超声波探伤

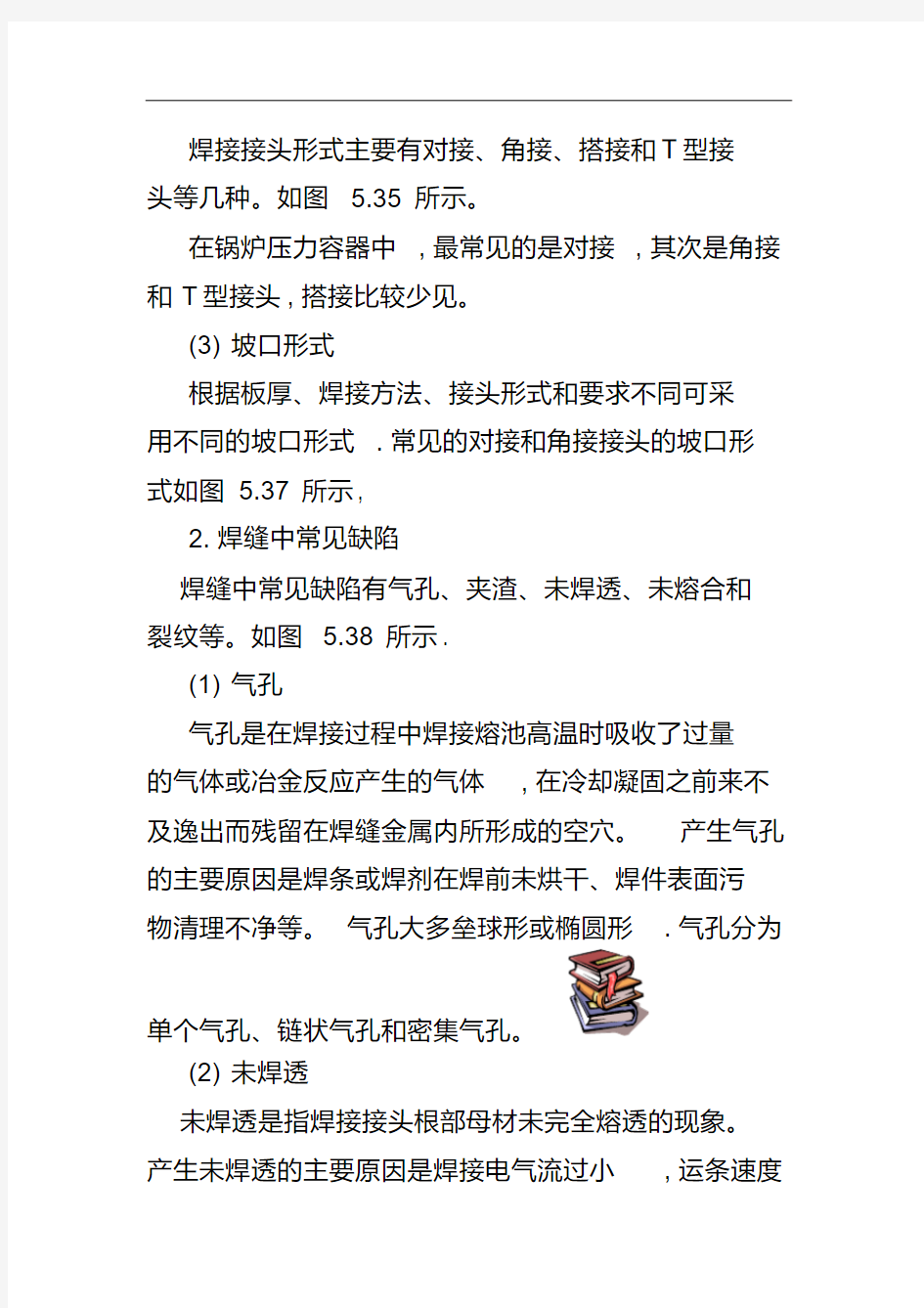
§5.4焊缝探伤
一、焊接加工及常见缺陷
锅炉、压力容器主要是采用焊接加工成形的。焊
缝内部质量主要利用射线和超声波来检测。但对于焊缝中的裂纹、未焊透等危险性缺陷,超声波探伤比射线更容易发现。
为了有效地检出焊缝中的缺陷,探伤人员除了具备超声波探伤的测试技术外,还应对焊接过程、焊接接头和坡口形式以及焊缝中常见缺陷有所了解。
1.焊接加工
(1)焊接过程
常用的焊接方法有手工电孤焊、埋孤自动焊、气
体保护焊和电渣焊等。焊接过程实际上是一个冶炼和铸造过程,首先利用电能或其他形式的能产生高温使金属溶化,形成熔池,烧融金属在熔池中经过冶金反应后冷却,将两母材牢固地结合在一起。为了防止空气中的氧、氮进入熔融金属,在焊接过程中通常有一定的保护措施。手工电弧焊是利用焊条外层药皮高温时分解产生的中性或还原性气体作保护层。埋弧焊和电渣焊是利用液体焊接剂作保护层,气体保护焊是利用氧气或二氧化碳等保护气体作保护层。
(2)接头形式
焊接接头形式主要有对接、角接、搭接和T型接
头等几种。如图 5.35所示。
在锅炉压力容器中,最常见的是对接,其次是角接和T型接头,搭接比较少见。
(3)坡口形式
根据板厚、焊接方法、接头形式和要求不同可采
用不同的坡口形式.常见的对接和角接接头的坡口形式如图5.37所示,
2.焊缝中常见缺陷
焊缝中常见缺陷有气孔、夹渣、未焊透、未熔合和裂纹等。如图 5.38所示.
(1)气孔
气孔是在焊接过程中焊接熔池高温时吸收了过量
的气体或冶金反应产生的气体,在冷却凝固之前来不及逸出而残留在焊缝金属内所形成的空穴。产生气孔的主要原因是焊条或焊剂在焊前未烘干、焊件表面污
物清理不净等。气孔大多垒球形或椭圆形.气孔分为
单个气孔、链状气孔和密集气孔。
(2)未焊透
未焊透是指焊接接头根部母材未完全熔透的现象。产生未焊透的主要原因是焊接电气流过小,运条速度
太快或焊接规范不当(如坡口角度过小、根部间隙过小或钝边过大等)。未焊透分为根部未焊透、中间未
焊透和层间未焊透等。
(3)未熔合
熔合主要是指填充金属与母材之间没有熔合在一
起或填充金属层之间没有熔合在一起。产生未熔合的主要原因是坡口不干净,运条速度太快,焊接电流过小,焊条角度不当等。未熔合分为坡口面表熔合和层间未熔合。
(4)夹渣
夹渣是指焊后残留在焊缝金属内的熔渣或非金属
夹杂物。产生夹渣的主要原因是焊接电流过小,速度过快,清理不干净,致使熔渣或非金属夹杂物来不及
浮起而形成的。夹渣分为点状和条状。
(5)裂纹
裂纹是指在焊接过程中或焊后,在焊缝或母材的热影响区局部破裂的缝隙。按裂纹成因分为热裂纹、冷裂纹和再热裂纹等。热裂纹是由于焊接工艺不当在施焊时产生的。冷裂纹是由于焊接应力过高、焊条焊剂中含氢量过高或焊件刚性过大造成的,常在焊件冷却
到一定温度后才产生,因此又称延迟裂纹。再热裂纹一般是焊件在焊后再次加热(消除应力热处理或其他
