炼厂C4有机硫脱除技术的研究进展
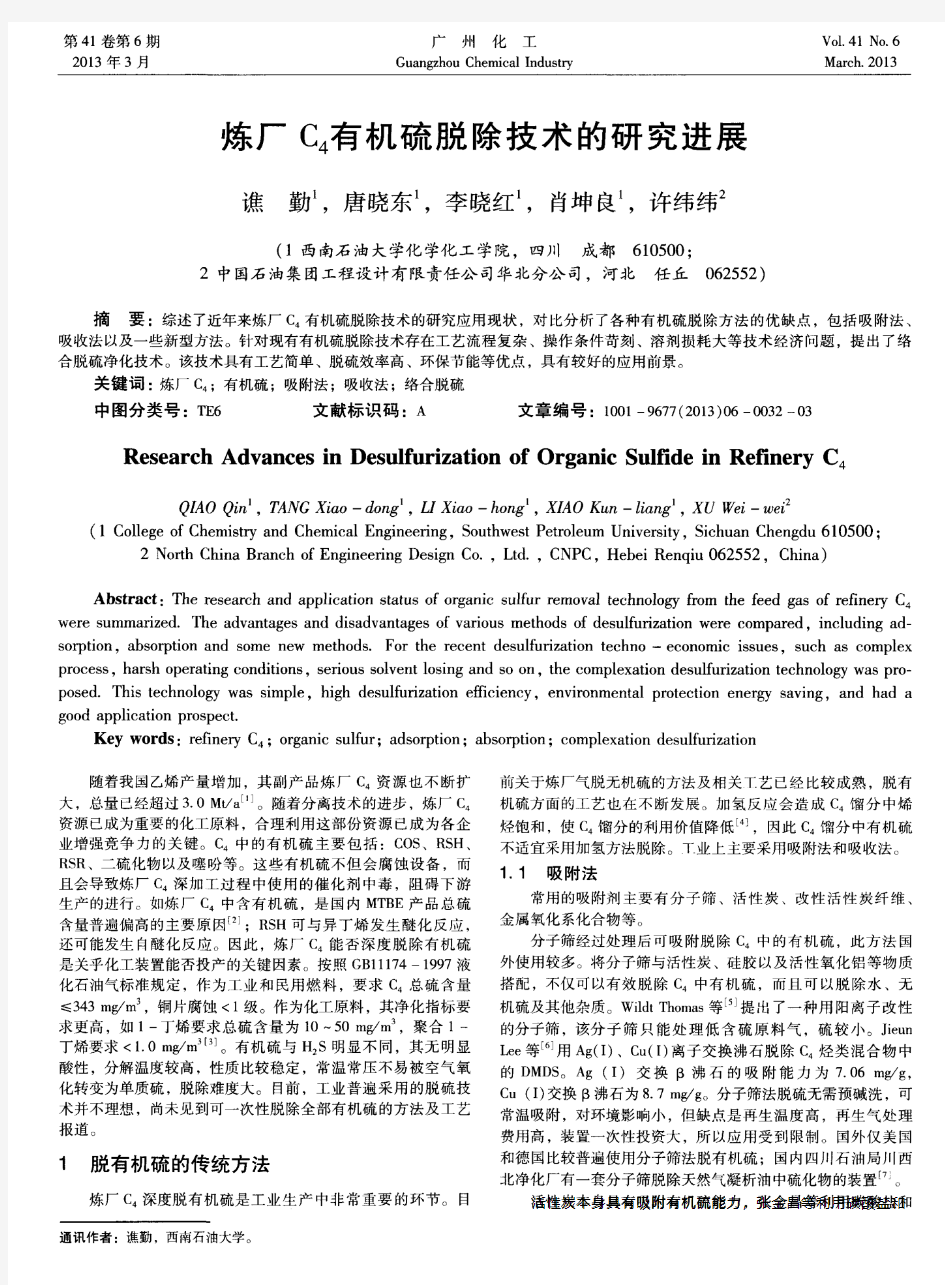
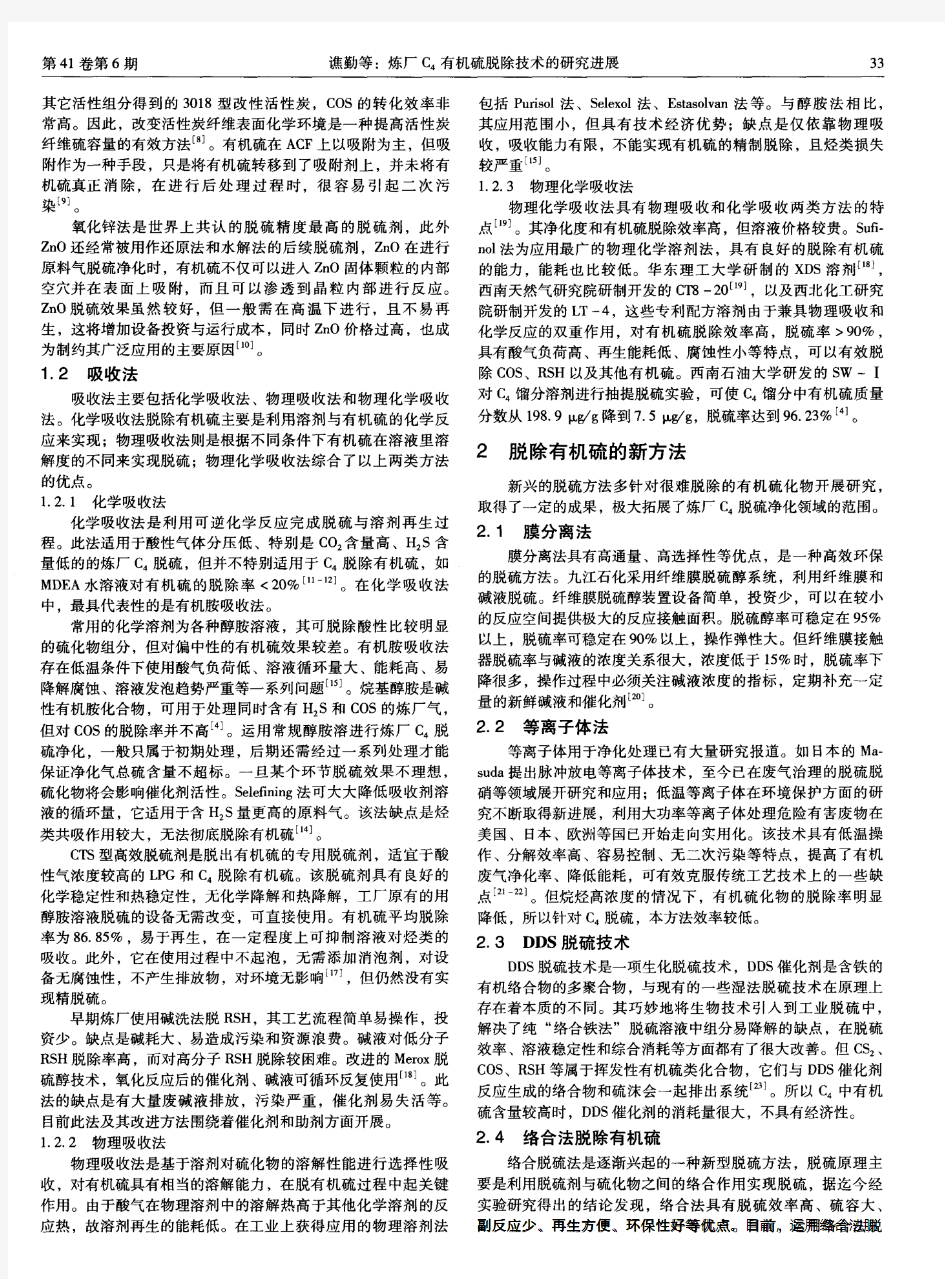
除尘技术与设备的发展
N A N C H A N G U N I V E R S I T Y 期中考试 《大气污染控制工程》 班级:环境工程141班 学生姓名:康秋云 学号: 2017年4月
除尘技术与设备的发展 学生姓名:康秋云学号: 摘要:介绍了目前主要的空气除尘设备的工作原理、除尘性能和适应场合,从环境保护角度简要分析了各类除尘器的存在的不足以及当今社会除尘技术发展的新趋势。 关键词:除尘技术、除尘设备、大气污染 我国是一个能源生产与消费大国,大气环境污染基本特征是直接燃煤的煤烟型大气污染。20世纪末,国内大中城市由煤烟型大气污染向煤烟与汽车尾气复合型污染转移,这些空气中、微煤粉尘,尤其是直径为的飘尘对人体健康有极大危害。如何防治大气污染、洁净空气环境也是人们不断研究的课题。 工业除尘技术应用于气体中含有粉尘的情况,如加工木制品、打磨、焊接、粉碎等操作过程为保护人的健康,维护设备的性能,实际中有必要去除气体中悬浮的粉尘微粒。目前,工业中应用的除尘设备种类很多,可以有效地截留和去除很宽范围的一些粒子污染物。但为了适应现代工业的要求,仍急需开发一些新的技术,以进一步的节约能源,简化维修,提高效率,降低投资。另外,难以用现有除尘技术处理的情况也层出不穷,这也就要求开发一些新的相关除尘技术。 1.空气除尘设备研究现状 按捕集粉尘的作用力及原理,除尘设备可分为4类:机械式除尘、电除尘、过滤式除尘和湿式洗涤除尘设备。按除尘效率可分为:高效除尘设备,包括电除尘、袋式除尘、高效文丘里除尘等;中效除尘设备,包括旋风除尘及其他湿式除尘等;低效除尘设备,包括重力沉降、惯性除尘等。 沉降室
沉降室也叫重力除尘器,是一种借助重力作用使含尘气体中粉尘自然沉降以达到净化气体目的的装置。当含尘气体水平通过沉降室时,尘粒受沉降力的作用向下运动,经过一定时间后尘粒沉降到沉降室的底部而分离,净化后的气体通过出口排出。沉降室的沉降速度太小,一般只用于分离50um以上的尘粒。因此沉降室通常用于粗尘粒的预除尘。 惯性除尘器 惯性除尘器是利用粉尘在运动中惯性力大于气体惯性力的作用,将粉尘从含尘气体中分离出来的设备。其利用一系列的挡板,惯性大的颗粒被阻挡下落,小的颗粒绕板而过。粉尘粒径越大、气流速度越大、挡板数越多和距离越小,则除尘效率越高,但压力损失也越大。这种除尘器结构简单,分离临界粒径为20--30um,压力损失为100--1000Pa。 旋风分离器 旋风分离器是利用旋转的含尘气体所产生的离心力,将粉尘从气流中分离出来的一种干式气-固分离装置。当含尘气体进入旋风分离器时,气流将由直线运动变为圆周运动。含尘气体在旋转过程中产生离心力,将密度大于气体的尘粒甩向器壁,进入排灰管。旋风分离器用于工业生产已有100余年历史。对于捕集、分离5--10um粉尘的效率较高,一般能达85%,但对于5um以下的颗粒效率只有50%。同时,旋风分离器的理论与实验研究十分困难,其应用也因此受到限制。旋风分离器有如下特点:结构简单,不需特殊的附属设备;操作、维护简单,压力损失中等,动力消耗不大;操作弹性大,性能稳定,不受含尘气体的浓度和温度等影响。旋风分离器对粉尘的物理性质无特殊要求,作为一种重要的二级除尘设备被广泛应用于化工、石油、冶金、建筑、矿山、机械、轻纺等工业部门。 湿式除尘器 湿式除尘器是使含尘气体与水或其他液体接触,利用水滴和尘粒的惯性碰撞等作用把尘粒从气流中分离出来的设备。其除尘机理是:当含有悬浮
转化催化剂硫中毒的原因和处理
转化催化剂硫中毒的原因和处理 肖春来(辽宁葫芦岛锦西石化分公司,辽宁葫芦岛125001) 2007-11-14 制氢转化过程中,硫对转化催化剂具有明显的毒害作用,因硫中毒导致转化催化剂失活甚至报废的情况时有发生,给炼厂造成巨大的经济损失。为保证装置安全生产,保证转化催化剂长周期运行,需要高度重视硫对催化剂的危害。 1 硫的来源 硫是转化催化剂最主要的毒物之一,制氢原料中均含有不同量的硫。随着焦化干气制氢技术的普及,原料含硫量也在进一步增加。脱硫单元效果变差,是使硫进入转化系统的最直接来源,大多数时候是由于加氢条件异常使原料中的有机硫氢解不完全,导致脱硫剂出现硫穿透现象;也可能由于原料中的硫含量在短时间内大幅度上升致使加氢脱硫能力不足引起硫穿透。此外,汽包给水也有可能带入一定量的硫酸根。 2 硫对转化催化剂的危害 硫是转化催化剂最常见、也是难以彻底清除的毒物。不同的制氢原料含有不同量的硫,硫存在的形态十分复杂,大致可分为有机硫和无机硫。常用的干法脱硫流程是先用加氢催化剂将有机硫氢解成无机硫H2S,然后用脱硫剂将无机硫脱除。现有工业装置的脱硫精度一般能达到小于0.5×10-6或小于0.2×10-6的水平,残余的微量硫进入转化系统。转化催化剂具有一定的抗硫性能,就目前常用的转化催化剂而言,脱硫气中硫含量小于0.5×10-6时,能够保证转化催化剂正常发挥活性,可以保证转化催化剂长期使用。但是,如果进入转化催化剂的硫含量超标,将会引起转化催化剂中毒。 转化催化剂中毒是可逆的。一般情况下,硫主要引起转化炉上部催化剂中毒,而不易引起整个床层中毒,硫严重超标时也会导致整个系统被污染。硫中毒后的转化催化剂可以通过蒸汽再生而恢复活性。转化催化剂严重硫中毒将使转化催化剂严重失活甚至报废。 3 硫中毒的机理 转化催化剂中毒一般认为是硫化氢与催化剂的活性组分镍发生了反应: 硫化氢使活性镍变成非活性的Ni3S2,因而使转化催化剂活性下降甚至失活。 