电路板PCBA制造技术规范
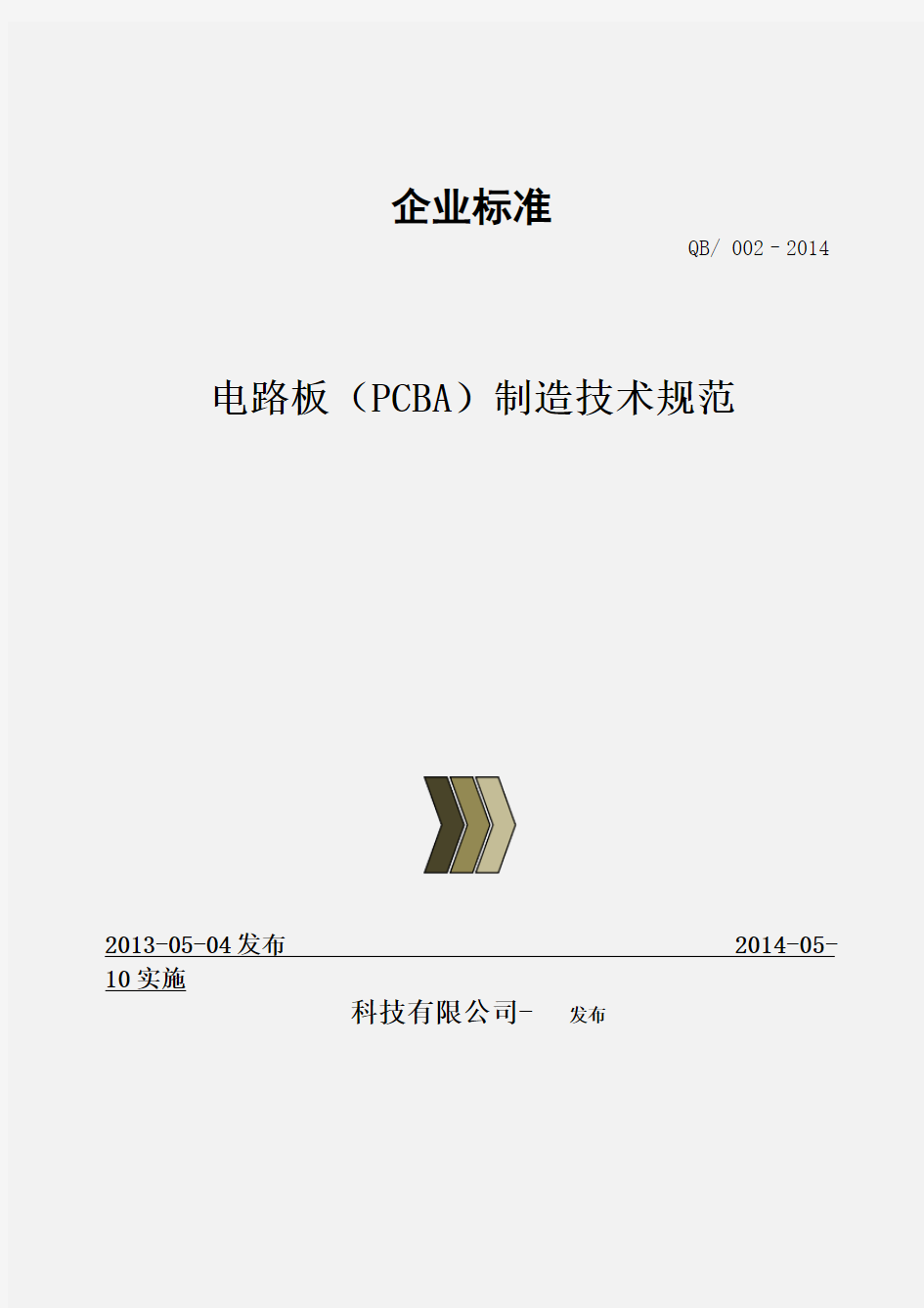

企业标准
QB/ 002–2014电路板(PCBA)制造技术规范
2013-05-04发布 2014-05-10实施
科技有限公司- 发布
修订声明
?本规范于2013年05 月04日首次试用版发布。
?本规范拟制与解释部门:
?本规范起草单位:
?本规范主要起草人:范学勤
?本规范审核人:
?标准化审核人:
?本规范批准人:
●本规范修订记录表:
修订日期版本修订内容修订人2013-05-04A试用版发行
2014-5-10B修改使用公司名称
目录
封面:
电路板(PCBA)制造技术规范 (11)
修订声明 (22)
目录 (33)
前言 (55)
术语解释 (66)
第一章 PCBA制造生产必要前提条件 (77)
1.1 产品设计良好: (77)
1.2 高质量的材料及合适的设备: (77)
1.3 成熟稳定的生产工艺: (77)
1.4 技术熟练的生产人员: (88)
附图1 SCC标准PCBA生产控制流程 (88)
附图2 SCC标准SMT工艺加工流程 (99)
第二章车间温湿度管控要求 (1010)
2.1 车间内温度、相对湿度要求: (1010)
2.2 温度湿度检测仪器要求: (1010)
2.3 车间内环境控制的相关规定: (1010)
2.4 温湿度日常检查要求: (1010)
第三章湿度敏感组件管制条件 (1111)
3.1 IC类半导体器件烘烤方式及要求: (1111)
3.2 IC类半导体器件管制条件: (1111)
3.3 PCB管制规范: (1212)
第四章表面组装元器件(SMC/SMD)概述 (1313)
4.1 表面组装元器件基本要求: (1313)
4.2 表面组装元器件(SMC/SMD)的包装类型: (1313)
4.3 表面组装元器件使人用注意事项: (1414)
第五章 SMT工艺概述 (1515)
5.1 SMT工艺分类: (1515)
5.2 施加焊膏工艺: (1616)
5.3 施加贴片红胶工艺: (1717)
5.4 施加贴片红胶的方法和各种方法的适用范围:.............. 错误!未定义书签。错误!未定义书签。
5.5 贴装元器件:.......................................... 错误!未定义书签。错误!未定义书签。
5.6 贴片回流焊(再流焊):................................ 错误!未定义书签。错误!未定义书签。
5.7 回流焊特点:.......................................... 错误!未定义书签。错误!未定义书签。
5.8 回流焊的分类:........................................ 错误!未定义书签。错误!未定义书签。
5.9 回流焊的工艺要求:.................................... 错误!未定义书签。错误!未定义书签。第六章表面组装工艺材料介绍―焊膏............................ 错误!未定义书签。错误!未定义书签。
6.1 简介:错误!未定义书签。错误!未定义书签。
6.2 焊膏的分类、组成:.................................... 错误!未定义书签。错误!未定义书签。
6.3 合金焊料粉与焊剂含量的配比:.......................... 错误!未定义书签。错误!未定义书签。
6.4 焊剂组份知识:........................................ 错误!未定义书签。错误!未定义书签。
6.5 对焊膏的技术要求:.................................... 错误!未定义书签。错误!未定义书签。
6.6 焊膏的选择依据及管理使用:............................ 错误!未定义书签。错误!未定义书签。第七章表面组装工艺材料介绍―红胶............................ 错误!未定义书签。错误!未定义书签。
7.1 概况:错误!未定义书签。错误!未定义书签。
7.2 性能参数(举例):................................... 错误!未定义书签。错误!未定义书签。
7.3 固化条件:............................................ 错误!未定义书签。错误!未定义书签。
7.4 使用方法:............................................ 错误!未定义书签。错误!未定义书签。第八章 SMT生产线概况及其主要设备 ............................. 错误!未定义书签。错误!未定义书签。
8.1 SMT生产线概况:...................................... 错误!未定义书签。错误!未定义书签。
8.2 SMT生产线主要设备:.................................. 错误!未定义书签。错误!未定义书签。
8.3 贴装机 &贴片机:...................................... 错误!未定义书签。错误!未定义书签。
8.4 回流焊炉:............................................ 错误!未定义书签。错误!未定义书签。第九章波峰焊接工艺........................................... 错误!未定义书签。错误!未定义书签。
10.1 波峰焊原理:.......................................... 错误!未定义书签。错误!未定义书签。
10.2 波峰焊工艺对元器件和印制板的基本要求:................ 错误!未定义书签。错误!未定义书签。
10.3 波峰焊工艺材料:...................................... 错误!未定义书签。错误!未定义书签。
10.4 典型波峰焊工艺流程:.................................. 错误!未定义书签。错误!未定义书签。
10.5 波峰焊的主要工艺参数及对工艺参数的调整:.............. 错误!未定义书签。错误!未定义书签。
10.6 预热温度和时间:...................................... 错误!未定义书签。错误!未定义书签。
10.7 焊接温度和时间:...................................... 错误!未定义书签。错误!未定义书签。
10.8 印制板爬坡角度和波峰高度:............................ 错误!未定义书签。错误!未定义书签。
10.9 工艺参数的综合调整:.................................. 错误!未定义书签。错误!未定义书签。
10.10 波峰焊接质量要求: .................................. 错误!未定义书签。错误!未定义书签。第十章 ESD防静电知识 ........................................ 错误!未定义书签。错误!未定义书签。
10.1 静电放电及防护基础知识:.............................. 错误!未定义书签。错误!未定义书签。
10.2 静电的产生:.......................................... 错误!未定义书签。错误!未定义书签。
10.3 静电对电子工业的影响:................................ 错误!未定义书签。错误!未定义书签。
10.4 E SD形成的三种型式:.................................. 错误!未定义书签。错误!未定义书签。
10.5 E SD静电防护方式:.................................... 错误!未定义书签。错误!未定义书签。
10.6 防静电设备工具:...................................... 错误!未定义书签。错误!未定义书签。
10.7 防静电的一般工艺规程要求:............................ 错误!未定义书签。错误!未定义书签。第十一章电子元器件的储存要求................................ 错误!未定义书签。错误!未定义书签。
