橡胶概述
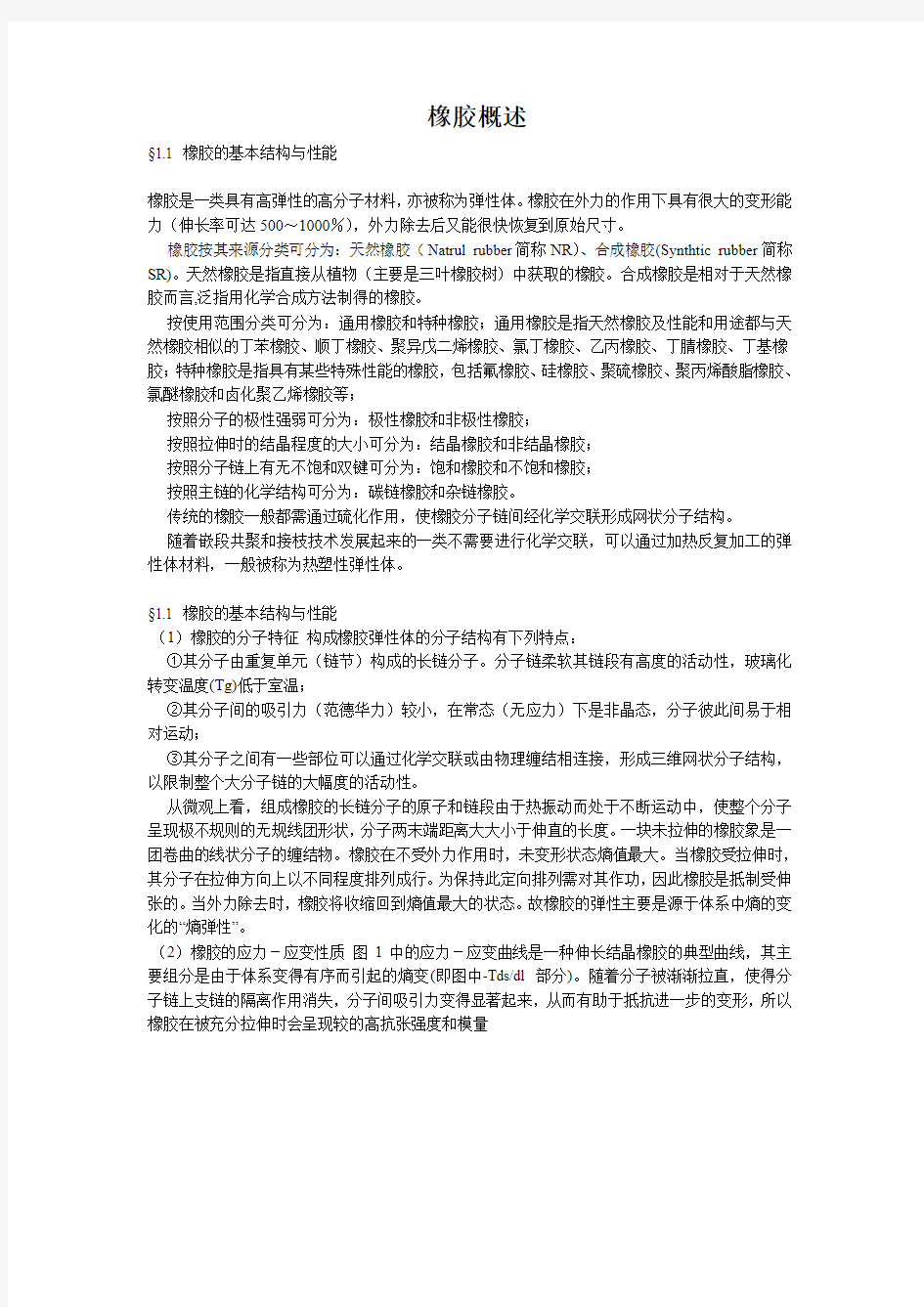

橡胶概述
§1.1 橡胶的基本结构与性能
橡胶是一类具有高弹性的高分子材料,亦被称为弹性体。橡胶在外力的作用下具有很大的变形能力(伸长率可达500~1000%),外力除去后又能很快恢复到原始尺寸。
橡胶按其来源分类可分为:天然橡胶(Natrul rubber简称NR)、合成橡胶(Synthtic rubber简称SR)。天然橡胶是指直接从植物(主要是三叶橡胶树)中获取的橡胶。合成橡胶是相对于天然橡胶而言,泛指用化学合成方法制得的橡胶。
按使用范围分类可分为:通用橡胶和特种橡胶;通用橡胶是指天然橡胶及性能和用途都与天然橡胶相似的丁苯橡胶、顺丁橡胶、聚异戊二烯橡胶、氯丁橡胶、乙丙橡胶、丁腈橡胶、丁基橡胶;特种橡胶是指具有某些特殊性能的橡胶,包括氟橡胶、硅橡胶、聚硫橡胶、聚丙烯酸脂橡胶、氯醚橡胶和卤化聚乙烯橡胶等;
按照分子的极性强弱可分为:极性橡胶和非极性橡胶;
按照拉伸时的结晶程度的大小可分为:结晶橡胶和非结晶橡胶;
按照分子链上有无不饱和双键可分为:饱和橡胶和不饱和橡胶;
按照主链的化学结构可分为:碳链橡胶和杂链橡胶。
传统的橡胶一般都需通过硫化作用,使橡胶分子链间经化学交联形成网状分子结构。
随着嵌段共聚和接枝技术发展起来的一类不需要进行化学交联,可以通过加热反复加工的弹性体材料,一般被称为热塑性弹性体。
§1.1 橡胶的基本结构与性能
(1)橡胶的分子特征构成橡胶弹性体的分子结构有下列特点:
①其分子由重复单元(链节)构成的长链分子。分子链柔软其链段有高度的活动性,玻璃化转变温度(Tg)低于室温;
②其分子间的吸引力(范德华力)较小,在常态(无应力)下是非晶态,分子彼此间易于相对运动;
③其分子之间有一些部位可以通过化学交联或由物理缠结相连接,形成三维网状分子结构,以限制整个大分子链的大幅度的活动性。
从微观上看,组成橡胶的长链分子的原子和链段由于热振动而处于不断运动中,使整个分子呈现极不规则的无规线团形状,分子两末端距离大大小于伸直的长度。一块未拉伸的橡胶象是一团卷曲的线状分子的缠结物。橡胶在不受外力作用时,未变形状态熵值最大。当橡胶受拉伸时,其分子在拉伸方向上以不同程度排列成行。为保持此定向排列需对其作功,因此橡胶是抵制受伸张的。当外力除去时,橡胶将收缩回到熵值最大的状态。故橡胶的弹性主要是源于体系中熵的变化的“熵弹性”。
(2)橡胶的应力-应变性质图1中的应力-应变曲线是一种伸长结晶橡胶的典型曲线,其主要组分是由于体系变得有序而引起的熵变(即图中-Tds/dl 部分)。随着分子被渐渐拉直,使得分子链上支链的隔离作用消失,分子间吸引力变得显著起来,从而有助于抵抗进一步的变形,所以橡胶在被充分拉伸时会呈现较的高抗张强度和模量
图1橡胶伸应力的内能组分和熵组分与伸长率的关系图2橡胶在恒定伸长下应力与温度关系
橡胶在恒应变下的应力是温度的函数。随温度的升高橡胶的应力将成比例地增大。这可由图2中的曲线看出。
橡胶的应力对温度的这种依赖称为焦耳效应,它可以说明金属弹性和橡胶弹性间的根本差别。在金属中,每个原子都被原子间力保持在严格的晶格中,使金属变形所做的功是用来改变原子间的距离,引起内能的变化。因而其弹性称为“能弹性”。其弹性变形的范围比橡胶中主要由于体系中熵的变化而产生的“熵弹性”的变化范围要小得多。
图3是典型的拉伸结晶橡胶的预测曲线和实验曲线的比较。在一般的使用范围内,橡胶的应力-应变曲线是非线性的,因此橡胶的弹性行为不能简单地以杨氏模量来确定。
图3橡胶的单向拉伸和压缩曲线图4增大变形对橡胶的剪切模量-温度曲线的影响
(3)橡胶的变形与温度、变形速度和时间的关系橡胶分子的变形运动不可能在瞬时完成,因为分子间的吸引力必须由原子的振动能来克服,如果温度降低时,这些振动变得较不活泼,不能使分子间吸引力迅速破坏,因而变形缓慢。在很低温度下,振动能不足以克服吸引力,橡胶则会变成坚硬的固体。
如果温度一定而变形的速度增大,也可产生与降低温度相同的效果。在变形速度极高的情况下,橡胶分子没有时间进行重排,则会表现为坚硬的固体。
橡胶材料在应力作用下分子链会缓慢的被破坏,产生“蠕变”,即变形逐渐增大。当变形力除去后,这种蠕变便形成小的不可逆变形、称为“永久变形”(见图5)。
(4)橡胶的能量吸收和损失橡胶受力时能贮存大量的能量,而在它回缩时释放出其贮存的绝大部分能量。这是它独特的应力-应变性质的结果。
然而,由于蠕变(应力松弛)的效应,回缩的应力-应变曲线不能够与上升曲线重合,因而有能量损失(滞后损失)。
表1 同重量的橡胶与其他各种材料的贮能能力比较
材料名称贮能,(J/Kg)
灰铸铁 1.11
软钢9.18
磷青铜12.2
轧制铝22.6
弹簧钢284
胡桃木365
硫化橡胶44800
图5橡胶的蠕变曲线和恢复曲线图6橡胶的滞后环(ABC所包围的面积表示生热所消耗的能量)
(5)橡胶的热性能
①导热性橡胶是热的不良导体,其导热系数在厚度为25毫米时约为2.2~6.28瓦/米2·0K。是优异的隔热材料,如果将橡胶做成微孔或海绵状态,其隔热效果会进一步提高,使导热系数下降至0.4~2.0瓦。任何橡胶制件在使用中,都可能会因滞后损失产生热量,因此应注意散热。
②热膨胀由于橡胶分子链间有较大的自由体积,当温度升高时其链段的内旋转变易,会使其体积变大。橡胶的线膨胀系数约是钢的20倍。这在橡胶制品的硫化模型设计中必须加以考虑,
因为橡胶成品的线性尺寸会比模型小1.2~3.5%。对于同一种橡胶,胶料的硬度和生胶含量对胶料的收缩率也有较大的影响,收缩率与硬度成反比,与含胶率成正比。各种橡胶在理论上的收缩率的大小顺序为:
氟橡胶>硅橡胶>丁基橡胶>丁腈橡胶>氯丁橡胶>丁苯橡胶>天然橡胶
橡胶制品在低温使用时应特别注意体积收缩的影响,例如油封会因收缩而产生泄漏,橡胶与金属粘合的制品会因收缩产生过度的应力而导致早期损坏。
(6)橡胶的电性能通用橡胶是优异的电绝缘体,天然橡胶、丁基橡胶、乙丙橡胶和丁苯橡胶都有很好的介电性能,所以在绝缘电缆等方面得到广泛应用。丁腈橡胶和氯丁橡胶,因其分子中存在极性原子或原子基团,其介电性能则较差。在另一方面,在橡胶中配入导电炭黑或金属粉末等导电填料,会使它有足够的导电性来分散静电荷,或者甚至成为导电体。
表2各种橡胶纯胶的电性能参数
胶种介电常数体积电阻ρ,Ω.m功率因数击穿电压,MV/m
天然橡胶 2.4~2.6 (1~6)×1017 0.16~0.29 20~30
丁苯橡胶 2.4~2.5 1016~1017 0.1~0.3 20~30
丁腈橡胶7~12 1012~1013 5~6 20
氯丁橡胶7~8 1011~1014 3 20
丁基橡胶 2.1 >1017 0.04 24
乙丙橡胶 2.35 6×1017 0.02~0.03 28~30
硅橡胶3~4 1013~1014 0.04~0.06 15~20
表3各种橡胶硫化胶的电性能参数
胶种介电常数体积电阻ρ,Ω.m功率因数击穿电压,MV/m
天然橡胶 3.0~4 1016~1017 0.5~2.0 20~30
丁苯橡胶 3.0~4 1014~1017 0.5~2.0 20~30
顺丁橡胶 3.0~4 1074~1017 0.5~2.0 20~30
丁基橡胶 3.0~4 1017~1018 0.4~1.5 25~35
乙丙橡胶 2.5~3.5 1017~1018 0.3~1.5 35~45
氯丁橡胶 5.0~8.0 1014~1015 2~20 15~20
丁腈橡胶 5.0~12.0 1012~1013 2~20 -
氯磺化聚乙烯4~5 1014~1016 2~10 20~25
硅橡胶3~4 1015~1018 0.5~2.0 20~30
氟橡胶3~6 1014~1017 2~10 20~25
聚硫橡胶4~6 1015~1016 2~10 15~20
(7)橡胶的气体透过性(气密性) 橡胶的气透率是气体在橡胶中的溶解度与扩散度的乘积。气体的溶解度随橡胶的溶解度参数增加而下降,气体在橡胶中的扩散速度取决于橡胶分子中侧链基团的多少。气体在各种橡胶中的透过速度有很大的不同,在橡胶中气透性较低的是聚醚橡胶和丁基橡胶,丁基橡胶气透性只有天然胶的1/20。而硅橡胶的气透性最大。橡胶的气透性随温度的升高而迅速上升,对于使用炭黑作填料的制品来说,其品种和填充量对气透性能影响不大。但软化剂的用量大小对硫化胶的气透性能影响很大,对气透性能要求较高的橡胶制品,软化剂的用量尽可
