压铸机铸造原理

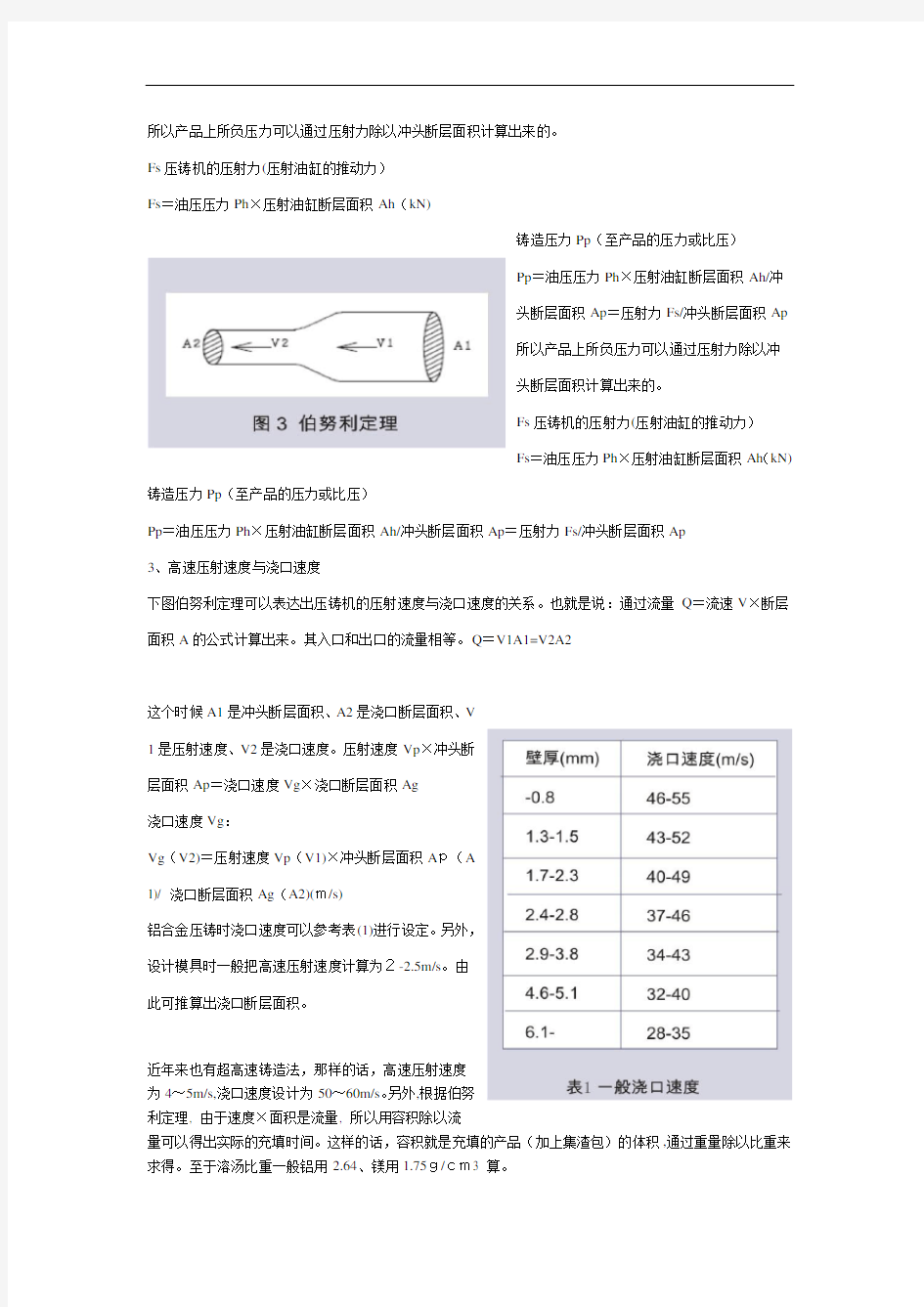
一、压铸机铸造原理
1、压铸机压射部的结构
压铸机的压射(铸造)简单来说正如图1所示。
通常设定铸造条件是通过压铸机上速度、压力以及速度的切换位置的调整,其他方面可在模具上进行调整。通过以下各项目的计算方法,说明一下压铸机的铸造构成。
φD = 压射油缸直径mm
φd = 冲头直径mm
Ah = 压射油缸断层面积mm2
Ap = 冲头断层面积mm2
Ag = 浇口断层面积mm2
A1 = 铸造面积mm2
Fs = 压射力kN
Ph = 油压压力(蓄能器压力)Mpa
p = 铸造压力(压射压力)Mpa
F1 = 开模力kN
Fd = 锁模力kN
Vg = 浇口速度m/s
Vp = 压射速度m/s
2、压射力和铸造压力
所以产品上所负压力可以通过压射力除以冲头断层面积计算出来的。
Fs压铸机的压射力(压射油缸的推动力)
Fs=油压压力Ph×压射油缸断层面积Ah(kN)
铸造压力Pp(至产品的压力或比压)
Pp=油压压力Ph×压射油缸断层面积Ah/冲
头断层面积Ap=压射力Fs/冲头断层面积Ap
所以产品上所负压力可以通过压射力除以冲
头断层面积计算出来的。
Fs压铸机的压射力(压射油缸的推动力)
Fs=油压压力Ph×压射油缸断层面积Ah(kN)铸造压力Pp(至产品的压力或比压)
Pp=油压压力Ph×压射油缸断层面积Ah/冲头断层面积Ap=压射力Fs/冲头断层面积Ap
3、高速压射速度与浇口速度
下图伯努利定理可以表达出压铸机的压射速度与浇口速度的关系。也就是说:通过流量Q=流速V×断层面积A的公式计算出来。其入口和出口的流量相等。Q=V1A1=V2A2
这个时候A1是冲头断层面积、A2是浇口断层面积、V
1是压射速度、V2是浇口速度。压射速度Vp×冲头断
层面积Ap=浇口速度Vg×浇口断层面积Ag
浇口速度Vg:
Vg(V2)=压射速度Vp(V1)×冲头断层面积Ap(A
1)/ 浇口断层面积Ag(A2)(m/s)
铝合金压铸时浇口速度可以参考表(1)进行设定。另外,
设计模具时一般把高速压射速度计算为2-2.5m/s。由
此可推算出浇口断层面积。
近年来也有超高速铸造法,那样的话,高速压射速度
为4~5m/s,浇口速度设计为50~60m/s。另外,根据伯努
利定理, 由于速度×面积是流量, 所以用容积除以流
量可以得出实际的充填时间。这样的话,容积就是充填的产品(加上集渣包)的体积,通过重量除以比重来求得。至于溶汤比重一般铝用2.64、镁用1.75g/cm3 算。
充填时间t:
t=产品体积/浇口流量=(产品重量/比重)/ 浇口速度Vg×浇口断层面积Ag(Sec)
表(2)能帮助我们简单地判断压射速度,浇口面积大致是否适当。充填时间过长可能会导致结束前就提前凝固。此外,凝固也会受熔汤温度、模温等温度的影响造成充填不良。
以下是计算从凝固时间到充填时间的简易公式:充填时间t=α×(铸造品的薄肉部厚度)2 ;一般α用铝:0.01、镁:0.005计算。
4、浇口
面积和
冲头直
径
从图2
的压力
和图3
的速度关系得到冲头直径和铸造压力;冲头直径和浇口速度之间的关系,如图4表所示。
除了确定正确的冲头直径、浇口尺寸、除铸造压力、浇口速度以外,压室的充填率、压室的厚度以及影响浇口处理(切边)等其他要素也必须充分考虑到,以便于恰当的浇口设计方案。下图5为改变冲头直径、
浇口面
积时,所
产生的
铸造影
响。
5
、低速速
度
通常铝合金铸造的低速速度为:
一般情况0.20m/s-0.25m/s
压室的充填率小(20%以上),薄壁产品0.25m/s-0.30m/s
压室的充填率大(30%以上),厚壁产品,真空压0.15m/s-0.20m/s。
低速压射的目的是为了防止压室内卷进空气,根据浇铸量进行调整。另外,多段压射系统可以在0.
