自动配料系统设计PLC课程设计报告
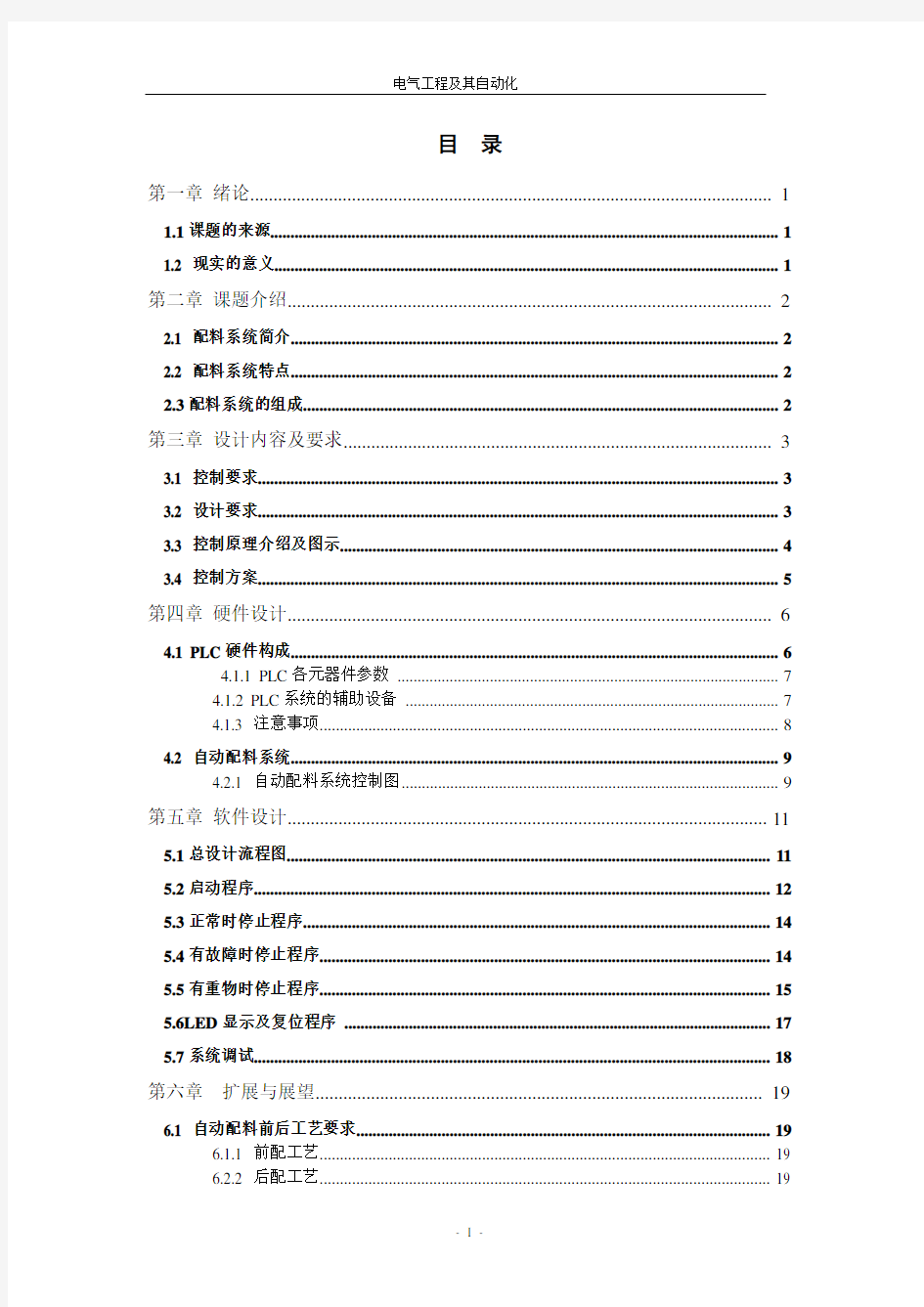

目录
第一章绪论 (1)
1.1课题的来源 (1)
1.2 现实的意义 (1)
第二章课题介绍 (2)
2.1 配料系统简介 (2)
2.2 配料系统特点 (2)
2.3配料系统的组成 (2)
第三章设计内容及要求 (3)
3.1 控制要求 (3)
3.2 设计要求 (3)
3.3 控制原理介绍及图示 (4)
3.4 控制方案 (5)
第四章硬件设计 (6)
4.1 PLC硬件构成 (6)
4.1.1 PLC各元器件参数 (7)
4.1.2 PLC系统的辅助设备 (7)
4.1.3 注意事项 (8)
4.2 自动配料系统 (9)
4.2.1 自动配料系统控制图 (9)
第五章软件设计 (11)
5.1总设计流程图 (11)
5.2启动程序 (12)
5.3正常时停止程序 (14)
5.4有故障时停止程序 (14)
5.5有重物时停止程序 (15)
5.6LED显示及复位程序 (17)
5.7系统调试 (18)
第六章扩展与展望 (19)
6.1 自动配料前后工艺要求 (19)
6.1.1 前配工艺 (19)
6.2.2 后配工艺 (19)
6.2发展趋势 (19)
设计小结 (21)
致谢 (22)
参考资料 (23)
附录ⅠPLC程序 (24)
第一章绪论
1.1课题的来源
