250T氧气顶吹转炉主体设备设计及支撑机构设计详解
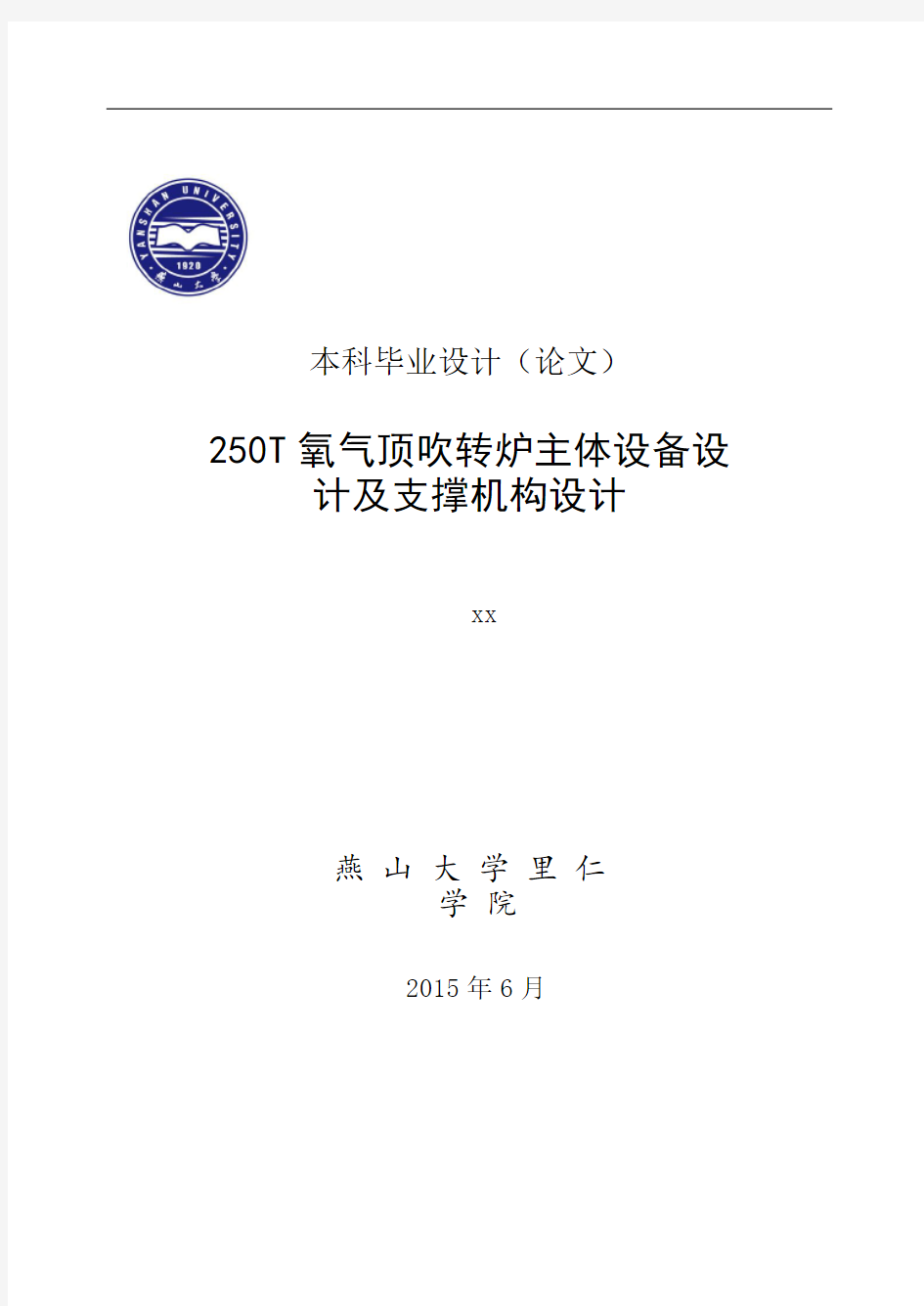

本科毕业设计(论文)
250T氧气顶吹转炉主体设备设计及支撑机构设计
xx
燕山大学里仁
学院
2015年6月
燕山大学
里仁学院
本科毕业设计(论文)
课题名称:250T氧气顶吹转炉
主体设备设计及支撑机构设
计
系别:机械工程系
年级专业:冶炼11-3班
学生姓名: xx
指导教师:许xx
完成日期: 2015年6月
燕山大学里仁学院毕业设计(论文)任务书
学院:里仁学院系级教学单位:机械工程系
学号xxxxx
学生
姓名
xx 专业
班级
冶炼11-3
课题题目250T氧气顶吹转炉主体设备设计及支撑机构设计来源模拟
主要内容1)转炉炉型设计;
2)炉液倾动力矩计算;
3)总装图;
4)炉体与支撑机构设计。
基本要求1) 用计算机完成炉型设计及倾动力矩和转动惯量计算;
2) 总装图和零件图必须满足国标要求;
3) 总图纸量不少于6个A1,至少2张A1手工图;
4) 设计说明书不少于2万字,摘要不少于300字,且汉英对照
5) 翻译相关外文资料不少于5000汉字,参考文献不少于15篇;
参考资料1)转炉连铸工艺设计与程序,贾凌云,冶金工业出版社;
2)宝钢参考资料;
3)谭牧田著《氧气顶吹转炉》。
周次1周2—3周4—7周8—13周14—17周
应完成的内容收集资料
炉型设计
倾动力矩及转
动惯量计算
炉型校核
总体方案
制定
完成总装
图
炉体与托
圈联接结构
设计
托圈结构
设计
完善设计
撰写设计说明书
准备答辩
指导教师:系级教单位审批:
摘要
氧气顶吹转炉主体设备是实现炼钢工艺操作的主体设备,它由炉体、炉体支撑系统、炉体倾动机构以及炉体与托圈联接装置等组成。本次设计针对250T氧气顶吹转炉主体设备和支撑机构进行。
炉体采用A型炉(即锥球型),活炉帽死炉底结构;托圈采用整体式托圈结构,其断面形状选择矩形断面;炉体倾动力矩的计算利用Solidworks 软件绘制实体从而得到炉体、炉液的重心和重量,结合计算公式进行计算;为保证转炉在倾动过程中的安全性,最佳耳轴位置的确定利用全正力矩原则进行;炉体支撑系统选用耳轴与耳轴轴承座的支承方式;倾动机构选用带有扭力杆式缓冲装置的四点才啮合全悬挂式倾动机构;炉体与托圈联接装置采用活节螺栓与止动托座配合的连接结构。
同时对250T氧气顶吹转炉的主体设备和支撑装置中的各个部分进行工作原理的分析和结构设计。并且针对其工作状况和受力情况等进行理论分析和校核。
关键字氧气顶吹转炉主体设备;倾动机构;支撑装置
Abstract
The main equipment in oxygen top-blown converter Is the realization of the main equipment in bof steelmaking process the body of the equipment operation, and it is supported by furnace, furnace system, furnace tilting mechanism, as well as linkage and coil, furnace lining, etc. The design for the main equipment in 250 t oxygen top-blown converter and tilting mechanism.
Furnace adopt type A furnace (namely cone ball type), live hat die hearth furnace structure; Supporting ring with the ring structure, the cross section shape select rectangle cross section; Furnace tilting torque calculation using Solidworks software rendering entities to get the center of gravity and weight of the furnace, furnace, combined with the formula to calculate; In order to ensure the safety in the process of converter in tilting, best trunnion position using the principle of positive moment; Furnace body support system selects the trunnion and trunnion bearing supporting way; Tilting mechanism with torsion bar used buffer device only four meshing full suspension type tilting mechanism; Furnace body and supporting ring connection device adopts eyelet bolt and retaining bracket with the connection of the structure.
At the same time for 250 t oxygen top-blown converter of the individual parts of the body of the equipment and the connecting device for the analysis of the working principle and structure design. And for its working condition and stress distribution of the theory analysis and checking.
