锂离子电池设计公式
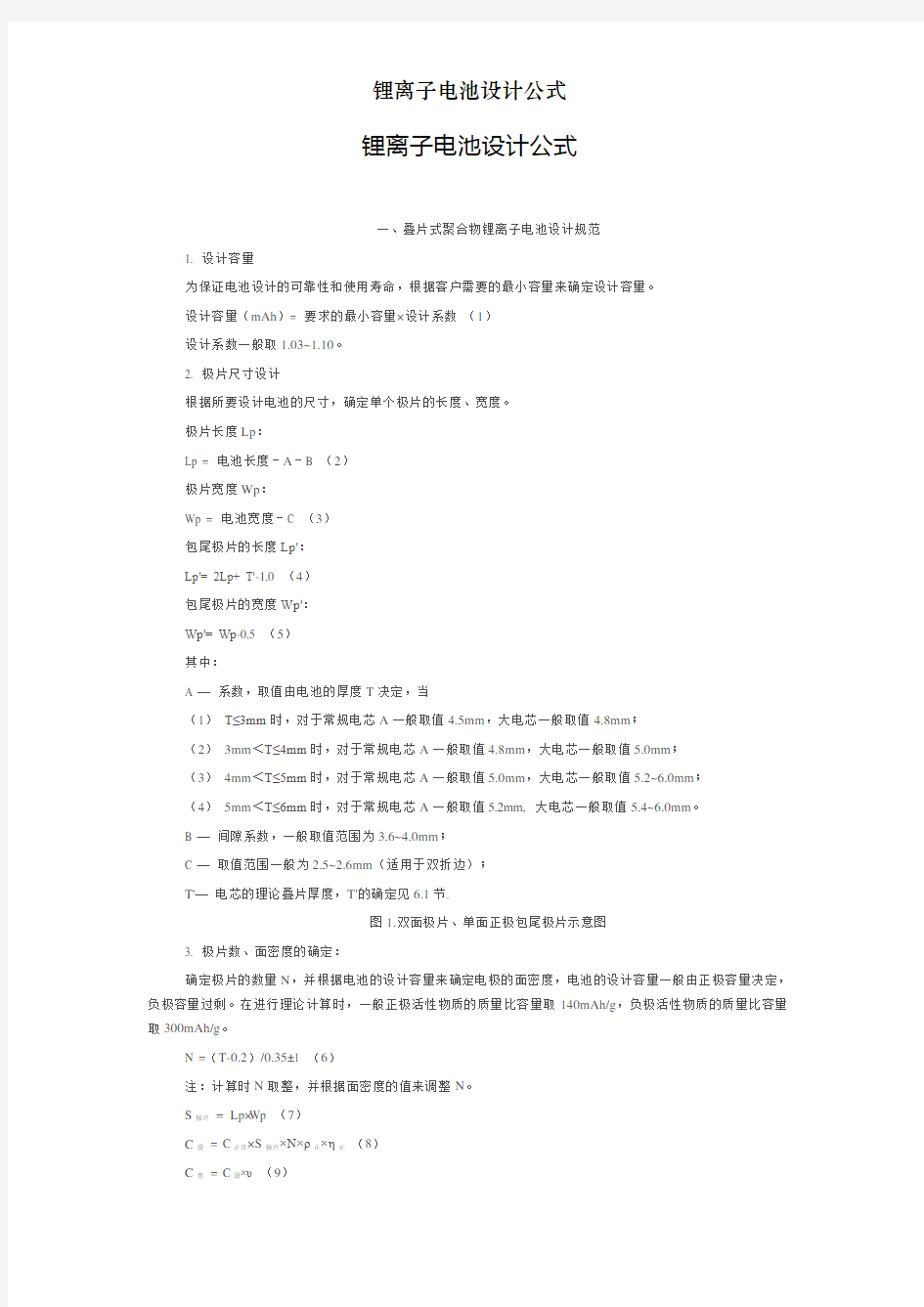

锂离子电池设计公式
一、叠片式聚合物锂离子电池设计规范
1. 设计容量
为保证电池设计的可靠性和使用寿命,根据客户需要的最小容量来确定设计容量。
设计容量(mAh)= 要求的最小容量×设计系数(1)
设计系数一般取1.03~1.10。
2. 极片尺寸设计
根据所要设计电池的尺寸,确定单个极片的长度、宽度。
极片长度Lp:
Lp = 电池长度-A-B (2)
极片宽度Wp:
Wp = 电池宽度-C (3)
包尾极片的长度Lp′:
Lp′= 2Lp+ T'-1.0 (4)
包尾极片的宽度Wp′:
Wp′= Wp-0.5 (5)
其中:
A —系数,取值由电池的厚度T决定,当
(1)T≤3mm时,对于常规电芯A一般取值4.5mm,大电芯一般取值4.8mm;
(2)3mm<T≤4mm时,对于常规电芯A一般取值4.8mm,大电芯一般取值5.0mm;
(3)4mm<T≤5mm时,对于常规电芯A一般取值5.0mm,大电芯一般取值5.2~6.0mm;
(4)5mm<T≤6mm时,对于常规电芯A一般取值5.2mm, 大电芯一般取值5.4~6.0mm。
B —间隙系数,一般取值范围为3.6~4.0mm;
C —取值范围一般为2.5~2.6mm(适用于双折边);
T'—电芯的理论叠片厚度,T'的确定见6.1节.
图1.双面极片、单面正极包尾极片示意图
3. 极片数、面密度的确定:
确定极片的数量N,并根据电池的设计容量来确定电极的面密度,电池的设计容量一般由正极容量决定,负极容量过剩。在进行理论计算时,一般正极活性物质的质量比容量取140mAh/g,负极活性物质的质量比容量取300mAh/g。
N =(T-0.2)/0.35±1 (6)
注:计算时N取整,并根据面密度的值来调整N。
S极片= Lp×Wp (7)
C设= C正比×S极片×N×ρ正×η正(8)
C负= C设×υ (9)
= C负比×S极片×N×ρ负×η负(10)
其中:
S极片—单个极片的面积;
C正比—正极活性物质的质量比容量,一般取值140mAh/g;
η正—正极活性物质的百分含量;
ρ正—正极极片的双面面密度(g/m2);
C负—负极的设计容量;
υ —负极容量过剩系数,一般常规电池取值1.00~1.06;DVD电池以及容量大于2000mAh的取值1.05~1.12;
C负比—负极活性物质的质量比容量,一般取值300mAh/g;
η负—负极活性物质的百分含量;
ρ负—负极极片的双面面密度(g/m2);
4. 极片厚度的确定:
为保证极片中活性物质的性能发挥,涂布后的极片要进行适当轧片,一般根据材料的压实密度来确定不同面密度的极片的轧片厚度。
表1. 不同材料的压实密度
5. 隔膜尺寸的确定
现在使用的隔膜的规格一般为厚度0.020mm、0.022mm的,隔膜的长度Ls、宽度Lt由以下公式确定:Ls = (Wp+0.5)×(2×N+2) (11)
Lt = Lp+Ψ (12)
其中:
Ψ —隔膜宽超出极片的长度,范围为2.0~4.0mm,一般取3.0mm.
