带传动设计要求
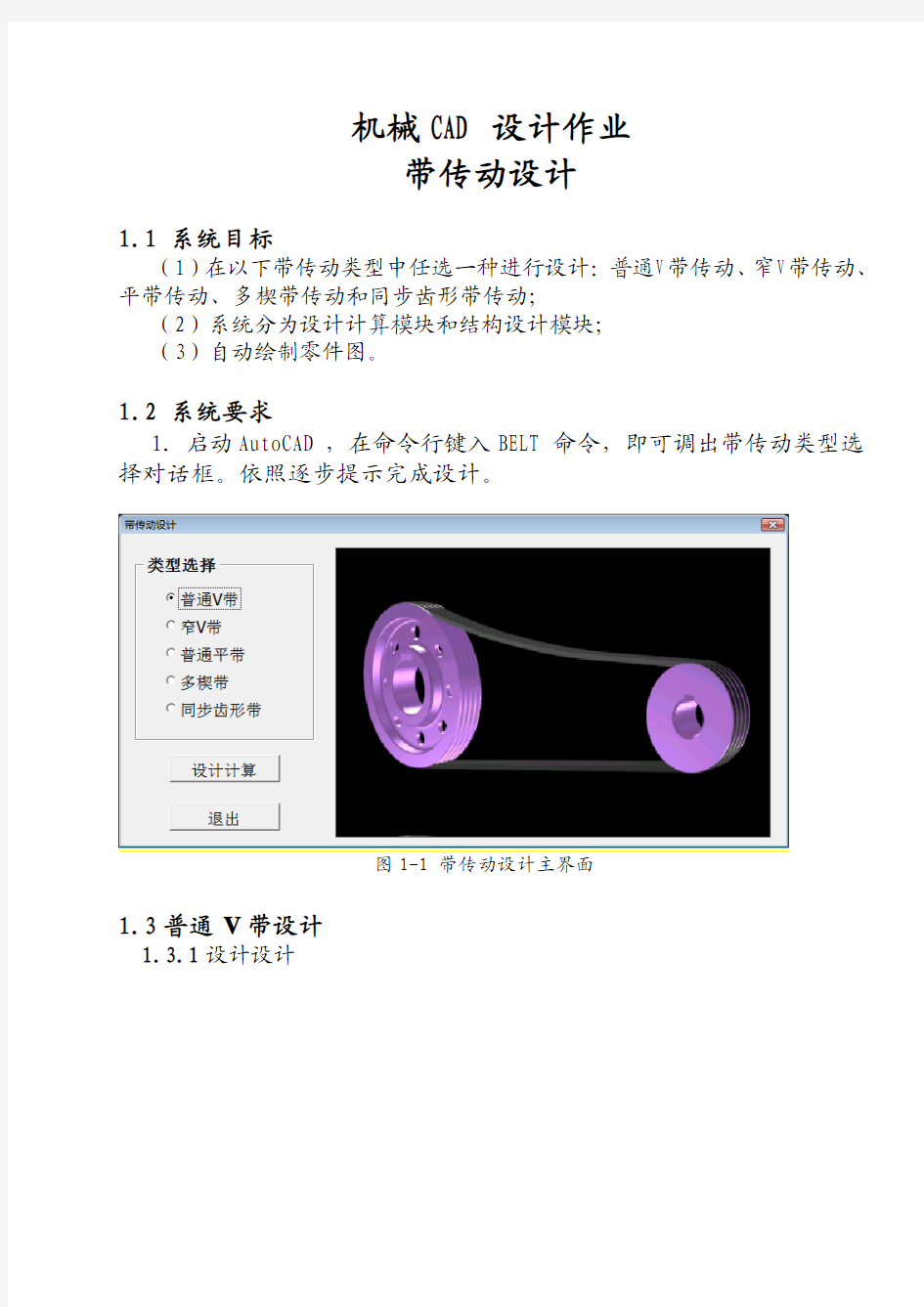

机械CAD设计作业
带传动设计
1.1 系统目标
(1)在以下带传动类型中任选一种进行设计:普通V带传动、窄V带传动、平带传动、多楔带传动和同步齿形带传动;
(2)系统分为设计计算模块和结构设计模块;
(3)自动绘制零件图。
1.2 系统要求
1.启动AutoCAD,在命令行键入BELT命令,即可调出带传动类型选择对话框。依照逐步提示完成设计。
图1-1 带传动设计主界面
1.3普通V带设计
1.3.1设计设计
图1-2 普通V 带设计计算
在设计计算界面中,用户可在下拉列表和文本框中选择所要求的工作性能指标
【单击“上一页”按钮】返回类型选择界面
【单击“确定”按钮】确认输入参数,进入带型选择界面,如图1-3示。 1.3.2带型选择
普通V 带选型图中的十字交叉线指示出已知条件主动轮转速和设计功率在选型图中的位置
在参数选择面板中根据交叉线的交点在参数选择栏中选取合适的带型及主动轮直径。
【单击“上一页”按钮】 返回“设计计算”界面。
【单击“确定”按钮】进入“中心距、带长、包角的确认”界面 如图1-4所示
1.3.3中心距,带长,包角的确认
图1-3 带型选择
【键盘输入“输入中心距”】根据参考参数的最大,最小参数进行选择 【单击“计算带长”按钮】软件计算各参数
【单击“选定”按钮】从两组计算结果中选定一组
【单击“参数回显”按钮】查看完整的计算结果,如图2-5所示 【单击“上一页”按钮】返回“带型选择”界面
【单击“确定”按钮】确认输入参数,进行“带轮内孔结构设计”界面, 如图1-6所示
1.3.4内孔结构设计
【单击“选择带轮”】指明要设计大带轮(从动轮)还是小带轮 (主动轮)。
【单击“力矩传递形式”】进入“多楔带设计---类型选择”界面, 如图1-7所示
【单击“结构设计”】向下进行带轮结构设计。如图1-12所示
1.3.4.1类型选择
图1-4 中心距、带长。包角确认
图1-5 主要参数
图1-6带轮内孔结构设计
【单击“
键连接”】设计单键及双键,如图2-8所示 【单击“矩形花键”】设计矩形花键,如图2-10所示 【单击“矩形花键”】设计渐开线花键 如图2-11所示 1.3.4.2键联接
图 1-8键联接
【单击 “左边图片” 】设计单键。输入和选择相应参数。
【单击 “右边图片” 】设计双键。输入和选择相应参数。会弹出对话框要求输入双键夹角。如图1-9
图1-7类型选择
图1-9双缝的夹角
1.3.4.3矩形花键
图1-10 矩形花键
【选择“选系列”】根据传递载荷大小选择轻系列或中系列。
【选择“选精度及其它”】根据提示选择键的精度等级(默认为H7)及其它。
【单击“小径d”】从下拉框中选取标准系列值。
1.3.4.4渐开线花键对话框。
图1-11渐开线花键
【选择“基准齿型”】选择渐开线齿型压力角,角度越大承载能力越强。【选择“公差项选择”】从下拉框中选取。
【选择“选系列”】选择出图时绘制渐开线花键的参数表。
1.3.5带轮结构设计对话框
图1-12 带轮结构设计
【单击“确定”按钮】出现“结构参数、图辐设置”界面,如图1-13所示
1.3.6结构参数,图幅设置
【选择“图纸形式”】装配图是指出图时仅画出带轮实体,不包括标注、图辐设置等。
【单击“图幅”按钮】出现“设置图纸”界面,如图1-14所示 【单击“绘图”按钮】确认输入参数,进行下面的计算。 【单击“退出”按钮】结束本次设计过程。
1.4窄V 带设计
窄V 带设计和普通V 带设计过程十分相似,仅仅是带型选型图不同,其他基本与普通V 带设计一致。如有问题可以参考普通V 带设计。
1.5普通平带设计
1.5.1基本参数对话框
图1-13 结构参数、图辐设置
图1-14设置图纸
图1-15 普通平带设计—基本参数
【选择“基本参数”】P: 传动功率。n1:主动轮转速。i:传动比。
a:中心距,可以不输,但应将它置0,系统会计算一个合适的值。
【选择“工作机”】选择工作情况。
【选择“动力机”】两种类型,可供选择。在该栏,可以点击单选按钮选择动力机类型,或者从下拉框中选择动力机。
【选择“每天工作小时数”】三个选项:<10,>10并<16,>16。
【选择“带型”】两组选项:包边式或切边式,环形或有端。
【选择“恶劣条件选项”】指明工作条件是否十分恶劣。
【选择“传动形式选择”】选择传动布置形式,指定传动比误差,及其它。如图1-16所示。
【选择“计算”】计算并显示结果。如图1-17所示。
【选择“带轮结构设计”】向下进行结构设计步骤。
1.5.2传动形式对话框
图1-16传动形式
【选择“传动形式”】点击即选中
【选择“β 传动布置角”】两带轮中心线与水平面的夹角 【选择“传动比误差”】Δi=(i ’-i)/i ,两个选项:<3%,<5%。 【选择“带轮数目”】 主动轮、从动轮和辅助轮的总数。 【选择“自动张紧”】指明传动系统是否有自动张紧装置。
1.5.3
带轮内孔结构设计对话框 【选择“
选择带轮”】 指明要设计大带轮(从动轮)还是小带轮(主动轮)。
【选择“力矩传递形式”】 选择键连接形式,参看1.3.4节 【选择“结构设计”】 向下进行带轮结构设计,如图1-24所示 1.5.4带轮结构设计
【选择“普通平带带轮结构选型图”】白色十字交叉线的交点指示系统
1-24带轮结构设计
图1-17计算结果
推荐的带轮结构形式,并且在对话框启动时已经为您选择了该结构形式,您所要做的是具体选择带轮的偏置形式。
【选择“带轮结构简图”】如果您觉得系统推荐的形式不合适,可以自行选择。
【选择“确定”按钮】出现“带轮结构参数”界面,如图1-25所示
1.5.5带轮结构参数
图1-25带轮结构参数
【选择“待定参数”】选择轮毂长度、轮缘偏距、辐板厚度参数。
单位:mm。
【选择“辐板孔数或轮辐数”】根据带轮形式不同,代表的含义不同,在某些形式下不可选。
【选择“出图方式”】零件图:包括图框、标题栏、标注、技术要求等。
装配图:只有带轮主视图,没有标注。
【选择“右上图片”】指示所选带轮形式。
【选择“右下图片”】指示所选键连接形式。
【点击“绘图”按钮】开始绘图。
1.6多楔带设计
多楔带设计与普通平带设计过程相似,可参考普通平带设计
1.7同步齿型带设计
1.7.1参数确定对话框
1.7.1.1动力参数属性页,如图1-30所示
【选择“动力参数”】选择传动功率、传动性质(加速或减速)、传动比、主动轮转数参数。
1.7.1.2原动机属性页,如图1-31所示
【选择“原动机”】共分两大类,根据您的实际情况选择。
图1-30参数确定——动力参数
图1-31参数确定——原动机