加强过程)而产生的裂纹。
按裂纹的分布分为焊缝区裂纹和热影响区裂纹。
按裂纹的取向分为纵向裂纹和横向裂纹。
焊缝中的气孔、夹渣是立体型缺陷,危害性较小,而裂纹未熔合是平面型缺陷,危害性大。
在焊缝探伤中,由于加强高的影响及焊缝中裂纹、未焊透、未熔合等危险性大的缺陷往往与探测面垂直
或成一定的角度,因此一般采用横波探伤。
二、中厚板对接焊缝探伤
1.探测条件的选择
(1)探测面的修整
表面状况,直接影响探伤结果。因此,应清除焊接工件表面飞溅物、氧化皮、凹坑及锈蚀等。一般使用
砂轮机、铿刀、三喷砂机、钢丝刷、磨石等对探测面
进行修整。光洁度一般不低于▽4。
焊缝两侧探测面的修整宽度P一般规定为:
厚度为8—46mm的焊缝探测面修整宽度
厚度大于46~120mm的焊缝探测面修整宽度
式中:k一探头的K值(S
K tg)
T一工件厚度。
(2)耦合剂的选择
在焊缝探伤中,常用的耦合剂有机油、甘油、浆糊、
润滑脂和水等。
从耦合效果看,浆糊同机油差别不大,不过浆糊有一定的粘性,可用于任意姿势的探伤操作
,并具有较好的水洗性,常用于倾斜面或垂直面探伤。
(3)频率选择
焊缝的晶粒比较细小,可选用较高的频率探伤,一般为2.5—5.0MHz 。对于板厚较小的焊缝,可采用较高的频率,对于板厚较大、衰减明显的焊缝
,应选用较低的频率。
(4)K值选择
探头K值的选择应从以下三个方面考虑:
①能使声束能扫查到整个焊缝截面。
②能使声束中心线尽量与主要危险性缺陷垂直。③保证有足够的探伤灵敏度。
由图5.39可以看出,用一、二次波单面探测双面焊时:
其中一次波只能扫查到
1d 以下的部分,二次波只能扫查到2d 以上的部分,因底面b 为曲面。为保证能扫查
整个焊缝截面,必须满足12a d T ,从而得到:0a b
l K T (5.18)
式中:a一上焊缝宽度的一半;
b 一下焊缝宽度的一半;
0l ―探头的前沿距离;
T ―工件厚度;
K 一探头的K 值,K tg
对于单面焊,b 可忽略不计,这时0
a l K T 。
一般斜探头K 值可根据工件厚度来选择,薄工件采用大K值,以便避免近场区探伤,提高定位精度。厚工件采用小K 值,以便缩短声程减少衰减和打磨宽度,提高探伤灵敏度。实际探伤时,可按表 5.1选择K 值。在条件允许的情况下,应尽量采用大K 值探头。
实际探伤中,常利用CSK-IA 和CSK-ⅢA 试块来测定探头的K 值。
CSK-IA 试块测定法
探头对准CSK-IA 试块上中1.5或50反射体,前后平行移动探头,找到最高回波,这时探头入射点对应的刻度值即为探头的
K 值。
②CSK-ⅢA 试块测定法
探头对准CSK-ⅢA 试块上某一φ1×6横孔,前后平行移动探头,找到最高回波,并量出入射点至该孔的水平距离l 和该孔的深度d 。则K 值为:
(5)探测方向的选择
为发现纵向缺陷,常采用以下三种方式进行探测:
1.板厚T=8~46mm的焊缝,以一种K值探头用一、二次波在焊缝单面双侧进行探测。如图
5.40(a)。
2.板厚46 3.板厚T>1201mm的焊缝,除以两种K值探头用一次波在焊缝两面双侧进行探测外,还应加用K1探头在焊缝单面双侧进行串列式探测。如图 5.40(c) 为了发现横向缺陷,常采用以下三种方式探测: ①在已磨平的焊缝及热影响区表面以一种(或两 种)K值探头用一次波在焊缝两面作正、反两个方 向的全面扫查,如图5.41(α) ②用一种(或两种)K值探头以一次波在焊缝两面双侧作斜平行探测、声束轴线与焊缝中心线夹角小于10如 图5.41(b)。 ③对于电渣焊中的人字形横裂,可用一种(或两种)K 值探头在45方向以一次波在焊缝两面双侧进行探测。如图5.41(c) 2.扫描速度(扫描线)的调节 第四章中介绍了三种调节横波扫描速度的方法z 声程定位法、水平定位法和深度定位法。在焊缝探伤 中最常用的是后两种。当板厚小于20mm时,常用水平定位法,当板厚大于20mm时,常用深度定位法。 (1)声程定位法 此方法是把荧光屏上的横轴数值调整成声程读数 的一种方法。常用CSK-IA试块、半圆试块、IIW试块等来调整。我们只介绍两种试块调节方法。 ①CSK-IA试块法 该法是利用两个半径不同的曲面作为标准反射体来 进行声程定位的。其调整方法如下: 将探头放在CSK-IA型试块上,见图5.42。移动探头找出最大反射波,调整"增益"旋钮,使两个曲面的最大反射波同时出现在示波屏上,用"水平'和"微调"将两反射波调至50和100,这时声程扫描速度为l:1 ②半圆试块法 该法是以曲面的多次反射进行声程定位。与CSK-IA 型试块法不同点是只利用一个曲面。当探头在半圆试 块圆心时(见图 5.43),声波入射到A点后产生反射,在荧光屏上出现一次声程(R)的反射波。声波继续传播,经过圆心反射到B点由于反射方向改变,探头接收不到这个回波,所以在荧光屏上没有2R的反射波。声波又经圆心向A点传播,并反射至探头在荧光屏上出现3R的反射波。调整方法与CSK-IA型试块法相同。 (2)水平定位法 该方法是使荧光屏横轴刻度板的读数与探头入射 点距反射体水平距离形成一定比例的定位方法。这里 仅介绍几种1:1水平定位法。 ①CSK-ⅢA试块法 该方法是利用几个不同距离的1×6短横孔来调整时间扫描线,调整方法如下(见图5.44)。 A.测出探头的入射点和K值。 B.把荧光屏上的始脉冲先左移10mm。 C.把探头放在横孔试块上前后移动,找出的孔的最大反射波,量出1d孔的水平 距离1l,用仪器上的"微调'旋钮调整该孔至荧光屏刻 度板1l的位置,并作好标记(可用仪器上的标距点标出)。 D.后移探头,找出2d孔的最大反射波,量出2l值。若2d 孔反射波在荧光屏上出现的读数(y)与2l值不相符时, 应找出二者之间的差(x〉 x=2l-y 若差(x)为正值时,应转动微调把2d孔最大反射波向大读数移动,如两孔距探测面的垂直距离之比值为2,以顺时针方向转动微调旋钮,将2d孔最大反射波调 至Y+2x处。 