6. 包装袋的设计
6.1槽深设计
根据叠片后电芯的厚度T'确定铝塑包装膜的槽深H,为避免铝塑包装膜的二次拉伸,冲槽深度原则上等于叠片后电芯的厚度。
T'= T正+T负+T隔膜(13)
= h正×N正+2h单+h负×N负+h隔膜×(N负+1)×2 (14)
H = T'±0.1 (15)
注:以上计算针对单冲槽槽深设计,目前只能满足冲槽深度≤4.2mm的,对于4.2~5.0mm槽深的要依据生产上所能达到的实际尺寸。
其中:
T正—正极片的总厚度;
T负—负极片的总厚度;
T隔膜—叠成电芯后隔膜的总厚度,隔膜的厚度一般为0.020/0.022mm;h正—正极片(双面)轧片后的厚度;
h单—正极单面极片轧片后的厚度;
h负—负极片(双面)轧片后的厚度;
N负—负极片的数量;
h隔膜—隔膜的厚度.
6.2 包装袋膜腔长度的确定
膜腔的长度与电芯的长度有以下关系:
膜腔长度= 电芯长度-A (16)
注:参数A的确定参见公式(2).
6.3 包装袋膜腔宽度的确定
膜腔的宽度与电芯的宽度有以下关系:
膜腔宽度= 电芯宽度-B (17)
B—系数,一般取值1.0~1.2mm.
7. 电解液量的确定
根据电池的设计容量确定电解液的加入量M
M = C设÷ξ (18)
其中:
ξ—一般为250~300,单位mAh/g.
锂离子电池设计原理教材
锂离子电池原理及设计教材 原理篇 电池原材料 化工类材料:正极:钴酸锂、锰酸锂、镍酸锂、磷酸铁锂、三元材料 负极:人造石墨、中间相碳微球(沥青基)、针状焦、改性天然石墨 其他:隔膜、电解液、导电剂、PVDF、NMP、草酸、SBR、CMC、高温胶纸、铜箔、铝箔等 五金类材料:钢壳、铝壳、盖帽、隔圈、铝带、镍带、铝镍复合带等、铝塑膜等电池原材料是决定电池性能的最重要的因素,电池性能的提升归根结底来自于电池材料的优化及更新。 锂离子电池反应机理 锂离子电芯的反应机理是随着充放电的进行,锂离子在正负极之间嵌入脱出,往返穿梭电芯内部而没有金属锂的存在,因此锂离子电芯更加安全稳其反应示意图如下所示: 电芯的正极是LiCoO2加导电剂和粘合剂,涂在铝箔上形成正极板,负极是层状石墨加导电剂及粘合剂涂在铜箔基带上,目前比较先进的负极层状石墨颗粒已采用纳米碳。 根据上述的反应机理,正极采用LiCoO2、LiNiO2、LiMn2O2等,其中LiCoO2是一种层状结构很稳定的晶型,但当从LiCoO2拿走XLi后,其结构可能发生变化,但是否发生变化取决于X的大小。通过研究发现当X>0.5时Li(1-X)CoO2的结构表现为极其不稳定,会发生晶型瘫塌,其外部表现为电芯的电压及安全性能。所以电芯在使用过程中应通过限制充电电压来控制Li1-XCoO2中的X值,一般充电电压不大于4.2V。那么X小于0.5 ,这时Li1-XCoO2的晶型仍是稳定的。负极C6其本身有自己的特点,当第一次化成后,正极LiCoO2中的Li被充到负极C6中,当放电时Li回到正极LiCoO2中,但化成之后必须有一部分Li 留在负极C6中,以保证下次充放电Li的正常嵌入,否则电芯的寿命很短,为了保证有一部分Li留在负极C6中,一般通过限制放电下限电压来实现。所以锂电芯的安全充电上限电压≤4 .2V,放电下限电压≥2.5V。 锂离子电池的主要制造过程 Li-ion电池的工艺技术比较严格、复杂,这里只能简单介绍一下其中的几个主要工序。
锂电池的安全性设计参考文本
锂电池的安全性设计参考 文本 In The Actual Work Production Management, In Order To Ensure The Smooth Progress Of The Process, And Consider The Relationship Between Each Link, The Specific Requirements Of Each Link To Achieve Risk Control And Planning 某某管理中心 XX年XX月
锂电池的安全性设计参考文本 使用指引:此安全管理资料应用在实际工作生产管理中为了保障过程顺利推进,同时考虑各个环节之间的关系,每个环节实现的具体要求而进行的风险控制与规划,并将危害降低到最小,文档经过下载可进行自定义修改,请根据实际需求进行调整与使用。 为了避免因使用不当造成电池过放电或者过充电,在 单体锂离子电池内设有三重保护机构。一是采用开关元 件,当电池内的温度上升时,它的阻值随之上升,当温度 过高时,会自动停止供电;二是选择适当的隔板材料,当 温度上升到一定数值时,隔板上的微米级微孔会自动溶解 掉,从而使锂离子不能通过,电池内部反应停止;三是设 置安全阀(就是电池顶部的放气孔),电池内部压力上升 到一定数值时,安全阀自动打开,保证电池的使用安全 性。 有时,电池本身虽然有安全控制措施,但是因为某些 原因造成控制失灵,缺少安全阀或者气体来不及通过安全 阀释放,电池内压便会急剧上升而引起爆炸。
一般情况下,锂离子电池储存的总能量和其安全性是成反比的,随着电池容量的增加,电池体积也在增加,其散热性能变差,出事故的可能性将大幅增加。对于手机用锂离子电池,基本要求是发生安全事故的概率要小于百万分之一,这也是社会公众所能接受的最低标准。而对于大容量锂离子电池,特别是汽车等用大容量锂离子电池,采用强制散热尤为重要。 选择更安全的电极材料,选择锰酸锂材料,在分子结构方面保证了在满电状态,正极的锂离子已经完全嵌入到负极炭孔中,从根本上避免了枝晶的产生。同时锰酸锂稳固的结构,使其氧化性能远远低于钴酸锂,分解温度超过钴酸锂100℃,即使由于外力发生内部短路(针刺),外部短路,过充电时,也完全能够避免了由于析出金属锂引发燃烧、爆炸的危险。 另外,采用锰酸锂材料还可以大幅度降低成本。
锂离子电池设计总结