1.7.1.3工作机属性页,如图1-32所示
【选择“工作机”】共分八大类,根据实际选择与工作情况相近似的工
作机。
1.7.1.4运转时间属性页,如图1-33所示
【选择“选择运转时间”】有三个选项,根据您的实际工作情况选择。 1.7.1.5张紧轮属性页,如图1-34所示
图
1-32参数确定——工作机
图1-33参数确定——运转时间
【选择“是否有张紧轮”】两个选项,根据您的实际工作情况选择。
【选择“张紧轮的位置”】四个选项,张紧轮在松边内侧、松边外侧、紧边内侧、紧边外侧。 【选择“右上图片”】显示是否有张紧轮。 【选择“右下图片”】显示张紧轮的位置。
【单击“确定”按钮】进入“带型选择”界面,如图1-35所示
1.7.2带型选择对话框
【选择“已知参数”】选型所需的参数:小带轮转速、设计功率。
图1-34参数确定——张紧轮
图1-35带型选择
【选择“带型选择”】根据选型图提示,从下拉框中选取。
【选择“小带轮齿数”】优先:系统推荐标准系列值;
自选:可以输入非标准值系列。
【选择“计算结果”】计算结果,供您参考选择使之合适的小带轮齿数。
【选择“确定”】确认计算结果,进入“中心距、带长”界面,如图所示
1.7.3中心距,带长
图1-36 中心距,带长
【单击“参数回显”按钮】进入“参数回显”界面如图1-37,其中【单击“报表”按钮】将计算结果保存到文件
图1-37参数回显
【单击“确定”按钮】进入“带轮内孔结构设计”界面,如图1-38所示
1.7.4带轮内孔设计
图1-38带轮内孔结构设计
【单击“力矩传动形式”按钮】进入“类型选择”界面,参看3.4节 【单击“结构设计”按钮】进入“带轮结构设计”界面,如图1-44所示
1.7.5带轮结构形式对话框
【选择“带轮齿廓”】 选择轮齿形状:渐开线齿廓、直边齿廓。 【选择“带轮挡圈”】选择挡圈设置位置:共四种情况。 【选择“挡圈设计”】 设计挡圈特征参数。如图2-45所示 【选择“数据存盘”按钮】 将此次设计参数保存在文件。
【选择“确定”按钮】确认选择结果,进行“结构参数,图幅设计”界
图1-44带轮结构形式
面,如图1-46所示
1.7.6带轮挡圈设计对话框
【选择“带轮挡圈尺寸示意图”】指明参数含义。 【选择“高度”】K:系统将提示允许的最小值。 【选择“厚度”】t: 系统将提示允许的取值范围。 【选择“内孔直径”】d: 系统将提示允许的取值范围。 【选择“弯曲角度”】α: 系统将提示允许的取值范围。 1.7.7结构参数,图幅设计
【选择“图纸形式”
】装配图是指出图时仅画出带轮实体,不包括标注、图辐设置等。
图1-45带轮挡圈设计
图1-45 结构参数、图辐设置 图1-46设置图纸
【单击“图幅”按钮】出现“设置图纸”界面,如图1-46所示
【单击“绘图”按钮】确认输入参数,进行下面的计算。
【单击“退出”按钮】结束本次设计过程。
1.8出图过程
1.8.1图纸设定对话框
图2-47图纸设定
【选择“装订线”】图纸侧面宽度为25mm的空白区域,供图纸装订用。
【选择“图纸布置”】横置或纵置。
【选择“对中符号”】位于图纸两个对称轴上的小段直线,用于标记图纸对称轴。
【选择“图幅分区”】将绘图平面分为指定数量的网格区域,并用字母和【选择“幅面设置”】下拉框:可以从中选取合适的图辐;点选:从对比图中选取。
【选择“比例设置”】“基数”下拉框:可以从中选取合适的比例系数;
“幂次”下拉框:10的n次方。“放大”选择框:所绘图形是否将来会为放大图。
1.8.2技术要求对话框可以从中选取需要填写的技术要求。
图1-48技术要求
可以通过鼠标选择技术指标,单击OK确定1.8.3生成图形。
V带传动设计计算
设计行车驱动装置中的V带传动 行车驱动装置的传动方案如下图所示。室内工作、工作平稳、机械成批生产,其他数据见下表。 一带传动计算 1.确定计算功率 设计功率是根据需要传递的名义功率再考虑载荷性质、原动机类型和每天连续工作的时间长短等因素而确定的,表达式为 式中 ——所需传递的名义功率(KW); ——工作情况系数,按表。 选取=1.2 则=1.2 2.2 =2.64 2.选择带的型号 带的型号可根据设计功率和小带轮转速由图7.11选取。因为 ,,所以选取型带。 3.确定带轮的基准直径和 传动带中的弯曲应力变化是最大的,它是引起带疲劳破坏的主要因素。带轮
直径愈小,弯曲应力愈大。因此,为减小弯曲应力应采用较大的小带轮直径。但过大,会使传动的尺寸增大。由于无特殊要求,取大于等于许用的最小带轮基准直径即可(见表7.7)。取=95 。 所选带轮直径应圆整为带轮直径系列值,即表7.3中“注”所列数值。则取=100 。 由于并不必要使传动比太精确,则无要考虑滑动系数来计算轮径。则大带轮直径 =。 符合表7.7及表7.3中“注”所列数值 4.验算带的速度 即 故符合要求。 5.确定中心距和带基准长度 中心距小,可以使传动结构紧凑。但也会因带的长度小,使带在单位时间内绕过带轮的次数多,降低带的寿命。同时在传动比和小带轮直径一定的情况 下,中心距小,小带轮包角将减小,传动能力降低。中心距大则反之。其次,中心距过大,当带速高时,易引起带工作时抖动。 由于无特殊要求,可在下列范围内初步选取中心距 即 初步取,则带的基准长度计算公式 则′。由表7.2选取接近的标准基准长度,则实际中心距(通常中心距是可调的) ′ 6.计算小轮包角 由小带轮上的包角计算公式
传动轴设计计算
编号: 传动轴设计计算书 编制:日期: 校对:日期: 审核:日期: 批准:日期:
一.计算目的 我们初步选定了传动轴,轴径选取Φ27(详见《传动轴设计方案书》),动力端选用球面滚轮万向节,车轮端选用球笼万向节。左、右前轮分别由1根等速万向节传动轴驱动。通过计算,校核选型是否合适。 二.计算方法 本车传动轴设计不是传统载货车上从变速器到后驱动桥之间长轴传动设计,而是半轴传动设计。而且传动轴材料采用高级优质合金钢,且热处理工艺性好,使传动轴的静强度和疲劳强度大为提高,因此计算中许用应力按照半轴设计采用含铬合金钢,如40Cr、42CrMo、40MnB,其扭转屈服极限可达到784 N/mm2左右,轴端花键挤压应力可达到196 N/mm2。 传动轴校核计算流程:
1.1 轴管直径的校核 校核: 两端自由支撑、壁厚均匀的等截面传动轴的临界转速 22 2 8 1.2x10 n e l d D+ =(r/min) 式中L传动轴长,取两万向节之中心距:mm D为传动轴轴管外直径:mm d为传动轴轴管直径:mm 各参数取值如下:D=φ27mm,d=0mm 取安全系数K=n e/n max,其中n max为最高车速时的传动轴转速,取安全系数K=n e/n max=1.2~2.0。 实际上传动轴的最大转速n max=n c/(i g×i0),r/min 其中:n c-发动机的额定最大转速,r/min; i g-变速器传动比; i0-主减速器传动比。
