品质部组织管理规定

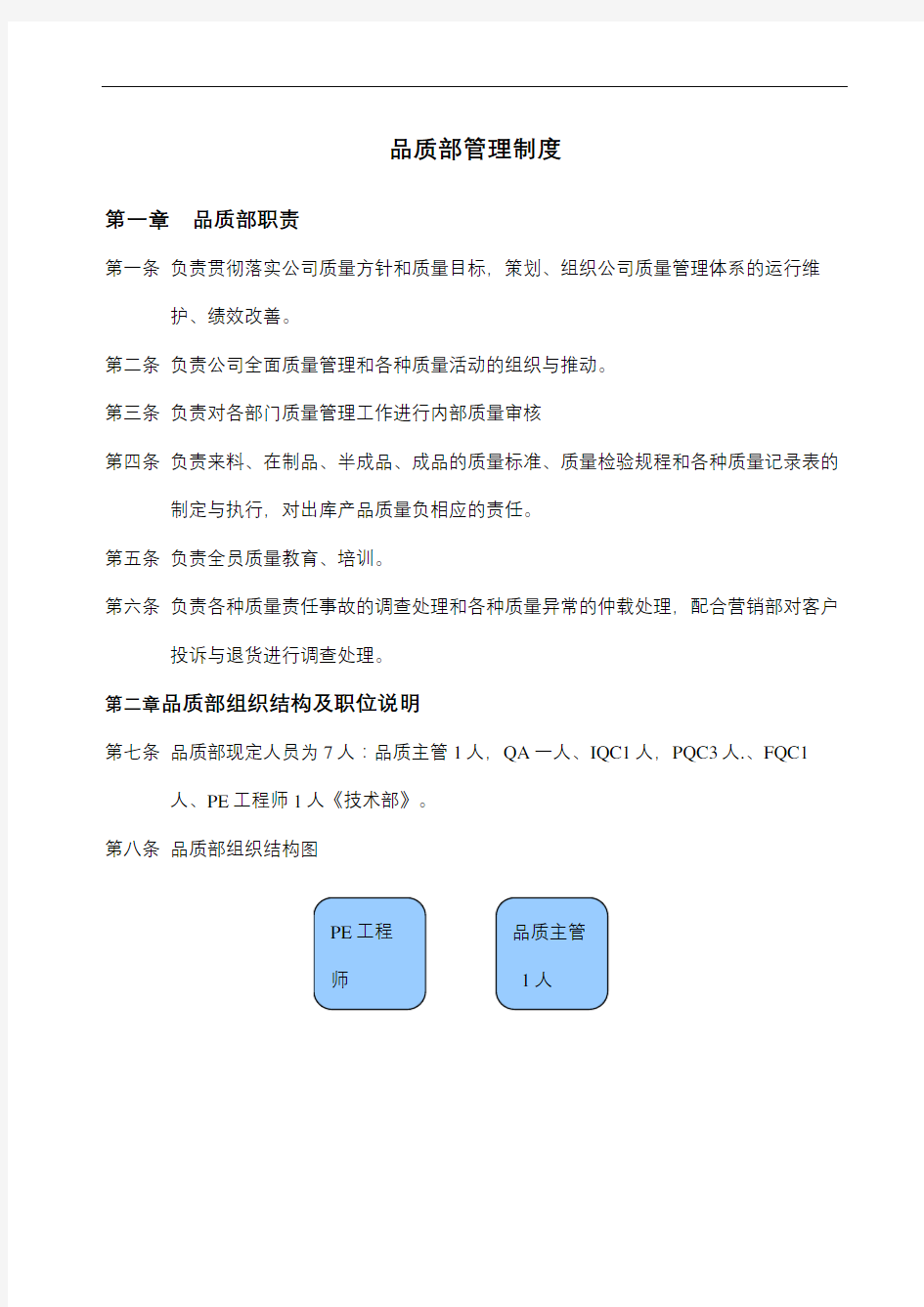
品质部组织管理规定 Prepared on 22 November 2020
品质部管理制度
第一章品质部职责
第一条负责贯彻落实公司质量方针和质量目标,策划、组织公司质量管理体系的运行维护、绩效改善。
第二条负责公司全面质量管理和各种质量活动的组织与推动。
第三条负责对各部门质量管理工作进行内部质量审核
第四条负责来料、在制品、半成品、成品的质量标准、质量检验规程和各种质量记录表的制定与执行,对出库产品质量负相应的责任。
第五条负责全员质量教育、培训。
第六条负责各种质量责任事故的调查处理和各种质量异常的仲载处理,配合营销部对客户投诉与退货进行调查处理。
第二章品质部组织结构及职位说明
第七条品质部现定人员为7人:品质主管1人,QA一人、IQC1人,PQC3人.、FQC1人、PE工程师1人《技术部》。
第八条品质部组织结构图
第九条品质主管岗位责职
第十条IQC岗位责职
第十一条PQC岗位职责
第十二条QA岗位职责
第十三条FQC岗位职责
第四章品质人员工作流程图第十四条IQC日常工作流程图
第十五条:PQC日常工作流程图
第十六条FQC日常工作流程图
抽样管理制度
第一条目的
制定抽样检验管理制度,以便抽样检验方案之了解与运作执行,确保产品抽样检验作业的正常进行。
第二条范围
适用于品质部抽样检验时检验方案的制定
第三条职责
1、I QC:来料检验
2、F QC:最终检验
第四条定义
1、批量:来料数量
2、样本量:抽样数量
3、Ac:接收数
4、Re:拒收数
5、AQL:接收质量限
第五条作业内容
1、根据不同的检验阶段和检验内容选择相应的抽样方案、检验水平和AQL值
(1)检验阶段:IQC(来料检验)、FQC(最终检验)
(2)检验内容:外观、结构、尺寸、功能、装配、包装及其它检验
(3)抽样方案:分为“正常检验单次抽样方案”,“放宽检验单次抽样方案”,“加严检验单次抽样方案”
(4)检验水平和AQL值:各检验阶段的检验内容对应的检验水平和AQL值见下表
3、不同阶段
的抽样检验步骤
(1)来料检验(IQC):IQC根据来料的批数和之前来料的合格批数选择正确的检验类型、抽样数量、Ac和Re的取值、抽样方案
(2)最终检验(FQC):
根据批量、检验内容、检验水平从“样本量字码”表中选择相应的样本量字码从“正常检验单次抽样方案”中选择样本量;特殊检验时,检验数量即为样本量,按AQL判定
Ac和Re值
4、相关规定
(1)批量外箱抽检:对批量之产品进行随机抽取样本箱数,而样本箱数的取得,通常按LEVEL:Ⅱ进行抽取,且抽取时箱与箱之间隔,尽量分布均匀。从不同的包装箱内抽取样品进行检验,如果只有4箱,则需从每箱中抽取样品,如果超过4箱,至少需要达到80%的开箱检验率(开箱计算方式小数位都采用进位方式,不采取四舍五入,例:7箱×80%≈6箱;9箱×80%≈8箱)
(2)检验时需要依次从外观及结构、尺寸、功能、装配、包装、其它等方面进行全面检查,所检项目及不良品总数在允收范围内,才可进行收货或允许出货