锂离子电池设计总结 (一)液锂电池设计 (1)根据壳子推算卷芯 1、核算容量:(设计最低容量= average * 0.935) 2、极片宽度: 隔膜宽度= 壳子高- 0.6 - 2 - 0.3 - 0.5 图纸高壳子底厚盖板厚绝缘垫厚余量 负极片宽度= 隔膜纸宽度- 2mm 正极片宽度= 负极片宽度- (1~2mm) 注:核算后正负极片宽度要去查找分切刀,最好有对应分切刀;箔材的选择也要依分切刀而定。比如:40mm的分切刀,可以一次分裁8片,则箔材尺寸应该为40*8+(10~15余量)=330~335mm,若没有合适的也可以选择40*7+(10~15mm)的箔材。 3、卷芯宽度: 卷芯设计宽度= 壳子宽度- 0.6 -(0.5~1.5) 图纸宽度两层壳壁厚余量 4、卷芯厚度: (1)卷芯设计厚度= 壳子厚度- 0.6 - 0.6 图纸厚度两层壳壁厚余量 (2)卷芯设计厚度= (规格厚度–0.2 –0.6)/ 1.08 规格书厚度max 余量两层壳壁厚膨胀系数 5、卷尺宽度: 卷尺= 卷芯宽–卷芯厚–卷尺厚(0.5mm)–(1.5~2.5)余量 6、最后根据(2、3、4)进行调整、确认。 7、估算卷芯/电芯最终尺寸 卷芯厚度= 正极片厚+ 负极片厚+ (隔膜厚*2) 卷芯宽度= 卷尺宽+ 卷尺厚+ 卷芯厚+(1~2.5)余量 最终电芯厚度= 卷芯厚度* 1.08 + 壳子厚度+(0.2~0.5) 层数单层厚度卷芯厚卷芯厚* 1.08 +(0.3~0.4)≤规格要求 (二)电池设计注意事项: 1、极耳距极片底部≤极片宽度*1/4 2、极耳外露≥12mm~15mm 负极耳外露:6~10mm 3、小隔膜= 加垫隔膜处光泊区尺寸+(2~3mm) 4、壳子底部铝镍复合带尺寸: 4mm * 13mm * 0.1mm (当壳子底部宽w ≥7mm时) 3mm * 13mm * 0.1mm (当壳子底部宽w <7mm时) 5、极片称重按涂布时箔材和敷料计算
叠片式聚合物锂离子电池设计规范
一、叠片式聚合物锂离子电池设计规范 1. 设计容量 为保证电池设计的可靠性和使用寿命,根据客户需要的最小容量来确定设计容量。 设计容量(mAh)= 要求的最小容量×设计系数(1) 设计系数一般取1.03~1.10。 2. 极片尺寸设计 根据所要设计电池的尺寸,确定单个极片的长度、宽度。 极片长度Lp: Lp = 电池长度-A-B (2) 极片宽度Wp: Wp = 电池宽度-C (3) 包尾极片的长度Lp′: Lp′= 2Lp+ T'-1.0 (4) 包尾极片的宽度Wp′: Wp′= Wp-0.5 (5) 其中: A —系数,取值由电池的厚度T决定,当 (1)T≤3mm时,对于常规电芯A一般取值4.5mm,大电芯一般取值4.8mm; (2) 3mm<T≤4mm时,对于常规电芯A一般取值4.8mm,大电芯一般取值5.0mm; (3) 4mm<T≤5mm时,对于常规电芯A一般取值5.0mm,大电芯一般取值5.2~6.0mm; (4) 5mm<T≤6mm时,对于常规电芯A一般取值5.2mm, 大电芯一般取值5.4~6.0mm。
B —间隙系数,一般取值范围为3.6~4.0mm; C —取值范围一般为2.5~2.6mm(适用于双折边); T'—电芯的理论叠片厚度,T'的确定见6.1节. 图1.双面极片、单面正极包尾极片示意图 3. 极片数、面密度的确定: 确定极片的数量N,并根据电池的设计容量来确定电极的面密度,电池的设计容量一般由正极容量决定,负极容量过剩。在进行理论计算时,一般正极活性物质的质量比容量取140mAh/g,负极活性物质的质量比容量取300mAh/g。 N =(T-0.2)/0.35±1(6) 注:计算时N取整,并根据面密度的值来调整N。 S 极片 = Lp×Wp(7) C 设 = C 正比 ×S 极片 ×N×ρ 正 ×η 正 (8) C 负 = C 设 ×υ(9) = C 负比×S 极片 ×N×ρ 负 ×η 负 (10) 其中: S 极片 —单个极片的面积; C 正比 —正极活性物质的质量比容量,一般取值140mAh/g; η正—正极活性物质的百分含量; ρ正—正极极片的双面面密度(g/m2); C 负 —负极的设计容量; υ—负极容量过剩系数,一般常规电池取值1.00~1.06;DVD电池以及容量大于2000mAh的取值1.05~1.12; C 负比 —负极活性物质的质量比容量,一般取值300mAh/g;
锂离子电池安全性
车用锂离子动力电池系统的安全性剖析 国家大力支持以电动汽车为主的新能源汽车新兴产业。然而以热失控为特征的锂离子电池系统的安全性事故时有发生,困扰着电动汽车的发展。动力电池安全性事故的常见形式及成因是什么?又该采取怎样的防范措施?小编带你一览要点。 1 动力电池安全性问题 锂离子动力电池事故主要表现为因热失控带来的起火燃烧。如表1和图1 所示。 表1 近年发生的锂离子动力电池事故 图1 近年来部分锂离子动力电池事故 锂离子动力电池系统安全性问题表现为3个层次(图2)。 1)电池系统安全性的“演变”。即电池系统长期老化——“演化”(事故1、2、3、5、7)和突发事件造成电池系统损坏——“突变”(事故4、6)。 2)“触发”——锂离子动力电池从正常工作到发生热失控与起火燃烧的转折点。 3)“扩展”——热失控带来的向周围传播的次生危害。
图2 动力电池系统安全性问题的层次 2 动力电池安全性演变 2.1 “演化”与“突变” 电池系统长期老化带来的可靠性降低,演化耗时长,可以通过检测电池系统的老化程度来评估电池系统安全性的变化;相比而言安全性突变难以预测,但是可以通过既有事故的形式来改进电池系统的设计。 2.2 安全性演化机理 电池系统任何部件的老化都可能带来安全事故的触发,如事故1、7。除此之外,电池本身的安全性演化主要表现为内短路的发展。电池内部的金属枝晶生长是造成内短路的主要原因之一。值得一提的是,老化电池的能量密度降低,热失控造成的危害可能会降低;另一方面老化电池更容易发生热失控。 图3 锂离子电池内部金属枝晶的生长与隔膜的刺穿
3 电池安全事故触发 3.1 热失控机理 经过演变过程,电池事故将会进入“触发”阶段。一般在这之后,电池内部的能量将会在瞬间集中释放造成热失控,引发冒烟、起火与爆炸等现象。当然电池安全事故中,也可能不发生热失控,热失控后的电池不一定会同时发生冒烟、起火与爆炸,也可能都不发生,这取决于电池材料发生热失控的机理。 图4、图5与表2展示了某款具有三元正极/PE基质的陶瓷隔膜/石墨负极的25 A·h锂离子动力电池的热失控机理。热失控过程分为了7个阶段。 图4 某款三元锂离子动力电池热失控实验数据(实验仪器为大型加速绝热量热仪,EV-ARC) 图5 某款三元锂离子动力电池热失控不同阶段的机理 表2 某款锂离子动力电池热失控的分阶段特征与机理