第十二章电子车间防静电要求及规范............................ 错误!未定义书签。错误!未定义书签。
附录1:湿度对电子元器件和整机的危害 .......................... 错误!未定义书签。错误!未定义书签。
附录2:温湿度及清洁度对电子设备的影响 ........................ 错误!未定义书签。错误!未定义书签。
附录3:长期存放电子元器件的解决方案 .......................... 错误!未定义书签。错误!未定义书签。
前言
本标准文件中所提及的部分标准参数及具体要求数据摘取自同行业企业标准文件内容,实际执行过程中可能会出现不适应状况,如遇此特殊情况时可由部门经理决策后做临时变跟后执行。
本标准文件适用于PMC计划、仓储部、采购部、生产制造及品质管控部门作为参考使用,实际运用请自行查阅相对应章节。
本标准文件中未提及的事项,烦请当时人及时提出予以指正,以进一步完善此标准文件。
本标准文件编制过程中,因本人能力有限,难免有不足之处,还请各位给予指正。
术语解释
SMT:全称是Surface mount(或mounting)technology,中文意思为表面粘着(或贴装)技术。SMC\SMD:片式元件片/片式器件。
SMA:表面组装组件。
ESD:全称是Electro-static discharge,中文意思为静电放电。
PCB:印制电路板。
FPT:窄间距技术,FPT是指将引脚间距在0.635-0.3mm之间的SMD和长乘宽小于等于
1.6mm*0.8mm的SMC组装在PCB上的技术。
MELF:圆柱形元器件。
SOP:羽翼形小外形塑料封装。
SOJ:J形小外形塑料封装。
TSO:超薄形小外塑料封装。
PLCC:塑料有引线(J形)芯片载体。
QFP:四边扁平封装器件。
PQFP:带角耳的四边扁平封装器件。
BGA:球栅阵列封装(ball grid array)。;
DCA:芯片直接贴装技术。
CSP:芯片级封装(引脚也在器件底下,外形与BGA相同,封装尺寸比BGA小。芯片封装尺寸与芯片面积比≦1.2称为CSP)
THC:通孔插装元器件。
ESD:静电放电
第一章 PCBA制造生产必要前提条件
1.1 产品设计良好:
●参照成功的设计样板和机型
●在生产制造中将不足和缺陷反馈给开发技术人员不断改善.
●制造工艺更加简单和生产加工工时减少.
●销售的卖点增多和利润附加值增高.
●生产成本不断降低和销售价格升值和保持
1.2 高质量的材料及合适的设备:
●在同一价格水平基础上、高质量的材料
●包装方式不能影响产品的性能和外观
●材料的质量不断的改进
●通用的制造设备
●设备的损耗折旧成本低
●设备的操作简单,备件易购买
1.3 成熟稳定的生产工艺:
●严格的静电要求;
●成熟稳定的DIP制造工艺
●成熟稳定的SMT制造工艺
●成熟稳定的PCBA防护处理工艺
●成熟稳定的波峰焊接防护处理工艺
●成熟的PCBA防护处理工艺
●成熟稳定的装焊工艺制造要求
● 严格、苛刻的测试工艺制造要求 ● 严格、可靠的包装工艺制造要求
1.4 技术熟练的生产人员:
● 要掌握基本的作业技巧,能够熟练作业3-5个工位 ● 要具备改进意识
● 将工作结果数据化,不断追求工作结果提升 ● 熟练掌握工序作业技能后,不断培养多面手员工 ● 给员工创造职业晋升的机会和体制 ● 员工入职前要认真把关
附图1- KLHBS 标准PCBA 生产控制流程
PMC 物料需求
物料采购
来料检验 入电子料仓库
电子元件供应商
PASS
FAIL 仓库备料、发料 PMC 生产任务需求 外协SMT 贴片加工
来料检验 入电子料仓库
SMT 贴片加工商
PASS
FAIL
DIP 后焊加工
烧写MCU 程序
功能测试
寿命老化
老化后全功能测试
外观维修/返修
PMC 生产任务需求
仓库备料、发料
波峰焊加工
PCBA 裸板外观全检
FAIL
OK
OK
OK
功能维修/返修
FAIL
FAIL
OK
OK
FAIL
附图2- KLHBS 标准SMT 工艺加工流程
PCBA 表面三防处成品PCBA 功能测试
防静电包装
入电子料仓库
PCBA 表面涂刷CRC70防潮漆
PCBA 表面涂刷环氧树脂 供应商领料、备料
PCB 板烘烤去潮
A 面-高速贴片机贴装器件
(电阻、电容、二极管、三极管类小封装器
件)
大型、异性器件手工贴片
A 面-多功能贴片机贴装器件
(贴SOP\QFP\BGA\TSSOP 等封装芯片类器
件)
FAIL
PASS
AOI 光学检查
维 修
A 面 回 流 焊 接
回流焊接前检查
NG
OK
NG OK
A 面锡膏印刷
A 面锡膏印刷检查
B 面锡膏印刷
B 面锡膏印刷检查
B 面-高速贴片机贴装器件
(电阻、电容、二极管、三极管类小封装器
件)
大型、异性器件手工贴片
B 面-多功能贴片机贴装器件
(贴SOP\QFP\BGA\TSSOP 等封装芯片类器
件)
A 面首件检
查
AOI 光学检查
B 面 回 流 焊 接 回流焊接前检查
B 面首件检查
OQC/FQC 检验 纠正制程
NG
OK
OK
功能维修/返修
FAIL
第二章车间温湿度管控要求
2.1 车间内温度、相对湿度要求:
温度: 24±2℃
湿度: 60±10%
2.2 温度湿度检测仪器要求:
2.2.1 采用Pt100铂电阻做测温传感器,保证了测量温度的准确性和稳定性
2.2.2 采用通风干湿球法测量相对湿度,避免了风速对湿度测量的影响
2.2.3 分辨率:温度:0.01℃;湿度:0.01%RH;
2.2.4 整体误差(电测+传感器):温度:±0.1~0.2℃;湿度:±1.5%RH。
2.3 车间内环境控制的相关规定:
3.3.1 参数值根据产品要求、季节变化,由PE工程师负责设定。
3.3.2 日常温湿度计的放置位置:采用电子指针式干湿球温湿度计,放置在机器最密集的区
域,以便能采集到最显著的温湿度变化。
3.3.3 温湿度计的记录周期设定为7天,每星期一早上7:30更换记录表。换下的记录表存
放在特定的文件夹里,温湿度计的记录周期设定为7天,每星期一早上7:30更换记
录表。换下的记录表存放在特定的文件夹里,保存期至少为1年,新的记录表可向工
程课申领,表上须写明开始日期、更换记录表时、记录起始时间须与更换表格时间相
同。
3.3.4 室内空调系统的开关、湿度控制系统(加湿机,加湿器)开关,交由工程部(行政部)
有关人员负责,其它部门的人员不得擅自使用。
3.3.5 回流焊的抽风口必须每月清理1次,防止积水过多。
3.3.6 逢节假休息日须关闭空调系统的吹风口开关,并要求工程部(行政部)不要关闭空调系
统的抽风口开关,以防机器内壁结露。
2.4 温湿度日常检查要求:
2.4.1 检查工作由PE工程组负责。
2.4.2 检查次数为一天四次,分四个时间段,分别为7:00~12:00;12:00~19:00 ;19:00~
2:00;
2:00~7:00;(白班及夜班各二次)
2.4.3 每次检查结果须记录在规定的表格中,并签上检查人的姓名。
2.4.4 温湿度记录表上的温湿度数值若在要求的范围内,则在附表中<温度状况>/湿度状况>两
栏中写上“OK”,若发现数值不在要求的范围内, 则在附表中相应的栏中写上“NG ”
及对应的温湿度超标值,并即刻通知PE工程组负责人。
2.4.5 PE工程组负责人在接到通知后应即刻通知生产线负责人,必要时可要求停机, 并通知
工程部(行政部)检查空调系统和湿度控制系统。
2.4.6 待温湿度数值回归到要求的范围内后, PE工程组负责人应即刻通知生产部门恢复生产。
2.4.7 逢休息日或节假日可不作温湿度记录。
第三章湿度敏感组件管制条件
3.1 IC类半导体器件烘烤方式及要求:
3.1.1 BGA封装器件,超出管制期限、真或真空包装状态失效或真空包装拆封后湿度指示卡超
出规定,烘烤方法为:120℃±5℃×24小时,或者80℃±5℃×48小时。
3.1.2 QFP / TSOP封装器件,超出管制期限、真或真空包装状态失效或真空包装拆封后湿度
指示卡超出规定,烘烤方法为:120℃±5℃×16小时,或者80℃±5℃×24小时。
3.1.3 TQFP/QFP封装器件,超出管制期限、真或真空包装状态失效或真空包装拆封后湿度指
示卡超出规定,烘烤方法为:120℃±5℃×12小时,或者80℃±5℃×20小时。
3.1.4 SOP/DIP封装器件,超出管制期限、真或真空包装状态失效或真空包装拆封后湿度指示
卡超出规定,烘烤方法为:120℃±5℃×24小时,或者80℃±5℃×48小时。
3.1.5 其它封装IC类半导体器件,超出管制期限或真或真空包装状态失效或真空包装拆封后
湿度指示卡超出规定,烘烤方法为: 120℃±5℃×12小时80℃±5℃×20小时。
