产品检验流程图

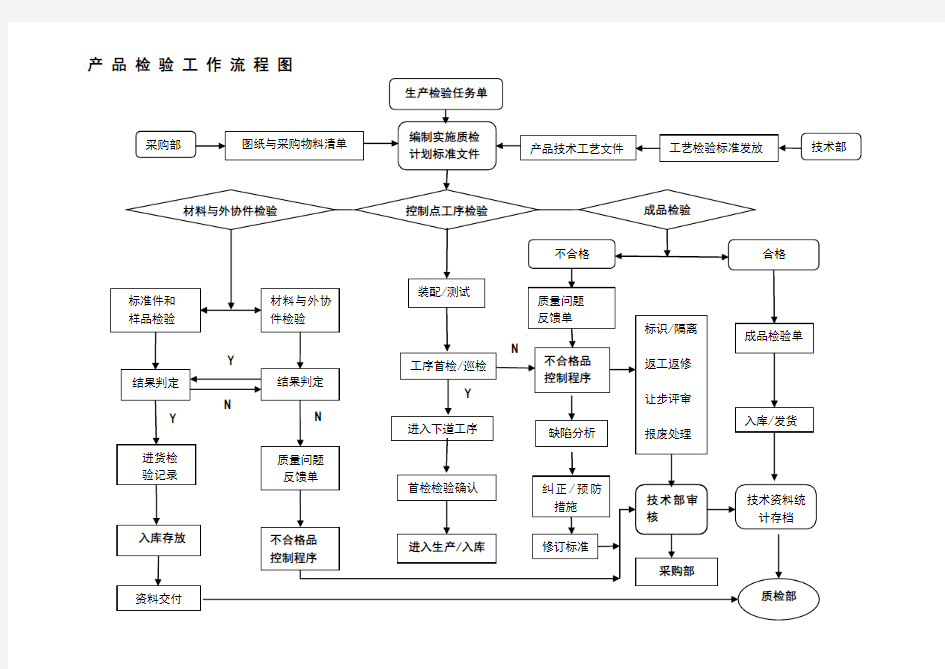
产品检验工作流程说明:文件编号:
产品检验工作流程图
产品质量检验标准及流程
产品质量检验标准及流程 (初稿)◆目的:规格质量检验流程,保证产品出货质量;◆适用范围:与本公司合作的供应商;◆质量检验标准:1、MIL-STD-105E 一次正常抽样二级水平2、ANSI/ASQC-Z1.4 ◆允收水准:MIL-STD-105E.II.(如下图,详细的参考AQL表) 缺点AQL AC RE CRI 0 MAJ 0.65 MIN 2.5 ◆检验方式:抽检、全检;抽检:抽检箱数以货物箱数的开平方取整数;抽检数量以货物数对AQL表定;◆检验流程:1、数量:数量分为货物总箱数和单个箱的产品数(如有内箱的需检查内箱数);清点数量的时候,须先清点货物的总箱数,与单上的数量箱数是否一致。再抽点箱子里的产品数量跟单子指定的每箱数量是否一样。如发现有误须马上指出并将检查结果记录下来;2、包装:检查货物的包装是否稳实,包装带打的是否牢固。原则上以在运输过程中不会造成对产品的损坏为考虑的首要因素。如检查发现有问题,须马上指出并将结果记录下来;3、唛头:仔细核对订单上的唛头与外箱的唛头是否一致。如发现有误须马上指出并将检查结果记录下来;4、产品质量检查,以严谨认真的态度,对产品的外观和功能以及是否会对人畜造成伤害等各方面进行检验。并将检验情况记录下来。具体的检验方法,参看下面产品检验方法;5、根据检验情况,填写检验报表。依据AQL 标准,作出合格与否的决定。◆产品检验方法■、参照客户确认的样板进行检验;A、外观■五金类外观方面需要注意以下几点:1、产品表面有否生锈、伤痕或刮花现象;2、接口吻合部份连接是否紧密;3、套接或旋转是否灵活,无阻碍;4、电镀产品,有否色差、汽泡或掉镀现象,镀层和镀色是否均匀;5、客户需印的LOGO是否清楚。有否漏字、错字、图案不全或错误现象。6、检查里面的电池是否干净,有否绝缘片。有否发莓或锈斑现象;■塑胶类外观方面需要注意以下几点:1、产品表面有否伤痕或刮花现象;2、接口吻合部份连接是否紧密;3、套接或旋转是否灵活,无阻碍;4、喷油、烤漆或电镀产品,有否汽泡或掉油、掉漆、掉镀现象,镀层和镀色是否均匀,有否色差现象;5、客户需印的LOGO是否清楚。有否色差、漏字、错字、图案不全或错误现象。6、检查里面的电池是否干净,有否绝缘片。有否发莓或锈斑现象;7、透明产品,查看透明度是否良好。有否杂质、黑点;8、产品有否披锋。披锋情况是否严重;■带子类外观方面需要注意以下几点:1、长度是否够;2、带子边缘是否整齐,无漏线、脱线或掉线现象;3、带子颜色是否有色差;4、带子的材料与样板材料是否一样;■水晶类外观方面需要注意以下几点:1、产品表现是否光滑、有否伤痕、刮伤、缺口现象;2、倒角是否均匀,倒角宽度是否在允可的范围内;3、产品的透明度是否好。产品里面是否有杂质、黑点或汽泡现象;4、内雕产品,雕刻图案是否完整清楚;■磁力扣外观方面需要注意以下几点:1、封胶是否均匀无杂质、黑点;2、印刷颜色是否有色差;3、产品线路板边缘磨合是否良好、整齐;■彩卡需要注意以下几点:1、卡纸的规格是否和样品的一样;2、彩卡的印刷颜色是否一样,有否色差;3、印刷图案和文字是否和样品一样。有否错字、漏字和印错图案,图案不全现象;■吸塑外观方面需要注意以下几点:1、吸塑规格是否和样品一样;2、吸塑表面是否干净、无杂质、无黑点;注意事项:1、印刷LOGO:抽10PCS用专业胶纸(3M600)测试印刷的LOGO,有否掉色现象。如有,3个以下为通过。3个以上要整批货返工重新印刷;2、五金件边缘是否整齐光滑,有否披锋。有否对人会造成致命伤害的可能存在,如有,AQL表里列入CRI。无论货物的数量多少,整批货需要返工;3、外观严重视为重缺陷,AQL表里列入:MAJ;B、功能■发光棒1、检验按键开关是否灵敏,按动是否灵活。2、灯光颜色是否有色差、灯光有否偏暗;3、有否缺灯或灯不亮现象;4、灯光闪动是否按订单要求的闪法;5、电池电压是否足、有否短路现象以及电池周围是否用绝缘片封套6、磁力扣产品要注意看灯光位置是否居中(如五角星)。7、线路板焊接是否牢固,使用过程中有否会掉落或松开的可能;8、对于棒类产品。要查看一端旋进的过程中会否顶到灯头以致影响功能的可能;C、生产过程中之货物检验如检验的时候,产品还没完成,正在制作过
质量检验流程图
产品质量检验流程图 1.产品质量检验流程与风险控制图 产品质量检验流程与风险控制 业务风险 不相容责任部门/责任人的职责分工与审批权限划分 阶段 总经理 技术总监 质量管理部 各生产单位 D1 D2 D3 审核 如果没有规范的产品质量检验标准和操作规范,企业生产的产品质量就得不到有效保障 如果对产品质量检验的每个环节把关不 严,产品质量就会受到影响,企业形象和消费者利益也会受到损害 如果不对产品存在的 质量缺陷和问题进行反思总结,产品的质量就得不到有效改善,最终将不利于企 业的长远发展 制定质量检验标准 结束 1 审批 原材料检验 在制品检验 产成品检验 开始 进行生产 审核 审批 执行质量检验标准 配合工作 修订质量检验标准 及操作规范 3 4 5 制定《质量检验 操作规范》 2 编写《年度质检 总结报告》 6
