第七章 固定轮廓铣【Fixed Contour】(二)
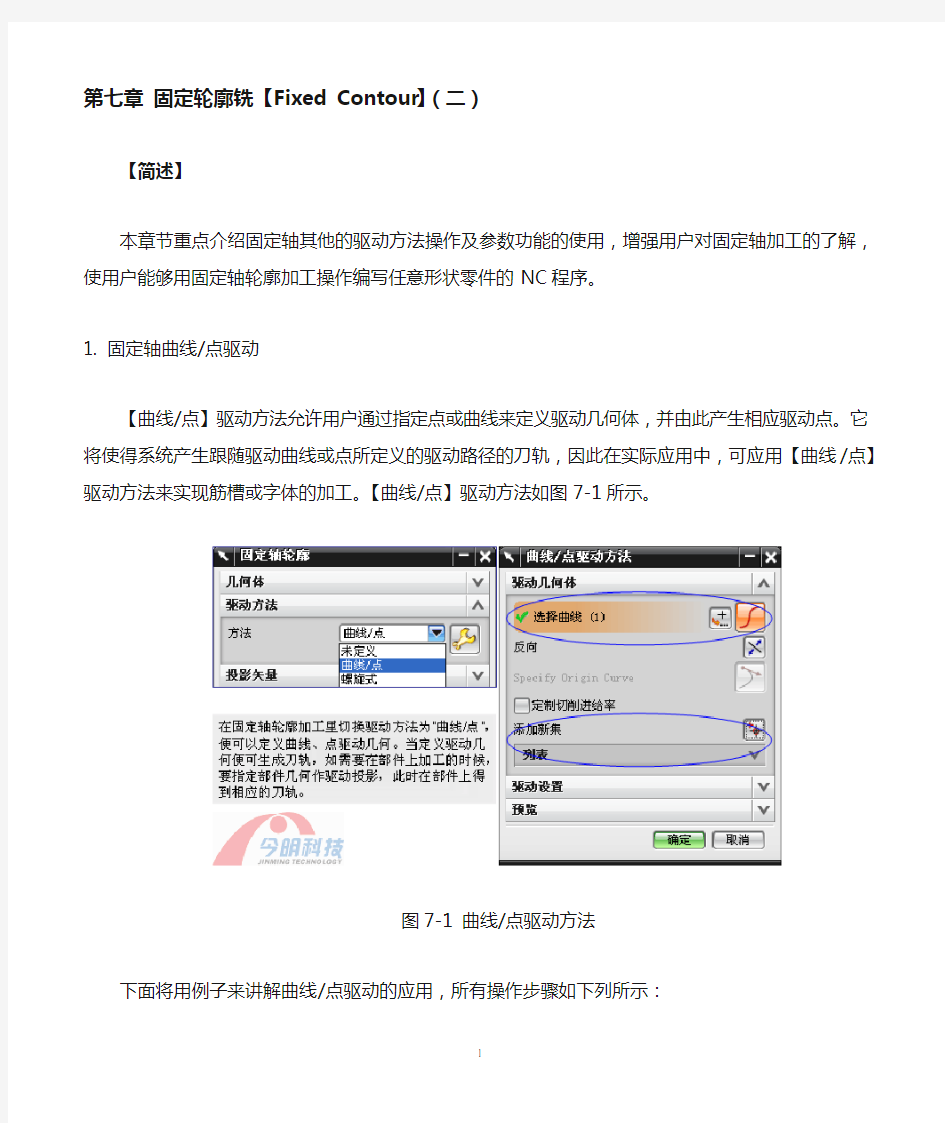

第七章固定轮廓铣【Fixed Contour】(二)
【简述】
本章节重点介绍固定轴其他的驱动方法操作及参数功能的使用,增强用户对固定轴加工的了解,使用户能够用固定轴轮廓加工操作编写任意形状零件的NC程序。
1. 固定轴曲线/点驱动
【曲线/点】驱动方法允许用户通过指定点或曲线来定义驱动几何体,并由此产生相应驱动点。它将使得系统产生跟随驱动曲线或点所定义的驱动路径的刀轨,因此在实际应用中,可应用【曲线/点】驱动方法来实现筋槽或字体的加工。【曲线/点】驱动方法如图7-1所示。
图7-1 曲线/点驱动方法
下面将用例子来讲解曲线/点驱动的应用,所有操作步骤如下列所示:
⑴.打开文件(curve point_drive.prt),并进入到加工模块,由于此模型定义过加工参数,所以不需要
初始化。如图7-2所示。
图7-2 curve point_drive.prt
⑵.创建固定轴曲线/点驱动操作,操作的步骤如流程图7-3所示。
图7-3 曲线/点驱动操作
⑶.定义“曲线/点”驱动几何。在【固定轴轮廓】操作对话框里,将驱动方法设置为〖曲线/点〗,点
击编辑图标,进入【曲线/点驱动方法】对话框,在操作界面里选取曲线作为驱动几何,确定
完成后生成刀轨。多段曲线选择的区别,如图7-4所示。
图7-4驱动曲线选择的区别
⑷.按模型所示的曲线作为驱动几何加工,投影到部件几何体表面所得的刀轨,如图7-5所示。其他
相同的参数在此不再重述。
图7-5 曲线/点驱动刀轨
2. 固定轴螺旋驱动
⑴.螺旋驱动使得系统产生从指定的中心位置向外螺旋的驱动点,螺旋驱动方法如图7-6所示。驱动
点位于垂直于投影矢量方向的平面内,然后按投影矢量方向投影到加工面上,从而产生螺旋的刀轨,如图7-7所示。
图7-6 螺旋驱动
图7-7 螺旋驱动方法的刀轨
⑵.在螺旋式驱动方法中,系统不是通过指定驱动几何体来产生驱动点,而是通过指定中心螺旋中心
位置、最大螺旋半径和步进距离来产生螺旋式的驱动点。由于不需要改变切削方向,并且始终保持均匀点距而由中心点向外光顺切削,故螺旋驱动方法更加适用于高速加工。
3. 固定轴边界驱动
【边界驱动方法】允许用户通过指定边界和环定义切削区域;将已定义的切削区域所产生的驱动点按照指定的投影矢量的方向投影到部件表面,这样就可以创建出刀轨。【边界驱动方法】对话框如图7-8所示。
图7-8 边界驱动方法对话框
在【边界驱动方法】对话框中,单击“指定驱动几何体”在边的选择或编辑驱动几何体图标,将
弹出【边界几何体】对话框,它允许使用曲线/边、边界、面和点四种模式来指定边界。由于【边界几何体】的内容在前面【平面铣】操作里介绍过,在此将不再重述。驱动几何体的边界既可以超过部件几何体的尺寸,也可以限制在部件几何体内,也可以与部件几何体的外部边缘一致,如图7-9所示。
图7-9 驱动几何的边界
当【创建边界】或【编辑边界】中,可以定义刀具在边界位置,包括有:对中、相切和接触三种方法。使用不同的位置,所加工的区域范围也不一样,如图7-10所示。
图7-10 边界驱动刀具的位置
注:如果刀具位置为对中,并且当驱动几何体的边界与部件几何体的尺寸之差大于刀具半径时,将会在部件几何体的外部边缘出现滚动的刀轨,通常这不是预期的结果。
4. 固定轴曲面驱动
曲面驱动方法操作对话框如图7-11所示。【曲面驱动方法】允许用户指定类似风格排列的曲面来定义驱动几何体,并由此产生一系列呈矩阵分布的驱动点。
图7-11 曲面驱动方法对话框
在【曲面驱动方法】对话框中,驱动几何体参数区,单击“指定驱动几何体”的“选择或编辑驱动几何体”图标,并弹出【驱动几何体】对话框,它允许依顺序地指定有规律排列的曲面定义驱动几何体,
如图7-12所示。使用例子(surface_drive_1.prt)文件,定义模型顶部曲面为驱动几何体,并指定切削方向与材料侧方向。如图7-13所示。
图7-12 曲面驱动几何的选择
图7-13 surface_drive_1.prt
5. 固定轴流线驱动
【流线驱动方法】对话框如图7-14所示。流线驱动方法允许用户指定曲线或边缘(近似创建风格曲面)建立隐含的曲面来定义驱动几何体,并由此产生按曲面UV方向分布的驱动点。流线驱动不需要创建驱动面,在加工复杂的具有非规则排列的曲面时,更加灵活,并且加工精度也更高。
图7-14 流线驱动方法
在【流线驱动方法】对话框中,有两种选择方法分别为:自动和指定。〖自动〗选择是NX根据主操作对话框中指定的切削区域的边界创建流动曲线集和交叉曲线集;〖指定〗选择是用户手工选择流动曲线和交叉曲线或自动编辑创建的流动/交叉曲线。〖流曲线〗选项卡里主要是定义驱动曲面的长边缘;类型有
