喷雾干燥优缺点

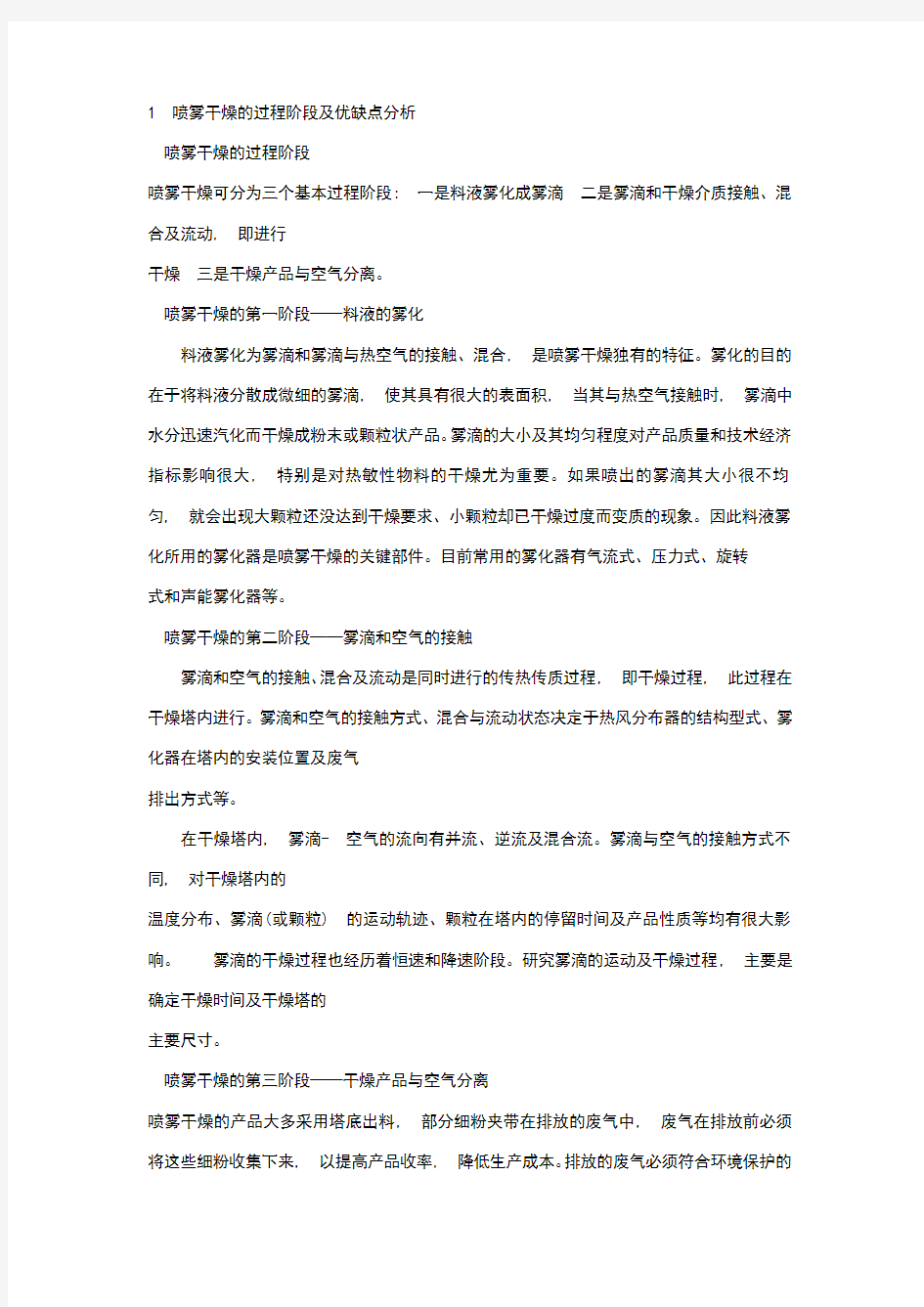
对喷雾干燥的过程阶段及优缺点进行了分析, 综述了喷雾干燥技术的研究进展, 并对喷雾干燥技术的应用前景进行了分析, 最后给出了喷雾干燥技术在中药制药生产中的应用实例——中药液一步喷雾干燥造粒。该项技术将中药稀药液直接喷雾干燥制成干颗粒, 将中药加工中药液的浓缩、多效浓缩、造粒、干燥四步合为一步, 大大简化并缩短了中药提取液到半成品或成品的工艺和时间, 提高了生产效率和产品质量。可
为喷雾干燥技术的推广应用以及提高中药制药水平提供借鉴与帮助。关键词喷雾干燥雾化技术喷雾造粒中药制药一步造粒
喷雾干燥是将原料液用雾化器分散成雾滴, 并用热空气(或其它气体) 与雾滴直接接触的方式而获得粉粒状产品的一种干燥过程。原料液可以是溶液、乳浊液或悬浮液, 也可以是熔融液或膏状物。干燥产品可以
根据需要, 制成粉状、颗粒状、空心球状或团粒状。
喷雾干燥技术已有一百多年的历史。自1865 年喷雾干燥最早用于蛋品处理以来, 这种由液态经雾化和干燥在极短时间直接变为固体粉末的过程, 已经取得了长足的进步。它使许多有价值但不易保存的物料得以大大延长保质期, 使一些物料便于包装、使用和运输, 同时也简化了一些物料的加工工艺。由于喷雾干燥具有“瞬时干燥”、“干燥产品质量好”、“干燥过程简单”等特点, 明显优于其它干燥方式, 到20 世纪三四十年代, 该技术已经被广泛地应用于乳制品、洗涤剂、脱水食品以及化肥、染料、水泥的生产, 目前常见的速溶咖啡、奶粉、方便食品汤料等就是由喷雾干燥得到的产品[ 1, 2 ]。我国最早将喷雾干燥用于工业化规模生产的是乳品行业, 之后是洗涤剂和染料行业等, 目前应用已十分广泛, 遍及了以上所涉及
的所有行业, 尤其在陶瓷和制药行业喷雾干燥的应用更为普遍。
对于中药制药行业, 喷雾干燥技术的应用有其独特的作用, 大大简化并缩短了中药提取液到制剂半成品或成品的工艺和时间, 提高了生产效率和产品质量。本文对喷雾干燥的过程阶段及优缺点进行分析, 综述喷雾干燥技术的研究进展, 并对喷雾干燥技术的应用前景进行分析, 最后给出喷雾干燥技术在中药制药生产
中的应用实例——中药液一步喷雾干燥造粒。
1 喷雾干燥的过程阶段及优缺点分析
喷雾干燥的过程阶段
喷雾干燥可分为三个基本过程阶段: 一是料液雾化成雾滴二是雾滴和干燥介质接触、混合及流动, 即进行
干燥三是干燥产品与空气分离。
喷雾干燥的第一阶段——料液的雾化