经过催化剂厂家实验分析,含镍15%的催化剂在775℃的条件下,仅含0.005%的硫已经显示出中毒迹象,当硫达到0.015%时,镍表面硫的覆盖率达到44%,相对活性只剩下20%。因此,镍中毒机理的新理论认为:硫进入转化炉后均氢解成硫化氢,硫化氢在催化剂表面发生强烈的化学吸附过程: 这种化学吸附在硫浓度很低的条件下就能发生,要远远优先于生成固体Ni3S2的条件。即使催化剂吸附少量硫也会降低催化剂的反应活性。 4 硫中毒后转化催化剂的表现 在转化过程中,硫中毒导致催化剂活性下降,首先表现为转化炉管上部温度的升高,转化管中二、三米点温度的升高是判断硫中毒或催化剂活性下降的方法之一。随着硫中毒的不断加深,转化催化剂失活将引起高级烃下移造成转化催化剂上积碳现象的发生。硫中毒还表现为转化气中残余甲烷含量的增加。工艺气中硫含量增加,直接引起转化炉出口转化气中甲烷含量的上升,资料报导:工艺气中每增加0.1×10-6
5制氢催化剂的使用
第五章制氢催化剂的性质和使用 制氢过程使用的催化剂有如下几种: (1)钴——钼加氢转化脱硫催化剂; (2)脱氯催化剂; (3)氧化锌脱硫剂; (4)烃类——水蒸汽转化催化剂; (5)中温变换催化剂; (6)低温变换催化剂; (7)甲烷化催化剂; (8)吸附剂。 这些催化剂的使用条件非常苛刻,为了使装置实现安稳长满优生产,确保经济、合理、高效的生产目的,必须严格控制原料杂质的浓度,以避免杂质对催化剂的损害。 制氢所使用的原料一般都是轻油,近年一些装置掺用部份炼厂干气制氢,这些制氢原料中通常含有的对制氢催化剂有影响的杂质是硫、氯、有机金属化合物。 硫对含镍的转化催化剂和甲烷化催化剂,对含铜的低温变换催化剂都会造成毒害,一般转化炉入口原料中硫含量要求小于0.5ppm。硫中毒会使转化炉管产生“热带”,也会促使出口气体甲烷含量增高。 氯离子具有很高的迁移性,可随工艺气流迁移,对下游催化剂及设备造成威胁。许多合金钢受氯侵蚀后产生应力腐蚀,氯的侵蚀导致许多换热器破裂。氯会导致转化催化剂失活,对铜系低温变换催化剂的影响更大,氯与铜形成的新物质的熔点很低,易升华又易熔于水,在低变工艺条件下,这些氯化合物可以穿透整个床层。一般要求原料中含氯应低于5 ppb。 有机金属化合物会沉积在加氢脱硫及转化催化剂表面,导致催化剂活性的永久性衰退,一般要求原料中重金属含量应低于5ppb。 5.1加氢转化催化剂 制氢原料中含有不同数量的有机硫和无机硫,这些硫化物的存在,会增加原料气体对设备的腐蚀,尤其重要的是制氢过程所使用的含镍、含铜的催化剂极容易被硫中毒,失去活性,严重影响生产的顺利进行。但是,有机硫化物性能稳定,不容易被脱除,只有在加氢催化剂的作用下,与氢气反应将有机硫转化生成硫化氢,才能被脱除。传统加氢转化催剂的主要成份是υ-Al2O3担载的C O O和M O O3,即钴——钼加氢转化催化剂,近年来北京海顺德催化剂有限公司生产的加氢催化剂的载体改用钛的氧化物,这种催化剂也取得一定的实用业绩。5.1.1加氢剂的种类及物化性质 5.1.1.1国内常用加氢转化催化剂的型号及性能υ 国内加氢转化催化剂现有十几种型号,经常用于制氢装置上的仅有几种,如表5-1所示。大型氨厂加氢转化催化剂(如T201型)寿命最长超过十年,此类催化剂质量已不亚于国外催化剂的水平,因此,国产化率已达100%。
用物理_化学混合溶剂选择性脱除硫化氢与有机硫
石油与天然气化工 !?## ??#用物理一化学混合溶剂选择性脱除硫化氢与有机硫四川石油局天然气研究所% &组?摘要在小()?)的填料吸收塔试验装置上,采用甲基二乙醇胺一环丁枫+水溶液对高含硫天然气,?./0(?#1#?一,甲,23.0&?45#?一名甲,有机硫06 7897“:进行了;?;<=>压力下的选择性脱除硫化氢与有机硫试验,考查了溶液组成、吸收温度、气液比等对净化气中硫化氢含量、230共吸收率 与有机硫脱除率的影响。在适宜的操作条件下,净化气中硫化氢含量稳定低于 6 7897”,有机硫低于) 7897,,230共吸收率约为) 1#?‘?。一、前?;??归???口丫公在各种气体脱硫方法中,选择性脱硫过程相对于非选择性脱硫过程而言,由于在几乎全郁脱除原料气中硫化氢的同时仅脱除其中部分二氧化碳,故脱除的酸气量减少,酸气硫化级浓度提高,溶液循环量下降,能量消耗降低。这不仅有利于所得酸气的后续加工利用,降低脱硫装里的操作费用,还会由于相关设备尺寸相应缩小而使新建脱硫装置的投资有所节省。据报道,脱硫装置投资的,& 一( :1 一“与溶液环循量的大小直接相关,另外, 一6 :5 ??取决于再生过程的能量消耗。而再生能量消耗又约占操作费用,劳动力费用除外:的( 1#。“?〔 〕。因此,从气流中选择性脱除硫化氢及其他含硫化合物的技术近年来受到人们越来越多的关注,井取得了迅速的发展。目前,在能够应用于大处理量和较高操作压力下的各种选择性脱除硫化氢的方法当中,以使用甲基二乙醇胺,<ΑΒΥ:水溶液的化学吸收法和以使用多乙二醇二甲醚的物理吸收法,即/Γ#Γ1。 法:较有代表性。前者是利用<ΑΒΥ与硫化氢和二氧化碳反应速度上的巨大差异,即借助于吸收过程的反应动力学实现这两种酸性气体的选择性分离,适用于处理硫化级含量较低而23.9?0/比较高的某些气体。该过程的本特征性要求气液两相接触时间应尽可能短,加之叔胺的碱性较弱,故选择性、净化深度与溶液酸气负荷之间常常相互制约。为使溶液对硫化氢的吸收保持有较大的推动力和较快的速度,以保证吸收过程具有一定的选择性并达到规定的产品气规格,溶液的酸气负荷往往不能太高〔6一:。因而,用其处理硫化氢含盆较高的原料气时经济性将相应变差。