贴片机抛料的详细介绍

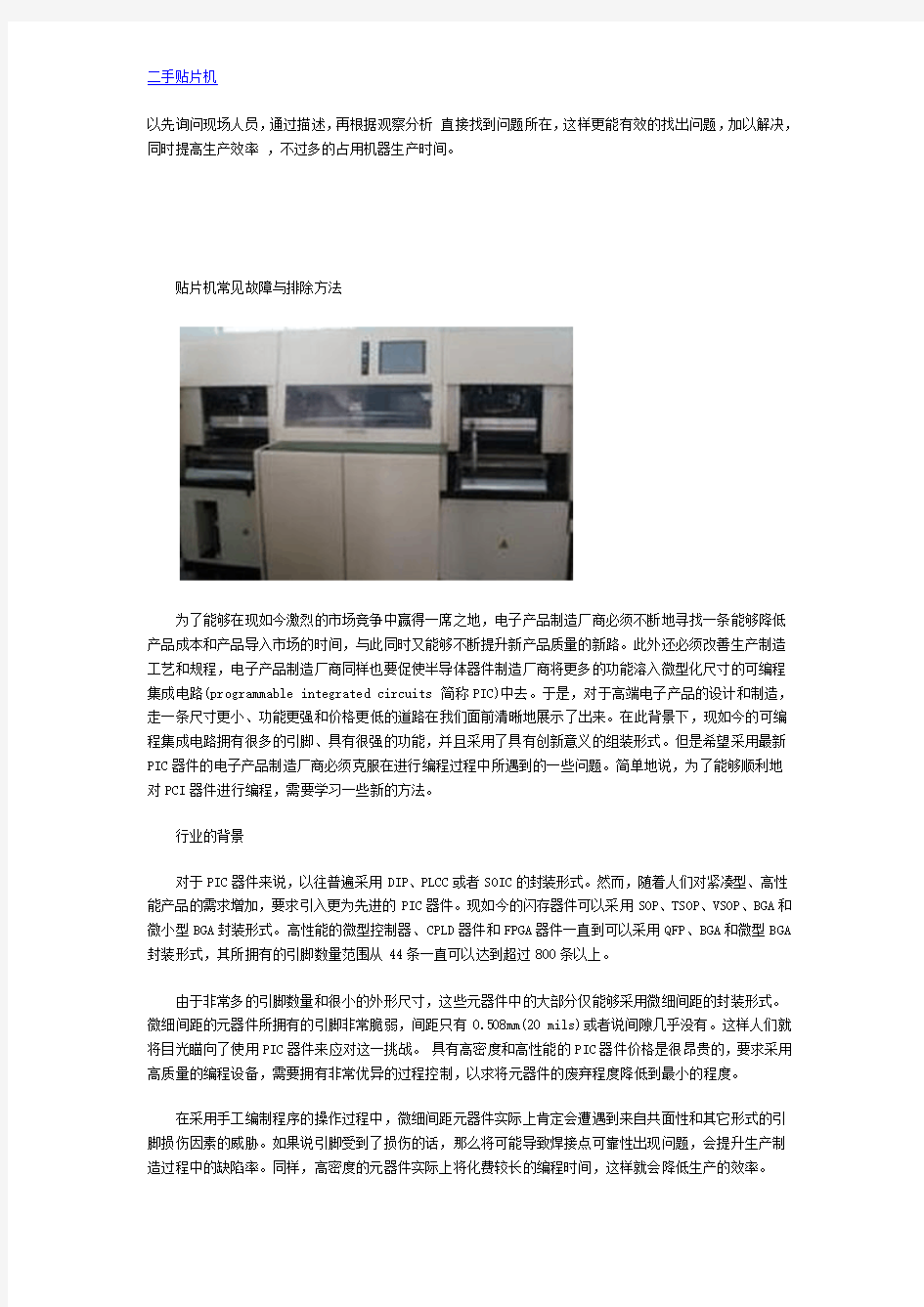
贴片机抛料的详细介绍
贴片机抛料的主要原因分析及解决,效率的提高贴片机抛料的主要原因分析
在SMT生产过程中,怎么控制生产成本,提高生产效率,是企业老板及工程师们很关心的事情,而这些跟贴片机的抛料率有很大的联系,以下就谈谈贴片机的抛料问题。所谓抛料就是指贴片机在生产过种中,吸到料之后不贴,而是将料抛到抛料盒里或其他地方,或者是没有吸到料而执行以上的一个抛料动作。抛料造成材料的损耗,延长了生产时间,降抵了生产效率,抬高了生产成本,为了优化生产效率,降低成本,必须解决抛料率高的问题。
抛料的主要原因及对策:
原因1:吸嘴问题,吸嘴变形,堵塞,破损造成气压不足,漏气,造成吸料不起,取料不正,识别通不过而抛料。对策:清洁更换吸嘴;
原因2:识别系统问题,视觉不良,视觉或雷射镜头不清洁,有杂物干扰识别,识别光源选择不当和强度、灰度不够,还有可能识别系统已坏。对策:清洁擦拭识别系统表面,保持干净无杂物沾污等,调整光源强度、灰度,更换识别系统部件;
原因3:位置问题,取料不在料的中心位置,取料高度不正确(一般以碰到零件后下压0.05MM为准)而造成偏位,取料不正,有偏移,识别时跟对应的数据参数不符而被识别系统当做无效料抛弃。对策:调整取料位置;
原因4:真空问题,气压不足,真空气管通道不顺畅,有导物堵塞真空通道,或是真空有泄漏造成气压不足而取料不起或取起之后在去贴的途中掉落。对策:调气压陡坡到设备要求气压值(比如
0.5~~0.6Mpa--YAMAHA贴片机),清洁气压管道,修复泄漏气路;
原因5:程序问题,所编辑的程序中元件参数设置不对,跟来料实物尺寸,亮度等参数不符造成识别通不过而被丢弃。对策:修改元件参数,搜寻元件最佳参数设定;
原因6:来料的问题,来料不规则,为引脚氧化等不合格产品。对策:IQC做好来料检测,跟元件供应商联系;
原因7:供料器问题,供料器位置变形,供料器进料不良(供料器棘齿轮损坏,料带孔没有卡在供料器的棘齿轮上,供料器下方有异物,弹簧老化,或电气不良),造成取料不到或取料不良而抛料,还有供料器损坏。对策:供料器调整,清扫供料器平台,更换已坏部件或供料器; 有抛料现象出现要解决时,可
以先询问现场人员,通过描述,再根据观察分析直接找到问题所在,这样更能有效的找出问题,加以解决,同时提高生产效率,不过多的占用机器生产时间。
