夹紧力计算
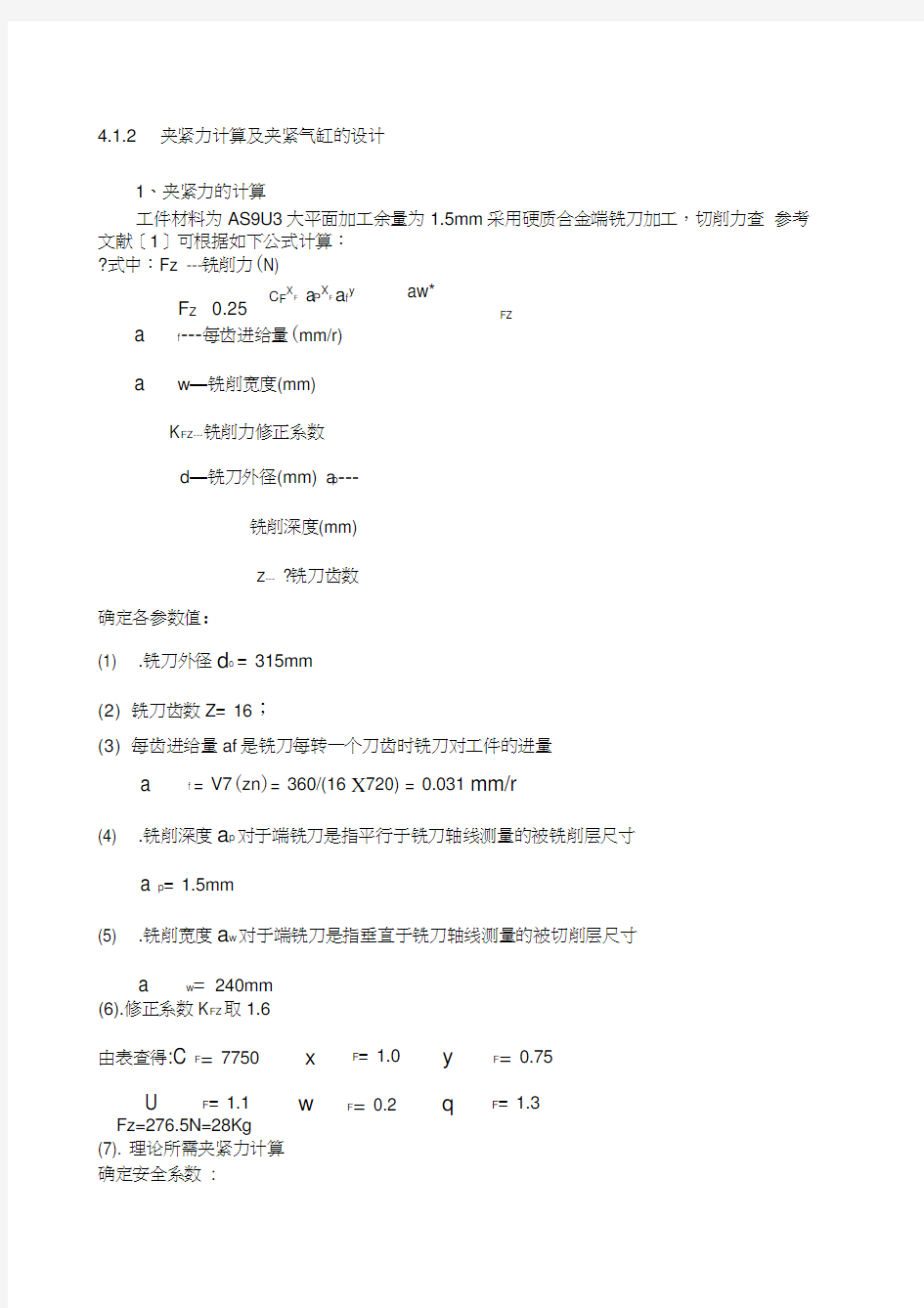

4.1.2 夹紧力计算及夹紧气缸的设计
1、夹紧力的计算
工件材料为AS9U3大平面加工余量为1.5mm 采用硬质合金端铣刀加工,切削力查 参考
文献〔1〕可根据如下公式计算:
?式中:Fz ---铣削力(N)
a
f ---每齿进给量(mm/r) a w —铣削宽度(mm)
K FZ ---铣削力修正系数
d —铣刀外径(mm) a p ---
铣削深度(mm)
Z --- ?铣刀齿数
确定各参数值:
(1) .铣刀外径d o = 315mm
(2) .铣刀齿数Z = 16;
(3) .每齿进给量af 是铣刀每转一个刀齿时铣刀对工件的进量
a f = V7(zn )= 360/(16 X 720) = 0.031 mm/r
(4) .铣削深度a p 对于端铣刀是指平行于铣刀轴线测量的被铣削层尺寸
a p = 1.5mm
(5) .铣削宽度a w 对于端铣刀是指垂直于铣刀轴线测量的被切削层尺寸
a w = 240mm (6).修正系数K FZ 取1.6
由表查得:C F = 7750 x F = 1.0 y
F = 0.75 U F = 1.1 w
F = 0.2 q F = 1.3
Fz=276.5N=28Kg
(7). 理论所需夹紧力计算
确定安全系数 : F Z 0.25 C F X F a P X F a f y aw*
FZ
总的安全系数k = k1 ? k2 ? k3 ? k4
k i---- 一般安全系数;k i取1.7 ;
k 2----加工状态系数;由于是精加工,所以k2取1;
k 3 --- 刀具钝化系数;k 3取i.4;
k 4 --- 断续切削系数;k 4取1.2;
??? k = 1.7 x 1X 1.4 X 1.2 ?3
W = k ? p= 3X 28kg= 84kg
2. 气缸的选择
Q=W /(i ?n 1 ? n) = 84/(0.8 x 0.8 x 3) = 44kg
由气缸传动的计算公式:
Q=P°( nD 2/4) ?n
式中:P --压缩空气压力=6atm= 6kg/cm2
n-- 气缸摩擦系数,取0.8
i —压板与工件的摩擦系数, 取0.8
n—夹紧气缸个数,本夹具为3
D -- 气缸直径(cm)
D=34.2cm
通过以上理论计算,可以选择直径为50mm勺气缸。但是,考虑到由于铣削过程中每个刀齿的不连续切削,作用于每个刀齿的切削力大小及方向随时都在变化,致使在铣削过程中产生较大的振动,因此,夹具需有足够的夹紧力。此外还考虑到工厂所供压缩空气压力不稳定,零件加工余量发生变化,零件材料缺陷,以及其它不可预见性因素的影响,为安全可靠起见,选择直径为63mm勺气缸。
4.2 铣侧面工装定位精度计算
定位误差是由基准位移误差和基准不重和误差组成的。下面对工序尺寸31.85±0.075 的定位误差进行分析计算。
4.2.1 基准直线位移误差△x1
定位孔尺寸为? 6.045 00.022,园柱定位销尺寸为? 6.045 0.0;;,因工件定位后处于垂
直状态,由于自重定位孔与定位销总是单方向接触,所以基准直线位移误差为:
4.2.2基准角位移误差厶X2
由图可知2-①6.045 00.022孔中心距
L = . 1602348.65" = 414.6mm
定位时因零件自身重量,使得两定位孔移动方向相同。
?? tg △B#X2max—X lma))/(2L)
式中:△ 0 ----两定位孔同向移动时,定位基准的转角
X 2max----定位孔与菱形销之间的最大配合间隙
X 1max —-定位孔与圆柱销之间的最大配合间隙
L ----两定位孔中心距
菱形销尺寸为? 6 0.013,定位孔尺寸为? 6.045 00.022
?X2max= 0.022+0.028+0.045 = 0.95mm
X 1max—0.022+0.028=0.05mm
tg △& —(X2max—X imax)/(2L) —(0.95 —0.05)/(2X414.6)
-4
—0.54 X 10
△ 0 —0.003 °
加工面(长240)两端角位移误差厶X2'为:
240 X sin △& —0.013mm
4.2.3基准不重合误差厶B
由工序简图可知,定位基准是由底平面B和2—? 6.045 00.022孔组成。而工序尺寸31.83 ± 0.4的工序基准为? 6.045 o0.022孔。所以基准不重合误差厶B—0mm
定位误差AD —A X1 +△ X2+A B
—0 + 0.013 + 0—0.013mm
由于0.013mm<± 0.075mm故能很好地满足加工精度求。
4.3 铣侧面工装设计
4.3.1 铣削力的计算
工件材料为铸造铝合金。侧平面加工余量为1mm?采用硬质合金端铣刀加工。切削力可根据如下公式计算:
式中:Fz ---铣削力(N)
a f --- 每齿进给量(mm/r)
a w--- 铣削宽度(mm)
K FZ--- 铣削力修正系数
d 0--- 铣刀外径(mm)
a p--- 铣削深度(mm)
z--- ? 铣刀齿数
确定各参数值:
1、铣刀外径d o= 125mm
2、铣刀齿数Z= 8;
3、每齿进给量af 是铣刀每转一个刀齿时铣刀对工件的进量:
a f = V f/(z n) = 638/(8 X1120) = 0.071mm/r
4. 铣削深度a p 对于端铣刀是指平行于铣刀轴线测量的被铣
削层尺寸:
a p = 1mm