Keyword The main equipment in oxygen top-blown converter ;Tilting mechanism ;support device
目录
摘要 ................................................................................................ 错误!未定义书签。Abstract .......................................................................................... 错误!未定义书签。第1章绪论.. (8)
1.1氧气顶吹转炉主体概述 (8)
1.2 250T氧气顶吹转炉主体设备设计总体说明 (9)
第2章转炉炉型的设计 (10)
2.1设计参数 (10)
2.2根据原始数据对转炉炉型进行选择及计算 (11)
2.3对转炉主体进行计算 (12)
2.4 250T转炉炉型设计过程 (12)
第3章水冷炉口的设计 (17)
3.1水冷炉口的结构说明 (17)
3.2水冷炉口的设计与计算 (17)
第4章托圈的设计 (19)
4.1 托圈部件整体说明 (19)
4.2 托圈断面形状的选择 (20)
4.3托圈基本尺寸参数的确定 (21)
4.4托圈制造的技术要求和材料 (22)
第5章倾动力矩的计算 (23)
5.1 倾动力矩简述 (23)
5.2 空炉重量及重心位置计算 (24)
5.2.1计算思想 (24)
5.2.2新炉空炉重量及重心位置 (24)
5.2.3老炉空炉重量及重心位置 (25)
5.2.4新老炉钢液的重心位置的确定 (26)
5.3倾动力矩的计算 (27)
5.3.1.转炉倾动力矩的计算步骤: (27)
5.3.2.转炉倾动力矩的计算数据 (28)
第6章倾动机构的设计 (35)
6.1倾动方案的确定 (35)
6.2电动机的选择 (36)
6.3一级减速器的选择 (38)
6.4二次减速器的设计 (38)
第7章耳轴的设计 (45)
7.1 耳轴概述 (45)
7.2 耳轴的设计 (46)
第8章炉体与托圈连接结构的设计 (47)
8.1活节螺栓连接的设计 (47)
8.2连接装置的设计原理 (48)
结束语 (50)
参考文献 (51)
致谢 (53)
第1章绪论
钢铁行业是衡量整个行业发展的标准,对任何一个国家来说,钢铁产量对其经济的发展有着重大意义。随着第二次行业革命的发展和现代科学技术的提高,对高质量钢的需求不断增加,炼钢工艺和技术不断的进步,因此对于炼钢设备来说也得到了很大的提升空间。过去钢铁行业在一个很长的时间内,以普通的平炉炼钢为首。从1952年氧气顶吹转炉出现以后,使炼钢行业发生了蜕变,使得全球的钢产量得到了迅速的提高。
氧气顶吹转炉炼钢又称L-D炼钢法,上个世纪50年代在奥地利的其所属的林次(Linz)和道纳维次C Donawitz)两钢厂中由V oest-Alpine联合公司试验成功并在投入行业生产,氧气顶吹转炉的别称为L-D炼钢炉,其中的L 和D分别是林茨和道纳维茨的开头字母。氧气顶吹转炉炼钢出现后,在全球得到了快速的发展,各国炉钢的产量也得到了迅速的提升,上世纪60年代末的产钢量为20300万吨。其中,L-D转炉炼钢占全球总量的37.5%。L-D 转炉炼钢能够有这样的结果,其原因主要在与传统炼钢方法相比,它具有一系列的优势。包括有: (1)产量高(2)质量高,性能好(3)原材料消耗少,热效率高,钢的成本低(4)对原材料的适应性强(5)基础设施投资少,建设效率高(6)对于实现自动化有着重要作用,并能和其他炼钢工艺能很好的结合。进入七十年代后,L-D转炉炼钢法已逐渐取代当时世界上其他的传统炼钢方法,而且L-D转炉炼钢法的技术逐渐成熟。
1.1 氧气顶吹转炉主体概述
LD炼钢炉是实现炼钢工艺操作的主体设备,它由转炉主体、转炉主体支撑装置和转炉主体倾动机构等组成。转炉主体的作用是盛装铁水并进行有氧吹炼,它通过托圈和耳轴支撑在其支座上,利用倾动装置可以0.1~1.5
转/分的速度随耳轴、托圈在正负360°内转动,以满足装炼钢,出渣,维修等的需要。倾动系统是由电动机、减速机、扭力杆系统和制动保护器等组成。
1.2 250T氧气顶吹转炉主体设备设计总体说明
本次设计内容包括转炉主体以及托圈连接机构。
在本设计中,转炉炉型采用A型,采用死炉底活炉帽的结构形式。这种结构不但简单,并且相比传动的炼钢炉来说质量轻。最重要的是制造简单,具有较高可靠性,并符合经济指标。
水冷炉口采用铸铁埋管式水冷炉口,这个结构是不易被烧透而导致钢水的泄漏,从而能达到延长炉体寿命的效果,缺点是不容易在泄漏后进行焊接修补,并使多。
为了保证水冷炉口和炉体之间连接强度,应采的形式是用π形卡板焊接而成。
本设计采用隔热板和挡渣板来保护炉体,使其受到较少的热辐射和腐蚀。由于炉渣安息角45-50度,所以取各板倾斜角度50度,以利于炉渣下滑。
第2章 转炉炉型的设计
2.1 设计参数
工艺参数
平均出钢量:吨250
供氧强度:分吨标米./5.33
供氧压力:2
/10厘米公斤力 吹氧时间:分钟17
转炉主体支承系统分为两部分,主动侧支承系统直接固定在地面上,从动侧支承装置设计为铰链式轴承支座结构,以适应托圈和耳轴的热膨胀。
转炉主体采用二支点方式支承在托圈上,其支承装置采用球面带销螺栓将转炉主体和托圈连接在一起。整个连接装置由两部分组成:一部分是托圈上三个球面带销活节螺栓与炉壳上部连接支承法兰组成的倾动承载部分,承受转炉主体在垂直位置和倾动过程中的转炉主体载荷;另一部分是安装在两耳轴部位的托圈上下的两组止动托座,在转炉主体倾动到水平位置时将载荷传递给托圈。连接设备可以满足性能要求的连接设备,且结构简单,制造、安装容易,维护方便,是一种简单可靠并且值得推广的设备。
2.2 根据原始数据对转炉炉型进行选择及计算
a-筒球型;b-锥球型;c-截锥型
图2-1 转炉常用炉型示意图
(a)筒球型炉型:该炉型由圆筒型的炉身、球缺型的炉底和截锥型的炉帽组成。其特点是结构简单、砌砖较容易,反应比较充分,适合中型转炉。
(b)锥球型炉型:该炉型由倒置截锥体、球缺体组成的炉底和圆筒型的炉身以及截锥型的炉帽组成。其特点是容量大,反应面积大、反应充分,适用于吹炼高磷铁水,但炉底砌砖比较复杂,适合大型转炉。
(c)截锥型炉型:该炉型由倒置的截锥体炉底、圆筒型的炉身和截锥型的炉帽组成。其特点是形状简单,炉底砌砖方便,但反应不太充分,适合小型转炉。
2.3 对转炉转炉主体进行计算(炉衬、炉壳厚度、炉帽、炉
身、炉底尺寸);
不合不设定炉型参数
(V/T,h/d,d1/d ,d3/d,r/d,α1,T1,T2,T3)
计算熔池直径d
计算炉型内膛尺(h,d1,d3,r,V)
验证V/T 合格
计算炉衬尺寸
格
计算炉壳外径
验证高宽比
结束
合格
合格
2.4 250T 转炉炉型设计过程
本次设计中,转炉炉型采用A 型,炉帽为截锥形,炉身为圆筒形,炉底为球缺形。
(1)熔池直径计算
供氧强度为:分吨标米./5.33
cm
p Q p d g g chD 38.1518.13285
.00
285
.0=-?=--275
2501.11.1=?=?=o G G G 为金属装容量
4.0)0
5.06
6.0(G D R ?±= 为熔池表面直径R D
m D R 71.6-77.5275)05.066.0(4.0=?±= m D R 8.5为取
氧枪出口直径计算 ;
/9.2260/1.12505.3429.160/000秒公斤=???=??=G q Q γ
单孔枪头出口直径
2
/10厘米公斤力取为氧气工作压力,一般g P
而大型转炉采用三孔枪头:
氧枪枪头出口面积:
氧枪出口氧流速度:
氧枪理论工作高度
cm
d d chD
chs 88.83
==
2
2
83.1854
3cm d F chs chs =??
=π
s
m F G
q W chs
c /25.86360
10)(
4
00=??=
氧气与钢液相遇直径:
(4)理论熔池直径:
mm
W d H c chD R 19313.50=?=
(5)理论氧气穿透深度:
取K=1.893,则mm
c 111
d =
采用三孔枪头,其中m
h h R chu 774.0~48.0)4.025.0(=-=
取mm h chu 500=,符合最大范围。代入方程两侧满足平衡条件。 (6)炉底、炉帽、炉口、出钢口等尺寸的确定 250T 氧气顶吹转炉的炉型选取A 型,取球缺半径
(0.80.9) 4.64~5.22R R D m
=-=, 取R=5.2m 设球缺高884h mm = 其球缺部分体
m D R
H 64.09
d ==
m
d d h chD
H 54.1tan 20=?-=αG
g
c
chu chu p d h h h γ4
.39.204)(1013?+?=-chD
c d k d 1d c =
氧枪枪头喉口直径其中
铁水体积
3
/39.28t Y V G m εγ==
铁水在炉身高度 2
1.0314t Q
t R
V V h m D π-==?