03m/s-0.7m/s之间,或者匀加速等。最大可以进行9段的调整。因此,压室充填速度、浇道充填速度、产
品充填速度,可分别设定。可慢慢加速调整等,达到条件设定的多样化。
低速速度的稳定性,对产品品质有很大影响。与高速速度也一样,需要进行监视管理。另外,压室、冲头的卡住等,也是实际速度不安定的原因,必须注意。
6、速度切换位置
对压射速度切换位置和压射状态的关系加以说明。
基
本的压
射切换
位置和
其要点
如右边
图6所
示,各状
态位置加以设定,注意以下各点进行条件设定。
A.给汤完了状态
压射时间内,溶汤安定后,开始压射
B.低速压射,压室充填设定防止空气卷入的速度
注意无溶汤飞溅,冲头的卡住等的影响。
C.低速压射,浇道充填
多段压射的机器另外可以设定,一般情况下,以加速度的匀加速进行设定。
D.高速切换位置
一般来说以溶汤到达浇口
的位置为基准进行设定,根据产品前后调整切换位置来决定最佳的位置。
E.减速位置
产品充填完了后,在集渣包充填完了之前进行有效减速的决定,设定后短射必然会有,但必须对
产品的影响加以确认。
F.增压位置
增压为充填完了开始增压,切换位置一般在充填完了的前20mm左右设定。
不论哪一个切换要点,都要计算机器、电气工作时间的延迟,比计算值之前10~15mm左右进行设定。
7、高速压射行程的计算方法
在6所做的说明,从溶汤到达浇口位置作为高速切换位
置是最基本的。因此,可根据充填质量和压室(冲头)的直径,能
够计算出高速的行程。
从左图可以知道,高速行程×冲头断层面积和充填体
积是相等的。
因此,从充填, 重量求得充填体积,用充填体积除以冲
头横断层截面积,可以求得高速行程。
充填质量Wg=产品+集渣包填质量(测量浇口部切断的
产品以及集渣包的重量)
高速行程=(Wg/溶汤比重)÷
※溶汤比重一般来说铝为2.64g, /cm3、镁为冲头横
断层截面积。1.75g/cm3
例:充填质量6000g的铝制品,用70直径的压室进行
铸造时,其高速行程为:
6000/2.64÷(π×72/4)=5.9cm=59mm
8、增压时间
增压为浇口凝固之前必须向产品传递的压力,所以其增压启动时间和应答性是有一定要求的。增压启动过早,对高速有影响,是产生飞边的原因。
过迟则没有增压效果。有必要进行根据产品的凝固时间,调整增压启动时间。
浇口(汤口)凝固时间的简单计算方法为:
浇口凝固时间t=B×α×(浇口厚度)2
此时B是铝:2.0、镁:1.5 α是铝:0.01、镁:0.005 。
一般来说以上这些为参考,决定压射速度、冲头直径、浇口尺寸等。还有设计模具也必须以此为参考,对于正在生产的不良模具,以数据、计算为基础对模具进行改进,从而能够提高生产性、良品率。
9、开模力的计算
开模力
指的是从铸造时
产品压力开模所
需的力量。
开模力
可用铸造面积×
铸造压力求得。
铸造面
积的计算
铸造面
积A1=a1+a2+a3
+a4=料柄面积+浇
道面积+产品面积
+集渣包面积
涨型力
的计算
开模力F1=铸造压力Pp×铸造面积A1+中子分力Fc
详细的计算
对各部分施加压力分类如下:
产品部分=计算
铸造压力×75%
集渣包部=计算
铸造压力×25%
料柄、浇道部=计
算铸造压力×100%
有滑块中子时,需
计算中子分子。
中子返回力Fr
=产品面积Ac×计算铸造
压力×75%
中子分力Fc=中
子返回力Fr×tanθ
开模力F1=(a1
+a2)×Pp+a3×Pp×0.7
5+a4×Pp×0.25+Fc
压铸机锁模力>
开模力F1×1.1
锁模力需要开模力的1.1倍以上的力量,开模力若比锁模力大,则易发
生飞边(短射)、尺寸过大等现象,不能进行实际生产。
10、充填完了的能量
高速充填完了对产品所施加的能量可以根据其速度、压射油缸活塞部分及压射杆的质量来进行计算。
压射能量E=W(V)2/2g
W:压射油缸活塞部分+压射杆重量kg
V:压射速度m/s
G:重力加速度9.8m/sec2
从上述的计算方式可以看出,充填时的冲击能量力为压射速度的成倍。压射时的飞边发生(短射)多为高速充填时的冲突所造成的。
通过利用压射、减速系统等的条件设定,可以有效防止飞边的发生。
二、产品不良及其对策
1、产品不良及压射条件
将因压射条件引起产品不良及其一般的原因和对策方法总结如图9。
有许多原因引起产品不良,首先查明原因是很重要的。针对一个原因采取的措施也影响到其他不良因素。所以,采取措施时,一点一点一边观察其结果,一边去实施为好。
根据产品的不同,引起不良的原因可有多个。一个对策可能对其他不良有副作用,故必需有综合的对策。
2、产品不良和模具
将因模具引起产品不良及其一般的原因和对策方法总结为如图10。
与压射条件的对策同样,必须找到真正原因采取对策,另要注意采取对策时应避免引起其他不良。
铸造,锻造,压,铸造的区别
铸造,锻造,冲压,铸造的区别 一、锻造的工艺过程 1、加热 1.1锻造温度范围的确定 锻造温度范围是指锻件由开始锻造温度(称始锻温度)到停止锻造温度(称终锻温度)的间隔。 ,应尽量提高始锻温度,使金属具有良好可锻性。使锻温度一般控制在固相线以下 150~250℃。 ,停止锻造后金属的晶粒还会继续长大,锻件的力学性能也随之下降;终锻温度过低,金属再结晶进行得不充分,加工硬化现象严重,内应力增大,甚至导致锻件产生裂纹。 2、金属在加热时易产生的缺陷 2.1氧化、脱碳 钢加热到一定温度后,表层的铁和炉气中的氧化性气体(O2、CO2、H2O、SO2)发生化学反应,使钢料表层形成氧化皮(铁的氧化物FeO、Fe3O4、F2O3),这种现象称为氧化。大锻件表层脱落下来的氧化铁皮厚度可达7~8mm,刚在加热过程中因生成氧化皮而造成的损失,称为烧损。 刚加热到高温时,表层中的碳被炉气中的O2、CO2等氧化或与氢产生化学作用,生成CO或甲烷而被烧掉,这种因钢在加热时表层碳量降低的现象称为脱碳。 脱碳的钢,使工件表面变软,强度和耐磨性降低。碳中碳的质量分数越高,加热时越易脱碳。 减少脱碳的方法是: a)采取快速加热; b)缩短高温阶段的加热时间,对加热好的坯料尽快出炉锻造; c)加热前在坯料表面涂上保护涂层。 2.2过热、过烧 过热是指金属加热温度过高,加热时间过长引起晶粒粗大的现象。过热使钢坯的可锻性和力学性能下降,必须通过退货处理来细化晶粒以消除过热组织,不能进行退火处理的钢坯通过反复锻打来改善晶粒度。 二、锻造成形 金属加热后,就可锻造成形,根据锻造时所用的设备、工模具及成形方式的不同,可将
锻造与铸造的区别