料液雾化为雾滴和雾滴与热空气的接触、混合, 是喷雾干燥独有的特征。雾化的目的在于将料液分散成微细的雾滴, 使其具有很大的表面积, 当其与热空气接触时, 雾滴中水分迅速汽化而干燥成粉末或颗粒状产品。雾滴的大小及其均匀程度对产品质量和技术经济指标影响很大, 特别是对热敏性物料的干燥尤为重要。如果喷出的雾滴其大小很不均匀, 就会出现大颗粒还没达到干燥要求、小颗粒却已干燥过度而变质的现象。因此料液雾化所用的雾化器是喷雾干燥的关键部件。目前常用的雾化器有气流式、压力式、旋转
式和声能雾化器等。
喷雾干燥的第二阶段——雾滴和空气的接触
雾滴和空气的接触、混合及流动是同时进行的传热传质过程, 即干燥过程, 此过程在干燥塔内进行。雾滴和空气的接触方式、混合与流动状态决定于热风分布器的结构型式、雾化器在塔内的安装位置及废气
排出方式等。
在干燥塔内, 雾滴- 空气的流向有并流、逆流及混合流。雾滴与空气的接触方式不同, 对干燥塔内的
温度分布、雾滴(或颗粒) 的运动轨迹、颗粒在塔内的停留时间及产品性质等均有很大影响。雾滴的干燥过程也经历着恒速和降速阶段。研究雾滴的运动及干燥过程, 主要是确定干燥时间及干燥塔的
主要尺寸。
喷雾干燥的第三阶段——干燥产品与空气分离
喷雾干燥的产品大多采用塔底出料, 部分细粉夹带在排放的废气中, 废气在排放前必须将这些细粉收集下来, 以提高产品收率, 降低生产成本。排放的废气必须符合环境保护的
排放标准, 以防止环境污染。
喷雾干燥的优缺点分析
喷雾干燥的优点
只要干燥条件保持恒定, 干燥产品特性就保持恒定喷雾干燥的操作是连续的, 其系统可以是全自动控制操作喷雾干燥系统适用于热敏性和非热敏性物料的干燥, 适用于水溶液和有机溶剂物料的干燥原料液可以是溶液、泥浆、乳浊液、糊状物或熔融物, 甚至是滤饼等均可处理喷雾干燥操作具有非常大的灵活
性,喷雾能力可达每小时几千克至200 吨[ 4 ]。
喷雾干燥的缺点
喷雾干燥投资费用比较高喷雾干燥属于对流型干燥, 热效率比较低(除非利用非常高的干燥温度) ,
一般为30%~40%。 2 喷雾干燥技术的研究进展
喷雾干燥技术的核心是流化技术, 具有从流体到固体瞬时干燥的突出优势。其设备一般是由雾化器(喷头) 、干燥塔、进出气及物料收集回收系统等组成。其中使料液雾化所用的雾化器是喷雾干燥装置的关键
部件。
雾化器的种类和雾化形式
一般在生产中常用的雾化器有气流式雾化器、压力式雾化器和旋转式雾化器几种。不同
的雾化器可以产生不同的雾化形式, 按照不同的雾化形式可以将喷雾干燥分为气流式雾化、压力式雾化和旋转式雾化。雾化形式的选择取决于料液的性质和最终产品所要求的特性。对于液体的雾化机理, 基本上可分为三种类型, 即滴状分裂、丝状分裂和膜状分裂。在喷雾干燥操作中, 雾化机理与雾化方法、操作条件、流体的物
性等有关。雾化机理可以指导我们进行合理的雾化器的设计和操作。
