挤塑模具设计
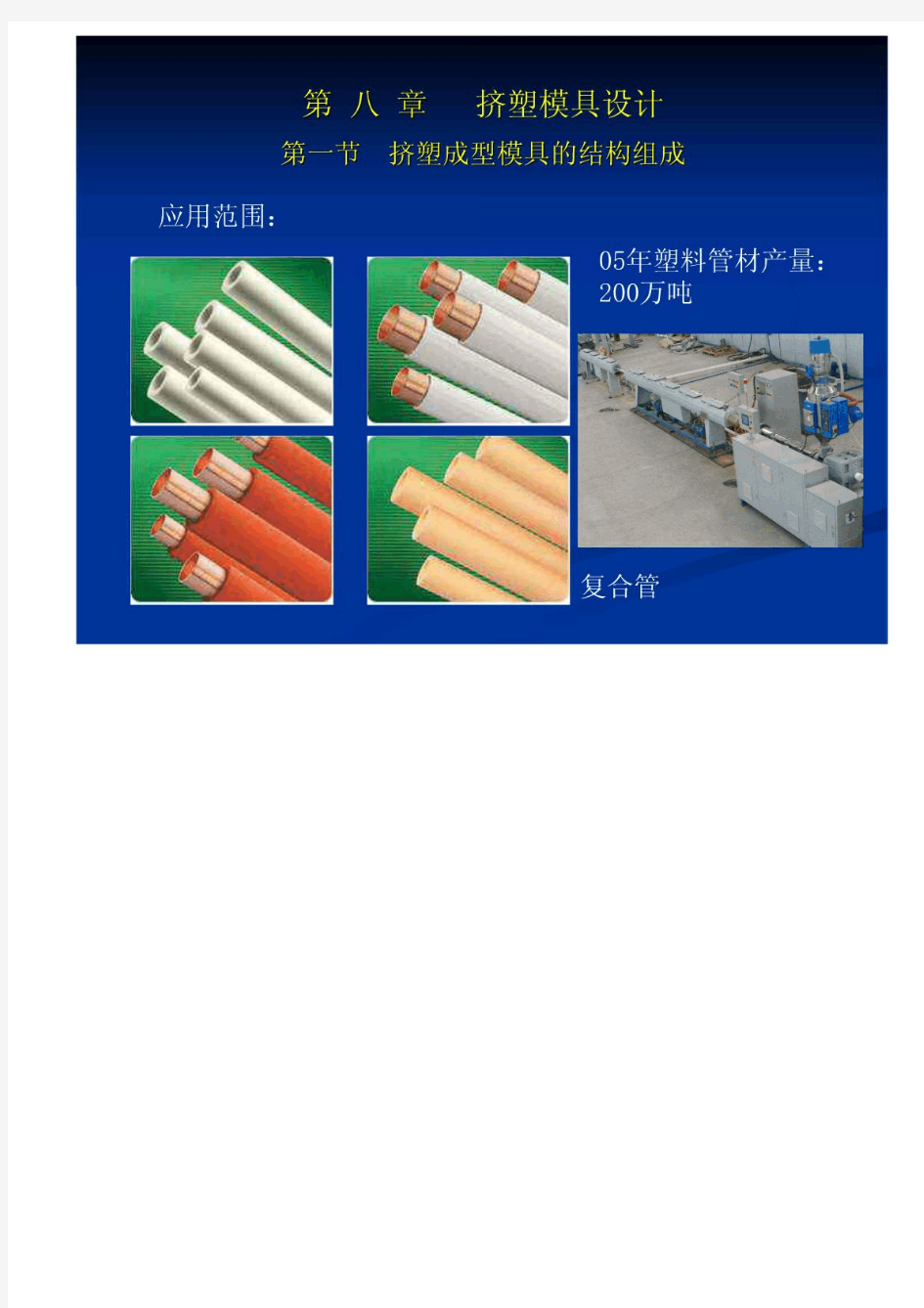

电缆用模具的分类和设计
浙江三科线缆有限公司 模具有关知识 1模具的分类 此类模具一般称为线模,可分圆模和型模,常用线模材料有钻石模、硬质合金模、聚晶模等。 a钻石模:钻石模也称金刚石,具有最高的硬度,耐磨,但价格较贵。在拉丝中,一般用在拉小规格单丝,如Φ0.40mm及以下规格。 b硬质合金模:在拉伸生产中,过去使用的钨钢模全为硬质合金模所代替的。因为硬质合金模拉伸模与钢模相比具有:耐磨性较好,抛光性好、对被加工金属的粘附性小,摩擦系数小,导热系数高和具有很高的耐腐蚀性。 c 聚晶模:也称人造钻石,是目前最常用的模丝模,它具有耐磨性,但也有不足之处就是生产出产品表面不光滑。 d 钨钢模:目前常用于铝拉,且使用寿命较短,一般用于过桥模,钨钢模耐磨性一般、价格低廉,其强度不适合于铜拉,拉制线芯表面不光滑。 2模孔结构 2.1入口区: 一般有圆弧,便于拉制线材进入工作区,不被模孔边缘所损伤;润滑液储蓄、并起到润滑拉制线材作用,在拉伸模孔中靠这部分来加大工作区的高一般为模坯总高H的25%,角度为60度。 2.2工作区: 是整个模孔的重要部分,金属拉伸塑性变形是该区进行的就是金属材料通过此区由尺寸的截面。此区的选择主要是高度和锥角,高度的选择原则是: a)拉制软金属线材应拉制硬金属线材为短, b)拉制小直径线材应拉制较大直径线材为短, c)湿法拉伸应干式润滑拉伸为短, d)一般为定径区d的1~1.4倍。 工作锥角根据下列原则选择: a)压缩率越小,工作锥角越小, b)拉制材料越硬,工作锥角越小, c)拉制小直径的材料的材料为小,一般有金属及其合金拉伸时,角度为16~26°,一般拉铜线圆锥角为16~18°,拉铝线时圆锥角为20~24°。 2.3定径区: 它的作用是使制品得到最终尺寸,其高度的选择原则是: a)拉制软金属材料较拉制金属材料要短, b )拉制大直径材料应较拉制小直径的炎短, c )湿式拉伸较之干式润滑拉伸的为短,一般选择h=0.5~1.0d。 2.4出口区: 出口区是拉制材料离开模孔的最后一部分,它能保护定径区不致于崩裂,出口锥角可避免金属线材被定径的出口处损伤和停机时线倒退被括伤,一般为45°。金属的强度极限与拉伸应力之比称为拉伸的安全系数。它的制范围:1.4~2.0。 电缆行业紧压成型类模具最常见的是异型压轮,适用于多芯电缆线芯的压制。 按其用途及角度主要分:180°两芯电缆用、120°三芯电缆用、90°四芯或3+1芯电缆及3+2或4+1芯电缆用。也有将3+1芯、3+2芯及4+1芯电缆用紧压成型模具细分为:90°、100°等。
塑料成型工艺及模具设计
复习题 1.什么是塑料? 2.在注射过程中有那些影响产品质量的因素? 3.如何确定注射模的分型面?如何进行注射模的总体布局? 4.浇注系统有那些部分组成?设计时有那些要求? 5.简述塑料中的 5 种添加剂作用是什么? 6.什么是热塑性塑料?什么是热固性塑料?两者间的区别是什么? 7.设计塑料模具时,模具的长宽和厚度尺寸与注射机的参数间的关系应满足哪些要求? 8.注射模的浇口有那些典型类型?各有何用? 9.脱模机构分为那几种?10.侧向分型与抽芯机构有那几类?各有何特点? 11.斜导柱分型抽芯机构的形式有几种?应用情况如何? 12.列出至少六种常见的浇口形式,并简述在选择浇口位置时应该考虑的因素。 13.简述斜导柱侧向分型与抽芯机构设计中,侧型芯滑块压紧、定位及导滑机构的作用。 14. 简述分型面的设计原则。 15. 简述冷却回路的布置原则。 16、哪些情况下要考虑采用先行复位机构 ? 17、常见的排气方式有哪些? 18.塑料的主要成分是什么 ? 19.注塑成型工艺三个基本参数是什么? 20.什么样塑件的注射模需要设置侧分型与抽芯机构? 21.点浇口和侧浇口分别适用于哪种典型的注射模具? 22.注射模具中复位杆的作用是什么? 23.注射模具的长和宽受到注射机什么部位的尺寸限制?厚度受到什么限制? 24.浇口套零件上凹球面直径和小孔直径与注射机的什么部位的尺寸有关? 25.注射机的主要技术指标有哪些? 26.模具在注射机上是怎样定位和固定的? 27.简述选择注射机时要校核哪些参数? 28.注射成型的工艺过程有哪些内容?简述各部分的作用? 29.分别简述热塑性塑料和热固性塑料在注射成型过程中的特点?两者间的区别是什么? 30.