3.1.6 如条件允许,可直接询问原材料供应商商会得到更好的标准。
3.2 IC类半导体器件管制条件:
3.2.1 拆封后的IC储存方法
(1)真空包装未拆封前的IC须储存温度低于+30°C,相对湿度小于90%的环境,存储期限为一年。
(2)真空包装已拆封的IC 须标明拆封时间,未上线的IC须储存于防潮柜中,储存条件为:
+25±2℃;65±5%RH,储存期限为72hrs。
(3)若已拆封IC但未上线使用或余料,必须储存于防潮箱内(条件+25±2℃;65±5%RH),若退回
仓库之前的IC由须仓库烘烤后,改以抽真空包装后储存。
3.2.2 IC烘烤方法及条件
(1)超过储存期限者,须以125°C/24hrs烘烤,无法以125°C烘烤者,则以
80°C/48hrs烘烤(若多次烘烤则总烘烤时数须小于96hrs),才可上线使用。
(2)若零件有特殊烘烤规范者,另行订入SIP和SOP文件内。
3.3 PCB管制规范:
3.3.1 PCB拆封与储存期限
(1)PCB板密封包装未拆封,距离制造日期在2个月内可以直接上线使用。
(2)PCB需抽真空包装后方可进行运输及储存。
(3)PCB板制造日期在2个月内,拆封后必须重新标识首次拆封日期。
(4)PCB板制造日期在2个月内,拆封后必须在5天内上线使用完毕。
3.3.2 PCB储存期限过期后烘烤条件
(1)PCB 于制造日期2个月内密封拆封超过5天者,请以120 ±5℃烘烤1小时。
(2)PCB如超过制造日期2个月,上线前请以120 ±5℃烘烤1小时。
(3)PCB如超过制造日期2至6个月,上线前请以120 ±5℃烘烤2小时。
(4)PCB如超过制造日期6个月至1年,上线前请以120 ±5℃烘烤4小时。
(5)烘烤过之PCB须于5天内使用完毕,未使用完毕则需再烘烤1小时才可上线使用。
(6)PCB如储存时间超过1年,上线前请以120 ±5℃烘烤4小时,严重时可返送PCB供应商对焊盘重新喷锡或沉金等表面处理后,才可上线使用。
PCB烘烤方式
(1)大型PCB采取平放式摆放,一叠最多数量30片,直立式数量不限,烘烤完成10分钟内打开烤箱取出PCB平放自然冷却。
(2)中小型PCB采取平放是摆放,一叠最多数量40片,直立式数量不限,烘烤完成10分钟内打开烤箱取出PCB平放自然冷却。
(3)冷却过程中PCB需要用治具压平,以防PCB板弯曲变形。
第四章表面组装元器件(SMC/SMD)概述
表面组装元件/表面组装器件的英文翻译是:Surface Mounted Components/Surface Mounted Devices,缩写为SMC/SMD(以下称SMC/SMD)。
表面组装元器件是指外形为矩形片式、圆柱形或异形,其焊端或引脚制作在同一平面内并适用于表面组装的电子元器件。
4.1 表面组装元器件基本要求:
4.1.1 元器件的外形适合自动化表面组装,元件的上表面应易于使用真空吸嘴吸取,下表面
(背面)具有使用胶粘剂(红胶)的能力。
4.1.2 尺寸、形状标准化、并具有良好的尺寸精度和互换性。
4.1.3 包装形式适合贴装机自动贴装要求(适用编带、托盘、料管这3种标准包装方式)。
4.1.4 具有一定的机械强度,能承受贴装机的贴装应力和基板的弯折应力。
4.1.5 元器件的焊端或引脚的可焊性要符合以下耐温度要求:
235℃±5℃*2±0.2s或230℃±5℃*3±0.5s,焊焊端90%沾锡(上锡)
4.1.6 符合无铅工艺回流焊和波峰焊的耐高温焊接要求
回流焊:265℃±5℃,2±0.2s。
波峰焊:260℃±5℃,5±0.5s。
4.1.7 能承受有机溶剂的洗涤(如洗板水)
4.2 表面组装元器件(SMC/SMD)的包装类型:
4.2.1 表面组装元器件的包装类型有编带、散装、管装和托盘。
4.2.2 表面组装元器件包装编带有纸带和塑料带两种材料。
4.2.3 纸带主要用于包装片式电阻、电容的8mm编带。塑料带用于包装各种片式无引线元件、
复元件、异形元件、SOT、SOP、小尺寸QFP等片式元件。
4.2.4 纸带和塑料带的孔距为4mm,(1.0*0.5mm以下的小元件为2mm),元件间距 4m的倍数,
根据元器件的长度而定。编带的尺寸标准见表4-1。
4.2.5 散装包装:
散装包装主要用于片式元引线元极性元件,例如电阻、电容
表4-1表面组装元器件包编带的尺寸标准
4.2.6 管装包装:
主要用于SOP 、SOJ 、PLCC 、PLCC 插座,以及异形元件等。
4.2.7 托盘包装
托盘包装用于QFP 、窄间距SOP 、PLCC 、PLCC 的插座等。
4.3 表面组装元器件使人用注意事项:
4.3.1 存放表面组装元器件的环境条件:
(1) 环境温度:+ 30℃以下 (2) 环境湿度:<60%RH
(3) 环境气氛:库房及使环境中不得有影响焊接性能的疏、氯、酸等有害气体。 (4) 防静电措施:要满足表面组装对防静电的要求。
4.3.2 表面组装元器件存放周期,从生产日期起为二年。到用户手中算起一般为一年(南方潮
湿环境下3个月以内)。
4.3.3 对具有防潮要求的SMD 器件,打开封装后一周内或72小时内(根据不同器件的要求而
定)必须使用完毕,如果72小时内不能使用完毕,应存放在 4.3.4 操作人员拿取SMD 器件时应带好防静电手镯。 4.3.5 运输、分料、检验、手工贴装等操作需要拿取SMD 器件时尽量用吸笔操作,使用镊子时 要注意不要碰伤SOP 、QFP 等器件的引脚,预防引脚翘曲变形。` 编带宽度mm 8 12 16 24 32 44 56 元件间距mm 2、4 4、8 4 8 12 12 16 20 24 16 20 24 28 32 24 28 32 36 40 44 40 44 48 52 56 第五章 SMT工艺概述 5.1 SMT工艺分类: 5.1.1 按焊接方式,可分为回流焊和波峰焊两种类型: (1)回流焊工艺――先将微量的锡铅焊膏施加到印制板的焊盘上,再将片式元器件贴放在印刷板表面规定的位置上,最后将贴装好元器件的印制板放到回流焊设备的传送带上, 从炉子入口到出口(大约5-8分钟)完成干燥、预热、熔化、冷却全部焊接过程。 (2)波峰焊工艺――先将微量的贴片胶(绝缘粘接胶)施加到印制板的元器件底部或边缘位置上,再将片式元器件贴放在印制表面规定的位置上,并放到回流焊设备的传送带 上进行胶固化;片式元器件被牢固地粘接在印制板的焊接面,然后插装分立元器件, 最后对片式元器件与插装元器件同时进行波峰焊接。 5.1.2 按组装方式,可分为全表面组装、单面混装、双面混装三种方式(见表2-1) 组装方式示意图电路基板元器件特征 全表面组装单面表面 组装 单面PCB 表面组装 元器件 工艺简单、 适用于小 型、薄型简 单电路双面表面 组装 双面PCB 表面组装 元器件 高密度组 装、薄型化 单 面混装SMD和THC 都在A面 双面PCB 表面组装 元器件和 通孔插装 元器件 一般采用先 贴后插,工 艺简单 THC在A 面SMD在B面单面PCB 表面组装 元器件和 通孔插装 元器件 PCB成本 低,工艺简 单,先贴后 插如采用先 插后贴,工 艺复杂。 双面混装THC在A 面,A、B 两面都有 SMD 双面PCB 表面组装 元器件和 通孔插装 元器件 适合高密度 组装 A、B两面 都有SMD 和THC 双面PCB 表面组装 元器件和 通孔插装 元器件 工艺复杂, 尽量不采用 5.2 施加焊膏工艺: 5.2.1 施加焊膏工艺目的: 把适量的SN/PB焊膏均匀地施加在PCB焊盘上,以保证各种封装片式元器件引脚与 PCB相对应的焊盘形成良好的电气连接。 5.2.2 施加焊膏的要求: (1)要求施加的焊膏量均匀,一致性好。焊膏图形要清晰,相邻的图形之间尽量不要粘连,焊膏图形与焊盘图形要一致,尽量不要错位。 (2)一般情况下,焊盘上单位面积的焊膏量应为0.8mg/mm2左右,窄间距元器件应为 0.5mg/mm2左右。 (3)焊膏应覆盖每个焊盘的面积,应在75%以上; (4)焊膏印刷后,应无严重塌落,边缘不整齐,错位不大于0.2mm;对窄间距元器件焊盘,错位不大于0.1mm。 (5)基板其它地方不允许被焊膏污染。 5.2.3 PCB施加焊膏的方法: ?施加焊膏的方法有三种:滴涂式(即注射式,滴涂式又分为手工操作和机器制作)、丝网印刷和金属模板印刷,各种方法的适用范围如下: (1)手工滴涂法―用于极小批量生产,或新产品的模型样机和性能样机的研制阶段,以及生产过程中修补、更换元器件等。 (2)丝网印刷―用于元器件焊盘间距较大,组装密度不高的中小批量生产中。 (3)金属模板印刷―用于大批量生产以及组装密度大,有多引线窄间距元器件的产品,金属模板印刷的质量比较好,模板使用寿命长,因此一般应优先采用金属模板印 刷工艺。 5.3 施加贴片红胶工艺: 5.3.1 施加贴片红胶工艺目的: 在片式元件与插装元器件混装采用波峰焊工艺时,需要用贴片红胶把片式元件暂时 固定在PCB的焊盘位置上,防止在传递过程或插装元器件、波峰焊等工序中元件掉 落。