选择曲线()、反向()、指定原始曲线()和添加新集()四个内容。〖交叉曲线〗定义与流曲线相交的刀轨模式行为。〖指定切削方向〗选择合适的矢量定义起始点和加工方向,如图7-15所示。〖修剪与延伸〗分为:起始切削%、结束切削%、起始步长%、结束步长%,作用如图7-16所示。
图7-15 流线驱动指定切削方向
图7-16 流线驱动的修剪与延伸
6. 固定轴径向切削驱动
【径向切削驱动方法】对话框如图7-17所示。径向切削允许用户指定任意曲线和边缘定义驱动几何体,由此产生垂直于驱动边界的、具有一定宽度的带状驱动点。常用于清除工件底部的残留材料。定义“驱动几何体”边界时,可以指定曲线或边缘作为驱动几何,可以是开放式的边界,也可以是封闭式的,如图7-18所示。
图7-17 径向切削驱动
图7-18 径向切削驱动方法
径向切削驱动方法所加工的区域范围是由材料侧的条带与另一侧的条带所限定的;区域范围是“材料侧”和“另一侧”偏置值的总和。“材料侧”是从按照边界指示符的方向看过去的边界右手侧,如图7-19所示。“另一侧”是左手侧。“材料侧”和“另一侧”的总和不能等于零。
图7-19 材料侧与另一侧
7. 固定轴清根驱动
【清根驱动方法】对话框如图7-20所示。清根驱动是使得系统产生沿着部件几何体的凹形状分布的刀轨。清根驱动常用于加工模型底部的凹角。系统基于双相切接触点原理和部件几何体曲面间的凹角来确定在何处将会产生清根刀轨。也就是说,要产生清根刀轨,首先部件几何体曲面必须形成一个内凹角,如图7-21所示,形成内凹角的曲面不必是相邻的两个曲面,然后刀具必须同量在两个不同点处分别相切接触部件几何体曲面,图7-22所示列出了几种可能的情况。
图7-20 清根驱动方法
图7-21 部件几何体形成的凹角
图7-22 双相切接触点
在【清根驱动方法】对话框里的“驱动设置”选项卡,它允许用户设置清根类型、切削类型、步距和顺序来定义清根的各种参数。设置不同的清根类型,系统也会提供相应的参数选项。清根类型分为:单刀路、多个偏置和参考刀具偏置三种类型。
1.“单刀路”将沿着凹角和凹谷产生一个切削刀路,如图7-23所示.单刀路选项不会激活“清根”
对话框中的任何附加刀具输出参数选项。
图7-23 清根单刀路
2.“多个偏置”允许用户指定偏置数和偏置之间的“步距”,这样便可在中心清根的任一侧产生多
个切削刀路。此选项可激活如下所述的“切削类型”、“步距”、“序列”和“偏置数”选项。如图7-24
所示。
图7-24 清根多个偏置
当你设置类型为“多个偏置”时,相应会出现“偏置数”参数选项。偏置数使您能够指定要在中心“清根”每一侧生成的刀路的数目。例如,如图7-25中所示的“偏置数”等于2。默认值是零,该值导致系统只能计算并输出中心清根。只有在指定了“多个偏置”的情况下,“偏置数”才是可用的。
图7-25 清根偏置的刀轨
3.“参考刀具偏置”允许用户指定一个参考刀具直径从而定义要加工的区域的整个宽度,还可以
指定一个“步距”从而定义内部刀路,这样便可在中心清根的任一侧产生多个切削刀路。此选项
有助于在使用大(参考)刀具对区域进行粗加工后清理加工。此选项可激活对话框中的“切削类
型”、“步距”、“序列”、“参考刀具直径”以及“重叠距离”字段。“参考刀具直径”允许用户根据粗
加工球面刀的直径来指定精加工切削区域的宽度。参考刀具通常是用来先对区域进行粗加工的
刀具。系统根据指定的“参考刀具直径”计算双切点,然后用这些点来定义精加工操作的切削区
域。您必须从键盘输入一个大于当前使用的刀具直径的直径值。例如,如果在先前的操作中使
用 1 英寸的球头铣刀粗加工某一区域,而在当前的操作中,您希望用0.25 英寸的球头铣刀对
同一区域进行精加工,则应该从键盘输入一个 1 英寸的“参考刀具直径”。“重叠距离”使用
户能够沿着相切曲面延伸由“参考刀具直径”定义的区域宽度。只有在指定了“参考刀具偏置”的
情况下,“重叠距离”才是可用的。如图7-26所示。
图7-26 清根参考刀具直径
注:有在指定了“参考刀具偏置”的情况下,“参考刀具直径”才是可用的。
在【清根驱动方法】对话框中的“输出”选项卡,将切削顺序设置为自动时,则系统将自动确定各个凹角的清要切削顺序。如果将切削顺序设置为用户定义,当产生刀轨时,系统将弹出如图7-27所示的【手工装配】对话框,它允许用户根据实际加工意图,对各个凹角的清根刀路进行重新排序、反向、移除、光顺和剪切等操作。
图7-27 清根“手工装配”〖小结〗:本节重点介绍固定轴轮廓铣中相关了驱动方法。
〖附练习文件〗curve point_drive.prt surface_drive_1.prt