贴片机常见故障与排除方法
为了能够在现如今激烈的市场竞争中赢得一席之地,电子产品制造厂商必须不断地寻找一条能够降低产品成本和产品导入市场的时间,与此同时又能够不断提升新产品质量的新路。此外还必须改善生产制造工艺和规程,电子产品制造厂商同样也要促使半导体器件制造厂商将更多的功能溶入微型化尺寸的可编程集成电路(programmable integrated circuits 简称PIC)中去。于是,对于高端电子产品的设计和制造,走一条尺寸更小、功能更强和价格更低的道路在我们面前清晰地展示了出来。在此背景下,现如今的可编程集成电路拥有很多的引脚、具有很强的功能,并且采用了具有创新意义的组装形式。但是希望采用最新PIC器件的电子产品制造厂商必须克服在进行编程过程中所遇到的一些问题。简单地说,为了能够顺利地对PCI器件进行编程,需要学习一些新的方法。
行业的背景
对于PIC器件来说,以往普遍采用DIP、PLCC或者SOIC的封装形式。然而,随着人们对紧凑型、高性能产品的需求增加,要求引入更为先进的PIC器件。现如今的闪存器件可以采用SOP、TSOP、VSOP、BGA和微小型BGA封装形式。高性能的微型控制器、CPLD器件和FPGA器件一直到可以采用QFP、BGA和微型BGA 封装形式,其所拥有的引脚数量范围从44条一直可以达到超过800条以上。
由于非常多的引脚数量和很小的外形尺寸,这些元器件中的大部分仅能够采用微细间距的封装形式。微细间距的元器件所拥有的引脚非常脆弱,间距只有0.508mm(20 mils)或者说间隙几乎没有。这样人们就将目光瞄向了使用PIC器件来应对这一挑战。具有高密度和高性能的PIC器件价格是很昂贵的,要求采用高质量的编程设备,需要拥有非常优异的过程控制,以求将元器件的废弃程度降低到最小的程度。
在采用手工编制程序的操作过程中,微细间距元器件实际上肯定会遭遇到来自共面性和其它形式的引脚损伤因素的威胁。如果说引脚受到了损伤的话,那么将可能导致焊接点可靠性出现问题,会提升生产制造过程中的缺陷率。同样,高密度的元器件实际上将化费较长的编程时间,这样就会降低生产的效率。
在电路板上的编程
先进的PIC器件的使用者会面临一项困难的选择:是冒遭受质量问题的风险,采用手工编制程序呢?还是另外寻找一种可以替代的编程方法,从而消除掉手工触摸的方法呢?