注射模具主要有哪几个部分组成?每个部分的作用是什么? 31.注射模推出机构的作用是什么?推杆推出机构有哪些零件组成? 32.侧分型与抽芯机构为什么要设置定位、锁紧装置? 1.什么是塑料? 塑料是在一定条件下,一类具有可塑性的高分子材料的通称,一般按照它的热熔性把它们分成:热固性塑料和热塑性塑料。它是世界三大有机高分子材料之一(三大高分子材料是塑料,橡胶,纤维)。 2.在注射过程中有那些影响产品质量的因素?答:因此最重要的工艺条件应该是足以影响塑化和注射充模质量的温度(料温、喷嘴温度、模具温度)、压力(注射压力、模腔压力)和相应的各个作用时间(注射时间、保压时间、冷却时间)以及注射周期等。而会影响温度、压力变化的工艺因素(螺杆转速、加料量及剩料等)也不应忽视。料筒温度关系到塑化质量。具温度影响塑料熔体充模时的流动行为,并影响制品
电线电缆制造流程概述
电线电缆制造流程概述内部编号:(YUUT-TBBY-MMUT-URRUY-UOOY-DBUYI-0128)
电线电缆制造流程概述 电线电缆的制造与大多数机电产品的生产方式是完全不同的。机电产品通常采用将另件装配成部件、多个部件再装配成单台产品,产品以台数或件数计量。电线电缆是以长度为基本计量单位。所有电线电缆都是从导体加工开始,在导体的外围一层一层地加上绝缘、屏蔽、、成缆、护层等而制成电线电缆产品。产品结构越复杂,叠加的层次就越多。 一、电线电缆产品制造的工艺特性: 1.大长度连续叠加组合生产方式 大长度连续叠加组合生产方式,对电线电缆生产的影响是全局性和控制性的,这涉及和影响到: (1)生产工艺流程和设备布置 生产车间的各种设备必须按产品要求的工艺流程合理排放,使各阶段的半成品,顺次流转。设备配置要考虑生产效率不同而进行生产能力的平衡,有的设备可能必须配置两台或多台,才能使生产线的生产能力得以平衡。从而设备的合理选配组合和生产场地的布置,必须根据产品和生产量来平衡综合考虑。 (2)生产组织管理 生产组织管理必须科学合理、周密准确、严格细致,操作者必须一丝不苟地按工艺要求执行,任何一个环节出现问题,都会影响工艺流程的通畅,影响产品的质量和交货。特别是多芯电缆,某一个线对或基本单元长度短了,或者质量出现问题,则整根电缆就会长度不够,造成报废。反之,如果某个单元长度过长,则必须锯去造成浪费。 (3)质量管理
大长度连续叠加组合的生产方式,使生产过程中任何一个环节、瞬时发生一点问题,就会影响整根电缆质量。质量缺陷越是发生在内层,而且没有及时发现终止生产,那么造成的损失就越大。因为电线电缆的生产不同于组装式的产品,可以拆开重装及更换另件;电线电缆的任一部件或工艺过程的质量问题,对这根电缆几乎是无法挽回和弥补的。事后的处理都是十分消极的,不是锯短就是降级处理,要么报废整条电缆。它无法拆开重装。 电线电缆的质量管理,必须贯串整个生产过程。质量管理检查部门要对整个生产过程巡回检查、操作人自检、上下工序互检,这是保证产品质量,提高企业经济效益的重要保证和手段。 2.生产工艺门类多、物料流量大 电线电缆制造涉及的工艺门类广泛,从有色金属的熔炼和压力加工,到塑料、橡胶、油漆等化工技术;纤维材料的绕包、编织等的纺织技术,到金属材料的绕包及金属带材的纵包、焊接的金属成形加工工艺等等。 电线电缆制造所用的各种材料,不但类别、品种、规格多,而且数量大。因此,各种材料的用量、备用量、批料周期与批量必须核定。同时,对废品的分解处理、回收,重复利用及废料处理,作为管理的一个重要内容,做好材料定额管理、重视节约工作。 电线电缆生产中,从原材料及各种辅助材料的进出、存储,各工序半成品的流转到产品的存放、出厂,物料流量大,必须合理布局、动态管理。 3.专用设备多 电线电缆制造使用具有本行业工艺特点的专用生产设备,以适应线缆产品的结构、性能要求,满足大长度连续并尽可能高速生产的要求,从而形成了线缆制造的专用设备系列。如挤塑机系列、拉线机系列、绞线机系列、绕包机系列等。
冲孔模设计圆筒件翻边
