方案十三(催化剂硫化方案)
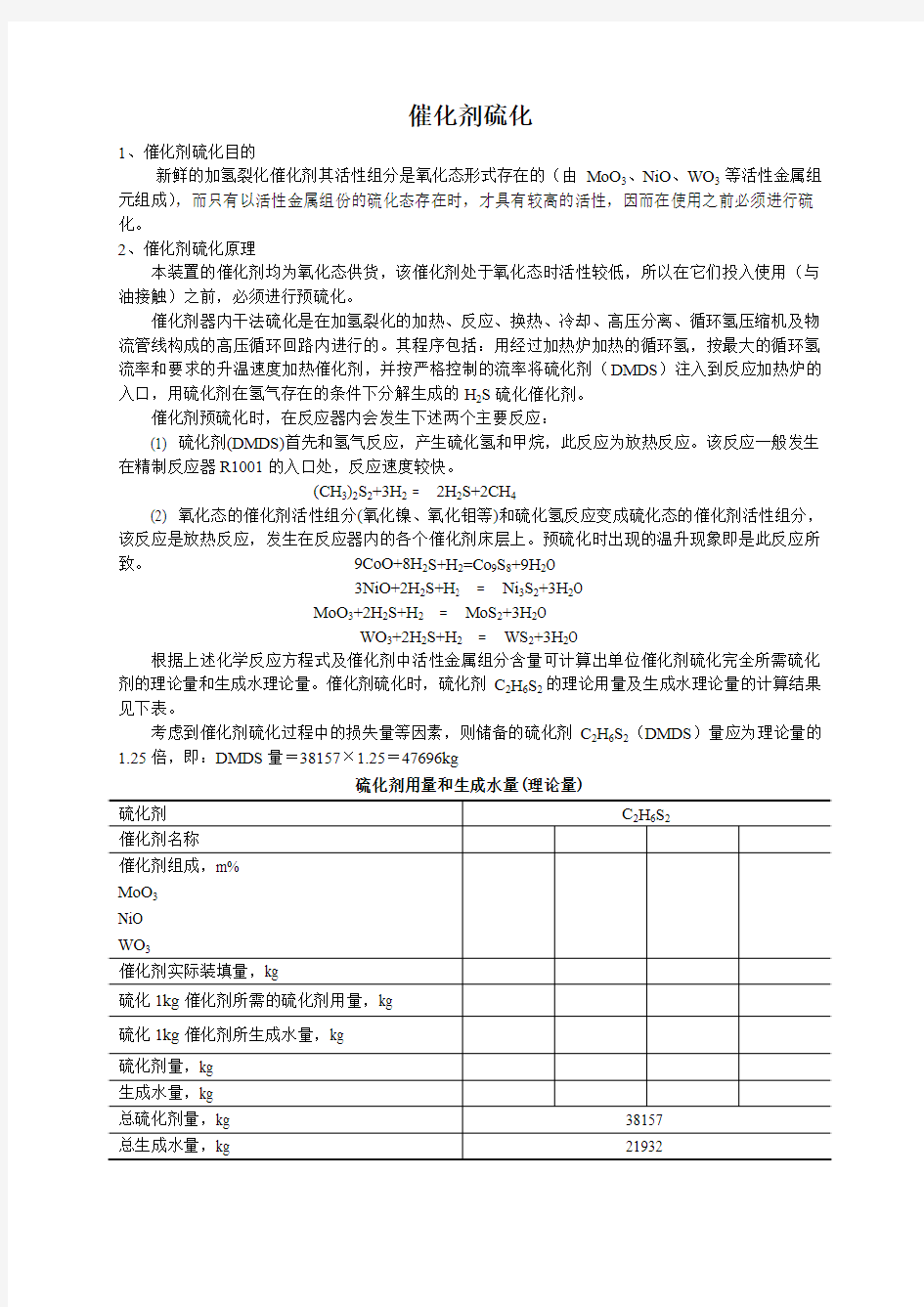

催化剂硫化
1、催化剂硫化目的
新鲜的加氢裂化催化剂其活性组分是氧化态形式存在的(由MoO3、NiO、WO3等活性金属组元组成),而只有以活性金属组份的硫化态存在时,才具有较高的活性,因而在使用之前必须进行硫化。
2、催化剂硫化原理
本装置的催化剂均为氧化态供货,该催化剂处于氧化态时活性较低,所以在它们投入使用(与油接触)之前,必须进行预硫化。
催化剂器内干法硫化是在加氢裂化的加热、反应、换热、冷却、高压分离、循环氢压缩机及物流管线构成的高压循环回路内进行的。其程序包括:用经过加热炉加热的循环氢,按最大的循环氢流率和要求的升温速度加热催化剂,并按严格控制的流率将硫化剂(DMDS)注入到反应加热炉的入口,用硫化剂在氢气存在的条件下分解生成的H2S硫化催化剂。
催化剂预硫化时,在反应器内会发生下述两个主要反应:
(1) 硫化剂(DMDS)首先和氢气反应,产生硫化氢和甲烷,此反应为放热反应。该反应一般发生在精制反应器R1001的入口处,反应速度较快。
(CH3)2S2+3H2 = 2H2S+2CH4
(2) 氧化态的催化剂活性组分(氧化镍、氧化钼等)和硫化氢反应变成硫化态的催化剂活性组分,该反应是放热反应,发生在反应器内的各个催化剂床层上。预硫化时出现的温升现象即是此反应所致。9CoO+8H2S+H2=Co9S8+9H2O
3NiO+2H2S+H2 = Ni3S2+3H2O
MoO3+2H2S+H2= MoS2+3H2O
WO3+2H2S+H2= WS2+3H2O
根据上述化学反应方程式及催化剂中活性金属组分含量可计算出单位催化剂硫化完全所需硫化剂的理论量和生成水理论量。催化剂硫化时,硫化剂C2H6S2的理论用量及生成水理论量的计算结果见下表。
考虑到催化剂硫化过程中的损失量等因素,则储备的硫化剂C2H6S2(DMDS)量应为理论量的1.25倍,即:DMDS量=38157×1.25=47696kg
硫化剂用量和生成水量(理论量)
硫化过程中还可能有不希望发生的副反应:氧化态的催化剂活性组分(氧化镍、氧化钼、氧化钨)被氢气还原,生成金属单质和水,这会极大损害催化剂的活性。该反应危害极大,应尽量避免发生。这个副反应在有氢气存在,无硫化氢的条件下,温度越高(大于230℃),越容易发生。
3、化准备工作
3.1反应系统最终气密合格,收尾工作结束。
3.2硫化剂注入系统准备完毕,注入点盲板开通具备注入条件。
3.3氢气管网具备供给稳定、合格、充足氢气的能力,氢气浓度在线分析仪已经投用。
3.4硫化所用工具、资料、图表等各部门均已做好准备。
3.5维持反应系统流程不变,改好硫化部分流程,检查急冷氢线上的阀门操作性能,然后关闭两器各路急冷氢控制阀。
3.6注硫泵P-105确认单机试运合格。
3.7硫化剂DMDS已经按要求装入硫化剂罐。
3.8高压仪表、报警、联锁、ESD系统,已经全面测试好用。检查和关闭硫化流程中现场所有铜制压力表的手阀(必须留用的,硫化后更换新表),防止铜制部分H2S腐蚀(直到钝化结束)。
3.9硫化过程中所需要的工具、安全措施已经落实。
3.10检查D-105底酸性水采样阀是否灵活好用,D-105能够准确计量硫化过程中生产的水。
3.11通知化验车间,做好氮气和氢气纯度、循环氢中硫化氢浓度、酸性水中硫含量分析的准备。
3.12做好现场测定循环氢露点的准备。
4、硫化初始条件
R101入口温度 190℃R101床层任一点温度>175℃
R102入口温度 190℃
循环氢中氢浓度>85%
冷高分温度≯50℃
以尽可能大的流率循环氢气,调节两炉循环氢流率。
5、硫化步骤
5.1引硫化剂进入系统
(1)确认硫化流程:硫化剂在加热炉(F-101)入口与循环氢混合,经加热后进入加氢精制反应器(R-101),然后进入加氢裂化反应器(R-102),对催化剂进行预硫化。循环气自裂化反应器出来后经(E-101)与冷循环氢换热、经(E102)与低分油换热降温后进入热高压分离器(D-103)。循环气自热高压分离器出来后经(E-103)与冷循环氢换热、经(E107与低分油换热,之后经空冷器(A-101)冷至50℃,进入冷高压分离器(D-105)。气体自顶部出来,进入(C101)循环氢脱硫塔后,再经循环氢分液罐(D-107)进入循环氢压缩机实现循环氢的循环。催化剂硫化过程中产生的水间断从冷高分(D-3105)底部排除。
(2)启动P105,先向放空线排放3-5分钟。加热炉入口处设一操作人员先打开F-101入口第一道阀(Y型止回截止阀),另一操作人员逐步关小返回阀,将P-105出口压力憋至16.0MPa(G),F-101入口操作人员稍开DMDS注入加热炉的第二道阀,把DMDS注入到F-101入口管路中,关闭返回阀。注入硫化剂的操作要特别的小心,防止气体回窜。
(3)泵缓慢将注硫量从500Kg/h升到1885Kg/h(按290000nm3/h循环氢计算)。注意任何时候都不得超过1885Kg/h此速率,每次提量为200kg/h,间隔为10分钟(注意最大注硫量为65kgDMDS/万Nm3循环氢,任何时候都不得超过此注入量。)。
(4)察催化剂床层温升情况,大约会有15-30℃的温升,这个温波通过反应器大约用1~2小时,温波通过后才能继续下一步工作。在该温波未通过反应器催化剂床层之前,应保持R-101入口温度,硫化操作不应往下一步进行。温波超过30℃要降低硫化剂注入量
(5)如果注入DMDS后5分钟内,观察不到R-101床层入口温度的上升,检查是否DMDS已
经注入,若已经注入则停止。提高R-101入口温度至195℃,再恢复注入DMDS。如果再次注入DMDS 后5分钟内,还观察不到R-101床层入口温度的上升,停止注入DMDS,检查原因。
(6)随着硫化的进行会不断有甲烷生成,为了保持循环氢中必要的氢气浓度>75%(V)需外排循环氢入火炬系统并补新氢。
(7)开始注硫后,每半小时分析一次R102出口循环氢的H2S含量及露点,直到测出H2S后,改为每小时测一次。催化剂硫化过程中,在冷高分中会有水出现,记录冷高分液面,液面较高时可排放部分酸性水。每小时采样分析一次酸性水中的硫含量,注意防止硫化氢中毒。
5.2 230℃硫化阶段
(1)吸附温波过后,以≯3℃/h的速度(此速度依开工方案可做调整),平稳升R101入口温度,直到床层最高温度达到230℃,此时R101入口温度大约为200~210℃。
(2)在R102出口测出H2S之前,不允许任何一床层,任何点温度超过230℃,若出现超过230℃的温度点,则采取降低硫化剂注入速度的办法使之降下来,同时维持R101入口温度不上升,直到温度被控制住为止。密切观察床层任一点温度≯230℃,任意床层温升≯28℃,否则减少DMDS 的注入量。预硫化期间,任意床层温升≯28℃。
(3)确认H2S穿透反应器各床层之后,调整硫化剂的注入速度,维持循环氢中H2S含量在1000ppm~5000ppm。
(4)调整操作,使R101入口温度达到230℃,保持恒温8小时以上,在反应器入口温度高于230℃前,R102出口流出物露点必须低于-19℃。