5. 铣削宽度a w对于端铣刀是指垂直于铣刀轴线测量的被切削层尺寸
a w= 70mm
6. 修正系数K FZ取1.6 ;
由表查得: c F= 7750 x F= 1.0 y F= 0.75 u F= 1.1 w F= 0.2 q F= 1.3
=168N=17Kg
?
4.3.2 铣削夹具底板强度校核
1 、夹具底板受力分析
底板材料采用45钢,其屈服极限c s= 245N/mm2安全系数ns= 1.5?
2
故其许用应力[c]=c s/ n s=245/1.5 =163N/mm
2 2
许用剪切应力[T ] = 0.6[(T ] = 0.6 x 163N/mm= 98N/mm
底板受力情况如下图所示:
图4.3底板受力图
(1) 支承反力计算如下:
根据公式可知:R B= P= 168N
(2) 弯矩计算如下:
已知:P: 168N L : 420mm
M^=—PL=—168x 0.42 =一70.56N.m
(3) 底板转角计算如下:
- 4
已知:P:168N L : 420mm E:200GPa I : 364583mm
2
9 A=—168X 420 /(2 X200X 364583) = 0.00108 °
2、由上图可知:
(1) 夹具底所承受的最大弯矩:
Qmax=168N
Mmax=16X 0.42=70.56N.m
(2) 对截面尺寸进行校核
弯曲正应力:Wz=bh76=280 x 252/6=1.75 x 105mrri
3 5 -2 2
(T max=Mmax/Wz=70.5X 10/(1.75 X 10 )=40.32 X 10 N/mm
-2 2 2
因为:c max=40.32X 10 N/mm < [①]=163N/mm
另:底板受力转角仅为0.00108。,故可忽略,不予考虑。
所以:底板所选截面280X 25完全满足强度要求。
第三章夹具设计
3.1选择工序
3.2确定定位方案和定位元件
根据零件结构和工序安排,本工序加工时的主要定位基准(限制三个自由度)有二种方案可供选择:
(1)以顶面B作为主要定位基准。
(2)以底面F作为主要定位基准。
方案一与方案二相比较,方案二的定位面积要大一些,而且与其它工序相适应,可
以在整个工艺过程中采用统一的定位基准。因此,本工序决定以底面F为主要定位基准。定位元件选择支承板B10X 90(GB2236-80),带有排屑槽,切屑易清除,宜用于底面上的支承。
图3.1 B型支承板
辅助定位面选择左侧面 E (限制两个自由度),定位元件选择支承板A10X 90(GB2226-80,螺钉头处有1~2mm的^间隙,切屑落进不易清除,宜用于侧面或顶面的支承。
图3.2 B型支承板
3.3切削力及夹紧力的分析计算
本工序为用硬质合金端铣刀粗铣G面,根据手册[1],铣削切削力的计算公式为:F=490a p1.0f z0.74d 10b D0.90z
(3.1 )
注:式中F —铣削力(N);
a p —铣削深度(mr);
f z—每齿进给量(mm/力;
d—铣刀直径(m);b D—铣削宽度(m);z—铣刀的齿数。
其中,a p =2.3mm f z =0.28mm/z, d=160mm b D =78mm z=8,所以
F=490X 2.3 1.0X 0.28 X 160 X 78 X 8
=1108N
根据手册[1],夹紧力的计算公式为:
KF
F k=」^ (3.2)
1 2
夹紧力计算
单螺旋所产生的夹紧力计算 在图1中,螺纹可认为绕圆柱体上的一个斜面,螺母看成是斜面上的一个滑块A ,因此其夹紧力可根据楔的工作原理来计算。 在手柄的作用下,滑块A 沿螺旋斜面移动。已知螺纹为方牙螺纹,手柄上的外加力为P , 手柄长度为L ,螺纹中经为r ,则可求出作用 在滑块A 上的水平力Q1,即: r Q L P ?=?1,r L P Q ?= 1。---(a ) 挡滑块A 沿着斜面作匀速运动时,从图2中可求出水平力Q 1和夹紧力W 之间的关系。 若不考虑摩擦力时,则作用在滑块A 上的力有三个,即夹紧力W 、斜面反作用力N 和水平力Q 1。由于这三个力处于平衡状态,所以可得: αtg W Q ?=1。 若滑块A 与斜面有摩擦力,则反作用力R 与法线N 偏斜一个摩擦角1β。(参看图3) 根据平衡条件,由三角形ARW 可得: ()11βα+?=tg W Q 。------(b ) 将式(a )代入式(b ),可以求出夹紧力W ,即: () 1βα+??= tg r L P W ;
式中:W-----工作夹紧力(公斤力); α-----螺纹升角,r t tg ?= πα2; β1----螺纹配合面的摩擦角(实际计算β1可取°); t------螺纹螺距。 对于标准三角螺纹,升角不大于°,自索性良好,当使用力臂L=14d 平均 的标准扳手时,上式可简化为W ≈130P 。 当螺钉头部为平端面或用螺母夹紧形式时,我们还必须考虑其旋转面间的摩擦力炬损失,此时夹紧力计算的一般公式为: ()1 1?βαtg r tg r L P W ?'++??= ; 式中:1?----旋转接触面的摩擦系数,可取1?tg =; r '----摩擦力炬的半径,与接触处 的形状有关(参见图4)。 当用上述条件同样简化,则得: (1)螺栓头部是平的则W=90P; (2)螺母夹紧形式,则W ≈70R 。 图4
夹紧力计算