在双面回流焊工艺中,为防止已焊好面上大型器件因焊接受热熔化而掉落,也 需要用贴片红胶起辅助固定作用。 5.3.1 表面组装工艺对贴片红胶的要求: (1)具有一定粘度,胶滴之间不拉丝,在元器件与PCB之间有一定的粘接强度,元器件贴装后在搬运过程中不掉落。 (2)触变性好,涂敷后胶滴不变形、不漫流,能保持足够的高度。 (3)对印制板和元器件无腐蚀,绝缘电阻高和高频特性好。 (4)常温下使用寿命长(常温下固化速度慢)。 (5)在固化温度下固化速度快,固化温度要求在150℃以下,5分钟以内完全固化。 (6)固化后粘接强度高,能经得住波峰焊时260℃的高温以及熔融的锡流波的冲击;在焊接过程中无释放气体现象,波峰焊过程中元件不掉落。 (7)有颜色,便于目视检查和自动检测。 (8)应无毒、无嗅、不可燃,符合ROHS环保要求。 5.3.2 贴片红胶的选择方法: (1)用于表面组装的贴片胶主要有两种类型:环氧树脂和聚丙烯。 (2)环氧树脂型贴片胶属于热固型:一般固化温度在150±10℃/5min以内。 1.目的 本规程规定了铆接工艺要求及质量标准 2.适用范围 本操作指导适用于本公司在制产品的铆螺母、压铆螺母、拉铆钉的铆接工序 3.铆接工艺要求 3.1拉铆 拉铆操作的主要工艺过程是:首先根据铆钉芯棒直径选定铆枪头的孔径,并调整导管位置,用螺母锁紧,然后将铆钉穿入钉孔,套上拉铆枪,夹住铆钉芯棒,枪端顶住铆钉头部,开动铆枪,依靠压缩空气产生的向后拉力,使芯棒的凸肩部分对铆钉形成压力,铆钉出现压缩变形并形成铆钉头,同时,芯棒由于缩颈处断裂而被拉出,铆接完成。 3.1.1拉铆螺母 又称铆螺母,拉帽,瞬间拉帽,用于各类金属板材、管材等制造工业的紧固领域,目前广泛地使用在汽车、航空、铁道、制冷、电梯、开关、仪器、家具、装饰等机电和轻工产品的装配上。 为解决金属薄板、薄管焊接螺母易熔,攻内螺纹易滑牙等缺点而开发,它不需要攻内螺纹,不需要焊接螺母、铆接牢固效率高、使用方便。 3.1.2拉铆螺母分类 3.1.2.1种类:有通孔的平头、小头、六角不锈钢铆螺母,有盲孔的平头、小头、六角不锈钢 铆螺母. 3.1.2.2拉铆螺母的头型见下表 3.1.3拉铆螺母作业指导 3.1.3.1熟悉图纸和工艺要求,对拉铆螺母型号规格进行确认,并检查要铆工件。确认好铆接用的工具和设备并对场地进行清理。 3.1.3.2基材材料板厚和底孔尺寸确认 在正式拉铆螺母前,必须确认板材的底孔尺寸是否合符各型号底孔尺寸要求。如果不能满 足要求,停止拉铆作业。具体拉铆螺母底孔尺寸见下表一: 表一:拉铆螺母底孔尺寸要求 3.1.3.3调节铆枪 使用前检查拉铆枪是否完好,检查气动枪的气压是否符合说明的最低标准。进行拉杆与风动拉铆枪装配,根据铆螺母的长度不同,调节拉杆的装入长度,以拉杆到达铆螺母最后 2~3扣螺纹为合适。同时调节拉杆行程,检测拉伸长度是否合适(根据附表二),未达到拉伸长度要求时,应调节行程,直到符合拉伸长度要求,再进行批量操作。 表二:铆螺母拉铆后收缩长度表 3.1.3.4 将拉铆螺母放入底孔中,放入时只能用手轻松放入,不能用其他工具将其强行敲入。安装时,铆螺母至少突出工件0.1mm。安装完成后进行铆接。铆枪必须与工件表面垂直,并且枪头与工件压紧。拉铆后检测收缩量 3.1.4检验 3.1. 4.1检测拉铆螺母拉铆后收缩长度(按表二) 3.1. 4.2检测拉铆螺母的扭矩(按表三) 表三:拉铆螺母的扭矩表 铜要求不允许线路露铜粘锡现象;阻焊油表面不允许有指纹,水纹或皱褶情形产生;零件面丝印不能有损坏的不可辨认;PCB板面不能残留助焊剂、胶质等油污, 因本厂对丝印特殊要求,如果PCB要求盖黑色油,则丝印必须为黑色。 (3)尺寸:尺寸根据我司印制板的图纸要求检验。PCB的结构、尺寸、厚度、相互配合孔应符合设计图纸要求。 (4). 连板要求:采用双面V形槽(V-割)时,两边V形槽的深度应控制在单边1/6板厚,双边1/3板厚左右,要求刻槽尺寸精确,深度均匀。 (5). 导通性:线路无短路或开路现象 (6). 零件插件孔及孔偏要求:孔破面积小于5%,沾漆(阻焊油上PAD焊盘),面积小于5%;实际线路宽度不得偏离原始设计宽度的±20%;阻焊油丝印偏移不超过±0.15mm。孔偏要求:焊盘中心孔的偏移,导致焊盘环宽的一边减少,其剩余环宽的最小值不得小于环宽的1/3。 (7).非线路之导体(残铜):非线路之导体(残铜)须离线路≥2.50mm以上,面积必须≤2.50mm,外形公差为±0.15mm, PAD(焊盘)上沾漆面积必须小于是10%原始面积。 (8).丝印附着力:丝印和绿油的附着力用3M胶纸贴在丝印或绿油覆盖处, 2秒钟后用力快速撕去,丝印或绿油应无脱落。 (9).可焊性:将PCB板过波峰焊(260±5)℃后,PCB板的所有焊盘上锡应饱满,不允许出现绿油和铜箔起泡现象,PCB上锡率≥95%。 七. 质量标准: (1).抗剥离强度:铜箔的抗剥离强度应符合以下实验: ①印制线路板在125℃±5℃连续置8小时后,基板不应有分层起泡、焊盘与基板分离、互连电路不得断开等不良现象。 ②将PCB板(正常)过波峰焊(235±5)℃后,应无绿油脱落或板材起泡现象。 发放号: 印制电路板检验规范 讨论稿 控制类别: 版本号: A 拟制/日期: 10/15/04 审核/日期: 批准/日期: 1目的 为规范印制电路板的进货检验,本规范规定了印制电路板的进货检验程序、检验要求、检验方法和抽样方案。 检验方法和抽样方案。 2适用范围 本规范适用于本公司印制电路板的进货检验。 3引用标准 GB/T2828-1987 逐批检 查计数抽样程序及抽样表(适用于连续批的检查) 4进货检验程序 印制电路板到达仓库待检区后,由仓库保管员核对印制电路板的品名、数量等。由质检部对印制电路板进行抽样检验,并负责做好检验记录和提出检验结论性意见。 5检验要求与检验方法 5.1 尺寸检验 5.1.1 检验要求 5.1.2 检验方法 用测量精度小于等于0.02mm的游标卡尺检测外形尺寸、厚度,用量角器量角度。 5.2 外观检验 5.2.1 检验要求 5.2.2 检验方法 用放大镜目测法观察,并用光绘胶片比对印制电路板,观察孔、线位置是否准确,有关尺寸用测量精度小于等于0.02mm的游标卡尺检测,用3M胶带试附着力。 5.3 电路隔离性(短路) 5.3.1 检验要求 检验印制电路板是否有短路现象。 5.3.2 检验方法 用数字万用表蜂鸣器档测量印制电路板上的电源端与地端。不应有导通现象;对目测观察有可能发生短路处,用数字万用表检查核实。 5.4 电路连接性(断路) 5.4.1 检验要求 检验印制电路板是否有断路现象。 5.4.2 检验方法 用数字万用表蜂鸣器档,检测通过仔细观察发现的可疑之处(如印制电路板铜箔被修补之处)是否有断路现象。 6抽样方案 6.1 印制电路板进行全数检验。 6.2 结构件抽样检验按GB/T2828的规定。抽样方案为一次抽样,一般检查水平Ⅱ,合格质量水平(AQL值)为1.5。 6.3 泡沫衬垫及纸箱的检验为首件检验方法,当首次进货或改变供货厂家时,需进行首件检验。 具体样本数量、合格及不合格判定数见表1。 PCBA制程能力技术规范 ____________________________________________________________________________________ 修订信息表 目录 前言 (4) 1.目的 (5) 2.适用范围 (5) 3.引用/参考标准或资料 (5) 4.名词解释 (5) 4.1 一般名词 (5) 4.2 等级定义 (5) 5.规范简介 (6) 6.规范内容 (6) 6.1 通用要求 (6) 6.1.1 文件处理 (6) 6.1.2 工艺材料 (6) 6.1.2.1 指定材料 (6) 6.1.2.2 推荐材料 (7) 6.1.3 常规测试能力 (7) 6.1.4 可靠性测试能力 (7) 6.2 工序工艺能力 (8) 6.2.1 器件成型 (8) 6.2.2 烘板 (9) 6.2.3 印刷 (9) 6.2.4 点涂 (9) 6.2.5 贴片 (9) 6.2.6 自动插件 (11) 6.2.7 回流焊 (11) 6.2.8 波峰焊 (12) 6.2.9 手工焊 (14) 6.2.10 压接、铆接 (14) 6.2.11 超声波焊接 (14) 6.2.12 超声波清洗(可选) (14) 6.2.13 清洁 (14) 6.2.14 点固定胶 (14) 6.2.15 Bonding (14) 6.2.16 返修 (15) 6.2.17 表面涂覆 (15) 6.2.18 分板 (15) 6.2.19 灌封 (17) 6.2.20 磁芯粘结能力 (17) 6.2.21 检验 (18) 6.3 成品性能 (18) 6.3.1 抽样检验 (18) 6.3.2 技术指标 (18) PCB工艺设计规范 1. 