若差(x)为负值时,则将2d孔最大反射波向小读数方向移动,使读数为y-2x。 再用水平旋钮,把马孔撮大反射波移动到2l值的位置。这样水平距离的时间扫描线已调整完毕。若按 上述方法调整后,d1孔与刻度板有误差时应再进行调整,直至读数相符为止。但要注意仪器水平线性的误差,否则会给时间扫描线的调整带来困难。 例如:己知1d=1l=40mnb2d=2l=80mm,按上述方法调整时间扫描线。可首先用微调把1d孔的最大反射波调节到40mm处,然后探头向后移动找出2d孔的最大反射波。.若该波不是80mm处,而是y=78mm,则x=80一78=+2。这时,转动微调,把 d.孔最大反射波向大读数移动,即使它到82处,再用水平旋钮把2d孔的最大反 射波从82处移回到80处即可。 边角水平定位法 该方法是利用试块上边角和下边角进行定位的一 种方法,调整步骤如下: 将探头放在试块上前后移动,找出下边角的最大反射波,量出水平距离1l,如图5.45所示,用"微调"旋钮,把该波调至1l处,然后移动探头,找出上边角的最大反 射波,量出水平距离2l ,然后用"微调"、"水平"旋钮使 该波在荧光屏上的读数等于 2l .(3)深度定位法 此方法是以荧光屏刻度板的读数代表探头至反射 体的垂直距离(d)。若已知垂直距离d(或深度),可用l=Kd 求出水平距离。用深度调整时间扫描线的方法与水平定位法相似。 1.双孔标定法 选择A 、B 两个横孔,A 孔的探测声程应在探头的近场区以外,B 孔的声程应接近所需探测的最大声程, 反复调节"水平'旋钮和"微调"旋钮,使两孔的最大回波各处于示披屏上与深度1d 和2d 相对应的位置。如要求精确,应扣除与横孔半径相当的深度 用这种方法需反复多次调节 ,显然比半圆试块法麻烦。 2.半圆试块法 首先把探头放在半困试块上,如图5.47所示。调节仪器,使示波屏上出现圆孤曲面的多次反射披123,,......H H H ,第一次反射波 1H 对应的深度:121R a K (5.19) 式中:R ――半圆试块的半径; K 一一探头的K 值。 以后各次反射波 23,......H H ,对应的深度为3d 、15......d . 。调节"徽调,和"水平"使12,H H 分别对准水平刻度值1d 和31d ,这时深度1:1就调好了。 因此法调节会产生一些误差,为了减少误差,可将探头置于φ2长横孔试块上进行修正。 3.距离-波幅曲线的绘制与应用 缺陷波高与缺陷大小、距离有关,大小相同的缺陷由于声程不同,回波高度也不相同。描述某一确定反射体回波高度随距离变化的关系曲线称为距离-波幅曲线。距离-波幅曲线是AVG 曲线的特例。 距离-波幅曲线由定量线、判废线和距离测长线组成,如图5.48所示。测长线和定量线之间称为I 区,定量线与判废线之间称为Ⅱ区 ,判废线以上称为Ⅲ区。不同板厚范围的距离 -波幅曲线的灵敏度见表5.2。 