夹紧力计算及夹紧气缸的设计 1、夹紧力的计算 工件材料为AS9U3,大平面加工余量为,采用硬质合金端铣刀加工,切削力查参考文献〔1〕可根据如下公式计算: ?式中:Fz ---铣削力(N) a f ---每齿进给量(mm/r) a w ---铣削宽度(mm) K FZ ---铣削力修正系数 d 0---铣刀外径(mm) a p ---铣削深度(mm) z ---?铣刀齿数 确定各参数值: (1).铣刀外径d 0=315mm ; (2).铣刀齿数Z =16; (3).每齿进给量af 是铣刀每转一个刀齿时铣刀对工件的进量: a f =V f /(z ·n)=360/(16×720)=r (4).铣削深度a p 对于端铣刀是指平行于铣刀轴线测量的被铣削层尺寸: a p = (5). 铣削宽度a w 对于端铣刀是指垂直于铣刀轴线测量的被切削层尺寸: a w =240mm (6). 修正系数K FZ 取; FZ w q 0 V w y f X P X F Z K n d Z a a a c 25.0F f F F f F F ??????? =?
由表查得: c F =7750 x F = y F = u F = w F = q F = 1.00.75 1.1 1.3 0.2 77501.50.03124016 0.25 1.6 315720 Z F ????=? ?? Fz==28Kg (7). 理论所需夹紧力计算 确定安全系数: 总的安全系数k =k1·k2·k3·k4 k 1---- 一般安全系数; k 1取; k 2----加工状态系数; 由于是精加工,所以k 2取1; k 3----刀具钝化系数; k 3取; k 4----断续切削系数; k 4取; ∴ k =×1××≈3 W =k ·p =3×28kg =84kg 2. 气缸的选择 Q=W/(i ·η1·n )=84/××3)=44kg 由气缸传动的计算公式: Q=P·(πD2/4)·η 式中: P--压缩空气压力=6atm =6kg/cm2 η--气缸摩擦系数,取 i —压板与工件的摩擦系数,取 n —夹紧气缸个数,本夹具为3 D--气缸直径(cm) D = =D=
夹紧力计算
夹紧力的计算 Mz=328.715Nm 转台径向转矩n=4 刹车片个数Mh=Mz/n 每个刹车片承受的摩擦力矩d=0.3 刹车位置到转台中心距离Fh=2*Mh/d 单个刹车片的摩擦力f=0.18 摩擦系数 F=Fh/2/f 油压提供的法向力ds=0.030 油压作用面的直径s=pi*ds^2/4 油压作用面积P=F/s 油压求得 P =2.1529e+006=2.1529MP 4.1.2 百度夹紧力计算及夹紧气缸的设计 1、夹紧力的计算 工件材料为AS9U3,大平面加工余量为1.5mm,采用硬质合金端铣刀加工,切削力查参考文献〔1〕可根据如下公式计算:?式中:Fz ---铣削力(N) af---每齿进给量(mm/r) aw---铣削宽度(mm) KFZ---铣削力修正系数d0---铣刀外径(mm) ap---铣削深度(mm) z---?铣刀齿数确定各参数值: (1).铣刀外径d0=315mm;(2).铣刀齿数Z=16; (3).每齿进给量af是铣刀每转一个刀齿时铣刀对工件的进量: af=Vf/(z·n)=360/(16×720)=0.031mm/r (4).铣削深度ap对于端铣刀是指平行于铣刀轴线测量的被铣削层尺寸:
ap=1.5mm (5). 铣削宽度aw对于端铣刀是指垂直于铣刀轴线测量的被切削层尺寸: aw=240mm (6). 修正系数KFZ取1.6; 由表查得: cF=7750 xF=1.0 yF=0.75 uF=1.1 qF=1.3 F Fz=276.5N=28Kg (7). 理论所需夹紧力计算确定安全系数: 总的安全系数k=k1·k2·k3·k4 k1---- 一般安全系数;k1取1.7; k2----加工状态系数;由于是精加工,所以k2取1;k3----刀具钝化系数;k3取1.4;k4----断续切削系数;k4取1.2;∴k=1.7×1×1.4×1.2≈3W=k·p=3×28kg=84kg 2. 气缸的选择 Q=W/(i·η1·n)=84/(0.8×0.8×3)=44kg 由气缸传动的计算公式:Q=P·(πD2/4)·η 式中: P--压缩空气压力=6atm=6kg/cm2 η--气缸摩擦系数,取0.8
夹紧力计算
创作编号: GB8878185555334563BT9125XW 创作者: 凤呜大王* 4.1.2 夹紧力计算及夹紧气缸的设计 1、夹紧力的计算 工件材料为AS9U3,大平面加工余量为1.5mm ,采用硬质合金端铣刀加工,切削力查参考文献〔1〕可根据如下公式计算: ?式中:Fz ---铣削力(N) a f ---每齿进给量(mm/r) a w ---铣削宽度(mm) K FZ ---铣削力修正系数 d 0---铣刀外径(mm) a p ---铣削深度(mm) z ---?铣刀齿数 确定各参数值: (1).铣刀外径d 0=315mm ; (2).铣刀齿数Z =16; (3).每齿进给量af 是铣刀每转一个刀齿时铣刀对工件的进量: a f =V f /(z ·n)=360/(16×720)=0.031mm/r (4).铣削深度a p 对于端铣刀是指平行于铣刀轴线测量的被铣削层尺寸: a p =1.5mm (5). 铣削宽度a w 对于端铣刀是指垂直于铣刀轴线测量的被切削层尺寸: FZ w q 0 V w y f X P X F Z K n d Z a a a c 25.0F f F F f F F ??????? =?