(5)升温时,要注意在H2S含量接近5000ppm时进行,以防止因升温而造成H2S含量回降至1000ppm以下。
(6)硫化开始后,会不断有水生成,要设专人负责生成水的记录、计量工作。D103要用专门的计量器计量,在没有特别要求的情况下,每1小时排一次水。要求绘制出硫化过程中
相应曲线,如温度和生成水曲线,DMDS注入速度和生成水关系曲线等。
5.3 230~290℃升温阶段
(1)完成230℃恒温,R102出口流出物露点<-19℃,调整DMDS注入速度,使R102出口测得的H2S浓度在5000~10000ppm,并继续保持此范围。
(2)以≯4℃/h的速度将R101入口温度升至290℃,升温过程中每30分钟测一次R102出口循环氢中H2S含量和露点,若发现露点>-19℃或H2S浓度低于5000ppm,则停止升温。
5.4 290~370℃升温阶段
(1)当R101入口温度达到290℃后,即以≯6℃/h的速度将R101入口温度升至370℃。继续维持R102出口流出物中H2S浓度为5000~10000ppm,露点<-19℃。
(2)当升高反应器入口温度,催化剂床层最高温度超过入口温度25℃时,不要再提入口温度,若最高温度继续升高,超过35℃,则停注DMDS,把入口温度降低30℃,但不允许循环
氢中的H2S浓度小于2000ppm。如果反应器温度不能采取降低加热炉温度控制,且反应器
内任一点温度已超过400℃,此时应采用0.7MPa/min泄压系统,并将加热炉熄灭,引入
氮气冷却反应器(氮气纯度在99.9%以上)。
注意:非特殊情况下,一般不使用急冷氢降低床层温度。
5.5 370℃恒温阶段
在R101入口温度达到370℃,温度恒定的条件下保持H2S含量在10000~20000ppm,使各反应器入口均达到370℃,然后恒温8小时以上。
5.6硫化终点判定
R101、R102入口温度均为370℃,循环氢中H2S含量10000~20000ppm条件下
(1)R101入口气体与R102出口气体的露点差≯3℃。
(2)R101入口气体与R102出口气体的H2S含量相同。
(3) D105无水生成。
(4) 硫化剂实际注入量达到或接近理论注硫量。
达到以上条件即可认为到了硫化终点,然后保持条件继续恒温1小时。 5.7冷却
(1) 排净D105的生成水。 (2) 进行急冷氢系统试验。
A .试验各阀的开关灵活性、准确性。
B .检验阀位与控制信号的一致性。
C .检验控温效果:记录温度变化幅度及滞后时间,要求从R102最后一床层开始逐个向前试验,记录全部过程中各床层温度变化情况,当阀开度为50%时,床层温降大于15℃,即认为合格。
(3) 逐渐降低DMDS 的注入量,但应保持系统内H 2S 含量不小于1000ppm 。
(4) 以≯25℃/h 的速度降R101、R102入口温度至150℃(保证热高分温度>121℃)。 6硫化过程中有关记录
6.1硫化曲线
0 18 26 41 55 63 72
时间 /h
催化剂预硫化升温曲线
6.2硫化程序控制指标
催化剂干法硫化的控制指标主要有:各硫化阶段的升温速度、循环氢中H 2S 含量、床层温升、裂化反应器出口循环氢中水含量和恒温硫化时间等。裂化反应器出口循环氢中水含量和床层温升,其实质是催化剂硫化速度的表征,在一定条件下受注硫速率和升温速度的影响。
6.3、硫化期间硫平衡表
温度 /℃
7催化剂硫化注意事项
硫化期间催化剂的活性是相当高的,如遇紧急事故温度难以控制,很有可能发生飞温,必须严格遵守升温曲线并监视床层温度。硫化过程中操作时,原则上应避免使用急冷氢,只有在其它控制催化剂床层温度的措施力所不及时才使用。硫化期间,还原会造成催化剂的损坏,还原使催化剂上的金属氧化物反应成金属单质,而不是反应成金属硫化物,在较高温度下和硫化还没有产生更多硫化氢时,还原反应发生更快,硫化期间催化剂的安全温度是195℃或更低,升温前注入一些DMDS 会多生成一些硫化氢有助于硫化反应。此外,在硫化过程中,除了H2S以外,还会生成甲烷,必须脱除生成过量的甲烷,可通过排放尾气和补充新氢的方法,始终维持循环氢纯度不小于85%。
7.1、硫化期间新氢的中断
反应硫化期间,DMDS反应生成硫化氢所需的新氢量以及补充反应器回路中损失的氢气量和泄露氢气量是很少的,因此不需要补充很多的新氢。硫化期间新氢中断必须降低温度以防止催化剂还
原,尽可能放慢压力损失的速度。当氢气恢复后,装置再进行硫化。
处理步骤:
(1)停止注入DMDS,如果正在往循环回路外面排放时,停止排放。保持最大量氢气循环,迅速将床层温度入口温度降到195℃,必要时可使用冷氢。
(2)当新氢恢复时,反应系统压力恢复14.0MPa(G),温度回升至195℃,重新注入DMDS。如果循环氢中硫化氢开始超过1%(V)时减少DMDS注入量,如果循环氢中硫化氢超过2%(V)时停止注入DMDS,循环氢中硫化氢含量开始减少后再逐渐恢复注硫。
(3)继续进行正常的硫化步骤。
7.2、硫化期间循环氢压缩机停机
循环氢带出硫化反应时放出的反应热量,如果没有循环氢压缩机循环气体时,新鲜催化剂上有可能发生飞温现象。如果硫化期间循环氢压缩机发生故障,采取正常停循环氢压缩机处理步骤,并且停止和切断DMDS的注入。
当循环氢压缩机重新启动时,密切观察反应器床层的温度,必要时用冷氢控制温度。反应器床层温度稳定后,重新注入DMDS恢复硫化。反应器床层温度稳定之前不要注入DMDS,否则会使温度更加不稳定。注入DMDS之后,温度回升至压缩机中断时的状态,继续进行硫化步骤。
7.3、硫化过程发生反应器温度偏离和飞温
硫化期间,不允许反应器床层任何点温度超过400℃,且任一床层温升不能超过35℃。硫化期间发生反应器床层温度偏离或飞温情况,一般是因为在这一反应器床层温度条件下注入的DMDS太多。如果发生温度偏离时,立即停止注入DMDS并采取用冷氢来控制温升,反应器温度应降到195℃以下。
7.4、DMDS注入中断
中断DMDS会导致催化剂缺少硫化氢,从而导致催化剂金属还原和活性损失。发生DMDS中断时可以降低催化剂的温度直到恢复DMDS的注入。
处理步骤:
(1)立即停止升温。
(2)如果硫化氢穿透之前发生DMDS中断,把反应器温度降到195℃以下。如果穿透之后发生DMDS中断,温度降到比DMDS中断时温度低30℃,定期检查循环氢中硫化氢的含量,如果循环氢中的硫化氢含量开始明显减少时,继续把温度降低到195℃。
(3)当DMDS恢复时,立即开始注入,把温度升到DMDS中断时的温度,继续正常的硫化步骤。
7.5、加强巡检
在催化剂预硫化期间,注意进行现场检查,发现漏点及时汇报和处理。当R-3101入口温度达到250℃时,可对反应系统法兰进行热紧。由于循环气中过高的硫化氢含量,可能会有硫化氢的存在,操作时要防止中毒。
加氢催化剂硫化方案