目的 规范产品的PCB工艺设计,规定PCB工艺设计的相关参数,使得PCB的设计满足可生产性、可测试性、安规、EMC、EMI等的技术规范要求,在产品设计过程中构建产品的工艺、技术、质量、成本优势。 2. 适用范围 本规范适用于所有电了产品的PCB工艺设计,运用于但不限于PCB的设计、PCB投板工艺审查、单板工艺审查等活动。 本规范之前的相关标准、规范的内容如与本规范的规定相抵触的,以本规范为准。 3. 定义 导通孔(via):一种用于内层连接的金属化孔,但其中并不用于插入元件引线或其它增强材料。 盲孔(Blind via):从印制板内仅延展到一个表层的导通孔。 埋孔(Buried via):未延伸到印制板表面的一种导通孔。 过孔(Through via):从印制板的一个表层延展到另一个表层的导通孔。 元件孔(Component hole):用于元件端子固定于印制板及导电图形电气联接的孔。 Stand off:表面贴器件的本体底部到引脚底部的垂直距离。 4. 引用/参考标准或资料 TS—S0902010001 <<信息技术设备PCB安规设计规范>> TS—SOE0199001 <<电子设备的强迫风冷热设计规范>> TS—SOE0199002 <<电子设备的自然冷却热设计规范>> IEC60194 <<印制板设计、制造与组装术语与定义>> (Printed Circuit Board design manufacture and assembly-terms and definitions) IPC—A—600F <<印制板的验收条件>> (Acceptably of printed board) IEC60950 5. 规范内容 5.1 PCB板材要求 5.1.1确定PCB使用板材以及TG值 确定PCB所选用的板材,例如FR—4、铝基板、陶瓷基板、纸芯板等,若选用高TG值的板材,应在文件中注明厚度公差。 5.1.2确定PCB的表面处理镀层 确定PCB铜箔的表面处理镀层,例如镀锡、镀镍金或OSP等,并在文件中注明。 发放号: 印制电路板检验规范 讨论稿 控制类别: _________________________ 版本号: _____________ A _____________ 拟制/日期: _______________ 10/15/04 审核/日期: __________________________ 批准/日期: __________________________ 1目的 为规范印制电路板的进货检验,本规范规定了印制电路板的进货检验程序、检验要求、检验方法和抽样方案。 检验方法和抽样方案。 2适用范围 本规范适用于本公司印制电路板的进货检验。 3引用标准 GB/T2828-1987 逐批检 查计数抽样程序及抽样表(适用于连续批的检查) 4进货检验程序 印制电路板到达仓库待检区后,由仓库保管员核对印制电路板的品名、数量等。由质检部对印制电路板进行抽样检验,并负责做好检验记录和提出检验结论 性意见。 5检验要求与检验方法 5.1尺寸检验 5.1.1 检验要求 5.1.2检验方法用测量精度小于等于0.02mm 的游标卡尺检测外形尺寸、厚度,用量角器量角度。 5.2外观检验5.2.1检验要求 522 检验方法 用放大镜目测法观察,并用光绘胶片比对印制电路板,观察孔、线位置是否准确,有关尺寸用测量精度小于等于0.02mm 的游标卡尺检测,用3M胶带试附着力。 5.3 电路隔离性(短路) 5.3.1检验要求 检验印制电路板是否有短路现象。 5.3.2检验方法 用数字万用表蜂鸣器档测量印制电路板上的电源端与地端。不应有导通现 象;对目测观察有可能发生短路处,用数字万用表检查核实。 5.4 电路连接性(断路) 541 检验要求 车架铆接工艺准则 1 目的 为加强公司的工艺管理,完善车架铆接工艺,保证车架铆接质量,提高产品竞争力,特制定本准则。 2 范围 本规范适用于本公司中重型卡车的车架总成及其零部件。 3 铆钉 3.1 铆钉材料、化学成分、机械性能应符合Q450-1995; 3.2 铆钉表面一般进行氧化处理。 4 铆钉孔 4.1 铆钉孔中心到弯曲边的最小距离(见图1)应符合表1规定。 表1 (单位:mm) 4.2 测量点 铆钉孔孔边距“X”应从图2所示测量点计起。 4.3 角度偏差 纵梁上、下翼面对腹板的角度偏差为±1°或±1.5mm (当翼板宽度为90mm时),见图3. 4.4 铆钉孔的直径,见表2. 表2 (单位:mm) 4.5 去毛刺 4.5.1 无论产品图样上是否注明去毛刺,实际加工过程中都必须对孔的两端打磨或倒角,以去除毛刺。去毛刺后,手指肚划过孔端边沿应感觉平滑、无明显凸兀感,孔内必须无残留铁屑或飞边。 4.5.2 零件装配时铆钉孔允许的最大位移量(错位量)为 1.6mm,为消除位移可采用与孔径对应的铰刀绞孔,以保证铆钉能顺利插入。 4.5.3 铆钉孔位移量不大于1.0mm时,允许使用导正销或其它方法来使铆钉顺利插入铆钉孔, 否则应绞孔至铆钉能顺利插入。 4.5.4 绞孔时铰刀的最大倾斜角为5°,铆钉插入前铆钉孔两端应按4.4.1的要求去毛刺。 5 铆接 5.1 铆钉墩头成型应为球冠形(或近似球冠形),其直径dk应不小于铆钉杆直径的 1.5倍,其高度K应不小于铆钉预制头高度,见图4。 5.2 铆钉、铆接零件表面应清洁,不得有锈层、油垢,铆钉孔不得有毛刺。 5.3 铆接后,铆钉头与钢板间及各铆接零件间的贴合面必须紧密贴合。 5.3.1 铆钉头(包括成型头及预制头)与被铆钢板间必须紧密贴合,其间隙不得大于0.05mm,见图5。 5.3.2 被铆零件间的贴合面在铆钉沿周3d(3倍铆钉杆直径)范围内必须紧密贴合,其间隙不得大于0.05mm ,见图5。 5.3.3 铆钉孔到弯边距离小于3d时,圆角部分不做上述要求。 5.4 铆接操作时,上、下铆头和铆钉应同心,以保证铆钉成形准确。 5.5 车架及其零部件采用冷铆铆接。当技术文件有明确要求时,可采用热铆铆接。 5.6 热铆铆钉加热温度为800℃~900℃,并在500℃以上完成铆接过程。 5.7 热铆铆钉在装入铆钉孔前,必须清除氧化皮,对烧损、烧细、烧坏的铆钉不允许使用。 5.8 铆接后,不符合要求的铆钉应铲去重铆;铲去铆钉时,不应损坏母体金属及相邻铆钉,其铲入深度不得超过0.5 mm。 1.目的 PCB 工艺设计规范 2. 本规范归定了我司PCB 设计的流程和设计原则,主要目的是为PCB 设计者提供必须遵循的规则和约定。提高PCB 设计质量和设计效率。提高PCB 的可生产性、可测 试、可维护性。 适用范围 本规范适用于所有电了产品的PCB 工艺设计,运用于但不限于PCB 的设计、PCB 投板工艺审查、单板工艺审查等活动。 3. 规范内容 3.1 PCBA 加工工序合理 制成板的元件布局应保证制成板的加工工序合理,以便于提高制成板加工效率 和直通率。PCB 布局选用的加工流程应使加工效率最高。 常用PCBA 的7 种主流加工流程 序号名称工艺流程特点适用范围 1 单面插装成型—插件—波峰焊接效率高,PCB 组装加热次数为一次器件为THD 2 单面贴装焊膏印刷—贴片—回流焊接效率高,PCB 组装加热次数为一次器件为SMD 3 单面混装焊膏印刷—贴片—回流焊接— THD—波峰焊接 焊膏印刷—贴片—回流焊接— THD—波峰焊接 器件为SMD、THD 4 PCB 工艺设计规范 双面混装双面混装贴片胶印刷—贴片—固化—翻效率高,PCB 组装加热次数 板—THD—波峰焊接—翻板—手工焊为二次 器件为SMD、THD 5 双面贴 装、插装 6 常规波峰焊 双面混装 7 常规波峰焊 双面混装 焊膏印刷—贴片—回流焊接—翻板— 焊膏印刷—贴片—回流焊接—手工焊 焊膏印刷—贴片—回流焊接—翻板— 贴片胶印刷—贴片—固化—翻板 —THD—波峰焊接—翻板—手工焊 焊膏印刷—贴片—回流焊接—翻板— 焊膏印刷—贴片—回流焊接—翻板 —THD—波峰焊接—翻板—手工焊 效率高,PCB 组装加热次数为 二次 效率较低,PCB 组装加热次数 为三次 效率较低,PCB 组装加热次数 为三次 器件为SMD、THD 器件为SMD、THD 器件为SMD、THD 印制电路板检验规范讨论稿(doc 10页) 发放号: 印制电路板检验规范 讨论稿 控制类别: 版本号: A 拟制/日期: 10/15/04 审核/日期: 批准/日期: 技术文件 印制电路板检验规 范页码:第 1 页共 4 页 文件号:讨论稿 版本:A 修改状 况:0 1目的 为规范印制电路板的进货检验,本规范规定了印制电路板的进货检验程序、检验要求、检验方法和抽样方案。 检验方法和抽样方案。 2适用范围 本规范适用于本公司印制电路板的进货检验。 