a w =240mm (6). 修正系数K FZ 取1.6; 由表查得: c F =7750 x F =1.0 y F =0.75 u F =1.1 w F =0.2 q F =1.3 1.00.75 1.1 1.3 0.2 77501.50.03124016 0.25 1.6 315720 Z F ????=? ?? Fz=276.5N=28Kg (7). 理论所需夹紧力计算 确定安全系数: 总的安全系数k =k1·k2·k3·k4 k 1---- 一般安全系数; k 1取1.7; k 2----加工状态系数; 由于是精加工,所以k 2取1; k 3----刀具钝化系数; k 3取1.4; k 4----断续切削系数; k 4取1.2; ∴ k =1.7×1×1.4×1.2≈3 W =k ·p =3×28kg =84kg 2. 气缸的选择 Q=W/(i ·η1·n )=84/(0.8×0.8×3)=44kg 由气缸传动的计算公式: Q=P·(πD2/4)·η 式中: P--压缩空气压力=6atm =6kg/cm2 η--气缸摩擦系数,取0.8 i —压板与工件的摩擦系数,取0.8 n —夹紧气缸个数,本夹具为3 D--气缸直径(cm) D = =D=34.2cm 通过以上理论计算,可以选择直径为50mm 的气缸。但是,考虑到由于铣削过程中每个刀齿的不连续切削,作用于每个刀齿的切削力大小及方向随时都在变化,致使在铣削过程中产生较大的振动,因此,夹具需有足够
夹紧力计算
盛年不重来,一日难再晨。及时宜自勉,岁月不待人。 4.1.2 夹紧力计算及夹紧气缸的设计 1、夹紧力的计算 工件材料为AS9U3,大平面加工余量为1.5mm ,采用硬质合金端铣刀加工,切削力查参考文献〔1〕可根据如下公式计算: ?式中:Fz ---铣削力(N) a f ---每齿进给量(mm/r) a w ---铣削宽度(mm) K FZ ---铣削力修正系数 d 0---铣刀外径(mm) a p ---铣削深度(mm) z ---?铣刀齿数 确定各参数值: (1).铣刀外径d 0=315mm ; (2).铣刀齿数Z =16; (3).每齿进给量af 是铣刀每转一个刀齿时铣刀对工件的进量: a f =V f /(z ·n)=360/(16×720)=0.031mm/r (4).铣削深度a p 对于端铣刀是指平行于铣刀轴线测量的被铣削层尺寸: a p =1.5mm (5). 铣削宽度a w 对于端铣刀是指垂直于铣刀轴线测量的被切削层尺寸: a w =240mm (6). 修正系数K FZ 取1.6; 由表查得: c F =7750 x F =1.0 y F =0.75 u F =1.1 w F =0.2 q F =1.3 FZ w q 0 V w y f X P X F Z K n d Z a a a c 25.0F f F F f F F ??????? =?
1.0 0.75 1.1 1.3 0.2 77501.50.03124016 0.25 1.6 315720 Z F ????=? ?? Fz=276.5N=28Kg (7). 理论所需夹紧力计算 确定安全系数: 总的安全系数k =k1·k2·k3·k4 k 1---- 一般安全系数; k 1取1.7; k 2----加工状态系数; 由于是精加工,所以k 2取1; k 3----刀具钝化系数; k 3取1.4; k 4----断续切削系数; k 4取1.2; ∴ k =1.7×1×1.4×1.2≈3 W =k ·p =3×28kg =84kg 2. 气缸的选择 Q=W/(i ·η1·n )=84/(0.8×0.8×3)=44kg 由气缸传动的计算公式: Q=P·(πD2/4)·η 式中: P--压缩空气压力=6atm =6kg/cm2 η--气缸摩擦系数,取0.8 i —压板与工件的摩擦系数,取0.8 n —夹紧气缸个数,本夹具为3 D--气缸直径(cm) D = =D=34.2cm 通过以上理论计算,可以选择直径为50mm 的气缸。但是,考虑到由于铣削过程中每个刀齿的不连续切削,作用于每个刀齿的切削力大小及方向随时都在变化,致使在铣削过程中产生较大的振动,因此,夹具需有足够的夹紧力。此外还考虑到工厂所供压缩空气压力不稳定,零件加工余量发生变化,零件材料缺陷,以及其它不可预见性因素的影响,为安全可靠起见,选择直径为63mm 的气缸。 4.2 铣侧面工装定位精度计算 定位误差是由基准位移误差和基准不重和误差组成的。下面对工序尺寸31.85±0.075的定位误差进行分析计算。 4.2.1 基准直线位移误差△x 1 定位孔尺寸为φ6.0450.0220+,园柱定位销尺寸为φ6.0450.013 0.028--,因工件定位后
夹紧力计算 (2)
4.1.2 夹紧力计算及夹紧气缸的设计 1、夹紧力的计算 工件材料为AS9U3,大平面加工余量为1.5mm ,采用硬质合金端铣刀加工,切削力查参考文献〔1〕可根据如下公式计算: ?式中:Fz ---铣削力(N) a f ---每齿进给量(mm/r) a w ---铣削宽度(mm) K FZ ---铣削力修正系数 d 0---铣刀外径(mm) a p ---铣削深度(mm) z ---?铣刀齿数 确定各参数值: (1).铣刀外径d 0=315mm ; (2).铣刀齿数Z =16; (3).每齿进给量af 是铣刀每转一个刀齿时铣刀对工件的进量: a f =V f /(z ·n)=360/(16×720)=0.031mm/r (4).铣削深度a p 对于端铣刀是指平行于铣刀轴线测量的被铣削层尺寸: a p =1.5mm (5). 铣削宽度a w 对于端铣刀是指垂直于铣刀轴线测量的被切削层尺寸: a w =240mm (6). 修正系数K FZ 取1.6; 由表查得: c F =7750 x F =1.0 y F =0.75 u F =1.1 w F =0.2 q F =1.3 FZ w q 0 V w y f X P X F Z K n d Z a a a c 25.0F f F F f F F ??????? =?