1.2 轴管的扭转应力的校核 校核扭转应力: τ= ][164 4τπ≤) -(d D DT J (N/mm 2) ][τ……许用应力,取][τ=539N/mm 2[高合金钢(40Cr 、40MnB 等)、中频淬火抗拉 应力≥980 N/mm 2,工程应用中扭转应力为抗拉应力的0.5~0.6,取该系数为0.55,由此可取扭转应力为539 N/mm 2,参考GB 3077-88] 式中: T j ……传动系计算转矩,N ·mm ,2/k i i T T d g0g1x ema j η= N ·m T emax -发动机最大转矩N ·mm ; i g1-变速器一档传动比或倒档传动比; i g0-主减速器传动比 k d -动载系数 η-传动效率 1.3 传动轴花键齿侧挤压应力的校核 传动轴花键齿侧挤压应力的校核 ][)2 )(4(2121j j ZL D D D D T σσ≤-+= (N/mm 2 ) 式中:T j -计算转矩,N ·mm ; D 1,D 2-花键的外径和径,mm ; Z ………花键齿数 L ………花键有效长度
传动轴设计
本科毕业设计(论文)通过答辩 课程设计 题目:转向轴的设计 学生: 学号: 院(系): 专业: 指导教师: 2006年 12月 10日
转向轴的设计 陕西科技大学 机械制造技术基础课程设计任务书题目:设计“转向轴”(年产10000件) 内容:⑴零件图 1张 ⑵毛坯图 1张 ⑶工序图 1张 ⑷机械加工工艺卡片 1套 ⑸工艺规程 1套 ⑹课程设计说明书 1份
陕西科技大学课程设计说明书 目录 第1章………………………………………设计说明 第2章………………………………………零件分析 第3章………………………………………工艺分析 第4章………………………………………制定工艺路线 第5章………………………………………机械加工余量的确定第6章………………………………………确定切削用量 第7章………………………………………加工的几点说明 第8章………………………………………总结 第9章………………………………………参考文献
转向轴的设计 设计说明 本次课程设计是在我们学完了大学的全部基础课、技术基础课之后进行的。这是我们在进行毕业设计之前所学各课程的一次深入的综合性的总复习,也是一次理论联系实际的训练。因此,它在我们四年的大学生活中占有重要的地位。 就我个人而言,我希望能通过这次课程设计对自己未来将从事的工作进行一次适应性训练,从中锻炼自己分析问题、解决问题的能力,为今后参加祖国的现代化建设打下一个良好的基础。 由于能力所限设计尚有许多不足之处,恳请各位老师给予指教。 1 .2.1 零件的分析 1.2.1.1 生产类型 本题目所要加工的为一阶梯轴,要求批,量为10000件,可确定其生产类型为大批量生产。 1.2.1.2 零件分析 题目所给定的零件是一主要支撑传动件和传递扭矩的阶梯轴,轴类零件是旋转体零件,其长度大于直径,一般由圆柱面、圆锥面、螺纹、花键、沟槽等。考虑到加工工艺,在车外圆时在两端车刀无法顺利退出所以零件在两端应加退刀槽,详见零件图。 1.2.1.3 零件的工艺分析 阶梯轴零件图样的视图正确、完整、尺寸、公差及技术要求齐全。本零件各表面的加工并不困难,但零件左边的键槽与其左端面距离只有3mm,有点小加工时估要精确的保证上述要求则比较困难。分析该零件是作传动齿轮转矩所用,故可以将其键槽长度做的稍微小一点,也保证了阶梯轴的强度。又零件图中的直线度精度要求较高,加工时比较困难,即定位基准要保证。 1.2.2 工艺规程的设计 1.2.2.1 确定毛坯的制造形式
机械设计—V带轮的设计
机械设计说明书 设计题目:V带轮传动设计班级:学号: 设计人:
完成日期:2012 年12 月12 日 目录 第一章普通V带传动设计. . . . . . . . . . . . . . . . . . . . . . . . ........... 3 第二章轴径的设计 (5) 一、主动轮轴材料的选 择 (5) 二、主动轮轴的设计及校 核 (5) 三、从动轮轴材料的选择...................................... . . ... 6 四、从动轮轴的设计及校核........................................ 6 第三章V带轮的结构设计....................................... 7 一、主动带轮的结构形 式 (7) 二、从动带轮的结构形 式 (8) 第四章键的选择及强度校核 (9)
一、主动轮轴的键的设计及校核.................................. 9 二、主动轮轴的键的设计及校核................................. 10 第五章装配图及爆炸图........................................ 11 一、零件的爆炸图.............................................. 11 二、零件的装备图.............................................. 12 第六章设计总结............................................... 14 第七章参考文献............................................... 15
传动轴结构分析与设计(精)