(3)将检验结果,详细记录清楚所有不良,以便质量信息能得以迅速反馈和相关部门能及时做出改善
(4)来料检验/IQC:填写《IQC检验报告》最终检验/FQC:填写《成品检验报告》
第六条表单/记录
1、《IQC检验报告》、《评审报告》
2、《FQC检验报告》
PQC质量管理制度
第一节总则
第一条目的
为了确保制和程质量稳定,并力求改善质量、提高生产效率、降低生产成本,本公司特制定本办法,以供相关人员查阅。
第二条范围
从原料投入经加工至生产成品的整个过程
第二节制程质量检查
第三条品质部对各在制品均依《品质部管理制度》的规定实施质量检验,以便提早发现异常,迅速处理,确保在制品的质量
第四条在制品质量检验依制程区分,由PQC负责检验
第五条PQC应配合生产部做好制造中加工条件的测试工作
第六条各部门在制造过程发现异常时,生产组长和PQC应立即追查原因,同时以“质量异常反馈单”的形式提交到相关部门。
第七条PQC在抽检过程中发现异常时,应及时反映给品质主管及QA。
IQC质量管理制度
第一条职责
进料又称来料检验,是杜绝不合格物料进入生产的首要环节的控制点。来料检验由品质部IQC负责。
第二条进料检验要点
1、IQC对来料进行检验前,首先要清楚该批物料的质量检测要项,有不明之处提前向主管
汇报,直到清楚不止。
2、必要时IQC可从进料中随机抽取两件货物,交上级确认,作为临时样品,并附上相应的
说明。
第三条影响进料检验的方法、方式的因素
1、来料对产品的影响程度
2、供应商的控制能力及以往的信誉
3、该货品以往经常出现的质量异常
4、进料对工厂成本的影响
5、客户的要求
第四条来料检验项目与方法
1、外观检测:一般用目视、手感、限度样品等方法进行验证
2、尺寸检测:一般有卡尺
3、结构检测:一般用目视,以样品有参照物
4、特性检测:一般用仪器和特定方法来检测
5、安装检测:一般是与半成品或成品进行试装
6、包装检测:一般是目视,与成品样品进行对照或与对供应商的要求进行核实
第五条进料检测的方式选择
进料检验的方式包括全数检验、免检等多种,IQC应根据进料的具体情况进行选择。各种方式的具体适用范围如下:
第六条检验结果的处理方式
1、检验合格
经IQC检验,不合格数低于限定的不合格品个数时,则判定该批来料为允收。IQC应填写《IQC检验报告》并签名。并在物料标签上盖章,绿色“OK”章,在状态栏上标识“合格”。
2、拒收/退货
若不合格个数大于限定不合格数,认为拒收,IQC应及时填写《IQC检验报告》、《评审报告》并签名,交于上级和其它部门确认,经有关部门签名后通知仓库退货,并在物料标签上盖章红色“NG”,在状态栏上标识“退货”。
3、特采
所谓特采,即经IQC检验,质量低于允收水准,IQC应及时填写《IQC检验报告》、《评审报告》并签名,交于上级其它部门确认,经有关部门确认为“特采”并签名后,IQC通知仓库,并在物料标签上盖章,黄色“NG”章,并在物料标签的状态栏上标识“特采”。
4、挑选使用