课题4-1 外轮廓零件加工用到的指令一 (基本指令)
数铣中级实习教案4
复习导入新授课题 活动探究相关工艺复习:对本次课题必须用到的知识进行简单的复习并提问: ①怎样建立工件坐标系 ②对刀的目的及意义 ③手动加工的基本方法 导入:建立好工件坐标系后如何进行自动加工,导入新课题并提出任务。 轮廓的自动加工 出示任务: FANUC 0i 系统编程基础指令 一、加工程序格式 1、加工程序号 加工程序号为O和最多4位数字组成,如O××××,其中××××为0000~9999中的某数。如:O1234。 2、程序段 常见格式为: 3、程序结束符“;” 二、FANUC 0i系统常用M代码
四、基本编程指令 1、G00 快速定位X Y Z G01 直线插补X Y Z F (mm/min) GO2 顺圆弧X Y R G03 逆圆弧X Y R F (mm/min) G41左刀补:从加工方向望过去,刀具在工件的左侧称之为左刀补。 G42左刀补:从加工方向望过去,刀具在工件的右侧称之为右刀补。 2、刀具补偿功能 (1)刀具补偿功能在数控编程过程中,为了编程方便,通常将数控刀具假想成一个点。在编程时,一般不考虑刀具的长度与半径,而只考虑刀位点与编程轨迹重合。但在实际加工过程中,由于刀具半径与刀具长度各不相同,在加工中势必造成很大的加工误差。因此,实际加工时必须通过刀具补偿指令,使数控机床根据实际使用的刀具尺寸自动调整各坐标轴的移动量,确保实际加工轮廓和编程轨迹完全一致。数控机床的这种根据实际刀具尺寸,自动改变坐标轴位置,使实际加工轮廓和编程轨迹完全一致的功能,称为刀具补偿功能。 数控铣床的刀具补偿功能分为刀具半径补偿功能和刀具长度补偿功能。 (2)刀位点刀位点是指加工和编制程序时,用于表示刀具特征的点,如图2-26所示,也是对刀和加工的基准点。车刀与镗刀的刀位点,通常是指刀具的刀尖;钻头的刀位点通常指 钻尖;立铣刀、端面铣刀的刀位点指刀具底面的中心;而球头铣刀的刀位点指球头中心。 如图数控刀具的刀位点
第4讲 CAXA数控车零件内轮廓和两头加工的CAM方法
CAXA数控车零件内轮廓和两头加工的CAM方法 --项目四传动轴的完整加工 项目名称:传动轴的完整加工周次:4 [教学时数]2学时(4课时)[教学方式]课堂操作讲授+学生实践[教学目的及要求] 理论目标:(1)学会分析两头加工的工艺过程。 (2)掌握“两头”不同坐标系的G54转化方法。 (3)掌握程序连接的方法。 (4)掌握不同机床仿真软件的区别。 技能目标:(1)掌握VNUC仿真软件的机床操作方法。 (2)掌握主子程序的设置方法。 (3)掌握将CAM程序应用到实际机床的方法。 [重点及难点] (1)两头加工的CAM图纸“分开”做法。 (2)内轮廓加工的绘制与加工。 (3)CAXA的打孔工艺在仿真和真实机床上都无法实现的! [教学内容:顺序+时间分配] 一、具体讲授所含章节 4.1 两头加工的方法---------------------------------(约50分钟) (1)什么样的零件必须两头加工?-过于复杂的成型面 (2)两头加工的图纸绘制 4.2 中心孔的画法和程序生成--------------------------------(约20分钟)4.3 内轮廓的画法和程序生成--------------------------------(约30分钟)4.4 内沟槽的画法和程序生成--------------------------------(约20分钟)4.5 内螺纹的画法和程序生成 -------------------------------(约20分钟)
4.6 自主练习数控车习题库--------------------------------(约60分钟) 二、重点讲授内容 (一)项目要求:。 项目1-2,使用CAXA数控车2008和VNUC软件,完成图1-2所示“传动轴”的造型,并将其在仿真机床上加工出来。 (二)项目实施: (1)各部分加工的CAM图纸需要区别、改动绘制。 (2)两头加工时,两段程序不要做成一个程序。 (3)仿真分段加工时,也要考虑装夹位置分段加工。 (4)VNUC和宇龙仿真软件都无法实现程序自动钻孔,需要手动控制孔的深度。(5)为了防止大家互相复制作业,每个人的加工工艺参数不能相同:每位同学取自己学号的后两位设为A;粗加工的切削量为0.1*A,主轴转速为500*A,精加工加工余量为0.02*A,切削量为0.01*A,主轴转速为1000*A。以此生成各自的加工程序。 (三)项目解决: (1)选择两头加工的分界位置,绘制左右加工的两组CAD图形。
第七章固定轮廓铣【FixedContour】(二).