能减少为好。
表4各种橡胶气体透过率的相对值(以天然胶为100)
胶种空气He H2 O2 N2 CO2
天然橡胶100 100 100 100 100 100
丁苯橡胶76 74 81 73 78 94
顺丁橡胶81 86 82 82 105
氯丁橡胶15 27 17 14 20
丁腈橡胶(-CN20%)33 55 51 35 31 48
丁腈橡胶(-CN32%)8.5 32 24 10 7.5 14
丁腈橡胶(-CN39%)3.4 22 15 4.1 2.9 5.7
丁基橡胶 4.8 21 15 5.6 5.0 4.0
硅橡胶2700 1070 2200 3300 1600
聚硫橡胶 3.2 12 2.4
(8)橡胶的溶解与溶胀未硫化的橡胶可以溶于与其溶解度参数相近的溶剂中。对硫化胶而言,由于化学交联使橡胶大分子联接成三维网状结构,故在溶剂中仅能吸收溶剂逐渐胀大并达到平衡值(最大溶胀)。这种现象称为橡胶的“溶胀”。溶胀后的体积可达橡胶体积的数倍。并伴随机械强度的损失。硫化胶的最大溶胀与其交联密度有关。在吸收溶剂时,硫化橡胶的交联网络也胀开而产生将溶剂挤出网外的弹性收缩力,当溶剂扩散渗入的压力与交联网络的弹性收缩力相等时,即达到溶胀平衡。
由于液体浸入橡胶的深度是接触时间平方根的函数,因此,即使橡胶对所接触的液体无特别阻抗能力,如果橡胶制件本身有一定的体积,也能使其有一定的使用寿命。
(9)橡胶的可燃性大多数橡胶具有程度不同的可燃性。而分子中含有卤素的橡胶如氯丁橡胶、氟橡胶等,则具一定的的抗燃性。因此,含有氯原子的氯丁胶和氯磺化聚乙烯在移开外部火焰后,既便燃烧也是困难的,而氟橡胶则完全是自行灭火的。在胶料中配入阻燃剂(例如磷酸盐或含卤素物质)可提高其阻燃性。
§1.2 橡胶的配合
任何一种橡胶只有通过配合和加工,才能满足不同的产品性能的要求。橡胶的配合主要有硫化、补强和防老化三大体系:
(1)橡胶的硫化体系橡胶的硫化就是通过橡胶分子间的化学交联作用将基本上呈塑性的生胶转化成弹性的和尺寸稳定的产品,硫化后的橡胶的物性稳定,使用温度范围扩大。“硫化过程(Curing)”一词在整个橡胶工业中普遍使用,在橡胶化学中占有重要地位。橡胶分子链间的硫化(交联)反应能力取决于其结构。不饱和的二烯类橡胶(如天然橡胶、丁苯橡胶和丁腈橡胶等)分子链中含有不饱和双键,可与硫黄、酚醛树脂、有机过氧化物等通过取代或加成反应形成分子间的交联。饱和橡胶一般用具有一定能量的自由基(如有机过氧化物)和高能辐射等进行交联。含有特别官能团的橡胶(如氯磺化聚乙烯等),则通过各种官能团与既定物质的特定反应形成交联,如橡胶中的亚磺酰胺基通过与金属氧化物、胺类反应而进行交联。
不同类型的橡胶与各种交联剂反应生成的交联键结构各不相同,硫化胶性能也各有不同。橡胶的交联键有三种形式:
①②③
第①种是使用硫黄或硫给予体作交联剂的情况,生成的可以是单硫键(x=1)、双硫键(x=2)和多硫键(x=3~8);
第②种是使用树脂交联和肟交联的情况;
第③种是使用过氧化物交联的过氧化物硫化和利用辐射交联的辐射硫化的情况,生成碳-碳键。
多数的通用橡胶采用硫黄或硫给予体硫化,即在生胶中加入硫黄或硫给予体以及缩短硫化时间的促进剂和保证硫黄交联效率的氧化锌和硬脂酸组成的活性剂。在实际中通常按硫黄用量及其与促进剂的配比情况划分成以下几种典型的硫化体系:
①普通硫磺硫化体系由常用硫黄量(>1.5份)和常用促进剂量配合组成。使用这种硫化体系能使硫化胶形成较多的多硫键,和少量的低硫键(单硫键和双硫键)。硫化胶的拉伸强度较高,耐疲劳性好。缺点是耐热和耐老化性能较差。
②半有效硫化体系由硫黄量0.8~1.5份(或部分硫给予体)与常用促进剂量配合所组成。使用这种硫化体系能使硫化胶形成适当比例的低硫键和多硫键,硫化胶的扯断强度和耐疲劳性适中,耐热、耐老化性能较好。
③有效硫化体系由低硫黄量(0.3~0.5份)或部分硫给予体与高促进剂量(一般为2~4份)配合组成。使用这种硫化体系能使硫化胶形成占绝对优势的的低硫键(单硫键和双硫键),硫化胶的耐热、耐老化性能好,缺点是拉伸强度和耐疲劳性能较低。
④无硫硫化体系不用硫黄而全部用硫给予体和促进剂配合组成。这种硫化体系与有效硫化体系的性能相似。
(2)橡胶的补强及补强填充体系
橡胶的补强是指能使橡胶的拉伸强度、撕裂强度及耐磨耗性等获得明显提高的作用。对于非自补强的合成橡胶,如果没有加入补强剂,便没有使用价值。加入炭黑等补强剂,可以使这些橡胶的强度提高数倍至十倍。炭黑对橡胶的强系数见表8.4-5
补强剂也使橡胶其它的性能发生变化,如硬度增大、定伸应力提高、应力松驰性能变差、弹性下降、滞后损失变大、压缩永久变形增大等。
①补强剂橡胶的补强填充剂是按粒径来分类的,粒子的大小是填料对物性影响的主要依据。补强性填料的粒子极小,能赋予非结晶橡胶以有用的强度性能,并对结晶橡胶的强度也有一些改进。填料质量和粒子大小可用来控制这两类橡胶胶料的伸长性能。
炭黑是较优良的橡胶补强剂,多用于需要补强的场合。白色或浅色胶料的补强则使用被称为白炭黑的二氧化硅(SiO2)。
表5炭黑对橡胶补强系数
胶种拉伸强度,MPa 补强系数
未补强的硫化胶补强的硫化胶
丁苯橡胶(SBR) 2.5~3.5 20.0~26.0 5.7~10.4
丁腈橡胶(NBR) 2.0~3.0 20.0~27.0 0.6~13.5
乙丙橡胶(EPDM) 3.0~6.0 15.0~25.0 2.5~8.3
顺丁橡胶(BR)8.0~10.0 18.0~25.0 1.8~3.1
天然橡胶(NR)16.0~24.0 24.0~35.0 1.0~2.2
炭黑是按制法(炉法或热裂法)、粒子大小(20毫微米到50微米)和“结构”(粒子连接成短链或集团)的多少来分类的。每一参数都对胶料性能有显著
的影响。其代表性用量是25~50phr,此量是用每百份橡胶
(phr)中的重量份数来表示的。
从图中可以看出,随着炭黑用量的增加,橡胶的物性并
不在单一炭黑用量上达其最优值。硫化胶的伸长率随着炭
黑用量的增加而不断降低,同时其模量或刚度却不断升高。
随着模量或刚度的增大,橡胶的变形性能(弹性)随之削
弱,而更象皮革,导致动态应变时滞后损失和生热增加。
②增容粒状填料这是些粒径比补强性填料大得多的物
料,粒径通常是20微米。增容填料的主要功用是降低成本。
随着其在胶料中的配入量增加,抗张强度和耐撕裂成比例
的降低。因此其用量由物性要求所决定。通常的做法是在
同一胶料中并用补强性和增容性填料,以便增加较廉的非
橡胶物料含量,而不太损害橡胶的物性。具有代表性的增容性填料是碳酸钙和陶土。
③增塑(软化)剂油类油类被用做增容和软化材料,引起塑性增加用来抵消大量填料所引起的胶料在加工中流动阻力的增加和硫化胶刚度的增大。同时会造成滞后损失增加和蠕变及应力松弛速度的增加。图7天然橡胶的物性与炭黑含量的关系
(3)橡胶的老化及防老剂与许多其它有机材料一样,橡胶的强度、延伸性能和其它有用的机械性能会随时间的延续而逐渐劣化,称之为橡胶的老化。其主要原因是热氧老化和臭氧老化所致,它会因光或高温亦或某些微量元素(如铜或锰)而更加恶化。
热氧老化是一个复杂的过程,包括许多反应。影响反应的条件有:工艺条件,金属催化剂,温度及配合剂配方等。热氧老化的结果有两种:
①因断链导致橡胶软化发粘。天然橡胶和丁基胶发生的氧化主要是这种反应机制。
②因不断导致橡胶硬化发脆。丁苯胶、氯丁胶、丁腈胶及三元乙丙胶发生的氧化主要是这种反应机制。
大多数情况下,这两种损害机制都会发生,哪种机制占优势,哪种机制就决定制品的变化趋势。而且不管发生哪种损害机制,橡胶伸长率的损失都是测试橡胶老化最敏感的指标。
某些金属(主要是铜、锰、铁及钴)离子能通过影响过氧化物的分解催化橡胶氧化反应,加速氧的侵蚀。这种情况对橡胶的生胶比对硫化胶更为明显。硫黄硫化的硫化胶中,仅天然橡胶及其它含不饱和异戊二烯单元的橡胶会被影响至明显程度。改善方法是消除有害金属的来源,和在胶料中加入能与金属离子起反应生成稳定产物的金属稳定剂。
