最新整理铝型材质检规程教学教材
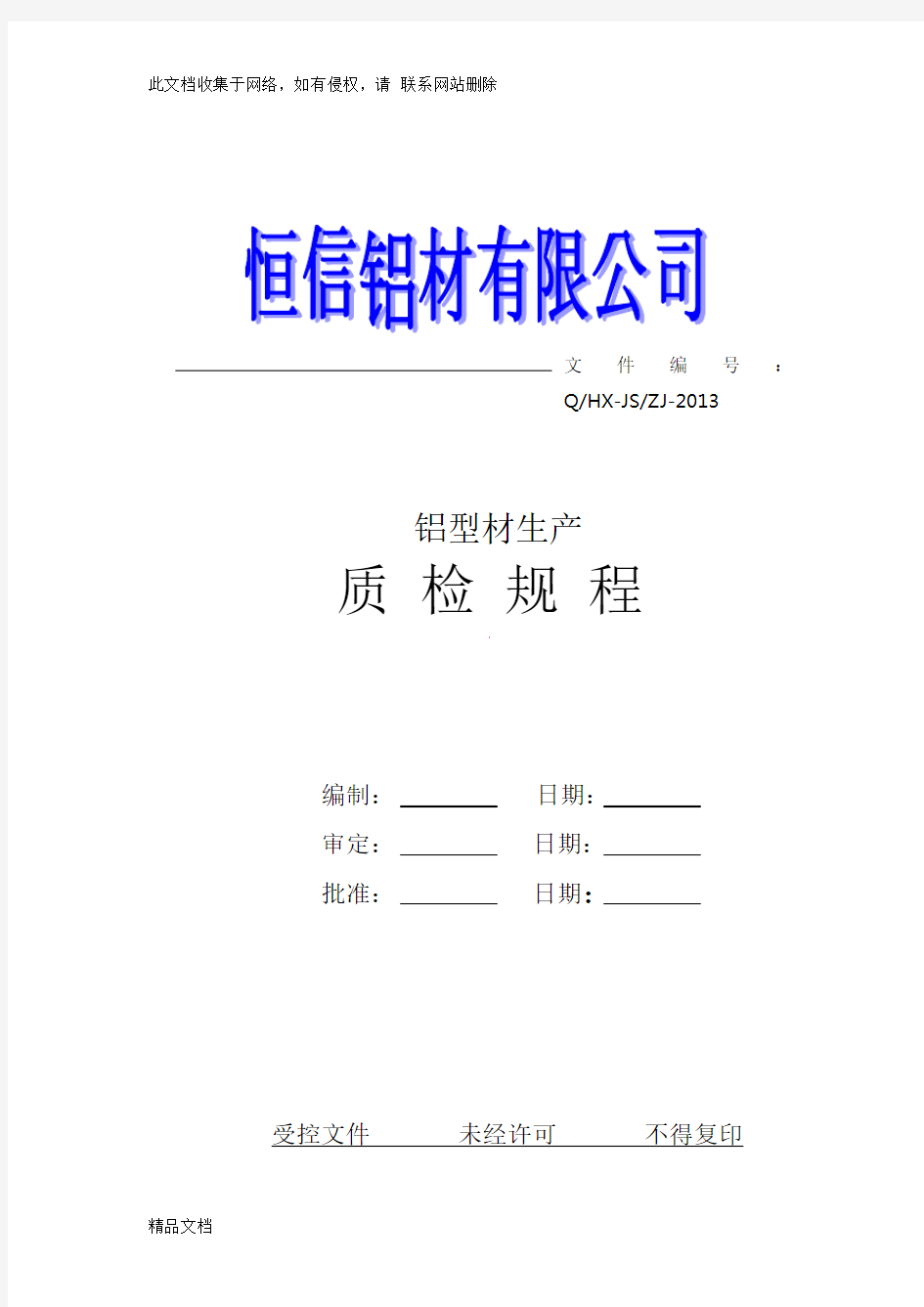

铝型材生产
质 检 规 程
编制: 日期: 审定: 日期: 批准: 日期:
受控文件 未经许可 不得复印
目录
第一部分圆铸锭的检验规程
第二部分型材半成品检验规程
第三部分型材成品检验规程
第四部分《铝合金建筑型材》国家标准GB5237-2008(摘要)
第一部分圆铸锭的检验规程
1.引用标准
GB/T3190-2008 变形铝及铝合金化学成分
YS/T67-2005 变形铝及铝合金圆铸锭
2.检验项目
外观质量、外形尺寸、低倍组织、化学成份、显微组织
2.1外观质量
从每炉料中不同部位任取5根圆铸棒,目视观察,必须符合YS/T67-2005《变形铝及铝合金圆铸锭》外观质量的要求,如果5支样品中有2支或2支以上不合格,即判该批圆铸棒不合格,也可逐根检验,合格交货。
2.2外形尺寸
从每铸次每种规格的圆铸棒中任意抽取5支,对抽取的样本逐支检验,使用钢卷尺,游标卡尺和角尺进行测量,尺寸允许偏差应符合YS/T67-2005《变形铝及铝合金圆铸》,如果5支样品中有2支或2支以上不合格,即判该批圆铸锭不合格,也可逐根检验,合格交货。
2.3低倍组织
每铸次任意抽取一支未经锯切的圆铸锭,去掉铸造开头部分50mm,尾部100mm后,从每根的头、尾各切取一个厚度为20~30mm的低倍试片,检验结果应符合YS/T67-2005《变形铝及铝合金圆铸锭》的低倍组织的要求。
2.4化学成分
铸锭的化学成分应符合GB/T3190的规定
检验方法参见《铝合金成分分析方法》
2.5每批从热处理炉高温区中的两块铸锭上各切一个试样,检验结果不允许有过烧显微组织。
3.铸棒检验规则
3.1外形尺寸
铸棒外形尺寸由车间生产人员自检,检验人员或指定人员每批抽样检验。出现超标由质检部门主持评审。
3.2表面质量
3.2.1铸棒表面质量由车间生产人员自检,检验人员或指定人员每批抽样检验。抽查时存在质量问题通知车间重新自检。
3.2.2铸棒表面存在多条深度大于5mm的但宽度小于1.5mm的裂纹,要限时(三天)限品种(建筑门窗)使用。存在裂纹宽度超过2mm的要挑出报废。
3.2.3铸棒表面有轻微夹渣的要通知生产车间清理干净,严重且不易清除的要挑出报废。
3.2.4铸棒表面存在的其他缺陷能够修整的应交回车间修整,不能修整的报废。
4.检验结果的判定
4.1化学成分分析不合格时,判该批不合格。
4.2尺寸偏差不合格时,判单根不合格,可逐根检验,合格交货,不合格报废。
4.3低倍组织检验参照GB/T3246.2-2000。低倍组织检验不合格时,允许重新取样(去掉料头400mm)进行重复试验,如其中仍有试样不合格,则全批报废。
4.4显微组织检验参照GB/T3246.1-2000。显微组织不合格时,作报废处理。
4.5外观质量不合格时,判单根不合格。
5、包装、标记及运输
5.1铸棒应整齐堆码,防止歪斜弯曲、变形。
5.2标记:铸棒应作好炉号标记。
5.3运输中应防止歪斜。
附: 低倍组织检验
试样评定面应经机械加工,使其表面光滑,必要时可用砂纸磨光。