自动配料系统是一个针对各种不同类型的物料(固体或液体)进行输送、配比、加热、混合以及成品包装等全生产过程的自动化生产线。广泛应用于化工、冶金、建材、食品、饲料加工等行业。
在氧化铝生产及其它工业生产中,经常会遇到多种物料配比控制的情况。在手动控制状态下,需要根据生产情况,计算出各物料的配比,再根据配比,分别计算出各物料的理想下料量,对各台设备分别设定,来满足配比的要求。当生产情况发生变化,需要改变下料量时,则需要再次分别计算各物料的设定值,再次分别设定。这种人工操作方式计算,操作时间长,且容易出错,给生产带来不良因素。
而采用PLC控制方式以及新颖的变频调速喂料机构,配合配料控制软件包,实现物料传送、配料控制、配方设计、生产数据管理等功能。并可以通过网络实现多个配料系统的集合控制。
1.2 现实的意义
配料工人收到每天的生产作业表后, 将依次对每种原料进行称重?根据配料的多少, 先计算每种成分的重量,然后在各种成分的料桶中取料,送到电子称上进行称重,最后进行包装?在这个过程中工人工作繁重,出错率高,称重重量无监测,生产数据无纪录等不能保证企业的生产工艺?文中以PC机编程,可编程逻辑控制器(PLC),现场总线技术等现代工控技术为基础,开发了以PC机为上位机, 以PLC作为下位机的自动配料系统?在整个生产过程中,一旦生产计划制定完成,计算机将按照计划对每种原料进行称重,不再需要人工来干预?在这个过程中工人只是进行取料,由计算机通过电子称发来的数据校核重量,减轻了工人的工作负担,提高了工作效率?