气流式雾化利用压缩空气(或水蒸气) 高速从喷嘴喷出并与另一通道输送的料液混合,借助空气(或水蒸气) 与料液两相间相对速度不同产生的摩擦力, 把料液分散成雾滴。根据喷嘴的流体通道数及其布局, 气流式雾化器又可以分为二流体外混式、二流体内混式、三流体内混式、三流体内外混式以及四流体外混式、
四流体二内一外混式等等[ 3 ]。气流式雾化器的结构简单, 处理对象广泛, 但能耗大。
压力式雾化利用压力泵将料液从喷嘴孔内高压喷出, 直接将压力转化为动能, 使料液与干燥介质接触并被分散为雾滴。压力式雾化器生产能力大, 耗能小细粉生成少, 能产生小颗粒, 固体物回收率高。旋转式雾化利用高速旋转的盘或轮产生的离心力将料液甩出, 使之与干燥介质接触形成雾滴。旋转式雾
化器受进料影响(如压力) 变化小控制简单。三种雾化器的比较见表1[ 3, 4, 5 ]。
三种雾化原理的理论研究, 主要围绕着喷雾器的关键参数与雾化性能而展开, 黄立新等[ 3 ]对此做了综述报道。这方面的研究将有助于喷雾器性能的改进, 也有利于应用过程中根据喷雾料液及其产品要求对雾化
器进行选择。
中药提取液的喷雾干燥, 基本上是以旋转式雾化和气流式雾化形式进行的, 而后者以小型试验设备多见。从雾化的实现而言, 压力式雾化需要高压泵和较大的雾化空间, 气流式雾化能耗又很高, 这些都限制了它
们的应用。相对而言, 旋转式雾化器技术要求相对较低, 是最容易实现的。
喷雾干燥机理的研究
影响喷雾干燥效果的因素很多, 除雾化器外, 还有干燥塔、进出气及物料收集回收系统以及整个干燥器系统。国内外许多学者对喷雾干燥的数学模型进行了研究, 以期给出干燥塔内气体流动状态和各种热力学参数的分布信息, 这对喷雾干燥器的设计、优化以及干燥效果等的提高都具有很重要的意义。吴中华等[ 6 ]应用气- 粒两相流理论和计算流体力学(CFD) , 结合喷雾干燥的特点, 建立了模拟喷雾干燥塔内气体- 颗粒两相湍流流动的CFD 模型, 并对实验室脉动燃烧喷雾干燥过程进行了数值模拟。其结果具有详细、直观的特点模拟得到的喷雾干燥塔内气相流场和各种热力学参数的分布信息, 可以为喷雾干燥器的设计、干燥过程的优化等提供参考。戴命和等[ 7 ]进行了喷雾干燥过程的热力学建模及仿真, 根据质量平衡原理、
热平衡原理和牛顿定律推导了逆流喷雾干燥过程的一维双向静态热力学数学模型它包括了物料温度方程、热风温度方程、颗粒速度方程、热风湿含量方程、物料含水率方程, 用MA TLA 仿真后, 得到了增大空气
量比提高空气温度更具技术经济性的结论。
喷雾工艺优化的研究