内蒙庆华20万吨/年甲醇装置 JT-8焦炉气加氢催化剂予硫化方案 一、催化剂装填前准备 1.检查反应器内清洁无水无杂质; 2.准备好内件、填料及催化剂,其中有: ①2mm不锈钢丝网16张左右(直径与反应器直径相同); ②瓷球约数吨左右; ③催化剂;JT-8 装填数量:87M3其中:予加氢反应器D61201A、B各14.5 M3 一级加氢反应器D61202:29.06 M3;二级加氢反应器D61205:29 M3 ④φ300、6.5-10.5米长帆布筒子2根、剪刀2把; ⑤装料漏斗(需预制); ⑥500×700轻质木板2块; ⑦葫芦2只或吊车。 ⑧在设备内的工作人员以及所需的人孔值班人员在装填作业开始前必须具备具有认可的安全培训,所有时候进入设备内工作都须持有进入许可证以及反应器内气体测试报告。 ⑨装填前要对设备进行检验以确保所需的内件都已正确的安装好,特别是温度计导管和取样管,还要检验所有的施工材料是否都已拆掉并且反应器壁已清除氧化物和铁屑。钢丝网除锈,用白布擦净,检查各测温热电偶管,取样管的安装及连接管口方位是否符合图纸要求,特别注意固定筛网支架。 二、装填作业 1、检查反应器内清洁无水无杂质; 2、底部格栅安装牢固; 3、画出催化剂装填上下界限标记及中间分段标记; 4、底部格栅上面平铺1层不锈钢丝网; 5、装入填料(瓷球)至标志线铺平;瓷球上面平铺2层不锈钢丝网 6关闭下部人孔; 7装催化剂 装填催化剂时应避免阴天,下雨,以防催化剂受潮而影响其使用活性。催化剂装填之前
应先筛去粉尘。催化剂装填时,从上人孔放入加料帆布筒10.0米左右和漏斗连接;催化剂装填时视装填设备及人员情况,可进行一台或多台反应器的装填作业。 ①漏斗内倒入催化剂0.5-1.0吨;可根据具体情况确定。并用吊车吊至反应器人 孔上方,漏斗与帆布筒相连,放入催化剂。 ②视吊装催化剂的量,取出漏斗和帆布筒由软梯进入反应器,用木板刮平催化剂; ③刮平后,根据具体装填高度,帆布筒剪掉约1米,继续装催化剂,装量根据第 一次实际装填情况可调节。在整个装填过程中,要求均匀平整,防止粉碎变潮, 勿在催化剂上直接踩踏。 ④装入催化剂至分段标记高度后,均匀平整,然后继续装入催化剂。 ⑤装入催化剂至额定高度后,扒平后铺2层不锈钢丝网,再装瓷球; ⑥瓷球装到预定高度,扒平后铺一层不锈钢丝网; 7、安装并固定填料压实格栅; 8、安装上人孔。各加氢反应器催化剂的装填方法基本相同。 三、JT-8型焦炉气加氢催化剂的硫化 催化剂在正常使用之前,为获得较高的加氢转化活性,应对其进行硫化。 采用H2S为硫化剂时,发生如下反应: MoO3+2H2S+H2→MoS2+3H2O 系统在试压、试漏结束后,以氮气或其它惰性气体吹净置换后,开始催化剂的升温。升温时,可用氮气或氢氮气。 在对处理有机硫含量较高,硫形态较复杂的焦炉气原料时,为了获得较高的加氢转化活性,催化剂首次使用时,应进行预硫化,预硫化结束时,催化剂吸硫量约为本身重量的4-5%左右。 预硫化条件推荐如下: 气源:氢氮气或含氢的焦炉气中配入CS2 催化剂床层温度升至180℃以上时可在硫化用气中配入CS2。 空速:200~500h-1,压力:常压或低压(≤0.5MPa) 气体中含硫量:0.5~1.5%(体积)氧含量<0.2% 边升温边预硫化(升温速度20℃/小时),260℃、300℃分别恒温2小时,最终升温至正常的操作温度,再恒温,按催化剂理论吸硫量将CS2加完为止,可认为预硫化结束,然后系统逐步升压到正常操作压力,转入正常操作。
硫磺回收开工方案
硫磺回收装置开工方案 硫磺四班 1、设备及管线吹扫、气密、水洗。 1)主流程的吹扫、气密: 吹扫介质:压缩空气; 主流程吹扫时,先关闭液硫池管线,设备逐一吹扫,有排污阀门的,打开低点排污,进行排污,后逐个试通每条硫封。 制硫炉F-7301→废热锅炉E-7309→排污口进行排污→一级冷凝冷却器E-7304A→一级高温掺合阀→一级反应器R-7301→二级冷凝冷却器E-7304B→二级高温掺合阀→二级反应器R-7302→三级冷凝冷却器E-7305→捕集器D-7304→尾气换热器E-7311→加氢反应器R-7303→急冷塔C-7301→塔底排污打开进行排污。 气密压力:在0.05MPa条件下对动过的法兰进行气密。 2)制硫炉和尾气焚烧炉吹扫。 制硫炉:吹扫完毕后,调整炉前风压至0.12MPa,对制硫炉进行气密。对制硫炉防爆孔、人孔、出口蝶阀气密。 尾气焚烧炉:尾气焚烧炉→尾气换热器→烟囱,流程吹扫。吹扫完毕后,调整炉前风压至0.12MPa,对焚烧炉进行气密。对焚烧炉防爆孔、人孔气密。3)急冷塔水洗:自急冷水泵注水,经过急冷水过滤器、急冷水空冷、急冷水冷却器,注入急冷塔,急冷他液位达到50%时,注水停止,系统形成闭路循环,视水质情况可多循环几次。 2、水联运 1)打通吸收塔C-7302、闪蒸塔C-7102、再生塔C-7101、循环流程 2)自富液泵P-7302注水洗水到闪蒸塔,闪蒸塔液位达到60%以上时,启动闪蒸塔底富液泵P-7106,经二级贫富夜换热器E-7103B,送至再生塔,富液泵注水不停。 3)当再生塔液位达到60%以上时,经过一级贫富液换热器E-7103A,启动贫液泵P-7101,经过二级贫富液换热器、空冷A-7101、水冷E-7104、过滤器SR-7102,送水至吸收塔,溶剂储罐D-7101,当吸收塔液位,溶剂储罐液位达到50%以上时,系统水洗水量已足够,富液泵停止注水,启动吸收塔底富液泵、溶剂加入泵,系统形成闭路循环。
催化剂预硫化之令狐文艳创作
黑龙江安瑞佳石油化工有限公司 令狐文艳 学习资料 (催化剂预硫化方法) 气分车间 2013年4月 催化剂的预硫化 催化剂的预硫化有两种方法:一是干法预硫化,亦称气相预硫化,即在循环氢或氢氮混合气或氢气与丙烷或氢气与丁烷混合气存在下注入硫化剂进行硫化;二是湿法预硫化,亦称液相预硫化,即在循环氢存在下以轻油等为硫化油携带硫化剂注入反应系统进行硫化。 催化剂硫化的基本原理 催化剂硫化是基于硫化剂(CS2或二甲基二硫DMDS)临氢分解生成的H2S,将催化剂活性金属氧化态转化为相应的硫化态的反应。 干法硫化反应:用氢气作载体,硫化氢为硫化剂。 MoO3 + 2H2S + H2 MoS2 + 3H2O 9CoO + 8H2S + H2 Co9S8 + 9H2O
3NiO + 2H2S + H2 Ni3S2 + 3H2O 湿法硫化反应:用氢气作载体,CS2为硫化剂。 CS2 + 4H2 2H2S + CH4 MoO3 + CS2 + 5H2 MoS2 + 3H2O + CH4 MoO3 + CS2 + 3H2 MoS2 + 3H2O + C 9CoO + 4CS2 + 17H2 Co9S8 + 9H2O + CH4 9CoO + 4CS2 + 9H2 Co9S8 + 9H2O + 4C 3NiO + 2CS2 + 5H2 Ni3S2 + 3H2O + CH4基于上述硫化反应式和加氢催化剂的装量及相关金属含量可估算出催化剂硫化剂的理论需要量。其硫化剂的备用量(采购量)一般按催化剂硫化理论需硫量的1.25倍考虑即可。 硫化剂和硫化油的选择 实际上催化剂硫化时是H2S在起作用,所以所选用的硫化剂在临氢和催化剂存在的条件下,能在较低反应温度下分解生成H2S,以有利于催化剂硫化的顺利进行,提高硫化效果,同时硫化剂中的硫含量应较高,以减少硫化剂的用量,避免其它元素对硫化过程的不利影响,另外硫化剂价格便宜、毒性小、使用安全。 常用硫化剂的理化性质见表4。 表4 常用硫化剂的理化性质
预加氢催化剂预硫化方法