什么叫铸造?什么叫锻造? 悬赏分:10 - 解决时间:2006-1-16 10:13 两者之间有什么不同? 主要各用于什么地方?生产出来的产品特性都有些什么不同? 提问者:kaka_1982 - 四级 最佳答案 铸造 将金属熔炼成符合一定要求的液体并浇进铸型里,经冷却凝固、清整处理后得到有预定形状、尺寸和性能的铸件(零件或毛坯)的工艺过程。现代机械制造工业的基础工艺。铸造生产的毛坯成本低廉,对于形状复杂、特别是具有复杂内腔的零件,更能显示出它的经济性;同时它的适应性较广,且具有较好的综合机械性能。但铸造生产所需的材料(如金属、木材、燃料、造型材料等)和设备(如冶金炉、混砂机、造型机、造芯机、落砂机、抛丸机等)较多,且会产生粉尘、有害气体和噪声而污染环境。 铸造是人类掌握较早的一种金属热加工工艺,已有约6000年的历史。公元前3200年,美索不达米亚出现铜青蛙铸件。公元前13~前10世纪之间,中国已进入青铜铸件的全盛时期,工艺上已达到相当高的水平,如商代的重875千克的司母戊方鼎、战国的曾侯乙尊盘和西汉的透光镜等都是古代铸造的代表产品。早期的铸造受陶器的影响较大,铸件大多为农业生产、宗教、生活等方面的工具或用具,艺术色彩较浓。公元前513年,中国铸出了世界上最早见于文字记载的铸铁件——晋国铸鼎(约270千克重)。公元8世纪前后,欧洲开始生产铸铁件。18世纪的工业革命后,铸件进入为大工业服务的新时期。进入20世纪,铸造的发展速度很快,先后开发出球墨铸铁,可锻铸铁,超低碳不锈钢以及铝铜、铝硅、铝镁合金,钛基、镍基合金等铸造金属材料,并发明了对灰铸铁进行孕育处理的新工艺。50年代以后,出现了湿砂高压造型,化学硬化砂造型和造芯、负压造型以及其他特种铸造、抛丸清理等新工艺。 铸造种类很多,按造型方法习惯上分为:①普通砂型铸造,包括湿砂型、干砂型和化学硬化砂型3类。②特种铸造,按造型材料又可分为以天然矿产砂石为主要造型材料的特种铸造(如熔模铸造、泥型铸造、铸造车间壳型铸造、负压铸造、实型铸造、陶瓷型铸造等)和以金属为主要铸型材料的特种铸造(如金属型铸造、压力铸造、连续铸造、低压铸造、离心铸造等)两类。铸造工艺通常包括:①铸型(使液态金属成为固态铸件的容器)准备,铸型按所用材料可分为砂型、金属型、陶瓷型、泥型、石墨型等,按使用次数可分为一次性型、半永久型和永久型,铸型准备的优劣是影响铸件质量的主要因素;②铸造金属的熔化与浇注,铸造金属(铸造合金)主要有铸铁、铸钢和铸造有色合金;③铸件处理和检验,铸件处理包括清除型芯和铸件表面异物、切除浇冒口、铲磨毛刺和披缝等凸出物以及热处理、整形、防锈处理和粗加工等。 锻造 利用锻压机械对金属坯料施加压力,使其产生塑性变形以获得具有一定机械性能、一定形状和尺寸锻件的加工方法。锻压的两大组成部分之一。通过锻造能消除金属的铸态疏松,焊合孔洞,锻件的机械性能一般优于同样材料的铸件。机械中负载高、工作条件严峻的重要零件,除形状较简单的可用轧制的板材、型材或焊接件外,多采用锻件。锻造按成形方法可分为:①开式锻造(自由锻)。利用冲击力或压力使金属在上下两个抵铁(砧块)间产生变形以获得所需锻件,主要有手工锻造和机械锻造两种。②闭模式锻造。金属坯料在具有一定形状的锻模膛内受压变形而获得锻件,可分为模锻、冷镦、旋转锻、挤压等。按变形温度锻造又可分为热锻(加工温度高于坯料金属的再结晶温度)、温锻(低于再结晶温度)和冷锻(常温)。锻造用料主要是各种成分的碳素钢和合金钢,其次是铝、镁、
锻造冲压和铸造的区别
锻造,冲压和铸造的区别 1、锻造和铸造的区别 (1)铸造:是把没有形状的金属液变成有形状的固体。 锻造:是把一种形状固体变成另一种形状的固体。 铸造好比是你玩蜡,你买了蜡(废钢,或生铁)然后将这个蜡化为液体,放入一个什么模子,这样你就得到不同形状的东西。(固体-液体-固体)锻造,好比是做面饼的过程,你把小的面团揉,放到模子里面,做成不同形状的产品。差不多是固体在高温下,形状可变成别的形状(固体到固体)。 所谓铸造,是将熔融的金属浇铸到模型中获得铸件的过程。铸造专业侧重的是金属熔炼过程,以及浇铸过程中工艺的控制。 锻造是固态下的塑性成型,有热加工,冷加工之分,像挤压、拉拔、墩粗,冲孔等都属于锻造。 (2)锻造是慢慢成型,铸造是一次成型 铸造:熔融的液态金属填满型腔冷却。制件中间易产生气孔。 锻造:主要是在高温下用挤压的方法成型。可以细化制件中的晶粒。 2、自由锻和模锻的区别 自由锻是将加热好的金属坯料放在锻造设备的上,下砥铁之间,施加冲击力或压力,直接使坯料产生塑性变形,从而获得所需锻件的一种加工方法. 自由锻由于锻件形状简单,操作灵活,适用于单件,小批量及重型锻件的生产.自由锻分手工自由锻和机器自由锻.手工自由锻生产效率低,劳动强度大,仅用于修配或简单,小型,小批锻件的生产,在现代工业生产中,机器自由锻已成为锻造生产的主要方法,在重型机械制造中,它具有特别重要的作用. 模锻全称为模型锻造,将加热后的坯料放置在固定于模锻设备上的锻模内锻造成形的。 模锻可以在多种设备上进行。在工业生产中,锤上模锻大都采用蒸汽-空气锤,吨位在5KN~300KN(0.5~30t)。压力机上的模锻常用热模锻压力机,吨位在25000KN~63000KN。 模锻的锻模结构有单模堂锻模和多模膛锻模。如图3-13所示为单模堂锻模,它用燕尾槽和斜楔配合使锻模固定,防止脱出和左右移动;用键和键槽的配合使锻模定位准确,并防止前后移动。单模膛一般为终锻模膛,锻造时常需空气锤制坯,再经终锻模膛的多次锤击一次成形,最后取出锻件切除飞边。 3、铸造,锻造,冲压,铸造的区别 (1)铸造是将原材料融化让其在成型模具中自然成型 锻造是将原材料加热到一定温度然后使用工具锻打成型 冲压是将原材料用合适的冲压模具冲压成型 压铸是在铸造的基础上采用压力将融化后的原料注入模具使其得到更高的密度或更精密的形状 铸造:熔融的液态金属填满型腔冷却。制件中间易产生气孔。 (2)锻造:主要是在高温下用挤压的方法成型。可以细化制件中的晶粒。 零件厚度基本相当的适于用板材成型的用冲压。 零件厚度悬殊,形状复杂的,不受热的,用压铸。
铸造的特点
锻造、铸造的区别?用途,优劣势? 浏览次数:1324次悬赏分:0 |解决时间:2009-10-20 09:08 |提问者:四噜噜 最佳答案 锻造是利用锻压机械对金属坯料施加压力,使其产生塑性变形以获得具有一定机械性能、一定形状和尺寸锻件的加工方法 铸造——熔炼金属,制造铸型,并讲熔融金属浇入铸型,凝固后获得具有一定形状、尺寸和性能金属零件毛坯的成型方法 比较:金属经过锻造加工后能改善其组织结构和力学性能。铸造组织经过锻造方法热加工变形后由于金属的变形和再结晶,使原来的粗大枝晶和柱状晶粒变为晶粒较细、大小均匀的等轴再结晶组织,使钢锭内原有的偏析、疏松、气孔、夹渣等压实和焊合,其组织变得更加紧密,提高了金属的塑性和力学性能。 铸件的力学性能低于同材质的锻件力学性能。此外,锻造加工能保证金属纤维组织的连续性,使锻件的纤维组织与锻件外形保持一致,金属流线完整,可保证零件具有良好的力学性能与长的使用寿命采用精密模锻、冷挤压、温挤压等工艺生产的锻件,都是铸件所无法比拟的 参考资料:百度百科 一次投资成本低,模具易制作(泡馍、木型、塑料、金属等模具方式不受限制),生产运行成本也低。