1.00.75 1.1 1.3 0.2 77501.50.03124016 0.25 1.6 315720 Z F ????=? ?? Fz=276.5N=28Kg (7). 理论所需夹紧力计算 确定安全系数: 总的安全系数k =k1·k2·k3·k4 k 1---- 一般安全系数; k 1取1.7; k 2----加工状态系数; 由于是精加工,所以k 2取1; k 3----刀具钝化系数; k 3取1.4; k 4----断续切削系数; k 4取1.2; ∴ k =1.7×1×1.4×1.2≈3 W =k ·p =3×28kg =84kg 2. 气缸的选择 Q=W/(i ·η1·n )=84/(0.8×0.8×3)=44kg 由气缸传动的计算公式: Q=P·(πD2/4)·η 式中: P--压缩空气压力=6atm =6kg/cm2 η--气缸摩擦系数,取0.8 i —压板与工件的摩擦系数,取0.8 n —夹紧气缸个数,本夹具为3 D--气缸直径(cm) D = =D=34.2cm 通过以上理论计算,可以选择直径为50mm 的气缸。但是,考虑到由于铣削过程中每个刀齿的不连续切削,作用于每个刀齿的切削力大小及方向随时都在变化,致使在铣削过程中产生较大的振动,因此,夹具需有足够的夹紧力。此外还考虑到工厂所供压缩空气压力不稳定,零件加工余量发生变化,零件材料缺陷,以及其它不可预见性因素的影响,为安全可靠起见,选择直径为63mm 的气缸。 4.2 铣侧面工装定位精度计算 定位误差是由基准位移误差和基准不重和误差组成的。下面对工序尺寸31.85±0.075的定位误差进行分析计算。
夹紧力计算
4.1.2夹紧力计算及夹紧气缸的设计1、夹紧力的计算工件材料为AS9U3,大平面加工余量为1.5mm,采用硬质合金端铣刀加工,切削力查参考文献〔1〕可根据如下公式计算:?式中:Fz---铣削力(N)af---每齿进给量(mm/r)aw---铣削宽度(mm)KFZ---铣削力修正系数d0---铣刀外径(mm)ap---铣削深度(mm)z---?铣刀齿数确定各参数值:(1).铣刀外径d0=315mm;(2).铣刀齿数Z=16;(3).每齿进给量af是铣刀每转一个刀齿时铣刀对工件的进量:af=Vf/(z·n)=360/(16×720)=0.031mm/r(4).铣削深度ap对于端铣刀是指平行于铣刀轴线测量的被铣削层尺寸:ap=1.5mm(5).铣削宽度aw对于端铣刀是指垂直于铣刀轴线测量的被切削层尺寸:aw=240mm(6).修正系数KFZ取1.6;由表查得:cF=7750xF=1.0yF=0.75uF=1.1wF=0.2qF=1.3Fz=276.5N=28Kg(7).理论所需夹紧力计算确定安全系数:总的安全系数k=k1·k2·k3·k4k1----一般安全系数;k1取1.7;k2----加工状态系数;由于是精加工,所以k2取1;k3----刀具钝化系数;k3取1.4;k4----断续切削系数;k4取1.2;∴k=1.7×1×1.4×1.2≈3W=k·p=3×28kg=84kg2.气缸的选择Q=W/(i·η1·n)=84/(0.8×0.8×3)=44kg由气缸传动的计算公式:Q=P·(πD2/4)·η式中:P--压缩空气压力=6atm=6kg/cm2η--气 ? 提出了一种计算铣削加工中夹紧工件所需最小夹紧力的简洁方法。
夹紧力计算 (2)
4、1、2 夹紧力计算及夹紧气缸的设计 1、夹紧力的计算 工件材料为AS9U3,大平面加工余量为1、5mm,采用硬质合金端铣刀加工,切削力查参考文献〔1〕可根据如下公式计算: ?式中:Fz ---铣削力(N) a f ---每齿进给量(mm/r) a w ---铣削宽度(mm) K FZ ---铣削力修正系数 d 0---铣刀外径(mm) a p ---铣削深度(mm) z ---?铣刀齿数 确定各参数值: (1)、铣刀外径d 0=315mm ; (2)、铣刀齿数Z =16; (3)、每齿进给量af 就是铣刀每转一个刀齿时铣刀对工件的进量: a f =V f /(z ·n)=360/(16×720)=0、031mm/r (4)、铣削深度a p 对于端铣刀就是指平行于铣刀轴线测量的被铣削层尺寸: a p =1、5mm (5)、 铣削宽度a w 对于端铣刀就是指垂直于铣刀轴线测量的被切削层尺寸: a w =240mm (6)、 修正系数K FZ 取1、6; 由表查得: c F =7750 x F =1、0 y F =0、75 u F =1、1 w F =0、2 q F =1、3 FZ w q 0V w y f X P X F Z K n d Z a a a c 25.0F f F F f F F ???????=?