为了能够实现后者,制造厂商们最初开始采用板上编程(on-board programming 简称OBP)的方式。OBP 是一种简单的方法,它是将PIC贴装到印刷电路板(printed circuit board 简称PCB)上以后再进行编程的。一般情况下在电路板上进行测试或者说进行功能测试。闪存、电子式可清除程序化唯读内存(Electrically Erasable Programmable Read-Only Memory简称EEprom)、基于EEprom的CPLD器件、基于EEprom的FPGA器件,以及内置闪存或者EEprom的微型控制器,所有这些元器件均采用OBP形式进行编程。
为了能够满足闪存和微型控制器的使用要求,在实施OBP的时候最常用的方法就是借助于针盘式夹具(bed-of-nails fixture),使用自动测试设备(automatic test equipment 简称ATE)编程。对于逻辑器件来说进行编程颇为复杂,不太适合利用ATE针盘式夹具来进行编程。
一项基于IEEE规范原创开发的新型OBP技术可以支持测试,展现出充满希望的前程。这项规范称为IEEE 1149.1,它详细规定了边界扫描的一系列协议,目前用于许多PIC编程方法中。
如果电子产品制造商要使用IEEE 1149.1的编程方法时,他们所依赖的具有知识产权保护的工具主要是由各种各样的半导体制造厂商所提供。但是使用他们的工具进行编程非常慢。同样,因为他们出于保护知识产权的本能,每个工具仅限于单个用户所使用的器件。如果说在一块电路板上的PIC器件是由多个用户所使用的话,这将是一个很大的缺陷。
总而言之,使用OBP方法可以消除掉手工操作器件和将编程溶入测试中去,以及制造生产缓慢的现象。然而,编程所需的时间可能也是缓慢的。
ATE针盘式编程
ATE设备最初的使用是用于对PCB组件进行在线测试,以求发现诸如走线开路、短路,元器件缺失和元器件排列不准等制造过程中所产生的缺陷。针盘式夹具是一种阵列配置,具有弹性荷载的测试端点,它可以在PCB和ATE测试设备的信号策动电路之间形成一种机械和电气的连接界面。
一旦PCB可靠地与针盘式夹具连接好了以后,ATE测试设备的信号策动电路将会通过针盘式夹具和PCB,发送编程信号到目标器件PIC上面。除了对机械缺陷进行测试以外,ATE设备也能够用于对PIC器件的编程操作。对元器件的编程和消除程序被嵌入到电路板测试程序中去,从而用来对目标器件进行编程。
IEEE 1149.1边界扫描编程
为了提升PCB组件的密度和复杂性,使电路板和元器件的测试工作面临着非常大的困难,尤其是对付空间受到限制的PCB组件。为了能够有效的解决这一问题,一种边界扫描测试协议(IEEE 1149.1)应运而生。
IEEE 1149.1测试标准能够通过一台智能化外部设备,对在组装的电路板上的逻辑器件或者闪存器件进行编程。这种编程设备通过标准的测试访问口(Test Access Port 简称TAP)与电路板形成连接界面。所有这些需要采用JTAG硬件控制装置、JTAG软件系统、与JTAG兼容的PCB电路板,和一个四线测试访问口。
实现边界扫描工作可以采用一种专业化的专用电路板上编程设备,或者采用另外一种选择方案,利用由美国GenRad、Hewlett-Packard和Teradyne ATE testers等公司提供的一些工具,于是可以在ATE测试设备上实现IEEE 1149.1边界扫描编程工作。
采用IEEE标准的最大优点之一就在于,它可以对在同一块PCB上由不同供应商提供的各种各样的元器件进行编程。这样就可以降低整个编程时间,简化生产制造流程。
自动化编程(AP)设备
PIC技术不断地向前发展,所以新的自动化编程设备和技术也保持着相同的发展步伐。举例来说,Data I/O''s ProMaster 970自动化微细间距编程设备能够对采用先进封装形式的PIC器件进行编程,其中包括BGA、微型BGA、SOP、VSOP、TSOP、PLCC、SON和CSP。双重贴装(Dual pick-and-place简称PNP) 端头和可供选择的可插8、10或者12的插座可以最大程度的提高设备的工作效率。该编程设备也可以进一步涉及有关器件的质量控制。举例来说,共平面性问题和引脚的损伤实际上是不会存在的,因为集成了激光视觉系统,所以能够确保非常精确的器件贴装。