模具课程设计计算说明书 目录 摘要 (3) 绪论 (5) 一、冲压工艺性分析 (7) 二、冲压工艺方案的确定 (8) 1.方案种类 (8) 2.方案的比较 (8) 3.方案的确定 (8) 三、模具结构形式的确定 (9) 四、设计工艺计算 (10) 1.基本尺寸与计算 (10) 2.冲裁压力的计算 (12) 3.压力机公称压力的确定 (12) 4.冲裁压力中心的确定 (13) 5.工作零件刃口尺寸的计算 (15) 五、模具总体结构设计 (19) 六、主要零部件的设计 (20) 1.工作零件的结构设计 (20) 2.定位零件的设计 (22) 3.卸料部件的设计 (23) 4.导柱、导套位置的确定 (23) 5.模架及其他零部件的设计 (24) 七、模具总装图 (24) 八、填写冲压工艺卡片 (27) 九、填写模具零件加工工艺卡 (29) 十一、结束语 (34) 致谢 (35) 主要参考文献 (36) 摘要 论文是由翻边设计、冲孔模设计组成,冲压模具主要是将板料分离或成形而得到制件的加工方法。因为模具的生产主要是大批量的生产,而且模具可以保证冲压产品的尺寸精度和产品质量,模具的设计与制造主要考虑到模具的设计能否满足工件的工艺性设计,能否加工出合格的零件,以及后来的维修和存放是否合理等。在本次设计中的取暖器主机连接座中,不仅要考虑要使做出的零件能满足工作要求,还要保证它的使用寿命。 其次设计中还要考虑到它的实际工作环境和必须完成的设计任务,两套模具的模架分别采用后置和中间形式,凹模采用整体凹模,这样可以采用线切割等数控设备来一次完成全部的工序加工,在设计中我要考虑到很多关于我所设计模具的知识,包括它的使用场合、外观要求等,从这里可以知道模具设计是一项很复杂的工作,所以在设计要不断的改进直到符合要求。 关键词:翻边冲孔工艺性 Abstract Paper is designed by the flanging, punching mould design, sheet metal stamping is mainly will get separated or forming parts processing methods. Because the mold production mainly mass production, and mould can ensure the precision stamping products and product quality, the mold
终端电缆盒基础组合模具
终端电缆盒基础组合模具 一. 工程概况 越南北方铁路通信信号现代化工程,包括河内枢纽8个车站、正线86km ;河内—同登线19个车站、正线167km ;河内—太原线7个车站、正线76km ;河内—老街线31个车站、正线295km 范围内全部通信及信号设备改造。工程全部采有中国铁路技术设备,执行中华人民共和国铁道行业标准“铁路信号工程质量检验评定标准”和“铁路通信工程质量检验评定标准”。 二. 终端电缆盒 电缆盒基础分为终端电缆盒和方向电缆盒两种。终端电缆盒基础如图所示: M10*200 终端电缆盒基础 三. 终端电缆盒组合模具的设计及使用 为提高预制终端电缆盒混凝土基础的施工效率,同时保证施工质量,我们没 有按照书本教条的打造站立式的单个模具。经过经理和书记,以及有十几年工作经验的老职工们共同研究,献计献策,产生了一次打造多个基础的组合模具的想法。这样把此大型组合模具平躺在地面上,既能按照规定造出混凝土基础,又使各种工序变得轻松方便,而且节省时间,提高效率。 模具主要由两块角钢和十二块经精确测量而打造的标准铁板组成。模具的组装及拆卸非常方便。如下图所示:
模具的组装 组装好的模具
拆卸模具,打造出的基础美观而且质量俱佳 四.终端电缆盒组合模具的优点及经济效益 如果使用单个模具一个一个的生产终端电缆盒基础,不但要耗费大量用于支撑模具的钢材料,而且使加入混凝土,振捣,抹面等工序变得非常困难。此组合模具一次可以打造出十一个终端电缆盒基础,不但节约了用于支撑单个模具所用 的大量钢材料,而且使用起来省时省力,使加入混凝土,平振变得简单可行。
加入混凝土省时省力,操作简单。 抹面工序轻松方便,且效果显著
塑料成型工艺及模具设计重点分析