试样浸蚀前应该用酒精或丙酮清洗干净。
1.低倍检验试样浸蚀
铸造铝合金的试样清洗干净后用80-120g/l氢氧化钠水溶液浸蚀,浸蚀时间与温度有关,,推荐温度为20-30度,时间10-30分钟。
变形铝合金(加工制品)的试样采用150-250g/l的氢氧化钠水溶液浸蚀,在10-35度室温下浸蚀,浸蚀时间20-30分钟。以能清晰显示组织缺陷为准。
焊缝和氧化膜检测时间相应增加1-2倍。
试样在以上溶液中浸蚀后,快速转入清水中冲洗,再放入20-30%(V/V)硝酸水溶液中光洗,除去黑色碱蚀产物,酸洗后再经流动的清水冲洗干净,即可进行检查。
2.宏观晶粒度检测试样浸蚀
对于软铝合金样品,用特强混合酸溶液(HF:HNO3:HCl=1:5:15ml)浸蚀一段时间后立即用水冲洗,反复进行,直至晶粒清晰呈现为止。
对于硬铝合金样品可用150-250g/l氢氧化钠水溶液,也可用高浓度混合酸溶液(HF:HNO3:HCl:H2O=10:5:5:380ml)进行浸蚀。浸蚀方法同上所述。
3.判定
3.1晶粒度:一级晶粒度晶粒平均面积0.026mm2,二级晶粒度晶粒平均面积0.40mm2,三级晶粒度晶粒平均面积1.2mm2,四级晶粒度晶粒平均面积2.6mm2,五级晶粒度晶粒平均面积8.0mm2,六级晶粒度晶粒平均面积16mm2,七级晶粒度晶粒平均面积36mm2,八级晶粒度晶粒平均面积80mm2。
3.2缺陷分类:疏松、气孔、夹渣、裂纹、羽毛晶、光亮晶等。
第二部分型材半成品检验规程
1.检验项目
当班生产型材的装配性、表面质量、角度、几何尺寸、定尺长度、锯口质量等。
2.检验计量器具
卡尺、千分尺、卷尺、万能角度尺、R规、塞尺等。
3.检验标准
产品图纸
GB5237.1-2008 铝合金建筑型材第一部分基材
4.1化学成份
铝棒化学成分按内控标准执行。
4.2力学性能
型材硬度:常规料≧10HW。硬度偏低,退回挤压重新时效。重新时效后,低于8HW的报废处理,大于8 HW的可让步放行。
工业材:根据客户要求。硬度偏低重新时效;硬度偏高可退火处理。
6063T5 抗拉强度≥160MPa,屈服强度≥110MPa。延伸率≥8%。
参见室温拉伸试验方法GB/T228-2002
4.3尺寸要求
4.3.1型材的横截面尺寸允许偏差
建材横截面尺寸允许偏差一般按高精级和超高精级验收。
GB5237.1非壁厚允许偏差
客户另有要求的按客户要求执行。
压线和压盖类的型材除满足图纸公差要求外,还需实际装配一下,以不松不紧为宜,压不进或压进后可脱落的皆为不合格。
有配合关系的型材,主型材配合尺寸偏差应符合超高精级,辅助型材相应的配合尺寸的偏差应满足配合要求。幕墙型材立柱与插芯的配合间隙在0.3-0.8mm(双边),门窗、含幕墙开启窗、组角料与角码配合间隙在0.2-0.6mm (双边)。
图纸中不标注偏差值但可以直接测量的部位的尺寸,其允许偏差按高精级验收。
4.3.2型材角度允许偏差
按±0.5O执行,挤角用角铝的角度允许偏差按±0.25O执行,特殊要求在合同中注明。
4.3.4型材的曲面间隙
0.13*弦长/25
4.3.5型材的弯曲度