第七章固定轮廓铣【Fixed Contour】(二) 【简述】 本章节重点介绍固定轴其他的驱动方法操作及参数功能的使用,增强用户对固定轴加工的了解,使用户能够用固定轴轮廓加工操作编写任意形状零件的NC程序。 1. 固定轴曲线/点驱动 【曲线/点】驱动方法允许用户通过指定点或曲线来定义驱动几何体,并由此产生相应驱动点。它将使得系统产生跟随驱动曲线或点所定义的驱动路径的刀轨,因此在实际应用中,可应用【曲线/点】驱动方法来实现筋槽或字体的加工。【曲线/点】驱动方法如图7-1所示。 图7-1 曲线/点驱动方法 下面将用例子来讲解曲线/点驱动的应用,所有操作步骤如下列所示: ⑴.打开文件(curve point_drive.prt),并进入到加工模块,由于此模型定义过加工参数,所以不需要 初始化。如图7-2所示。
图7-2 curve point_drive.prt ⑵.创建固定轴曲线/点驱动操作,操作的步骤如流程图7-3所示。 图7-3 曲线/点驱动操作 ⑶.定义“曲线/点”驱动几何。在【固定轴轮廓】操作对话框里,将驱动方法设置为〖曲线/点〗,点 击编辑图标,进入【曲线/点驱动方法】对话框,在操作界面里选取曲线作为驱动几何,确定
完成后生成刀轨。多段曲线选择的区别,如图7-4所示。 图7-4驱动曲线选择的区别 ⑷.按模型所示的曲线作为驱动几何加工,投影到部件几何体表面所得的刀轨,如图7-5所示。其他 相同的参数在此不再重述。
图7-5 曲线/点驱动刀轨 2. 固定轴螺旋驱动 ⑴.螺旋驱动使得系统产生从指定的中心位置向外螺旋的驱动点,螺旋驱动方法如图7-6所示。驱动 点位于垂直于投影矢量方向的平面内,然后按投影矢量方向投影到加工面上,从而产生螺旋的刀轨,如图7-7所示。 图7-6 螺旋驱动
固定轮廓铣
固定轮廓铣【Fixed Contour】 【简述】本章节重点讲述固定轴铣区域铣削驱动操作的参数功能,掌握固定轴加工的原理,对于复杂的曲面加工奠定基础;让学者往能够使用固定轴轮廓加工操作编写任意工件的程序。在固定轴轮廓加工中,先由驱动几何体产生驱动点,并按投影方向投影到部件几何体上,得到投影点,刀具在该点处与部件几何体接触点,然后系统根据接触点位置的表面曲率半径、刀具半径等因素,计算得到刀具定位点,如图6-1所示。最后后,当刀具在部件几何体表面从一个接触点移动到下一个接触点,如此重复,就形成了刀轨,这就是固定轴铣刀轨产生的原理。固定轴区域铣削适用于加工平坦的曲面操作,常用于复杂曲面的半精加工与精加工。 图6-1 固定轴加工的刀轨驱动原理 固定轴轮廓区域功能选项的介绍 在插入工具条里,点击创建操作图标,并进入到【创建操作】对话框,设置〖类型〗为“mill_contour”,在操作子类型里选择【轮廓区域】操作图标,点击【确定】便可创建【轮廓区域】操作,如图6-2所示。下面针对固定轴轮廓区域操作,还讲述在固定轴轮廓铣里专有的参数选项。
图6-2 固定轴轮廓区域操作 驱动方法 在固定轴轮廓铣有多种驱动方法,应用于不同类型的加工,驱动如:曲线/点、螺旋式、边界、区域铣削、曲面、流线、刀轨、径向切削、清根和文本等10种驱动方法。在本章编写中,主要讲解“区域铣削”、“曲线/点”与“清根”驱动,其他驱动作为一般的介绍。各驱动如图6-3所示。每个驱动在创建操作的时候,操作子类型里也有相应驱动选项。 图6-3 固定轴驱动方法 此操作在创建的时候选项了操作子类型为“区域铣削”,固操作里驱动方法所显示的也是“区域铣削”驱动。每种驱动都有不同的参数选项,如需要编辑驱动参数的时候,可以点击驱动方法旁边的编辑图标。相对“区域铣削”驱动的参数
第六章 固定轮廓铣【Fixed Contour】(一)
第六章固定轮廓铣【Fixed Contour】(一) 【简述】 本章节重点讲述固定轴铣区域铣削驱动操作的参数功能,掌握固定轴加工的原理,对于复杂的曲面加工奠定基础;让学者往能够使用固定轴轮廓加工操作编写任意工件的程序。在固定轴轮廓加工中,先由驱动几何体产生驱动点,并按投影方向投影到部件几何体上,得到投影点,刀具在该点处与部件几何体接触点,然后系统根据接触点位置的表面曲率半径、刀具半径等因素,计算得到刀具定位点,如图6-1所示。最后后,当刀具在部件几何体表面从一个接触点移动到下一个接触点,如此重复,就形成了刀轨,这就是固定轴铣刀轨产生的原理。固定轴区域铣削适用于加工平坦的曲面操作,常用于复杂曲面的半精加工与精加工。 图6-1 固定轴加工的刀轨驱动原理 一. 固定轴轮廓区域功能选项的介绍 在插入工具条里,点击创建操作图标,并进入到【创建操作】对话框,设置〖类型〗为“mill_contour”, 在操作子类型里选择【轮廓区域】操作图标,点击【确定】便可创建【轮廓区域】操作,如图6-2所示。下面针对固定轴轮廓区域操作,还讲述在固定轴轮廓铣里专有的参数选项。
图6-2 固定轴轮廓区域操作 1.驱动方法 在固定轴轮廓铣有多种驱动方法,应用于不同类型的加工,驱动如:曲线/点、螺旋式、边界、区域铣削、曲面、流线、刀轨、径向切削、清根和文本等10种驱动方法。在本章编写中,主要讲解“区域铣削”、“曲线/点”与“清根”驱动,其他驱动作为一般的介绍。各驱动如图6-3所示。每个驱动在创建操作的时候,操作子类型里也有相应驱动选项。 图6-3 固定轴驱动方法 此操作在创建的时候选项了操作子类型为“区域铣削”,固操作里驱动方法所显示的也是“区域铣削”驱动。每种驱动都有不同的参数选项,如需要编辑驱动参数的时候,可以点击驱动方法旁边的编辑图标。相对“区域铣削”驱动的参数编辑,点击编辑图标,弹出【区域铣削驱动方法】对话框,如图6-4所示。
外轮廓零件加工1
教案