精心整理 中国石化九江分公司 30×104t/a重整预加氢装置FH-40C催化剂原则开工方案中国石油化工股份有限公司抚顺石油化工研究院 二○○九年四月 一、催化剂干燥 1、干燥前的准备工作 (1)催化剂装填完毕, (2)绘出催化剂干燥脱水升、恒温曲线。 (3) 2、干燥示意流程 ↓N2 ↑↓ ↓放水 3 循环氮气量:循环压缩机全量循环 干燥温度要求见表2。 表2催化剂干燥温度要求 反应器入口温度 ℃ 床层温度 ℃ 升、降温速度 ℃/h 升、恒温参考时间 h 常温→250- 10~15 15
250~280 ≮200- 至干燥结束 250→<150≯15020~25 4~5 4、干燥结束标准 高分无明水放出。 5、干燥操作 (1)在氮气压力1.5MPa/h的升 温速度将反应器入口温度升至250℃, 不到200 (2)在干燥过程中,每2 (3) (4) <150 (如DMDS)分解生成H2S,H2S使 H2S反应转化成硫化态之前被热氢还原。所以,催化剂预硫化时,必须控制好预硫化温度与循环氢中H2S含量的关系,在H2S未穿透催化剂床层前,床层最高点温度不应超过230℃。 1、预硫化前的准备工作 (1)催化剂干燥结束后,将催化剂床层温度降至150℃,泄压至0.2MPa,引氢气置换至氢纯度>85%,再升压至操作压力,建立氢气循环。
(2)绘出预硫化过程的升、恒温曲线。 (3)注硫系统吹扫干净,并将硫化剂装入硫化罐内。 (4)准备好不同规格的H 2S 检测管。硫化过程中每1小时测一次循环氢中的H 2S 浓度。 2、催化剂硫化示意流程 硫化油↓DMDS ↑ ↑分液罐→循环压缩机↓ ↑ ←高分←水冷←空冷←换热器 3、催化剂硫化条件 反应压力:操作压力 (CS 2)。 则需按照CS 2硫化剂含硫量的不同进行硫化温度及循环氢中H 2S 含量控制要求见表3。 表3催化剂硫化阶段温度要求 反应器入温度 ℃ 升温速度 ℃/h 升、恒温参考时间 h 循环氢H 2S 控制 v% 常温→150 15~20
盐酸罐施工方案
盐酸储槽防腐工程 施 工 方 案 单位:正昊能源设备防护安装工程有限公司 编制人:崔西敬 日期:2014年11月15日 施工方案 贵单位的设备盐酸储槽,内盛放介质为25-30%的盐酸,由于工作的需要还要来回的运输,一般液态盐酸的浓度最高也就37%左右,所以罐内腐蚀环境就是液相的盐酸和挥发气相的HCL。针对贵单位的盐酸储槽内的生产环境,腐蚀介质的种类及腐蚀形式,结合我们多年来对各种化工设备衬里的防腐施工经验,为了确保贵厂的防腐工程质量、进度和安全,减少设备的维修次数,以增强企业的社会效益与经济效益,我们推荐以下施工方案,仅供贵厂参考。 一、推荐方案: 在防腐蚀施工过程中,正确的选择防腐工程所用的材料,是保证防腐工程质量的关键,因此选材方面要做到有地放矢,一定要按腐蚀介质的种
类和特征、接受物理机械作用的实际情况、作用部位的大小、工程的重要程度、结合材料的耐腐蚀性能,正确选用以达到预期的防腐目的。我们的选材原则是: A、材料化学性能或耐蚀性能满足生产需要。 B、物理机械和加工工艺性能满足设计要求。 C、总的经济效果优越。 (1)复合砖板衬里: 酚醛胶泥砌筑3mm厚耐酸砖板双层(使用寿命在15年以上)适用于静置设备或不接受物理撞击的部位。很显然贵单位的设备存在运输与装卸,难免存在磕碰撞击等问题。贵单位可结合设备衬里完成后的受力情况,进行综合评估,审慎选择。(价格较贵) (2)橡胶衬里 衬里用橡胶板一般有天然胶板与合成胶板。天然胶板一般耐浓盐酸的性能要优越与合成胶板,但天然硬胶板存在柔韧性差,衬里完成后需要硫化等诸多条件的限制,小设备必须运往工厂加工,太大的设备硫化罐内又放不进去,温度高易开裂等缺点。针对常温与低温条件下的常压设备,预硫化丁基胶板具有柔韧性好,耐酸性强的特点,用丁基胶板3mm+3mm的复合衬里法,设备的使用寿命也可达到15年。(价格适中)推荐选用。 (3)玻璃钢衬里 玻璃钢也是一种优良的耐酸材料,一般耐稀酸的性能较好,盐酸的浓度大于20%时,5mm厚的玻璃钢+鳞片使用寿命也在4-5年。(价格便宜) 二、编制依据: 1、《涂装前钢材表面锈蚀等级和除锈等级》(GB8923-88); 2、《橡胶衬里化工设备》HG/T20677-1990
预加氢催化剂预硫化方案
中国石化九江分公司 30×104t/a重整预加氢装置FH-40C催化剂原则开工方案中国石油化工股份有限公司抚顺石油化工研究院 二○○九年四月 一、催化剂干燥 1、干燥前的准备工作 (1)催化剂装填完毕,临氢系统进行氮气置换、气密合格。催化剂干燥用氮气作介质。 (2)绘出催化剂干燥脱水升、恒温曲线。 (3)催化剂干燥前,各切水点排尽存水,并准备好计量水的器具。 2、干燥示意流程 ↓N2 循环氢分液罐→循环压缩机→换热器→加热炉 ↑↓ 分离器←水冷←空冷←换热器←反应器 ↓放水 3、催化剂干燥条件: 高分压力: 反应器入口温度:250℃ 循环氮气量:循环压缩机全量循环 干燥温度要求见表2。 表2 催化剂干燥温度要求 反应器入口温度 ℃床层温度 ℃ 升、降温速度 ℃/h 升、恒温参考时间 h
常温→250-10~1515 250~280≮200-至干燥结束 250→<150≯15020~254~5 4、干燥结束标准 高分无明水放出。 5、干燥操作 (1)在氮气压力下,循环压缩机全量循环,加热炉点火,以10~15℃/h的升温速度将反应器入口温度升至250℃,开始恒温脱水。如果催化剂床层最低点温度达不到200℃,可适当提高反应器入口温度,但反应器入口温度≯280℃。 (2)在干燥过程中,每2小时在高分放水一次,并计量。 (3)画出催化剂脱水干燥的实际升、恒温曲线图。 (4)干燥达到结束标准后,以≯25℃/h的降温速度将反应器床层各点温度均降至<150℃,方可引入氢气进行高压气密,合格后进行催化剂预硫化。 二、催化剂预硫化 催化剂预硫化是指催化剂在氢气存在下,硫化剂(如DMDS)分解生成H2S,H2S使催化剂金属组分由氧化态转化成相应的硫化态。 在预硫化过程中,关键问题是要避免金属氧化态在与H2S反应转化成硫化态之前被热氢还原。所以,催化剂预硫化时,必须控制好预硫化温度与循环氢中H2S含量的关系,在H2S未穿透催化剂床层前,床层最高点温度不应超过230℃。
11制氢装置的原始开工(修改完)