因为有着多种编程接口和PNP器件的配置,自动集群编程一般可以做到比ATE编程的速度快上5倍到10倍。同样,这些编程工具是专门为了编程而设计的,不是为了对电路板或者说功能进行测试的,所以它们可以提供非常好的编程质量。
微细间距的PIC器件可能是非常贵的,所以如果能降低其在生产制造过程中的损伤率,将极大的提升制造商的盈亏平衡点。能够适用于大多数元器的自动编程系统也是非常灵活的,可以适应于先进封装器件形式。由于能够将高生产率、高质量和灵活性综合在一起,导致了每个器件最低可得到的编程价格常常低于ATE编程价格的20%。
回流焊
回流焊技术在电子制造领域并不陌生,我们电脑内使用的各种板卡上的元件都是通过这种工艺焊接到线路板上的,这种设备的内部有一个加热电路,将空气或氮气加热到足够高的温度后吹向已经贴好元件的线路板,让元件两侧的焊料融化后与主板粘结。这种工艺的优势是温度易于控制,焊接过程中还能避免氧化,制造成本也更容易控制。
由于电子产品PCB板不断小型化的需要,出现了片状元件,传统的焊接方法已不能适应需要。首先在混合集成电路板组装中采用了回流焊工艺,组装焊接的元件多数为片状电容、片状电感,贴装型晶体管及二极管等。随着SMT整个技术发展日趋完善,多种贴片元件(SMC)和贴装器件(SMD)的出现,作为贴装技术一部分的回流焊工艺技术及设备也得到相应的发展,其应用日趋广泛,几乎在所有电子产品领域都已得到应用,而回流焊技术,围绕着设备的改进也经历以下发展阶段。
回流焊接设备进化的原因: 热传递效率和焊接的可靠性的不断提升!
第一代回流焊:热板传导回流焊设备
深力拓科技HN-835回流焊
(热传递效率最慢:5-30 W/m2K(不同材质的加热效率不一样),有阴影效应,.)
第二代回流焊:红外热辐射回流焊设备
(热传递效率慢:5-30W/m2K(不同材质的红外辐射效率不一样),有阴影效应,元器件的颜色对吸热量有大的影响.)
第三代回流焊:热风回流焊设备
(热传递效率比较高:10-50 W/m2K,无阴影效应,颜色对吸热量没有影响.)
第四代回流焊:(气相回流焊接)系统
(热传递效率高:200-300 W/m2K,无阴影效应,焊接过程需要上下运动.冷却效果差.)
第五代回流焊:真空蒸汽冷凝焊接(真空汽相焊)系统
(密闭空间的无空洞焊接,热传递效率最高:300 W-500W/m2K,焊接过程保持静止无震动.冷却效果优秀.颜色对吸热量没有影响.) 目前最完美的焊接系统!
热板传导回流焊
这类回流焊炉依靠传送带或推板下的热源加热,通过热传导的方式加热基板上的元件,用于采用陶瓷(Al2O3)基板厚膜电路的单面组装,陶瓷基板上只有贴放在传送带上才能得到足够的热量,其结构简单,价格便宜。我国的一些厚膜电路厂在80年代初曾引进过此类设备。
红外线辐射回流焊
此类回流焊炉也多为传送带式,但传送带仅起支托、传送基板的作用,其加热方式主要依红外线热源以辐射方式加热,炉膛内的温度比前一种方式均匀,网孔较大,适于对双面组装的基板进行回流焊接加热。这类回流焊炉可以说是回流焊炉的基本型。在我国使用的很多,价格也比较便宜。
红外加热风(Hot air)回流焊
类回流焊炉是在IR炉的基础上加上热风使炉内温度更均匀,单纯使用红外辐射加热时,人们发现在同样的加热环境内,不同材料及颜色吸收热量是不同的,即(1)式中Q值是不同的,因而引起的温升ΔT也不同,例如IC等SMD的封装是黑色的酚醛或环氧,而引线是白色的金属,单纯加热时,引线的温度低于其黑色的SMD本体。加上热风后可使温度更均匀,而克服吸热差异及阴影不良情况,IR + Hot air的回流焊炉在国际上曾使用得很普遍。
充氮(N2)回流焊:
随着组装密度的提高,精细间距(Fine pitch)组装技术的出现,产生了充氮回流焊工艺和设备,改善了回流焊的质量和成品率,已成为回流焊的发展方向。氮气回流焊有以下优点:
(1) 防止减少氧化
(2) 提高焊接润湿力,加快润湿速度
(3) 减少锡球的产生,避免桥接,得到较好的焊接质量