在喷雾干燥的实验研究方面, 康智勇[ 8 ]研究了压力式喷雾干燥塔喷嘴孔径对粉料的影响, 认为大孔径更适于喷雾颗粒的分布向大颗粒集中。王晓兰等[ 9 ]在工厂大生产的条件下研究了影响喷雾干燥粉粒粒度分布的因素, 分析了陶瓷坯料泥浆粘度、含水率、喷雾压力、喷雾器孔径与粉粒粒度分布之间的关系, 得出其影响系数由大至小分别为喷雾器孔径、压力、粘度、含水率等。杨志生等[ 10 ]在对农药水分散性颗粒喷雾干燥过程的研究中, 分析了干燥进气温度、进料量对干燥产品的悬浮率、粒子密度、粒子形状等的
影响。
喷雾干燥在越来越广泛的应用中, 已经不仅限于传统的干燥模式, 刘相东等[ 11 ]进行了脉动气流的喷雾干燥研究。利用脉动燃烧产生的高频脉动气流对aCl 溶液进行了喷雾干燥试验, 结果表明: 高温、高频振
荡气流下的喷雾干燥比传统喷雾干燥的蒸发速率提高了倍。
喷雾干燥技术的发展趋势
喷雾干燥技术应用广泛, 其优势明显, 但其理论仍然落后于实践, 突出表现在干燥理论的实践指导性差。干燥动力学、非球形颗粒的干燥模拟、喷雾干燥等领域有待进行更深入的研究[ 3 ]。喷雾干燥热效率低, 因此, 喷雾干燥的节能降耗问题就比较突出[ 1 ] 亚高温喷雾干燥(进风温度60~150 ℃) 、常温喷雾干燥(进风温度60℃以下) 、降低能耗与多级干燥等都将是今后的研究重点。另外, 喷雾干燥技术与具
体的应用领域结合还将用于喷雾冷却造型、喷雾反应、喷雾吸收、喷雾涂层和喷雾造粒等领域。
笔者认为, 在今后还应注意加强下述几方面的研究与开发。
(1) 采用组合干燥。当喷雾干燥本身不能完成干燥任务时, 首先要想到组合干燥。如喷雾干燥加流化
床(干燥及冷却)、喷雾干燥加带式干燥等。
(2) 雾化器的改进。当某种物料雾化很困难时, 可改进原有雾化器的结构, 以适应新物料的雾化要求。例
如, 对旋转雾化器已做了多种改进, 能够雾化粘性大的物料及喷雾造粒等。
(3) 静电雾化技术的研究与开发。此项技术正处于研究与开发阶段, 它可以制造出微米及亚微米级粒
子, 制造机能性粒子, 制造薄膜和喷涂等, 预测其将来有广阔的发展前景。(4) 开发和完善在线测量系统。使系统操作自动化, 确保产品的质量和产量。
(5) 开发过热蒸汽的喷雾干燥系统。这是一个闭路循环系统, 可以节省能量, 省去氮气循环的操作。(6) 利用计算流体力学(CFD) 的方法, 解决喷雾干燥器的设计问题。将来可以利用一些可靠的实验数据(包括流动图形) , 利用CFD 的方法, 比较准确
地算出干燥器尺寸及热风分布方式, 代替目前的半理论、半经
验的方法(目前的方法误差太大)。
(7) 开发专用喷雾干燥机, 以适应特殊物料的需要。如软化点低的中药、番茄粉、特殊食品等。专用
干燥机应达到这样的水平——不用做实验, 按物料性质直接选型购置。
(8) 控制环境污染。在设计时就必须考虑到系统的噪声、粉尘、排放的气体、湿法除尘的液体等对环
境不构成污染。