第十一章制氢装置的原始开工 装置在开车前要进行开车前的准备,对装置中所需要的原材料、辅助材料、公用工程系统进行检查和接收,所有条件一切良好才具备开车的条件。 11.1准备工作 11.1.1开工检查项目 1.所有容器和设备在填充闭之前,已经过仔细地检查,内部清洁无损,内件安装完整。2.转化炉及废热烟道衬里经干燥以后进行过仔细检查,完整无损,质量良好。 3.所有的管道和设备经检验,包括阀门、孔板、测压点、放空排污阀、安全阀、疏水器等在内安装正确无误,并对设备和管道进行过仔细冲洗和吹扫。 4.所有仪表、控制阀经过检查和调试合格。电磁阀、变送器送电。调节阀气源接通。所有一次仪表,信号取压管上的及至变送器的脉冲管线上阀打开,所有安全阀前的阀门打开。5.所有放空阀、排液阀、通向地管的阀门、取样管上的阀关闭。 6.泵、压缩机、风机等动设备按专门说明书经过检查,并做过运转试验,性能良好。7.联锁系统经过检查,功能良好,并作好设定。 8.所有安全阀经过检查合格,并作好压力设定。 9.所有设备和管道已做过气密试验,以及N2置换工作。 10.所有疏水器经检验功能良好。 11.所有临时盲板拆除。 12.控制室内所有调节阀处于手动状态,所控制所阀门处于关闭状态。 13.现场所有工艺管线上的截止阀处于关闭状态。 14.所有工艺主流程上的盲板翻为通板。 15.各种原材料、辅助材料均已具备接受条件。 16.开工所需物料已关至装置界区。 11.1.2开工人员培训 为确保装置安全、平稳、高效、一次投料试车成功,必须对参加开工的所有人员进行全面系统的开工培训,让所有人员训练掌握开工方案和步骤,并进行上岗取证考试,取得上岗证的人员才能参与装置的初次开工。 11.1.3成立开工指挥小组 为明确各级开工人员在开工过程中所负责的具体工作,便于开工的统筹安排,明确指挥和操作职责,开工前要成立装置开工指挥小组,编制指挥网络图。 11.2开工步骤 制氢装置的原始开工步骤较为复杂,主要是因为有较多种类的催化剂的预处理。催化剂预下处理的好坏直接影响到装置生产的平衡和效益的高低。因此,制氢装置原始开工的各个环节都要严格把好质量关。 11.2.1系统气密 根据装置各系统的压力等级和流程,编制气密流程图,用气密介质对各系统进行气密,具体方法见上一章相关内容。
加氢催化剂的预硫化及其影响因素
加氢催化剂的预硫化及其影响因素 张笑剑 摘要:加氢催化剂的预硫化是提高催化剂活性,优化加氢催化剂操作,获得理想经济效益的关键之一。为获得理想的硫化效果,必须严格控制各阶段的反应条件。本文介绍了加氢催化剂预硫化的反应原理,探讨了在预硫化过程中影响催化剂预硫化效果的因素。 关键词:加氢催化剂硫化技术操作条件影响因素 加氢催化剂硫化是提高催化剂活性,优化装置操作,延长装置运转周期,提 高经济效益的关键技术之一。加氢催化剂主要由金属组分(一般为W,Mo,Co, , Ni 等)和载体(氧化铝 ,二氧化硅,沸石,活性炭,黏土,渗铝水泥和硅藻土等)两部分组成,金属组分以氧化态的形式负载在多孔的载体上,促进加氢脱氮,加氢脱硫,加氢脱芳烃,加氢脱金属,加氢脱氧和加氢裂化等反应。生产经验和理论研究表明:氧化态催化剂的加氢活性,稳定性和选择性均低于硫化态催化剂。只有将催化剂进行硫化预处理,使金属组分从氧化态转变为硫化态,催化剂才具有较高的活性,稳定性和选择性,抗毒性强,寿命长,才能够最大限度地发挥加氢催化剂的作用。 1硫化原理 1.1 H 2 S的制备 H 2 S主要来自硫化剂的分解:硫化剂的分解均为放热反应,且理论分解温度与 实际操作条件下的分解温度有所差别,一般有机硫化物在催化剂和H 2 条件下分解温度通常比常温下分解温度低10~25o C。 CS 2+4H 2 =CH 4 +2H 2 S CH 3SSCH 3 +3H 2 =2CH 4 +2H 2 S 1.2金属氧化物的硫化 金属氧化物的硫化是放热反应。理想的硫化反应应为 MoO 3+2H 2 S+H 2 =MS 2 +3H 2 O 9CoO+8H 2S+H 2 =Co 9 S 8 +9H 2 O 3NiO+2H 2S+H 2 =NiS+3HO WO 3+2H 2 S+H 2 =WS 2 +3H 2 O
催化剂预硫化
黑龙江安瑞佳石油化工有限公司 学习资料 (催化剂预硫化方法) 气分车间 2013年4月 催化剂的预硫化
催化剂的预硫化有两种方法:一是干法预硫化,亦称气相预硫化,即在循环氢或氢氮混合气或氢气与丙烷或氢气与丁烷混合气存在下注入硫化剂进行硫化;二是湿法预硫化,亦称液相预硫化,即在循环氢存在下以轻油等为硫化油携带硫化剂注入反应系统进行硫化。 催化剂硫化的基本原理 催化剂硫化是基于硫化剂(CS2或二甲基二硫DMDS )临氢分解生成的H2S, 将催化剂活性金属氧化态转化为相应的硫化态的反应。 干法硫化反应:用氢气作载体,硫化氢为硫化剂。 M O O3 + 2H2S + H2 ----------- ? M0S2 + 3H2O 9CoO + 8H2S + H2 --------- ? C09S8 + 9H2O 3NiO + 2H2S + H2 ________ . M3S2 + 3出0 湿法硫化反应:用氢气作载体,CS2为硫化剂。 CS2 + 4H2 ----------- ? 2H2S + CH4 M O O3 + CS2 + 5H2 --------------- k M0S2 + 3H20 + CH4 M O O3 + CS2 + 3H2 ---------------- ? M0S2 + 3H2O + C 9C O O + 4CS2 + 17H2 -------------- 09S8 + 9H20 + CH4 9C O O + 4CS? + 9H2 ----------- k C09S8 + 9H2O + 4C 3Ni0 + 2CS2 + 5H2 ------------ ? M3S2 + 3出0 + CH4 基于上述硫化反应式和加氢催化剂的装量及相关金属含量可估算出催化剂硫化剂的理论需要量。其硫化剂的备用量(采购量)一般按催化剂硫化理论需硫量的1.25倍考虑即可。
加氢精制及制氢联合装置技术方案
30万吨/年加氢精制及制氢联合装置初步技术方案 Zhejiang Meiyang International Petrochemical Pharmaceutical Engineering Design CO.,LTD. 2008年9月21日
目录 第一节工程简述及设计原则 (2) 第二节装置规模、原料及产品方案 (3) 第三节工艺技术方案及流程简述 (5) 第四节装置平面布置 (15) 第五节公用工程消耗 (16) 第六节投资估算 (18) 第七节技术保证 (19)
第一节工程简述及设计原则 一、工程简述 xx公司拟建设30万吨/年汽柴油加氢精制装置,原料组成为15万吨/年催化柴油,11~12万吨/年焦化柴油,3~4万吨/年焦化汽油,根据加氢精制装置的生产规模及产品方案,需配套5000m3n/h制氢装置。(年操作时数为8000小时)。 二、设计范围及原则 1、30万吨/年汽柴油加氢精制装置、5000m3n/h制氢装置按联合装置布置,制氢装置只为汽柴油加氢精制装置供氢。设计范围为联合装置边界线以内,主要内容包括:加氢的反应、分馏部分,制氢的转化造气、变换和PSA部分,以及联合装置的变配电室和中心控制室。加氢精制装置的含硫气体送至催化的产品精制装置与催化干气一起脱硫。脱硫后的气体作为制氢装置的主原料,石脑油作为辅助原料。 2、加氢精制装置的目的以脱硫、脱氮和烯烃饱和为主,不考虑加氢改质。采用国内催化剂、设备和工艺技术。 3、制氢装置造气单元采用催化干气蒸汽转化制氢专有技术;净化单元采用国内变压吸附(PSA)技术。 4、按年开工8000小时计算小时加工量。 5、严格执行国家有关工程建设质量管理法规,确保装置安全、稳定、长周期运行,减少维护维修的工作量,从而提高整体的经济效益。 6、认真贯彻国家关于环境保护和劳动保护的法规和要求。认真贯彻安全第一预防为主的指导思想。对生产中易燃易爆有毒有害物质设置必要的防范措施。三废排放要符合国家现行有关标准和法规。
净化装置变换催化剂硫化方案0904