18650锂电池生产工艺设计2
18650锂电芯诞生全过程揭秘(图) 2014-12-01 10:47:42来源:充电头 导读: 18650是目前最常见的锂电封装方式,无论是当下最流行的三元材料,还是国家力推的磷酸铁锂,以及尚未普及的钛酸锂,均有18650的规格。18650型电芯,采用Cylindrical圆柱形封装方式,这种电芯直径18mm,长度65mm,广泛应用于充电宝、电动车、笔记本、强光手电筒等领域。 OFweek锂电网讯:锂电池是目前数码领域使用最多的电池。其最突出的优点是能量密度高,适用于非常注重体积、便携的数码产品。同时,相对于以往的干电池,锂离子电池可以循环利用,在环保方面也有优势。锂离子电池的正负极材料都可以吸收、释放锂离子。但是锂离子在正极和负极中的化学势能有所不同。负极中的锂离子化学势能高,正极中的锂离子化学势能低。锂离子放电时,负极中存储的锂离子释放出来,被正极所吸收。由于负极中锂离子的化学势能高于正极,这部分势能差就以电能的形式释放出来。充电过程则是上述过程的逆转,将正极中的锂离子释放到负极中。由于这种锂离子在正负极中的来回迁移,锂离子电池又被称为摇椅电池。 18650是目前最常见的锂电封装方式,无论是当下最流行的三元材料,还是国家力推的磷酸铁锂,以及尚未普及的钛酸锂,均有18650的规格。18650型电芯,采用Cylindrical圆柱形封装方式,这种电芯直径18mm,长度65mm,广泛应用于充电宝、电动车、笔记本、强光手电筒等领域,这类封装的好处是规格统一,方便自动化、规模化生产,具有机械强度高、耐冲击性强、良品率高等特点;此外还有Prismatic方形软包封装,常见于手机和平板电脑,这类封装最直接的好处是轻薄,体积小,便携。 在笔记本电脑时代,18650电芯还只是数码产品的幕后英雄。随着智能手机和平板等智能设备的普及,移动电源成为了人们出行必不可少的装备,18650也得以开始从幕后走向前台,被大众所熟知。那么,看似简单的18650电芯是如何诞生?它有什么秘密呢?接下来,让我们一起去探索它的诞生过程。近日笔者有幸进入东莞一家电芯厂拜访学习,将从涂布、组装、测试三方面图文并茂,为大家介绍18650电芯的诞生过程。 电芯的生产过程一:涂布
锂离子电池安全的设计与维护
040 The Design and Preservation of the Safety of Lithium-ion Battery LiFePO4 LiCoO2 PTC LiFePO4 Separator has much influence on the electrical properties and safety of the Cell. Microporous poly- meric membranes must be mechanically strong enough to keep the structure integrity while shutdown activated. Inorganic composite membranes show a higher ability than Microporous polymeric mem- branes to withstand overcharge. Two types of overcharge protector are introduced and each of these has a specific redox potential range that suitable for LiFePO4 and LiCoO2 respectively. Phosphor contented fire-retardant additive prevents the cell from overheating. A carbon and polymer composite with PTC properties is introduced into the cathode preparation. When the cell is heated over the melting point of the polymer, the resistance of the cathode electrode increases drastically and cut-off the current through it. That prevents the cell from thermal runaway. LiFePO4 has the character of overcharge protector too. /Key Words (Thermal Runaway) (Separator) (Overcharge Protector) (Fire-retardant Additive) (PTC Cathode) J. J. Lee1 C. R. Yang2 (MCL/ITRI) 1 2 60 70 1989 Li/MoS2 (1) 1990~1991 Nagoura SONY Moli
锂电池生产厂易忽视的安全问题及安全对策措施
锂电池生产厂易忽视的安全问题及安全对策措 施 公司标准化编码 [QQX96QT-XQQB89Q8-NQQJ6Q8-MQM9N]
锂电池生产厂易忽视的安全问题 主要危险因素及相应的安全对策措施 近来,在工作中发现,我国锂电池生产企业对锂电池生产中的安全问题认识不足,主要表现在: ①电池液的毒性认识不足,许多企业不知道电池液是有毒的; ②对锂电池的火灾、爆炸危险性认识不足。下面介绍并分析锂电池生产、储存过程中 的毒性危险和火灾、爆炸危险性。 1、中毒危险电池液中一般含有六氟磷酸锂以及作为溶剂使用的碳酸二甲酯、碳酸甲乙酯、碳酸二乙酯、碳酸乙烯酯、碳酸丙烯酯。六氟磷酸锂是有毒物质,而上述碳酸酯类物质化学性质则比较稳定,没有被列入有毒物质类,但是可燃。六氟磷酸锂是电池液中 的重要成分,国内及一些国外出品的六氟磷酸锂没有说明其毒性,但据国际知名的 sigma-aldrich(西格玛公司)制定的六氟磷酸锂《化学品安全技术说明书》(CSDS),说 明了其毒性。六氟磷酸锂的性质简述如下:分子式:LiPF6;燃烧性:不燃(0);毒性:中等(2);剌激性:中等(2);化学活性:低(1);慢性影响:中等(2);TLV-TWA:m3(ACGIH)。括号 内的数字表示分级,从0到4共分5级。 TLV-TWA是美国卫生医师协会推荐的时间加权平均浓度的最高允许值。六氟磷酸锂:白色粉末,吸湿性强,遇水易分解;进入体内可损害健康,多次接触可产生累积的毒性效应,呼吸道、眼、皮肤可受到损伤。一些国内企业出品的六氟磷酸锂,产品说明中注明 含氟化氢(也称为氢氟酸)≤10-4。氟化氢为高毒物质,具有强烈的腐蚀性,损伤呼吸 道、眼、皮肤,可引起支气管炎和肺炎,吸收后可产生全身的毒作用。六氟磷酸锂分解 后的产物是高毒性的,应引起注意。韩国三星公司电解液包装桶上标签注明其应在30℃