第五节传动轴结构分析与设计 传动轴总成主要由传动轴及其两端焊接的花键轴和万向节叉组成。传动轴中一般设有由滑动叉和花键轴组成的滑动花键,以实现传动长度的变化。为了减小滑动花键的轴向滑动阻力和磨损,有时对花键齿进行磷化处理或喷涂尼龙层;有的则在花键槽中放入滚针、滚柱或滚珠等滚动元件,以滚动摩擦代替滑动摩擦,提高传动效率。但这种结构较复杂,成本较高。有时对于有严重冲击载荷的传动,还采用具有弹性的传动轴。传动轴上的花键应有润滑及防尘措施,花键齿与键槽间隙不宜过大,且应按对应标记装配,以免装错破坏传动轴总成的动平衡。 传动轴的长度和夹角及它们的变化范围由汽车总布置设计决定。设计时应保证在传动轴长度处在最大值时,花键套与轴有足够的配合长度;而在长度处在最小时不顶死。传动轴夹角的大小直接影响到万向节十字轴和滚针轴承的寿命、万向传动的效率和十字轴旋转的不均匀性。 在长度一定时,传动轴断面尺寸的选择应保证传动轴有足够的强度和足够高的临界转速。所谓临界转速,就是当传动轴的工作转速接近于其弯曲固有振动频率时,即出现共振现象,以致振幅急剧增加而引起传动轴折断时的转速。传动轴的临界转速为 22 2 8 10 2.1 C c C k L d D n + ? = (4—13) 式中,n k为传动轴的临界转速(r/min);L C为传动轴长度(mm),即两万向节中心之间的距离;d c和D c分别为传动轴轴管的内、外径(mm)。 在设计传动轴时,取安全系数K=n k/n max=1.2~2.0,K=1.2用于精确动平衡、高精度的伸缩花键及万向节间隙比较小时,n max为传动轴的最高转速(r/min)。 由式(4—13)可知,在D c和L c相同时,实心轴比空心轴的临界转速低,且费材料。另外,当传动轴长度超过1.5m时,为了提高n k以及总布置上的考虑,常将传动轴断开成两根或三根,万向节用三个或四个,而在中间传动轴上加设中间支承。 传动轴轴管断面尺寸除满足临界转速的要求外,还应保证有足够的扭转强度。轴管的扭转切应力τc应满足
传动轴结构分析与设计
传动轴结构分析与设计 传动轴总成主要由传动轴及其两端焊接的花键轴和万向节叉组成。传动轴中一般设有由滑动叉和花键轴组成的滑动花键,以实现传动长度的变化。为了减小滑动花键的轴向滑动阻力和磨损,有时对花键齿进行磷化处理或喷涂尼龙层;有的则在花键槽中放入滚针、滚柱或滚珠等滚动元件,以滚动摩擦代替滑动摩擦,提高传动效率。但这种结构较复杂,成本较高。有时对于有严重冲击载荷的传动,还采用具有弹性的传动轴。传动轴上的花键应有润滑及防尘措施,花键齿与键槽间隙不宜过大,且应按对应标记装配,以免装错破坏传动轴总成的动平衡。 传动轴的长度和夹角及它们的变化范围由汽车总布置设计决定。设计时应保证在传动轴长度处在最大值时,花键套与轴有足够的配合长度;而在长度处在最小时不顶死。传动轴夹角的大小直接影响到万向节十字轴和滚针轴承的寿命、万向传动的效率和十字轴旋转的不均匀性。 在长度一定时,传动轴断面尺寸的选择应保证传动轴有足够的强度和足够高的临界转速。所谓临界转速,就是当传动轴的工作转速接近于其弯曲固有振动频率时,即出现共振现象,以致振幅急剧增加而引起传动轴折断时的转速。传动轴的临界转速为 22 2 8 10 2.1 C c C k L d D n + ? = (4—13) 式中,n k为传动轴的临界转速(r/min);L C为传动轴长度(mm),即两万向节中心之间的距离;d c和D c分别为传动轴轴管的内、外径(mm)。 在设计传动轴时,取安全系数K=n k/n max=1.2~2.0,K=1.2用于精确动平衡、高精度的伸缩花键及万向节间隙比较小时,n max为传动轴的最高转速(r/min)。 由式(4—13)可知,在D c和L c相同时,实心轴比空心轴的临界转速低,且费材料。另外,当传动轴长度超过1.5m时,为了提高n k以及总布置上的考虑,常将传动轴断开成两根或三根,万向节用三个或四个,而在中间传动轴上加设中间支承。 传动轴轴管断面尺寸除满足临界转速的要求外,还应保证有足够的扭转强度。轴管的扭转切应力τc应满足
同步带传动类型及及设计计算标准
同步带传动类型及及设计计算标准 (GB-T10414?2-2002同步带轮设计标准) 圆弧齿同步带轮轮齿ArctoothTimingtooth 直边齿廓尺寸Dimensionoflineartypepulley
1、同步带轮的型式 2、齿型尺寸、公差及技术参数 3、各种型号同步带轮齿面宽度尺寸表 4、订购须知 圆弧齿轮传动类型: 1)圆弧圆柱齿轮分单圆弧齿轮和双圆弧齿轮。 2)单圆弧齿轮的接触线强度比同等条件下渐开线齿轮高,但弯曲强度比渐开线低。 3)圆弧齿轮主要采用软齿面或中硬齿面,采用硬齿面时一般用矮形齿。圆弧齿轮传动设计步骤: 1)简化设计:根据齿轮传动的传动功率、输入转速、传动比等条件,确定中心距、模数等主要参数。如果中心距、模数已知,可跳过这一
步。 2)几何设计计算:设计和计算齿轮的基本参数,并进行几何尺寸计算。 3)强度校核:在基本参数确定后,进行精确的齿面接触强度和齿根弯曲强度校核。 4)如果校核不满足强度要求,可以返回 圆弧齿轮传动的特点: 1)圆弧齿轮传动试点啮合传动,值适用于斜齿轮,不能用于直齿轮。 2)相对曲率半径比渐开线大,接触强度比渐开线高。 3)对中心距变动的敏感性比渐开线大。加工时,对切齿深度要求较高,不允许径向变位切削,并严格控制装配误差。 单圆弧齿轮传动 小齿轮的凸齿工作齿廓在节圆以外,齿廓圆心在节圆上;大齿轮的凹齿工作齿廓在节圆内,齿廓圆心略偏於节圆以外(图2单圆弧齿轮传动的嚙合情况)。由於大齿轮的齿廓圆弧半径p2略大於小齿轮的齿廓半径p1,故当两齿廓转到K点,其公法线通过节点c时,齿便接触,旋即分离,但与它相邻的另一端面的齿廓随即接触,即两轮齿K1﹑K'1、K2﹑K'2﹑K3﹑K'3……各点依次沿嚙合线接触。因此,圆弧齿轮任一端面上凹﹑凸齿廓仅作瞬时嚙合。一对新圆弧齿轮在理论上是瞬时点嚙合,故圆弧齿轮传动又常称为圆弧点嚙合齿轮传动。轮齿经过磨合后,实际上齿廓能沿齿高有相当长的一段线接触。圆弧齿轮传动的特点是:(1)综合曲率半径比渐开线齿轮传动大很多,其接触强度比渐开线齿轮传动约高0.5~1.5倍;
普通V带轮传动设计
第三节普通V带传动的设计... 一、失效形式和设计准则... 二、单根V带所能传递的功率... 三、设计计算和参数选择... 四、带轮设计... 五、V带传动的张紧装置... 第三节普通V带传动的设计 一、失效形式和设计准则 如前所述,带传动靠摩擦力工作。当传递的圆周阻力超过带和带轮接触面上所能产生的最大摩擦力时,传动带将在带轮上产生打滑而使传动失效。 另外,传动带在运行过程中由于受循环变应力的作用会产生疲劳破坏。 因此,带传动的设计准则是:既要在工作中充分发挥其工作能力而又不打滑,同时还要求传动带有足够的疲劳强度,以保证一定的使用寿命。 二、单根V带所能传递的功率
单根V带所能传递的功率是指在一定初拉力作用下,带传动不发生打滑且有足够疲劳寿命时所能传递的最大功率。从设计要求出发,应使≤,根据(7–14)可写成 ≤ 这里,[s]为在一定条件下,由疲劳强度决定的V带许用拉应力。由实验知,在108~109次循环应力下为 (MPa) 式中Z–––V带绕过带轮的数目; v––– V带的速度(m/s); L –––V带的基准长度(m); d T–––V带的使用寿命(h); C–––由V带的材质和结构决定的实验常数。 由式(7–4)和式(7–5)并以当量摩擦系数f v替代f,可得最大有效圆周力