塑料成型工艺及模具设计复习 红色部分不考 绪论 1、塑料制品的质量与塑料成型模具、塑料成型设备和塑料成型工艺密切相关。 2、模具热处理的发展方向是采用真空热处理。 3、塑料成型模具的分类:(1)注射模(2)压缩模(3)压注模(传递模)(4)挤出模(5)气动成型模 第二章塑料的组成与工艺特性 1、名词解析:热塑性塑料;热固性塑料 热塑性塑料主要由合成脂(分子为线型或者带有支链的线型结构)制成,其成型过程是物理变化。 热固性塑料主要是以缩聚树脂(分子为立体网状结构)为主,加入各种助剂制成的,但它的成型过程不仅是物理变化,更主要的是化学变化。 2、塑料一般由哪些成分组成?各自起什么作用? 塑料是一种以合成树脂(高分子聚合物)为基体的固体材料,除了合成树脂作为基体外,还有某些特定用途的添加剂(少数情况下可以不加添加剂)。 1.合成树脂:合成树脂实质上是高分子化合物质或其预聚体,它是塑料的基材,对塑料的物理、化学性能起着决定作用。 2塑料添加剂:1)增塑剂主要作用是削弱聚合物之间的作用力(范德华力),从而增加聚合物分子间的移动性,降低聚合物分子链的结晶性,亦即增加聚合物的塑性。2)填料 a 增加容量,降低塑料成本。b 改善塑料性能,提高塑料的物理性能、加工性能和塑件的质量。3)稳定剂提高树脂在热、光和霉菌等外界因素作用时的稳定性。4)润滑剂以改进高聚物的流动性、减少摩擦、降低界面粘附为目的。5)着色剂使塑料件具有各种颜色。 3、塑料是如何进行分类的?热塑性塑料和热固性塑料有什么区别? (1)从应用角度,可分为普通塑料和工程塑料,其中工程塑料又可分为通用工程塑料和特种工程塑料。(2)按照制造树脂的方法,分为缩聚型塑料和加聚型塑料。(3)最常用的,按塑料树脂的大分子类型和特性,分为热塑性塑料和热固性塑料。 热塑性塑料受热可软化或熔融,成型加工后冷却固化,再加热仍可软化,可回收利用。热固性塑料成型加工时也可受热软化或熔融,但一旦成型固化后不再能够软化,也不可回收利用。 4、什么是塑料的计算收缩率?影响塑料收缩率的因素有哪些? 塑料制件从模具中取出冷却后一般都会出现尺寸缩减的现象。这种塑料成型冷却后发生体积收缩的特性称为塑料的成型收缩性。一般塑料收缩性的大小常用实际收缩率和计算收缩率来表征。影响收缩率的因素有很多,如塑料品种、成型特征、成型条件及模具结构等。 5、什么是塑料的流动性?影响流动性的因素有哪些? 时发生的大分子之间的相对滑移现象,表塑料的流动性是指树脂聚合物所处的温度大于其粘流温度 f 现为成型过程中在一定温度和一定压力下塑料熔体充填模具型腔的能力。塑料的结构、成型工艺和模具结构等是影响流动性的主要因素。 6、阐述常用塑料的性能特点?P26 第三章塑料成型制件的结构工艺性 1、名词解析:尺寸精度、脱模斜度
快速成型制造实训报告
快速成型制造实训报告 1.实习目的 1).通过快速成型制造实训了解怎么利用快速成型设备制作模型,学会怎么操作快速成型机,然后根据模型做出硅胶模具,让我们对塑料模具的基本结构有了更深的理解,再用硅胶模具浇注出工件。 2.实习要求 1).自己用PRO-E软件设计模型,用快速成型机器制造出模型,模型做好后,用硅胶做出硅胶模具。等模具固化后,用AB胶浇注出一个工件。 3.模型的设计与选择 1)用PRO-E设计出一个猪仔的模型,尺寸自定,模型有明显的分型面,所以比较容易做分模。(模型如图所示)
4.原型的制作 1).用PRO-E造型的模型用stl格式保存好后,拿到FDM 200快速成型机上,开始做模型。 (制作过程如图所示)
5.硅胶模方案与结构的设计 1)制作硅胶模,我们用上下分模的结构,对角做了两个突起作为导柱。我们没有用油泥,而是直接在浇硅胶时控制好只浇到分型面处。 硅胶与固化剂搅拌均匀. 模具硅胶外观是流动的液体,A
组份是硅胶,B组份是固化剂。取
250克硅胶,加入25 克固化剂(注:硅胶与固 化剂一定要搅拌均匀,如 果没有搅拌均匀,模具会 出现一块已经固化,一块 没有固化,硅胶会出现干 燥固化不均匀的状况就会影响硅胶模具的使用寿命及翻模次数,甚至造成模具报废状况。 6.硅胶模的制作流程 1).先用纸板围成一个能包住模型的框,模型要距离纸板10到15MM,用铅笔尖的一头连接模型,作为浇注工件时的胶口。在框里面喷上脱模剂,方便做好后的处理。然后把配好的硅胶浇到框中,浇完后拿到真空机中做抽真空处理。 抽真空排气泡处理: 硅胶与固化剂搅拌均匀后,进行抽 真空排气泡环节,抽真空的时间不 宜太久,正常情况下,不要超过十 分钟,抽真空时间太久,硅胶马上 固化,产生了交联反映,使硅胶变 成一块一块的,无法进行涂刷或灌 注,这样就浪费了硅胶,只能把硅 胶倒入垃圾桶,重新再取硅胶来
线缆技术中选配模具的必备经验