距离-波幅曲线有两种形式。一种是波幅用dB 值表示作为纵坐标,距离为横坐标,称为距离-dB 曲线,另一种是波幅用毫米〈或%〉表示作为纵坐标 ,距离 为横坐标,称为距离-毫米〈或%〉曲线。 距离一波幅曲线与AVG 曲线一样可以实测得到,也可由理论计算公式或通用AVG 曲线得到。由于实际探 伤中经常是利用试块实测得到的,因此这里仅以CSK-ⅢA试块为例介绍距离-dB曲线的绘制方法。设板厚T=30mm。 (1)距离-dB曲线的绘制 ①测定探头的入射点和K值,并根据板厚按水平或深度调节扫描速度,一般为1:1。这里按深度1:1调节。 ②探头置于CSK-ⅢA试块上,衰减48dB(假定〉,调增益使深为10mm的16孔的最高回波达基准50%高,记下这时衰减器读数和孔深。然后分别探测不同 深度的16,增益不动,用衰减器将各孔的最高回波 调至5o%高.记下相应的dB值和孔深填如表中,并根据板厚T=30mm算出定量线、判废线和测长线对 应的dB值填入表中。 ③利用表 5.3中所列数据,以孔深为横坐标,以dB 值为纵坐标,在坐标纸上描点绘出定量线,判废线和测长线,标出I区、Ⅱ区和Ⅲ区,并注明所用探头的频率、晶片尺寸和K值。如图5.49。 (2)距离-dB曲线的应用 ①了解反射波高和距离之间的对应关系。 ②现场探伤中采用便携式试块可用它来校正灵敏度。 这就减少了试块数量、简化操作步骤、节约时间。 ⑥用来比较缺陷的大小 例:缺1深hi=40mm,当量为1×6+2dB,缺陷2深 h=90mm,当量为1×6-3dB,试比较两个缺陷大小。2 从距离-波幅曲线中可知,40mm与90mm深 度,1×6孔的反射波相差12dB.深度40mm时,1×6+2dB可换算成46dB,放在90mm深度时应为46dB-12dB=34dB。而90mm深度时,1×6-3dB=29dB,34dB>29dB。可见1缺陷当量大于2缺陷当量。 ④缺陷进行定量 例:探8Omm板厚的焊缝,作出的距离-波幅曲线如表5.4所示(耦合补偿3dB己加入)。 从表5.4中查得8Omm处的dB值为19(定量线),测长线为19-6=13dB,如果耦合修正为3dB,则探伤灵敏度可取10dB。如果在40mm处发现一个缺陷,这个缺陷波高超过基准波高(基准波高定为荧光屏满刻度的50%高)。用衰减器把缺陷反射波降到基准波高,这时衰减器读数为29dB。查表5.4得出401nm深的孔定量线为31dB,缺陷29dB<31dB,在定量线以下,不必测长。 ⑤调整灵敏度 8—46mm板厚的焊缝,用两倍板厚的声程处来选 取灵敏度。例如:对20mm厚的板(定量线中1×6-3dB, 。选用40mm的孔测长线中1×6-9dB),2×2Omm=40mm 深1×6-9dB来作为探伤灵敏度。如考虑表面糯合损 失3dB,则灵敏度为1×6-12dB。46~120mm板厚的焊缝,用深度与板厚相同的孔来调节灵敏度。例如80mm 板厚,就用80mm深1×6-6dB为灵敏度。