锂离子电池组安全设计指南 编制说明
《锂离子电池组安全设计指南标准》 编制说明 一、工作简况 本标准制定任务来源于国标委计划 项目计划发布文件号:国标委综合〔2016〕89号 计划代号:20162475-T-339 本标准由中华人民共和国工业和信息化部提出。 本标准由中国电子技术标准化研究院归口。 本标准起草单位:中国电子技术标准化研究院、×××××××、等。 主要工作过程如下: (1)2015年3月,成立本标准的编制工作小组,着手研究本标准的制定工作。 (2)2015年7月,完成本标准的起草项目建议书和本标准草案稿,申请立项。 (3)2016年12月,国标委下达计划。 (4)2017年1月--5月,查找相关标准和技术资料,进一步完善本标准的草案稿。 (5)2017年6月,编制组第1次工作会议,讨论形成本标准的正式草稿。 (6)2017年9月,标准编制组进行第2次征求意见,起草组处理反馈意见形成本标准的征求意见1稿。 (7)2018年3月,标准编制组第2次工作会议,讨论形成本标准的征求意见2稿。 期间该标准在锂离子电池安全标准特别工作组内广泛征求意见,对标准的编辑性、技术性内容询问相关企业、认证机构及实验室的建议,并对其进行了汇总分析。标准编制组成员分工进行试验验证。 二、标准编制原则和确定主要内容的论据及解决的主要问题 本标准按照GB/T 1.1-2009给出的规则起草。 本标准适用于锂离子电池组的设计,提供了在设计锂离子电池组时涉及的与
电池组安全特性相关的指导,从电池、保护电路、材料与部件、热设计、防火及安装等方面给出了提升产品安全特性的建议,以指导研发设计人员注重关键控制点,保证锂离子电池组的安全性。 三、知识产权情况说明 无 四、产业化情况、推广应用论证和预期达到的经济效果 锂离子电池作为供电电源,已广泛应用于手机、笔记本电脑等便携式电子产品领域的同时,在动力、储能领域的发展迅速。锂离子电池能量密度高、无污染、自放电率低、无记忆效应、充放电速度快等优越性能得到业界认可。从2008年起,我国已经成为全球最大的锂离子电池生产国和消费国。 锂离子电池是一种化学能源,本身的化学特性和体系组成决定了锂离子电池的潜在危险性。在锂离子电池的运输、存储、使用和回收过程中,在外部因素,如高温、过充、过放、短路等条件下,会引发安全问题,如电池漏液、起火、甚至爆炸。锂离子电池一旦发生安全问题,很有可能会直接危害到人身安全。制定、发布、实施相关安全标准有利于促进锂离子电池产业的健康持续发展。 锂离子电池不能单独作为电源使用,必须安装保护电路、保护装置等,以电池组的形式应用。但在电池组的生产过程中,对安全有影响的关键点没有被厂家重视,如保护电路设计不全,电池匹配性差,内部配线不合理等,一些电池组生产厂家为了节省成本和一味追求电性能,尽量节省和压缩原材料,如不使用过热断路装置、阻燃材料不达标等,这些都会降低电池的安全性。 制定锂离子电池组的安全设计的相关标准,不仅能够给设计人员提供专业的指导,提高锂离子电池组的安全性,从而保护消费者人身和财产的安全,同时对锂离子电池产业的健康有序发展具有积极意义。该国家标准实施之后,将对后续的合格评定和市场准入提供重要的参考依据,对提高相应产品安全质量水平有着重要的意义。 五、采用国际标准和国外先进标准情况 无 六、与现行相关法律、法规、规章及相关标准的协调性 该标准符合现行法律法规,与相关标准相协调。
卷绕式锂离子电池设计规范
卷绕式锂离子电池设计规范 一、观察给定型号和客户需求 1、型号制定了电池的尺寸(以063048为例,尺寸为6.0×30×48mm) 2、客户要求的容量和电池的放电类别(动力型、高温型、普通型),通常而言电 池所能达到的容量一般为普通型>高温型>动力型(以便确定所需要的材料) 3、材料的选用: 3.1容量≥1000mAh的型号,如果客户无容量或高温要求的用正极CN55系列 3.2有高温要求的型号,正极材料必须使用Co系列,电解液必须用高温电解液 二、卷芯设计 1、容量设计 根据客户要求的最小容量来确定设计容量。 设计容量(mAh)= 要求的最小容量×设计系数=(长×2-刮粉)×宽÷10000×面密度×理论克容量 注:设计系数: 标称容量≤200mAh设计系数一般取1.10~1.20; 标称容量200<C≤350mAh设计系数一般取1.08±0.02; 标称容量C>350mAh设计系数一般取1.07±0.02。 2、卷针的设计 2.1 卷针的宽度 Wj=电芯的宽度-卷针厚度-电芯的厚度-1.7(根据实际情况而定) 2.2 卷针厚度 Tj由卷针的宽度决定,具体见卷针统计表。
3、包装膜尺寸设计 3.1包装膜膜腔长度的确定: 膜腔长度=成品高-顶封宽度(5mm) 3.2包装膜膜腔长度的确定: 膜腔宽度=成品宽-1.2mm 3.3 槽深的设计: 槽深H与电芯厚度的关系如下:H = T-α 其中: T —电芯的厚度; α—当型号为双坑电池时,α取0.2 当型号为单坑电池时,α取-0.2 3.4 包装袋长、宽尺寸的确定: 3.4.1 包装袋宽度: a. 厚度≤5mm的电池铝塑膜宽度为电池本体宽度+(45~50mm),取代5mm 的整数倍为规格; b. 厚度﹥5mm的电池铝塑膜宽度为电池本体宽度+(55~60mm),取代5mm 的整数倍为规格; 3.4.2包装袋长度: 铝塑膜长度=成品电池长度×2+10mm 5、极片的设计: 5.1隔膜宽度=卷芯高度=电芯高度-5mm,(客户容量要求高的小型号电池或极片较 宽的各别型号除外);
锂离子电池充放电安全检测设计
