合金钢焊接 Word 文档

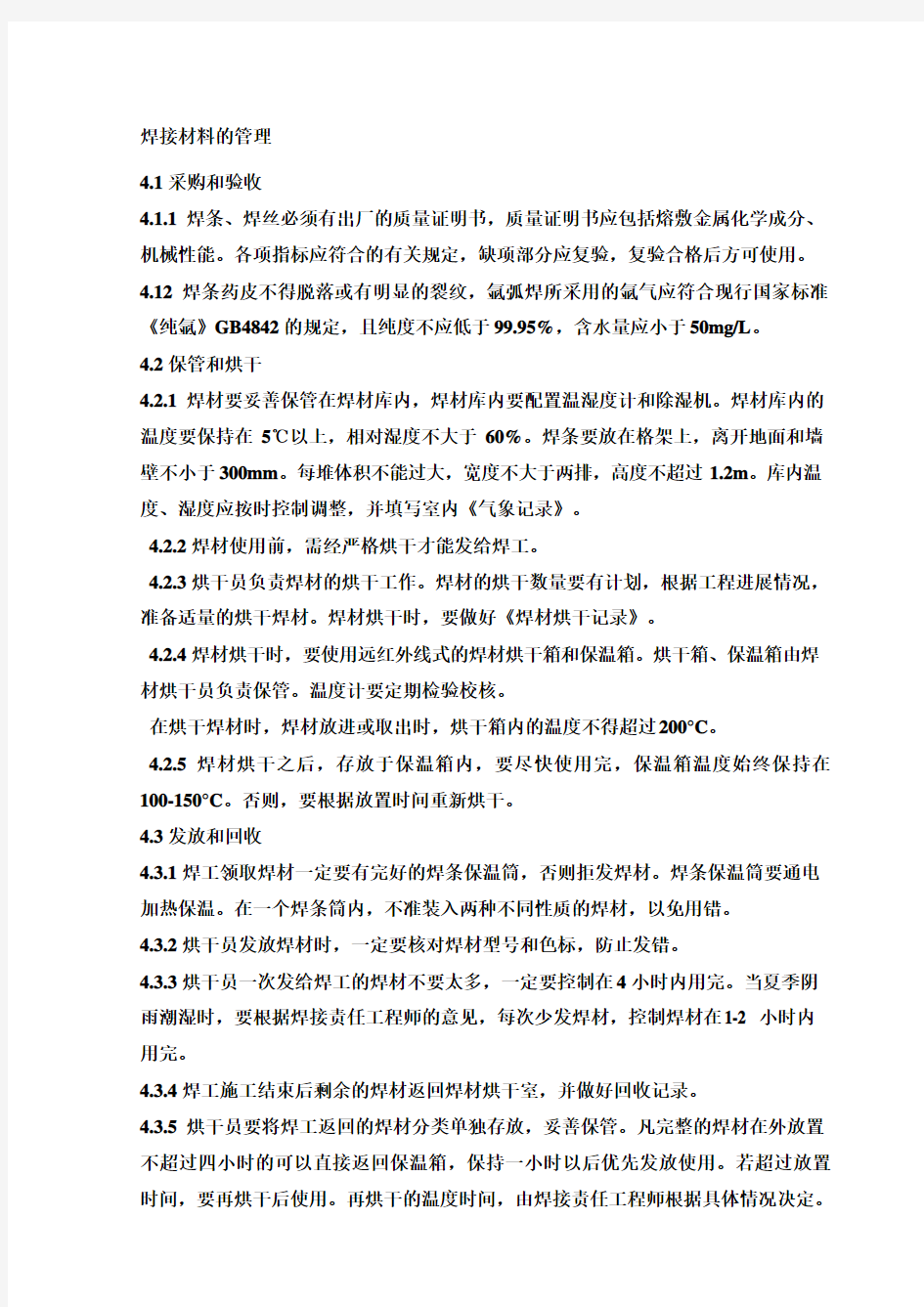
合金钢焊接 Word 文档
焊接材料的管理
4.1采购和验收
4.1.1焊条、焊丝必须有出厂的质量证明书,质量证明书应包括熔敷金属化学成分、机械性能。各项指标应符合的有关规定,缺项部分应复验,复验合格后方可使用。
4.12焊条药皮不得脱落或有明显的裂纹,氩弧焊所采用的氩气应符合现行国家标准《纯氩》GB4842的规定,且纯度不应低于99.95%,含水量应小于50mg/L。
4.2保管和烘干
4.2.1焊材要妥善保管在焊材库内,焊材库内要配置温湿度计和除湿机。焊材库内的温度要保持在5℃以上,相对湿度不大于60%。焊条要放在格架上,离开地面和墙壁不小于300mm。每堆体积不能过大,宽度不大于两排,高度不超过1.2m。库内温度、湿度应按时控制调整,并填写室内《气象记录》。
4.2.2焊材使用前,需经严格烘干才能发给焊工。
4.2.3烘干员负责焊材的烘干工作。焊材的烘干数量要有计划,根据工程进展情况,准备适量的烘干焊材。焊材烘干时,要做好《焊材烘干记录》。
4.2.4焊材烘干时,要使用远红外线式的焊材烘干箱和保温箱。烘干箱、保温箱由焊材烘干员负责保管。温度计要定期检验校核。
在烘干焊材时,焊材放进或取出时,烘干箱内的温度不得超过200°C。
4.2.5焊材烘干之后,存放于保温箱内,要尽快使用完,保温箱温度始终保持在100-150°C。否则,要根据放置时间重新烘干。
4.3发放和回收
4.3.1焊工领取焊材一定要有完好的焊条保温筒,否则拒发焊材。焊条保温筒要通电加热保温。在一个焊条筒内,不准装入两种不同性质的焊材,以免用错。
4.3.2烘干员发放焊材时,一定要核对焊材型号和色标,防止发错。
4.3.3烘干员一次发给焊工的焊材不要太多,一定要控制在4小时内用完。当夏季阴雨潮湿时,要根据焊接责任工程师的意见,每次少发焊材,控制焊材在1-2 小时内用完。
4.3.4焊工施工结束后剩余的焊材返回焊材烘干室,并做好回收记录。
4.3.5烘干员要将焊工返回的焊材分类单独存放,妥善保管。凡完整的焊材在外放置不超过四小时的可以直接返回保温箱,保持一小时以后优先发放使用。若超过放置时间,要再烘干后使用。再烘干的温度时间,由焊接责任工程师根据具体情况决定。
焊材再干燥的次数,一般不超过两次。超过两次的降低使用,不能再用于管道的焊接。
4.4焊材烘干室控制流程图
4.5焊材色标规定