即 式中A–––V带的截面面积(mm2)。 单根V带所能传递的功率为 即 (kW) (7–15)在传动比i=1(即包角a=180°)、特定带长、载荷平稳条件下由式(7–15)计算所得的单根普通V带所能传递的基本额定功率P1值列于表7–4。 当传动比i>1时,由于从动轮直径大于主动轮直径,传动带绕过从动轮时所产生的弯曲应力低于绕过主动轮时所产生的弯曲应力。因此,工作能力有所提高,即单根V带有一功率增量DP1,其值列于表7–4。这时单根V带所能传递的功率即为(P1+DP1)。如实际工况下包角不等于180°、胶带长度与特定带长不同时,则应引入包角修正系数K (表7–5)和长度修正系数K L(表7–6)。
普通V带传动设计
普通V 带传动设计 已知条件:P=15KW ,小带轮转速n=960r/min,传动比i=2,传动比允许误差≤±5%,轻度冲击;两班工作制。 一.V 带传动的设计计算: 1. 确定计算功率: 查P156表8-7得工作情况系数:A K =1.1 ca P =A K P=1.1×15=16.5Kw 2. 选择V 带的带型: 根据计算功率ca P 和小带轮转速1 n ,由P157图8-11选择V 带的带 型为:B 型 3. 初选小带轮的基准直径1 d d : 查P155表8-6得:min )(d d =125 根据1 d d ≥min )(d d 查P157表8-8取:1 d d =200㎜ 验算带速v :根据P150公式8-13得: v= = ???= ???m/s 1000 60960 20014.31000 6011n d d π10.05m/s 计算大带轮直径,由公式2 d d =i 1 d d 并根据P157表8-8加以适当圆整 取2 d d =400㎜ 4.确定中心距a ,并选择V 带的基准长度d L 根据P152公式8-20初定中心距0 a :0.7(1 d d +2 d d )≤0a ≤2(1d d +2 d d ) 得420≤0 a ≤1200 于是初定0 a =1000 计算相应的带长0Ld :
据式0 d L ≈0 2a + + +)(2 21d d d d π0 2 124) (a d d d d - =1000 4)200400()400200(2 14.31000 22 ?-+ +?+ ?=2952 再根据P146表8-2选取:d L =3150 5.按P158式8-23计算实际中心距a : a ≈0 a + 2 d d L L -=1000+ 2 2952 3150-=1049 并根据公式 d d L a a L a a 03.0015.0max min +=-=】;的中心距的变化范围为1001.8~1143.5 6.验算小带轮上的包角1 a : 1α≈180°-(12d d d d -) a 3.57=180°-(400-200)1049 3.57 ? ≈169° 7.计算带的根数z: 由1 d d =200㎜和1n =960r/min,查P152表8-4a 取:0 P =3.77Kw ; 根据1 n =960r/min,i=2和B 型带,查P154表8-4b 取2:0 P ?=0.3; 查P155表8-5取:αK =0.98;查P146表8-2取:L K =1.07于是: = r P (0 P P ?+)α K L K 所以:Z== ??+?= ?+= 98 .007.1)3.077.3(15 1.1)(00L A r ca K K P P P K P P α 3.87 取Z=4根。 8.确定单根V 带得初拉力0 F : 查P149表8-3得B 型带的单位长度质量q=0.18kg/m,所以 根据P158式8-27得: min 0)(F =2 2 05 .1018.005 .10407.15.16)07.15.2(500)5.2(500 ?+???-? =+-qv zv K P K ca a α
万向传动轴设计实例
万向传动轴设计说明书
商用汽车万向传动轴设计 摘要 万向传动轴在汽车上应用比较广泛。发动机前置后轮或全轮驱动汽车行驶时,由于悬架不断变形,变速器或分动器的输出轴与驱动桥输入轴轴线之间的相对位置经常变化,因而普遍采用可伸缩的十字轴万向传动轴。本设计注重实际应用,考虑整车的总体布置,改进了设计方法,力求整车结构及性能更为合理。传动轴是由轴管、万向节、伸缩花键等组成。伸缩套能自动调节变速器与驱动桥之间距离的变化;万向节是保证变速器输出轴与驱动桥输入轴两轴线夹角发生变化时实现两轴的动力传输;万向节由十字轴、十字轴承和凸缘叉等组成。传动轴的布置直接影响十字轴万向节、主减速器的使用寿命,对汽车的振动噪声也有很大影响。在传动轴的设计中,主要考虑传动轴的临界转速,计算传动轴的花键轴和轴管的尺寸,并校核其扭转强度和临界转速,确定出合适的安全系数,合理优化轴与轴之间的角度。 关键字:万向传动轴、伸缩花键、十字轴万向节、临界转速、扭转强度
目录 一、概述 (04) 二、货车原始数据及设计要求 (05) 三、万向节结构方案的分析与选择 (06) 四、万向传动的运动和受力分析 (08) 五、万向节的设计计算 (11) 六、传动轴结构分析与设计计算 (17) 七、法兰盘的设计 (19) 八、参考文献 (20)
一、概述 汽车上的万向传动轴一般是由万向节、轴管及其伸缩花键等组成。主要是用于在工作过程中相对位置不断变化的两根轴间传递转矩和旋转运动。 在动机前置后轮驱动的汽车上,由于工作时悬架变形,驱动桥主减速器输入轴与变速器输出轴间经常有相对运动,普遍采用万向节传动(图1—1a、b)。当驱动桥与变速器之间相距较远,使得传动轴的长度超过1.5m时,为提高传动轴的临界速度以及总布置上的考虑,常将传动轴断开成两段,万向节用三个。此时,必须在中间传动轴上加设中间支承。 在转向驱动桥中,由于驱动桥又是转向轮,左右半轴间的夹角随行驶需要而变,这是多采用球叉式和球笼式等速万向节传动(图1—1c)。当后驱动桥为独立悬架结构时也必须采用万向节传动(图1—1d)。 万向节按扭转方向是否有明星的弹性,可分为刚性万向节和挠性万向节两类。刚性万向节又可分为不等速万向节(常用的为普通十字轴式),等速万向节(球叉式、球笼式等),准等速万向节(双联式、凸块式、三肖轴式等)。 万向节传动应保证所连接两轴的相对位置在预计范围内变动时,能可靠地传递动力,保证所连接两轴尽可能同步运转,由于万向节夹角而产生的附加载荷、振动和噪声应在允许范围内。
传动轴毕业设计
毕业设计(论文) (说明书) 题目: 姓名: 编号: 平顶山工业职业技术学院 年月日