锂离子电池充放电安全检测设计 手机的锂离子电池充电安全性日益受到消费者重视,因此充电器制造商在设计产品时,须掌握锂离子电池的相关规格和特性,并使用具备完善电池检测及保护功能的充电芯片,以降低过电流、过电压或过温等状况所造成的危险。 随着科技进步、生活质量提升,电子产品的踪迹到处可见,其中又以手机为人类生活中不可或缺的必需品。不论是早期黑金刚手机或现今功能强大的智能手机,皆需要电源才能运作。 早期手机的电池主要有二种,一是镍氢、镍镉电池,二是锂离子电池,但现在使用镍氢、镍镉电池来做为电源的手机,已经是非常的少见,绝大部分都是使用锂离子电池,尤其消费者希望手机待机时间更长,且体积要更小,所以镍氢、镍镉电池已经慢慢不能符合消费者的期望而被淘汰。虽然镍氢、镍镉电池在价格以及替代电池取得的便利性优于锂离子电池,在其他电子产品上仍旧可看到镍氢、镍镉电池的踪迹;但是,在体积、重量及容量方面,镍氢、镍镉电池皆不如锂离子电池,所以现今标榜着轻薄短小的电子产品,几乎都是使用锂离子电池。 智能型手机因其功能强大、屏幕耗电量大,更是需要电池容量大及电力更耐久的锂离子电池。当手机电池电量不足时,使用者通常会以充电器或搭配一组移动电源随时对电池进行充电。 体积/容量兼具锂离子电池为电子产品首选 充电电池依其材质的不同可分为四类:铅酸电池、镍镉电池、镍氢电池和锂离子电池。
表1 充电电池比较表 由表1优缺点看来,镍镉、镍氢及锂离子电池较适合使用在电子产品上;而锂离子电池无论是在体积、重量及容量(电子产品的使用时间)较优于镍镉、镍氢电池,也无记忆效应的问题,所以锂离子电池在电子产品使用上似乎方便许多。 延长使用寿命锂离子电池充/放电压成关键 一般来说,锂离子电池会有电性安全的范围限制。由于锂离子电池的特性,当电池电压在充电时上升到最高设定电压后,要立即停止充电,避免电池因过充电造成电池损毁而产生危险;电池供电(放电)时,电池电压如果降至最低设定电压以下便要停止放电,避免因过放电而降低使用寿命。 此外,为确保电池使用上的安全,锂离子电池还必须要加装短路保护,以避免发生危险;即使大多数的锂离子电池都有加装保护电路,然而在选择优质的充电器或移动电源时,这仍然是一项重要的考量因素。
锂电池的安全性设计正式版
Through the reasonable organization of the production process, effective use of production resources to carry out production activities, to achieve the desired goal. 锂电池的安全性设计正式 版
锂电池的安全性设计正式版 下载提示:此安全管理资料适用于生产计划、生产组织以及生产控制环境中,通过合理组织生产过程,有效利用生产资源,经济合理地进行生产活动,以达到预期的生产目标和实现管理工作结果的把控。文档可以直接使用,也可根据实际需要修订后使用。 为了避免因使用不当造成电池过放电或者过充电,在单体锂离子电池内设有三重保护机构。一是采用开关元件,当电池内的温度上升时,它的阻值随之上升,当温度过高时,会自动停止供电;二是选择适当的隔板材料,当温度上升到一定数值时,隔板上的微米级微孔会自动溶解掉,从而使锂离子不能通过,电池内部反应停止;三是设置安全阀(就是电池顶部的放气孔),电池内部压力上升到一定数值时,安全阀自动打开,保证电池的使用安全性。
有时,电池本身虽然有安全控制措施,但是因为某些原因造成控制失灵,缺少安全阀或者气体来不及通过安全阀释放,电池内压便会急剧上升而引起爆炸。 一般情况下,锂离子电池储存的总能量和其安全性是成反比的,随着电池容量的增加,电池体积也在增加,其散热性能变差,出事故的可能性将大幅增加。对于手机用锂离子电池,基本要求是发生安全事故的概率要小于百万分之一,这也是社会公众所能接受的最低标准。而对于大容量锂离子电池,特别是汽车等用大容量锂离子电池,采用强制散热尤为重要。 选择更安全的电极材料,选择锰酸锂材料,在分子结构方面保证了在满电状
锂离子电池设计公式
锂离子电池设计公式 一、叠片式聚合物锂离子电池设计规范 1.设计容量 为保证电池设计的可靠性和使用寿命,根据客户需要的最小容量来确定设计容量。 设计容量(mAh)=要求的最小容量 x设计系数(1) 设计系数一般取 1.03?1.10。 2.极片尺寸设计 根据所要设计电池的尺寸,确定单个极片的长度、宽度。 极片长度Lp : Lp =电池长度—A -B (2) 极片宽度Wp : Wp =电池宽度—C (3) 包尾极片的长度 Lp': Lp ' = 2Lp+ T1.0 (4) 包尾极片的宽度 Wp : Wp = Wp0.5 (5) 其中: A —系数,取值由电池的厚度T决定,当 (1) T<3mm时,对于常规电芯 A 一般取值4.5mm,大电芯一般取值 4.8mm; (2) 3mm < T<4mm时,对于常规电芯 A 一般取值 4.8mm,大电芯一般取值 5.0mm ; (3) 4mm < T<5mm时,对于常规电芯 A 一般取值 5.0mm,大电芯一般取值 5.2~6.0mm ; (4) 5mm < T<6mm时,对于常规电芯 A 一般取值 5.2mm, 大电芯一般取值 5.4~6.0mm。 B —间隙系数,一般取值范围为 3.6?4.0mm ; C —取值范围一般为 2.5?2.6mm (适用于双折边); T'—电芯的理论叠片厚度,T'的确定见6.1节. 图1.双面极片、单面正极包尾极片示意图 3.极片数、面密度的确定: 确定极片的数量 N,并根据电池的设计容量来确定电极的面密度,电池的设计容量一般由正极容量决定,负极容量过剩。在进行理论计算时,一般正极活性物质的质量比容量取140mAh/g,负极活性物质的质量比容量取 300mAh/g。 N = (T-0.2 ) /0.35 ± (6) 注:计算时N取整,并根据面密度的值来调整N。 S 极片=Lp XWp ( 7) C 设=C 正比xS 极片x NXpE X TJE ( 8)
锂电池的安全性设计