教学 过程 质和外观等都不得有影响。 Ra:轮廓的平均算术偏差,取样长度L范围内,补测轮廓线上各点至基准线的距离的算术平均值。 Ry:轮廓最大高度,即在取样长度L内轮廓峰顶线与轮廓谷底线之间的距离。 Rz:就是在基本测量长度范围内,自被测轮廓上五个最高点至五个最低点的平均距离, ※Ra数值愈小,零件表面愈趋平整光滑;Ra的数值,零件表面愈粗糙。 尺寸公差标注: 理论 结合 实际 使用
教学过程 形状/位置公差种类: 形状公差标注: 读懂 图纸 必备
教学 过程 位置公差标注: 识图练习教学生如何将理论知识用于实际加工
教学 过程 表面粗糙度标注: 读懂 图纸 必备
教学 过程 尺寸精度检验:常用游标卡尺、百分尺等来检验。 若测得尺寸在最大极限尺寸与最小极限尺寸之间,零件合格。若测得尺寸大于最大实体尺寸,零件不合格,需进一步加工。若测得尺寸小于最小实 体尺寸,零件报废。 形状精度的检验:通常用直尺、百分表、轮廓测量仪等来检验。 位置精度的检验:常用游标卡尺、百分表、直角尺等来检验。 加工精度主要用于生产产品,加工精度与加工误差都是评价加工表面几何参数的术语。加工精度用公差等级衡量,等级值越小,其精度越高;加工误差用数值表示,数值越大,其误差越大。加工精度高,就是加工误差小,反之亦然。公差等级从IT01,IT0,IT1,IT2,IT3至IT18一共有20个,其中IT01表示的话该零件加工精度最高的,IT18表示的话该零件加工精度是最低的,IT7、IT8是加工精度中等级别。 加工精度:实际零件的形状、尺寸和理想零件的形状、尺寸相符合程度。读懂图纸必备 实际生产必备知识
型腔铣和等高轮廓铣
4.1 型腔铣概述 4.1.1型腔铣和平面铣的比较 平面铣和型腔铣操作都是在水平切削层上创建的刀位轨迹,用来去除工件上的材料余量。 1.相同点 这两种的相同点 (1)而者的刀具轴都垂直于切削层平面。 (2)刀具路径的所用切削方法相同,都包含切削合乎轮廓的铣削(注:型腔铣中没有标准驱动铣)。 (3)切削区域的开始点控制选项以及进刀/退刀选项相同。可以定义每层的切削区域开始点。提供多种方式的进刀/退刀功能。 (4)其他参数选项,如切削参数选项、拐角控制选项、避让几何体选项等基本相同。 2.不同点 这两种操作的不同点: (1)平面铣用边界定义零件材料。边界是一种几何实体,可用曲线/边界、面(平面的边界)、点定义临时边界以及选用永久边界。而型腔铣可用任何几何体以及曲面区域和小面模型来定义零件材料。 (2)切削层深度的定义二者不相同。平面铣通过所指定的边界和底面的高度差来定义总的切削深度,并且有5种方式定义切削深度;而型腔铣通过毛坯几何体和零件几何体来定义切削深度,通过切削层选项可以定义最多10个不同切削深度的切削区间。 4.1.2型腔铣的适用范围 在很多情况下,特别是粗加工,型腔铣可以替代平面铣。而对于模具的型腔或型芯以及其他带有复杂曲面的零件的粗加工,多选用岛屿的顶平面和槽腔底平面之间为切削层,在每一个切削层上,根据切削层平面与毛坯和零件几何体的交线来定义切削范围。因此,型腔铣在数控加工应用中最为广泛,可用于大部分的粗加工以及直壁或者斜度不大的侧壁的精加工;通过限定高度值,只作一层切削,型腔铣也可用于平面的精加工,以及清角加工等。型腔铣加工在数控加工应用中要占到超过一半的比例。 型腔铣用于加工非直壁的、并且岛屿的顶面和槽腔的底面为平面或曲面的零件,在许多情况下,特别是粗加工,型腔铣可以代替平面铣。型腔铣在数控加工应用中最为广泛,可用于大部分粗加工以及直壁或者斜度不大的侧壁的精加工;通过限定高度值,只作一层,型腔铣也可用于平面的精加工以及清角加工等。 4.1.3型腔铣的特点 型腔铣操作与平面铣一样是在与XY平面平行的切削层上创建刀位轨迹,其操作有以下特点: ●刀轨为层状,切削层垂直于刀具轴,一层一层的切削,如图4-1所示,即在加工过 程中机床两轴联动。 ●采用边界、面、曲线或实体定义刀具切削运动区域(即定义部件几何体和毛坯几何 体),但是实际应用中大多数采用实体。 ●切削效率高,但会在零件表面上留下层状余料,如图4-2所示,因此型腔铣主要用
CAM-固定轴轮廓铣—驱动方法练习
6.1.1.1 曲线与点驱动方法练习 用固定轴铣中的曲线与点驱动方法,在零件曲表面上雕刻图案。 第1步;打开文件。 ?在NX中打开本书所附光盘chapt06_part\srf目录下Srf_Curve_Engrave_0 零件,选择加工应用,进入加工应用环境。 图6-21 固定轴轮廓铣操作对话框 第2步;编辑操作。 ?将操作导航工具切换到程序顺序视图,并将鼠标定位在Engrave节点上双击 左键,弹出如图6-21所示的【固定轴铣】操作对话框。 ?在【固定轴铣】操作对话框中,从【驱动方法】下拉列表框中选择【曲线/ 点】选项,弹出如图6-22所示的【曲线与点驱动方法】对话框。在该对话框 中,从【切削步长】下拉列表框中选择【公差】选项,并在【公差】文本框 中输入0.005.再从【投射矢量】下拉列表框中选择【刀轴】选项。 ?在【曲线与点驱动方法】对话框中,单击驱动几何体下的【选择】选项,弹 出如图6-17所示的【曲线与点选择】对话框。在该对话框中打开【局部抬刀 直至结束】的选项。然后在图形窗口,按如图6-23所示标记位置顺序选择曲 线1、2、3、4、5。
? 在【曲线与点选择】对话框中.关闭【局部抬刀直至结束】选项,然后在图 形窗口,按如图6-23所示标记位置、顺序选择曲线6、7、8、9。并单击【确定】,直到返回到固定轴铣操作对话框。 图6-22 曲线/点驱动方法对话框 图6-22 曲线选择顺序 第3步;刀轨生成和模拟。 ? 在固定轴铣操作对话框底部,选择刀具路径产生图标,并在弹出的对话框中 单击【确定】,则显示如图6-23所示刀具路径。若再选择验证刀具路径图标,来模拟刀具切削运动。 ? 【文件】→【关闭所有文件】。 图6-23 刀轨结果 1 2 3 4 5 6 7 8 9
第七章 固定轮廓铣Fixed Contour二