摘要 通过在校期间对传动轴的学习和认识对传动轴进行一下系统的分析和设计,支承传动件的零件称为轴。轴类零件毕业设计是机械工程类专业学生完成本专业教学计划的最后一个极为重要的实践性教学环节,是使学生综合运用所学过的基本理论、基本知识与基本技能去解决专业范围内的工程技术问题而进行的一次基本训练。这对学生即将从事的相关技术工作和未来事业的开拓都具有一定意义传动轴是组成机器零件的主要零件之,一切做回转运动的传动零件(例如:齿轮,蜗轮等)都必须安装在传动轴上才能进行运动及动力的传动,传动轴常用于变速箱与驱动桥之间的连接。这种轴一般较长,且转速高,只能承受扭矩而不承受弯矩。应该使传动轴具有足够的刚度和高临界转速,在强度计算中,由于所取的安全系数较大,从而使轴的尺寸过大,本文讨论的传动轴工艺设计方法,并根据现行规范增添了些表面处理的方式比如表面发兰。 关键词:传动轴,零件,刚度,强度,表面发兰
ABSTRACT Through the study of shaft during school and transmission of the system are analyzed and design. Supporting transmission parts called shaft. Axial parts of graduation design is mechanical engineering specialty students complete the teaching plan last a very important practical teaching link is to make the students comprehensive use of basic theory, we learned the basic knowledge and skills to solve major problems within the scope of the engineering technology and a basic training. The student is engaged in technical work related to the development and future career has certain Shaft is composed of the main parts of the machine parts, all of the transmission parts motion (for example: gear, gear, etc.) must be installed in the transmission of power to exercise and shaft transmission, often used in the connection between the transmission and drive. The shaft generally is long, and the high speed, can withstand torque not inherit the moment. Should make the shaft has enough rigidity and high speed, strength calculation, because of the large safety factor, thus make shaft dimension, this paper discusses the transmission technology design methods, and according to the current standard added some way of surface treatment Keywords:Shaft, parts, stiffness, strength, surface flange
传动轴的设计及校核
第一章轻型货车原始数据及设计要求 发动机的输出扭矩:最大扭矩·m/2000r/min;轴距:3300mm;变速器传动比: 五挡1 ,一挡,轮距:前轮1440毫米,后轮1395毫米,载重量2500千克 设计要求: 第二章万向传动轴的结构特点及基本要求 万向传动轴一般是由万向节、传动轴和中间支承组成。主要用于在工作过程中相对位置不节组成。伸缩套能自动调节变速器与驱动桥之间距离的变化。万向节是保证变速器输出轴与驱动桥输入轴两轴线夹角的变化,并实现两轴的等角速传动。一般万向节由十字轴、十字轴承和凸缘叉等组成。 传动轴是一个高转速、少支承的旋转体,因断改变的两根轴间传递转矩和旋转运动。重型载货汽车根据驱动形式的不同选择不同型式的传动轴。一般来讲4×2驱动形式的汽车仅有一根主传动轴。6×4驱动形式的汽车有中间传动轴、主传动轴和中、后桥传动轴。6×6驱动形式的汽车不仅有中间传动轴、主传动轴和中、后桥传动轴,而且还有前桥驱动传动轴。在长轴距车辆的中间传动轴一般设有传动轴中间支承.它是由支承架、轴承和橡胶支承组成。 传动轴是由轴管、伸缩套和万向此它的动平衡是至关重要的。一般传动轴在出厂前都要进行动平衡试验,并在平衡机上进行了调整。因此,一组传动轴是配套出厂的,在使用中就应特别注意。 图 2-1 万向传动装置的工作原理及功用 图 2-2 变速器与驱动桥之间的万向传动装置 基本要求: 1.保证所连接的两根轴相对位置在预计范围内变动时,能可靠地传递动力。 2.保证所连接两轴尽可能等速运转。 3.由于万向节夹角而产生的附加载荷、振动和噪声应在允许范围内。 4.传动效率高,使用寿命长,结构简单,制造方便,维修容易等 第三章轻型货车万向传动轴结构分析及选型 由于货车轴距不算太长,且载重量吨属轻型货车,所以不选中间支承,只选用一根主传动轴,货车发动机一般为前置后驱,由于悬架不断变形,变速器或分动器输出轴轴线之间的相对位置经常变化,根据货车的总体布置要求,将离合器
传动轴和万向节设计-汽车设计课程设计说明书
目录 传动轴与十字轴万向节设计 1.1结构方案选择 (02) 1.2计算传动轴载荷 (03) 1.3传动轴强度校核 (04) 1.4十字轴万向节设计 (04) 1.5传动轴转速校核及安全系数 (07) 1.6参考文献 (09)