经IQC检验,质量低于允收水准,IQC应及时填写《IQC检验报告》、《评审报告》并签名,交于上级其它部门确认,经有关部门确认为“挑选”并签名后,IQC通知仓库,并在物料标签上盖章,紫色“NG”章,并在物料标签的状态栏上标识“挑选”。(挑选可分为:1、本公司装配部挑选;2、供应商挑选。如是装配部挑选,则IQC需在外箱上贴上“装配部挑选”字样,可以先入库;如是供应商挑选,采购部需通知供应商,挑选之后才能入库)。
第七条相关品质记录
不管是什么样的检验结果,IQC都必须记当于《IQC检验报告》或《评审报告》并输入电子档案。(便于产品质量追踪和对供应商的管理)
不良物料的处理管理制度
第一节总则
第一条目的
本处理程序涉及不良物料控制的职责、权限作出了规定。执行该程序将有效防止不良物料与合格物料混在一起从而影响对供应商的管理与维护。
第二条不良物料处理的范围
1、来料检验和试验中发现的不良物料
2、过程检验和试验中发现的不良物料
3、生产过程中发现的不良物料
第三条职责
1、生产部对生产过程中挑选出来的不良物料应做好分类与标识
2、生产部、品质部、技术部、采购部应对不良物料进行评审
3、仓库应将不良物料放置不良区
4、采购部、品质部须做好与供应商的沟通
其他相关部门配合上述部门对不合格品进行处理。
第二节不良物料处理工作程序
第四条不良物料标识
对不良物料应立即分类标识,并填写不良物料处理单
第五条不良物料隔离
对不良物料进行标示后,应将不良物料和合格物料隔离开来,并送往不良品区。
第六条不良物料评审
公司品质部根据不合格品产生的环节,召集采购部、生产部、技术部等部门对不良物料进行评审以确定是让步接收,还是降级或报废
第七条不良物料处理
应按实际情况及时对不良物料做出处理。生产部确认是否报废、退货并填写不良物料处理单,由品质部、技术部、采购部进行确认之后方可做出下一步处理。
第三节相关部门的职权范围
1、品质部
(1)对于没有分类或没有标识好的不良物料有权不在处理单上签字并有权要求生产部重新挑选或再标识
(2)对于采购部不签字的处理单,品质部有权要求其提供不签字的理由
2、采购部
对于不属实的不良物料有权不签字
3、仓库
对于没有提供完整的不良物料处理单的物料,仓库有权拒收相应的不良物料
第四节不良物料处理流程图
质量异常处理管理制度第一节总则
第一条目的
为了明确制定发现质量异常时应采取的措施,以使问题能迅速得到解决,并防止再次发生,并维持质量的稳定,特制定办法
第二条范围
本办法适用于制程异常处理工作
第三条制程质量异常的定义
1、不良率高或发现严重缺陷
2、控制图曲线有连续上升或下降趋势时
第二节实施要点
第四条PQC在制造过程中发现质量异常时,应立即知会生产部并填写异常处理单通知相关部门。
第五条填写《质量异常反馈单》应注意以下几点:
1、必须由PQC填写
2、同一异常已填写后在24小时内不得填写
3、详细填写,尤其是不良描述
4、全程跟踪
第六条相关部门根据流程尽快跟进
1、PQC负责填写“问题描述”、“效果确认”
2、生产进行确认
3、技术部负责“原因分析”、“临时措施”、“根本措施”
第三节质量异常处理工作流程