目录 1 概述 3 2 准备工作 3 3 催化剂的升温硫化 4 4 注意事项7 5 附录9
1概述 1.1变换单元所用催化剂K8-11为新型耐硫变换触媒,含有特殊载体,具有良好的低温变换 活性、宽温和宽硫特性,较强的抗毒性能,较高的选择性。 1.2钴钼系列耐硫变换催化剂使用前其活性组分呈氧化态,催化活性很低,需要经过硫化变 成硫化态才具有良好的活性。首次硫化过程对催化剂的性能、使用寿命都有直接影响,因此硫化操作至关重要。 1.3催化剂硫化原理 1.3.1硫化时起作用的硫化剂为H2S,硫化过程的主要反应式如下: CoO+H2S CoS+H2O ΔH0298= ―13.4kJ/mol (方程式1.3.1-1)MoO3+2H2S+H2MoS2+3H2O ΔH0298= ―48.1kJ/mol (方程式1.3.1-2)1.3.2考虑到安全因素,一般不采取直接引H2S气体进行催化剂的硫化。H2S的制备可通过CS2 和COS等与氢或水的反应得到。其主要反应式如下: CS2+4H2 2H2S+CH4ΔH0298= ―240.6kJ/mol (方程式1.3.2-1) COS+H2O CO2+ H2S ΔH0298= ―35.2kJ/mol (方程式1.3.2-2)1.3.3对耐硫变换催化剂而言,一般倾向于非在线预硫化。但通常情况下,工厂没有外来氢源, 则只能采取在线硫化(氢源来自上游气化装置)。硫化时,一般要求系统内硫化氢含量≥1000ppm,为缩短硫化时间可通过补加硫化剂(如CS2)等方法来完成。 2准备工作 2.1现场各安装项目完毕,触媒装填结束,系统气密试验合格,置换合格(O2<0.2%)。2.2公用工程系统(水、电、气、汽等)正常。 2.3氮气循环风机试运正常,处于备用状态。 2.4上游气化装置至少一台气化炉运行稳定。 2.5二硫化碳槽已经充装7.6t CS2,并用氮气充压至0.7MPa(G)备用, 氮气压力维持稳定。 2.6开工加热器146E114正常备用。 2.7相关仪表、阀门均已调校完成。
预加氢催化剂预硫化方案审批稿
预加氢催化剂预硫化方 案 YKK standardization office【 YKK5AB- YKK08- YKK2C- YKK18】
中国石化九江分公司 30×104t/a重整预加氢装置FH-40C催化剂原则开工方案 中国石油化工股份有限公司抚顺石油化工研究院 二○○九年四月
一、催化剂干燥 1、干燥前的准备工作 (1)催化剂装填完毕,临氢系统进行氮气置换、气密合格。催化剂干燥用氮气作介质。 (2)绘出催化剂干燥脱水升、恒温曲线。 (3)催化剂干燥前,各切水点排尽存水,并准备好计量水的器具。 2、干燥示意流程 ↓N2 循环氢分液罐→循环压缩机→换热器→加热炉 ↑↓ 分离器←水冷←空冷←换热器←反应器 ↓放水 3、催化剂干燥条件: 高分压力: 反应器入口温度:250℃ 循环氮气量:循环压缩机全量循环 干燥温度要求见表2。 表2 催化剂干燥温度要求 反应器入口温度 ℃床层温度 ℃ 升、降温速度 ℃/h 升、恒温参考时间 h 常温→250- 10~15 15 250~280 ≮200 - 至干燥结束250→<150≯150 20~25 4~5 4、干燥结束标准
高分无明水放出。 5、干燥操作 (1)在氮气压力下,循环压缩机全量循环,加热炉点火,以10~15℃/h的升温速度将反应器入口温度升至250℃,开始恒温脱水。如果催化剂床层最低点温度达不到200℃,可适当提高反应器入口温度,但反应器入口温度≯280℃。 (2)在干燥过程中,每2小时在高分放水一次,并计量。 (3)画出催化剂脱水干燥的实际升、恒温曲线图。 (4)干燥达到结束标准后,以≯25℃/h的降温速度将反应器床层各点温度均降至<150℃,方可引入氢气进行高压气密,合格后进行催化剂预硫化。 二、催化剂预硫化 催化剂预硫化是指催化剂在氢气存在下,硫化剂(如DMDS)分解生成H2S,H2S使催化剂金属组分由氧化态转化成相应的硫化态。 在预硫化过程中,关键问题是要避免金属氧化态在与H2S反应转化成硫化态之前被热氢还原。所以,催化剂预硫化时,必须控制好预硫化温度与循环氢中H2S含量的关系,在H2S未穿透催化剂床层前,床层最高点温度不应超过230℃。
加氢催化剂的硫化_翟京宋
2011 年第 1 期 2011 年 1 月
化学工程与装备 Chemical Engineering & Equipment
59
生产实践
摘 前言 1 催化剂的硫化原理 应。硫化的反应方程式如下: (CH3)2S2 +3H2 = 2H2S + 2CH4 MoO3+2H2S+H2 = MoS2+3H2O 9CoO+8H2S+H2 = Co9O8+9H2O 3NiO+2H2S+H2 = Ni3S2+3H2O WO3+2H2S+H2 = WS2+3H2O 2 硫化方法和硫化剂的选择 硫化。
加氢催化剂的硫化
翟京宋
(广西石化公司,广西 钦州 535008)
要:加氢催化剂的硫化是提高催化剂活性、优化加氢催化剂操作,确保装置安全、平稳、高效运行。
本文从生产实践中介绍了加氢催化剂硫化的原理、方法、硫化剂的选择,以及催化剂器内硫化通用操作步 骤,并介绍了硫化过程中的事故处理、主要注意事项。 关键词:催化剂硫化;事故处理;注意事项
CS2、二甲基二硫化物等)进行硫化;另一种是依靠硫化油 自身的硫进行硫化。 干法硫化是在氢气存在下, 直接用含有 一定浓度的硫化氢或直接向循环氢中注入有机硫化物进行 硫化。 在开工硫化阶段需要使用硫化剂, 而硫化剂的选择应考 虑以下因素: (1)硫化剂在临氢和催化剂存在的条件下,能在较低 反应温度下分解生成H2S,有利于催化剂硫化的顺利进行, 提高硫化效果。 (2) 硫化剂的硫含量应较高, 以减少硫化剂的使用量, 避免其他元素对硫化过程的不利影响。 (3)硫化剂价格便宜、毒性小,使用安全可靠。 3 催化剂器内硫化 催化剂的湿法硫化可分为原料油自身的含硫化物的湿 法硫化和外加硫化剂湿法硫化两种。 虽然原料油的自身湿法 硫化方法简单、省事,但由于原料油本身所含硫化物低,难 以分解、分解温度高,容易使催化剂被还原的危险,一旦形 成低价态的金属氧化物, 就很难再与硫化氢反应, 则无法在 理想的时间内完成硫化,因此催化剂硫化效果较差。 在湿法硫化中,使用馏分油作为催化剂湿法硫化用油, 其馏分范围一般应接近或略轻于加氢原料油, 通常以直馏柴 油馏分应用较多, 不含烯烃且氮含量应低于200ppm, 其总硫 含量要求低于2% wt(包括加入的有机含硫化合物) 。烯烃加 氢反应会增加放热并导致催化剂上焦炭沉积, 为取得好的硫 化效果,所选用的硫化油的干点不宜过高(一般不大于 370oC) 。 因为在硫化温度下可能发生饱和反应对正常的硫化 操作造成干扰,导致催化剂床层温度不稳定,氢耗过高,同 时裂化原料中含有转化难度很高的含氮化合物, 具有较强的 吸附能力和较高结焦倾向。 3.1 催化剂的湿法硫化
新鲜的催化剂或再生后的催化剂, 其所含的活性金属组 分(Mo、Ni、Co、W)都是以氧化态的形式存在。经过研究 和工业化运用实践证明,当催化剂以硫化态的形态存在时, 催化剂具有较高的活性、稳定性和选择性,抗毒性强,寿命 长,才能够最大限度地发挥加氢催化剂的作用。 催化剂的硫化是在一定的温度和氢气分压下, 通过加氢 催化剂中的氧化态活性组分(氧化镍、氧化钼等)和硫化剂 化学作用变为活性较高的硫化态金属组分, 达到催化剂长周 期稳定运行的目的。 催化剂硫化是基于硫化剂临氢分解生产 的 H2S 将催化剂活性金属氧化态转化为相应金属硫化态的反