1.传动轴与十字轴万向节设计要求 1.1万向传动轴总体概述 万向传动轴是汽车传动系的重要组成部件之一。传动轴选用与设计的合理与否直接影响传动系的传动性能。选用、设计不当会给传动系增添不必要的和设计未能估算在内的附加负荷,可能导致传动系不能正常运转..。 传动轴是将发动机输出的转知经分动器传递给前驱和后驱的传动机构,转速达3000~7000r/min,振动是传动轴总成设计需考虑的首要问题。尽管采取涂层技术来减小滑移阻力,但产生的滑移阻力仍为等速万向节的10~40倍,而滑移阻力将产生振动。为选型设计提供依据,传动轴分为CJ+CJ型、BJ+BJ型(靠花键产生滑移)BJ+DOJ型、BJ+TJ型、BJ+LJ型5种类型。 传动布置型式的选择 万向节传动轴是汽车传动系的重要组成部件之一。传动轴选用与设计布置的合理与否直接影响传动系的传动性能。选用与布置不当会给传动系增添不必要的和设计未能估算在内的附加动负荷,可能导致传动系不能正常运转和早期损坏。 车辆的万向节传动,主要应用于非同心轴间和工作中相对位置不断改变的两轴之间的动力传递。装在变速器输出轴与前后驱动桥之间。变速器的动力输出轴和驱动桥的动力输入轴不在一个平面内。有的装载机在车桥与车架间装有稳定油缸、铰接式装载机在转向时均会使变速箱与驱动桥之间的相对位置和它们的输出、输出入轴之间的夹角不断发生变化。这时常采用一根或多根传动轴、两个或多个十字轴万向节的传动[7]。图2.1为用于汽车变速箱与驱动桥之间的不同万向传动方案。 (a)单轴双万向节式
传动轴设计
德州科技职业学院 毕业设计(论文)题目传动轴的工艺设计 系(部):机电工程系 学生姓名:苗壮青 学号:070201317 班级名称:07机电3班 指导教师:李娟 答辩教师:孙丽华 时间:2010年5月12日
摘要 机械制造工业是在我国国民经济中起着极其重要作用的基础工业。近年来,随着现代科学技术的进步,机械制造工业的面貌发生了深刻的变化,呈现出激烈的国际性竞争的高速发展态势。 机械工业的高速发展,对高职院校培养工程技术人才提出了新的更高的要求。机械制造工艺在机械制造工业中为国民经济各部门和自身的技术进步提供先进的技术、装备,在国民经济中具有重要的地位和作用,应用于各个领域。机械工业的规模和技术水平是衡量国家科技水平和经济实力的重要标志。 机械制造工艺知识具有很强的实践性。因此,本课题的内容重视的是零件的作用,结构和工艺过程的拟制及夹具设计和加工方案的确定。即通过设计及车间调研来更好的体会,加深理解。本课题给出的仅是零件图,真正的设计与加工必须在不断的实践、理论循环中总结。 在研究本课题过程中通过各种渠道搜集了一些与本课题相关的资料。例如:图书查阅、上网搜集、请教老师及和同学之间的讨论。本课题的重点零件的工艺分析和工艺规程制定 关键词:机电一体化,传动轴,零件,刚度,强度
ABSTRACT Mechanical manufacturing industry in the national economy in China is plays an important role in the basic industry.In recent years,along with the development of modern science and technology progress,machinery manufacturing industry,great changes have taken place,the fierce international competition of high-speed development trend. The rapid development of industry,mechanical engineering in higher vocational colleges are put forward new talents of higher requirements. Mechanical manufacturing process in mechanical manufacturing industry for national economic sectors and its technical progress of advanced technology and equipment provided in the national economy,and has an important position and role,applied in various fields.Mechanical industrial scale and technology level of national science and technology level and measure is an important symbol of economic strength. Mechanical manufacturing process knowledge is strong practicality. Therefore,the importance of this topic is part of the content,structure and process of artificial and fixture design and processing of the scheme. Through the investigation and design and workshop,better to deepen understanding.This topic is only part of the design and fabrication,in practice,and to summarize cycle theory. This topic in the research process through various channels and collected the data of topic.Example:the Internet access,collect books, consult teachers and classmates and the discussion between.The key parts of the subject of process analysis and procedure Keywords:mechanical and electrical integration,Shaft,parts,stiffness, strength
机械设计带传动的问题