3引用标准 GB/T2828-1987 逐批检 查计数抽样程序及抽样表(适用于连续批的检查) 4进货检验程序 印制电路板到达仓库待检区后,由仓库保管员核对印制电路板的品名、数量等。由质检部对印制电路板进行抽样检验,并负责做好检验记录和提出检验结论性意见。 5检验要求与检验方法 5.1 尺寸检验 板弓曲和扭曲对SMT板≤0.7%,特殊要求SMT板≤0.5%,对非SMT板≤1.0%;(FR-4) 对SMT板≤1.0%,对非SMT板≤1.5%;(高频材料) 板厚公差厚度应符合设计文件的要求 板厚≤1.0mm,公差±0.10mm;板厚≥1.0mm,公差为±10% 外形公差外形尺寸应符合设计文件的要求 板边倒角(30o、45o、70o)±5o;CNC铣外形:长宽小于100mm公差±0.2mm; 长宽小于300mm公差±0.25mm;长宽大于300mm公差±0.3mm;键槽、凹槽开口:±0.13mm;位置尺寸:±0.20mm V形槽V槽深度允许偏差为设计值的±0.1mm;槽口上下偏移公差K:±0.15mm;D≤0.8mm,余留基材厚度S=0.35±0.15mm;0.8 军品PCB工艺设计规范 1. 目的 规范军品的PCB工艺设计,规定PCB工艺设计的相关参数,使得PCB的设计满足可生产性、可测试性、安规、EMC、EMI等的技术规范要求,在产品设计过程中构建产品的工艺、技术、质量、成本优势。 2. 适用范围 本规范适用于所有军品的PCB工艺设计,运用于但不限于PCB 的设计、PCB投板工艺审查、单板工艺审查等活动。本规范之前的相关标准、规范的内容如与本规范的规定相抵触的,以本规范为准。 3. 定义 导通孔(via):一种用于内层连接的金属化孔,但其中并不用于插入元件引线或其它增强材料。 盲孔(Blind via):从印制板内仅延展到一个表层的导通孔。 埋孔(Buried via):未延伸到印制板表面的一种导通孔。 过孔(Through via):从印制板的一个表层延展到另一个表层的导通孔。 元件孔(Component hole):用于元件端子固定于印制板及导电图形电气联接的孔。 孔化孔(Plated through Hole):经过金属化处理的孔,能导电。 非孔化孔(Nu-Plated through Hole):没有金属化理,不能导电,通常为装配孔。 装配孔:用于装配器件,或固定印制板的孔。 定位孔:指放置在板边缘上的用于电路板生产的非孔化孔。 光学定位点:为了满足电路板自动化生产需要,而在板上放置的用于元件贴装和板测试定位的特殊焊盘。 Stand off:表面贴器件的本体底部到引脚底部的垂直距离。 回流焊(Reflow Soldering):一种焊接工艺,既熔化已放在焊点上 的焊料,形成焊点。主要用于表面贴装元件的焊接。 波峰焊(Wave Solder):一种能焊接大量焊点的工艺,即在熔化焊料形成的波峰上,通过印制板,形成焊点。主要用于插脚元件的焊接。 PBA(Printed Board Assembly):指装配元器件后的电路板。 4. 引用/参考标准或资料 5. 规范内容 5.1 PCB板材要求 5.1.1确定 PCB使用板材以及 TG值 确定PCB所选用的板材,例如FR—4、铝基板、陶瓷基板、纸芯板等,若选用高TG值的板材,应在文件中注明厚度公差。 5.1.2确定 PCB的表面处理镀层 确定PCB铜箔的表面处理镀层,例如镀锡、镀镍金或OSP等,并在文件中注明。 5.2热设计要求 5.2.1 高热器件应考虑放于出风口或利于对流的位置 PCB 在布局中考虑将高热器件放于出风口或利于对流的位置。 5.2.2 较高的元件应考虑放于出风口,且不阻挡风路 5.2.3 散热器的放置应考虑利于对流 5.2.4 温度敏感器械件应考虑远离热源 对于自身温升高于30℃的热源,一般要求: a.在风冷条件下,电解电容等温度敏感器件离热源距离要求大于或等于2.5mm; PCBA铆接工艺规范 华为技术有限公司企业技术规范 DKBA3054-2003.04 PCBA铆接工艺规范 2003-05-01发布 2003-05-01实施 华为技术有限公司发布 目次 前言 .............................................................. 3 1 范围和简介 (4) 1.1 范围 (4) 1.2 简介 (4) 1.3 关键词 (4) 2 规范性引用文件.................................................... 4 3 术语和定义 (4) 4 规范内容 (5) 4.1 铆接工艺结构设计要求 (5) 4.1.1 欧式连接器和护套的铆接 (5) 4.1.2 拉手条、扳手、加强筋铆接 (6) 4.2 铆接调制基本要求 (8) 4.2.1 合理选用拉铆杆与拉铆杆的使用控制 (8) 4.2.2 铆接设备调制操作要求 (9) 4.3 质量要求 (9) 4.3.1 欧式连接器、护套铆接 (10) 4.3.2 拉手条、扳手、加强筋铆接 ............................. 10 5 附录A:铆接设备性能.............................................. 10 6 参考文献 (11) 密级:秘密 DKBA3054-2003.04 前言 本规范的其他系列规范:无 与对应的国际标准或其他文件的一致性程度:无 规范代替或作废的全部或部分其他文件:无 与其他规范或文件的关系:无 与规范前一版本相比的升级更改的内容:第一版,无升级更改信息。 本规范由单板工艺研究部提出。 本规范主要起草和解释部门:单板工艺研究部 本规范主要起草专家:单板工艺研究部:王振华(09545)、李文建(16921) 本规范主要评审专家:单板工艺研究部:王界平(07531)、张小毛(11514)、付应虎(08634)、罗美春(18024)、张国栋(29723)、刘常康(17222)、张寿开(19913)、金俊文(18306),质量工艺部:倪刚(08368)、刘向阳(18988)、王壁(07249),TQC:李布劲(06721),整机工程部:侯树栋(10084)、刘恒(20098) 本规范批准人:吴昆红 本规范所替代的历次修订情况和修订专家为:无 规范号主要起草专家主要评审专家 2016-06-14,21:45:50 3 PCBA铆接工艺规范 1 范围和简介 1.1 范围 1.0 目的 为确保PCB线路板的质量满足客户需求,为检验和质量控制提供判定依据,统一内部检验可接受标准。 2.0 适用范围 本规范适用于所有高频RF35/RF60材质及普通FR4材质PCB的进料检验。 3.0 参考文件 3.1 GB2828-2003 《逐批检查计数抽样程序及抽样表》 3.2 JCG-XX-XXX-XXX 来料不合格等级分类规范 3.3 XXX-XXX-XXXX《进料检验与试验控制程序》 3.4 XXX-XXX-XXX《进料检验管理规范》 3.5 IPC-A-600D:Acceptability of printed boards 3.6 IPC-6012:Qualification and performance specification for rigid printed boards 3.7 《来料包装标识通用规范》 4.0 检验方式及接收判别标准 4.1依据GB2828-2003计数型抽样标准,正常一次性抽样方案 4.2 抽样等级---正常抽样(II) 4.3允许水准: 严重缺陷AQL=0.65,轻微缺陷 AQL=1.5 5.0 本标准采用下列定义 5.1 严重缺陷:影响PCB线路板性能或严重影响PCB线路板外观的缺陷; 5.2 轻微缺陷:影响PCB线路板外观质量。 6.0 检验条件以及检验工具 6.1 应在白色荧光灯照明良好的区域进行检验; 6.2 对所有表面进行检验时,光线都不能直接反射到观测者; 6.3 目视检测应在放大1.75倍(屈光率为3)下进行,如果缺陷为不易于显现的,则必须放大40倍进行检测。对于尺寸 检测要求,例如间距或导线宽度的测量可以要求采用其它放大倍数并配有标线刻度的仪器以达到尺寸的精确测量。对于镀通孔部位必须在100X±5%的放大倍数下检查铜箔与孔壁镀层的完整性。 6.4 按上述5.0检验无明显缺陷的产品均视为合格品。不能有意识地长时间观察某一部位来进行目视检验判断。 6.5 游标卡尺、水平尺、放大镜、显微镜、百倍镜、卷尺、大理石平台、刀口尺。 7.0 检验注意事项 7.1 送检PCB线路板必须开具送检单,其内容(名称、版本号、数量、日期)符合要求; 7.2 当物料或产品有异常而生产需求迫切时,必须依照《MRB处理作业指引》提出申请; ---------------------------------------------------------------------------------------------------------------------------------------------------------------- 企业标准 QB/ 002–2014电路板(PCBA)制造技术规范 2013-05-04发布 2014-05-10实施 科技有限公司- 发布 修订声明 ?