缺点是员工需要一定技能,工艺如果不成熟易导致废品率高。 铸造是将金属熔炼成符合一定要求的液体并浇进铸型里,经冷却凝固、清整处理后得到有预定形状、尺寸和性能的铸件的工艺过程。铸造毛胚因近乎成形,而达到免机械加工或少量加工的目的降低了成本并在一定程度上减少了时间.铸造是现代机械制造工业的基础工艺之一。 铸造种类很多,按造型方法习惯上分为:①普通砂型铸造,包括湿砂型、干砂型和化学硬化砂型3类。②特种铸造,按造型材料又可分为以天然矿产砂石为主要造型材料的特种铸造(如熔模铸造、泥型铸造、铸造车间壳型铸造、负压铸造、实型铸造、陶瓷型铸造等)和以金属为主要铸型材料的特种铸造(如金属型铸造、压力铸造、连续铸造、低压铸造、离心铸造等)两类。 铸造是比较经济的毛坯成形方法,对于形状复杂的零件更能显示出它的经济性。如汽车发动机的缸体和缸盖,船舶螺旋桨以及精致的艺术品等。有些难以切削的零件,如燃汽轮机的镍基合金零件不用铸造方法无法成形。 另外,铸造的零件尺寸和重量的适应范围很宽,金属种类几乎不受限制;零件在具有一般机械性能的同时,还具有耐磨、耐腐蚀、吸震等综合性能,是其他金属成形方法如锻、轧、焊、冲等所做不到的。因此在机器制造业中用铸造方法生产的毛坯零件,在数量和吨位上迄今仍是最多的。
压铸机的基本构造与成型原理
壓鑄机的基本构造与成型原理 壓鑄工業源于十九世紀三十年代的美國,至二十世紀初鋁合金鑄造已成為商業所應用,壓鑄工業目前已發展成為多种合金進行壓鑄的行業,包括鋁合金、鋅合金、鎂合金和銅合金的鑄件。在一些地方,也在詴驗黑色金屬壓鑄。壓鑄件產品中占最大比重的是鋁合金鑄件,占30%--50%;其次為鋅合金鑄件;銅合金鑄件只占壓鑄件總產量的1%--2%。應用最多的是汽車、拖拉机制造工業;其次是儀表制造和電子儀器工業;此外還有農業机械、國防工業、計算机、醫療机械制造業中,壓力鑄造也用得較多。用壓鑄方法生產最大鋁合金鑄件重量可達50KG,鑄件最大直徑2米,最輕的壓鑄件只有几克。用壓鑄生產的零件有發動机气缸体、气缸蓋、變速箱、發動机罩、儀表和照相机的殼体和支架、管接頭、齒輪等。 第一章壓鑄的基本概念 一、壓鑄的定義 壓鑄根据其發展過程,各個時期的定義有所不同,目前壓鑄行業普遍接受的壓鑄定義為:在高壓下,將熔融金屬壓入精密的金屬模具內,在短時間內獲得高精度且良好鑄造表面的鑄件,這其中包含了下述的几個要素: 1.制成精密的金屬壓鑄模具; 2.配以可以開閉模具和可以壓入金屬溶液的裝置; 3.將鋁液以高壓方式壓入封閉的模具內; 4.冷卻后將模具打開; 5.可將鑄件從模具型腔內自動頂出的裝置; 6.反复進行上述過程動作且大批量生產。 二、壓鑄工藝過程 壓鑄工藝流程可用下圖來簡略地表示: 三、壓鑄的特點 (一)与其它鑄造方法相比,壓力鑄造有以下几方面优點: 1.鑄件的尺寸精度高,尺寸偏差小后續加工少; 2.表面光滑,可獲得良好的光洁度; 3.可以壓鑄形狀复雜的薄壁鑄件;
4.在壓鑄中可嵌鑄其它材料(如電熱管)的零件; 5.設計自由度大,可降低后續加工費用; 6.具有高的生產率,過程易于自動化,一般冷壓室壓鑄机平均每班可壓鑄600~700模次,我們公司201PH机种最高記錄為1692模此/班2人。 (二)壓鑄的主要特點: 1.壓鑄時由于液体金屬在腔內的流動速度极高,液流會包住大量空气,最后以气孔形式留在鑄件中,所以用一般壓鑄方法得到的鑄件不能進行較多余量的机械加工。但鑄孔并不是不可以改善,通過改進模具設計、成型工藝,可大幅度減少鑄孔的產生。 2.對內凹复雜的鑄件,壓鑄最為困難; 3.高熔點合金(如銅、黑色金屬)壓鑄時壓鑄模具壽命低; 4.不宜小批量生產,因壓鑄模具制造成本高,壓鑄机生產效率高,小批量生產經濟上不合理。 第二章壓鑄机的基本构造 一、壓鑄机的种類 壓鑄机一般分為熱壓室壓鑄机和冷壓室壓鑄机兩大類。冷壓室壓鑄机按其壓室結构和布置方式分為臥式壓鑄机和立式壓鑄机兩种,臥式壓鑄机液体金屬進入型腔流程壓力損失小,有利于傳遞最終壓力,便于提高比壓,故使用最廣。 二、這里介紹的是我們公司選用的臥式冷室壓鑄机的結构。 壓鑄机主要有開合模結构,壓射結构,動力系統和控制系統等組成。 (一)合模机构: 開合模及鎖模机构統稱為合模机构,是帶動壓鑄模的活動模部分進行壓鑄的開合机构。推動活動模合模的力稱為合模力。由于充填時壓力的作用,合攏的壓鑄模仍有被脹開的可能,故合模机构有鎖緊壓鑄模的作用,鎖緊壓鑄模的力稱為鎖模力,一般鎖模力等于或小于壓鑄机額定合模力的85%,開模力為鎖模力的1/8—1/16,隨机种而异。 合模机构的傳動形式包括動力式(即全液壓式)和机械式兩种。而机械式又分為曲肘式、斜模式和混合式三种,我們公司壓鑄机采用得是曲肘式。此机构由三塊座板組成,并且用四根導柱將其串聯起來,中間是活動模板,由合模缸的活塞杆經過曲肘机构來帶動,動作過程如下:當液壓軸進入合模缸時,推動合模活塞帶動連杆,使三角形鉸鏈擺動。通過力臂將力傳給動模,產生合模動作,要求活動模和固定模閉合時成一直線,亦稱為“死點”,即利用這個“死點”進行鎖模。 (1)合模力大,曲肘連杆系統可將合模缸推力放大16—26倍,這樣合模缸直徑可大大減小,同時高壓油的耗量也顯著減少。 (2)運動特性好合模速度快,在合模中曲肘离“死點”越近,動模移動速度越慢,使活動模与固定模緩慢閉合;同樣在剛開模時,動模運動速度也慢,這利于防止開模時將產品拉裂,也有利于頂出鑄件。 (3)合模机构剛性大。 (4)控制系統簡單 曲肘合模机构缺點是對曲肘系統的轉軸和軸套材料,加工精度和潤滑要求高。 (二)壓射机构 壓射机构是實現壓鑄工藝的關鍵部分,它的結构性能決定了壓鑄過程中的壓射速度、增壓時間等主要參數。
模具制造中铸造和锻造的区别
工艺│模具制造中铸造和锻造的区别 在模具制造中,我们通常能听到铸造与锻造,究竟这两种制造工艺有什么区别呢? 一、铸造 铸造是将金属熔炼成符合一定要求的液体,并浇进铸型里,经冷却凝固、清整处理后得到有预定形状、尺寸和性能的铸件(零件或毛坯)的工艺过程,是现代机械制造工业的基础工艺。 铸造生产的毛坯成本低廉,对于形状复杂、特别是具有复杂内腔的零件,更能显示出它的经济性;同时,它的适应性较广,且具有较好的综合机械性能。但铸造生产所需的材料(如金属、木材、燃料、造型材料等)和设备(如冶金炉、混砂机、造型机、造芯机、落砂机、抛丸机、铸铁平板等)较多,且会产生粉尘、有害气体和噪声而污染环境。 1、铸造种类 按造型方法习惯上分为: ①普通砂型铸造,包括湿砂型、干砂型和化学硬化砂型三类。 ②特种铸造,按造型材料又可分为以天然矿产砂石为主要造型材料的特种铸造(如熔模铸造、泥型铸造、铸造车间壳型铸造、负压铸造、实型铸造、陶瓷型铸