第七章固定轮廓铣【Fixed Contour】(二)【简述】 本章节重点介绍固定轴其他的驱动方法操作及参数功能的使用,增强用户对固定轴加工的了解,使用户能够用固定轴轮廓加工操作编写任意形状零件的NC程序。 1. 固定轴曲线/点驱动 【曲线/点】驱动方法允许用户通过指定点或曲线来定义驱动几何体,并由此产生相应驱动点。它将使得系统产生跟随驱动曲线或点所定义的驱动路径的刀轨,因此在实际应用中,可应用【曲线/点】驱动方法来实现筋槽或字体的加工。【曲线/点】驱动方法如图7-1所示。 图7-1 曲线/点驱动方法 下面将用例子来讲解曲线/点驱动的应用,所有操作步骤如下列所示: ⑴.打开文件(curve point_drive.prt),并进入到加工模块,由于此模型定义过加工参数,所以不需要初始化。如图7-2所示。
1 7-2 curve point_drive.prt 图所示。7-3⑵.创建固定轴曲线/点驱动操作,操作的步骤如流程图 /曲线点驱动操作图7-3
,点点〗/⑶.定义“曲线点”驱动几何。在【固定轴轮廓】操作对话框里,将驱动方法设置为〖曲线/,进入【曲线/击编辑图标点驱动方法】对话框,在操作界面里选取曲线作为驱动 几何,确定 2 完成后生成刀轨。多段曲线选择的区别,如图7-4所示。 图7-4驱动曲线选择的区别 ⑷.按模型所示的曲线作为驱动几何加工,投影到部件几何体表面所得的刀轨,如图7-5所示。其他相同的参数在此不再重述。
3 点驱动刀轨7-5 图曲线/固定轴螺旋驱动2. 所示。驱动⑴.螺旋驱动使得系统产生从指定的中心位置向外螺旋的驱动点,螺旋驱动方法如图7-6点位于垂直于投影矢量方向的平面内,然后按投影矢量方向投影到加工面上,从而产生螺旋 的刀所示。轨,如图7-7 螺旋驱动图7-6
05UGCAM教材模块五--固定轴曲面轮廓铣-区域铣削
模块五 固定轴曲面轮廓铣创建 一、学习目标 学习本项目后,掌握UG 软件加工模块Fixed_Contour (固定轴曲面轮廓铣)加工操作,利用区域铣削驱动完成小型腔曲面的半精加工,并合理定义各加工参数。 1、掌握固定轴曲面轮廓铣的特点 2、掌握刀轴与投影的概念 3、掌握区域铣削驱动的创建 4、掌握区域铣削的特点 5、掌握定向陡峭区域的概念 6、掌握主要切削参数的定义 二、工作任务 1、创建区域铣削驱动 2、定义主要切削参数 三、相关实践知识 在实践操作中,利用区域铣削驱动完成小型腔曲面的半精加工,定义各项内容如表7-5-1所示。 表7-5-1 加工程序五:小型腔曲面的半精加工 程序名 AREA_MILLING01 定 义 项 参 数 作 用 程序组 NC_PROGRAM 指定程序归属组 使用几何体 MILL_GEOM001 指定MCS 、加工部件、毛坯 使用刀具 MILL_D10R5 指定直径10的球刀 使用方法 MILL_SEMI_FINISH 指定加工过程余量 驱动方式 区域铣削 定义切削范围 切削区域 小型腔底面 定义加工范围 裁剪 未定义 约束加工范围 图样 “跟随周边” 确定刀具切削方式 加 工 操 作 步进 恒定的,数值0.1 确定刀具切削横跨距离
切削部件余量0.1 指定加工过程保留余量转速S=2600rpm 确定刀轴转速 进给率进刀速度F=400 第一刀速度F=400 步进速度F=800 切削速度F=1000 横越速度F=1200 退刀速度F=2000 定义加工中各过程速度 (数值仅作参考,具体加工根据机 床功率、部件材料、刀具类型及材 料来指定。) 其他按默认值 固定轴曲面轮廓铣加工的创建步骤如下: 1、进入固定轴曲面轮廓铣加工 选择“加工生成”工具条中“创建加工操作”命令,在类型中选择“mill_contour”。 子类型中选择第五项“Fixed_Contour”(固定轴曲面轮廓铣)。 “程序”选项里按默认;“使用几何体”选择“MILL_GEOM001”;“使用刀具”选择“MILL_D10R5”;“使用方法”选择“MILL_SEMI_FINISH”;名称命名为“AREA_MILLING01”。确认后进入建立固定轴曲面轮廓铣对话框。如图7-5-1所示。 图7-5-1 固定轴曲面轮廓铣对话框
固定轴轮廓铣(使用手工驱动曲面选择创建流线操作)
流线驱动方法根据选中的几何体来构建隐式驱动曲面。流线使您可以灵活地创建刀轨。规则面栅格无需进行整齐排列。 流线示例:较大的面由许多较小的不规则的面包围 刀轨在圆角处封闭。 流线和曲面区域驱动方法之间的差异包括:
可变流线 可变流线支持所有在可变轴曲面轮廓铣中可用的刀轴选项。 自动驱动曲面创建 对于更简单的加工,选择切削区域并将选择方法设置为自动。软件: ? 根据“切削区域”边界边缘生成流曲线集和交叉曲线集。 ? 消除孔和小的内部修剪区域。 ? 填充流曲线集和交叉曲线集内的小缝隙并光顺其中的小纽结。 如果切削区域几何体是从若干个不相连的区域选择的,则系统会标识并处理具有最长周边的单一连续区域。所有其他区域均被忽略。 如果切削区域几何体是从不同体选择的,则自动将它们看作是不相连的。 您可以使用指定手工定义具有缝隙的曲线集或从多个体选择曲线。 请参见带缝隙的曲线集选择提示了解更多信息。 手工驱动曲面创建 要更精确地控制刀轨,将选择方法设置为指定并手工定义驱动曲面的选择曲线。系统填充流曲线集和交叉曲线集内的小缝隙并光顺其中的小纽结。 您通过选择流 (A) 和可选的交叉 (B) 曲线为流线驱动方法定义驱动曲面。选择面边缘、线框曲线或点来创建任意数目的流曲线和交叉曲线组合。如果您未选择交叉曲线,则软件使用线性段 (C) 将流曲线的末端连接起来。