则实际熔池高度为 1.915R t H h h m =+= 0.261chu R h H = 符合要求
炉口直径
(0.430.53) 2.494~3.074
LK R d D =-=,取3LK d m
=
出钢口直径63 1.7522.37ZG d Q mm =+?=,取22ZG d cm = 炉帽高度1
()tan 2.6832MA R LK MA H D d m α=-=,取62.5MA α=°
取 2.68MA H m
= 炉帽体积:223
1()42.1212MA
MA R R LK LK H V D D d d m π?=+?+= 2
3
22 2.474MA LK MA V d h m π==
3
44.6MA V m =
炉身尺寸确定
取转炉工作容积与炉容量之比V/T=0.86 则V=236.53m
炉身体积3
155.08sh MA T V V V V m =--=
炉身高2
5.864sh sh R V h m D π==? ,取 5.9sh h m =
则实际体积3
223.77MA Q sh V V V V m =++=
炉衬尺寸的确定
根据具体的设计要求和工艺要求的需要,选取炉衬厚度如下表所示:
工作层
填充层
永久层
钢板
3
204.12)3
(m h
R h V Q =-??=π
炉身部分(mm) 900 60 148 85 炉底部分(mm) 700
60 450 85 材料
焦油白云石 焦油镁砂 镁砂
15MnVg 密度(吨/立方米)
2.85
2.6
2.8
7.85
炉壳外径的确定:
2122δδ++=R K D D
为炉壳钢板厚度为炉衬厚度,式中21δδ 下面确定炉壳钢板的厚度:
转炉炉壳部分材料选择的一般准则是:要有良好的韧性和弹性,有良好的工艺性能,较高的抗疲劳强度;另外根据经济指标来选择材料以符合成本的经济性。
目前炼钢转炉发展和设计的趋势是使炉壳各部分的厚度相同,这能使制造工艺的简化以及降低边界效应有很大的意义。根据转炉设计的安全性原则和经验,取钢板厚度为85mm ,材料为抗高温抗腐蚀的碳素钢和抗疲劳强度高的低合金钢。
因此,m D K 072.8=
水冷炉口高取350毫米,则炉壳高m 259.11=Z H ,372.1/=K Z D H 符合要求。
第3章 水冷炉口的设计
3.1 水冷炉口的结构说明
水冷炉口基本有两种结构形式,即水箱式和铸铁埋管式。
水箱式水冷炉口为钢板焊接,它冷却强度大,工作效果好,易于制造,并且漏水时,可以补焊,维修方便。
铸铁埋管式水冷炉口,往返曲折的钢管埋铸在铸铁炉口中,另外还有蛇形,螺旋曲型的钢管埋铸在铸铁中的结构。
铸铁埋管式水冷炉口比水箱式水冷炉口不易烧穿漏水,使用寿命长,但是漏水不易焊接,且制造繁琐。
水冷炉口地寿命,根据国内实践,钢板焊接的水箱式水冷炉口大致需要半年左右更换一次,而铸铁埋管式是半年到一年的时间更换一次。
水冷炉口与炉壳的连接形式,在我国多采用“π”型卡板焊接的形式。为了拆卸方便,曾采用过螺栓连接,但由于炉口与炉壳变形不一样,拆卸后再装配时,螺栓孔不易对正。有的在使用过程中讲螺钉拉断,也有的由于炉口喷溅讲螺钉粘接,更换时仍需用火焰切割。实践表明,螺钉连接不如“π”型卡板适用可靠。
本次设计采用埋管式水冷炉口,材料选用球墨铸铁QT40-10。水冷炉口与炉壳的连接采用“π”型卡板16块厚度为30毫米的钢板进行连接。
3.2 水冷炉口的设计与计算
炉口承受炉气高温作用,其吸热强度q 可按下列数据考虑:
大型转炉
时米千卡??-?2
55102.1101 中型转炉
时米千卡??-?244109108 小型转炉
时米千卡??-?244107106 受热面积可以按炉口内侧面积和顶面面积之和计算。
(1)炉口冷却水用量的计算
时公斤j
ch t t F Q -?=q ζ
式中 ζ---水冷炉口材料的辐射黑度
此次设计中,水冷炉口材料选用球墨铸铁,ζ取0.90。 水冷炉口的吸热强度。---q
此次设计中,250吨LD 炼钢转炉为大型转炉,故时。米千卡取??25/101.1q
水冷炉口的传热面积。---F
此次设计中,水冷炉口高mm 150 m R 5.11= m R 592.22=
炉口内侧面积 2
11 1.60220.11.73.142h 2米=???==R F π
顶面面积
:
222212
220356.12)7.15925.2(1416.3米)(=-?=-=R R F π
所以,受热面积 2
216378.13米=+=F F F
根据安全原则考虑,水冷炉口受热不仅是由内侧和顶面带来的热量,在
外侧和下定面均有热传导和热辐射,因此应在计算时乘以一个安全系数K 。在此次设计中K 取值为1.4.
冷却水进温度、----t ch j t ,此次设计中,℃
℃,50t 30t ==ch j
由以上分析,炉口冷却水用量
时
公斤/1075.630
506378.13101.19.0q 55?=-???=-?=j ch t t F Q ζ
进水管直径的计算
铸铁埋管式水冷炉口,进、出水管直径取值为一致。
πνγKQ d 410*3615=
式中,Q ——水冷炉口需要的水量。 由以上的计算,Q=6.75x10000公斤/时 K ——安全系数。 由以上的计算,K=1.3 ν——冷却水流速 γ——冷却水比重 水的比重:
3/1米吨=γ
取水压:
时厘米公斤力2/4=P ,
v=3米/秒
由以上分析,进、出水管直径
πνγKQ d 410*3615= 毫米米101101.01*3*1416.310*75.6*3.1*410*3614
5
===
查取有关手册取低压流体输送焊接管(GB3091-82)取4in 管,内径100mm ,可以满足要求。
第4章 托圈的设计
4.1 托圈部件整体说明
托圈是转炉的重要承载和传动部件,工作过程中,除承受炉体、钢液及
炉体附件的静载荷和传递倾动力矩外,还承受频繁启、制动产生的动负荷,以及来自炉体、钢水罐、渣罐、烟罩及喷溅物等的热辐射、热传导所产生的热负荷。因此,托圈应具有足够的强度和刚度。
本次设计采用整体托圈结构。托圈是一个整体的钢板焊接的箱形结构,有四个部分,即由驱动侧耳轴座、从动侧耳轴座、出钢侧托圈瓣、装料侧托圈瓣焊接成一个整体托圈的。
托圈耳轴座和耳轴铸成一体,为了减少托圈内外腹板与耳轴座联接处,因为刚度的急剧变化而引起的应力集中,所以将耳轴轴承座与内外腹板连接部位做成叉型过渡形式,并且和腹板与腹板焊接处的尺寸相同,向着缓慢的增厚到耳轴附近处。
同样,由于连接板刚度急剧变化,并且为了减少应力集中引起的连接板刚度,因此距离焊缝的地方加上隔离板。隔离板焊在耳轴两侧各一块儿,其焊接位置在托圈中间。为了增加腹板的刚度和强度,在两耳轴同一侧的两块隔板之间应该焊有八块筋板。
为了增强托圈的刚度以及炉壳与托圈的冷却效果,应当在每两块加强筋
中间焊接上穿通内外腹板的圆管。为了减少钢水和炉渣带来的的辐射热对托圈的作用,在出钢口附近的托圈外腹板上应有楔形块儿块和螺钉来联接挡板。
另外,由于托圈各部位受热不均,因此会导致高于机械载荷应力的热应力出现。该托圈采用了水冷措施,从水冷炉口,炉顶钢板,渣裙排出的冷却水,进排水集水箱由驱动侧耳轴座上部进入托圈,再由靠近从动侧耳轴座的外腹板上部的排水管引出。托圈通水冷却可使托圈各部位温度趋于均匀,降低温度梯度。托圈和炉体连接方式,在托圈上利用吊耳,吊耳成120°均匀分配来实现炉体和托圈之间的连接。
两耳轴侧的人孔用十焊接横隔板的对接焊缝和腹板上下盖板与耳轴座连接处的内焊缝。
4.2 托圈断面形状的选择
托圈的断面结构大致有两种结构,其中包括开口和闭口侧面两种形式。闭口断面多为矩形,开口断面有C形和反C形两种。反C形开口断面是指开口向着炉体的断面。
托圈断面的几种结构形式,如下图所示
现在,托圈断面通常会采用矩形断面结构,其中a所示。在这种托圈断面中,切应力以均匀环流的方式分布在托圈上。同时开口断面的抗扭刚度比矩形断面结构的要小很多。尤其是大型转炉托圈的矩形封闭断面结构的热应力可以通入冷却水来降低。
世界氧气顶吹转炉炼钢技术发展史
世界氧气顶吹转炉炼钢技术发展史 氧气顶吹转炉炼钢(oxygen top blown converter steelmaking)由转炉顶部垂直插入的氧枪将工业纯氧吹入熔池,以氧化铁水中的碳、硅、锰、磷等元素,并发热提高熔池温度而冶炼成为钢水的转炉炼钢方法。它所用的原料是铁水加部分废钢,为了脱除磷和硫,要加入石灰和萤石等造渣材料。炉衬用镁砂或白云石等碱性耐火材料制作。所用氧气纯度在99%以上,压力为0.81~1.22MPa(即8~12atm)。 简史 空气底吹转炉和平炉是氧气转炉出现以前的主要炼钢设备。炼钢是氧化熔炼过程,空气是自然界氧的主要来源。然而空气中4/5的气体是氮气,空气吹炼时,这样多的氮气在炉内穿行而过,白白带走大量的热且有部分氮溶解在铁液中,成为恶化低碳钢品质的重要原因。平炉中,氧在用于燃烧燃料之后,过剩的氧要通过渣层传入钢水,所以反应速率极慢,这也就增加了热损失。因此,直接把氧气吹入熔池炼钢,成为许多冶金学家向往的目标。早在19世纪,现代炼钢法的创始人贝塞麦(H.Bessemer)就有了纯氧炼钢的设想,但因没有大量氧气而未进行试验。20世纪20年代后期,以空气液化和分馏为基础的林德一弗兰克(Linde—Frankel)制氧技术开发成功,能够生产可供工业使用的廉价氧气,氧气炼钢又为冶金界所注意。从1929年开始,柏林工业大学的丢勒尔教授(R.Durrer)在实验室中研究吹氧炼钢,第二