为有效防止焊丝发生混淆导致错误使用,对现场的焊丝涂刷色标来区别。色标的涂刷方法是在焊丝的一端涂上5-10mm 的色标,焊丝的色标规定如下表所示:
序号 名称 牌号
颜色 1 焊丝 TIG-50/H08Mn2Si 无 2 焊丝 TIG-R30/H13CrMoA 红色 3 焊丝 TIG-R40/H08Cr2Mo1 白色 4 焊丝 H00Cr21Ni10/ER308L 蓝色 5 焊丝 H0Cr20Ni10Nb/ER347
黄色 6
焊丝
H1Cr24Ni13
黑色
4.5管材、管件、阀门、法兰管理
应符合《石油化工铬钼耐热钢焊接规程》SH/T3520-2004和《石油化工铬镍奥氏体钢、铁镍合金和镍合金管道焊接规程》SH/T3523-1999相关规定。
焊接责任工程师 提出焊材计划
焊接工艺规程
焊接责任工程师填写 焊材发放记录表头
烘干室
焊接管理员、QC 工程师监控
物质经销公司
焊材库 烘干室 烘干员 烘干 发放回收 领用退库
温度5℃以上 湿度不大于60%
堆放位置离开地面和墙壁大于300mm
焊材复验 填写烘干记录 防止剧冷剧热
温度计定期校验 烘干不超过两次 填写发放记录 必须有焊材筒
剩余焊材退库
资料交焊接工程师
5.焊工管理
5.1参加焊接施工的所有焊工必须持有质量技术监督局颁发的相应项目的焊工资格证
书,经监理机构审查合格后进行相应材质现场在线考试合格,报联合项目部(IPMT)
和监理公司审核备案,同时发给合格焊工标识签,焊工应在合格项目准许的范围内
施焊。焊工应接受技术交底,按照现场的焊接工艺规程(WPS)规定的工艺参数施
焊。
5.2在焊接施工中焊工应严格按照焊接技术方案和焊接工艺要求进行施焊和检查,如
果遇到与焊接工艺要求不符的情况时焊工有权停止焊接,并应及时反映给技术人员。
5.3如果施工人员在焊接施工中发现重大质量问题时应及时报告给技术人员,不得擅
自处理。
6.焊接工艺
6.1主要材料焊接工艺(WPS)一览表
序
号
母材壁厚焊接材料焊接方法预热焊后消氢热处理
1 A106Gr.B/20# ≤
19mm
H08Mn2Si+J427
GTAW+
SMAW
- - -
2 A106Gr.B/20# >19mm H08Mn2Si+J427 GTAW+
SMAW
150-200℃250-300℃630℃
3 A335P11 <13mm TIG-R30+R307 GTAW+
SMAW
150-200℃- -
4 A335P11 ≥
13mm
TIG-R30+R307
GTAW+
SMAW
150-200℃300-350℃720℃