此外,该法脱除有机硫化合物的能力有限。而/ΔΦ。 法则是利用过程所用溶剂对硫化氢的溶解度远高于对二氧化碳的溶解度,前者约为后者的牙倍:〔们,即借助于过程的热力学特征来实现选择性分离的。由于硫醇、二硫化碳这样一些 有机硫化合物在该溶剂中也有相当高的溶解度,故有利于降低产品气中总硫含量。各组分在物理溶剂中的溶解变与其各自的气相分压成正比,因而这类方法特别适用于处理高压、高酸气含量的气体。其主要缺点是溶剂对烃类,特别是分子量较高的烃类:溶解度较大,以及在吸收操作压力较低时难以达到必要的净化深度。为了兼收上述两类方法的优点,相互弥补不足之处,增加过程的灵活性,扩展适用范围,近年来国外正致力于开发物理一化学混合溶剂选择性脱除硫化氢与有机硫化合物的技术,并已取得一定进展。如以<ΑΒΥ和某种有机物理溶剂组合并配以少量水作为吸收溶液的/Γ#ΓΓΖΗΖΗ8法,),?〕,以<ΑΒΥ取代传统/Κ#ΓΖΗ?#溶液中二异丙醇胺,Α4=Υ:的新/Κ#ΓΖΗ?#法〔。〕,以及??ΛΖΜ?#法〔4Α〕,均属此类,并且都已进入工业应用阶段。鉴于我局已开发的气田中不乏压力较高、硫化氢与有机硫含量较高并含有一定数量二氧化碳的实例,开发一种类似于上述方法,既具有良好技术经济性能又具有一定适用范围的气体净化新工艺,无论对我局川西北矿区天然气净化厂脱硫装置及川东天然气净化总厂脱硫装置改造,抑或类似新脱硫装置建设及其他可能的潜在用户,都具有重要的实际意义。为此,我们根据以往科研成果,借鉴国外有关资料报道。于 ?(年&月在乐山召开的局炼化系统技术座谈会上正式建议开展本课题研究,遂即被批准为重点科研项目开始实施。是年底在川西北矿区夭然气净化厂内安装了一套设计处理能力为 7>9Ν,吸收压力为%<=>的小型脱硫试验装置。随后进行了溶液配伍、气液比、吸收温度、溶液再生深度等二十多项条件试验,考查了影响净化气硫化氢与有机硫含量及二氧化碳共吸收率的主要因素,并对通过条件试验所选定的溶液在较佳操作条件下进行了& 小时的连续运行,取得了满意的结
精脱硫系统催化剂与转化催化剂的升温与还原复件
精脱硫转化系统开车方案及操作规程 第一节精脱硫转化系统生产原理及流程 一、原理 1、精脱硫原理 通过铁钼触媒及镍钼触媒将焦炉气中的硫醇(RSR,噻吩(GH4S)、二硫化碳(CS)、硫氧化碳(COS等有机硫加氢转化成无机硫HS、不饱和烃加氢转化为饱和烃;再利用铁锰脱硫剂及氧化锌脱硫剂,除去HS,使焦炉气硫含量w O.lppm。 (1)加氢反应 RSH+H2=RH+H2S +Q;RSR ' +H=RH+R H+HS+Q C4H4S+4H2=C4H10+H2S+Q; CS 2+4H2=CH4+2H2S+Q COS+2H=CO+2HS C 2H4+H2=C2H6+Q 生产中铁钼触媒在进行上述反应的同时还存在以下副反应: CO+3H2=CH4+H2 O+Q (甲烷化反应) 2 H+O=2HO+Q( 燃烧反应) C2H4=C+CH4 +Q(析碳反应) 2CO=C+C2+OQ(析碳反应) 生产中加氢反应及副反应均为放热反应,在操作中应控制好触媒层温度。铁钼触媒主要的副反应是甲烷化反应,因此操作中要注意原料气中CO含量的变化。 (2)脱硫反应
①铁锰脱硫剂对H2S的吸收反应: FeS+H2S=FeS2+H2 MnO+2HS=MnS+2HO Mn S+2S= MnS+H ②氧化锌脱硫剂对硫的吸收反应: Zn O+bS=Z nS+bO 2、转化原理 在焦炉气中加入水蒸汽,在一定压力及温度下,通过催化剂作用, 生成合成甲醇有用的H2、CO及CQ。 转化反应:CH4+H2O= C0+3出Q CO+ H 20= CQ+H2+Q CH 4 = C+2H— Q 二、流程 1 、精脱硫转化系统流程叙述 来自焦炉气压缩机(C201)的焦炉气含H b S< 20mg/Nm有机硫 250mg/Nm其压力为2.5MPa温度100?110C。焦炉气通过两台并联的脱油剂槽(D106a、b)脱除掉焦炉气中的油水之后进入冷热交换器 (E104),被来自铁锰脱硫槽D103a D103b的一级脱硫气第一次加热;然后进入原料气第一预热器(E101)被来自转化气废热锅炉(E105)的转化气第二次加热;再经原料气第二预热器(E102)被来自气气换热器
国内外除尘技术进展-静电除尘
国内外除尘技术进展-静电除尘 前言: 在当今社会中,人类不断的在扩大生产规模,环境污染日益严重,包括:水资源污染、空气污染、噪音污染、垃圾污染、可再生资源污染等等,而对空气造成破坏的罪魁祸首就是粉尘。根据资料显示,全球一年中混入空气的各类污染物质加起来总共有6亿多吨,其中粉尘占的比重就达到了16%[1]。而如此之多的粉尘是从何而来的呢?在全国乃至全世界都存在许多产生粉尘污染的因素,包括煤炭的使用和无节制地开采、电为系统、化工厂所、造纸行业等,它们都涉及粉尘的排放。工业粉尘如此肆无忌偉地排向大气中,不仅会危害人体的健康,更会造成大自然系统的失衡,资源的流失,其结果是极其严重的。而现如今,大部分地区陷入雾靈的笼罩之下,环境保护己经刻不容缓了。 为了减少工业粉尘向大气中的投放,提高空气质量,各种样式的除尘装置因运而生,它们为空气治理提供了不少保障。由于除尘装置的多样性,可根据除尘理念的区别,分为湿式除尘器、旋风除坐器、沉降室、过滤式除尘器等,它们分别是利用水、颗粒自身的重力、各种过滤材料等手段来进行除尘,其中以静电除尘器的应用最为广泛,其原理则是利用静电场力的作用来除尘的。 1 除尘器简介 除尘器是将含尘气体里的粉尘分离出来,留下粉尘颗粒而排出干净气体的设备。除尘器的工作原理都是以对粉尘的作用力为理论依据,根据力的性质的不同,除尘器的种类也各式各样。