臭氧侵蚀机制通常认为是臭氧与橡胶中的不饱和部分(即“双键”)发生反应生成臭氧化物,臭氧化物容易分解,造成橡胶断链引起橡胶表面龟裂,龟裂随机械破裂而进一步增长。如果制品处于应变条件就产生龟裂。随着臭氧侵蚀历程的反复进行,龟裂增长则愈大。无应力的橡胶,其外表面会形成一层称为“霜”的银灰色薄层,在湿热环境下这种现象很容易发生。
橡胶防老剂是一类能防止(严格的说是延缓)橡胶老化的物质。因为橡胶老化的本质是橡胶的热氧老化和橡胶的臭氧老化,所以橡胶防老剂包括橡胶抗氧剂和抗臭氧剂。一般情况下,一种高效的抗臭氧剂也是一种抗氧剂,反之则不然。选择防老剂的标准是以最低的成本获得满意的防老效果,需要考虑的因素包括防老剂的污染性、变色性、挥发性,溶解性、稳定性以及物理状态.胺类防老剂——不同类型的单胺和双胺是高效抗氧剂,但一般都会产生较严重的变色和污染。这类防老剂广泛使用的典型种类有:
①苯基萘胺类;
②二氢化喹啉类;
③二苯胺衍生物类;
④取代的对苯二胺类。
酚类防老剂的效果一般不如胺类防老剂,但不存在变色问题。故不能使用胺类防老剂浅色橡胶制品,可选用酚类防老剂。非污染不变色抗氧剂有如下5类:
①受阻酚类抗氧剂;
②受阻双酚类抗氧剂;
③对苯二酚类抗氧剂;
④亚磷酸酯类抗氧剂;
⑤有机硫化合物类抗氧剂。
抗臭氧剂的选择要根据橡胶的不同应用而定,静态臭氧防护与动态臭氧防护各有许多不同的要求。针对不同的环境条件及不同的臭氧浓度,有如下四类物质可选作抗臭氧剂,其中有些物质的抗臭氧作用有一定的局限性。
①石蜡;
②二丁基二硫代氨基甲酸盐;
③6-乙氧基-2,2,4-3甲基-1,2-二氢喹啉;
④取代的对苯二酚。
防老剂在使用过程中的挥发损失,与防老剂的分子量和分子类型有关。通常,分子量越大,挥发性就越低。分子类型的影响又比分子量更大。例如,受阻酚的挥发性比具有相同分子量的胺类防老剂高。
防老剂在橡胶中的溶解度取决于防老剂的化学结构以及胶种和温度等因素。在橡胶中溶解度高,在水和有机溶剂中溶解度低是比较理想的。在橡胶中的溶解度低,则容易发生喷霜。在水和有机溶剂中的溶解度高,则在使用过程中易被水或溶剂抽出而损失
防老剂的物理状态也是一个重要特征。橡胶聚合物制造部门需要液态和易于乳化的材料,而橡胶制品部门则需要选用固态的、能自由流动但无粉尘飞扬的材料。
防老剂用量的原则是能保证橡胶制品在长期使用后不全部被消耗。必须同时考虑诸多因素,如材料的成本、胶种、污染的要求等。一般配方中的防老剂用量为3份左右。
§1.3 橡胶的加工
(1)橡胶的塑炼及塑炼工艺将橡胶生胶在机械力、热、氧等作用下,从强韧的弹性状态转变为柔软而具有可塑性的状态,即增加其可塑性(流动性)的工艺过程称为塑炼。
塑炼的目的是通过降低分子量,降低橡胶的粘流温度,使橡胶生胶具有足够的可塑性。以便后续的混炼、压延、压出、成型等工艺操作能顺利进行。同时通过塑炼也可以起到“调匀”作用,使生胶的可塑性均匀一致。塑炼过的生胶称为“塑炼胶”。如果生胶本身具有足够的可塑性,则可免去塑炼工序。
塑炼的方法按所用的设备主要分为开炼机塑炼、密炼机塑炼和螺杆塑炼机塑炼。
①开炼机塑炼利用开炼机前后两个速度不同的辊筒形成的相对速度差所引起的撕拉力(剪切力),在逐渐缩小的辊距内对橡胶施以强烈的碾压和撕拉作用。这种机械作用,扯断了橡胶分子链,在空气中塑炼还伴有热和氧的裂解作用等,降低了橡胶的分子量,降低了粘流温度,使其可塑性增大。
开炼机塑炼的影响因素有辊温、辊距、转速和速比、塑炼时间、炼胶容量、辊筒的工作长度、割刀次数和方式、胶料放置时间等。
②密炼机塑炼将橡胶投到密炼机的密炼室内,对物料进行加压。密炼室内两个转子以不同的速度相向回转,使被加工的生胶在转子间隙中、转子与密炼室壁的间隙中以及转子与上、下顶栓的间隙中受到不断变化的剪切、扯断、搅拌、折卷和磨擦的强烈的捏炼作用。在高温、快速和加压的条件下很快的提高橡胶的可塑性(塑炼)。密炼机的塑炼作用主要靠转子机械作用和热氧化裂解作用。
密炼机塑炼的影响因素有转子转速、密炼室温度、塑炼时间、容量和上顶压力等。由于密炼机塑炼属高温塑炼,塑炼效果随温度升高而增大,但温度高会导致橡胶分子链过度降解,致使胶料物理机械性能下降,而诸如丁苯橡胶,用密炼机塑炼时如超过140℃还会产生支化、交联,形成凝胶,反而降低可塑性,在170℃下塑炼还会生成紧密型凝胶,即使用精炼方法也不能使它消除。为了提高密炼机使用效率,通常对可塑性要求高的胶料(威氏可塑性在1.5以下者),需采用分段塑炼或加塑解剂塑炼。
③螺杆塑炼机塑炼是用螺杆塑炼机的螺杆与机筒间的机械剪切力和高温热作用使橡胶分子链断裂。与开炼机和密炼机塑炼的差别是螺杆塑炼法中氧对生胶的作用较小。螺杆塑炼法有生产能力大、节电效果明显、操作简单容易掌握、可实现塑炼的连续化生产等优点。使用螺杆塑炼机塑炼时应该严格控制排胶温度在180℃以下,注意防止出胶后胶料表面氧化作用,并尽量避免产生夹生胶。
应用开炼机塑炼和密炼机塑炼时,都可采用塑解剂来加速塑炼过程。塑解剂是通过化学作用增强生胶塑炼效果、缩短塑炼时间的物质,又称化学增塑剂。它与一般物理增塑剂如油品、酯类脂肪酸衍生物类等相比,具有增塑效果强、用量少、且对橡胶制品物理机械性能几乎没有影响等特点。
塑解剂增强塑炼效果的作用机理主要有两方面:一是塑解剂在塑炼过程中受热、氧的作用,分解产生自由基,这些自由基能使橡胶大分子链发生氧化降解;二是塑解剂能封闭塑炼过程中橡胶大分子链断裂生成的端基,并使其丧失活性,不再重新结合,从而使可塑性增加。
由于塑解剂的效能是随温度的升高而增强,所以在密炼机高温塑炼中使用塑解剂比在开炼机低温塑炼中更为有效。
(2)橡胶的混炼及混炼工艺混炼是将塑炼胶或已具有一定可塑性的生胶,与各种配合剂经机械作用使之均匀混合的工艺过程。混炼过程就是将各种配合剂均匀地分散在橡胶中,以形成一个以橡胶为介质或者以橡胶与某些能和它相容的配合组分(配合剂、其它聚合物)的混合物为介质,以与橡胶不相容的配合剂(如粉体填料、氧化锌、颜料等)为分散相的多相胶体分散体系的过程。对混炼工艺的具体技术要求是:配合剂分散均匀,使配合剂特别是炭黑等补强性配合剂达到最好的分散度,以保证胶料性能一致。混炼后得到的胶料称为“混炼胶”,其质量对进一步加工和制品质量有重要影响。
混炼常用的设备是开炼机和密炼机。
①开炼机混炼开炼机混炼的必要条件是根据各种橡胶的粘弹性、松弛时间和转变温度等基本性质,选择合适的辊温(下表),使之处于包辊状态,以便进行混炼。
表6各种橡胶开炼机混炼的适用温度
胶种辊温,℃胶种辊温,℃
前辊后
辊前辊后辊
天然橡胶 55~60 50~55 氯醚橡胶 70~75 85~90
丁苯橡胶 45~50 50~60 氯磺化聚乙烯 40~70 40~70
丁腈橡胶 35~45 40~50 氯丁橡胶≤40≤45
丁基橡
胶 40~45 55~60
丙烯酸酯橡胶40~55 30~50
顺丁橡胶 40~60 40~60 聚胺酯橡胶 50~60 55~60
乙丙橡胶 60~75 约85 聚硫橡胶 45~60 40~50
加料顺序是影响开炼机混炼质量的一个重要因素。加料顺序不当会导致分散不均匀,脱辊、过炼,甚至发生早期硫化(焦烧)等质量问题。原则上应根据配方中配合剂的特性和用量来决定加料顺序,宜先加量少、难分散者。后加量大,易分散者;硫黄或者活性大、临界温度低的促进剂(如超速促进剂)则在最后加入,以防止出现早期硫化(焦烧)。液体软化剂一般在补强填充剂等粉剂混完后再加入,以防止粉剂结团、胶料打滑、胶料变软致使剪切力小而不易分散。
橡胶包辊后,按下列一般的顺序加料:橡胶、再生胶、各种母炼胶→固体软化剂(如较难分散的松香、硬脂酸、固体古马隆树脂等)→小料(促进剂、活性剂、防老剂)→补强填充剂→液体软化剂→硫黄→超促进剂→薄通→倒胶下片。
对于某些特殊胶料(如硬质胶、海绵胶等),则需采取与上述一般加料顺序不同的混炼方法。
除了辊温和加料顺序影响开炼机混炼质量之外,在操作上尚需注意:填胶容量不宜过多,否则不易混炼均匀,一般合成胶容量应比天然橡胶小一些。在保证混炼质量的前提下,混炼时间应尽量缩短,以防止胶料因过炼而导致物理机械性能下降和影响生产效率。辊筒速度和速比要适宜,既要有利于混合、分散,又不致因生热过快导致早期硫化(焦烧)。