得到更好的焊接质量特别重要的是,可以使用更低活性助焊剂的锡膏,同时也能提高焊点的性能,减少基材的变色,但是它的缺点是成本明显的增加,这个增加的成本随氮气的用量而增加,当你需要炉内达到1000ppm含氧量与50ppm含氧量,对氮气的需求是有天壤之别的。现在的锡膏制造厂商都在致力于开发在较高含氧量的气氛中就能进行良好的焊接的免洗焊膏,这样就可以减少氮气的消耗。
对于回流焊中引入氮气,必须进行成本收益分析,它的收益包括产品的良率,品质的改善,返工或维修费的降低等等,完整无误的分析往往会揭示氮气引入并没有增加最终成本,相反,我们却能从中收益。
在目前所使用的大多数炉子都是强制热风循环型的,在这种炉子中控制氮气的消耗不是容易的事。有几种方法来减少氮气的消耗量,减少炉子进出口的开口面积,很重要的一点就是要用隔板,卷帘或类似的装置来阻挡没有用到的那部分进出口的空间,另外一种方式是利用热的氮气层比空气轻且不易混合的原理,在设计炉的时候就使得加热腔比进出口都高,这样加热腔内形成自然氮气层,减少了氮气的补偿量并维护在要求的纯度上。
内容来源:https://www.360docs.net/doc/6f4733180.html, 欢迎多多交流!!!
JUKI贴片机的使用教程
贴片机的介绍与使用 目录 一:贴片技术与贴片机关系讲解 二:贴片机的编程循序 三:贴片机的保养目的 贴片技术与贴片机关系讲解 (一)X-Y 与Z轴 X-Y 定位系统是评价贴片机精度的主要指标,它包括传动机构和伺服系统;贴片速度的提高意味着X-Y 传动机构运行速度的提高而发热,而滚珠丝杆是主要的热源,其热量的变化会影响贴装精度,最新研制的X-Y 传动系统在导轨内设有冷却系统;在高速机中采用无磨擦线性马达和空气轴承导轨传动,运行速度做得更快。 西门子贴片机是采用同步带-直线轴承驱动,该系统运行噪声低,工作环境好。 X-Y 伺服系统(定位控制系统) 由交流伺服电机驱动,并在传感器及控制系统指挥下实现精确定位,因此传感器的精度起关键作用。位移传感器有园光栅编码器、磁栅尺和光栅尺。 1.园光栅编码器园光栅编码器的转动部位上装有两片园光栅,园光栅由玻璃片或透明塑料制成,并在片上镀有明暗相间的放射状铬线,相邻的明暗间距称为一个栅节,整个园周总栅节数为编码器的线脉冲数。铬线的多少也表示精度的高低。其中一片光栅固定在转动部位作指标光栅,另一片则随转动轴同眇运动并用来计数,因此指标光栅与转动光栅组成一对扫描系统,相当于计数传感器。园光栅编码器装在伺服电机中,它可测出转动件的位置、角度及角加速度,它可以将这些物理量转换为电信号舆给控制系统。编码器能记录丝杆的放置数并将信息反馈给比较器,直至符合被线性量。该系统抗干扰性强,测量精度取决于编码器中光栅盘上的光栅数及溢珠丝杆导轨的精度。 2.磁栅尺 由磁栅尺和磁头检测电路组成,利用电磁特性和录磁原理对位移进行测量。磁栅尺是在非导磁性标尺基础上采用化学涂覆或电镀工艺在非磁性标尺上沉积一层磁性膜(一般10~20um)在磁性膜上录制代 表一定年度具有一定波长的方波或正弦波磁轨迹信号。磁头在磁栅尺上移动和读取磁恪,并转变成电信号输入到控制电路,最终控制AC伺服电机的运行。磁栅尺的优点是制造简单、安装方便、稳定性高、量程范围大,测量精度高达1~5um,贴片精度一般在0.02mm。 深圳金狮王科技长期有JUKI:750、760、2010、2020、2030、2050、2060、2070、2080、JX-100LED、JX-200LED、JX-300LED等机器。 金狮王:1、3、5、7、0、8、6、9、7、1、5李工 3.光栅尺 由光栅尺、光栅读数头与检测电路组成。光栅尺是在透明下班或金属镜面上真空沉积镀膜,利用光刻技术制作均匀密集条纹(每毫米100~300 条),条纹距离相等且平等。光栅读数头由指示光栅、光源、透镜及光敏器件组成,光栅尺有相同的条纹,光栅尺是根据根据物理
基于DSP的SMT贴片机运动控制卡设计