4.3.6型材的扭拧度
4.3.7型材长度允许偏差
一般型材按+15mm,隔热料和幕墙料按+5~+10mm。
以倍尺交货的需要加锯口余量,应在合同中注明。
按客户要求定尺。
4.3.8端头切斜度允许偏差
≤2o
4.4外观质量
4.4.1型材表面应整洁,无明显手感(机械纹),不允许有裂纹、起皮、腐蚀和气泡等缺陷存在。
4.4.2型材表面上允许有轻微的压坑,碰伤和擦伤存在,其允许深度见下表,模具挤压痕的深
4.5判定原则
4.5.1化学成分不合格时,判整批不合格。尺寸、外观质量不合格时,为单件不合格,允许逐根检验,合格交货。
4.5.2力学性能有一个不合格时应从该批中另取4个试样复检,复检结果仍有一个不合格时,判全批不合格,也可逐根检验或重复热处理,重新取样。
5.检验规则
5.1首检
挤压工序班长(自检员)对挤压开始前三支(棒)型材应仔细检查几何尺寸、形位尺寸、实物装配和表面质量,符合图纸和标准才可以继续批量生产。对产品质量有异议时,通知巡检员判定。新产品、新模具试模、试产时,班长要仔细检查产品质量,并及时通知巡检员到场,判定能否生产。
5.2挤压过程检验
5.2.1挤压工序班长在每挤10-15支棒(大机取下限,小机取上限)检查一次几何尺寸、实物装配和表面质量,型材质量变化后不符合标准的应通知生产人员停止生产更换模具,并对报废型材作好废品标识。巡检员要加强每台机的巡检力度,发现不合格品出现要及时通知机台停产,防止出现批量报废。
5.2.2生产人员负责检查型材的表面质量。机手和中断人员应随时检查出口处型材的表面质量,矫直人员应随时检查滑出台、冷床、矫直机和锯台上型材的表面质量,锯切人员应翻面检查型材的表面,监视和保证挤出型材在各个移动环节和操作过程不受到损伤和变形。
5.2.3挤压工序班长、巡检员对有装配要求的型材要进行试验检查,对于喷涂后有装配关系的型材配合部位尺寸,要考虑漆膜厚度(0.06-0.12mm),批量生产前,要考虑涂层厚度余量或试喷试装配合格后再批量生产。
5.2.4挤压机台班长、巡检员对用于氧化着色处理的容易出现焊合线、亮晶带的型材应在首检中取样碱蚀试验,检验合格后才可以批量生产。在挤压过程中每20-50(大机取下限,小机取上限)支棒要取样实验一次。机台班长、巡检员对容易出现喷涂印痕的品种要取样用自喷漆试喷,看是否存在喷涂印痕。
5.2.5挤压班长在型材定尺锯切时要对型材的几何尺寸和表面质量进行抽查,同一模具生产的型材第一锯锯切产品要全面检查几何尺寸和表面质量,锯切中应抽查1-3次几何尺寸,随时检查型材表面质量。对于开口尺寸要在矫直过程中测量,调直幅度大易造成变形的型材要配合矫直人员有效调整控制,幕墙和高档工业材要每支检查弯曲度和扭拧度。
5.2.6班长、巡检员、锯切操作手应随时检查型材装筐表面质量、定尺长度。
5.2.6时效工每炉、每框两头上、中、下、左、右全面检查时效冷却后基材的硬度,确保
硬度符合要求。不合格可重复热处理,也可逐根检验。
5.3巡视检查和基材验收
质量巡检员负责挤压工序各机台质量的巡视检查和基材验收。巡视检查内容:抽查产品、机台操作员自检情况,执行规程情况、首检和过程检验。