工程除尘中常用的除尘器大多都是依靠各种作用力从含尘气体中过滤掉粉尘颗粒的,根据作用力的不同可以分为以下四种:机械除尘器、沉降室、惯性除尘器和旋风除尘器。 沉降室利用的是重力作用力,也就是地球对物体的吸引力,在重力的作用下含尘气体中的粉尘在沉降室中会逐渐地被分离出来;惯性除尘器是利用惯性作用力分离粉尘的,惯性作用力是指给物体赋予加速度时,物体本身的惯性力会使物体保持原有的运动状态,在相同的作用力下,惯性小的物体得到的加速度比惯性大的物体大,会更容易改变运动状态,这对粉尘分离来说是有利的;旋风除尘器利用的是离屯、力,离也力也是一种惯性力,但是是以圆周运动为方式来产生背离中也的作巧力,这类除尘器是根据物体在旋转过程中质量越大旋转速度越快,使得大颗粒粉尘会获得较大的离也力的原理进行除尘的。
钴钼系耐硫变换催化剂使用注意事项
K8-11系列催化剂使用注意事项 一、催化剂的使用 1.1 催化剂的装填 装填催化剂之前,必须认真检查反应器,保持清洁干净,支撑栅格正常牢固。为了避免在高的蒸汽分压和高温条件下损坏失去强度,催化剂床层底部支撑催化剂的金属部件应选用耐高温和耐腐蚀的惰性金属材料。惰性材料应不含硅,防止高温、高水汽分压下释放出硅。 催化剂装填时,通常没有必要对催化剂进行过筛,如果在运输及装卸过程中,由于不正确地作业使催化剂损坏,发现有磨损或破碎现象必须过筛。催化剂的装填无论采取从桶内直接倒入,还是使用溜槽或充填管都可以。但无论采用哪一种装填方式,都必须避免催化剂自由下落高度超过1米,并且要分层装填,每层都要整平之后再装下一层,防止疏密不均,在装填期间,如需要在催化剂上走动,为了避免直接踩在催化剂上,应垫上木版,使身体重量分散在木版的面积上。 一般情况下,催化剂床层顶部应覆盖金属网和/或惰性材料,主要是为了防止在装置开车或停车期间因高的气体流速可能发生催化剂被吹出或湍动,可能由于气体分布不均发生催化剂床层湍动,损坏催化剂。 由于高压,原料气密度较大,为了尽可能的减小床层阻力降,应严格控制催化剂床层高度和催化剂床层高径比。通常催化剂床层高度应控制在3~5m;催化剂床层高径比控制在1.0~1.8。 1.2 开车 1.2.1 升温 为防止水蒸气在催化剂上冷凝,首次开车升温时,应使用惰性气体(N 2、H 2 、 空气或天然气)把催化剂加热到工艺气露点以上温度,最好使用N 2 。 采用≤50℃/h的升温速度加热催化剂,根据最大可获得流量来设定压力,从而确保气体在催化剂上能很好分布。在通常情况下,气体的有效线速度不应小于设计值的50%,但也不应超过设计值。 当催化剂床层温度达到100℃~130℃时,恒温2~3小时排除吸附的物理水,然后继续升温至200℃~230℃时,进行下一步的硫化程度。如果最初加热选用的是空气,在引入硫化气之前,必须用氮气或蒸汽吹扫系统,以置换残余氧气。硫化气的切换基本上在常压或较高压力下进行,这取决于气流的方便。 1.2.2 硫化 与铁铬系催化剂的还原相似,钴钼系耐硫变换催化剂使用前一般需要经过活化(硫化)方能使用,硫化的好坏对硫化后催化剂的活性有着重要作用。 如果工艺气中的硫含量较高,一般使用工艺气直接硫化时,硫化过程中可能发生下述反应: CoO+H 2S ? CoS+H 2 O ?H0 298 =-13.4KJ/mol (1) MoO 3+2H 2 S+H 2 ? MoS 2 +3H 2 O ?H0 298 =-48.1KJ/mol (2) CO+H 2O ? CO 2 +H 2 ?H0 298 =-41.4KJ/mol (3) CO+3H 2? CH 4 +H 2 O ?H0 298 =-206.2KJ/mol (4) 硫化过程为了使产生的热量尽可能小,便于硫化温度控制,在硫化过程中应尽可能地抑制这后两个反应,特别是反应(4),通常催化剂转化成硫化态后,对反应(3)是有利的,但催化剂为氧化态时,并在较高的压力下,即开车的初期
T202型铁钼有机硫加氢转化催化剂的硫化工艺
T202型铁钼有机硫加氢转化催化剂的硫化工艺 T202型铁钼有机硫加氢转化催化剂的硫化工艺 童庆慧,潘利新 (黑龙江黑化集团有限公司,黑龙江齐齐哈尔161041)摘要:介绍了T202 型铁钼有机硫加氢转化催化剂硫化工艺的应用情况,阐述了以CS2为硫化剂时的操作要点,指出在系统外硫化工艺可以提高经济效益,工艺管线改造后使干法脱硫槽可以根据生产实际情况倒换,无需停车。 关键词:焦炉气;硫化反应;硫化剂 中图分类号:TQ 113 文献标识码:A 文章编号:1004-0935(2013)07-0877-03 黑龙江黑化集团有限公司硝铵厂合成氨系统是以焦化厂副产焦炉气为原料生产合成氨,设计生产能力为55 kt/a, 经过技术改造,生产能力达到65kt/a。焦炉气中硫的存在除了会毒害催化剂外,还会腐蚀设备和管道,因此原料气的净化脱硫是很重要的一步。有机硫的脱除多采用加氢转化脱除方法。加氢转化催化剂的作用在于使烃类原料中所含的有机硫化合物产生氢解反应,转化成易于脱除的无机硫(主要是硫化氢),以便进一步除去。焦炉气中有机硫组份较复杂,多用铁钼催化剂。国内常用的铁钼加氢转化多为T202 型,系用γ-Al2O3 担载2.9%~4.3% Fe2O3 和7.5%~10.5% MoO3。 1·催化剂的装填及升温硫化 1.1 催化剂的装填 在加氢转化反应器中,T202 型有机硫加氢催化剂一般分三段填装。按照触媒装填要求,每一层下面覆二层白钢网,网上压大小瓷球各一层,然后装触媒,触媒上再压大小瓷球各一层。最下面一层装触媒106 桶计4.24 t。中层装触媒130 桶计5.2 t。