硫化技术的分类方法根据硫化反应进行的场所来确定, 加氢催化剂硫化可分为器内硫化和器外硫化。 而催化剂的器 内预硫化可以分为气相(干法)预硫化和液相(湿法)预硫 化两大类。 目前, 国内工业加氢装置大都实行器内预硫化方 法, 除对于择形裂解活性, 弱加氢活性的临氢活性的降凝催 化剂、 分子筛加氢裂化催化剂的预硫化大多采用干法硫化以 外, 其他的加氢精制、 加氢处理装置的催化剂普遍采用湿法 湿法硫化是在氢气存在下, 采用含有硫化物的烃类或馏 分油在液相或半液相状态下硫化。 湿法硫化又分为两种, 一 种是催化剂硫化过程所需要的硫由外部加入的硫化物(如
催化剂预硫化
黑龙江安瑞佳石油化工有限公司 学习资料(催化剂预硫化方法) 气分车间 2013年4月
催化剂的预硫化 催化剂的预硫化有两种方法:一是干法预硫化,亦称气相预硫化,即在循环氢或氢氮混合气或氢气与丙烷或氢气与丁烷混合气存在下注入硫化剂进行硫化;二是湿法预硫化,亦称液相预硫化,即在循环氢存在下以轻油等为硫化油携带硫化剂注入反应系统进行硫化。 催化剂硫化的基本原理 催化剂硫化是基于硫化剂(CS2或二甲基二硫DMDS)临氢分解生成的H2S,将催化剂活性金属氧化态转化为相应的硫化态的反应。 干法硫化反应:用氢气作载体,硫化氢为硫化剂。 MoO3 + 2H2S + H2MoS2 + 3H2O 9CoO + 8H2S + H2Co9S8 + 9H2O 3NiO + 2H2S + H2Ni3S2 + 3H2O 湿法硫化反应:用氢气作载体,CS2为硫化剂。 CS2 + 4H22H2S + CH4 MoO3 + CS2 + 5H2MoS2 + 3H2O + CH4 MoO3 + CS2 + 3H2 MoS2 + 3H2O + C 9CoO + 4CS2 + 17H2Co9S8 + 9H2O + CH4 9CoO + 4CS2 + 9H2Co9S8 + 9H2O + 4C 3NiO + 2CS2 + 5H2Ni3S2 + 3H2O + CH4 基于上述硫化反应式和加氢催化剂的装量及相关金属含量可估算出催化剂硫化剂的理论需要量。其硫化剂的备用量(采购量)一般按催化剂硫化理论需硫量的1.25倍考虑即可。 硫化剂和硫化油的选择 实际上催化剂硫化时是H2S在起作用,所以所选用的硫化剂在临氢和催化剂存在的条件下,能在较低反应温度下分解生成H2S,以有利于催化剂硫化的顺利进行,提高硫化效果,同时硫化剂中的硫含量应较高,以减少硫化剂的用量,
长青预硫化变换催化剂性能考核方案(1)
陕西长青能源化工有限公司 预硫化耐硫变换催化剂性能考核方案 编制: 审核: 审定: 批准: 编制单位:山东齐鲁科力化工研究院有限公司
一、概况 QCS-01S预硫化耐硫变换催化剂是含有新型组份和特殊助剂的新一代钴钼系一氧化碳耐硫变换催化剂,适用于以重油、渣油、沥青、煤渣、煤为原料造气的含硫气体的变换工艺,是一种宽温(200~500℃)、宽硫(工艺气硫化氢含量≥200ppm(干基))和宽水气比(0.8~2.0)的钴钼系CO耐硫变换催化剂。 我公司提供的67m3QCS-01S预硫化耐硫变换催化剂于2017年5月底装填就位并投入生产,投运以来一直运行状况良好,现申请对该炉催化剂进行性能考核。 二、考核依据 陕西长青能源化工有限公司与山东齐鲁科力化工研究院有限公司签订的预硫化耐硫变换催化剂合同及合同技术附件。 三、考核要求及说明 1、变化催化剂在技术协议约定的正常工况下运行。正常工况:进变换工段气量(干基)为25.6-28.4万 Nm3/h,压力5.7-5.9Mpa,入变换炉CO 36-49%,水气比:0.8-1.1。由于气化碳洗塔出口流量计指示不准,认可气化满负荷运行工况气量为正常工况气量。 2、性能考核期间每6小时取样分析一次变换炉进出口气样,由长青能化质检中心负责采样及数据分析。 3、变换炉进出口压差及变换炉出口温度以DCS显示PDIA2104/TI2107示值为准,每2小时记录一次数据,变换炉出口CO含量以质检中心手动分析数据为准,取考核期间数据的平均值。 4、考核相关仪表需准确、可靠,校验日期在有效期以内。
5、性能考核期间,操作人员应按规程和批准发布的考核方案进行操作,尽量维持工况稳定,要保持上下游负荷的一致性。 6、如因特殊原因导致性能考核无法按计划进行下去,经双方商定,另行选定时间重新进行考核。 四、考核主要指标 1、变换炉进出口压差≤0.06MPa; 2、变换炉出口CO≤6.0%; 3、变换炉出口温度≤470℃。 五、性能考核时间 2018年 5 月日至2018年 5 月日(72小时)
重整预加氢催化剂干燥 硫化方案
中国石油宁夏石化公司 60万吨/年连续 重整装置预加氢催化剂预硫化方案 宁夏石化公司二联合车间 2011年11月10日
一、组织机构 二联合车间60万吨/年重整装置预加氢催化剂硫化由二联合车间主任直接指挥,下设副组长及成员,为预加氢催化剂硫化工作提供人力、物力、技术及安全保障。 二联合车间60万吨/年重整装置预加氢催化剂硫化领导小组: 组长:谭斌 副组长:吴建军 成员:王春江李进、各班值班长、副值班长、运行工程师 职责: 1.认真贯彻公司总体试车安排,直接指挥重整装置预加氢催化剂硫化工作。 2.制定重整装置预加氢催化剂硫化的方案和进度。 3.协调解决预加氢催化剂硫化过程中出现的问题,与施工方积极沟通。 4.负责编制预加氢催化剂硫化方案,及时上报审批,并组织岗位人员讨论学习。 5.负责落实前期人员的培训考核工作和上岗取证工作,确保上岗人员达到“三个百分百”上岗条件 6.全力组织、实施预加氢催化剂硫化工作。 二、准备工作 1.通知生产调度,要求供排水、电站、空分、油品等单位确保 水、电、气、风正常供应,联系化验、仪表、电气、钳工等单位配合 开工。 2.全部设备处于完好备用状态。 3.全部仪表检验完毕,处于备用状态。 4.氮气来源应满足用气要求,氮气纯度要求>99.5v %、氧含量 <0.5v%、氢+烃含量<0.5v%。 5.工艺流程经三级检查准确无误,加好系统气密隔离盲板。 6.准备好气密用的肥皂水、刷子及检修用工具。 三、系统置换吹扫