造等)和以金属为主要铸型材料的特种铸造(如金属型铸造、压力铸造、连续铸造、低压铸造、离心铸造等)两类。 2、铸造工艺 ①铸型(使液态金属成为固态铸件的容器)准备,铸型按所用材料可分为砂型、金属型、陶瓷型、泥型、石墨型等;按使用次数可分为一次性型、半永久型和永久型。铸型准备的优劣是影响铸件质量的主要因素; ②铸造金属的熔化与浇注,铸造金属(铸造合金)主要有铸铁、铸钢和铸造有色合金; ③铸件处理和检验,铸件处理包括清除型芯和铸件表面异物、切除浇冒口、铲磨毛刺和披缝等凸出物,以及热处理、整形、防锈处理和粗加工等。 二、锻造 锻造是利用锻压机械对金属坯料施加压力,使其产生塑性变形以获得具有一定机械性能、一定形状和尺寸锻件的加工方法,是锻压的两大组成部分之一。 通过锻造,能消除金属的铸态疏松、焊合孔洞,锻件的机械性能一般优于同样材料的铸件。机械中负载高、工作条件严峻的重要零件,除形状较简单的可用轧制的板材、型材或焊接件外,多采用锻件。 1、锻造按成形方法分 ①开式锻造(自由锻)
锻造基础知识大汇集
2015-06-08锻压世界锻压世界 forming1950专注锻造、冲压、钣金成形行业,汇聚作者与读者、用户与装配商、行业与市场最新动态,通过行业市场类、技术交互类、技术文章类题材为锻压行业打造一流的交流学习、技术传播、信息服务平台。锻造工艺(Forging Process)是一种利用锻压机械对金属坯料施加压力,使其产生塑性变形以获得具有一定机械性能、一定形状和尺寸锻件的加工方法,锻压(锻造与冲压)的两大组成部分之一。 变形温度 钢的开始再结晶温度约为727℃,但普遍采用800℃作为划分线,高于800℃的是热锻;在300~800℃之间称为温锻或半热锻。 坯料 根据坯料的移动方式,锻造可分为自由锻、镦粗、挤压、模锻、闭式模锻、闭式镦锻。 1、自由锻。利用冲击力或压力使金属在上下两个抵铁(砧块)间产生变形以获得所需锻件,主要有手工锻造和机械锻造两种。 2、模锻。模锻又分为开式模锻和闭式模锻.金属坯料在具有一定形状的锻模膛内受压变形而获得锻件,又可分为冷镦、辊锻、径向锻造和挤压等等。 3、闭式模锻和闭式镦锻由于没有飞边,材料的利用率就高。用一道工序或几道工序就可能完成复杂锻件的精加工。由于没有飞边,锻件的受力面积就减少,所需要的荷载也减少。但是,应注意不能使坯料完全受到限制,为此要严格控制坯料的体积,控制锻模的相对位置和对锻件进行测量,努力减少锻模的磨损。 锻模 根据锻模的运动方式,锻造又可分为摆辗、摆旋锻、辊锻、楔横轧、辗环和斜轧等方式。摆辗、摆旋锻和辗环也可用精锻加工。为了提高材料的利用率,辊锻和横轧可用作细长材料的前道工序加工。与自由锻一样的旋转锻造也是局部成形的,它的优点是与锻件尺寸相比,锻造力较小情况下也可实现形成。包括自由锻在内的这种锻造方式,加工时材料从模具面附近向自由表面扩展,因此,很难保证精度,所以,将锻模的运动方向和旋锻工序用计算机控制,就可用较低的锻造力获得形状复杂、精度高的产品,例如生产品种多、尺寸大的汽轮机叶片等锻件。锻造设备的模具运动与自由度是不一致的,根据下死点变形限制特点,锻造设备可分为下述四种形式: 1、限制锻造力形式:油压直接驱动滑块的油压机。 2、准冲程限制方式:油压驱动曲柄连杆机构的油压机。 3、冲程限制方式:曲柄、连杆和楔机构驱动滑块的机械式压力机。 4、能量限制方式:利用螺旋机构的螺旋和磨擦压力机。
铸造和锻造如何区别
个人收集整理仅供参考学习 铸造和锻造如何区别 铸造和锻造的区别: 1、铸造:就是将金属熔炼成符合一定要求的液体并浇进铸型里,经冷却凝固、清整处理后得到有预定形状、尺寸和性能的铸件(零件或毛坯)的工艺过程。现代机械制造工业的基础工艺。铸造生产的毛坯成本低廉,对于形状复杂、特别是具有复杂内腔的零件,更能显示出它的经济性;同时它的适应性较广,且具有较好的综合机械性能。但铸造生产所需的材料(如金属、木材、燃料、造型材料等)和设备(如冶金炉、混砂机、造型机、造芯机、落砂机、抛丸机、铸铁平板等)较多,且会产生粉尘、有害气体和噪声而污染环境。铸造是人类掌握较早的一种金属热加工工艺,已有约6000年的历史。公元前3200年,美索不达米亚出现铜青蛙铸件。公元前13~前10世纪之间,中国已进入青铜铸件的全盛时期,工艺上已达到相当高的水平,如商代的重875千克的司母戊方鼎、战国的曾侯乙尊盘和西汉的透光镜等都是古代铸造的代表产品。早期的铸造受陶器的影响较大,铸件大多为农业生产、宗教、生活等方面的工具或用具,艺术色彩较浓。公元前513年,中国铸出了世界上最早见于文字记载的铸铁件——晋国铸鼎(约270千克重)。公元8世纪前后,欧洲开始生产铸铁件。18世纪的工业革命后,铸件进入为大工业服务的新时期。进入20世纪,铸造的发展速度很快,先后开发出球墨铸铁,可锻铸铁,超低碳不锈钢以及铝铜、铝硅、铝镁合金,钛基、镍基合金等铸造金属材料,并发明了对灰铸铁进行孕育处理的新工艺。50年代以后,出现了湿砂高压造型,化学硬化砂造型和造芯、负压造型以及其他特种铸造、抛丸清理等新工艺。文档收集自网络,仅用于个人学习 铸造种类很多,按造型方法习惯上分为:①普通砂型铸造,包括湿砂型、干砂型和化学硬化砂型3类。②特种铸造,按造型材料又可分为以天然矿产砂石为主要造型材料的特种铸造(如熔模铸造、泥型铸造、铸造车间壳型铸造、负压铸造、实型铸造、陶瓷型铸造等)和以金属为主要铸型材料的特种铸造(如金属型铸造、压力铸造、连续铸造、低压铸造、离心铸造等)两类。铸造工艺通常包括:①铸型(使液态金属成为固态铸件的容器)准备,铸型按所用材料可分为砂型、金属型、陶瓷型、泥型、石墨型等,按使用次数可分为一次性型、半永久型和永久型,铸型准备的优劣是影响铸件质量的主要因素;②铸造金属的熔化与浇注,铸造金属(铸造合金)主要有铸铁、铸钢和铸造有色合金;③铸件处理和检验,铸件处理包括清除型芯和铸件表面异物、切除浇冒口、铲磨毛刺和披缝等凸出物以及热处理、整形、防锈处理和粗加工等。文档收集自网络,仅用于个人学习 2、锻造:是利用锻压机械对金属坯料施加压力,使其产生塑性变形以获得具有一定机械性能、一定形状和尺寸锻件的加工方法。锻压的两大组成部分之一。通过锻造能消除金属的铸态疏松,焊合孔洞,锻件的机械性能一般优于同样材料的铸件。机械中负载高、工作条件严峻的重要零件,除形状较简单的可用轧制的板材、型材或焊接件外,多采用锻件。文档收集自网络,仅用于个人学习 锻造按成形方法可分为:①开式锻造(自由锻)。利用冲击力或压力使金属在上下两个抵铁(砧块)间产生变形以获得所需锻件,主要有手工锻造和机械锻造两种。②闭模式锻造。金属坯料在具有一定形状的锻模膛内受压变形而获得锻件,可分为模锻、冷镦、旋转锻、挤压等。按变形温度锻造又可分为热锻(加工温度高于坯料金属的再结晶温度)、温锻(低于再结晶温度)和冷锻(常温)。锻造用料主要是各种成分的碳素钢和合金钢,其次是铝、镁、钛、铜等及其合金。材料的原始状态有棒料、铸锭、金属粉末和液态金属等。金属在变形前的横断面积与变形后的模断面积之比称为锻造比。正确地选择锻造比对提高产品质量、降低成本有很大关系。文档收集自网络,仅用于个人学习 1 / 1
锻造基本知识