1.00.75 1.1 1.30.277501.50.031240160.25 1.6315720Z F ????=??? Fz=276、5N=28Kg (7)、 理论所需夹紧力计算 确定安全系数: 总的安全系数k =k1·k2·k3·k4 k 1---- 一般安全系数; k 1取1、7; k 2----加工状态系数; 由于就是精加工,所以k 2取1; k 3----刀具钝化系数; k 3取1、4; k 4----断续切削系数; k 4取1、2; ∴ k =1、7×1×1、4×1、2≈3 W =k ·p =3×28kg =84kg 2、 气缸的选择 Q=W/(i ·η1·n )=84/(0、8×0、8×3)=44kg 由气缸传动的计算公式: Q=P·(πD2/4)·η 式中: P--压缩空气压力=6atm =6kg/cm2 η--气缸摩擦系数,取0、8 i —压板与工件的摩擦系数,取0、8 n —夹紧气缸个数,本夹具为3 D--气缸直径(cm) D ==D=34、2cm 通过以上理论计算,可以选择直径为50mm 的气缸。但就是,考虑到由于铣削过程中每个刀齿的不连续切削,作用于每个刀齿的切削力大小及方向随时都在变化,致使在铣削过程中产生较大的振动,因此,夹具需有足够的夹紧力。此外还考虑到工厂所供压缩空气压力不稳定,零件加工余量发生变化,零件材料缺陷,以及其它不可预见性因素的影响,为安全可靠起见,选择直径为63mm 的气缸。 4、2 铣侧面工装定位精度计算 定位误差就是由基准位移误差与基准不重与误差组成的。下面对工序尺寸31、85±0、075的定位误差进行分析计算。
实用文库汇编之夹紧力计算
*实用文库汇编之4.1.2 夹紧力计算及夹紧气缸的设计* 1、夹紧力的计算 工件材料为AS9U3,大平面加工余量为1.5mm ,采用硬质合金端铣刀加工,切削力查参考文献〔1〕可根据如下公式计算: ?式中:Fz ---铣削力(N) a f ---每齿进给量(mm/r) a w ---铣削宽度(mm) K FZ ---铣削力修正系数 d 0---铣刀外径(mm) a p ---铣削深度(mm) z ---?铣刀齿数 确定各参数值: (1).铣刀外径d 0=315mm ; (2).铣刀齿数Z =16; (3).每齿进给量af 是铣刀每转一个刀齿时铣刀对工件的进量: a f =V f /(z ·n)=360/(16×720)=0.031mm/r (4).铣削深度a p 对于端铣刀是指平行于铣刀轴线测量的被铣削层尺寸: a p =1.5mm (5). 铣削宽度a w 对于端铣刀是指垂直于铣刀轴线测量的被切削层尺寸: a w =240mm (6). 修正系数K FZ 取1.6; 由表查得: c F =7750 x F =1.0 y F =0.75 u F =1.1 w F =0.2 q F =1.3 FZ w q 0 V w y f X P X F Z K n d Z a a a c 25.0F f F F f F F ??????? =?
1.00.75 1.1 1.3 0.2 77501.50.03124016 0.25 1.6 315720 Z F ????=? ?? Fz=276.5N=28Kg (7). 理论所需夹紧力计算 确定安全系数: 总的安全系数k =k1·k2·k3·k4 k 1---- 一般安全系数; k 1取1.7; k 2 ----加工状态系数; 由于是精加工,所以k 2 取1; k 3----刀具钝化系数; k 3取1.4; k 4----断续切削系数; k 4取1.2; ∴ k =1.7×1×1.4×1.2≈3 W =k ·p =3×28kg =84kg 2. 气缸的选择 Q=W/(i ·η1·n )=84/(0.8×0.8×3)=44kg 由气缸传动的计算公式: Q=P·(πD2/4)·η 式中: P--压缩空气压力=6atm =6kg/cm2 η--气缸摩擦系数,取0.8 i —压板与工件的摩擦系数,取0.8 n —夹紧气缸个数,本夹具为3 D--气缸直径(cm) D = =D=34.2cm 通过以上理论计算,可以选择直径为50mm 的气缸。但是,考虑到由于铣削过程中每个刀齿的不连续切削,作用于每个刀齿的切削力大小及方向随时都在变化,致使在铣削过程中产生较大的振动,因此,夹具需有足够的夹紧力。此外还考虑到工厂所供压缩空气压力不稳定,零件加工余量发生变化,零件材料缺陷,以及其它不可预见性因素的影响,为安全可靠起见,选择直径为63mm 的气缸。 4.2 铣侧面工装定位精度计算 定位误差是由基准位移误差和基准不重和误差组成的。下面对工序尺寸31.85±0.075的定位误差进行分析计算。
夹紧力参考计算
2.4 切削力和夹紧力计算 本设计采用主偏角45=?°,刀尖圆角半径r=2mm 的YG8刀具粗镗,无外皮加工,已知HB=200,V=40(米/分),S=1(毫米/转),t=2mm 21.165.02.1X 0.051P PX K HB s t = 3255.075.014.5PZ PZ Z K K HB ts P = 102 60P N Z ?=v 式中:v----------------切削速度(米/分); X P -------------------轴向力(公斤);Z P -----------圆周力(公斤) S---------每转进给量(毫米/转); HB----------布氏硬度 N---------------切削功率(千瓦); t---------------切削深度(毫米); 由主偏角45=?°查得PX2K =1,PZ2K =1。由刀尖圆角半径r=2mm ,查得PZ3K =1。 X P =0.051120012.115.60.21????=39.80(公斤) Z P =11200124.155.505.70?????=94.74(公斤) 102 604094.74N ??==0.62(千瓦) 镗削时圆周切削力Z P 方向是变化的,按照可能出现的最坏情况来确定所需的夹紧力。