次世界大战开始后转到瑞士的冯?罗尔(V.Roll)公司继续进行研究。1936~1939年勒莱普(O.Lellep)在奥伯豪森(Oberhausen)进行了底吹氧炼钢的试验,由于喷嘴常损坏未能成功。1938年亚琛(Aachen)工业大学的施瓦茨(C.V.Schwarz)提出用超音速射流向下吹氧炼钢,并在实验室进行了试验,将托马斯生铁吹炼成低氮钢,但因熔池浅而损坏了炉底。1948年丢勒尔(R.Durrer)等在冯?罗尔(VonRoll)公司建成2.5t的焦油白云石衬的试验转炉,以450的斜度将水冷喷嘴插入铁水吹氧炼钢,无论贝塞麦生铁或托马斯生铁都能成功炼成优质钢水,而且认识到喷嘴垂直向下时,最有利于喷嘴和炉衬的寿命。这样就最后完成了转炉吹氧炼钢的实验室试验。从实验室研究向工业化试验的进一步发展是由奥地利的沃埃施特(VOEST)公司完成的。第二次世界大战后奥地利面临重建钢铁工业的需要,该国缺少废钢使得平炉或电炉炼钢法缺乏竞争力。沃埃施特公司注意到丢勒尔的试验,决心开发一个具有竞争力的新的炼钢方法。1949年5月在奥地利累欧本(Leoben)开了一次氧气炼钢的讨论会,决定冯?罗尔、曼内斯曼(Mannesmann)、阿尔派(ALPINE)和沃埃施特4个公司协作,在沃埃施特的林茨(Linz)钢厂作进一步的试验。1949年6月在林茨建成2t顶吹氧试验转炉,由苏埃斯(T.Suess)和豪特曼(H.Hauttmann)负责,在丢勒尔参与下,成功地解决了合适的氧气压力、流量和喷嘴与熔池面距离等工艺操作问题。之后迅速建立15t试验转炉,广泛研究新方法所冶炼钢的品质。由于钢的质量很好而且炼钢工艺的
100t顶底复吹转炉炉型设计说明书
目录 前言 (1) 一、转炉炉型及其选择 (1) 二、炉容比的确定 (3) 三、熔池尺寸的确定 (3) 四、炉帽尺寸的确定 (5) 五、炉身尺寸的确定 (6) 六、出钢口尺寸的确定 (6) 七、炉底喷嘴数量及布置 (7) 八、高径比 (9) 九、炉衬材质选择 (9) 十、炉衬组成及厚度确定 (9) 十一、砖型选择 (12) 十二、炉壳钢板材质与厚度的确定 (14) 十三、校核 (15) 参考文献 (16)
专业班级学号姓名成绩 前言: 转炉是转炉炼钢车间的核心设备。转炉炉型及其主要参数对转炉炼钢的生产率、金属收的率、炉龄等经济指标都有直接的影响,其设计是否合理也关系到冶炼工艺能否顺利进行,车间主厂房高度和与转炉配套的其他相关设备的选型。所以,设计一座炉型结构合理,满足工艺要求的转炉是保证车间正常生产的前提,而炉型设计又是整个转炉车间设计的关键。 设计内容:100吨顶底复吹转炉炉型的选择与计算;耐火材料的选择;相关参数的选择与计算。 一、转炉炉型及其选择 转炉有炉帽、炉身、炉底三部分组成。转炉炉型是指由上述三部分组成的炉衬内部空间的几何形状。由于炉帽和炉身的形状没有变化,所以通常按熔池形状将转炉炉型分为筒球形、锥球型和截锥形等三种。炉型的选择往往与转炉的容量有关。
(1)筒球形。熔池由球缺体和圆柱体两部分组成。炉型形状简单,砌砖方便,炉壳容易制造,被国内外大、中型转炉普遍采用。 (2)锥球型。熔池由球缺体和倒截锥体两部分组成。与相同容量的筒球型比较,锥球型熔池较深,有利于保护炉底。在同样熔池深度的情况下,熔池直径可以比筒球型大,增加了熔池反应面积,有利于去磷、硫。我国中小型转炉普遍采用这种炉型,也用于大型炉。 (3)截锥形。熔池为一个倒截锥体。炉型构造较为简单,平的熔池底较球型底容易砌筑。在装入量和熔池直径相同的情况下,其熔池最深,因此一般不适用于大容量炉,我国30t以下的转炉采用较多。不过由于炉底是平的,便于安装底吹系统,往往被顶底复吹转炉所采用。 顶底复吹转炉炉型图 顶底复吹转炉炉型的基本特征如下: (1)吹炼的平稳和喷溅程度优于顶吹转炉,而不及底吹转炉,故炉子的高宽比略小于顶吹转炉,却大于底吹转炉,即略呈矮胖型。 (2)炉底一般为平底,以便设置喷口,所以熔池常为截锥型。 (3)熔池深度主要取决于底部喷口直径和供气压力,同时兼顾顶吹氧流的穿透
顶吹转炉
太原科技大学 课程设计说明书 设计题目: 50t 氧气顶吹转炉设计 设计人:郭晓琴 指导老师:杨晓蓉 专业:冶金工程 班级:冶金工程081401 学号: 200814070105 材料科学与工程学院 2011年12月30 日
目录 摘要................................................ 错误!未定义书签。第一章绪论................................................ 错误!未定义书签。 1.1 氧气顶吹转炉炼钢的发展概况......................... 错误!未定义书签。 1.2 氧气顶吹转炉炼钢的优点............................. 错误!未定义书签。 1.3 转炉炼钢生产技术发展趋势........................... 错误!未定义书签。第二章炉型尺寸计算........................................ 错误!未定义书签。 2.1转炉炉型及其选择.................................... 错误!未定义书签。 2.2转炉炉型尺寸计算.................................... 错误!未定义书签。 2.2.1 熔池尺寸...................................... 错误!未定义书签。 2.2.2 炉容比(容积比).............................. 错误!未定义书签。 2.2.3炉帽尺寸...................................... 错误!未定义书签。 2.2.4炉身尺寸...................................... 错误!未定义书签。 2.2.5出钢口尺寸.................................... 错误!未定义书签。第三章氧气顶吹转炉耐火材料................................ 错误!未定义书签。 3.1 炉衬的组成和材质的选择............................. 错误!未定义书签。 3.2炉衬厚度的确定...................................... 错误!未定义书签。第四章氧气顶吹转炉金属构件的确定.......................... 错误!未定义书签。 4.1炉壳组成及结构形成................................. 错误!未定义书签。 4.2炉壳钢板材质与厚度的确定 (7) 4.3支撑装置 (7) 4.3.1 托圈......................................... 错误!未定义书签。 4.3.2炉衬的组成和材质的选择....................... 错误!未定义书签。 4.3.3耳轴及其轴承................................. 错误!未定义书签。 4.4倾动机构........................................... 错误!未定义书签。 4.5高径比的核定....................................... 错误!未定义书签。参考文献.............................................................. - 12 -
氧气顶吹转炉炼钢
R.D.佩尔克等著,邵象华、楼盛赫等译校:《氧气顶吹转炉炼钢》,冶金工业出版社,北京,(上册)1980,(下册)1982。(R.D.Pehlke,ed., BOF Steelmaking,AIME,1974~1977.) 氧气顶吹转炉炼钢 责任编辑:苏方来源:成都钢铁网2008年06月20日 氧气顶吹转炉炼钢(oxygen top blown converter steelmaking) 由转炉顶部垂直插入的氧枪将工业纯氧吹入熔池,以氧化铁水中的碳、硅、锰、磷等元素,并发热提高熔池温度而冶炼成为钢水的转炉炼钢方法。它所用的原料是铁水加部分废钢,为了脱除磷和硫,要加入石灰和萤石等造渣材料。炉衬用镁砂或白云石等碱性耐火材料制作。所用氧气纯度在99%以上,压力为0.81~1.22MPa(即8~12atm)。 简史空气底吹转炉和平炉是氧气转炉出现以前的主要炼钢设备。炼钢是氧化熔炼过程,空气是自然界氧的主要来源。然而空气中4/5的气体是氮气,空气吹炼时,这样多的氮气在炉内穿行而过,白白带走大量的热且有部分氮溶解在铁液中,成为恶化低碳钢品质的重要原因。平炉中,氧在用于燃烧燃料之后,过剩的氧要通过渣层传入钢水,所以反应速率极慢,这也就增加了热损失。因此,直接把氧气吹入熔池炼钢,成为许多冶金学家向往的目标。早在19世纪,现代炼钢法的创始人贝塞麦(H.Bessemer)就有了纯氧炼钢的设想,但因没有大量氧气而未进行试验。20世纪20年代后期,以空气液化和分馏为基础的林德一弗兰克(Linde —Frankel)制氧技术开发成功,能够生产可供工业使用的廉价氧气,氧气炼钢又为冶金界所注意。从1929年开始,柏林工业大学的丢勒尔教授(R.Durrer)在实验室中研究吹氧炼钢,第二次世界大战开始后转到瑞士的冯?罗尔(V.Roll)公司继续进行研究。