2.产品质量检验流程控制表 产品质量检验流程控制 控制事项详细描述及说明 阶段控制D1 1.质量管理部会同相关部门及专业人员参考国家标准、行业标准、国外标准、客户需求及本身制造能力等,严格制定产品质量检验标准,并报技术总监审核、总经理审批2.质量管理部应制定《质量检验操作规范》,对原材料、在制品、产成品的检查项目、质量标准、检验频率、检验方法及使用仪器设备等进行详细说明 D2 3.原材料购入时,仓库管理部门应依据相关规定办理收料,并通知质量管理部人员进行检验,质量管理部检验人员应依照原材料质量标准及检验规范的规定完成检验,对不 符合质检要求的原材料进行相应的退换货处理 4.质量管理部检验人员对制造过程的在制品均应依照在制品质量标准及检验规范实施质量检验,以提早发现问题并迅速处理,确保在制品质量 5.质量管理部检验人员应依照产成品质量标准及检验规范实施质量检验,以提早发现问题并迅速处理,以确保产成品质量 D3 6.质量管理部应每年提交《年度质检总结报告》,对本年度产品质量检验的标准、规范及执行情况进行总结,并提出产品质量检验标准及检验规范的修订意见 相关规范应建 规范 《产品质量管理制度》 《产品质量检验操作规范》 参照 规范 《企业内部控制应用指引》 《中华人民共和国产品质量法》 文件资料 《产品质量操作规范》 《年度质检总结报告》 责任部门及责任人 质量管理部、相关部门 总经理、技术总监、质量管理部经理
质量控制流程图
3.1.1 现场质量控制流程图 施工准备 项工程施工计划施工方案 工程质量控制指标 检验频率及方法 材料、机械、劳动力、现 场管理人员准备 分项开工报告 批准 分项开工批复单 每道工序施工 施工测量放线 报告 检验试验报告设计施工复核 不批准 分析原因,及时修复改正或返工 材料检查工艺流程检查测量检测试验检测质检工程师检查 自检结果 工序交接报告 不合格 抽样检查资料检查试验抽测测量检测工序检验记录检查 交工报告 不合格 合格 交工证书 现场质量控制流程图
3.1.2 质量管理组织机构流程图 指挥长 生产副指挥长 质量安全 总工程师 材 料 厂 科 程 工 安全质量 试 验 室 指挥部质管 工程师 质量安全 委员会办 指挥部质管 工程师 工 程 队 队 程 工 程 队 工 质量管理组织机构流程图
3.1.3 质量检验总流程图 原材料取样 不 合 标准试验格 试验结果评定、是否合格 试验报告 实施控制检验 成品抽样检验 试验结果评定、是否合格 合格不合格 作业结论分析原因 结束提出处理意见 质量检验总流程图
3.1.4 工程材料、构配件和设备质量控制流程图 承包单位填写 《工程材料/构配件/设备报验单》 方法: 承包单位另选不合格 监理工程师审核 合 格 1.审核证明资料 2.到厂家考察 3.进场材料检验 4.进行验证复试承包单位使用 工程材料、构配件和设备质量控制流程图
3.1.5 技术质量主要工作流程图 图纸会审 参加设计交底 编制施工组织设计工程师审批 工程物料确认 进场验收 技术复核 分部工程验收 技术交底工程定位交接 甲方、监理确认工程师确认 隐蔽验收质量验收 资料审核 甲方、乙方、设计联合验收 交付使用送交资料和竣工图 回访维修 技术质量主要工作流程图
质量检验流程图
产品质量检验流程图 1. 产品质量检验流程与风险控制图 产品质量检验流程与风险控制 不相容责任部门/责任人的职责分工与审批权限划分阶业务风险 总经理技术总监质量管理部各生产单位段如果没有规范的产品开始 质量检验标准和操作 审批规范,企业生产的产 品质量就得不到有效 保障 如果对产品质量检验 的每个环节把关不 严,产品质量就会受 到影响,企业形象和 消费者利益也会受到 损害 如果不对产品存在的 审批质量缺陷和问题进行 反思总结,产品的质量 就得不到有效改善, 最终将不利于企业的 长远发展 1 审核制定质量检验标准 2 制定《质量检验 操作规范》 执行质量检验标准 3 原材料检验 4 在制品检验 5 产成品检验 6 编写《年度质检 审核 总结报告》 修订质量检验标准 及操作规范 结束 D1 进行生产 配合工作 D2
D3 2. 产品质量检验流程控制表 产品质量检验流程控制 控制事项详细描述及说明
1. 质量管理部会同相关部门及专业人员参考国家标准、行业标准、国外标准、客户需求 及本身制造能力等,严格制定产品质量检验标准,并报技术总监审核、总经理审批D1 2. 质量管理部应制定《质量检验操作规范》,对原材料、在制品、产成品的检查项目、质 量标准、检验频率、检验方法及使用仪器设备等进行详细说明 3. 原材料购入时,仓库管理部门应依据相关规定办理收料,并通知质量管理部人员进行 阶 检验,质量管理部检验人员应依照原材料质量标准及检验规范的规定完成检验,对不段 符合质检要求的原材料进行相应的退换货处理 控 D2 4.质量管理部检验人员对制造过程的在制品均应依照在制品质量标准及检验规范实施质制 量检验,以提早发现问题并迅速处理,确保在制品质量 5.质量管理部检验人员应依照产成品质量标准及检验规范实施质量检验,以提早发现问 题并迅速处理,以确保产成品质量 6.质量管理部应每年提交《年度质检总结报告》,对本年度产品质量检验的标准、规范及D3 执行情况进行总结,并提出产品质量检验标准及检验规范的修订意见相应建《产品质量管理制度》 关规范《产品质量检验操作规范》 规参照《企业内部控制应用指引》 范规范《中华人民共和国产品质量法》 《产品质量操作规范》 文件资料 《年度质检总结报告》 责任部门及责任人质量管理部、相关部门 总经理、技术总监、质量管理部经理