第二章课题介绍
2.1 配料系统简介
自动配料控制系统在各行业的应用已屡见不鲜,如:冶金,有色金属,化工,建材,食品等行业。它是成品生产的首要环节,特别是有连续供料要求的行业,其配比的过程控制直接影响了成品的质量,它是企业取得最佳经济效益的先决条件。虽然行业各自不同的工艺特点对配料控制要求也不同,但其高可靠性,先进性,开方性,免维护性,可扩展性是工厂自动化FA所追求的一致目标。
2.2 配料系统特点
(1) 配料现场粉尘大, 环境恶劣;
(2) 各组份在配方中所占比例不同, 有时甚至差异悬殊;
(3) 配料速度和精度要求高;
(4) 配方可能经常变换、调整;
(5) 物料可能受环境温度、湿度影响。
2.3配料系统的组成
自动配料系统是对粉粒或液体物料进行单秤称重并按所选配方混合这一工业过程进行实时监控管理的自动化系统,已广泛应用于冶金、建材、化工、医药、粮食及饲料等行业。一般的工业自动配料系统由以下几部分组成。
(1) 给料部分:给料部分是从料仓(或储罐)向称重设备中加料的执行机构。根据物料的不同特性,可以选用不同的给料设备,如电磁振动给料机、螺旋给料机、单(双) 速电磁阀等。
(2) 称量部分:称量部分由传感器、标准连接件、接线盒和称量斗组成,与称量仪表一起进行物料的称量以及误差的检测。
(3) 排料设备:排料可以是称重设备(减量法) 或排放设备(增量法、零位法) 。通常由排空阀门、电磁振动给料机、螺旋给料机、电(气) 动阀门等组成。所有设备均应根据现场的工艺条件和物料的性质等进行设计和选择。
(4) 配料控制系统:配料控制系统由称量仪表、可编程控制器、上位工控机及其它控制器件等组成。
(5) 校秤系统:配料系统传感器应进行定期调校,以保证系统配料精度。
第三章设计内容及要求
3.1 控制要求
系统启动后,配料装置能自动识别货车到位情况及对货车进行自动配料,当车装满时,配料系统自动关闭。本设计的突出点是故障检测部分的设计,首先,当某一节传送带发生故障时,该节传送带和其前面的传送带会立即停止,该节之后的传送带会在一定的延时后停止。其次,当某节传送带上的物体过重时,该节传送带和其前面的传送带会立即停止,并且数码显示电路会显示发生故障的电机的号码,该节之后的传送带会在一定的延时后停止。
3.2 设计要求
考虑到配料现场粉尘大, 环境恶劣;各组份在配方中所占比例不同, 有时甚至差异悬殊; 配料速度和精度要求高;配方可能经常变换、调整;物料可能受环境温度、湿度影响等特点,将系统设计成高精确度,高稳定性和快速性的符合工业标准的自动配料系统。
3.3 控制原理介绍及图示
自动配料的模拟面板如图2.1所示,从图中可以看出四节传送带是本次设计的核心电路,PLC编程也是围绕此面板进行的
图2.1 自动配料系统图
表2.1 输入/输出接线列表
表2.2 输入地址表
表2.3 输出地址表
3.4 控制方案
初始状态:红灯L2灭,绿灯L1亮,表明允许汽车开进装料。料斗出料口D2关闭,若料位传感器S1置为OFF(料斗中的物料不满),进料阀开启进料(D4亮)。当S1置为ON(料斗中的物料已满),则停止进料(D4灭)。电动机M1、M2、M3和M4均为OFF。
运行状态:装车过程中,当汽车开进装车位置时,限位开关SQ1置为ON,红灯信号灯L2亮,绿灯L1灭;同时启动电机M4,经过2S后,再启动启动M3,再经2S后启动M2,再经过2S最后启动M1,再经过2S后才打开出料阀(D2亮),物料经料斗出料。
当车装满时,限位开关SQ2为ON,料斗关闭,2S后M1停止,M2在M
1停止2S后停止,M3在M2停止2S后停止,M4在M3停止2S后最后停止。同时红灯L2灭,绿灯L1亮,表明汽车可以开走。
第四章硬件设计
4.1 PLC硬件构成
从结构上分,PLC分为固定式和组合式(模块式)两种。固定式PLC包括CPU 板、I/O板、显示面板、内存块、电源等,这些元素组合成一个不可拆卸的整体。模块式PLC包括CPU模块、I/O模块、内存、电源模块、底板或机架,这些模块可以按照一定规则组合配置。
