface film of certain parts of the process, remove after this, wafer surface will stay with the film structure. The part can be eliminated within the aperture shape is thin film or residual island. Keywords: the photoresist, Exposure; Bake; Enhancement; prospects 基本光刻工艺流程— 1 基本光刻工艺流程—从表面准备到曝光 1.1 光刻十步法 表面准备—涂光刻胶—软烘焙—对准和曝光—显影—硬烘焙—显影目测—刻蚀—光刻胶去除—最终目检。 1.2 基本的光刻胶化学物理属性 1.2.1 组成聚合物+溶剂+感光剂+添加剂,普通应用的光刻胶被设计成与紫外线和激光反应,它们称为光学光刻胶(optical resist),还