上层连中心管装触媒161 桶计6.44 t。共计397 桶,总计15.88 t。下层装完瓷球后距人孔100 mm,中层距人孔150 mm,上层距中心管上端100 mm。 1.2 催化剂的升温硫化 T202 型催化剂在未硫化前其金属组分铁和钼为氧化态,对一氧化碳含量高的原料气甲烷化副反应较大,同时,对有机硫化物虽有一定活性,但活性不稳定,而且活性较硫化态的低,因此,T202 型催化剂在使用前必须进行硫化处理。 我公司的硫化方法在2007 年以前用焦炉气中的硫进行硫化,之后用二硫化碳作为硫化剂,加到焦炉气中,由于客观条件限制,无法采用循环方式进行硫化,因此二硫化碳用量比循环方式有所浪费。大多数加氢催化剂完成硫化需用硫(0.06~0.09)kg/kg 催化剂,但实际加入硫量需按过量20%左右考虑,即以(0.07~0.11)kg/kg 催化剂为宜,以确保硫化安全,因此我公司购进2 t 二硫化碳作硫化剂。 1.2.1 硫化流程 焦炉气流程:小铁钼→2#铁钼→放空。CS2 流程:干法冷激气→CS2 贮罐→2#小铁钼。 1.2.2 升温硫化时间表(见表1) 1.3 硫化过程 ⑴置换合格后系统引入焦炉气,按升温要求将床层温度升至200 ℃后恒温,恒温期间将各温度点拉齐。 ⑵当床层温度拉齐后开始向系统加CS2,用针型阀控制加入量。并逐渐将压力提至1.0 MPa 以上。 ⑶硫化初期:CS2 加入少量,以工焦气3 000m3/h,入口CS2 浓度2 000×10-6。通过
高温气体除尘技术研究
技术与市场技术应用2019年第26卷第2期 高温气体除尘技术研究 王天宇 (辽宁环宇环保科技股份有限公司,辽宁营口115100) 摘 要:随着科学技术的不断发展,高温气体除尘技术被广泛应用于各个领域。高温气体除尘技术对污染物的过滤具有很强的实际意义。在一定条件下,有必要对高温气体除尘技术进行深入研究。介绍了几种常见的高温气体除尘技术,就高温气体除尘技术及其研究进展进行详细的探讨。 关键词:高温气体;除尘技术;必要性;研究 doi:10.3969/j.issn.1006-8554.2019.02.084 高温气体除尘技术概述 高温气体除尘技术的核心是保护后续工艺设备的平稳运行和气体净化。中等过滤净化和除尘技术在许多高温气体净化和除尘技术中,具有许多重要的优点。实际上,经常使用的圆柱形过滤器的过滤器元件通常由硬质陶瓷或多孔金属制成。中间过滤除尘过程分为两个主要阶段:粉尘气体的过滤和净化以及过滤材料(中间体)的再生。目前,在国内外开发的中型过滤器清洁剂和除尘器中,大多数过滤材料再生采用与过滤方向相反的脉冲反冲流,以去除过滤器元件在生产线上的向后流动,通过落入腔室中实现过滤器元件再生。在线脉冲回收技术在维持过滤元件的正常运行和设备的连续运行方面起着重要作用。脉冲反冲再生条件的变化对过滤元件的寿命具有显着影响。 必要性 在现代工业生产中,高温含尘气体的清洁除尘技术对相关行业非常重要。高温气体除尘技术的研究和开发始于20世纪70年代。传统的除尘方法主要是湿式除尘。首先冷却热气体,然后在冷态下除去灰尘,浪费大量热量。热气直接净化除尘技术是高温气源综合利用的关键技术,也是一种先进的环保技术。目前,直接高温除尘器主要包括高温旋风除尘器,旋风分离器(龙卷风除尘器),多管除尘器和中型过滤除尘器。 高温气体除尘技术种类 3.1 陶瓷高温除尘技术 陶瓷过滤器是高性能的阻隔过滤器,使用陶瓷孔去除灰尘。过滤方法是吸附,表面过滤和深层过滤的组合。过滤原理主要是惯性碰撞、扩散和保留。随着研究的逐步加大,陶瓷高温除尘技术取得了重大进展,主要表现在两个方面:滤芯多样化,各种滤芯,各种条件,主要是陶瓷纤维袋式除尘器、陶瓷纤维毯式过滤器、试管过滤器、蜂窝过滤器等得到改进,改进的目的是改善陶瓷的韧性、延展性和抗热冲击性。制备技术从气泡类型变为网格类型,以减少压降,增加表面积,提高与流体的接触效率,并在流体通过时减少流体重量。 3.2 颗粒层过滤除尘技术 颗粒过滤器集尘器是由具有非常稳定的物理和化学性质的固体颗粒组成的过滤层。惯性碰撞、扩散沉积、重力沉积、直接阻挡和静电吸引,以去除多尘气体。它具有耐高温性、耐用性和其他特性。颗粒层的除尘技术对细尘颗粒的收集效率低,并且大量过滤介质循环到床外,导致高能耗和高磨损。而且,在大规模上,需要研究介质的均匀分布和气流的均匀分布的问题。 中国电力科学研究院开发了一种非筛分式逆流颗粒过滤器,并对大气压高温除尘工艺的结构和参数优化进行了实验研究,开发了一种用于研究大田的颗粒层气体循环清洗系统。颗粒层中的灰尘颗粒的振动运动提出了通过使灰尘颗粒带电并向颗粒层施加外部电场来提高细尘颗粒的除尘效率的方法,并且理论上证明在某些方面它是可行的条件。 3.3 金属微孔过滤除尘技术 金属微孔过滤材料的最大优点是具有优异的耐热性和优异的机械性能,并且由于优异的韧性和导热性而具有优异的抗热冲击性。此外,金属微孔材料具有良好的加工性和可焊性。金属微滤和除尘仍然存在一个问题,即在使用过程中温度受到限制,因为高温下的金属过滤材料具有高强度降低。 3.4 旋风除尘技术 旋风分离器是一种干式振动抑制装置,利用含有灰尘的高速气体产生的离心力将气体和固体分离。本实用新型结构简单,无活动部件,制造安装成本低,操作维护简单,性能稳定,气体浓度和温度低,压力损失小,功耗低,应用广泛。核心部件由高温陶瓷旋风器制成。高温燃烧气体在去除灰尘方面非常有效,并且温度降低受到最低限度的控制以满足工艺生产需要。3.5 静电除尘技术 静电除尘器的原理将是污物颗粒在通过电场和灰尘颗粒的作用,带正电的板中的灰尘颗粒带负电荷的移动后到达板时负电荷被发射,附着由高电压的静电的作用它开始了。