CPU的构成:CPU是PLC的核心,起神经中枢的作用,每套PLC至少有一个CPU,它按PLC的系统程序赋予的功能接收并存贮用户程序和数据,用扫描的方式采集由现场输入装置送来的状态或数据,并存入规定的寄存器中,同时,诊断电源和PLC内部电路的工作状态和编程过程中的语法错误等。进入运行后,从用户程序存贮器中逐条读取指令,经分析后再按指令规定的任务产生相应的控制信号,去指挥有关的控制电路。
CPU主要由运算器、控制器、寄存器及实现它们之间联系的数据、控制及状态总线构成,CPU单元还包括外围芯片、总线接口及有关电路。内存主要用于存储程序及数据,是PLC不可缺少的组成单元。
在使用者看来,不必要详细分析CPU的内部电路,但对各部分的工作机制还是应有足够的理解。CPU的控制器控制CPU工作,由它读取指令、解释指令及执行指令。但工作节奏由震荡信号控制。运算器用于进行数字或逻辑运算,在控制器指挥下工作。寄存器参与运算,并存储运算的中间结果,它也是在控制器指挥下工作。
CPU速度和内存容量是PLC的重要参数,它们决定着PLC的工作速度,IO数量及软件容量等,因此限制着控制规模。
4.1.1 PLC各元器件参数
I/O模块:PLC与电气回路的接口,是通过输入输出部分(I/O)完成的。I/O 模块集成了PLC的I/O电路,其输入暂存器反映输入信号状态,输出点反映输出锁存器状态。输入模块将电信号变换成数字信号进入PLC系统,输出模块相反。I/O 分为开关量输入(DI),开关量输出(DO),模拟量输入(AI),模拟量输出(AO)等模块。
开关量是指只有开和关(或1和0)两种状态的信号,模拟量是指连续变化的量。常用的I/O分类如下:
开关量:按电压水平分,有220VAC、110VAC、24VDC,按隔离方式分,有继电器隔离和晶体管隔离。
模拟量:按信号类型分,有电流型(4-20mA,0-20mA)、电压型(0-10V,0-5V,-10-10V)等,按精度分,有12bit,14bit,16bit等。
除了上述通用IO外,还有特殊IO模块,如热电阻、热电偶、脉冲等模块。
按I/O点数确定模块规格及数量,I/O模块可多可少,但其最大数受CPU所能管理的基本配置的能力,即受最大的底板或机架槽数限制。
电源模块:PLC电源用于为PLC各模块的集成电路提供工作电源。同时,有的还为输入电路提供24V的工作电源。电源输入类型有:交流电源(220VAC或110VAC),直流电源(常用的为24VAC)。
4.1.2 PLC系统的辅助设备
1.编程设备:编程器是PLC开发应用、监测运行、检查维护不可缺少的器件,用于编程、对系统作一些设定、监控PLC及PLC所控制的系统的工作状况,但它不直接参与现场控制运行。小编程器PLC一般有手持型编程器,目前一般由计算机(运行编程软件)充当编程器。
2.机界面:最简单的人机界面是指示灯和按钮,目前液晶屏(或触摸屏)式的一体式操作员终端应用越来越广泛,由计算机(运行组态软件)充当人机界面非常普及。
3.输入输出设备:用于永久性地存储用户数据,如EPROM、EEPROM写入器、条码阅读器,输入模拟量的电位器,打印机等
4.1.3 注意事项
保证PLC的正常运行,因此在使用中应注意以下问题。
1.1 温度
PLC要求环境温度在0~55℃,安装时不能放在发热量大的元件下面,四周通风散热的空间应足够大,基本单元和扩展单元之间要有30mm以上间隔;开关柜上、下部应有通风的百叶窗,防止太阳光直接照射;如果周围环境超过55℃,要安装电风扇强迫通风。
1.2 湿度
为了保证PLC的绝缘性能,空气的相对湿度应小于85%(无凝露)。
1.3 震动
应使PLC远离强烈的震动源,防止振动频率为10~55Hz的频繁或连续振动。当使用环境不可避免震动时,必须采取减震措施。
1.4 空气