②密炼机混炼密炼机通过转子、上下顶栓在密炼室中产生复杂的流动方式和高剪切力,使橡胶配合剂和粒状添加剂很快粉碎和均匀分散,是一种高效的混炼方法。但是高剪切力会使物料温度在混炼中迅速上升,一般会达到130℃。这已超过了大多数硫化系统的活化温度,会使胶料发生早期硫化(焦烧)。一般的做法是将大部分物料在密炼机中混炼,然后将胶料从密炼机排放到开炼机上,在开炼机上加硫化剂或超速促进剂。由于开炼机实际上只在辊缝线上对胶料有挤压作用,而提供了很大的冷却面积,致物料的温度降低。在这一阶段加入硫化剂可以避免胶料发生早期硫化(焦烧)。
密炼机混炼方法主要有一段混炼法、二段混炼法、引料法和逆混法:
一段混炼法指经密炼机和压片机一次混炼制成混炼胶的方法。通常加料顺序为:生胶→小料→填充剂或1/2→1/2炭黑→油料软化剂→排料。胶料直接排入压片机,薄通数次后,使胶料降至100℃以下,再加入硫黄和超促进剂,翻炼均匀后下片冷却。此法的优点是比二段混炼法的胶料停放时间短和占地面积小,其缺点是胶料可塑性偏低,填充补强剂不易分散均匀,而且胶料在密炼机中的炼胶时间长,易产生早期硫化(焦烧)。此法较适用于天然橡胶胶料和合成橡胶比例不超过50%的胶料。
二段混炼法将混炼过程分为两个阶段,其中第一段同一段混炼法一样,只是不加硫黄和活性较大的促进剂,首先制成一段混炼胶(炭黑母炼胶),然后下片冷却停放8小时以上。第二段是对第一段混炼胶进行补充加工,待捏炼均匀后排料至压片机加硫化剂、超促进剂,并翻炼均匀下片。为了使炭黑更好地在橡胶中分散,提高生产效率,通常第一段在快速密炼机(40r/min 以上)中进行,第二段则采用慢速密炼机,以便在较低的温度加入硫化剂。一般当合成胶比例超过50%时,为改进并用胶的掺合和炭黑的分散,提高混炼胶的质量和硫化胶的物理机械性能,可以采用二段混炼法。
引料法在投料同时投入少量(1.5~2Kg)预混好的未加硫黄的胶料,作为“引胶”或“种子胶”,当生胶和配合剂之间浸润性差、粉状配合剂混入有困难时,这样可大大加快粉状配合剂(填充补强剂)的混合分散速度。例如,丁基橡胶即可采取此法。而且不论是在一段、二段混炼法或是逆混法中,加入“引胶”均可获得良好的分散效果。
逆混法加料顺序与上述诸法加料顺序相反的混炼方法,即先将炭黑等各种配合剂和软化剂按一定顺序投入混炼室,在混炼一段时间后再投入生胶(或塑炼胶)进行加压混炼。其优点是可缩短混炼时间。还可提高胶料的性能。该法适合于能大量添加补强填充剂(特别是炭黑)的胶种,如顺丁橡胶、乙丙橡胶等,也可用于丁基橡胶。逆混法还可根据胶料配方特点加以改进,例如抽胶改进逆混法及抽油改进逆混法等等。
(3)橡胶的硫化、硫化条件及硫化方法橡胶的硫化是指在一定的温度和压力下,使橡胶分子从线形结构通过交联变为三维网状结构的工艺过程。是橡胶加工中最主要的物理—化学过程和工艺过程。硫化后的橡胶一般称为“硫化胶”。
橡胶的硫化历程可以分为四个阶段:
①诱导期胶料放入模腔内,随着温度上升,其粘度逐渐降到最低值,由于继续受热,橡胶开始轻度硫化。这一过程所需要的时间称为诱导期,通常称为焦烧时间。诱导期的长短决定着胶料的操作安全性能。
②热硫化期是硫化反应的交联阶段,在这一阶段中,橡胶分子链逐渐生成三维网状结构,弹性和拉伸强度迅速提高。热硫化期的长短取决于胶料的配方,热硫化期常作为衡量硫化速度的尺度。硫化速度可以通过硫化曲线中
热硫化阶段的斜率来定量表征。理论
上讲,热硫化期越短越理想。
③正硫化期又称平坦硫化期,
是硫化胶物理性能维持最佳值所经
历的时间范围。达到这一阶段所对应
的温度时间分别称为正硫化温度与
正硫化时间,合称为“正硫化条
件”。正硫化期在硫化历程图上表现
为一个平坦区。正硫化期的长短取决
于硫化配合剂的选择,也与硫化温度
相关。
④过硫化期相当于硫化过程中三维网络形成阶段的后期。这一阶段中,主要是交联键发生重排、裂解等副反应,因此表现为胶料的物理机械性能显著下降。若分析图中的过硫化阶段,则可以出现两种情况:(A)曲线保持较长的平坦期后再下降称为硫化返原现象,此时硫化胶变软变粘。通常用硫黄硫化的天然橡胶、丁腈橡胶、氯丁橡胶、乙丙橡胶等会出现这种情况。(B)曲线继续上升,硫化胶变硬变脆。这是由结构化作用或断裂后的交联键重新交联引起的,通常非硫黄硫化的丁苯橡胶、丁腈橡胶、氯丁橡胶、乙丙橡胶等会出现此类现
象。
图8橡胶硫化历程图
橡胶硫化过程中的温度、压力和时间等条件对硫化胶的质量具有决定性影响,通常称为:硫化三要素:
①硫化压力一般橡胶制品(除胶布等薄制品外)在硫化时往往要施加一定的压力。用以防止制品在硫化过程中产生气泡,提高硫化胶的致密性;使胶料充分流动并充满模具;提高橡胶与骨架材料间的密着度;提高胶料的物理机械性能(或橡胶制品的使用性能)。
在一定的范围内,随着硫化压力的增加,硫化胶的拉伸强度、动态模量、耐疲劳性和耐磨性等都会相应地提高。
通常,对硫化压力的选取应根据胶料的配方、胶料的可塑性、产品的结构等来决定。各类橡胶制品的适宜硫化压力范围如表8.4-7所示。
硫化的加压方式通常有以下几种:一是用平板硫化机将液压泵的压力传递给模型,由模型再传递给胶料;二是有硫化介质(如蒸汽)直接加压;三是由压缩空气加压;四是由注射机的活塞加压等。在热空气连续硫化、红外线或远红外线硫化时,则采用常压。
②硫化温度与硫化时间硫化温度是橡胶进行硫化反应的基本条件,直接影响硫化速度和硫化胶的性能。各种橡胶的适宜硫化温度为:
天然橡胶<143℃ 异戊橡胶<151℃ 顺丁橡胶<151℃
丁苯橡胶<180℃ 氯丁橡胶<151℃ 丁腈橡胶<180℃
表7各类橡胶制品的适宜硫化压力
制品类型加压方式硫化压力,MPa
模型制品平板硫化机 2.4
注射机加压 120~150
汽车外胎水胎过热水加压 2.2~4.8
外模加压 15.0
传动带平板硫化机 0.9~1.6
输送带平板硫化机 1.5~2.5
胶管(缠水布)直接蒸汽加压 0.3~0.5
胶鞋,热空气或混气加压 0.2~0.4
薄胶布直接蒸汽加压 0.1~0.3 橡胶制品的硫化的方法可按使用设备类型、加热介质种类和硫化工艺方法等分类:
目录
§1 橡胶概述
§2 天然橡胶(NR)
§3 聚丁二烯橡胶
§4 丁苯橡胶(SBR)
§5 聚异戊二烯橡胶(IR) §6 乙丙橡胶(EPM、EPDM)
§10 硅橡胶
§11 氟橡胶(FPM)
§12 聚丙烯酸酯橡胶(ACM)§13 聚氨酯橡胶(PU)
§14 聚硫橡胶(T)
§15 氯醚橡胶
§7 氯丁橡胶(CR)
§8 丁腈橡胶(NBR)
§9 丁基橡胶(IIR)和聚异丁烯§16 氯化聚乙烯(CM)和氯磺化聚乙烯和(CSM)
§17 热塑性弹性体(TPE)
天然橡胶行业的起源
我国经济自改革开放之后,天然橡胶产业得以迅速发展。自我国加入世界贸易组织后,天然橡胶的进口需求量逐年增加。 天然橡胶最早被发现于南美亚马逊雨林,19世纪后期从南美大陆移植于刚果、利比里亚、尼日利亚、斯里兰卡等地,而后由斯里兰卡移植到马来、印尼等热带地区。 目前,天然橡胶种植主要分布在南北纬15°之间的低海拔、低纬度的热带地区,我国是世界上第1个在北纬18~24°范围内大面积植胶成功的国家。印尼位于赤道附近,气温、降雨相对稳定,产量也相对稳定。 我国科研人员选育出“热研72059”优良品种,可实行全周期间作,提高土地利用率50%以上,目前已在海南儋州、昌江等地示范推广。我国天然橡胶亩产长期在80公斤左右徘徊,但在海南、云南等植胶区发现单株产量超过100公斤甚至200公斤的橡胶树,如能利用超高产单株培育出超高产品种,将大幅度提高产量和效益。此外,我国科研人员正研究新型橡胶生产模式,从幼龄橡胶树的茎叶直接萃取天然橡胶,初步试验数据显示,每亩可收获茎叶等干物质1吨,提取出60公斤天然橡胶。 以上就是天然橡胶行业的起源,中国的橡胶行业正在蓬勃地发展当中,现在很多专业做橡胶定制的厂家能根据买家的需求定制各种不一样的模具,有的公司还有十几二十几年以上的橡胶定制经验,选择这样的公司来进行定制是比较不错的。 深圳佳诺佳精密科技有限公司一直致力于模具和中高端橡塑制品的研究和开发工作。拥有成套的橡塑模具及生产设备和检测试验设备。团队有多名从事模具设计、橡塑配方、及超过20年以上相关经验的工程技术和管理人员。公司从
模具设计、模具制造、橡塑产品材料开发,半成品、成品、印刷、包装的完整生产线。从胶料引进到多样化产品的出厂,每一个生产过程都得到严密的控制,成熟的生产设备,现代的生产管理是品质产品的保障。引进橡塑模具和橡塑产品的专业生产设备和检测试验设备,不断改进生产工艺,为业内提供更好的塑胶配件,是我们共同的理想,也是我们砥砺前行的伟大使命!