锂电池的安全性设计为了避免因使用不当造成电池过放电或者过充电,在单体锂离子 电池内设有三重保护机构。一是采用开关元件,当电池内的温度上 升时,它的阻值随之上升,当温度过高时,会自动停止供电;二是 选择适当的隔板材料,当温度上升到一定数值时,隔板上的微米级 微孔会自动溶解掉,从而使锂离子不能通过,电池内部反应停止; 三是设置安全阀(就是电池顶部的放气孔),电池内部压力上升到一定数值时,安全阀自动打开,保证电池的使用安全性。 有时,电池本身虽然有安全控制措施,但是因为某些原因造成 控制失灵,缺少安全阀或者气体来不及通过安全阀释放,电池内压 便会急剧上升而引起爆炸。 一般情况下,锂离子电池储存的总能量和其安全性是成反比的,随着电池容量的增加,电池体积也在增加,其散热性能变差,出事 故的可能性将大幅增加。对于手机用锂离子电池,基本要求是发生 安全事故的概率要小于百万分之一,这也是社会公众所能接受的最 低标准。而对于大容量锂离子电池,特别是汽车等用大容量锂离子 电池,采用强制散热尤为重要。
选择更安全的电极材料,选择锰酸锂材料,在分子结构方面保证了在满电状态,正极的锂离子已经完全嵌入到负极炭孔中,从根本上避免了枝晶的产生。同时锰酸锂稳固的结构,使其氧化性能远远低于钴酸锂,分解温度超过钴酸锂100℃,即使由于外力发生内部短路(针刺),外部短路,过充电时,也完全能够避免了由于析出金属锂引发燃烧、爆炸的危险。 另外,采用锰酸锂材料还可以大幅度降低成本。 提高现有安全控制技术的性能,首先要提高锂离子电池芯的安全性能,这对大容量电池尤为重要。选择热关闭性能好的隔膜,隔膜的作用是在隔离电池正负极的同时,允许锂离子的通过。当温度升高时,在隔膜熔化前进行关闭,从而使内阻上升至2000欧姆,让内部反应停止下来。 当内部压力或温度达到预置的标准时,防爆阀将打开,开始进行卸压,以防止内部气体积累过多,发生形变,最终导致壳体爆裂。
锂离子电池安全性问题(最新版)
锂离子电池安全性问题(最新 版) Safety management is an important part of enterprise production management. The object is the state management and control of all people, objects and environments in production. ( 安全管理 ) 单位:______________________ 姓名:______________________ 日期:______________________ 编号:AQ-SN-0176
锂离子电池安全性问题(最新版) 1、使用安全型锂离子电池电解质 目前锂离子电池电解液使用碳酸酯作为溶剂,其中线型碳酸酯能够提高电池的充放电容量和循环寿命,但是它们的闪点较低,在较低的温度下即会闪燃,而氟代溶剂通常具有较高的闪点甚至无闪点,因此使用氟代溶剂有利于抑制电解液的燃烧。目前研究的氟代溶剂包括氟代酯和氟代醚。 阻燃电解液是一种功能电解液,这类电解液的阻燃功能通常是通过在常规电解液中加入阻燃添加剂获得的。阻燃电解液是目前解决锂离子电池安全性最经济有效的措施,所以尤其受到产业界的重视。 使用固体电解质,代替有机液态电解质,能够有效提高锂离子
电池的安全性。固体电解质包括聚合物固体电解质和无机固体电解质。聚合物电解质,尤其是凝胶型聚合物电解质的研究取得很大的进展,目前已经成功用于商品化锂离子电池中,但是凝胶型聚合物电解质其实是干态聚合物电解质和液态电解质妥协的结果,它对电池安全性的改善非常有限。干态聚合物电解质由于不像凝胶型聚合物电解质那样包含液态易燃的有机增塑剂,所以它在漏液、蒸气压和燃烧等方面具有更好的安全性。目前的干态聚合物电解质尚不能满足聚合物锂离子电池的应用要求,仍需要进一步的研究才有望在聚合物锂离子电池上得到广泛应用。相对于聚合物电解质,无机固体电解质具有更好的安全性,不挥发,不燃烧,更加不会存在漏液问题。此外,无机固体电解质机械强度高,耐热温度明显高于液体电解质和有机聚合物,使电池的工作温度范围扩大;将无机材料制成薄膜,更易于实现锂离子电池小型化,并且这类电池具有超长的储存寿命,能大大拓宽现有锂离子电池的应用领域。 常规的含阻燃添加剂的电解液具有阻燃效果,但是其溶剂仍是易挥发成分,依然存在较高的蒸气压,对于密封的电池体系来说,
锂电池的安全性设计(标准版)
( 安全管理 ) 单位:_________________________ 姓名:_________________________ 日期:_________________________ 精品文档 / Word文档 / 文字可改 锂电池的安全性设计(标准版) Safety management is an important part of production management. Safety and production are in the implementation process
锂电池的安全性设计(标准版) 为了避免因使用不当造成电池过放电或者过充电,在单体锂离子电池内设有三重保护机构。一是采用开关元件,当电池内的温度上升时,它的阻值随之上升,当温度过高时,会自动停止供电;二是选择适当的隔板材料,当温度上升到一定数值时,隔板上的微米级微孔会自动溶解掉,从而使锂离子不能通过,电池内部反应停止;三是设置安全阀(就是电池顶部的放气孔),电池内部压力上升到一定数值时,安全阀自动打开,保证电池的使用安全性。 有时,电池本身虽然有安全控制措施,但是因为某些原因造成控制失灵,缺少安全阀或者气体来不及通过安全阀释放,电池内压便会急剧上升而引起爆炸。 一般情况下,锂离子电池储存的总能量和其安全性是成反比的,随着电池容量的增加,电池体积也在增加,其散热性能变差,出事故的可能性将大幅增加。对于手机用锂离子电池,基本要求是发生
安全事故的概率要小于百万分之一,这也是社会公众所能接受的最低标准。而对于大容量锂离子电池,特别是汽车等用大容量锂离子电池,采用强制散热尤为重要。 选择更安全的电极材料,选择锰酸锂材料,在分子结构方面保证了在满电状态,正极的锂离子已经完全嵌入到负极炭孔中,从根本上避免了枝晶的产生。同时锰酸锂稳固的结构,使其氧化性能远远低于钴酸锂,分解温度超过钴酸锂100℃,即使由于外力发生内部短路(针刺),外部短路,过充电时,也完全能够避免了由于析出金属锂引发燃烧、爆炸的危险。 另外,采用锰酸锂材料还可以大幅度降低成本。 提高现有安全控制技术的性能,首先要提高锂离子电池芯的安全性能,这对大容量电池尤为重要。选择热关闭性能好的隔膜,隔膜的作用是在隔离电池正负极的同时,允许锂离子的通过。当温度升高时,在隔膜熔化前进行关闭,从而使内阻上升至2000欧姆,让内部反应停止下来。 当内部压力或温度达到预置的标准时,防爆阀将打开,开始进