如果补偿5dB,则灵敏度为1×6-11dB。 实际探伤中,使用距离-dB曲线比较麻烦,为此有时将距离-dB曲线直接绘制在仪器示波屏面板上,称为面板曲线。面板曲线使用方便,可根据缺陷波高直接确定缺陷当量和区域。面板曲线绘制方法如下: ①测定探头的入射点和K值,根据板厚按深度或水平调节扫描速度。这里按深度1:1调节。 ②探头对准CSK·-ⅢA试块上深为1Omrn的1×6 横孔找到最高回波,调至满幅度的100%(但不饱 和),在面板上标记披峰对应的点1,并记下此时 的dB值N(假定N=30dB)。 ③固定增益和衰减器,分别探测深度为20、30、40、 50、60111m的1×6横孔,找到最高回波,并在面 板上标记对应的点2、3、4、5、6,然后连接点1、 2、3、 4、5、6,得到一条1×6的参考曲线,如图5.50所示。 ④灵敏度的调节不低于测长线。若工件厚度在 15~46mm范围内,只要在N=30dB的基础上再提高9dB 即可,即衰减器读数为21dB。,如果考虑补偿,应再提高需补偿的dB数。设补偿5dB,则衰减器读数为16dB。 ⑤探伤时若缺陷波高低于参考线,则说明缺陷波低于测长线,可以不予考虑。若缺陷波高于参考线,则用衰减器将缺陷波调至参考线,根据衰减的dB值求出缺陷的当量和区域。 例如: +4dB,则缺陷当量为1×6-9+4=1×6一5dB,在I区, +8dB,则缺陷当量为1×6-9+8=1×6-1dB,在Ⅱ区, +16dB,则缺陷当量为1×6-9+16=1×6+7dB,在Ⅲ区。 应用上述面板曲线时,只要记住+6dB和+14dB即可。十6dB表示缺陷达定量线,注意测长。+14dB表示缺陷达判废线,应判废。 4.表面声能损失差的测定 (1)薄板焊缝表面声能损失差的测定 制作与被检工件材质相同或相近、厚度相同,上下表面光沽度与CSK-ⅢA试块相同的平面型试块(图5.51)。 用同型号的两个斜探头沿探伤方向置于工件上 (不通过焊缝)。探头间距为2P,作一发一收测试,使其最大穿透波幅为荧光屏上3格高。在同样条件下,用与上述相同的方法,将两探头置于平面型试板近2P处,只调节衰减器,使其最大穿透波幅也为3格高,此时工件与试板的衰减dB差,即为薄板焊缝的表面声能损失差。 (2)中厚板焊缝表面声能损失差的测定 作平面型试板,A面光洁度与被检工件相同,B面光洁度与CSK-ⅢA试块相同,其他要求同上述薄板型试板(见图5.52)。 用同型号的两个斜探头沿探伤方向置于焊缝两侧 的探伤面上,作一发一收测试,使其最大穿透波幅为3格高。在同样条件下,用与上述相同的方法,将探头置于平面型试板B面上,只调节衰减器,使其最大穿透波辐也为3格高,此时工件探伤面与试板的衰减dB差,即为上表面声能损失差,见图 5.52(a)。 重复上述步骤,按图5.52(b)测出被检工件(不通过焊缝)与平面型试板A面的衰减dB差.因探伤时声束两次触及下表面,取其dB差的两倍,即为下表面声能损失差。 