线缆技术中选配模具的必备经验 选配模具的经验 <1> 16mm 及以下的绝缘线芯的配模,要用导线试验模芯,以导线通过模芯为宜。不要过大,否则将产生倒胶现象。 <2> 抽真空挤塑时,选配模具要合适,不宜过大,绝缘层或护套层容易生耳朵,起棱松套现象。 <3> 挤塑过程中,实际上塑料均有拉伸现象存在,一般塑料的实际拉伸在2.0mm左右.根据拉伸考虑模套的放大值,拉伸比大的塑料模套放大值大于拉伸比小的塑料模套放大值,如聚乙烯大于聚氯乙烯.<4>安装模具时要调整好模芯与模套间的距离,防止堵塞,造成设备事故. 2挤压式模具设计中主要参数的选择 电线电缆塑料模具设计要保证线缆制品的三个基本要求:形状正确;尺寸合格;粗糙度小。 2.1挤压式模芯的主要参数的确定 各参数见图2。 β—模芯外锥角。一般可在20°~40°范围内选取,对于塑料挤包层较厚而又需挤包得紧些时,也可取β=60°。 图2挤压式模芯各参数示意图 D—模芯外锥最大直径。该尺寸由模芯支持器(或模芯座)的尺寸决定的,要求严格吻合,不得出现“前台”和“后台”,否则将造成存胶死角,直接影响胶层组织和表面质量。 D"—内锥最大直径。该尺寸主要取决于加工条件和螺柱的壁厚,在保证螺柱壁厚的前提下,越大越好。 d—模芯孔径。这是对挤压质量影响最大的结构尺寸,按线芯结构特性及其几何尺寸设计。若线芯直径为d0,则 单线取d=d0+(0.05~0.15)mm; 绞合线芯d=d0+(0.1~0.25)mm; 成缆芯线d=d0+(0.2~0.50)mm; 大截面成缆芯线d=d0+(0.40~1.0)mm; 对镀锡线d要相应增加(0.10~0.50)mm。 d'—模芯外锥最小直径。 若模芯头部端面厚度为δ0,则 一般δ0=(0.3~1)mm;d'=d+2δ0 l—模芯定径区长度。 l=(0.5~1.5)d l决定线芯通过模芯的稳定性,但也不能设计得太长,否则将造成加工的困难,工艺上的必要性也不大。因此,模孔d大的取下限,模孔d小的取上限。 L—模芯锥体长度。 由图2可知,,所以。 如果由上式计算出来的L太长或太短,与机头内部结构配合不当,可重新改变锥角β。 2.2挤压式模套主要参数的确定 各参数见图3。 图3挤压式模套各参数示意图 D2—模套压座外径,根据模套座内孔设计。若模套座内孔直径为φ0则D2=φ0-(0.5~1)mm。 D3—内锥最大直径。这是模套设计的精密尺寸之一。其大小必须严格与模套座(或机头内锥)末端内径一致,组装后不准产生阶梯死角。 D0—模套定径区直径。这又是模套设计的精密尺寸之一,要根据产品直径,考虑挤出各工艺参数及挤制塑料特性严格设计,一般 D0=d0+(0.05~0.15)mm 有时可设计为D0=d0-(0.05~0.10)mm。 式中:d0—电线(或电缆)外径。 D0决定挤出层外径大小及挤出层表面质量。D0太大,塑料拉伸较大,使挤出物表面粗糙无光。D0
塑料成型工艺及模具设计
复习题 1.什么是塑料? 2.在注射过程中有那些影响产品质量的因素? 3.如何确定注射模的分型面?如何进行注射模的总体布局? 4.浇注系统有那些部分组成?设计时有那些要求? 5.简述塑料中的5种添加剂作用是什么? 6.什么是热塑性塑料?什么是热固性塑料?两者间的区别是什么? 7.设计塑料模具时,模具的长宽和厚度尺寸与注射机的参数间的关系应满足哪些要求? 8.注射模的浇口有那些典型类型?各有何用? 9.脱模机构分为那几种? 10.侧向分型与抽芯机构有那几类?各有何特点? 11.斜导柱分型抽芯机构的形式有几种?应用情况如何? 12.列出至少六种常见的浇口形式,并简述在选择浇口位置时应该考虑的因素。13.简述斜导柱侧向分型与抽芯机构设计中,侧型芯滑块压紧、定位及导滑机构的作用。 14.简述分型面的设计原则。 15.简述冷却回路的布置原则。 16、哪些情况下要考虑采用先行复位机构? 17、常见的排气方式有哪些? 18.塑料的主要成分是什么? 19.注塑成型工艺三个基本参数是什么? 20.什么样塑件的注射模需要设置侧分型与抽芯机构? 21.点浇口和侧浇口分别适用于哪种典型的注射模具? 22.注射模具中复位杆的作用是什么? 23.注射模具的长和宽受到注射机什么部位的尺寸限制?厚度受到什么限制?24.浇口套零件上凹球面直径和小孔直径与注射机的什么部位的尺寸有关?25.注射机的主要技术指标有哪些? 26.模具在注射机上是怎样定位和固定的? 27.简述选择注射机时要校核哪些参数? 28.注射成型的工艺过程有哪些内容?简述各部分的作用? 29.分别简述热塑性塑料和热固性塑料在注射成型过程中的特点?两者间的区别是什么? 30.注射模具主要有哪几个部分组成?每个部分的作用是什么? 31.注射模推出机构的作用是什么?推杆推出机构有哪些零件组成? 32.侧分型与抽芯机构为什么要设置定位、锁紧装置?