锂电池保护电路设计方案
锂电池保护电路设计方案 锂电池材料构成及性能探析 首先我们来了解一下锂电池的材料构成,锂离子电池的性能主要取决于所用电池内部材料的结构和性能。这些电池内部材料包括负极材料、电解质、隔膜和正极材料等。其中正、负极材料的选择和质量直接决定锂离子电池的性能与价格。因此廉价、高性能的正、负极材料的研究一直是锂离子电池行业发展的重点。 负极材料一般选用碳材料,目前的发展比较成熟。而正极材料的开发已经成为制约锂离子电池性能进一步提高、价格进一步降低的重要因素。在目前的商业化生产的锂离子电池中,正极材料的成本大约占整个电池成本的40%左右,正极材料价格的降低直接决定着锂离子电池价 格的降低。对锂离子动力电池尤其如此。比如一块手机用的小型锂离子电池大约只需要5克左右的正极材料,而驱动一辆公共汽车用的锂离子动力电池可能需要高达500千克的正极材料。 尽管从理论上能够用作锂离子电池正极材料种类很多,常见的正极材料主要成分为LiCoO2,充电时,加在电池两极的电势迫使正极的化合物释出锂离子,嵌入负极分子排列呈片层结构的碳中。放电时,锂离子则从片层结构的碳中析出,重新和正极的化合物结合。锂离子的移动产生了电流。这就是锂电池工作的原理。 锂电池充放电管理设计 锂电池充电时,加在电池两极的电势迫使正极的化合物释出锂离子,嵌入负极分子排列呈片层结构的碳中。放电时,锂离子则从片层结构的碳中析出,重新和正极的化合物结合。锂离子的移动产生了电流。原理虽然很简单,然而在实际的工业生产中,需要考虑的实际问题要多得多:正极的材料需要添加剂来保持多次充放的活性,负极的材料需要在分子结构级去设计以容纳更多的锂离子;填充在正负极之间的电解液,除了保持稳定,还需要具有良好导电性,减 小电池内阻。 虽然锂离子电池有以上所说的种种优点,但它对保护电路的要求比较高,在使用过程中应严格避免出现过充电、过放电现象,放电电流也不宜过大,一般而言,放电速率不应大于0.2C。锂电池的充电过程如图所示。在一个充电周期内,锂离子电池在充电开始之前需要检测电池的电压和温度,判断是否可充。如果电池电压或温度超出制造商允许的范围,则禁止充电。允许充电的电压范围是:每节电池2.5V~4.2V。
锂离子电池生产主工艺设计
目录 1.设计的目的与任务 (1) 1.1课程设计背景 (1) 1.2课程设计目的与任务 (1) 2.设计的详细内容 (2) 2.1原材料及设备的选取 (3) 2.2电池的工作原理 (3) 2.3电池的制备工艺设计 (4) 2.3.1制片车间的工艺设计 (4) 2.3.2装配车间的工艺设计 (8) 2.3.3化成车间工艺设计 (9) 2.3.4包装车间工艺设计 (11) 2.4厂房设计 (13) 3.经济效益 (13) 4.对本设计的评述 (14) 参考文献 (16)
1.设计的目的与任务 1.1课程设计背景 自从1990年SONY采用可以嵌锂的钴酸锂做正极材料以来,锂离子电池满足了非核能能源开发的需要,同时具有工作电压高、比能量大、自放电小、循环寿命长、重量轻、无记忆效应、环境污染少等特点,现成为世界各国电源材料研究开发的重点[1~3]。锂离子电池已广泛应用于移动电话、便携式计算机、摄像机、照相机等的电源,并在电动汽车技术、大型发电厂的储能电池、UPS电源、医疗仪器电源以及宇宙空间等领域具有重要作用[4~5]。 正极材料作为决定锂离子电池性能的重要因素之一,研究和开发更高性能的正极材料是目前提高和发展锂电池的有效途径和关键所在。目前,已商品化的锂电池正极材料有钴酸锂、锰酸锂、镍酸锂等,而层状钴酸锂正极材料凭借其电压高、放电平稳、生产工艺简单等优点占据着市场的主要地位,也是目前唯一大量用于生产锂离子电池的正极材料[6~8]。 18650电池是指外壳使用65mm高,直径为18mm的圆柱形钢壳为外壳的锂离子电池。自从上个世纪90年代索尼推出之后,这种型号的电池一直在生产,经久不衰。经过近20年的发展,目前制备工艺已经非常成熟,性能有了极大的提升,体积能量密度已经提高了将近4倍,而且成本在所有锂离子电池中也是最低,目前早已走出了原来的笔记本电脑的使用领域,作为首选电池应用于动力及储能领域。 1.2课程设计目的与任务 如前文所述,在目前商业化的锂离子电池中,很多厂家都选用层状结构的
锂电池的安全性设计
仅供参考[整理] 安全管理文书 锂电池的安全性设计 日期:__________________ 单位:__________________ 第1 页共7 页
锂电池的安全性设计 为了避免因使用不当造成电池过放电或者过充电,在单体锂离子电池内设有三重保护机构。一是采用开关元件,当电池内的温度上升时,它的阻值随之上升,当温度过高时,会自动停止供电;二是选择适当的隔板材料,当温度上升到一定数值时,隔板上的微米级微孔会自动溶解掉,从而使锂离子不能通过,电池内部反应停止;三是设置安全阀(就是电池顶部的放气孔),电池内部压力上升到一定数值时,安全阀自动打开,保证电池的使用安全性。 有时,电池本身虽然有安全控制措施,但是因为某些原因造成控制失灵,缺少安全阀或者气体来不及通过安全阀释放,电池内压便会急剧上升而引起爆炸。 一般情况下,锂离子电池储存的总能量和其安全性是成反比的,随着电池容量的增加,电池体积也在增加,其散热性能变差,出事故的可能性将大幅增加。对于手机用锂离子电池,基本要求是发生安全事故的概率要小于百万分之一,这也是社会公众所能接受的最低标准。而对于大容量锂离子电池,特别是汽车等用大容量锂离子电池,采用强制散热尤为重要。 选择更安全的电极材料,选择锰酸锂材料,在分子结构方面保证了在满电状态,正极的锂离子已经完全嵌入到负极炭孔中,从根本上避免了枝晶的产生。同时锰酸锂稳固的结构,使其氧化性能远远低于钴酸锂,分解温度超过钴酸锂100℃,即使由于外力发生内部短路(针刺),外部短路,过充电时,也完全能够避免了由于析出金属锂引发燃烧、爆炸的危险。 另外,采用锰酸锂材料还可以大幅度降低成本。 第 2 页共 7 页