橡胶技术网 - 合成橡胶发展状况
我国合成橡胶产业现状及发展 周文荣 中国合成橡胶工业自1958年实现工业化生产以来,已经跨 过50年辉煌发展历程。中国合成橡胶工业是在自主创新和引进 技术为基础上起步,并以自主创新技术为主发展壮大起来的。 目前已经进入世界合成橡胶的生产和消费大国前列。 世界上通用的七大基本胶种中国均能生产。目前国内生产的主要合成橡胶产品是:丁苯橡胶(SBR)、丁二烯橡胶(BR)、氯丁橡胶(CR)、丁腈橡胶(NBR)、乙丙橡胶(EPDM)、丁基橡胶(IIR) 和新近投产的1.5万吨异戊橡胶等基本合成橡胶,以及苯乙烯类热塑性丁苯橡胶(SBCs),还生产多种合成胶乳及特种橡胶。 一、世界SR市场引擎地位日显 根据国际合成橡胶生产商协会(IISRP)统计,世界合成橡胶生产装置总能力1389.7万吨(2007年年底),其中中国为160.7万吨,占11.6%;2008年世界合成橡胶消费量为1317.2万吨,其中中国相应品种的消费量为266.8万吨,占20.3%。我国合成橡胶产能占世界总量比例见表l。 表1 我国合成橡胶产能占世界总量比例(07年底止) 项目 SBR BR IR EPDM IIR NBR CR SBCs 总计世界能力k t/.a–150693042 611 1318945 609 410 1894 13897 中国能力k t/.a–1697 510 0 20 30 65 55 230 1607 中国占比k t/.a–113.816.8 0 1.5 3.2 10.713.4 12.1 11.6 2009年中国合成橡胶装置能力和消费量与2007年相比均有显著增加,今后中国在世界合成橡胶市场的份额还将继续提升。 二、装置能力达250万吨 “十一五”期间,中国合成橡胶产业进入高速发展时期。四年内已新增能力117万吨/年,年均增长17.1%,主要合成橡胶(不包括胶乳和其它特种胶,下同)产量增加65万吨,年均增长10.5%。 这四年时间内的新增能力相当于2000年前四十多年发展能力的总和。我国合成橡胶装置能力跨上第一个百万吨的台阶经历了40多年,进入第二个百万吨能力只经历了8年,再过一、二年将进入第三个百万吨
合成橡胶总结
橡胶合成简介 合成简介 合成橡胶:在一定温度围具有高度的弹性,可用来替代天然橡胶的一类聚合物通称为合成橡胶。 合成生产工艺特点: 合成橡胶最常用的聚合实施方法是乳液聚合,其次,溶液聚合(包括淤浆聚合),本体聚合基本不用。 工艺包括: a.单体准备与精制; b.反应介质和辅助剂等的准备; c.聚合; d.单体和溶剂的回收; e.橡胶的分离; f.橡胶后处理(洗胶、脱水、干燥); g.成型和包装。 (一)顺丁橡胶(BR) 由丁二烯聚合制得结构规整的合成橡胶。 顺丁橡胶生产工艺——溶液聚合 A.催化剂 催化剂类型:钛系催化剂、钴系催化剂、镍系催化剂、稀土催化剂。 1.钛系催化剂 TiCl4—AlR3、TiCl4—AlR3—I (R是乙基或异丁基),优点是产品的凝胶含量低,充油和碳黑量高。但是催化剂的价格高,不可溶,产品的分子量分布窄,不利于加工冷流倾向大。 2.钴系催化剂 是由主催化剂二价钴化合物(氯化物、氧化物、有机酸盐和吡啶络合物)和助催化剂(AlR2Cl、AlCl3、Al2Et3Cl3等)组成。为提高催化剂的活性可加入第三组分,水、有机过氧化物、卤素、醇等。优点:由于可溶,催化剂可形成均相引发体系,活性大为提高可加入给电子体提高溶解性,但不能多加,否则形成反式-1,4-聚丁二烯,配置催化剂时,加入二烯烃易形成π络合物,可提高催化剂的稳定性。缺点是分子量大,易产生凝胶,产品加工性能不好,因聚合物的规整性高,影响聚合物的结晶想、倾向,降低橡胶弹性。 3.镍系催化剂 镍系催化剂属于均相催化剂 有机镍(环烷酸镍、辛酸镍、硬脂酸镍、苯甲酸镍等)
该组分是组成催化剂的核心,主要起定向作用,具有高顺式能力,环烷酸镍较为常用。三氟化硼乙醚络合物 与烷基铝共同提供催化剂活性和提高聚合物分子量,能提高收率,凝胶含量降低。 烷基铝 作为助催化剂,用于还原镍,且有清除杂质的作用。 在镍系催化剂中,在环烷酸镍和烷基铝反应前,可加入少量丁二烯,以提高催化剂的稳定性及聚合物的分子量。 镍系催化剂特点:顺式含量高,可达96%,催化剂活性高,性能稳定,用量少,单程转化率高,聚合速率易控制,提高单体浓度对聚合物无不利影响,可节省溶剂回收费用,定向能力高,生成聚合物凝胶含量少,支链少,分子量分布宽,在加工上比钛系和钴系优越。 4.稀土催化剂 由三部分组成,稀土卤化物,羧酸盐或螯合物,烷基卤化铝。特点:分子量分布宽,挂胶少,冷流性较小,可得顺式含量大于97%的顺丁橡胶。 B.影响聚合的主要因素 1.改变催化剂的配比及用量 可以适当调节聚合物的聚合速率和分子量。 2.催化剂的化方式及条件 a)化方式 分为二元化和三元化 b)化条件 分为化时间和化温度。其中化温度对产品的质量起控制门尼粘度的作用。催化剂通过化反应生成配位络合物,化温度高,副反应增加,活性下降,活性中心也减少,因此聚合速率降低,分子量增大,凝胶含量增多,一般采用低温下化,一般在-5~40℃。 3.单体浓度 单体浓度低,对应的溶剂量增大,导致设备的利用率降低,而且增大溶剂回收的负荷,浓度过高会导致聚合速率过快,转化率增大,体系粘度显著上升,给搅拌和散热以及输送带来困难。 4.聚合温度 温度升高,催化剂诱导期缩短,反应速率常数增大,聚合速率加快,同时也加快了活性中心的再生,使得分子量降低。可以适当提高聚合温度以降低催化剂的用量。在生产中,由于随聚合反应的进行,单体浓度逐渐降低,可以通过提高后釜的温度来提高转化率。 5.聚合时间 在聚合反应转化率达到一定值后,随时间的进行,单体的转化率增加就变得缓慢,单体浓度降低生成的聚合物分子量变低,导致分子量分布变宽,影响橡胶的性能,因此生产中一般都是当转化率到达一定值时终止反应。 6.调节剂 一般可以加入醇类物质,通过消耗一定的活性中心,提高聚合物的分子量。 7.溶剂 要求溶剂的溶解度参数要与聚合物的接近。 8.杂质 会影响聚合物的聚合速率、分子量、聚合物结构。所以单体、溶剂、惰性气体、反应设备都必须纯化。 C.顺丁橡胶的生产工艺过程 经精制的单体和溶剂以一定比例与催化剂混合后连续加至3~4个串联的带夹套压力釜
济南橡胶制品项目建议书
济南橡胶制品项目 建议书 参考模板
报告说明— 聚异戊二烯橡胶简称异戊橡胶,其发展史起源于对天然橡胶的研究,而异戊橡胶的工业化则是在其单体和Ziegler型催化剂有了确实保证之后才实现的。20世纪80年代以后,由于国际环境进一步趋向缓和,天然橡胶生产稳定增长;加之人工合成的聚异戊二烯橡胶的综合性能始终不及天然橡胶,而且受到单体来源、生产成本的制约,因而除前苏联外的其他一些国家纷纷终止了聚异戊二烯橡胶的生产,目前仅有美国、日本少量生产聚异戊二烯橡胶。但从长远和发展的观点看,聚异戊二烯橡胶仍是一个值得关注的合成橡胶品种。 该异戊二烯橡胶项目计划总投资12389.61万元,其中:固定资产投资9137.19万元,占项目总投资的73.75%;流动资金3252.42万元,占项目总投资的26.25%。 达产年营业收入23686.00万元,总成本费用18129.37万元,税金及附加234.98万元,利润总额5556.63万元,利税总额6558.04万元,税后净利润4167.47万元,达产年纳税总额2390.57万元;达产年投资利润率44.85%,投资利税率52.93%,投资回报率33.64%,全部投资回收期4.47年,提供就业职位343个。 在我国,异戊二烯橡胶主要应用于全钢载重子午胎的胎圈钢丝部位。在胎圈钢丝部位使用异戊二烯橡胶,可以改善胶料的加工性能,同时胶料
具有较高的硬度、耐撕裂性和耐疲劳性能,胶料的流动性好,钢丝表面附 胶均匀;斜交胎也使用异戊二烯橡胶,主要是取代天然橡胶,以降低成本。
目录 第一章项目概述 第二章投资单位说明 第三章背景、必要性分析第四章项目市场研究 第五章项目建设方案 第六章选址可行性分析第七章项目工程方案分析第八章工艺技术方案 第九章环境保护可行性第十章生产安全保护 第十一章建设风险评估分析第十二章节能可行性分析第十三章实施进度 第十四章投资方案 第十五章经济评价 第十六章项目总结 第十七章项目招投标方案
天然橡胶行业分析报告2011
2011年天然橡胶行业 分析报告
目录 一、天然橡胶行业基本情况 (4) 1、自然属性 (4) 2、产品分类 (5) 二、国际天然橡胶行业分析 (6) 1、国际天然橡胶需求情况 (6) (1)概览 (6) (2)需求的地区结构 (7) (3)需求的行业结构 (8) (4)天然橡胶与合成橡胶的替代关系 (9) 2、国际天然橡胶供给 (11) (1)天然橡胶种植面积和产量 (11) (2)天然橡胶生产的地区结构 (12) (3)供给方面的垄断因素 (13) 3、国际天然橡胶市场价格 (14) 4、国际天然橡胶产业的生产组织、产品结构和技术发展趋势 (16) (1)行业生产的组织方式 (16) (2)生产工艺与产品结构 (17) (3)技术发展趋势 (17) 三、我国的天然橡胶行业分析 (18) 1、我国天然橡胶行业的政策环境和管理体制 (19) (1)产业政策环境 (19) (2)主管部门和管理体制 (19) (3)具体政策、管理制度 (20) 2、国内天然橡胶需求 (24) (1)需求总量居世界首位、高度依赖进口 (24) (2)下游行业发展还将引领天然橡胶的需求 (25) 3、国内天然橡胶供给 (26)
(1)产量增长缓慢,国内自给水平严重不足 (26) (2)生产布局、产品结构 (27) 4、我国的天然橡胶进口 (27) 5、影响我国天然橡胶产业发展的有利因素和不利因素 (28) (1)有利因素 (28) (2)不利因素 (30) 6、行业内主要参与者 (30)