模具圆筒件翻边、冲孔模设计
毕业设计(论文) 题目:圆筒件翻边、冲孔模设计 年级专业:模具设计与制造 学生姓名: 指导教师: 2010 年8 月26 日
目录 摘要 (3) 绪论 (5) 一、冲压工艺性分析 (7) 二、冲压工艺方案的确定 (8) 1.方案种类 (8) 2.方案的比较 (8) 3.方案的确定 (8) 三、模具结构形式的确定 (9) 四、设计工艺计算 (10) 1.基本尺寸与计算 (10) 2.冲裁压力的计算 (12) 3.压力机公称压力的确定 (12) 4.冲裁压力中心的确定 (13) 5.工作零件刃口尺寸的计算 (15) 五、模具总体结构设计 (19) 六、主要零部件的设计 (20) 1.工作零件的结构设计 (20) 2.定位零件的设计 (22) 3.卸料部件的设计 (23) 4.导柱、导套位置的确定 (23) 5.模架及其他零部件的设计 (24) 七、模具总装图 (24) 八、填写冲压工艺卡片 (27) 九、填写模具零件加工工艺卡 (29) 十一、结束语 (34) 致谢 (35) 主要参考文献 (36)
摘要 论文是由翻边设计、冲孔模设计组成,冲压模具主要是将板料分离或成形而得到制件的加工方法。因为模具的生产主要是大批量的生产,而且模具可以保证冲压产品的尺寸精度和产品质量,模具的设计与制造主要考虑到模具的设计能否满足工件的工艺性设计,能否加工出合格的零件,以及后来的维修和存放是否合理等。在本次设计中的取暖器主机连接座中,不仅要考虑要使做出的零件能满足工作要求,还要保证它的使用寿命。 其次设计中还要考虑到它的实际工作环境和必须完成的设计任务,两套模具的模架分别采用后置和中间形式,凹模采用整体凹模,这样可以采用线切割等数控设备来一次完成全部的工序加工,在设计中我要考虑到很多关于我所设计模具的知识,包括它的使用场合、外观要求等,从这里可以知道模具设计是一项很复杂的工作,所以在设计要不断的改进直到符合要求。 关键词:翻边冲孔工艺性 Abstract Paper is designed by the flanging, punching mould design, sheet metal stamping is mainly will get separated or forming parts processing methods. Because the mold production mainly mass production, and mould can ensure the precision stamping products and product quality, the mold design and manufacture of the main consideration of mould design can meet the design, can processing manufaturability qualified parts, and then repair and storage whether reasonable, etc. In the design of the main building, connect heater to make the parts can satisfy the requirements, it also ensures that its service life. Second design to consider its actual working environment and must complete the task, two sets of mould design of formwork used respectively, and the form of dies.the using integral dies.the, so can using such equipment to a linear control all the process in the design, I will consider a lot about my knowledge of mould design, including the use of its appearance, etc,
快速成型与快速模具制造技术及其应用考试重点总结
1.1 1988年,3Dsystems公司将SLA-250光固化设备系统运送给三个用户,标志着快速成型设备的商业化正式开始。 1.3 快速成型技术的特点:1自由成型制造2制造过程快速3添加式和数字化驱动成型方式4技术高度集成5突出的经济效益6广泛的应用领域 1.4 快速成型技术的优越性:1设计者受益2制造者受益3推销者受益4用户受益 2.1 快速成型工艺基本原理:基于离散堆积原理的累加式成型,从成型原理上提出了一种全新的思维模式,即将计算机上设计的零件三维模型,表面三角化处理,存储成STL文件格式,对其进行分层处理,得到各层截面的二维轮廓信息,按照这些轮廓信息自动生成加工路径,在控制系统的控制下,选择性的固化或烧结或切割一层层的成型材料,形成各个截面轮廓薄片,并逐步顺序叠加成三维实体,然后进行实体的后处理,形成原型。 快速成型:1液态(SLA FDM)2粉末粒子(SLS)3薄层材料(LOM) 2.2.1 光固化成型工艺的基本原理及过程: 光固化成型工艺的特点:优点:1成型过程自动化程度提高2尺寸精度高3优良的表面质量4可以制造结构十分复杂,尺寸比较精细的模型5可以直接制作面向熔模精密铸造的具有中空结构的消失型6制作的原型可以再一定程度上替代塑件 缺点:成型过程中伴随着物理和化学变化,制件易弯曲,需要支撑2液态树脂固化后的性能尚不如常用的工业塑料3设备运转及维护成本较高4使用的材料种类较少5液态树脂有一定的气味和毒性,而且要避光保护6光固化后的原型树脂并未完全被激光固化,为提高使用性能和尺寸稳定性,通常需要二次固化。 2.2.2 光固化成型的工艺过程 1 前处理:1 CAD三维造型2数据转换3确定摆放方位4施加支撑5切片分层 2原型制作3后处理 2.2.4 光固化成型的支撑结构必须设计一些细圆柱状或肋状支撑结构,以便确保制件的每一结构部分都能可靠固定,同时也有助于减少制件的翘曲变形。 2.2.5 光固化成型的收缩变形:1树脂收缩原因2零件成型过程中树脂收缩产生的变形3零件后固化收缩产生的变形 光固化成型误差分析: 影响制作时间的因素t=Σtci+Ntp 2.3 叠层实体制造工艺的基本原理和特点 工艺过程 误差分析 表面涂覆的具体工艺过程:1将剥离后的原型表面用砂纸轻轻打磨2按规定比例配备环氧树脂3在原型上涂刷一薄层混合后的材料,因材料的粘度较低,材料会很容易侵入原型中4再次涂覆同样的混合后的环氧树脂材料,以填充表面的沟痕并长时间固化5对表面已经涂覆了坚硬的环氧树脂材料的原型再次用砂纸进行打磨,打磨之前和过程中注意测量原型的尺寸,以确保尺寸在公差之内。6对原型表面进行抛光。 2.3.6 叠层实体快速原型的应用1汽车车灯2铸铁手柄3LOM原型在制鞋业的应用 2.4.1 选择性激光烧结工艺的基本原理 2.4.2 选择性激光烧结工艺的特点:优点:1可采用多种材料2制造工艺比较简单3高精度4无需支撑结构5材料利用率高缺点:1表面粗糙2烧结过程挥发异味3有时需要比较复杂的辅助工艺 2.4.4 高分子粉末烧结件的后处理:1收缩精度的影响2力学性能的影响 2.4.6 选择性激光烧结工艺的应用:1直接制作快速模具2复杂金属零件的快速无模具铸造3
热成型工艺与模具设计---教学大纲
《热成型工艺与模具设计》课程教学大纲 课程代码:050141013 课程英文名称:Hot Working Technology and Die Design 课程总学时:48 讲课:44 实验:4 上机:0 适用专业:材料成型及控制工程专业 大纲编写(修订)时间:2017. 07 一、大纲使用说明 (一)课程的地位及教学目标 本课程是材料成型及控制工程专业模具方向的一门专业课,主要讲授金属材料热成型工艺及模具设计的基本理论和基本方法,包括锻造用材料的准备,锻造用材料的热规范,自由锻工艺,模锻工艺及模具设计;着重培养学生的设计思维,使学生具备初步分析和解决金属材料热成型工艺问题及模具设计的能力。 通过本课程的学习,学生将达到以下要求: 1.掌握热成型工艺及模具设计的设计原理、方法,具有热成型工艺及模具设计的初步能力; 2.树立正确的设计思想,了解国家当前的有关技术经济政策; 3.具有运用标准、规范、手册、图册等有关技术的能力; 4.了解典型自由锻工艺和模锻工艺的实验方法,获得实验技能的基本训练; 5.了解热成型工艺及模具设计的新发展。 (二)知识、能力及技能方面的基本要求 1.基本知识:掌握自由锻工艺,模锻工艺及模具设计一般知识,模具的主要类型、性能、结构特点、应用、材料、标准等。 2.基本理论和方法:重点掌握锻造用材料分类及下料方法,掌握钢锭的结构及内部缺陷,掌握钢坯内部缺陷。了解钢锭的冶炼和浇注方法。了解精密下料方法。重点掌握金属材料锻造温度范围及加热、冷却规范的确定。掌握金属材料在锻造加热、冷却过程中的组织性能变化,掌握金属材料在锻造加热过程中缺陷的产生原因与防止措施。了解少无氧化加热技术在锻造加热过程中地应用,了解锻后热处理方法。重点掌握镦粗、拔长自由锻工艺变形过程的金属流动规律及自由锻工艺规程制订,掌握冲孔、扩孔及芯轴拔长等自由锻工艺。了解大型锻件锻造的特点。重点掌握锤上模锻工艺变形过程的金属流动规律及锤上锻工艺规程的制订及模具设计,掌握模具材料及模具实效的基本知识,掌握机械压力机模锻、螺旋压力机模锻和平锻机模锻工艺变形过程的金属流动规律及模具设计。了解精密模锻及其他模锻工艺及模具设计知识。掌握模锻后续工序及模具设计,了解锻后清理知识。 3.基本技能:掌握工艺计算、模具结构设计,实验技能,编制技术文件技能等。 (三)实施说明 1.教学方法:课堂讲授中要重点对基本概念、基本方法和解题思路的讲解;采用启发式教学,培养学生思考问题、分析问题和解决问题的能力;引导和鼓励学生通过实践和自学获取知识,培养学生的自学能力;增加讨论课,调动学生学习的主观能动性;注意培养学生提高利用标准、规范及手册等技术资料的能力。讲课要联系实际并注重培养学生的创新能力。 2.教学手段:本课程属于专业课,在教学中采用电子教案、CAI课件及多媒体教学系