集尘板的表面形成灰尘块。然后振动装置撞击板以在污垢积聚上产生冲击力,从而去除灰尘。静电除尘技术是一种有效的除尘技术,具有明显的优势。然而,当前的应用程序从高温和高压环境仍然从如电晕稳定性、材料稳定性和长期运行的材料的热膨胀问题困扰的污垢。静电除尘器昂贵并且具有诸如防尘性和对气体组成和电极腐蚀的敏感性的问题。因此,静电除尘器技术在去除热尘方面存在一定的局限性。 结语 高温气体除尘技术具有很强的现实意义。目前,它还处于研发阶段。需要解决的问题是延长过滤材料的高温寿命,优化过滤材料的再生技术,提高过滤效率。虽然几种常见的高温除尘技术取得了很大进展,但仍存在各自的问题。随着材料及相关科学的发展,高温除尘技术将逐步成熟和完善,具有更广阔的工业应用前景。 参考文献: [1] 姬宏杰,杨家宽,肖波.陶瓷高温除尘技术的研究进展[J].工业安全与环保,2003,29(2):17-20. 3 6 1
高温气体除尘技术及其研究进展
高温气体除尘是在高温条件下直接进行气固分离,实现气体净化的一项技术,它可以最大程度地利用气体的物理显热、化学潜热和动力能以及最有效地利用气体中的有用资源。因此,它不仅成为电力、能源和相关加工工业的研究热点,也是过滤行业的重要研究课题。 目前,整体煤气化燃气蒸汽联合循环发电技术(I G C C )和增压流化床燃烧联合循环发电技术(PFB C )是先进的能源转换系统,但在这两种技术中,煤、飞灰和脱硫吸附剂会夹带在燃烧(气化)产物中,易从燃烧器或气化炉带进燃气轮机。由于进入燃气轮机的气体中含有大量粉尘,会引起燃气轮机叶片的磨损,影响燃气轮机叶片的寿命及工作效率。为了解决这个问题,燃气中的粉尘含量必须限制在一定范围内,同时,为了满足I G C C 和PF B C 对燃气高温的要求,人们正在试图摆脱传统的湿法气体净化工艺,采用高温干法气体净化技术来解决制约I G C C 和PFB C 发展的关键问题。因此,有效的高温除尘技术的作用是至关重要的。 1陶瓷过滤除尘技术 陶瓷过滤器属于高性能阻挡式过滤器,是利用陶 瓷材料的多孔性进行除尘,其过滤元件的过滤是吸 附、表面过滤和深层过滤相结合的一种过滤方式,其过滤机理主要为惯性冲撞、扩散和截留。随着对研究的深入进行,陶瓷过滤除尘技术取得了很大的进展。1.1 过滤元件结构上的多样化 其多样的过滤元件可以满足不同条件的除尘要求,并且不同的过滤元件随着应用的推进而经过了改进,例如,陶瓷纤维布袋过滤器、陶瓷纤维毯过滤器、试管式过滤器、蜂窝式过滤器。1.1.1 陶瓷纤维布袋过滤器 美国B uel l 公司、美国西屋公司以及美国电力研究所等用直径为10μm ~12μm 陶瓷纤维(由质量分数为62%A l 2O 3、24%Si O 2、14%B 2O 3组成)编织成布袋,在816℃、0.98M P a 的条件下,用0.033m /s 的过滤速度进行试验,除尘效率高达99.7%,压力降为176.4P a ~1489.6Pa,清灰时用脉冲空气反吹[1]。1.1.2 陶瓷纤维毯过滤器 美国A cur ex 公司采用直径为3μm 的陶瓷纤维编织成毯,两面再蒙上一层陶瓷纤维布或者不锈钢丝网,在800℃、0.98M Pa 条件下试验,过滤速度为0.1m /s ,除尘效率可达99.9%,清灰时也采用脉冲空气反吹,在高温下反吹5×104次,纤维布和毯的强度仍可满足要求[2]。1.1.3 试管式过滤器 试管式过滤元件为一端封闭、一端开口的圆筒形 结构,典型尺寸为内径(或3),外径6,长为5。过滤气体穿过微孔滤管壁,由外向内流动而实现过滤,在滤管外表面形成粉尘层。早期的陶瓷滤管为单层结构,目前常采用双层结构,内层为平均孔 高温气体除尘技术及其研究进展 刘会雪 刘有智 孟晓丽 (中北大学山西省超重力化工工程技术研究中心,太原030051) 收稿日期作者简介刘会雪(—),女,5年毕业于河南农业大学,在读硕士研究生,主要研究方向为陶瓷膜高温气体除尘。 摘要 介绍了几种常用且有效的高温气体除尘技术及其研究进展,包括:陶瓷过滤除尘技术、颗粒层过 滤除尘技术、金属微孔过滤除尘技术、旋风除尘技术、静电除尘技术,其中,颗粒层过滤除尘技术是最有发展前途的可用于I G C C 和PF BC -C C(增压流化床联合循环)的高温除尘技术之一,指出高温除尘技术需要解决的问题是高温下延长滤材寿命、优化滤材再生技术、提高过滤效率。分析表明,高温除尘技术具有广阔的工业应用前景。 关键词 高温气体除尘 过滤 静电除尘 旋风除尘 文章编号:1005-9598(2008)-02-0014-05中图分类号:T Q 028.2文献标识码:A 第2期(总第135期) 2008年4月 煤化工 Co al Chemical Industry No.2(Total No.135) Apr.2008 40m m 0m m 0m m 1.m :2007-11-22 :1981200
脱硫除尘文献综述