锻造是一种利用锻压机械对金属坯料施加压力,使其产生塑性变形以获得具有一定机械性能、一定形状和尺寸锻件的加工方法,锻压(锻造与冲压)的两大组成部分之一。通过锻造能消除金属在冶炼过程中产生的铸态疏松等缺陷,优化微观组织结构,同时由于保存了完整的金属流线,锻件的机械性能一般优于同样材料的铸件。相关机械中负载高、工作条件严峻的重要零件,除形状较简单的可用轧制的板材、型材或焊接件外,多采用锻件。 1.变形温度 钢的开始再结晶温度约为727℃,但普遍采用800℃作为划分线,高于800℃的是热锻;在300~800℃之间称为温锻或半热锻,在室温下进行锻造的称为冷锻。用于大多数行业的锻件都是热锻,温锻和冷锻主要用于汽车、通用机械等零件的锻造,温锻和冷锻可以有效的节材。 2.锻造类别 上面提到,根据锻造温度,可以分为热锻、温锻和冷锻。 根据成形机理,锻造可分为自由锻、模锻、碾环、特殊锻造。 1)自由锻。指用简单的通用性工具,或在锻造设备的上、下砧铁之间直接对坯料施加外力,使坯料产生变形而获得所需的几何形状及内部质量的锻件的加工方法。采用自由锻方法生产的锻件称为自由锻件。自由锻都是以生产批量不大的锻件为主,采用锻锤、液压机等锻造设备对坯料进行成形加工,获得合格锻件。自由锻的基本工序包括镦粗、拔长、冲孔、切割、弯曲、扭转、错移及锻接等。自由锻采取的都是热锻方式。 2)模锻。模锻又分为开式模锻和闭式模锻.金属坯料在具有一定形状的锻模膛内受压变形而获得锻件,模锻一般用于生产重量不大、批量较大的零件。模锻可分为热模锻、温锻和冷锻。温锻和冷锻是模锻的未来发展方向,也代表了锻造技术水平的高低。 按照材料分,模锻还可分为黑色金属模锻、有色金属模锻和粉末制品成形。顾名思义,就是材料分别是碳钢等黑色金属、铜铝等有色金属和粉末冶金材料。 挤压应归属于模锻,可以分为重金属挤压和轻金属挤压。 闭式模锻和闭式镦锻属于模锻的两种先进工艺,由于没有飞边,材料的利用率就高。用一道工序或几道工序就可能完成复杂锻件的精加工。由于没有飞边,锻件的受力面积就减少,所需要的荷载也减少。但是,应注意不能使坯料完全受到限制,为此要严格控制坯料的体积,控制锻模的相对位置和对锻件进行测量,努力减少锻模的磨损。
锻造的重点总结
锻造的重点总结 1,锻造 ◆什么叫做锻造: □在加压设备及工(模具)的作用下,使坯料产生局 部或全部的塑性变形,以获得一定的几何形状,形 状和质量的锻件的加工方法称为锻造. ◆锻造的分类: □自由锻造 只用简单的通用性工具,或在锻造设备上、下砧间直 接使坯料变形而获得所需的几何形状及内部质量的锻 件. 模锻 利用模具使毛坯变形而获得锻件的锻造方法. □自由锻造的方法 镦粗:使毛坯高度减小,横断面积增大的锻造工序. 局部镦粗:在坯料上某一部分进行的镦粗. 镦粗的过程控制: 1.为了防止镦粗时产生纵向弯曲,圆柱体坯料的高度与直径之比不应超过 2.5-3,且镦粗前坯料端面应平整,并与轴心线垂直. 镦粗时要把坯料围绕着轴心线不断转动坯料发生弯曲时必须立即矫正。 芯棒拔长: 它是在空心毛坯中加芯棒进行拔长以减小空心处径(壁厚)而增加其长度的锻造工序,用于锻造长筒类锻件. 芯棒拔长的过程控制: 1.芯棒拔长都应以六角形为主要变形阶段 即圆→六角→圆,芯棒拔长应尽可能在V 型下砧或110°下槽中进行. 2.翻转角度要准确,打击量在均匀,发现有壁 厚不均匀及两端面过度歪斜现象,应及时 把芯棒抽出,用矫正镦粗法矫正毛坯. 3.芯棒加工应有1/100~2/100日锥度. 拔长:使毛坯横断面积减小,长度增加的 锻造工序. 拔长锻造工艺参数的选择就是要在保证质量的前提下提高效率 1. 每次锤击的压下量应小于坯料塑性所允许的数值,并避免产生折叠,因此每次压缩后的锻件宽度与高度之比应小于2~ 2.5,b/h<2~2.5,否则翻转90°再锻造时容易产生弯曲和折叠。 2.每次送进量与单次压下量之比应大于1~1.5,即L/△h/2>1~1.5生产中一般采用L=(0.6~0.8) h (h为坯料高度)。如图
卧式冷室压铸机的构成与工作原理
第一章卧式冷室压铸机的构成与工作原理 压力铸造(简称压铸)是将熔化的金属,在高压作用下,以高速填充至型(模)具型腔内,并使金属在此压力下凝固而形成铸件的一种方法。高压、高速是压铸法与其他铸造方法的根本区别,也是最重要的特点。 压力铸造是所有铸造方法中生产速度最快的一种方法,填充初始速度在0.5~70m/s范围,生产效率高。用压铸机能压铸出从简单到相当复杂的各种铸件,压铸件重量可从几克到几十千克不等,并能实现压铸生产的机械化和自动化,压铸产品广泛应用于汽车、航空航天、电讯器材、医疗器械、电气仪表、日用五金等,如图1-1所示为压力铸造工程示意图。 图1-1 压力铸造工程示意图 压铸机分为热室压铸机和冷室压铸机两大类。热室压铸机与坩埚连成一体,其压室浸于金属熔液中,压射部件安装在熔炉坩埚的上面;冷室压铸机的压室与坩埚是分开的,压铸时,从熔炉的坩埚或保温炉中取出液体金属浇入压室后进行压铸,冷室压铸机适应于压铸各种有色合金和黑色金属。用压铸机压铸具有如下工作特点: 1)操作工序简单,生产效率高,容易实现自动化。 2)压铸可以代替部分装配,且原材料消耗少,能节省装配工时。 3)卧式冷室压铸机一般设有偏心和中心两种浇注位置,可供压铸型(模)设计时选用。4)金属液在浇道中流动时转折少,有利于发挥增压的作用,提高压铸件质量。 5)压铸件力学性能好,以铝合金、镁合金为例(见表1-1)说明。 6)互换性好,便于维修。 7)压铸产品轮廓清晰,压铸薄壁、复杂零件以及花纹、图案、文字等,能获得很高的清晰度。 8)压铸设备投资高,一般不宜于小批量生产。 表1-1 铝合金、镁合金不同铸造方法力学性能 注:① WCu 、WAl分别表示Cu 、Al的质量分数。 如图1-2所示为全自动镁合金卧式冷室压铸机在压铸生产时其设备配备图,其中压铸机是压铸生产的主导设备,其他各设备也都起着不可缺少的作用 图1-2是力劲机械厂有限公司生产的全自动化镁合金卧式冷室压铸机压铸生产时其设备配备图 图1-2 压力生产设备图 1--定量输送泵 2--压铸机 3--型(模)具加热器 4--喷涂装置 5--取件机械手 6--熔化炉7--预热炉 8--边角料传送带 9--压边机 10--压铸件传送带 11--废品传送带 第一节卧式冷室压铸机压铸原理 如图1-3所示,压铸型(模)合型(模)后,金属液3浇入压室2中,压射冲头1向前推进,将金属液经浇道7压入型腔6中,冷却凝固成型。开型(模)时,压射冲头前伸推出余料,顶出液压缸顶针顶出铸件,冲头复位,完成一个压铸循环。 图1-3 卧式冷室压铸机压铸过程简图 1--压射冲头 2--压室 3--液态金属 4--定模 5--动模 6--型腔 7--浇道 8--动型座板 9--顶出器 10--余料 11--定型座板
锻造工艺缺陷