模具毕业设计40挂板产品造型与模具设计
摘要 模具制造技术迅速发展,已成为现代制造技术的重要组成部分。如模具的CAD/CAM技术,模具的激光快速成型技术,模具的精密成形技术,模具的超精密加工技术。以及为了缩短模具设计生产周期而采用的Unigraphics NX,正是基于以上条件应运而生,它的出现,大大提高了模具生产的效率。本设计介绍了挂板塑料注射模具的设计与制造方法。该注射模采用了1模4腔的结构。 关键词:塑料;注射模具;设计;UG
Abstract Mold the rapid development of manufacturing technology, modern manufacturing techniques have become an important part. If the mold CAD / CAM technology, rapid prototyping mold laser technology, precision die forming technology, the ultra-precision mold processing technology. And mold design in order to shorten the production cycle and the use of Unigraphics NX, is created based on the above conditions, it appears, greatly improving the efficiency of the production mold. The design introduced the peg board plastic injection mold design and manufacturing methods. The use of an injection mold cavity mode structure of 4. Key words: plastics; injection mold; design; UG
翻边整形模模具设计规范
目录 序号内容页次 1 冲压力的计算 2 2 工作行程 4 3 凸模托料面的设计9 4 压件器的强度设计11 5 压件器与凹模分界的设定13 6 翻边模刃口的种类及使用15 7 翻边顶出器的安装标准25 8 退料块及定位块的形状28 9 翻边变形对策30 10 铸件壁厚设计32 11 铸造减轻孔设计33
1.冲压力的计算 1.1.弯曲成形力的计算P B =弯曲成形力(N) L=加工长度(mm) t=料厚(mm) σ b =抗拉强度(Mpa) ① P B =1/2*σ b *L*t ② P B =σ B *L*t ③ P B =3/2*σ B *L*t ④ P B =2*σ B *L*t ⑤ P B =2/3*σ B *L*t ⑥ P B =5/6*σ B *L*t ⑦ P B =7/6*σ B *L*t ⑧ P B =3/2*σ B *L*t ⑨ P B =0.8*L*t2*σ B /(R+t) 注:⑤、⑥、⑦、⑧其底面如需墩死成,弯曲成形力取计算值的1.5-2倍。 1.2.压料力 压料力一般为压弯力的15%-30%。 ?P为冲压开始点的压料力 外板P=0.3 P B (N) 内板P=(0.15-0.2)P B (N) ?弹簧等压力源尽量设在成形部位附近 制定部门制定日期制定审定批准版次发行部门
?视压料板形状确定是否兼负平衡作用,如存在平衡力的因素,压料力应大于计算压力。?上弹簧压料和下气垫压料同时使用时,主要考虑向下翻边时的上压料力。 ?内板件在成形时,如有向外拉料的可能时(如下图示),应加大压料力,计算方法与外板相同。 1.3.弯曲整形力的计算 弯曲整形力P=F*q F:为整形部分的投影面积(mm2) q:为整形所需的单位压力(MPa),见数据下表:
钣金成型课程模具设计
钣金成型课程设计说明书制件工艺分析与模具设计 院系: 专业: 班级: 学号: 姓名: 指导教师: 沈阳航空航天大学 2017年12月1日
摘要 本次综合实训设计垫片的冲压模具,零件结构简单对称,料厚较小,设计者将其设计为级进模模具,主要有冲孔落料两道工序。本说明书以图文并茂的方式对此零件的模具设计加以介绍,主要叙述了从零件的工艺性分析到模具结构的设计、工艺计算、冲模结构的设计以及主要零件设计等,直到最后的模具装配图、零件图、排样图等一系列的设计过程。其中详尽的分析讲述了针对于该零件的冲压模具完整设计方法,读者可以从本说明书中简单、明确的了解该设计的主要思想路线及合理设计制造方案,加深对级进模模具设计知识的了解、应用以及提升关于级进模模具的分析问题、解决问题的能力。 关键词:垫片、级进模、冲孔落料、模具、设计
目录 第1章冲压工艺分析......................................... 1.1零件工艺分析................................... 1.1.1产品结构形状及材料分析.................... 1.1.2产品尺寸精度、粗糙度、断面质量分析........... 1.2冲压工艺方案的确定............................... 1.2.1第一种方案......................... 1.2.2第二种方案............................ 1.2.3第三种方案................................ 第2章冲压工艺计算................................ 2.1排样....................................... 2.1.1搭边.................................... 2.1.2条料宽度和导尺间距离................. 2.1.3送料步距................................. 2.1.4材料利用率............................... 2.2计算冲压力............................... 2.2.1冲裁力计算............................... 2.2.2卸料力、推件力与顶件力的计算.............. 2.3压力中心的计算............................ 第3章级进模凸凹模设计........................... 3.1模具刃口尺寸的计算......................... 3.1.1冲孔凸、凹模....................... 3.1.2落料凹、凸模........................ 3.2凹模的设计........................... 3.2.1凹模厚度H的计算................ 3.2.2凹模长度和宽度......................... 3.2.3凹模材料..................................... 3.2.4凹模固定方法............................ 3.3凸模的设计................................... 3.3.1凸模强度——压应力校核.................... 3.3.2凸模材料................................. 第4章基本冲模结构的确定...................... 4.1模具的形式...............................