(1)从循环压缩机的出口,用氮气缓慢将反应系统压力升到0.5MPa(表压),启机-101A,全量循环10分钟,将机负荷为零,然后打开高分(D-101)放空阀,将系统的压力降到0.02MPa。 (2)反复进行上述步骤(1)2 次以上,直到反应系统中氧含量<0.5v 四、系统气密 1.系统气密的目的是保证装置在开工过程中不会出现严重泄漏。但装置达到正常操作温度时,由于管线和设备膨胀,也会导致泄漏,因此操作人员在开工和运转初期也应关注漏点的出现。 2.确定气密流程,用合适的盲板将不同压力等级的部分隔开。 3.气密要求:参照装置的操作手册的要求进行。 气密阶段及标准测压点:D-102 气密介质气密压力/MPa 压降(MPa/h)氢压机状态气密时间/h 氮气0.5 0.02 停 2 1.7 0.005 停 4 2.2 0.005 停 4 4.按升压速度,系统压力达到要求后,对装置进行全面检查,在确认无泄漏、静态允许压降合格后,将系统压力降至1.0MPa,准备催化剂干燥。 4.4 催化剂干燥 干燥流程: K-101A→E-101A/B→F-101→R-101→R-102→A-101→E-102→D-101→D-102→k-101入口 1. 将系统压力提高到1.0MPa 2.并确认该系统无存油,制定好方案。 3.确定切水点在高分D101和压缩机分液罐D102,催化剂干燥前将切水点的水排净。 4.准备好计量水的工具(如磅称、水桶等)。 5.联系好氮气来源,并事先分析氮气纯度,要求氮气中水含量<300μg/g,氢+烃<0.5%,氧<0.5v%。
预加氢催化剂预硫化方法
预加氢催化剂预硫化方 法 Document serial number【KK89K-LLS98YT-SS8CB-SSUT-SST108】
中国石化九江分公司 30×104t/a重整预加氢装置FH-40C催化剂原则开工方案 中国石油化工股份有限公司抚顺石油化工研究院 二○○九年四月 一、催化剂干燥 1、干燥前的准备工作 (1)催化剂装填完毕,临氢系统进行氮气置换、气密合格。催化剂干燥用氮气作介质。 (2)绘出催化剂干燥脱水升、恒温曲线。 (3)催化剂干燥前,各切水点排尽存水,并准备好计量水的器具。 2、干燥示意流程 ↓N2 循环氢分液罐→循环压缩机→换热器→加热炉 ↑↓ 分离器←水冷←空冷←换热器←反应器 ↓放水 3、催化剂干燥条件: 高分压力:1.5MPa 反应器入口温度:250℃ 循环氮气量:循环压缩机全量循环 干燥温度要求见表2。 表2催化剂干燥温度要求 反应器入口温度 ℃床层温度 ℃ 升、降温速度 ℃/h 升、恒温参考时间 h
常温→250-10~1515 250~280≮200-至干燥结束 250→<150≯15020~254~5 4、干燥结束标准 高分无明水放出。 5、干燥操作 (1)在氮气压力1.5MPa下,循环压缩机全量循环,加热炉点火,以10~15℃/h的升温速度将反应器入口温度升至250℃,开始恒温脱水。如果催化剂床层最低点温度达不到200℃,可适当提高反应器入口温度,但反应器入口温度≯280℃。 (2)在干燥过程中,每2小时在高分放水一次,并计量。 (3)画出催化剂脱水干燥的实际升、恒温曲线图。 (4)干燥达到结束标准后,以≯25℃/h的降温速度将反应器床层各点温度均降至 <150℃,方可引入氢气进行高压气密,合格后进行催化剂预硫化。 二、催化剂预硫化 催化剂预硫化是指催化剂在氢气存在下,硫化剂(如DMDS)分解生成H2S,H2S使催化剂金属组分由氧化态转化成相应的硫化态。 在预硫化过程中,关键问题是要避免金属氧化态在与H2S反应转化成硫化态之前被热氢还原。所以,催化剂预硫化时,必须控制好预硫化温度与循环氢中H2S含量的关系,在H2S未穿透催化剂床层前,床层最高点温度不应超过230℃。 1、预硫化前的准备工作 (1)催化剂干燥结束后,将催化剂床层温度降至150℃,泄压至0.2MPa,引氢气置换至氢纯度>85%,再升压至操作压力,建立氢气循环。 (2)绘出预硫化过程的升、恒温曲线。
22602设备、管道橡胶衬里施工工艺标准
设备、管道橡胶衬里施工工艺标准 (QB—CNCEC J22602-2006) 1 适用范围 本标准适用于钢质工业设备和管道衬热硫化橡胶板和预硫化合成橡胶板(自硫化合成胶板)的施工作业。 2施工准备 2.1 技术准备 2.1.1 施工技术资料 2.1.1.1 设计资料(施工图、材料表、设计说明及技术规定等)。 2.1.2 相关施工标准规范: 2.1.2.1 HGJ229《工业设备、管道防腐蚀工程施工及验收规》 2.1.2.2 GB/T 8923《涂装前钢材表面锈蚀等级和除锈等级》 2.1.2.3 HG4―541《化工设备及管件橡胶衬里》 2.1.2.4 GB/T 5575《化工设备衬里用未硫化橡胶板》 2.1.2.5 HG4―555《橡胶定负荷压缩塑性试验方法》 2.1.2.6 HG4―852《硫化橡胶与金属粘结扯离强度的测定》 2.1.2.7 GB/T 1922《溶剂油》 2.1.3 根据施工图及相关标准、法规及现场条件应编制施工方案。 2.2 作业人员 2.2.1 建立施工项目组织机构,明确各级责任人员,机构设置应齐全,包括工程进度、质量、安全、物资、后勤五个机构。
2.2.2 针对施工要求,对施工作业人员进行技术培训;三级安全与文明施工教育;经考试合格后持证上岗。表面除锈与橡胶衬里工应具备中级工资格,配备的工人技师和高级技工比例不低于施工人数的49%,并持证上岗,机电设备操作工和电工等工种均应持证上岗。 2.3 待衬设备、衬里材料的验收、保管 2.3.1 待衬设备的检查与验收: 2.3.1.1 设备进场时需由建设单位、施工、制造和监理等有关部门共同对名称、型号规格、数量等进行检查验收。 (1) 常温预硫化衬胶设备主要检查设备壁厚、直径、长度、椭园度等几何尺寸是否与图纸相符、进出口接管方位等与设计图纸是否符合。 (2) 需用0.2MPa或0.3MPa蒸汽进行自身热硫化的设备,应按压力容器要求检查,应有压力容器制作合格证明、试压检测报告、测试压力应按硫化蒸汽压1.5倍检测合格,有劳动部门颁发的合格证和检测报告。 (3) 管道衬胶应使用无缝钢管制作,法兰密封面应为不加工水线的平面。 2.3.1.2 衬胶钢设备要求如下: (1) 钢材表面不得有伤痕、气孔、焊渣、重叠皮、严重腐蚀斑,加工表面必须平整,表面局部凹凸不得超过2mm。 (2) 铸铁、铸钢类的设备、管道,原则不适合衬热硫化胶,但对一些形状简单的如平盖等部件可采用挂线排汽法衬胶。 (3) 设备表面应光滑平整,圆弧过度焊缝不得凸出表面2mm,不得有锐角、棱角。设备顶盖与筒体焊缝R≥5mm;筒体与底板焊缝R≥3mm。焊缝必须连续,焊缝和缺陷部位均应补焊成打磨合格。 (4) 设备接管不得深入内表面,设备内不应设加强筋板等构件,应为平滑的表面。 (5) 衬胶设备、管道均应采用法兰连接,大型设备应在现场制作就位后进行衬胶作业。 (6) 直径小于700mm的设备,其高度不应大于700mm,直径800至1200mm设备,高度不应大于1500mm,超过时应分段用法兰连接。 (7) 多孔板、离心机转鼓孔眼以及需要公差配合的部件,应预留衬胶层厚度尺寸,验收时应特别重视。 (8) 三通、四通等管件的尺寸应符合HGJ229《工业设备、管道防腐蚀工程施工及验收规范》标准要求。 2.3.1.3 经检查不符合规定的设备、管道、管件应返工至检收合格后方充许进行衬胶作业。 2.3.1.4 一切机械加工与焊接均应在验收前完成,严防衬胶完成后更改接管、部件,造成衬胶层局部损坏。衬胶完成后设备严禁动火作业。 2.3.2 衬里材料的检查、验收、存放与保管: 2.3.2.1 进口胶板的检查、验收 (1) 进口冷藏胶板的检查与验收:施工单位、使用单位、监理等有关部门应配合海关进行检查,检查包括数量、规格、胶板质量、尺寸、厚度;生产日期、合格证、检测报告、押运记录等,并取样进行硫化度,可塑性检测。合格后,运至施工现场专用仓库冷藏保管。