锻造工艺不当产生的缺陷通常有以下几种 1.大晶粒 大晶粒通常是由于始锻温度过高和变形程度不足、或终锻温度过高、或变形程度落人临界变形区引起的。铝合金变形程度过大,形成织构;高温合金变形温度过低,形成混合变形组织时也可能引起粗大晶粒晶粒粗大将使锻件的塑性和韧性降低,疲劳性能明显下降, 2.晶粒不均匀 晶粒不均匀是指锻件某些部位的晶粒特别粗大,某些部位却较小。产生晶粒不均匀的主要原因是坯料各处的变形不均匀使晶粒破碎程度不一,或局部区域的变形程度落人临界变形区,或高温合金局部加工硬化,或淬火加热时局部晶粒粗大。耐热钢及高温合金对晶粒不均匀特别敏感。晶粒不均匀将使锻件的持久性能、疲劳性能明显下降。 3.冷硬现象 变形时由于温度偏低或变形速度太快,以及锻后冷却过快,均可能使再结晶引起的软化跟不上变形引起的强化(硬化),从而使热锻后锻件内部仍部分保留冷变形组织。这种组织的存在提高了锻件的强度和硬度,但降低了塑性和韧性。严重的冷硬现象可能引起锻裂。 4.裂纹 裂纹通常是锻造时存在较大的拉应力、切应力或附加拉应力引起的。裂纹发生的部位通常是在坯料应力最大、厚度最薄的部位。如果坯料表面和内部有微裂纹、或坯料内存在组织缺陷,或热加工温度不当使材料塑性降低,或变形速度过快、变形程度过大,超过材料允许的塑性指针等,则在撤粗、拔长、冲孔、扩孔、弯曲和挤压等工序中都可能产生裂纹。 5.龟裂 龟裂是在锻件表面呈现较浅的龟状裂纹。在锻件成形中受拉应力的表面(例如,未充满的凸出部分或受弯曲的部分)最容易产生这种缺陷。引起龟裂的内因可能是多方面的:①原材料合Cu、Sn等易熔元素过多。②高温长时间加热时,钢料表面有铜析出、表面晶粒粗大、脱碳、或经过多次加热的表面。③燃料含硫量过高,有硫渗人钢料表面, 6.飞边裂纹 飞边裂纹是模锻及切边时在分模面处产生的裂纹。飞边裂纹产生的原因可能是:①在模锻操作中由于重击使金属强烈流动产生穿筋现象。②镁合金模锻件切边温度过低;铜合金模锻件切边温度过高。 7.分模面裂纹 分模面裂纹是指沿锻件分模面产生的裂纹。原材料非金属夹杂多,模锻时向分模面流动与集中或缩管残余在模锻时挤人飞边后常形成分模面裂纹。 8.折叠 折叠是金属变形过程中已氧化过的表层金属汇合到一起而形成的。它可以是由两股(或多股)金属对流汇合而形成;也可以是由一股金属的急速大量流动将邻近部分的表层金属带着流动,两者汇合而形成的;也可以是由于变形金属发生弯曲、回流而形成;还可以是部分金属局部变形,被压人另一部分金属内而形成。折叠与原材料和坯料的形状、模具的设计、成形工序的安排、润滑情况及锻造的实际操作等有关折叠不仅减少了零件的承载面积,而且工作时由于此处的应力集中往往成为疲劳源 9.穿流 穿流是流线分布不当的一种形式。在穿流区,原先成一定角度分布的流线汇合在一起形成穿流,并可能使穿流区内、外的晶粒大小相差较为悬殊。穿流产生的原因与折叠相似,是由两股金属或一股金属带着另一股金属汇流而形成的,但穿流部分的金属仍是一整体 穿流使锻件的力学性能降低,尤其当穿流带两侧晶粒相差较悬殊时,性能降低较明显。 10.锻件流线分布不顺 锻件流线分布不顺是指在锻件低倍上发生流线切断、回流、涡流等流线紊乱现象。如果模具设计不当或锻造方法选择不合理,预制毛坯流线紊乱;工人操作不当及模具磨损而使金属产生不均匀流动,都可以使
压铸机的工作原理与本体结构
第2章压铸设备 2.1 压铸机的工作原理与分类 2.1.1 压铸成型特点 熔融合金在高压、高速条件下充型,并在高压下冷却凝固成型的一种精密铸造方法。 压铸特点: ①压铸件尺寸精度和表面质量高; ②压铸件表层组织致密,硬度和强度较高,表层较耐磨。 ③可采用镶铸法简化装配和制造工艺; ④生产率高,易实现机械化和自动化; ⑤由于压铸速度极快,型腔气体难于完全排除,厚壁难以补缩,使压铸件易出现气孔和缩松; ⑥压铸模具结构复杂、材料及加工的要求高。 2.1.2 压铸机的分类、型号 1.分类 按熔炼炉设置、压射装置、锁模装置布局等。 热压室压铸机 卧式冷压室压铸机 立式冷压室压铸机 全立式冷压室压铸机 2.型号 J1113B J表示金属性铸造设备;第一位数字表示所属列,共有两列,“1”为冷压室,“2”为热压室;第二位数字表示所属“组”,共有9组,“1”表示卧式,“5”表示立式;第二位数字后数字表示锁模力的1/100kN;型号后的字母表示第几次改型设计。 2.1.3 压铸机的工作原理 2.1. 3.1 热压室压铸机
热压室压铸机工作原理图 1-动模;2-定模;3-喷嘴;4-压射冲头;5-压室;6-坩埚 a-压室通道;b-鹅颈嘴;c-鹅颈通道 压射部分与金属熔化部分连为一体,并浸在金属液中。鹅颈嘴b的高度应比坩埚内金属液最高液面略高,使金属液不致自行流入模腔。 模具闭合。压射时,冲头向下封住通道a时,压室、鹅颈通道、模腔构成密闭系统。冲头以一定的推力和速度将金属液压入模腔,充满型腔并保压适当时间后,冲头提升复位。 2.1. 3.2 立式冷压室压铸机 锁模部分呈水平设置,负责模具的开、合及压铸件的顶出。压射部分呈垂直设置,压室与金属熔炉分开。压铸时,模具闭合,舀取一定金属液倒入压室,反料冲头应上升堵住浇道b,以防金属液自行流入模腔。当压射冲头下降接触金属液时,返料冲头随压射冲头下移,使压射室与模具浇道相通,金属液迅速充满模腔a 。冷却后,压射冲头上升复位,反料冲头往上移动,切断余料e并将其顶出压室,接着开模顶出压铸件。 立式冷压室压铸机工作原理图 a)合模;b)压射;c)开模、取件 1-动模;2-定模;3-压射冲头;4-压室;5-反料冲头 a-模腔;b-浇道;c-金属液;d-压铸件;e-余料 2.1. 3.3 卧式冷压室压铸机 压室与熔炉分开设置,压室水平布置,并可从锁模中心向下偏移一定距离。 压铸时,金属液c注入压室→冲头向前压射→金属液经内浇道a压射入模腔b→保压冷却→开模,同时,冲头继续前推,将余料e推出压室,让余料随动模1移动,压射冲头复位。动模开模结束、顶出压铸件d,再合模。
锻造和铸造的区别