镗孔时的轴向切削力(走刀抗力)通常都很小而且方向不变,因此比较容易考虑其对夹紧力的影响. 由于是相同条件下的两面对镗,当圆周切削力Z1P 如下简图在垂直向下作用于工件,Z2P 垂直向上作用于工件时,有使工件产生绕O 点回转并同时抬起工件的最大翻转力矩。 此时为防止工件颠覆所需的夹紧力可按下列公式确定: 22112211l Q l Q L KP L KP Z Z +=+ 21Q Q = =Q Z2Z1P P ==94.74(公斤) 33L 1=mm 213L 2=mm =1l 0mm =2l 165mm 安全系数K=2 2?94.74?33+2?94.74?213=165021?+?Q Q Q=21Q Q ==248.5(公斤) 当Z1P 、Z2P 同时作用在水平相同方向上时,有使工件产生平移的趋势。当不允许定位销承受切削力时,工件的静力平衡条件为: K Z1P +K Z2P =2Q (1f +2f ) 查得工件与压杆摩擦系数1f =0.15 工件与支承板摩擦系数2f =0.2 Q=4?94.74()2.015.02+÷÷=541.4(公斤) 将防止工件抬起或平移所需的夹紧力加以比较,按较大值确定所需的夹紧
夹紧力计算
现代夹具设计手册: 《现代夹具设计手册》是2010年机械工业出版社出版的图书,作者是朱耀祥,浦林祥。 内容简介: 本手册全面总结了我国半个世纪来的工业化过程中机械制造业内设计制造各类夹具的丰富经验,绝大部分资料都通过生产实践的考验,包括从国外引进后消化、吸收和改进的内容,也包含作者以往亲历的研发项目的成果。 本手册内容主要包括:夹具总论;夹具功能部件的典型结构;夹具设计计算;专用夹具常用零件及其标准或规范;气动、液压、电力、电磁、真空夹具传动系统及其元件和夹具案例;机床专用夹具设计方法;机床专用夹具设计及典型图例;可调夹具和成组夹具;组合夹具,数控机床、加工中心、柔性制造系统用夹具;检验夹具;焊接夹具;计算机辅助夹具设计等。 本手册主要适用于各种机床夹具、焊接夹具、检验夹具等的设计、制作、使用人员,管理人员,相关专业在校师生。 图书目录: 序 第1章夹具总论 1.1 夹具产生和发展的背景 1.1.1 夹具和机床附件 1.1.2 机床专用夹具催生了现代大批大量生产
1.1.3 夹具是现代制造系统的重要组成部分1.2 夹具的功能、组成和设计要求 1.2.1 夹具的基本结构和组成 1.2.2 夹具的各种功能 1.2.3 设计夹具的基本要求 1.3 夹具和机械零件的分类 1.3.1 夹具的各种分类方法 1.3.2 根据生产规模或品种和批量的分类最重要1.3.3 机械零件和夹具分类编码系统 1.4 夹具系统的选择和技术经济指标 1.4.1 选择夹具系统的基本原则 1.4.2 选择夹具系统的步骤 1.4.3 常用夹具系统的技术经济指标 1.4.4 夹具设计制作成本的估算 1.4.5 使用专用夹具的简易经济分析 1.4.6 夹具系统的经济分析 1.5 现代夹具发展趋势 1.5.1 夹具柔性化 1.5.2 夹具自动化和智能化 1.5.3 计算机辅助夹具设计(CAD) 1.5.4 应对“寻位-加工”的挑战 1.5.5 结语
夹紧力计算
切削力和夹紧力的合理计算。在成为技术专家之前,我们都是初学者。我们只需要确定已知的参数,然后用程序计算切削力。 一、油缸切削力和夹紧力的计算。 根据一些已知的气缸参数,我们可以使用Novex软件快速估算切削数据。 1.切削力计算。 图形计算步骤如下: (1)1N.MM转换为N.M(698N.CM/1000=0.698N.M); 2N.M×102 kg(0.698×102=71.2 kg)。 2.气缸压紧力的计算。 1油缸直径换算为半径:25/20=1.25; 2计算面积:1.25*1.25=1.56*3.14=4.9; 3兆帕斯卡至千克:4Mpa=40kgf/cm2; 4面积乘以kg:4.9×40=196; 5乘以气缸数:196*3=588.8千克。 二是机床夹具设计过程中夹紧力的计算情况。 1.机械加工夹具夹紧力的计算。 机床(加工中心)液压夹具采用HLC-M32液压缸。 根据标准询价,圆柱体直径为φ32。
该夹具共使用6个液压缸。 夹紧力的计算方法如图6所示。 2,f=ps=pπ(d/2)2=4823.04n.。 根据力矩平衡(杠杆)原理,该夹具的动力臂为L1,阻力臂为L2。公式为:功率臂长度×功率=电阻臂长度×电阻。 计算三个电阻f1、f2和f3以及夹具的夹紧力(图7)。 铣削切削力的计算。 使用下面的软件,这个过程的基本参数,如转速和进给速率。经计算,进给力FF约为12052N,径向力FP约为12873N,主切削力Fe约为36522N。以上计算的机床夹紧力f为53053N。夹紧力×摩擦系数(支撑块和铝合金为0.45)=23874n>ff>fp。当摩擦力大于进给切削力和径向切削力时,确保定位销不受力。工件重力质量=9.8×质量=196N,小重力不影响结果,合理选择液压缸压力。 结论。 过去,油缸和钢瓶的尺寸大多由设计者的经验决定。利用软件计算结果进行合理选型,减少了因选错造成的浪费。合适的夹紧力可避免夹紧力过小、过紧对机床造成的损坏;夹紧力过大,会压碎工件,造成变形。夹具设计是一个复杂的过程,上述设计计算过程希望对设计者选择最合理的夹紧力,提高夹具的优化设计起到一定的参考作用。
夹紧力参考资料
附件1: 3.2.2 夹紧力作用点 选择作用点的问题是指在夹紧方向已定的情况下,确定夹紧力作用点的位置和数目。由于夹紧力作用点的位置和数目直接影响工件定位后的可靠性和夹紧后的变形,应依据以下原则: 1.夹紧力作用点应落在支承元件上或几个支承元件所形成的支承面内 如图3-6(a)所示,夹紧力作用在支承面范围之外,会使工件倾斜或移动,而如图3-6(b)所示,夹紧力作用在支承面范围之内则是合理的。 (a)不合理(b)合理 图3-6 夹紧力作用点应在支承面内 2.夹紧力作用点应落在工件刚性好的部位上 如图3-7所示,将作用在壳体中部的单点改成在工件外缘处的两点夹紧,工件的变形大为改善,且夹紧也更可靠。该原则对刚度差的工件尤其重要。 (a)不合理(b)合理 图3-7 夹紧力作用点应在刚性较好部位 3.夹紧力作用点应尽可能靠近被加工表面,以减小切削力对工件造成的翻转力矩 必要时应在工件刚性差的部位增加辅助支承并施加夹紧力,以免振动和变形。如图3-8所示,支承a尽量靠近被加工表面,同时给予夹紧力Q2。这样翻转力矩小又增加了工件的刚性R,既保证了定位夹紧的可靠性,又减小了振动和变形。