避免有腐蚀和易燃的气体,例如氯化氢、硫化氢等。对于空气中有较多粉尘或腐蚀性气体的环境,可将PLC安装在封闭性较好的控制室或控制柜中,并安装空气净化装置。
1.5 电源
PLC供电电源为50Hz、220(110%)V的交流电,对于电源线来的干扰,PLC 本身具有足够的抵制能力。对于可靠性要求很高的场合或电源干扰特别严重的环境,可以安装一台带屏蔽层的变比为1:1的隔离变压器,以减少设备与地之间的干扰。还可以在电源输入端串接LC滤波电路。
4.2 自动配料系统
系统启动后,配料装置能自动识别货车到位情况及对货车进行自动配料,当车装满时,配料系统自动关闭。本设计的突出点是故障检测部分的设计,首先,当某一节传送带发生故障时,该节传送带和其前面的传送带会立即停止,该节之后的传送带会在一定的延时后停止。其次,当某节传送带上的物体过重时,该节传送带和其前面的传送带会立即停止,并且数码显示电路会显示发生故障的电机的号码,该节之后的传送带会在一定的延时后停止。
4.2.1 自动配料系统控制图
1. 自动配料系统图
自动配料的模拟面板如图2.1所示,从图中可以看出四节传送带是本次设计的核心电路,PLC编程也是围绕此面板进行的
图2.1 自动配料系统图
自动配料系统的功能是利用四节传送带为小车自动配料,重物通过传送带进行传输,发生故障时系统自动停机。自动配料实验面板与PLC接线控制对应关系如表2.1所示。
表2.1 输入/输出接线列表
1. 数码显示电路
LED数码显示电路如图2.2所示。此电路在整个电路中起辅助性作用,即当四节传送带中的某一节发生故障时,LED显示有故障一节的编号,用户可以清楚的看到。
图2.2 LED数码显示电路
LED数码显示面板与PLC控制端口对应关系如表2.2所示。
表2.2 LED数码显示电路
第五章软件设计
5.1总设计流程图
图5.1自动配料流程图
自动配料系统的控制是采用PLC实现的,主要介绍的是PLC部分程序的实现过程。自动配料的流程图5.1所示。
5.2启动程序
启动时首先按下启动开关SB1,进入初使状态,表明允许汽车开进装料。料斗出料口D2关闭,若料位传感器S1置为OFF(料斗中的物料不满),进料阀开启进料(D4)。当S1置为ON(料斗中的物料已满)则停止进料(D4灭)。料斗装满后开始启动传送带,首先启动最末一条皮带机(D),经3秒延时,再依次启动其它皮带机,即D→C→B→A,最后D2亮,表示开始装车。启动程序流程图如下:
表5.1 启动程序
停止时先停止最前一条皮带机(A),待料运送完毕后再依次停止其它皮带机,即A→B→C→D。程序如表5.2所示:
表5.2 正常时停止程序
5.4有故障时停止程序
某条传送带发生故障时,该皮带机及其前面的传送带立即停止,而传送带以后的传送带待运完后才停止。例如,M1有故障时,M1立即停止,经过3秒后,M2停,再过3秒M3停,再过3秒M4停。部分程序如表5.3所示:
表5.3 有故障停止程序
当某条皮带机上有重物时,该皮带机前面的皮带机停止,该皮带机运行5秒以后的皮带机待料运完后才停止。例如,M3上有重物,M1、M2立即停,经过5秒,M3停,再过5秒,M4停。部分程序如表5.4所示:
表5.4 有重物时停止程序
如果存在几个皮带机上都有重物时,则存在优先级问题,即前面的优先级高于后面的。例如,M2与M3上同时有重物,在停机时应按M2上有重物进行处理。
故障流程图
图5.2 各故障流程图
5.6LED显示及复位程序
当四节传送带出现故障时,数码电路会显示出现故障皮带机的编号,故障排除后显示消失。例如,当M2出现故障时,数码电路会显示2,故障排除后数码2消失。部分程序如表5.5、5.6和5.7所示:
表3.5 LED数码显示主程序
续表3.5 LED数码显示主程序
表3.6 显示数字2子程序
表3.7 复位子程序
5.7系统调试
输入程序,编译无误后,运行程序。依次按表358中的顺序按下各按钮记录观察到的现象。
表5.8 系统测试结果
续表5.8 系统测试结果