5.3.1力学性能检查。
抽查时效产品的硬度。用韦氏硬度计检查,检查时对框中型材两端的四个边角点都检查。5.3.2尺寸偏差和外观质量检查。
流转卡签字前,仔细检查料框中产品是否有扭拧现象,料头是否变形,料口是否修整,必要时通知班组整改。发现有不合格时,再取双倍检查;不合格时,通知班组人员逐根检查,合格者验收。
5.3.3填写挤压检验原始记录。
5.3.4填写基材验收报告。当基材用于直接出厂销售时,直接填写成品验收报告。
5.3.5有特殊要求的工业型材的检验按特殊要求执行。
5.3.6巡检员对流转至下工序的每一框基材的产品质量负总责。
6 标志、包装、运输、贮存
6.1向下工序转序的基材,每框必须附挤压工序生产流程卡。
6.2直接出厂销售的基材包装按照生产单上注明的要求执行,外包装无论采用何种方式,均应包扎紧固,防止在移动中摩擦。
6.3基材在运输过程中应防碰擦伤、防水、防潮。
第三部分型材成品检验规程
1.主要内容与适用范围
1.1本标准规定了成品型材检验对象、检验项目、抽样数量与方法、检验频次、检验方法、采用仪器与设备、判定原则与报告。
1.2本标准适用于公司质量管理部对成品的检验
2.引用标准
GB5237.1-2008 铝合金建筑型材第一部分基材
GB5237.2-2008 铝合金建筑型材第二部分阳极氧化、着色型材
GB5237.3-2008 铝合金建筑型材第三部分电泳涂漆型材
GB5237.4-2008 铝合金建筑型材第四部分粉末喷涂型材
GB5237.6-2012 铝合金建筑型材第六部分隔热型材
3.检验对象
本标准规定检查的成品是指未经检验的工业材、氧化电泳型材、喷涂型材、隔热型材。
4.检验项目
第一章阳极氧化、着色型材
每批阳极氧化、着色型材均应进行化学成分、尺寸、力学性能、外观质量以及氧化膜厚度、封孔质量及氧化膜颜色、色差的检验。耐磨性、耐蚀性、耐候性采用(每1-3年一次)外协检验方式,一般不检验。
注:封孔质量的现场检验:对成品料用签字笔将墨水涂在型材表面上,过一分钟后用手擦掉无痕迹(或仅仅稍有一点点极为轻微的变色)为合格。
封孔质量的定量检测方法:
硝酸预浸的磷-铬酸法
硝酸预浸溶液:650ml硝酸(ρ=1.4g/l)于1000ml容量瓶中,用水稀释至刻度。
磷-铬酸溶液:取20g结晶三氧化铬(CrO3)和35ml磷酸(1.7g/ml),在容量瓶中用蒸馏水(或去离子水)稀释至1000ml。
型材取样其有效面积约1dm2(最小0.5 dm2),通常质量不超过200g,用锯片去掉表面毛刺,用酒精(或其它有机溶剂)对试样表面进行脱脂。干燥后,立即称重(a),称准至0.1mg。将试样直立地完全浸入温度为19±1℃的预浸溶液中,保持10min,取出用自来水洗净,再用蒸馏水彻底洗净。将试样直立地完全浸入预先加热至38±1℃磷-铬酸溶液中浸泡15分钟(使用水浴或连续搅拌以保证溶液温度均匀)。取出洗净干燥称重b(室温空气干燥5分钟,60度烘箱干燥15分钟,干燥器内干燥冷却30分钟),根据前后称量差a-b及有效反应面积S,计算结果,判断封孔质量。 (a-b)/S (mg/dm2)