1936~1939年勒莱普(O.Lellep)在奥伯豪森(Oberhausen)进行了底吹氧炼钢的试验,由于喷嘴常损坏未能成功。1938年亚琛(Aachen)工业大学的施瓦茨(C.V.Schwarz)提出用超音速射流向下吹氧炼钢,并在实验室进行了试验,将托马斯生铁吹炼成低氮钢,但因熔池浅而损坏了炉底。1948年丢勒尔(R.Durrer)等在冯?罗尔(V onRoll)公司建成2.5t的焦油白云石衬的试验转炉,以450的斜度将水冷喷嘴插入铁水吹氧炼钢,无论贝塞麦生铁或托马斯生铁都能成功炼成优质钢水,而且认识到喷嘴垂直向下时,最有利于喷嘴和炉衬的寿命。这样就最后完成了转炉吹氧炼钢的实验室试验。从实验室研究向工业化试验的进一步发展是由奥地利的沃埃施特(VOEST)公司完成的。第二次世界大战后奥地利面临重建钢铁工业的需要,该国缺少废钢使得平炉或电炉炼钢法缺乏竞争力。沃埃施特公司注意到丢勒尔的试验,决心开发一个具有竞争力的新的炼钢方法。1949年5月在奥地利累欧本(Leoben)开了一次氧气炼钢的讨论会,决定冯?罗尔、曼内斯曼(Mannesmann)、阿尔派(ALPINE)和沃埃施特4个公司协作,在沃埃施特的林茨(Linz)钢厂作进一步的试验。1949年6月在林茨建成2t顶吹氧试验转炉,由苏埃斯(T.Suess)和豪特曼(H.Hauttmann)负责,在丢勒尔参与下,成功地解决了合适的氧气压力、流量和喷嘴与熔池面距离等工艺操作问题。之后迅速建立15t试验转炉,广泛研究新方法所冶炼钢的品质。由于钢的质量很好而且炼钢工艺的效率很高,1949年末该公司决定在林茨投资建设世界第一个氧气顶吹转炉工厂。并命名该炼钢法为LD法。林茨的30tLD转炉工厂于1952年11月投产。翌年春季第2个30tLD转炉工厂在奥地利多纳维兹([)onawitz)建成投产。1950年由苏埃斯申请得到专利权。推动炼钢工业再次大变革的氧气顶吹转炉炼钢法登上了历史舞台。该法问世后,数十年内迅速取代了平炉炼钢而成为世界上最主要的炼钢方法。在北美,美国是平炉炼钢大国,有平炉熔池吹氧的经验。美国又是第二次世界大战的最大战胜国,工业基础雄厚。在得知转炉氧气炼钢的信息后,美国麦克劳斯(McLouth)公司和加拿大多法斯柯(DOFASCO)公司于1954年各迅速建成一个35t氧气顶吹转炉车间并投产。随后
氧气顶吹转炉炼钢终点碳控制的方法
氧气顶吹转炉炼钢终点碳控制的方法 终点碳控制的方法有三种,即一次拉碳法、增碳法和高拉补吹法。 一次拉碳法 按出钢要求的终点碳和终点温度进行吹炼,当达到要求时提枪。 这种方法要求终点碳和温度同时到达目标,否则需补吹或增碳。一次拉碳法要求操作技术水平高,其优点颇多,归纳如下: (1) 终点渣TFe含量低,钢水收得率高,对炉衬侵蚀量小。 (2) 钢水中有害气体少,不加增碳剂,钢水洁净。 (3) 余锰高,合金消耗少。 (4) 氧耗量小,节约增碳剂。 增碳法 是指吹炼平均含碳量≥0.08%的钢种,均吹炼到ω[C]=0.05%~0.06%提枪,按钢种规范要求加入增碳剂。增碳法所用碳粉要求纯度高,硫和灰分要很低,否则会玷污钢水。 采用这种方法的优点如下: (1)终点容易命中,比“拉碳法”省去中途倒渣、取样、校正成分及温度的补吹时间,因而生产率较高; (2)吹炼结束时炉渣Σ(FeO)含量高,化渣好,去磷率高,吹炼过程的造渣操作可以简化,有利于减少喷溅、提高供氧强度和稳定吹炼工艺; (3)热量收入较多,可以增加废钢用量。 采用“增碳法”时应严格保证增碳剂质量,推荐采用C>95%、粒度≤10毫米的沥青焦。增碳量超过0.05%时,应经过吹Ar等处理。 高拉补吹法 当冶炼中、高碳钢钢种时,终点按钢种规格稍高一些进行拉碳,待测温、取样后按分析结果与规格的差值决定补吹时间。 由于在中、高碳(ω[c]>0.40%)钢种的碳含量范围内,脱碳速度较快,火焰没有明显变化,从火花上也不易判断,终点人工一次拉碳很难准确判断,所以采用高拉补吹的办法。用高拉补吹法冶炼中、高碳钢时,根据火焰和火花的特征,参考供氧时间及氧耗量,按所炼钢种碳规格要求稍高一些来拉碳,使用结晶定碳和钢样化学分析,再按这一碳含量范围内的脱碳速度补吹一段时间,以达到要求。高拉补吹方法只适用于中、高碳钢的吹炼。根据某厂30 t 转炉吹炼的经验数据,补吹时的脱碳速度一般为0.005%/s。当生产条件变化时,其数据也有变化。
氧气底吹转炉炼钢
通过转炉底部的氧气喷嘴,把氧气吹入炉内熔池进行炼钢的方法。 简史?? 氧气底吹转炉始于改造托马斯转炉(见托马斯法)。西欧富有高磷铁矿资源,用它炼出的生铁含磷高达1.6%~2.0%。以这种高磷铁水为原料的传统炼钢方法即托马斯法,也即碱性空气底吹转炉法,其副产品钢渣可作磷肥。对于高磷铁水,托马斯法过去一直是综合技术经济指标较好的一种炼钢方法。直至20世纪60年代,西欧还存在年产能力约1000万t钢的托马斯炉。但作为炼钢氧化剂的空气,其中氧气仅占1/5,其余4/5的氮气不仅吸收大量热量,并使钢中氮含量增加,引起低碳钢的脆性。为此人们一直试图用纯氧代替空气,以改进钢的质量和提高热效率。但采用氧气后,化学反应区的温度很高,底吹所用氧气喷嘴很快被烧坏。1965年加拿大空气液化公司为了抑制氧气炼钢产生的大量污染环境的褐色烟尘,试验在氧枪外层通气态或液态冷却剂,取得了预期效果,并同时解决了氧枪烧损快的问题。1967年联邦德国马克西米利安冶金厂(Maximilianshttte)引进了这项技术,以丙烷为氧喷嘴冷却剂,用于改造容量为24t的托马斯炉,首先试验成功氧气底吹转炉炼钢,取名OBM 法。1970年法国文代尔一西代尔公司(Wendel—Sidelor?? Co.)的隆巴(Rombas)厂以燃料油为氧喷嘴冷却剂,也成功地将24t托马斯炉改造成氧气底吹转炉,称为LWS法。随后用氧气底吹氧枪改造的托马斯炉在西欧得到迅速推广,炉容量大多为25~70t,用于高磷铁水炼钢,脱磷仍在后吹期完成,副产品钢渣作磷肥。1971年美国钢铁公司(U.S.Steel? Corp.)引进COBM法,为了解决经济有效地吹炼低磷生铁和设备大型化问题,在该公司炼钢实验室的30t试验炉上作了系列的中间试验,增加了底部吹氧同时喷吹石灰粉的系统,吹炼低磷普通铁水可在脱碳同时完成脱磷,称为Q—BOP法。随后,在菲尔菲德(Fairfield)厂和盖里(Gary)厂分别建设了两座200tQ—BOP炉和3座235tQ—BOP炉。前者取代原有平炉,后者取代正在建设的氧气顶吹转炉。从而实现了氧气底吹转炉的大型化,并扩大了应用范围。到20世纪70年代末氧气底吹转炉年产钢能力总计约3500万t。在中国,1973年钢铁研究总院在300kg 氧气底吹试验转炉上进行了底吹氧气和石灰粉的炼钢试验。随后,该院与北京钢铁设计研究总院及有关单位合作,在唐山钢厂、首都钢铁公司、济南第二钢厂及马鞍山钢铁公司先后完成了5t氧气底吹转炉炼钢的工业性试验。同时还进行了铁水提铌、提钒的试验。后由于顶底复吹转炉的出现和发展而停止。 工艺特点?? 氧气底吹转炉所用炉衬耐火材料、原材料及基本工艺和氧气顶吹转炉相同或相似。主要金属炉料是铁水和约10%~25%的废钢。供氧压力约为0.6~1.0MPa(6~10atm)。每炉吹炼时间(吹氧时间)一般为15~20min。每炉冶炼周期(本炉出钢到下炉出钢时间)一般为30~40min。氧耗量为50~60m3/t。主要工艺特点是从转炉底部供氧。(见图1)装有氧喷嘴的转炉炉底可以拆卸、更换。氧喷嘴由同心的双层套管组成。内层为铜管或不锈钢无缝管,外层用碳素钢无缝管。内层通氧气,并可同时喷吹石灰粉。两层套管之间的间隙通冷却剂。冷却剂通常为气态或液态的碳氢化合物,如天然气、丙烷或燃料油等。依靠碳氢化合物裂解吸热,并在氧流周围形成保护气膜,以及高速气流带走热量,以降低氧喷嘴及其附近反应区的温度,达到保护氧气喷嘴、减缓烧损的目的。为了使熔池搅拌均匀,反应界面大,吹炼平稳,并避免氧喷嘴个数少、直径过大、氧流比较集中而导致氧气穿透熔池,因此采用多支氧喷嘴,分散供氧。每支氧喷嘴的内径尺寸不超过熔池深度的1/35。这个数据适用于吹氧压力约为0.5~1MPa的中、小型转炉。例如:容量为30t的转炉,熔池平均深度为700mm,据此每支氧喷嘴最大内径为20mm;氧气压力为0.8MPa;氧气含石灰粉为1~2kg/m3,则氧气流量约为130m3/h?cm2;耗氧量为60m3/t;吹炼时间最多为20min。因此可以算出:需要供氧流量为5400m3/h,所需氧喷嘴内管总横截面约为42cm2,所需氧喷嘴数为14个。大型氧气底吹转炉的氧喷嘴直径与熔池深度之比可以大于上述数据,一般不超过熔池深度的1/15。例如200~240t氧气底吹转炉所用氧喷嘴数可采用10~16个。氧喷嘴之间以及氧喷嘴与炉壁之间要有适当间距,使熔池搅拌均匀和反应平稳,并减轻对炉衬耐火材料的侵蚀。氧喷
氧气顶吹转炉设计