本规范于2013年05 月04日首次试用版发布。 ?本规范拟制与解释部门: ?本规范起草单位: ?本规范主要起草人:范学勤 ?本规范审核人: ?标准化审核人: ?本规范批准人: ●本规范修订记录表: 修订日期版本修订内容修订人2013-05-04A试用版发行 2014-5-10B修改使用公司名称 目录 封面: 电路板(PCBA)制造技术规范 (11) 修订声明 (22) 目录 (33) 前言 (55) 术语解释 (66) 第一章 PCBA制造生产必要前提条件 (77) 1.1 产品设计良好: (77) 1.2 高质量的材料及合适的设备: (77) 1.3 成熟稳定的生产工艺: (77) 1.4 技术熟练的生产人员: (88) 附图1 SCC标准PCBA生产控制流程 (88) 附图2 SCC标准SMT工艺加工流程 (99) 第二章车间温湿度管控要求 (1010) 2.1 车间内温度、相对湿度要求: (1010) 2.2 温度湿度检测仪器要求: (1010) 2.3 车间内环境控制的相关规定: (1010) 2.4 温湿度日常检查要求: (1010) 第三章湿度敏感组件管制条件 (1111) 3.1 IC类半导体器件烘烤方式及要求: (1111) 3.2 IC类半导体器件管制条件: (1111) 3.3 PCB管制规范: (1212) 第四章表面组装元器件(SMC/SMD)概述 (1313) 4.1 表面组装元器件基本要求: (1313) 4.2 表面组装元器件(SMC/SMD)的包装类型: (1313) 4.3 表面组装元器件使人用注意事项: (1414) 第五章 SMT工艺概述 (1515) 5.1 SMT工艺分类: (1515) 5.2 施加焊膏工艺: (1616) 5.3 施加贴片红胶工艺: (1717) 随着智能产品快速发展,让市场涌现出许多的外包服务平台,同样都是打着快速、专业等一系列口号,借着互联网春风大势传播,但其提供的服务往往停留在浅薄的层次,所以在选择外包服务平台的同时须了解他们平台是否具备该垂直领域的专业性很重要。 一、选择外包服务平台之前,需要考虑他们的基因 迅得电子成立于2005年,现已发展为一站式批量生产服务商,所涉服务包括PCB定制、样板组装、SMT贴片、DIP焊接、插件后焊、成品组装、元器件采购等。迅得电子提供的产品和服务广泛应用于通讯、工控、医疗、汽车、消费、物联网等各个领域。 本公司拥有1200㎡SMT防静电无尘车间,配备高度自动化电子组装生产线,先进的贴片设备,以及专业的检测仪器,能够快速地实现高难度、小批量电子组装任务,日均贴片高达200万点(20小时),波峰焊接3.5万件(12小时),可贴装0201,01005等器件,器件种类涉及密脚IC,QFN,QFP,BGA,WLCSP等。本公司专业的料件采购团队能够为客户提供多面的全BOM料件采 购服务,一次性满足客户对料件采购的多样性需求,并能实现在保证质量的前提下进行有效的成本控制。 二、电子组装服务 一个典型的电子组装过程包括:焊膏印刷、贴片、回流焊、波峰焊、测试等,下面对这些工序进行介绍: 1.焊膏印刷 焊膏印刷是SMT工艺中的首道工序,通过使用印刷机将焊膏从网板开孔中漏印到PCB焊盘上。据统计60%~70%焊接缺陷是由焊膏印刷不良造成的。要实现高品质焊膏印刷除了要考虑焊膏选择、焊膏印刷参数外,对PCB板设计加工也提出了具体要求。 2.贴片 贴片工艺技术是SMT产品组装生产中的关键工序。SMC/SMD(表面贴装元器件)贴装一般采用贴片机自动进行。贴片机是SMT产品组装生产线中的核心设备,也是SMT的关键设备,决定着SMT产品组装的自动化程度。 贴片的主要动作包括基板定位、元件拾取、元件定位、元件贴片等,要实现 印制电路板(PCB)检验规范 ————————————————————————————————作者:————————————————————————————————日期: 标准修订记录表 修订次数处数更改号修订日期修订人 1 BG003790862009/08/29伍宏文 2 BG003840882009/09/26陈友桂 3 BG004048882010/01/23 陈友桂 4 BG00449522 2010/10/21 梁峰 5 BG004743982011/03/07梁峰 QJ 股份有限公司标准 QJ/GD 41.10.020 代替J12.10.504印制电路板(PCB)检验规范 2011-03-14发布2011-03-14实施电器股份有限公司发布 目次 前言............................................................................. II 1 范围 (1) 2 规范性引用文件 (1) 3 术语和定义 (1) 4 技术要求 (2) 5 试验要求和方法 (6) 6 检验规则 (11) 7 标志、包装、运输和贮存 (11) 附录A(资料性附录)电迁移试验方法指导 (13) 附录B(规范性附录)经确认备案的各种材质覆铜板基材生产厂家 (15) 附录C(规范性附录)外观检验标准 (16) 附录D(规范性附录)检验报告模板 (17) 前言 电器股份有限公司技术标准是公司标准化技术委员会发布的标准,作为公司内部使用的技术法规性文件。 本标准与前一版本相比主要变化如下: ——完善PCB板V-CUT尺寸的要求。 ——完善翘曲度的试验要求和方法。 本标准由珠海格力电器股份有限公司提出。 本标准由珠海格力电器股份有限公司标准化技术委员会归口。 本标准由珠海格力电器股份有限公司制冷技术研究院、家用空调技术部、标准管理部、筛选分厂起草。 本标准主要起草人:李茜、欧毓迎、熊斌、刘涛、梁峰。 本标准本次修订人:金燎原、梁峰 本标准于2009年5月首次发布,第一次修订为2009年8月,第二次修订为2009年9月,第三次修订为2010年2月,第三次修订为2010年10月,本次修订为第五次修订。 PCBA生产加工通用操作规范要求 目录 1 目的 (4) 2 范围 (4) 3 术语与定义 (4) 4 引用标准和参考资料 (4) 5 写片要求 (4) 6 PCBA加工过程中辅料使用要求 (4) 7 表面贴装(SMT)工序 (5) 7.1 PCB烘烤要求 (5) 7.2 PCB检查要求 (5) 7.3 丝印机及钢网制作要求 (5) 7.3.1. 印刷设备的要求 (5) 7.3.2. 量产产品的钢网制作要求 (5) 7.4 焊膏使用要求 (5) 7.5 贴片要求 (6) 7.6 回流焊接曲线制订及测试要求 (6) 7.6.1. 回流焊接曲线制订 (6) 7.6.2. 热电偶选用及放置要求 (6) 7.6.3. 回流焊接曲线测试频率 (6) 7.7 炉后检查要求 (7) 7.8 湿敏感器件的确认、储存、使用要求 (7) 8 ESD防护 (9) 9 返修工序 (9) 9.1 电烙铁要求 (9) 9.2 BGA返修台要求 (9) 9.3 使用辅料要求 (9) 9.4 返修焊接曲线要求 (9) 10 物料使用要求 (10) 10.1 型号和用量要求 (10) 10.2 分光分色要求 (10) 10.3 插座上的附加物处理要求 (10) 11 元件成型 (10) 11.1 元件成形的基本要求 (10) 11.2 元器件成型技术要求 (10) 11.3 质量控制 (11) 11.3.1. 元件成型的接收标准 (11) 12 波峰焊接(THT)/后焊工序 (12) 12.1.1. 波峰焊接时板面温度要求 (12) 12.1.2. 浸锡温度和时间要求 (12) 12.1.3. 波峰焊温度曲线测试要求 (12) 12.2 插装器件安装位置要求 (12) 12.3 对于多引脚的连接器焊接工艺要求 (12) 12.4 分板后去除板边毛刺要求 (12) 13 清洗 (13) 13.1 超声波清洗 (13) 13.1.1. 超声波清洗的注意事项 (13) 13.1.2. 超声波清洗设备要求 (13) 13.2 水洗 (13) 13.2.1. 水洗工艺的注意事项 (13) 13.2.2. 