一、天然橡胶行业基本情况 天然橡胶具备优良的综合性能,表现为高弹性、高强度、高伸长率,耐磨、耐撕裂、耐冲击、耐油、耐酸碱、耐腐蚀,以及良好的绝缘性、密封性、柔韧性和黏合性。由于综合性能出众,天然橡胶被广泛运用到工业、农业、国防、交通、医疗卫生等各个领域。国际上天然橡胶工业大规模发展超过100 年,目前有超过5 万种工业制品以天然橡胶为原料或与其相关。天然橡胶与石油、煤炭、钢铁并称为四大工业原料,天然橡胶消费量成为一国工业化水平的重要标志。 传统理论认为,北纬18 度以北不适宜种植橡胶。上世纪50 年代起,经广大农垦人的不懈努力,我国在海南、云南西双版纳等北纬18-24 度地区逐步建立了天然橡胶种植基地,在理论和实践上推动了国际天然橡胶行业的发展。受自然条件限制,我国宜胶地区面积非常有限,我国政府一直从保障国家战略资源安全的角度,以多种产业支持政策来推动天然橡胶行业的发展。本世纪以来,我国已成为世界最大的天然橡胶消费国和进口国。 1、自然属性 现阶段世界上99%的天然橡胶产自巴西三叶橡胶树,主要种植在泰国、马来西亚和印度尼西亚等东南亚国家。一般情况下,橡胶树定植6-9 年后可以开割,开割期长达30 年左右。 天然胶乳由橡胶树树皮分泌产出,主要成分包括水和橡胶烃,也
世界合成橡胶工业发展回顾及展望
全球合成橡胶工业发展回顾及展望 一、世界合成橡胶工业发展简史 人工合成橡胶的思路渊源于人们对天然橡胶的剖析和仿制,合成橡胶工业的诞生和发展取决于原料来源、单体制造技术的成熟程度,以及单体、催化剂和聚合方法的选择。此外,由于橡胶是交通运输工具(汽车、飞机的轮胎等)的主要材料,因而它的发展又和战争对橡胶的需求密切相关。 第一次世界大战期间诞生了合成橡胶,并且有少量生产以应战争急需。20世纪30年代初期建立了合成橡胶工业。第二次世界大战促进了多品种、多性能合成橡胶工业的飞跃发展。50年代初,发明了齐格勒-纳塔催化剂,单体制造技术也比较成熟,使合成橡胶工业进入合成立构规整橡胶的崭新阶段。60年代以后,合成橡胶的产量开始超过了天然橡胶。 天然橡胶的剖析和仿制1826年,M.法拉第首先对天然橡胶进行化学分析,确定了天然橡胶的实验式为C5H8。1860年,C.G.威廉斯从天然橡胶的热裂解产物中分离出C5H8,定名为异戊二烯,并指出异戊二烯在空气中又会氧化变成白色弹性体。1879年,G.布查德用热裂解法制得了异戊二烯,又把异戊二烯重新制成弹性体。尽管这种弹性体的结构、性能与天然橡胶差别很大,但至此人们已完全确认从低分子单体合成橡胶是可能的。 世界合成橡胶工业发展里程碑事件 1900年И.Л.孔达科夫用2,3-二甲基-1,3-丁二烯聚合成革状弹性体。1927-1928年,氯丁橡胶问世。 德国于1917年首次用2,3-二甲基-1,3-丁二烯生产了合成橡胶,取名为甲基橡胶W 和甲基橡胶H 。 30年代初期,德国H.施陶丁格的大分子长链结构理论的确立(1932)和苏联H.H.谢苗诺夫的链式聚合理论(1934)的指引,为聚合物学科奠定了基础。代 1935年德国法本公司首先生产丁腈橡胶,1937年法本公司在布纳化工厂建成丁苯橡胶工业生产装置。 1943年,美国开始试生产丁基橡胶。 50年代中期,齐格勒-纳塔和锂系等新型催化剂的发明;石油工业提供了大量高品级的单体。代表产品:异戊二烯橡胶、顺丁橡胶、乙丙橡胶。 60年代,合成橡胶工业以继续开发新品种与大幅度增加产量平行发展为特征。目的是简化橡胶加工工艺,降低70年代,合成橡胶已基本可代替天然橡胶制造各种轮胎和制品,某些特种合成橡胶的性能是天胶所不具备的。
丁腈橡胶的生产工艺与技术进展
丁腈橡胶的生产工艺与技 术进展 Prepared on 24 November 2020
丁腈橡胶的生产工艺与技术进展 丁腈橡胶的生产工艺 2.1.1 丁腈橡胶的生产工艺 工业上生产丁腈橡胶采用连续或间歇式乳液聚合工艺,按聚合温度不同,分为热法聚合与冷法聚合两类。冷法聚合的反应温度一般控制在5~15℃,热法聚合则为30~50℃。冷法聚合通常采用连续聚合工艺,热法聚合通常采用间歇聚合工艺。目前世界上生产厂家,如朗盛公司、美国Lion Copolymer公司、日本瑞翁公司以及日本合成橡胶公司都采用低温乳聚法。产品类型包括固体丁腈橡胶(固体NBR)、氢化丁腈橡胶(HNBR)、粉末丁腈橡胶(PNBR)、羧基丁腈橡胶(XNBR)以及丁腈橡胶胶乳(NBR胶乳)等。 目前世界各国丁腈橡胶生产工艺流程多采用冷法乳液聚合连续生产,其工艺过程与丁苯橡胶类似。主要包括原料配制、聚合、单体回收、胶乳贮存及掺混、胶乳凝聚、干燥及压块包装等工序。 ①生产时,先将一定比例的丁二烯、丙烯腈混合均匀,制成碳氢相。在乳化剂中加入氢氧化钠、焦磷酸钠、三乙醇胺、软水等制成水相,并配制引发剂等待用。 ②将碳氢相和水相按一定比例混合后送入乳化槽,在搅拌下经充分乳化后送入聚合釜。 ③在聚合釜内直接加入引发剂,进行聚合反应,反应热量由列管内液氨蒸发排出。温度控制在30℃或5℃时,转化率可维持在70%~85%。
④而后分批加入调节剂,以调节橡胶的分子量。聚合反应进行至规定转化率时,加入终止剂终止反应,并将胶浆卸入中间贮槽。 ⑤经过终止后的胶浆,送至脱气塔,经三级闪蒸脱除未反应的丁二烯,然后再借水蒸汽加热真空脱出游离的丙烯腈。 ⑥丁二烯经压缩升压后循环使用,丙烯腈经回收处理后再使用。 ⑦经脱气后的胶浆加入凝聚剂、防老剂及其它助剂后,过滤除去凝胶,用食盐水凝聚成颗粒胶,经水洗后挤压除去水分,再用干燥机干燥,然后包装即得成品橡胶。经干燥后的橡胶含水量应低于1%,成品丁腈橡胶一般每包重25千克。 合成丁腈橡胶使用的主要设备有:聚合釜、闪蒸塔、脱气塔、干燥箱、干燥机等。 2.1.2 丁腈橡胶的生产工艺优缺点 冷法(低温)乳液聚合的丁腈橡胶在加工性能上优于高温乳液聚合的丁腈橡胶。冷法乳液聚合工艺优点: 1、以水为分散介质,价廉安全; 2、聚合体系粘度低,易传热,反应温度易控制; 3、尤其适宜于直接使用乳胶的场合。 工艺缺点: 1、产品中留有乳化剂等,影响产品电性能等; 2、要得到固体产品时,乳液需经过凝聚、洗涤、脱水、干燥等工序,成本较高。
中国天然橡胶产业现状及其发展建议
1我国天然橡胶产业发展概况1.1 我国橡胶树引种与产业兴起 我国自1904年引种橡胶树以来,至今已有百 年橡胶栽培历史。据相关史料记载,最早引种当属云南干崖(今盈江)土司刀安仁1904年从新加坡引种橡胶苗到今云南省德宏傣族苗族自治州盈江县,并种植成功[1]。1906年爱国华侨何麟书在海南岛乐会县(今琼海市)崇文乡合口湾(今东太农场坡塘区18队)建立琼安垦务公司(又称琼安胶园),开创了海南生产性种植橡胶成功的先河[2]。从1907年起,陆续有来自美国、加拿大、英国、西德、新加坡、马来西亚、泰国、印度尼西亚和我国香港等地的华侨来儋州投资创建橡胶种植园[3]。除了1907年我国华侨区幕颐和何子春从马来西亚引种橡胶苗4000余株创办了著名的侨兴胶园,当时还陆续创建了天任、蔡惠、联昌、万发、文明、民安、棠阴、许成、侨南、侨相等橡胶种植园[3],儋州地区逐渐发展成为了我国的植胶中心。 从规模要求,严格准确地说,橡胶产业真正开始蓬勃发展起来是在新中国成立之后。新中国成立之初,国家急需发展国民经济建设,1950年朝鲜战争爆发,以美国为首联合一些国家对我国实行经济封锁和物资禁运,而天然橡胶属于禁运之列。为确保我国国民经济建设和国防建设的顺利开展, 1951年8月30日,中央人民政府政务院第100次 会议作出《关于扩大培植橡胶树的决定》,党和国家相继组织广大科技人员对我国华南热区植胶环境条件和生长的橡胶树资源进行全面的勘查、研究及其利用工作。60a过去了,我国植胶已形成海南、云南、广东3大基地,具有相当规模,累计生产干胶逾1000万t。为进一步发展天然橡胶产业,国务院办公厅于2007年2月下发了《关于促进我国天然橡胶产业发展的意见》,国家农业部2007年8月颁布实施了《全国天然橡胶优势区域布局规划 (2008~2015年)》,2010年国务院办公厅下发了 《关于促进我国热带作物产业发展的意见》。作为天 中国天然橡胶产业现状及其发展建议① 祁栋灵② 王秀全 张志扬 黄月球 (中国热带农业科学院橡胶研究所/国家重要热带作物工程技术研究中心 海南儋州571737) 摘 要 从我国天然橡胶产业发展概况、产业的地位和作用,以及我国橡胶科技对植胶生产的推动作用等方面对中国天然橡胶产业发展现状进行了综述,并提出了促进我国天然橡胶产业发展提升的建议。关键词巴西橡胶树;天然橡胶产业;发展现状 分类号 S794.1 Current Situation of Chinese Natural Rubber Industry and Development Suggestions QI Dongling WANG Xiuquan ZHANG Zhiyang HUANG Yueqiu (Rubber Research Institute,CATAS /SETRCKTC ,Danzhou 571737,China) Abstract This paper analyzes general situation of development in Chinese natural rubber industry,the industrial status and role of Chinese natural rubber industry,as well as establish production impetus of Chinese rubber science &technology to rubber production,and putting forward some suggestions on how to improve Chinese natural rubber industry. Keywords Brazil rubber tree (Hevea brasiliensis );natural rubber industry ;current situation of development ①收稿日期:2012-10-30;责任编辑/黄艳;编辑部E-mail:rdnk@163.com。 ②祁栋灵(1979~),男,硕士,助理研究员,从事农业科技推广与技术经济合理性分析;E-mail:donglingqi@163.com。 Vol.33,No.2 2013年2月热带农业科学 CHINESE JOURNAL OF TROPICAL AGRICULTURE 第33卷第2期 Feb .201379--
丁腈橡胶的基本性能及用途