使用手工驱动曲面创建: ?如果您指定切削区域,它将起到空间范围的作用。 ?您可以仅根据线框加工。不必选择部件几何体。 ?如果选择部件几何体,线框曲线会(沿指定的投影矢量)投影到部件几何体上。 刀轨生成 默认情况下,刀轨先在第一条交叉曲线上开始,并沿流曲线移刀直到抵达最后一条交叉曲线,然后添加步距并进行下一次移动。您可以使用指定切削方向矢量将刀轨方向更改为所需的方向。 位于何处? 单击加工创建工具栏上的创建操作。 在创建操作对话框中: ?要创建固定轴操作,请从类型列表中选择mill_contour,并从操作子类型组中选择 STREAMLINE。 ?要创建可变轴操作,请从类型列表中选择mill_multi-axis,并从操作子类型组中选择 VARIABLE_STREAMLINE。 手工创建
UG轮廓铣加工
第4单元固定轴轮廓铣加工 固定轴轮廓铣加工是指在轮廓铣加工模板所提供的环境下,创建固定轴轮廓、轮廓曲面、曲面区域、等高轮廓曲面、曲面清根等铣加工操作。固定轴轮廓铣沿曲面轮廓进刀进行切削,因此可以加工陡峭和平缓的复杂曲面几何形体。 主要内容 项目4-1 台灯座凸模的加工 项目4-1 台灯罩凹模的加工 实战演练4:可乐瓶底座模芯的加工 知识梳理 返回目录退出
项目4-1 台灯座凸模的加工 项目目标: 在“轮廓铣”模板加工环 境下,运用粗铣表面、精铣键 形凹槽、精铣圆孔槽、半精铣 表面、精铣表面等操作,完成 图4-1所示“台灯座凸模”零 件的加工。 学习内容: 构建多重曲面工件模型、 设置轮廓铣加工环境、创建加 工坐标系、创建几何体、创建 刀具组;创建多重曲面型腔铣、 精铣孔槽、轮廓区域铣等加工 操作;生成刀具轨迹、检验刀 轨;后处理操作、生成加工程 序等。图4-1 台灯座凸模
任务分析: 1.加工条件 根据工艺要求,该工件在立式加工中心机床上加工。工件的毛坯为240×200×70板料,矩形体的所 有表面已经加工完毕,材料为65钢。使用专用夹具从侧面定位和装夹,固定在机床的工作台上。 2.工序安排 要求该加工件在一次装夹中完成所有的形面加工。共安排5个加工工步,即粗铣表面、精铣键形凹槽、精铣圆孔槽、半精铣表面、精铣表面。 【工步1】粗铣表面 采用“型腔铣”方式,粗铣灯座表面,选用?30下部圆角R4鼓形铣刀,侧面和底面留有1mm加工余量。【工步2】精铣键形凹槽 采用“平面铣”方式,精铣灯杆凸台中的键形凹槽,选用?4端铣刀,一次铣削到位。 【工步3】精铣圆孔槽 采用“平面铣”方式,精铣?20圆孔槽,选用?12端铣刀,一次铣削到位。 【工步4】半精铣表面 采用“等高沿边铣”方式,半精铣灯座表面,选用拔模角15o的?16下部圆角R2圆锥鼓形铣刀,侧面 留有0.5mm加工余量,所有平面底面不留余量,铣削到位。 【工步5】精铣表面 采用“轮廓区域铣”方式,精铣灯座表面,选用?10下部圆角R1鼓形铣刀,一次铣削到位。
UG数控加工讲义(4——固定轴曲面轮廓铣)
UG数控加工讲义(四) 固定轴曲面铣削加工操作流程与实例 一、操作流程 1、创建程序、刀具、几何体以及加工方法。 2、创建操作,选择操作子类型。选择程序、刀具、几何体以及加工方法父节点。 3、在创建操作对话框中指定驱动方式、设定驱动参数、刀轴矢量及投影矢量。 4、设置切削参数、非切削参数和进给率等。 5、生成刀轨。 6、通过切削仿真进行刀轨校验、过切及干涉检查。 7、输出CLSF文件,进行后处理,生成NC程序。 二.使用固定轴曲面轮廓铣实例操作 本例对零件上半部分进行加工。 步骤: 1、打开文件:fix_contour.prt,进入加工环境。在加工环境中,CAM进程配置“cam_general”, CAM配置选择“mill_contour”,单击“初始化”按钮。 2、创建加工刀具,刀具类型选择“mill_multi-axis”,子类型选择第一个“mill”。刀具直径 3mm,刀具长度50mm。 3、创建加工几何体,选择零件几何体,设定毛坯几何体偏置零件表面0.5mm。 4、选择创建好的刀具,右键后选择插入操作,选择“mill_contour”,子类型选择第一行最 后一个类型“ZLEVEL_PROFILE_STEEP”。创建等高轮廓铣 加工零件底座侧壁。选择底部侧壁作为切削面,生成刀轨,仿 真检查。通过等高轮廓铣操作,消除零件过多的侧面余量,为 创建固定轴曲面轮廓铣提供合适的工件结构。 5、创建固定轴曲面轮廓铣。 在创建操作中选择“mill_contour”,子类型选择第二行的第二个按 钮“FIXED_CONTOUR”。在“FIXED_CONTOUR”中驱动方式 中选择“区域铣削”,当不定义驱动区域时,系统默认零件沿Z向 投影为驱动几何体。步进设为刀具直径的20%。“陡峭包含”设为 “无”,即加工所有表面。由于是固定轴操作,因此刀轴矢量取+Zm 轴。 6、创建固定轴曲面轮廓铣操作加工陡峭面。可以选择子类型为第二行倒数第二个按钮“CONTOUR_AREA_DIR_STEEP”。或者直接使用FIXED_CONTOUR,通过选择“陡峭包含”设为“定向陡峭”来实现对陡峭面的加工。设置“陡角必须”为35度。生成刀轨验证。 7、创建固定轴曲面轮廓铣操作加工另一部分陡峭面,方法同上。在“切削角”设置为0度。 生成刀轨验证。
五 UG8.5 CAM 固定轴曲面轮廓铣创建
模块五固定轴曲面轮廓铣创建 一、学习目标 学习本项目后,掌握UG软件加工模块Fixed_Contour(固定轴曲面轮廓铣)加工操作,利用区域铣削驱动完成小型腔曲面的半精加工,并合理定义各加工参数。 1、掌握固定轴曲面轮廓铣的特点 2、掌握刀轴与投影的概念 3、掌握区域铣削驱动的创建 4、掌握区域铣削的特点 5、掌握定向陡峭区域的概念 6、掌握主要切削参数的定义 二、工作任务 1、创建区域铣削驱动 2、定义主要切削参数 三、相关实践知识 在实践操作中,利用区域铣削驱动完成小型腔曲面的半精加工,定义各项内容如表1-5-1所示。 确定刀具切削方式 “跟随周边”