产品质量检验流程
产品质量检验流程
1.产品质量检验流程与风险控制图 产品质量检验流程与风险控制 不相容责任部门/责任人的职责分工与审批权限划分 业务风险
总经理 技术总监 质量管理部 各生产单位
阶 段
如果没有规范的产品 质量检验标准和操作 规范,企业生产的产 品质量就得不到有效 审批 审核
开始 1 制定质量检验标准 2 制定《质量检验 D1 操作规范》
保障
如果对产品质量检验 的每个环节把关不
执行质量检验标准
3 严,产品质量就会受 到影响,企业形象和 消费者利益也会受到 损害 产成品检验 D2 6 如果不对产品存在的 审批 质量缺陷和问题进行 反思总结,产品的质 量就得不到有效改 善,最终将不利于企 结束 业的长远发展 D3 审核 编写《年度质检 总结报告》 》 修订质量检验标准 及操作规范 在制品检验 5 原材料检验 4 配合工作 进行生产
2.产品质量检验流程控制表 产品质量检验流程控制
控制事项 详细描述及说明 1.质量管理部会同相关部门及专业人员参考国家标准、行业标准、国外标准、客户需求 及本身制造能力等,严格制定产品质量检验标准,并报技术总监审核、总经理审批 D1 2.质量管理部应制定《质量检验操作规范》 ,对原材料、在制品、产成品的检查项目、质 量标准、检验频率、检验方法及使用仪器设备等进行详细说明
3.原材料购入时,仓库管理部门应依据相关规定办理收料,并通知质量管理部人员进行 阶 段 控 D2 制 4.质量管理部检验人员对制造过程的在制品均应依照在制品质量标准及检验规范实施质 量检验,以提早发现问题并迅速处理,确保在制品质量 5.质量管理部检验人员应依照产成品质量标准及检验规范实施质量检验,以提早发现问 题并迅速处理,以确保产成品质量 检验,质量管理部检验人员应依照原材料质量标准及检验规范的规定完成检验,对不 符合质检要求的原材料进行相应的退换货处理
6.质量管理部应每年提交《年度质检总结报告》 ,对本年度产品质量检验的标准、规范及 D3 执行情况进行总结,并提出产品质量检验标准及检验规范的修订意见
相 关 规 范
应建 规范
? 《产品质量管理制度》 ? 《产品质量检验操作规范》 ? 《企业内部控制应用指引》 ? 《中华人民共和国产品质量法》
参照 规范
? 《产品质量操作规范》
文件资料
? 《年度质检总结报告》
责任部门 及责任人
? 质量管理部、相关部门 ? 总经理、技术总监、质量管理部经理
最新整理建设工程质量监督工作流程图.doc
一、建设工程质量监督工作流程图 二、土建工程部分质量监督工作要点 (一) 熟悉图纸,制定监督方案和监督交底书。 (二) 现场工程质量监督交底、对参与各方资质以及承包范围、人员资格检查、参与施工许可证的发放。 (三) 检查图纸会审、设计交底工作情况( 尽量参与图纸会审、明确构造柱的具体位置及质量通病防治技术措施等) ; (四) 检查施工组织设计或方案,督促落实相关质量保证措施;检查开工报告、施工现场质量管理检查记录。 (五) 审查地基、钢结构、结构实体质量抽测等重要的工程检测方案,对检测方案进行备案归档。 (六) 基础验槽或检查试桩或桩基施工质量。 (七) 监督抽检基础部分的材料(材料监督抽检 1 次以上,同时检查现场材料送检频率、先检后用的情况)。 (八) 监督检查地基中验及中验登记(检查总监及施工项目经理到位情况、检查工程质保资料及监理资料、检查地基外观 质量)。 (九) 检查基础或地下室 ( 人防 ) 钢筋隐蔽工程(检查工程质保资料及实体质量)。 (十) 监督检查地下结构中验及中验登记(检查总监及施工项目经理到位情况、检查工程质保资料及监理资料、检查地下结构外观质量及防水质量)。
(十一) 检查首层结构及转换层钢筋隐蔽工程(检查工程质保资料及实体质量)。 (十二) 抽查标准层钢筋隐蔽工程(检查工程质保资料及实体质量)。 (十三) 检查首次砌筑质量(检查砌体材料、砌筑质量、构造柱设置等)。 (十四) 检查屋面层钢筋隐蔽工程(检查工程质保资料及实体质量)。 (十五) 主体部分的材料监督抽检(监督抽检 2 次以上,同时检查现场材料送检频率、先检后用的情况)。 ( 十六) 检查监理及施工的工程质量报告(针对工程质量报告提出的问题进行跟踪处理,质量问题跟踪处理资料及时归档)。 (十七) 主体结构外观质量检查(检查工程实体质量及质保资料,检查结构实体抽测报告)。 (十八) 监督检查主体结构中验及中验登记(检查总监及施工项目经理到位情况、检查质保资料及监理资料)。(十九) 监督检查建筑节能围护结构中验及中验登记。 (二十) 监督检查人防工程专项验收。 (二十一) 参加工程竣工验收前初检(发出抽查通知书或整改通知书)。 (二十二) 审查工程竣工验收资料、审查工程竣工验收条件。 (二十三) 监督工程的竣工验收。 (二十四) 制定工程质量监督报告。 (二十五) 审查工程竣工验收备案资料,协助工程竣工验收备案。 (二十六) 工程监督资料归档。 三、建筑设备工程部分质量监督工作要点 (一)熟悉图纸及审查报监资料,制定监督方案和监督交底书。 (二)参与施工许可证的发放,进行建筑设备工程质量监督交底,检查各参建单位的资质、人员资格、承包范围等质量行为情况。 (三)检查图纸会审情况。 (四)抽查建筑电气工程接地装置隐蔽验收情况。 (五)抽查各预埋管道、预埋件(含套管)、吊顶内各管道或管线、防雷引下线和均压环(带)、直埋电缆等安装工程的隐蔽验收情况。 (六)抽查防雷接闪器安装工程隐蔽验收情况。 (七)进行建筑设备工程质量二次监督交底,检查各分包单位资质、人员资格等质量行为情况;审查原材料进场检验方案。 (八)原材料监督抽检,并检查原材料进场检验方案的执行情况,对照检测报告检查现场材料的使用情况,材料先检后用的情况。 (九)现场监督抽测建筑电气工程接地电阻、绝缘电阻。 (十)现场监督检查备用电源(即柴油发电机组)的空载及带负荷试运行试验情况。 (十一)检查监理及施工的工程质量报告,针对工程质量报告提出的问题进行跟踪处理; (十二)跟踪落实材料不合格、现场不按图施工等质量问题的处理。 (十三)监督检查人防工程(设备部分)专项验收; (十四)监督检查低压配电分部工程中间验收:检查施工质量保证资料、监理资料,检查总监、施工项目经理到位情况,重点检查现场的施工图设计文件实施情况,出具低压配电中间验收登记表 (十五)审查电梯安装工程开工登记资料。 (十六)检查电梯工程安装质量,开具电梯检测通知书,审查电梯工程验收资料,出具电梯工程验收登记表。 (十七)组织本地区建筑设备工程季度质量大检查。 (十八)参加工程竣工验收前检查(初检)。 (十九)审查工程竣工验收资料,审查工程竣工验收条件。 (二十)监督工程竣工验收。
质量检验流程图
产品质量检验流程图
1.产品质量检验流程与风险控制图 产品质量检验流程与风险控制 不相容责任部门/责任人的职责分工与审批权限划分 业务风险
总经理 技术总监 质量管理部 各生产单位
阶 段
如果没有规范的产品 质量检验标准和操作 规范,企业生产的产 品质量就得不到有效 审批 审核
开始 1 制定质量检验标准 2 制定《质量检验 D1 操作规范》
保障
如果对产品质量检验 的每个环节把关不
执行质量检验标准
3 严,产品质量就会受 到影响,企业形象和 消费者利益也会受到 损害 产成品检验 6 如果不对产品存在的 审批 质量缺陷和问题进行 反思总结,产品的质 量就得不到有效改 善,最终将不利于企 结束 业的长远发展 D3 审核 编写《年度质检 总结报告》 》 修订质量检验标准 及操作规范 在制品检验 5 D2 原材料检验 4 配合工作 进行生产
2.产品质量检验流程控制表 产品质量检验流程控制
控制事项 详细描述及说明 1.质量管理部会同相关部门及专业人员参考国家标准、行业标准、国外标准、客户需求 及本身制造能力等,严格制定产品质量检验标准,并报技术总监审核、总经理审批 D1 2.质量管理部应制定《质量检验操作规范》 ,对原材料、在制品、产成品的检查项目、质 量标准、检验频率、检验方法及使用仪器设备等进行详细说明
3.原材料购入时,仓库管理部门应依据相关规定办理收料,并通知质量管理部人员进行 阶 段 控 制 检验,质量管理部检验人员应依照原材料质量标准及检验规范的规定完成检验,对不 符合质检要求的原材料进行相应的退换货处理 D2 4.质量管理部检验人员对制造过程的在制品均应依照在制品质量标准及检验规范实施质 量检验,以提早发现问题并迅速处理,确保在制品质量 5.质量管理部检验人员应依照产成品质量标准及检验规范实施质量检验,以提早发现问 题并迅速处理,以确保产成品质量
6.质量管理部应每年提交《年度质检总结报告》 ,对本年度产品质量检验的标准、规范及 D3 执行情况进行总结,并提出产品质量检验标准及检验规范的修订意见
相 关 规 范
应建 规范
? 《产品质量管理制度》 ? 《产品质量检验操作规范》 ? 《企业内部控制应用指引》 ? 《中华人民共和国产品质量法》
参照 规范
? 《产品质量操作规范》
文件资料
? 《年度质检总结报告》
责任部门 及责任人
? 质量管理部、相关部门 ? 总经理、技术总监、质量管理部经理
产品质量检验管理程序(含流程图)
文件制修订记录
1.0目的 为了有效测量与监控产品从进料、制程、成品及出货各阶段检验作业能始终符合产品工程规范的各项要求。 2.0范围:适用于品管IQC、IPQC、QA过程作业。 3.0权责: 3.1品管部:负责各阶段品质检验的执行、标识、追溯的管理、实际验货。3.2工程部:产品作业标准的制定与检查。 3.3生产部:依生产计划、工程标准、验收标准执行生产作业。 3.4业务部:依订单需求验收出货数量。 3.5资材部:采购物料的外部联络。 4.0定义:无 5.0作业内容: 5.1进料检验 5.1.1收料 5.1.1.1供应商依据采购订单交货到公司仓库。 5.1.1.2仓管依据采购订单核对送货单是否一致,如若不符则退货并要求供应商重新交货,符合则点收数量并开出[进货单]。 5.1.1.3仓管将[进货单]连同要求供应商提供的相关文件(如材质报告、检验报告、测试报告等)交品管部,通知IQC进行检验。 5.1.1.4检验参照依据AQL表或依客户端需求作抽样检验。 5.1.1.5品管部IQC接到[进货单]后对供应商所提供的文件进行验证,(有法规环保类要求的产品必须依客户指定或经国家认可有检测能力机构出具的测试报告,如“SGS报告”等);品管部可以根据批量大小、价值贵重程度来对供应商所提供产品的材质进行一次确认。 5.1.1.5下列几项物料必须由品管部进料检验:
a)生产性原材料。 b)外发加工产品。 c)包装材料等。 5.1.2需应用下列一种或多种方法进行验收、检验 5.1.2.1接收检验及测试: a)核对材质证明(限自购原材料,样品或来料加工产品可不需要提供材质证明),核对供应商提供的相关文件。 b)依《检验标准书》逐项检验与填写[进料检验报告],无《检验标准书》时,依图面求或样板检验,检验结果可直接记录于[进料检验报告]上。 c)凡属客户提供来料进行加工,如无图面,依据客户提供的规格进行检验;如既无规格又无图面,IQC只针对其外观进行检验并记录于[进料检验报告]上。 5.1.2.2IQC依据《检验标准书》进行检验,并将检验结果与判定结果记录于[进料检验报告]。 5.1.2.3指定外部商业实验室。 5.1.2.4如属工程样品进料由工程部验收。 5.1.2.5客户同意的其他方式进行检验。 5.1.3判定与处理 5.1.3.1合格 a)检验结果判定为合格,IQC人员则将[进料检验报告]以及相关数据呈主管确认经理核准。 b)IQC于进料检验合格时贴IQC合格标签。 5.1.3.2不合格 a)检验结果判定为不合格时各相关单位在[进料检验报告]进行评审,总监核准后生效。 b)不合格时填写[品质异常单]并通知资材部采购单位,并追踪改善效果。
产品检验流程图
产品检验控制程序(附流程图) 1 更多搜索AIEIN质量了解
1目的 统一产品检验和控制的流程,确保各部门按照产品检验按照既定要求执行图纸设计、物料采购、质量检验、不合格处理、生产制造,保证产品质量,提高顾客满意度和市场占有率。 2范围 适用于公司产品检验控制涉及的所有过程。 3职责 3.1生产部负责产品的生产制造。 3.2采购部负责外协或外购原材料、零部件或产品的采购工作。 3.3质量部负责对内外部原材料、零部件或产品的检验工作。 3.4设计部对内外部原材料、零部件或产品不合格的评审工作。 4工作程序 4.1检验分类 产品检验按抽样频次分包括首末件检验、抽样检验、100%全检。 产品检验按产品类别分样品检验、常规检验。 产品检验按产品来源分源检(供应商)、来料检验、过程检验、最终检验。产品检验按检验宽严度分严格检验、正常检验、宽松检验。 4.2检验流程 4.2.1检验需求 2 更多搜索AIEIN质量了解
质量部根据项目部样品检验需求、采购部来料到货入库需求、生产部生产需求、生产部完工入库需求对原材料、零部件或产品进行检验确认。 4.2.2检验准备 质量部根据检验需求准备检验作业指导书和检验器具,待原材料、零部件或产品。 4.2.3检验实施 质量部对入待检库原材料、零部件或产品实施检验,检验实施参照《抽检检验管理规定》。 4.2.4检验处置 质量部对实施的检验活动进行记录和处置 4.2.4.1检验记录 检验活动需对检验信息进行记录,完成后在原材料、零部件或产品上粘贴合格或不合格标签,不合格原材料、零部件或产品需填写《NC通知报告》通知相关部门,并要求责任部门填写《纠正预防8D报告》,质量部负责跟踪改进效果。 4.2.4.2检验处置 检验处置包括接收、挑选、退回: a.判为合格的检查批应整批接收; b.判为不合格的检查批原则上全部退回供货方,特殊情况下与供货方协商,实施检查水平Ⅳ进行挑选; 3 更多搜索AIEIN质量了解
工程质量验收流程纲要图.doc
1方案报审流程 施工单位根据图纸、合同 文件等要求编制施工组 织设计、施工方案等 施工组织设计 施工单位进行内部审批、 施工方案 手续齐全 施工单位进行施工技术 文件报审 形成 未批准批准 建设(监理)《施组、方案报审表》 单位批复意见 施工单位依据批复意见 1、施工组织设计交底 与技术文件进行技术交 2、施工方案交底 底 3、分项工程施工技术交底 进入施工质量验收报批 流程 方案报审流程图
2物资进场验收流程 相关质量证明文件包括 厂合格证; 供应单位根据供货合同 厂家质量检验报告;提交相关质 组织工程物资进场 厂家质量保证书; 量证明文件 进口商品商检证明; 质量检验部门出具的检 验报告; 环保、消防部门出具的 施工单位组织工程物资进场检验认可文件等。 注:提交的质量证明文 件 抽样复试不合格开箱检查 合格 材料、构配件进场检验记录 材料试验报告 设备开箱检验记录 施工单位进行工设备及管道附件试验记录 程物资进场验收形成物资进场复试报告(试验检验单位提 供) 报 送 建设(监理) 审批签工程物资进场报 认形成验表 单位审核 退货或按 合 合同约定 格 处理 工程使用 物资进场验收流程图
3检验批质量验收流程 施工单位根据图纸、规范、 方案、交底等组织施工 按规范、方案等形成以下资 料: 施工测量记录整施工单位负责进行过程质量施工物资资料 施工记录改 控制检查、检验形成 施工试验记录等 施工完成,施工 不合格 单位自检 监理(建设)单位《检验批质量验收记不合格组织检验批质量验形成录表 收 施工单位进入下一道工序施工 检验批质量验收流程图
4分项工程质量验收流程 同一分项工程检验批 施工完成并验收通过 (第 1 个) 同一分项工程全 部检验批完成 . 同一分项工程检验批同一分项工程检验批施工完成并验收通过施工完成并验收通过(第 2 个)(第n个) 施工单位自检 合格,报监理 监理(建设)单位组织《分项工程质量验施工单位进行分项工收记录表》《分项/分部程质量验收形成工程施工报验表》 下一个分项工程质量验收 流程 分项工程质量验收流程图
质量控制方法和控制流程图