基于DSP的SMT贴片机运动控制卡设计 易思伟 胡勇 宋张 龙绪明 易思伟先生,西南交通大学硕士研究生; 胡勇先生,硕士研究生; 宋张先生,硕士研究生; 龙绪明先生,硕士研究生。 关键词:DSP控制 PID前馈 PCI总线 伺服系统 一序言 SMT贴片机是一个视觉机器人系统,由X-Y-Z-q 4个自由度机械手,PCB板传输定位系统,元器件上料系统和视觉系统构成。决定贴片速度和精度是机械手的运动控制。开放式的运动控制技术利用了近年来电子、网络通信、计算机和控制理论等领域的新成果,通过对以电机驱动的执行机构等设备进行运动控制,以实现预定运动轨迹目标的装置,用于完成多个运动轴(2~32轴)位置、速度和同步的控制。本运动控制系统的任务是研制高速高精度视觉贴片机DSP多轴运动控制卡,同时实现4个轴(如图1)的位置控制,研究高速度、高加速度运动与贴片精度的难题。 二系统设计 贴片机主要包括两个传送机构。一个是X-Y传送机构(X-Y平台);另一个是Z与q传送机构。贴
片机的精度和进度主要是由X轴和Y轴运动传动机构决定的。高精度的闭环位置控制系统一般采用滚珠丝杆传送机构。电子尺线性编码器将贴片机的实际位置直接反馈,比旋转轴编码器更精确,可靠性高,不受机械磨损的影响。Z轴运动主要是适应不同PCB板厚和不同元器件的高低,Z轴由气动驱动,步进电机/伺服电机驱动丝杆3种,有些贴片机还采用球形花键克服丝杆转动时径向的抖动,对于贴细间距器件用途很大。q运动精度对贴片精度影响很大,分辨率要高。 贴片机运动控制卡系统与贴片机控制系统总体框架如图2所示。 运动控制卡以美国TI公司的16位定点DSP TMS320LF2407A为核心微处理器,它集成了编码器信号采集和处理电路,D/A输出电路,扩展存储器电路和DSP—PC机通信电路。PC机把粗插补的数据通过PCI总线传递给轴控制卡系统,DSP通过对光电编码器反馈信号处理电路的结果分析,计算出与给定位置的误差值,再通过软件PID+前馈算法调节器获得位置控制量,计算出速度控制量,产生的输出信号经D/A转换将模拟电压量送伺服放大器,通过对伺服电机的控制实现对位置的闭环控制。 1. DSP部分 我们选用TI公司的TMS320LF2407A型DSP。这主要是由于其具有以下一些特点: (1)采用高性能静态CMOS技术,使得供电电压降为3.3V,减小了控制器的功耗;30MIPS的执行速度使得指令周期缩短到33ns(30MHz),从而提高了控制器的实时控制能力; (2)片内有高达32k字节×16位的FLASH程序存储器;高达2.5k字×16位的数据/程序RAM;544字双端口RAM;2k字的单口RAM; (3)两个事件管理器模块EV A和EVB,每个均包括如下资源:两个16位通用定时器;8个16位的脉宽调制(PWM)通道,可以实现三相反相器控制、PWM的中心或边缘校正、当外部引脚PDPINTX/出现低电平时快速关闭PWM通道;防止击穿故障的可编程的PWM死区控制;对外部事件进行定时捕获的3个捕获单元;片内光电编码器接口电路;16通道的同步A/D转换器。事件管理器模块适用于控制
国产高端贴片机软件系统开发-龙绪明
Welcome: xmlong@https://www.360docs.net/doc/6f4733180.html, Welcome: xmlong@https://www.360docs.net/doc/6f4733180.html, https://www.360docs.net/doc/6f4733180.html, 西南交通大学 常州奥施特信息科技有限公司 国产高端贴片机软件系统开发 龙绪明
Welcome: xmlong@https://www.360docs.net/doc/6f4733180.html, Welcome: xmlong@https://www.360docs.net/doc/6f4733180.html, 1.SMT制造技术的发展 全球68%电子制造产业在中国,中国电子制造产业50%在珠三角, 30%在长三角。 国产SMT 设备品牌 1% 腾世泰姆瑞汉诚通翌贝拓贴片机30% 复蝶思泰克SPI 70% 50% 30% 40%80% 50% 70% 市场占有率卓茂福斯托新泽谷 安达腾盛日联神州振华兴凯格德森、日东日东、劲拓科隆威、安达、和西 国产品牌 返修站 挿件机 点胶涂覆AXI AOI 印刷机 波峰焊再流焊设备名称 SMT 电子组装技术向着敏捷、柔性、集成、智能、环保的方向发展