固定轴曲面轮廓铣加工的创建步骤如下: 1、进入固定轴曲面轮廓铣加工 选择“加工生成”工具条中“创建加工操作”命令,在类型中选择“mill_contour”。子类型中选择第五项“Fixed_Contour”(固定轴曲面轮廓铣) 。 “程序”选项里按默认;“使用几何体”选择“MILL_GEOM001”;“使用刀具”选择“MILL_D10R5”;“使用方法”选择“MILL_SEMI_FINISH”;名称命名为“AREA_MILLING01”。确认后进入建立固定轴曲面轮廓铣对话框。如图1-5-1所示。
图1-5-1 固定轴曲面轮廓铣对话框 2、固定轴曲面轮廓铣参数定义 固定轴曲面轮廓铣的创建过程并不复杂,但一定要充分理解其内在的含义,即“部件几何体”-“驱动方式”-“指定切削区域”-“部件余量”-“部件余量偏置”之间的关系。下面以固定轴曲面轮廓铣中最为常用的驱动方式--区域铣削,对小型腔曲面进行半精加工。 选择驱动方式为区域铣削,其主要对话框选项如图1-5-2所示。
固定轴曲面轮廓铣(优化刀路)UG模型
固定轴曲面轮廓铣(优化刀路)建议完成时间:30分钟 (档案名称:Counter1.prt) 1. 进入加工环境应用 2. 放置坐标系(设计)到零件顶部上方 3. 重合加工坐标系 4. 插入一个新的操作Fix_counter 5. 新建或选择一把铣刀M14R7 6. 选择零件几何体为实体 7. 选择驱动方法为AreaMilling 8. 发现不需要驱动几何体(介绍与边界的区别) 9. 生成刀轨(缺点介绍) 10. 重新选择pattern 类型为Follow periphery(介绍其他类型)跟随外形 11. 生成刀轨(缺点介绍) 12. 选择参数Aplly —— on part 13. 生成刀轨(时间较长)
14. 介绍加工方法(一把刀打天下不合适)(硬质合金刀适用性) 15. 介绍Steep Containment 参数 none none_steep 平坦面 Directional Steep 方向陡峭面 16. 设定none_steep=50° 17. 生成刀轨,介绍 18. 选择一个新的操作Zlevel_Profile_steep 19. 选择同一把铣刀(M14R7) 20. 选择Steep Angle=50° 21. 介绍Merge Distance值(以刀具直径为限)、Minimum Cut Length (碎片)避免跳刀 22. 选择零件几何体为实体 23. 设定Depth per Cut (Range1)=5(层设定) 24. 生成刀轨 (观察,介绍纯90°不加工) Tolerant Machining (Trim by)——Exterior edge (外形边缘) 、Silhouette (外形轮廓) 25. 去掉角度值 26. 生成刀轨(观察介绍0°不加工) 27. 利用Cut Level选项去除下部不加工区域 28. 重新生成刀轨(观察)
ug等高轮廓铣
等高轮廓铣 【简述】本节重点讲解【深度铣】操作的参数功能,“深度铣”是一个固定轴 铣削模块,其设计目的是对从多个切削层中的实体/面建模的部件进行轮廓铣;“深度铣”对于高速加工特别有效。所谓深度铣,就是针对模型的外形轮廓进行加工;跟我们前一章节所学的【型腔铣】操作→切削方式为“轮廓”类型相似,大部分切削参数都相同,相同的参数在此不再重述,仅介绍【深度铣】操作中专有参数选项。 【案例操作】 为了使学者更容易地学好【深度铣】加工操作,本章节用案例做操作流程来说明各参数选项,下面打开例子(Zlevel_Profile.prt)如图5-1所示,并进入加工模块。【深度铣】操作适合用于半精加工或精加工“陡峭”的模型,对于此模型如何粗加工在此将不作讲述。 图5-1 深度铣案例图 一、定义加工几何 在前几个章节的内容都讲到如何定义加工坐标与几何体,这里不再讲述如何来操作。在模型进入到加工模块后,设置加工坐标与安全平面,如图5-2所示。加工几何体,直接选取模型为“部件几何”,“毛坯几何”在【深度铣】操作里不需要设定。
图5-2 定义加工几何 二、定义加工方法 定义“加工方法”组主要是为了使多个操作的时候产生继承父级组,从而减少再次定义加工方法的参数。在此【深度铣】操作里,设定“加工方法”组参数如表5-1所示。 表5-1 加工方法参数
三、创建刀具 在做加工操作之前需要对于模型分析,考虑模型使用何种刀具做加工操作才合理。根据此模型的分析,在这里创建一把“直径D12,底角半径R1”的端铣刀具。按照表5-2所提示的参数来创建刀具。 表5-2 刀具参数表 序号刀具名称刀具直径圆角半径刀具号长度补偿 1 JMSK_D1 2 R12 1 1 1 四、创建深度铣操作 表5-2 刀具参数表序号刀具名称刀具直径圆角半径刀具号长度补偿 1JMSK_D12R112111 在加工创建工具条点击【创建操作】图标,弹出【创建操作】对话框,选项组的〖类型〗默认选择“mill_contour”,在选项组〖操作子类型〗中,选择“ZLEVEL_PROFILE”图标,各个选项位置如下: 1.“程序”选择父级组“PROGRAM”。 2.“刀具”选择前面已创建好的刀具名称,即“JMSK_D12R1”。 3.“几何体”选择前面已创建好的几何体节点名称,即“WORKPIECE”。4.“方法”选择前面已创建好的方法名称,即“MILL_SEMI_FINISH”。5.“名称”将原来系统的名称改为“SEMI_PROFILE”。 按上面所设,所有选项设置完毕,点击【确定】,即可进入【深度加工轮廓】操作对话框。在【深度加工轮廓】操作里,默认所有参数选项,直接在“操作”区点击生成图标,计算出刀轨如图5-3所示。我们从刀轨可以看出,【深度加工轮廓】操作是对模型的轮廓做加工;点击【确定】按钮完成此操作。从刀轨来分析不太理想,如想要更加优化刀轨路径,还需要其他的参数设置;接下来就针对【深度加工轮廓】操作的参数选项作详细的讲述,跟前面所学的加工操作相同的参数选项不再介绍。 注:如果没有定义任何切削区域几何体,则系统将整个“部件”几何体当作切削区域。 图5-3 深度加工轮廓刀轨