图3-8 夹紧力作用点应靠近加工表面 3.2.3 夹紧力大小 夹紧力的大小主要影响工件定位的可靠性、工件夹紧变形以及夹紧装置的结构尺寸和复杂性,夹紧力大小要适当,过大了会使工件变形,过小了则在加工时工件会松动,造成报废甚至发生事故。 1.夹紧力的大小确定方法 在实际设计中确定夹紧力大小的方法有两种:经验类比法和分析计算法。 经验类比法如手动夹紧时,可凭人力来控制夹紧力的大小,一般不需要算出所需夹紧力的确切数值,只是必要时进行概略的估算。 采用分析计算法,一般将夹具和工件看做一刚性系统,以简化计算。根据工件在切削力、夹紧力(重型工件要考虑重力,高速时要考虑惯性力)作用下处于静力平衡,列出静力平衡方程式,即可算出理论夹紧力/Q ,再乘以安全系数K ,作为所需的实际夹紧力Q 。 K 的取值范围一般为1.5~3,粗加工时为2.5~3,精加工时为1.5~2。 夹紧力的计算可根据图3-4中的几种情况来进行。现分析其中的三种情况: 1)切削力完全作用在支承上。 这时可不增加夹紧力或增加少量的夹紧力,如在拉削套筒、盘类零件的孔时就可不增加夹紧力。 2)切削力与夹紧力的方向垂直。 夹紧力的情况如图3-4(b )所示,切削力F 的计算公式为: ()121Gf f f Q F ++= (3-1) 式中,f 1为工件已加工定位面与定位元件之间的摩擦系数,一般取0.10~0.15;f 2为夹紧元件与工件夹紧表面之间的摩擦系数,一般取0.2~0.25。 不计工件重力,并考虑安全系数,则由式(3-1)变形可得夹紧力为: (3-2) 3)切削力与夹紧力的方向相反。 夹紧力的情况如图3-4(f )所示:此时需要夹紧力最大为: G KF Q += (3-3) 2.计算夹紧力的典型实例 1)车削加工时的夹紧力计算
夹紧力计算
塑料零件夹紧力的计算方法和注塑机选择的经验方法:夹紧力=产品的投影面积×面积常数面积常数的选择如下:序号塑料类型面积常数1.5?2ton / in2(0.233 ?0.31kg / cm2)2工程塑料3?4TON / in2(0.465?0.62kg / cm2)3纤维工程塑料4?6ton / in2(0.62?0.93kg / cm2)优点:简单方便;缺点:太多粗糙,随机且精度低;只有基于丰富的经验,我们才能知道如何选择合适的常数。常数法:夹紧力=投影面积×常数×1.2常数的选择如下:序号塑料类型面积常数1pe1.0?1.5ton / in2(0.155?0.233kg / cm2)2软pvc1.5?2.0ton / in2(0.233?0.31kg / cm2)3ps / pp1.5?2.5ton / in2(0.233?0.387kg / cm2)4pa2.0?2.5ton / in2(0.31?0.387kg / cm2)4pa2.0?2.5ton / in2(0.31?0.387kg / cm2)5abs2.0?3.0ton / in2(0.0.0.0.0.0?3.0ton / in2 / in2 / in2(0.2336 PPS 3.0吨/ in2(0.465 kg / cm2)7pc3.0- 3.5吨/ in2(0.465?0.5421kg / cm2)的优点8纤维pc4.0?6.0ton / in2(0.62?0.93kg / cm2)的优点是增加了安全系数,考虑到不同塑料之间的差异,列出不同的常数,这比经验方法更合理;缺点:对于相同的原料和不同的零件结构,该方法的应用仍然是任意的;工艺夹紧方法:投影面积s×腔压力P≤工艺夹紧力P≤(0.8?0.9)ra锁模力P腔压力与壁厚和流长比的关系曲线如下:
夹紧力计算
夹紧力大小对于保证定位稳定、夹紧可靠、确定夹紧装置的结构尺寸等都有很大关系。夹紧力过小,则夹紧不稳定,在加工过程中工件仍会发生位移而破坏定位,轻则影响加工质量,重则造成生产事故;夹紧力过大,将会增大夹紧装置的结构尺寸,也会使夹紧变形增大,影响加工质量。所以,在夹紧力方向、作用点确定之后,还须确定切合实际、恰当的夹紧力大小。 在加工过程中,工件受到切削力、离心力、惯性力及重力的作用,理论上夹紧力的作用效果应与上述各力(矩)相平衡,但在不同条件下,这些作用力(矩)在平衡力系中对工件所起的作用并不相同。如常规切削加工中、小型工件时,起决定作用的因素是切削力(矩)。此外,切削力本身在加工过程中随切削过程的进行而变化,很难用准确的公式确定其大小;夹紧力大小还与工艺系统的刚度、夹紧机构的传动效率等有关,因此夹紧力的计算是一个很复杂的问题,一般只能作粗略的估算。 目前,大多采用切削原理实验公式粗略算出切削力(矩),再对夹紧力作简化估算。 估算夹紧力时,首先假设系统为刚性系统,切削过程处于稳定状态。常规情况下,为简化计算,只考虑切削力(矩)对夹紧的影响,切削力(矩)用切削原理的实验公式计算,对重型工件应计及工件重力对夹紧的影响;在工件高速运动的场合,必须计入惯性力,尤其在精加工时,惯性力常是影响夹紧力的主要因素。其次,分析并弄清对夹紧最不利的加工瞬时位置和情况,将此时所需的夹紧力定为最
大值;根据此时受力情况列出其静力平衡方程式,即可解算出理论上的夹紧力Fj。最后按下式计算出实际需要的夹紧力。 FjK =K·Fj (5-6) 式中FjK-实际需要的夹紧力,单位为N; K-安全系数,一般取K=1.5~3,粗加工取大值,精加工取小值; Fj-在最不利的条件下由静力平衡计算出的夹紧力,单位为N。 上述估算方法,对夹具设计来说,其准确程度是能满足要求的。