2.贴片机的关键技术 1.高速度高精度运动控制技术 2.视觉技术 3.软件技术 4.精密机械Welcome: xmlong@https://www.360docs.net/doc/6f4733180.html, Welcome: xmlong@https://www.360docs.net/doc/6f4733180.html,
Welcome: xmlong@https://www.360docs.net/doc/6f4733180.html, Welcome: xmlong@https://www.360docs.net/doc/6f4733180.html, 1.贴片头(Z 轴,θ轴,吸嘴,下视)6.1.控制箱 6.4.面板和示教盒 5. 视觉系统(下视,上视) 4.送料器架和吸 嘴座 3.PCB 传动(轨道调宽,皮带传输,定位针,平台上升) 2.X-Y 轴 6.5.气路板 6.3.步进驱动箱6.2.AC 驱动箱 2.1. 贴片机结构
SMT贴片机原理
SMT贴片机工作原理介绍 2012-01-13 11:19 A.M. 表面贴装技术(Surface mountingTechnology,简称SMT)由于其组装密度高及良好的自动化生产性而得到高速发展并在电路组装生产中被广泛应用。SMT是第四代电子装联技术,其优点是元器件安装密度高,易于实现自动化和提高生产效率,降低成本。SMT生产线由丝网印刷、贴装元件及再流焊三个过程构成,如图1所示。其中SMC/SMD(surfacemount component/Surface mountdevice,片式电子元件/器件)的贴装是整个表面贴装工艺的重要组成部分,它所涉及到的问题较其它工序更复杂,难度更大,同时片式电子元件贴装设备在整个设备投资中也最大。 目前随着电子产品向便携式、小型化方向发展,相应的SMC/SMD也向小型化发展,但同时为满足IC芯片多功能的要求,而采用了多引线和细间距。小型化指的是贴装元件的外形尺寸小型化,它所经历的进程:3225→3216→2520→2125→1608→1003→1603→0402→0201。贴装QFP的引脚间距从1.27→0.635→0.5→0.4→0.3mm将向更细间距发展,但由于受元件引线框架加工速度的限制,QFP间距极限为0.3mm,因此为了满足高密度封装的需求,出现了比QFP性能优越的BGA(Ball Grid Array)、CSP(Chip SizePackage)、COB(Chip On Board)裸芯片及Flip Chip。 片式电子元件贴装设备(通称贴片机)作为电子产业的关键设备之一,采用全自动贴片技术,能有效提高生产效率,降低制造成本。随着电子元件日益小型化以及电子器件多引脚、细间距的趋势,对贴片机的精度与速度要求越来越高,但精度与速度是需要折衷考虑的,一般高速贴片机的高速往往是以牺牲精度为代价的。 2 贴片机的工作原理 贴片机实际上是一种精密的工业机器人,是机-电-光以及计算机控制技术的综合体。它通过吸取-位移-定位-放置等功能,在不损伤元件和印制电路板的情况下,实现了将SMC/SMD 元件快速而准确地贴装到PCB板所指定的焊盘位置上。元件的对中有机械对中、激光对中、视觉对中3种方式。贴片机由机架、x-y运动机构(滚珠丝杆、直线导轨、驱动电机)、贴装头、元器件供料器、PCB承载机构、器件对中检测装置、计算机控制系统组成,整机的运动主要由x-y运动机构来实现,通过滚珠丝杆传递动力、由滚动直线导轨运动副实现定向的运动,这样的传动形式不仅其自身的运动阻力小、结构紧凑,而且较高的运动精度有力地保证了各元件的贴装位置精度。 贴片机在重要部件如贴装主轴、动/静镜头、吸嘴座、送料器上进行了Mark标识。机器视觉能自动求出这些Mark中心系统坐标,建立贴片机系统坐标系和PCB、贴装元件坐标系之间的转换关系,计算得出贴片机的运动精确坐标;贴装头根据导入的贴装元件的封装类型、
G200贴片机精度校正作业规范