质量控制方法和控制流程 为了严把质量关,保证产品质量,冀州市****玻璃钢防爆电器设备有限公司经过实践摸索,创造了一整套严格有效的质量控制方法和控制流程,形成一个质量控制体系。为了让大家对我公司质量工作有更全面的了解,我把这套体系介绍大家。 一、质量控制方法: 为了保证质量控制的有效性和及时性,我们采取两种方法进行质量控制,一是通过实时质量检测控制产品质量,二是通过质量报表进行质量分析和质量管理监督。 我公司制订了完善、详尽的质量管理制度,制度中对相关质量检测要素进行了规定,简介如下: 1、对原材料的检测。常言道,巧妇难为无米之炊,没有好的原材料,难以生产 质量过硬的产品。我公司为保证生产出高质量的产品,对所进原材料严格把 关,由技检部质检员、生产部质检员、采购员、库管员组成验收小组,对所 进材料进行联合检测,确保材料质量满足生产要求。 2、对生产工序半成品、成品的质量检测。生产过程是一个前后连接的过程,整个 过程中的任一个环节出现问题,都会直接或间接影响到最终产品的质量。为此,我们公司对每一个生产工序都进行了严格的质量把关。对于生产过程中的各个工序我们采取四级质量检验制度,一级检验是由本工序工作人员对本工序产品进行产品检验,我们称为自检。自检不通过的产品不能流入下道工序。自检合格的半成品,进入下道工序前由下道工序进行二级检验,再次把住质量关,我们称为互检。互检制度即可以避免自检过程中出现的自觉不自觉的自私行为,又可以增加产品质量检测的准确性和全面性。在整个生产过程进行中,生产部设有专门的序检员,对整个生产过程进行质量跟踪检测,保证整个生产全局的质量稳定,这是第三级检验。第四级检验是在产品入库前由技检部质检员对产
质量检验_控制流程图
内部日常管理办法文件编号 版本A/0 IQC管理流程图生效日期 共页第页 管理流程图相关文件及表单 责任单位 供应商仓库仓库送货单据(到货单,供方自检报告,产品、状态标识) 收货单 报检单(附带到货数量、供方出厂报告、来料批次) IQC 参照作业指导书/控制计划/ 抽样规则GB2828.1-2003 入库(准确区域) IQC 相关单位 相关单位 IQC作业指导书 IQC检验报告/进厂检验申请 单 MRB会 议 让步放行申请单 MRB会议纪要/会签单 品质异常通知单 /再发防止对策报告书 ▼ 贴 蓝 色 标 签 贴 黄 色 标 签 IQC 标识贴纸 置退货区IQC、仓库IQC 检验报告出 库、退货单 制定赵志国2014810审核核准
A/0文件编号 管理流程图供应商品质控制管理流程图 版本 生效日期 共页 相关文件及表单 质量保证部 产品技术部 供应商 IQC工程师 IQC工程师 IQC工程师 IQC工程师 IQC作业指导书 进厂检验申请单/报告 IPQC巡检作业指导书 IPQC巡检记录 试验报告 品质异常通知单/ 再 发防止对策报告 通知单/函件 再发防止对策报告 进厂检验申请单/报告 通知单/函件 再发防止对策报告 制定赵志国2014.8.10审核核准
制定 审核 核准 日常内部管理办法 文件编号 版 本 A/0 -- 图 ------------------ 生效日期 管理流程图 相关文件及表单 生产领料 * 生产投产 生产车间 制造部 IPQC 制造部 FQC 相关责任部门 相关责任部门 品质部(IPQC IPQC 制造部、工 程部 制造部、工程部 品质部 出库单 排拉表、作业标准书 IPQC 巡拉报告/BOM 修理日报表 QC 日报表 纠正/预防措施通知单 IPQC 巡拉检查报告 纠正/预防措施通知单 首件检验报告 IPQC 核对 OK OK NG FQC 检测 OK IP NQ C 检验 送首件确认 OK OK 效果 确认 生产、工程 分析原因 修理 确认责任部门 不良率较高 写纠正/预防措施 不良率较低 批量生产
(全面质量管理)质量手册程序文件流程图
质量手册程序文件流程图
目录 8.2.3.4a.质量手册编号3 8.2.3.4b.程序文件编号3 8.2.3.4d.质量记录编号3 8.2附图1:组织(及所属部门)制订、发放的文件受控流程图4 8.2附图2:外来受控文件受控流程图4 8.3.2质量记录控制流程图5 8.4.2内部质量审核工作流程图6 8.5.26.10进货检验的不合格品控制程序6 8.5.26.10产品已交付和使用时发现的不合格品控制程序7 8.5.2产品最终检验的不合格品控制程序流程图8 8.5.2产品实现过程中不合格品控制程序流程图8 8.6.2A类纠正措施流程图9 8.6.2B类纠正措施10 8.6.2C类纠正措施10 8.7.2《质量情况通报》的编制、发放、回收、处理11 8.7.2财务状况预警系统11 8.7.2预防措施的制订、实施和评价11 8.8.2管理评审控制程序流程图12 8.9.2人员招聘录用程序流程图12 8.9.2培训程序流程图12
8.9.2考核程序流程图12 8.11.2产品实现过程策划程序流程图12 8.11.2策划依据12 8.12.2产品要求的识别与评审过程13 8.12.2产品合同修改过程14 8.12.2市场信息控制过程15 8.13.2设计和开发控制程序16 8.14.2采购控制程序流程图17 8.15.2生产运作程序流程图18 8.17.2测量和监控策划程序19 8.18.2体系业绩的测量和监控过程程序20 8.19.2过程的测量、监控和分析程序流程图21 8.20.2产品测量和监控程序流程图21 8.21.2持续改进过程控制程序21 8.2.3.4a.质量手册编号 8.2.3.4b.程序文件编号 8.2.3.4c. 程序文件编号