上、下表面声能损失差之和,即为反射法探伤表面 声能损失差。 最后需要指出,中厚板表面声能损失差测定中己 包括焊缝及热影响区的材质衰减。表面声能损失差应 取多次测试的平均值。 5.扫查方式 焊缝外观及探测面经检查合格后,方可进行探伤。斜探头的扫查方式分下列几种: (1)锯齿形扫查。这是检查焊缝中有无缺陷的一般 方法,特别要注意的是=锯齿形扫查时,探头要作10~15的转动。这是因为探头不转动,就不能发现与焊缝倾斜的缺陷。此外,每次前进齿距d不得超过探头晶片直径.这是因为间距太大,会造成漏检(见图5.53)。 (2)左右扫查与前后扫查〈见图5.54〉。当用锯齿形扫查发现缺陷时,可用左右扫查和前后扫查找到回波的最大值,进而判定缺陷位置,可用左右扫查来确定缺陷沿焊缝方向的长度,用前后扫查来确定缺陷的水平距离或深度。 (3)转角扫查〈见回 5.54〉。利用它可以推断缺陷的方向性质。 (4)环绕扫查〈见图 5.54〉,它可作为推断缺陷的形状使用,如果环绕扫查时,回波高度几乎不变,则可判断为点状〈球形)缺陷。 (5)为了检验焊缝或热影响区的横向缺陷,对于磨平的焊缝可将斜探头直接放在焊缝下作平行移动,对于有加强层的焊缝可在焊缝两侧边缘 (6)串列式扫查。在厚板焊缝探伤中,与探伤面垂直的内部未焊透、未熔合等缺陷用单斜探头很难探 出。国内一般采用两种探头,即小K值探头和大K值 探头,也有采用串列扫查(见图5.56)。 6.缺陷位置的测定 在探伤中发现缺陷波以后,应根据示波屏上缺陷波的位置来确定缺陷在实际焊缝中的位置。缺陷定位 法分为z声程定位法、水平定位法和深度定位法三种。 (1)声程定位法 当仪器按声程1:n调节扫描速度时,应采用声程定位法来确定缺陷的位置。如图 5.57所示, 用一次波探伤发现缺陷时: d x n(5.20) cos cos f f f 用二次波探伤发现缺陷时: d T x T n(5.21) 2cos2cos f f f 式中:f x----缺陷的横波声程; f----缺陷波前沿所对的刻度值; -----探头的折射角(横波); T-----厚板; f l -----缺陷的水平距离;f d ------缺陷至探测面的深度。 例:用=40的探头探测T=30mm 的对接焊缝,仪器按声程1:1调节扫描速度,探伤中在示波屏水平刻皮60处出现一缺陷,求此缺陷在焊缝中的位置。 解:由已知得一、二次波的声程为: 因为21278.4( )x x mm 3902mm ﹤f x =60mm ﹤78.4mm 所以此缺陷的水平距离为 38.6mm ,深度为14mm 。 (2)水平定位法当仪器按水平1:n 调节扫描速度时,应采用水平定位法来确定缺陷的位置。若仪器按水平1:1调节扫描速度,那么示波屏上缺陷波前沿所对的水平刻度值f 就是缺陷的水平距离f l 用一次波探伤发现缺陷时 s f f f f l n l d K (5.22)用二次被探伤发现缺陷时