5 A335P22 全部TIG-R40+R407 GTAW+
SMAW
200-300℃300-350℃750℃
6 00Cr19Ni10 5-20 ER308L+A002 GTAW+
SMAW
- - -
7 A312TP321H 5-20 ER347+A132 GTAW+
SMAW
- - 900℃
8 20#+00Cr19Ni10 5-20 ER308L +A302 GTAW+
SMAW
- - -
6.2焊接方法6.2.1工艺管线采用氩弧打底电焊盖面(GTAW+SMAW)的方法施焊,对于壁厚小于6mm,管径小于DN50的对接焊管道可采用全氩弧或氩电联焊方法施焊,承插焊和管台均要求氩弧焊打底。
6.3焊前准备
6.3.1焊接设备和机具必须性能优良、完好。焊接设备要放在机具房内,距离工作地点50m以内。焊接回路线要使用焊接卡子,防止闪击工件。应选择性能优良的具有引弧功能的氩电联焊焊机,如:YC300TSP、LTG-400、ZX7-500S等。现场管道焊接禁止用自制电焊把,必须用带绝缘的正式焊把施焊。焊接设备的电流表、电压表、气体流量计、仪表以及规范参数调节装置应按要求定期检验,上述装置失灵时不得使用,并接受相关部门的检查。
6.3.2材料检验
6.3.2.1合金管道组成件的光谱(PMI)检验范围和比例执行相关规范和联合项目部颁布的《合金材料检验鉴定》IPMT-MS/TM-002-02的规定。特别要注意的是合金钢管子A335P11和A335P22要逐根进行光谱检验,每根管子做一点。
6.3.2.2管道编号为HG103.01Ⅰ、HG115.02、HG155.02和VF142.01中设计压力大于或等于10MPa,的管子外表面按SH3501-2002的要求逐根做磁粉或渗透检测。
6.3.3管道切割及坡口制备
6.3.3.1管道切割和坡口加工,对于碳钢和低合金钢采用氧-乙炔焰切割,不锈钢采用等离子法切割,但切割后必须用砂轮将氧化层、渗碳层彻底清除,并将凹凸不平处打磨平整。
6.3.3.2坡口内用砂轮打磨直至露出金属光泽,并不得有裂纹、分层、夹渣等缺陷,坡口两侧10mm范围内的水、油、锈、漆等杂质要清理干净方可施焊。施焊完应将管内外壁清扫干净,管内不允许有杂物存在,暴露管口应临时采取保护措施,用塑料或管堵封闭。
6.3.3.3用于工艺气体管线(PG)上的合金钢(A335P11和A335P22)管道坡口两侧,应100%进行渗透检测,确认无裂纹时方可施焊。
坡口的组对加工形式,如下图所示。