脱硫除尘文献综述 摘要: 除尘和脱硫技术是当前两种主要的烟气污染物控制技术。通过阅读、分析和评估相关工程应用及文献,对现有除尘,脱硫技术进行总结和综述,对常用除尘、脱硫技术进行对比分析,具体分析探讨袋式除尘技术、石灰石-石膏法脱硫技术的原理方法及存在的问题和解决措施。 关键词:除尘;脱硫;烟气;文献综述 引言: 目前中国的一次能源结构仍旧以煤炭为主。2016年,全国煤消费量亿吨,煤炭消费量占能源消费总量的%[1]。煤炭燃烧产生二氧化硫,硫化氢,一氧化氮及粉尘等污染物,对自然环境造成严重污染。为此国家出台更为严格的GB13271-2014锅炉烟气污染物排放标准[2],燃煤锅炉烟气污染物以SO2、粉尘为主,颗粒物排放限值降低至50 mg/m3,,重点地区为30mg/m3;二氧化硫排放限制为300 mg/m3,重点地区为200 mg/m3。目的在于控制大气污染,保证可持续发展。 一除尘技术 1.除尘技术的分类[3] 根据除尘机理的不同,除尘技术可分为机械力除尘技术和电力除尘技术两大类。共同特点是使含尘气体通过力场或电场,力场或电场作用在尘粒上,从而使气体与粉尘分离。 机械力包括重力、离心力、惯性力、冲击、碰撞等,过滤也是机械力的一种。常用的采用机械力除尘技术的设备有:重力沉降室、旋风除尘器、袋式除尘器、文氏管除尘器、重力喷雾塔[4]等。采用电力除尘技术的除尘器有干式电除尘器和湿式电除尘器,区别在于清灰方式的不同,前者采用干法清灰,后者采用湿法清灰。 以上分类仅是依据起主导作用的除尘机理,实际除尘器中,为提高除尘器的效率,往往综合运用了几种不同的除尘机理,如电袋复合除尘器、静电强化的除尘器等。 [3,4]
高温气体除尘技术及其研究进展_刘会雪
高温气体除尘是在高温条件下直接进行气固分离,实现气体净化的一项技术,它可以最大程度地利用气体的物理显热、化学潜热和动力能以及最有效地利用气体中的有用资源。因此,它不仅成为电力、能源和相关加工工业的研究热点,也是过滤行业的重要研究课题。 目前,整体煤气化燃气蒸汽联合循环发电技术 (IG CC)和增压流化床燃烧联合循环发电技术(PFBC)是先进的能源转换系统,但在这两种技术中,煤、飞灰和脱硫吸附剂会夹带在燃烧(气化)产物中,易从燃烧器或气化炉带进燃气轮机。由于进入燃气轮机的气体中含有大量粉尘,会引起燃气轮机叶片的磨损,影响燃气轮机叶片的寿命及工作效率。为了解决这个问题,燃气中的粉尘含量必须限制在一定范围内,同时,为了满足IGCC和PFBC对燃气高温的要求,人们正在试图摆脱传统的湿法气体净化工艺,采用高温干法气体净化技术来解决制约IGCC和PFBC发展的关键问题。因此,有效的高温除尘技术的作用是至关重要的。 1 陶瓷过滤除尘技术 陶瓷过滤器属于高性能阻挡式过滤器,是利用陶 瓷材料的多孔性进行除尘,其过滤元件的过滤是吸 附、表面过滤和深层过滤相结合的一种过滤方式,其过滤机理主要为惯性冲撞、扩散和截留。随着对研究的深入进行,陶瓷过滤除尘技术取得了很大的进展。 1.1过滤元件结构上的多样化 其多样的过滤元件可以满足不同条件的除尘要 求,并且不同的过滤元件随着应用的推进而经过了改进,例如,陶瓷纤维布袋过滤器、陶瓷纤维毯过滤器、试管式过滤器、蜂窝式过滤器。 1.1.1陶瓷纤维布袋过滤器 美国Buell公司、美国西屋公司以及美国电力研究所等用直径为10μm ̄12μ m陶瓷纤维(由质量分数为62%Al2O3、24%SiO2、14%B2O3组成)编织成布袋,在816℃、0.98MPa的条件下,用0.033m/s的过滤速度进行试验, 除尘效率高达99.7%,压力降为176.4Pa ̄1489.6Pa,清灰时用脉冲空气反吹[1]。 1.1.2陶瓷纤维毯过滤器 美国Acurex公司采用直径为3μm的陶瓷纤维编织成毯,两面再蒙上一层陶瓷纤维布或者不锈钢丝网,在800℃、0.98MPa条件下试验,过滤速度为 0.1m/s,除尘效率可达99.9%,清灰时也采用脉冲空 气反吹,在高温下反吹5×104次,纤维布和毯的强度仍可满足要求[2]。 1.1.3试管式过滤器 试管式过滤元件为一端封闭、一端开口的圆筒形 结构,典型尺寸为内径40mm(或30mm),外径60mm,长为1.5m。过滤气体穿过微孔滤管壁,由外向内流动而实现过滤,在滤管外表面形成粉尘层。早期的陶瓷滤管为单层结构,目前常采用双层结构,内层为平均孔 高温气体除尘技术及其研究进展 刘会雪 刘有智 孟晓丽 (中北大学山西省超重力化工工程技术研究中心,太原030051) 收稿日期:2007-11-22 作者简介:刘会雪(1981—),女,2005年毕业于河南农业大学,在读硕士研究生,主要研究方向为陶瓷膜高温气体除尘。 摘 要 介绍了几种常用且有效的高温气体除尘技术及其研究进展,包括:陶瓷过滤除尘技术、 颗粒层过滤除尘技术、金属微孔过滤除尘技术、旋风除尘技术、静电除尘技术,其中,颗粒层过滤除尘技术是最有发展前途的可用于IGCC和PFBC-CC(增压流化床联合循环)的高温除尘技术之一,指出高温除尘技术需要解决的问题是高温下延长滤材寿命、优化滤材再生技术、提高过滤效率。分析表明,高温除尘技术具有广阔的工业应用前景。 关键词 高温气体除尘 过滤 静电除尘 旋风除尘 文章编号:1005-9598(2008)-02-0014-05中图分类号:TQ028.2文献标识码:A 第2期(总第135期) 2008年4月 煤化工 CoalChemicalIndustry No.2(TotalNo.135) Apr.2008
20150409 有机硫加氢、设备及有关计算
有机硫加氢有关计算 一、有机硫加氢内容要点 1、各种原料对硫的限制 表1 工业催化剂工艺气中最低硫含量的要求 工艺气硫含量要求/mg.m-3 (标) CO耐硫变换催化剂入口 H 2 S≥80 CO中变催化剂入口 H 2 S <300 IGCC燃气 H 2 S≤20 管道输送气(天然气、煤气等)总硫≤20 碳酸丙烯酯法、本菲尔法、NHD法脱CO 2 H 2 S≤5 铜洗法脱除微量CO,CO 2 H 2 S≤5 CO低变催化剂入口总硫<1 甲烷化脱除微量CO,CO 2 总硫≤1 氨合成新鲜气总硫≤1 甲醇合成气总硫≤ 0.1 F-T合成油原料气总硫≤ 0.1 醋酸合成气总硫≤ 0.1 醇醚合成气总硫≤ 0.1 MCFC气体总硫≤ 0.1 富CO 2合成甲醇新鲜气硫(以H 2 S计)≤ 0.06 水蒸气制氢预转化催化剂入口总硫≤ 0.05 煤制油低温甲醇洗后合成气总硫≤ 0.05 焦炉气合成LNG 总硫≤ 0.05 2、有机硫加氢副反应 原料或H2中有CO、CO2存在时,可发生甲烷化副反应或羰基硫水解的逆反应等。有CO、CO2和水蒸汽同时存在时,发生CO变换反应。CO 浓度很高时,还可发生歧化副反应,这些都是应该尽量避免的。 CO+3H2CH4+H2O