1.目的: 保障贴片机贴装精度稳定性、持续提升产品品质 2.范围: 适用于本公司G200贴片机。 3.名词定义: 无 4. 权责: SMT生产技术人员负责定期对设备进行精度校正作业并记录校正精度差值以备查阅5. 精度校正工具及物料、作业流程、相关表单 5.1工具及物料﹕ 1.精度校正玻璃基板1PCS 2.AF06021吸嘴12 PCS 3.0802/paper feeder一支 4.双面胶纸一卷 5.皮带张力计及内六角扳手一套 6. 0201电阻一盘 5.2 作业流程: 1.在做精度校正前应确保贴装头之RT、RN皮带张力在标准范围内(标准如下:) RT张力计选用模式 NO14 M 004.0g/m W 015.0mm/R S 0087 mm 测试标准值:91-101N RN张力计选用模式 NO15 M 002.5g/m W 009.0mm/R S 0091 mm 测试标准值: 45-55N 2.RT皮带张力调整如图所示: a.先将皮带张力计探头靠近RT皮带一 侧,手动弹压皮带后得出数值(图1),张力值 不在范围内则进行调整如下图2所示图1 RT皮带所在位置
b. 先将上图四个螺丝松开(注:并不能完全松开使之处于假锁状态方便调整) c.同时用大号板手顶住RT 马达稍微用力向外(注:此时须两人做作一人测张力,一人调节螺丝) d.测出张力值若在范围内将螺丝锁死否则重复上面b.c 项动作。 3.RN 皮带张力调整如图3所示 a. 先将皮带张力计探头靠近RT 皮带一侧,手动弹压皮带后得出数值(图3)张力值 不在范围内则进行调整如下图4所示 b. 先将上图两个螺丝松开(注:并不能完全松开使之处于假锁状态方便调整) c.同时用大号板手顶住RN 马达稍微用力向外(注:此时须两人做作一人测张力,一人调节螺丝) d.测出张力值若在范围内将螺丝锁死否则重复上面b.c 项动作 4.装著精度校正步骤: a.确认装着精度校正项是否打开: 1:Table 台上升,打开“校正——标准工具选择——对象吸嘴头避开”,检查“裝著精度 補正”是否有效。 2:“裝著精度補正”失效,校正文件参数修改:若“裝著精度補正”项目为灰色,必须修改校正文件参数:路径C_asm_macdata1_calib.ini 。(注意:若前侧头选择macdata1文件夹,若是后侧头选择macdata2文件夹)将calib.ini 文件属性Read_only 勾 图2 RT 皮带张力调整螺丝位置 图 3 RN 皮带所在位置 图4 RN 皮带张力调整螺丝位置
贴片机维修注意事项
在各大型工厂或是工程在使用SMT贴片机时,不论是使用什么样的设备,使用状况都会随时时间的推移而逐渐变坏,这是一个科学道理。大部门情况都是由于受到环境的影响所造成的,另外一方面也考虑到灰尘没有及时清洗,机器内部产生大量的灰尘或是油垢等等都会对机器本身造成很严峻的影响,这些利与弊的关系都是波及到该机器的使用寿命。 贴片机是SMT工艺中比较精密的生产设备,按时对贴片机进行保养是提高贴片机生产效率和减少贴片机故障的保障。贴片机保养分为日保养、周保养和月保养。每个阶段的保养内容也有分别。下面羽成贴片机给大详细介绍下贴片机定期保养内容与保养后的注意事项。 SMT贴片机日常使用注意事项: 1、当检验设备、更换元件、修理设备或设置内部时,必须关闭(OFF)电源。 2、不要在可燃性气体或严重污染的环境条件下使用机器。 3、开机归零之前检查机器内部是否有杂物,防止损坏贴片头或卡坏其它移动部件。
4、移动XY 轴时看机器内部移动部件,视线在吸嘴部分。 5、手动放下所有吸嘴前,检查贴片头上吸嘴,对应吸嘴盒里的位置上是否有吸嘴,若有请手动取出吸嘴再做操作。 6、机器运行时禁止取放飞达、开安全门等。 7、禁止两个或者两个以上的人员同时操作同一台机器,机器运行时严禁把头或手等伸入机器内部。 8、急停开关必须保持有效,遇紧急情况及时按急停开关停止机器运转。 9、机器突然断电重新开启后,放吸嘴之前一定要检查吸嘴盒里的吸嘴与杆头上的是否匹配,如果不匹配,需要手动换吸嘴。 日常检查维护项目: 1、工作台面不得堆放任何杂物,做好日点检内容并做好记录表。 2、用干净白布清洁机器表面灰尘,包括机身表面、显视器、键盘、鼠标等,必要时用碎布蘸一点酒精擦拭机器表面,必须要拧干不滴水才使用,(绝对不允许用水、洗板水之类/腐蚀性溶剂清洗)。 3、肉眼检查进料器料架上有无元件或异物,在有元件或异物的情况下插入