清洗时间要求 (13) 13.3 手工清洗 (13) 13.4 清洗质量检查 (13) 14 点胶要求 (14) 14.1 点胶原则 (14) 14.2 点胶的外观要求: (14) 15 压接要求 (14) 15.1 压接设备要求 (14) 15.2 压接过程要求 (14) 15.3 压接检验 (14) 16 板卡上标识要求 (15) 17 包装要求 (15) DKBA 华为技术有限公司企业技术规范 DKBA3054-2003.04 PCBA铆接工艺规范 2003-05-01发布2003-05-01实施 华为技术有限公司发布 目次 前言 (3) 1范围和简介 (4) 1.1范围 (4) 1.2简介 (4) 1.3关键词 (4) 2规范性引用文件 (4) 3术语和定义 (4) 4规范内容 (5) 4.1铆接工艺结构设计要求 (5) 4.1.1欧式连接器和护套的铆接 (5) 4.1.2 拉手条、扳手、加强筋铆接 (6) 4.2铆接调制基本要求 (8) 4.2.1合理选用拉铆杆与拉铆杆的使用控制 (8) 4.2.2铆接设备调制操作要求 (9) 4.3质量要求 (9) 4.3.1欧式连接器、护套铆接 (10) 4.3.2拉手条、扳手、加强筋铆接 (10) 5附录A:铆接设备性能 (10) 6参考文献 (11) 前言 本规范的其他系列规范:无 与对应的国际标准或其他文件的一致性程度:无 规范代替或作废的全部或部分其他文件:无 与其他规范或文件的关系:无 与规范前一版本相比的升级更改的内容:第一版,无升级更改信息。 本规范由单板工艺研究部提出。 本规范主要起草和解释部门:单板工艺研究部 本规范主要起草专家:单板工艺研究部:王振华(09545)、李文建(16921) 本规范主要评审专家:单板工艺研究部:王界平(07531)、张小毛(11514)、付应虎(08634)、罗美春(18024)、张国栋(29723)、刘常康(17222)、张寿开(19913)、金俊文(18306),质量工艺部:倪刚(08368)、刘向阳(18988)、王壁(07249),TQC:李布劲(06721),整机工程部:侯树栋(10084)、刘恒(20098)本规范批准人:吴昆红 本规范所替代的历次修订情况和修订专家为:无 - 代替Q/ZX 04.100.1-2001A 2002-04-11 发布 2002-05-15 实施 深圳市中兴通讯股份有限公司 发 布 印制电路板设计规范 ——文档要求 Q/ZX 04.100.1 – 2002 Q/ZX 深圳市中兴通讯股份有限公司企业标准 (设计技术标准) Q/ZX 04.100.1 – 2002 目次 前言.................................................................... II 1 范围 (1) 2 规范性引用文件 (1) 3 定义 (1) 3.1 非金属化孔 (1) 3.2 机械加工图 (1) 3.3 字符 (1) 4 总要求 (1) 5 齐套性要求 (1) 6 一致性要求 (3) 6.1 文件输出前检查 (3) 6.2 文件间、文件与实物间的一致性要求 (3) 7 规范性要求 (3) 7.1 图纸封面 (3) 7.2 PCB文件首页 (3) 7.3 PCB图的标题栏 (4) 7.4 字符图 (4) 7.5 钻孔图 (4) 7.6 外形图 (7) 7.7 拼版图 (7) 附录A (11) 附录B (14) Q/ZX 04.100.1 – 2002 前言 Q/ZX 04.100《印制电路板设计规范》是系列标准,包括以下部分: 第1部分(即Q/ZX 04.100.1):文档要求; 第2部分(即Q/ZX 04.100.2):工艺性要求; 第3部分(即Q/ZX 04.100.3):生产可测试性要求; …… 它们从不同方面对印制电路板设计提出要求。 本标准是第1部分,是在Q/ZX 04.100.1-2001A《印制电路板设计规范——文档要求》基础上进行修订的。修订的内容主要有: a)对表1中齐套性的要求进行了修订,在PCB图中增加了测试数据文件。 b)修改了表1(文件齐套性表)注1中要求的内容,并变为可包含要求的表的脚注形式,简化了钻孔图中尺寸标注方法的要求。 c)在表1中增加图纸层面的叠放顺序; d)表1中的表示方法做了修改,把以前的符号改为“是”与“否”,便于阅读; e)输出PCB光绘文件格式增加了GERBER600; f)来料检验的依据改为光绘文件和拼版图; g)在第7章中增加了图纸封面的要求,增加了关于PCB文件封面的格式和模板; h)对印制板文件的格式要求做了明确规定,并有示例。 i)非金属化孔的要求有所改变; j) 6.1中增加了应“100%通过布通率检查”的要求; k)增加了PCB上防静电标识的规定; l)钻孔图中更明确对于尺寸标注、标注方法、技术要求的内容和要点; m)增加对于外形图文档的有关规定,明确了外形图和钻孔图应分别提供的信息; n)7.5.5技术要求中增加了特性阻抗的要求。 o)增加“7.7拼版图”的要求; p)去掉了表4印制板尺寸公差。 q)增加了PCB编码方法(附录A)的要求; r)增加了附录C,提供12个标注例供参考。 s)标明每次的标准修订人身份。 本标准自实施之日起代替Q/ZX 04.100.1-2001A。 由于此次修订改动较大,本标准除PCB编码要求(见附录A)外,自实施之日起试行半年。 本标准的实施方法: 自Q/ZX 04.100.1-2002实施之日起: 标准修订记录表 QJ 股份有限公司标准 印制电路板(PCB)检验规范 电器股份有限公司发布 目次 前言............................................................................. II 1 范围 (1) 2 规范性引用文件 (1) 3 术语和定义 (1) 4 技术要求 (2) 5 试验要求和方法 (6) 6 检验规则 (11) 7 标志、包装、运输和贮存 (12) 附录A(资料性附录)电迁移试验方法指导 (13) 附录B(规范性附录)经确认备案的各种材质覆铜板基材生产厂家 (15) 附录C(规范性附录)外观检验标准 (16) 附录D(规范性附录)检验报告模板 (17) 前言 电器股份有限公司技术标准是公司标准化技术委员会发布的标准,作为公司内部使用的技术法规性文件。 本标准与前一版本相比主要变化如下: ——完善PCB板V-CUT尺寸的要求。 ——完善翘曲度的试验要求和方法。 本标准由珠海格力电器股份有限公司提出。 本标准由珠海格力电器股份有限公司标准化技术委员会归口。 本标准由珠海格力电器股份有限公司制冷技术研究院、家用空调技术部、标准管理部、筛选分厂起草。 本标准主要起草人:李茜、欧毓迎、熊斌、刘涛、梁峰。 本标准本次修订人:金燎原、梁峰 本标准于2009年5月首次发布,第一次修订为2009年8月,第二次修订为2009年9月,第三次修订为2010年2月,第三次修订为2010年10月,本次修订为第五次修订。 印制电路板(PCB)检验规范 1 范围 本标准规定了印制电路板(PCB)的术语和定义、技术要求、试验要求和方法、检验规则、标志、包装、运输和贮存。 本标准适用于印制电路板(PCB)。 2 规范性引用文件 下列文件对于本文件的应用是必不可少的。凡是注日期的引用文件,仅注日期的版本适用于本文件。凡是不注日期的引用文件,其最新版本(包括所有的修改单)适用于本文件。 GB/T 4677 印制板测试方法 QJ/GD 12.12.004 环保标识使用管理规定(试行) QJ/GD 40.01.011 外协外购件入厂检验通则 QJ/GD 92.00.001 环保产品中有害物质控制管理规定 IPC-6012 刚性印制板的鉴定及性能规范 IPC-9253 CAF 测试板 IPC-9254 CAF 测试板 IPC-SM-840 永久阻焊油墨的鉴定及性能规范 IPC-TM-650 测试方法手册 3 术语和定义 3.1 PCB 印制电路或者印制线路的成品板称为印制电路板或者印制线路板,亦称印制板,英文名称是Printed Circuit Board,缩写:PCB,以下简称为PCB板。 3.2 印制电路 绝缘基材上,按预定设计形成的印制元件或印制线路以及两者结合的导电图形。 3.3 印制板 印制电路或印制线路成品板的通称。它包括刚性、挠性和刚挠结合的单面、双面和多层印制板等。 3.4 印制元件 用印制方法制成的元件(如印制电感、电容、电阻、传输线等),它是印制电路导电图形的一部分。 3.5 元件面 安装有大多数元器件的一面。 3.6 焊接面 通孔安装印制板与元件面相对的一面。 3.7 印制 用任一种方法在表面上复制图形的工艺。铆接工艺规范
PCB板检验规范
印制电路板检验规范
PCBA制程能力技术规范V1.0
线路板PCB布板焊接加工工艺文件
印制电路板检验规范标准
车架铆接工艺准则
PCBA工艺设计规范
印制电路板检验规范讨论稿(doc 10页)
军工优质PCB工艺设计规范汇总
pcba铆接工艺规范
PCB印刷线路板检验规范
电路板PCBA制造技术规范
电子外包组装服务
印制电路板(PCB)检验规范
PCBA生产通用工艺流程操作规范标准作业指导书(参考Word)
PCBA铆接工艺规范
印制电路板设计规范—文档要求
印制电路板(PCB)检验规范