冲压模具设计带凸缘圆筒件
带凸缘圆筒拉深模设计 班级: 姓名: 学号: 日期:
前言 冷冲压模具的设计与制造一材料的塑性变形理论为基础,综合了塑性力学、机械力学、机械原理与设计、机械设计制造工艺等多学科的应用,就是一门理论性与应用性很强的课程。围绕冷冲模设计,前向有冲压工艺,后有制造工艺,在数字化技术应用高度发展的今天,冷冲模开发的三个层面已经高度集成,紧密融合在一起。通过冷冲压的理论学习,然后再将理论知识用于实际中,不仅有助于理论知识的消化吸收,也可以提高自身的工程能力。为此,进行必要的冷冲模的课程设计很有必要。 结合所学到的理论知识与自身掌握的情况,特以带凸缘的圆筒件来设计冷冲压模具。此制件结构简单,容易上手学习,并且涵盖了所学的知识点,就是一个很好的设计素材。 本设计大致分为三个部分,一就是制件及模具的参数确定,一就是模具的结构设计,一就是制件的成形分析。
目录 前言.......................................................................................................................... I 一制件工艺分析 (1) 1、1 制件分析 (1) 1、2坯料直径确定 (1) 1、3 拉深成型次数计算 (2) 1、4 凸凹模圆角半径计算 (2) 1、5 拉深深度计算 (4) 1、6 拉深力的计算 (4) 1、7 凸凹模间隙计算 (5) 1、8 凸凹模工件尺寸计算 (5) 1、8、1 凸凹模计算公式 (5) 1、8、2 公差确定 (6) 1、9 凸模通气尺寸 (6) 二拉深模结构设计 (7) 2、1 拉深凸凹模结构 (7) 2、2 模具总体结构的设计 (7) 三Dynaform软件仿真分析 (9) 3、1网格划分 (9) 3、2 毛坯轮廓线计算 (10) 3、3 制件厚度分析 (10) 3、4 主应力分布 (11) 3、5 制件成形情况 (12) 总结 (13) 参考文献 (15) 附表 (16)
模具课程设计.docx
模具设计与制造 ——插头模具设计 姓名:陆峰峰 学号: 0701500226 院系:机械工程及其自动化 指导老师:黄晓华 日期: 2011-1-18
模具设计与制造——插头模具设计 陆峰峰 0701500226 20世纪80年代开始,发达工业国家的模具工业已从机床工业中分离出来,并发展成为独立的工业部门,其产值已超过机床工业的产值。改革开放以来,我国的模具工业发展也十分迅速。近年来,每年都以15%的增长速度快速发展。许多模具企业十分重视技术发展。加大了用于技术进步的投入力度,将技术进步作为企业发展的重要动力。此外,许多科研机构和大专院校也开展了模具技术的研究与开发。模具行业的快速发展是使我国成为世界超级制造大国的重要原因。今后,我国要发展成为世界制造强国,仍将依赖于模具工业的快速发展,成为模具制造强国。 中国塑料模工业从起步到现在,历经了半个多世纪,有了很大发展,模具水平有了较大提高。在大型模具方面已能生产48"(约122CM)大屏幕彩电塑壳注射模具,6.5KG大容量洗衣机全套塑料模具以及汽车保险杠和整体仪表板等塑料模具,精密塑料模方面,以能生产照相机塑料件模具,多形腔小模数齿轮模具及塑封模具。经过多年的努力,在模具CAD/CAE/CAM技术,模具的电加工和数控加工技术,快速成型与快速制模技术,新型模具材料等方面取得了显著进步;在提高模具质量和缩短模具设计制造周期等方面作出了贡献。 尽管我国模具工业有了长足的进步,部分模具已达到国际先进水平,但无论是数量还是质量仍满足不了国内市场的需要,每年仍需进口10多亿美元的各类大型,精密,复杂模具。与发达国家的模具工业相比,在模具技术上仍有不小的差距。今后,我国模具行业应在以下几方面进行不断的技术创新,以缩小与国际先进水平的距离。 (1)注重开发大型,精密,复杂模具;随着我国轿车,家电等工业的快速发展,成型零件的大型化和精密化要求越来越高,模具也将日趋大型化和精密化。 (2)加强模具标准件的应用;使用模具标准件不但能缩短模具制造周期,降低模具制造成本而且能提高模具的制造质量。因此,模具标准件的应用必将日渐广泛。 (3)推广CAD/CAM/CAE技术;模具CAD/CAM/CAE技术是模具技术发展的一个重要里程碑。实践证明,模具CAD/CAM/CAE技术是模具设计制造的发展方向,可显著地提高模具设计制造水平。 (4)重视快速模具制造技术,缩短模具制造周期;随着先进制造技术的不断出现,模具的制造水平也在不断地提高,基于快速成形的快速制模技术,高速铣削加工技术,以及自动研磨抛光技术将在模具制造中获得更为广泛的应用。