1.一般带传动的主要失效形式是带的___3________,及带的____6__________。 ①检验;②颤动;③疲劳破坏;④静力拉断;⑤弹性滑动;⑥打滑;⑦磨损 2.V带传动中的弹性滑动____A_______。 A.是不可避免的B.只要外载荷不超过带传动的有效圆周力,就可以避免C.增大包角和提高带与轮之间的摩擦系数就可以避免。 3.带传动限制小带轮直径dmin的目的是_____C___________。 A.减小滑动率ε B.使带传动结构紧凑 C.降低带的弯曲应力 D.降低离心应力 4.带传动中,带速V为什么不宜过低,也不宜过高?一般带速V在什么范围为宜?(5分) 带传动中,带的最大应力发生在_____A___________处。 A.带进入主动轮B.带退出主动轮 C.带进入从动轮D.带退出从动轮 5.选择V带的型号是根据(C )。 A.传递功率B.转速 C. 计算功率和转速D.小带轮直径 6.V带传动中,带在小带轮上的包角 1一般不小于(B )。 A.90°B.120°C.150°D.170° 7.带传动正常工作时,不能保证准确的传动比,是因为。 8.V带传动和平型带传动相比,V带传动的主要优点是 B 。 A.在传递相同功率条件下,传动尺寸小B.传动效率高 C.带的寿命长D.带的价格便宜 9.带张紧的目的是 D 。
A. 减轻带的弹性滑动 B. 提高带的寿命 C. 改变带的运动方向 D. 使带具有一定的初拉力 10.当带有打滑趋势时,带传动的有效拉力达到最大, 而带传动的最大有效拉力决定于?小轮包角、摩擦系数、初拉力三个因素。 11.带传动工作时,设小带轮主动,则带内拉应力的最大值应发生在带 C 。A.进入大带轮处B.离开大带轮处 C. 进入小带轮处D.离开小带轮处 12.带传动中,若V1为主动轮的圆周速度,V为带的运动速度,V2为从动轮的圆周速度,则它们的关系是_D A.V1=V=V2B.V1>V=V2C.V1=V>V2 D.V1>V>V2
传动轴设计指南介绍
奇瑞汽车有限公司 乘研三院底盘部设计指南 编制:梁晋 审核:吕波涛 批准:冯贺平
目录 §1 概述 (2) §1.1万向节和传动轴综述 (2) §1.2万向节的类型及适用范围 (2) §1.3万向节结构及工作原理 (2) §2 设计构想 (8) §2.1设计原则和开发流程 (8) §2.2 基本的设计参数制定 (9) §2.3 台架试验 (25) §3 材料及加工 (26) §4 图纸模式 (27) §4.1 尺寸公差 (27) §4.1 文字说明 (27)
§1 概述 §1.1万向节和传动轴综述 汽车上的万向节传动常由万向节和传动轴组成,主要用来在工作过程中相对位置不断改变的两根轴间传递动力。万向节传动应保证所连接两轴的相对位置在预计范围内变化时,能可靠的传递动力;保证所连接两轴尽可能同步(等转速)运转;允许相邻两轴存在一定的角度;允许存在一定轴向的移动。 §1.2万向节的类型及适用范围 万向节按其在扭转方向上是否由明显的弹性可分为刚性万向节和挠性万向节。刚性万向节又可分为不等速万向节(常用的十字轴式),准等速万向节(双联式、三销轴式等)和等速万向节(球叉式、球笼式等)。等速万向节,其英文名称为Constant Velocity Universal Joint,简称等速节(CVJ)。 CVJ的分类如下(德国分类): Fixed Joint(固定端万向节)——AC:椭圆截面滚道 ——RF: 圆形截面滚道 ——UF:尖拱形截面滚道 Plunging Joint(移动端万向节)——DOJ:双偏置式万向节 ——GI: 三球销式万向节 ——VLJ:斜滚道球笼万向节 以上是乘用车常用等速节的英文及德文缩写,对应着不同的结构与性能,这在下边的章节中会提到。 在发动机前置后轮驱动(或全轮驱动)的汽车上,由于工作时悬架变形,驱动桥主减速器输入轴与变速器(或分动器)输出轴间经常有相对运动,因此普遍采用万向节传动。在转向驱动桥中,由于驱动轮又是转向轮,左右半轴间的夹角随行驶需要而不断变化,这时多采用球叉式和球笼式等速万向节传动。当后驱动桥为独立悬架结构时,也必须采用万向节传动。万向传动装置除用于汽车的传动系外,还可用于动力输出装置和转向操纵机构。因为轿车普遍采用等速万向节,所以本设计指南重点介绍等速节驱动轴。 §1.3万向节结构及工作原理
机械设计基础皮带轮传动
试设计一普通V 带传动,主动轮转速1n =960r/min ,从动轮转速2n =320r/min ,带型为B 型,电动机功率P=4KW ,两班制工作,载荷平稳。 序号 计算项目 计算内容 计算结果 1 计算功率 ==P K P A C 1.2×4KW A K =1.2 C P =4.8KW 2 选择带型 B 型 3 确定带轮 由表10-9确定d1d d1d =140mm 基准直径 ()= -=ε1id d d1d2()02.01140320 960 -?? d2d = 425mm 4 验算带速 100060n d v 1d1?=π= s /m 1000 60960 140???π 因为符合5m/s 〈v =7.04m/s 〈 25m/s , 故符合要求 5 验算带长 初定中心距0a =500mm () ()0 2 d1d2d2d10d0a 4d d 2 d d a 2-+ ++ =πL =()()mm 5004140425242514050022?? ?????-+++?π d L =2000mm =1887.64mm 由表10-2选取d L =2000mm 6 确定中心距 ()2a a d0d 0L L -+≈ =()[]mm 500264.18872000-+ a=556mm =556mm d min 015.0a a L -==(556-0.015×2000)mm=526mm d max 03.0a a L +==(556+0.03×2000)mm=586mm 7 验算小带 1α=180°-57.3°×()d1d2d d -/a 因为1α>120°,
轮包角 =150.63° 故符合要求 8 单根V 带传 据d1d 和1n 查图 1P =1.6kw 递的额定功率 得1P =1.6kw 9 i ≠1时单根 根据带型及i 查表 1P ?=0.3kw V 带的额定功率 10-5得1P ?=0.3kw 增量 10 确定带的根数 查表10-6:a K =0.93 查表10-7:l K =0.98 取Z=3 c P Z =/[(1P +1P ?)a K l K ] =4.8/[(1.6+0.3)×0.93×0.98]=2.77 11 单根V 带的 查表10-1 初拉力 q=0.17kg/m 0F =200.26N 0F =5002c a q 15.2νν+?? ? ????????-??? ??Z P K ={500[(2.5/0.93)-1](04 .738 .4?)+0.17×204.7}N =200.26N 12 作用在轴 02ZF F Q =sin ()21 α= Q F = 上的力 13带轮的结构和 以小带轮为例确定其结构和尺寸 尺寸 由图10-7选定小带轮为实心轮 轮槽尺寸及轮宽按表10-3计算