3.1 转炉炉型设计3.1.1 转炉炉型设计概述(1)公称容量及其表示方法 公称容量(T),对转炉容量大小的称谓,即平时所说的转炉的吨位。它是转炉生产能力的主要标志和炉型设计的重要依据。目前国内外对公称容量的含义的解释还很不统一,归纳起来,大体上有以下三种表示方法: 1)以平均金属装入量(t)表示; 2)以平均出钢量(t)表示; 3)以平均炉产良坯量(t)表示。 在一个炉役期内,炉役前期和后期的装入量或出钢量不同,随着吹炼的进行,炉衬不断地受到侵蚀,熔池不断扩大,装入量增大,所以三种表示方法都是以其平均容量来表示。 这三种表示方法各有其优缺点,以平均金属装入量表示公称容量,便于进行物料平衡和热平衡计算,换算成新炉装入量时也比较方便。 以平均炉产良坯量表示公称容量,便于车间生产规模和技术经济指标的比较,但是在进行炉型设计时需做较复杂的换算。 以平均出钢量表示公称容量则介于两者之间,其产量不受操作方法和浇铸方法的影响,便于炼钢后步工序的设计,也比教容易换算成平均金属装入量和平均炉产良坯量。设计的公称容量与实际生产的炉产量基本一致。所以在进行炉型设计时采用以平均出钢量表示公称容量比较合理。 (2)炉型的定义: 转炉炉型是指转炉炉膛的几何形状,亦即指由耐火材料砌成的炉衬内形。 (3)炉型设计的意义 转炉是转炉炼钢车间的核心设备,炉型及其主要参数对转炉炼钢的生产率、金属收得率、炉龄等技术经济指标都有着直接的影响,炉型设计的是否合理关系到冶炼工艺能否顺利进行的问题,如喷溅问题,除与操作因素有关外,炉型设计是否合理也是个重要因素,并且车间的主厂房高度以及主要设备,像除尘设备,倾动机构设备等都与炉型尺寸密切相关。而且转炉一旦投产使用,炉型尺寸就很难再作改动,因为不论变动直径还是高度都牵涉到耳轴位置,它是与转炉基础联系在一起的,一般不能随意变动。 所以说,设计一座炉型结构合理,满足工艺要求的转炉是保证车间正常生产的前提。而炉型设计又是整个转炉设计的关键。 设计内容:炉型种类的选择; 炉型主要参数的确定; 炉型尺寸设计计算; 炉衬和炉壳厚度的确定; 顶底复吹转炉设计。 3.1.2炉型种类及其选择 吹炼过程中炉膛内进行着极其复杂而又激烈地物理化学反应和机械运动,因此,转炉的炉型必须适应这些反应特点和运动规律,否则就不能保证冶炼过程的正常进行。那么,什么样的炉型才是比较理想的炉型呢?也就是说,炉型具备什么特点才能适应转炉炼钢反应激烈,吹炼速度快的特点呢? (1)炉型种类的选择原则 选择炉型时应考虑以下几条基本原则: ①炉型应能适应炉内钢液、炉渣和炉气的循环运动规律,使熔池得到激烈而又均匀的搅拌,从而加快炼钢过程的物理化学反应; ②有利于提高供氧强度(B),缩短冶炼时间,减少喷溅,降低金属损耗; ③新砌好的炉子的炉型要尽量接近于停炉以后残余炉衬的轮廓,减少吹炼过程中钢液、炉渣和炉气对炉衬的冲刷侵蚀及局部侵蚀,提高炉龄,降低耐火材料的消耗; ④炉壳应容易制造,炉衬砖的砌筑和维护要方便,从而改善工人的劳动条件,缩短修炉时间,提高转炉作业率。 总之应能使转炉炼钢获得较好的经济效益,优质、高产、低耗。 (2)炉型种类及其选择
转炉炼钢工艺标准经过流程
转炉炼钢工艺流程 这种炼钢法使用的氧化剂是氧气。把空气鼓入熔融的生铁里,使杂质硅、锰等氧化。在氧化的过程中放出大量的热量(含1%的硅可使生铁的温度升高200摄氏度),可使炉内达到足够高的温度。因此转炉炼钢不需要另外使用燃料。 转炉炼钢是在转炉里进行。转炉的外形就像个梨,内壁有耐火砖,炉侧有许多小孔(风口),压缩空气从这些小孔里吹炉内,又叫做侧吹转炉。开始时,转炉处于水平,向内注入1300摄氏度的液态生铁,并加入一定量的生石灰,然后鼓入空气并转动转炉使它直立起来。这时液态生铁表面剧烈的反应,使铁、硅、锰氧化 (FeO,SiO2 , MnO,) 生成炉渣,利用熔化的钢铁和炉渣的对流作用,使反应遍及整个炉内。几分钟后,当钢液中只剩下少量的硅与锰时,碳开始氧化,生成一氧化碳(放热)使钢液剧烈沸腾。炉口由于溢出的一氧化炭的燃烧而出现巨大的火焰。最后,磷也发生氧化并进一步生成磷酸亚铁。磷酸亚铁再跟生石灰反应生成稳定的磷酸钙和硫化钙,一起成为炉渣。 当磷与硫逐渐减少,火焰退落,炉口出现四氧化三铁的褐色蒸汽时,表明钢已炼成。这时应立即停止鼓风,并把转炉转到水平位置,把钢水倾至钢水包里,再加脱氧剂进行脱氧。整个过程只需15分钟左右。如果空气是从炉低吹入,那就是低吹转炉。 随着制氧技术的发展,现在已普遍使用氧气顶吹转炉(也有侧吹转炉)。这种
转炉吹如的是高压工业纯氧,反应更为剧烈,能进一步提高生产效率和钢的质量。 转炉一炉钢的基本冶炼过程。顶吹转炉冶炼一炉钢的操作过程主要由以下六步组成: (1)上炉出钢、倒渣,检查炉衬和倾动设备等并进行必要的修补和修理;(2)倾炉,加废钢、兑铁水,摇正炉体(至垂直位置); (3)降枪开吹,同时加入第一批渣料(起初炉内噪声较大,从炉口冒出赤色烟雾,随后喷出暗红的火焰;3~5min后硅锰氧接近结束,碳氧反应逐渐激烈,炉口的火焰变大,亮度随之提高;同时渣料熔化,噪声减弱); (4)3~5min后加入第二批渣料继续吹炼(随吹炼进行钢中碳逐渐降低,约12min 后火焰微弱,停吹); (5)倒炉,测温、取样,并确定补吹时间或出钢; (6)出钢,同时(将计算好的合金加入钢包中)进行脱氧合金化。 上炉钢出完钢后,倒净炉渣,堵出钢口,兑铁水和加废钢,降枪供氧,开始吹炼。在送氧开吹的同时,加入第一批渣料,加入量相当于全炉总渣量的三分之二,开吹3-5分钟后,第一批渣料化好,再加入第二批渣料。如果炉内化渣不好,则许加入第三批萤石渣料。 吹炼过程中的供氧强度:
三吹二120吨顶吹转炉及炼钢车间设计毕业设计
太原科技大学毕业设计(论文)任务书 (由指导教师填写发给学生) 学院(直属系):材料科学与工程学院时间:2014年 3月 12日学生姓名指导教师 设计(论文)题目三吹二120T顶吹转炉及炼钢车间设计 主要研究内容1.物料平衡及热平衡计算 2.氧气顶吹转炉炉型设计及计算 3.氧枪设计及计算 4.转炉炼钢车间设计及计算 5.连铸设备的选型及计算 6.炉外精炼设备的选型与工艺布置 7.炼钢车间烟气净化系统的设计 研究方法 利用已学的冶金工艺和钢铁厂设计知识进行理论计算与设计; 利用机械设计基础知识,通过查阅相关资料与现有结构相结合对结构部件设计计算。鼓励采用新技术、新方法、新思路和创新设计。 主要技术指标(或研究目标) 毕业设计说明书一份(包括英文资料的中文翻译) 设计图纸三张 1)氧气顶吹转炉炉型图1# 2)年产260万吨良坯三吹二型氧气顶吹转炉炼钢车间工艺平面布置图1#3)年产260万吨良坯三吹二型氧气顶吹转炉炼钢车间剖视图1# 教研室 意见 教研室主任(专业负责人)签字:2014年03月12日说明:一式两份,一份装订入学生毕业设计(论文)内,一份交学院(直属系)。
毕业设计(论文)原创性声明和使用授权说明 原创性声明 本人郑重承诺:所呈交的毕业设计(论文),是我个人在指导教师的指导下进行的研究工作及取得的成果。尽我所知,除文中特别加以标注和致谢的地方外,不包含其他人或组织已经发表或公布过的研究成果,也不包含我为获得及其它教育机构的学位或学历而使用过的材料。对本研究提供过帮助和做出过贡献的个人或集体,均已在文中作了明确的说明并表示了谢意。 作者签名:日期: 指导教师签名:日期: 使用授权说明 本人完全了解大学关于收集、保存、使用毕业设计(论文)的规定,即:按照学校要求提交毕业设计(论文)的印刷本和电子版本;学校有权保存毕业设计(论文)的印刷本和电子版,并提供目录检索与阅览服务;学校可以采用影印、缩印、数字化或其它复制手段保存论文;在不以赢利为目的前提下,学校可以公布论文的部分或全部内容。 作者签名:日期:
转炉工作原理及结构设计要点
攀枝花学院本科课程设计 转炉工作原理及结构设计 学生姓名: 学生学号: 院(系): 年级专业: 指导教师: 二〇一三年十二月
转炉工作原理及结构设计 1.1 前言 1964年,我国第一座30t氧气顶吹转炉炼钢车间在首钢建成投产。其后,上钢一厂三转炉车间、上钢三厂二转炉车间等相继将原侧吹转炉改为氧气顶吹转炉。20世纪60年代中后期,我国又自行设计、建设了攀枝花120t大型氧气顶吹转炉炼钢厂,并于1971年建成投产。进入20世纪80年代后,在改革开放方针策的指引下,我国氧气转炉炼钢进入大发展时期,由于氧气转炉炼钢和连铸的迅速发展,至1996年我国钢产量首次突破1亿t,成为世界第一产钢大国。 1.2 转炉概述 转炉(converter)炉体可转动,用于吹炼钢或吹炼锍的冶金炉。转炉炉体用钢板制成,呈圆筒形,内衬耐火材料,吹炼时靠化学反应热加热,不需外加热源,是最重要的炼钢设备,也可用于铜、镍冶炼。转炉按炉衬的耐火材料性质分为碱性(用镁砂或白云石为内衬)和酸性(用硅质材料为内衬)转炉;按气体吹入炉内的部位分为底吹、顶吹和侧吹转炉;按吹炼采用的气体,分为空气转炉和氧气转炉。转炉炼钢主要是以液态生铁为原料的炼钢方法。其主要特点是:靠转炉内液态生铁的物理热和生铁内各组分(如碳、锰、硅、磷等)与送入炉内的氧进行化学反应所产生的热量,使金属达到出钢要求的成分和温度。炉料主要为铁水和造渣料(如石灰、石英、萤石等),为调整温度,可加入废钢及少量的冷生铁块和矿石等。 1.2.1 转炉分类 1.2.1.1 炼钢转炉 早期的贝塞麦转炉炼钢法和托马斯转炉炼钢法都用空气通过底部风嘴鼓入钢水进行吹炼。侧吹转炉容量一般较小,从炉墙侧面吹入空气。炼钢转炉按不同需要用酸性或碱性耐火材料作炉衬。直立式圆筒形的炉体,通过托圈、耳轴架置于支座轴承上,操作时用机械倾动装置使炉体围绕横轴转动。 50年代发展起来的氧气转炉仍保持直立式圆筒形,随着技术改进,发展成顶吹喷氧枪供氧,因而得名氧气顶吹转炉,即L-D转炉(见氧气顶吹转炉炼钢);用带吹冷却剂的炉底喷嘴的,称为氧气底吹转炉(见氧气底吹转炉炼钢)。
设计作业 300t顶底复吹转炉炉型计算