产品质量控制与检验流程
江苏永昇空调有限公司 产品质量控制与检验流程 为加强产品在采购、生产制造、调试试验、包装出厂等各个环节的质量控制,提高质量、降低质量损失,特对产品质量的形成过程的控制和检验流程进行统一化与程序化。 所有检验必须依据《产品检验调试规范》、《工艺文件》、标准、图纸、设备明细表、合同要求等。 一、外购、外协产品质量控制与检验 1、外购、外协产品进司后堆放在待检区或指定区域,由经办人员对其数量、规格型号、外观质量、附件资料等进行自行检查、核对; 2、外购、外协产品经办人检查核对无误后填写送检单,要求准确、详细,涉及到专用物资应备注,连同图纸、设备明细表等相应文件一并递交检验员报检; 3、检验员按送检单内容,对外购、外协产品进行资料收集、质量检验并填写检验报告,对质量检验状态进行标识,将检验结果在送检单上明确标注; 4、外购、外协产品经办人员根据检验结果,合格的办理进库手续。不合格的进行隔离并采取退货、更换、返工、维修等方法处理,自检合格后重新履行送检程序; 5、试用件的质量由质管部负责跟踪,并适时提供给供应部; 6、检验员对检验不合格的产品处理情况进行跟踪、追溯; 7、仓库和其他任何使用方不得接受不合格的外购、外协产品。 二、钣金油漆车间产品质量控制与检验 1、钣金油漆车间在施工前应认真阅读图纸、技术说明等,全面、真实了解产品技术要求、外观颜色、防腐级别、装配构造等; 2、机架组的制作的底座、机架在拼装前对已氧化、锈蚀的材料进行磷化、除油、除锈处理,对于外形尺寸较小、无保温材料的可以制作成型后进行磷化、除油、除锈处理。做好后进行自检、互检,报检验员确认合格后方可转序; 3、钣金组制作的框架、壳体、门板等下料、折边后需油漆的,进行自检、互检,检验员抽检确认合格后方可转序; 4、承水盘、电控箱、安装板、壳体、门板等需外协镀锌、喷塑、发泡的,必须提前将应存在的马脚、接地柱、导线板、螺丝孔等全部制作好,做好后进行自检、互检,报检验员确认合格后方可转外协加工。风冷分体空调如因导线板、马脚等不能预先焊接好,应采用二次装配,试装后再外协; 5、钣金组制作的框架、壳体、门板等拼装时,隐蔽部位或以后防腐有
产品质量检验标准及流程
产品质量检验标准及流程 ◆目的:规格质量检验流程,保证产品出货质量; ◆适用范围:与本公司合作的供应商; ◆质量检验标准:1、MIL-STD-105E 一次正常抽样二级水平2、ANSI/ASQC-Z1.4 ◆允收水准:MIL-STD-105E.II.(如下图,详细的参考AQL表) 缺点AQL AC RE CRI 0 MAJ 0.65 MIN 2.5 ◆检验方式:抽检、全检;抽检:抽检箱数以货物箱数的开平方取整数;抽检数量以货物数对AQL表定; ◆检验流程: 1、数量:数量分为货物总箱数和单个箱的产品数(如有内箱的需检查内箱数);清点数量的时候,须先清点货物的总箱数,与单上的数量箱数是否一致。再抽点箱子里的产品数量跟单子指定的每箱数量是否一样。如发现有误须马上指出并将检查结果记录下来; 2、包装:检查货物的包装是否稳实,包装带打的是否牢固。原则上以在运输过程中不会造成对产品的损坏为考虑的首要因素。如检查发现有问题,须马上指出并将结果记录下来; 3、唛头:仔细核对订单上的唛头与外箱的唛头是否一致。如发现有误须马上指出并将检查结果记录下来; 4、产品质量检查,以严谨认真的态度,对产品的外观和功能以及是否会对人畜造成伤害等各方面进行检验。并将检验情况记录下来。具体的检验方法,参看下面产品检验方法; 5、根据检验情况,填写检验报表。依据AQL标准,作出合格与否的决定。 ◆产品检验方法■、参照客户确认的样板进行检验; A、外观■五金类外观方面需要注意以下几点:1、产品表面有否生锈、伤痕或刮花现象; 2、接口吻合部份连接是否紧密; 3、套接或旋转是否灵活,无阻碍; 4、电镀产品,有否色差、汽泡或掉镀现象,镀层和镀色是否均匀; 5、客户需印的LOGO 是否清楚。有否漏字、错字、图案不全或错误现象。 6、检查里面的电池是否干净,有否绝缘片。有否发莓或锈斑现象; ■塑胶类外观方面需要注意以下几点:1、产品表面有否伤痕或刮花现象;2、接口吻合部份连接是否紧密;3、套接或旋转是否灵活,无阻碍;4、喷油、烤漆或电镀产品,有否汽泡或掉油、掉漆、掉镀现象,镀层和镀色是否均匀,有否色差现象;5、客户需印的LOGO 是否清楚。有否色差、漏字、错字、图案不全或错误现象。6、检查里面的电池是否干净,有否绝缘片。有否发莓或锈斑现象;7、透明产品,查看透明度是否良好。有否杂质、黑点;
程序文件流程图2(DOC 33页)
程序文件流程图2(DOC 33页)