字体大小:| | 2010-08-28 16:56 - 阅读:135 - :0 ,由丁二烯与丙烯腈共聚而制得的一种合成橡胶。是耐油(尤其是烷烃油)、耐老化性能较好的合成橡胶。丁腈橡胶中丙烯腈含量(%)有42~46、36~41、31~35、25~30、18~24 等五种。丙烯腈含量越多, 耐油性越好,但耐寒性则相应下降。它可以在120℃的空气中或在150℃的油中长期使用。此外,它还具有良好的耐水性、气密性及优良的粘结性能。广泛用于制各种耐油橡胶制品、多种耐油垫圈、垫片、套管、 软包装、软胶管、印染胶辊、电缆胶材料等,在汽车、航空、石油、复印等行业中成为必不可少的弹性材料。 丁腈橡胶基本性能 主要采用低温乳液聚合法生产,丁腈橡胶具有优良的耐油性,其耐油性仅次于聚硫橡胶和氟橡胶,并且具有的耐磨性和气密性,粘接力强。丁晴橡胶的缺点是不耐臭氧及芳香族、卤代烃、酮及酯类溶剂,不宜做 绝缘材料。丁腈橡胶耐低温性差,电性能低劣,弹性稍低。 丁腈橡胶主要用途 丁腈橡胶主要用于制作耐油制品,如耐油管、胶带、橡胶隔膜和大型油囊等,常用于制作各类耐油模压橡胶制品,如O形圈、油封、皮碗、 膜片、活门、波纹管等,也用于制作胶板和耐磨零件。
公司代理经销南帝公司的产品有:普通丁腈橡胶、特殊丁腈橡胶、丁腈胶乳、热塑性弹性体(TPV)等。其中镇江南帝主要牌号:NANCAR 1051、1052、1053、1052M30、1043N、2845、2865、2875、3345、3365、4155等。特殊丁腈橡胶有以下: ??羧化丁腈(XNBR):NANCAR 1072、1072CG、3245C 具优越耐磨性,适用于下列橡胶制品: a. 高耐磨的输送带、工业制品、纺织胶辊、及特殊鞋底等制品。 b. AB胶系接着剂及丙烯酸酯系接着剂。 c. 环氧树脂改性应用。 d. 软性电路板。 ??充油丁腈(NBR/DOP):NANCAR 1082 适用于超低硬度(40 Shore A以下) 并兼具耐油特性之橡胶制品,如:工业胶辊、工业制品等。 ??丁腈/PVC (NBR/PVC):NANCAR 1203D、1203HD、1203L D、具有良好的耐候性、耐油性,适用于下列橡胶制品: a. 耐臭氧的汽车部品(防尘套及胶管)、工业制品(胶板及杂件)、及电缆被 覆等制品。 b. 耐酒精汽油、低萃取燃料油管。 c. 耐溶剂的胶辊(工业胶辊、造纸胶辊、印刷胶辊)及纺织皮圈等制品。 d. 保温材料及运动器材等发泡制品。 ??丁腈/PVC/DOP (NBR/PVC/DOP):NANCAR 1204D 适用于超低硬度并兼具耐油耐臭氧之橡胶制品,如:印刷胶辊厂、工业制品等。 ??预交联丁腈(NBR):NANCAR 1022 具良好的尺寸安定性,特别适用于PVC改质,提高橡胶质感。 ??超低,极高丙烯腈丁腈(NBR):NANCAR 1965、4580
我国合成橡胶的发展现状
我国合成橡胶的发展现状及其展望 化工本122班朱凯玲 2012110183 摘要:简述了我国合成橡胶工业发展历程,阐述了我国大宗合成橡 (SBR、BR、NBR、EPDM等)发展历程、技术现状以及对合成橡胶工业发展趋势进行了展望。 关键词:合成橡胶;发展现状;展望 合成橡胶(SR)是化学工业中占有重要地位的三大合成材料之一,它与天然橡胶一起构成橡胶加工行业的最基本原材料,广泛用于制造轮胎、胶管胶带、胶鞋、机械配件和日用橡胶制品。其中轮胎制造是合成橡胶最大消费市场。合成橡胶已成为我国国民经济中不可缺少的材料之一。 1.合成橡胶发展历程 20世纪50年代末,随着我国采用中国科学院长春应用化学研究所开发技术的第一套乙炔法氯丁橡胶(CR),采用引进前苏联技术在兰州化学工业公司的第一套乳聚丁苯橡胶(ESBR)及丁腈橡胶(NBR)三套生产装置的建成投产,标志着我国合成橡胶工业正式步入发展阶段。60年代初,在消化吸收引进技术的基础上,完成了ESBR由热法聚合向冷法聚合技术的改造。70年代,采用国内开发的镍系顺丁橡胶(Ni-BR)技术建成投产了一批Ni-BR生产装置。进入80年代,从日本引进的两套大型(产能为8.0万t/a)冷法ESBR生产装置,分别在吉林石化公司和齐鲁石化股份公司建成投产,从而实现了ESBR大规模国产化。80年代后期至90年代,我国自行开发和建成投产了锂系SR[包括溶聚丁苯橡胶(SSBR)、苯乙烯-丁二烯-苯乙烯三元共聚物(SBS)和低顺式聚丁二烯橡胶(LCBR)]生产装置。90年代末,由意大利IP公司引进的3.0万t/a的丁基橡胶(IIR)和由日本瑞翁公司引进的1.5万t/a的NBR生产装置也相继建成投产。与此同时,各大BR生产厂分别对各自的BR装置进行了扩能改造。至此,我国已具有大规模生产SBR、BR、CR、NBR、EP(D)M、IIR六大基本胶种及热塑性弹性体SBS等合成橡胶的能力。 我国合成橡胶工业经过40余年的发展已形成比较完整的生产体系。我国已进入世界合成橡胶生产、消费大国行列,具有相当的规模和实力,而且市场需求增长速度较快,市场容量空间较大。随着我国经济的快速发展,合成橡胶工业将迎来一个新的发展时期。 2.我国合成橡胶发展现状 2.1产业化技术现状[3]
橡胶离型剂(脱模剂)知识与最新产品动向
橡胶离型剂(脱模剂)知识与最新产品动向 一、橡胶离型剂的类型分类: 1、橡胶离型剂:指用于防止橡胶产品与模具表面粘连,并能使之顺利出模而不致撕裂的一类物质。使用时将它喷或涂于模腔表面,以形成一层有效的隔离层。对离型剂的主要要求是:有一定的热稳定性和化学惰性,不腐蚀模腔表面;在模腔表面下残留分解物;不影响产品色泽,但能赋予良好的外观、无毒;易于配制,使用方便。 2、氟系离型剂:氟离型剂继承了含氟材料的特点,能够显著降低固体的表面能,使其产生难浸润和不粘着性,不易与其他物质溶合,很好的解决了成品与模具之间的粘结问题,配制成离型剂时,含氟化合物的用量极小。对热固性树脂、热塑性树脂和各种橡胶制件均适用,模制品表面光洁,二次加工性能优良,特别适合于精细电子零部件的脱模。 3、硅系离型剂:有机硅离型剂是以有机硅氧烷为原料制备而成,其优点是耐热性好,表面张力适中,易成均匀的隔离膜,脱模寿命长。缺点是脱模后制品表面有一层油状面,二次加工签必须进行表面清洗。常用的有硅油,硅橡胶,乳化硅油以及硅脂等。有机硅离型剂是目前橡塑离型剂中档市场的主流产品,在聚氨酯、橡胶、等树脂的加工中均有广泛应用。 4、蜡( 油) 系离型剂蜡油系列离型剂特点是价格低廉, 粘敷性能好, 缺点是污染模具,其主要品种有: ①工业用凡士林, 直接用作离型剂; ②石蜡, 直接用作离型剂; ③磺化植物油, 直接用作离型剂; ④印染油( 土耳其红油、太古油) , 在100 份沸水中加0.9~ 2 份印染油制成的乳液, 比肥皂水脱模效果好; ⑤聚乙二醇( 相对分子质量200~ 1 500) , 直接用于橡胶制品的脱模。 5、表面活性剂系离型剂表面活性剂离型剂特点是隔离性能好, 但对模具有污染。主要有以下几类: ①肥皂水,用肥皂配成一定量浓度的水溶液, 可作模具的润滑剂, 也可作为胶管的脱芯剂; ②油酸钠,将22份油酸与100份水混合,加热至近沸, 再把3份苛性钠慢慢加入, 并搅拌至皂化, 控制pH值为7~ 9,使用时按1:1 的水稀释,用作外胎硫化脱模时, 需在200份上述溶液中加入2份甘油; ③甘油,可直接用作离型剂或水胎润滑剂。 ④脂肪酸铝溶液,将脂肪铝溶于二氯乙烷中配成1%溶液,适用于聚氨酯制品, 涂1次, 可重复用多次, 脱模效果好; ⑤硬脂酸锌是透明塑料制品的离型剂。 6、内加型离型剂 ①硬脂酸锌、硬脂酸铵、石蜡等宜作内加型离型剂; ②模得丽935P 离型剂, 直接加入胶料中使用。 善贞实业(上海)有限公司在橡胶离型剂技术上研究多年,专业生产橡胶内离型剂,橡胶内离型剂:金属皂盐、脂肪酸酯类等环保型产品,具有很好的平滑、分散、隔离脱模性、耐高低温性能,不转移至成品上等优点。 概述:D 985S 高效离型剂及内分散作用,广泛适用于天然橡胶(NR)、异戊橡胶(IR)、丁苯橡胶(SBR)、顺丁橡胶(BR)、丁腈橡胶(NBR)、三元乙丙橡胶(EPDM)、氯磺化聚乙烯(CSM)、氟橡胶(FKM)、丁基橡胶(IIR)以及再生胶,。 用量推荐: 一般生胶:按生胶量添加1.5~2.5 份。 卤化橡胶(氯、溴、氟):按生胶量添加2~4 份。 使用方法: 高效内离型剂 D 985S 在混炼时和小料同时加入。 高效内离型剂 D 985S 用同时与高效分散剂 D 586S 配合使用,能体现更优的的加工性和离模效果。 适合模压、射出、挤出工艺中,建议高效内离型剂 D 985S 使量为1.5~2.5 份,高效内离型剂 D 985S 除离模作用之外还具有加工分散剂功能,可以大幅降低压出螺杆的扭矩,使制品批次指标稳定无波动,可得到更高的产品质量稳定性
天然橡胶的发展历史
天然橡胶的发展历史 1493年,伟大的西班牙探险家哥伦布率队初次踏上南美大陆。在这里,西班牙人瞧到印第安人小孩与青年在玩一种游戏,唱着歌互相抛掷一种小球,这种小球落地后能反弹得很高,如捏在手里则会感到有粘性,并有一股烟熏味。西班牙人还瞧到,印第安人把一些白色浓稠的液体涂在衣服上,雨天穿这种衣服不透雨;还把这种白色浓稠的液体涂抹在脚上,雨天水也不会弄湿脚。由此,西班牙人初步了解到了橡胶的弹性与防水性,但并没有真正了解到橡胶的来源。 1693年,法国科学家拉康达到南美又瞧到土著人玩这种小球,科学家与军人思维与眼光就是不同的,追根寻底调查这种小球,才得知这种小球就是砍一种印地安人称为"橡胶"的树而流出的浓稠液体缺制造的。 1736年,法国科学家康达敏从秘鲁带回有关橡胶树的详细资料,出版了《南美洲内地旅行记略》,书中详述了橡胶树的产地、采集乳胶的方法与橡胶的利用情况,引起了人们的重视。 1763年,法国人麦加发明了能够软化橡胶的溶剂。 1770年,英国化学家普立斯特勒发现橡胶能擦去铅笔字迹。 1823年,英人马金托什,像印第安人一样把白色浓稠的橡胶液体涂抹在布上,制成防雨布,并缝制了"马金托什"防水斗蓬,这也可能就就是世界上最早的雨衣吧。 1852年,美国化学家古特义在做试验时,无意之中把盛橡胶与硫磺的罐子丢在炉火上,橡胶与硫磺受热后流淌在一起,形成了块状胶皮,从而发明了橡胶硫化法。古特义的这一偶然行为,就是橡胶制造业的一项重大发明,扫除了橡胶应用上的一大障碍,使橡胶从此成为了一种正式的工业原料,从而也使与橡胶相关的许多行业蓬勃发展成为了可能。随后,古特义又用硫化橡胶制成了世界上的第一双橡胶防水鞋。 1876年,英国人魏克汉九死一生,从亚马逊河热带丛林中采集7万粒橡胶种子,送到英国伦敦皇家邱植物园培育,然后将橡胶苗运往新加坡、斯里兰卡、