锻造和铸造的区别 铸造:熔融的液态金属填满型腔冷却。制件中间易产生气孔。 锻造:主要是在高温下用挤压的方法成型。可以细化制件中的晶粒。 锻造:用锤击等方法,使在可塑状态下的金属材料成为具有一定形状和尺寸的工件,并改变它的物理性质。 铸造:把金属加热熔化后倒入砂型或模子里,冷却后凝固成为器物。 性能的区别锻造时,金属经过塑性变形,有细化晶粒的做用,切纤维连续,因此常用于重要零件的毛丕制造,例如轴、齿论等。铸造对被加工才料有要求,一般铸铁、铝等的铸造性能较好。铸造不具备锻造的诸多优点,但它能制造形状复杂的零,因此常用于力学性能要求不高的支称件的毛丕制造。例如机床外壳等。 铸造是将金属熔炼成符合一定要求的液体并浇进铸型里,经冷却凝固、清整处理后得到有预定形状、尺寸和性能的铸件(零件或毛坯)的工艺过程。现代机械制造工业的基础工艺。铸造生产的毛坯成本低廉,对于形状复杂、特别是具有复杂内腔的零件,更能显示出它的经济性;同时它的适应性较广,且具有较好的综合机械性能。但铸造生产所需的材料(如金属、木材、燃料、造型材料等)和设备(如冶金炉、混砂机、造型机、造芯机、落砂机、抛丸机等)较多,且会产生粉尘、有害气体和噪声而污染环境。 铸造种类很多,按造型方法习惯上分为:①普通砂型铸造,包括湿砂型、干砂型和化学硬化砂型3类。②特种铸造,按造型材料又可分为以天然矿产砂石为主要造型材料的特种铸造(如熔模铸造、泥型铸造、铸造车间壳型铸造、负压铸造、实型铸造、陶瓷型铸造等)和以金属为主要铸型材料的特种铸造(如金属型铸造、压力铸造、连续铸造、低压铸造、离心铸造等)两类。铸造工艺通常包括:①铸型(使液态金属成为固态铸件的容器)准备,铸型按所用材料可分为砂型、金属型、陶瓷型、泥型、石墨型等,按使用次数可分为一次性型、半永久型和永久型,铸型准备的优劣是影响铸件质量的主要因素;②铸造金属的熔化与浇注,铸造金属(铸造合金)主要有铸铁、铸钢和铸造有色合金; ③铸件处理和检验,铸件处理包括清除型芯和铸件表面异物、切除浇冒口、铲磨毛刺和披缝等凸出物以及热处理、整形、防锈处理和粗加工等。 锻造是利用锻压机械对金属坯料施加压力,使其产生塑性变形以获得具有一定机械性能、一定形状和尺寸锻件的加工方法。锻压的两大组成部分之一。通过锻造能消除金属的铸态疏松,焊合孔洞,锻件的机械性能一般优于同样材料的铸件。机械中负载高、工作条件严峻的重要零件,除形状较简单的可用轧制的板材、型材或焊接件外,多采用锻件。锻造按成形方法可分为:①开式锻造(自由锻)。利用冲击力或压力使金属在上下两个抵铁(砧块)间产生变形以获得所需锻件,主要有手工锻造和机械锻造两种。②闭模式锻造。金属坯料在具有一定形状的锻模膛内受压变形而获得锻件,可分为模锻、冷镦、旋转锻、挤压等。按变形温度锻造又可分为热锻(加工温度高于坯料金属的再结晶温度)、温锻(低于再结晶温度)和冷锻(常温)。锻造用料主要是各种成分的碳素钢和合金钢,其次是铝、镁、钛、铜等及其合金。材料的原始状态有棒料、铸锭、金属粉末和液态金属等。金属在变形前的横断面积与变形后的模断面积之比称为锻造比。正确地选择锻造比对提高产品质量、降低成本有很大关系
压铸机的工作原理与本体结构
第2章压铸设备 2.1压铸机的工作原理与分类 2.1.1压铸成型特点熔融合金在高压、高速条件下充型,并在高压下冷却凝固成型的一种精密铸造方法。压铸特点: ①压铸件尺寸精度和表面质量高; ②压铸件表层组织致密,硬度和强度较高,表层较耐磨。 ③可采用镶铸法简化装配和制造工艺; ④生产率高,易实现机械化和自动化; ⑤由于压铸速度极快,型腔气体难于完全排除,厚壁难以补缩,使压铸件易出现气孔和缩松; ⑥压铸模具结构复杂、材料及加工的要求高。 2.1.2压铸机的分类、型号 1 .分类 按熔炼炉设置、压射装置、锁模装置布局等。 热压室压铸机卧式冷压室压铸机立式冷压室压铸机全立式冷压室压铸机 2 .型号 J1113B J表示金属性铸造设备;第一位数字表示所属列,共有两列,“1”为冷压室, 字表示所属“组”,共有9组,“1 ”表示卧式,“ 5 ”表示立式;第二位数字后数字表示锁模力的型号后的字母表示第几次改型设计。 2.1.3 压铸机的工作原理 2.1. 3.1 热压室压铸机 热压室压铸机工作原理图 2 ”为热压室;第二位数 1/100kN;
1-动模;2-定模;3-喷嘴;4-压射冲头;5-压室;6-坩埚 a-压室通道;b-鹅颈嘴;c-鹅颈通道 压射部分与金属熔化部分连为一体,并浸在金属液中。鹅颈嘴b的高度应比坩埚内金属液最高液面略高, 使金属液不致自行流入模腔。 模具闭合。压射时,冲头向下封住通道a时,压室、鹅颈通道、模腔构成密闭系统。冲头以一定的推力和 速度将金属液压入模腔,充满型腔并保压适当时间后,冲头提升复位。 2.1. 3.2 立式冷压室压铸机 锁模部分呈水平设置,负责模具的开、合及压铸件的顶出。压射部分呈垂直设置,压室与金属熔炉分开。 压铸时,模具闭合,舀取一定金属液倒入压室,反料冲头应上升堵住浇道b,以防金属液自行流入模腔。 当压射冲头下降接触金属液时,返料冲头随压射冲头下移,使压射室与模具浇道相通,金属液迅速充满模腔a。冷却后,压射冲头上升复位,反料冲头往上移动,切断余料e并将其顶出压室,接着开模顶出压铸 件。 立式冷压室压铸机工作原理图 a)合模;b)压射;c)开模、取件 1-动模;2-定模;3-压射冲头;4-压室;5-反料冲头 a-模腔;b-浇道;c-金属液;d-压铸件;e-余料 2.1. 3.3 卧式冷压室压铸机 压室与熔炉分开设置,压室水平布置,并可从锁模中心向下偏移一定距离。 压铸时,金属液c注入压室T冲头向前压射T金属液经内浇道a压射入模腔b T保压冷却T开模,同时, 冲头继续前推,将余料e推出压室,让余料随动模1移动,压射冲头复位。动模开模结束、顶出压铸件d , 再合模。 卧式冷压室压铸机工作原理图 a)合模;b)压射;c)开模、取件 1-动模;2-定模;3-压室;4-压射冲头; a-内浇道;b-模腔;c-金属液;d-压铸件;e-余料 2.1. 3.4 全立式冷压室压铸机 (1 )压射冲头上压式压铸机
铸造工艺及锻造工艺比较
铸造工艺及锻造工艺比较 1、铸造: 铸造种类很多,按造型方法习惯上分为:特种铸造,按造型材料又可分为以天然矿产砂石为主要造型材料的特种铸造(如熔模铸造、泥型铸造、铸造车间壳型铸造、负压铸造、实型铸造、陶瓷型铸造等)和以金属为主要铸型材料的特种铸造(如金属型铸造、压力铸造、连续铸造、低压铸造、离心铸造等)两类。 铸造工艺通常包括 ●普通砂型铸造,包括湿砂型、干砂型和化学硬化砂型3类。 ●铸造金属的熔化与浇注,铸造金属(铸造合金)主要有铸铁、铸钢和铸造有色合金; ●铸件处理和检验,铸件处理包括清除型芯和铸件表面异物、切除浇冒口、铲磨毛刺 和披缝等凸出物以及热处理、整形、防锈处理和粗加工等。 ●铸型(使液态金属成为固态铸件的容器)准备,铸型按所用材料可分为砂型、金属 型、陶瓷型、泥型、石墨型等,按使用次数可分为一次性型、半永久型和永久型, 铸型准备的优劣是影响铸件质量的主要因素; 2、锻造: 是利用锻压机械对金属坯料施加压力,使其产生塑性变形以获得具有一定机械性能、一定形状和尺寸锻件的加工方法。 锻压的两大组成部分之一。通过锻造能消除金属的铸态疏松,焊合孔洞,锻件的机械性能一般优于同样材料的铸件。机械中负载高、工作条件严峻的重要零件,除形状较简单的可用轧制的板材、型材或焊接件外,多采用锻件。 锻造按成形方法可分为: ●闭模式锻造。金属坯料在具有一定形状的锻模膛内受压变形而获得锻件,可分为模 锻、冷镦、旋转锻、挤压等。按变形温度锻造又可分为热锻(加工温度高于坯料金 属的再结晶温度)、温锻(低于再结晶温度)和冷锻(常温)。锻造用料主要是各种
成分的碳素钢和合金钢,其次是铝(铝合 开式锻造(自由锻)。利用冲击力或压力使金属在上下两个抵铁(砧块)间产生变形以获得所需锻件,主要有手工锻造和机械锻造两种。