目录 8.2.3.4 a. 质量手册编号............................................ 错误!未定义书签。 8.2.3.4 b. 程序文件编号 ........................................... 错误!未定义书签。 8.2.3.4 d. 质量记录编号 ........................................... 错误!未定义书签。 8.2 附图1:组织(及所属部门)制订、发放的文件受控流程图 (6) 8.2 附图2:外来受控文件受控流程图 (8) 8.3.2 质量记录控制流程图 (10) 8.4.2 内部质量审核工作流程图 (13) 8.5.2 6.10 进货检验的不合格品控制程序 (13) 8.5.2 6.10 产品已交付和使用时发现的不合格品控制程序 (14) 8.5.2 产品最终检验的不合格品控制程序流程图 (16) 8.5.2 产品实现过程中不合格品控制程序流程图 (18) 8.6.2 A 类纠正措施流程图 (20) 8.6.2 B 类纠正措施 (22) 8.6.2 C 类纠正措施 (24) 8.7.2 《质量情况通报》的编制、发放、回收、处理 (26) 8.7.2 财务状况预警系统 (28) 8.7.2 预防措施的制订、实施和评价 (30) 8.8.2 管理评审控制程序流程图 (31) 8.9.2 人员招聘录用程序流程图 (33) 8.9.2 培训程序流程图 (35)
8.9.2 考核程序流程图 (37) 8.11.2 产品实现过程策划程序流程图 (39) 8.11.2 策划依据 (41) 8.12.2 产品要求的识别与评审过程 (43) 8.12.2 产品合同修改过程 (44) 8.12.2 市场信息控制过程 (46) 8.13.2 设计和开发控制程序 (47) 8.14.2 采购控制程序流程图 (49) 8.15.2 生产运作程序流程图 (51) 8.17.2 测量和监控策划程序 (52) 8.18.2 体系业绩的测量和监控过程程序 (54) 8.19.2 过程的测量、监控和分析程序流程图 (56) 8.20.2 产品测量和监控程序流程图 (58) 8.21.2 持续改进过程控制程序 (60)
成品检验工作流程图
1.目的 规范成品出货检验流程,防止不合格出货,及时发现、纠正产品质量隐患,保证产品质量。 2.适用范围 适用于本厂加工、制造的各类产品的成品出货前的检验。 3.QA检验流程/职责和工作要求 流程职责工作要求相关文件/记录
流程职责开始工作要求 相关文件 /记录 投产 首件检验 检查结果确认生产 ?生产?每一订单生产的第一台机送OQC检验《首件检查检验员按订单、样机、检验标准或规范、说明书、ECN、表》OQC组长料表、设计文件作首件检验 填写《首件检查表》(外观、功能) ?QE?QE对首件及《首件检查表》确认,并签署合格 与否意见 首件不合格处理?PIE/OQC 组 ? OQC、PQC和PIE对机确认,《OQC检验报长/PQC组长告》 OQC不合格发出《OQC检验报告》,注明首件检查《坏机分析PIE工程PIE分析原因,发出《坏机分析报告》报告》 生产部已投产机返工,生产再重送首件 首件合格处理?OQC 组长 ?首件检验合格,OQC通知生产线组长在《首件确 认表》上签字确认后,生产部批量生产 批量检验?检验员?首件检验合格,OQC批量抽检 根据产品检验标准、规范,《产品检验抽样规 定》,设计文件,批量抽检 记录抽检的每台机流水号 首批检验合格机抽一箱做整箱落地试验 首批检验合格机(配有电源的产品)抽一箱做24 小时煲机试验 根据抽检结果填写OQC检验报告 抽检不合格处理?OQC组长 /PQC组长/PIE ?批量抽检不合格PQC、OQC、PIE对机确认 OQC主管OQC主管在OQC检验报告上签字确认 检验员OQC在生产部产成品送检单上填写REJ,注明不 良项目,发出《OQC检验报告》, PIE工程PIE发出《坏机分析报告》,在线指导生产 线返工,返工后重新送检
质量体系文件流程图(DOC37页)
目录 8.2.3.4 a. 质量手册编号 (2) 8.2.3.4 b. 程序文件编号 (2) 8.2.3.4 d. 质量记录编号 (2) 8.2 附图1:组织(及所属部门)制订、发放的文件受控流程图 (3) 8.2 附图2:外来受控文件受控流程图 (4) 8.3.2 质量记录控制流程图 (5) 8.4.2 内部质量审核工作流程图 (6) 8.5.2 6.10 进货检验的不合格品控制程序 (7) 8.5.2 6.10 产品已交付和使用时发现的不合格品控制程序 (8) 8.5.2 产品最终检验的不合格品控制程序流程图 (10) 8.5.2 产品实现过程中不合格品控制程序流程图 (11) 8.6.2 A 类纠正措施流程图 (12) 8.6.2 B 类纠正措施 (14) 8.6.2 C 类纠正措施 (15) 8.7.2 《质量情况通报》的编制、发放、回收、处理 (16) 8.7.2 财务状况预警系统 (17) 8.7.2 预防措施的制订、实施和评价 (18) 8.8.2 管理评审控制程序流程图 (19) 8.9.2 人员招聘录用程序流程图 (20) 8.9.2 培训程序流程图 (21) 8.9.2 考核程序流程图 (22) 8.11.2 产品实现过程策划程序流程图 (23) 8.11.2 策划依据 (24) 8.12.2 产品要求的识别与评审过程 (25) 8.12.2 产品合同修改过程 (26) 8.12.2 市场信息控制过程 (27) 8.13.2 设计和开发控制程序 (28) 8.14.2 采购控制程序流程图 (30) 8.15.2 生产运作程序流程图 (31) 8.17.2 测量和监控策划程序 (32) 8.18.2 体系业绩的测量和监控过程程序 (33) 8.19.2 过程的测量、监控和分析程序流程图 (34) 8.20.2 产品测量和监控程序流程图 (35) 8.21.2 持续改进过程控制程序 (36)