丁腈橡胶的基本性能及用途
丁腈橡胶的基本性能及 用途 Company Document number:WTUT-WT88Y-W8BBGB-BWYTT-19998
字体大小: | | 2010-08-28 16:56 - 阅读:135 - :0 ,由丁二烯与丙烯腈共聚而制得的一种合成橡胶。是耐油(尤其是烷烃油)、耐老化性能较好的合成橡胶。丁腈橡胶中丙烯腈含量(%)有42~46、36~41、31~35、25~30、18~24 等五种。丙烯腈含量越多,耐油性越好,但耐寒性则相应下降。它可以在120℃的空气中或在150℃的油中长期使用。此外,它还具有良好的耐水性、气密性及优良的粘结性能。广泛用于制各种耐油橡胶制品、多种耐油垫圈、垫片、套管、软包装、软胶管、印染胶辊、电缆胶材料等,在汽车、航空、石油、复印等行业中成为必不可少的弹性材料。 丁腈橡胶基本性能 主要采用低温乳液聚合法生产,丁腈橡胶具有优良的耐油性,其耐油性仅次于聚硫橡胶和氟橡胶,并且具有的耐磨性和气密性,粘接力强。丁晴橡胶的缺点是不耐臭氧及芳香族、卤代烃、酮及酯类溶剂,不宜做绝缘材料。丁腈橡胶耐低温性差,电性能低劣,弹性稍低。 丁腈橡胶主要用途 丁腈橡胶主要用于制作耐油制品,如耐油管、胶带、橡胶隔膜和大型油囊等,常用于制作各类耐油模压橡胶制品,如O形圈、油封、皮碗、膜片、活门、波纹管等,也用于制作胶板和耐磨零件。
公司代理经销南帝公司的产品有:普通丁腈橡胶、特殊丁腈橡胶、丁腈胶乳、热塑性弹性体(TPV)等。其中镇江南帝主要牌号:NANCAR 1051、1052、1053、1052M30、1043N、2845、2865、2875、3345、3365、4155等。特殊丁腈橡胶有以下: 羧化丁腈(XNBR):NANCAR 1072、1072CG、3245C 具优越耐磨性,适用于下列橡胶制品: a. 高耐磨的输送带、工业制品、纺织胶辊、及特殊鞋底等制品。 b. AB胶系接着剂及丙烯酸酯系接着剂。 c. 环氧树脂改性应用。 d. 软性电路板。 充油丁腈(NBR/DOP):NANCAR 1082 适用于超低硬度(40 Shore A以下) 并兼具耐油特性之橡胶制品,如:工业胶辊、工业制品等。 丁腈/PVC (NBR/PVC):NANCAR 1203D、1203HD、1203L D、具有良好的耐候性、耐油性,适用于下列橡胶制品: a. 耐臭氧的汽车部品(防尘套及胶管)、工业制品(胶板及杂件)、及电缆被 覆等制品。 b. 耐酒精汽油、低萃取燃料油管。 c. 耐溶剂的胶辊(工业胶辊、造纸胶辊、印刷胶辊)及纺织皮圈等制品。 d. 保温材料及运动器材等发泡制品。 丁腈/PVC/DOP (NBR/PVC/DOP):NANCAR 1204D 适用于超低硬度并兼具耐油耐臭氧之橡胶制品,如:印刷胶辊厂、工业制品等。 预交联丁腈(NBR): NANCAR 1022 具良好的尺寸安定性,特别适用于PVC改质,提高橡胶质感。 超低,极高丙烯腈丁腈(NBR):NANCAR 1965、4580
常用橡胶性能一览表
常用橡胶性能一览表
由于具有优异的耐老化性能耐冲击性也较好,所以常用做胎侧。EPDM三元乙丙胶三元乙丙橡胶是一种在乙烯和丙烯共聚物中引入了第三单体的高分子聚合物,产品性能及优点:超高分子量,高乙烯含量,可高度填充填充剂和油,易碎的性能缩短了混炼的时间. 分子结构和特性 三元乙丙是乙烯、丙烯和非共轭二烯烃的三元共聚物。二烯烃具有特殊的结构,只有两键之一的才能共聚,不饱和的双键主要是作为交链处。另一个不饱和的不会成为聚合物主链,只会成为边侧链。三元乙丙的主要聚合物链是完全饱和的。这个特性使得三元乙丙可以抵抗热,光,氧气,尤其是臭氧。三元乙丙本质上是无极性的,对极性溶液和化学物具有抗性,吸水率低,具有良好的绝缘特性。
在三元乙丙生产过程中,通过改变三单体的数量,乙烯丙烯比,分子量及其分布以及硫化的方法可以调整其特性。 热塑性弹性体(TPE) 高刚性耐高温且保有低温的弯曲性,优异的耐化学品性,应用于管材、静音齿轮、电线被覆、发卷、自动收缩管线. TPE热塑性弹性体特性: 1、材料有半透、高透明、白色、黑色供选择。 2、已通过ROHS、PAHs、FDA测试,等级测试。 3、材料环保无卤无毒无味,不含塑胶软化剂、磷苯二甲酸盐、重金属等化合物。 4、良好的减震性和防滑耐磨。 5、良好的抗紫外线及耐化学药品性。 6、广阔的硬度范围选择(邵氏0度-110度)。可根据需求任意调整。 7、在—60度至135度的长期使用温度 8、压缩变形及永久变形小 9、卓越的抗动态疲劳性能 10、极优的耐臭氧及耐候性能 11、亮面、雾面均可,光滑的外观和舒适的橡胶柔软质感。 12、材料不含水分,无须干燥可直接使用,节约能源。 13、易于加工,着色。水口料即边角料可百分百回收再利用,降低产品,且不影响产品物性。 14、它可以通过二次注塑成型,与PP、PE、PS、ABS、PC、PA等基体材料包覆粘合,也可单独成形。替代软质PVC部分硅橡胶。 TPE/TPR 之应用领 域运动器材: 手把类(高尔夫球、各种球拍、脚踏车、滑雪器材、滑水器材等), 潜水器材(蛙鞋、蛙镜、呼吸管、手电筒等)、刹车块、运动护垫。日常用品:
2014年橡胶行业分析报告
2014年橡胶行业分析 报告 2014年6月
目录 一、橡胶产业发展回顾 (4) 1、产业简介 (4) 2、规模式发展成为过去十年主旋律 (5) 3、产业进入由“大”变“强”新阶段 (6) 4、原材料低位利好下游制造,短期龙头毛利有望继续上升 (8) (1)全球天然橡胶呈现供大于求,原材料低位盘整局面恐难改变 (8) (2)主要合成橡胶品种产能过剩,毛利空间受制于天然橡胶与油价双重压力 (9) 二、轮胎与橡胶制品:进口替代、产业升级 (10) 1、轮胎:车用消费品迎来黄金发展新阶段 (10) (1)汽车消费观“平民化”将促使车用消费品迎来国产化浪潮 (10) (2)国内轿车替换胎市场将成为轮胎国产化的突破口 (12) (3)并购重组、集中度提升是大势所趋 (14) (4)具有品牌、渠道、技术能力的龙头公司将会逆势崛起 (16) 2、橡胶制品:高端制造带来产业升级 (18) (1)橡胶制品行业竞争格局稳定 (18) (2)产品升级是行业发展的核心驱动力 (19) (3)产业链一体化打开成长空间 (21) 三、配套行业:需求稳定,格局优化 (21) 1、需求增长:全球需求稳定增长,中国仍是最大驱动力 (21) (1)全球橡胶及助剂消费量保持稳定增长 (21) (2)中国需求依然是最大驱动力 (22) 2、橡胶助剂:环保风暴促行业健康发展 (24) (1)橡胶助剂的产业演变:一场进口替代的盛宴 (24) (2)环保风暴促进行业快速健康发展 (27) 3、炭黑:集中度提升格局优化,行业进入周期反转 (29) (1)我国炭黑工业占据全球重要地位 (29) (2)行业集中度提升是大势所趋 (29)
丁腈橡胶的详细分析
3.9 丁腈橡胶与改性丁腈橡胶 3.9.1 丁腈橡胶概述 丁二烯-丙烯腈橡胶(acrylonitrile-butadiene rubber)是丁二烯与丙烯腈两种单体经乳液聚合而得的共聚物,简称丁腈橡胶(NBR)。NBR于1930年由德国Konrad和Thchunkur研制成功,1937年由德国I.G. Farben公司首先实现了工业化生产。 NBR的丙烯腈含量为15%~53%,分为低腈、中腈、中高腈、高腈、极高腈五个等级。在市售商品中,丙烯腈含量在31%~37%的NBR占总NBR的40%,尤其是丙烯腈含量为33%的NBR居多数[1]。 NBR的基本特点包括[2]: (1)NBR是非结晶性无定型聚合物,生胶强度较低,须加入补强剂才具有使用价值。丙烯腈 质量分数较高的NBR有助于提高硫化胶的强度和耐磨性,但会使弹性下降。 (2)耐油是NBR最突出的特点,NBR含有极性腈基,对非极性或弱极性的矿物油、动植物油、 液体燃料和溶剂等化学物质有良好的抗耐性。丙烯腈质量分数愈高,耐油性愈好。 (3)耐热性优于NR、SBR和CR,可在120℃的热空气中长期使用。 (4)耐寒性、耐低温性较差,丙烯腈质量分数愈高,耐寒性愈差。 (5)气密性较好,在通用橡胶中仅次于IIR。 (6)耐热氧老化、日光老化性能优于NR。 (7)NBR的介电性能较差,属半导体橡胶。 NBR具有二烯类橡胶的通性,可采用与NR、SBR等通用橡胶相同的方法加工成型,常用的硫化体系为硫磺、过氧化物和树脂硫化体系等。 NBR因其优异的耐油性能,广泛用于制备燃料胶管、耐油胶管、油封、动态和静态用密封件、橡胶隔膜、印刷胶辊、胶板、橡胶制动片、胶粘剂、胶带、安全鞋、贮槽衬里等各种橡胶制品,涉及汽车、航空航天、石油开采、石油化工、纺织、电线电缆、印刷和食品包装等诸多领域[1]。 NBR分子主链上存在不饱和双键,影响了它的耐热、耐天侯等化学稳定性。为了使NBR 性能更符合不同用途制品的要求,国内外相继开发出具有特殊性能的NBR新品种,如氢化丁腈橡胶、羧基丁腈橡胶、粉末丁腈橡胶、液体丁腈橡胶等,以及与不同橡胶共混、橡塑并用等来改善丁腈橡胶的综合性能,使得NBR产品系列化、功能化、高档化。 3.9.2 氢化丁腈橡胶 氢化丁腈橡胶(hydrogenated acrylonitrile-butadiene rubber 简称HNBR)是通过氢化丁腈橡胶主链上所含的不饱和双键而制得,又称为高饱和度丁腈橡胶。由于HNBR具有合理的分子结构,因此不仅继承了NBR的耐油、耐磨等性能,而且还具有更优异的耐热、耐氧化、耐臭氧、耐化学品性能,可以与氟橡胶相媲美,在许多方面可取代氟橡胶、CR、NBR等特种橡胶。 从1984年开始,德国Bayer、日本Zeon、加拿大Polysar等公司相继投产HNBR,目前各厂家均有多种牌号的产品。但是由于工业生产HNBR的方法仍存在诸如流程长、成本高等缺