转炉炉型设计计算 1.1原始数据 (1)、转炉的公称容量为300t 。 (2)、采用顶底复吹冶炼工艺 1.2 转炉的炉型选择 图为常见转炉炉型 (a)筒球型; (b)锥球型; (c)截锥型 根据原始条件及采用顶底复吹工艺的要求,为便于安装底部供气元件,要求转炉底部为平的,所以本设计将采用截锥型炉型作为设计炉型。 1.3炉容比 炉容比系指转炉有效容积与公称容量之比值。转炉炉容比主要与供氧强度有关,与炉容量关系不大。从目前实际情况来看,顶底复吹转炉炉容比一般取0.85~0.95m 3/t 。 本设计为300t ,取V/T=0.92 1.4熔池尺寸的计算 熔池直径的计算公式 t G k D 式中 D ——熔池直径,m ; G ——新炉金属装入量,t ,可取公称容量; K ——系数,参见表1-1;
t ——平均每炉钢纯吹氧时间,min 表1-1 系数K 的推荐值 b.确定吹氧时间 表1.2 推荐的转炉纯吹氧时间 本设计的转炉公称容量为300t , 又根据国家关于新建转炉的要求,吹氧时间在16min , 所以选择的吹氧时间为16min 。 取K=1.50 则)(495.616 30050.1m t G K D =?=? = ② 截锥型熔池深度的计算公式为: )(822.1495.6574.0119 .44574.0574.02 22m D V D V h =?=?== ) (金池 V 池=G/Y=44.119m 3 其中Y=6.8t/ m 3 ③熔池其他尺寸确定. )(546.4495.67.07.01m D D =?== 1.5炉帽尺寸的确定 ①炉口直径d 0.取 )(2475.3495.65.00m d =?= ②炉帽倾角: 取?60 ③炉帽高度H 帽: 取H 口=400mm , )(76.260tan )2475.3495.6(2 1 tan )(2100m d D H =?-=?-= θ锥 则整个炉帽高度为:
50吨氧气顶吹转炉炉体设计
50吨氧气顶吹转炉炉体设计 1 氧气顶吹转炉炼钢的发展概况 氧气顶吹转炉炼钢法是20世纪50年代产生和发展起来的炼钢技术,但从起出现至今已有100多年的历史。早在1856年英国人亨利·贝塞麦就研究开发了酸性底吹转炉炼钢法,以铁水为原料,从转炉底部通入空气氧化去除杂质冶炼成钢。第一次实现了液态钢冶炼的规模生产,从此进入了现代钢铁工业生产阶段。1878年德国尼·托马斯研究发明的碱性底吹转炉炼钢法,以碱性耐火材料砌筑炉衬,吹炼过程中可加入石灰造渣,能够脱除铁水中的P、S,解决了高磷铁水冶炼技术问题。由于转炉炼钢法有生产率高、成本低、设备简单等优点,在欧洲得到迅速的发展,并成为当时主要的炼钢方法。 第二次世界大战之后,从空气中分离氧气技术的成功,提供了大量廉价的工业纯氧,使贝塞麦的氧气炼钢设想得以实现。由于氧气顶吹转炉炼钢首先在林茨和多那维茨两城投入生产,所以取这两个城市名称的第一个字母L-D(LD)作为氧气顶吹转炉炼钢法的代称。 LD炼钢法具有反应速度快,热效率高,又可使用约30%的废钢为原料;并克服了底吹转炉钢质量差,品种少的缺点;因而一经问世就显示出巨大的优越性和生命力。进入20世纪70年代以后,顶吹转炉炼钢技术趋于完善。转炉的最大公称吨位达380t;单炉生产能力达到400~500万t/a;能够冶炼全部平炉钢种,若与有关精炼技术相匹配,还可以冶炼部分电炉钢种;大型转炉炉龄在1999年达到10000炉次/炉役以上;并实现了计算机控制终点碳与出钢温度。 1951年碱性空气侧吹转炉炼钢法首先在我国唐山钢厂试验成功,并于1952年投入工业生产。1954年开始了小型氧气顶吹转炉炼钢的试验研究工作,1962年将首钢试验厂空气侧吹转炉改建成3t氧气顶吹转炉,开始了工业性试验。在试验取得成功的基础上,我国第一个氧气顶吹转炉炼钢车间(2×30t)在首钢建成,于1964年12月26日投入生产。以后,又在唐山、上海、杭州等地改建了一批3.5~5t的小型氧气顶吹转炉。1966年上钢一厂将原有的一个空气侧吹转炉炼钢车间,改建成3座30t的氧气顶吹转炉炼钢车间,并首次采用了先进的烟气净化回收系统,于当年8月投入生产,还建设了弧形连铸机与之相配套,试验和扩大了氧气顶吹转炉炼钢的品种。这些都为我国日后氧气顶吹转炉炼钢技术的发展提供了宝贵经验。此后,我国原有的一些空气侧吹转炉车间逐渐改建成中小型氧气顶吹转炉车间,并新建了一批中、大型氧气顶吹转炉车间。20世纪80年代宝钢从日本引进建成具有70年代末技术水平的300t大型转炉3座、首钢购入二手设备建成210t转炉车间;90年代宝钢又建成250t转炉车间,武钢引进250t 转炉,唐钢建成150t转炉车间,重钢和首钢又建成80t转炉炼钢车间;许多平炉车间改建成氧气顶吹转炉车间等。到1998年,我国氧气顶吹转炉共有221座,其中100t以下的转炉有188座,(50-90t的转炉有25座),100-200t的转炉有23
150吨转炉设计
转炉炉型设计 转炉是转炉炼钢车间的核心设备。转炉炉型及其主要参数对转炉炼钢的生产率、金属收得率、炉龄等经济指标都有直接的影响,其设计是否合理也关系到冶炼工艺能否顺利进行,车间主厂房高度和转炉配套的其他相关设备的选型。2.1 炉型的选择 本设计为150t的中型转炉,选用筒球型转炉。 2.2 炉容比与高宽比 2.2.1 炉容比(V/T , m3/t) 炉容比是转炉有效容积与公容量的比值,主要与供氧强度有关,本设计选取炉容比为0.93 2.2.2 高宽比 高宽比是指转炉炉壳总高度与炉壳外径的比值,是作为炉型设计的校核数据。在 1.25-1.45之间。 2.3 转炉主要尺寸的确定 2.3.1 熔池尺寸 (1)熔池直径D 熔池直径是指转炉熔池在平静状态时金属液面的直径。可根据公 式 D?K G ——新炉金属装入量,t;(取公称容量) t ——吹氧时间,min,取16min K——比例系数,取1.70 则熔池直径D?K 1.7×√(150÷16)=5.21m 熔池深度是指转炉熔池在平静状态时,从金属液面到炉底的深度。对于筒球 型熔池,取球缺体半径R = 1.1D = 5726mm,此时熔池体积VC与熔池直径存在如下关系:VC?0.790hD?0.046D,即h0? 2 3 VC?0.046D 0.79D 2 3 。 熔池体积VC = 装入量/比重 =150/5.0 = 30m3 则熔池深度h0? VC?0.046D 0.79D 2 3 =(30+0.046×5.21)/(0.790×5.21)=1.70m 32
2.3.2 炉帽尺寸 (1)炉帽倾角? 倾角过小,炉帽内衬不稳定,容易倒塌;过大则出钢时容易钢渣混出和从炉口大量流渣。在本设计中取? = 60°. (2)炉口直径d0 本设计中取炉口直径为熔池直径的48%,即d0 = 5.21×48% = 2.5m =2500mm (3) 炉帽高度H 帽 口 = 350 mm,则炉帽高度为: 取炉口上部直线段高度H H帽 = ? (D?d)tan??H= 1/2(5.21 — 2.5)tan60°+ 0.35 = 2.70m 002 2.3.3 炉身尺寸 (1)炉身直径 转炉炉帽以下,熔池面以上的圆柱体部分称为炉身。其直径与熔池直径一致,即为D。(2)炉身高度H 身 2 2 H身 = 4V 式中 V 身 身 /(?D)?4(Vb?V帽?VC)/(?D) 、V帽、VC——分别为炉身、炉帽、熔池的容积。其中: V帽??/24(D3?d口3)tan???/4d口2H口 =0.262(H帽?H口)(D+Dd口+d口)+0.785d口H口 2 2 2 Vb ——转炉有效容积,为V身、V帽、VC三者之和,取决于容量和炉容 比。Vb = 炉容比×G。 根据已得的数据,则有: 3 Vb = 炉容比×G = 0.93×150 =140 m V帽?0.262(H帽?H口)(D+Dd口+d口)+0.785d口H口 222 =0.262(2.70-0.35)(5.21+5.21×2.5+2.5)+0.785×2.5×0.35 = 30.30 m3 2 22 由此,则有炉身高度为: H身 = 4V 身 /(?D)?4(Vb?V帽?VC)/(?D) 22
氧气顶吹转炉炉体设计
氧气顶吹转炉炉体设计
目录 一转炉系统设备.............................................................................................................- 1 - 1.1 炉型.....................................................................................................................- 1 - 1.1.1 转炉炉型概念.............................................................................................- 1 - 1.1.2 合理的炉型要求.........................................................................................- 1 - 1.1.3 转炉的基本炉型.........................................................................................- 2 - 1.1.3.1 筒球型.................................................................................................