CO2+H2S COS+H2O CO2+H2CO+H2O CO+H2O CO2+H2 2CO CO2+C 歧化反应生成的碳以碳黑形式沉积在催化剂上,使催化剂的活性降低。 3、加氢反应原理分析 大部分有机硫加氢反应的平衡常数相当大,随温度升高而降低。但由于平衡常数相当大,甚至温度高至500℃时平衡常数仍为正值。所以在工业操作条件下(不大于427℃)反应基本不可逆,不存在热力学限制,即采用较高的操作温度也不致因化学平衡的限制而影响脱硫效果。 加氢反应按反应速率大小,有以下规律: 脱金属> 二烯烃饱和> 脱硫> 脱氧> 单烯烃饱和> 脱氮> 芳烃饱和 噻吩类和其它几种有机硫加氢反应的速度有明显的差别。在被处理的烃中含有几种硫化物时,其加氢速度被其中最难反应的硫化物(实际上就是噻吩类化合物)所控制。 4、催化剂中各种组分的作用 就形态而言,催化剂组份分为三类: (1)无催化活性的Al2O3、CoAl2O4(深蓝色的尖晶石结构,不易被硫化); (2)具有中等活性的CoO、MoO3和CoMoO4(紫色,在加热及含硫化氢的氢气中能硫化生成Co9S8和MoOS的混合物,MoOS通常认为它是MoO2和MoS2的混合物); (3)催化活性较高的钴、钼氧化物的复合物。 催化剂在氧化态时显示出一定的活性,但在变成硫化态以前不可能达到最佳活性。在所有活性组份中,真正的"活性"催化剂是被不可还原的钴促进的MoS2,这是一种四面体结构的络合物。从微观结构上考虑,有机硫化物在钴钼催化剂活性表面上的反应复杂,涉及到硫原子与钼原子的吸附成键,C-S键的断裂,生成烃分子的脱附等诸多步骤。 研究表明,Co-Mo系催化剂中各化学组分的作用如下: (1)MoS2是活性相。 (2)CoO使MoS2晶体分离,减少熔结,使表面积不减少,从而避免活性减退。 (3)Al2O3不仅提供了较大的表面积和孔容,而且由于它的酸性比较弱,减少了烃类的裂解反应和积碳。
高温滤料
新洁环保介绍高温过滤材料的应用及发展趋势 摘要:综述了国内外高温滤料的研究和发展情况,介绍了各种高温滤料的性能及其在相关行业的应用状况,分析了高温滤料的市场前景和技术发展趋势。 关键词:耐高温,过滤材料,纤维,袋式除尘器 1 前言 当前,我国经济已进入高速发展阶段,以资源、能源消耗性为主的重工业(电力、建材、冶金、化工等)迅速发展,我国已成为世界第一大钢铁、水泥、煤炭、化纤生产国;第二大电力、有色金属、化肥生产国。2008年,我国钢铁产量突破5亿吨,约占全球产量的40%,连续23年居世界第1位;水泥产量13.9亿吨,约占全球产量的1/2,连续24年居世界第1位;火电发电量27,793亿千瓦时,仅次于美国,居世界第2位。上述高耗能、高污染产业的发展,带来了严重的环境污染问题,由于空气、水以及工业等环境污染带来的经济损失每年在1000亿元以上,我国“十五”期间用于环境保护的投资为GDP的2.2%。我国近年来废气中主要污染物排放量见表1。 重工业排放的大气污染物以高温烟气为主要特征,烟尘类颗粒物为主要控制对象之一。作为控制总量法规,国家对工业领域的各类锅炉、炉窑制定的排放值陆续进行修订,严格要求其降低排放量。由于袋式除尘技术能使烟气出口烟尘浓度小于30mg/m3,高温烟气排放控制技术已由电除尘技术逐步转变到以袋式除尘技术为主。 袋式除尘器是治理大气污染的高效除尘设备,主要优点是:不受粉尘种类、粒径大小以及粉尘浓度(可高至≥1000g/m3)、比电阻的限制;除尘效率可稳定达到99.5%~99.99%,排放浓度<30mg/m3,甚至<5mg/m3;可有耐常温80℃~130℃、耐高温180℃~260℃、耐腐蚀、拒水防油、防燃防爆、长寿命(1.5~4年)等不同性能的各种滤料供选择;处理风量大,占地面积小,能适应工艺负荷变化和风量的波动;可不停机而分室停风进行维修换袋;可利用原有的电除尘器、效率较低的袋式除尘器的壳体,改造成为新的高效袋式除尘器;结构较电除尘器简单,一次性投资较低,可灵活分室,模块式布置。 袋式除尘器的缺点是:要求控制烟气的温度在滤袋所能承受的范围内,以防止超高温或酸结露损伤滤袋,防止水结露糊袋;袋除尘器本体阻力较电除尘器大,一般为1000~1500Pa,最大为2000Pa;滤料寿命一般为1~3年,每隔数年就需更换滤袋。 在化学、石油、冶金、电力、水泥等工业生产中,会产生大量的高温含尘气体,涉及含尘气体在高温下直接净化除尘和应用的领域十分广泛。 以前高温烟尘的治理主要是采用电除尘器,但随着国家对环保标准的不断提高,特别是近年来国家对烟尘排放标准提高,出口浓度指标为50~100mg/m3,有的地方要求排放浓度<50mg/m3,甚至20~30mg/m3,而电除尘器已难以达到,从而推动了袋式除尘器的应用。近10年来,袋式除尘技术发展迅速,过去在应用中遇到的耐高温、耐腐蚀、抗结露、抗静电过滤材料的许多技术难题已逐步得到解决,袋式除尘技术和产品已完全可以满足当前国内冶金、建材、化工、电力等行业处理各类性质烟气的需要。 高温气体介质过滤除尘技术的核心是高温滤料。滤料是袋式除尘器的关键材料,其优劣直接关系到除尘器性能,一般应满足以下条件:结构合理,粉尘捕集率高;剥离性能好,易清灰,