- 2 - 1.1.3.2 锥球型.................................................................................................- 2 - 1.1.3.3 截锥型.................................................................................................- 2 - 1.2 转炉炉型主要参数确定.....................................................................................- 3 - 1.2.1 转炉的公称容量.........................................................................................- 3 - 1.2.2 炉容比.........................................................................................................- 3 - 1.2.2.1 铁水比、铁水成分.............................................................................- 3 - 1.2.2.2 供氧强度.............................................................................................- 3 - 1.2.2.3 冷却剂的种类.....................................................................................- 4 - 1.2.3 高径比.........................................................................................................- 4 - 1.3 炉型主要尺寸的确定.........................................................................................- 4 - 1.3.1 筒球型氧气顶吹转炉的主要尺寸.............................................................- 4 - 1.3.1.1 熔池直径D..........................................................................................- 5 - 1.4 炉壳.....................................................................................................................- 6 - 1.4.1 炉壳的作用.................................................................................................- 6 - 1.4.2 炉壳的组成.................................................................................................- 6 - 1.4. 2.1 炉帽.....................................................................................................- 6 - 1.4. 2.2 炉身.....................................................................................................- 8 - 1.4. 2.3 炉底.....................................................................................................- 8 - 1.4. 2.4 制作及要求.........................................................................................- 8 - 1.5 炉体支撑系统.....................................................................................................- 9 - 1.5.1 托圈与耳轴.................................................................................................- 9 - 1.5.1.1 托圈与耳轴的作用、结构.................................................................- 9 - 1.5.1.2 托圈与耳轴的连接...........................................................................- 10 - 1.5.2 炉体与托圈...............................................................................................- 10 - 1.5.3 耳轴轴承座...............................................................................................- 13 - 1.6 转炉倾动机构...................................................................................................- 14 - 1.6.1 工作特点...................................................................................................- 14 - 1.6.1.1 减速比大...........................................................................................- 14 - 1.6.1.2 倾动力矩大.......................................................................................- 14 - 1.6.1.3 启动制动频繁,承受的动载荷大...................................................- 14 - 1.6.1.4 工作条件恶劣...................................................................................- 15 - 1.6.2 结构要求...................................................................................................- 15 - 1.6. 2.1 满足工艺需要...................................................................................- 15 - 1.6. 2.2 具有两种以上倾动速度...................................................................- 15 - 1.6. 2.3 安全可靠运转...................................................................................- 15 - 1.6. 2.4 良好的适应性...................................................................................- 15 - 1.6. 2.5 结构紧凑效率高...............................................................................- 15 -